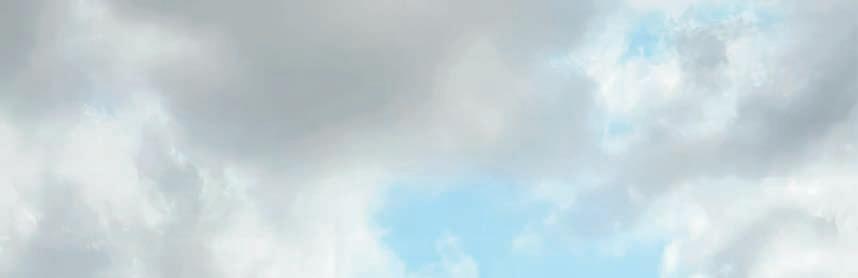
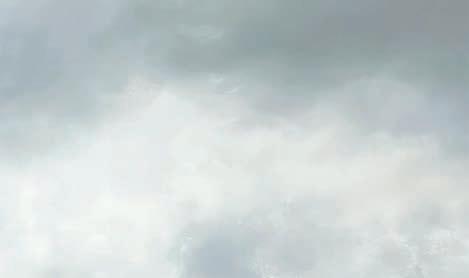
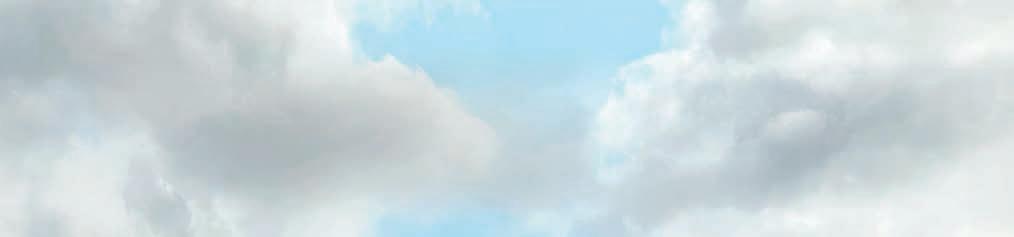
The story of Adept Plant Hire and its loyalty to John Deere graders, a two decade long partnership
HELP FOR ALL Fulton Hogan and the Black Dog Institute have partnered to address and improve mental health sector wide
THE FUTURE IS HERE
Take a peak into the future of infrastructure development technologies and how companies are benefiting right now
Deadlines don’t stop for delays. And with the revolutionary Premium Circle on a John Deere Motor Grader, neither will you. This fully sealed system is more powerful and accurate while being lower maintenance, which means less downtime and more productivity. No need to compensate for wear in the circle or stop to adjust for looseness. It’s also available on any John Deere Motor Grader you choose. The grading game has moved forward. Don’t get left behind.
COVER STORY
7 Adept for any project
Inside Adept Plant Hire’s operation and relationship with John Deere graders.
11 For the entire industry
Fulton Hogan and the Black Dog Institute are working to address and improve mental health across the sector.
14 Building in the smarts
What the future of technology, sustainability and project delivery could look like for the sector.
16 Ahead of the game Industry first technology provides a temporary traffic management system to centralise works.
19 The paradigm shift
Reveal Technologies research has shown a positive future for reality capture in road construction works.
22 Changing your community
eLu is helping to increase access to electric vehicle charging infrastructure for regional communities.
25 Revolutionising road repairs
New methods are surpassing traditional forms of road and other infrastructure repairs.
27 All part of the plan
Recent works have highlighted the effectiveness of project consultation and leadership from Plan B Comms.
29 No limits
On-going support and the technological capabilities of its six metre telescopic sprayer have elevated SRE.
31 Safety first, McLeod first TRT cranes form a key part of McLeod’s commitment to safety and quality.
34 Century of success
Astec looks back and celebrates its 100th handover of pavers to Fulton Hogan.
37 A concrete fact Eifers has become the exclusive dealer in Australia for evolutionary volumetric equipment.
40 Building on a legacy
Matthews Brothers Engineering is reaffirming its commitment to customer support and maintenance.
42 Racing into the future Komatsu has signed a new, multi-year deal with Williams Racing in Formula One.
44 Safer and cleaner
Quality Fabrication & Engineering’s Road Ant can provide greater safety and sustainability outcomes for users. Here’s how.
46 Rollin, rollin, rollin CEA’s expertise in manufacturing has led to the creation of a premier road roller.
48 Paving for stability Caterpillar equipment is being used to assist flood affected communities through repaired local transport infrastructure.
50 The long-awaited Contractor Capability Showcase returns in 2024, with information and details for some of the sectors leading providers.
Explore the latest in machinery technology, as well as road construction planning software in this edition of Roads & Infrastructure Magazine.
WORKPLACE INJURIES and fatalities are a sad part of the roads and civil construction industries. But advances in technology are helping change high-risk patterns and behaviours, as we find in this edition of Roads & Infrastructure Magazine
There are roughly 150 fatal accidents and 100,000 serious injuries in the Australian workplace each year. Heavy industries, including construction, logistics and warehousing, agriculture and forestry, manufacturing, and mining, disproportionally contribute to these statistics, with nearly 65 per cent of all fatalities [Safe Work Australia].
It’s not just the physical health of workers from across our sector that continues to be an issue. According to SafeWork NSW, Australian construction workers are six times more likely to die from suicide than an accident at work, with young construction workers more than two times more likely to take their own lives than other young Australian men (Mates in Construction).
Fulton Hogan, in partnership with the Black Dog Institute, is aiming to make a difference by delivering practical strategies and methods for those working in the sector. The Black Dog Institute’s approach to mental health centres around research and science, focusing on mass behavioural change for people of all ages. Both companies explain how and why partnerships such as this can help to make a real impact when it comes to the mental health crisis in construction.
In this month’s cover story, we shed light on the long-term relationship between Adept Plant Hire and John Deere. Both companies have gone from strength to strength thanks to this partnership, which was one of the founding relationships for the growth of John Deere’s grader division. We also look further into the origins of Adept Plant Hire, a great story that focuses on family, determination and expansion.
Technology once again is a big focus of this edition. Reveal, which specialises in the use and development of subsurface utility detections software and hardware, provides an insight into its progress in researching reality capture technology. This technology aims to increase the accuracy and efficiency of subsurface detections, while providing an ultra-realistic model for which project stakeholders and asset managers can use for construction works.
For motorsport fans, Komatsu shines light on its renewed partnership with the Williams F1 racing team, which looks to be the continuation of what could be a fortuitous partnership.
Look out for this and more, in this edition of Roads & Infrastructure Magazine Happy reading!
Tom O’Keane Roads & Infrastructure MagazineCOO
Christine Clancy christine.clancy@primecreative.com.au
PUBLISHER
Sarah Baker sarah.baker@primecreative.com.au
MANAGING EDITOR
Mike Wheeler mike.wheeler@primecreative.com.au
EDITOR
Tom O’Keane tom.okeane@primecreative.com.au
JOURNALIST
Chris Edwards chris.edwards@primecreative.com.au
DESIGN PRODUCTION MANAGER
Michelle Weston michelle.weston@primecreative.com.au
ART DIRECTOR
Blake Storey
DESIGN
Bea Barthelson
BUSINESS DEVELOPMENT MANAGER
Brad Marshall brad.marshall@primecreative.com.au
CLIENT SUCCESS MANAGER
Salma Kennedy salma.kennedy@primecreative.com.au
HEAD OFFICE
Prime Creative Pty Ltd
379 Docklands Drive, Docklands VIC 3008 Australia p: +61 3 9690 8766 enquiries@primecreative.com.au www.roadsonline.com.au
SUBSCRIPTIONS
+61 3 9690 8766 subscriptions@primecreative.com.au
Roads & Infrastructure Australia is available by subscription from the publisher. The rights of refusal are reserved by the publisher.
ARTICLES
All articles submitted for publication become the property of the publisher. The Editor reserves the right to adjust any article to conform with the magazine format.
COPYRIGHT
Roads & Infrastructure Australia is owned and published by Prime Creative Media. All material in Roads & Infrastructure Australia is copyright and no part may be reproduced or copied in any form or by any means (graphic, electronic or mechanical including information and retrieval systems) without the written permission of the publisher. The Editor welcomes contributions but reserves the right to accept or reject any material. While every effort has been made to ensure the accuracy of information, Prime Creative Media will not accept responsibility for errors or omissions or for any consequences arising from reliance on information published. The opinions expressed in Roads & Infrastructure Australia are not necessarily the opinions of, or endorsed by the publisher unless otherwise stated.
ADEPT PLANT HIRE HAS BEEN USING JOHN DEERE GRADERS SINCE THE COMPANY WAS FOUNDED. SINCE THEN, THE COMPANY’S FLEET, CAPABILITIES AND PARTNERSHIP WITH JOHN DEERE HAS ONLY GROWN STRONGER.
In 2006/07, former Adept Plant Hire Director and company owner Kevin Jones sought to establish a lasting relationship with a quality provider of grading equipment. This led him to initiate discussions with John Deere.
“At the time, a lot of Australian operators were using another company’s machinery,” Jones says. “When I heard about the John Deere machines, I went out to see them and they actually had a stronger machine, it had more power. They also had the 9-litre Power tech engine, not just the 6.8 litre. That was a big factor, because the John Deere had a damn good engine. It was also a fair bit cheaper, so it was a bit of a no-brainer.
“We knew that going with John Deere was a bit of a risk for us at the time, but we knew they had the trust and quality operators to back that up. Our operators were soon after telling us that they were able to do jobs the same, if not better. They ended up really liking them.”
Jones says that the professional relationship between John Deere and Adept Plant Hire and the support from local John Deere
dealer RDO Equipment was significant.
Jones says another contributing factor in his choice to go with John Deere was the manufacturers decision to continue to offer the steering wheel option, alongside the option of joystick or fingertip control design, giving operators the choice of how they want to work.
John Deere graders have formed most of Adept Plant Hire’s machinery fleet ever since, with 16 ‘Deeres’ in the current fleet of 18. In all, they’ve had close to 50 Deere motor graders.
Equipped with Trimble UTS systems, Adept Plant Hire’s fleet of graders is regularly maintained and updated by RDO Equipment, to ensure that the company can deliver optimal performance.
This has proven key in the company’s ongoing successes working on the Rockhampton Ring Road and the Coomera Connector, two of the largest infrastructure projects in Queensland.
Pete Comerford, along with his wife Teagan, are now both Co-Directors of the company, having taken over from previous
owner and heralded founder Kevin Jones. A long-time operator at the company, Comerford eventually was elevated to the role of Operations Manager three years ago. After being in this role for only a year, brief discussions between Jones and Comerford led to an enticing opportunity.
“When I became Operations Manager, I was basically running most of the business for Kevin. As time went on, we were growing bigger and bigger, I wanted to re-establish a few things post-COVID to build the company back up,” Comerford says.
“About two years ago, Kevin and I started having conversations about possibly buying into the business and what that could look like. We spent about 18 months discussing that and in July last year we finally locked things into place.”
For Jones, it was a big adjustment. But he says there’s no one he’d rather have running the company.
“[Peter] started working for me when he was young and you could see his potential as a leader. I knew he was the type of person going forward who would be trusted with
management, he just needed to learn some skills first,” Jones says.
“He’s taken the bull by the horns. He knows a lot of people in the industry and the biggest thing for me is that he’s got a real passion for the company. It was a bit of a no-brainer, Teagan could see taking up the office managers role. They both loved the idea. We’ve given it a shot and it’s worked. I’m happy to let him take the reins.
“A big thing for me is trust. I trust him and Teagan and they trust me. I don’t think I would’ve been keen to sell or break off the company to someone that’s not as passionate and trusting as Peter is.”
Comerford handles everything from an operations perspective, while Teagan covers the logistics and financial aspects. He says it’s the company’s attention to detail, from its operators to its equipment, that’s helped to maintain its reputation in Queensland.
“I’ve long been impressed and aware of what Kevin had established,” he says. “It’s been around for so long and stood the test of time through the Global Financial Crisis, through the wet weather between 2012 and 2020, it’s withstood a lot of hard times.”
Teagan says being involved with Adept for such a long time made both of them really love the company and the opportunity and lifestyle it provided, making running the company an exciting prospect.
“It feels quite prestigious. The company has developed a good reputation and very loyal employees. There’s such a good ethos and culture within the company, you really want to be a part of it,” she says.
Combining top operators with top machinery is a philosophy that’s been constant throughout Adept Plant Hire’s history. To support this notion, the company uses what Comerford refers to as “industryleading equipment”.
“They’re a great machine. In my opinion, they’re a superior machine. I really do think that they’re the best grader in the industry. You might call me shallow, but I also love the way they look. They’ve kept that classy, traditional look,” Comerford says.
Adept Plant Hire’s fleet of 16 late model John Deere graders comprises the 670GP, the 672GP and the 770GP. The G-series graders
down the East Coast and on some of the biggest major projects in the country. Some of the graders are fitted with the industry exclusive John Deere Premium Circle option.
Being in the final trim business, accuracy is key. With Premium Circle, Adept no longer has to compensate for wear in the circle or stop the machine to adjust for looseness of the circle, not to mention the saving on circle maintenance.
The G-series also supports machinery pre-sets, saving operators time in terms of adjusting functions and machine positions for specific jobs, all with the touch of a button. These features are easily accessible from an operation and maintenance perspective.
“For our operators, the comfort and operation is really great. They’ve also provided great vision. These two things are really important to us, as our guys have to sit in the cabin for around 10 (plus) hours most days,” Comerford says.
“In terms of running them, we’ve rarely had any issues. We’re focused on maintaining them well because we like to have them at a high standard. They’re just a great all-round grader. I’ve had some of the crew who were die-hard for other brands. Once I’ve put them in these machines, they’re more than happy to stay with the John Deere.”
Another big plus is the relationship and partnership that Comerford and Adept Plant Hire have established with their local John Deere dealer, RDO Equipment.
“They’re really good to us. We buy as many genuine parts as we can, you can ring up
Adept Plant Hire’s John Deere graders have worked on projects such as the Coomera Connector.“THEY’RE JUST A GREAT ALL-ROUND GRADER. I’VE HAD SOME OF THE CREW WHO WERE DIE-HARD FOR OTHER BRANDS. ONCE I’VE PUT THEM IN THESE MACHINES, THEY’RE MORE THAN HAPPY TO STAY WITH THE JOHN DEERE.”
and it’s never a problem with those guys,” Comerford says.
Teagan says John Deere and RDO have also been efficient and easy to deal with when it comes to the financial side.
“It’s good to keep building and maintaining that relationship with RDO. We have recently utilised the great John Deere finance deals, and the transactions have gone incredibly smoothly, and we appreciate what they are able to offer us,” she says.
“Everything that we do with RDO and John Deere seems simple and straightforward, they are receptive to our needs and always have supportive options to help us out. They’re professional and easy to deal with, which I really appreciate.”
Having only the best machinery won’t equate to the best results, Comerford says. A key reason why the team takes prospective employees to lunch first is to evaluate whether or not they would be a good fit for the company’s culture.
“A main focus for us is having operators that are of a very high skill level, but if they don’t have good people skills and don’t get along with people, eventually they’ll probably get replaced on jobs,” he says. “Our crew is very skilled and we try to attract
good people because of the culture that we’ve built over the last couple of years.
“It’s the people side of things first, along with the machinery, that has given us the foundation to grow into the company that we are today.”
Adept Plant Hire’s mixture of reliability, its attitude and its people make the company easy to deal with. When combined with John Deere graders, Comerford thinks Adept Plant Hire’s package is hard to knock back for projects of all sizes.
“The way that we communicate on our projects and how easy we are to deal with means that there’s never a problem with us. We try and help the project as much as we can. I believe that having that positive attitude has allowed us to win many of the contracts that we have now,” he says.
“Certainly, the operators are important for these projects, but I think Adept Plant Hire as a whole, and being the company that we are, is on the rise and growing, along with our great reputation that continues to grow is a real factor.
“There’s very few that you talk to in the major project industry in Queensland that don’t know Adept Plant Hire, don’t know our John Deere graders, and don’t know some of our operators. That’s in part due to Kevin (Jones) and the reputation
that he built as well.”
The future of Adept Plant Hire looks bright, so does the company’s ever-growing relationship with John Deere and RDO Equipment. Comerford says the company’s potential in the next five to ten years is what really excites him.
“We’ve got different ideas that could potentially change the business, but not its fundamentals or foundation. We want to keep that intact. Adept’s been set up really well, it’s got great people, it’s got a great history. We never want to change that,” he says.
“It feels like a real family company, especially now that we’ve got three kids running around the office. A lot of our operators have kids, that’s part of our positive culture.”
Teagan says she looks forward to growing upon the impact that she and Peter have already made.
“We’re always looking to improve and I like that about our operators as well. They’re constantly looking to get better,” she says.
“We’re having such a good time creating that culture and maintaining it. We love working with each other and with our team and we want Adept to be a destination company where people want to come to work because they’re having a good time and feel appreciated. I think our employees could testify to that as well.”
Want to know more about Adept Plant Hire? Visit their website –adeptplanthire.com.au
Introducing the first and only skid steer with a telescopic boom the JCB Teleskid; a truly unique, versatile skid steer with endless possibilities. Now you can lift higher, reach further, dig deeper.
This revolutionary product is designed to suit all types of job sites meeting the need of multiple machines wrapped nicely into one. Combining the strength and safety of our single side boom with side door entry and extendable boom JCB has increased the versatility of the SSL-CTL world.
To find out more contact your local JCB CEA dealer today.
Ph: 1300 522 232
www.jcbcea.com.au
According to the Black Dog Institute, one in five Australians will experience symptoms of mental illness annually, equating to around five million people.
Unfortunately, around 60 per cent of these people won’t seek help.
Mental health has long been one of the infrastructure and construction sector’s glaring issues.
Fulton Hogan, like many in the sector, is actively working to improve awareness and education, to normalise discussion and treatment for mental illness.
The company continues to be successful in this area, being recognised at an industry level, as the winner of the 2023 Victorian Workplace LiFE (Living is For Everyone) Award, distributed by Suicide Prevention Australia. These awards celebrate the commitment and determination of companies working towards the reduction of suicide within the community. Fulton Hogan has also been recognised by the Mental Health First Aid Workplace Recognition Program as a “Skilled Workplace”.
Sarah Marshall - Executive General Manager - People, Safety and Sustainability, has been one of the key leaders and trailblazers in establishing a structure around supporting the mental health of employees of all levels across the entire business.
“Mental illness in our industry has long been a silent and problematic challenge that has had a profound impact on individuals, their families, friends and colleagues,” she says. “I have been working in the mental health space in the construction industry since 2008 and whilst lots of work has been done in the industry over that time and construction workers are generally more comfortable having conversations, the dial hasn’t really shifted.”
Marshall says it takes a significant amount of energy and effort to make meaningful change, especially when it comes to minimising critical risks such as mental health.
“In 2019, we established the Fulton Hogan Mental Health Strategy. We all agreed that this was not going to be a quick fix, it was going to take concerted effort over a long period of time to get the cultural change that we needed to see,” she says.
This led to the development of Fulton
Hogan’s five-year comprehensive mental health strategy, which focused on the organisational readiness, awareness and education, active intervention and support, recovery and maintenance, prevention and early intervention.
The implementation of the strategy has been successful, including 80 per cent of its leaders having undertaken mental health leadership training. As a result, Fulton Hogan now has over 500 trained mental health first aiders in its business nationally including a percentage of their CEOs and General Managers.
Zach Humphrey – National Health and Safety Manager, says mental health plans for the company’s projects and sites have also been developed.
“Fulton Hogan comes from a grassroots history that values its people above all else. That encompasses both physical and nonphysical illnesses and injuries. That starts from our senior leaders and at the executive leadership down, giving practical tools to members of our team and being able to refer them to really good resources,” he says.
Fulton Hogan has committed significant resources to maintain its current momentum in this space.
“Health and wellbeing, including mental health, is one of our six critical risks in our recently launched health and safety strategy,” Humphrey says. “It is the basis for one of our critical risk groups, each of which are chaired by a member of our Executive who
can endorse identifying, conceptualising and funding further improvement projects within the business, focused on improved mental health outcomes for our workforce.”
“That will continue to identify really great innovations, initiatives and other opportunities internally.”
To further expand its access to resources and information around mental health – and in line with its five-year mental health strategy – Fulton Hogan reached out to the Black Dog Institute in 2020 to begin discussions around a potential partnership.
Both organisations see eye to eye when it comes to mental health, identifying that fundamental change is required across the sector.
Tasman Cassim is the Head of Partnerships at the Black Dog Institute. As he explains, the enterprise aims to make an impact and influence change for the better on a massive scale.
“We’re looking to influence significant changes to the population’s mental health right across Australia,” Cassim says. “We’re doing that through finding new and better solutions and putting them in the hands of the right people at the right time. We’re one of the only organisations in Australia and the world that conducts research in this space and translates that research into action.”
“We focus on tangible things that are going to help people with their mental health and what that means is that we spend a lot of time
understanding what’s happening with two of the major mental health disorders in Australia, which are depression and anxiety.”
“We design and understand the best research that’s going to help Australians at a time that works best for them. All of our work is evidence based and goes through very rigorous scientific trials. We’re fully rooted in evidence. The Black Dog Institute is also the only organisation and researcher in Australia that looks at mental health right across the lifespan. We cover research from young people, to older people and everyone in between.”
He adds that there are many “fantastic organisations” that are helping to contribute to a society that can better discuss and treat mental health, but the Black Dog Institutes’ approach differs slightly.
“A lot of other organisations mainly focus on the individual, providing what I’d call crisis care 24/7, which is a fantastic service. We look from a population level to influence a large majority of Australians to reduce collectively any mental health illnesses that they’re going through,” Cassim says.
The construction industry represents one of a few sectors that exhibit disproportionally higher rates of mental illness, along with the tech, media and legal industries.
Cassim says that factors such as the intensiveness, isolation, pressure and exhaustion of construction work can often play a role. The sector being male dominated also plays a role.
Dr Andrew Arena is a Postdoctoral Research Fellow in the Workplace Mental Health Research Team at the Black Dog Institute, Australia’s largest and most influential research team working in the area of workplace mental health. Dr Arena recently led a large survey of construction and utilities workers across Australia, which found that one in four workers had high symptoms of depression and/or anxiety.
The survey also found that 25 per cent of workers who needed mental health support never accessed it.
“Rates of help-seeking tend to be low in male-dominated industries like construction, where stigma around mental health issues remains quite high,” says Dr Arena.
Marshall says the Black Dog Institute’s research focused approach was a big tick for Fulton Hogan, who were looking for a partner that could influence systematic change.
“We do see lots of really great work going on, but we needed to look for something that was different to what we’ve seen before.
Conversations and talks can be moving and we can resonate with what we’re being told, but for whatever reason, it wasn’t moving us from A to B,” she says.
Marshall adds that employee participation and interest has been really encouraging as both organisations work to further grow their existing partnership.
“The whole partnership is about doing something that was industry changing. It’s enticing from an employee value proposition,” she says. “Our employees really engage and understand why we partner with the Black Dog Institute.
“They’re absolutely engaged during fundraising activities and are really supportive and want to have that conversation and make a difference. That’s why this partnership came about.”
Humphrey says the benefits and impact of the partnership have been clear to see.
“On both sides of the partnership, there’s a real hunger to affect change across the entire industry. We understand that this is an industry-wide problem, not just something that affects our organisation,” he says.
“Irrespective of whether it’s the Black Dog Institute or Fulton Hogan, we have a fundamental obligation to look out for people in our industry. We have a long way to go as an industry, but we are getting better. And as leaders in the industry, we need to be doing better.”
Cassim says the Black Dog Institute has on-going partnerships with companies across a variety of industries. Each play an important role in increasing the organisation’s researching capacity and capability.
“One of the reasons why these types of partnerships are really important is that we’re able to get direct access to industries where typically workers don’t report on their mental health or might not be able to identify the signs. It’s a brilliant way to reach a new audience who might not engage in discussions around mental health,” Cassim says.
“The Fulton Hogan partnership is powerful because we can access a part of their cultural ecosystem. It’s also really important because Fulton Hogan and some of our other partners fund the work that we do. That’s incredibly important to our success and longterm viability.”
One of the shining lights of Fulton Hogan and the Black Dog Institute’s partnership has been the agreement to develop an online mental health solution for construction workers that provides practical ways for workers to improve their mental health.
As Humphrey explains.
“Through the partnership we recognised that there was an absence of a coherent app that speaks to construction workers about mental health and provides impactful advice on their lifestyle, working life and personal life. Based on previous evidence, we anticipate that the app or other solution will provide practical guidance on opportunities to improve your mental health, whether that’s through seeking help, lifestyle changes and more,” he says.
“When we looked at health and wellness apps and initiatives in the past, we realised that they didn’t account for the nature of our workforce and sector, as well as the prevalence of mental health issues in the industry.”
The solution will build on findings from the existing ‘Headgear’ app, which includes a 30day mental fitness challenge.
Cassim says the Headgear trial showed pleasing results, with users of the app reducing their depressive symptoms over the course of the trial, compared to people who weren’t using the app.
“It’s one of the first apps in the world that has shown an evidence-based reduction in depression. We both wanted to have real action on the back of this partnership and the this new initiative forms a strong part of that focus,” he says.
The new solution will be developed in the coming months, and is intended to be rolled out across the sector.
“This is a really exciting development,” Cassim says. “Our aim is to make a positive difference for construction workers, especially on site. That’s what we’ve been working towards for the last three years and that’s really our north star in terms of this partnership.”
Marshall says the potential impact on individual life is the fundamental reason for the partnership.
“Sometimes as businesses and leaders we can have big, audacious goals, that take a long time to achieve, but for me when it comes to mental health, if we can positively impact one employee, then it makes all of the hard work worth it,” she says.
“That’s the main thing that drives me, is the possibility of saving someone’s life. At the end of the day, it’s all about the people in our company and our industry. That’s why we do it.”
If you or someone you know is experiencing difficulty with mental health, reach out to Lifeline on 13 11 14. For more information on the Black Dog Institute, visit: blackdoginstitute. org.au
Komatsu’s proven intelligent Machine Control (iMC) concept has now penetrated markets worldwide. Thousands of operators and owners enjoy the safety and precision of Komatsu’s exclusive technology, factory fitted on both dozers and excavators, and the outstanding improvement in productivity it brings to the jobsite. Customer productivity is the driving principle behind Komatsu intelligent Machine Control.
Call us today on
Sales: 1300 074 249 | Support: 1300 445 978 komatsu.com.au
ROADS & INFRASTRUCTURE MAGAZINE HEARS FROM BENTLEY SYSTEMS’ ROB MALKIN, SENIOR REGIONAL DIRECTOR, ANZ, AND STEWART SMITH, SOLUTION ARCHITECT, ON WHAT THE FUTURE OF TECHNOLOGY, SUSTAINABILITY AND PROJECT DELIVERY COULD LOOK LIKE FOR THE SECTOR.
Bentley Systems’ Rob Malkin, Senior Regional Director, ANZ, and Stewart Smith, Solution Architect, are both passionate and knowledgeable when it comes to digital transformation and tailoring solutions for infrastructure projects.
Smith and Malkin have 55 years’ worth of accumulated industry experience between them. As a result, they both view change as a natural progression, rather than something that should be feared or avoided.
According to them, it’s Bentley Systems itself that’s contributing to change by further pushing the boundaries globally when it comes to the development of infrastructure engineering software.
This includes asset performance, structural analysis, building and bridge design, geotechnical engineering, reality and spatial modelling, and more.
Due to its reputation and stature in the sector, Bentley Systems is regarded as a caretaker of infrastructure intelligence, described as an essential aspect that must be incorporated into future infrastructure development. But what is infrastructure intelligence? Smith explains.
“For me, it’s about leveraging the capabilities and systems that we have now to improve project delivery and asset performance. It’s about how you can bring all those ecosystems together to analyse and use data during the design, construction and operation and maintenance phases,” Smith says.
“Infrastructure intelligence can form an important part of a company’s quality assurance processes by being able to deliver quality that’s driven by data. It’s a big plus, being able to analyse and make good decisions at important stages of design and
construction. It can help to identify things that could potentially happen, such as reducing risks and making sure you can satisfy project costs and timelines.”
Malkin says leveraging this data, right from the early engineering concept drawings through to operations management, is now an essential component of asset maintenance, performance and preservation.
“The asset is going to live for 50, 100 or even 125 years, so more of the cost is going to be associated with its operation and not the time in design. So having inputs around vibration, people movement, capacity and more is important,” Malkin says.
“You take the Auckland Airport, for example, where they’ve been using Bentley solutions. Now they’ve got a roadmap of what the airport, parking, hotel and everything might look in 45 years based on the last 20 years of
population growth, and they can forecast the increase in demand for the airport. They can go and acquire land 20, 30 or 40 years ahead of time as their design and plans to expand the site continue to evolve. It’s bringing together rich intelligence and visualisation by using that imperative data.”
Evaluating such data enables users to take the past and use previous data to be better prepared for the future. Such technologies can also contribute to increasing the overall safety of a worksite by replacing staff in potential high-risk areas with drones, for example, to carry out maintenance and condition reports.
Greater sustainability outcomes are another benefit of incorporating infrastructure intelligence.
“Resilient infrastructure is at the forefront and is a big focus for us when developing technology. It means people can make the right decisions at the right time to provide the best outcome for a project. Resilient infrastructure also plays a key role in increasing the sustainability of urbanisation around the world,” Malkin says.
“Recently another storm hit Victoria with flooding in the north. We have an open solution that can incorporate other software and other analysis packages to make the best-informed intelligent infrastructure that helps people plan for the unplanned. Where other vendors might lock their systems, we’re open to absorbing that information and taking that data.”
Just one example of this technology is Bentley’s iTwin Platform. This purposemade technology enables users to create, visualise and analyse digital twins of infrastructure assets.
these technologies can best be optimised.
“These STEM programs are paramount for us because as more mature and experienced people retire, that knowledge transfer can be lost. The younger population may not have the same experience with or adaptability to these applications. With remote working, people are no longer there physically to help. Back in the day, you’d sit around an elder engineer; now, you sit around the laptop,” Malkin says.
“Technology is evolving, especially at Bentley. We’re starting to bring these developments to the market on big projects, allowing project teams to work quicker, easier and less segregated. We’re allowing all of that in an infrastructure cloud environment.”
“When I first started, I was working off a drafting board. It used to take me several days to produce a single drawing. Now, people can do that in a matter of hours.”
Australia is at the forefront when it comes to the adoption and development of the technologies, says Malkin.
These digital twins can be constantly updated and synchronised to ensure all project stakeholders are on the same page. Streamlining design changes and client communication boosts not only project timelines, but also a company’s bottom line.
Engineering, geospatial and operational data can all be centralised, while also incorporating real-world conditions to predict future conditions for inspections, reporting, and insights. This is achieved using AI and ML (artificial intelligence and machine learning, respectively).
Malkin says this is just one example of Bentley’s innovative digital applications, and one of many that utilise the latest AI technology.
Bentley is also going beyond just promoting its
“For us, educating the next generation of students means the world is going to be better and more adaptable to future change, helping them make more informed decisions.”
Smith says aspects such as project delivery, infrastructure intelligence and sustainability will suffer if this knowledge transfer is not completed.
“The younger generation are the future. Speaking as someone who has been in the industry for some time, we have a responsibility to mentor them and give them as much knowledge as we’ve learned in our lifetimes,” he says.
Despite these challenges, both Smith and Malkin have positive outlooks for the future, saying there’s plenty of opportunities and solutions in development to counter skills shortages, as well as financial and resource constraints.
“What really excites me is the digital transformation that’s underway,” Smith says.
“Australia adopts technology much faster than most. I’d even go as far as to say that the country is just as innovative, if not more than the United States, which is still very legacy orientated. We use technology better probably because of the tyranny of distance. We use it to really elevate our capabilities way beyond what some people might think,” he says.
Smith agrees.
“We use 3D modelling, we use digital twins, we started using the cloud way before most other nations did,” he says. “I’ve travelled around the world, and Australia is known as having the innovators that are willing to adopt new technologies and see where it leads.”
Malkin adds that its companies, like Bentley, that are helping to forge this path ahead.
“Within Bentley, we’ve got a whole ecosystem of solutions,” he says. “We’re listening to the market and looking at international trends, not only now, but also into the future. We’re bringing that to the forefront.”
“I envision Bentley as an organisation that caters and enhances people’s day-today decision making and quality of life for the better.”
FOR THE FIRST TIME, THE INFRASTRUCTURE SECTOR NOW HAS A TEMPORARY TRAFFIC MANAGEMENT SYSTEM, THAT CENTRALISES ALL COMMUNICATIONS AND PROVIDES REAL-TIME PROGRESS VISIBILITY AND TRANSPARENCY FOR CLIENTS, GOVERNMENT AGENCIES, PRINCIPAL CONTRACTORS AND SUBCONTRACTORS.
As for the engineering industry, engineers always believed that there are better ways of doing things and understood that the current utilised tools did not centralise the communications, nor did they provide adequate transparency, direct visibility and consistency.
Previously as a Traffic Engineer working in mega projects, Mustafa Smeida saw the need in the market for an advanced tool to simplify doing traffic management
administrative works for all relevant teams within the project.
“Although there was a previous system attempt that only served a specific project scope, there wasn’t a single software available to manage all temporary traffic management projects’ scopes and requirements. Engineers and other teams were still relying on spreadsheets, emails and phone calls to communicate, which came at a big price,” Smeida says.
Using his personal experience as a key driver, Smeida set about finding the solution to close the gap and alleviate the need for multiple programs. This led to the formation of Integrated Project Management Systems (IPMSystems) in 2019, which initiated and introduced its flagship development, a software for Temporary Traffic Management.
TOOFA is a bespoke software that is developed by traffic team experts who worked in the temporary traffic
management industry. TOOFA is the first in the market that aims to simplify and consolidate the construction/ utilities temporary traffic management booking needs, from planning to resource scheduling and management, all the way to implementation and completion.
On a project level, TOOFA is the centralised platform that provides quality assurance, document control, risk optimisation for scheduling, cost management and builds historical data for easy audits from anywhere at any time.
But growing the business and its platform did present multiple challenges. One of the biggest being the need to develop a system that could cater for one of Australia’s most dynamic industries.
“Our intention was to ensure that TOOFA is compatible and adaptable for all projects, regardless of scope and requirements. Something that current
utilised tools cannot offer,” Smeida says.
“We believe that such a platform would need to be flexible to satisfy constantly moving goal posts around specifications, infrastructure delivery and the infrastructure pipeline. One of the main reasons why IPMSystems is heavily invested in constant adaption and development.
“We were fortunate to have Sydney Gateway mega project signup to use TOOFA as our first project. TOOFA’s value has been apparent, with the platform still being used as works progress on the project.”
Lee Vossen Traffic Manager – Seymour Whyte Construction says working with the TOOFA software has increased quality and productivity in the traffic booking workflow processes.
“The ability to understand your historical resourcing, costing and future
data within a few clicks is invaluable. The simplicity of having the latest TGS’s and occupancy licences automatically linked to the TGS takes the error out of having incorrect information in the field on a shift-by-shift basis and adds comfort in the quality and auditing processes,” Vossen says.
“Further, the additional benefit of capturing incidents on the server allows for a complete project traffic management platform in a single location, all to hand.”
TOOFA has also been utilised by a number of other projects in New South Wales and Victoria. These projects include some of Australia’s and the world’s largest tier one contractors and subcontractors.
“IPMSystems’ culture of continuous improvement has translated to its platform, with on-going updates being made to TOOFA software with feedback from clients and industry standards. This extends to ease of use for the users,” Smeida says.
Smeida says taking the decision to invest a substantial amount of money and time was one of the hardest steps ever taken but the result was worth it.
He says he’s excited for what the future holds.
IPMSystems encourages companies in the infrastructure sector to continue investing in system innovations for the temporary traffic management activities.
Investing in TOOFA software on a project level, will increase efficiency, productivity and cost management.
Whilst, investing on a company level will assist with better management and allocation for the traffic team resources, leading to greater productivity and cost saving.
Tim Rastall, Chief Technical Officer of Reveal, is passionate when it comes to the development of new technology. With experience in design, consultation, gaming and development, he leads Reveal’s efforts in identifying, testing and using nascent technologies to make the underground more knowable.
Now he’s deploying his experience and practical skills on the world of reality capture.
For the infrastructure and construction sectors, reality capture is a radical new approach to recording highly accurate information on the location and conditions of assets that is typically too costly or timeconsuming to obtain.
Rastall says, “Historically, the location of infrastructure was recorded on paper plans by contractors just before the ground was closed, or simply copied over from the engineering plans with no verification at all. Most of the utility plans we encounter are outdated, incomplete or inaccurate in some form.”
“For us, photogrammetry is an enabling technology that solves what we as a business are aiming to solve; that is people being aware of what’s underground.
“Reveal’s focus isn’t on building photogrammetric algorithms, but it’s about leveraging that technology while ensuring that the data capture process is easy and can be made accessible and intuitive to everyone who needs it.”
From its headquarters in New Zealand, Reveal offers a platform for combining and visualising subsurface infrastructure data from sites or projects worldwide. The Reveal platform combines technology, data and field services to help build up the most accurate, comprehensive picture of the underground utilities and risks in a given area.
Images: Reveal.
The company’s technology has already been deployed on infrastructure projects throughout New Zealand and has been acknowledged as a key contributor to productivity gains and cost savings on major infrastructure developments.
“One of the biggest reasons why we’re doing this is that every year, dozens of people die in utility strikes (an incident where a tool or worker damages an underground utility) and thousands more are injured. If we could record information around the position of every asset that has ever been exposed to the naked eye, within 10 to 15 years no more shovels will need to go through another main in the wrong spot, ever again.”
Rastall is leading Reveal’s research into reality capture – the practice of using image sensors to record the true reality of a physical environment using the principles and physics of light.
One familiar technology, LiDAR, uses a rotating laser to scan a surrounding area and determining distances by measuring the time required for the light to reflect back from an object. This is either done using as static
Photogrammetry, on the other hand, builds up a realistic, three-dimensional model of an area using still photos captured with inexpensive digital cameras.
“Whenever a technology comes around that’s transcendent and transformative for the good of an industry, where it can result in making things more efficient and can help people, that always gets me excited,” Rastall says.
Reveal has already conducted experiments with reality capture, using photogrammetry and LiDAR separately, and in combination, to rapidly capture as-built info from exposed utilities, chamber interiors and surface models of the road corridor. These experiments have led to the use of both technologies in dayto-day utility surveys as well as Reveal now offering services to verify, refine and package the resultant data collected by its customers.
“What we do as a business is not exclusively reliant on photogrammetry or reality capture, but it’s an increasingly big part of our goal
When looking further into the realm of reality capture, the Reveal team realised that what previously could only be achieved with high-quality cameras and desktop software, could now be done with the convenience of one’s smartphone.
“It’s rare that you get the opportunity to collect visual information about the subsurface, as assets spend the majority of their lifespan buried under metres of dirt and concrete. Of course, visual evidence is the gold standard that can remove most of the ambiguity around the location and condition of assets. But no one is going to wait to fill in a road, that might have a lane closed, so we can arrive with survey gear, unless it’s a project deliverable,” Rastall says. “But if the team that is doing the work on site can pull out their phone and spend five minutes scanning the exposed assets, we see that there’s no reason that information can’t be captured.
“The utility locating industry has developed a suite of tools, standards, and practices that can be used to piece together a good estimation of where buried assets are, but there are inherent limitations to these non-invasive locating practices. However, we can eliminate any remaining ambiguity when an asset is exposed by excavation. The opportunity that we saw from smartphonebased photogrammetry is that the value of information about exposed assets in the context of the utility locating industry is enormous.”
Reveal currently uses an application called Pix4D, a combination of Pix4D Catch (phone app) and a cloud-based application called Pix4D Cloud. With a small amount of training and additional equipment, the Reveal team
can quickly record high-quality data for both exposed assets and the interior of subsurface structures, such as chambers.
Rastall admits that there are still some associated challenges. One is accurate georeferencing (putting the scan in the right place on a map), as a smartphone’s GPS can’t provide sufficient accuracy for this purpose and an incorrectly placed scan diminishes its usefulness, particularly when it is otherwise the best source of information available about the assets that were scanned.
Based upon the trends he’s been observing, Rastall believes the majority of georeferencing challenges will be solved in the next five years.
“We want things like reliable georeferencing to be as automated as possible and there’s a few emerging technologies that we’re watching that might be able to solve that. One is a Visual Positioning Systems, that uses real time imagery from the surroundings to localise the smartphone. Advances in artificial intelligence will start to have an impact as well,” he says.
Environmental conditions can also play a part; if a surface is wet, reflective or dark, it may not be suitable for photogrammetry, but AI is likely to help minimise the effects of these conditions.
“The quality of the image that you’re collecting directly correlates to the quality of the scan,” Rastall says. “But it looks likely that AI will eventually provide the means to detect and repair these kinds of issues and that’s already happening in fact.
“In the next few years, I expect that there’ll be some real shifts in the uptake of this technology. Currently, whenever we do a photogrammetric scan, we include a ruler to confirm that it’s scaled appropriately once processed and to prove that the scan is dimensionally accurate. It’s remarkably precise for the fact that it’s compiling a bunch of
photos and building a three-dimensional model from them. It’s almost magical in terms of its ability to do that.”
This high-fidelity information can then be used almost immediately in projects by importing the models into design software packages so engineers can create more efficient and higher quality concept and design drawings.
Further improvements to reality capture technology will also be spurred by more people using similar platforms. Rastall uses the development of the Pix4D mobile app as an example.
“When it’s in your pocket and can provide real time feedback to ensure your efforts result in a good scan such as, whether you are moving the camera too fast or too slow, as well as visual feedback on what has and what hasn’t been captured, that’s going to drive adoption and as a result, the rate of advancement will only accelerate,” he says.
“With some of our younger team members, we’re able to give them a smartphone, give them 10 minutes of training and then they’re off doing it. Very quickly, people are going to recognise the value of this technology in a real-world setting. There’s going to be continuous improvements in terms of usability and scalability. It’s a no-brainer.”
“The costliest element of real-world data capture for projects is most often the human component, either in time to collect information or time to process it. The ideal future would be the creation of a digital model that’s indistinguishable from the real thing, that gets you to a point where you’ve collected enough information to never need to go back again.”
“To be able to collect all the data you need at once, then to have that perfect replica of the original, would be enormously valuable to us. It’d be gold.”
Where
ELU’S COMMITMENT TO COMMUNITY IS EVIDENT WHEN ONE LOOKS CLOSER INTO ITS DEVELOPMENT OF NEXT GENERATION ELECTRIC CHARGING INFRASTRUCTURE DESIGNED TO ADD VALUE TO LOCAL COMMUNITIES.
As of the end of June last year, 46,624 electric vehicles (EVs) had been sold across the country. This is almost three times higher than the same period in 2022, representing an increase in uptake of 269 per cent (Electric Vehicle Council). The increasing popularity of electric vehicles has placed a strain on Australia’s electric vehicle charging infrastructure, particularly in rural areas, where the development of said infrastructure is still in its infancy.
Electric charging infrastructure innovator, designer and manufacturer eLu is hoping to shape the market for the better. A subsidiary of Australian company Lumen Energy Australia, eLu focuses on the delivery of electric charging infrastructure
at a community level, providing flexibility and minimal impacts when compared to other options.
Doug Fraser, Director of Queensland –eLu, says the company’s vision of providing electric charging infrastructure is focused on convenient and user-friendly solutions.
“Our focus is about community and the EV (electric vehicle) charging experience that we provide. What we do is quite different,” Fraser says. “We’ve recently launched our Australian flagship electric vehicle charging station on the Gold Coast at the Titans High Performance Centre at Parkwood Village. What we have there is an ultra-fast DC charger, or what we call a ‘supercharger’.
“The idea is that people can come in, have a coffee or a meal at The Club, or go to your
medical appointment, you can charge your car with the supercharger. If you’re playing a round of golf, you can use the AC charger. By the time you finish your game, you’ll have charged up your car at a cheaper rate.”
eLu aims to install its EV charging options in locations that are community orientated, or where electric charging may not yet be available for the public. The latest eLu charging station installed is operational off the Bruce Highway in Gympie, at Gunabul Homestead Golf Club.
“It’s a golf and country club that’s just north of the Sunshine Coast. It’s a great location for traffic that’s driving up the East Coast. It’ll very much service the needs of the local community, which has very little charging capability,” Fraser says.
“This will let them charge up all models. Some charging infrastructure can support one model such as a Tesla, but not for other vehicles. It’s a good community focused solution.”
This is also a key example of the flexibility provided by eLu’s charging infrastructure options. The country club itself was built in 1881 and has legacy electrical systems as a result, meaning there’s a limited power supply. To put a normal DC charger would’ve been difficult with these constraints.
Luckily, eLu’s ultra-fast DC chargers have 200kw battery integrated into the charger itself.
“Because we have that in-built battery, it can act as a buffer between the grid and the car charger, instead of taking a big hit out of the electrical network. Usually, with EV charging you need to put additional infrastructure in place. You don’t need that to power these machines,” Fraser says.
This drastically reduces the associated challenges with setting up EV charging infrastructure in very remote areas, or locations with low power supply.
“That project shows our capability of being able to establish a super fast charger in an area that’s challenged in terms of power capability. That can often make it difficult or impossible for charging to be setup. With our units, we can virtually raise it anywhere,” Fraser says. “It’s a great solution for ‘plug and play’, for it to serve as the power supply.”
It’s Fraser and eLu’s hope that the establishment of such EV charging can help to create a community hub for locals and passers-by alike.
“We look at sites to see if they could become a community hub. Providing a
service where the community can not only charge their cars, but they can have an experience there as well,” Fraser says.
“That’s a good charging experience, along with food, drink or a round of golf, whatever it is. We want to offer an experience that’s more than just waiting for your car to charge.”
eLu has ambitious goals for its future charging output, with the company aiming to have 30 charging stations in place in the next 12 to 18 months. “Our long-term goal is to provide a service for the community and create a brand that’s community friendly,” Fraser says. “Battery energy storage systems
are another piece of hardware that we’ll be exploring in the future.
“We want to embrace the community and give them a sense of ownership over the services that we’ll end up providing. That sense of community is something that’s ingrained in me, as well as the company.”
Another exciting development in 2024 will be the establishment of eLumina and eLu’s brand new, state-of-the-art research and development centre in Queensland. This centre is expected to further add to the company’s innovation in the space, while also providing a big boost in terms of manufacture to keep up with demand.
Fraser says keeping the product’s research, development and manufacture on home soil is a particular aspect that of which he’s very proud.
“We place great importance on having a manufacturer in Australia,” he says. “We’ve got a great local supply chain that’s secure and reliable for parts and the machines themselves, which we can deliver quickly. If repairs or maintenance are required, we’ll have all of those parts in our own warehouse to be able to facilitate servicing machines very quickly, right here in Australia.
“If somebody has an issue or a query, they’ll be able to contact a person based locally here on the Gold Coast who can respond to them straightaway. We’ve already got staff on the ground, but the facility will help us deliver that support even more.”
However, emerging technologies are reshaping the landscape of road maintenance, offering efficient and non-invasive solutions that promise significant time and cost savings.
Unlike traditional methods that require extensive excavation and labour-intensive procedures, Teretek® offers a streamlined approach that prioritises efficiency and effectiveness. By harnessing advanced materials and techniques, Teretek enables void filling, level correction, and ground improvement with minimal disruption to existing infrastructure.
The significance of Teretek lies in its ability to expedite repair processes and its capacity to deliver substantial savings for asset owners and managers.
By reducing downtime, minimising traffic disruptions, and optimising resource utilisation, Teretek offers a cost-effective alternative that enhances the overall sustainability of road maintenance operations.
In this article, we talked to Laurie Andrews, the Regional Business Development Manager (NSW/ACT) for Mainmark, who has 30 years of experience as a Civil Engineer, about using Teretek, exploring its key features, benefits, and real-world applications.
Mainmark is the pioneer of Teretek/ polyurethane in the Australian market with a tried and tested track record of over 30 years. It has tested and developed its product range, equipment, and team to suit Australian conditions.
“We support our application capability with a technical team of Engineers across our regions,” says Andrews.
“We are accredited with ISO 9001, 14001 and 4801 systems and processes and pride ourselves on our unique B2B project management capability. We also have a broad range of Teretek products tailored for the requirements of our specific application.”
“We use Teretek beneath both flexible and
rigid pavements, culverts, bridge approach slabs, embankments, and for the support of foundation systems” he says.
Teretek can re-confirm support and limit deflection and deterioration by filling voids underneath pavements. It eliminates the rocking of pavements and the subsequent pumping of subgrades.
“Teretek is frequently used to fill voids and raise bridge approach and relieving slabs,” Andrews says. “Including targeted ground improvement in suitable soils.”
One of the biggest challenges associated with any road repair is the time it takes to complete the repair. Mainmark’s Teretek products are designed to take effect almost immediately.
“Teretek is inert and is created by an irreversible reaction that results from a combination of plural components at the point of injection,” Andrews says.
“There is no degradation of the mixture once it has been injected and cured. Teretek is solid within 15 to 60 seconds and achieves approximately 90 per cent of its strength within the first hour.
“Teretek has been assessed as having a life span of more than 120 years,” he says.
Mainmark has continuously worked with a
single material manufacturer for the research and development of its Teretek materials for geotechnical applications.
By having a national footprint and more than a dozen specialised self-contained mobile Rigs, with operations staff employed in all major capital cities across Australia, Mainmark’s Teretek range of materials has been developed to solve the challenges associated with a wide range of applications and corresponding mechanical properties.
“For over 30 years, we have been working with asset owners, asset managers, remediation contractors and design practitioners explaining that there are ‘new’ options out there in Teretek that are more environmentally friendly and commercially viable compared to the traditional remove and replace mindset, ”Andrews says.
Part of that sustainable outcome is from the reduced impact of injecting the resin to remediate a pavement compared to the environmental impact of the traditional complete pavement remove and replace process.
While Teretek injection is still perceived as a new technology, it has provided solutions for leading roading authorities across Australia for over 30 years.
“Still today, there are many asset owners, asset managers, civil remedial works practitioners and applicators that are unfamiliar with the technology,” Andrews says.
“As governments and businesses become more aware of the environmental impact of the older remove-and-replace mindset, I see the adoption of the far less intrusive resin remedial works growing in the future.
“Mainmark have completed over 80,000 projects with our Teretek technology, even though there is still a relatively low level of understanding in the civil pavements segment. Much of the industry is still learning about the numerous advantages and applications of Teretek.”
With Reveal, you can eliminate subsurface risks, deliver infrastructure projects faster and minimise cost blow-outs and variations.
If you need to understand your underground, get in touch with the world’s leading subsurface experts.
Road construction can often take the centre stage and limelight when it comes to infrastructure development. Moving existing infrastructure to a future proofed location while negotiating complex requirements from utilities is often painful, costly and time consuming.
But for companies like Plan B Comms, it’s the basis upon which it contributes to major infrastructure works.
Plan B Comms forms part of the wider Plan B Group, which is made up of two other subsidiaries (Plan B Services and Plan B Auditing). Founded in 2004, Plan B Group is now one of Australia’s largest electrical and communication consultancies in Australia.
The company’s capabilities continues to grow, as does its portfolio of works across Victoria. This includes services such as feasibility modelling, project design and project management of new and existing infrastructure.
Plan B Comms’ experience was one of the reasons why, in late 2022, it was engaged by Stockland for proposed works that presented a variety of complications.
The Minta IN05 – Intersection Relocation project connected Soldiers, Grices and Bells roads, a roundabout to a signalised intersection, while also connecting to the M1 Monash Freeway in central Melbourne.
In the way of the intersection were critical telecommunication assets owned by multiple carriers, which would need to be relocated for the intersection to be constructed.
Harrison Kelly, Business Delivery Manager – Plan B Comms, says one of the biggest challenges presented by the project was coordination.
As part of the intersection works, three authorities needed to be relocated due to utilities intruding on the proposed project area for the intersection works.
“There were three carriers on this project, so we had to coordinate with all three authorities, rather than a single authority for gas and one for water,” Kelly says.
“We acted as the middlemen between our clients Stockland and their consultants, civil engineers and the three carriers. We designed a solution that satisfied our clients
requirements and managed the construction to completion. We’re the experts in this space and our clients trust us to do that.”
Plan B Comms has built a strong reputation with all telecommunication carriers and its subcontractors, leveraging these relationships to the betterment of its clients.
The required construction program, developed by Stockland, also comprised multiple moving parts, requiring clear communication and coordination between all project stakeholders. An area of expertise for Plan B Comms.
“It was a main intersection, which connects with a signalised intersection and roundabout signals ultimately connecting to the M1,” Kelly says. “The program outlined some strict requirements on timing. It was particularly complex due to the multiple roads and trying to design and coordinate new assets being installed but keeping the existing assets in-situ.
“Effectively we were duplicating the network within the same amount of space.”
Works included sections being bored, with trenches under and above storm water. These structures were designed to deviate to avoid live electricity as well as surrounding assets.
Generally, according to Kelly, the cost for a project of this size would’ve been over $1.5 million and it would have taken well over a year to complete.
Plan B Comms were able to deliver the
relocation works at a third of the cost and in half the time a project of this size would generally take to complete.
This approach allowed progress to power ahead on both the road construction and relocation works with minimal disruptions to either work packages.
Plan B Comms’ consultation and delivery project services were available for the client – from the planning and designing phases to after delivery.
“After we managed the relocation works to completion, we went the extra mile and offered support to our client to ensure the intersection would continue to be built. Often the assets are at risk at being disrupted after they have been installed due to them being the first to be relocated,“ Kelly says.
“We specialise in this area. By having us involved in the project it helped smooth these works over for our client and their consultant team. In a lot of cases the civil engineers will manage these types of projects and may complete one to two projects a year. We complete two to three projects per week and have built a team to obtain the best possible results for our clients.”
Plan B Comms works on the MINTA IN05 intersection project showed the company’s ability to coordinate and provide consultation services on a larger scale. Image: Plan B Comms.
Fulton Hogan delivers high-quality infrastructure to improve the lives of people in Australia and New Zealand, every day. Our 10,000+ strong team works in every kind of weather, creating, connecting, and caring for communities.
After 90 years in business, we believe resilient infrastructure will help tackle the challenges of a changing world, and we will continue to invest and innovate to play our part.
From asphalt, binders and aggregates, through to recycled pavement materials, we have been supplying top-quality construction products to the industry for decades.
Our experience, combined with our wealth of plant and resources, gives us the technical knowledge and skills to provide a wide range of construction services.
Fulton Hogan started on roads, and in the last 90 years we’ve gained vast experience across a range of sectors.
We understand the extreme performance requirements of civil infrastructure and the unique demands on their owners and operators. We work collaboratively with our customers and design partners to safely deliver quality customer centric outcomes.
Chris Kaelin, Specialised Roading Equipment (SRE) Technical Manager, is as passionate as they come when it comes to the development of equipment, hardware and software in the road construction machinery sector.
His long-term employer – SRE – has made a name for itself, thanks to its design, manufacturing and distribution of road construction equipment, particularly telescopic bitumen sprayers across Australia and New Zealand.
SRE’s six-metre telescopic bitumen sprayer is one of the most technologically advanced sprayers currently available in the market. Designed specifically for both emulsion and bitumen use, including crumb rubber for Australian applications, it’s the “sprayer that’s got everything”.
“Our six-metre sprayers have been around since 2000 and have been constantly updated since then,” Kaelin says. “The main goal was to be able to provide a locally built sprayer that gives enhanced functionality when it comes to automation. That’s really where it started and additional features have been put on it ever since.”
When it comes to the many technological milestones reached throughout the life of the sprayer, Kaelin says SRE’s real time job data transfer system comes close to taking the cake.
“A big change for us about eight years ago was the introduction of our web-based job management system. When the spray run is complete, all the key metrics about the spray run can be sent back to the cloud and the supervisor or facility manager can download that data and view that information online or physically, almost instantly,” he says.
“It helps to streamline that documentation and required recording of information around aspects such as binder types, application rates, coats, chip sizes, additives and more. We’ve been able to tailor that system to work in conjunction with existing software that companies may be already using.”
Feedback from operators and fleet managers, as well as modern in industry requirements, have kept the SRE team on its toes. One example has been the implementation of
systems that make it possible and easier to use crumb rubber, now a must for many operators in the Australian market.
“In Australia many still used fix-wing spraying, so we’ve created a fix-wing function,” Kaelin says.
“When you go between a crumb rubber product and an emulsion product there can sometimes be a bit of product that is stuck and leftover. That’s why we introduced a function where the end of the jet helps to suck that product out of the nozzle.”
SRE welcomes such changes, instead of viewing differing requirements as a hassle.
“We’re very open to what the customer wants and the dynamic of the business makes it very easy to implement some of these changes, especially when you’ve got a PLC-based control system. It’s very easy to add functionality. You don’t need to run wires and switches and that tends to be straight forward,” Kaelin says.
A factor in the success of SRE’s equipment and growth throughout the past 10 years, in particular in Australia, has been the company’s devotion to taking care of the customer.
How does the company do this? It uses the latest technology, as well as dedicated staff to minimise downtime.
As Kaelin explains, the company uses a
proven process to first assess and diagnose the seriousness of a mechanical or electrical issue.
“We can look remotely from the office, tap in, and see if the issue is related to the control system, if it’s a sensor issue or if there’s more to it,” he says. “If it’s a mechanical issue, the next steps will usually see us call a local support contact. If we need to change a part, depending on where it is, we can ship in parts. The advantage of being in New Zealand is that we’re only a two-hour flight away.”
Customers can also request additional training and guidance for their SRE machinery. This service is frequented by companies with newer operators and also a useful reminder of how to optimise certain features.
Kaelin says this training and guidance usually takes between two to three days. The same goes for an initial machine handover.
This support is available nationwide across both New Zealand and Australia, with SRE targeting the latter for greater growth, as well as the potential establishment of a dedicated site for local support services.
“Continuing to push in the Australian market is a really exciting prospect. I’ve been travelling out to Australia quite a bit recently, bringing a more advanced product into the Australian market that’s tailored to the industry’s needs and seeing the results have been great,” Kaelin says.
“That, I’m very proud of.”
Connect the physical and virtual world to plan, design, construct, and operate better road networks.
Understand and access models
Improve data access, management, and consistency
Leverage design automation
Reuse data to enhance construction hand-off
Questions? To learn more, scan the QR code below or visit: bentley.com/industries/roads-and-bridges/
MCLEOD’S PURSUIT OF SAFETY AND QUALITY OUTCOMES FOR CLIENTS HAS PLACED IT AMONG THE TOP PROVIDERS OF CRANES, HIABS AND TRANSPORT SERVICES IN NEW ZEALAND. TRT’S PRODUCTS AND SERVICES HAVE BEEN THERE EVERY STEP OF THE WAY.
“It’s been a business doing pleasure with you” is a quote from McLeod Founder Curly McLeod that perfectly reflects the company’s different approach to personalised service, reliable operations, expert advice.
It’s also the ethos that drives the company’s determination to always exceed customer expectations, says Scott McLeod, Managing Director – McLeod.
“The company was founded by my father in 1996, and I started in 2006 and took over in 2012 with my brother and my cousin. We’ve now got around 170 staff across three divisions, McLeod Crane, McLeod Hiabs and McLeod Transport. We cover everything from the Bay of Plenty to Waikato,” he says.
“We’re in multiple industries, covering nearly everything and anything that needs to be lifted. So, we’ve ended up in horizontal construction, vertical construction, industrial and also commercial jobs, including roading and infrastructure. We do a little bit of everything.”
McLeod describes the New Zealand-based company as versatile, with options able to cater for requirements across the whole market. Because of this, the company has a great number of assets, including machinery and equipment from global providers.
In his words, McLeod says the company’s philosophy and culture is considered
just as, if not more important, than the business’ equipment.
This company’s commitment to safety in each of its divisions is just one example. As McLeod explains, the new generation of leadership set out to establish a legacy of prioritising safety wherever possible.
“My cousin (Phil Hutchinson) my brother Peter McLeod and I combined our knowledge together to change the way that we were doing things to place safety first. In fact, now on all of our machines we have the branding ‘safety first, McLeod first’. We decided that we wanted to do health and safety properly,” he says.
“We knew that we weren’t just going to tick some boxes for the sake of it. We wanted it to have a purpose, that was driven by legislation as well as best practice. That would make it easier for our own teams to embrace and follow these standards, then to live and breathe it.”
Such was McLeod’s success in improving safety across the board, the company has been recognised twice on a national level.
“We’re always thinking about how we can improve safety and this ethos led to us having success at the New Zealand Health and Safety Awards. It’s flowed down throughout our entire business, now our processes and steps just blend into the background. You don’t’ even notice
that they are there, they just become a part of the job. It’s just a way of thinking,” McLeod says.
“It’s really refreshing also with our customers. We can be transparent around any investigations that we might do with incidents that occur on site. We just own it, and then we fix it. We don’t just make small changes; we make sure that we’re either eliminating or isolating the activity by putting in really robust administration around hazard controls. We work very hard to make sure it won’t happen again.”
It’s this hunger for optimising safety where possible that led McLeod to Tidd Ross Todd’s (TRT) range of pick-and-carry cranes, the TIDD Crane, each of which present their own developments in safety technology.
A mainstay of McLeod’s machinery fleet, TRT products are a range that McLeod says he takes great pride in.
“We believe massively in TRT’s decision to manufacture cranes in New Zealand, we think that’s amazing. They’ve not only set out to build cranes here, which is an undertaking that shouldn’t be underestimated, they’ve also gone out and built what I would say is the safest pick-andcarry crane on the market,” McLeod says.
McLeod currently has two models of TRT’s TIDD PC28-2, 28-tonne Pick-and-Carry Crane. This is on top of the company’s
variety of Hiab truck cranes and mobile cranes, with TRT being the certified dealer for HIAB, Manitowoc, Grove, Potain and Kobelco crawler crane products in New Zealand.
Whether it’s construction, civil projects, mining, or infrastructure, the versatile TIDD PC28-2 crane proves to be a suitable choice for various operating environments.
“They’ve designed the TIDD PC28-2 in such a way that it’s actually moved the market. Previously the market was quite stagnated when it came to health and safety in this space. But TRT’s designs have helped to move the ball forward,” McLeod says. “I could quite confidently say that there’s others that are now playing catchup as a result.”
A key feature of the TIDD PC28-2 is the machine’s ‘Slew Safe’, which gives the operator maximum control and security while lifting and moving. The Slew Safe system reduces steering speed down to 15 per cent in the unsafe direction and 100 per cent steering speed in the safe direction with an override alarm audible in and outside the cab.
“With the Slew Safe feature, you effectively know when you’ve entered ‘no man’s land’, or exceeded the capability of the crane. You’re no longer just flying by the seat of your pants, it accurately shows the exact point that you need to stop at to stay within the capability of the main lift rated charts that are set out by industry,” McLeod says.
“By now having that knowledge, that makes the crane massively safer. The innovation is industry leading. By eliminating dangers through engineering controls, we’re setting up our operators to succeed every time.”
The safety features don’t just stop there. As McLeod adds, improvements over time are helping to maintain the PC28-2’s position as one of the safest options currently available in the pick-and-carry market.
“I’ve watched as things have developed from the PC25 to the PC28 and the product is leaps and bounds better,” he says. “They’ve eliminated the pain points, increased the capacity and made it safer.
“For example, if you look at the computer system, in real time it’s telling you where its safe and where it’s not. If you’re working off a 75 per cent chart when you can work off a 66 per cent chart, you can dial it back. A contractor might want us to work at a lower percentage to increase the safety. It’s
very clever stuff.”
Jordin Hutchinson, New Zealand Crane Sales Engineer – TRT says the PC28-2 presents the market with a purpose-built tool, replacing methods in the past that have relied on the services of cranes not entirely suited to an individual task.
“In the past, operators have been able to use other tools, but businesses like McLeod have found that having a second pick-andcarry crane is a more productive tool for the sort of works that they’re getting involved with,” he says.
The culture is changing in a positive way towards pick-and-carry cranes in New Zealand.
“Customers are finding more preferred tools for different sites. Bringing a machine like the PC28-2 that serves a specific purpose is definitely a safer method”.
He adds that the quality design and output of a crane such as the PC28-2 can play a role in increasing the confidence and morale amongst operators.
“The biggest benefit I guess is the efficiency. It’s having that confidence that the machine will work in the most safe and efficient way possible,” he says.
“Another key aspect of TRT’s machinery is constant innovation, which is another thing that we’ve heard consistently from Scott and the rest of the team at McLeod. The upgrades that we’re bringing to the market are second to none, there are similar products out there in the market, but none are on par in terms of the safety
“That’s where I believe we trump others.”
TRT will soon release its latest iteration within the PC28 range, with the PC28-3G set to provide a more sustainable option for businesses.
The PC28-3G’s Cummins ISB6.7 Engine consists of a diesel particulate filter, as well as selective catalytic reduction technology. Both systems help to create near-zero emissions while also ensuring no compromises are made to fuel economy and performance.
This means the PC28-3G still has a 28-tonne maximum lifting capacity on the lug and 27.6 tonnes on the hook block.
“I love that the new version takes another massive leap, this time with the engine. If you’re really passionate about the environment, as our business is, then that’s a brilliant step forward,” McLeod says.
For McLeod, the existing professional relationship between the company and TRT is likely to expand and grow even further.
“We’re a growing company, alongside our customers. It’s not just growth for growth’s sake, because our customers are coming to us and helping us to broaden our scope. We’re a big believer of that and the way I like to describe it is like a deck of cards, we like to make sure that we’ve got the right card for the job,” he says.
“When the opportunity comes along and the growth of the business gets to a certain point, I’m certainly a customer who will be knocking at TRT’s door again.”
/ Australian owned / RCM certified / Exceptional for Australia’s tough environment / Local maintenance team via cloud platform
D1 Key features:
• Just 10kW-40kW input for up to 204kW combined EV charging
• Single gun maximum output at 160kW
• Built in 193 kWh battery with liquid cooling, supports v2g
D1
• Two charging guns with concurrent charging
• Built in eftpos supports tap and charge
L200
L1000
• Backup power for grid outages
• Solar integration, storing excess solar power
• Modular, scalable design for precise project sizing Please
• 233 kWh to 1491 kWh outdoor-rated cabinet storage system
• Preinstalled liquid cooled eLumina Power Battery modules
L1500
ASTEC INDUSTRIES HAS RECENTLY HANDED OVER ITS 100TH PAVER TO FULTON HOGAN, SIGNIFYING A MILESTONE IN THE EVER-GROWING AND STRENGTHENING PARTNERSHIP BETWEEN THE TWO COMPANIES.
Astec Industries and Fulton Hogan are two names that are synonymous with infrastructure and construction works across Australia and New Zealand.
Not only have both companies elevated themselves in their own right to the status of leaders of construction machinery and infrastructure development respectively, they have also helped to elevate each other through a strong professional relationship.
Astec Industries recently celebrated its 100th paver handover to Fulton Hogan, hosting senior representatives from the infrastructure provider to commemorate the milestone at its head office at Acacia Ridge in Brisbane.
John White, General Manager, Group Asset Management – Fulton Hogan, was one of the representatives present at the event. He says the milestone represents a long history of success, as well as collaboration between both enterprises.
“It’s been a long, enduring relationship because the supplier understands what the customer requires and vice versa,” he says. “They understand the objectives that we’re trying to reach and again and again they’ve come to the party to ensure that those aspects are sorted.
“It was great to catch up with the Astec team, to celebrate, sit down and discuss the relationship in terms of how it’s been as well as what it looks like in terms of the future.”
These objectives relate to the machinery requirements of Fulton Hogan, which is tasked with delivering some of the largest infrastructure works in the country’s history.
“We have a big focus and a need for machinery that has lower operating costs, together with a low frequency for repairs and maintenance and a premium backup service that ensures that if anything goes wrong, we can get everything sorted,” White says.
“It’s a relationship that’s based on honesty and being open. They value what we’re trying to achieve, that’s been really evident between both parties. We’re straight up with each other, if there’s any issues, we can talk to them to sort it. We don’t hide anything and neither do they.”
Jorge Boil, Astec Business Line Manager – Infrastructure, says the longevity of the relationship between both companies is emblematic of the value of trust and understanding what’s required.
“Astec and Fulton Hogan have had an established relationship in Australia for a very long time. In terms of our involvement in Australia, they’re our largest customer in the Infrastructure sector,” Boil says.
Boil says the relationship goes beyond just machinery purchases and trials. As is the Astec way, the company frequently receives and implements feedback to alter machinery for the better, to ensure it can satisfy and excel industry requirements.
“We’ve partnered with them in a number of areas. When we’re developing new units and machines, we frequently get feedback from them on how we can make these models better,” he says. “Whatever the new unit is, we usually bring it in to them to go over and check, just to see what their thoughts are.”
White says these conversations don’t just stop at product development. Instead, it’s an on-going discourse to ensure that both machinery and operation are performing at their optimum.
“That’s happening all the time,” he says. “We’re always in an open dialogue around improvements, from the small stuff to the larger features on the pavers. A lot of those changes are made straightaway, or if we needed to get something done, it’ll be done
in the workshop before delivery.
“They’ve always been willing to listen and action changes that we’ve discussed, which is great. It’s a key reason why Astec pavers make up the largest proportion of our paving fleet. That includes our push around reducing emissions, fuel consumption and other aspects.”
This relationship covers much more than just pavers as well.
“It’s not just the pavers, they’re also one of our largest customers and owners of the material transfer vehicles or shuttle buggies,” Boil says.
“They’ve also got a number of our profiling machines. These are complemented by a large number of fixed and mobile asphalt plants in New Zealand and Australia, which is fantastic. They were also among the first to receive our new, latest generation BG Series of Asphalt Batch plants.”
When it comes to aggregates, Fulton Hogan also owns and uses Astec’s crushing equipment.
While the volume and type of Astec machinery in Fulton Hogan’s fleet may have changed over time, that personal touch from Astec has been ever-present.
“I haven’t really seen Astec’s service change. It’s always been consistent and the door’s always been open,” White says.
“The expectation is that we’ll maintain the relationship we already have and grow from there. They’ve been a part of our journey, and so have we for them. Astec gear is crucial for us to meet our future objectives and works.”
Boil says both companies will continue to shape each other’s future, with key projects and machinery developments in the slate for 2024 and beyond.
“Moving forward, we want to improve the partnership and make sure it continues being beneficial for both parties. They have a number of contracts on-going and upcoming around the country and we look forward to servicing their future needs,” he says.
EIFERS HAS RECENTLY BECOME THE EXCLUSIVE DISTRIBUTOR OF BAY-LYNX VOLUMETRIC MOBILE BATCH PLANTS IN AUSTRALIA. THESE ROBUST PIECES OF EQUIPMENT ARE PAVING THE WAY FOR BETTER CONTROL OF CONCRETE MIX ONSITE WITH BETTER CONSISTENCY OF THE MIX, NO WASTE AND IMPROVED MIX OPTIONS.
Trust, passion, safety, mutual respect and family are the core pillars for Eifers, a company whose expertise in time critical civil construction works, both in the public and private sectors, are fast becoming renowned for their unique capabilities and ethos.
Eifers, an Australian owned company was formed in 2003 by father and son team of three, Wayne, Daniel and Matthew. These three men have grown the organisation to now approximately 40 employees who tender for works on major infrastructure projects around the country.
Eifers specialises in innovative infrastructure delivery, which includes time-critical civil construction works. This focus has played a pivotal role in the company’s growth. Eifers expertise in time-critical deployments has grown their reputation as a trusted, reliable and respected project partner across multiple sectors and industries.
“We’re an innovative civil company made up of two divisions, our innovation centre that houses our high-strength rapid set concrete, and our lightweight Ecofil concrete product,” says Matt Eifermann, the company’s General Manager and Co-Founder.
“And then we have our standard civil side, an ISO-accredited service that caters for roads, airports, ports, carparks, substations, public lighting, earthworks and more.”
both the right machines and manpower is a good example of how the company is always looking to adopt and implement new and innovative solutions into the market.
As a forward-thinking company, Eifers became a trailblazer with High-Early Strength Concrete and forged a path as experts in its field, utilising volumetric mobile batch plants to deliver the fast, efficient, accurate concrete blend direct to site without waste, mess or fuss. Eifers team are highly trained making large scale projects easily manageable.
“We’ve used volumetric mixers since 2011. In late 2018 we enquired about purchasing a Bay-Lynx unit, our first unit arrived in 2019 and it was a game changer. From there our relationship with Bay-Lynx grew, but what really stood out was their level of support. From installation through to parts and servicing,” Eifermann says.
“Even though they’re based out of Canada which has some time zone challenges, their response rate is fast, if we have any questions about mechanical or software-related issues, it only takes them a short time to respond.
Eifers already had experience with volumetric cement batch plants, making
for what would turn out to be a fortuitous relationship between both companies.
“We have developed a really good relationship with the Baylynx Canada team over time. One day, they had asked us if we knew anyone in Australia who would be interested in potentially becoming a dealer. We talked internally and decided that it was something that we’d be able to do ourselves,” Eifermann says.
“It was enticing because we could add another bow to what we already have within our business group.”
Eifers is now the exclusive distributor of Bay-Lynx volumetric mixers in Australia, with the new-found partnership seen as a new era of the company.
Essentially, the Bay-Lynx Volumetric Mixer is an onsite concrete batch plant that is mounted onto a truck, it is also a pugmill and materials blender. The unit comprises three separate bins, one for aggregates, one for sand and one for cement, along with a water tank.
A conveyor underneath the unit brings the material towards the rear of the machine. All components are dry until the machine has been activated. These materials are then mixed
on a 2.4 metre auger, taking around 35 seconds to produce a concrete mix.
“One of the biggest benefits is that we’re producing concrete on site, so it’s fresh. It hasn’t been sitting there for a while, which means you can take away the time needed for an added hydration process. You also don’t need to mess around with your technical specifications, you get a lot more workability than standard equipment,” Eifermann says.
“Another massive benefit revolves around sustainability. As soon as you’ve made what you need, you simply turn off the machine so you’re saving on emissions and energy. There’s also no wastage, because whatever you don’t use just stays on the truck dry.”
Eifermann says Bay-Lynx batch plants can also provide greater versatility and flexibility when it comes to mix designs.
“We can change the mix design from the truck that can fit 7m3 (or ‘’cubes’) onboard,” he says. “We can make 2m3 of 25mpa (a measure of the compressive strength of concrete), change a couple of settings and make another mix such as 32mpa.
“You can make 2m3 on one side, drive half an hour to another job and make 2m3 on the other side.”
Bay-Lynx units can also support the use of mixes incorporating recycled materials such as rubber, glass and aggregate.
This also includes slag or fly ash, further boosting the machine’s capabilities when it comes to sustainability.
“With the volumetric mixer there are less truck movements because the unit is stationary on site. We also have a silo with us. We have a cement tanker come in every hour compared to having five or six coming in every hour. The process is better, and it works. It’s great for those types of scenarios and can really give you an edge,” Eifermann says.
“If someone has a construction company or a concrete business and are tired of having to wait around to get your concrete supply, this unit is perfect for them. They’ve essentially got full control over when and where they get their concrete.”
Eifers has already successfully used the BayLynx volumetric mixer unit as part of its works on major infrastructure projects. One of the largest was its recent works on a large-scale year long Melbourne Airport Project working as a subcontractor for Fulton Hogan.
“These were works that were very time critical, so we were required to ‘get in and get out’. The volumetric mixer was great for that,” Eifermann says.
The MAPMP 2.0 - DP2 Expedient Pavement Works included replacing over 8000m2 of concrete with Rapid Hardening Concrete at Melbourne Airport to support aircraft operational use, in preparation for the Taxiway Alpha reconstruction. This comprised slab replacement works to 144 defective concrete pavement areas and pavement repairs to patches which took place overnight over the course of a year.
“We envisage this becoming a better way forward to sustainable and easily manage civil works in both urban and remote areas,” Eifermann says.
Another benefit of using Bay-Lynx volumetric equipment is the backup support, as well as the variety of options available.
When it comes to support, Eifermann says Eifers are fully equipped with spare parts in Australia. They also have the team to provide mechanical fixes on site as required. However, here is where the technology comes in. For software adjustments, Bay-Lynx is able to hook into their Batch Pro Connect onboard system to assist remotely through a laptop.
“From Canada, Bay-Lynx’s support team can support you anywhere in the country. The person who owns the unit can have the support team dial into their laptop using TeamViewer and start diagnosing the problem and making any required adjustments straight away,” he says.
Bay-Lynx Volumetrics are fully customisable adding to the overall versatility of the product, Eifermann adds.
“It really just depends on what the customer requires. If they want to have a white truck with a dark coloured body for the volumetric unit, that’s easy. We can also arrange sign writing on the truck too.
“YOU CAN MAKE 2M3 ON ONE SIDE, DRIVE HALF AN HOUR TO ANOTHER JOB AND MAKE 2M3 ON THE OTHER SIDE.”
This project makes up one of many packages that Eifers has delivered at the Melbourne Airport.
Another recent project milestone was the company’s contributions to the Santos Moomba Gas Plant, which required the delivery of remote mobile concrete production in Central Australia.
For these works, Eifers provided Bay-Lynx volumetric mixers along with other equipment for the project. Eifers shipped all materials and machinery across 2000 kilometres of rough terrain. Tackling remote and extreme conditions, Eifers produced 650 cubic metres of fresh concrete on site without a problem.
Another example is the Rye Park Wind Farm in New South Wales. Eifers produced more than 400 cubic metres of fresh 32mpa structural concrete designed and certified by the client with its Bay-Lynx volumetric mixers. Remote and regional work is easier to manage with a Volumetric mobile batch plant.
They can also have a fibre feeder added, to create fibre reinforced concrete and use powder oxide, to make coloured concrete,” he says.
“You can also have an additional eight mix tanks. Customers can also ask for a water reducer or retarder, as well as an errand treatment on the concrete. There’s plenty that we can do, depending on what customer’s need. Having these capabilities opens the user up to many more types of tenders and projects.
“Overall, we are happy with our Volumetrics and the versatility and capability they bring us. We think that other construction companies in Australia would benefit from having this type of machinery at their fingertips. We see vast opportunity with these trucks which is why we are backing this brand all the way.”
To find out more about the BayLynx Volumetric mobile batch plant simply visit https://baylynx.com.au/
MATTHEWS BROTHERS ENGINEERING TAKES PRIDE IN ITS AFTER-SALES SUPPORT AND MAINTENANCE SERVICES. RICHARD BAILEY, GENERAL MANAGER AND DESIGN MANAGER EXPLAINS HOW THE COMPANY HAS TAKEN GREAT STRIDES IN THIS AREA OVER THE PAST 12 MONTHS, AS WELL AS WHAT CUSTOMERS CAN EXPECT FOR THE FUTURE.
For 100 years, Matthews Brothers Engineering (MBE) has taken its customers step by step along the way, throughout design, development and delivery of its premium road making machinery. As a result, its after-sales support and maintenance services were always a consistent presence.
But now the Australian owned and operated company has placed a greater emphasis on ensuring that customers can quickly and easily receive the support they need across Australia.
Richard Bailey, MBE General Manager, Design Manager says that when he and Sally Rolfe, Sales and Operations, took on the mantle of running MBE in 2022, service and maintenance was a key area of interest that was highlighted for potential growth.
Prior to establishing dedicated staff and resources to this area of the business, Managing Director Paul Matthews was tasked with answering customer queries and requests regarding machinery maintenance, on top of running the company during the day.
“Historically, it was always Paul who would be there on the other side of the phone, answering calls for what seemed like 24-hours a day. You really can’t pay for that level of commitment,” Bailey says.
“When Paul stepped back, we identified that the support side was a bit of a gap for us. Our support and service were a bit more ad-hoc. The first step for us was to identify that and go ‘right, we really need to work on this’. Now it’s a great strength of ours, along with our Australian-made product.”
A big step for MBE was the allocation of a dedicated team member who would oversee service, maintenance and technical support, catering for issues from mechanical issues, right through to electrical, or even spare parts.
“He’s now a central conduit for coordinating all of that. He’s previously fitted out these vehicles and did that for the entirety of his apprenticeship, so he knows these vehicles inside and out,” Bailey says.
“Having that single point of contact allows him to really build upon that knowledge. This has really become his bread and butter.” Issues are usually coordinated within MBE’s experienced team to find the best possible
solution for the issue at hand.
“We make sure that we stay in really close communication with the customer to see if it’s an issue that can be solved over the phone, or whether or not they might need to bring the machine into our shop for more works. Again, that can now all be coordinated through a single contact,” Bailey says.
MBE is also working to establish servicing schedules, enabling services and general maintenance to be applied to equipment before problems arise.
Bailey describes these as “preventative works”.
“It’s about addressing potential issues, before they turn into an issue. It’s great to get that out of the way in the offseason to reduce downtime on site,” he says.
Spare parts have also been a growing area of emphasis for MBE.
“The great thing is that it’s our own OEM componentry, so we don’t have to wait for an online order, bring it in from somewhere else and add to the waiting time. We can just take the parts off the shelf and they’re ready to go,” Bailey says.
“It’s a really quick turnaround. If someone
needs something very urgently, we can get it to them overnight to get them back up and running as soon as possible. That’s the essence of our service – that so much of our equipment is locally sourced.”
Training for customers when they receive MBE machinery is another aspect that the team is currently working on, with some clients who seeking additional training in how to optimise MBE machinery.
These training sessions have also been an opportunity to receive feedback from operators.
“We’re sitting with the sprayer operators who might go ‘well we like this, but usually we’d do this’. It all ties back to getting active engagement and live feedback that we can use to refine our products even more,” Bailey says.
“This and the general servicing and maintenance are areas that we’re looking to financially invest in, not just put time into it. It’s something that we really want to grow, because we recognise how important it is. Our product is only ever as solid as the support that we can provide. We think it’s a big advantage that we can offer this to our customers.”
❙
❙
❙
❙
We raise, re-level & re-support sunken concrete, roads and buildings.
Immediately Trafficable NonInvasive
ONE OF THE LEADING HEAVY EQUIPMENT MANUFACTURERS HAS SIGNED A MULTI-YEAR DEAL WITH WILLIAMS RACING TO BECOME THE PRINCIPAL PARTNER OF THE BRITISH TEAM FROM THE START OF THE 2024 FIA FORMULA ONE WORLD CHAMPIONSHIP SEASON.
Komatsu was a key partner of Williams Racing in Formula One during the 1980s and 1990s, a period of abundant success for the team. The most notable achievements were in 1996 and 1997 when Komatsu supported Williams Racing to Constructors’ and Drivers’ Championships with Damon Hill and Jacques Villeneuve, respectively. With an eye to the future, both brands are excited to build on their shared history as they embark on a new era.
Tokyo-based Komatsu has been leading innovation in the equipment manufacturing sector for more than 100 years. As embodied by its brand promise, “creating value together,” the company believes that collaborative partnerships are the optimal way to create a lasting positive impact.
Komatsu’s official designations with Williams Racing reflect the companies’ shared focus on the long-term development of engineering, technology, and new generations of talent. It will be the Official STEM and Early Careers Partner, Esports Partner, and Construction Machinery Partner. These areas will overlap and combine within the partnership. Komatsu endeavours to engage and bring focus to the next generation of innovators through STEM events enriched by the Williams Racing Esports platform.
“Komatsu and Williams Racing have shared values around innovation and the development of our people,” says Hiroyuki Ogawa, President and CEO of Komatsu. “Through our partnership, we look forward to creating value together, both on and off the track. Our partnership with Williams Racing is aligned with Komatsu’s mission to create value through manufacturing and technology innovations to empower a sustainable future where people, businesses, and our planet can thrive together.”
One of the driving forces behind the partnership was the alignment of vision that the two brands share. The characteristics embedded in Komatsu’s DNA and values, such as cutting-edge technology, outstanding quality, and unwavering reliability, are all demonstrated by Williams Racing at the highest level of motorsport. This new partnership creates a foundation for future cross-collaboration between Williams and Komatsu. Komatsu is looking forward to working with Williams across a range of disciplines, especially relating to the development of its people and exploring potential opportunities in the technical engineering ecosystem.
“Williams Racing is delighted to be rekindling our relationship with Komatsu,” James Vowles, Team Principal of Williams
Racing, says. “We have enjoyed huge success together in the past, and reuniting is a significant step in Williams Racing’s long-term mission to return to the front of the grid. Both Williams and Komatsu are committed to attracting and developing the best young talent in pursuit of our goals, and we look forward to working together again.”
Komatsu’s logo and branding will feature prominently on the 2024 Williams Racing livery, as well as the team’s overalls and kit, during the upcoming Formula One season.
With operations in over 140 countries, Komatsu is a global provider of premium heavy equipment, services, and solutions. The company introduced the world’s first autonomous dump truck in 2008 and is helping customers advance towards carbon neutrality with its growing range of electric, hybrid and fuel cell construction and mining equipment.
Williams Racing is one of the world’s most iconic Formula One teams. The British outfit has been competing at the highest level for almost five decades, amassing 114 victories, 313 podiums and 128 pole positions in that time. Williams Racing has also won nine Constructors’ Championships, making them the second most successful team in the sport’s history.
QUALITY FABRICATION AND ENGINEERING’S ROAD ANT, A FORWARD-MOVING AGGREGATE SPREADER, IS SUPPORTING GREATER SAFETY AND SUSTAINABILITY.
Since its initial launch, Quality Fabrication and Engineering’s Road Ant has steadily gained traction, embodying a commitment to long-term sustainability and safety. Glenn Hardiman, General Manager of Quality Fabrication and Engineering, emphasises the enduring performance and resilience not only of the Road Ant but also of the company’s broader product range.
“With 22 units currently in operation across Victoria and deployed by major road-focused companies, along with usage in NSW and South Australia, the Road Ant exemplifies our dedication to sustainable solutions,” he says. “Our design prioritises longevity and ease of maintenance, ensuring that the Road Ant remains a dependable asset for years to come.
“By ensuring 365 year round usage, that would otherwise necessitate multiple vehicles, the Road Ant emerges as a sustainable choice, maximising the ROI on capital outlays and optimising resource consumption over its extended lifespan.”
Highlighting the company’s track record of longevity, Hardiman adds, “our initial powered road brooms, delivered over two decades ago and continue to operate efficiently to this day.”
A pivotal aspect of the Road Ant’s appeal lies in its safety features, a cornerstone of its inception and ongoing development. This emphasis on safety underscores Quality Fabrication and Engineering’s commitment to the well-being of users and pedestrian workers on site.
The Victorian Department of Transport’s mandate of the use of forward-moving aggregate spreaders on its spray seal sites was introduced in July 2022 to modernise and increase the safety of these operations.
“Since day one, safety has always been a high priority and reason why we’ve put so much time and effort in developing a dual-control aggregate spreader,” Hardiman says.
“Tragically – in December 2023 – a road worker was killed by a reversing truck on a spray seal work site, highlighting why safety needs to be a priority. While the risk can never be removed, it’s paramount that we make the process as safe as we possibly can.”
The Road Ant features both a front and rear cabin with full operation of the truck, spreader and safety controls from either end, eliminating the need to spread in ‘reverse’. The rear cabin is also dual control, enabling operation from either the left or right hand side of the cabin for a clear view of the spread line.
“A clear line of sight for the operator while spreading is really important as roadworks can often be very busy, hectic workspaces, with a lot of personnel on the ground and other machines such as bitumen sprayers and rollers,” Hardiman says
To ensure that the machine could satisfy and exceed safety standards, Quality Fabrication and Engineering undertook a thorough accreditation and testing phase.
“We had to make sure our unit could satisfy National Heavy Vehicle Regulations, we achieved that accreditation with the terrific assistance of Transport Certification Services,”
“We reached out to a local company that developed a reverse safety system, where the brakes are automatically applied when the unit is reversing and a pedestrian or other object comes within close proximity of the unit, greatly reducing the risk there.”
In addition to its longevity and safety features, the Road Ant champions efficiency in throughput, thanks to ongoing innovations spearheaded by Quality Fabrication and Engineering’s team.
Design Engineer David Taylor says the smart spread system streamlines operations by automating adjustments based on road speed, minimising the need for manual intervention by operators.
“This empowers operators to focus solely on their line of sight and vehicle positioning. It’s a great safety initiative that we have developed,” he says.
Beyond operational enhancements, the incoming system aligns with sustainability objectives. Hardiman elaborates. “The precision of the smart spread function minimises stone wastage, translating into substantial annual savings. Moreover, the Road Ant’s compatibility with alternative materials, including recycled ones, highlights our commitment to sustainability.”
David Taylor says this approach underscores the ongoing pursuit of simplicity and efficiency, “our team has been diligently working on software enhancements to the user interface. These updates, due shortly, will offer improved graphics, a more intuitive driver experience, and more streamlined operations, based on feedback.”
As Quality Fabrication and Engineering continues to evolve, the Road Ant stands as a testament to innovation, efficiency, and
AN UNASSUMING MACHINE THAT PLAYS A CRUCIAL AND OFTEN UNSEEN ROLE IN PREPARING AND MAINTAINING THE EXTENSIVE ROADWAYS IS THE ROAD ROLLER.
Have you ever thought about what machinery is used to prepare and keep roads flat? They are called asphalt rollers, and simpler devices are often found at sporting grounds across Australia. However, a very specific device does much of the heavy work for flattening and smoothing roads.
These workhorses of the construction industry are not known for being glamorous, but their impact is undeniable. From ensuring smooth and safe journeys to laying the foundation for lasting infrastructure, road rollers are the silent partners in building the roads that connect us and power the economy.
Double drum asphalt rollers are also known as tandem rollers or vibratory rollers. They are workhorses of the road construction industry. These beasts of the road are used to compact asphalt pavement, ensuring it is dense, smooth, and durable. The rollers achieve compaction through a combination of their weight and vibration.
So, how are they influencing projects around Australia? Dynapac CEA has a range of high-quality pieces of capital equipment, including the Dynapac CC2200 Asphalt double drum roller.
The Dynapac CC2200 has a rolling width of one and a half metres. They are designed with efficiency in mind, derived from operational features that deliver high-quality surface finishes.
Those operational features include soft starting and stopping to prevent unevenness or cracking in the asphalt layers. This allows even an unskilled operator to start and stop without leaving marks. In a panic situation, the machine will drop out of the soft mode and brake immediately, signalling the need for an emergency stop.
FEATURE PACKED
Several features of the CC rollers make servicing quick and easy, ensuring maximum
uptime. Using a double pump vibration system eliminates the need for a vibration valve, making the system more efficient, aiding servicing, and reducing fuel consumption.
There is one pump for the front drum and one for the rear, which can be shut off. With a volume of 750 litres for the CC2200 – CC3300, 900 litres for CC4200 and as much as 1400 litres as an option for CC5200 – 6200, it gives ample water resources that can be used later for other purposes.
All machines can be equipped with the optional offset drum (split drum and combi rollers have offset as standard.) This, in combination with the asymmetric cab, makes the machines very easy to operate.
The CC2200’s articulated steering system provides great flexibility, allowing the front and rear halves of the machine to pivot independently. This enables tighter turns and improved manoeuvrability in confined spaces, navigating around obstacles, or following curves on winding roads.
The CC2200 also offers adjustable vibration frequency and amplitude, allowing operators to tailor the compaction process to different materials and project requirements.
Compared to larger rollers, the CC2200 boasts a relatively compact footprint. This can be advantageous in tight job sites or where manoeuvrability is essential.
One way of achieving high-quality compaction is to optimise the ergonomics for the user. This ensures that operators have continuous visibility of the operation and comfortable access to the controls.
You can tailor your roller to local conditions, including the operator’s platform with a Roll Over Protection Structure (ROPS) cab and air conditioning.
The clear LCD control panel gives operators the information they need. All the gauges
are displayed, and the operator can change between menus at the touch of a button.
Dynapac CEA has equipped the machines with slideable and turnable seats and steering modules for the best ergonomics. The engine is placed on the rear module with less heat and noise for the operator. The very low vibration level on the operator´s platform also adds to the operator’s comfort.
The new range of CC2200s are powered by Cummins QSB 3.3, QSB 4.5 or Deutz TCD3.6 engines. Both Stage IIIA/T3 and Stage IIIB/ T4i versions are available. Dynapac’s automatic engine idling system, together with a highly efficient hydraulic system, makes fuel consumption low and efficient. Infinite adjustable maximum speed is standard.
Daily service points are few and easily accessible. The position of the engine on the rear module and the large, easy-to-open engine hoods contribute to easy and fast service. The service info displayed directly on the driver’s LCD also facilitates service jobs.
At the same time, the periods between servicing have been extended. Corrosion-free water tank and sprinkler tubes, in combination with easily accessible filters, ensure reliability and easy maintenance.
This improved maintenance schedule provides better environmental outcomes for any organisation taking one on board.
Efficiency enhancements have saved some eight kilowatts in the operation of a typical model in the range. Dynapac CEA also offers an optional EcoMode, which offers fuel savings of up to 15 per cent.
It also makes the already quiet CC roller even more silent. Biodegradable hydraulic fluid is optional, while emission-controlled engines are standard.
In February 2022, an inundation of rain smashed New South Wales, resulting in one of Australia’s most catastrophic flooding events. Community members tragically lost their lives, homes and properties were destroyed and roads were among the swathe of infrastructure across the eastern seaboard that was washed away.
Almost two years later, road rehabilitation company Stabilcorp is helping the community by revamping local transport infrastructure damaged or unusable by the devastating floods. The local community is warmly receiving their help. They are going out of their way to make contractors feel welcome and thank them for contributing to reconnecting towns and neighbours.
“Some of the communities we’ve been working in still have marginal access or no access to heavy vehicles,” Stabilcorp General Superintendent Brendan Pinson explains. “The community definitely appreciates what we’re doing out there.”
Most of Stabilcorp’s recent work has involved overlaying, stabilising, and sometimes wholly replacing roads impacted by the 2022 floods.
“The biggest project at the moment is Grafton,” Pinson says. “At the moment, we are up the top of Clarence Way. The roads out there have been impassable to the point where the Council has been up there just ripping up the road and regrading it.”
With at least another eight months of works at Clarence Way alone, Stabilcorp has armed itself with a WesTrac-supplied Cat® RM400 Road Reclaimer designed to rehabilitate roads and provide soil stabilisation efficiently and effectively.
For Pinson, the Cat RM400 not only suits the job, but is also comfortable and easy to operate.
“A new operator would pick it up very quickly; everything’s laid out very well, and the operator’s very comfortable sitting inside the cab,” he says. “We’ll definitely go with the Cat brand for any of our reclaimers that we update in the future.”
WesTrac Product Specialist – Paving and Forestry Products Michael Kelly says the Cat
RM400’s main attraction is the vast range of features, including operator comfort, easy-touse multifunction controls, a suspension seat, and machine size.
“Because of the size of the machine, it’s very easily transportable, like a little pocket rocket,” Kelly says.
According to Kelly, demand for Cat Road Reclaimers has continued to rise in New South Wales as more flood repair work is commissioned.
“In some areas where roads were washed off the surface, they had to build the road base back up and then build a road over the top. As such, we’ve seen a massive uptake in the requirements of these machines to undertake these jobs,” he says.
For Stabilcorp, investing in a Cat RM400 Road Reclaimer through WesTrac was about more than just the machine.
“One of the main reasons why we went with Cat gear was that we knew we would get good service out of WesTrac,” Pinson says. “No matter where you are in the State, there’s usually, within half an hour, a WesTrac service vehicle available.”
WesTrac’s service proved invaluable when Stabilcorp had a mechanical issue with its newly acquired machine.
“Their communication was key there,” Pinson says. “They were honest the whole way through, which was refreshing.”
WesTrac Product Support Sales Representative Jim Hewitt was on the front foot with this support. He ensured Stabilcorp’s machine was back up and running with minimal downtime.
“They’re quite complex pieces of equipment. When new gear like that is in the field, fresh off the production line, commissioning with WesTrac support is critical to ensure the customer will reach full productivity fast,” he says.
“Getting through that process as quickly as possible is our highest priority. We do that by utilising our local field service technicians, WesTrac’s team of experts back at the branch, and with the help of Caterpillar’s specialists.”
With 14 branches across New South Wales, WesTrac has businesses like Stabilcorp covered in servicing Cat Road Reclaimers.
“We understand that whenever there’s any mechanical concern in the field, we must be on it as soon as possible. We also need to keep the customer informed on the progress. If they need anything from us.”
WesTrac’s primary service goal is to reduce downtime. It is why WesTrac collaborates with Stabilcorp to provide flexible maintenance and repair options.
“We’ll be flexible and work around their productive timeframe,” Hewitt says. “These machines pay mortgages, send kids to school, and if they have a down event, it has a massive impact on a small business.”
For Pinson, bringing the Cat Road Reclaimer into Stabilcorp’s fleet is only the beginning.
“We want to increase our fleet to have more Cat equipment. We’re just about to hit the button on buying a new grader,” he says. “There is no one in Australia that can match WesTrac’s service.”
Proud Suppliers of Telescopic Bitumen Sprayers to the Australasian Roading Construction market for over 20 years
Over the last 20+ years, we’ve listened to our customers’ feedback and continuously evolved our range of sprayers, meeting the specific and unique demands of the Australasian roading market.
From our highly manoeuvrable 4.5m telescopic urban sprayers right up to our 6.0m reseal sprayers we have the right sprayer for the job – all offering the ease of use and efficiency of our telescopic spray bar.
Find out today why operators across Australia and New Zealand are ditching fixed wing sprayers and demanding SRE’s range of telescopic bitumen sprayers. www.specialisedroadingequipment.com
Email info@specialisedroadingequipment.com
Ph +64 7 848 1197
Roads & Infrastructure Magazine, in partnership with the Australian Flexible Pavement Association has proudly brought back the Contractor Capabilities Showcase for 2024, sponsored by SAMI Bitumen Technologies. Beyond this page lies a valuable resource for asset managers, road owners, governments and more to easily find contractors for projects of any size and scale. This year’s showcase provides a resource of more than 300 contractors.
NOW IT’S TIME FOR YOU TO DISCOVER WHAT THIS YEAR’S CONTRACTOR CAPABILITIES SHOWCASE HAS TO OFFER!
SAMI Bitumen Technologies, established in 1978, has been a pioneer in the Australian roads industry, meeting the market demand for advanced bitumen technology. We pride ourselves on being a reliable company, consistently supplying the full range of high-quality bituminous products for the construction of critical infrastructure such as highways, bridges, runways, and local roads. Our commitment to sustainability is ingrained in our operations, as we continually strive to develop environmentally friendly solutions that contribute to the long-term durability of Australia’s road network.
Innovation is at the heart of SAMI’s success story. Over the years, we have invested heavily in research and development, pushing the boundaries of bitumen technology to provide cutting-edge solutions to our customers. Our forwardthinking approach enables us to adapt to the ever-evolving needs of the road industry, delivering innovative products that enhance the safety and efficiency of road construction and maintenance. At SAMI, we firmly believe in the intrinsic link between quality and reliability. Our products undergo rigorous testing and adhere to the highest industry standards, ensuring that they meet and exceed our customers’ expectations. As a result, SAMI Bitumen Technologies has earned a reputation as a trusted and dependable supplier in the Australian market, building strong and enduring relationships with our valued clients. As we move forward, sustainability remains a core focus for SAMI. We are dedicated to reducing our environmental footprint and promoting eco-friendly practices throughout our supply chain. By prioritising sustainable sourcing, production, and distribution methods, we contribute to the preservation of natural resources and the reduction of our industry’s environmental impact. SAMI Bitumen Technologies stands as a beacon of innovation, sustainability, quality, reliability, and resilience in the Australian roads industry. With an unwavering commitment to excellence, we continue to lead the way in providing advanced bitumen solutions that strengthen the infrastructure backbone of Australia while ensuring a greener and more sustainable future for generations to come.
SAMIfalt I-Brid: Advanced hybrid-modified bitumen that excels in extreme conditions. Developed with RMIT University, this versatile asphalt binder incorporates innovative polymers for exceptional resistance to deformation and cracking, perfect for demanding Australian roads. It offers excellent workability and compactability, simplifying paving and compaction. Its self-crosslinking abilities ensure durability, surpassing traditional PMB products. With high cohesive strength, it resists crack initiation and propagation in various asphalt mixtures, making it ideal for heavily trafficked areas. The selected polymers also provide resistance to fuel and hydrocarbons, making it suitable for regions prone to leaks. Additionally, it offers exceptional moisture damage resistance for stability in wet environments.
SAMIbond 007: Rapid-setting polymer-modified bitumen emulsion designed for use as a high-performance tack coat in heavily stressed areas. It is particularly suitable for airports and main roads with high shear forces during braking or accelerating. Its trackless properties prevent pickup of residual binder by asphalt trucks and pavers during construction, improving pavement performance and avoiding tracking of fresh bitumen. Laboratory and field studies demonstrate that SAMIbond 007 provides superior shear strength between pavement layers, enhancing bonding and then improving the fatigue performance of the pavement. Its unique chemical composition enables faster breaking and curing times, increasing productivity on paving job sites. It has also proven performance in composite pavements when need a high shear strength bond between concrete and asphalt layer.
SAMIBioPrime: SAMIBioPrime is a petroleum solvent-free cationic bitumen emulsion that contains vegetable-derived oil from renewable sources. It quickly penetrates stabilised, bound, or unbound granular compacted base courses, eliminating the need for a curing period and allowing for same-day application of the next layer. This enhances project productivity. SAMIBioPrime is nearly carbon-neutral, reducing the carbon footprint of pavement construction. It is also safe to use, posing no explosion hazards or risks associated with VOCs. It can be used beneath various bituminous layers without causing softening, unlike conventional cutback primers.
SAMIGreen: Eco-conscious Polymer Modified Binder and emulsion range designed to reduce the carbon footprint of the road industry. By partially substituting petroleum bitumen with a blend of biogenic renewable resources, SAMIGreen minimises reliance on fossil fuel-derived sources, leading to a significant reduction in carbon emissions. This advanced PMB meets rigorous specifications while offering a carbon footprint that is more than 50 per cent lower than conventional correspondent. By integrating renewable and eco-friendly resources, SAMIGreen contributes to the conservation of nonrenewable resources and supports the industry’s goal of achieving a net-zero carbon footprint.
SAMI Bitumen Technologies2, 3-5 Gibbon Road
Winston Hills, NSW 2153
P: (02) 9624 0101
W: www.sami.com.au
Key personnel:
Sebastien Chatard
General Manager schatard@sami.com.au
SAMIFloat: Versatile and environmentally friendly high-float emulsion designed for surfacing roads. Its gel-like structure, created with special polymers and additives, enhances binder adhesion and minimises early aggregate loss. Unlike traditional methods, SAMIFloat eliminates the need for petroleum cutters to soften binders before spraying and pre-coating aggregates. It offers a more sustainable solution by requiring lower heating during application. SAMIFloat is a unique cationic high-float emulsion, avoiding logistical issues associated with anionic emulsions. It provides reliable and adaptable spraysealing binder options with superior performance and durability for various pavement treatments.
Velofalt: Innovative hybrid polymer modified binder designed for race tracks, offering exceptional performance. Its superior cohesion and adhesion properties provide an unparalleled grip for car tyres, ensuring enhanced safety and confidence for drivers during sharp turns, braking, and accelerating zones. Velofalt effectively prevents aggregate loss, maintaining track integrity. With excellent rutting and fatigue resistance, Velofalt is highly reliable under high-frequency loads, making it an ideal choice for demanding race track conditions.
SAMIfalt CRUMBflex: Innovative hybrid polymer-modified binder that prioritises sustainability in pavement construction. By incorporating crumb rubber from end-of-life tires, this binder reduces its carbon footprint by approximately 10 per cent, replacing the need for virgin bitumen. SAMIfalt CRUMBflex adheres to the engineering properties of conventional PMB binders and ensures equivalent performance. Carefully blended additives and polymers guarantee compatibility and excellent storage stability. This eco-friendly binder represents a significant step towards greener infrastructure development, utilising waste materials to create a more sustainable and resilient future for the pavement construction industry.