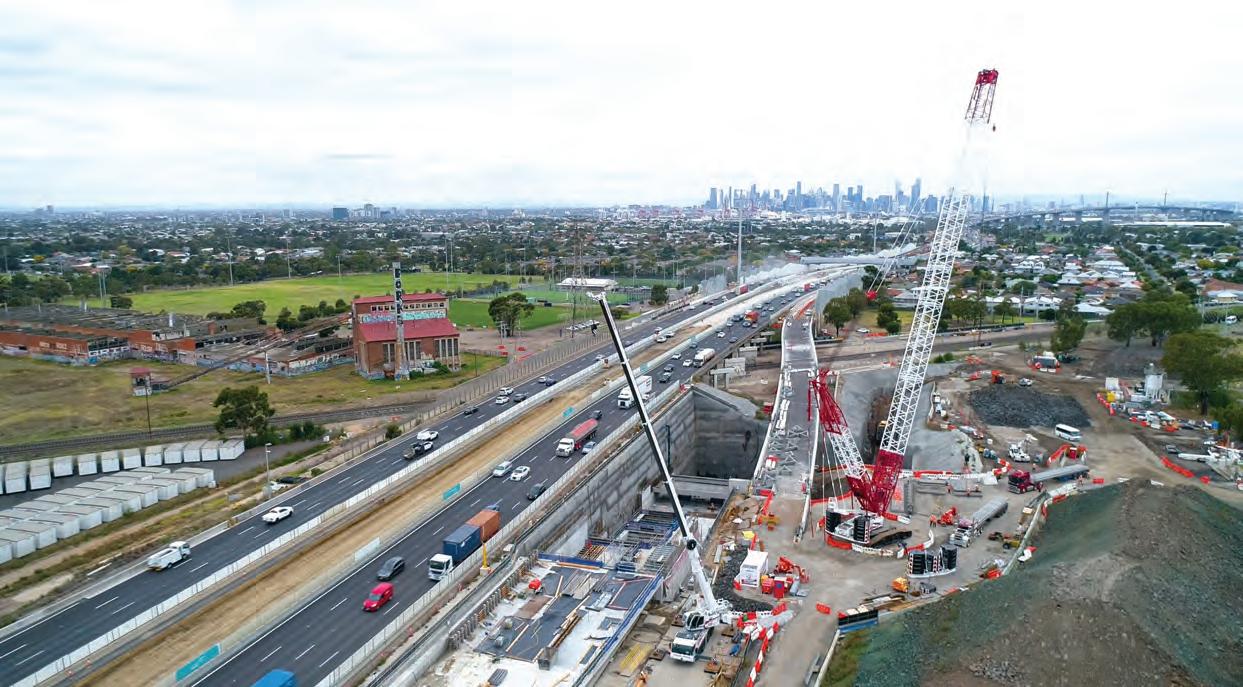
10 minute read
Building the portals for West Gate
WEST GATE TUNNEL PROJECT:
BUILDING THE PORTALS
ROADS & INFRASTRUCTURE GOES BEHIND THE SCENES WITH THE WEST GATE TUNNEL PROJECT CONTRACTORS CPBJH JV AND THEIR LIFTING PARTNER, PREMIER CRANES AND RIGGING, TO LOOK AT THE CHALLENGES IN SHAPING THE TUNNELS’ ENTRY AND EXIT PORTALS.
For Sam Clark, a professional crane operator of nine years, picking the first concrete segment for the West Gate Tunnel’s southern portal was the most memorable one.
It was not every day he would pick a 60-tonne precast concrete section and place it on surveyed marks at a 48-metre operating radius with a beast of a machine, the 350-tonne Liebherr LR1350/1 crawler crane.
“Together we would be lifting bigger loads in the end, but that first lift took the longest to plan,” he says, looking back at the nine months he operated the giant crane while the tunnels’ southern portal walls were taking shape.
More than 200,000 vehicles, including a majority of Melbourne’s commercial traffic, travel on the West Gate Freeway each day. The West Gate Tunnel is aiming to provide an alternative to the West Gate Bridge for people travelling to Melbourne from the western suburbs and reduce large vehicle traffic congesting suburban streets.
The westbound exit portal is in Altona North, just to the south side of the existing freeway and it’s where the outbound tunnel will re-surface and cars will join the surface freeway. This is where Premier Crane’s 350-tonne crawler was stationed for nine months to assist the crew with the heavy lifts to help build the portal’s entrance.
As a preferred lifting partner for the project contractor, CPB John Holland Joint Venture (CPBJH JV), the Premier Cranes team has been heavily involved with the project from the first days on the project, helping with early site establishment works, utility service re-locations, and removal of existing steel gantries.
Premier Cranes also handled all of the heavy lifts around the construction of the southern and the northern tunnel portals which began in 2018 and are still ongoing.
CPBJH JV started construction at the westbound portal in 2018 with clearing and preparation work on the site, before starting excavation in 2019. Apart from building the tunnels’ walls using a bottom-up approach, the southern portal construction also includes building a collector distributor
Premier Cranes and Rigging handled all of the heavy lifts for the construction of the West Gate Tunnel’s northern and southern portals.
bridge to collect vehicles from Williamstown Road and merging them with the westbound freeway lanes to the west of the tunnel.
With the scope of the project involving a combination of precast installations and in-situ structures erected next to the busiest freeway in Melbourne, and with the excavation level more than 30 metres below the freeway, there were various intricacies involved in the project.
EARLY PLANNING The start and end of each tunnel is being built using the ‘cut and cover’ method. This involves excavating a trench and then covering it with a concrete deck to form a roof. The cut and cover structure for the southern portal is formed in three levels. The deepest end of the portal is where the tunnel boring machine (TBM) will be dismantled and retrieved after reaching the finish line. The main carriage way or the road level is built above this level, with two more levels constructed above the road level to house the tunnel’s ventilators.
The Premier Cranes team had begun planning the lifts for the southern portal months before Sam sat behind the ‘beast’ for that first lift. In fact, it started when the team was still working on the northern portal and they identified the need to purchase the 350T crawler crane specifically for that part of the project.
Premier Cranes’ Head of Sales, Travis Smith led the charge with acquiring the crawler crane and getting it to the project.
“We knew from the first day that the southern portal construction would be the most challenging,” he says. “Not only is the site located close to moving traffic and in a narrow strip, but we were also working alongside other civil construction teams on the site, so we wanted to make sure there was as little disruption to their works as possible.”
The Liebherr LR1350/1 crawler crane that the Premier Cranes team acquired, offered

Premier Cranes acquired the 350-tonne Liebherr LR1350/1 crawler crane specifically for the project.
The teams from Premier Cranes and CPBJH JV worked closely together on the project. Standing from the left: Aidan Winkler and Joshua Vassallo from Premier Cranes, Nat Lewis from CPBJH JV.
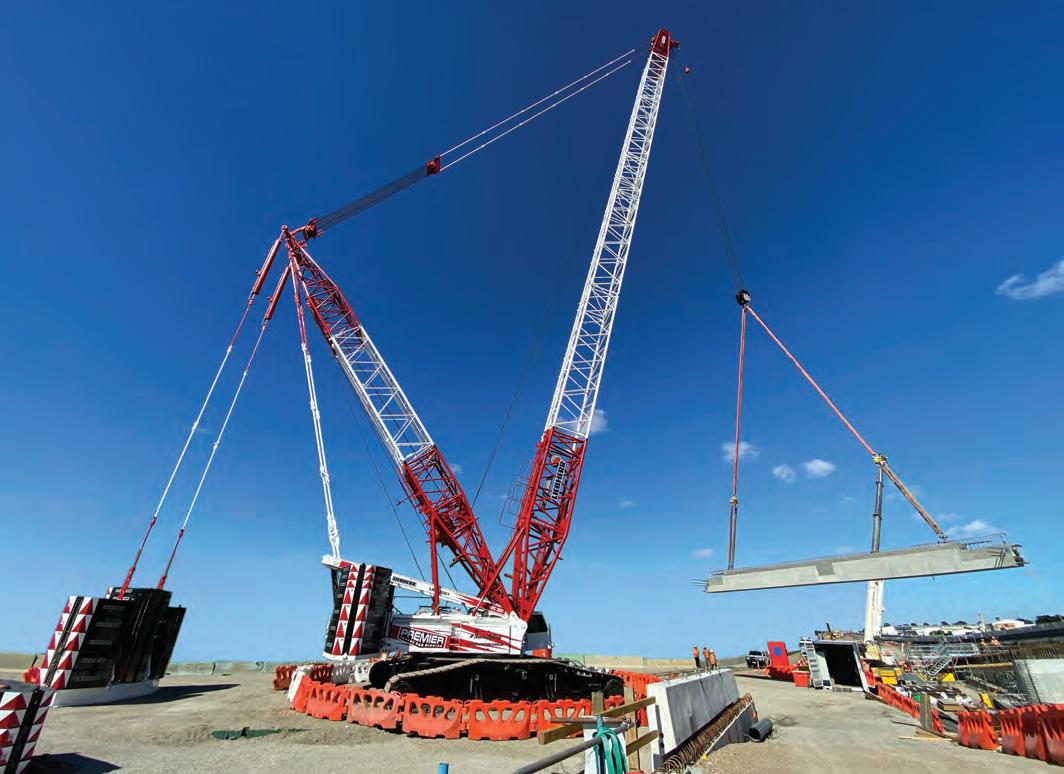
certain advantages that ensured a smooth operation. Among these, Travis says, the easier set-up for the super lift tray meant considerable time-savings by the team.
“The LR1350/1 is the top of its class in crawler cranes. The main advantage for us was the flexibility in setting up and attaching and detaching the super lift tray. We also did not necessarily have to level the tray for each lift, which saved us at least an hour every day. If you consider the savings over the duration of about nine months that the crane was on the project, it’s a lot of time and a lot of money saved,” says Travis.
THE CHALLENGES Though the Premier Cranes team ordered the crane early on in preparation for the task, getting the crane to the site was not easy. This was back in 2020 and COVID-related travel restrictions had just kicked in. Apart from some of the Premier Cranes’ operators having to work on rosters, this meant the team could not travel overseas to inspect the machine before the purchase.
“We had to invest more and rely on Liebherr specialised Mechanical Engineering inspectors overseas to check the crane and to ship it to the site. Around the same time, we began conversations with the CPBJH JV team to plan for when the crane arrived on the site. A crane that size, you can’t just roll it out. It took us about six months of planning and engineering calculations to make sure the base was ready to set-up the crane.”
Deciding where to position the crane was the next critical task.
Premier Crane’s Program Manager Renier Coetzee and his team worked closely with the CPBJH JV superintendents to identify the best location for positioning the crane to make sure all of the heavy lifts on the project could be handled without re-locating.
“We had to start early and work closely with the CPBJH JV team to plan all of the lifts beforehand. We were very keen on choosing a location for the crane so that the boom could reach all of the required locations, with minimal disruption for the other teams working on site,” says Renier.
Even after the crane arrived on site and was safely anchored to the ground, Sam and the team were conscious of operating the crane in the least disruptive manner.
“It takes a lot of negotiations to get things done right,” says Sam. “For example, the length of the crane’s boom is 72 metres, but it takes 80 metres to lay it all out when we were setting up the crane. I had to make sure that the boom was off the ground so that the other companies could access the area, so that everyone can achieve their work.” COLLABORATION IS KEY All of that collaboration between the Premier Crane team and CPBJH JV crew on the ground helped orchestrate the perfect lift plans, as Nat Lewis, General Superintendent for CPBJH JV, confirms.
“Nominating craneage and locations for that craneage, given the complex lifts in relatively small areas, has been a major challenge. Incorporating Premier Cranes in with our long-term planning process has been a critical link for the success of the project and it has emphasised the relationship and professionalism of the Premier Cranes’ team,” says Nat.
“Premier Cranes’ work is not confined to the southern portals. We have worked with them extensively on the project on either end of the tunnel zone and they have been managing the interface very well in both of those situations. The best thing about them is their flexibility. Their hands-on approach and the relationship of their on-site people with the relevant superintendents has made those complex lifts seem easy.”
Mitchell Lunt, Site Superintendent at CPBJH JV, concurs with Nat.
“Every lift undertaken on the job has required a significant amount of time and planning from both Premier Cranes and the CPBJH JV, in turn ensuring every lift was
The Premier Cranes and Rigging team handled loads up to 60-tonnes during construction of the southbound portal.
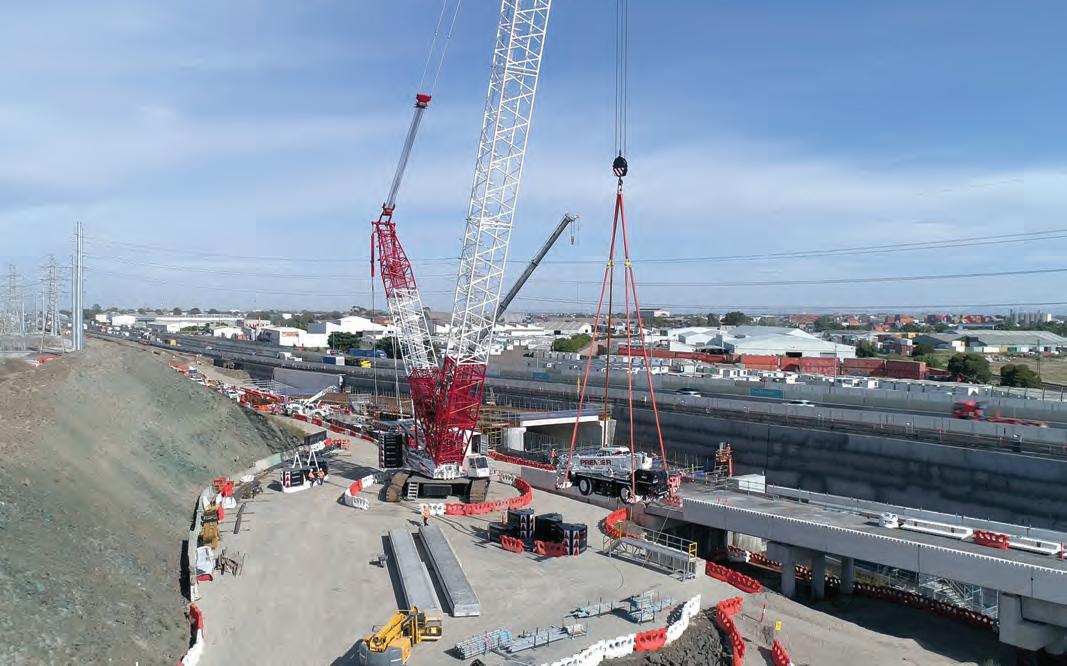
well planned, effectively communicated to all personnel involved and carried out in a timely and safe manner,” he says.
“Premier Cranes have always been easy to work with, well organised, highly experienced and always present in a very professional manner,” he adds.
IN THE SPIRIT OF #TEAMLIFTING For Steve Warton, Chief Executive Officer of Premier Cranes and Rigging, the level of coordination between the Premier Cranes’ team and their employer on the West Gate Tunnel project is what the company’s #TeamLifting tag is all about.
“We believe the project has been a success, not only from the timing point of view and the way the works unfolded, but because the performance of our crews and their interactions with the project team network showed how #TeamLifting actually works in action,” says Steve.
“As a company, our culture is driven by the #TeamLifting tag, which ensures that we approach every job with transparency, respect, candor and a can-do attitude,” he adds.
TBMs Bella and Vida, named after exceptional women Bella Guerin and Vida Goldstein, will start their journey at the northern portal in Yarraville and move southwest towards the southern portals on the West Gate Freeway near South Kingsville. Work will start on the four-kilometre outbound tunnel first, closely followed by the 2.8-kilometre inbound tunnel. The longer tunnel will take around 18 months to dig.
With the bulk of the heavy lifting now completed on the southern portal, Premier Crane’s Liebherr LR1350/1 crawler crane has already mobilised to the next project, but the team has stayed on the ground, helping in the hauls with their fleet of 200 and 250-tonne mobile cranes.
Since its inception, Premier Cranes and Rigging has grown its fleet of cranes, whilst supporting its clients on key projects, from civil and rail to bridges and precast.
Boasting a diverse range, from Liebherr All Terrain Cranes to three Franna AT20s and now the 350-tonne crawler crane, the company keeps upgrading its fleet. Simultaneously, Warton says the company has been successful in attracting some of the best talent in the field.
“By creating structured teams, both in the office and in the field, we have attracted, retained and empowered the talent to understand the unique needs of each job in their quest to offer holistic and optimal solutions for our clients,” he says.
Now, Premier Cranes is looking forward to even bigger projects and reaching new heights with each project, according to Travis.
“Every project we work on is trumped by the next one. Everything is getting bigger and bigger,” he says.
As for the 350-tonne Liebherr LR1350/1 crawler, it’s become “hot property” in Melbourne, Travis says.
“This is now one of the busiest cranes in Melbourne!” Travis says. “With the way the infrastructure sector is going, and with Premier’s #TeamLifting approach, we are planning works with major contractors on some of the largest projects in Melbourne.
“There’s also still a lot of lifting to cover on the West Gate Tunnel Project and we will continue to collaborate on the job until we get the result for CPBJH JV.”
AUSTRALIA’S NO.1 WHEELED EXCAVATOR JCB HYDRADIG
Contact your local dealer today 1300 522 232 www.jcbcea.com.au

The JCB Hydradig is a ground-breaking sorting, lifting, loading and tool-carrying machine for a wide variety of operations. Its low centre of gravity allows for stable lifting while working at full reach, and its two and four wheel steer and crab steering delivers maximum usability on the smallest of job sites. With ground level access to all maintenance points and a lift-up engine canopy providing excellent access to the engine and filters, servicing and maintenance can be carried out with ease.