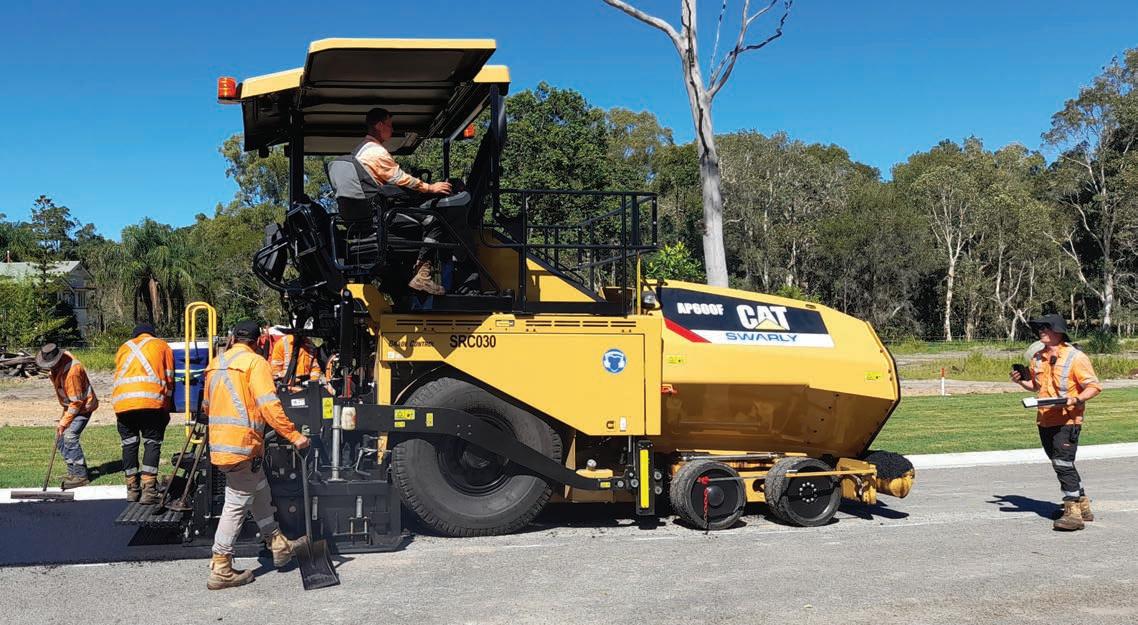
5 minute read
From strength to strength
GOING FROM STRENGTH TO STRENGTH
SINCE UPGRADING TO THE CAT AP600F WHEEL ASPHALT PAVER, SWARLY ROAD CONSTRUCTION HAS SEEN THE DOORS OPEN TO LARGER PROJECTS AND MORE WORK VOLUMES. OPERATIONS SUPERVISOR ADAM DAHLENBURG SAYS HASTINGS DEERING’S SUPPORT HAS BEEN INVALUABLE TO THE COMPANY.
Started out as a cartage service company in the Moreton Bay region in Queensland, family owned and operated business Swarly Road Construction has since grown its asphalt paving business to conduct multiple residential, commercial and industrial projects in Brisbane, the Sunshine Coast and Gold Coast.
Over the last three to four years and with support from Hastings Deering, Swarly Road Construction has actively grown its fl eet of Caterpillar asphalt paving machinery, while training and hiring more operators to grow its team of paving experts.
Adam Dahlenburg, Operation Supervisor at Swarly, says the addition of a Cat AP600F Asphalt Paver to the company’s fl eet was a “no-brainer” as the team looked to expand its fl eet.
“I decided we should go with the Cat paver as they’ve got a lot to offer. With the value of the machine and the cost and availability for parts, it was a sensible choice for us,” he says. “With some other [machinery manufacturing] companies, parts are a lot harder to come by. Caterpillar’s record for spare parts and their warranty is really impressive.”
KEEPING QUIET Initially, Swarly operated as a labour hire business, sending crews who would operate other contractor’s machinery. Over the past few years, the company has grown its own fl eet of machinery.
Purchasing the AP600F Asphalt Paver marks the company’s fi rst introduction into larger machinery, having owned the smaller Cat AP300 Paver prior to this. Dahlenburg expects the purchase to provide a signifi cant increase in the company’s capabilities to undertake larger projects.
With a large number of Swarly’s paving operations happening close to residential areas, quietness is another key feature in the Cat paver that has impressed Dahlenburg.
“In terms of operating the machine, one of the standouts is the reduction of noise when operating the paver. They are probably one of the quietest machines around.”
Ryan Van Den Broek, Industry Manager for Road Construction at Hastings Deering, says the AP600F Wheel Asphalt Paver is ideal for contractors who usually operate within urban areas, due to its reduced sound output.
“For projects in urban area, noise is very much a concern. The F Series pavers are
Queensland-based Swarly Road Construction recently acquired a new Cat AP600F Wheel Asphalt Paver.

Cat supplier Hastings Deering has been supporting Swarly Road Construction with training and aftersales services.

Swarly Road Construction is aiming for bigger paving projects with its new Cat paver.
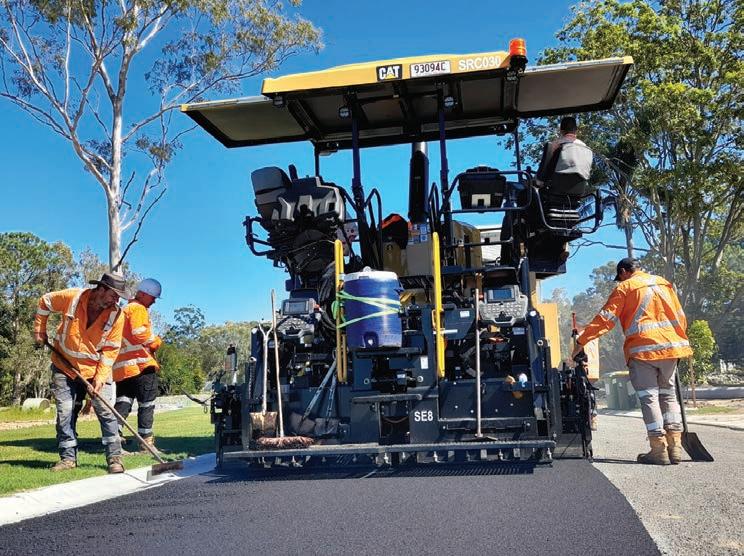
very quiet machines. They are designed to be quiet and for the noise and emissions to be moved out of the way of the driver,” Van Den Broek says.
This is in part thanks to the AP600F Asphalt Paver’s ‘Eco-Mode’. This operating option uses a lower engine speed of 1650 roundsper-minute (RPM) to moderate noise, as well as reducing fuel burn by fi ve per cent over Cat E-series pavers.
Additionally, the top-mounted airfl ow system in the F Series pavers is designed to direct fumes and sound away from the crew, creating a more operator-friendly environment.
Van Den Broek says the AP600F Asphalt Paver provides the operator with a fl exible paving solution.
“Like all Caterpillar machines, the AP600F Asphalt Paver is very productive. It has features that really help to produce a high level of rideability for customers and satisfy the parameters of the project,” he says.
EASE OF OPERATION As an experienced Operation Supervisor, Dahlenburg says the simplicity of operation is essential as operators switch from one machine to another.
“When learning how to operate a new machine, it’s very similar across different pavers, it’s just about the new features and how they work,” he says.
All Cat F Series asphalt pavers, from the AP300F up to the AP1000F model, feature the same operating console. This enables the user to change between machinery, without having to re-adjust to different controls.
Van Den Broek says the implementation of the same operating console provides comfort to operators.
“The functions are all the same, the buttons are in the same position, so it creates more comfort and confi dence for operators as they go from one machine to another.”
Additionally, Hastings Deering branches also provide training and even re-training for their customers – a service that Van Den Broek says customers appreciate even more with the current shortage of skills in the industry.
“We understand that there is a turnover of staff and operators in the paving industry. Right now, there’s also a shortage of people in the workplace, so people move around more often. Our local branches are offering a lot of re-training and follow-up training to our customers to make sure they are getting the most out of their machine,” he says.
During his experience with Hasting Deering’s Sunshine Coast and Brisbane branches, Dahlenburg says Swarly Road Construction has been supported every step of the way.
“They are very close to us, as their main workshop is in Caboolture so it’s really great. They have provided a very good service,” he says.
“Hastings has assigned one paving specialist to look after us exclusively. I can talk to him if I have any issues, parts requirements, or enquiries about warranty, etc. It really has benefi tted our business,” he adds.
With more and more investments pouring in from the federal and state governments into road projects in Queensland, Van Den Broek says the Hastings Deering team is geared up to support growth for its customers like Swarly.
Currently, the Hastings Deering branches across all major cities in Queensland are helping maintain a fl eet of over 70 Caterpillar Asphalt Pavers for their customers, while also providing follow-up training and preventive maintenance services to those who require them. Van Den Broek says the team is growing to keep up with the increased demand.
“As the size of the existing equipment across the state grows, so does our support team. We have recently hired a new application specialist to help with the followup training sessions. We are also stocking more parts at our regional branches in Cairns, Townsville, Rockhampton and Darwin to assist customers,” says Van Den Broek.
“Hot mix asphalt is a perishable product, so our customers often cannot afford to wait for parts delivery when they have a breakdown. Our product support representatives are the fi rst point of contact, wherever in Queensland or the Northern Territory our customers may be. This gives them confi dence and peace of mind knowing that we are just a phone call away.”
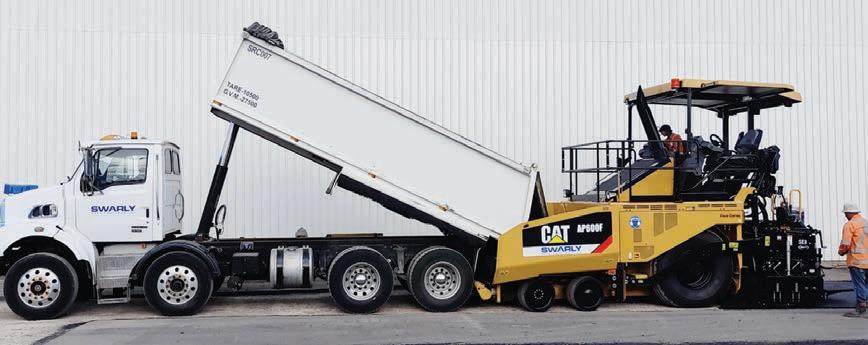
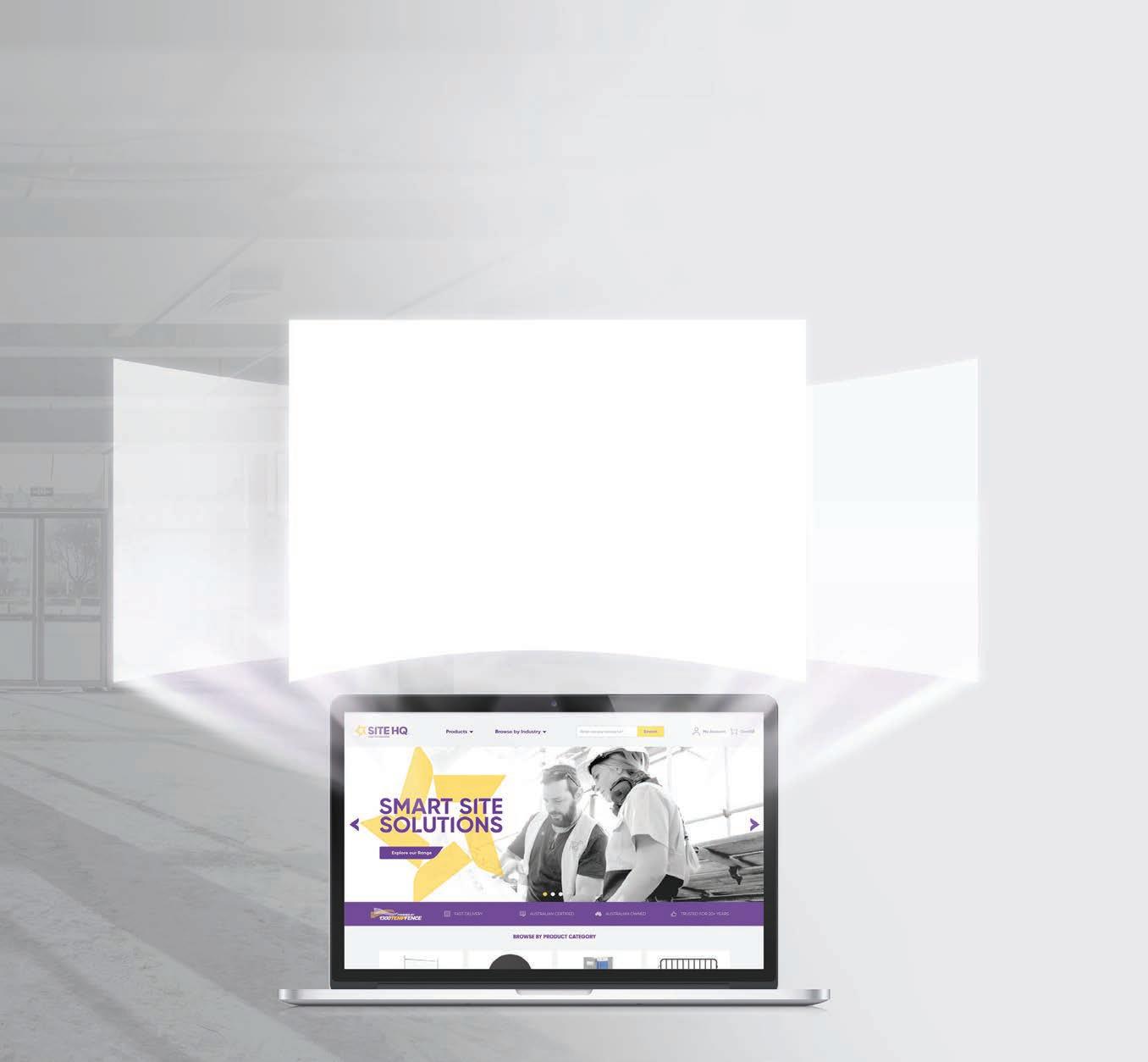
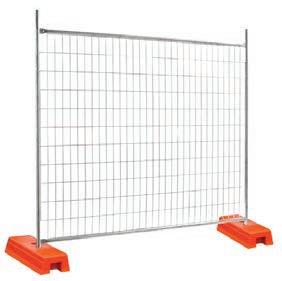
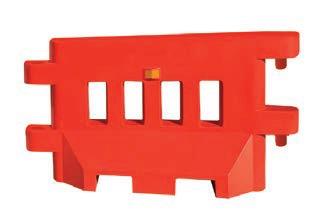