
5 minute read
Mixing time tech
MIXING FOR HIGH PERFORMANCE
TO CREATE A HIGH-PERFORMANCE ASPHALT MIX, THE AGGREGATES AND BINDER NEED TO BE SEAMLESSLY BLENDED. CIBER’S MARCELO ZUBARAN EXPLAINS HOW MIXING TIME CONTROL CAN HELP IMPROVE THE ADHESION OF ASPHALT MIXES.
As the chemical bond between aggregates and bitumen depends heavily on the minerals that constitute the aggregates, quality asphalt relies on these materials being well mixed.
For aggregates that are more challenging to bond with bitumen, such as granite, mixing control can play a key role in ensuring the final asphalt mix is of a high quality.
Ciber Equipamentos Rodoviários, commonly known as Ciber, has been making asphalt plants for around 60 years. The company has delivered more than 1800 asphalt plants across the globe, including in Australia.
Marcelo Zubaran, Ciber Product and Application Specialist, says the company has been exploring ways to improve mix adhesion. To that end, Ciber has found certain factors can influence the final product. The first is applying high shear mixing force between the materials, which ensures the aggregates are coated.
“Once the mixing project requirements are defined with inputs and proportions of material, it is possible to enhance adhesion between materials in the asphalt plant through mixers,” Mr. Zubaran says.
“Granite, for example, has clay minerals, which do not bond well with bitumen. Instead, granite attracts water, and if water comes between the bitumen and the aggregate, the final mix will be poorly bonded and may result in quicker pavement degradation.”
If mixers provide a high shearing rate, this can help guarantee the final asphalt mix is bonded well and will
The first image shows an iNOVA 1500 plant by Ciber with different filling levels, from 30 to 70 per cent. In this case, the best mix had 60 per cent of the filling level.
perform to a high standard.
To achieve high shearing rates, an external pug mill mixer can be used. Although this is traditionally used on batch plants, Ciber has refined its pug mill mixer to operate on continuous plants.
“Batch plants were the first to use pug mill mixers because the production is cyclic. This means there is no need for a specific material movement in the mixer as afterwards the mix falls down, by gravity, towards the truck bucket or to a storage silo,” Mr. Zubaran says.
“Conversely, the continuous mixer must project the mix forward in a continuous flow to avoid material sticking to the plant in the process.”
Because a pug mill mixer consists of a double axis mixer, with arms and paddles that rotate and strike the material continuously, it helps to force the adhesion of the binder and aggregates.
“The pug mill mixer helps to make certain all surfaces of the aggregate are coated with bitumen, but it also ensures the bitumen is injected into the mix at a controlled temperature,” Mr. Zubaran says.
The burner and the pug mill mixer are separate components, so this eliminates any chance that the bitumen will be heated by the burner flame before being added to the mix.
“In some asphalt plants without pug mill mixers, the bitumen is injected inside the drum and close to the flame, and this can cause the binder to prematurely oxidise and affect pavement performance,” Mr. Zubaran says.
He says that in addition to high shear force, Ciber has found mixing time to be an important factor that can influence the adhesiveness of the asphalt mix.
“In general terms, the longer the mixing time, the larger the capacity to homogenise the materials,” Mr. Zubaran says. In batch plants, he says, the production rate depends on the size of the mixer, how much material it can mix for each cycle and on the cycle time. However, the only variable in batch plants is the mixing time. The material quantity or filling level inside the mixer will normally be the maximum capacity of the plant.
In a continuous plant, the amount of material cannot surpass the limit of the asphalt plant, so the mixing time is adjusted depending on the type of mix and the amount of material.
“If the mixer is too empty, the aggregates are projected too far to the front, not mixing enough for sufficient homogeneity. When it is too full, movement from the bottom of the mixer up does not happen, also affecting homogeneity,” Mr. Zubaran says.
In a mixer, the aggregates should be thrown up from the bottom to contact with the paddles. They are then cushioned by the mixer structure and, by gravity, fall into the lower portion of the mixer to be thrown upwards again.
“This movement allows for an intense shock between the different sizes of aggregates with bitumen making the mix homogeneous,” Mr. Zubaran says.
Modern Ciber continuous plants with a pug mill mixer can adjust the mixing
time, which is controlled by plant automation, eliminating the need for mechanical intervention.
The company has been refining its mixing time control technology since 2017 to further improve asphalt adhesion.
“It is possible in both continuous and batch plants to adjust the mixing time to achieve better adhesiveness, even at maximum plant production,” Mr. Zubaran says.
The filling level for the pug mill mixer will be indirectly controlled by the continuous plant through the position of a gate placed between the mixer and the drag elevator.
“The gate will work automatically according to the filling level that is determined by the plant operator,” Mr. Zubaran says.
This image shows the mixer operating with a filling level of 60 per cent and different production rates: 75, 112 and 150 tonnes per hour.

In a test using an iNOVA 1500 plant by Ciber, Mr. Zubaran says the best mix had a 60 per cent filling level, after testing filling levels from 30 to 70 per cent. However, this will vary on a case by case basis.
Importantly, Mr. Zubaran says the best filling rate for each plant and mix type needs to be determined for optimum production.
“Once the ideal filling level is defined and maintained, if the production rate of the plant is reduced, the technology will increase the mixing time at the same proportion,” he says.
“In this case, the maximum production capacity in the plant was 150 tonnes per hour, a filling level of 60 per cent was found as the best mix performance,” Mr. Zubaran says.
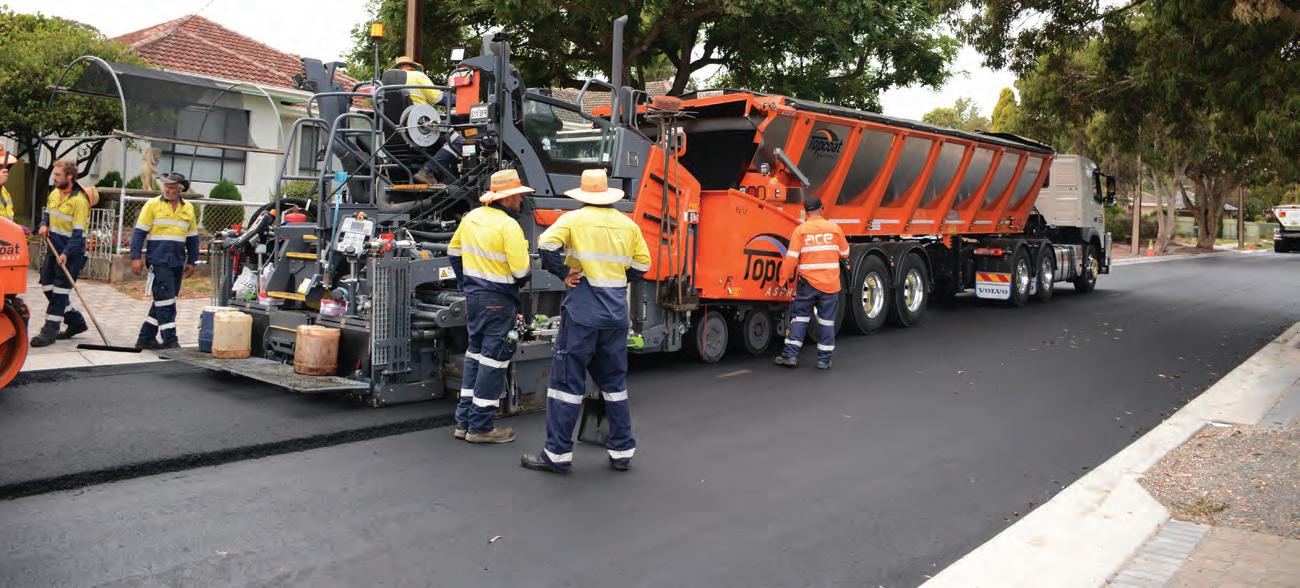
Furthermore, with increased filling levels, the standard mixing time will be increased and the production will decrease.
“These components and technologies, when applied to a mixer in continuous and batch plants, enhance the adhesiveness of the asphalt mix dependent on the way the characteristics of the materials react with each other,” Mr. Zubaran says.
Mr. Zubaran says customisation of mixing time is essential to the production of special mixes, ensuring they perform to a high standard in construction.
He says Ciber aims to achieve the result of quality mixing by the attainment of a highperformance asphalt mix as projected in a lab, where the environment is controlled and there is a much smaller production rate.