
5 minute read
Collaboration for innovation
COLLABORATION CREATES
INNOVATION
STRONG RELATIONSHIPS WITH INDUSTRY HAS ENABLED QUALITY FABRICATION AND ENGINEERING TO COME UP WITH TAILORED SOLUTIONS FOR ROAD BUILDING IN AUSTRALIA. THE COMPANY EXPLAINS WHY COLLABORATION IS INTEGRAL TO SUCCESS.
In April 2020, the world economic forum announced it found global internet traffic increased by about 30 per cent as COVID-19 spread across the globe.
The ability to stay connected during the COVID-19 era has fallen on mobile and internet communications and created a need for closer collaboration to ensure supply chains function seamlessly and effectively.
This is something the Quality Fabrication and Engineering (Q-FE) team know well. The company and its staff have long been engaging with the road construction industry to provide innovative solutions for their machinery and equipment.
When VicRoads announced in 2016, its intention to mandate the use of forward moving aggregate spreading equipment, Q-FE used its extensive industry knowledge to design an innovative forward moving (dual control) aggregate spreader.
With the initial unit scoped, Q-FE engaged with industry to demonstrate and seek their feedback about practical and safety features whilst optimising the effectiveness of the machine.
From this the Q-FE team created the Road Ant, which is a dual controlled forward moving aggregate spreader that can be driven from either end.
David Lockwood, Q-FE’s head of sales, says the engineering and design components of the Road Ant, including optimising the line of sight and other operator safety features, came from collaborating with both road contractors and suppliers.
“Our Road Ant forward moving aggregate spreader puts the operator’s cabin right at the edge of the spreader so that when driven in a forward direction, the operator has a clear and unobstructed view of the work site,” Lockwood says.
“Q-FE’s approach is to leverage our extensive in-house expertise with the practical experiences of the machinery operators so that our engineering designs and solutions are innovative yet also deliver the productivity and safety aspects that the road and infrastructure sectors demand.”
Glenn Hardiman, Q-FE’s General Manager, says that having been involved with the spray sealing industry over many years, the team knew that in southern parts of Australia the spray sealing season is only around six months long. This meant that any dedicated spray seal machines may not be used for the other half of the year.
“Our Road Ant machine is built to fit any standard Trout River body attachment and it can also be used conventional for transporting materials or to feed an asphalt paver. Meaning the truck can be used in the spray sealing off-season for other things,” he says.
“We listen to people in the industry because they are the experts. No one can tell you what the real issues are other than the people using the machines out on the road.”
Hardiman says the experience the team has with the road building industry is another factor that drives innovation at the company.
“Many of us have hands on experience of working with this type of plant and equipment over the years. This gives us a good foundation when exploring design solutions,” he says.
After hearing about durability issues with some spray sealing brooms, Hardiman says the company also decided to design their own solution based on input and feedback from a then new player in the spray sealer industry in early 2000’s.
He says the design and robust build ensures durability and ease of use.
Lockwood says the company aims to be an innovative and practical design solutions company rather than just a machinery manufacturer. Part of this he says is down to their collaboration with Australian suppliers.
“We are proudly Australian owned, and we proudly prefer Australian components and collaborate with those in the local manufacturing community. There is a lot of innovation and engineering within Australia, it’s just a matter of working out where they are and what they can do.”
He says local manufacturers are keen to invest in research and development to ensure they are providing local companies with the solutions they need.
Hardiman says innovation at Q-FE will continue to develop.
“We have a few ideas up our sleeve related to road building and maintenance machinery and equipment, and I would like to think our expertise and the relationships we’ve formed over the years with contractors, will keep us at the forefront of important solutions for the industry.” For more information contact: sales@qualityfab.com.au or +613 5955 0000
The Q-FE team have long been engaging with the road construction industry.
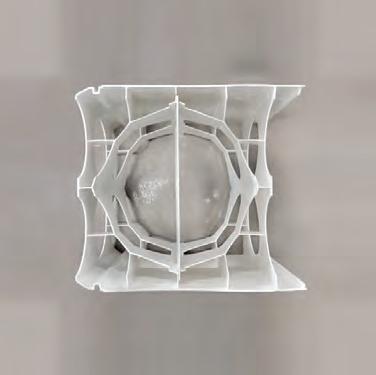
Dincel 275 Profile Strength Tested at UTS
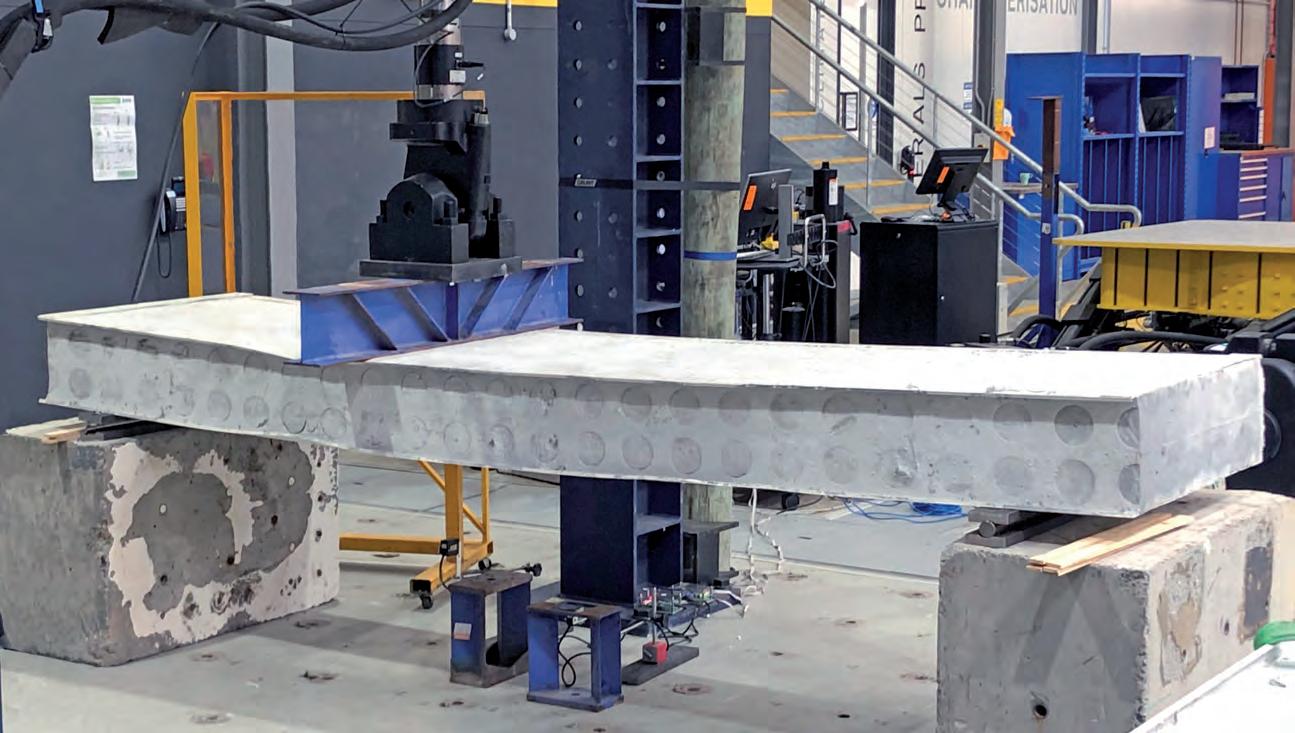

Industry first innovation
By omitting steel reinforcement bars, Dincel 275 is able to offer the following benefits:
Faster, safer and less excavation resulting in incredibly cost-effective installation.
Significant reduction in embodied energy and carbon footprint.
(reduced steel manufacturing)
Exceptional concrete compaction,
as the omission of horizontal steel reinforcement bars in particular enables unimpeded concrete flow. When coupled with 275 Dincel’s unique ability to handle up to 300mm slump concrete, air-voids are not possible. Air-void free concrete in Dincel 275 ensures an increased asset life by preventing potential corrosion issues and eliminates the need for wall waterproofing. The Dincel 275 profile, which contains a unique cylindrical formwork shell, has undergone strength testing at the University of Technology Sydney (UTS). UTS has confirmed that 275 Dincel can be designed and installed without the use of steel reinforcement bars, consisting of the following concrete infill:
Mass concrete, or Macro synthetic fibre (BarChip) reinforced concrete The testing was completed in accordance with the requirements of AS3600-2018 (Appendix B) and is certified by UTS as compliant with the National Construction
Code ‘deemed-to-satisfy’ provisions for structural requirements.
In addition, the loading was applied onto Dincel 275 walls containing either early-age concrete (after 24 hours) or later-age concrete (after 28 days). Results demonstrate that Dincel 275 walls can be backfilled 24 hours following concrete infill (with appropriate bracing), which allows for construction of the superstructure to take place earlier.
For more information visit dincel.com.au
Watch the 275 Dincel video
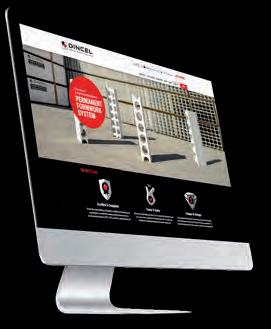
Download The Dincel 275 Report by UTS testing