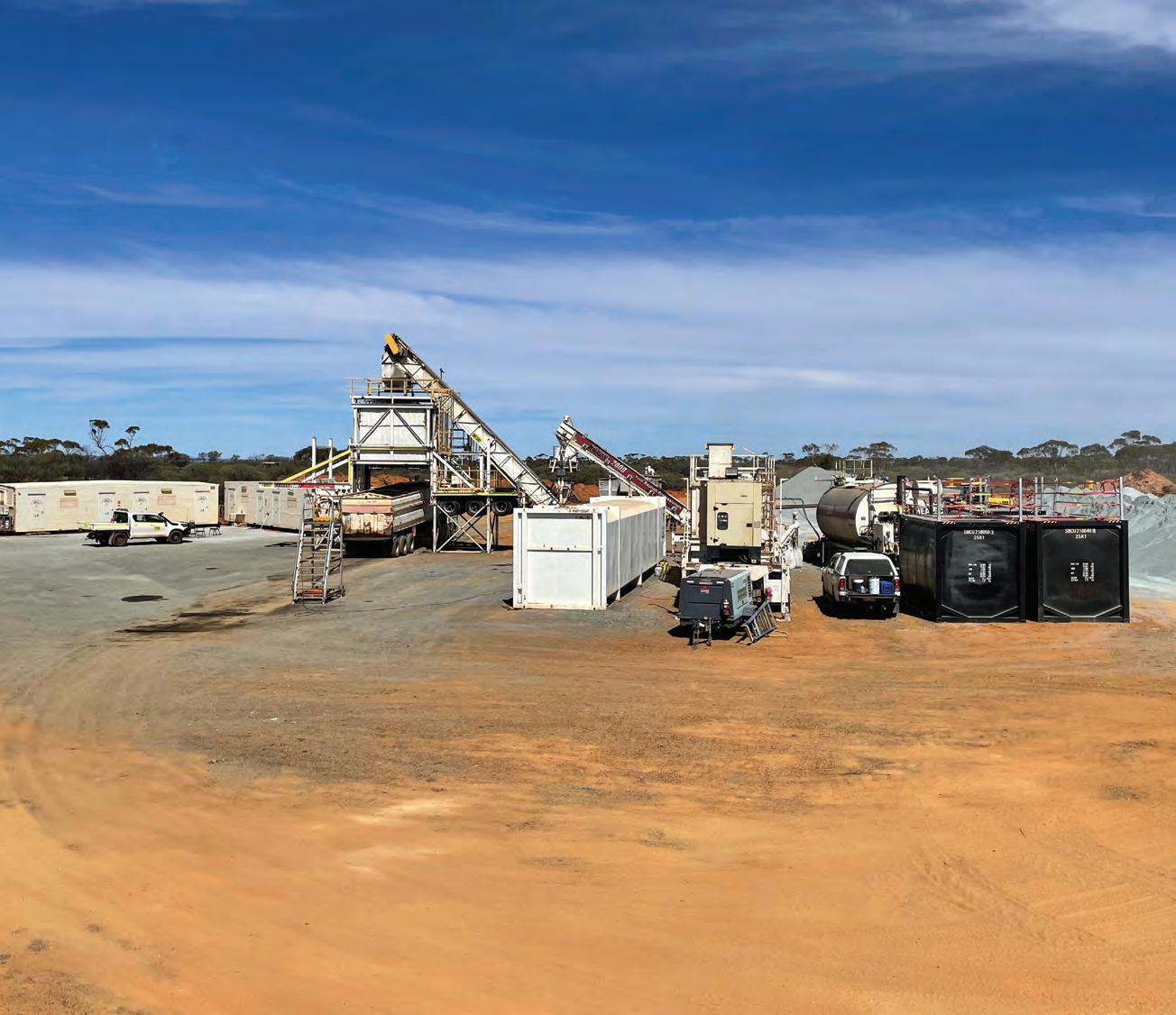
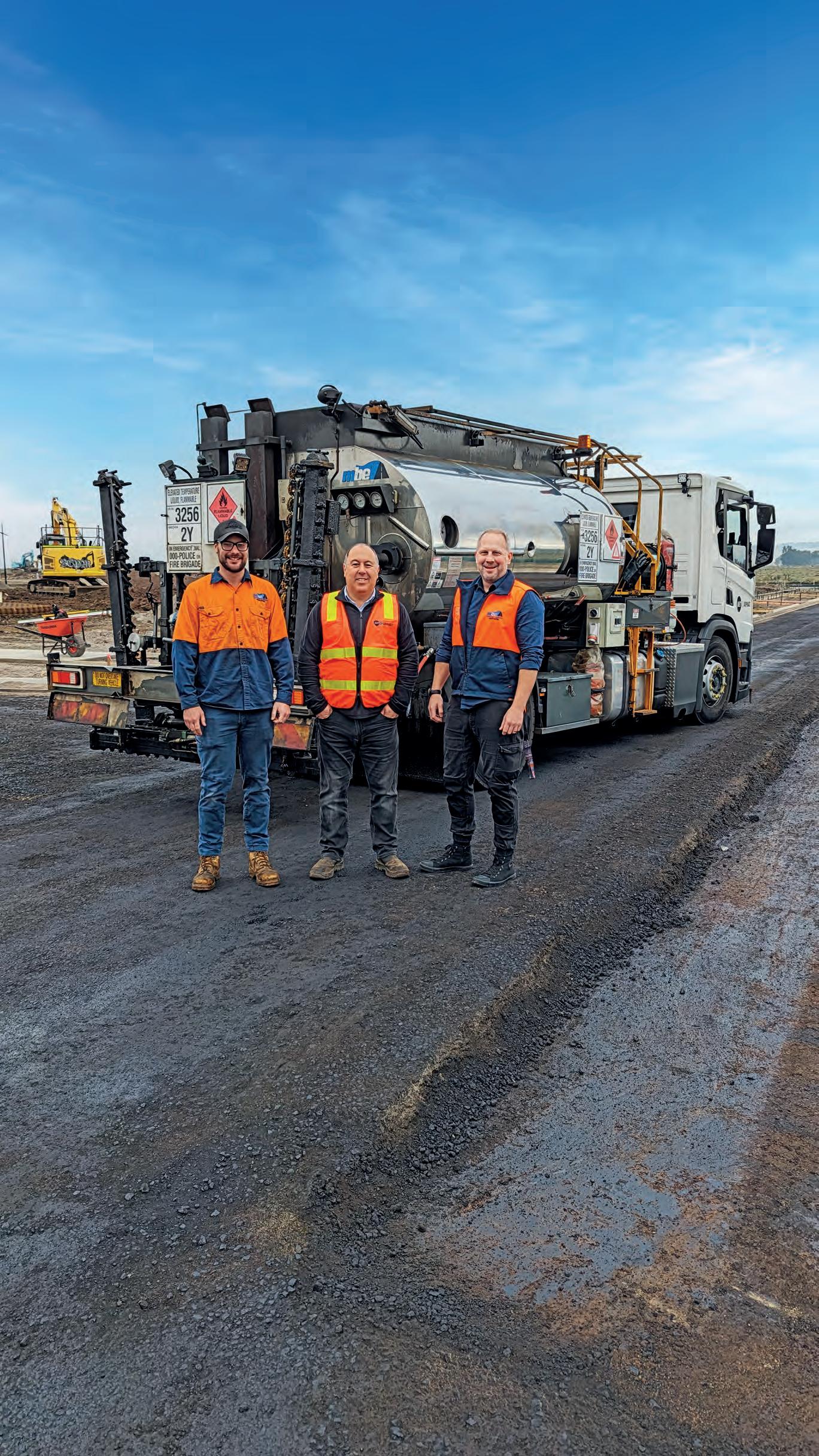
A collective passion for quality, growth and local business has connected two of the sectors key innovators
AN ENGINEERING BREAKTHROUGH
What’s the best way to revolutionise a legacy product?
AROUND THE WORLD OF ASPHALT
A peak inside the latest technologies, methods and equipment from the international ‘World of Asphalt’ event
Deadlines don’t stop for delays. And with the revolutionary Premium Circle on a John Deere Motor Grader, neither will you. This fully sealed system is more powerful and accurate while being lower maintenance, which means less downtime and more productivity. No need to compensate for wear in the circle or stop to adjust for looseness. It’s also available on any John Deere Motor Grader you choose. The grading game has moved forward. Don’t get left behind.
15 Paving in partnership
Matthews Brothers Engineering has become the trusted equipment supplier and partner of Metro Asphalt, thanks to a collective passion for quality, growth and local business. Roads & Infrastructure is taken behind the scenes.
19 An engineering breakthrough Geosynthetics have been a part of the construction sector for decades. So how do you revolutionise a legacy product? You combine the expertise of two companies that are among the leading innovators within the industry.
22 Quality, wherever you go VSA, Inroads and SAMI Bitumen Technologies together have helped to deliver an innovative solution, for a municipal based infrastructure
40 Astec and the World of Asphalt
Astec Industries’ recent presentation and participation in the World of Asphalt Conference, the largest event of its kind for the asphalt and aggregates sectors.
43 Innovation, reliability, and performance
As the construction industry continues to expand in the face of increasingly complex infrastructure projects, multinational companies are expanding their operations in Australia.
46 Taking action
The roads sector is stepping up to protect frontline workers from road trauma, urging drivers to take extra care, while also introducing an Australian first guideline for the betterment of the sector.
48 Greener roads
Australia’s largest council-led recycled rubber road project is paving the way for greater environmental and economic outcomes for road construction.
50 Compliance on show
When running a transport or logistics business, it’s essential that everyone and everything is up to code. The cutting edge of compliance and more will be on show at the anticipated MEGATRANS 2024.
53 The heady heights of keeping safe
Vertical access and working at height solutions are ongoing issues for many companies and industries, which will be highlighted at the upcoming BULK 2024 Expo.
56 The PNG Expo
The Papua New Guinea Industrial and Mining Resources Exhibition and Conference (PNG Expo) will be a top event for the industry in early July.
4 Editor’s letter
7 News
58 Contracts & Tenders
HOW DOES ONE CONTINUOUSLY INNOVATE? It’s the question that drives what is one of the oldest sectors and industries on earth.
Construction among humans can be traced back to 4000 BC. Obviously, things look different these days, with the technological revolution forever changing the way that the construction industry interacts within itself, as well as with surrounding sectors. We now have more tools than any previous point in civilisation, so how can we make the most of this gift to deliver the best possible infrastructure for the community? That’s what we set out to discover in the July edition of Roads & Infrastructure Magazine.
In our cover story, innovation and compassion are thrust into the limelight as we examine the close professional relationship between Metro Asphalt and specialised road making equipment manufacturer Matthews Brothers Engineering. Matthews Brothers Engineering has been a key supporter of Metro Asphalt for years and the partnership is flourishing, in part due to the machinery, but also due to Matthews Brothers Engineering’s support and maintenance services.
For Matthews Brothers Engineering, this is far from a closed chapter. The company approaches its support and servicing department as it would with any machine, looking at what works well, as well as what could be upgraded.
We also spotlight geosynthetics and how innovation is transforming what is a material that’s long been used for construction, creating even more possibilities for engineers and project managers. The team at Reinforced Earth is combining its knowledge with proven geosynthetic experts to create innovative drainage solutions, helping to aid the cost, time and materials related with infrastructure development. Materials transport is yet another innovative area that we highlight in this edition of Roads & Infrastructure Magazine , with SAMI Bitumen Technologies and TEC Container Solutions both exhibiting the capabilities to cater for all types of projects, regardless of scale or location.
This and much more is in the latest edition of the magazine.
Happy reading!
Tom O’Keane Roads & Infrastructure MagazineCOO
Christine Clancy
christine.clancy@primecreative.com.au
PUBLISHER
Sarah Baker sarah.baker@primecreative.com.au
MANAGING EDITOR
Mike Wheeler mike.wheeler@primecreative.com.au
EDITOR
Tom O’Keane tom.okeane@primecreative.com.au
JOURNALIST
Chris Edwards chris.edwards@primecreative.com.au
DESIGN PRODUCTION MANAGER
Michelle Weston michelle.weston@primecreative.com.au
ART DIRECTOR
Blake Storey
DESIGN
Bea Barthelson
BUSINESS DEVELOPMENT MANAGER
Brad Marshall brad.marshall@primecreative.com.au
CLIENT SUCCESS MANAGER
Salma Kennedy salma.kennedy@primecreative.com.au
HEAD OFFICE
Prime Creative Pty Ltd
379 Docklands Drive, Docklands VIC 3008 Australia p: +61 3 9690 8766 enquiries@primecreative.com.au www.roadsonline.com.au
SUBSCRIPTIONS
+61 3 9690 8766 subscriptions@primecreative.com.au
Roads & Infrastructure Australia is available by subscription from the publisher. The rights of refusal are reserved by the publisher.
All articles submitted for publication become the property of the publisher. The Editor reserves the right to adjust any article to conform with the magazine format.
COPYRIGHT
Roads & Infrastructure Australia is owned and published by Prime Creative Media. All material in Roads & Infrastructure Australia is copyright and no part may be reproduced or copied in any form or by any means (graphic, electronic or mechanical including information and retrieval systems) without the written permission of the publisher. The Editor welcomes contributions but reserves the right to accept or reject any material. While every effort has been made to ensure the accuracy of information, Prime Creative Media will not accept responsibility for errors or omissions or for any consequences arising from reliance on information published. The opinions expressed in Roads & Infrastructure Australia are not necessarily the opinions of, or endorsed by the publisher unless otherwise stated.
The city shaping commitment from the Federal Government will help to deliver transport links that will help the new city grow. Image: New South Wales Government.
The Federal Government has announced a $1.9 billion investment to support the delivery of future and on-going transport projects across Sydney’s west.
The new funding will provide a boost for one of the nation’s fastest growing regions. This will include $500 million for Mamre Road Stage Two. This is on top of the $253.6 million already allocated
Track improvements in Nagambie and Wahring have been delivered as part of the $400 million Stage Three Shepparton Line Upgrade project, in Northern Victoria.
Crews have replaced more than 13 kilometres of ageing wooden track with 15,000 new concrete sleepers, while adding more than 35,000 tonnes of new ballast along the line. Further improvements included rebuilding the track through four level crossings in Wahring, which followed previous upgrades made to a 26-kilometre section late last year.
Stage Three of the Shepparton Line Upgrade will enable faster and more frequent services. The third stage of the project will deliver signalling upgrades
by the State Government for the first stage of the project.
$500 million has also been committed for works at Richmond Road, Garfield Road and Memorial Avenue, while a $400 million investment will help to deliver priority sections of Elizabeth Drive upgrade. This funding builds on financial commitments already made by the
State Government.
A f urther $115 million has been commitment for Mulgoa Road Stage Two, $100 million to deliver new infrastructure to support bus services to the WSI airport and a $20 million investment to support the delivery of the final business case for the first stage of the Western Sydney Freight Line.
between Seymour and Shepparton to allow nine weekday return services; track upgrades between Seymour and Shepparton to allow trains to travel faster.
It will also deliver an expanded stabling for VLocity trains to support more services, as well as a further 1.1km extension of the Murchison East crossing loop to allow a 1200 metre freight train and two six-car VLocity trains to pass each other.
The Shepparton Line Upgrade has
time, upgraded stations at Mooroopna, Murchison East and Nagambie, and delivered extra services.
Acciona Rail and KBR are delivering Stage Three as part of an alliance with the Regional Rail Revival and V/Line.
Signalling design work is continuing to allow more trains to run on the line when the project is complete.
Central Queensland is set to benefit from the deliver of $500 million of upgrades to priority road corridors.
These projects will aim to improve critical road infrastructure for the state’s beef industry, with the network stretching across close to 218,000 kilometres, running east to west in central Queensland.
The State Government, in partnership with Federal Government, will work with seven local government mayors and key industry stakeholders on the identification of short, medium and long-term beef road priorities to inform a 10-year Central Queensland Beef Roads Investment Strategy.
Construction on these projects are expected to commence progressively from 2024-25. To kick start the initiative, an early works package is being developed with the Miles Government funding contribution, prioritising the a number of projects.
These include pave and seal sections along Clermont-Alpha Road in Mackay/ Whitsunday and Central West districts, as well as pave and seal and widening of floodway along Alpha-Tambo Road in the Central West district. Also pave
Queensland Department of Transport and Main Roads.
and seal works in sections of the Fitzroy Developmental Road between Bauhinia – Duaringa in the Fitzroy district and a pave and seal section along May Downs Road in the Mackay/ Whitsunday district.
TBMs Catherine and Marlene are halfway to St Marys as tunnelling continues on the Sydney Metro – Western Sydney Airport project.
Both TBMs (tunnel boring machines) have already helped to build 2.4 kilometres of tunnels. Tunnelling at an average speed of 120 metres a week, the TBMs are carving out the twin 4.3-kilometre tunnels to the new St Marys Metro Station site. They have removed 600,000 tonnes of spoil so far and have helped to install 17,820 precast concrete segments since being launched at the Orchard Hills Station site in July and August 2023. Both TBMs are expected to reach St Marys in mid-2024.
When the
The 23-kilometre new railway will link residential areas with job hubs including the new Aerotropolis, and connect travellers from the new airport to the rest of Sydney’s public transport system.
The Australian and NSW Governments have awarded all three major contracts
passengers
option directly to the new Western Sydney International Airport. Image: New South Wales Government.
for the Sydney Metro – Western Sydney Airport project. The tunnelling contract was awarded in December 2021 to CPB Contractors and Ghella Joint Venture to build the new twin metro rail tunnels.
In March 2022, the contract to deliver approximately 10.6 kilometres of elevated viaduct, earthworks for track formation, a rail bridge over the new M12 motorway, a rail bridge within the airport and associated works, was awarded to CPB Contractors and United Infrastructure Joint Venture.
In December 2022 the largest Public Private Partnership (PPP) contract in New South Wales was awarded to Parklife Metro. The consortium will deliver six new stations between St Marys and the new Aerotropolis, 12 new metro trains, core rail systems and the stabling and maintenance facility to be built at Orchard Hills.
Parklife Metro will also operate and maintain the Sydney Metro – Western Sydney Airport line for 15 years after it becomes operational.
A further two TBMs, Eileen and Peggy, are building the two 5.5-kilometre southern tunnels from Airport Business Park to the Aerotropolis.
The Queensland Government has committed an additional $432 million to support the delivery of the first stage of works on the Coomera Connector.
The Coomera Connector will provide a much-needed alternative to the M1 for local journeys and will alleviate M1 congestion by accommodating an estimated 60,000 daily trips. Stage one includes 16-kilometres, from Coomera to Nerang, and features additional
crossings at the Coomera and Nerang Rivers.
The corridor is wide enough for an ultimate six-lane motorway. The 16 kilometre Stage One route will be built to four lanes to meet medium-term traffic needs. Key major structures will be future-proofed to six lanes, to help minimise future construction impacts to adjacent residents and the travelling public.
The project will be delivered in three
construction packages. Stage One North: Shipper Drive, Coomera to Helensvale Road, Helensvale. Stage One Central: Helensvale Road, Helensvale to Smith Street Motorway, Molendinar and Stage One South: Smith Street Motorway, Molendinar to Nerang-Broadbeach Road, Nerang.
Stage One North of the project is well underway, with expected completion with community consultation ongoing for Stage One Central and tenders being assessed for the Stage One South package.
Stage One North will open progressively from late 2025. The additional $432 million brings the State’s total contribution on the project to $1.513 billion.
Due to the rising cost of labour and materials, as well as the industry supply and demand challenges for specialist construction equipment, a further $864 million is required to complete Stage One.
The Queensland Government has sought a $432 million matching contribution from the Australian Government which will be considered in the upcoming Federal Budget in May.
The Federal Government has begun the search for a chief commissioner and two commissioners to lead Infrastructure Australia (IA), the Commonwealth’s expert and independent infrastructure adviser.
This is part of the Government’s commitment to re-establishing IA as the pre-eminent adviser on nationally significant infrastructure planning and investment.
This was following an independent review conducted in 2022 by Ms Nicole Lockwood and Mr Mike Mrdak AO which recommended reforms to ensure IA can fully deliver on its responsibilities.
There will be a merit-based process to select the Commissioners to ensure they have the appropriate skills, qualifications, knowledge and experience to lead and deliver on Infrastructure Australia’s mandate.
The commissioners will be supported by an advisory council with experts from infrastructure, experts from related sectors
The refreshed IA will better support infrastructure investment objectives through improved evaluation of infrastructure proposals and through providing a more targeted infrastructure priority list.
Applicants will be assessed by an Australian Government selection panel against specific criteria. The decision to introduce three commissioners for IA will improve outcomes for Australians by strengthening the foundations for better decisions on significant infrastructure investment.
www.wirtgen-group.com/australia
The number one paving brand on the global market presents innovative “Dash 3” pavers and screeds for the Australian market. Equipped with state-of-the-art Cummins engines, these two power packs, that are also available with rubber tracks, are the perfect choice for any application in the Universal (2.5m) and Highway (3.0m) paver classes.
Thanks to the easy-to-understand ErgoPlus 3 operating system which is common across all VÖGELE products both paver and screed operators can handle all VÖGELE pavers simply and safely. In combination with advanced features, such as VÖGELE EcoPlus, AutoSet and PaveDock Assistant, these new additions to the world’s most extensive range of paving products are the stars of any road construction site.
It’s our competitive ethos of solving the unsolvable, finding a way, and just getting on with it, that helps us make things possible for ourselves, our partners, and our customers.
It’s this drive that has led to our new generation TIDD Pick and Carry Crane. See for yourself and talk to us today about the TIDD PC28-3G.
In a new major testing milestone for the Sydney Metro, all 45 metro trains have completed a least one 51-kilometre journey between Tallawong and Sydenham at operational speed.
Each train stopped at each station during the tests. These journeys aimed to confirm train and platform screen doors performed as designed. Passenger help points and information displays on the trains were also put through their paces.
The performance of each train is being monitored closely to ensure the trains, signalling and station systems are working together and functioning seamlessly along the Metro North West Line and the new City section.
This comes as services are set to begin on the Sydney Metro City & Southwest line later this year, providing direct, fast and reliable public transport services.
Preparations are now underway for the next
major phase of testing – trial running, which is expected to begin in the coming months. Trial running is the last stage of testing before the launch of the new metro line, where network operator Metro Trains Sydney will run a series of timetable running and operational tests.
Sydney Metro is Australia’s biggest public transport project. Building, operating and maintaining a network of four metro lines, 46 stations and 113 kilometres of new metro rail for the network.
The Victorian Government has unveiled new concept designs for the new Melton Station, west of Melbourne.
The new Melton Station will be built with four platforms to cater for one of the fastest-growing communities in Australia – paving the way for future improvements and increased capacity on the line.
The elevated station will become accessible from both sides of the rail line – with pedestrian walkways, cycling paths, pick-up and drop-off zones, and lifts and stairs to each platform.
The new station will provide better connections for cyclists, trains, buses and car parking with a new multi-bay bus
interchange also included in the designs.
Community feedback, alongside technical requirements, have shaped the early concept designs for the new Melton Station precinct and the level crossing removals.
The Melton level crossing removal works will also pave the way for the introduction of larger nine-car VLocity trains as part of the $650 million Melton Line Upgrade, increasing capacity for passengers by 50 per cent.
New rail bridges will also take trains over Coburns and Exford roads and new road bridges will be built over Ferris Road, and Hopkins Road in Truganina, making Melton boom gate free in 2026 – two years ahead of schedule, as part of separate and additional works.
Designs for the level crossing removals at Ferris Road in Melton and Hopkins Road in Truganina will be released in the coming months, with consultation to follow.
Key scope elements have been confirmed for the $390 million Mount Ousley interchange, with detailed design works now progressing on the project in New South Wales.
The new interchange will improve the efficiency and safety of freight movements by introducing a heavy vehicle only bypass lane for southbound travel separating cars and trucks, as well as two new heavy vehicle safety ramps.
Refinements have been made to the scope and the design of the interchange to ensure it will improve safety and access to and
from Wollongong, support freight growth and improve traffic flow whilst delivering value for money.
Changes to these designs include traffic lights instead of a roundabout on the eastern side of the interchange to improve efficiency for traffic. The pedestrian bridge over Mount Ousley Road has also been removed from the design. Instead, Transport for NSW will deliver other improvements to cycle and pedestrian connections along and across Mount Ousley Road.
A detailed design will be shared with the public in the coming months, with major
works on track to begin at the end of this year.
Early work for the interchange project is well under way with survey, vegetation removal, pavement and geotechnical investigations being carried out to inform the project’s detailed design.
In January, Fulton Hogan were awarded the major works contract for the project, which is expected to be completed in 2028.
The $390 million project is jointly funded, with the Federal Government committing $240 million and the NSW Government $150 million.
Manufacturing has begun on 23 new VLocity trains that will be rolled out across Melbourne’s west.
The extra trains, when added to the existing fleet, will increase the number of VLocity trains to 141 in the state. These trains will service the Melton Line, as well as the regions of Geelong and Bacchus Marsh.
The VLocity trains are more accessible, produce less carbon emissions and are more reliable than V/Line’s older classic fleet. Each VLocity also has six spaces in each three-carriage set for wheelchair or mobility scooter users, and a dedicated storage area for bicycles.
The State Government invested $601 million in the Victorian Budget 23/24 to build 23 new VLocity trains –supporting around 500 local jobs – as
well as a $219 million investment for almost 200 additional weekend V/Line train services.
The trains are being constructed at The Alstom factory in Dandenong South, South-East of Melbourne.
MATTHEWS BROTHERS ENGINEERING HAS BECOME THE TRUSTED EQUIPMENT SUPPLIER AND PARTNER OF METRO ASPHALT, THANKS TO A COLLECTIVE PASSION FOR QUALITY, GROWTH AND LOCAL BUSINESS. ROADS & INFRASTRUCTURE IS TAKEN BEHIND THE SCENES.
With services including but not limited to asphalt spraying, civil construction, bulk earthworks, road reconstruction, concrete and asphalt paving and more, Metro Asphalt could be described as a Swiss army knife of Victoria’s asphalt industry.
Operating throughout Melbourne, a big part of Metro Asphalt’s adaptability is the versatility of its crews, and importantly, its machinery. Quality and achieving the best possible outcome for its clients rank high in the company’s list of objectives.
Identifying the opportunity for the company to increase its capacity and reach within the sector, Elvis Centofanti, Contracts Manager –Metro Asphalt & Cole Civil, set out to acquire an additional spraying unit at the turn of the decade.
This marked the beginning of the professional relationship between Metro Asphalt and specialised road making
equipment manufacturer Matthews Brothers Engineering.
“We were looking at expanding our business and capabilities within the industry. We were aware of the Matthews Brothers Engineering product, which had a very good reputation in the marketplace,” he says.
“A big thing for us was being able to deal with a local supplier, whether it be for spare parts or repairs and maintenance, having a local service was – and still is – important to us. On a couple of bases, they ticked all of the boxes.”
Matthews Brothers Engineering have been manufacturing specialised bitumen handling equipment since the 1970s, designing and producing such machines in-house, built for Australian conditions and applications.
Since the delivery of the first machine in 2020, Matthews Brothers Engineering has been a key supporter of Metro Asphalt, with
the first new unit being delivered during the COVID-19 pandemic in 2020.
Despite challenges such as the pandemic itself, financial pressures from the market, as well as a transition within the Matthews Brothers Engineering business, the relationship has flourished. Centofanti believes this is due to an un-dying commitment from the company catering to its customers’ needs.
“When I initially met with Paul Matthews (Managing Director), he immediately understood who we were, what we did and what our vision was for the future. He was very accommodating with his time and knowledge,” he says.
“He was instrumental in advising us in the early days and what options Matthews Brothers Engineering had. He was very pivotal in terms of getting us off the ground, in a fashion that we could build upon going forward.”
This also marked the first official handover
between Matthews Brothers Engineering and Metro Asphalt, which came with a complementary training session.
“I asked him if he could help out with some training and he obliged, spending about half a day with us, getting myself and the team up to speed. That experience was invaluable,” he says.
Richard Bailey, General Manager and Design Manager – Matthews Brothers Engineering, has been a leading force in placing a greater emphasis on the company’s servicing and support. Matthews Brothers Engineering approaches its support and servicing department as it would with any machine, looking at what works well, as well as what could be upgraded.
“The on site handover in 2022 would’ve been a completely different beast to what we’re doing now. Originally it was about getting them in the cab, showing them the sprayer, some of the buttons and then sending them on their way,” he says.
“Now we’ve tried to make that handover training a lot more inclusive. We fill up the spray tank with water and actually take the customer out on spray runs. We let their operators jump into the driving seat and have a go rather than simply pointing out the controls and explaining what they do. It’s a great opportunity to give them hands on experience within a controlled environment, where they can experiment and really get to know the machine.”
Centofanti says that from a customer’s perspective, this culture and support can be
“That knowledge and IP has been transferred more than adequately across their team. They’re exceptional across the board. Their turnaround for repairs and maintenance in particular has been great,” he says.
“The transition has been seamless from my end. The service hasn’t changed; what we got from Paul, we’re still getting now. It was great working with Paul and great working with their team because I feel as though we speak the same language.”
One figure that has been instrumental in this ethos across the company is Service and Maintenance Coordinator – Jake Hally, who works directly with clients on areas concerning support and repairs.
Centofanti says his dealings with Hally and the rest of the support team has been an easy and streamlined process.
“Jake’s very good to deal with, not only on a technical level, but also in the way that he communicates. He’s very clear and keeps us abreast of what’s going on. He’s a pleasure to deal with,” he says.
“It’s one thing to have the knowledge, it’s another to be able to communicate that effectively. In those areas he’s exceptional.”
Hally is relatively new in the role, but not new to the Matthews Brothers Engineering business. He’s worked on just about everything that comes out of the company’s workshop for six years, primarily as a fitter.
He says the creation of his role represents a renewed effort from the company to have an efficient and easy to use support service.
“It felt like a fairly natural transition, moving from working on the floor to then learning about the backend of the sprayers as well,” he says. “Also, how specific clients like to use our machines.
“It’s about developing a good rapport. Metro Asphalt are looking to get larger and grow and we’ve been lucky enough to be able to work
with them on that goal and help them work towards it.”
“A lot of operators are very familiar with their products, which is a huge bonus,” he says.
sprayer as well,” he says.
Bailey says Hally has hit the ground running, exemplifying the company’s commitment to assisting clients wherever and whenever possible.
“He’s taken the opportunity with both hands. He’s very involved with all stages of the process, which our clients really appreciate. He’s obviously got the background knowledge, he understands the products and he’s interested in learning and developing,” he says.
“Not only developing his role, but also the support services that we can provide. He recognises the importance of having good relationships with customers, which is ultimately critical to the role.”
Another component of this service is the ability to provide spare parts on a local basis, which are manufactured locally. A massive tick for Centofanti and the Metro Asphalt team.
“If we need spare parts, we’re hardly 30 minutes down the road and parts are generally always available. Whether it’s gaskets, spray nozzles, it’s all just a hop, skip and a jump away,” he says.
THE MATTHEWS MACHINERY DIFFERENCE
Metro Asphalt currently has two units from Matthews Brothers Engineering. The highlight among its fleet is the patented 6K Ozibar Sprayer.
It’s in this machine that you can feel Matthews Brothers Engineering’s halfa-century worth of experience, as Centofanti explains.
“The crew that we have at the moment are all very familiar with it and the system that they’ve developed, which allows you to dial in your application rates. It’s very user-friendly.
“We’ve found that those factors make it really easy to train up newer operators to the business. It obviously also gives you the benefits of a very accurate application. Particularly through the G-TAR.”
Matthews Brothers Engineering’s G-TAR, or Guaranteed Target Application Rate, provides two benefits. First, it aims to provide a guarantee to the application rate for the operator. Second, it aims to simplify the process for operators by removing the need for traditional road speed charts and a manual set up.
The sprayer operator can select the number and type of jet to be used, then set the desired application rate.
“It’s a very easy to use and very well incorporated system that helps us on multiple fronts,” Centofanti says.
Customisation is another aspect that has impressed Centofanti. Multiple options enable the operator to tailor a solution that works best for them, with Matthews Brothers Engineering helping to guide and recommend options where needed.
“When I was looking at the first sprayer, they had a whole menu of options, which was really impressive. We took up a lot of those extra options on our first model, we’ll be goingback to that same design for our new
Metro Asphalt is currently working with Matthews Brothers Engineering to fine-tune the new model, which isn’t the only new development in the works at the company. It will also soon be opening a new facility in Campbellfield, which will house all of its staff and fleet of new and old machines.
“That new unit will be a big help in boosting our productivity and expanding our reach and ability to do more in the marketplace,” Centofanti says. “The great thing is that it’s going to be a very easy transition because we know the product so well. We’ll be hitting the ground running from day one.”
From a Matthews Brothers Engineering perspective, much like Metro Asphalt, one of the main focuses will be growth, not only of its machinery and technological offerings, but also its now established support services. As Bailey explains.
“We want to expand not only the services we offer, but also our product range, to allow us to provide even more value to our customers. It’s about us working with customers such as Elvis from Metro Asphalt, to develop an even deeper understanding of their operations and how they use the equipment on site, to identify any areas where we may be able to support them even further,” he says.
“Engineering is in our name. If there’s a need within your operations, then between our design department and the wider hands-on team, we’ve got the expertise to deliver and make our customers ‘wants’ a reality.”
GEOSYNTHETICS HAVE BEEN A PART OF THE CONSTRUCTION SECTOR FOR DECADES. SO HOW DO YOU REVOLUTIONISE A LEGACY PRODUCT? YOU COMBINE THE EXPERTISE OF TWO COMPANIES THAT ARE AMONG THE LEADING INNOVATORS WITHIN THE INDUSTRY.
The first reported use of textiles in road construction can be traced back to the 1920s in the United States (Gateway Structure SDN BHD). One hundred years later, the world of geosynthetics is a far cry from these initial experimentations and applications.
Geosynthetics still plays a key role in the delivery of construction and infrastructure projects.
The Reinforced Earth Company has recently partnered with AFITEX-Texel Geosynthetics here in Australia to innovate the geosynthetics space.
Pascal Saunier, Business Development Manager North America & Pacific – AFITEXTexel Geosynthetics, says while geosynthetics isn’t brand new to the construction and infrastructure sectors, there’s plenty of chances to innovate and expand, and the company’s collaboration with Reinforced Earth in Australia aims to deliver cutting-edge drainage geosynthetics.
“Geosynthetics have been used in the construction industry for many years. They offer many advantages, with one of the biggest being the reduction in the consumption of gravel, creating a better environmental outcome,” he says.
“The more people use aggregates, the more expensive and rarer they become. They can have a poor environmental impact particularly when they’re being carted across long distances.”
AFITEX-Texel’s collaboration with Reinforced Earth aims to further develop drainage solutions in this space, combining a unique and specialised knowledge around geosynthetics with experts in soil structure interaction to retain, cross, protect and strengthen.
On top of its structure design, protection systems, and retaining structure services, Reinforced Earth also has a foothold in the geosynthetics field, particularly in designing and supplying materials for geosynthetic
soil reinforcement in applications like basal reinforcement and slope stabilisation.
These services have helped to provide solutions for industries and works such as roads, railways, mining, energy, military and more.
Saunier says the relationship between the two companies has led to exciting work, pushing the envelope when it comes to geosynthetic production and uses in Australia.
“The work that I’m doing in Australia is dedicated to drainage. Reinforced Earth are already well known for their work across a number of different types of geosynthetics applications, especially involving reinforcement,” he says.
“They have great solutions and a wellestablished name in the industry. They’re super professional and it’s really a pleasure to work with them, helping to add to their drainage solutions to find one that will fit perfectly with their technology.
“They’re a very well developed and highly technical company with a great track record. We’re very happy to be considered as a supplier of such a solution for them.”
One example of Reinforced Earth’s strong experience in the geosynthetics market is its ArmaLynk product, which incorporates high tensile geosynthetic strips, amongst other components to produce a geogrid for use in ground stabilisation needs to support the construction of roads, bridges, railways and heavy-duty pavements.
Another example of Reinforced Earth’s variety of options when it comes to geosynthetic materials is its new DrainTube technology, which it is rolling out with Saunier’s AFITEX-Texel. DrainTube is a conductive drainage geocomposite consisting of a conductive grid made of Stainless-Steel cables placed inside a DrainTube product.
This product aims to provide mechanical protection, filtration, drainage and leak detection.
Multiple solutions such as these are available in customised lengths and stiffness, depending on the requirements of the design.
Somnath Biswas, Zone Manager, Asia – Reinforced Earth, has been involved developing and manufacturing geosynthetic applications since the early 1990s, and leads the manufacture and supply of the company’s ArmaLynk products. He’s seen the engineering world embrace what he says has been a “breakthrough” product for the sector.
“The use of geosynthetics in infrastructure projects is becoming more popular due to installation efficiency, cost competitiveness
over conventional solutions whilst ensuring mid-to long-term performance,” Biswas says.
“The solutions must be well designed and engineered for the project. Geosynthetics have been used over several decades and whilst one section of these products has been commoditised, applications with products like our new DrainTube offering are highly customised with an engineered solution package.
“It’s an exciting time and I’m excited more and more about the development of customised products to suit specialised applications.”
reinforcement brand with several versatility of product characteristics. These include low modulus, ultra-high strengths, composites with drainage and separation, filtration capabilities and special grades with high frictional resistance for marginal fills,” Biswas says.
DrainTube, meanwhile, is just one example of a new spin on geosynthetic products, helping to provide engineers with more options for any given infrastructure project.
Fluid control is critical for civil engineering applications. DrainTube is especially suited to mining and construction related drainage, with both sectors requiring customised solutions
“IT’S A HIGH-PERFORMANCE, HIGH-STRENGTH REINFORCEMENT GEOSYNTHETIC. THE PRODUCT IS MADE FROM BOTH HIGH TENACITY POLYESTER (PET) AND PVA YARNS AND IS MAINLY USED FOR BASAL REINFORCEMENT APPLICATIONS.”
Biswas says ArmaLynk satisfies this criterion.
“It’s a high-performance, high-strength reinforcement geosynthetic. The product is made from both high tenacity polyester (PET) and PVA yarns and is mainly used for basal reinforcement applications,” Biswas says.
“These applications include embankments on soft and very soft foundations, piled embankments or load transfer platforms, bridging over voids and subsidence, as well as piggy-backing landfills. ArmaLynk can also be used for construction of reinforced steep slopes.”
The ArmaLynk product is now available in Australia. It has already been used for embankment reinforcement applications in Europe and Asia. Bi-axial ArmaLynk has also recently been used to stabilise load platforms in Malaysia.
These works exemplified benefits over the use of conventional materials and methods.
“ArmaLynk is a global high-performance
specifically adapted to dynamic situations. It’s here that DrainTube is key, Saunier says.
“It will help engineers to design with a higher capacity drainage solution, that’s able to handle high loads, which isn’t the case with too many products in Australia at the moment,” Saunier says.
With infrastructure only set to grow, along with an increased reliance on materials, geosynthetics look set to become a primary option for many project managers and engineers. Biswas says Reinforced Earth is well and truly up to the task.
“Engineers all over the world consider geosynthetics as a major break-through construction material for civil and environmental applications,” he says.
“I expect more demanding projects requiring highly engineered and customised solutions to appear in the future across civil infrastructure, environmental and mining projects in Australia.”
VSA,
SAMI
INROADS
AND
BITUMEN TECHNOLOGIES HAVE HELPED TO DELIVER AN INNOVATIVE SOLUTION, FOR A MUNICIPALBASED INFRASTRUCTURE PROJECT, WHICH IS SET TO BENEFIT THE LOCAL COMMUNITY.
Kangaroo Island is one of Australia’s natural wonders. Located just off the mainland of South Australia, over a third of the island encompasses nature reserves, home to iconic wildlife like koalas as well as local penguin colonies.
The island’s isolation, while part of the region’s wonder, can also present challenges, especially for transport and transit. Particularly for a construction project, which already has multiple moving parts to consider.
When the local Kangaroo Island Council required spray sealing works for its local network, aggregates, emulsions and bitumen provider VSA Roads Group jumped at the proposition.
When tendering for the project late last year, the Group came across a unique logistical concern; what would be the best way to transport the necessary materials with limited vessels going between mainland South Australia and the Island itself?
Luckily, all contractors involved share a key connection. Inroads forms part of the VSA Roads Group, an amalgamation of five different brands.
SAMI Bitumen Technologies, being one of the leading suppliers of bituminous products in Australia, has considerable logistical capabilities in the bitumen industry, including specialised tanker and container services.
As Tim Pickert, Business Manager –
Inroads explains, having already used their bituminous products, utilising SAMI’s container service felt like a natural progression.
“We thought this would be a perfect chance to use their bitumen containers, rather than getting tankers shipped across on the ferry, it just made sense for use to go to SAMI to get their help,” he says.
“I believe there’s only two or three dangerous goods ships per week that go across, so it would’ve been a logistical nightmare to compete with conventional tankers. All we had to do was work with them around the logistics such as dates and the quantity, which was around 80,000 litres.”
Inroads and VSA Roads’ experience in providing spray sealing services, combined with the material production and expertise
The location and geography presented multiple challenges for spray sealing works, which were solved through the communication and innovation of Inroads, the VSA Roads Group and SAMI Bitumen Technologies.
cost-effective choice for the customer, which was to use bitumen containers for product delivery,” he says.
“The bitumen was transported from SAMI Laverton plant, at temperatures
We were looking at nearly less than a week, just before the school holidays. Our main goal was to make sure that the product was available on quality and on time,” Berard says. “We had everything
each project on an individual basis, rather than providing a blanket solution. This applies to projects both large and small. SAMI has several different solutions for transporting and supplying the products.
Island with shipping limitations, supply the containers filled with product and product heating services at the site,” Berard says.
Pickert says all associated parties have received positive feedback from the local council and believes the experience of each company played a part in the finished product.
“They were really happy with it, and everything went smoothly. We use SAMI Bitumen and field blend our crumb rubber everywhere across all of our jobs, so our crews are really great and productive with it,” he says.
“In using field blended crumb rubber, we managed to save the equivalent of 3200 passenger tyres going to land fill.
“If we had gone with truck tankers instead of the containerised approach, who knows what would’ve happened. They were by far the best option for us to use. They worked really well.”
Berard says he’s not only pleased with the client’s response, but also with the coordination, efficiency and quality provided by SAMI and Inroads.
“I’m proud when we can give our clients a comprehensive turnkey solution on product manufacture and delivery,” he says. “We are confident that we can deliver products to remote and urban locations.
“Although there are always new challenges coming up, we will ensure for all clients that we can cover all t heir needs.”
TEC CONTAINER SOLUTIONS’ ALL-IN-ONE STORAGE SYSTEM HAS EMERGED AS A PREFERRED METHOD OF BITUMEN STORAGE FOR MANY MAJOR INFRASTRUCTURE PROVIDERS ACROSS THE COUNTRY.
and storage.
For as essential of a component as it is, bitumen has previously been logistically challenging, with transport being just one aspect. Having a product that’s ready to go and in the right window is another.
single skinned bitumen/asphalt containers, while also delivering a solution that doesn’t require heat maintenance.
This was no easy feat, with years of development and research committed to provide a unit that could benefit the
with major construction companies such as Colas, Downer, Fulton Hogan etc., who have been proud users of TEC’s solutions over the years.
TEC’s newest addition to the Bitutainer™ Storage range – the MEST Bitutainer™ – is the
culmination of years of experience designing tanks, as well as thousands of hours’ worth of engineering and industry expertise.
The MEST Bitutainer™ is a 40ft self-contained bitumen storage container that simplifies the handling, storage, and transportation of bitumen. The unit has been tailored to improve the efficiency and safety of bitumen transport and storage, particularly for speciality bitumen’s, such as emulsions, PMB’s and crumb rubber.
Able to fill, discharge and recirculate product via the built-in pipework manifold system, the MEST Bitutainer’s™ advanced control system is equipped with state-ofthe-art monitoring and control technology to ensure safe optimal operation conditions are maintained.
Such technology is crucial to satisfy compliance with the rigorous AS Standards of both Australia and New Zealand.
The addition of a bottom mounted agitation system is ideally suited for use with crumb rubber, ensuring that rubber particles remain evenly distributed to maintain the optimal properties of modified bitumen.
TEC’s design also ensures a well-insulated interior, featuring an efficient electric element heating system for lowering operation costs associated with bitumen storage.
Safety is always an important consideration, which is why users can have peace of mind.
features a secondary containment wall, which surpasses traditional safety requirements, avoiding the need for additional costly walls.
One of the best features of the MEST Bitutainer™ is its versatility to be used as part of an isolated, or major construction/ infrastructure operation, due to the scalable and transportable nature of the system.
TEC has also designed its very own Bitumen Storage Facility, made specifically for bulk bitumen storage, often directly from vessels. Flexible, relocatable and scalable, the MEST Bitutainer™ and TEC’s Storage Facility work hand in hand for a comprehensive storage and distribution system that enhances operational efficiency.
The efficiency gains experienced from streamlining operations come about thanks
“THE MEST BITUTAINER™ REPRESENTS A SIGNIFICANT LEAP FORWARD IN ROAD CONSTRUCTION LOGISTICS. WE DESIGNED THIS INNOVATIVE SOLUTION TO SPECIFICALLY TACKLE THE INEFFICIENCIES AND BOTTLENECKS ASSOCIATED WITH TRADITIONAL BITUMEN STORAGE AND TRANSPORT, PARTICULARLY FOR PROJECTS INVOLVING SPECIALITY BITUMENS.”
to reduced product handling times and minimised logistical bottlenecks, both of which are prevalent with small capacity transport trucks.
This can also be used to support larger applications of materials such as crumb rubber and other forms of modified bitumen, helping to optimise the sustainable outcomes for a construction operation. All the while, having a quality, ready-to-go supply within close proximity to the construction site.
Savings on cost, time and material wastage are just some of the biggest benefits, combined with the customisation capabilities, allowing operations of all sizes to find an ideal solution for their needs.
This is also backed by TEC Container Solutions’ extensive technical support and expert advice, making sure that the MEST Bitutainer™ can fit seamlessly into an existing operation.
Jon Whittall, Managing Director at TEC Container Solutions commends the introduction of the MEST Bitutainer™ in the Australian and New Zealand markets.
“The MEST Bitutainer™ represents a significant leap forward in road construction logistics,” he says. “We designed this innovative solution to specifically tackle the inefficiencies and bottlenecks associated with traditional bitumen storage and transport, particularly for projects involving speciality bitumens. The MEST integrates seamlessly with our Bitutainer™ Storage Facility, offering a flexible and scalable system that adjusts to the evolving needs of our clients. By focusing on operational efficiency, safety, and compliance, the MEST Bitutainer™ empowers construction companies to streamline their bitumen logistics and deliver projects with greater precision and speed.”
Teretek Resin Injection is used as a ground strengthening and liquefaction mitigation solution at a waste water treatment plant.
ROADS, AIRPORTS, PORTS, AND WASTEWATER TREATMENT PLANTS SERVE AS THE LIFEBLOOD OF MODERN COMMUNITIES. AS THE PIONEERS OF RESIN INJECTION TECHNOLOGY IN AUSTRALIA, MAINMARK OFFERS INNOVATIVE SOLUTIONS TO PROACTIVELY MAINTAIN AND REHABILITATE THESE ESSENTIAL FACILITIES, ENSURING THEIR DURABILITY AND LONGEVITY FOR THE FUTURE.
Amere two years ago, the closure of Sunshine Coast Airport’s runway due to a sinkhole served as a poignant reminder of the fragility beneath the surface of seemingly robust infrastructure. Such incidents underscore the critical importance of maintaining and improving aging infrastructure. This is particularly the case in regional areas where its functionality is paramount to public safety and economic continuity.
Since 1989, Mainmark has been at the
forefront of providing advanced and effective solutions to remediate and extend the life of existing infrastructure. Led by individuals like Sasanka Gunawardana, Technical Manager for Mainmark in Queensland, the company is committed to understanding and addressing the underlying challenges infrastructure asset managers face. Underlain soil conditions are crucial for the stability of built structures in infrastructure maintenance. Mainmark emphasises the significance of assessing soil properties
to determine the most effective ground improvement solutions tailored to each unique project.
Whether enhancing load-bearing capacity, composite stiffness, or mitigating liquefaction risks, Mainmark’s suite of technologies offers bespoke solutions to address diverse soil conditions and project requirements. There are unique challenges posed by critical infrastructure such as airports and seaports. For example, these are sites where large-scale vehicle movements exert significant stress on
engineered pavements over time.
“Unforeseen circumstances like weakened subgrade soils can precipitate pavement failures,” says Gunawardana.
“This underscores the need for proactive maintenance measures to avert disruptions to business operations and public services.”
Conversely, the resilience of infrastructure assets like wastewater treatment plants is paramount, given the potentially far-reaching impacts of extended shutdowns or failures on public health and environmental integrity.
Herein lies the crux of Mainmark’s mission: to provide innovative ground improvement solutions that fortify infrastructure and safeguard the well-being of communities and the environment.
Mainmark’s approach to ground improvement is characterised by close collaboration with engineers, asset owners, and managers to comprehensively assess each project’s unique requirements. By analysing root causes and operational complexities, the company ensures the delivery of tailored and optimal solutions.
Mainmark specialises in advanced ground improvement methods.
“Ground improvement modifies a soil’s properties, improving its load-bearing capacity or resilience against liquefaction. Mainmark specialises in delivering a suite of technologies that cover densification, solidification, and soil replacement methods,” Gunawardana says.
to a diverse array of infrastructure assets,” Gunawardana says.
With offices in Australia, New Zealand, the United Kingdom, and Japan, Mainmark continues to expand its global footprint and is poised for further growth and innovation. In an era defined by the imperative of resilient infrastructure development, Mainmark takes pride in being an industry leader in the field of innovative ground improvement solutions.
As Mainmark continues to expand into new territories, its legacy of excellence in infrastructure maintenance remains steadfast, ensuring the stability and longevity of vital assets for many years.
THE NATIONAL TRANSPORT RESEARCH ORGANISATION (NTRO) IS HELPING TO CREATE A SAFER AND BETTER TRANSPORT FUTURE NATIONWIDE, BY COMBINING ACTIONABLE DATA WITH TECHNOLOGY. HERE’S HOW.
The National Transport Research Organisation (NTRO) has long played a pivotal role in shaping the modern and future trends and habits of the transport sector.
With the organisation’s potential influence and technological capabilities, the NTRO is a gateway between both public and private industry.
Leveraging this unique position, the NTRO aims to ensure that the future of road safety is a positive one, taking the industry’s previous learnings and transforming them into preventive measures.
Few are more passionate, or have more experience in this field than Jeff Doyle, Executive Director Roads at the NTRO.
Having spent seven years as the CEO of Altus Traffic, what was the largest traffic management company
nationally, a major focus of his team was “getting you home safely”. This mantra and ethos endure to this day.
That’s also why Doyle has now added Road Safety to his remit, reinforcing the NTRO’s commitment to safety.
With more than a decade’s worth of experience in and around the road safety sphere, Doyle is placed as an instrumental voice and influence, as the industry continues to push to reduce road trauma.
“Recent data has shown an 8.2 per cent increase in the overall death toll year on year,” he says. “Despite the industry’s best efforts and hopes, it’s a figure that continues to rise.
“At the NTRO, safety is at the heart of everything that we do. As a research organisation that combines data and innovation, we believe that we can assist to reduce fatalities and serious injuries.”
Forming relationships and partnerships for the betterment of the industry is the NTRO’s ‘bread and butter’. Doyle has made many connections throughout his journey, but few as impactful and inspirational as Peter Frazer.
Frazer is the Founder and President of the SARAH Group (Safer Australian Roads and Highways), named after his daughter whose life was tragically lost in a preventable crash on the Hume Freeway in 2012.
The SARAH Group provides a boost to industry efforts in improving road safety outcomes. It’s people like Frazer that Doyle believes are helping to make a difference.
“Peter and his family and I have become very friendly over many years. In helping to advocate and promote, we’ve been able to grow the SARAH
contribute and advocate for the new guidelines, which aim to empower the sector to better utilise technology and methods to mitigate potential risks.
The NTRO played a key part in the development of this report, surveying 1100 industry participants about their experience of safety on Australian roads.
Findings from this survey overwhelmingly showed that there’s more work to be done, with Roads Australia describing the findings as “shocking”.
“I’m extremely proud of the sector for that launch and the forum. The NTRO played a big role all the way through, but it shows that there’s still quite a bit of work that needs to be done to make sure that everyone can go home safely,” Doyle says.
“It’s a great first step. There’s still a number of areas that still need tackling and improvements that’re in play.”
Doyle says the NTRO is also pleased with the support shown by the State and Federal governments, with Minister for Infrastructure, Transport, Regional Development and Local Government, Catherine King, announcing a $21 million investment in the National Road Safety Data Hub.
This hub will help to centralise important data for local government, as well as the states and territories.
“We very much welcome the level of
“AT THE NTRO, SAFETY IS AT THE HEART OF EVERYTHING THAT WE DO. AS A RESEARCH ORGANISATION THAT COMBINES DATA AND INNOVATION, WE BELIEVE THAT WE CAN ASSIST TO REDUCE FATALITIES AND SERIOUS INJURIES.”
Group. I couldn’t speak higher of Peter. Sometimes I just look to him in awe of the way he speaks and what he achieves,” Doyle says.
“It’s partnerships like this that we need to take to the next level.”
A shining example of collaboration was put on display at Roads Australia’s recent Transforming Transport Summit in Melbourne.
The event laid a foundation for the launch of Australia’s first Road Worker Safety Industry Guideline, coinciding with the beginning of Road Safety Week. Industry leaders combined to develop,
investment from a government level into road safety. There’s a big focus on bolstering access to national road safety data. It’s very important timing for an important area,” Doyle says.
“It’s about getting that mix right between the public and private sectors. In many ways we can act as a conduit between both, so we’re really hoping to play a big role in this space. And I do too. It’s a real passion of mine and will continue to be, moving forward.”
Doyle adds that the NTRO is well placed to assist with this initiative. He says an effective way of combatting
these rising statistics is datadriven innovation.
“If we look at different tools that are out there, there’s an opportunity to provide a rich source of data, so that we can give that information right back to those local authorities and road networks to make safer decision on their network,” he says.
“Being able to then process that data in real time, and then visualise that will only help from a road safety standpoint.”
The NTRO has developed innovative tools that pinpoint dangerous roads and crash trends, helping both the public and private sectors to greater understand where high-risk sections are, aiding the accurate allocation of essential funding.
Just one of these tools is the NTRO’s web-based Road Safety Intelligence Toolkit, which identifies crash points by location and provides valuable information around crash trends.
It can even provide a demographic breakdown including age, gender, crash types and more.
“It gives you the speed and compliance to filter crashes by various
options, helping you to identify emerging trends,” Doyle says.
“We’re offering that service free of charge until June 30 to local councils as a sign of goodwill off the back of National Road Safety Week, because we think this tool will make a real difference. It can really assist local councils to hone in on their specific networks.”
Another tool that the NTRO has developed to aid actionable outcomes off the back of data analysis is what’s called ‘NetRisk2’.
This is another web-based tool that focuses on high-risk locations and compares treatments and their impact on road safety risks.
“Some people may wonder ‘what’s an infrastructure risk assessment?’ It’s a proactive analysis of risk across the network, allowing high-risk locations to be identified and targeted with a proactive treatment, without having to wait for a crash to happen,” Doyle says.
“It’s the only platform that incorporates Australian Road Assessment Program (AusRAP/iRAP) and Australian National Risk Assessment Model (ANRAM) fatal and serious injury
“ONE OF OUR OTHER MACHINES, THE ILINE CAN BE USED TO COLLECT LINE MARKING CONDITION DATA ACROSS THE NETWORK. CLEAR LINE MARKING TENDS TO EQUAL SAFER ROADS.”
results into a single platform.”
Doyle says both tools are centred around the NTRO’s focus to provide the right information that its customers need to be able to make better safety decisions.
It’s not only web-based tools that the NTRO has developed to counter the rising number of road trauma related incidents.
Two vehicles are also helping to pave the way, the first being the Intelligent Safe Surface Assessment Vehicle (iSSAVE).
The iSSAVE emits water from a large tank, spraying it onto the road surface in front of the test wheels at a given rate, while the truck travels at a constant speed so that it can measure surface friction.
This process can provide unique perspectives into aspects such as skid resistance, roughness, rutting and even GPS imaging.
“It helps by giving you the complete picture of the road network. If you think
of safety on the road network like a jigsaw puzzle, what the iSSAVE allows you to do is put all the pieces together,” Doyle says.
“One of our other machines, the iLINE can be used to collect line marking condition data across the network. Clear line marking tends to equal safer roads.”
iLINE allows road managers to collect line marking condition data across their network, quickly identifying roads or sections of roads that are below standard and need to be re-marked.
Doyle says those two machines are examples of combining data, with innovation.
“I’ve got a saying that ‘if nothing changes, nothing changes’. That speaks for itself,” he says.
“There’s enough fantastic people and fantastic organisations right around the country to be able to make a difference. Let’s start making that change.”
We raise, re-level & re-support sunken concrete, roads and buildings.
MECON HAS EMERGED AS ONE OF THE LEADING PROVIDERS OF TAILORED AND PRACTICAL CONSTRUCTION INSURANCE SOLUTIONS. KISHAN DASAN, GENERAL MANAGER EXPLAINS THE COMPANY’S UNIQUE APPROACH AND PHILOSOPHY IN THE CIVIL CONSTRUCTION SPACE.
MECON’s approach to coverages is underpinned by its commitment to finding the best possible outcome for both their broker partners, as well as the insured.
Kishan Dasan, General Manager – MECON Insurance says the company is amongst the most trusted names in the construction and infrastructure sectors, including civil insurance.
“As an underwriting agency, one of our
key roles is to provide education to our clients, and to provide a solution that matches the requirements of their civil contract,” he says. “That’s something that we really pride ourselves on, is the products that we have tend to match the contracts, which we’ve done a lot of work on.”
While not limited to just the construction sector, MECON specialises in tailoring solutions – in close consultation and
collaboration with its connection of insurance brokers – directly for companies across the civil works sector.
MECON is an experienced insurance provider, understanding the dynamic and at times challenging facets of the sector, an essential aspect of ensuring that its clients can be properly insured.
Further adding to its capabilities and experience within the insurance sector, in 2022 MECON joined forces with plant
and mobile equipment insurance experts Underwriting Agencies of Australia.
This merger blends both companies’ expertise in order to provide a holistic approach to underwriting across a number of sectors, including but not limited to, construction, earthmoving, the cranes sector as well as mining.
Dasan says the unification of both companies will help to build on the market dominance of both providers.
“It’s great to have a proper company structure between the two brands. We have a business development structure that really supports and allows us to utilise staff that are trained in both construction and mobile plant and equipment,” he says.
“Now we’re more capable of going out to our clients and offer a structure by which our clients can be supported across both brands. That’s something that will continue to progress, to see how much more value as a group we can provide to our broker partners and clients.”
When it comes to modern risks throughout the industry, factors such as
cost, weather and potential delays all play roles. That’s why MECON has worked to implement protections around these potential risks as part of its underwriting.
“From a risk perspective, weather is a big factor that comes to mind. Generally civil construction projects are open to the elements, so weather associated risks are amongst the biggest concerns for insurers,” Dasan says.
“From a client side of things, it can obviously cause significant delays and increase the cost overall. The second biggest consideration is design, whether it’s a road, pipeline or a bridge, ensuring that it’s designed in accordance with requirements, with the appropriate due diligence being done prior to the project.”
Geotechnical reports, flood reports, and the right investigations from a land perspective help to ensure that the design is appropriate to the surrounding terrain, another important concern.
When it comes to aiding the underwriting process, Dasan says transparency and communication are key from civil construction providers.
“The key is to make sure that you’re working with your broker to get the right information that we need on the project,” he says. “The more information we have, the higher chance that we can provide the best terms.
“And again, the investigation or the reports that you’ve done to show us that you’ve got the right design for the terrain, risk mitigations, adequate weather delays built into the construction program and the appropriate allocation of risk between yourself and the principal, will assist us in better assessing your risk.”
One of the many reasons why MECON has remained at the forefront of underwriting services for the construction sector is its constant focus on updating and improving.
“MECON has been around for 20 years and over time we’ve expanded our wording and improved on that to cater for the needs of our brokers. That’s something that we do really well. If a broker highlights a potential gap in our wording that may not cover a certain item, we work with them to find a solution by an endorsement policy,” Dasan says.
Even on its own, the civil construction sector has made adjustments in order to mitigate risk.
“FROM A RISK PERSPECTIVE, WEATHER IS A BIG FACTOR THAT COMES TO MIND. GENERALLY CIVIL CONSTRUCTION PROJECTS ARE OPEN TO THE ELEMENTS, SO WEATHER ASSOCIATED RISKS ARE AMONGST THE BIGGEST CONCERNS FOR INSURERS.”
“A lot of contractors are quite cautious and make sure that they have a risk register in place and making sure that they’re tracking potential risks quite diligently. Risk is front and centre, now more than ever it can be a complex issue,” Dasan says.
That’s why MECON focuses on delivering information around insurance and requirements in a manner that’s simple, easy to understand and easier to incorporate for both the broker and the client.
While relatively new in his role at MECON, Dasan has extensive experience in the civil construction and underwriting spheres. Despite his short time at the company, he says the talent and skill of his colleagues made an immediate impression.
“Ever since I’ve started, I’ve heard constant feedback on the outstanding service our claims team provides. That’s something that’s so important, because at the end of the day, an insurance policy is a promise to our clients,” Dasan says.
“We really pride ourselves with our claims and customer service, in addition to providing the right insurance advice”.
CEA HAS RECENTLY TAKEN UP A NEW DEVICE FROM DYNAPAC IN THE SD2500WS WHEELED PAVER. THERE ARE MANY OPPORTUNITIES FOR ITS IMPLEMENTATION WITHIN THE ROADING INDUSTRY, AS ROADS & INFRASTRUCTURE MAGAZINE LEARNS.
Properly paving roads is vital for many different groups. This is where Dynapac CEA devices regularly step in with their high-quality machines. The newest of these machines is the Dynapac SD2500WS and V5100TVE wheeled pavers. They have a standard operating weight of 18,500 kilograms and a hopper capacity of six cubic metres. The wheeled pavers are known for their reliability over many years of operation and have a significant range of applications. The SD2500WS and V5100TVE are ideal for paving urban roads, partly due to their flexibility across multiple industry sectors.
Dynapac CEA has worked tirelessly to respond to the needs of end users and the industry in general. As such, a wide range of optional equipment and attachments are available, further enhancing their versatility.
POWER AND PERFORMANCE
The Dynapac SD wheeled pavers range provides powerful engines with high-end features and the flexibility to adapt to different site conditions. They are known for their compact design and superior manoeuvrability, which helps with the advanced new drive concept and the power to lay a working width of up to nine metres.
Part of what makes the Dynapac SD wheeled paver range so unique is the improved traction. The exclusive AddTraxxion feature hydraulically optimises the traction of the front wheels while accounting for the load in the hopper. It combines seamlessly with the electronically controlled rear-wheel drive, providing optimum traction through precision
and power.
“This innovative approach to traction provides an outstanding driving experience,” says Ralf Peter, Dynapac CEA National Technical Paving Specialist. “It all comes from a well-balanced undercarriage, wide tyres, and a pendulum front axle bogie. The Dynapac SD wheeled pavers also have a wide wheelbase, a low centre of gravity and a small turning circle.”
The new hydrostatic, wear-free brake system offers maximum deceleration for increased safety. The SD2500W is a fourwheel drive vehicle, and the WS version has a six-wheel drive.
The powerful drive gives end-users a high transport speed – from standstill to top speed in just a few seconds – making it easy to follow the traffic flow.
Dynapac wheeled machines are equipped with high-performance tyres specifically selected for paving applications. They
have excellent ground contact and traction, providing cross-stability and power transmission.
Dynapac has designed the hopper to transfer outstanding materials. It’s long at 1953 millimetres and has a very low dump height for fast and easy material transfer from lorries.
Separately controlled hopper wings with generous solid rubber flaps ensure quick and easy material handling. The chamfered hopper corners prevent cold material from being left in the hopper. The conveyor
The Dynapac SD2500WS is designed for paving highways, urban roads and speeding up the process through its efficiencies.
tunnel has been shaped for optimal flow and minimal segregation, with a reversible twin conveyor system offering smooth transfer.
The SD2500WS and V5100TVE offer a robust paddle sensor system for proportional control to ensure flawless material flow. This new optional hopper front flap reduces material spillage on the push rollers and the road. It also helps to empty the hopper completely and reduces the need for manual work.
“The Dynapac SD wheeled pavers offer a shock absorption system based on profile dampers,” says Peter.
The left and right augers are independently driven and provide continuously variable control, even in reverse mode. Dynapac’s robust auger system has improved torque to yield perfect paving at all working widths. The auger height can be adjusted independently while paving.
The operator of a Dynapac has a clear view into the hopper, conveyor, and auger compartment. They also have direct eye contact with screed operators and truck drivers. The platform slides out up to 50 centimetres on both sides just by pressing a button on the dashboard.
“The cabin has been ergonomically designed to ensure that the operator
can work comfortably and effectively throughout all the process stages,” says Peter. “The platform provides plenty of headroom and a flat floor with lots of storage space.”
The big storage boxes in the platform’s floor improve the view out of the back of the cabin. The roof provides two integrated working lights, one at the front and one at the rear.
With the improved dashboard console, repositioning the dashboard has become even more accessible. The Dynapac SD paver generation also offers a weather house with opening side and front windows for comfortable operation in all weather conditions.
An optional fume suction system is available to improve the working environment and keep the fume level around the operator stand low.
Dynapac TruckAssist system is designed to help trucks dock correctly and safely with the paver by simplifying communication between the paver and truck driver.
The system comprises two sturdy, dimmable LED bars strategically positioned on both hopper edges.
TruckAssist allows safe, efficient communication between the paver and truck drivers. It enables the paver driver to always control the truck docking process. This feature is handy at night and in low-
the horn.
any paving operation.
This system is beneficial where a lot of spot work is involved. That is because it is designed to reduce setting and transport times on the job site.
The paver driver now has the option to save the position of the auger and screed before moving from one section to the next.
One push of a button on the redesigned operator panel will lift the hydraulic front flap, auger, and screed, lock the screed for transport and reverse the conveyor slightly. Other features can be added on demand.
Celebrating 50 years in Australia, Reinforced Earth provides solutions for soil structure interaction to retain, cross, protect and strengthen.
Protect
Our protection systems mitigate the damage caused by natural disasters.
Strengthen
We design and supply materials for geosynthetic soil reinforcement for various applications, such as basal reinforcement and steepen slopes.
Cross
We deliver structures designed to cross obstacles, including bridge abutments, underpasses, tunnel extensions, cut & covers, culverts, arch bridges and wildlife crossings.
We tailor earth retaining solutions, from our own Mechanically Stablised Earth walls, to a wide range of other retaining structures.
A RUNDOWN OF ASTEC INDUSTRIES’ RECENT PRESENTATION AND PARTICIPATION IN THE WORLD OF ASPHALT CONFERENCE, THE LARGEST EVENT OF ITS KIND FOR THE ASPHALT AND AGGREGATES SECTORS. ROADS & INFRASTRUCTURE TALKS TO ASTEC’S JORGE BOIL ABOUT THE EVENT.
According to Business Wire, the global market for asphalt in 2020 was estimated at 119.4 million tonnes, a volume that’s projected to grow to 183 million tonnes by 2027.
With the material’s widespread use, companies across the world are always looking for the latest batch mixes and machinery to produce the best possible outcome with what has for decades been a staple of road construction.
The desire to centralise innovation and discussions led to the launch of what is now a major event for the asphalt industry.
The first ‘World of Asphalt’ event was held in 2001 and has run every year since (except for years when CONEXPO-CON/ AGG is held). That first show featured 3200 asphalt professionals across 28,000 square feet of displays from 86 exhibitors.
Now the event attracts more than 15,000 visitors, featuring 440 companies across
This growth has led to it becoming an enticing opportunity for attendees and exhibitors from across the world.
Building on Astec Industries’ strong presence in the United States, representatives from Astec Australia recently travelled to take part in the event.
The World of Asphalt and NSSGA’s AGG1 Aggregates Academy Expo 2024, held between March 25-27 in Nashville, Tennessee showcased the next generation of industry machinery and equipment, as well as solutions to tackle hot topics such as sustainability, safety and diversity.
Labelled as the largest event for asphalt professionals and contractors from across the aggregates, asphalt paving, haulage and technology solutions spaces, the expo featured some of the largest players in the asphalt space from across the globe.
This included aggregate and asphalt producers, asphalt equipment and machinery manufacturers, and infrastructure providers as well as sustainable material developers.
The event presented an opportunity for Astec to showcase five new pieces of equipment, most of which are recently or yet to be released in the Australian market. Most products were part of Astec’s ‘rock to road’ range, an area in which the company has more than 50 years’ worth of experience.
F-Series Highway Class Pavers, the RP-175 and RP-195.
Jorge Boil, Business Line Manager –Infrastructure, says a key feature of the F-Series is the paver’s conveyor and auger design which keeps material live and moving, thereby increasing production throughput and material flow.
“We have also introduced innovations for asphalt plants when it comes to accurately measuring the moisture level of the material, via a state-of-the-art optional sensor, before it enters the mixing drum. And we’ve updated the systems controlling the burners which, in turn, control the feed of the plant and so on. The overall result is that it’s now a lot more accurate,” he says.
“Sustainability was a big focus of the expo, and by controlling the moisture, the burner doesn’t have to run as hard, so it’s using less fuel while reducing emissions.”
The F-Series Roadtec pavers can also incorporate another key optional feature developed by Astec. ‘SmartEdge Joint Detection’ is an innovative screed automation technology that uses laser imaging to generate a 3D model of a lane edge.
The laser is mounted on the paver in front of the screed so that during paving operations, a sensor scans the
lane edge and creates a 3D profile of the edge condition. This information is then passed to the control head unit which automatically charts a flight path for the screed extension to follow.
‘SmartEdge Joint Detection’ is invaluable for both straight mainline work and curved edges, and the system is interchangeable for both left- and right-hand side use.
On top of enhancing the quality of every
pass, the feature allows fleet managers and team leaders to decrease the number of crew members required for a job, and helps reduce the skill gap for operators who might be new to the industry or the machine itself.
Another highlight and technical innovation on show was Astec’s RX-405 cold planer.
First revealed at ConExpo in 2023, the planer incorporates the latest technology to increase the safety and overall efficiency of the machine.
“A key feature of the RX-405 is the almost 360-degree camera vision around the machine, helping the operator to identify if there’s a person, machine or object in the way. It provides a true bird’s eye view of the entire machine from the operator console,” Boil says.
This ‘environmental awareness system’ provides an aerial view of the machine in real time to enhance safety and visibility to surrounding hazards. The technology made its debut at the event and is expected to become a standard feature on all Astec milling machines from Q4 2024.
To enable the operator to optimise the output of the RX-405, Astec developed and installed a mid-mount variable cutter system which helps deliver the most accurate cuts possible, with every pass.
This is achieved through cutting widths ranging from 609mm to 1524mm, and a
maximum cutting depth of 355mm.
The ease of operation and accuracy of the RX-405 comes via exceptional engine torque and horsepower. The cold planer’s Stage Five Cummins QSL-9 engine delivers 430 horsepower.
A variety of cutter drums are also available for customers, and other optional extras include a night light package, vacuum dust extraction kit and rear object detection system.
“There’s a big trend towards compact machinery with better fuel economy and less emissions. The days of going out and working on a single site for weeks are now pretty limited. Flexibility is what’s required today. Operators need to be able to go from site to site, sometimes in the same day,” Boil says.
“That’s been a big change in the United States as well. Nowadays you’re doing a job in the morning, one in the afternoon and another one at night.”
In the equipment it designs and manufactures, Astec has achieved the right balance between mobility, agility
and power. Its machinery is flexible enough to move around on site, compact enough to be transported between different sites and, at the same time, powerful enough to get the job done efficiently and well.
Garry van den Beld , N ational Account Manager – Mobile Asphalt, says taking strides in these areas is part of the Astec way.
“Astec is always looking at new technologies in reducing fuel consumption and emissions from its machines, and delivering even greater efficiencies when it comes to the hydraulic parasitic pressure to ensure smooth operation and less heat. We’re pushing very hard in these important areas with a number of specialised engineering resources,” he says. “It’s all part of our commitment to continuous improvement and helping our customers succeed.”
Astec’s RX-405, RP-175 and RP-195 will be available to Australian customers later this year.
AS THE CONSTRUCTION INDUSTRY CONTINUES TO EXPAND IN THE FACE OF INCREASINGLY COMPLEX INFRASTRUCTURE PROJECTS, MULTINATIONAL COMPANIES ARE EXPANDING THEIR OPERATIONS IN AUSTRALIA. INNOVATION SEES NEW LEADERS COMING TO THE FORE.
The road construction and infrastructure industries form part of the larger construction industry. Xuzhou Construction Machinery Group Co., Ltd, better known as XCMG, is expanding its Australian operations. It is committed to providing customers with quality engineering, supply, and service.
It’s under the leadership of people like Roy Rossini, the Deputy General Manager of XCMG Australia, that the company is expanding across Australia through innovation, reliability, and performance.
“XCMG stands out in the industry due to its commitment to innovation, quality, and sustainability,” Rossini says. “We are pioneers in cutting-edge technology and machines. This ensures that our machines are efficient and designed for the increasing demand within the infrastructure industry and a broad collection of projects.”
XCMG has teams dedicated to quality at every operational level, from the initial design to the final manufacturing stages. Those teams employ the highest of standards throughout every testing stage to ensure that every piece of equipment will meet the highest expectations of its customers and the industry.
“Sustainability is another core aspect
that defines the uniqueness of XCMG,” says Rossini. “We’re actively working to reduce the environmental impact of our machinery through innovations, increased efficiencies, and emissions reduction. Our goal is to help pave the way in construction practices globally while maintaining the performance reliability our clients rely on.”
Innovation is central to XCMG’s activities. Rossini values satisfying customers’ evolving needs.
“That is why we invest in research and development, to develop cutting-edge technologies that improve performance viability and the sustainability of our machinery,” Rossini says. “By staying at the forefront of innovation, we ensure that our customers have access to the most advanced solutions available to our market.”
XCMG is pursuing several key innovations that will benefit the industry as a whole.
The first of these developments is autonomous and remote-control machinery.
“As autonomous technology advances, we’re likely to see an increase in the use of autonomous and remote-controlled machines,” says Rossini. “These technologies not only enhance precision in tasks by paving and grading but also improve safety
and reduce the need for human operators in potentially hazardous environments.”
The electrification of machines and equipment reflects a growing emphasis on sustainability. ESG requirements are set to accelerate the uptake of electric machines. Benefits include reduced carbon emissions, lower noise levels, and decreased maintenance costs compared to traditional diesel equipment.
“The integration of different technologies is transforming the management and execution of projects,” Rossini says. “These new technologies allow for real-time data monitoring and analysis, which leads to more informed decision-making and optimised performance.”
Structured 3D printing technology is beginning to make a mark on the infrastructure sector, as it offers rapid printing of complex components. This shortens project timelines and could revolutionise how roads and infrastructure components are built.
XCMG is actively pursuing improvements in sustainability outcomes and reducing waste in the construction industry. It is achieving this through innovative practices, technological integration, and
strategic calibrations.
“Energy-efficient machinery is a key part of this process,” Rossini says. “We are continuing to upgrade machines to be more energy efficient, significantly reducing our operations’ carbon footprint. This includes the development and rollout of electric and hybrid machines that consume less fuel and emit less compared to traditional machinery.”
Recycling and reusing materials exchanges are involved in initially promoting the recycling and reuse of materials within the construction industry to reduce pollutants, including PFOA, PFOS and PFAS. This includes the manufacturing and development of more environmentally friendly, coating-free materials for producing construction machinery. This optimises waste and reduces the demand for new raw materials.
“We have worked tirelessly on our sustainability manufacturing process,” says Rossini. “It is optimised for sustainability ease. This includes utilising renewable energy sources in our facilities, implementing waste reduction programmes and adopting water conservation practices. By enhancing the sustainability of manufacturing operations, we’ve reduced the overall environmental impact of our products from production through to the end of life.”
Looking ahead, XCMG’s future in the roads and infrastructure industries appears to be both innovative and expansive. Rossini anticipates several different developments that could impact the industry.
“XCMG will continue to expand its presence globally, entering new markets and strengthening its foothold in existing ones,” Rossini says. “This expansion will be supported by our commitment to understanding and meeting the specific needs of different regions, ensuring that our machinery and services are tailored to local requirements and regulations.”
Rossini also foresees a deeper integration
of advanced technologies such as AI, IoT, and autonomous systems into its equipment. This integration will enhance XCMG machinery’s efficiency, safety, and reliability. This will see XCMG pushing the boundaries of what is currently possible in road construction and maintenance.
“XCMG will increasingly focus on sustainability, aligning with global efforts to combat climate change. This will involve not only the development of more electric and hybrid vehicles but also the incorporation of renewable energy sources into our manufacturing processes and exploring new durable and eco-friendly materials,” says Rossini.
“WE ARE CONTINUING TO UPGRADE MACHINES TO BE MORE ENERGY EFFICIENT, SIGNIFICANTLY REDUCING OUR OPERATIONS’ CARBON FOOTPRINT. THIS INCLUDES THE DEVELOPMENT AND ROLLOUT OF ELECTRIC AND HYBRID MACHINES THAT CONSUME LESS FUEL AND EMIT LESS COMPARED TO TRADITIONAL MACHINERY.”
THE ROADS SECTOR IS STEPPING UP TO PROTECT FRONTLINE WORKERS FROM ROAD TRAUMA, URGING DRIVERS TO TAKE EXTRA CARE, WHILE ALSO INTRODUCING AN AUSTRALIAN FIRST GUIDELINE FOR THE BETTERMENT OF THE SECTOR.
Following Road Safety Week in May, as well as a confirmation of an 8.2 per cent year-on-year increase in the national road toll, the road transport sector is accelerating action to save lives by publishing Australia’s first Road Worker Safety Industry Guideline.
Formally launched at the Roads Australia Transforming Transport Summit in Melbourne on May 2, this guideline seeks to protect the industry’s frontline workers – those who build, operate and maintain our roads – and contribute to safer roads for all drivers.
It is an initiative of the Roads Australia Road Worker Safety Working Group, which includes the Australian Flexible Pavement Association, Altus Traffic, CPB Contractors, Transurban, Institute of Public Works Engineers, National Transport Research Organisation, the New Zealand Transport Agency, Roadmarking Industry Association of Australia, Service Stream and Warp Group.
Roads Australia CEO, Ehssan Veiszadeh, says the road transport sector has come together to challenge the current standard of practice and support and prioritise a vision zero future
for the road worker industry.
“Industry has seen an unacceptable rise in the number of incidents, serious injuries and fatalities impacting road workers, signalling a need to continually improve the safety of road workers as well as the public travelling through work zones,” he says.
“Austroads data published in 2022 found that over a ten-year period, an average of 18 fatal worksite crashes and 245 serious injury crashes were recorded annually. This is just the tip of the iceberg, as many crashes and near misses in work zones are significantly underreported.
“Industry is committed to showing leadership on this critical issue, and as a result nine leading organisations who work to build, operate and maintain our roads have come together to raise the bar on road worker safety in Australia. We know more of our members and partners are looking to step up and encourage them to sign on and show their support by signing up to our Safer Workzone Commitment.”
The National Transport Research Organisation recently surveyed 1100 industry
participants about their experience of safety on Australian roads. Their responses when asked if they’ve observed or been directly involved in any incidents near to road construction or road maintenance work sites or incident response were shocking.
The top five incidents they saw were speeding by members of the public, disobeying warning/control signs, verbal and physical abuse from members of the public, dangerous manoeuvres by members of the public (including driving through traffic control) and heavy braking by members of the public when approaching traffic control.
Veiszadeh says following National Road Safety Week, all Australian drivers have the opportunity to make a pledge to drive so others survive.
“With the release of this guideline, we call on all drivers to consider the impact they can make on improving their behaviour, as the industry looks to partner with all levels of government to make our roads safer,” he says.
“Roads Australia and our members are active participants in work at the national,
state and territory level to reduce road trauma including the National Road Safety Action Plan 2023- 25.”
James Pennings, Chief Commercial Officer at Altus says the industry can and should lead the development of higher standards for road worker safety.
“With its focus on capturing ever safer technologies and methods of work, Safer Workzones represents such a framework, and we look forward to it being supported by organisations across the construction, maintenance, utilities and local government sectors.”
The Australian Flexible Pavement Association, one of the key supporters during the development of the guidelines, welcomed the launch.
Tony Aloisio, interim CEO of the Australian Flexible Pavement Association, says the leadership of Roads Australia was to be commended.
“Driving safer outcomes for our workers on the ground is a critical issue for all industry members of the Australian Flexible Pavement Association Members (AfPA), and we are privileged to contribute to the development of this guideline by Roads Australia as well as provide ongoing support in its implementation,” he says.
“There is no IP in safety, and AfPA will continue to work with all stakeholders for
“INDUSTRY HAS SEEN AN UNACCEPTABLE RISE IN THE NUMBER OF INCIDENTS, SERIOUS INJURIES AND FATALITIES IMPACTING ROAD WORKERS, SIGNALLING A NEED TO CONTINUALLY IMPROVE THE SAFETY OF ROAD WORKERS AS WELL AS THE PUBLIC TRAVELLING THROUGH WORK ZONES.”
the continuous improvement of safety practice and policy for all road users.”
Geoff Allan, Chief Executive, Austroads says the Road Worker Safety Industry Guideline will be a valuable resource for enhancing safety across the road construction industry for years to come.
“Industry adoption of the guideline and use of Austroads’ Guide to Temporary Traffic Management will help save lives,” Allan says.
“Additionally, we encourage companies to submit their innovative products for assessment by AITDSA, fostering a culture of innovation and continuous improvement. I am looking forward to the ongoing partnership with Roads Australia and industry to ensuring the safety and well-being of our road workers.”
The Southern Sydney Regional Organisation of Councils (SSROC) has led one of Australia’s largest multi-council demonstration projects, using rubber recovered from end-of-life tyres blended into bitumen to enhance asphalt durability, performance, and environmental sustainability of road pavements.
Conducted by RMIT University, a Life Cycle Assessment entitled Life Cycle Assessment and Potential Environmental Benefits of Crumb Rubber Asphalt using Field Data has studied the environmental impacts associated with incorporating recycled rubber from end-of-life tyres into bitumen for asphalt pavement construction.
Such studies have found that recycled rubber extends pavement service life, reduces demand for raw materials, and lowers environmental impacts.
Led by SSROC with the support of Tyre Stewardship Australia (TSA), and in partnership with the Australian Flexible Pavement Association (AfPA), the Paving the Way: Recycling Tyres for Roads project involved Bayside, Burwood, Canada Bay, Canterbury-Bankstown, City of Sydney, Georges River, Inner West, Randwick, Sutherland, Waverley and Woollahra and Northern Beaches councils.
In 2023, the 12 participating councils each resurfaced a road using a recycled rubbermodified asphalt mix.
Of the demonstration sites, three – in Burwood Council, City of Sydney and Northern Beaches Council areas – were selected for an in-depth investigation into the potential environmental benefits of using the rubber-modified bitumen in council asphalt roads.
The comprehensive Life Cycle Assessment assessed the carbon footprint (kilogram CO2- equivalent) and other environmental impacts of production, construction, and maintenance of recycled rubber asphalt pavements compared to conventional asphalt mix (without recycled rubber) laid at the same location and exposed to comparable traffic and weather conditions.
The study found that incorporating recycled rubber into asphalt mixes using
the wet method can reduce environmental impacts during the production and construction phase compared to conventional asphalt.
By adding 10 per cent crumb rubber by weight of the total binder (100 grams of crumb rubber to 900 grams of virgin bitumen to manufacture one kilogram of rubber-modified binder) resulted in lower environmental impacts compared to using one kilogram of conventional bitumen.
The assessment considers existing research that has demonstrated improvements in pavement performance due to rubber-modified asphalt needing fewer maintenance interventions during the service life, consequently reducing environmental impacts (up to 30 per cent) associated with the maintenance phase of the road asset.
It also demonstrated indirect environmental benefits, such as recovering steel from end-of-life tyres during crumb rubber production and diverting waste tyres from landfills, which will further decrease greenhouse gas emissions.
SSROC President and Mayor of Burwood, Councillor John Faker thanked those who participated in the trial, as well as the team for their achievement.
“Using crumb rubber in asphalt pavement construction and maintenance operations makes a substantial contribution to low-
carbon infrastructure, minimising long-term maintenance costs, maximising performance, and promoting a more sustainable approach,” Faker says.
RMIT Civil and Infrastructure Engineering Professor, Filippo Giustozzi, says the project highlights the effectiveness and potential of this sustainable process.
“The calculations done by RMIT University regarding project-level environmental impacts at SSROC councils have demonstrated that incorporating crumb rubber into asphalt roads using the wet method holds significant promise for reducing the total carbon footprint of these roads by up to 30 per cent throughout their service life,” he says.
“This can potentially offset the environmental impacts generated by new road construction and ongoing maintenance operations, therefore contributing to the decarbonisation of the road infrastructure.”
Australian Flexible Pavement Association Executive Director Technology and Leadership, Anna D’Angelo, says the project is a great example of the circular economy.
“Using crumb rubber from end-of-life tyres can help Australia cut down on the more than 450,000 tonnes of waste tyres generated annually. The use of crumb rubber in asphalt increases the performance and durability of the roads while fostering a more sustainable waste-to-resource approach,” D’Angelo says.
TSA Chief Executive Officer, Lina Goodman, says ‘Paving the Way’ demonstrates the value of crumb rubber.
“Not only does it offer performance benefits to extend the roads’ life and increase performance, but crumb rubber also reduces carbon emissions and environmental impacts. Using crumb rubber in roads is a key way Australia can derive value from end-of-life tyres in the circular economy,” Goodman says.
The extended service life and reduced environmental impacts underscore the importance of incorporating recycled materials, like recovered crumb rubber, in asphalt for sustainable infrastructure development.
Altora’s products are designed to be user-friendly and system-agnostic.
WHEN RUNNING A TRANSPORT OR LOGISTICS
BUSINESS, IT’S ESSENTIAL THAT EVERYONE AND EVERYTHING IS UP TO CODE. COMPANIES LIKE ALTORA ARE AT THE CUTTING EDGE OF COMPLIANCE AND WILL EXHIBIT AT MEGATRANS 2024.
MEGATRANS is Australia’s largest integrated conference and exhibition dedicated to the logistics industry. It is an interactive expo reserved for companies offering advanced technology technologies and services grouped by their contributions to the sustainable supply chain.
This is where Altora steps in. It is a company that provides simple, costeffective online workforce management solutions. The goal is to help solve real challenges for Australian businesses. Altora has been an innovator in providing quality online induction software for over a decade. Customers of Altora experience a radically simple-to-use interface for both administrators and
end-users, which offers value for money.
COMPLIANCE CRITICAL
Compliance is a phrase that can send shivers down the spine of inexperienced or questionable administrators. For those with experience and morals, compliance represents the ability to showcase the expertise and knowledge of its staff. Grace Clueit, the Marketing Manager of Altora, spoke about the importance of compliance.
“There are a lot of laws and regulations surrounding the transportation industry,” says Clueit. “Vital safety regulations must be followed, and there are severe consequences if these organisations are not compliant. That’s why it’s so
important to have proper processes in place nestled within a high-quality compliance system.”
Specific regulations impact the transportation industry. These include heavy vehicle licenses, permits, public liability insurance, and weight and size restrictions before considering companyspecific requirements.
“To give you an idea of the benefits, Freight Specialist is one of our valued clients,” Clueit says. “They ensure that all their staff are fully inducted before they even step behind the wheel. The company wants to be certain that everything is ticked off before new staff even arrive to start their jobs. It means they can relax and be safe knowing that all their drivers have the proper requirements to do their jobs.”
That same client also uses a checklist system developed by Altora. If any requirements are missing, the client is informed that a specific person is missing something that forms part of their induction. This allows the company to follow up with staff to provide the proper compliance materials.
AUSTRALIAN-OWNED ALTORA Altora prides itself on having local
support staff available for its customers.
While the Altora system is easy to use, having technical support available anytime can be a saviour for its clients.
“We take a lot of pride being Australian-owned and operated,” Clueit says. Many companies are outsourcing their development or might be located overseas. We have everything here in Australia, which satisfies many of our clients.”
Another benefit of being Australianowned is the ability to offer competitive pricing. This helps Altora stand out from its competition by providing its services on a subscription basis without limiting the number of users.
“This is a big reflection of our transparency and integrity as a company,” Clueit says. “By not charging on a peruser basis, our customers have standard costs on a month-to-month basis. If contractors come on-site, there’s no concern about how much it will cost them to include them in the Altora system. Many of our clients have multiple sites with a large number of staff, so you can imagine a huge amount of administration would be involved in ensuring all workers are compliant without a good system in place. Another of our clients, Linfox, now has over 100,000 users on our platform, and they’ve been our solid customers for years now.”
This year, leaders from across the supply chain will gather in Melbourne to discuss
It is simple to manage the compliance issues associated with contractors and permanent staff.
The Altora team works together to ensure that their clients get the most out of their software.
the future of the logistics industry. World events have shown that a sustainable supply chain is critical—but it will not happen on its own. It will take the most advanced technology, groundbreaking initiatives, forward-thinking companies, and exceptional talent to create a truly sustainable supply chain that the industry can be proud to pass on to the next generation.
That sustainable supply chain of the future will allow Altora to exhibit its innovative software to help clients across the logistics and transport industries.
“It’s a fantastic opportunity for us to network and catch up with current clients while also meeting potential future clients,” Clueit says. “We can showcase our upcoming advancements within our technology, of which we will have a few. It’s also an opportunity for us to gather feedback about our products and services to improve what we offer.”
It’s also an excellent chance for Altora to meet rural clients with whom we’ve not been able to connect regularly. Altora also relishes the opportunity to increase exposure to its products
“ANOTHER BENEFIT OF BEING AUSTRALIAN-OWNED IS THE ABILITY TO OFFER COMPETITIVE PRICING. THIS HELPS ALTORA STAND OUT FROM ITS COMPETITION BY PROVIDING ITS SERVICES ON A SUBSCRIPTION BASIS WITHOUT LIMITING THE NUMBER OF USERS.”
while finding inspiration in emerging technologies across MEGATRANS. Hamish Horvath is the Product Specialist for Altora and strongly believes in attending MEGATRANS whenever it comes around.
“It’s great to go to an established conference with excellent visitor numbers and plenty of delegates,” Horvath says.
In September, Altora will showcase new technological advances. The most significant change will be its brand-new fleet and asset management system.
“This will allow our customers to manage their fleets and assets, as opposed to just their staff,” Clueit says.
“It’s an exciting development for us, and we look forward to showcasing Altora as a leading induction and compliance solutions provider globally.”
VERTICAL ACCESS AND WORKING AT HEIGHT SOLUTIONS ARE ONGOING ISSUES FOR MANY COMPANIES AND INDUSTRIES. ONE COMPANY THAT WILL EXHIBIT AT BULK 2024 IS THE ALIMAK GROUP.
Encompassing some of Australia’s essential commodities, the bulk solids handling industry is a cornerstone of the local economy and critical to global security. But with rising skills shortages and an ageing workforce, how do we secure the future of this vital sector? With technology advancing and automation on the rise, these technologies will be crucial to the industry’s success in years to come.
There are technological and safety solutions that apply to the construction industry. Dealing with large volumes of materials or bulky supplies is an enormous hazard and can impact the most experienced staff. The construction and infrastructure industries can learn a lot from the bulk handling industry, and it’s why attending an expo dedicated to this area can be vital to ongoing business success.
The Australian Bulk Handling Expo (BULK) will return to Melbourne in September 2024, connecting people to people and business to business. At the same time, it is an opportunity to showcase solutions that will help the bulk solids handling industry move their products to where they are needed most – both domestically and internationally.
The event will feature an expansive trade show showcasing the latest industry solutions and hosting an informative twoday conference discussing how businesses can take the next step to remain cuttingedge in a constantly changing world.
At first glance, it might seem that a major iron ore mine, a cement plant, or a grain shipping terminal don’t have much in common. However, they each use similar equipment like conveyors, silos, hoppers, and more to move their materials from one point to another.
They are also grappling with a labour shortage. Skilled labour has also become more challenging to find and much harder to retain. Jobs and Skills Australia found that the shortage is being driven by the continued tightness in labour market conditions. This reflects either a lack of people with the essential technical skills
or those with the right skills and qualities who aren’t willing to apply for vacancies under current pay and working conditions. Occupations with a strong gender imbalance were also more likely to be in shortage.
A range of strategies are being implemented across the country to help
address the issue, but there is no silver bullet. It has led many organisations to look at innovations like autonomous machinery to help increase their efficiencies as much as possible, whether it’s a port, mine, or manufacturer.
Alimak Group is a global provider of sustainable premium height solutions. With a presence in more than 120 countries, the Group develops, manufactures, sells, and services vertical access and working at height solutions, focusing on adding customer value through enhanced safety, higher productivity, and improved cost efficiency.
Andrew Mercieca is the Sales Manager of Industrial, Light Range & Transport Platforms for Alimak Group Australia. He’s been working for Alimak for 20 years across all facets of the business.
“When I mean every facet of the business, I mean it,” Mercieca says. “I’ve worked everything from installation and service to operations and customer solutions. Alimak has been providing vertical access solutions to the construction, industrial and mining sectors for over 70 years.”
In Mercieca’s eyes, each site presents unique challenges for any installation. This means that a one-size-fits-all approach
will never work.
“While we have a standard range of lifts and materials hoists, we more often than not tailor a custom solution to suit the customer,” he says. “We have local design and engineering facilities available. The engineering teams in Europe, the United Kingdom, and Asia ensure our customers receive the high-quality products they need.”
It’s also the bridges and tunnels that see Alimak play a key role in major projects all over the world. Thompson points out that there are some enormous bridges in China that Alimak has worked on, including the Huajiang Grand Canyon Bridge in Guizhou Province.
The installation of an Alimak SC 65/32 Construction Hoist saw workers reach the top of each of the two towers more than 310 metres above the bridge deck, which will be more than 600 metres above the canyon floor. When completed in 2025, it will be the world’s highest bridge.
“It’s important that we also work on road and rail tunnels,” Thompson says. “For example, there is a lift at the centre of one of the road tunnels in Melbourne. It’s designed for four fully-kitted firemen with breathing apparatus to access the tunnel if anything were to go wrong. It shows the interesting challenges that need unique
solutions to make it happen.”
Alimak provides a range of equipment, from materials-only hoists to personal and materials solutions, with capacities ranging from 500kg to around 12000kg. The sky is the limit regarding capacity.
BULK2024 will be held from 10 am–5 pm on 18 and 19 September 2024 at the Melbourne Convention and Exhibition Centre. It will connect leading companies from across the bulk solids handling sector. Exhibitors can examine the role these technologies have within the industry, how to use them to their advantage, and what else can be done to further improve efficiencies.
Such an event provides a significant opportunity for companies such as Alimak to showcase their range of materials and personnel vertical access solutions.
“We are hoping to connect with potential partners in this field, among others. The important thing is that we are offering a solution that reduces injuries and improves safety. If companies are moving materials more efficiently without having staff getting potentially injured, that’s a positive outcome for the business,” says Mercieca. Exhibition sales are still available – go to https://www.bulkhandlingexpo.com.au/ benefits-of-exhibiting.
AGRICULTURE FARMING EDUCATION WASTE MANAGEMENT RESOURCE MANAGEMENT
CONSERVATION MANUFACTURING RESOURCES
ENERGY HEALTH & SAFETY INFRASTRUCTURE
ENGINEERING MINING CONSTRUCTION
QUARRYING AGRICULTURE FARMING EDUCATION
WASTE MANAGEMENT RESOURCE MANAGEMENT
CONSERVATION MANUFACTURING RESOURCES
ENERGY HEALTH & SAFETY INFRASTRUCTURE
ENGINEERING MINING CONSTRUCTION
QUARRYING AGRICULTURE FARMING EDUCATION
WASTE MANAGEMENT RESOURCE MANAGEMENT
CONSERVATION MANUFACTURING RESOURCES
ENERGY HEALTH & SAFETY INFRASTRUCTURE
ENGINEERING MINING CONSTRUCTION
QUARRYING AGRICULTURE FARMING EDUCATION
WASTE MANAGEMENT RESOURCE MANAGEMENT
SEARCH FOR TOP INDUSTRY TALENT THROUGH OUR JOBS BOARD. CONNECT WITH ALIGNED CANDIDATES.
BOOST YOUR CHANCES OF FINDING SKILLED APPLICANTS.
SCAN TO CREATE AN ACCOUNT TODAY AND DISCOVER YOUR PERFECT MATCH!
THE PAPUA NEW GUINEA INDUSTRIAL AND MINING RESOURCES EXHIBITION AND CONFERENCE (PNG EXPO) WILL BE A TOP EVENT FOR THE INDUSTRY IN EARLY JULY. WILL YOU BE HEADING TO PORT MORESBY?
In Papua New Guinea (PNG), the mining industry is a strong driver of economic growth. Since the 1900s, the industry has evolved to see vast quantities of gold, copper, silver, nickel, oil, and gas extracted and exported. It’s thought to have significant reserves of minerals, including cobalt. Extractive activities represent about 25 per cent of gross domestic product (GDP) in Papua New Guinea.
As such, this is a vital industry for the country’s economy. There is enormous potential for companies to work together to benefit the population.
That’s why the PNG Expo is back. It is the premier event that brings together all industrial, mining, and resource sectors into one location to create a marketplace where business is done. While under new ownership with Prime Creative Media, the PNG Expo will maintain its commitment to invest in the event’s professionalism, infrastructure, and marketing at both a local and international level.
In 2024, the two-day exhibition will feature over 100 displays of equipment and stands. The conference will showcase mining and resource sector experts, presenting challenges and opportunities for the local industry.
The presentations will also delve into the challenges and opportunities for the local industry. The keynote speakers will look at a vast array of topics that touch on the pressing issues impacting the PNG mining industry and the broader PNG economy.
A networking reception and official dinner will allow attendees to meet potential customers and partners in a relaxed setting.
“We have received positive feedback from the industry so far,” show director Lauren Chartres says. “We’re excited to see this event moving to a new phase of development
and bringing additional value to the PNG resources sector.”
Leaders in productivity solutions will be exhibiting at the event to present their innovative technology, showcasing how it benefits the PNG mining industry. The cutting-edge solutions will allow potential buyers to improve their productivity and yields.
“We know that productivity and efficiency are huge drivers of success in PNG,” Chartres says. “We’re excited to see how exhibitors address these issues with their solutions at the event in July.”
With the topics of sustainability and safety, the conference will aim to pave the way for companies striving for positive change. There will be numerous prospects for attendees to make various constructive transformations for their businesses and communities of interest.
Chartres says they understand how safety and sustainability could impact businesses within the PNG mining industry.
“The PNG Expo will allow businesses to drive transformative changes towards a sustainable future,” she says.
As the date for the 2024 event approaches, exhibitor spots are filling up fast.
The PNG Expo expects to attract more than 2000 key buyers and procurement managers from landowners, government, mining, energy, petroleum, and infrastructure industries.
Limited opportunities for leading companies in productivity solutions are still available.
Don’t miss out on this opportunity to grow your business in an expanding market.
To learn more about exhibitor opportunities, contact KahChi Liew at kahchi.liew@ primecreative.com.au or +61 421 474 407. For more information, visit pngexpo.com.
stands.
ROADS & INFRASTRUCTURE PROVIDES
Downer awarded $320M road maintenance contract
Downer has been awarded a road maintenance contract by the Department of Transport and Planning in Victoria over a maximum term of eight years. The contract begins in July 2024 for an initial four-year term, with two additional two-year extensions to be offered under the agreement. As part of the works, Downer will deliver routine maintenance, planned maintenance, defect inspections, hazard rectification and emergency response services to more than 1600 lane kilometres of road and 1900 structures in metropolitan Melbourne’s Western region. This adds to Downer’s existing maintenance works on more than 10,000 lane kilometres of state road across Victoria. Chief Executive Officer of Downer, Peter Tompkins, said the contract reinforces Downer’s position as one of the leaders in road maintenance across Australia and the state.
Inland Rail has selected John Holland to complete early commencement works and delivery activities for eight project sites in Victoria. The contract includes design and preparatory works at Benalla, Euroa, Wandong, Hume Freeway – Tallarook and Seymour, and three sites in Broadford on the existing North East Rail Line to allow for the safe passage of double-stack freight trains. These works are known as the Beveridge to Albury (B2A) –Tranche Two section. John Holland will now conduct site investigations and progress design work at each of these sites. Activities will include geotechnical investigations, ground water monitoring and additional surveys, as well as development of key management plans. Inland Rail’s appointment of a construction partner for the remaining Victorian sites is on schedule for mid-2024, with construction commencing in early-2025 and project completion in 2027. Inland Rail is a 1600 kilometre freight rail line that will connect Melbourne and Brisbane via regional Victoria, New South Wales and Queensland.
Expressions of interest are now open for two contracts to deliver new stations as part of the 90-kilometre Suburban Rail Loop in Melbourne. Successful proponents will help to deliver six new SRL stations, which will be delivered at Box Hill, Burwood, Glen Waverley, Monash, Clayton and Cheltenham. 15,000 passengers are expected to pass through Box Hill and Clayton stations every day. Two global bidders have also been shortlisted for the Linewide Alliance contract
to build the fleet of high-tech SRL trains, fit out the tunnels and operate and maintain the SRL East network. Works on all six station sites begin later this year. Tunnelling for the SRL East starts in 2026, with the $3.6 billion contract to build 16 kilometres of twin tunnels between Cheltenham and Glen Waverley awarded late last year to Suburban Connect, a consortium of CPB Contractors, Ghella and Acciona Construction. The Tunnels North contract will be awarded later this year. The project is expected to bring thousands of jobs and local services to the neighbourhoods around each station. SRL East will start taking passengers from 2035. The total estimated cost of the project is between $30-34.5 billion.
UGL, ADCO Joint Venture wins WA contract
UGL has been awarded a contract, in joint venture with ADCO, to construct new railcar maintenance facilities at Bellevue, Western Australia, for the State’s Public Transport Authority. The project expands on the existing Bellevue Railcar Manufacturing and Maintenance Facility and is expected to generate revenue of more than $110 million for UGL. UGL will provide the project’s civil works, track construction, signalling and trackside equipment installation, electrification works and connection to the site’s existing High Voltage Traction Power substation. A new assembly and commissioning facility has been built in Bellevue as part of the WA Railcar Program, which will deliver 246 new railcars required for METRONET projects and the subsequent retirement of the A-series trains. Situated at the end of the Midland Line, the site in Bellevue is an ideal location to assemble and commission new railcars. The main facility includes a 180 metre-long building with a railcar assembly area, offices, workshops and storage areas, two overhead cranes and a heavy maintenance railroad with a crane capable of lifting 10 tonne. Works commenced in the first quarter of 2024 and are expected to finish in mid-2026.
First significant subcontract awarded for Darwin Ship Lift project
The Clough BMD Joint Venture has awarded a contract for works on the Darwin Ship Lift, a project representing a $215 million investment from the Northern Territory Government. The ship lift will be a Northern Territory Government-owned facility that will provide wet and dry berths for vessels wash down, blasting, painting and general maintenance facilities on a common user basis. The contract works, valued at $16.9 million, have
been awarded to local Darwin-based entity Wilga Indigenous Corporation to supply and deliver around 430,000 tonnes of rock for the laying of groundwork ahead of major construction. The facility will be designed to meet the needs of the general fishing and maritime sector, the Department of Defence and the Australian Border Force. When complete, the ship lift will boast the capability to lift 5500 tonnes, enough to facilitate vessels such as the new fleet of offshore patrol vessels procured by the Australian Defence Force. Local procurement and contract designation has been a big focus during the early stages of the project. It is anticipated that several components of the ship lift facility will be completed in early 2025 and the balance of work completed in 2025–26. Over the next few months, additional works packages such as further quarry supply, site surveying, site facilities and plant equipment and hires, are expected to be awarded.
Companies invited to tender for $95M Lindesay Highway
Tenders have been released to market for works on the $95 million Mount Lindesay Highway in Queensland, with the detailed design for the new south bound bridge now finalised. Tenders for the construction of upgrade works on the Mount Lindesay Highway between Johanna Street and South Street in Jimboomba will deliver safety improvements, ease congestion, and reduce travel times by widening the highway from two to four lanes, including construction of a new south bound bridge over the disused rail corridor. The construction tender process is expected to take approximately three months and major construction is expected to start in late 2024 and expected to take approximately 18 months to complete. A construction tender was released to market in early 2023 but then withdrawn pending the outcome of the Australian Government Infrastructure Investment Program Review. Early works on the project were completed in 2023. The Department of Transport and Main Roads (TMR) has a 10-year forward plan (2018-2028) for the Mount Lindesay Highway, with construction projects being delivered as funding becomes available. Pedestrian and bike riders will also benefit with new active transport shared paths being installed and upgraded across the scope.
The H6+ is built tough with a weather-resistant HardHat body and features a user-friendly control panel for easy operation. With a long runtime and extended service intervals, the HiLight H6+ is the reliable lighting solution you’ve been looking for.
FEATURING:
• 55 Dba @ 7 metres (quietest on the market)
• .67lph fuel consumption
• 185 hrs continuous runtime
• 600 hour service intervals
• 6000m2 of light coverage at 20 Luxes
• Dual fork pockets
• 340O mast rotation & auto mast down feature
• Legendary Hardhat® cover
• Photo sensor for auto start/auto stop
LIKE TO KNOW MORE? SPEAK TO OUR TEAM TODAY