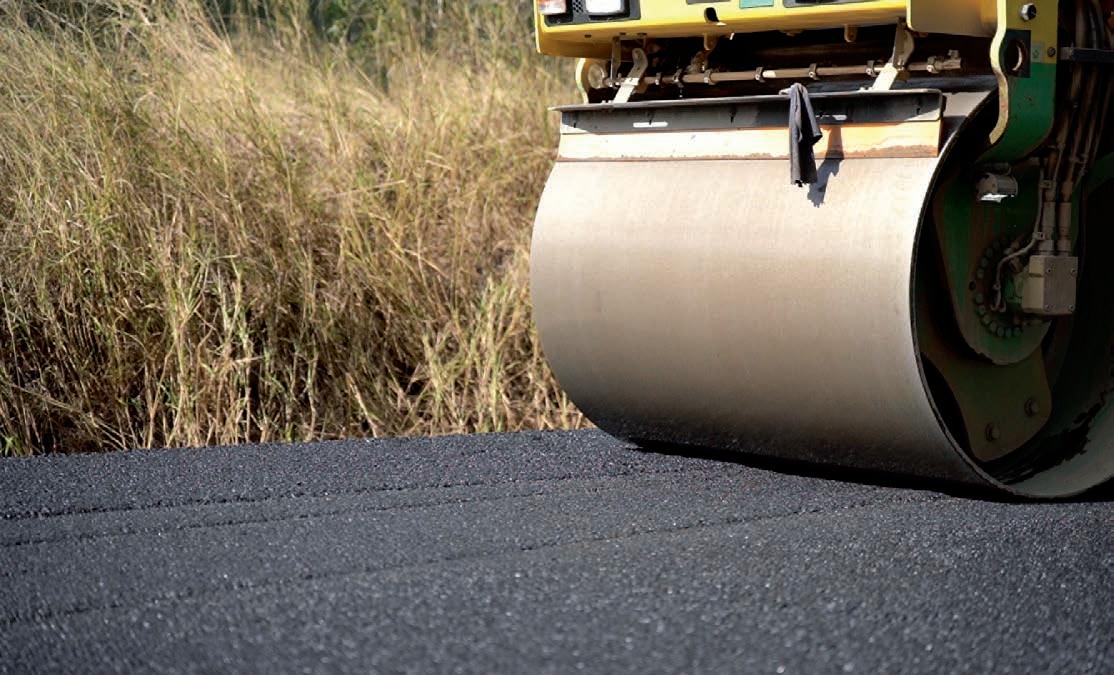
5 minute read
Bringing GB5 to Australia
AN INTERNATIONAL EXAMPLE: GB5
PUMA BITUMEN IS PARTNERING WITH A MAJOR FRENCH CONSTRUCTION COMPANY EIFFAGE TO BRING GB5 BASE COURSE MIX TO AUSTRALIA. THROUGH A DEMONSTRATION WITH BORAL, PUMA IS HOPING TO EMBED THE MIX AS COMMONPLACE FOR AUSTRALIAN ROADS.
In the early 2000s Eiffage, one of France’s largest construction companies, set out to create a road base course layer that featured both optimal aggregate interlock methods and the use of SBS rubber polymers.
This research and development hoped to create a base course with fatigue resistant properties to improve the longevity of roads.
In 2010, Effiage’s GB5 mix using these components was patented. Later that year the mix won an innovation award from SETRA, the French Department for Roads and Highways.
As a result of this award, the French Institute of Science and Technology for Transport, Development and Networks (IFSTTAR) performed accelerated testing on the base course mix. This included increased axle load testing, which put a high number of vehicle movements onto the pavement in a short amount of time.
In this trial, four GB5 mixes with different properties were tested against an EME2 base course mix, all of which included Reclaimed Asphalt Pavement (RAP).
After 10,000 loads at 6.5 tonnes, each of the GB5 mixes showed almost no cracking. When this was increased to 7.5 tonnes, only one of the GB5 mixes began to crack. The GB5 sections outperformed the EME2 control sections. This demonstrated impressive durability and fatigue resistance characteristics for the GB5 mix.
Since this trial, around four million tonnes of GB5 has been used on roads across France, Spain and South Africa.
As a major player in the Australian bitumen market, Puma Bitumen noticed the success of the GB5 mix and partnered with Eiffage to bring GB5 to Australia.
Puma’s Technical Manager Erik Denneman says GB5 is offered by Puma as an alternative to EME2, high modulus asphalt.
A demonstration in July, in partnership with Boral Asphalt in Queensland, marked the first time GB5 mix was used on an Australian road.
Prior to the demonstration, Puma and Boral performed Australian tests on the

Boral Asphalt laid the GB5 mix on a major project near Brisbane.
mix in its laboratory to ensure it could be safely applied.
The mix was then laid by Boral Asphalt on a major project, near Brisbane. The demonstration section was a combination of a GB5 base layer and Puma’s newest approved surface binder OLEXOCRUMB
Together the mixes feature significant sustainability benefits. Dr. Denneman says the GB5 mix is a stone skeleton mix with the benefit of requiring a reduced amount of bitumen.
“There are cost and sustainability benefits due to the reduced amount of bitumen needed for GB5. Then the surface, OLEXOCRUMB®, uses 10 per cent crumb rubber with every tonne of binder produced, recycling the equivalent of 15 passenger tyres,” he says.
For the project 2000 tonnes of GB5 and 700 tonnes of OLEXOCRUMB were laid. The GB5 base course was constructed during the weekend and OLEXOCRUMB was placed on top the next day.
Peter Carbone, Manufacturing Operations Manager at Boral Queensland, says Boral has always had high regard for innovation and research and development and this opportunity to work with Puma was exciting.
“The use of EME2 has seen exponential growth here in Australia that has provided numerous benefits to both the industry and road owners in terms of superior performance and cost savings through reduced pavement thicknesses,” Mr. Carbone says.
“We see GB5 as an important alternative to the high modulus asphalt product range that will bring equal if not better performance but also added project construction benefits.”
He says one of the key advantages of GB5 is that there are no real discernible differences to laying a GB5 asphalt or a conventional asphalt.
“We also found, in the demonstration, that the GB5 mix had high stability during placement and compaction. This indicates that the GB5 mix has the potential to be well positioned to have multiple deep lift asphalt layers constructed in a single shift,” Mr. Carbone says.
For the demonstration Boral and Puma undertook extensive work to provide assurance that GB5 meets the relevant specifications and requirements such as
The GB5 base course mix is well suited to roads with high traffic volumes.
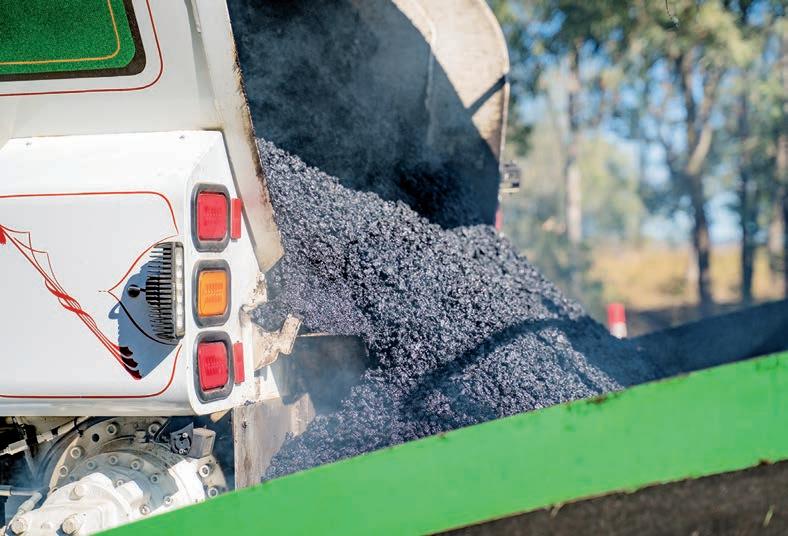
temperature monitoring, developing rolling patterns, undertaking surface texture measurements and more.
“Not only this, but the surface texture of a GB5 mix is such that it can be trafficked without the need for a grit sand and therefore speeds construction processes. GB5 is also a sustainable product in that RAP that can be incorporated into the mix and recycled again at the end of its life. In fact, there is opportunity to add higher RAP content in future projects, as already used in France,” Mr. Carbone says.
Dr. Denneman agrees with Mr. Carbone’s view that the ability to run traffic across a GB5 mix earlier than the conventional asphalt is an advantage that can significantly speed up works.
“Early trafficking can be a major issue when required to open a road during construction of the asphalt structure, and the base materials can be smooth and present skid issues for vehicles. GB5 has a coarse surface texture and therefore can prevent skidding.”
The coarse surface texture also helps to bond the base material to the surface course.
“Due to the roughness of GB5, the surface layer can interlock well with the mix below, which is an important part of the structure. This ensures an improved quality road and longevity in the pavement,” Dr. Denneman says.
In addition, he says use of a Polymer Modified Binder (PMB) in the GB5 mix results in improved rut resistance, which further helps to lengthen the life of the pavement.
PMBs have long shown performance benefits such as improved elasticity, stiffness or resilience, depending on which type is used or required.
Due to the strength of the GB5 base course mix it is well suited to main roads with high traffic volumes that are constructed with a full depth asphalt structure.
“We hope that after this demonstration, the GB5 mix will be a standard mix design in Queensland. We are also looking at offering the mix in other states across Australia,” Dr. Denneman says.
Following the production and field demonstrations of GB5, Boral will also look to offer the product as an alternative to EME2.