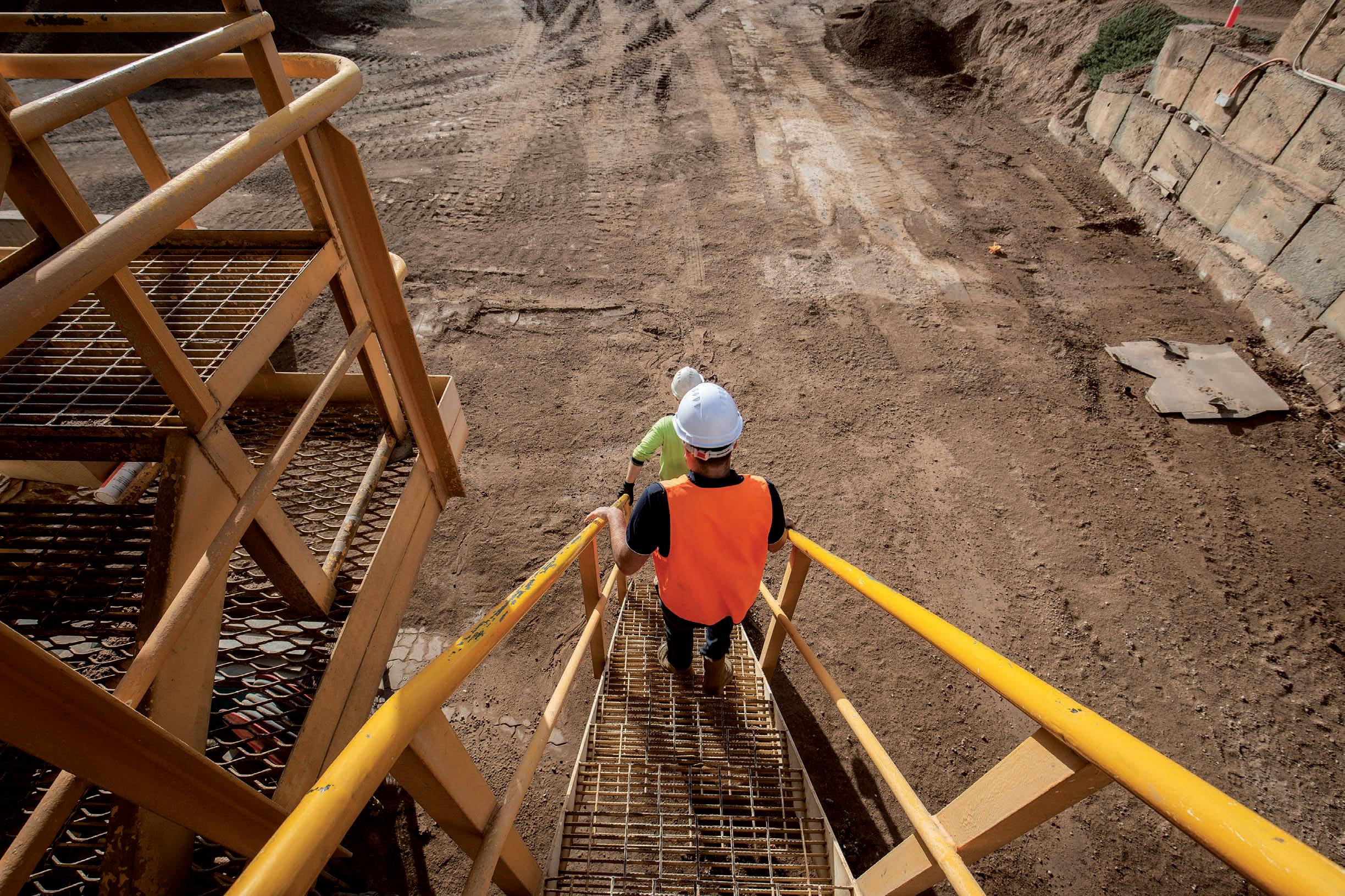
4 minute read
Setting a standard for health and safety
RESOURCECO IS IMPLEMENTING STRATEGIES TO MINIMISE RISKS AT EACH OF ITS SITES NATIONALLY. MAZEN ELFEKY, THE COMPANY’S NATIONAL MANAGER FOR HEALTH, SAFETY ENVIRONMENT AND QUALITY, IS LEADING THE CHARGE.
Preventing health risks for waste recycling business such as ResourceCo is no easy task.
With employees frequently exposed to hazards such as moving vehicles, working at heights, dust and noise, ResourceCo has taken steps to ensure its workers remain injury free.
As Mazen Elfeky, the company’s National Health, Safety, Environment and Quality Manager says, the goal is to create a safe working environment for all staff.
“We have a proactive approach to hazard management,” he says. “That is our philosophy and as a result, we are on a steady decline when it comes to the frequency of injuries at our sites.”
This approach has proven to be effective, with the number of Lost Time Injuries (LTIs) at ResourceCo decreasing by 90 per cent since 2004.
ResourceCo has multiple sites in Australia across recycling and waste management, tyre recycling, material solutions and energy. As a result, Elfeky says it is important to have a robust health and safety policy which could be applied across all areas of the ResourceCo business pillars.
Sanj de Silva, Director – Corporate Affairs and Sustainability at ResourceCo, says “We keep a keen eye on everything that’s happening at each of our sites. We want to make sure that our staff understand
Site investigations of operations and facilities are a part of health and safety checks at ResourceCo.
ResouceCo ensures that staff are aware of safety strategies when working close to moving machinery.
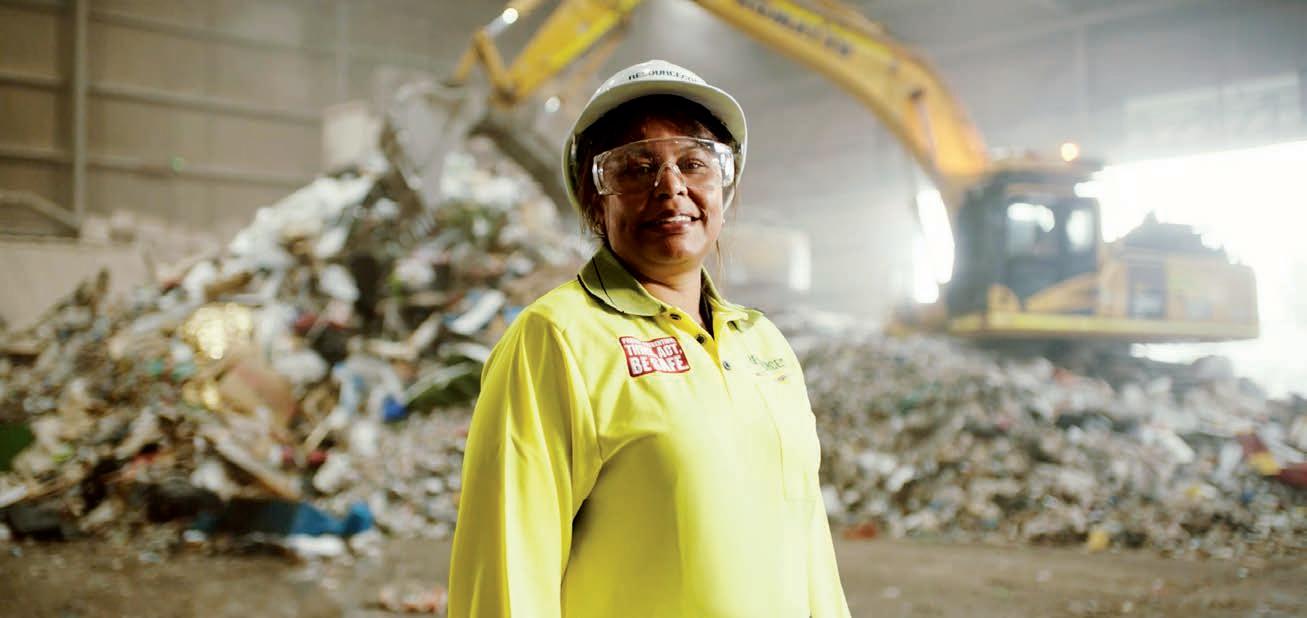
that it’s our priority to have safe working conditions at all times.”
This includes the company’s new purpose-build manufacturing plant in Erskine Park, New South Wales, which became Australia’s largest tyre recycling facility when it became operational in December last year.
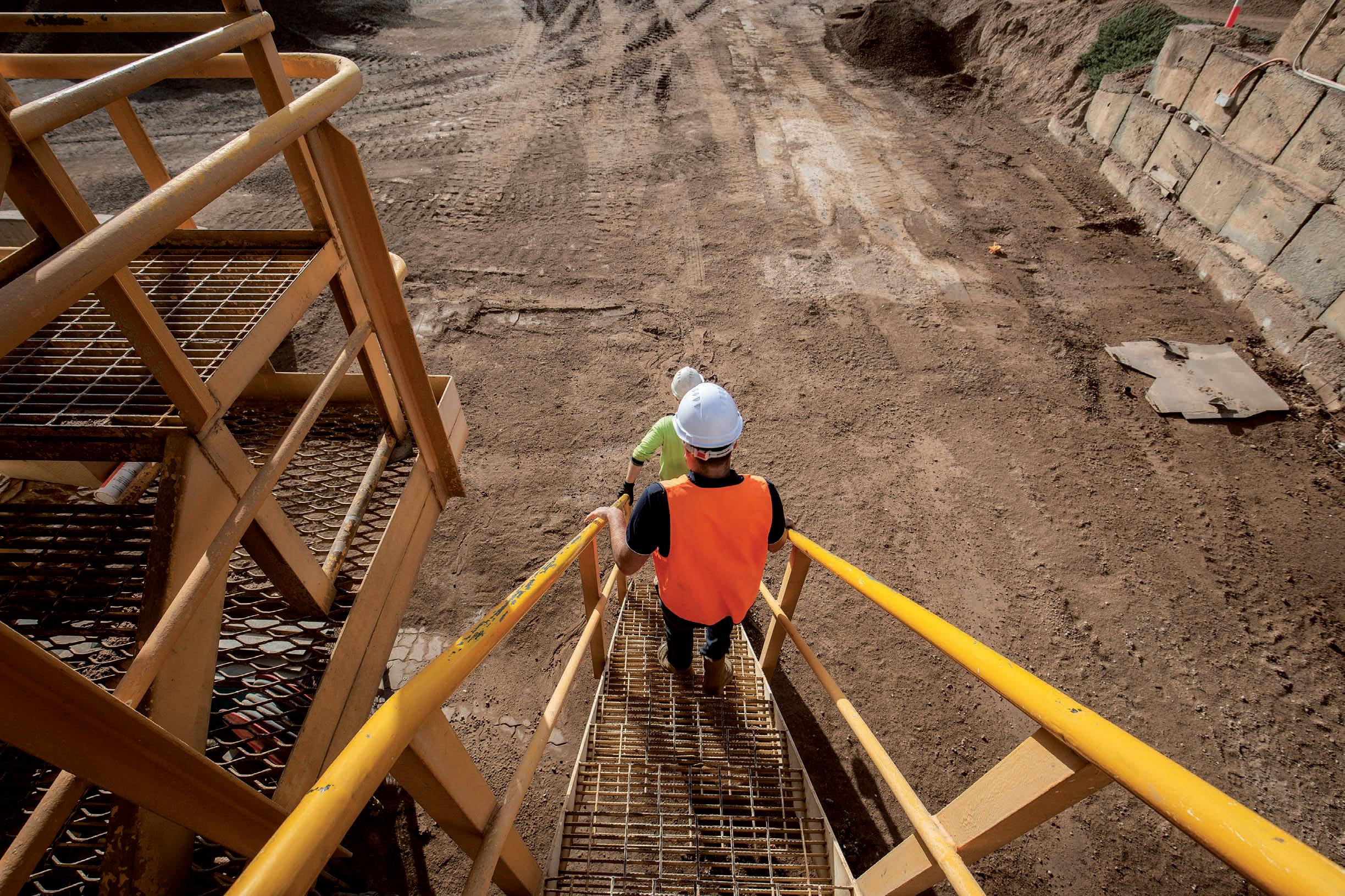
IMPLEMENTING STRATEGIES Although it is a national company, Elfeky says that the health and safety strategies ResourceCo has put in place can also be applied to start-up and small-scale businesses.
Communication is an aspect which he says is a simple, but effective tool.
“It is important for the whole [ResourceCo] group that we share the lessons we learn from each site. If something is working well, then it can be adopted to other sites as well,” he says.
“We have regular meetings with the management team, where strategies are often discussed.”
One such strategy which has been implemented is ‘take five’.
‘Take five’ is a small booklet, which encourages operators to evaluate the task at hand, to make sure they can complete it safely.
“Before carrying out any task, our staff need to take five minutes to make sure that appropriate control measures are put in place,” Elfeky says.
“If somebody is not satisfied with these measures before completing the task, if they identify a risk, or if they are not aware of the control measures, they have to stop and consult a supervisor.”
SAFETY INDUCTIONS The importance of health and safety is introduced early on for all employees, with operators participating in onboarding training courses for specific machinery which may be in high-risk environments.
Site Supervisors will take employees through the safety measures of machinery, as well as conduct tours of the facility to familiarise the operators with their surroundings.
“Our induction is very comprehensive. We also do refresher trainings. Some inductions require employees to complete this training annually,” Elfeky says.
“We use a program which sends out reminders to operators who are yet to complete the refresher course. For example, if they complete a course in January 2021, they will get a reminder in January 2022.”
SHARED PLANNING Annual audits of operations and facilities are a part of health and safety checks at ResourceCo. The company is now certified across the 45001:2018, ISO 14001 systems and ISO 9001 (occupational health and safety and quality standards).
Elfeky says planning plays a big part in this process.
“For the whole group, we recently implemented a ‘step change plan’, wherein we planned for a year and identified what the main risk exposure areas are in our worksites,” he says.
“We have a score card, where we record every month how many site visits have been completed. This ensures that everyone is being held accountable for health, safety and quality.”
Objectives also form part of the ‘step change plan’. This year, Elfeky is aiming to increase the quality of the hazard reports which are received from each site.
While safety has always been at the core of ResourceCo’s operations, de Silva says the work being completed by Elfeky and his team will shape the foundation of the business going forward.
“We are embedding a culture around safety and health. So, we are not just talking the talk, but also walking the walk,” she says.