
6 minute read
Material recycling
KLEEMANN...
THAT’S A RAP
RENOWNED GERMAN MACHINERY MANUFACTURER KLEEMANN HAS BEEN PRODUCING CRUSHERS AND SCREENS FOR MINERAL PROCESSING SINCE THE 1920S. NOW, WIRTGEN IS BRINGING THE LATEST TECHNOLOGY FROM THE OEM TO AUSTRALIA.
The finite nature of quarry materials has caused Reclaimed Asphalt Pavement (RAP) and recycled concrete to become increasingly crucial for the construction sector.
Recycling asphalt being incorporated into new road construction is not new. It’s now the normal and saves highly valued material being treated as waste.
During this process it is important to consider how an aged asphalt pavement can be recycled effectively ensuring the result is economically justifiable.
Kleemann GmbH is a member company of the worldwide Wirtgen Group and a business built on its expertise in crushing and screening.
The Kleemann MOBIREX MR130 Z EVO2 mobile impact crusher is used across many material processing applications from crushing and demolition waste, concrete through to asphalt. The Kleemann MR130 aims to excel at the economical processing of recovered asphalt for recycling.
INCREASED CAPACITY Patten Pavement Services is a Victorian road profiling business that crushes and produces construction materials.
Tony Ferguson, Operations Manager at Patten Pavement Services, says the business used other impactors in the past but with our Wirtgen profilers it made sense to transition over to the Kleemann.
The other deciding factor was the strong after sales service that we provide PPS on the profilers, they knew that they were going to expect the same service when it come to the Kleemann product.
“We purchased the MR130 Z around a year ago and what we have found is that it has changed the business model for us in terms of crushing,” he says.
Ferguson explains that as the machine is diesel electric driven, as opposed to diesel hydraulic, the fuel savings per tonne are a significant benefit.
“In any given year we could go through anywhere from $20,000 to $30,000 of hydraulic related expenses. We have found it’s also cut our fuel expenses, from the impactor, to almost half of what we were originally using,” he says.
“We have even gone to a bigger machine and we have a much better fuel economy for it with the electric drive.”
The design of the Kleemann is another factor that impressed Ferguson, he says in the past some machines struggled to remove contaminants with their returns systems. However, the recirculating conveyor has been successful in clearing out contaminants that keep going around and around thus eliminating the need for a picker to manually remove the un-crushable material from the circuit.
“The operator can control the recirculating belt via a wireless remote control and stockpile it off to the side of the machine, which allows you to remove these contaminants from the crushing circuit. Then you simply bring the belt back in and you can start again, without stopping the entire machine and all of this can be done on the fly,” Ferguson says.
The new material flow concept on the Kleemann MR130 Z, aims to ensure that there is no restriction to the flow of the material, prevents blockages, reduces wear and increases the performance of the entire plant
Some of the new elements of the Kleemann design include the independent double-deck pre-screen, a vibrating discharge chute or pan feeder under the crushing chamber as well as a new crusher with inlet geometry and rotor ledges technology.
Kleemann MOBIREX plants aim to crush stone so efficiently that the grain shape, grain size distribution and cleanness comply with strict standards for concrete and asphalt aggregates.
Ferguson says for one of his clients it wasn’t just the quality of the material produced that was so impressive.
“What they found to be the big difference was tonnes on the ground, and the reliability
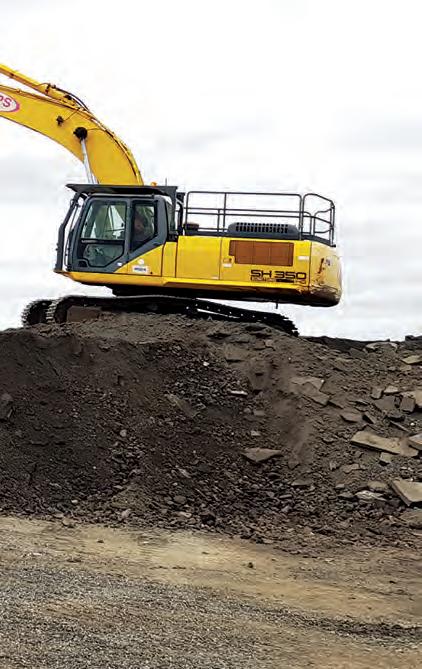
we could give them to produce crushed materials,” he says.
“This has allowed them to change their business model. We were able to crush to the bottom of their site in Dandenong, Victoria for the first time in 15 years and we now have done that at another of their sites too.”
CRITICAL SAVINGS Rostrevor Group is an emerging crushing and screening business, started by Cathal ClerkinParr 18 months ago.
Clerkin-Parr noticed a gap in the market and an opportunity when it came to asphalt recycling.
“When I was starting up the business, I had done some research into the best crushing and screening machine and from what I could tell the Kleemann was one to go for,” he says.
“One of the big things for me was simply how the machine was built and the quality of the finish. For me the quality of the welding was excellent on the Kleemann.”
He was also impressed by the fuel efficiency and ease of use due to the diesel electric drive running the machine.
“That was a winner for me, I’ve found by having a diesel electric drive machine versus that of a diesel hydraulic machine this alone brings our fuel consumption down by about two thirds overall. We used to use around 50-70 litres per hour depending on the material we put in the diesel hydraulic driven impactors, but the last 15 months we have averaged 27 litres per hour on the Kleemann,” Clerkin-Parr says.
“With the machine being diesel electric drive, it also makes operation really simple, instead of having thousands of litres of hydraulic fluid on site the diesel electric drive reduces this dramatically as the hydraulic components of the machine is drastically reduced. The electrical systems on board are also really good, using high quality components,” Clerkin-Parr says.
The Rostrevor Group uses the Kleemann for a range of materials including recycled asphalt, construction and demolition waste and rock.
Clerkin-Parr says one of the other great benefits of the machine is the material flow of the crusher.
The Kleemann MR130 Z has a fully automatic hydraulic gap setting system to adjust the close side settings with a push of a button. This works to improve the quality of the product but also the availability of the plant in combination with the effective overload protection system.
“When you feed material into the plant it goes from the pan feeder to a independent double deck pre-screen which opens up fractionally into the crusher. Material flows really nicely through the machine it doesn’t leak material or spill it out, it’s all kept in the machine which is great.”
He says in Australia it’s becoming ever more important; with some finite resources to use them to full capacity by recycling them at the end-of-life stage.
“With asphalt you can keep recycling it and that is one of the great things about the material,” Clerkin-Parr says.
Kyle Fredericks Crushing & Screening Buyer at Wirtgen Australia says there are significant considerations required when recycling asphalt with bitumen recovery at the top of the list.
“In general, it can be said that asphalt in Australia is made to a defined specifications. The gradation of the typical dense graded materials follow a similar grading curve from the 4.75 millimetre sieve down,” he says.
“It’s critical to preserve the particle size distribution of the materials. The intention here is not to crush the aggregate and increase the percentage of fines, but rather to separate the aggregate particles without increasing the surface area of the material.”
Fredericks says the Kleemann is best suited to processing RAP because it breaks the asphalt into smaller clumps, minimising the effect of downsizing the gradation and helping to achieve the original asphalt gradation.
“With the MR130 crushing path design, the effect of downsizing is really reduced, the addition of the integrated screen means that only sized material can be taken straight to the stockpile for testing,” he says.
Throughout Australia and New Zealand there are now several Kleemann crushers working to produce different types of recycled materials. Fredericks says the machines used to process RAP have so far been highly effective.
For any Kleemann Crushing and Screening enquiries please contact: Kyle Fredericks, Wirtgen Australia Pty Ltd Kleemann Crushers & Screens – Vic, Tas & SA 0447 539 302 or kyle.fredericks@wirtgen-group.com
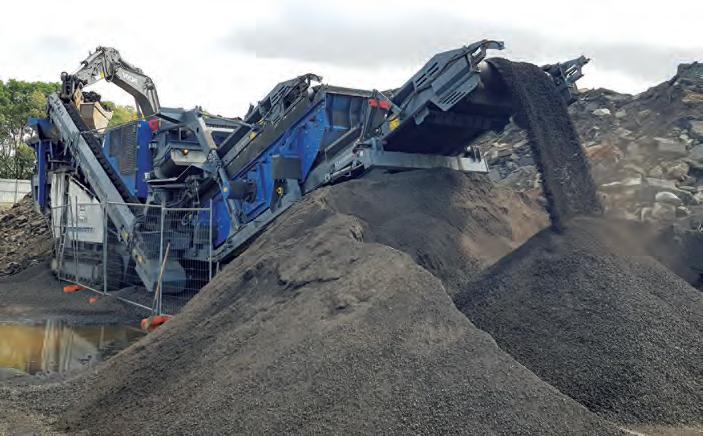