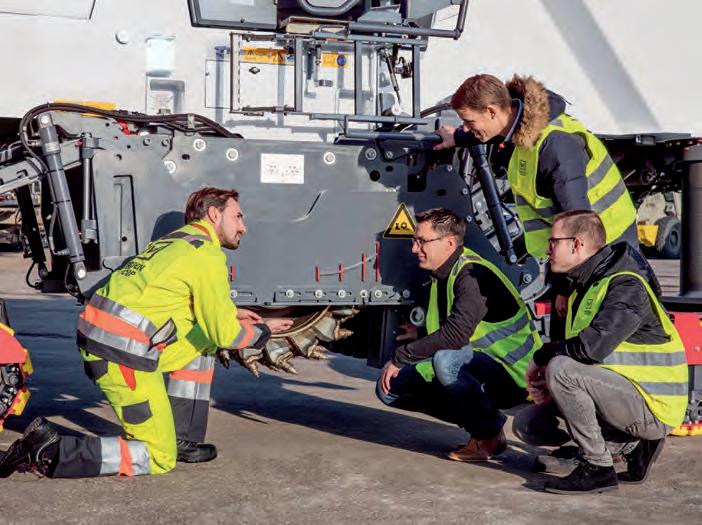
7 minute read
Pre-casting with a purpose
TRAINING TAILORED
FOR OPERATORS
WIRTGEN’S SPECIALISED TRAINING PACKAGE FOR THE OPERATORS PROVIDES CUSTOMISED TRAINING ON ALL ASPECTS OF OPERATING AND MAINTENANCE FOR EXISTING AND NEW WIRTGEN CUSTOMERS.
In the famous quote from international sales expert Trish Bertuzz, the CFO asks the CEO, “What happens if we invest in developing our people and they leave us?” to which the CEO responds, “What happens if we don’t, and they stay?”
Within the road paving industry, where careful and considered selection and purchase of equipment sometimes marks the difference between winning or losing a contract, much attention is diverted towards acquiring the latest equipment.
And while that’s an important part of the process, it could steal some of the attention away from ensuring the people that operate the equipment are suitably skilled and trained.
But, as Stuart Torpy, Managing Director at Wirtgen, points out, undue attention given to training and upskilling the operators can cost civil and construction companies as they suffer the consequences of poor-quality jobs.
“There is no doubt that training comes with a price tag, and hence finding cost effective ways to raise the skill levels of those trained is of utmost importance. Of course, the cost of re-work or injury arising from preventable but flawed work practices or actions may be less obvious but would easily outweigh the direct, indirect, and reputational costs of onthe-job issues,” he says.
Recognising the challenges and drivers facing businesses when it comes to training of field crews, Wirtgen has developed an extended training offering to users of its products.
“Customers who purchase any new Wirtgen Group equipment, whether that be Wirtgen stabilisers and cold milling machines, Vögele pavers and transfer vehicles, Hamm rollers and compactors, Kleemann crushers and screens or Ciber and Benninghoven asphalt plants, automatically qualify for a tailored training package beyond the initial commissioning,” says Torpy.
“Moreover, existing Wirtgen Group equipment owners can also request customised training to keep their staff up to date with the latest features and upgrades. Whilst the majority of our training courses are tailored around Wirtgen Group machinery, we do offer application related programs that can benefit the individual in increasing their knowledge and/or employability throughout the roads and minerals sector,” he adds.
A 100 PER CENT TAILORED TRAINING Wirtgen offers both general and detailed content-specific training for the activities undertaken by the crews operating Wirtgen Group equipment using combinations of inclassroom, hands-on practices, and on-thejob learning modes.
Chris Adams, Wirtgen Australia’s Service Manager for Australia and New Zealand, says the Wirtgen training program has become more and more customised over time. As such, the courses can be tailored to each business based on their machine models, operator experience levels and whether training is required for the operational or the maintenance staff.
“We have found that the majority of our customers prefer a customised training program. That’s because their crew have different experience levels and also, as is the case with some companies, they require their operators to have some level of maintenance and repair knowledge. So, while we still have a general training package, this is often combined with different contentspecific training to deliver the most optimum package for each customer,” he explains.
Traditionally, Wirtgen product managers and technicians have provided training either on the business’ site, a Wirtgen facility throughout Australia and New Zealand or at
The Wirtgen training program is ideal for anyone that directly works with Wirtgen Group machinery.
its CTT (Centre of Training and Technology) in Germany or the US.
With limitations around international and inter-state travel over the past year due to COVID-19-related restrictions, Adams says the Wirtgen team has adapted the training accordingly.
“Over the past year, we have performed various virtual trainings, with our product managers across every state travelling to the business’ site where possible to conduct face-to-face training. In one recent example, our product manager attended the customer’s yard and trained 30 staff members with hands-on training on their Wirtgen profiler. In another instance, a local Wirtgen technician was present with the machine, providing a live feed view via camera whilst the trainer instructed a seated class over video conference,” Adams says.
“Eventually we are looking at adopting technologies such as digital glasses, so that the trainer receives a live feed while a local technician looks at the key areas around the machine. This interactive scenario will help not just with the training but comes with other benefits for machine maintenance and fault detection,” he adds.
With the Wirtgen Group perpetually introducing new machines and advanced technologies, Adams says the team have been very busy training Wirtgen’s existing and new customers on the new Wirtgen milling machines, including the two-metre F Series recently rolled out in Australia and New Zealand.
“For any new product that’s purchased, we do offer a thorough training with the machine. Our product managers are currently busy providing both virtual and hands-on trainings. We have a minimum requirement of three attendees and recommend a maximum no more than 10 people. Depending on whether the customer has already held the model in their fleet or not, the trainer will commonly provide anywhere from one to five days for the training,” says Adams.
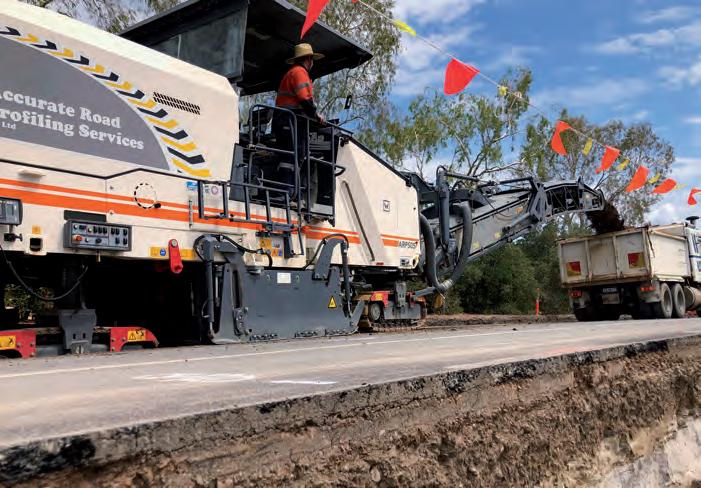
ACCURATE ROAD PROFILING SERVICES Accurate Road Profiling Services is a business based on the northern side of Brisbane, providing road profiling and associated services to the asphalt and construction industry.
Since establishing in 2016, the company has built a fleet of nine Wirtgen milling machines and 18 full-time operators and been involved with multiple patching and overlay projects across Queensland.
Recently, Accurate Road Profiling Services bought a new two-metre Wirtgen W210Fi milling machine featuring the Wirtgen Performance Tracker – a sensor-based Wirtgen technology that makes it possible to accurately and reliably document actual milling work completed. The company also had half of its existing Wirtgen milling machines retrofitted with the Wirtgen Performance Tracker, with the intention to retrofit all machines in the near future.
Director Keith Baines says the reason for upgrading the machines was to be able to track and report the pavement treatments to customers, as well as to improve knowledge of truck loading volumes and the milled areas.
“We currently service our customers with a range of Wirtgen milling machines including W100CF, W200, W200Hi, W210XP and W210Fi. Our team strives for the best results each time customers engage them. As such we are considered by many businesses as being part of their team leading to greater results for all involved,” he says.
Following the purchase of the new Wirtgen W210Fi milling machine with the Wirtgen Performance Tracker, all operators at Accurate Road Profiling Services underwent on-the-job training by Wirtgen trainers to learn about the latest features.
The delivery, Baines says, was “outstanding.”
“We jumped at the chance of receiving Wirtgen specialised training,” he says.
“Wirtgen’s specialists did an awesome job of explaining the features and operation of not only the W210Fi, but also the Wirtgen Performance Tracker installed on this machine.”
Ultimately, Torpy says Wirtgen’s goal is to ensure that all its customers get the absolute best out of the Wirtgen Group equipment they operate.
“Our support structure has been built around the objective and hence we have the expert knowledge and resources locally, in each operating location and with product specialists for each brand all based in Australia and New Zealand. Whilst trainers can and are invited from the brand headquarters in Germany, they are a ‘sometimes’ resource for local training,” he notes.
“Wirtgen’s capabilities don’t stop once you’ve bought a machine. On the contrary we’d like to think that the after-sale offerings are considered at least equal to those of the machines themselves.”
Tospy encourages customers to consider refresher training for their teams.
“We make a lot of offers to come and provide refresher training, not just on the machines themselves, but also the applications in which they’re put to work. But I’m always surprised at the lack of take up.
“If we can save an owner 30 minutes a day, avoid a high hazard practice or reduce fuel burn by 10 per cent a shift through better practice – that quickly adds up and can be the difference between winning or losing work. Like every business, there’s always gains to be made, however small, and we want to be part of the team that delivers them through training.”
For more information on Wirtgen’s training programs visit: www.wirtgen-group.com/enau/customer-support/training
Accurate Road Profiling Services’ operators received on-the-job training by Wirtgen on the new W210Fi milling machine.