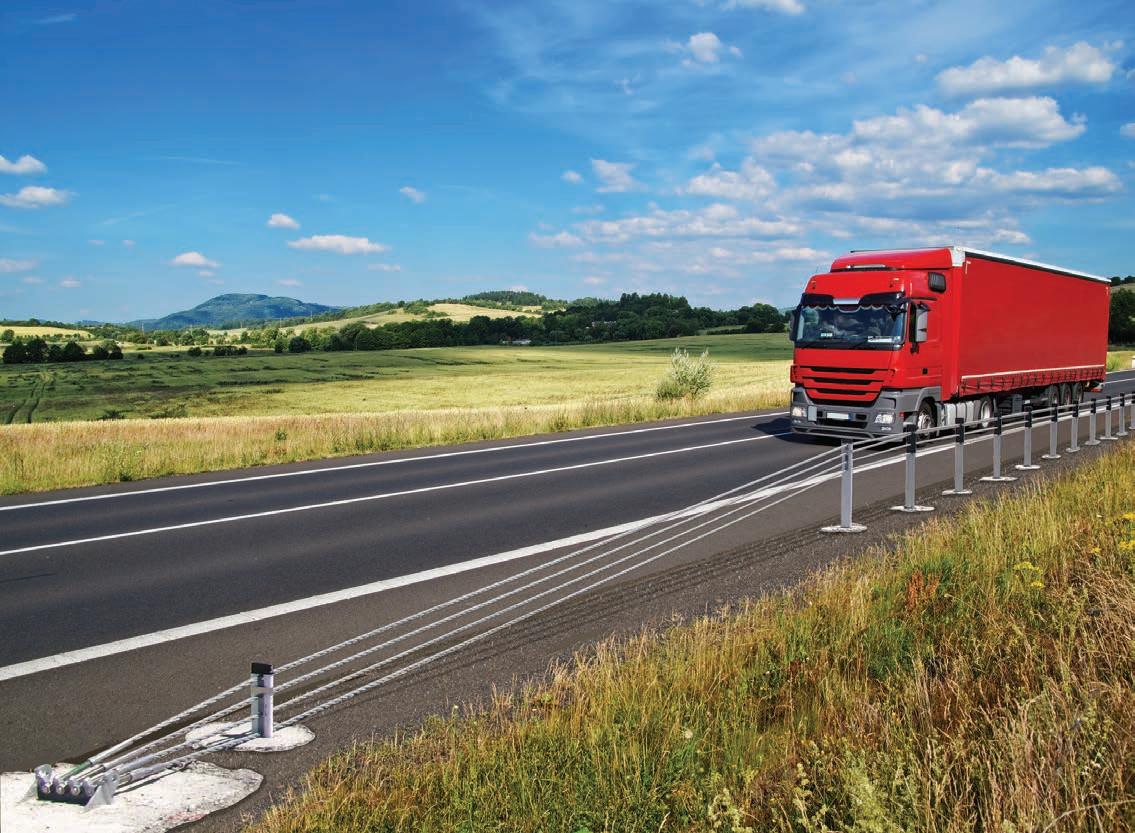
5 minute read
The evolution of safety systems
THE EVOLUTION OF
SAFETY SYSTEMS
WITH ALL STATES AND TERRITORIES NOW MANDATING MASH GUIDELINES FOR COMPLIANCE OF PERMANENT AND TEMPORARY SAFETY BARRIERS, ROADS & INFRASTRUCTURE LOOKS AT HOW THE INDUSTRY HAS ADAPTED TO THE CHANGES.
Ingal Civil’s re-designed MashFlex system is 30 to 40 per cent quicker to install than its predecessor.
Over the past few years, the eligibility criteria for product submissions to the Austroads Safety Barrier Assessment Panel (ASBAP) have been evolving.
In April 2018, ASBAP announced all new submissions were required to meet AASHTO’s Manual for Assessing Safety Hardware (MASH) guidelines, or an equivalent, in line with the Australian and New Zealand Standards 3845 Parts 1 and 2.
What followed was a gradual transition of the accepted road safety barrier systems and devices within the Australasian market.
The transition began with steel rail barriers and permanent concrete barriers on 31 December 2018, then terminals on 30 June 2019 and wire rope safety barriers and crash cushions on 31 December 2019.
The final set of products to make the change were barrier transitions, temporary barriers and Part 2 products.
As of January this year, road authorities across all states and territories had mandated the MASH compliance criteria for road safety barrier systems and devices.
Australian company Ingal Civil Products is one manufacturer that has been at the forefront of this transition with the evolution of its temporary and permanent road safety barrier products.
The company’s Ezy-Guard Smart System was the first MASH compliant system to be approved in Australia. This was soon followed with the release of other MASHcompliant permanent barrier systems, such as the Ezy-Guard 4 Guardrail Crash Barrier, the ET-SS MASH Guardrail End Terminal, QuadGuard M10 MASH Crash Cushions and Ingal’s motorcyclist protection equipment, all of which are now compliant with the MASH crash testing protocol.
Luke Gallagher, Product Manager at Ingal Civil Products, says the company has since expanded this transition to its temporary safety barrier systems with the introduction of the next generation of work zone crash cushions, the MASH TL3 ArmorBuffa.
Having successfully rolled out hundreds of kilometres of Flexfence wire rope safety barrier systems to the market for the past 25 years, Ingal Civil upgraded this product a few years ago and replaced it with a MASH complaint version called MashFlex.
The efforts to continually improve the product lines can be seen with the recent upgrade to MASH TL4.
THE DESIGN EVOLUTION MashFlex, as Gallagher explains, was developed to meet the new industry requirements, while also introducing design improvements that benefit installers and contractors. For this, feedback from Ingal Civil clients played a key part, he says.
“As our engineers looked at replacing the Flexfence wire rope with a MASH compliant product, they also aimed at simplifying the design to reduce installation and repair time,” he says.
“Ease of installation was a key attribute we wanted to achieve with MashFlex. Since the introduction of Flexfence nearly 25 years ago, some changes had been applied along the way to improve its performance. But as a result, the system now had too many components, which could hinder quick installation and repair.”
The result of this re-design philosophy is a wire rope system that can be installed in a much shorter time. Gallagher says installation in the field can be up to 30 to 40 per cent quicker with MashFlex.
“In this new design, we have consolidated seven or eight components into just three components. This has led to a product that exceeds the performance of the old one, but also improves installation efficiency.”
With hundreds of kilometres of Flexfence wire ropes already installed throughout the road network, Gallagher says minimising replacement costs was another decisive factor in the design.
“With MashFlex, we wanted to offer the opportunity for the road networks to upgrade their existing installed base of barriers to MASH, without having to completely demolish the existing infrastructure,” says Gallagher. “As such, the Mashflex system has been designed so that you can replace only a few components in your existing wire rope system – mainly the post and cap – and reuse the existing cables and concrete footings. This means network operators can now have a fully compliant barrier system for a fraction of the cost of installing an entirely new one.”
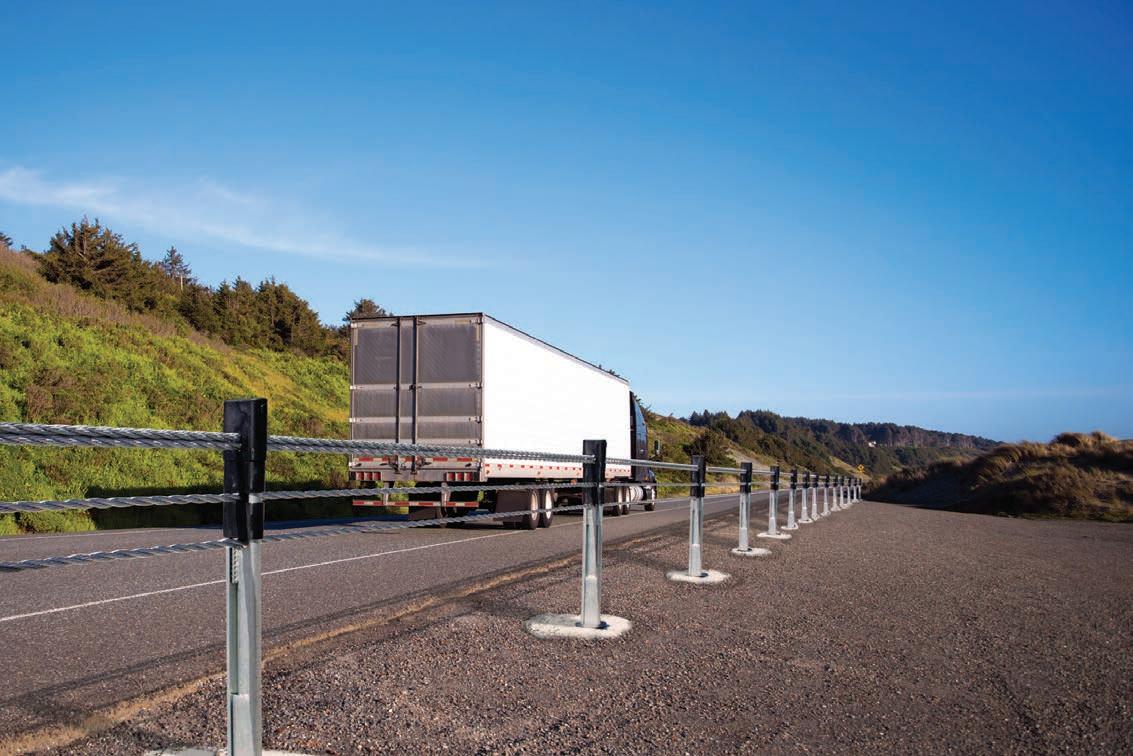
Ingal Civil’s MashFlex wire rope safety barrier system has been tested and approved to meet MASH TL4.
EXCEEDING REQUIREMENTS MashFlex was initially designed to meet the MASH TL3 requirement, so it was crash tested with a 2270-kilogram pick-up truck travelling at 100 kilometres per hour and impacting the barrier at an angle of 25 degrees.
Following a successful approval from ASBAP and roll out to market, this year Ingal Civil also crash tested MashFlex to MASH TL4, which involves running a 10-tonne truck into the barrier at a speed of 90 kilometres per hour, and at a 15-degree angle.
“When we introduced the MashFlex wire rope safety barrier a couple of years ago, it was compliant with MASH TL3,” says Gallagher. “We were confident that the barrier system could also meet the TL4 requirements, so we conducted the test without any further design upgrades, and the barrier easily withstood the higher impact load with very good deflection results.
The MashFlex TL4 product has already been approved by ASBAP and is being specified as the barrier of choice on multiple projects. AUSTRALIAN-MADE STEEL With full control over the manufacturing process at its Minto factory in New South Wales, Ingal Civil manufactures all of its barrier systems, from guardrails to wire rope barriers, using Australian-made steel sourced from BlueScope. For the plastic components, the company uses recycled plastic wherever possible, Gallagher says.
“From the beginning, it was very important for us to use recycled materials as much as possible. So not only are our steel products made with Australian steel, the plastic components are all recycled plastic. This is a key benefit for major projects where our clients need to account for the carbon footprint of their designs,” he says.
“Also, all of our steel products are galvanised to Australian standards to give them maximum durability in the field,” he adds.
The wire ropes were the last category of products Ingal Civil upgraded to MASH.
With it, Gallagher says the company now holds one of the widest – if not the widest – range of MASH compliant safety barriers in the market.
So what’s next for the company? Gallagher says continuing to work with the industry to improve designs and to help upgrade the legacy barrier systems already in place are top priorities for the team.
“We are keen to assist the road network operators to upgrade their legacy systems. Our designs offer the opportunity to do so with a minimal cost. Given how much faster the new MashFlex wire rope barrier systems can be installed, the motivation for upgrades is quite compelling.”