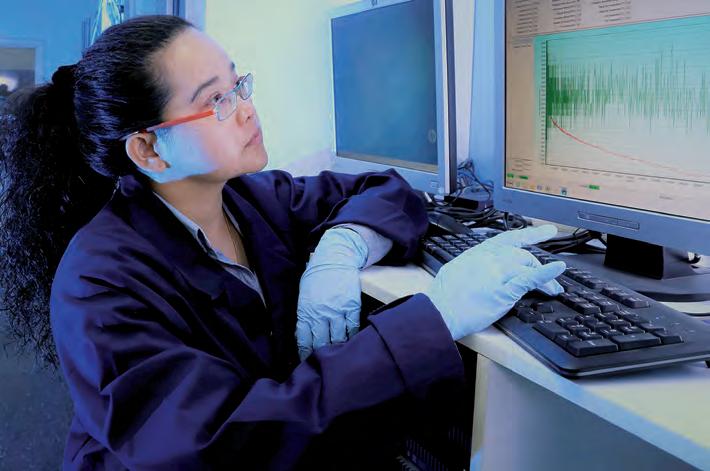
7 minute read
Bituminous binders of tomorrow
CREATING THE BITUMINOUS BINDERS OF TOMORROW
ROADS & INFRASTRUCTURE SITS DOWN WITH SAMI BITUMEN TECHNOLOGIES’ NATIONAL R&D AND LABORATORY MANAGER KANJANA YINDEE TO TALK ABOUT INNOVATIONS IN THE WORLD OF BITUMINOUS BINDERS AND EMULSIONS.
SAMI Bitumen Technologies has been at the forefront of innovations in the world of bituminous binders and emulsions in Australia since its establishment more than 40 years ago.
The SAMIfalt I-Brid hybrid binder is one such example. Developed in collaboration with the RMIT University, SAMIfalt I-Brid combines plastomeric and elastomeric polymers, resulting in a binder with both high deformation and fatigue resistance over a wide spectrum of traffic loading and ambient conditions.
Dubbed as the ‘universal binder,’ SAMIfalt I-Brid is a next generation type of binder which has at its foundations the concept of hybrid co-polymerisation, with the base polymers acting synergistically to impart exceptional deformation resistance and resilience to the binder.
Developed two years ago, SAMI has successfully trialled the SAMIfalt I-Brid binder with outstanding performance benefits at two projects, first at Bundaberg Airport in June 2020 and more recently at Bendigo, Victoria in March 2021.
Over the years, SAMI has also been introducing a range of emulsions that help eliminate or minimise use of petroleumbased solvents and cutters in asphalt and spray seal applications.
SAMIBond 007 – the winner of this year’s Innovation Award at the Australian flexible Pavement Association’s 2021 State Industry Awards in Western Australia – is a trackless cationic bitumen emulsion that ensures good bonding between the base course and the asphalt overlay.
SAMI’s crumbed rubber modified binders such as S45R-LV enable contractors to continue spray sealing in the colder season without using cutters. BioPrime, another innovation by SAMI Bitumen Technologies, is an environmentally friendly prime coat emulsion that contains no petroleum solvents. More recently, SAMI developed SAMIfloat, a cationic high float emulsion that can replace conventional standard emulsions for spray sealing applications for use in the construction of graded and conventional emulsion seals with dusty aggregates.
Kanjana Yindee is the manager of SAMI’s central technology R&D laboratory in Camellia, New South Wales. THE JOURNEY TO INNOVATION SAMI Bitumen Technologies’ innovative products are developed at research and development laboratories across different states, all of which are coordinated by a team at SAMI’s central technology R&D laboratory in Camellia, New South Wales. Managing the SAMI’s R&D laboratory teams is Kanjana Yindee.
With a background in chemical and environmental sciences and currently undertaking her PhD studies in civil and infrastructure engineering at the RMIT University, Yindee says developing ecofriendly binders and emulsions is a major focus for the team.
Having spent most of her career working as researcher with companies within the Colas Group, starting with Tipco Asphalt in Thailand, then with Colas in Australia and Mauritius and finally with SAMI in Australia, Yindee says she has enjoyed being part of the innovative journey with SAMI.
“SAMI’s products are developed either as responses to market needs, or as expansions of our product range based on recommendations from the internal team. Our social responsibility is reflected in all new product developments to make sure we are contributing to safe and sustainable technologies,” she says.
Yindee says every product developed in the research lab gets tested, first at the yard within one of SAMI’s plants, and then applied in road projects, usually by the Colas Group.
“There is generally a lot of interaction between plant managers and the quality teams at each plant. Any product developed by the ‘binders’ team gets tested by the ‘asphalt’ team. After an initial pre-screening check, we do a long series of tests and trials with different raw materials and once we are happy with the formulation, we conduct the first trail in one of the plants. If we are happy with the initial trial, we then talk to
contractors, both internal and external, to bring the product to the road and trial it at a bigger scale.”
An example, she notes, is how SAMI’s trackless tack/bond coat SAMIbond 007 emulsion was developed.
SAMIbond 007 is a specialised emulsion that resists being picked up from the paving traffic, therefore guaranteeing that the residual binder provides maximum bonding between the asphalt base course and the wearing course while in service.
Yindee says the SAMI team of researchers conducted numerous iterations to develop the formulation for SAMIbond 007, with specialised testing being undertaken at the laboratory level.
“Samples of the product were initially assessed on a small scale and following encouraging results, the next step was that SAMIbond was to be trialled at a larger scale, with a specialised sprayer truck at our facilities in Sydney. With the expected performance being met, the final step was to launch SAMIbond onto the market with various contractors successfully using it over the last two years on asphalt resurfacing projects, such as airports,” she explains.
Being part of a global infrastructure group like Colas has also benefited SAMI from the perspective of technology transfer and worldwide expertise within the group.
A good example in this is the transfer and the adoption by the Australian road authorities and industry of the EME2 technology, a technology developed in France by Colas at the beginning of ‘90s. By investing in technology at an industrial scale on a national basis, such as specialised bitumen oxidisers, SAMI has been playing a central role in transferring and implementing the EME2 technology in Australia.
TOWARDS GREATER SUSTAINABILITY In line with its mission to introduce more eco-friendly paving products in Australia, Yindee says SAMI is pursuing this strategy from many fronts.
“One of the things we are trying to convince the people in the industry is that they can replace the conventional hot binders used in spray sealing with suitable emulsions. SAMI’s PMB emulsions such as SAMIflex HR and the newly developed SAMIfloat emulsion are examples of products that contractors can use in their projects to improve their sustainability rating and improve safety level at the same time,” she says.
Emulsions and primers incorporating biodegradable raw materials are also on the table for SAMI.
“Designing emulsions is a bit of an art,” says Yindee. “It can be very challenging to design a material that is both environmentally friendly and has all the performance properties you are looking for. A product like SAMI’s BioPrime, which is used for the priming of granular base courses, uses biodegradable raw materials that contain no petroleum solvents that have flammable vapours,” she adds.
Being a priming product that doesn’t contain any hydrocarbon solvents, as opposed to the standard cutback primers, SAMI’s BioPrime allows safe usage, without exposing workers to fumes during the priming process. Being solvent-less, it is also environmentally friendly as no flammable or harmful volatiles are being emitted into the ambient during application.
Another added benefit of SAMI BioPrime is the ability of the contractors to complete the sealing operation within a single shift with positive outcomes regarding productivity, Yindee explains.
“Being a solvent-less primer, they do not have to wait for the solvent present in the standard cutback primers to evaporate prior to the application of the seal over it.”
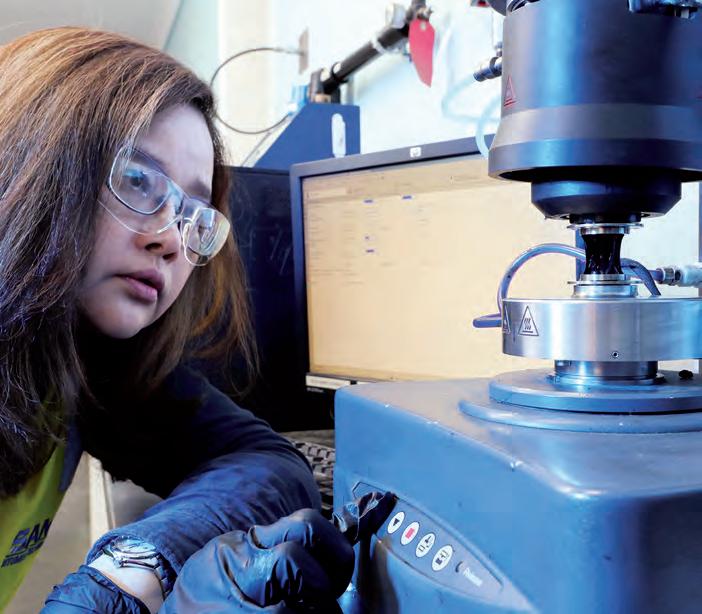
THE ROAD AHEAD Going forward, Yindee says SAMI will keep on developing products with a view to remain competitive, but also to enhance the level of sustainability within the paving industry.
Incorporating more recycled waste in the asphalt hot mix is one process towards which SAMI is actively contributing.
“We are working extensively on incorporating waste plastic and other recycled material into our binders for asphalt, blending it with the hybrid technology to get more recycled products into the pavement,” says Yindee.
Additionally, Yindee says SAMI’s focus is on improving efficiency of application.
“For example, a product like SAMIfalt I-Brid is a highly engineered binder. By employing the hybrid concept, you can achieve all those properties like high rutting resistance and the high flexibility. By using a product like that, you are extending the life of the road, which means it requires less maintenance and therefore less energy spent in the long term.”
The next step, she says is to try to incorporate recycled materials, like crumbed rubber and plastic waster, under the hybrid concept.
“The next step is to develop new version of hybrid binders by using recycled waste materials as we want to maximise the use of plastic waste in our products. It can be blended with virgin polymers and/or with another recycled material like crumbed rubber under the same hybrid concept.”
Developing eco-friendly binders is a major focus for the research team at SAMI.