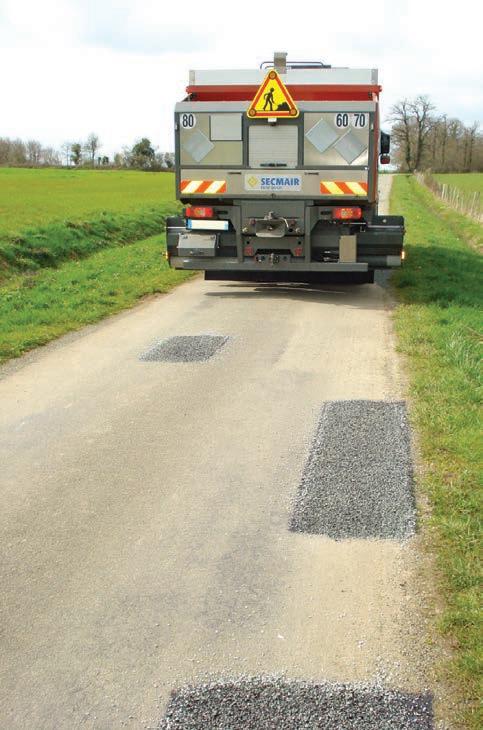
5 minute read
Secmair’s Chipsealer moving forward
A Chipsealer fi tted onto a four-axles truck. The machine can be designed according to the truck chassis type.

The Chipsealer can handle multiple sprayed seal repairs on the go.
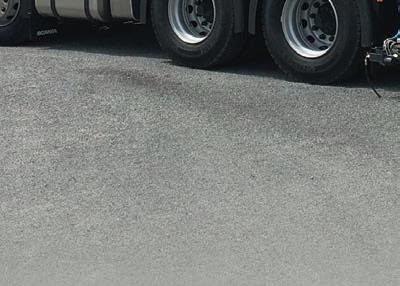
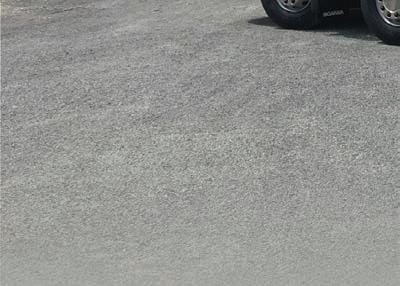
SECMAIR’S CHIPSEALER
MOVING FORWARD
SECMAIR’S CHIPSEALERS HAVE BEEN USED FOR 40 YEARS IN FRANCE. THEY ARE NOW BEING USED IN MANY MORE COUNTRIES FOR ALL TYPES OF SPRAYED SEAL APPLICATIONS. ROADS & INFRASTRUCTURE LOOKS AT THEIR EVOLUTION AND CURRENT APPLICATIONS.
When the fi rst Secmair Chipsealer – also called Secmair synchronous sprayer-spreader – was invented in early 1980s, it had been designed specifi cally to carry out sprayedseal patch repairs. Since then, its use and technical capabilities have evolved, making it suitable for different types of sprayed-seal applications.
Sprayed-seal treatment is one of the most popular road maintenance techniques in the world. The traditional setup for sprayed-seal applications consists of the binder sprayer on one side, and a chipspreader on the other side. While this setup is still used to apply sprayed seals, having multiple equipment and operators involved (even for small to medium jobs), and the time lap between the movement of the sprayer and the chipspreader, can pose constraints to the application process.
ONE MACHINE, ONE OPERATOR For small to medium sprayed-seal treatments, the Chipsealer is an alternative to consider. It offers the option to apply a high-performing sprayed seal with only one machine and one operator.
By simultaneously spraying the asphalt and spreading the chips while the binder is still hot, the Chipsealer guarantees perfect bonding between the two materials. Applications rates for both materials are computer controlled to ensure a high level of accuracy. As the machine is forward operated, no truck drives on the freshly applied surface.
The spray bar is equipped with an independent left/right hydraulic height adjustment, making it easy to precisely control the spray pattern. This also means if there’s a side shift, such as while turning, the binder still gets perfectly covered by the chips. The spray bar has a working width of up to 4.4 metres, offering coverage for an entire lane section in a single pass.
Last but not least, having a single machine on site with a compact overhang means it’s easier for operators to access narrow jobsites.
THE PATCHING PROCESS Consistent with what it has been originally designed for, the Chipsealer can handle multiple sprayed seal repairs on the go. Thanks to Secmair’s long proven New Pilot
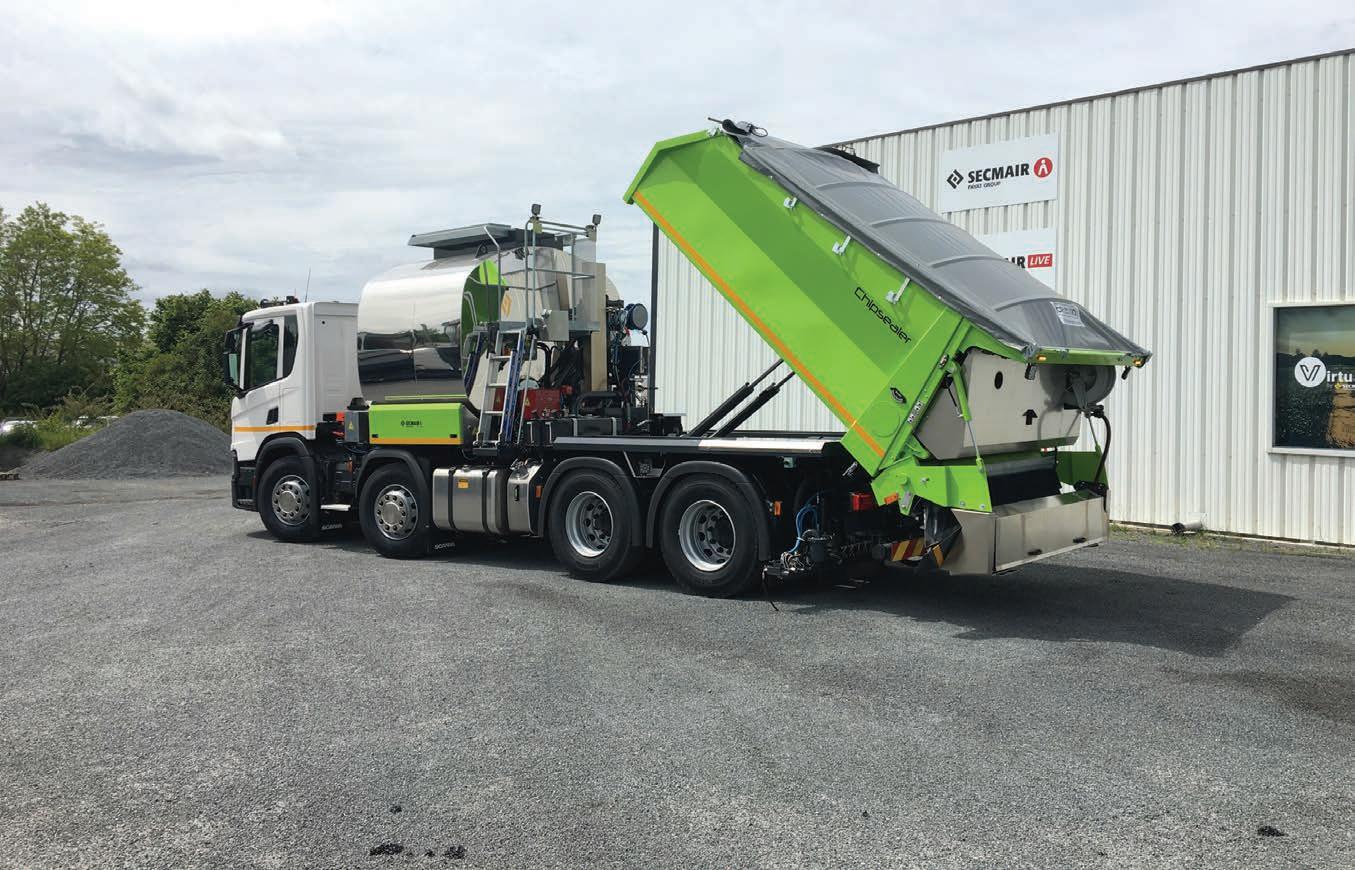


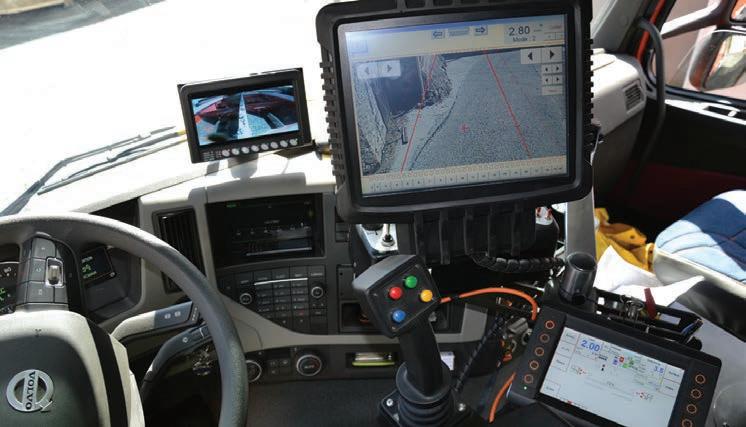
The New Pilot Video system provides an eightmetre-long road view to the operator.
system, the operator can defi ne the sections he needs to repair anywhere across the working width with an adjustable patch width of 200 millimetres – all while sitting in the cab.
A video camera fi tted to the front of the truck provides an eight-metre-long road view to the operator through a video screen. Superimposed on the road view, the operator can trigger the machine using a joystick to draw the patch as per the road repair requirements.
This feature offers a unique way to provide a preventive maintenance approach, which complements the standard sprayed seal applications.
HOT BINDER APPLICATIONS Some specifi c sprayed-seal applications may require spraying hot binder with temperature as high as 200°C, depending on the binder’s class and whether it is polymer modifi ed (e.g., with crumb rubber). In addition to the high-temperature binder – which requires a Dangerous Goods compliant machine – high application rates might have been specifi ed.
Secmair can provide Chipsealers with an appropriate binder system to tolerate such high temperatures. In combination with Secmair’s standard fully automatic purging system, a thermal oil heating system, consisting of binder pump, fi lter, and spraybar, can also be proposed for the binder system to avoid clogging.
Where a high application rate is required, the asphalt system can deliver up to 3 kg/m² with a full spraying width operation.
LIGHT BINDER SPRAYING Another area of application for the Chipsealer is in light binder spraying, such as for typical tack coats/bond coats.
Due to the Chipsealer’s computerised system, the operator can reach application rates as low as 0.1 kg/m². The machine will then propose the right application condition to get the right pressure in the system to get a good spray. Depending on the required range of application rates, Secmair’s experts can advise on the right nozzle type on offer.
With the techniques involving light application of materials expanding in the market, new solutions are coming to the world of road maintenance. ASI Solutions’ Rhinophalt is one such asphalt treatment solution. Rhinophalt bonds with the bitumen binder through a cold spray-applied process to slow down the rate of deterioration. Due to a collaboration between Secmair and ASI Solutions, Secmair customers can now use the Chipsealer for this process.
NEXT STEPS David Redelsperger is Secmair’s Area Sales Manager for the Oceania region, based in Melbourne. In his role, he oversees the Australian and New Zealand markets and responds to customer queries.
He says thanks to local support provided by Secmair, some of the best-known contractors are already teaming up with Secmair.
“We currently have some more units on order to be delivered within the next few months to handle crumb-rubber sprayed seal, Rhinophalt or computer-controlled tack coat, to name a few. You will keep hearing and seeing more of Secmair,” he says.
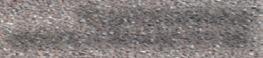
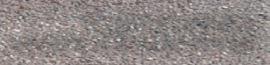
The synchronous forward application of the binder and chips.
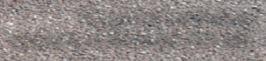
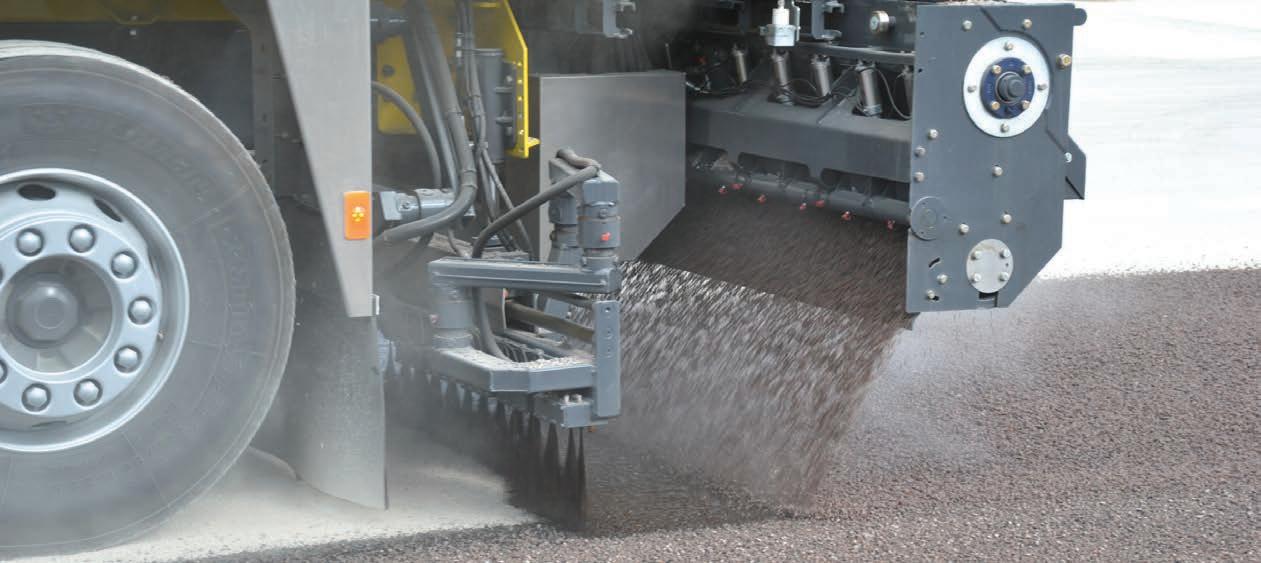