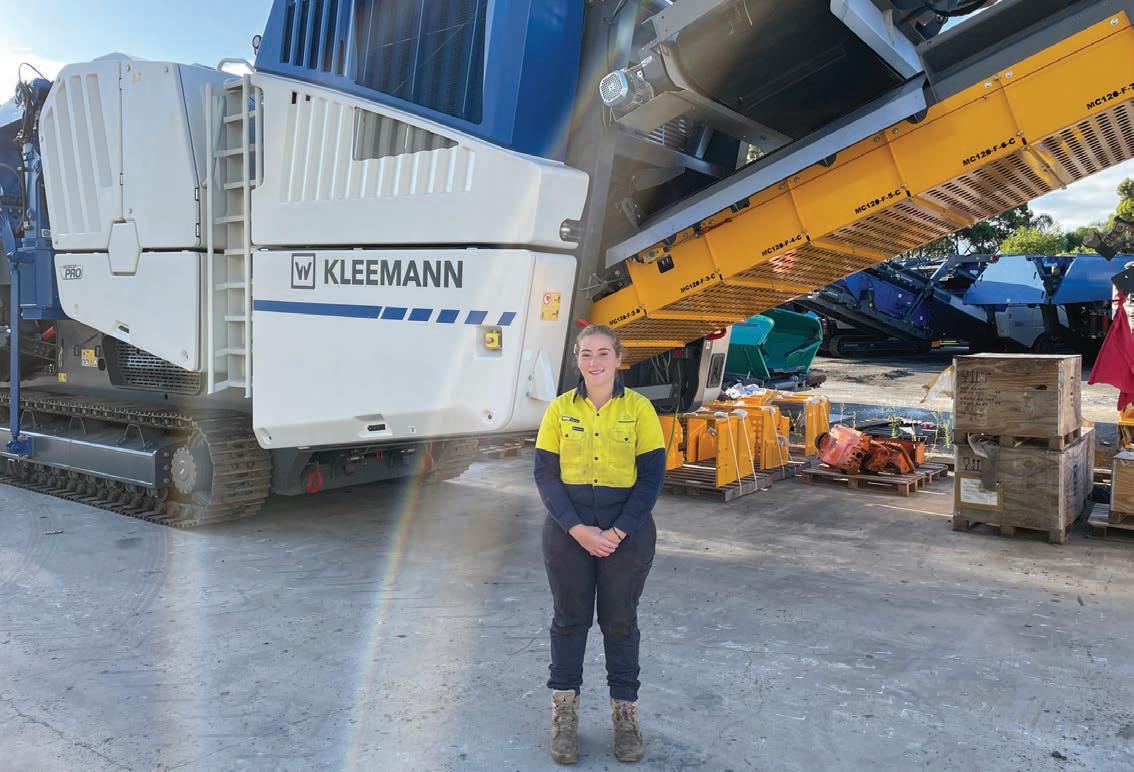
4 minute read
Learning by doing
Rebecca Kassabian is Wirtgen Australia’s fi rst female Apprentice Technician.
ROADS & INFRASTRUCTURE CAUGHT UP WITH WIRTGEN AUSTRALIA’S FIRST FEMALE APPRENTICE TECHNICIAN TO LEARN ABOUT HER EXPERIENCE SO FAR AND HER GOALS FOR THE FUTURE.
In 2021, when Rebecca Kassabian saw an advertisement online for a service technician vacancy that offered vocational training and apprenticeship by Wirtgen Australia, she didn’t know what to expect from the job. She had never worked with vehicles or heavy machinery, except for her year-long experience as traffi c controller.
Seven months into the four-year program as Wirtgen Australia’s fi rst female Apprentice Technician, she’s fi nding the job a lot more interesting than she had imagined.
“I didn’t think I’d enjoy it as much as I do,” says Kassabian. “Every day is different. We come into the workshop every morning and we are assigned the required tasks for the day, which can be anything from servicing machines, building or preparing new machines to be sent out or helping introduce customers to the machines they have purchased.”
While the program combines theoretical classes at TAFE New South Wales with hands-on experience at Wirtgen’s workshop in Western Sydney, Kassabian says most of her learning so far has come from working with experienced Wirtgen service technicians and learning on the job.
“Apart from another second-year apprentice and myself, everyone here is fully qualifi ed. So, if I ever struggle with anything, I can just ask one of the guys and they will point me in the right direction, whether that’s using a different tool or just using the tools differently.”
Kassabian says while her family were supportive of her career choice, some thought she might not be cut out for it.
“My brother thought I was not ‘hardy’ enough,” she jokes.
But the experience is already coming in handy, she says. Recently, she was able to replace the water pump on her own car without much help from her supervisor.
Kassabian’s training exposes her to working on the full range of Wirtgen Group’s machinery, from Kleemann cone crushers and screens to Wirtgen’s rollers, asphalt pavers, milling machines and more. But her core focus is to become an expert on repairing Kleemann crushers.
“At some point in the future, I can see myself heading out to the country and working solely on crushers. For now, I just want to learn as much as I can and grow my skills. We have a mechanic here in the workshop who knows everything there’s to know about Kleemann crushers. My goal is to get to that level,” she says.
WIRTGEN’S TRAINING MODEL The apprenticeship program, which has been offered by Wirtgen Australia since the late 1990s and more regularly since 2021, is part of the company’s strategy to absorb and train the right talent, Chris Adams, Wirtgen’s Service Manager for Australia and New Zealand, explains.
“To date, every Wirtgen apprentice who has completed their apprenticeship has been offered a full-time position with Wirtgen,” Adams says.
“Wirtgen fi rst engaged apprentices back in the late 1990’s with an intention to invest, grow and provide development paths. Since then, we have become a lot more structured in our approach to apprentices and have developed the program to a point where we employ 12 per cent of our service workforce via the apprentice program. Our goal is to increase this to 20 per cent by 2024.”
While the program’s intake has been intermittent in previous years, Adams says Wirtgen is looking to expand its apprenticeship program.
“Wirtgen Australia operates in a comparatively small niche market, which creates some limitation with respect to the sheer number of apprentices we employ. With that said, it also enables us to be dynamic and personable when it comes to our staff and particularly the apprentices.”
The Wirtgen program is currently offered in New South Wales, Queensland, Western Australia and Auckland, New Zealand.
“Wirtgen has always strived to provide opportunities for education and work experience. Together with an apprenticeship provider we look for candidates who are eager and have the willingness to learn and constantly be challenged. We seek candidates who are resilient. Our technology continues to evolve and so must our work practices.”
Adams, who himself completed his apprenticeship with Wirtgen in 2006, says seeing more female applicants and people with disability show interest in the training is a positive and welcomed sign.
“Since the introduction of the program, Wirtgen has made it a priority to diversify our staff intake, provide equal opportunities and promote all applicants to come forward. In 2021, we employed our fi rst female Apprentice Technician and hope to provide future employment on the successful completion. Wirtgen believes diversity is one of the critical ingredients of a healthy work environment,” says Adams.
“Both Wirtgen and our parent company John Deere believe that by strengthening the diversity of our workforce, we can provide everyone an equal opportunity to achieve their best and make the biggest impact as their true self.”
PGXpand®
A Unique Innovative Polymer
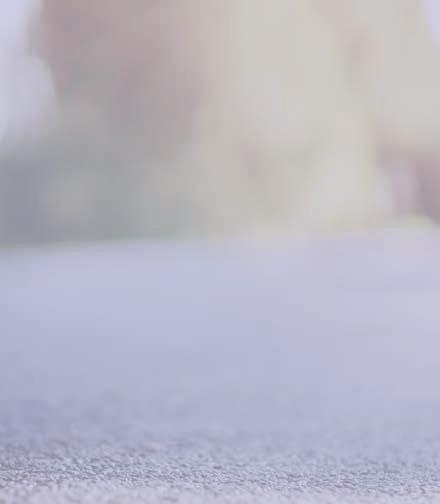

PGXpand enhances high temperature properties and delivers outstanding rutting resistance, fatigue properties & durability. Easy to use.
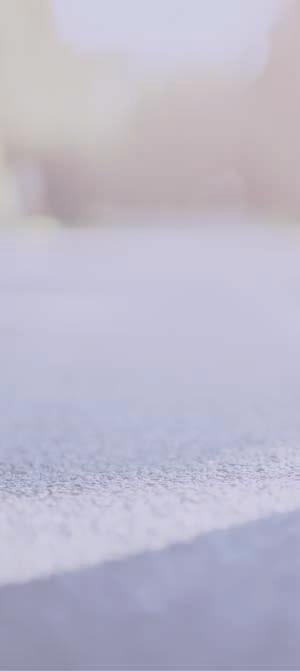
Tested. Proven. Trusted by users worldwide.
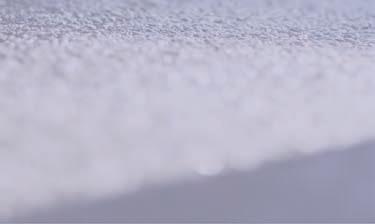
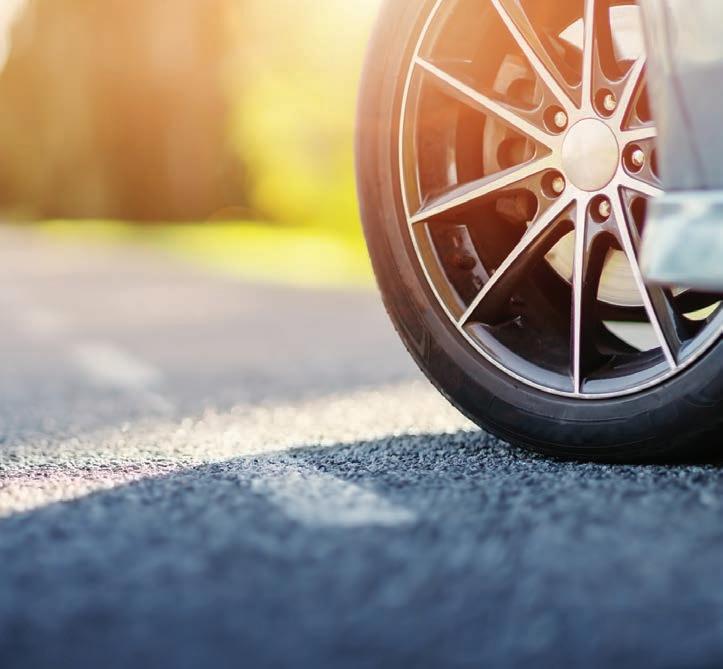