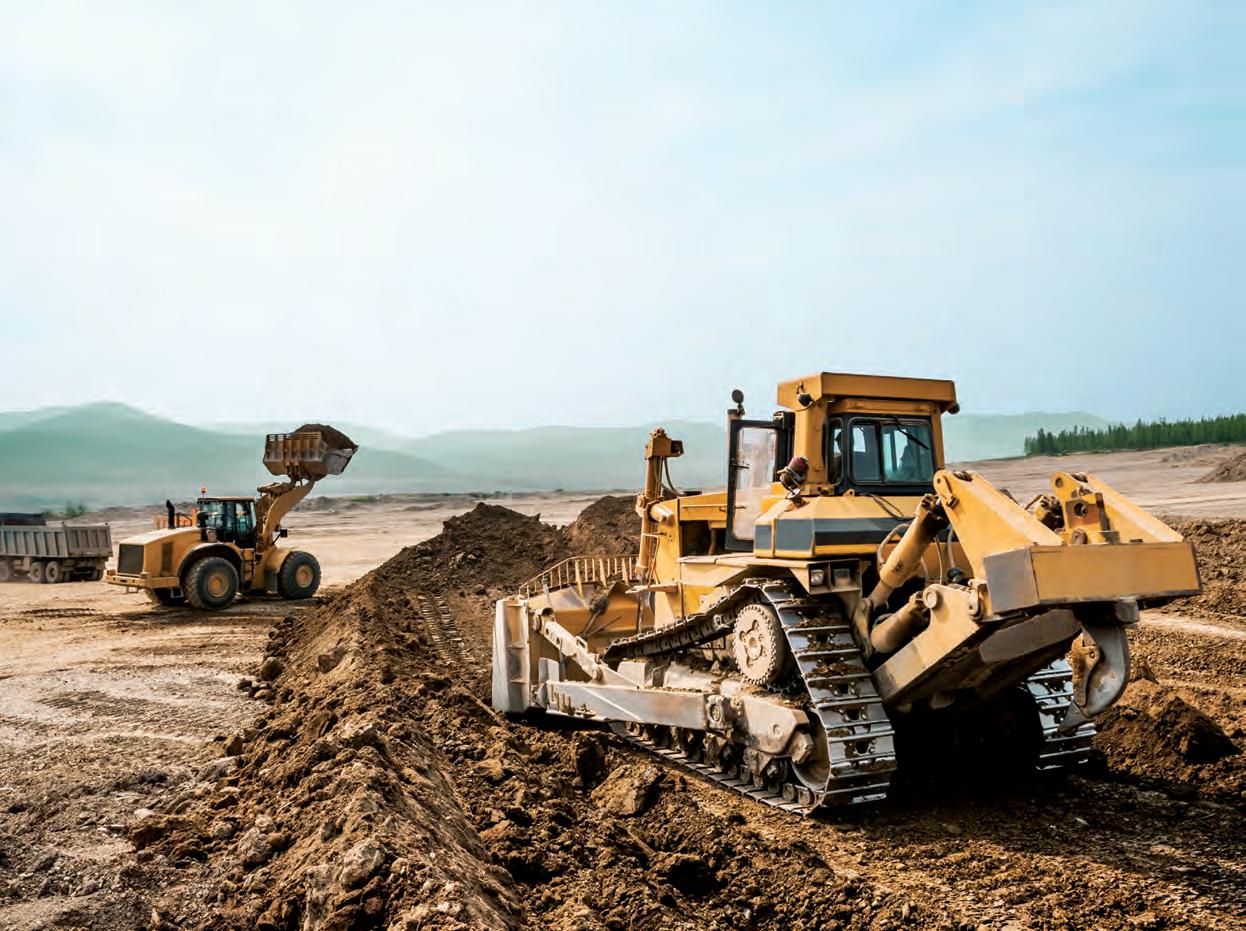
6 minute read
Covering unique risks
COVERING UNIQUE ROAD RISKS
THE ROAD CONSTRUCTION AND INFRASTRUCTURE INDUSTRY OPERATES IN ONE OF THE MOST DYNAMIC AND HAZARDOUS WORK ENVIRONMENTS, AND WHILE THERE ARE NUMEROUS FACTORS BEHIND CONSTRUCTION SITE CLAIMS, MOBILE PLANTS AND MACHINERY ARE INVOLVED IN A NUMBER OF THESE. T he basic engineering principles used in the construction of advanced plant and machinery involves the full spectrum of both mechanical and structural design. While some of these machines share a common goal and function, the types and uses of machinery fall into a wide array of applications.
These uses are subject to a number of environmental conditions and external forces, which include geographical location, terrain, wind, weather and frequency of use, as well as the operator’s experience and skill level.
According to Stan Alexandropoulos, Underwriting Agencies of Australia (UAA) Chief Operating Officer, the unique exposures that mobile plants and equipment face means adequately covering the sector is not a job for everybody.
“When we have machinery claims, they are usually low in frequency but high in severity, such as serious property damage and personal injury, so you need a very specialised product that identifies those exposures and makes sure that they are actually being covered and the insured’s business is effectively protected,” Mr. Alexandropoulos says.
“We’ve got a very comprehensive policy called the Industrial Special Plant (ISP) policy, which has been developed for mobile plant and machinery such as road making equipment.”
UAA, the largest specialist underwriting agency for mobile plant and construction equipment in Australia and New Zealand, has seven sections in its ISP policy, which cover the different exposures associated with the equipment.
The first section is Damage cover, where UAA will indemnify the insured against damage to a machine that occurs within the territorial limits and period of insurance.
“It’s what we call an ‘all risks’ policy, which pays for the machine to be repaired or replaced depending on the severity of the damage, while also covering other exposures likes theft and malicious damage. Basically, if it is not listed as a specific exclusion in our policy, then it is covered,” Mr. Alexandropoulos explains.
Under section two – Hired-in Plant cover – UAA will indemnify the insured against liability to the owner arising from damage to a machine hired by the insured that occurs within the territorial limits.
This must be during the period of insurance, during the period of hire, and while the machine is in the physical possession and control of the insured.
“If the insured hires equipment in from an equipment hire company, we will cover it even though they don’t own it, because these places require them to have some sort of insurance cover in place when
their equipment is hired,” Mr. Alexandropoulos says.
“We do offer an option for our clients to take out their own insurance cover, which usually ends up costing considerably less than what other hire companies charge for broader cover.”
UAA also has the ability to offer an annual blanket hired-in plant coverage which removes the need for the insured to notify their broker every time they hire something, reducing any gaps in cover.
This cover is increasingly important during busier times when the hiring in of machines is more prevalent such as the current business environment.
The third section, Additional Benefits cover, covers things like damage to transported goods, multiple crane operations, recovery costs and extra costs of reinstatement, new vehicle replacement, employee’s property damage, signwriting and emergency service charges, to name few.
In section four, Financial Protection cover, UAA indemnifies the insured against consequential loss that occurs during the indemnity period. This applies if damage to the machine or machine breakdown (if breakdown section is taken) occurs within the policy limits and if it causes interruption during the period of insurance.
“We cover things like loss of revenue associated with a piece of equipment in the event that it is damaged, and the client loses revenue because they are not working,” Mr. Alexandropoulos says.
“We can also cover exposures such as additional increased costs of working in the event of a claim, like the costs associated with hiring another piece of equipment in to do the job.”
The high cost of the equipment insured by UAA often means it is financed. UAA also covers the monthly finance cost in the event of a claim while it is not working.
Section five is Breakdown cover, which is where the insurer will indemnify the insured against breakdown damage that occurs in a machine within the policy limits and definitions and during the period of the insurance.
In section six, Road Risk cover, UAA will indemnify the insured against legal liability for personal injury or property
Stan Alexandropoulos says its important UAA clients get the right expertise and service.
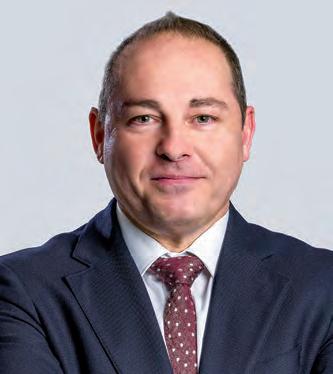
damage first occurring during the period of insurance, and caused by an occurrence within the territorial limits arising from using, operating or towing a roadregistered vehicle/machine in connection with the business.
“This is covering road-registered machines such as a road-registered roller or backhoe whilst it is travelling on a road and being used as a road vehicle and not performing as a tool of trade,” Mr. Alexandropoulos says.
Finally, in section seven – Broadform Liability cover – the insurer will indemnify the insured against legal liability for personal injury, property damage or advertising injury first occurring during the period of insurance, and caused by an occurrence in connection with the business.
“It’s a public liability policy that covers the declared activities of our client, and that is the full business activities of our clients, not exposures and claims associated with the plant and machinery only,” Mr. Alexandropoulos says.
“For example, if a machine was to crash into a building and our insured was deemed to be negligent, we will cover the damages to the building, as well as any third-party personal injuries that may occur in the incident.”
Mr. Alexandropoulos also notes that the claims they deal with are more often than not related to human error.
“Machines these days, particularly the newer ones, are all very high tech – they’ve all got sophisticated safety mechanisms such as alarms and cut-off switches, which pretty much protects them from most situations, so we still find human error to be the most common cause of a claim,” Mr. Alexandropoulos says.
He adds that while mistakes do happen, the number of incidences has reduced as the industry in general has become more professional and companies are increasingly training and hiring more qualified and experienced operators.
“In saying that, we also find that claims increase during the busier times like the current business environment. Either way, UAA has your back,” Mr. Alexandropoulos says.
UAA has very specialised local claims teams who are experienced in all manner of plant and machinery claims, and when an incident occurs, aim to be quick to appoint the right assessor and repairer.
“We don’t have in-house assessors or repairers, they are all third party, but we go out and recruit them based on competency on different types of equipment.
“They are specialists in these pieces of equipment.”
Mr. Alexandropoulos also stresses the importance of appointing the right assessor and repairer at the beginning to get the process off to the best start possible.
This enables the item of machinery to get back up and operating and making money for owners as soon as possible.
“Most manufacturers prefer to replace parts and machines in these situations, but we always try to repair rather than replace if possible, because when a part or machine is replaced, you’ve usually got to wait quite some time for those parts to be delivered as they mostly come from overseas,” Mr. Alexandropoulos says.
“Commonly that can take many months for delivery, in some cases taking up to 12 months for some less common parts or machines to arrive.
“In cases like that, contracts are often lost because the principle contactor can’t or won’t wait that long, so they’ll find someone else who can [complete the job],” he says.
“So, it is really worthwhile for our clients to have the right coverage, the right service and expertise, and get their machine repaired properly and have it up and running and making money as soon as possible.”