
3 minute read
Australian Rail Technology improving OHW safety
from REX Dec 2019
by Prime Group
Time-saving tech boosts OHW maintenance efficiency
Australian-owned electro-technology company Australian Rail Technology has developed a significantly more efficient way to isolate overhead traction supply.
TIME DELAYS ON RAIL NETWORKS have become a major issue for politicians and a source of ongoing frustration for commuters. One contributing factor is the technical challenge of isolating a set of complex systems that make up a rail network.
The problem: complexity, safety, time Most in the industry know that a modern electrified railway possesses a complex electrical distribution network consisting of multiple substations, protection and isolation devices, overhead wiring (OHW) and sometimes problematic sections and zones when it comes time to isolate them. The complexity of such systems and high-consequence nature of electrical work can make the maintenance and repair of equipment a time-consuming task. It is particularly problematic when an unplanned event occurs, impacting revenue service, and when overhead lines may be dragged down and potentially into contact with rollingstocks, other rail assets, or people.
“Currently the procedures for isolation and earthing of the OHW requires a switching crew to be deployed to the section isolators to isolate the section from the substation,” Australian Rail Technology (ART) national sales manager Darren Will tells Rail Express. “The work crews must then add additional rail connections from the OHW to the rail to short-out the section in the event of a fault. Only after both of these operations have been completed can a work permit be issued.”
This process can take several hours, and once work is complete must then be performed in reverse in order to re-energise the OHW.
In an era when operators are trying to send their network uptime up, and maintenance budgets down, crews are already contending with shorter maintenance windows and less staff to perform the works, and a lower tolerance for mistakes.
“Current procedures involve manually switching the isolator(s) and grounding or shorting the overhead to rail. Safety lockouts, including interlocking keys, prevent the inadvertent re-energising of the system. This method relies on the switch operator travelling to the switch location to isolate the supply, visually checking the isolator has successfully moved into the correct position and that the manual gate is locked in the correct position.”
Not only are both procedures timeconsuming, but physically travelling to those isolation locations can be problematic and in some instances dangerous for maintenance staff. “Then there’s tunnels...” Will adds warily.
ART’s Remote Isolation System Taking a pragmatic approach to developing a better solution for this complex issue, ART has invested time and resources in developing a motorised isolator system which is modular, compact and readily fitted to existing infrastructure. It removes the need to replace existing isolators and earthing switches, while providing core functionality and elements to support safety rating of the entire system.
A modular solution such as the ART Remote Isolation (RI) solution means flexibility in meeting different requirements as well as allowing component ART’s Remote Isolation solution.
approvals to be reused between different applications. The ART RI system contains a safety PLC allowing for flexibility of integration, and future proofing for unique system installations.
“The system not only provides a much faster time to isolation – improving operational efficiency – but assures a much higher level of safety by removing human error that currently exists with visual inspection requirements.”
The remote isolation ability can be staged through an initial implementation of remote switching which is then fully compatible with future remote isolation functionality enablement.
“For operators, maintainers, constructors and asset owners, ART is ready to supply your remote isolation needs,” Will concludes. “With a bolt-on ready product and engineering expertise to achieve integration with appropriate SIL ratings, save yourself the time of development and utilise and Australian-developed, adaptable, configurable and safe system for your AC and DC traction supplies.”
Visit ART at AusRAIL at Stand 160.
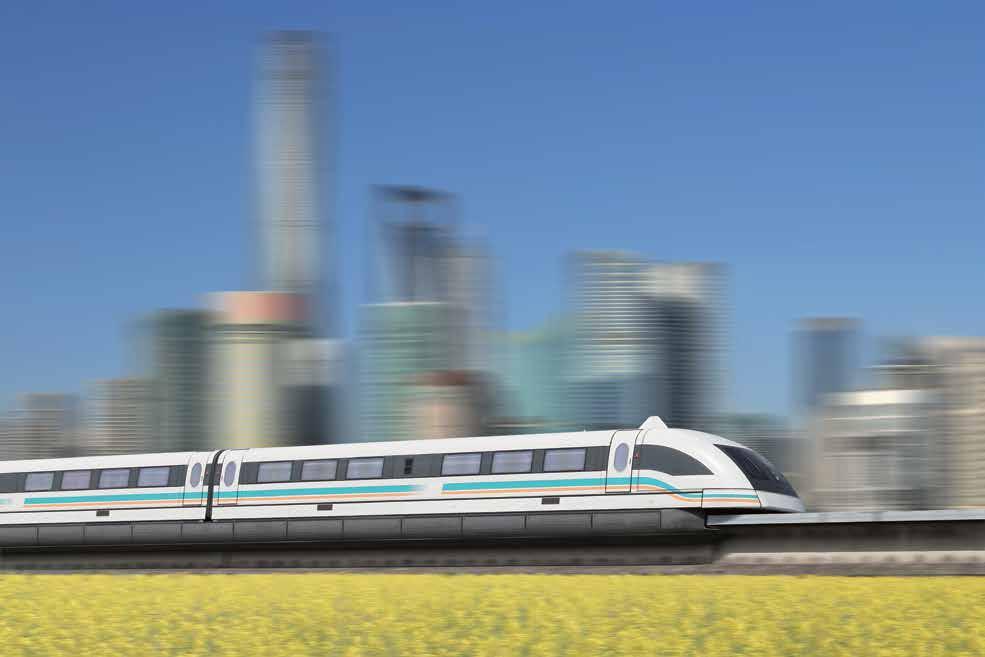


