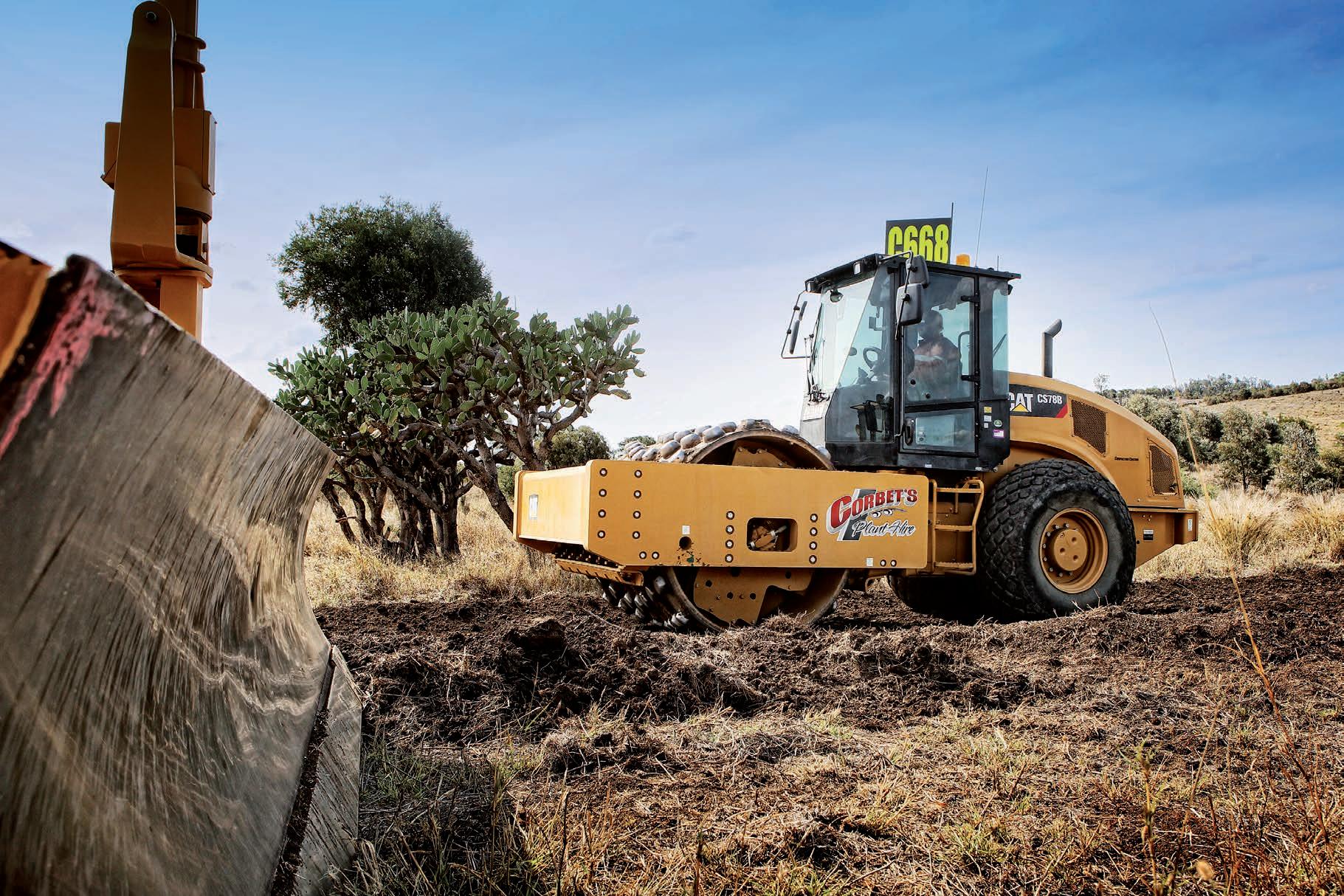
4 minute read
Intuitive machinery maintenance
WITH HASTINGS DEERING
HASTINGS DEERING’S HDADVANTAGE IS HELPING CUSTOMERS ANALYSE THE PERFORMANCE AND HEALTH OF THEIR CAT MACHINERY. ROADS & INFRASTRUCTURE LEARNS MORE FROM CORBET’S GROUP’S EXPERIENCE.
If one were to view Hastings Deering’s values, words such as ‘care, communication and commitment’ are emphasised again, and again.
As part of its commitment to support customers, long after a sale has been made, the Caterpillar machinery supplier now has 14 workshops across Queensland and the Northern Territory.
For the Hastings Deering service team, technology plays a role in delivering their support to customers, through the HDAdvantage service and maintenance program.
HDAdvantage is a management tool, enabling customers to monitor data, which gives an insight into the overall health and productivity of their Cat construction machinery.
As Ross Meyer, Hastings Deering’s Manager of Business Solutions explains, the HDAdvantage tool offers the “next step” in machine maintenance.
“HDAdvantage is a complimentary service program which combines Hastings Deering’s service capabilities with the Cat technology,” he says.
HDAdvantage provides access to machine data, such as working hours, daily fuel burn, service history and machine location. It can be accessed via both the Cat platforms –the Cat App and My.Cat. Com – and the Hastings Deering online portal, allowing operators to receive notifications for service reminders and critical machine faults.
In addition, customers will receive crucial alerts and preventive maintenance notifications recommending what needs to be done and, most importantly, putting them in contact with the Hastings Deering Service Support team to provide immediate solutions. It’s designed to reduce chances of unplanned downtime and helps to maintain the heath of the construction machine for customers.
CORBET’S GROUP’S EXPERIENCE Lee Wodetzki, Operations Manager of Corbet’s Group, has benefitted from the HDAdvantage. He says the program has
Corbet’s Group is using HDAdvantage as part of its works on the Bruce Highway program. HDAdvantage enables users to track daily fuel burn and view the service history and location of Cat machinery.

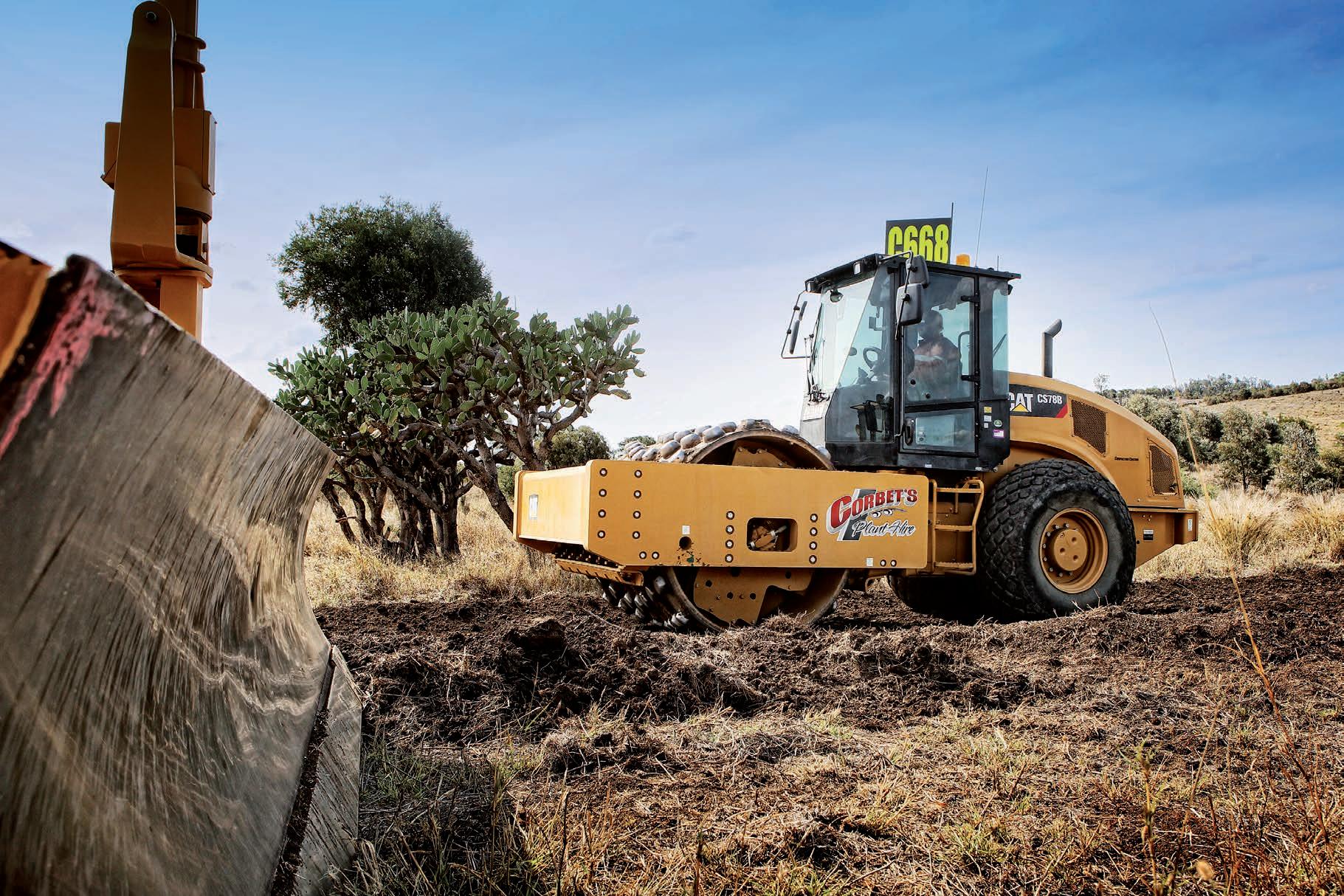
provided him a greater understanding of the machinery in their fleet.
“The system encompasses most of the aspects a business requires to manage equipment from an ownership perspective,” he says.
For over 40 years, the family-owned company has offered a range of services, including heavy plant and equipment hire from its base in Gympie, Queensland. This includes hire options for dozers, excavators, grinders, front end loaders, graders and rollers.
The company owns a fleet of around 1000 units, 100 of which are Cat machines.
Wodetzki says the HDAdvantage is actively used on each Cat model.
“The biggest benefit for us is being able to remotely track Service Meter Unit (SMU) hours and plant utilisation. Our maintenance department appreciates the remote access to fault codes and warranty information,” he says.
“The HDAdvantage program has been easy to use by all departments in our business.”
Wodetzki and his team have been actively using HDAdvantage as part of their works on the Cooroy to Curra section of the Bruce Highway Upgrade program in Queensland.
This project involves a 62-kilometre realignment and upgrade of the Bruce Highway to four lanes between Cooroy and Curra and is among Queensland’s highest priority road projects.
“All of our Cat gears on the Cooroy to Curra project are tracked with HDAdvantage. It’s really helped in reconciling hours against client generated reports,” Wodetzki says.
CUSTOMISING THE PLATFORM Being a user-friendly platform, Meyer says HDAdvantage offers flexibility for all users.
“We allow customers access to all machine and business information both in an App and online so operators can make the most of the program, by looking at performance trends and oil sampling results,” Meyer says.
“For those more traditional operators of machinery, they need not go online and instead are sent machine and service alerts via text or email. All they need to do is respond to these messages.”
Flexibility is also offered to cater for the size of each individual business.
“Some customers with one or two machines may just want general data, like service needs and to be notified when a fault code is critical. Those with a bigger fleet can identify trends across their fleet, including productivity or payload trends,” Meyer says.
“Customers can also pay an additional subscription fee, granting them access to additional information. As part of the subscription, they will be supported by Hastings Deering’s Condition Monitoring experts, who can help to identify issues and trends specific to their fleet, such as safety or reliability. Oil analysis is also available as part of the subscription.”
HDAdvantage is installed as standard on all new Cat certified used and Cat certified rebuild construction machines. It can also be retrofitted to older Cat machines.
The standard service is provided for up to 36 months from the date of purchase of the Cat machine. Customers are contacted prior to the expiry date, allowing them to renew the program if they desire.
“Not only does it provide data on where the machine is and its performance, it helps to identify ways in which machinery issues can be resolved,” Meyer says.
Customers can contact Hastings Deering’s field service teams, which are available 24/7, to rectify the issues HDAdvantage has identified.
“The platform is there to help customers when needed. It’s very simple to use and understand,” Meyer concludes.