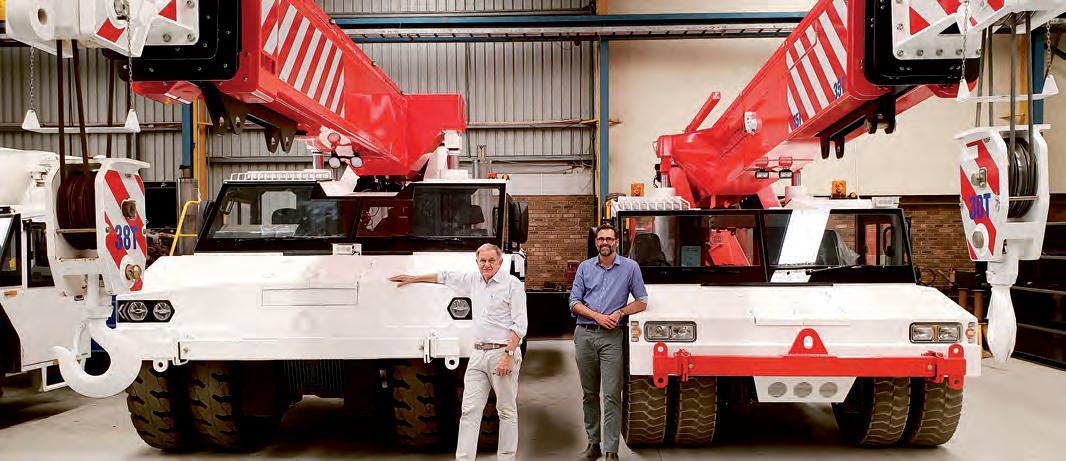
2 minute read
Humma pick and carry crane
HUMMA MAKES CONCRETE CASTING A BREEZE
LONG STANDING PICK & CARRY CRANE MANUFACTURER DRA GROUP IS BRINGING HUMMA CRANES TO THE ROAD CONSTRUCTION AND PRECAST CONCRETE INDUSTRIES. I n 1996 Construct Engineering a division of DRA Industries launched the Humma pick and carry crane project as the engineering division specialising in design and build of material handling systems had little design work available. At the time there was only one Australian manufacturer and a market survey confirmed a new entrant with innovative and new technology would be accepted by the construction and heavy engineering maintenance sector.
Peter Dalla Riva with his engineers prepared the crane specification which not only had many modern and innovative ideas but is the footprint of the Humma today, twenty four years later and five models built. The first model was the 18 tonne, followed by 20, 25, 35 and in 2018 the 55 tonne. The market has changed as items have increased in weight with Humma now supplying three models with the 35 and 55 tonne the preferred models.
The Pick & Carry market in Australia has evolved with Humma now the only Australian owned and manufactured crane with the Humma 55 the highest rated capacity articulated crane. The costs associated with Humma are the purchase price, operator/driver costs, maintenance and operating costs where fuel is the largest component. Humma 35 was subjected to 2000 hours hire over eighteen months by Hanchard Crane Hire which established fuel usage was up to 25% lower with minimal maintenance compared to the competition. Peter Dalla Riva said the design and quality of componentry on Humma is the reason for the savings.
The Cummins automotive engine is used in all models, although expensive it uses less fuel and the electronics allow the horsepower to be adjusted to suit the size of the crane and the one engine is used in the 25, 35 and 55 tonne cranes. The Jacobs brake is expensive but it greatly reduces the wear on brake pads. The air-spring suspension replaces the leaf spring used by others and greatly reduces road and engine noise and road vibration. The suspension not only gives the driver a comfortable ride, the cabin noise is below the Australian standard at 67 decibels and the absence of vibration extends the life of pivot bearings and eliminates weld cracking which in turn greatly reduces maintenance costs and crane downtime. Peter said Humma introduced the fully powered boom and still has the longest boom in the industry, digital rope compensation, auto levelling to Humma 55, unobstructed front vision of 180 degrees with four cameras allowing the operator to view the rear, sides and the winch while operating, all safe measures. There are Humma cranes approaching twenty years of operation with over 20,000 hours on the clock without having a ten year service.
There are long term Humma owners like Westlift in Victoria who operates a 20T and three 35T who states the biggest cost of Humma is the purchase price because from the day it starts working it saves money with its lowest operating costs. Humma is now the crane of preference where heavy lifts are involved, concrete casting yards finding the toughness, reliability and low operating cost a feature according to Peter and was used by John Holland in casting yards on projects in Brisbane and Sydney.