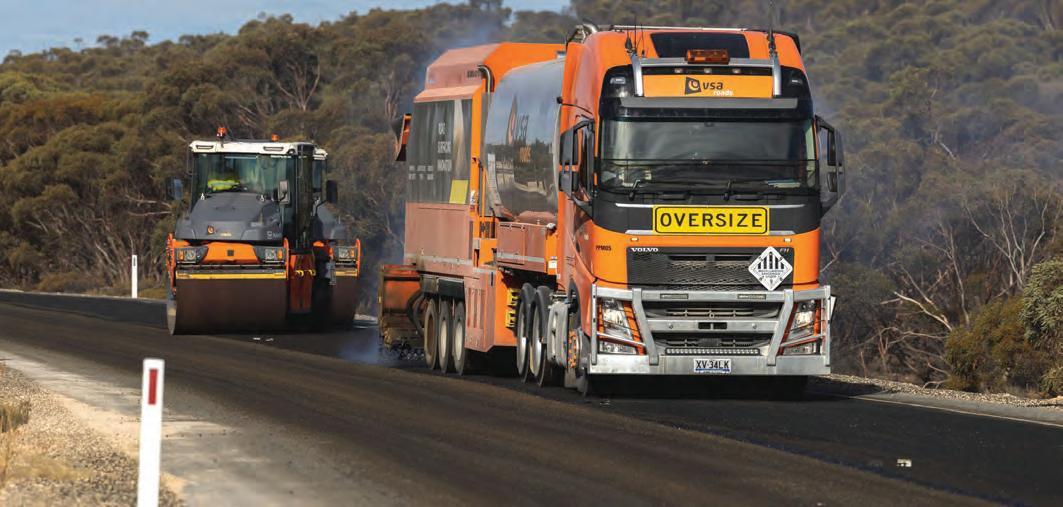
5 minute read
Innovation meets SAMI
INNOVATION
MEETS SAMI
SAMI BITUMEN’S INNOVATIVE LOW-VISCOSITY CRUMB RUBBER BINDER IS HELPING THE VSA GROUP CARRY ON SEALING IN THE COLDER SEASON, WITHOUT USING KEROSENE CUTTERS. ROADS & INFRASTRUCTURE LOOKS AT THE BENEFITS GAINED ON A RECENT PROJECT IN SOUTH AUSTRALIA.
Pinnaroo is the gateway to South Australia when travelling from Victoria and New South Wales on the Mallee Highway. The township was recently the site of a breakthrough highway resealing project conducted by Primal and InRoads – both part of the Victorian Sealing Alliance (VSA) – in collaboration with SAMI Bitumen Technologies.
The work, which involved resealing on 115 kilometres of the Browns Well and Karoonda Highways for McMahon Services team, was unique in many ways. Firstly, resealing was carried out during April and May, a time of year when traditional resealing often poses quality and environmental risks due to cool climatic conditions. The project was also significant for its environmental and safety benefits, with no kerosene cutter used in the spray sealing process.
These, and other efficiency and environmental gains on the project, were made possible through what SAMI Bitumen Technologies’ Technical Services Manager Iulian Man refers to as a case of “double innovations.”
Primal and InRoads were adopting their German-built synchronised bituminous surfacing technology, called the OBV production unit, on the project. The OBV technology, which the VSA team has been using on a variety of pavement projects in Australia over the past year, offers an innovative alternative to the traditional reverse aggregate spreading technique.
In 2017, the State Road Authority of Victoria mandated against the ongoing use of reversing aggregate spreader trucks on spray sealing worksites due to several significant safety incidents. Whilst much of the surfacing industry subsequently focused on re-engineering the task of spreading aggregate in a forward direction by placing spreader boxes on the front of trucks, VSA Roads adopted a holistic approach by using the OBV production unit to deliver a safer and more sustainable surfacing solution.
The OBV technology offers significant safety advantages by eliminating the use of reversing tippers, minimising the number of plants on the jobsite – thus reducing the risk of collision – and operating at a reduced speed. The OBV also provides environmental benefits by eliminating the use of hazardous cutback bitumen, the need for stack sites on the edge of the road and significantly reducing aggregate wastage.
Though adopting the OBV unit provided the VSA team with numerous safety and efficiency gains, the other aspect of the double innovation was the binder material used by the OBV crew.
While traditionally kerosene cutters have been introduced at high temperatures to reduce the viscosity of crumb rubber binders in cool periods of the year, the VSA team
VSA Roads uses the OBV technology for spray sealing, which eliminates the use of reversing tippers.
adopted a purpose-manufactured, lowviscosity version of SAMI’s S45R crumbed rubber binder, called S45R-LV, to help eliminate the use of kerosene cutters on its projects.
The break-through SAMI product paves the way for using crumb rubber from end-of-life tyres without having to cut back the viscous binder with kerosene to be able to spray it.
In the Pinnaroo project for example, 1.7 million litres of SAMI’s cutter-free S45RLV crumbed rubber binder was sprayed to cover an area of 789,000 square metres. This helped recycle 40,000 old tyres, which were used to produce 260 tonnes of rubber material.
SAMI’S INVOLVEMENT Brad Richards, SAMI Bitumen Technologies’ State Manager for the Southern Region, says the project is ground-breaking, not just for eliminating the use of cutters and reducing aggregate wastage, but for what it signifies in terms of extending the spraying season.
“The OBV technology drops the aggregates so close to the sprayed binder that it makes the process less susceptible to the cold temperatures. This means you can start spraying earlier, and you can keep spraying later in the season,” says Richards.
Over the past 12 months, SAMI has supplied the S45R-LV binder to VSA for several reseal projects in Victoria and New South Wales, but this was the first time an operation was completed in South Australia. The longer distance from SAMI’s production facility in Laverton to the project site meant the team had to make special provisions to maintain
SAMI’s S45R-LV crumbed rubber binder eliminates the use of kerosene cutters in cold season. “IN THE PINNAROO PROJECT, 1.7 MILLION LITRES OF SAMI’S CUTTER-FREE S45R-LV CRUMBED RUBBER BINDER WAS SPRAYED TO COVER AN AREA OF 789,000 SQUARE METRES. THIS HELPED RECYCLE 40,000 OLD TYRES, WHICH WERE USED TO PRODUCE 260 TONNES OF RUBBER MATERIAL. ”
the binder temperature and properties during delivery, Richards explains.
“To satisfy the Department for Infrastructure and Transport in South Australia, a sample of the product was taken and tested at the point of spraying. To do that, SAMI set up a mobile testing laboratory in Pinnaroo with the cooperation of the Pinnaroo local council, who let us use one of their sheds in the council depot. We used some of our spare equipment and an experienced laboratory technician to set up a mobile testing facility on the site,” Richards says.
“This was a first time that SAMI Victoria had to set up a mobile testing facility, though it is done in other states where our products are sent to remote areas. So, the product was tested here at the plant when it was manufactured, then it was sampled and tested as we loaded the tankers and then again sampled and tested at the point of delivery,” he adds.
OPENING NEW OPPORTUNITIES With the safety and environmental benefits offered by the SAMI S45R-LV binder and VSA’s OBV technology, Sylvain Clement, VSA Bituminous Surfacing Manager, is excited about future projects.
“Moving away from cutback bitumen is one of the greatest challenges for the Australian spray sealing industry and would lead to significant safety improvement whilst reducing its environmental impact,” he says.
“During the Pinnaroo project alone, over 100,000 litres of cutter material was saved in comparison to conventional spray sealing methods, thanks to S45R-LV and the OBV technology,” he says.
The VSA Group has already sprayed over five million square metres of surface with their OBV unit in the past 12 months and they are continuously monitoring the performance of the resealed roads. So far, Clement says the feedback from the industry has only been positive.
“We are still monitoring the road condition, but so far, we have received very positive feedback from our client in South Australia. The seal is performing as expected, with a great surface texture and aggregate retention,” he says.
“This initiative supports the industry’s drive to eliminate the use of volatile cutters in the spraying of hot binders. This is a win-win for the environment and worker safety. This project was a great opportunity to work in South Australia, where further opportunities were flagged by the Department for Infrastructure and Transport as part as its maintenance strategy for the rural road network.”
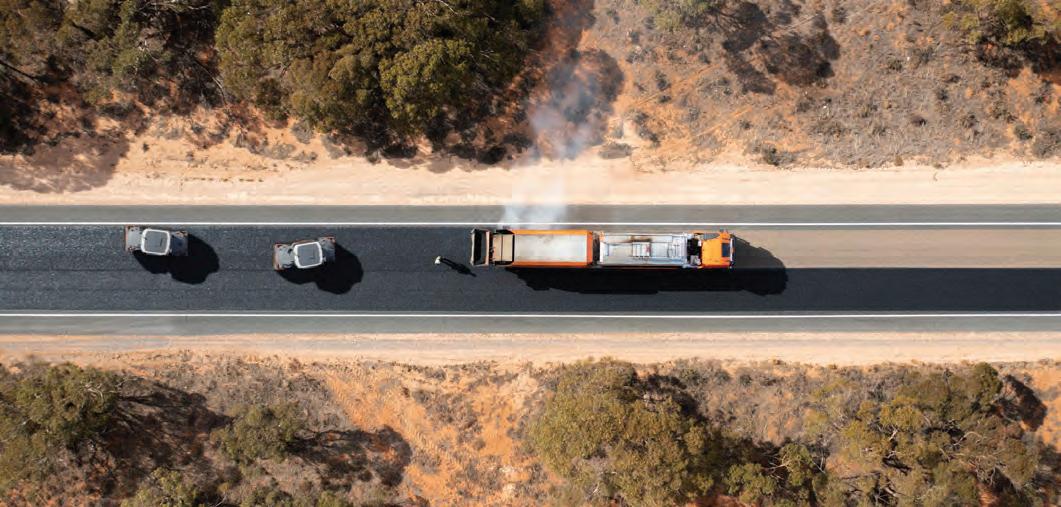