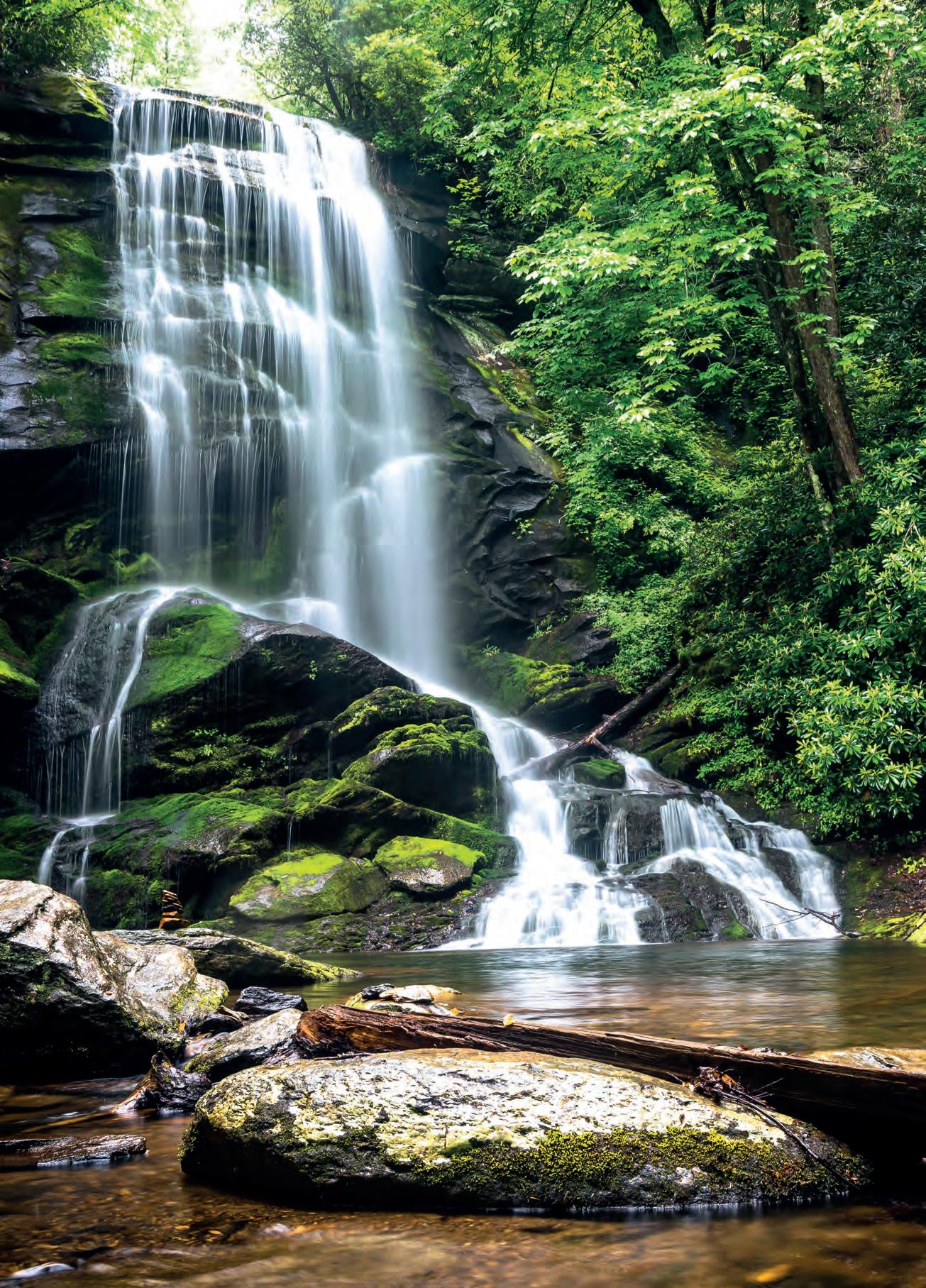
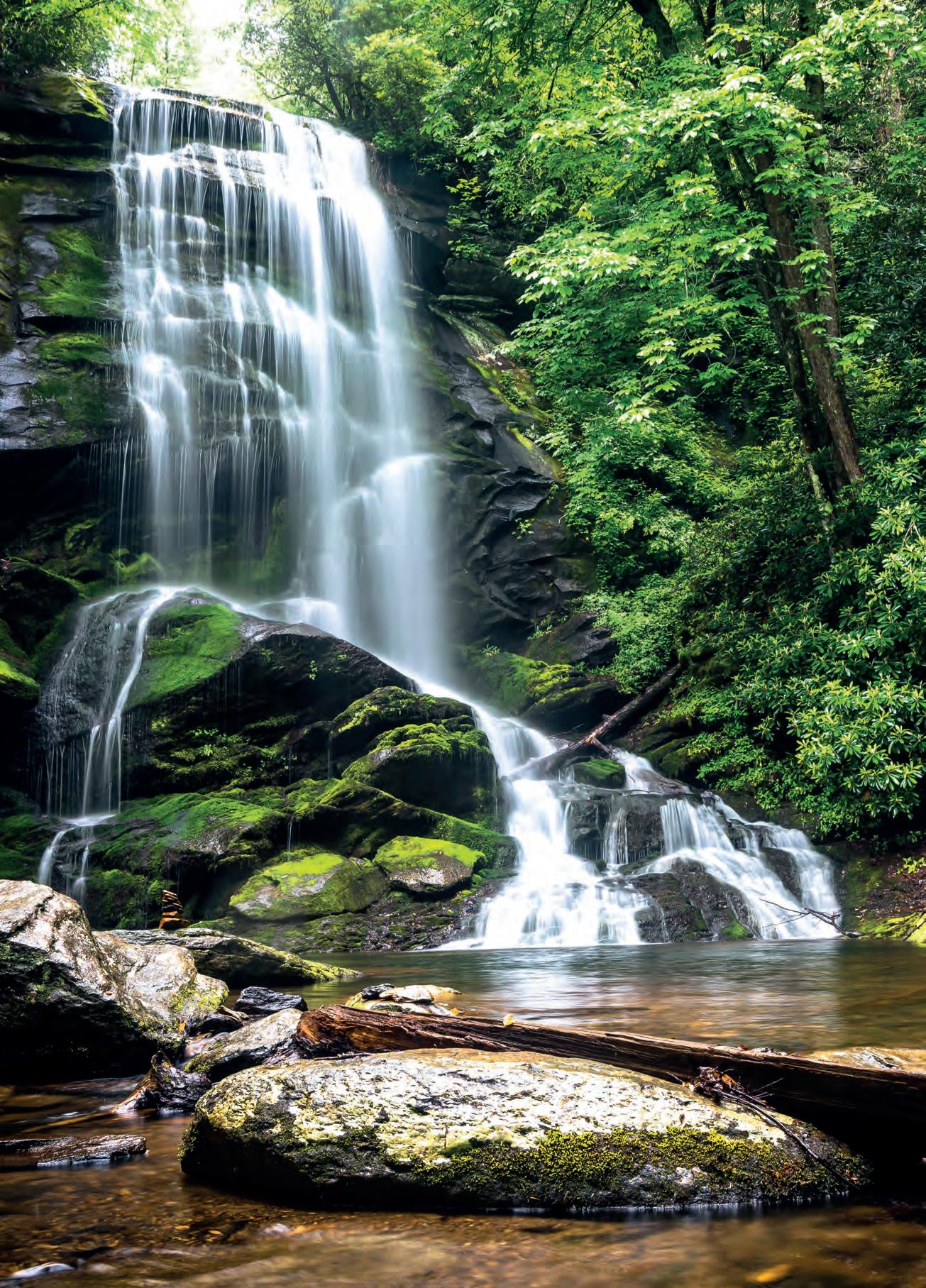
STAY
One of the world’s largest construction equipment manufacturers is eyeing further expansion across Australia
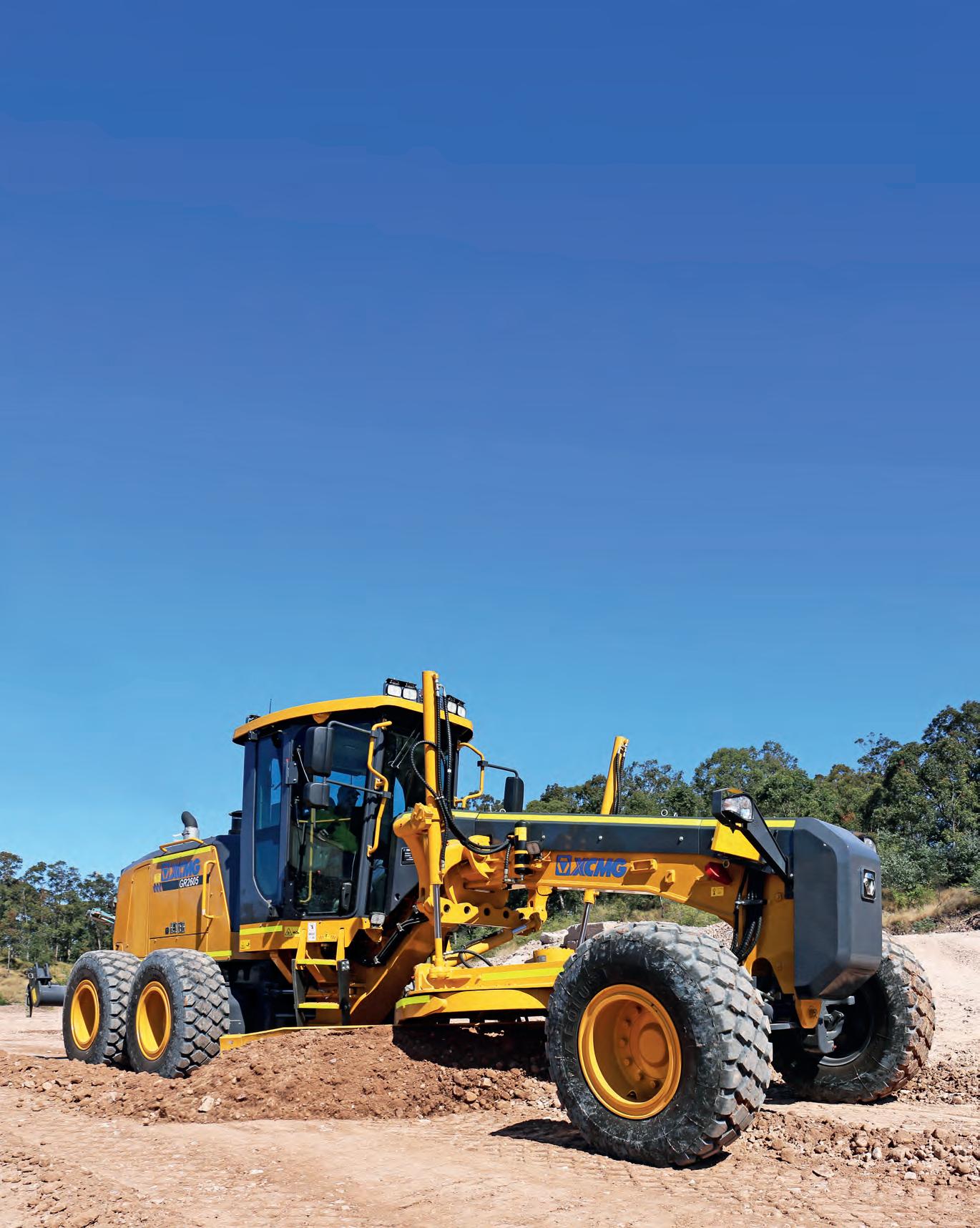
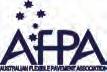
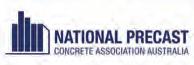
A SUSTAINABLE ‘MASTER’ CLASS
A brand-new range includes world-first materials and processes to support sustainable infrastructure development
SAVING LIVES SUSTAINABLY
A greener alternative to traditional road barriers has been found to be more sustainable, while outperforming and outliving conventional designs
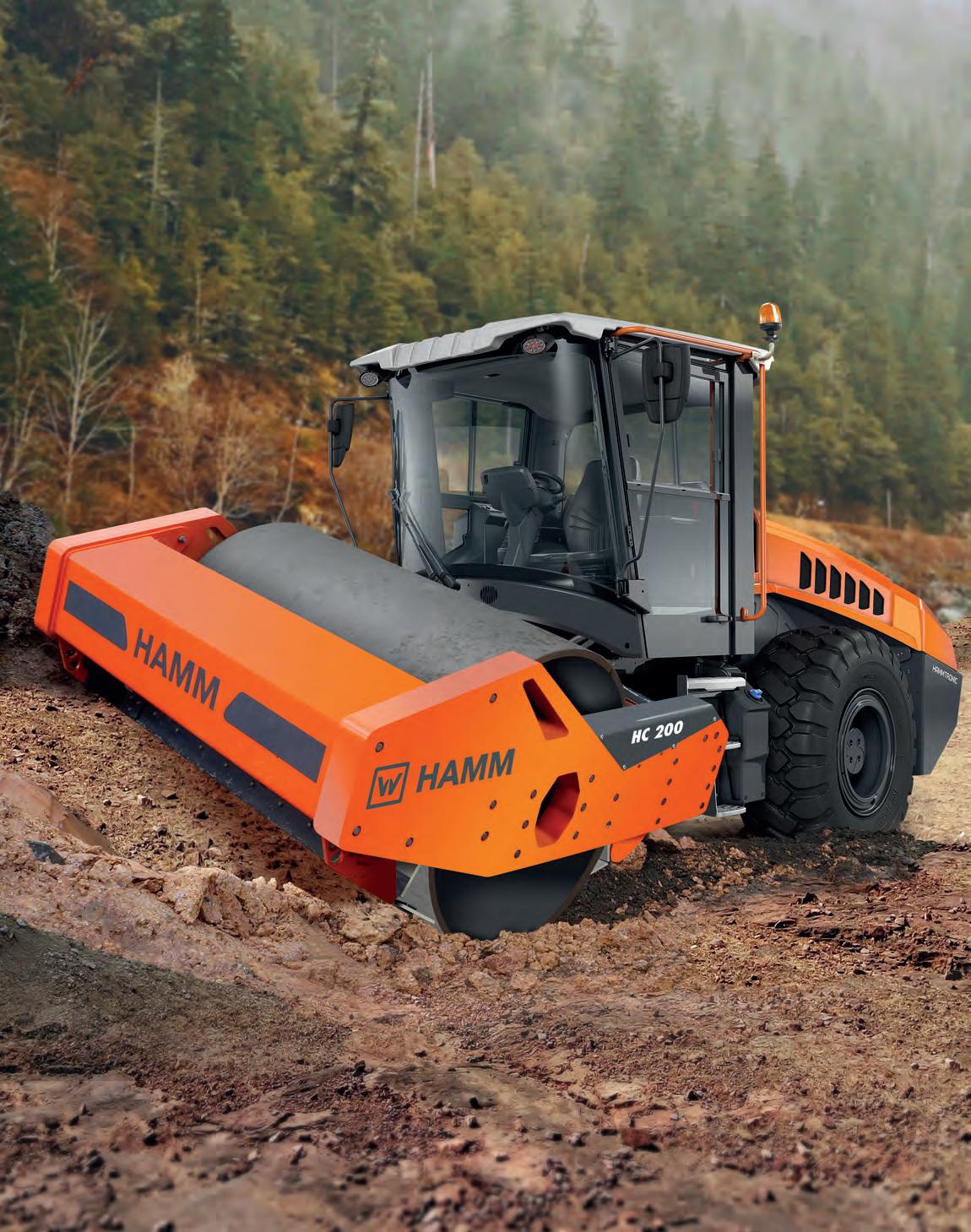
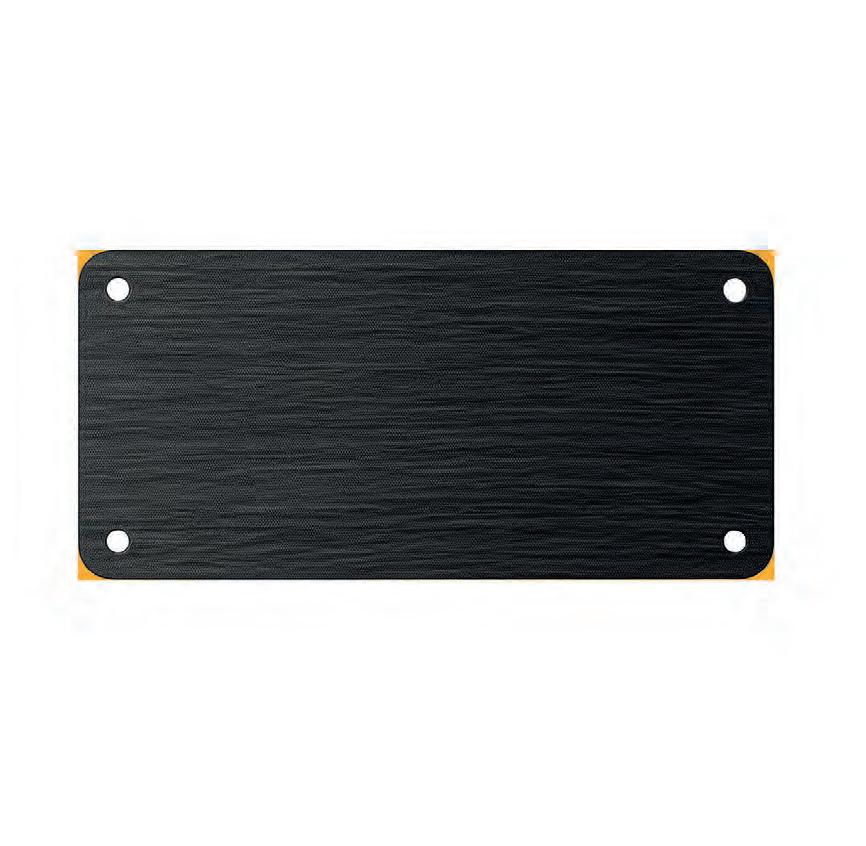
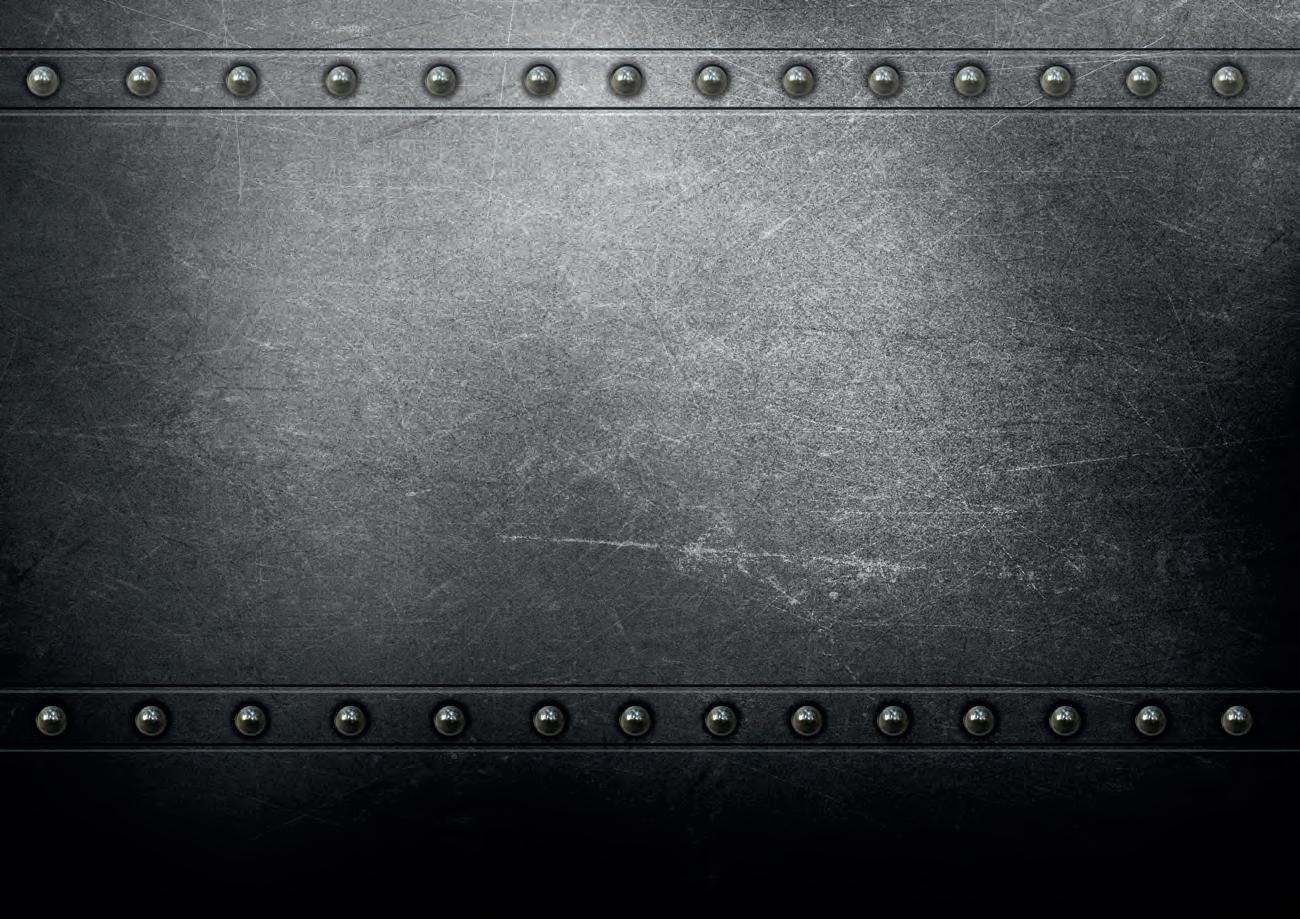
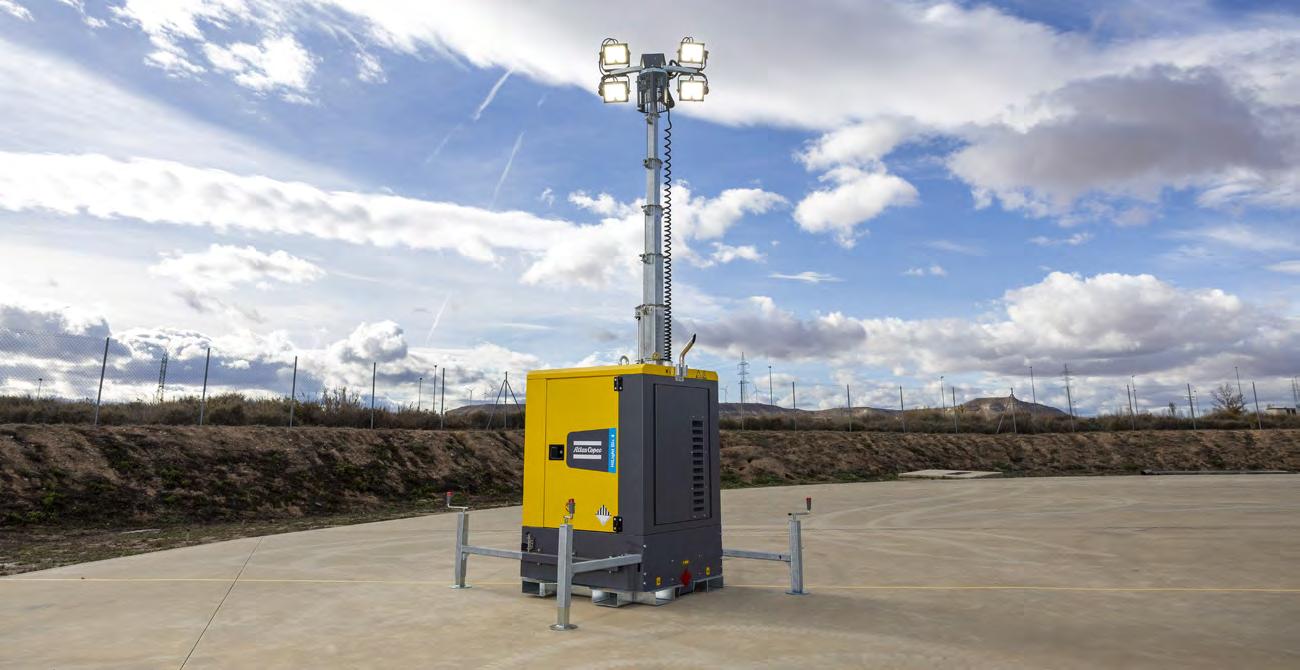
COVER STORY
6 Here to stay XCMG is synonymous with its Chinese origins, but in the past few years the company has been knocking louder on the door of the Australian market.
ROADS REVIEW
10 We asked the industry, ‘Despite ongoing industry challenges, what innovations or achievements are giving you optimism for the sector’s future prosperity?’
COMPANY PROFILE
12 Challenges and triumphs
R&S Grating’s story and ongoing success can predominantly be attributed to the company’s commitment to family, and the legacy of its past leaders.
SUSTAINABILITY
16 A masterclass in sustainability
Continual innovation and a commitment to community has led to a brand new, worldfirst development from Hiway.
19 Saving lives sustainably
The ArmorZone temporary barrier is not only more sustainable than conventional road barriers, but it’s also proven to outperform
PROJECT REPORT
24 The future of rollers In striving for optimum sustainability, Transport for NSW has tendered 38 Soil and Asphalt Dynapac double drum rollers.
TECHNOLOGY
26 Data done right
National civil engineering provider Civiltech Solutions has released its latest road data tracking innovation.
29 Optimising infrastructure design Automation and positioning technology provider Aptella has acquired Synergy Pavesmart, a paving services business.
32 Lighting the way
Orca Solar Lighting is distinguishing itself as a premium provider of solar lighting solutions for the road and rail sectors.
35 Your eye in the sky
Komatsu’s Smart Construction Edge 2 platform is transforming conventional surveying methods, offering a more efficient and safer alternative.
MACHINERY & EQUIPMENT
38 Getting the job done Holz Heavy Haulage has long used TRT trailers as a vital component in delivering its transport services.
41 Years in the making Primal Surfacing continues to benefit from Specialised Roading Equipment’s service.
44 Changing lanes
Hitachi Construction Machinery is expanding its wheel loader range, developing a line suitable for infrastructure and rail works.
47 One direction for safety
Quality Fabrication & Engineering’s Road Ant is helping to inspire the development of safer and more sustainable road construction machinery.
51 New names, same quality
Caterpillar is renaming several machines in its vibratory soil compactor range as part of a renewed approach to its nomenclature.
INNOVATION
55 Innovation for all Madison Express continues to innovate in the infrastructure space for the betterment of the entire sector.
EVENTS
57-58 A rundown of a number of upcoming events worth keeping an eye on.
ASSOCIATION SECTION
59-61 Hear from leading industry associations on the matters affecting the sector right now.
CONTRACTS
62 Roads & Infrastructure Magazine provides an update on some of the contracts and tenders recently awarded or put to market across the sector.
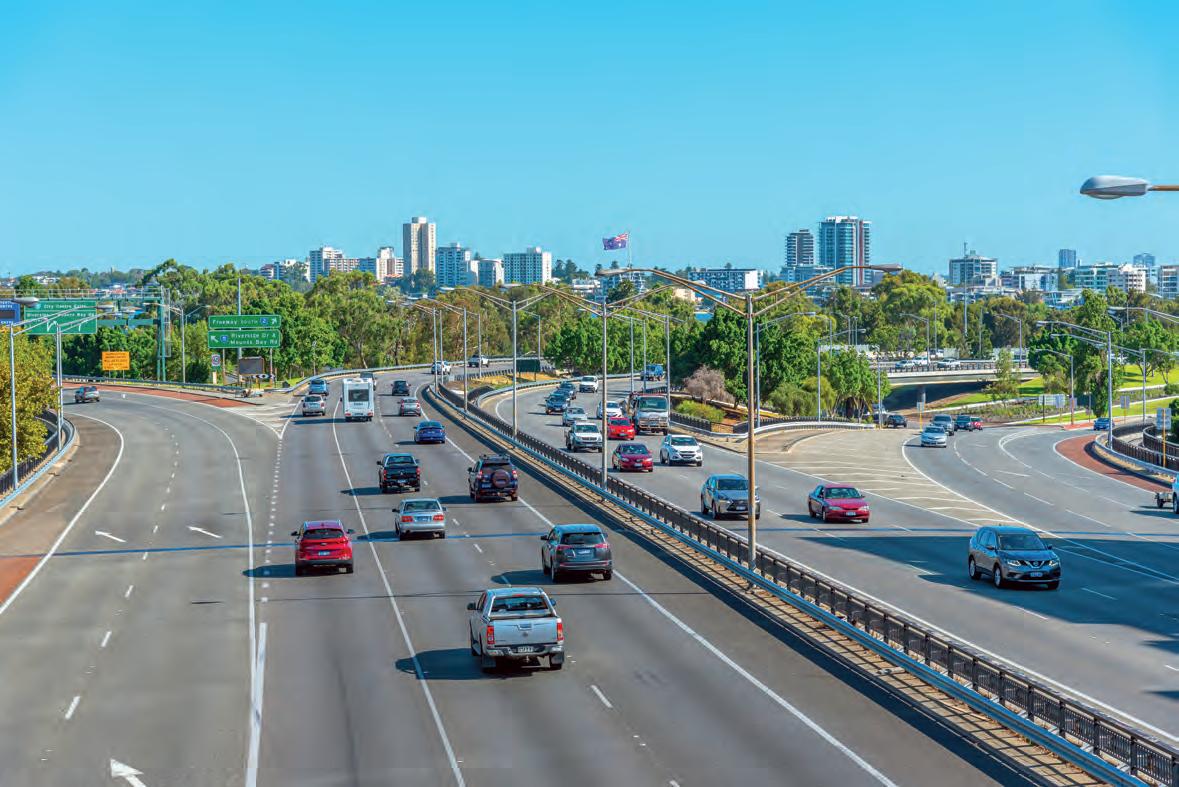
Material innovation, technology and safety are all focal points for Roads & Infrastructure Magazine’s October edition.
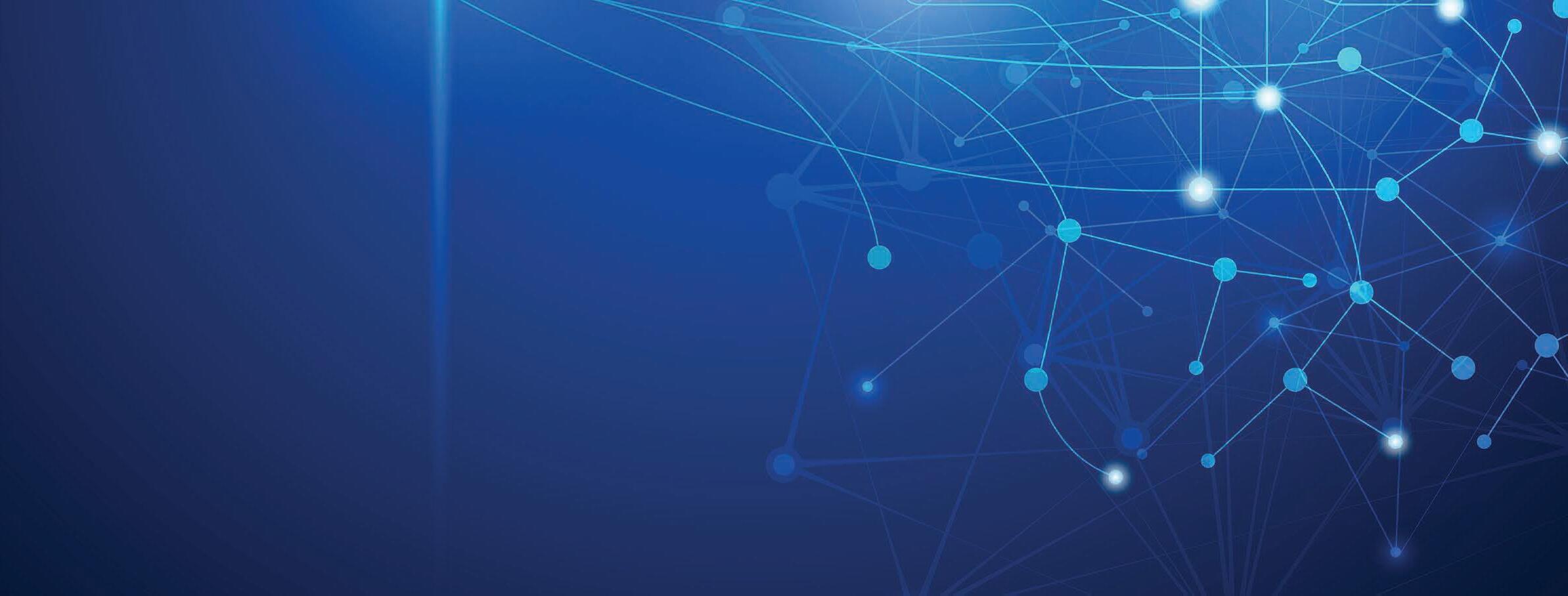
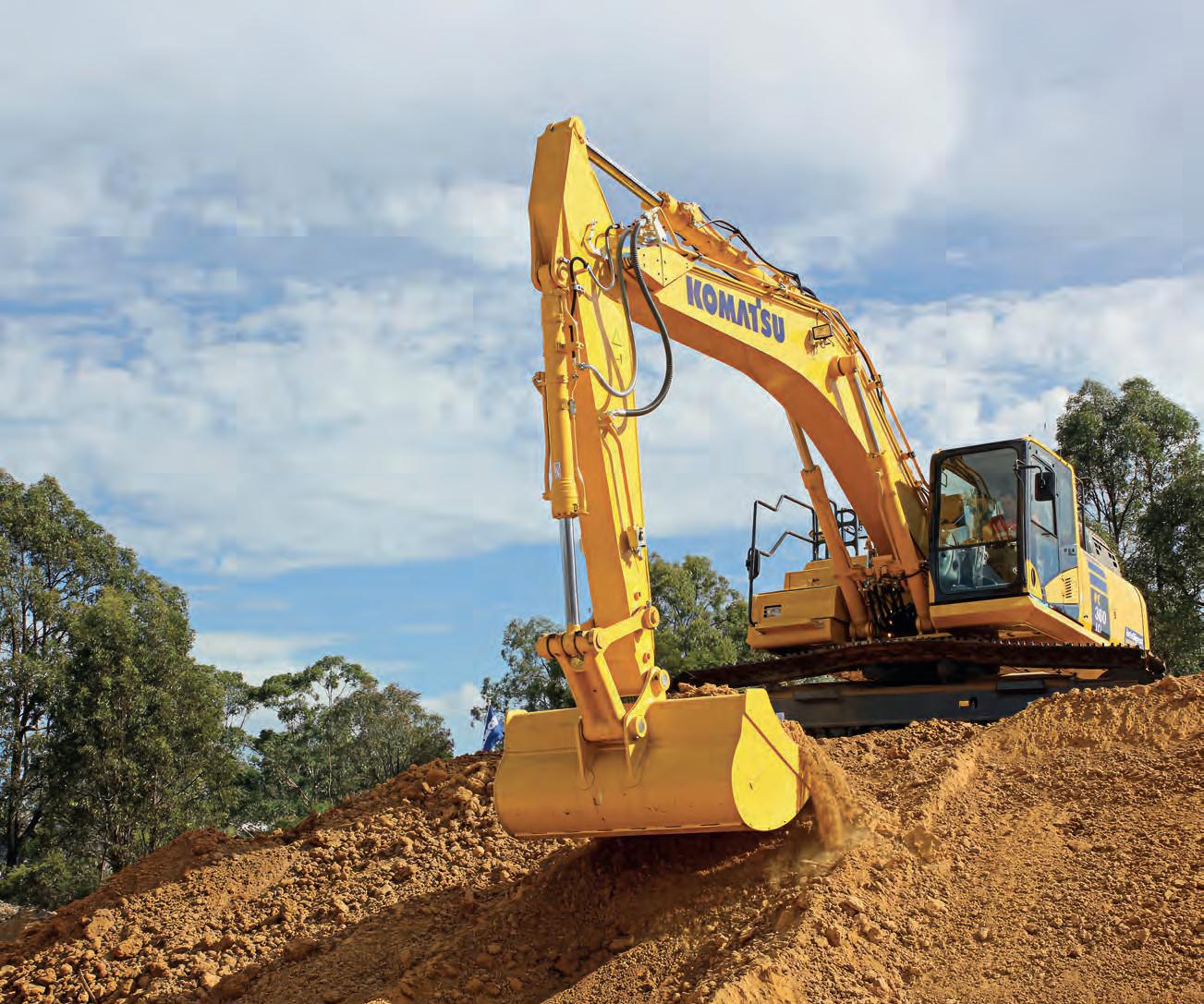
Elevate your worksite efficiency with Komatsu Excavators. Engineered for strength and precision, these machines redefine durability in every dig, conquering any terrain effortlessly.
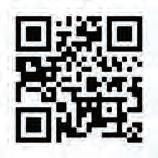
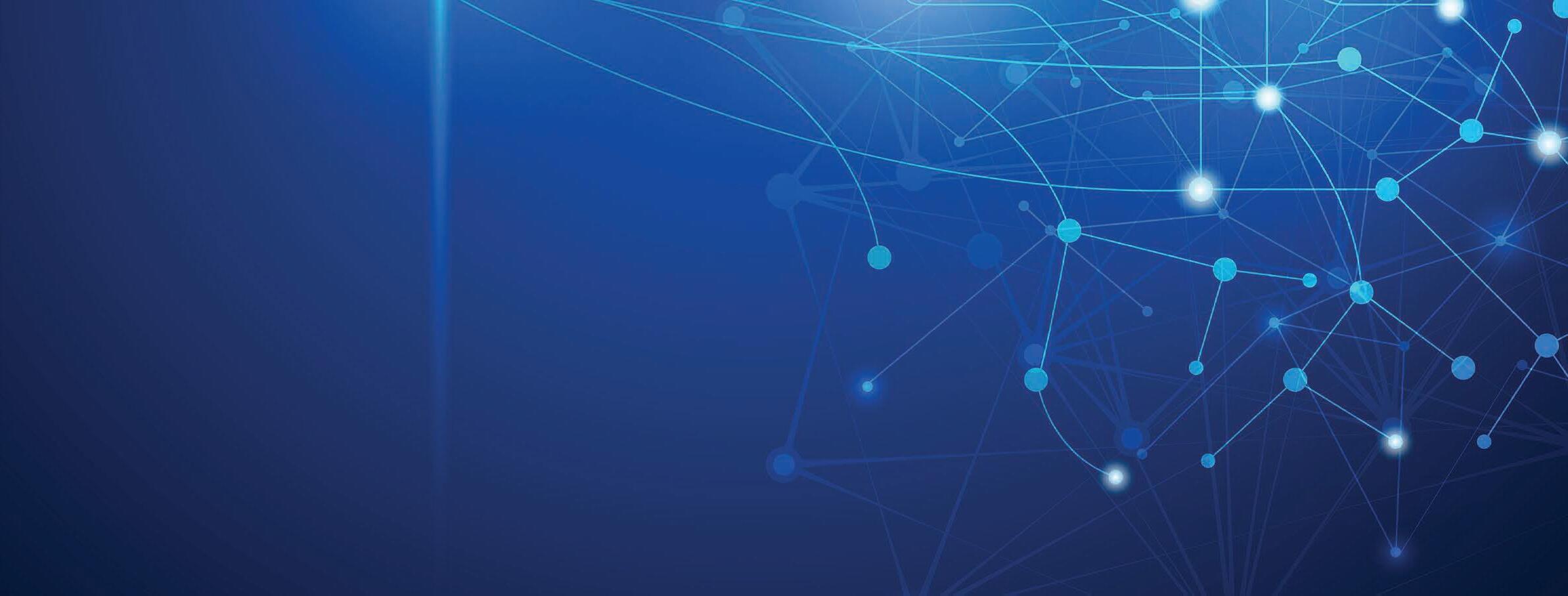
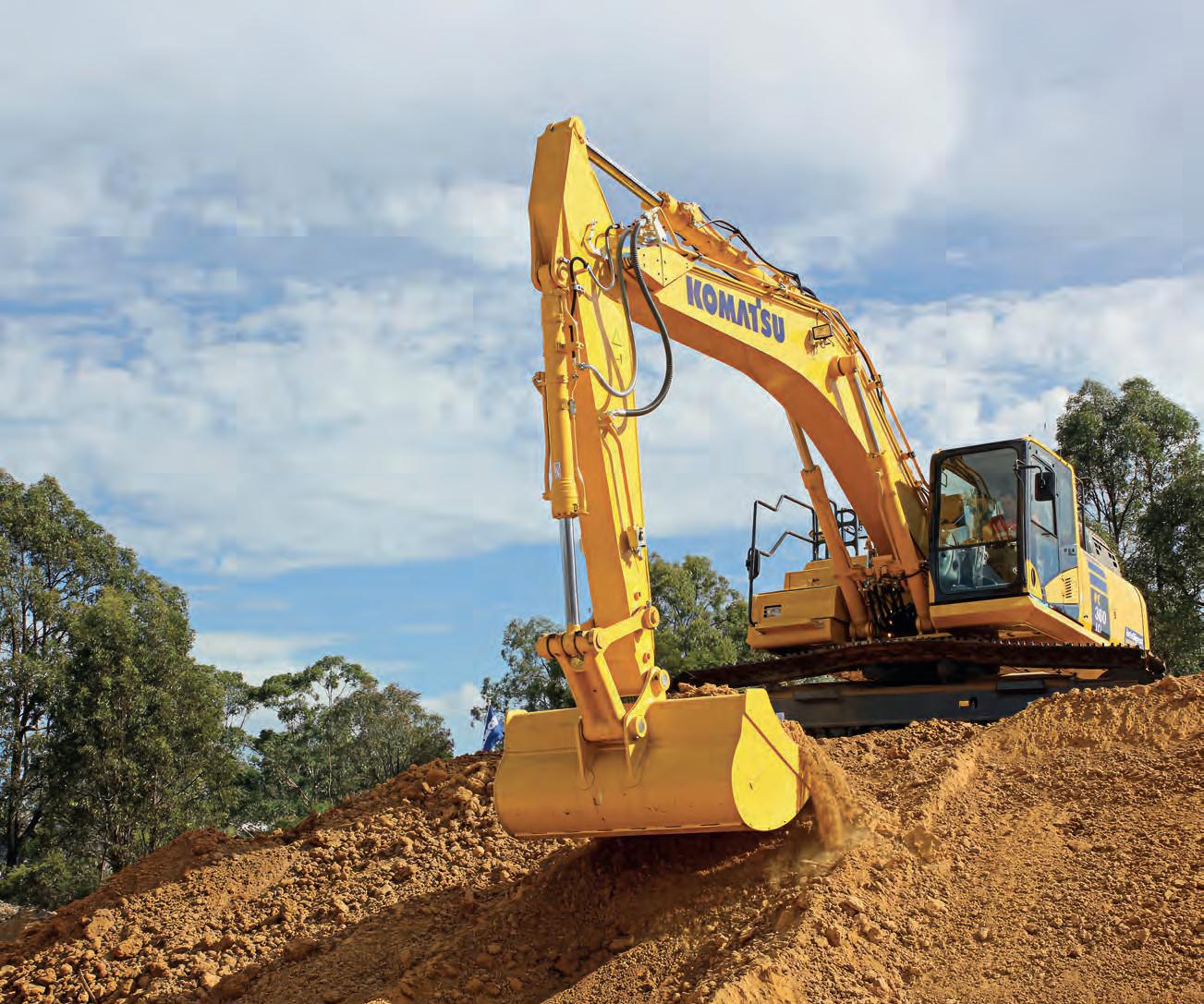
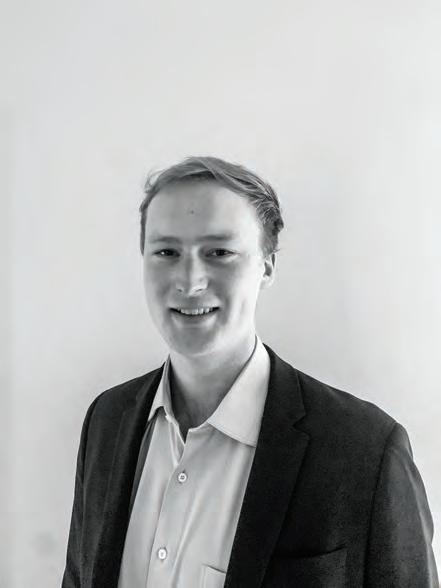
WHAT’S NEXT?
COVERING TRAFFIC MANAGEMENT, materials innovation and the rental market as part of the October edition of Roads & Infrastructure Magazine has filled me with hope and anticipation for the sector’s growth in the remaining months of 2024.
While 2024 has undoubtedly presented its challenges, from ‘lulls’ in the construction equipment market, to those provided by a lack of funding and legislative flexibility at a government level, I can sense the sector is ramping up momentum to face these trials head on.
In this month’s cover story, we sat down with XCMG General Manager Roy Rossini, one of the key leaders behind the construction equipment manufacturer’s push into the Australian market. Already one of the world’s oldest and largest equipment manufacturers, XCMG is aiming to build upon its existing presence in Australia to tackle new markets, while offering what Rossini believes to be “best-in-class machinery.”
Road worker safety is another topical subject at the moment, with tragic and untimely deaths and injuries providing a big wakeup call across the roads sector. To learn more about what’s happening in the space, as well as what more can be done, we hear from the Traffic Management Association Australia (TMAA). The TMAA recently conducted its annual National Traffic Controller Safety Survey, a comprehensive study shedding light on the experiences and concerns of workers across the country. These unique insights will help to better cater for the immediate and long-term needs of these (at times) at-risk workers.
Products such as Ingal Civil’s ArmorZone are the types of solutions that are helping to improve workplace safety for the better. The updated ArmorZone introduces recycled plastic into its design, enabling this innovative road barrier to not only be a safer option for infrastructure projects, but also a sustainable one.
Also in the October edition, we touch base with our key association partners to learn more about pressing issues in the sector.
The Australian Flexible Pavement Association, a long-time partner of the magazine, provides more insight into its proposed National Worker on Foot Awareness Online Course, which aims to encourage member organisations to invest in the safety and wellbeing of their workforce.
We also sit down with AustStab’s new Chief Executive Officer, Tanja Conners. Leading the Pavement Recycling and Stabilisation Association, Conners is hoping to bring in an exciting future for the organisation and its members.
This and so much more, in the October edition of Roads & Infrastructure Magazine
Happy reading!
Tom O’Keane Roads & Infrastructure Magazine
COO
Christine Clancy christine.clancy@primecreative.com.au
PUBLISHER
Sarah Baker sarah.baker@primecreative.com.au
MANAGING EDITOR
Lisa Korycki lisa.korycki@primecreative.com.au
EDITOR
Tom O’Keane tom.okeane@primecreative.com.au
JOURNALIST
Jennifer Pittorino jennifer.pittorino@primecreative.com.au
HEAD OF DESIGN
Blake Storey
ART DIRECTOR
Bea Barthelson
BUSINESS DEVELOPMENT MANAGER
Brad Marshall brad.marshall@primecreative.com.au
CLIENT SUCCESS MANAGER
Salma Kennedy salma.kennedy@primecreative.com.au
HEAD OFFICE
Prime Creative Pty Ltd
379 Docklands Drive, Docklands VIC 3008 Australia p: +61 3 9690 8766 enquiries@primecreative.com.au www.roadsonline.com.au
SUBSCRIPTIONS
+61 3 9690 8766 subscriptions@primecreative.com.au
Roads & Infrastructure Australia is available by subscription from the publisher. The rights of refusal are reserved by the publisher.
ARTICLES
All articles submitted for publication become the property of the publisher. The Editor reserves the right to adjust any article to conform with the magazine format.
COVER IMAGE XCMG
COPYRIGHT
Roads & Infrastructure Australia is owned and published by Prime Creative Media. All material in Roads & Infrastructure Australia is copyright and no part may be reproduced or copied in any form or by any means (graphic, electronic or mechanical including information and retrieval systems) without the written permission of the publisher. The Editor welcomes contributions but reserves the right to accept or reject any material. While every effort has been made to ensure the accuracy of information, Prime Creative Media will not accept responsibility for errors or omissions or for any consequences arising from reliance on information published. The opinions expressed in Roads & Infrastructure Australia are not necessarily the opinions of, or endorsed by the publisher unless otherwise stated.
TO STAY HERE
XCMG IS SYNONYMOUS WITH ITS CHINESE ORIGINS, BUT IN THE PAST FEW YEARS THE COMPANY HAS BEEN KNOCKING LOUDER ON THE DOOR OF THE AUSTRALIAN MARKET. WE SPEAK WITH THE MAN BEHIND THE RE-LAUNCH AND ESTABLISHMENT OF XCMG IN AUSTRALIA.
XCMG is well known for its Chinese heritage, being one of the world’s three largest manufacturers of construction and heavy equipment.
But what some might not know is that XCMG has been operating in Australia for close to two decades. Today, XCMG has an extensive dealer and part network throughout the country, with capability to provide services nationwide.
The company’s status in Australia certainly didn’t come by chance, as General Manager Roy Rossini – XCMG Mining Equipment Australia can attest.
Just prior to 2020, XCMG finalised plans for further expansion into the Australian market. All it needed was a key figure that could help deliver this transition. When XCMG came knocking, Rossini says it was a tough opportunity to refuse.
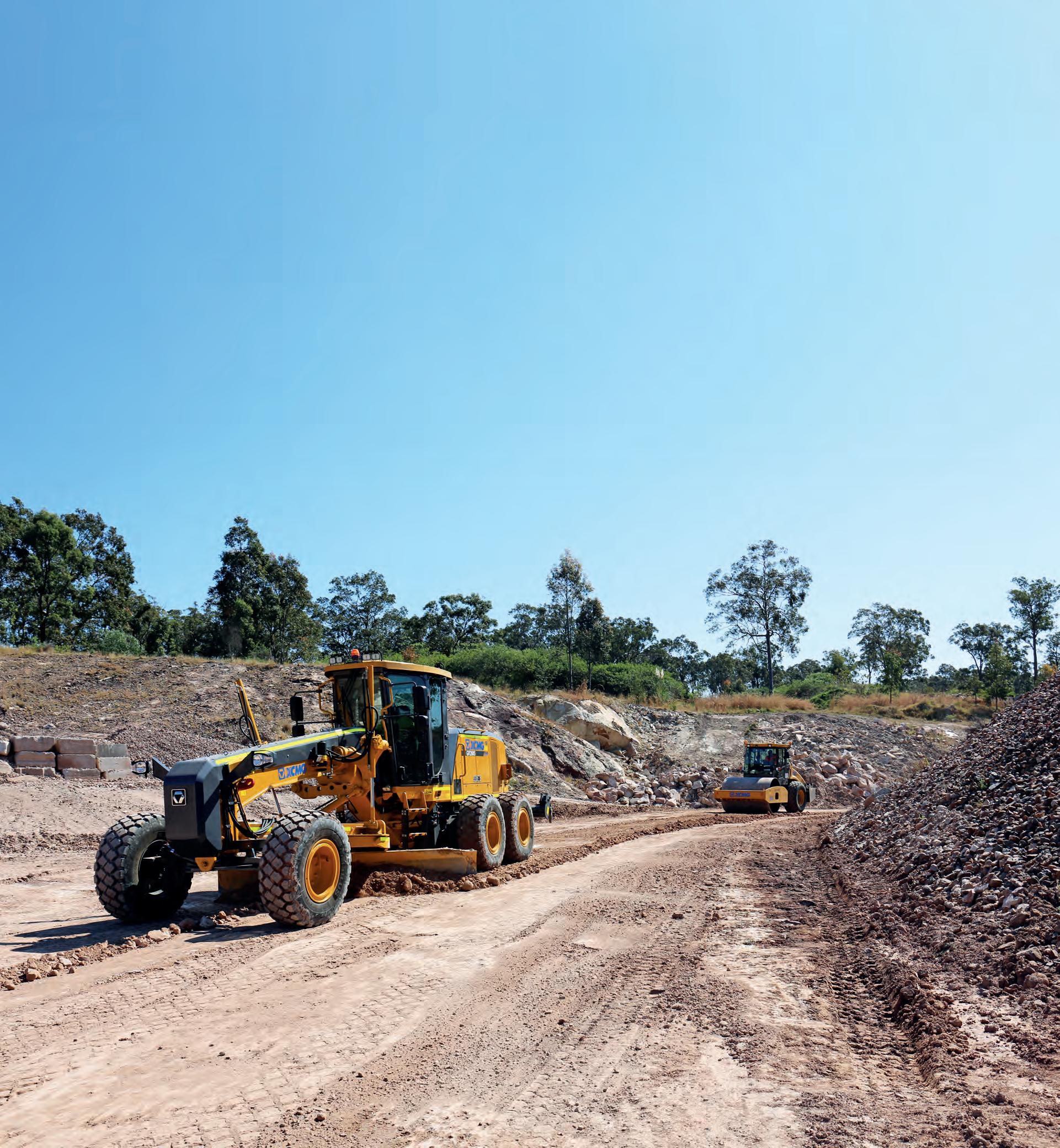
“I’ve been in the construction and mining sector for over 40 years, working for several OEMs and working in my own business. COVID hit, and XCMG were communicating with me openly for a period, I’d seen them at a few trade shows,” he says.
“XCMG itself is a company that’s been successful overseas since the 1940s, in the very top tier of companies in the world in the construction and mining sectors.
“They offered me the opportunity to come and assist the building of their presence in Australia. They’ve already been here previously for about 17 years, but only in a small and modest way. Their previous approach was to bring a few machines over, sell them, then return to China. They didn’t have plans to establish a support network in Australia. That’s where I came in.”
From humble beginnings, Rossini made his mark and influenced the direction of the machinery manufacturer’s early years in Australia. A challenging, but enjoyable part of his role, as he explains.
“We started off with just one container with a bunch of products. After we unloaded them on site in Melbourne, we put the first machines out and started making modifications to improve the product. After that, I set up a dealer network from contacts that I already had in the industry, some of which I’ve known for many years,” Rossini says.
“We had more products coming in and we had a bit of instant success. In three years, we sold around 3000 units.”
THE AUSTRALIAN CRITERIA
Rossini says tailoring the existing product and service offering to best suit the Australian market was one of the first key steps to establishing XCMG’s presence domestically.
“The support and service network that you need to give to any market to make it successful is quite unique in Australia,” he says. “The number one priority was the need to set up a reputable dealer network, with dealers who had service
XCMG’s grader and roller portfolios continue to expand, as does its presence across Australia.
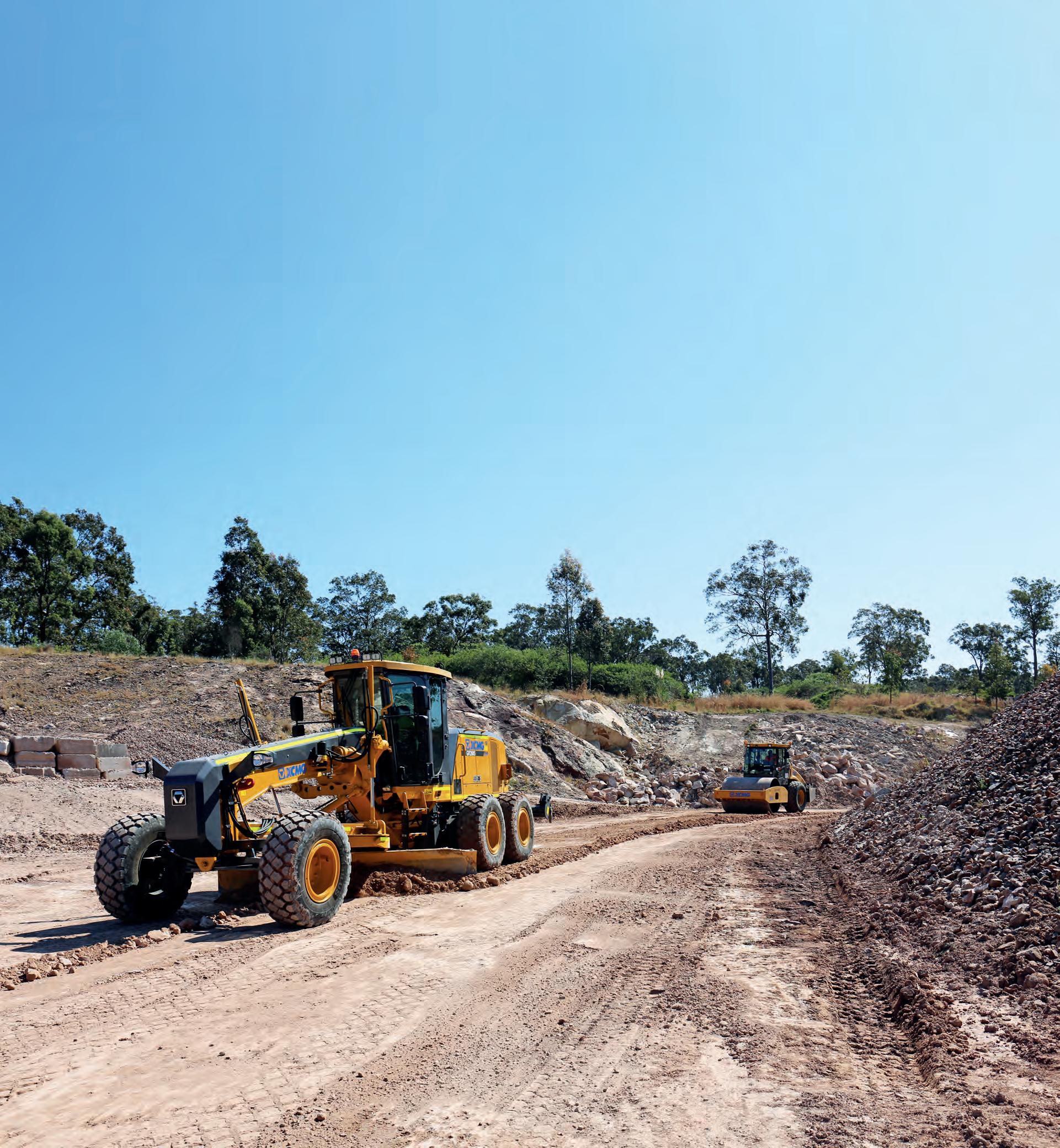
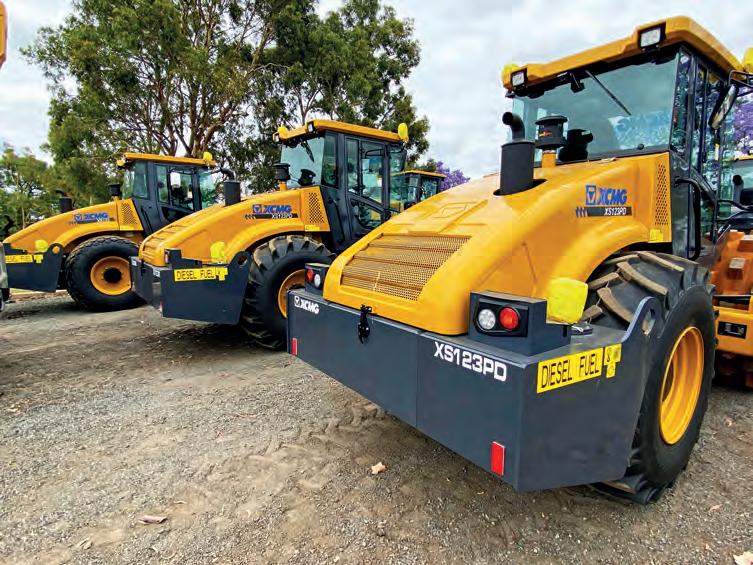
XCMG’s roller range has been configured to specifically suit Australian applications and projects.
and technical experience, support networks themselves with people on the ground and most importantly, people who understood the industry.”
The second step was establishing a headquarters for the planned expansion, a central site to support the national network.
“To have that base, which could have a million dollars’ worth of spare parts on the shelves, and technical people on the ground was imperative,” Rossini says. “Now we have long-term staff, a lot of whom have 20-30 years’ experience.
“They come with a unique set of qualifications and life experiences that helps to form the backbone of our business. Now we’ve got the equivalent of hundreds of years of experience injected into the organisation. Without that, we wouldn’t succeed.”
For its headquarters in Hallam, Melbourne, XCMG’s next phase is focused on having the systems in place to support additional growth and development, an aspect the XCMG team is still working on today.
Rossini adds that while all these steps have been crucial for establishing a sturdy foundation for future success, the most basic requirement is also the most important –having a decent product.
“You can’t go anywhere if you don’t have equipment that’s got great quality and is value for money for your customers,” he says.
“We’re not afraid to change as required within the industry. A key factor of our success has been listening and considering customer feedback, which has helped to
shape product modifications and changes to our support network.
“From my point of view, XCMG has been, and still is, second to none in this area. I’ve never worked for an organisation that makes changes this quickly if there’s improvements to be had. It’s a unique operation here and we’ll continue to do that.”
MACHINERY RANGE
A core component of XCMG’s product range for the construction sector is its motor graders and rollers. These machines could be considered XCMG’s ‘bread and butter’ and as Rossini explains, are setting the standard for versatility and performance.
“Our graders have benefitted greatly from a joint venture with Rio Tinto, who have helped us to better develop and adjust the product to suit,” he says. “That includes our GR2605, which has a 14-foot blade, along with 260 horsepower.”
The GR2605 has been designed to suit motor grading projects of any scale, thanks to its blade pitch and grading precision, which make it an ideal candidate for several applications including surface levelling, not just road grading in isolation.
“We’re moving on to our stage two cabin design, which gives the operator greater visibility, while being more ergonomic. It’s an extremely viable product for the market, the price point is reasonable, and the quality is very good. There’s some in the industry that have been ‘inspired’ by our designs,” Rossini says.
XCMG has made a name for itself internationally thanks to the robustness and performance of its machinery.
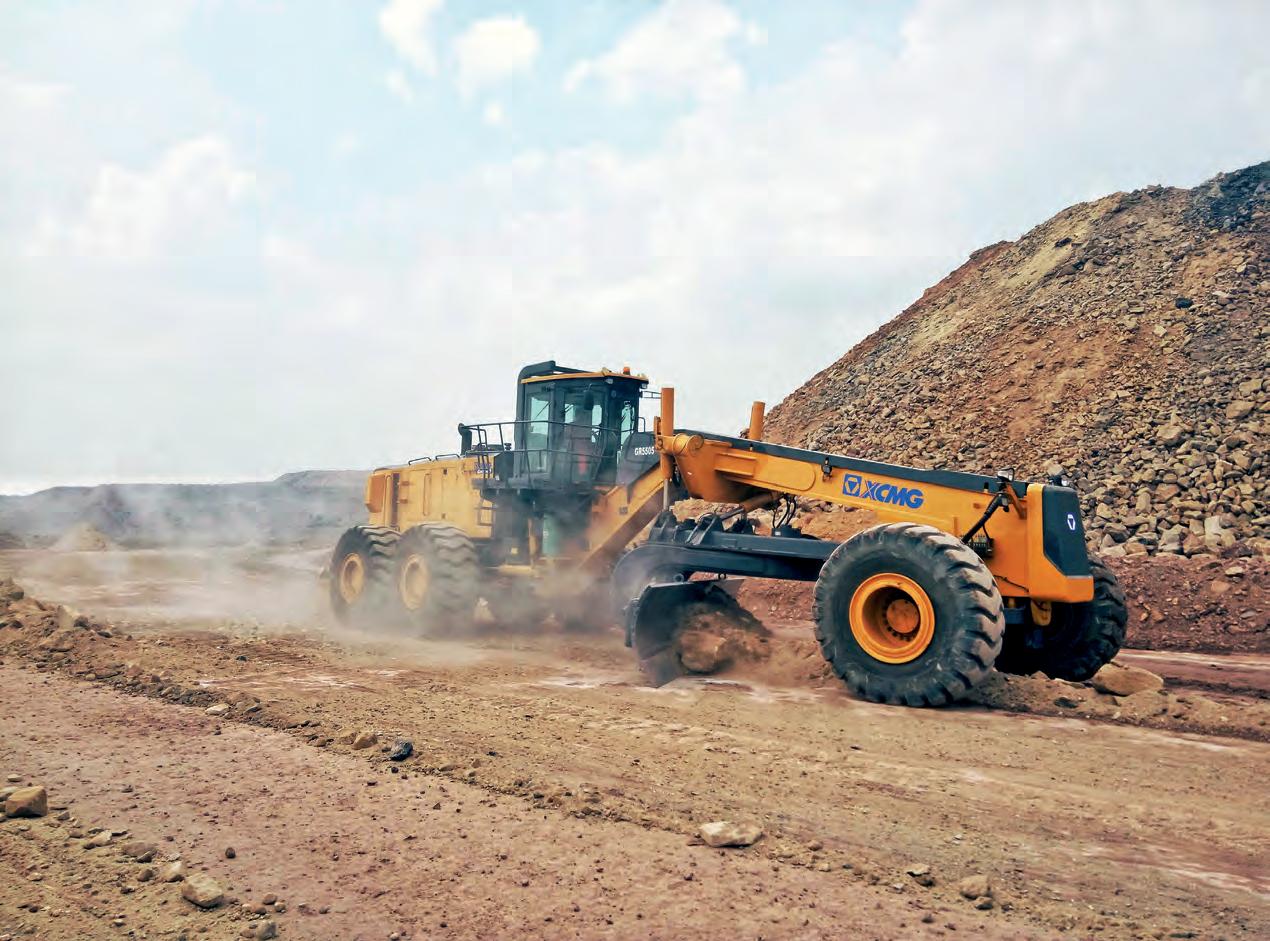
Another exciting aspect of XCMG’s grader range has been its ventures into the battery technology space, with the company developing a variety of prototype, batterypowered graders.
“We will have the first grader in the world to run on battery energy and those concepts have already been realised through our prototype models,” Rossini says.
“We already have joint ventures and partnerships in place, along with a dedicated team in China. We’ve committed a lot of resources, it can be a challenge to implement that technology into massive machines, but we’re making progress right across the board in the battery space.”
When it comes to rollers, XCMG manufactures a variety of both single and double drum models, ideal for both paving roads and compacting soils.
Whether it’s a smooth drum roller, dirt packer, or a ride-on vibratory roller, Rossini says the XS123 is just one in a suite of rolling options for the Australian market.
“The 12 tonne is among the most popular in the marketplace at the moment,” he says. “Feedback has been really positive around that model and it’s a product that continues to progress with each of our factories dedicated to getting it right.”
XCMG is also aiming to implement brand new technology into its future roller units, this time in the form of autonomous operation. Operators should keep their eyes out, with the autonomous options set for a wider rollout soon.
These products and much more are backed up by XCMG’s support and servicing networks across the globe, an aspect that’s been instrumental in the growth of XCMG in Australia.
“We always keep the line of communication open between sites, so whether it’s a customer or a matter for us, we can speak directly with an engineer in the factory,” Rossini says. “Whenever we have any issues or suggestions, we can have those conversations quickly.
“I might be standing with a customer in front of a unit, and they might say the seat needs to move, or they’re used to the armrest being in this position, or they might need better visibility in a certain situation. Usually, a big manufacturer would just say ‘too bad, that’s how we make them’, but we don’t.”
FUTURE PLANS
Reflecting on the progress made, Rossini says he’s “extremely proud” of how XCMG’s
venture into the Australian market is progressing, from an initial foray, to now an established and growing international brand.
He says the collective minds of XCMG domestically, as well as the company’s vast international experience is ensuring that the manufacturer is rising in the ranks of Australia’s premier construction machinery brands.
“It has not been a small task by any means, it’s been a huge challenge. To see what we’ve done, building from nothing to where we are now in such a short time, that’s a massive achievement,” Rossini says.
“At the end of the day we’d be nowhere if it wasn’t for the team’s effort. They’ve all dedicated so much to reach the position that we’re in today. That’s the benefit of having people with so much experience in the sector and having established relationships. I trust what they’re saying and the direction they want to go and likewise, it’s a strong collective.”
And while it won’t happen overnight, XCMG has its sights firmly set on the top step of the podium.
“We don’t shy away from the fact that we’re gunning to be number one in the world. That’s what we’re aiming and growing towards. On top of our customer’s needs, that’s what pushes us every day.”
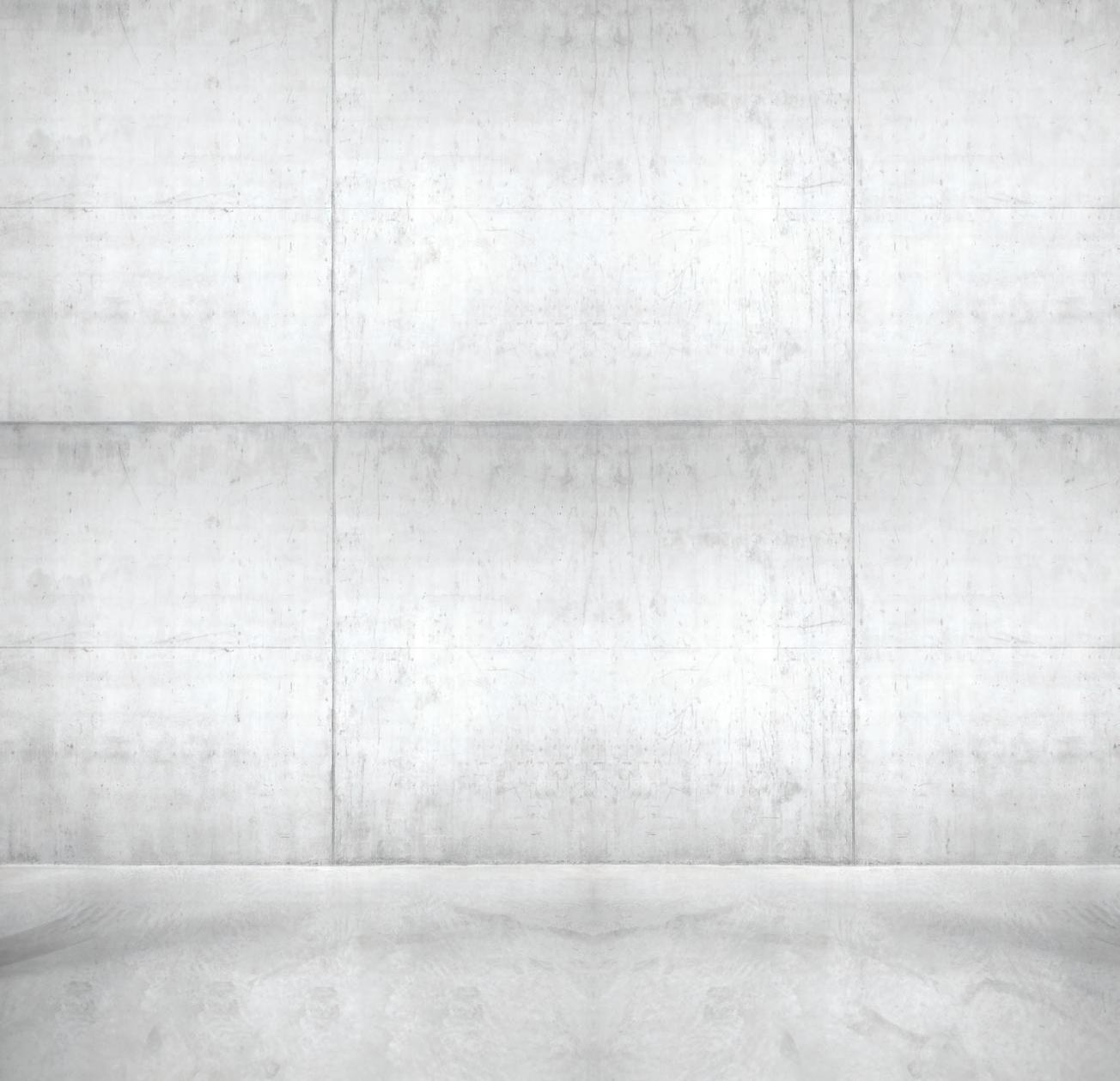
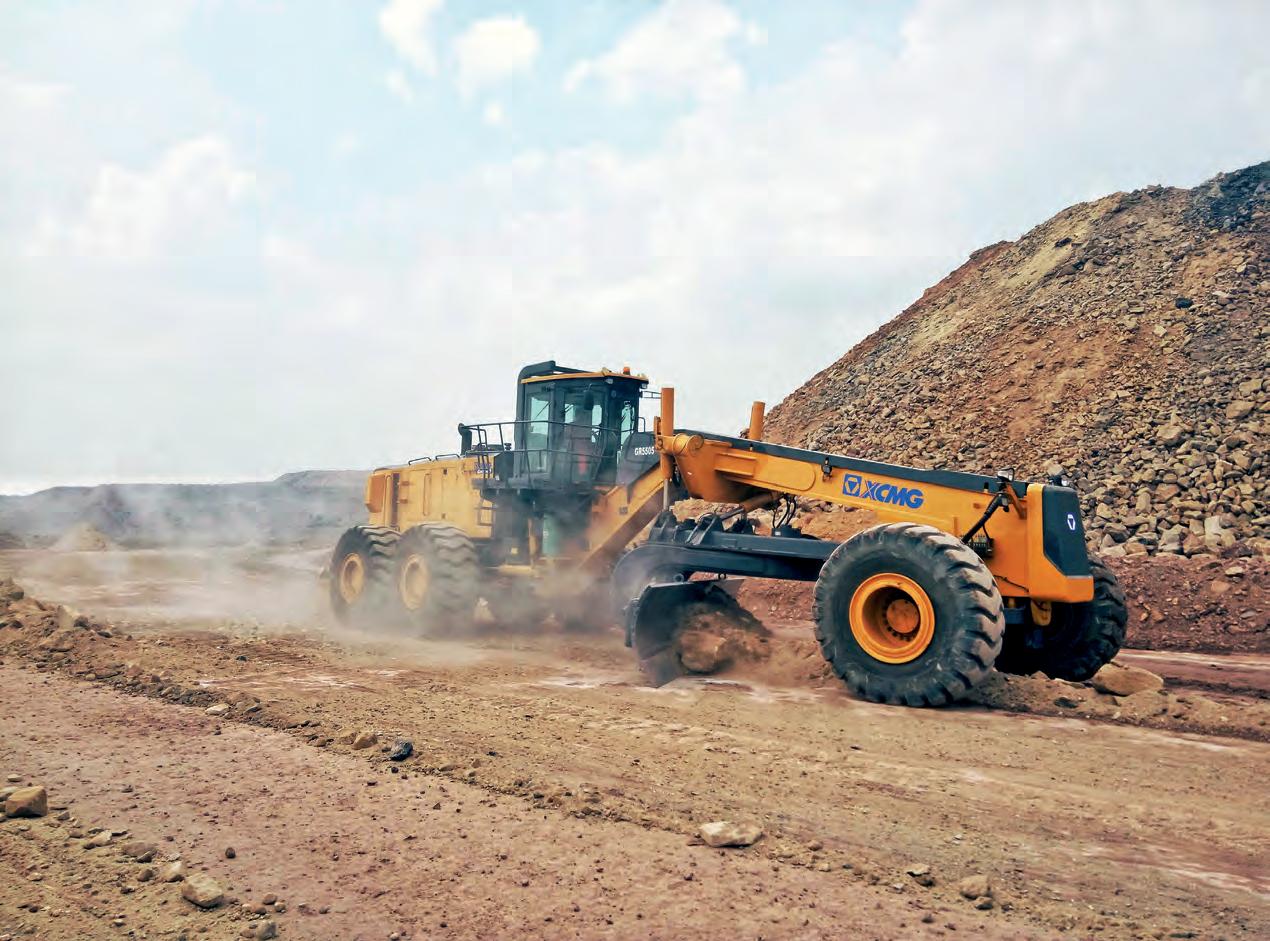
FREO GROUP INVEST IN INNOVATION
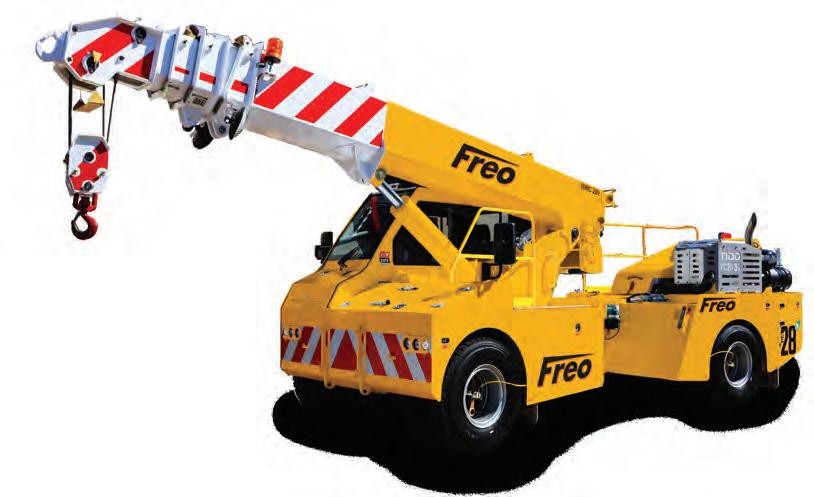
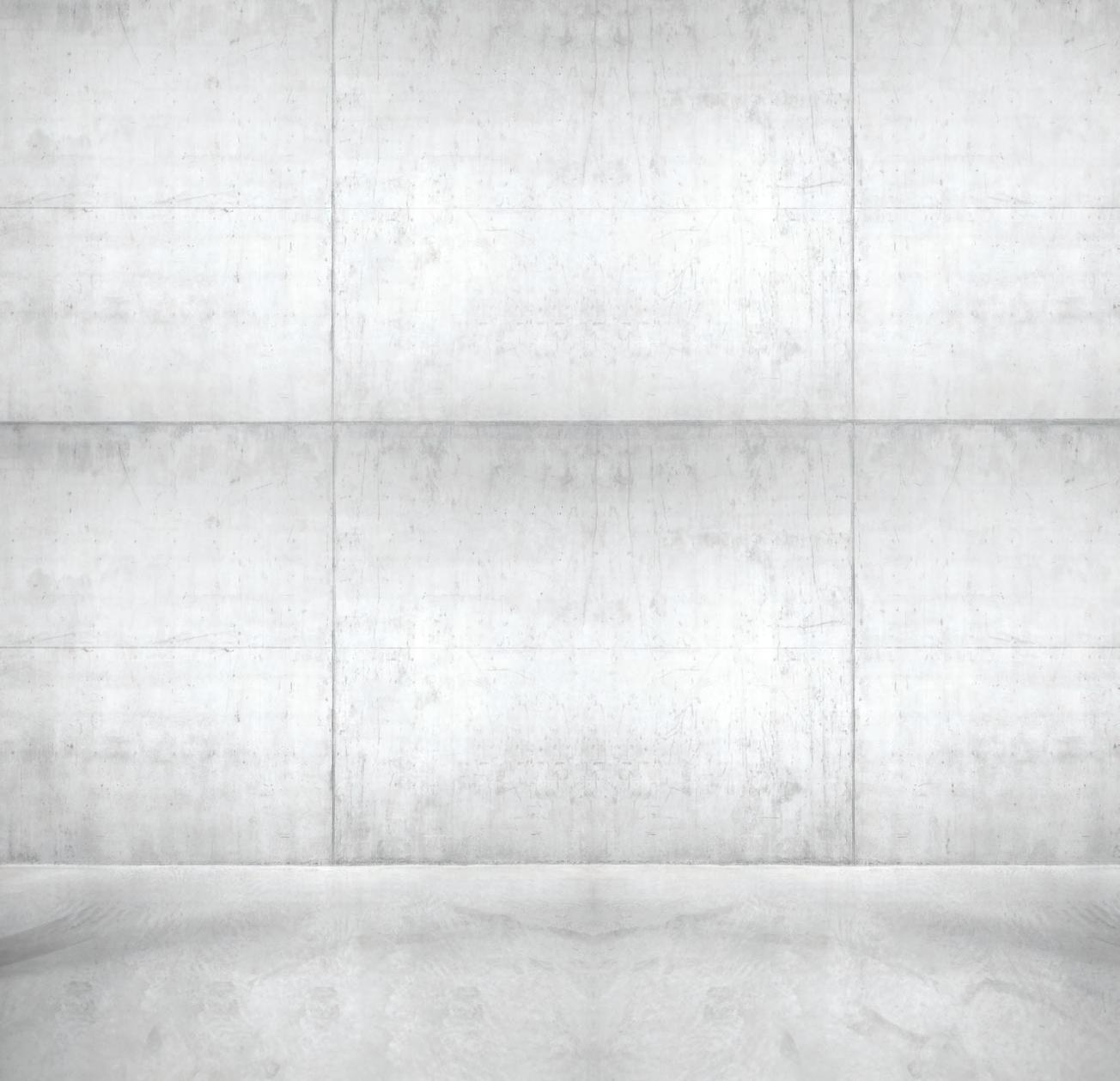
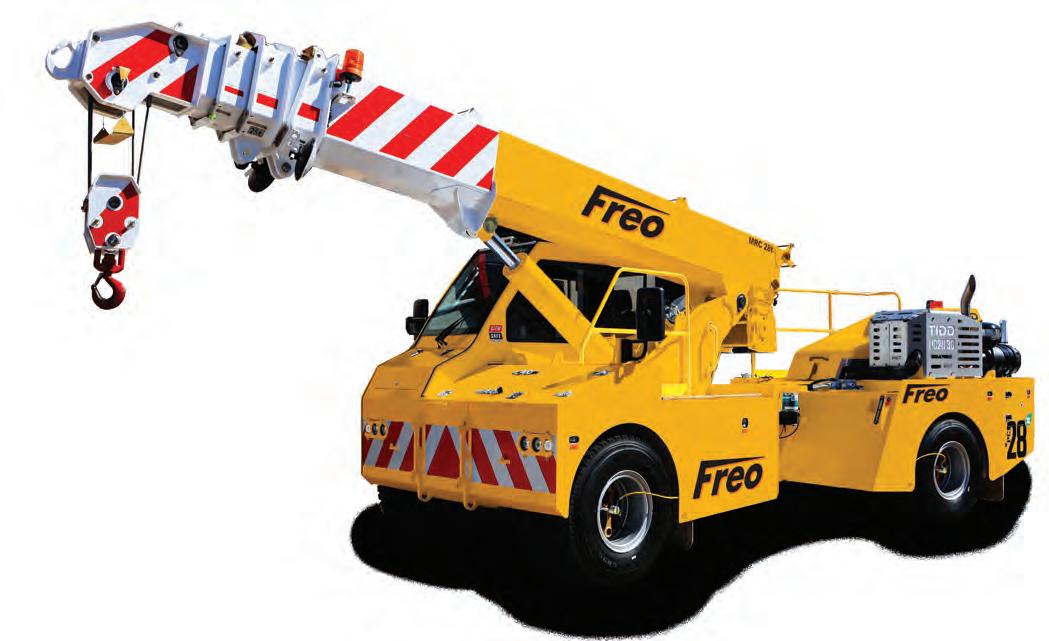
Freo Group’s Principal Assessor, Chris Everleigh, conducted a comprehensive two-day inspection of the TIDD Crane, evaluating its drivability, manoeuvrability, comfort, and operational lifting capability. Chris rated the crane a perfect 10/10 across all categories, stating:
“The TIDD Crane is very comfortable with the latest technology advancements, all coupled with TRT’s team of great knowledge. The TIDD is a very well-refined crane, 10/10.”

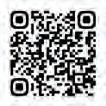
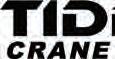

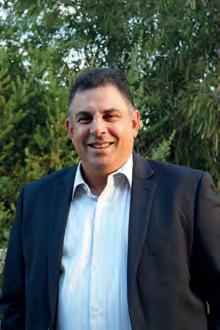
PETER ALI, CEO – MUNICIPAL WORKS
AUSTRALIA
The adaptability and commitment demonstrated by the next generation of municipal works practitioners gives me the most optimism. They are incredibly talented and use social media and other emerging technologies to create professional networks and share ideas. Their openness to new ideas and approaches reassures us that non-traditional solutions to long-held problems will continue to emerge. For example, we now see increased use of recycled materials in traditional pavement designs. The type of materials used is growing, and approval processes from regulatory authorities to use these products are faster. Image: Municipal Works Australia.
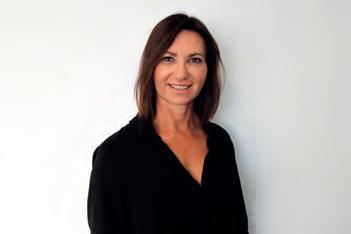
TANJA CONNERS, CEO – AUSTSTAB
Despite the ongoing challenges facing broader industry, AustStab’s outlook is with significant optimism driven by innovations and achievements in sustainable pavement recycling and stabilisation practices. These advancements are steering the sector toward net zero emissions, particularly through the development and adoption of cutting-edge recycling technologies that reduce the need for virgin materials and the generation of construction waste. Techniques like insitu stabilisation and cold recycling are not only extending the lifespan of existing infrastructure through resilience but are also minimising the carbon footprint associated with road rehabilitation. Additionally, the decarbonisation of our material inputs through increased use of renewable energy and recycled materials in stabilisation processes is helping to lower greenhouse gas emissions. These sustainable practices are proving that with the right strategies, our industry can play a pivotal role in the global push toward environmental stewardship while ensuring the longevity and quality of our roads. Image: AustStab.
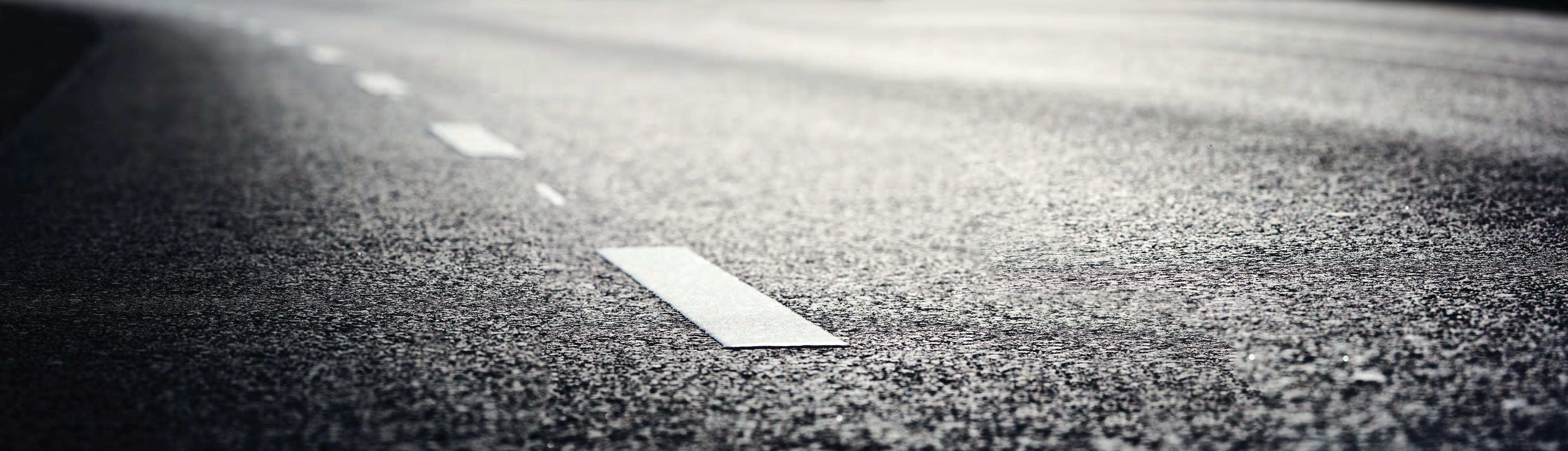
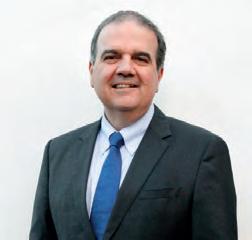
MICHAEL CALTABIANO, CEO – NATIONAL TRANSPORT RESEARCH ORGANISATION (NTRO)
From adversity comes innovation because doing the same thing results in the same outcomes. The infrastructure industry has been rocked by cost escalation and must now deliver on a culture of being “innovation driven”. This requires a genuine partnership with government and entities like NTRO that provide the bridge to certify the development of new standards for new products. Image: NTRO.
If you or someone at your organisation is an industry leader and would like to be a part of this monthly column in 2024, please get in touch with Editor, Tom O’Keane: tom.okeane@primecreative.com.au
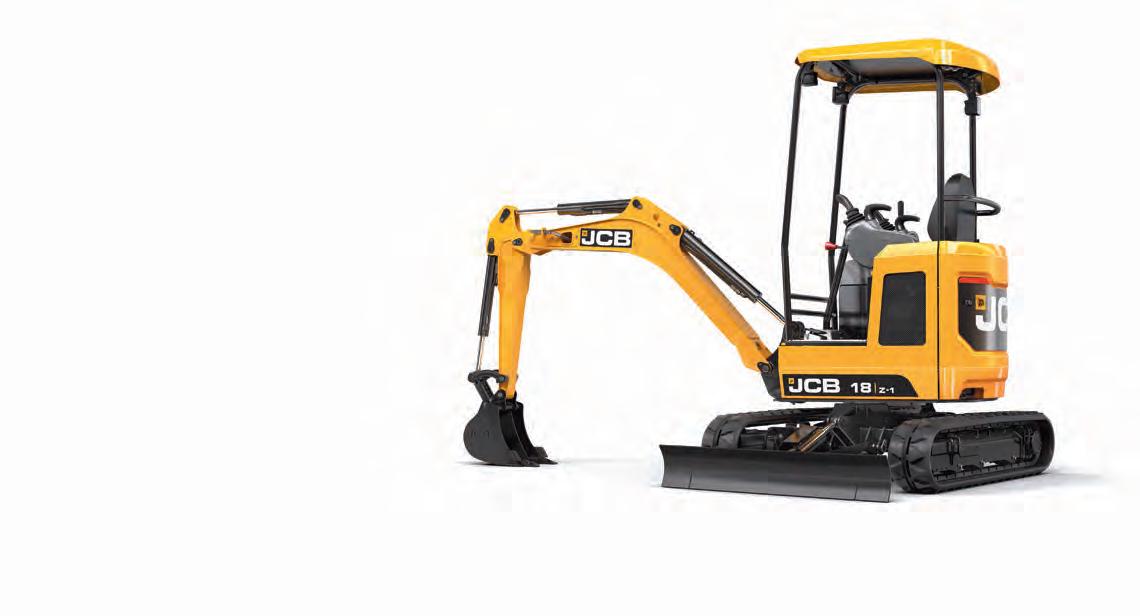

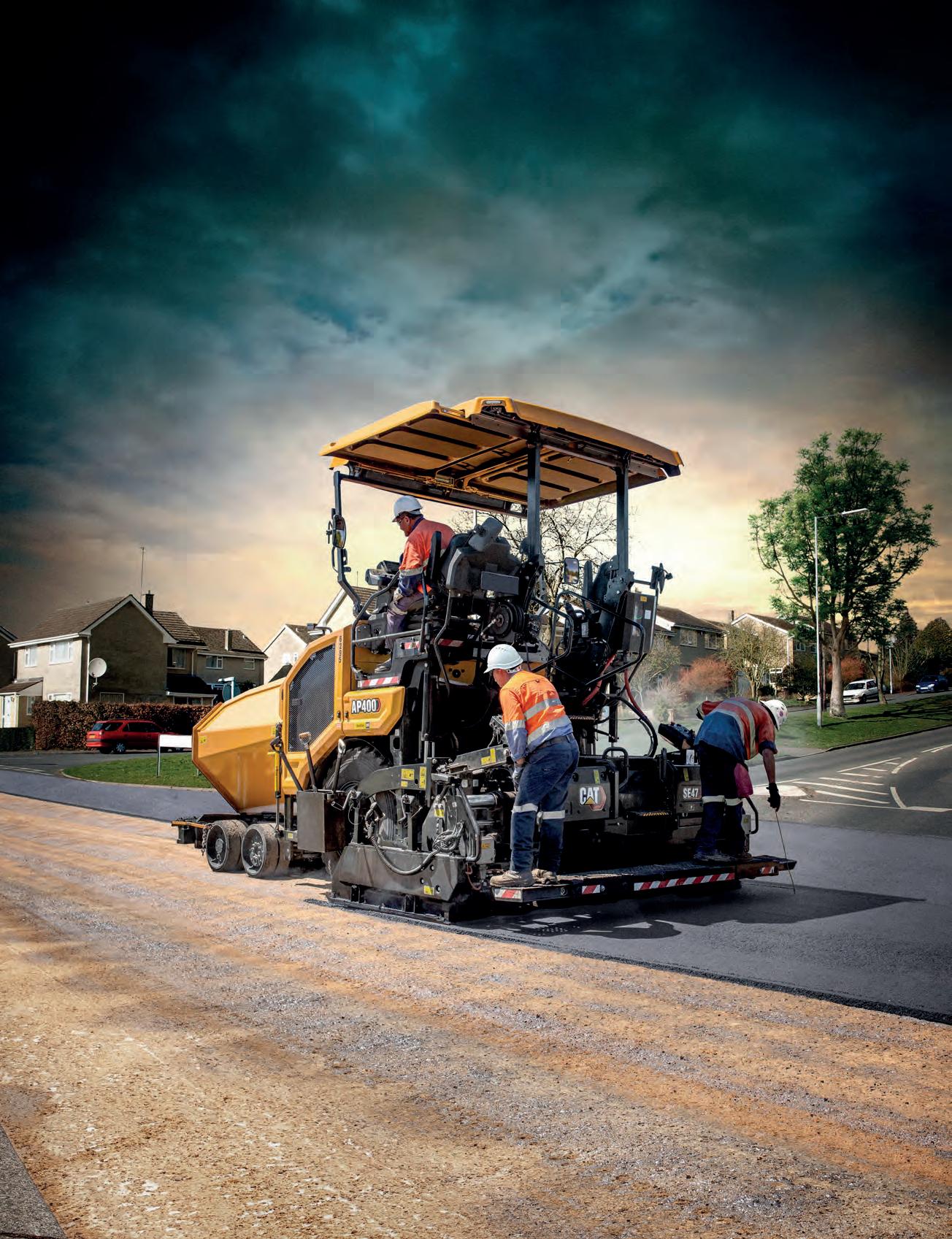
COMPACT SIZE CAN MEAN
A HUGE ADVANTAGE
CAT® AP400 ASPHALT PAVER
The Cat® AP400 is the perfect machine for those asphalt paving jobs where space is at a premium.
It’s got the compact size, flexibility and versatility you need, especially in built-up urban areas.
Plus, when you purchase a new Cat AP400, you’ll also have the option of:
• access to locally supported parts via the national dealer network
• a comprehensive warranty package
• a Cat Customer Value Agreement (CVA).
To find out more contact your local Cat dealer or visit cat.com/AP400-au
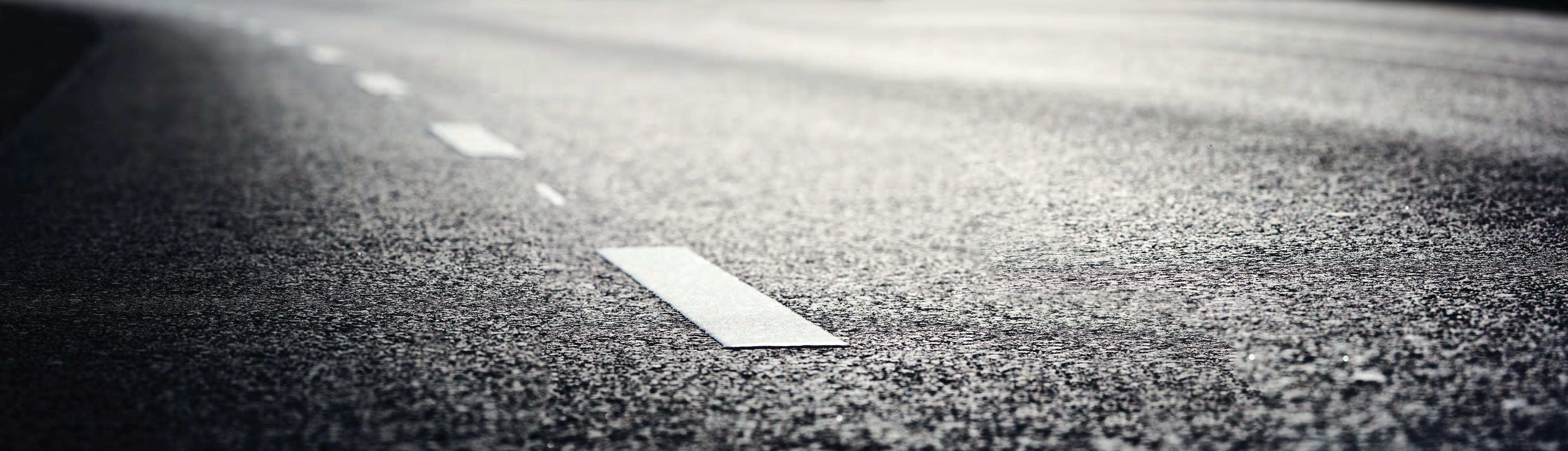
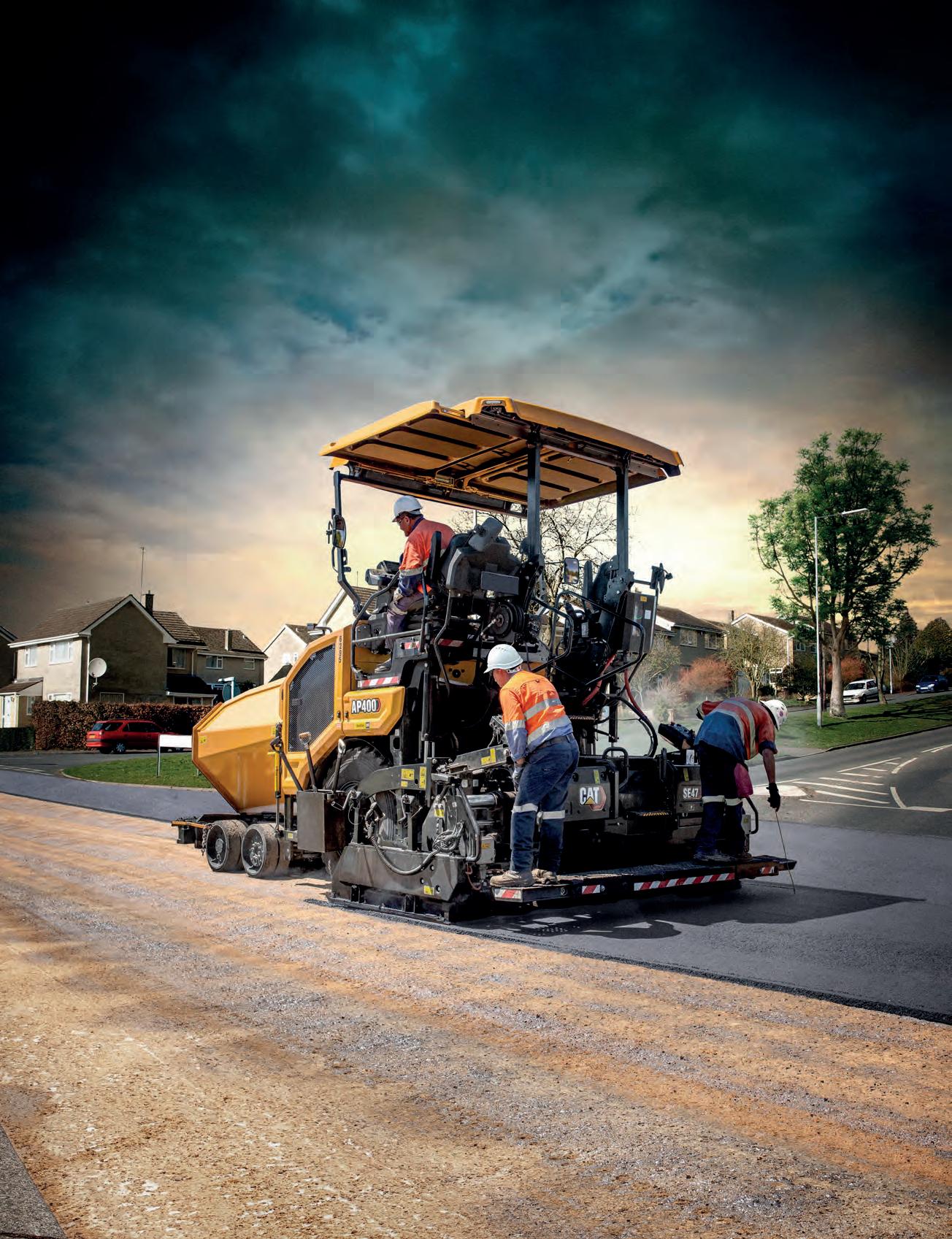
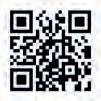
CHALLENGES AND TRIUMPHS: THE R&S STORY
R&S GRATING’S STORY AND ONGOING SUCCESS CAN PREDOMINANTLY BE ATTRIBUTED TO THE COMPANY’S COMMITMENT TO FAMILY, AND THE LEGACY OF ITS PAST LEADERS. TIM HOCKHAM AND STEVE SKINNER REFLECT ON THE PAST AND SHED SOME LIGHT ON THE FUTURE.
Not many businesses across the roads and infrastructure sectors began their journey in a backyard stable. But then again, Road Safety Grating (R&S Grating) has always succeeded in doing things a little differently.
Back in 1974, a small backyard stable in Mentone, Melbourne was the backdrop for what would become one of Victoria’s oldest and leading supplier of high quality grates into Melbourne’s major road projects, and eventually a leading civil drainage supplier.
All of this kicked off when the late Stephen “Stevo” Hockham and his brother sought to establish a modest business, focused on the manufacture of welded steel grates.
As Steve Skinner, National Sales and Business Development Manager – R&S Grating explains, Stevo’s desire for success was a key factor in the company becoming a
favoured grate supplier across Victoria for decades.
“To give you an idea of how things got started, someone came to Stevo one day and said ‘you should make grates’. That’s honestly where the business came from,” he says. “As Stevo would tell it, the story goes that he made the grate, the customer said it was the best he’d ever seen, and he asked if he could have another.
“I’m not sure if they even had a horse in the stable,” Skinner jokes. “It all started with Stevo. He was very passionate about grates. You think ‘how can you be passionate about grates?’ But he found a way, and that shone through in everything that he did.”
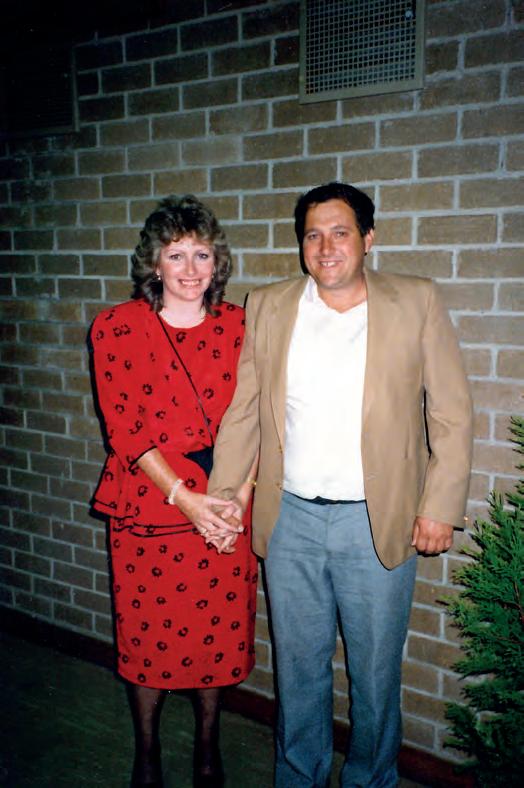
Skinner first joined the company over ten years ago, when R&S Grating was already an established and wellregarded manufacturer.
“I think the word got out that I wasn’t

working for my old company, so Stevo approached me to come and work for him,” he says. “His pitch was as simple as ‘I want you to come and work for me’. It started with a phone call, I came into the office to see him, we had a great chat and he gave me two bottles of wine.
“I thought ‘that’s the first job interview I’ve ever done where I’ve walked away with two bottles of wine’. That was Stevo, he’d bend over backwards for anybody.”
Stevo was much more than just the Founder and patriarch of R&S Grating. He’s a life member of Municipal Works Australia, an organisation that he was heavily involved and committed to. He’s also highly regarded in the local community.
Skinner says there are plenty of stories when it comes to Stevo, with most providing some insight into his selfless and considerate nature. Hence his wellknown nickname, the “Grate Man”.
“Years back, Stevo took a trip to the United States. He stayed up in a room that overlooked Niagara Falls. He thought it was one of the best things he’d ever seen. There were a few people at the business who were thinking of going on a holiday, so he said, ‘if you go over there, I’ll pay for your room to overlook the Niagara Falls, you have to see it’. He did
that for a couple of people and the offer was there for everyone,” he says.
“He’d take generosity to another level, and he always looked up to other people in the business, not down. You had to do something seriously wrong to get on his bad side, I’m not even sure if he had one.”
Widely known for his humour, humility and generosity towards R&S Grating’s customers – as well as the wider community – Stevo’s passion and determination endure through his three sons, all now working in the business, including his eldest son, Tim.
For Tim Hockham, R&S Grating was always a part of his life growing up.
“My earliest memories of the company are coming to work with Dad in the 1990s, I would’ve been about 12 at the time,” he says. “In those days, Dad would bring Pop along as well to help out. The company was much smaller then.
“There’s a lot of things that have changed since those days.”
A constant theme throughout the years has been a strong connection to family, as well as the past. As Hockham explains, he’s one of many employees who have a strong family connection to the business.
“It’s not just about my family and I think that’s what sets us apart. All our employees and their families really care. Everyone wants the business to do well, everyone wants each other to succeed. We really care about each other and that generational factor plays a big part in that,” he says.
Taking over the mantle from his father, Hockham is among the company’s leaders who are helping to settle the ship, with enduring market challenges not making life easy for the R&S Grating team.
The most important thing is that the team has each other, he says.
“The family element has been in this business since it started. It’s not just our family, there are many multi-generational family relationships across the business.”
Malifa Taeleipu, Production – R&S Grating, started coming to R&S Grating in 2006, helping his father Sam.
Taeleipu says the strong family values of R&S Grating are reflected in his family’s close ties to the business, with his father working at the grate manufacturer for more than 20 years. Taeleipu himself is coming up on 18 years of service.
“I was originally a labourer, cutting steel for my father to fabricate. I didn’t know
R&S Grating’s early days have laid the foundation for what the company is today.
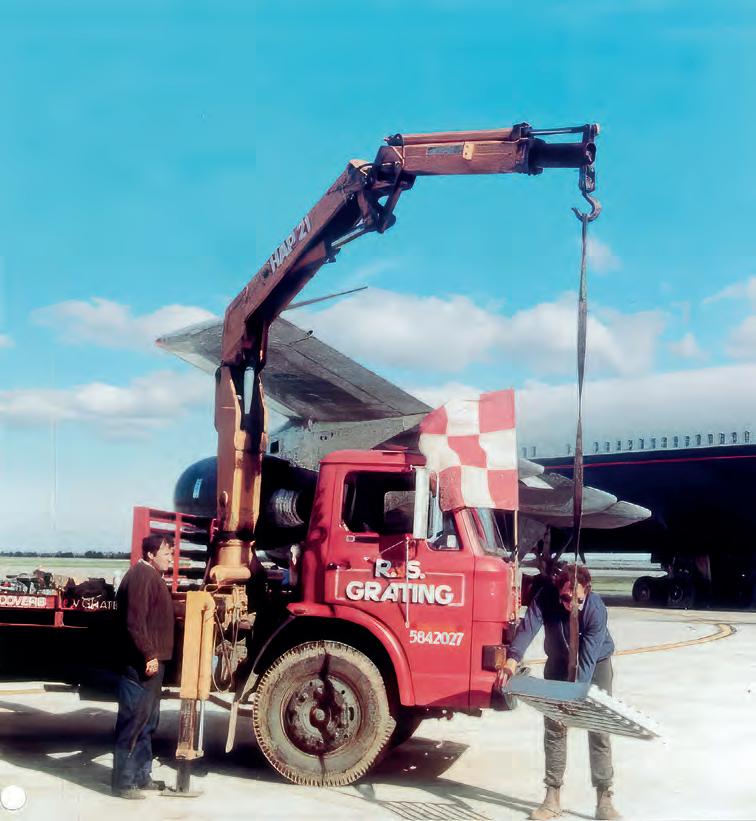
it at the time, but he took me under his wing and taught me about the real world. He’s taught me everything that I know today, and I grew to appreciate those opportunities to have lunch with Dad and spend time with him,” he says.
These experiences have been instrumental throughout his journey at R&S Grating. He adds that the support of Stevo, Hockham and Skinner, helps to create a positive workspace where integrity and honesty help to drive
“PLENTY
the year has also marked a year of celebration for R&S Grating. The company is celebrating 50 years of manufacturing in Australia.
From its beginnings in the backyard stable, R&S Grating has grown to be successful and competitive on major government contracts, helping to maintain the safety and structural integrity of grates on Melbourne’s major connections, such as the Bolte Bridge, Tullamarine Freeway (Citylink), the M80
OF OUR WEAVE GRATES ARE STILL IN MANY PLACES IN MELBOURNE, SOME HAVE BEEN THERE FOR 25-30 YEARS. AND THESE ARE CONNECTIONS THAT ARE TRAFFICKED BY UP TO 100,000 MOTORISTS DAILY.”
further product improvements.
“Stevo was always so supportive of my father and myself, he was a big part of not only work, but also my upbringing and the life lessons I learned along the way,” Taeleipu says. “The apple doesn’t fall far from the tree with Tim. His understanding and care for everyone here speaks volumes of where he and the company are heading.”
PUSHING FORWARD
While 2024 has come with its challenges,
Ring Road and the new West Gate Tunnel Project, to name just a few.
A key part of the company’s growth was the innovative Weaved Sump Grates, regarded as its signature product.
Such was the innovation and popularity of the Weaved Sump Grate that R&S Grating’s initial concept was subsequently re-created by competitors in the market.
“At the time we weren’t getting a lot of freeway work, even though we had the best product for freeways. We had one of our weave grates tested and we
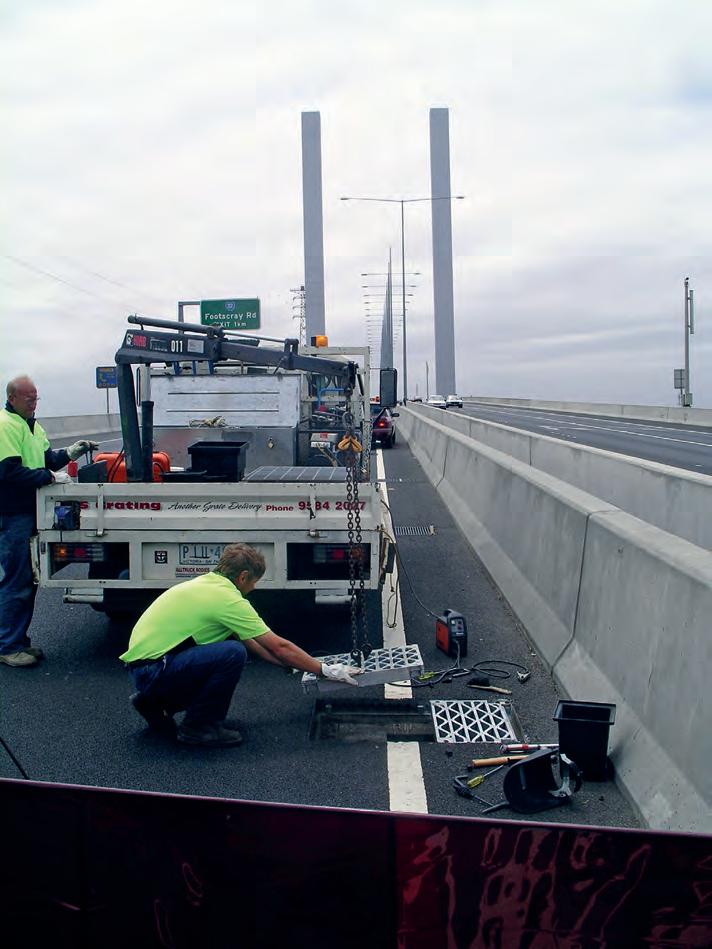
discovered that the grate had exceptional load sharing capabilities. After a report was conducted, we learnt that the uplift was greater than the downforce,” Skinner says.
“Effectively we were building a bridge, so we needed to have bridge-inspired technology in our grates if we wanted them to last. That’s where the extra bolt down came from. Plenty of our weave grates are still in many places in Melbourne, some have been there for 25-30 years. And these are connections that are trafficked by up to 100,000 motorists daily.”
R&S Grating’s weaved grates continue to be a popular solution. Hockham says it’s the versatility that’s added to the design’s longevity.
“We introduced the weaved grate in 1992, which coincided with the introduction of Australian Standards for access covers and grates,” he says. “Councils might’ve had their own requirements and standards, but there was nothing on a national level.”
The weave grate was among the first to provide a bike safe grate, with most
grate manufacturers at the time going for a traditional design. The way it’s welded makes it a very strong grate and more efficient by enabling the load bars to be at larger gaps, meaning less steel is involved in manufacture.
“Suddenly you had a very strong grate that was efficient, lighter and cheaper to produce, while also being bike safe. It was a big innovation that a lot of councils jumped on,” Hockham says.
“We look to continually innovate. We have an unwritten policy not to stagnate anywhere. We’re always looking at improving our products and optimising them to keep us competitive. That happens right across the board.”
This spirit of innovation lead to another success story for the company, with the development of its SMC Ecolite range of light-weight composite pit lids.
“We introduced a composite lid range around 15 years ago now,” Hockham says. “There were options available in the market, but these were made from a timber core, coated in fibreglass and were prone to damage and structural collapse. We introduced the
first full-depth composite pit lid into the market and worked hard to engineer it to be the lightest and strongest available. The hard work paid off and we’re now the leading supplier of composite pit lids in Victoria.”
For Skinner, it’s product consistency that continues to put R&S Grating in the box seat for upcoming contracts and opportunities.
“It’s extremely rare that one of our products fails. Occasionally we might lose a contract, then six to 12 months later, the contractor will come knocking at our doors asking if we can replace it,” he says.
“There’s been some horror stories where cheaper grates have been installed that don’t meet specifications and aren’t as safe as products made in Australia. R&S Grating has always had a reputation for quality, but it can be challenging when cheaper imports enter the market.
“At the end of the day, our grates work, and they’ve worked for years. The quality of our grates is the statement that we make to the sector. You put our product down, then you don’t need to worry about it again for years to come.”
LEAVING A LEGACY
When it comes to the future, Hockham says maintaining and improving R&S Grating’s product range is at the top of the priority list. So is continuing the strong platform for success that his father built.
“Dad was very proud to see one of his products in the ground. I just want to keep seeing our grates on important infrastructure. Seeing the R&S Grating name around Melbourne, as well as the growth of our team, is what fills me with the most pride,” Hockham says.
“Just the fact that we can have such a presence is amazing and it’s something that my family and many other families have been working on for five decades.”
He says, R&S Grating isn’t perfect, sure, but the drive of its team to eradicate imperfections is what’s helping to elevate its products and services from others in a competitive market.
“We don’t want anyone to remember R&S from our mistakes. We want to be remembered for what we did about those mistakes,” Skinner says.
“Even if it’s not our mistake, we approach each case in the same way. That’s who we are as a business.”
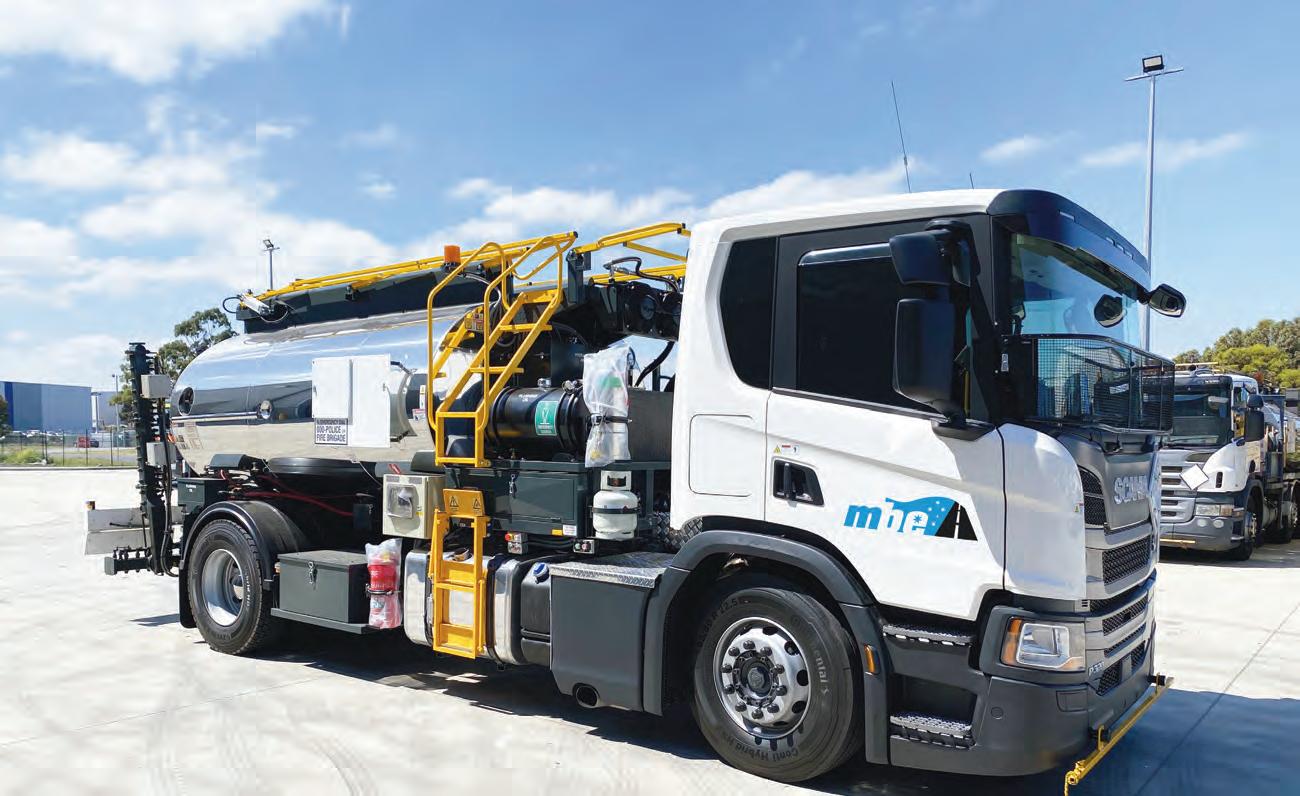
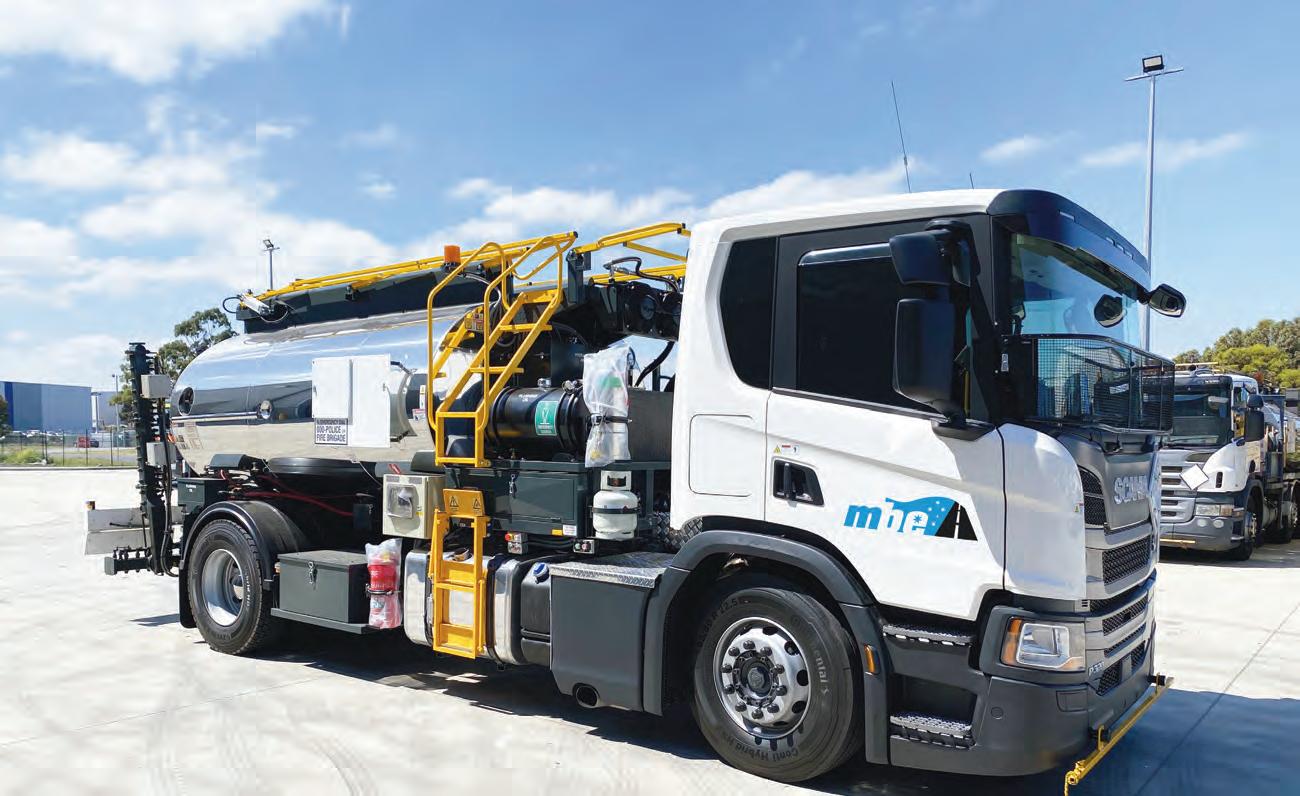
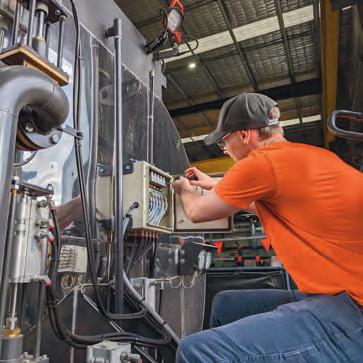
A MASTER-CLASS IN SUSTAINABILITY
CONTINUAL INNOVATION AND A COMMITMENT TO COMMUNITY HAS LED TO A BRAND NEW, WORLD-FIRST DEVELOPMENT FROM HIWAY. JIM APPLEBY AND ALLEN BROWNE EXPLAIN WHAT THE NEW MASTERS RANGE MEANS FOR SUSTAINABILITY IN INFRASTRUCTURE AND SOCIETY, AS A WHOLE.
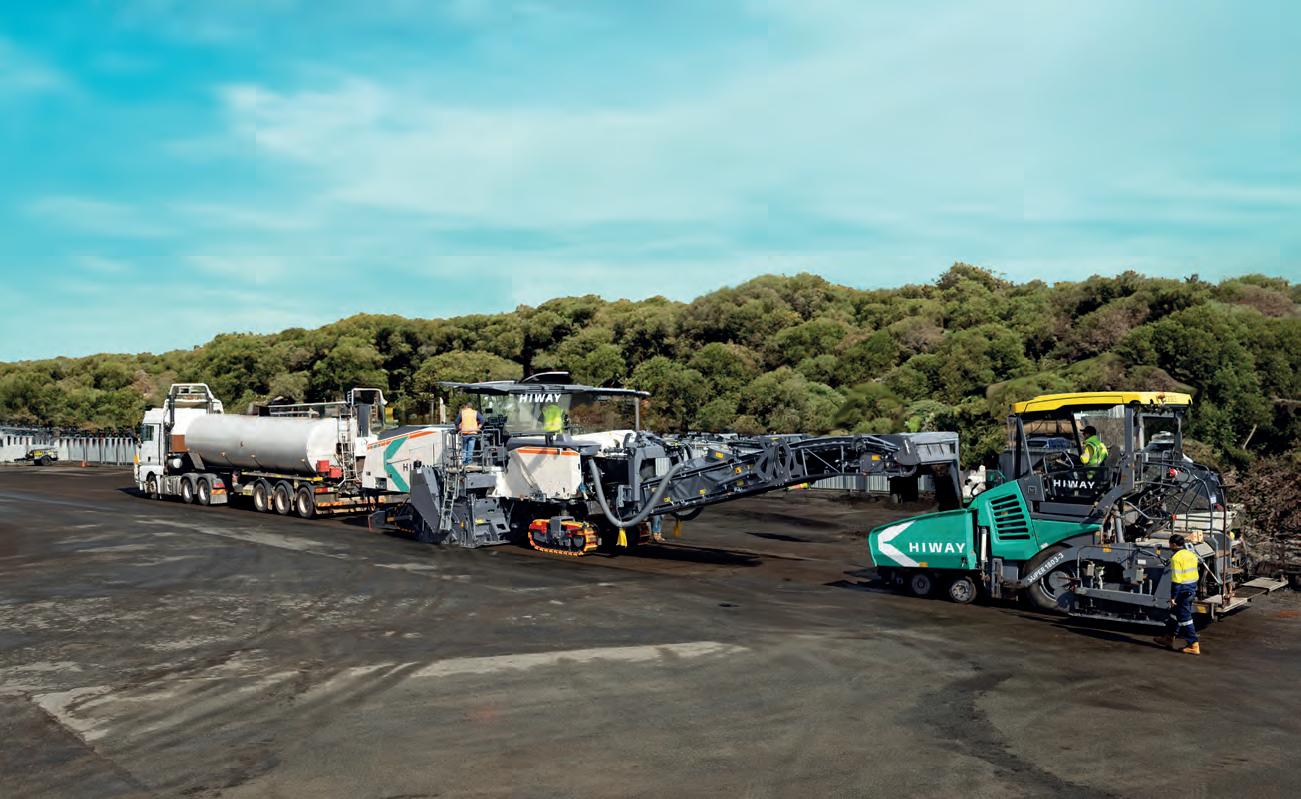
Sustainability is a concept that many companies claim is close to home. However, for a few, sustainability isn’t an additional focus area, but an aspect that guides every operational decision.
Hiway is one such company that’s constantly looking through a sustainable lens, assessing every opportunity in the hope to optimise the decarbonisation and long-term sustainability of its products and services while meeting performance requirements.
Sustainability is also an aspect that hits close to home on a personal level, especially for Hiway Chief Operating Officer Jim Appleby.
“We’re in an age now where carbon reduction is front and centre. Sustainability is rightfully getting the attention it deserves. At Hiway we have been working for some time on a range of sustainable outcomes that gives exactly what our clients need, all framed around carbon reduction and without technical compromise.” Appleby says.
“It’s exciting because I promised my daughters that we’d reach a sustainable future, and to be part of something that’s driving a better world makes me very proud.”
Allen Browne, Executive General Manager, Technical and Innovation – Hiway, says the company has a rich history in the sustainability space, helping the sector Australia-wide to achieve lower carbon outcomes.
“The company’s been recycling via the use of conventional or innovative binders for 38 years,” he says. “The market has come to us and recognised the importance of recycling and sustainability.”
Over the past 38 years, Hiway has worked closely with its customers to understand their needs and many of the issues surrounding traditional infrastructure products and service offerings. This understanding, combined with the company’s extensive research and development capabilities (and partners), has led to what Appleby and Browne refer to as the “global standard in sustainability and performance”.
As part of the company’s strong history
of adaption, Hiway is making changes to its internal structure to better cater for the needs of the market.
“We have a significant presence across Australia. We have operated under some incredible brands in different locations including SAT Civil in Queensland, W.A Stabilising in Western Australia and Hiway Stabilizers in all other states,” Appleby says.
“As part of our journey, we’re bringing all our brands under the one umbrella – a consistent brand under a consistent message. This will help to create a uniform approach to meet and drive our value for clients across all geographies.
“It’s giving commonality with no technical compromise, with no change to how we operate and even more belief in what we’re trying to achieve as a business.”
This rebrand echoes Hiway’s original DNA of being road recycling and stabilising practitioners, increasing its design and materials capability over time. Sustainability has been a constant, with the Masters Range set to further support its notion that ‘Our
communities deserve it. Our environment depends on it’.
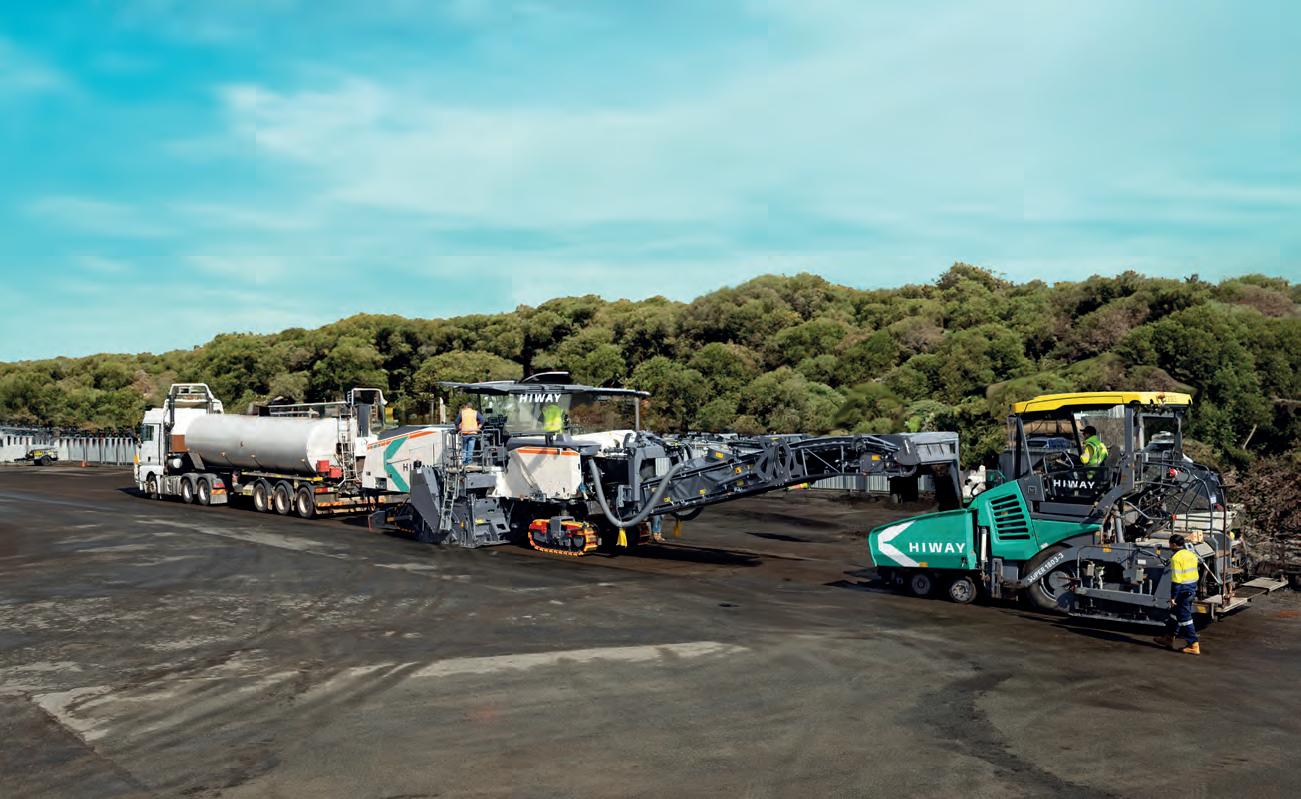
THE MASTERS RANGE
Hiway’s Masters Range is a collection of products and solutions with innovation at its core, focused on sustainability, durability and unsurpassed performance.
The Masters Range is ultimately designed to improve the quality of life and create a better future for the customers, communities and multiple sectors that Hiway services.
On top of its sustainability benefits and potential, the Masters Range will also help to provide unprecedented transparency to ensure that contractors and engineers are using the best and most suited option for their projects. As Browne explains.
“I see the Masters Range as a platform for clear, unambiguous messaging of the different applications and best utilisation,” he says.
“Broad terminology can create issues for engineers and the industry, that’s why we feel that the Masters Range allows us to better pigeonhole where some of the conventional and non-conventional binders sit.
“The amount of material you put in will determine the strength, durability, ability to handle deflection and related performance measures. The Masters Range will help designers cut through that uncertainty by showing what’s required to provide a different outcome.”
Just one of the highlights within the Masters Range is the recently developed MasterCarb A, carbon negative pavement, which has been developed in conjunction with research partner C-Twelve.
A world-first pavement solution, MasterCarb A delivers a cold in-situ recycled asphalt with superior load capacity, durability, and moisture resilience. Setting a new standard for basecourse layers, it’s both time and costeffective while, critically, achieving a carbon negative outcome for the entire process. With high modulus, fatigue capability, rut resistance and reduced construction times, MasterCarb A, along with the wider Masters Range, will help to reduce quarrying and cartage of virgin materials, therefore reducing the strain on Australia’s transport network and precious aggregate resources.
When discussing MasterCarb A, Appleby says: “To say it’s catching people’s attention would be an understatement. When you talk about the performance levels that are being achieved and the carbon negative outcome that’s associated with it, it’s groundbreaking.”
Hiway’s MasterCarb A represents an exciting
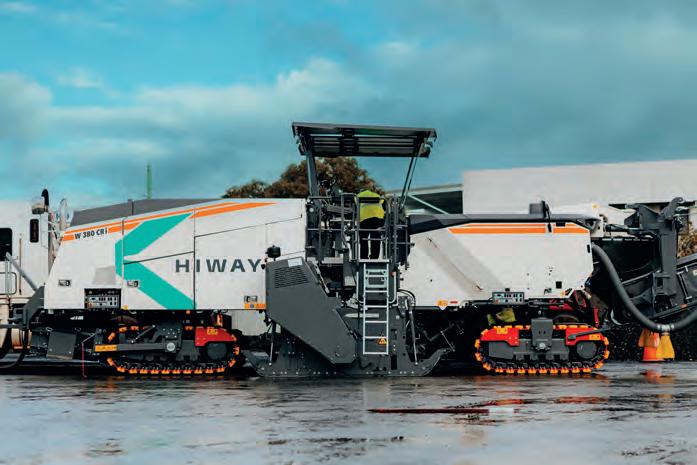
advancement in pavement technology with decarbonisation at its core. By blending a proprietary modified binder with a laboratory-designed carbon sequestration medium, this solution delivers a robust, high performing pavement that surpasses conventional solutions and plant-produced dense asphalt. The innovative approach behind MasterCarb A lies in its utilisation of recycled materials to produce a pavement that exhibits asphalt-like characteristics, yet outperforms hot-mix asphalt, while delivering maximum environmental benefits.
Findings from a recent large-scale project in Watheroo achieved a carbon negative outcome of minus 54,200 kilograms in
“The Masters Range will incorporate materials, services and processes, all formulated to give a client a different outcome to what they might’ve been able to achieve in a traditional format. It’s not just about materials, it’s about solutions” he says.
“There’s a dozen Masters Range processes or materials that give a whole spectrum of coverage to the transport and wider infrastructure sector to decarbonise, be more efficient and reduce costs, while providing a greater technical outcome.”
“I SEE THE MASTERS RANGE AS A PLATFORM FOR CLEAR, UNAMBIGUOUS MESSAGING OF THE DIFFERENT APPLICATIONS AND BEST UTILISATION.”
Scope 1 to 3 total carbon emissions, underscoring MasterCarb A’s significant contribution to sustainable infrastructure.
Further testing has been completed and will continue to provide greater confidence in the design and durability of MasterCarb A, as Browne adds.
“We are getting a huge amount of interest from all different sectors. We’ve done some large-scale field trials and now we’re looking to implement project level contracts both in the private and public sectors,” he says.
“The high-level research that we’re doing to support the process and provide context around performance has been important because it’s so different and so unique to conventional products. We’ve got research partners and great relationships with laboratories, it’s really exciting to see the development path from proof of concept to Masters Range roll-out.”
Appleby says the MasterCarb A is just a taste of what the overall Masters Range
Hiway is always looking to improve its products and services to stay ahead of industry requirements and demands, as the company’s history of pioneering reflects.
“To be able to alter your approach for the specific needs of the sector is a really important facet, to provide the right solution for the right circumstance. We’re very outcome and performance driven in the low emission pavement construction and rehabilitation space,” Appleby says.
With solutions such as the upcoming Masters Range, as well as the company’s rich history of developing and catering for infrastructure projects of all sizes, Hiway looks set to maintain its reputation as one of the industry’s leading innovators in the space.
But the company never rests on its laurels.
“I’m so proud of the progress we’ve made so far in the space. We genuinely want to see the best outcome for all our partners and that’s a philosophy that’s endured to this day,” Appleby says. “That’s the reason why people have been wanting to work with us again and again for 38 years. We’re still going strong and there’s no signs of slowing down.”
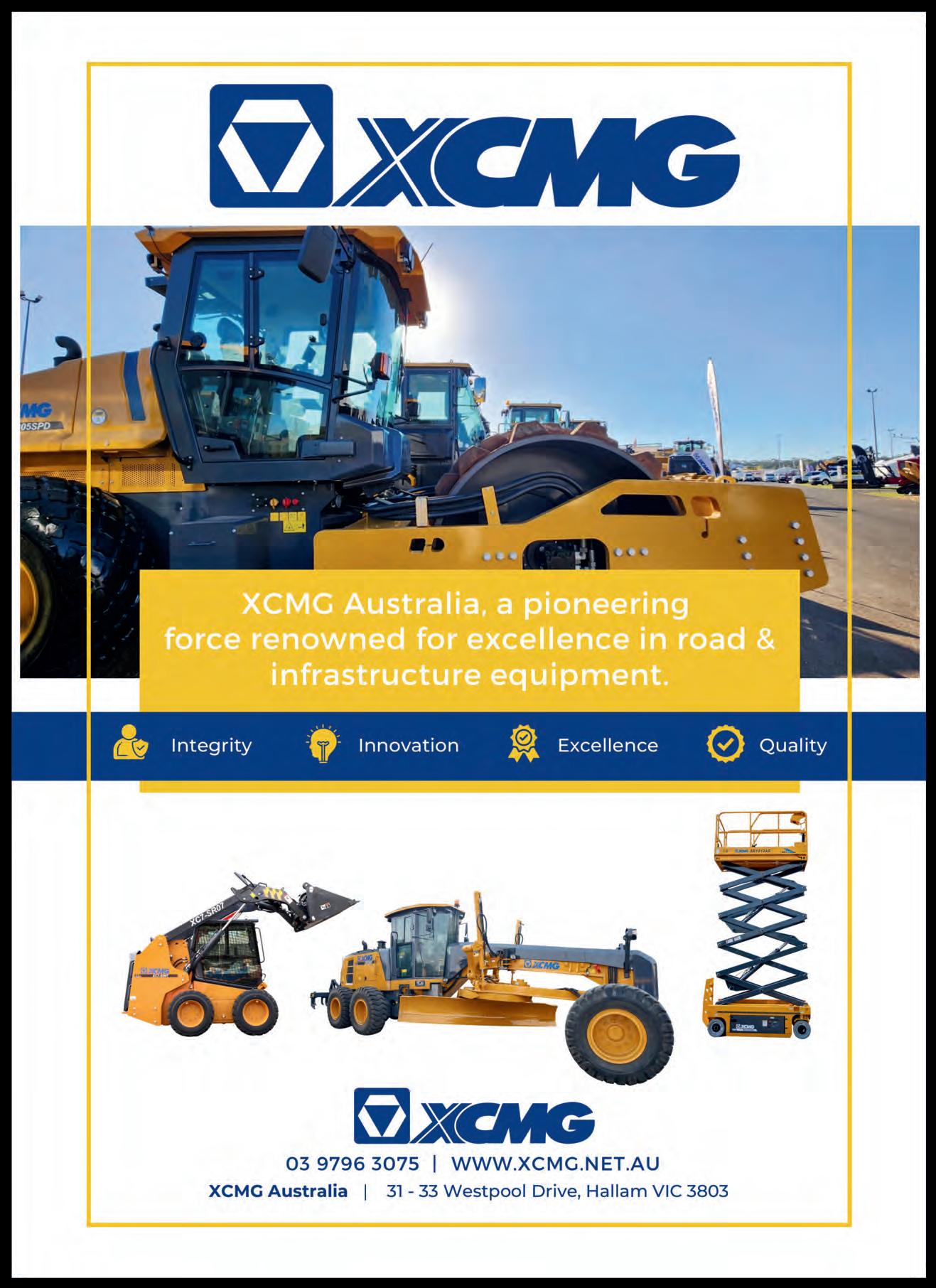
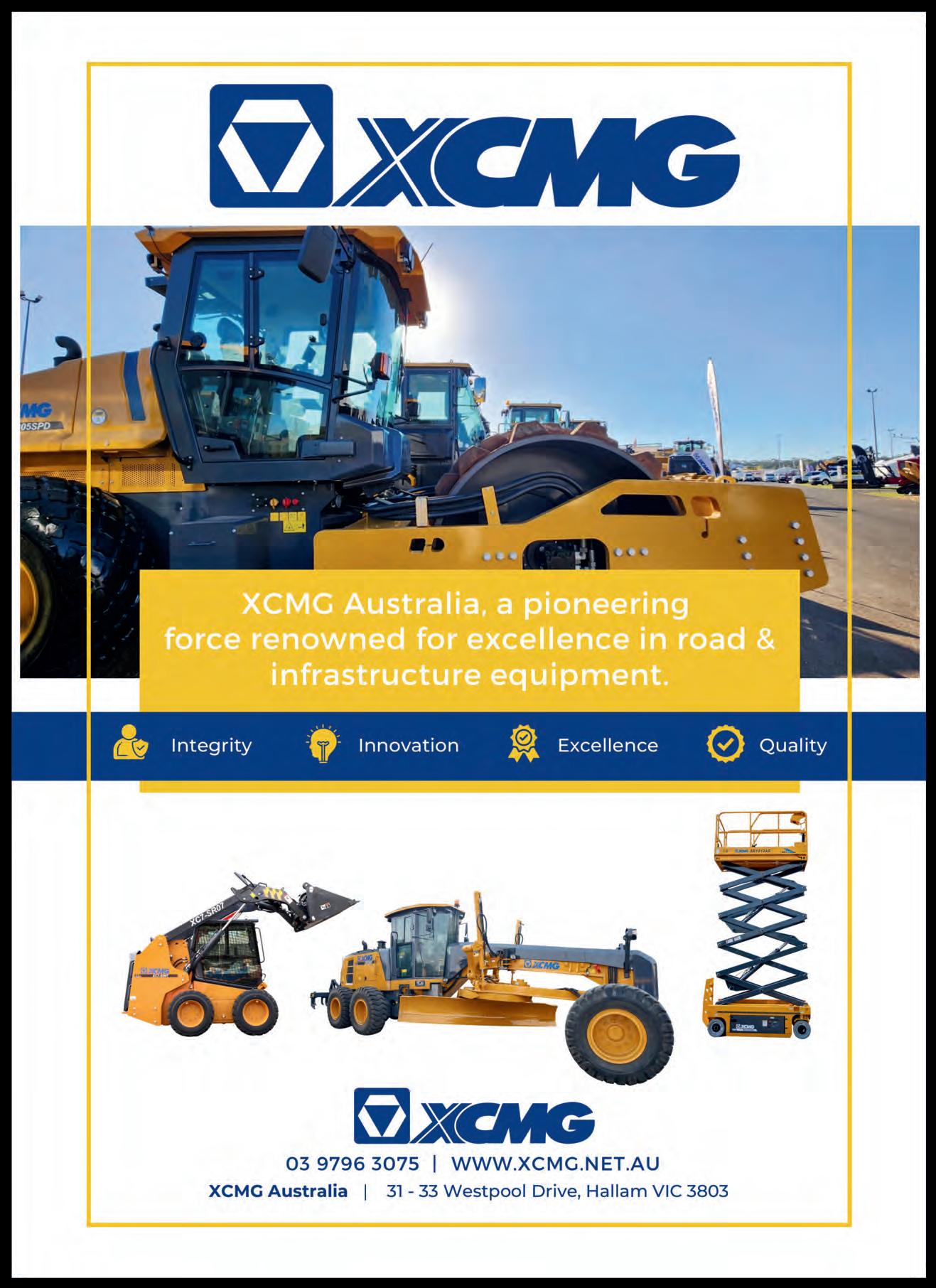
SUSTAINABLY SAVING LIVES,
THE ARMORZONE TEMPORARY BARRIER IS NOT ONLY MORE SUSTAINABLE THAN CONVENTIONAL ROAD BARRIERS, BUT IT’S PROVEN TO OUTPERFORM AND OUTLIVE CONVENTIONAL DESIGNS. ROADS & INFRASTRUCTURE SITS DOWN WITH THE CONGLOMERATE RESPONSIBLE FOR THE PRODUCT’S MANUFACTURE AND DISTRIBUTION TO LEARN MORE ABOUT ITS GROUNDBREAKING DESIGN.
Distracted, speeding or inexperienced drivers can pose a number of risks on local roads, not only to other motorists, but also pedestrians and nearby workers.
Protecting roadside workers has been, and is very much today, a topical subject, with many near-misses and too many fatalities still occurring.
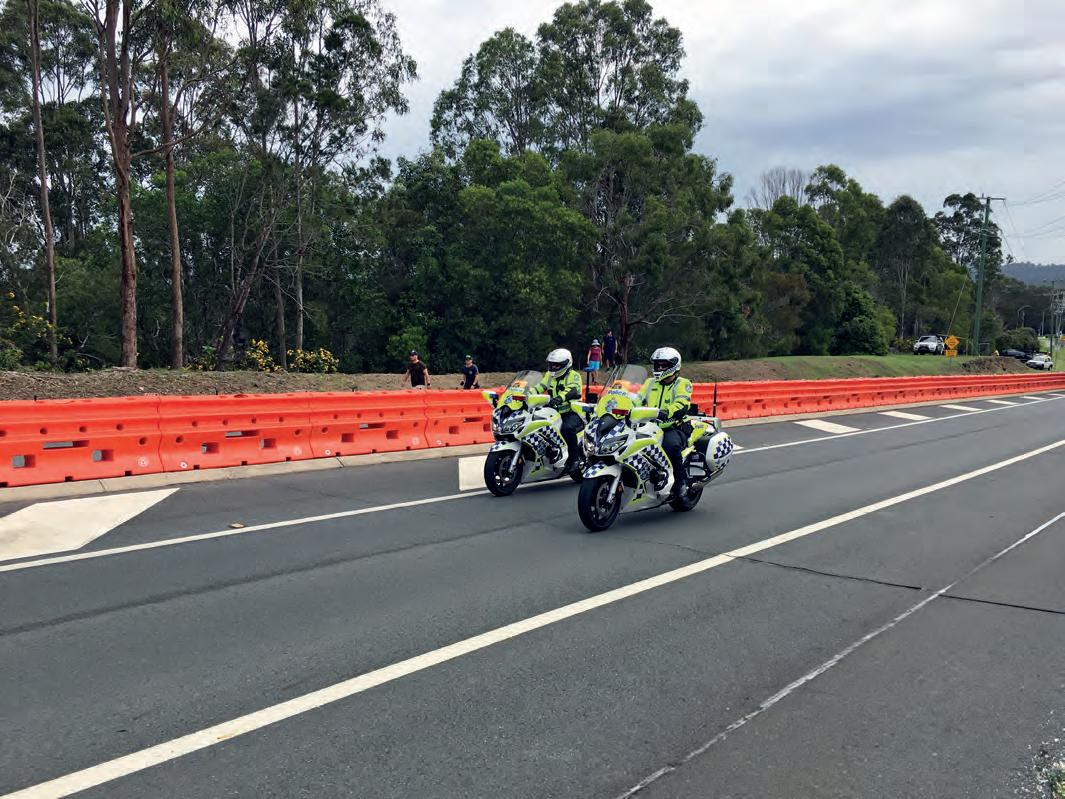
The Traffic Management Association of Australia’s 2024 National Traffic Controller Safety Survey highlights this issue, with 49 per cent of respondents reporting that they’ve nearly been struck by a distracted driver, and 44 per cent saying they’ve had near misses due to speeding vehicles. These are just some of the reasons why road barriers – temporary or permanent – are a standard requirement for most roadside, commercial and residential projects.
In a market that’s saturated, one roadside barrier has long been a successful option for road and infrastructure projects.
A plastic unit joined together using steel pins and filled with water, ArmorZone is a temporary work zone barrier, able to be
In the past 18 months, Ingal Civil Products and its manufacturing partners have managed to build upon what was already a popular design. The aim was to make the barrier more sustainable, as John Annison, Operations Manager – Ingal Civil Products explains.
“About four or five years ago, the International Crash Rating System was upgraded because cars and trucks around the world were getting heavier,” he says. “Crash barriers had to be improved as a result and that’s when development began on the MASH version (Manual for Assessing Safety Hardware).
“A lot of our customers were upgrading their road barrier fleet to the new MASH versions, and they were looking for a way to dispose of their older barriers. We started to look into how we could recycle the older versions of the ArmorZone, as it’s a
ArmorZone barriers. One of the first steps was partnering with organisations that could facilitate material testing and application.
This led Ingal Civil to the New Zealandbased roto-moulding experts in Vision Plastics and AR Moulding.
A TEAM EFFORT
The ArmorZone barrier is manufactured using a process called rotational moulding, a process by which a plastic material in powdered form is placed into a hollow mould, before being rotated and heated, making it a cost-effective process to manufacture large hollow plastic components.
Vision Plastics (VPLAS) is a rotational moulding material specialist. Steve Lewis, Sales and Marketing Manager, New Zealand – VPLAS says the unique formula used for
the ArmorZone is what gives the product its premium performance characteristics.
“It’s a formulation that’s got a very good balance of stiffness and impact that’s required for such a product,” he says. “It’s a huge physical demand that’s placed on the plastic, which is part of the reason why we’ve got very tight specifications with our suppliers and the production process.
“We can’t substitute materials, it’s this material or nothing and it took years to develop it, which is why there’s been a number of unsuccessful replications of this product from other providers.”
To manufacture the ArmorZone barriers, Ingal Civil Products works closely with AR Moulding, who (as the name suggest) help to mould the plastic and finish the final product to ensure that it fits industry requirements and expectations.
As Jason Walker, General Manager – AR Moulding recalls, ArmorZone had long been a successful product, but the recycling aspect added fuel to the fire.
“Ingal Civil Products’ client’s desire to be different in the market is really what initially drove the recycling aspect. They were making a push to contribute more to the circular economy, hoping to have an outcome that wasn’t just sending these products to landfill,” he says.
“We all said ‘yep, we can make that happen’. The focus then was to find a percentage/mix that would work, to see exactly how much recycled and virgin material we’d require to produce a stable product that would meet industry requirements.”

As a fellow New Zealand-based business, both VPLAS and AR Moulding share a close relationship. Lewis says this professional partnership, as well as VPLAS’ strict focus around quality, ensure that Ingal Civil Products can distribute the best product possible.
“AR Moulding is about a kilometre away from our site and I’m down there nearly weekly for a catch-up, which enables us to have our raw materials supply in line with their demands,” he says.
“It takes a group effort to make sure that Ingal Civil Products is adequately supplied. There’s a lot of requirements around recycled feedstock, which we’re sourcing from New Zealand and Australia. It’s important that the recycled feedstock is controlled and we put a lot of effort into ensuring that.”
It’s a relationship that’s strengthened by a commitment to helping both companies achieve quality outcomes for their customers, as Lewis adds.
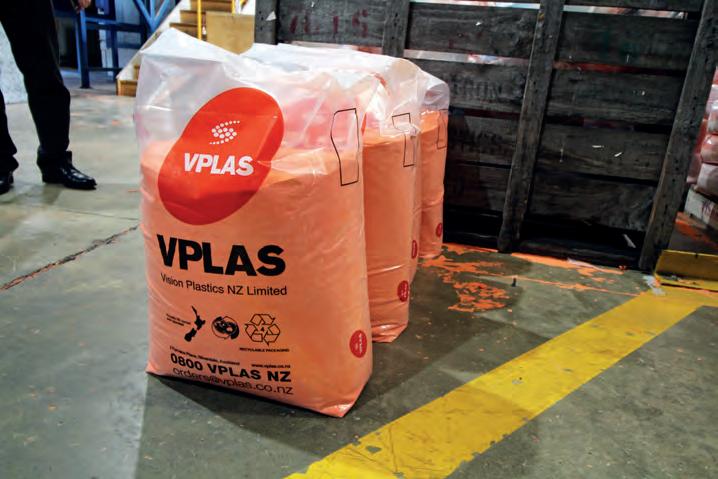
“Because we’re just around the corner, I have an intimate knowledge of their processes, to the point that I can run their machinery,” he says. “We spend a lot of time at AR Moulding, ensuring that both ours and their processes are consistent. That includes testing, which there is a lot of before all boxes can be ticked and the barrier can
“The communication and relationship between AR Moulding and VPLAS is a hugely important part of this product’s success.”
Walker says this trust between the two companies has helped to make what was
“There’s no secrets between us,” he says. “Our common goal with VPLAS and Ingal Civil Products was to make a greener plastic product. Plastic is often considered a dirty word, because most associate it with soft plastics.
Contractors can satisfy both specification and sustainability requirements for their projects by using ArmorZone road barriers.
“With ArmorZone, we’ve shown that the final recycled product can perform as good, if not better than virgin materials. We’ve demonstrated that it’s feasible to reuse plastic to give it a second life, and even maybe a third or fourth life and so on.”
PATH AHEAD
Despite only being released for a number of months, the ArmorZone – which satisfies both MASH TL-1 and TL-2 specifications – has already seen a high level of interest.
Annison attributes the majority of such interest to the changing needs of the market, where the depth of sustainable practices can make or break a tender submission.
“Both private and public sector projects across the country are adding sustainability clauses into their contracts, insisting that contractors and suppliers provide a product that’s sustainable and can be recycled,” Annison says.
“From a commercial point of view, having a barrier that ticks all of these boxes, that can give a commercial advantage, is a no-brainer. That’s being driven by our customers, as they’re the ones wanting to have sustainable products to offer in their hire fleets. The whole supply chain is on board as well.”
And Ingal Civil Products isn’t stopping there.
“It’ll take more testing and approvals, but we are looking at ways to increase the recycled content in the barrier. That’s the main driver at the moment, first and foremost to increase the recycled content. We’re fairly confident we’ll be able to,” Annison says. “It’s a great story and we’re just getting started.”
Owners of ArmorZone barriers in Australia and New Zealand can contact Ingal Civil Products for instructions on where to send their units for recycling into new ArmorZone barriers.


PICK THE RIGHT TOOL
Proud Suppliers of Telescopic Bitumen Sprayers to the Australasian Roading Construction market for over 20 years
Over the last 20+ years, we’ve listened to our customers’ feedback and continuously evolved our range of sprayers, meeting the specific and unique demands of the Australasian roading market.
From our brand new 4.0m emulsion only telescopic sprayer, through to our highly manoeuvrable 4.5m telescopic urban sprayers right up to our 6.0m reseal sprayers we have the right sprayer for the job – all offering the ease of use and efficiency of our telescopic spray bar.
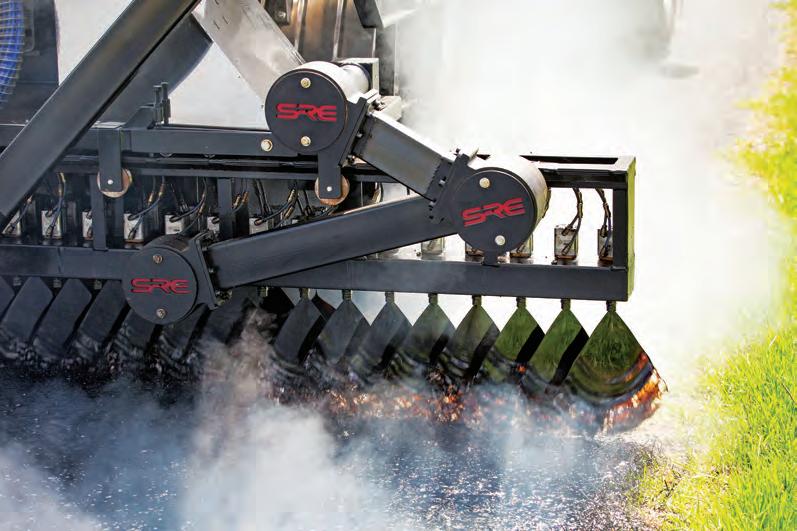
Find out today why operators across Australia and New Zealand are ditching fixed wing sprayers and demanding SRE’s range of telescopic bitumen sprayers.
www.specialisedroadingequipment.com
Email info@specialisedroadingequipment.com
Ph +64 7 848 1197
AS PURE AS IT GETS
IN A WORLD WHERE SUSTAINABILITY IS AT THE FOREFRONT OF CORPORATE CONCERN, INDUSTRIES ARE PROACTIVELY EXPLORING THE POTENTIAL TO SUBSTITUTE A PORTION OF THEIR PRODUCTS WITH SUSTAINABLE ALTERNATIVES. AS HAMIDREZA SAHEBZAMANI, PHD, MIEAUST, TECHNICAL SERVICES MANAGER – SAMI BITUMEN TECHNOLOGIES WRITES.
Often, alternative materials are derived from waste or by-products. The primary objective of using these alternatives is to meet one or more of the following targets: enhancing technical properties, reducing carbon emissions, supporting the circular economy, improving sustainability targets, and cutting costs.
Some of these alternatives can be utilised directly without any modifications, while others necessitate additional processing to ensure safety, or to enhance their properties.
As the global drive to reduce carbon emissions and non-renewable resource usage gains momentum, it can create potential doubts. This transition may open the way for the usage of materials that have yet to be proven safe and of effective performance.
Regarding the road industry, we must bear in mind that the most sustainable road is the one that lasts the longest. There is no advantage in constructing a road with a lower initial carbon footprint but a reduced lifespan when compared to traditional ones. The carbon cost of maintaining or prematurely reconstructing pavements may negate the initial gain of low carbon footprint if the pavement doesn’t have the same longevity.
Consequently, the whole of life carbon footprint would be higher. It is also necessary to consider the rolling resistance of roads. Notably, a road that is not smooth can generate additional emissions from cars and trucks that may exceed the carbon footprint of the road’s entire construction.
WEO AND REOB
Lubricating oils derived from petroleum are used in a variety of applications, ranging from the lubrication and protection of engine parts to heat and power transfers. Over time, depending on their application and operating environment, these oils become contaminated or otherwise degraded, resulting in what is known as Waste Engine Oil (WEO).
Despite its contamination and apparent dirtiness, WEO never becomes entirely unusable. In fact, WEO is recyclable and can be re-refined back into lubricating oils. The re-refining process employs distillation and
hydrotreating. WEO is dehydrated under atmospheric pressure to remove water and light hydrocarbons.
Atmospheric distillation then separates the reusable lubricating oil from the heavy oil. Vacuum distillation further separates the reusable lubricating oil into re-refinable base oil and a non-distillable residue, known as REOB or Vacuum Tower Asphalt Extender (VTAE).
The re-refinable base oil is further processed into re-refined base oil stocks, ready to be used in the production of new lubricating oil. Re-refined Engine Oil Bottom (REOB) or Vacuum Tower Asphalt Extender (VTAE), are the non-distillable residue from the WEO refining process.
Any re-refined products derived from used oil that do not meet this definition should not be referred to as REOB/VTAE, and the degree of their usage in asphalt production remains uncertain.
REOB comprises approximately 12 per cent of the total WEO composition.
It consists of higher boiling components, typically containing paraffinic lubrication oil, residual additives, and engine wear metals.
REOB can contain as much as 60 per cent residual lubricating oil, about four per cent polymer, and various soluble metals, which account for about five per cent of the total REOB composition1. Figure 1 shows the process of re-refining used oil and where the REOB/ VTAE is produced.
SAFETY
Used oils (WEO) can contain Polycyclic Aromatic Compounds (PACs), with some of these compounds classified as carcinogenic. During the processing of used oil in a vacuum tower refining system, PACs are typically removed from the residuum (bottoms). REOB/VTAE materials have been found to contain only trace levels of PACs.
Concerns have been raised about the PAC content in REOB/VTAE due to potentially carcinogenic levels in used oil. To investigate this concern, the Asphalt Institute conducted research, collecting seven samples at different stages of the re-refining process and testing
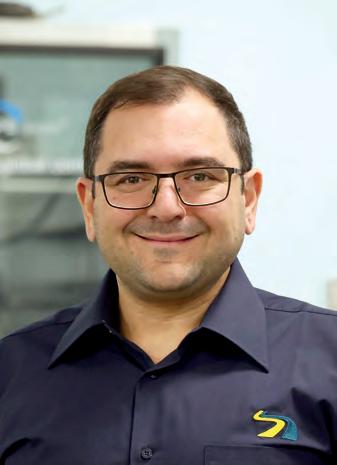
them for mutagenicity index (MI) and PAC levels which are measures of carcinogenicity of a chemical substance.
Samples taken before vacuum distillation exhibited high levels of MI and PACs, indicating a higher risk of carcinogenicity; however, these levels were significantly reduced in samples taken after the vacuum distillation process2
Currently, REOB/VTAE is not recognised as a carcinogen, although ongoing research is exploring more on this.
This highlights the importance of suppliers clearly declaring the contents of bitumen when they use any stream of re-refined used oils.
TECHNICAL PERFORMANCE
In the United States, some State Departments of Transportation (State DOTs) have raised concerns about pavement durability and may restrict the use of REOB. A review of State DOT specifications conducted in 2022 revealed that five State DOTs permit the usage or limited use of REOB. Among these, there was no consistent maximum usage limit; one State DOT allows up to 5.0 percent, while another permits a maximum of 8.0 percent.
The remaining three State DOTs impose no limits. Additionally, thirty-one State DOTs have no stated restrictions, with two requiring prior approval for potential use, and fourteen State DOTs do not allow the use of REOB1
Research on pavement performance impacts has yielded conflicting conclusions. There is
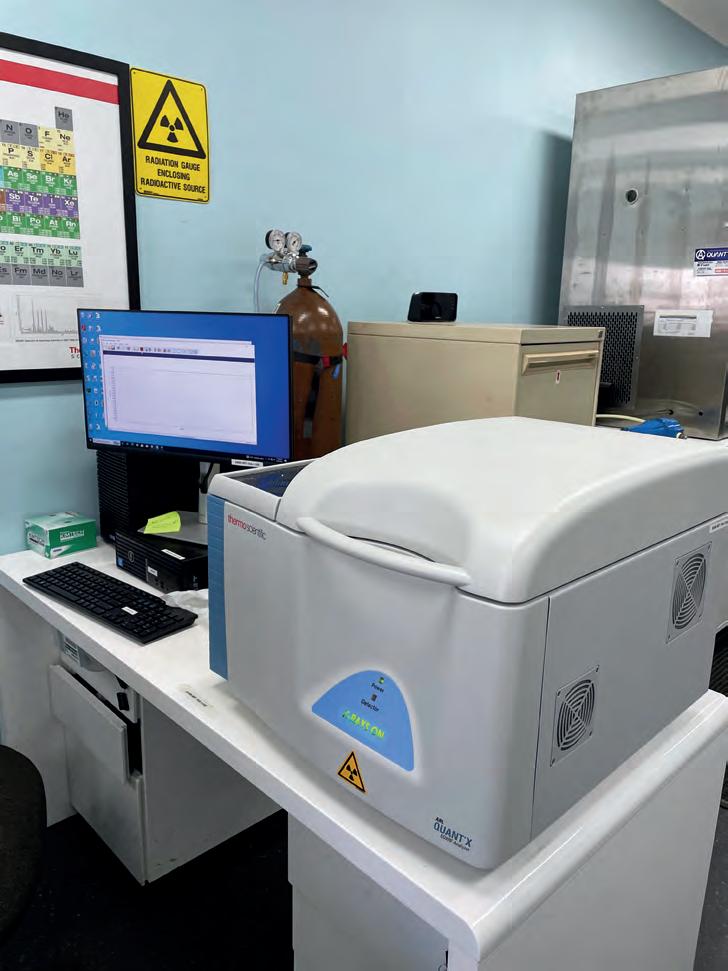
limited information regarding the comparative field performance of mixtures made with binders containing REOB/VTAE versus those without.
Some studies suggest that REOB/VTAE adversely affects the aging characteristics of bituminous binders, consequently reducing the cracking resistance of in-service pavements. In contrast, other researches indicate that asphalt mixtures blended with REOB/VTAE perform equally well or better than those made with neat bitumen of comparable stiffness.
The literature is inconsistent, with some authors asserting that REOB/VTAE is innocuous, while others warn of potential detrimental effects on performance. Furthermore, data indicate that the performance of binders and mixtures containing REOB/VTAE depends on the dosage, the source of REOB/VTAE, and the source of the bitumen. [1, 2, 3, 4, 5, 6, 7, 8]
Numerous studies suggest that current binder specifications require improvement to accommodate REOB use, such as extending Pressure Aging vessel (PAV) aging to better characterize all types of modified binders.
X-Ray Fluorescence (XRF) technology has been identified as a qualitative tool for detecting the presence of REOB/VTAE in bitumen.
A recurring theme in the research highlights the significant impact of aging on the relaxation properties of mixtures and binders. Extended PAV aging (greater than 20 hours) may be necessary to distinguish performance differences in binders that age variably.
The addition of recycled asphalt pavement (RAP) tends to make ΔTC more negative, as these materials are significantly aged in the field. Additives containing paraffinic base oils, when combined with REOB/VTAE, have been shown to accelerate the rate and extent of m-control in a binder (leading to a more negative ΔTC). The presence of REOB/ VTAE can adversely affect binder relaxation properties as it ages.
The Asphalt Institute has recommended further exploration of the binder parameter
ΔTC after 40 hours of PAV as a more effective method for characterizing long-term binder durability and performance (over five years)2 However, recent research suggests that this parameter may not be a reliable indicator for polymer-modified binders.
Studies have also shown that even trace amounts of REOB in bitumen can render it unsuitable for producing emulsion. Over the past two years, some incidents have occurred regarding the quality of bitumen emulsion in the Australian pavement industry.
Internal research by SAMI indicated that the base binder used for these emulsions contained trace metal elements typically found in REOB products, underscoring the importance of responsible usage of these additives and transparent declarations.
DETECTION
It is not possible to directly identify or quantify the exact content of REOB in bitumen. However, because bitumen does not naturally contain certain elements found in REOB, one can reasonably infer that the presence of these elements in bitumen suggests the potential inclusion of REOB. Several instrumental analytical techniques are available for determining and quantifying these elements. These methods include graphite furnace atomic absorption (AA) spectroscopy, inductively coupled plasma spectroscopy (ICP), energy dispersive X-ray fluorescence spectroscopy (EDXRF), and wavelength dispersive X-ray fluorescence spectrometry (WDXRF)1
The EDXRF method is versatile, capable of analysing various matrices, including solids, liquids, and powders. It typically covers an elemental range from sodium to uranium on the periodic table, with concentrations ranging from sub-parts per million (ppm) to 100 percent.
Elements with higher atomic numbers generally have better detection limits than lighter elements with lower atomic numbers. In EDXRF, X-rays produced by a source, such as
an X-ray tube, irradiate the sample.
The elements in the sample emit fluorescent X-ray radiation with discrete energies characteristic of those elements. By measuring the energies of the emitted radiation, one can identify which elements are present (qualitative analysis). Additionally, by measuring the intensities of these emitted energies, it is possible to quantify the amount of each element present in the sample (quantitative analysis)1
RESPONSIBLE USE
REOB/VTAE has been utilised in the bitumen industry for several years and is currently gaining increased attention due to sustainability targets and the push for cost optimization within corporations.
The use of this type of additive should be approached with caution and responsibility, ensuring clear communication with customers. There are several inconsistencies regarding the performance of asphalt and bitumen, particularly with emulsions made using these additives.
Additionally, certain streams in the rerefining process of waste engine oil have been shown to pose safety risks. It is essential for governmental regulations to be established to ensure transparency in these practices.
It is also crucial for users of bitumen to have a full understanding of the materials they are working with. At SAMI, we are committed to this principle and have recently set up an EDXRF device in our central laboratory in Camellia, NSW.
This device can detect trace elements in bitumen samples, enabling us to identify any unknown materials.
This technology and process are available to serve all stakeholders in the pavement industry, ensuring that binder users and producers can be confident that the product they are using is genuine and meets their specifications. This will decrease the risk of reduced quality and problems in production, especially with emulsions.
REFERENCE:
1. Responsible use of re-refined engine oil bottoms (REOB) in asphalt binder, 2023, FHWA
2. State of the knowledge – The use of REOB/VTAE in asphalt – IS-235, 2016, Asphalt Institute
3. Evaluation of rejuvenator’s effectiveness with conventional mix testing for 100% RAP mixtures, Martins Zaumanis, Rajib B. Mallick, Robert Frank, TRB 2013
4. The performance of aged asphalt materials rejuvenated with waste engine oil, Christopher D DeDene, Zhanping You, IJPE 2014
5. Five year performance review of a northern Ontario pavement trial: Validation of Ontario’s double-edge-notched tension test (DENT) and extended bending beam rheometer (BBR), S.A.M. Hesp, S.N. Genin, D. Scafe, H.F. Shurvell, S. Subramani, CTAA, 2009
6. Asphalt cement loss tangent as surrogate performance indicator for control of thermal cracking, Abdolrasoul Soleimani, Shanon Walsh, Simon A. M. Hesp, TRR, 2009
7. Effect of waste engine oil residue on quality and durability of SHRP Materials Reference Library Binders, Kelli-Anne N. Johnson, Simon A. M. Hesp, TRR, 2014
8. Cold winter and early asphalt pavement cracking observed in Ontario, Ludomir Uzarowski, Gary McDonald, John Rizoo, Gary Moore, Vimy Henderson, CTAA, 2015
THE FUTURE OF ROLLERS
IN STRIVING FOR OPTIMUM SUSTAINABILITY, TRANSPORT NSW HAS PURCHASED 38 SOIL AND ASPHALT DOUBLE DRUM ROLLERS FROM DYNAPAC CEA. SO WHY AND HOW DID DYNAPAC FIT THE BILL? ROADS & INFRASTRUCTURE FINDS OUT.
Dynapac’s long history of delivering high-quality products and services that contribute to customers’ sustainable productivity remains at the forefront of its brand promises.
Dynapac, much like its partners in the public and private sectors, shares an ambition towards greener and greater outcomes for construction projects. One such partner is Transport NSW.
Through its Transport Sustainability Plan, annual reporting and Transport Net Zero and Climate Change Policy, Transport NSW upholds its mission to remain eco-friendly.
Following federal guidelines to use clean energy on construction sites, Transport NSW follows the highest emission control standards.
Dynapac CEA is currently delivering 38 new soil and double drum rollers, all with Stage V engines, to Transport NSW, in line with the
authority’s mission to lead the development of safe, efficient and sustainable transport systems for New South Wales citizens.
Kerry McCauley, Dynapac CEA Brand Leader, says it was an important component of the tender for Transport NSW to have rollers equipped with Stage V engines.
“In Australia the legislation requires a minimum of tier three engines, that is the standard engine and the type most companies choose to go with,” she says.
“However, Transport NSW opted to buy all Stage V engines so they can meet the highest environmental criteria possible. They wanted the cleanest energy we could give them.”
GETTING STARTED
This time last year Dynapac CEA, along with a collection of other manufacturers, gathered to meet with Transport NSW to
undergo a product demonstration. Present at this demonstration were a selection of Dynapac’s Soil and Double Drum Rollers.
As McCauley explains, Dynapac was a front runner from the beginning, for multiple reasons.
“To win the tender you had to score well not only from an operators’ perspective, but also on all service points,” McCauley says.
“Transport NSW found our operator assessments to be best in class in terms of ergonomics, operator platform, visibility, and comfortability,” she says.
Daniel Axiak, Regional Manager Oceania, Dynapac says Transport NSW required 42 new Soil and Double Drum Rollers, 38 of which were chosen from Dynapac.
“The 38 rollers will be used for Transport NSW’s replacement program, which involves mostly rehabilitation and maintenance programs working on existing roads across regional road networks,” he says.
“While Transport NSW might use the rollers to build some new roads, the rollers will mostly be used for the rehabilitation of current existing road infrastructure.”
Soil Rollers included in the tender were a mix of smooth drum rollers, which provide pressure to the soil by compacting it to produce an even and uniform surface, as well as versatile Padfoot rollers, which cater for a range of applications on cohesive materials such as clay, silt and disintegrated rock.
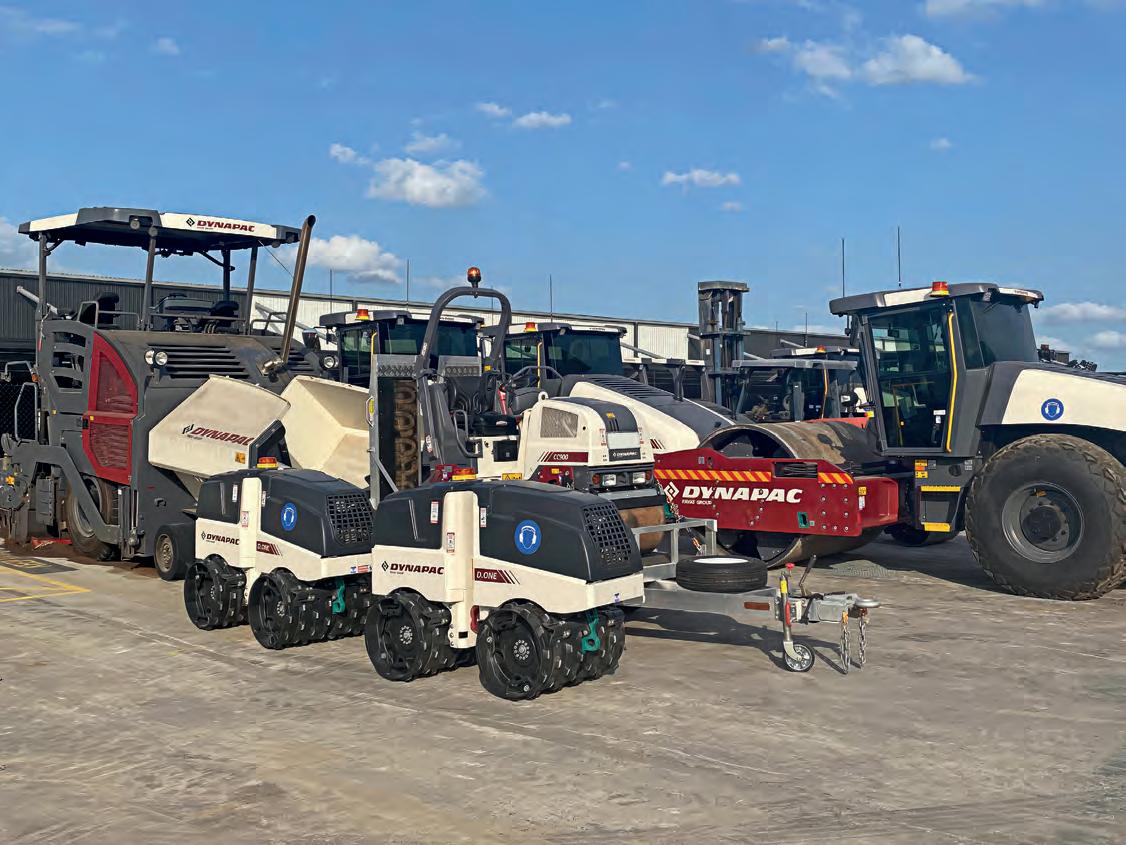
The order included a mix of CA1300PDB – five tonne, CA4000D 13 tonne Smooth Drums, CA5000D 16 tonne Smooth Drums and CA6000D 19 tonne Smooth Drums.
The Dynapac CA6000PD front
roller will keep the team confident and healthy when working on the job site.
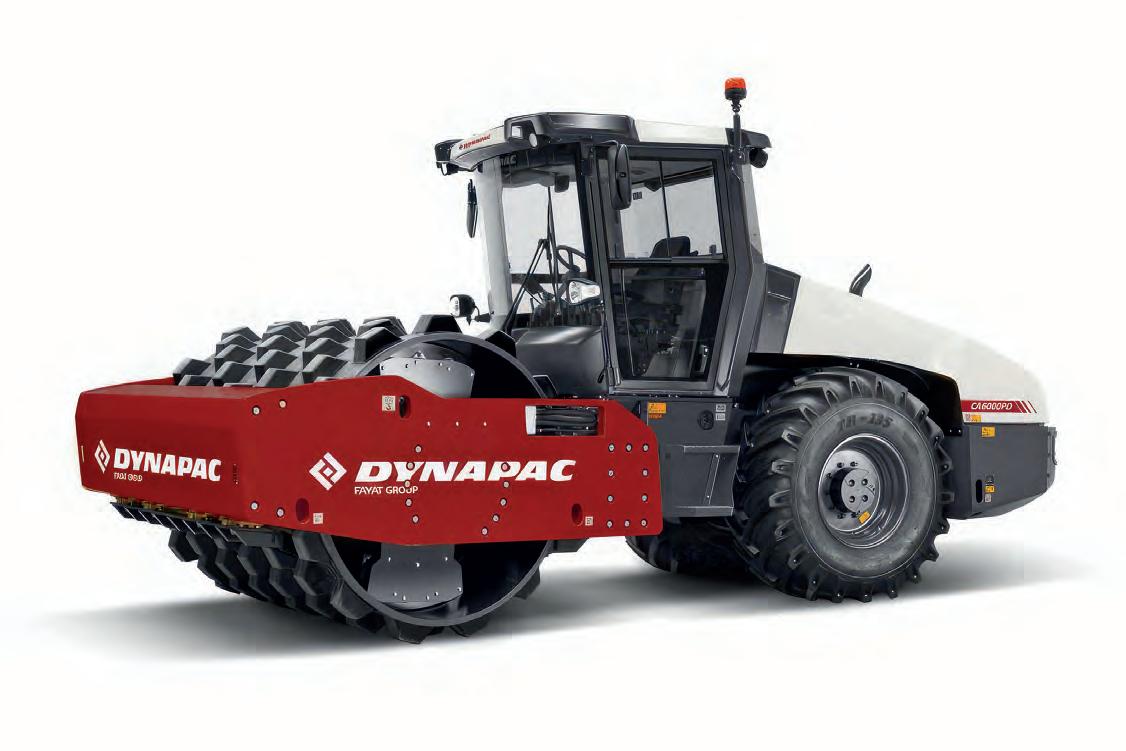
Padfoot rollers listed in the order include CA4000PD 13 tonne Padfoot’s, CA5000PD 16 tonne Padfoot’s, CA6000PD 19 tonne Padfoot’s, CP1200W – Pneumatic Tyre Rollers and D.ONE – Trench rollers.
SOIL ROLLERS
Dynapac’s current soil roller range is the fifth generation of Dynapac CA single drum vibratory rollers.
With unique features such as crossmounted engines to provide optimal serviceability access and 180-degree rotating operator station, Dynapac’s single drum vibratory rollers provide comfort when working on the toughest compaction applications.
McCauley says this tender has reinforced the strong working relationship Dynapac CEA has had with Transport NSW, as well as Dynapac’s innovation in the roller market.
“From the operator’s perspective the rollers ticked every box, from the ergonomics to the comfort, the design and more. One of the standout features which Dynapac has is its crossed-mounted engine,” she says. “All filters, oils and fluids can be checked and changed from the ground level, making it convenient and easy for operators.
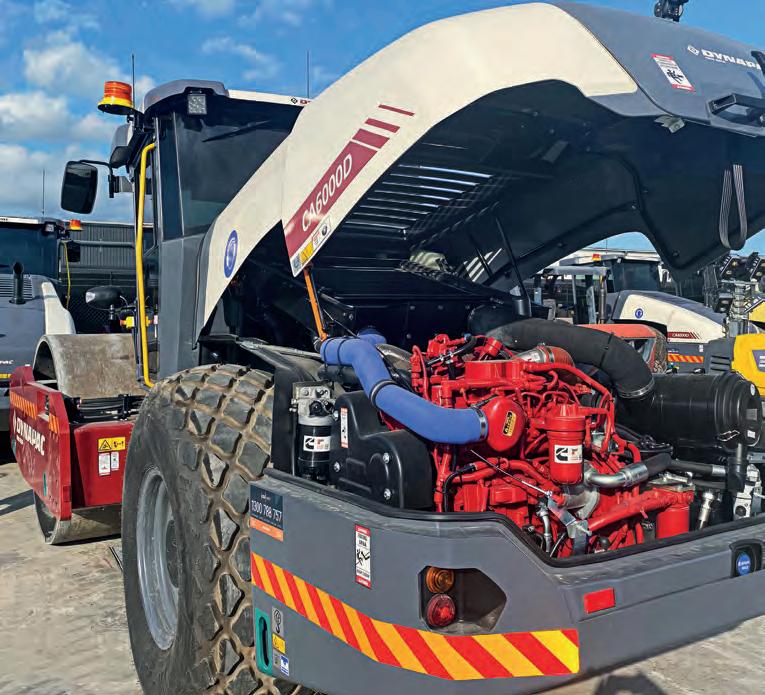
“That being operators’ and application efficiency, service efficiency and compaction control efficiency,” he says.
“Plus, the position of the combustion air intake has the advantage of keeping the inlet air as clean as possible, while giving optimal weight distribution.”
DOUBLE DRUM
Transport NSW selected two types of Double Drum Rollers, which Axiak says have been designed with efficiency in mind.
Across the range the machines are manufactured with unique designs to provide excellent visibility and increased serviceability.
Axiak says the Dynapac double drum rollers provide a range of machines from 1655 kilograms, up to 12,400 kilograms and with combination options available across the entire range.
“Double drums are used after the soil rollers, for the finishing process and preparation for spray seal, and
paving large sections of the road maintenance,” he says.
“The rollers are designed to meet the construction industry’s tough conditions with the operator in mind, resulting in a robust, comfortable and modern machine with the best compaction results.”
Axiak adds that the rollers will be spread around different sites as far north as Ballina, south to Bega and as far west as Broken Hill.
“Roads and Maritime Services (RMS) will be doing base course material compaction, which can be done with a multitude of different materials, whether that be rock fill or soil,” he says.
DATA DONE RIGHT
NATIONAL CIVIL ENGINEERING PROVIDER CIVILTECH SOLUTIONS HAS RELEASED ITS LATEST ROAD DATA TRACKING INNOVATION.
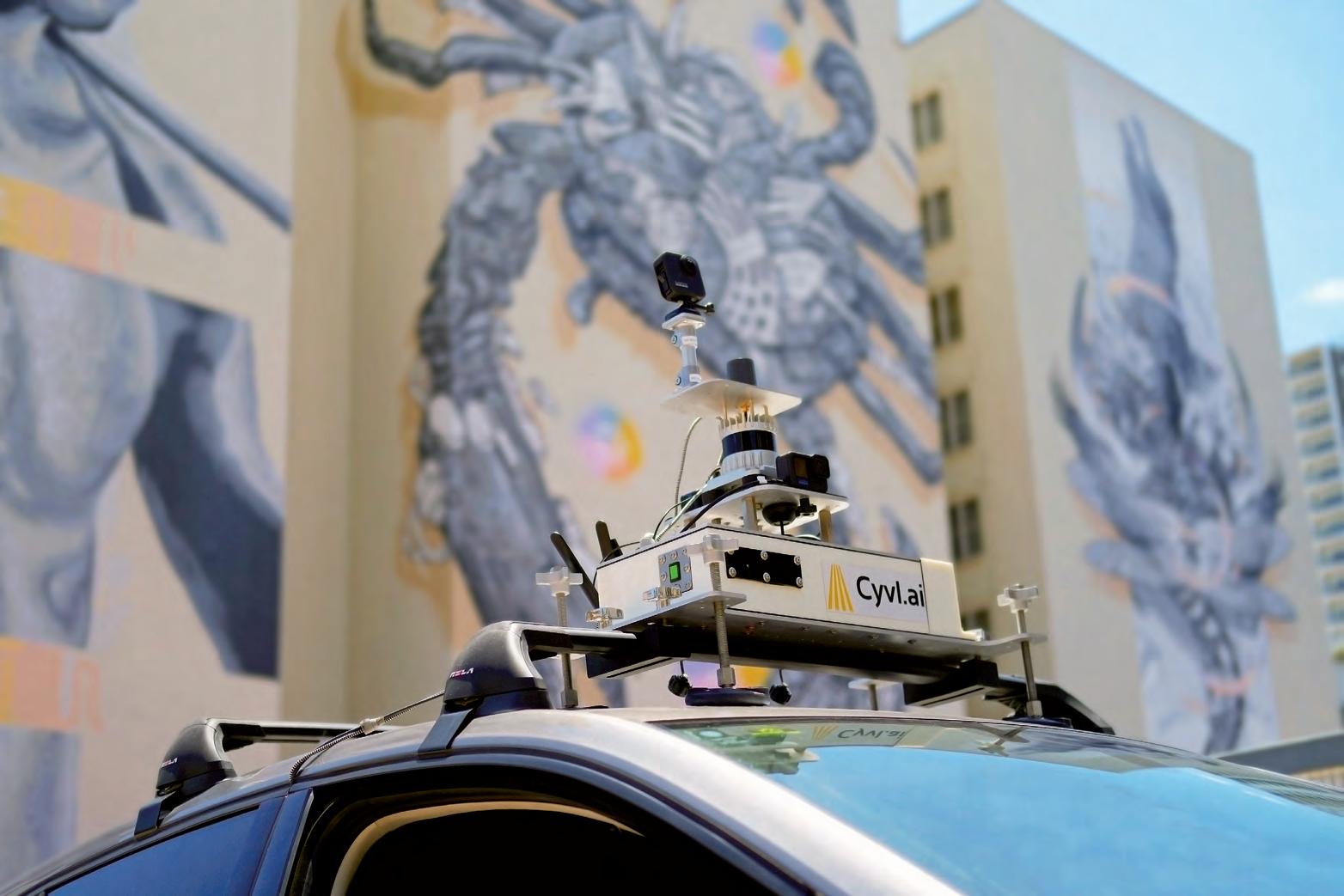
Civil engineering firm Civiltech Solutions delivers innovative and high-quality civil engineering and project delivery services across various industries.
Its mission, to provide project delivery solutions that cater to the unique needs of clients, is made possible through its newest road data sensors.
Leigh Carnall, Founder and Chief Executive Officer, Civiltech Solutions, says the sensors, operated with the help of Cyvl.ai, can improve the reuse of data to make better decisions about local roads.
“Local governments have a very big need for improving the way they look at their roads and understand their roads,” he says.
Carnall says councils can collect the data they need, when they need it, quickly, accurately and efficiently, to make better decisions to improve their road network.
To access this data, the council will attach the sensor, provided by Civiltech free of charge, to their vehicle. At their own pace, the council will drive around their road network to map out the municipality.
Once the data has been broken down, the council will meet with Civiltech to
discuss which aspects of the data they need from the collection, with the rest remaining on file with the possibility of later reuse.
The data will show a score of the road network, displaying cracks and inconsistencies in the roads.
Carnall says local governments do more than just look after roads. Councils also assess and maintain signs, pipes, potholes, guideposts and more.
With the road data gathered from Civiltech, councils will be able to plan future works, devise engineering plans and undergo major capital works such as resealing and asphalt patching.
“This level of infrastructure all has a value to it, and typically that level of information wouldn’t have been collected previously,” he says.
“Typical methods of collecting that information would be someone driving around in a car with a digital camera or even an iPad.”
The Civiltech sensor collects information on varying road data, including the condition of roads, signs and line marking.
Civiltech partners with United States company Cyvl.ai to ‘Australianise’ models of the road network and to develop more products specifically for Australia.
Carnall says there are two main uses for collecting this level of road data – daily maintenance and for asset evaluation.
“The data can be used for day-to-day maintenance on assessing where all the bins are, how many security cameras there are, how many trees are on the road, assessing if a sign needs to be replaced or if there’s any safety hazards,” says Carnall.
“This level of information can then go towards planning daily operations to upkeep the municipality.”
Carnall says the second reason falls on councils’ legal responsibility to undergo asset revaluation.
“There are checks and balances in place for councils who are obliged to spend money on infrastructure to continuously improve their assets,” he says.
“In order to get an evaluation, you need good information. If the value of the asset is being maintained and not going backwards, then that council will be seen to be doing the right thing,” he says.
Councils who access their road data through Civiltech sensors also have the option to reuse their data later.
Carnall says having the option to reuse data provides the council with flexibility on which information they want to access at which time.
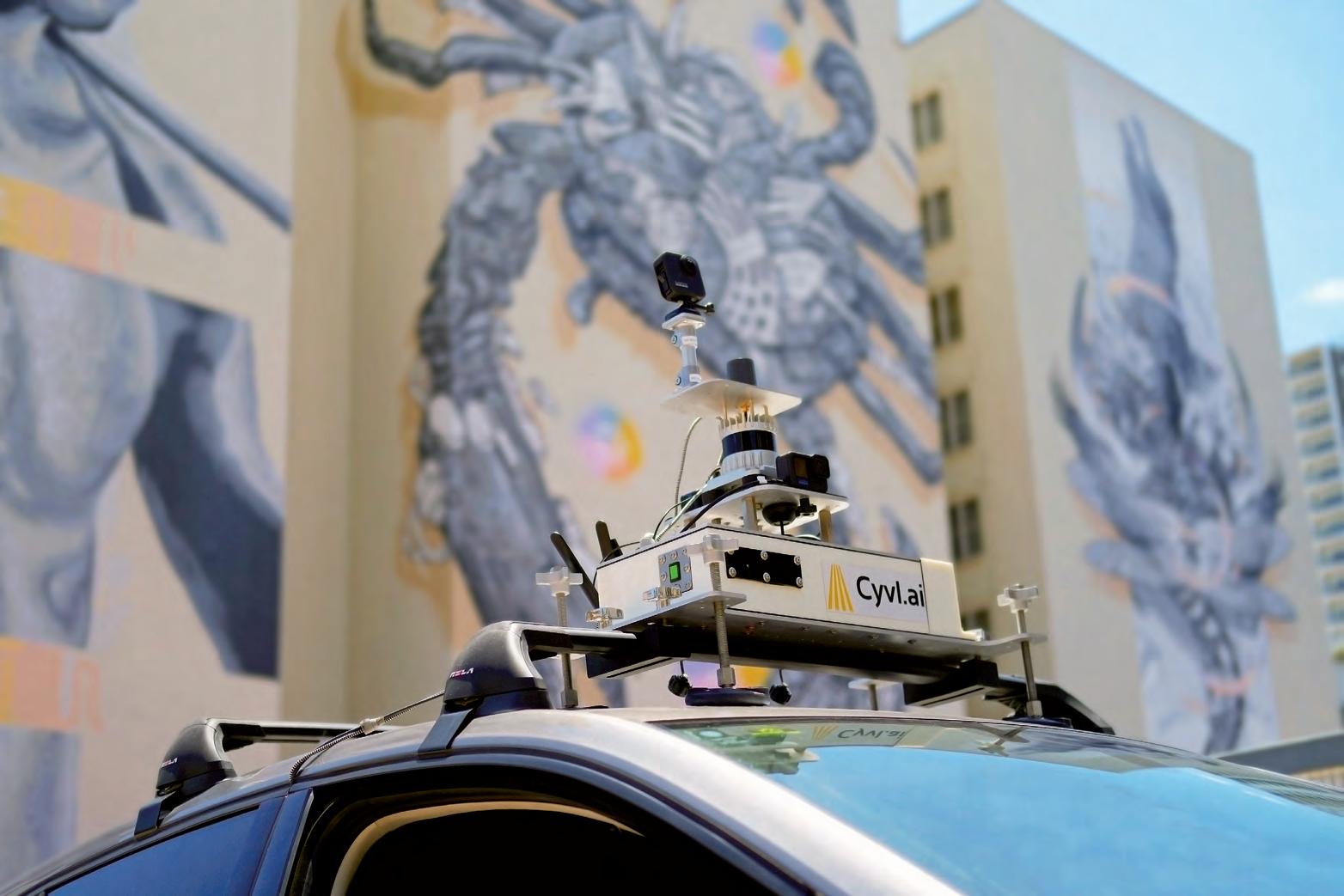
“COUNCILS HAVE THE ABILITY TO PICK DATA TO SUIT THEIR ASSET MANAGEMENT NEEDS. IF A COUNCIL LATER NEEDS A CERTAIN PIECE OF ASSET INFORMATION, WE CAN REPROCESS THE EXTENSIVE ROADWAY DATA OUR SENSOR COLLECTS WITHOUT DOING ANOTHER PICKUP”
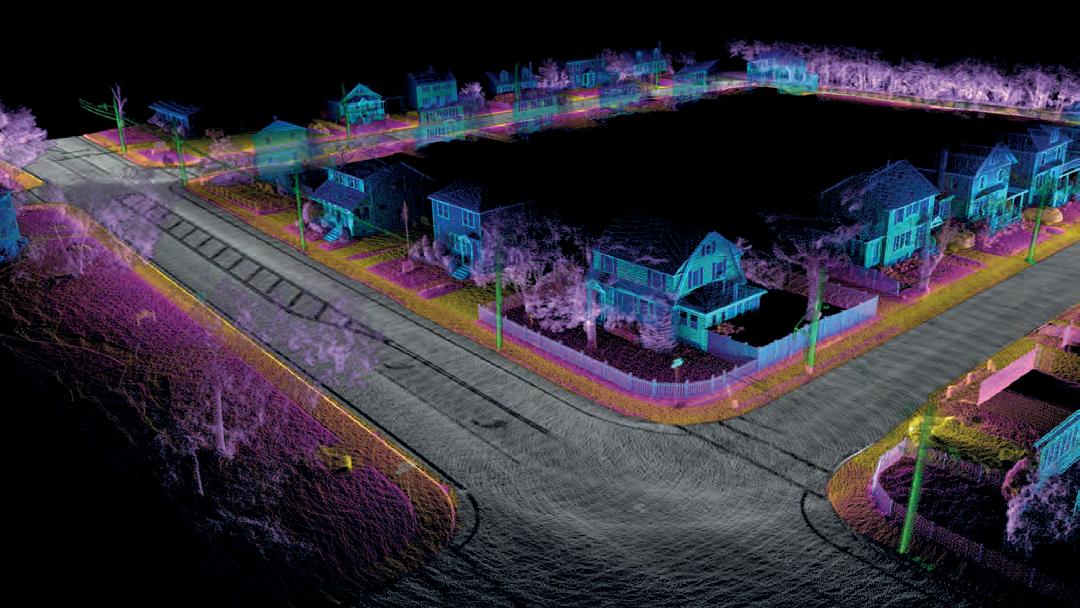
“If a council doesn’t want to access one piece of information at a certain time, but later needs that piece of information, we can reprocess the data and give it to them at a later stage,” he says.
“They might not want to know about the light poles now, but in six to 12 months they may want it to be reprocessed, without having to do much in the way of driving around the network again.”
CATERING FOR COUNCILS
The extent to which Civiltech can assist in reading the data varies from council to council. As Carnall says, there are some who understand asset management better than others.
“We cater for a wide range of councils, and there are some that have very little experience with asset management systems and want a very simple breakdown,” he says.
For these councils, Carnall says Civiltech works on a web GIS (Geographic Information System) platform where the council can assess the information they desire.
“We talk it over with them and we create something that is nice and easy to use, because most councils do not have GIS asset managers to use this information.
“It is very important to help where we can, because the majority of Australia’s
537 councils are small, regional and rural councils.”
QUALITY OF PCI
The Pavement Conditions Index (PCI) has been in operation for many decades, providing a snapshot of the pavement health of a road.
Civiltech’s road data is unique in the level of detail it can display on the PCI scale, right down to minor distresses.
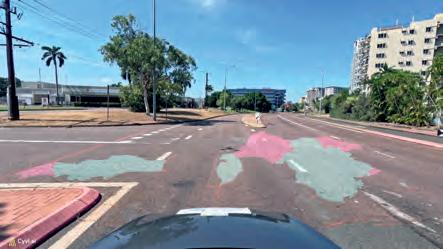
Carnall says the unique data is displayed on a highly detailed road map which shows different defects highlighted in varying colours.
“The council is able to zoom in and around their road network, click on a particular defect, view the image and zoom in, displaying the evidence which can then be used to send someone to go fix the defect,” he says.
“For example, an engineer could assess the image and decide reconstruction or resealing the payment is necessary.
“We have gone from solely providing an evaluation to providing answers on how to remedy these areas.”
GUIDING INFRASTRUCTURE DEVELOPMENT
Carnall believes up to date street level imagery is crucial in guiding infrastructure development for local councils, understanding the value in both planning and operations.
“Having street level imagery that is up
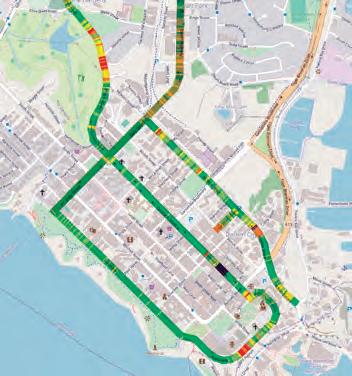
to date and collected within one year of the works is important,” he says.
“Councils can collect certain pieces of information in alternating years, and then use the updated information for their works.
“Civiltech is flexible in allowing councils to collect this information one year, so it can be re-evaluated at a later time.”
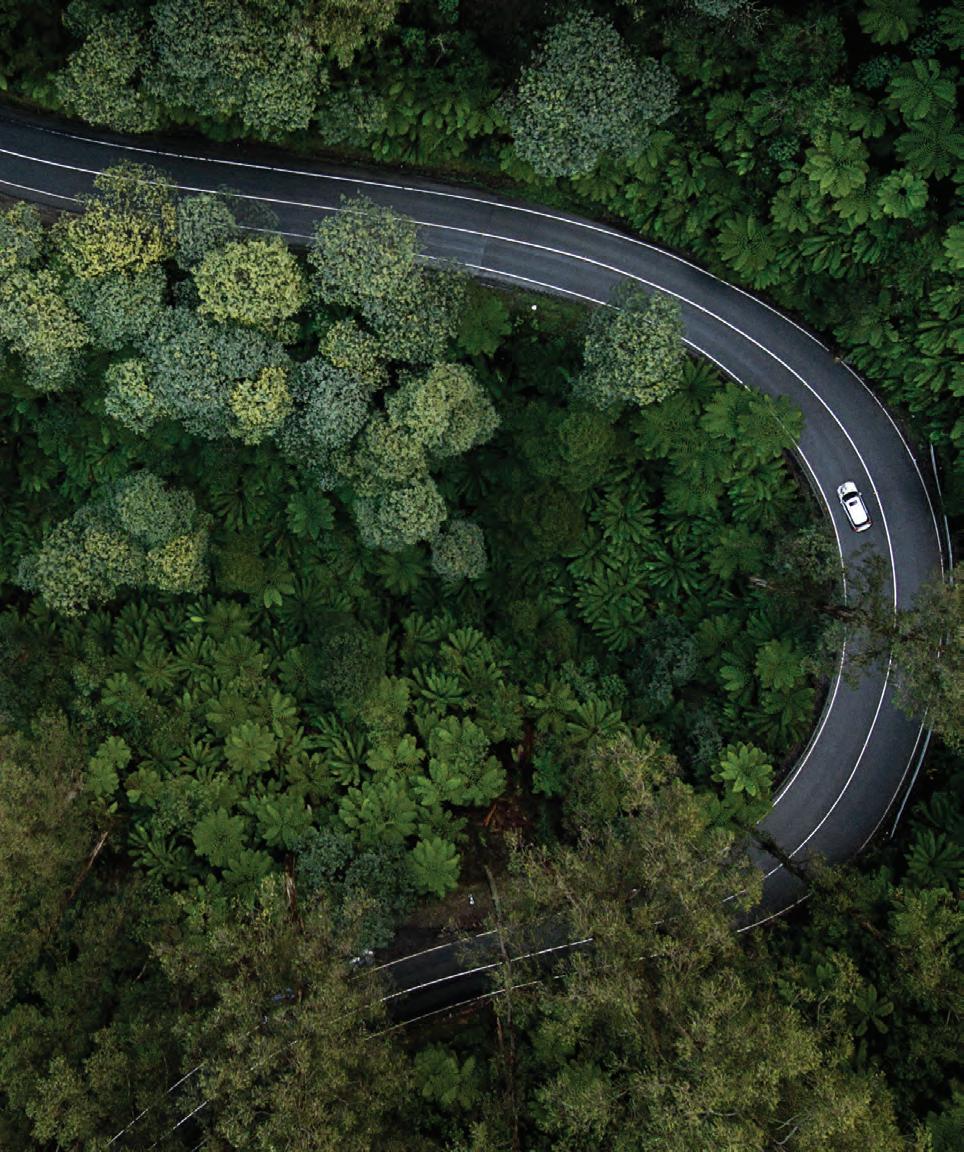
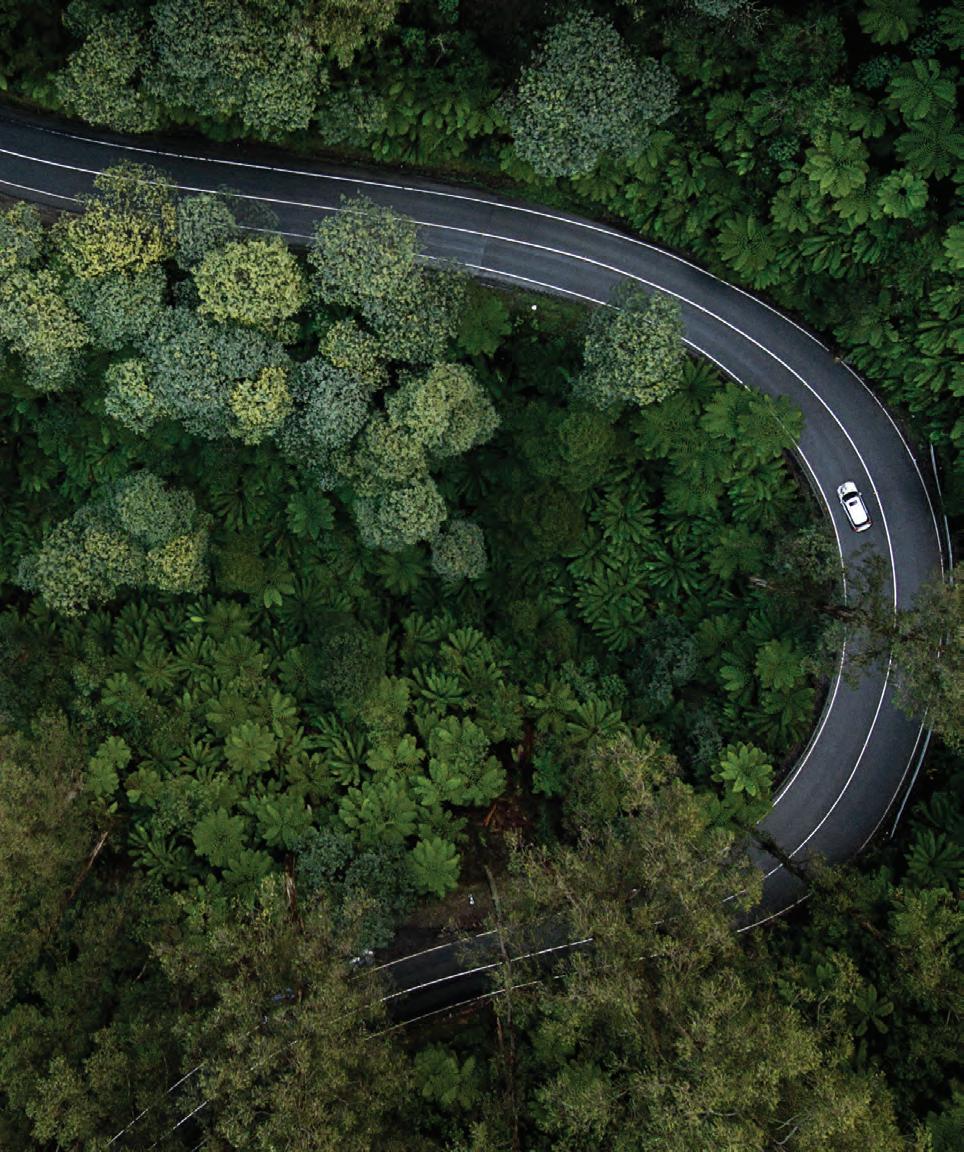
OPTIMISING INFRASTRUCTURE DESIGN
AUTOMATION AND POSITIONING TECHNOLOGY PROVIDER APTELLA HAS ACQUIRED SYNERGY PAVESMART, A PAVING SERVICES BUSINESS. ROADS & INFRASTRUCTURE
SPEAKS TO SENIOR LEADERS, AS WELL AS MEMBERS OF THE NEW PAVING SERVICES DIVISION, TO LEARN HOW THE ACQUISITION WILL BENEFIT THE SECTOR.
With more than 15 years’ experience on major projects that include airport runways and infrastructure, motorways, bridges, and sports tracks, Jason Carroll comes close to seeing it all.
As the Business Development Manager for Aptella’s new Paving Services division, Carroll says the company’s adaptation has been the result of a shift in demand for services, based on the accuracy he and his team can deliver.
“Two years ago, I would say our work was 80 per cent road infrastructure and 20 per cent airports, but nowadays it’s a more even split between the two,” he says.
Simon Chamberlain, General Manager, says the team’s specialist skills and ability to work collaboratively with clients to provide optimised paving outcomes through a proven methodology has been the foundation for success.
“I think that shift is due to our proven track record with our customers of achieving the higher accuracy that airports require, where you’re looking at vertical tolerances of plus/ minus five to seven millimetres – compared with roads where it’s ten,” he says.
As a provider of automation and positioning technologies, Aptella has made a name for
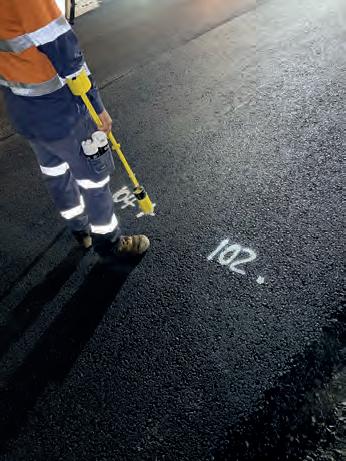
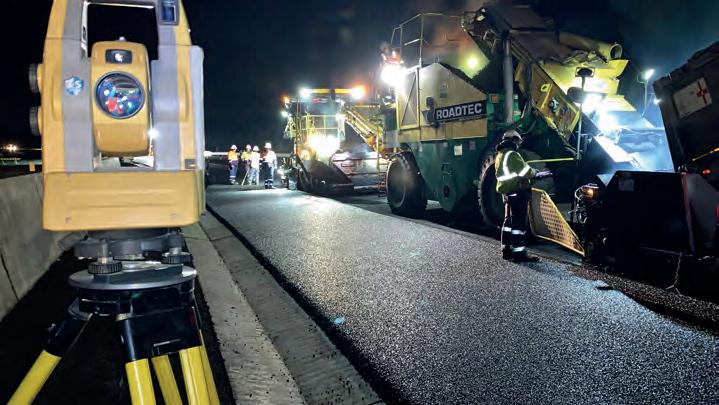
itself for its ability to implement worldleading technology, supported by its team of experienced professionals.
“We have a tried-and-tested workflow and process that is rigorously accurate, and NATA (National Association of Testing Authorities) accredited, so our clients can trust in its validity,” Carroll says.
THE ‘SOURCE OF TRUTH’
On any project, whether resurfacing or a new build, the Aptella team always begins with a survey of the existing surface. This is used to compare against any previous surveys for the job, as well as allow for pre-works volume calculations, cut and fill and so forth.
For road projects, the team performs a pretest using a high accuracy laser profileograph fitted to the body of a car. This scans the existing surface to calculate a bump count, or International Roughness Index (IRI) count.
In some cases, the original survey could have been done years before the project is ready to start, so there is potential for significant variations to the original design. In other scenarios, the team has picked up on errors in the original survey due to the use of different methods.
“It’s important that the figures and calculations are meticulously checked because our clients have signed a contract that dictates the amount of asphalt for the job,” Carroll says.
“Our pre-work survey gives peace of mind that the agreed amount is correct to avoid potentially huge cost blowouts. If there is a discrepancy it can get resolved before any asphalt is laid.”
The pre-works data also serves as a point of reference for all parties that can be referred to if anything does go wrong during construction.
“This stage of the project is also an opportunity to identify and survey any failures in the runway or road for the client to review,” Carroll says.
“The issue can be raised with the project owner so that they are aware and can make any adjustments to design if they choose to. If the surface fails in 10 years’ time, for example, everyone has a record to prove that it was a pre-existing fault and not due to their work.”
In some cases, the Aptella team is engaged part-way through a project, but the process remains the same in terms of beginning with a new survey. As Chamberlain explains.
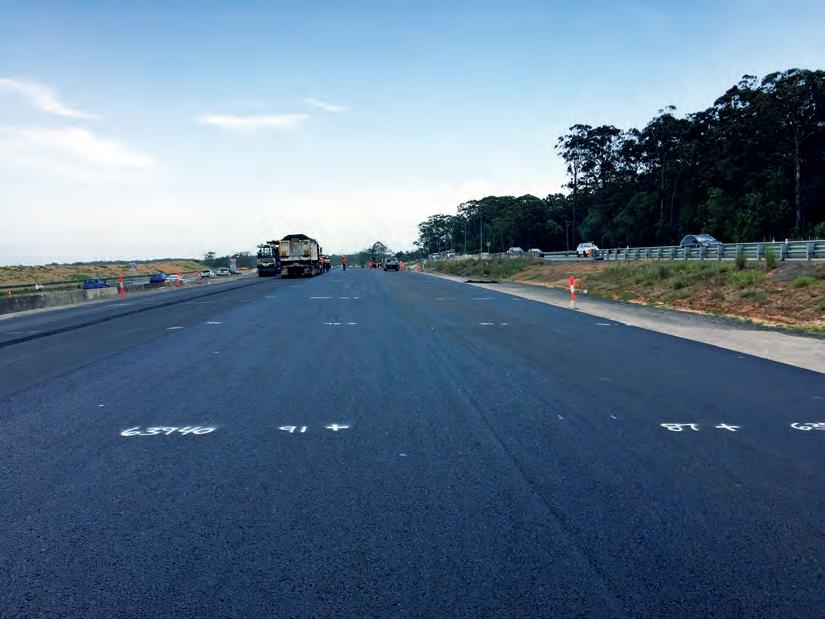
“Although we’re agile and adaptable to accommodate all the challenges paving jobs inevitably throw up, one thing that’s a non-negotiable is our independent survey methods,” he says.
Chamberlain adds that the Aptella team can come onto a job that is only 40 or 50 per cent conformance to design and turn it around to achieve 98 per cent conformance.
“We will never accept survey data that is not done by our team,” he says.
After pre-works surveys, Aptella can be asked to perform other survey work to compare as-built data to design, as well as calculate milling to depth numbers if they are taking up the existing surface.
Alternatively, the team calculates overall fill numbers for paving straight over the top of the existing surface.
Other services that might be required include setting out service locations, core hole testing, pickup location of underground electrical or other services, and line marking pickup. AGL lighting is another important asset to accurately set out.
If milling is to be done on the job, the next stage for the Aptella team is to mark out the milling design and verify its accuracy through as-built surveys.
PAVING SERVICES
Next, the asphalt paving begins, with multiple layers depending on the project design.
“The more layers that are laid, the better the result at the top, because you have time to identify and compensate for any errors,” Chamberlain says.
After each layer is paved, the survey crews perform conformance surveys. For airport jobs, there’s usually a need for daily CAD (computer aided design) outputs and volume reporting to demonstrate what’s been laid. At the end of the job, Aptella provides an asbuilt package with everything that has been done on the project.
Carroll says often there isn’t the luxury of completing paving in a linear process. This may
be because the runway or road needs to stay open during the life of the project.
The asphalt is ramped at the end of each shift to allow for a smooth surface and to correct any height discrepancies between the new and existing surface. The ramp is then milled out and paved over the next day.
“There are so many variables in paving that you have to accommodate and adjust for,” he says.
It’s this ability to deliver flexibility and adaptability for each project that’s enabled Aptella to win works across both the public and private sectors.
“With roads we’re often working in confined spaces and to extremely tight time frames, so it can be a high-pressure environment,” Chamberlain says. “We’ve got an optimised workflow that’s tried-and-tested.
“As soon as traffic control is in place, our crew is quick to fix our PaveSmart system to the paving machine(s) and begin the first survey resection, which is usually in 200-metre increments.”
The numbers marked out during the survey are then input into Aptella’s PaveSmart system, a unique variable depth paving control solution that eliminates the need for string lines and ensures smooth, accurate material placement.
For each layer the team inputs variable measures of asphalt allowing for compaction, mix of material, temperature and so forth.
Behind the machine, the team also dips the material to check that the levels laid are accurate.
“In theory, the numbers the surveyor puts down, the ones entered into the PaveSmart system, and the ones measured when dipped, all match up,” Chamberlain says. “If they don’t our expert operators can make small adjustments to further dial in the results.
“No matter how well calibrated the machine, there are always factors that affect the numbers, including machine speed, temperature of the mix, whether the screed is in or out, and so on. There needs to be human
intervention to interpret and adjust to the unique circumstances on any given shift.”
Now, with the integration to Aptella’s broader technology portfolio, Chamberlain says there is further opportunity to optimise different aspects of the paving process.
“Topcon’s milling machine control, for example, can assist with accurate variable depth milling to reduce rework,” he says.
“Plus, there’s the ability to use thermal mapping technology in conjunction with PaveSmart to check if the mix is running hot or cold, and intelligent compaction for the rollers to increase the accuracy of compaction patterns.”
THE TEAM APPROACH
Carroll says that the Aptella team regularly finds the original paving design is not physically possible, or extremely difficult to achieve, particularly over multiple runs with a machine.
In this case, Aptella’s team can advise of design optimisation to achieve similar outcomes but with a design that is built around the paving runs, so that it’s achievable.
“A paving screed can bend a little bit, but not a lot, and we often come across super elevation areas where they cut across two or three lanes, changing from a two-way crossfall to a one-way crossfall,” Carroll says.
The Aptella team also works closely with the client’s paving crew for every shift to ensure that other critical factors such as the rolling pattern are all optimised.
Detailed daily reports keep clients informed, helping to identify tolerance levels and optimise any design changes.
“I think that’s what our clients appreciate most about our working relationship,”
Chamberlain says.
“It’s definitely not an ‘us and them’ approach, but an ‘us with them’ one. That applies to the shift workers on site and the project management alike. We are always working together to optimise the design and get the best conformance possible as a team.”
Carroll agrees, saying his team is often involved in consulting work to analyse the data and design and make recommendations.
“Our experience from so many projects, and having worked with so many clients, means we’re in a unique position to help not only collect the data and complete the job, but also interpret the data and make recommendations to achieve results more efficiently and cost-effectively,” he says.
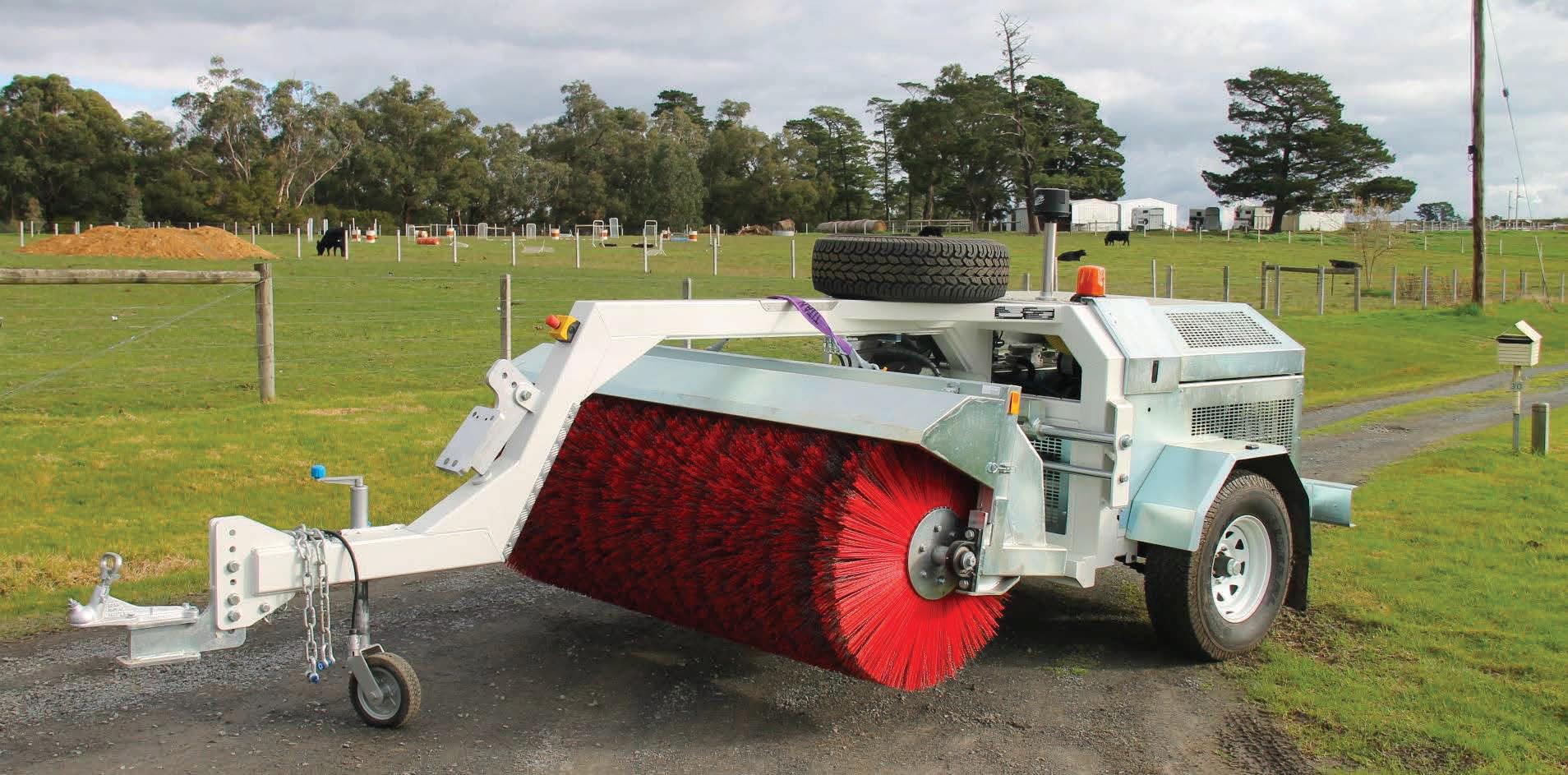
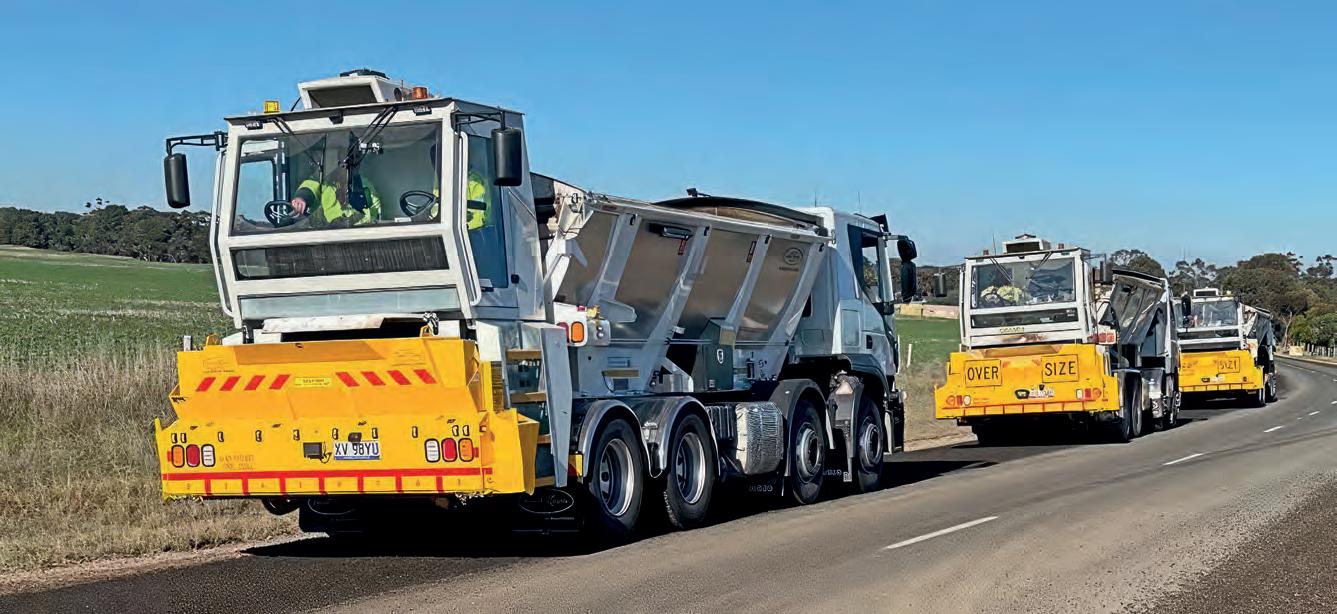
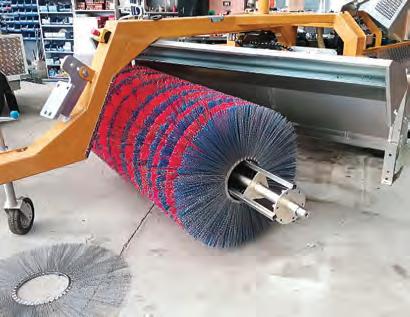
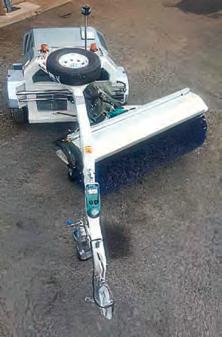
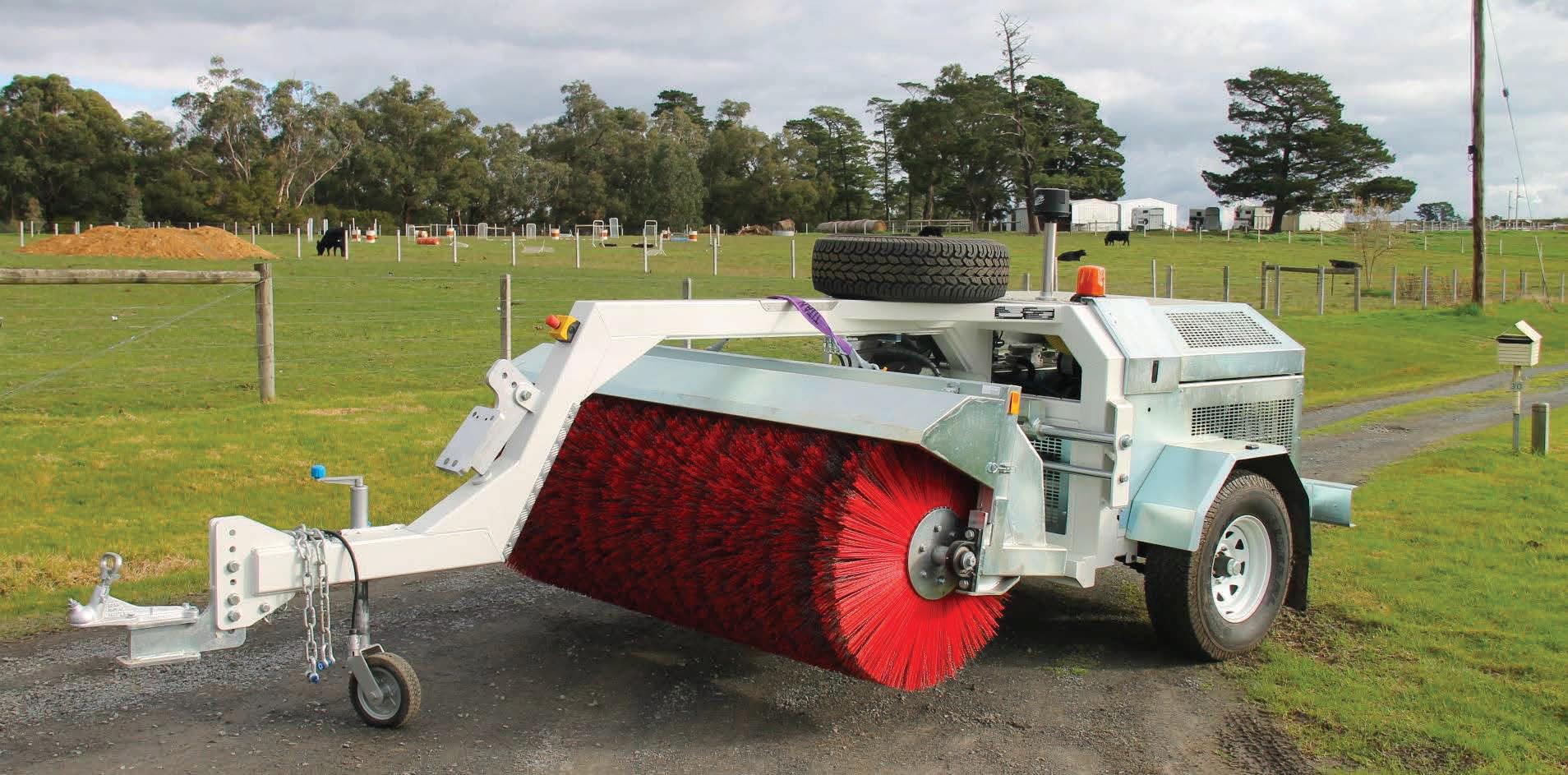
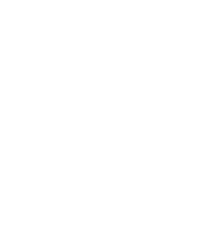
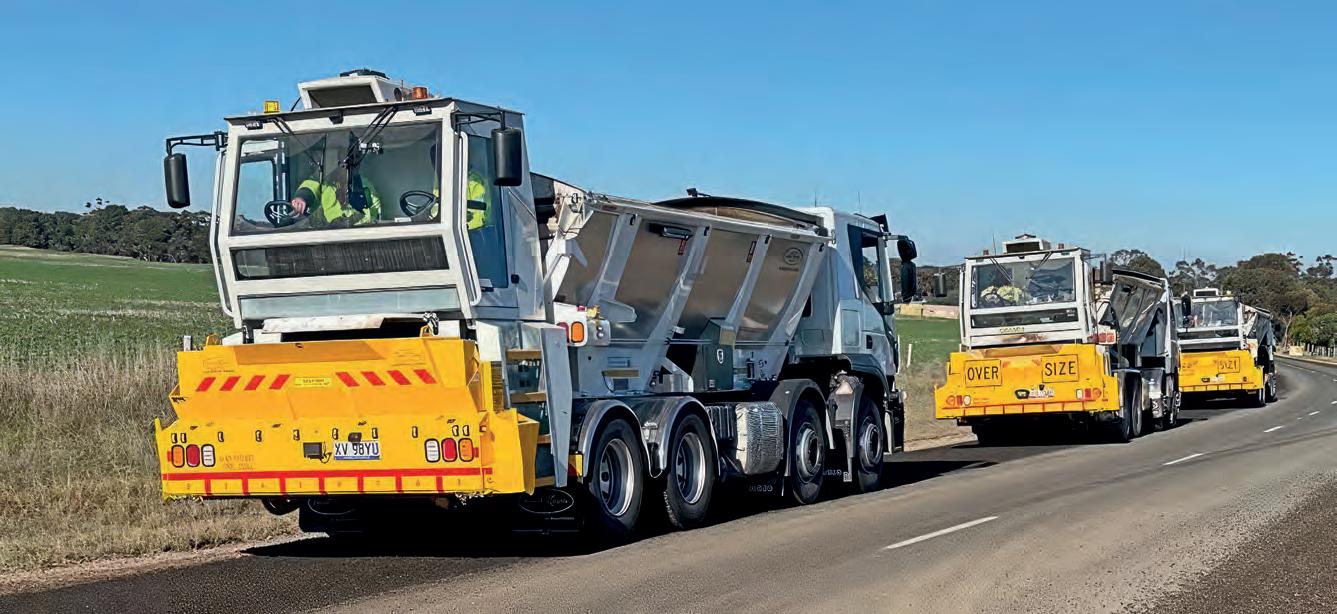
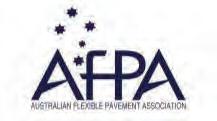





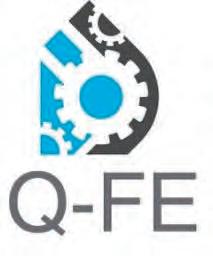

THE WAY LIGHTING
ORCA SOLAR LIGHTING IS DISTINGUISHING ITSELF AS A PREMIUM PROVIDER OF SOLAR LIGHTING SOLUTIONS FOR THE ROAD AND RAIL SECTORS.
JAMIE JANIDES, ORCA SOLAR GENERAL MANAGER, TAKES ROADS & INFRASTRUCTURE MAGAZINE THROUGH THE COMPANY’S EXTENSIVE PORTFOLIO.
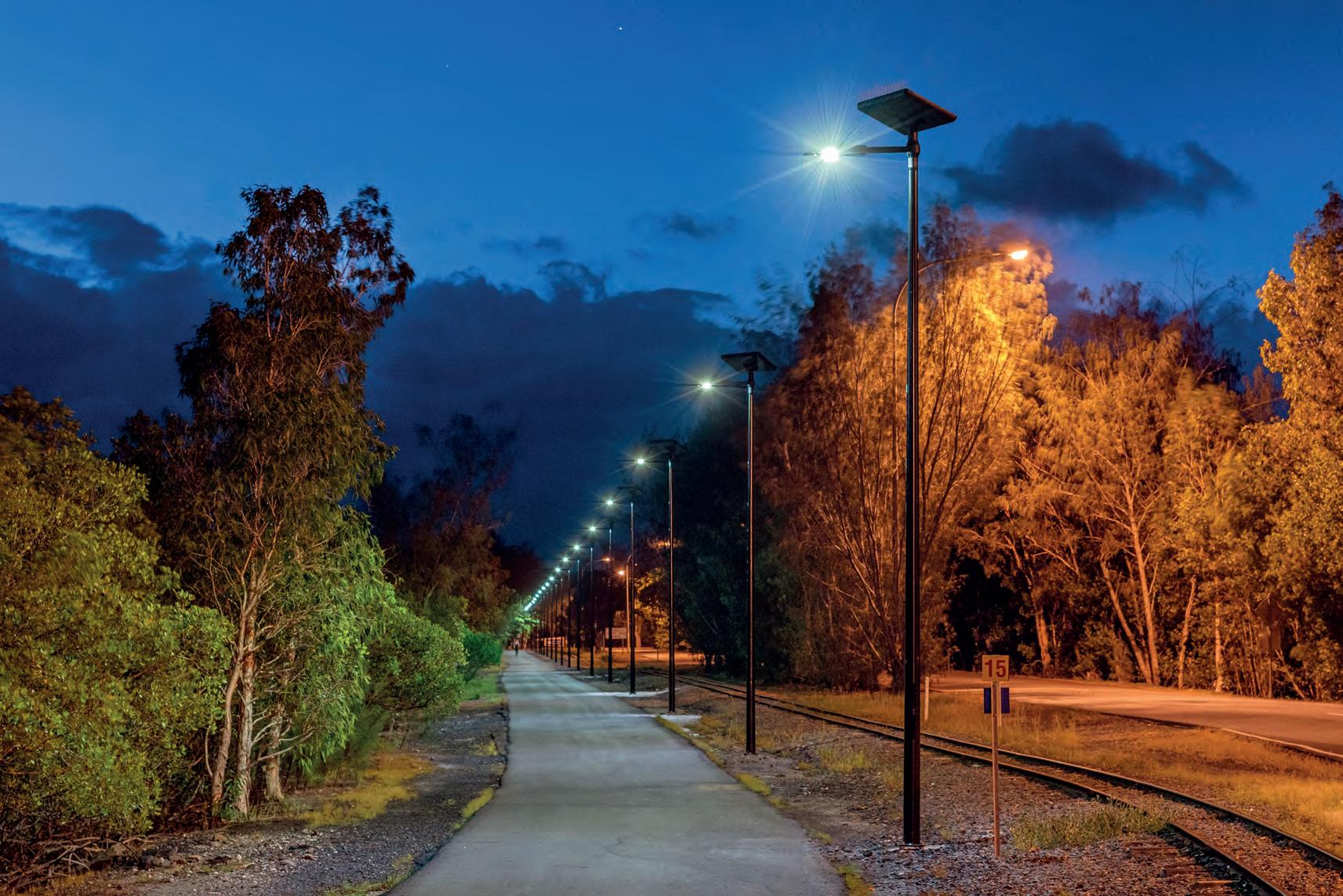
Australian Defence Force, Rio Tinto, BHP and Fulton Hogan all share one thing in common. On top of being some of the most recognised and influential organisations in Australia and the world, all have benefitted from one of the fastest growing names in solar lighting.
Orca Solar Lighting opened its doors in 2007, with solar lighting being its sole focus from day one.
Jamie Janides, General Manager – Orca Solar, says this singular focus has enabled the company to establish long-term relationships with its clients, while improving and expanding its product range over time.
“We’re really proactive as a company and we can guarantee that our product works,” he says.
“We give autonomy where other products don’t. What that means to us is having a solar product that can work when there’s been four or five days without any sun, our products still operate fine.”
Orca Solar Lighting can deliver services for developments both large and small. Among its standout projects was its work on the Department of Defence’s Robertson Barracks in the Northern Territory – the largest solar lighting project
in Australia’s history.
“Our larger products are assembled and manufactured in Australia and the batteries are made in New South Wales. We proudly manufacture a number of our major components in Australia,” Janides says.
One aspect that’s been a consistent and is largely responsible for the growth of Orca Solar Lighting’s service, has been its reliability.
Manufacturing its solar lighting systems locally is just one part of maintaining a reliable product and product pipeline, another is designing outstanding lighting outcomes.
While it may sound simple and obvious, small design tweaks here and there over the years have led to a suite of highly adaptable lighting solutions. As Janides explains.
“We’ve got a lot of support from suppliers, we’re compliant, we deliver on time and we’re reliable, that’s why people in the roads and infrastructure space use our products,” he says.
“Our solar panels aren’t just added to the top of the light. It’s independent of the luminaire, so we can tilt it towards the sun.”
Each project is treated individually, as such Orca Solar Lighting uses weather and
solar radiation data, creating simulations that the company uses to make sure its lighting solutions can work, even when the sun isn’t shining.
One of the biggest benefits of Orca Solar’s systems is increasing security and reducing crime in isolated areas. It’s for this reason that Orca Solar Lighting has
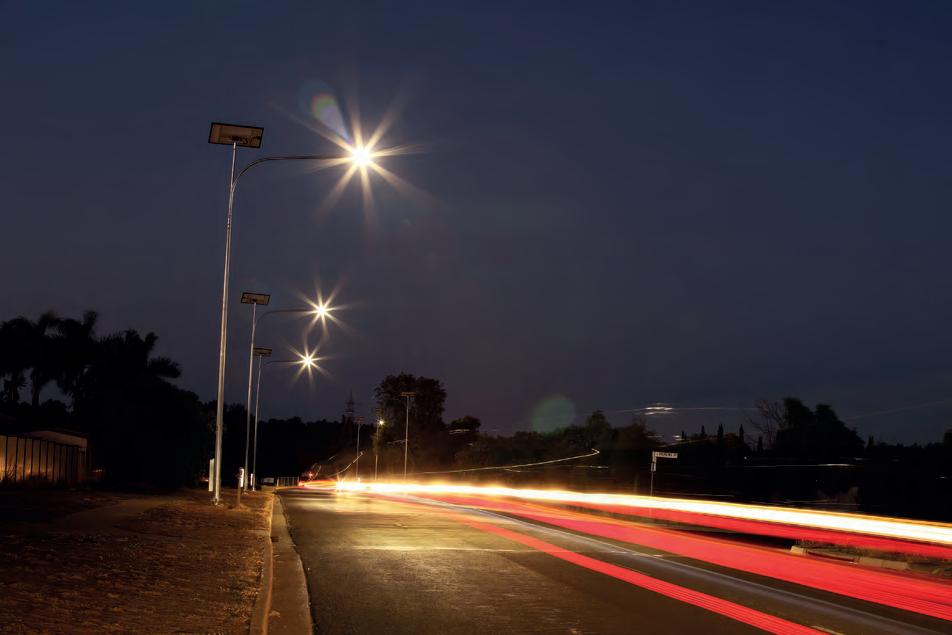
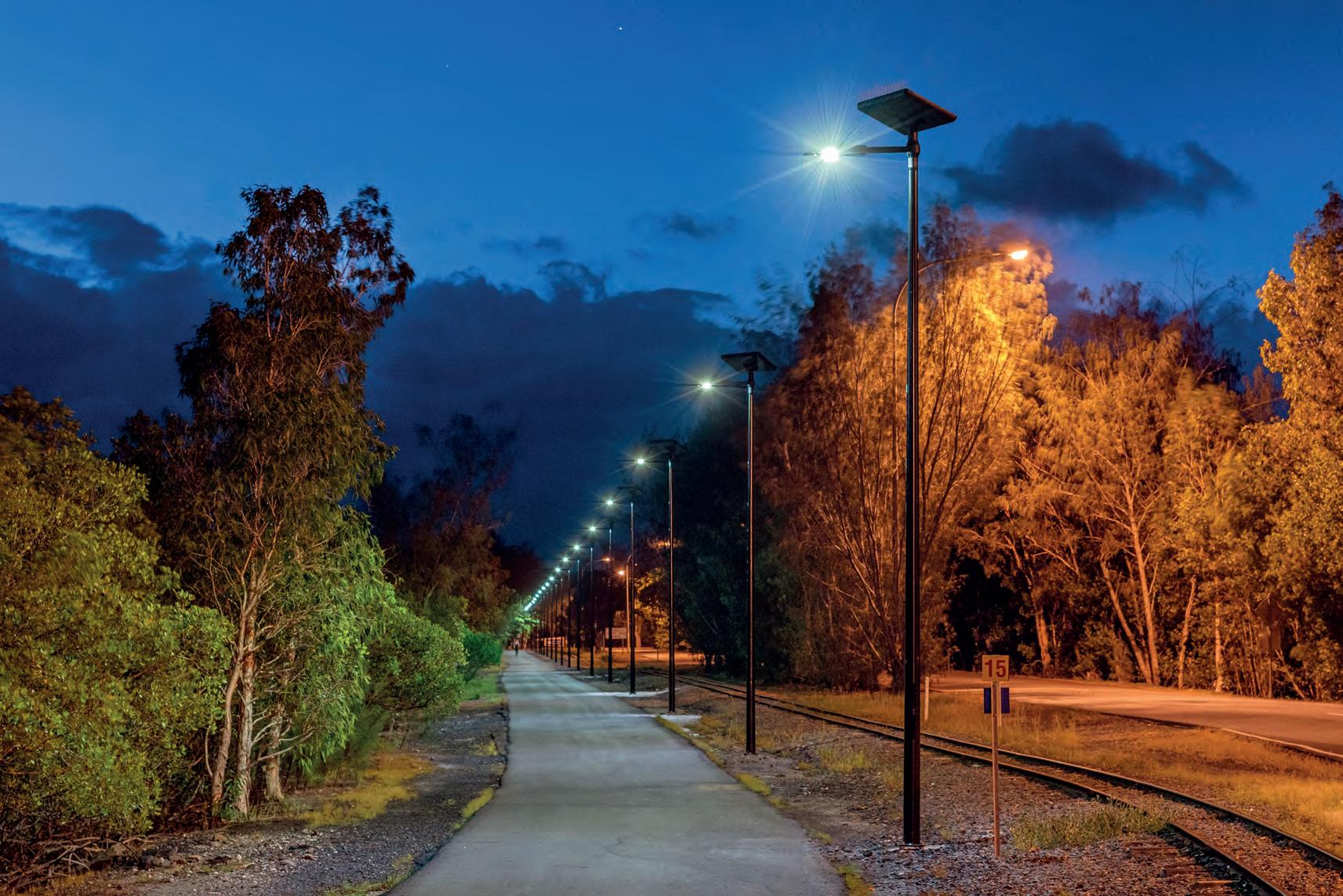
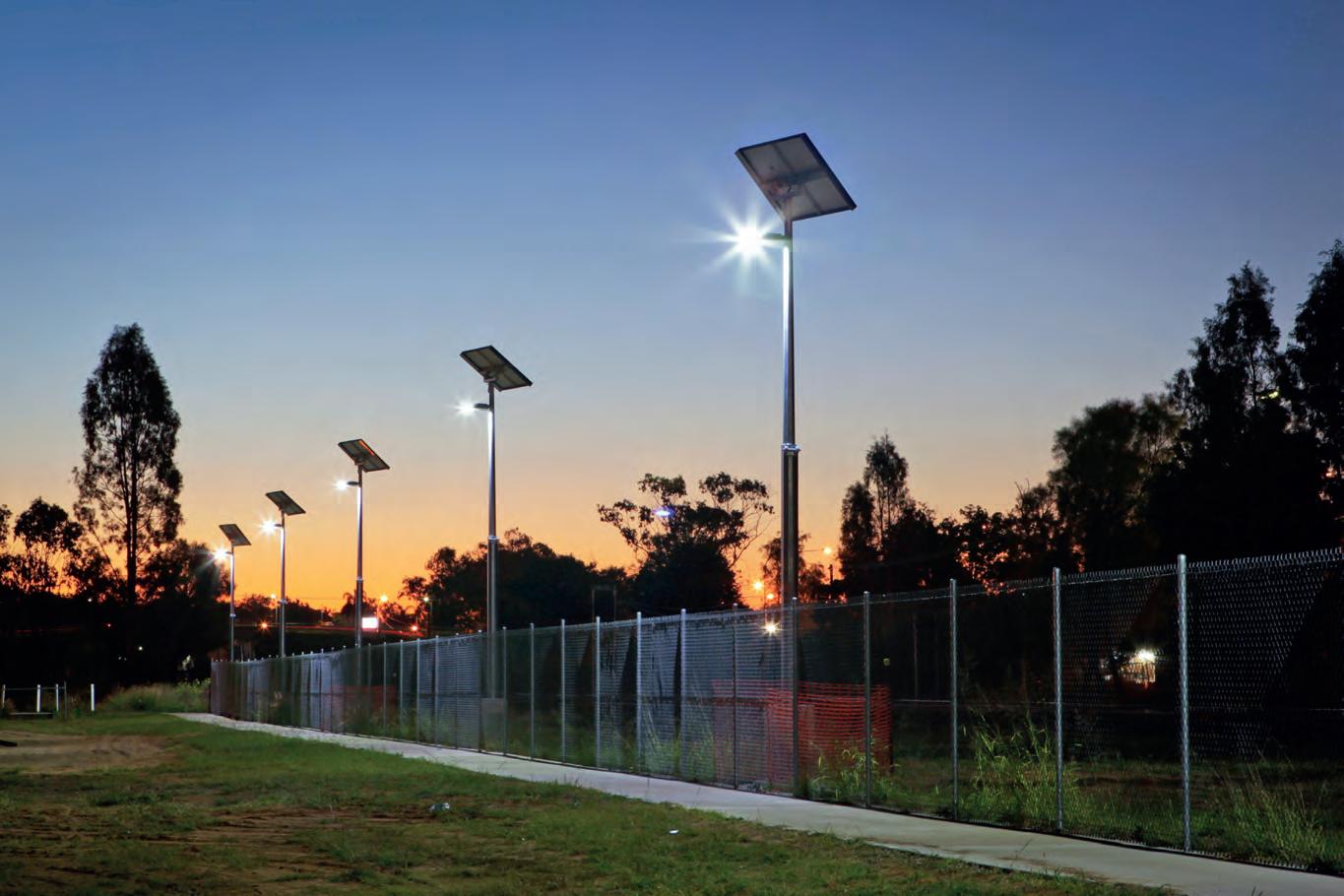
been selected to provide systems for use in areas such as train stations and other poorly lit public spaces.
Poor lighting in remote car parks, construction sites, parks and recreational areas can compromise security, increasing the risk of accidents and criminal activity.
of the Journal of Quantitative Criminology tested the impact of improved outdoor lighting in 40 different locations.
Results of the study showed that communities that were assigned more lighting experienced sizeable reductions in nighttime outdoor index crimes.
are engineered for the project at hand.”
Janides says Orca Solar Lighting also provides several battery options depending on the requirements and challenges presented by the project at hand.
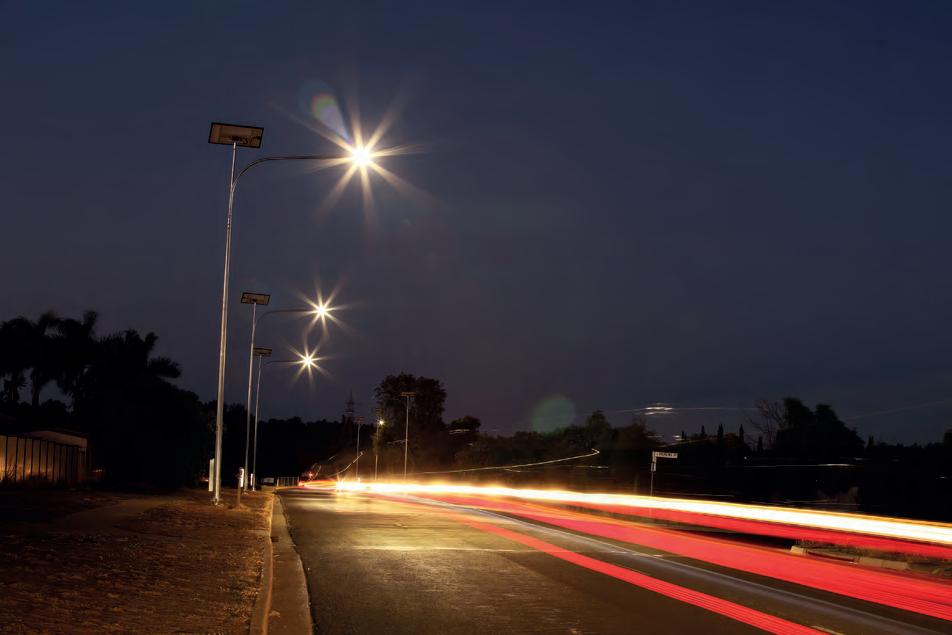
Janides says a 2021 study published as part
There was also a large decline in arrests, indicating that deterrence is the most likely mechanism through which the intervention reduced crime.
Every single site is assessed and designed to make sure that such lighting can be strategically placed, to maximise exposure and safety.
It’s differentiators like this that have made Orca Solar Lighting a supplier for VicRoads, Transport and Main Roads (Queensland) and Main Roads (Western Australia) for both road and railrelated projects.
“We design every project differently,” Janides says.
“Our solution in Queensland will be a different solution to a product that’s being installed in Victoria, because the sun’s on a different plane.
“Some of our clients inspect every single light pole that we manufacture, they need to sign them off one by one. Our poles
“One battery doesn’t fit all,” he says. “For a site that doesn’t get much sun, like in Victoria, we base our product on having a four or five-day autonomy. We use Google Earth and sophisticated weather data, so at any time in Australia we know exactly where the sun is going to be.”
Having access to such information also allows the Orca Solar Lighting team to be well aware of potential challenges before arriving on site, increasing the efficiency of installation and reducing delays for the customer.
“Sometimes it can be difficult to get 240volt power to certain locations, whether it’s cost related, a geographical challenge, or the project might be in a public space. Maybe there’s a main power grid under the road,” Janides says.
“Whatever it may be, we can find a way to supply the right solution. And a solution that works and will have at least 10 years battery life before it needs to be replaced.”
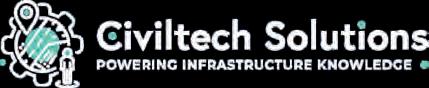
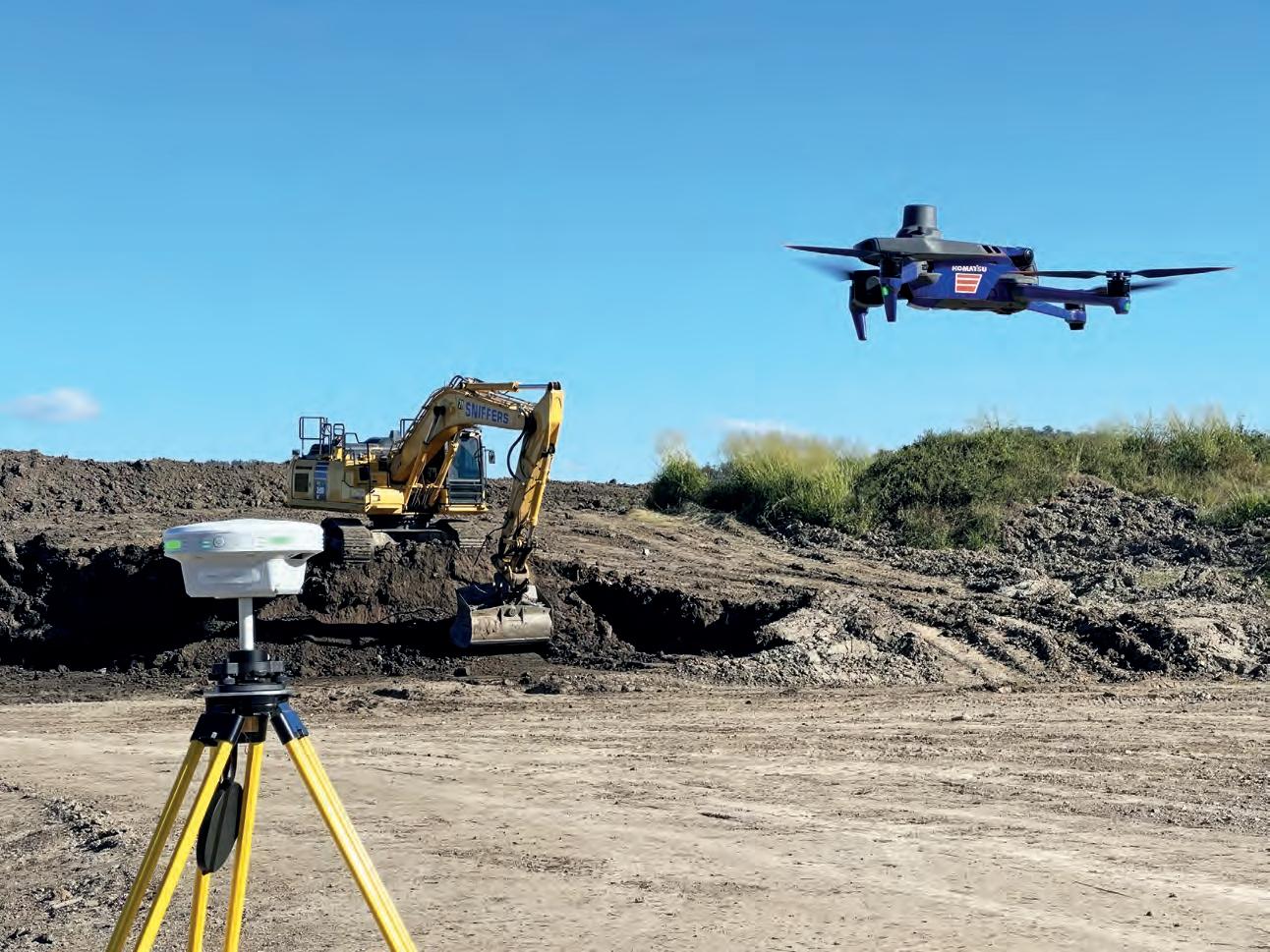
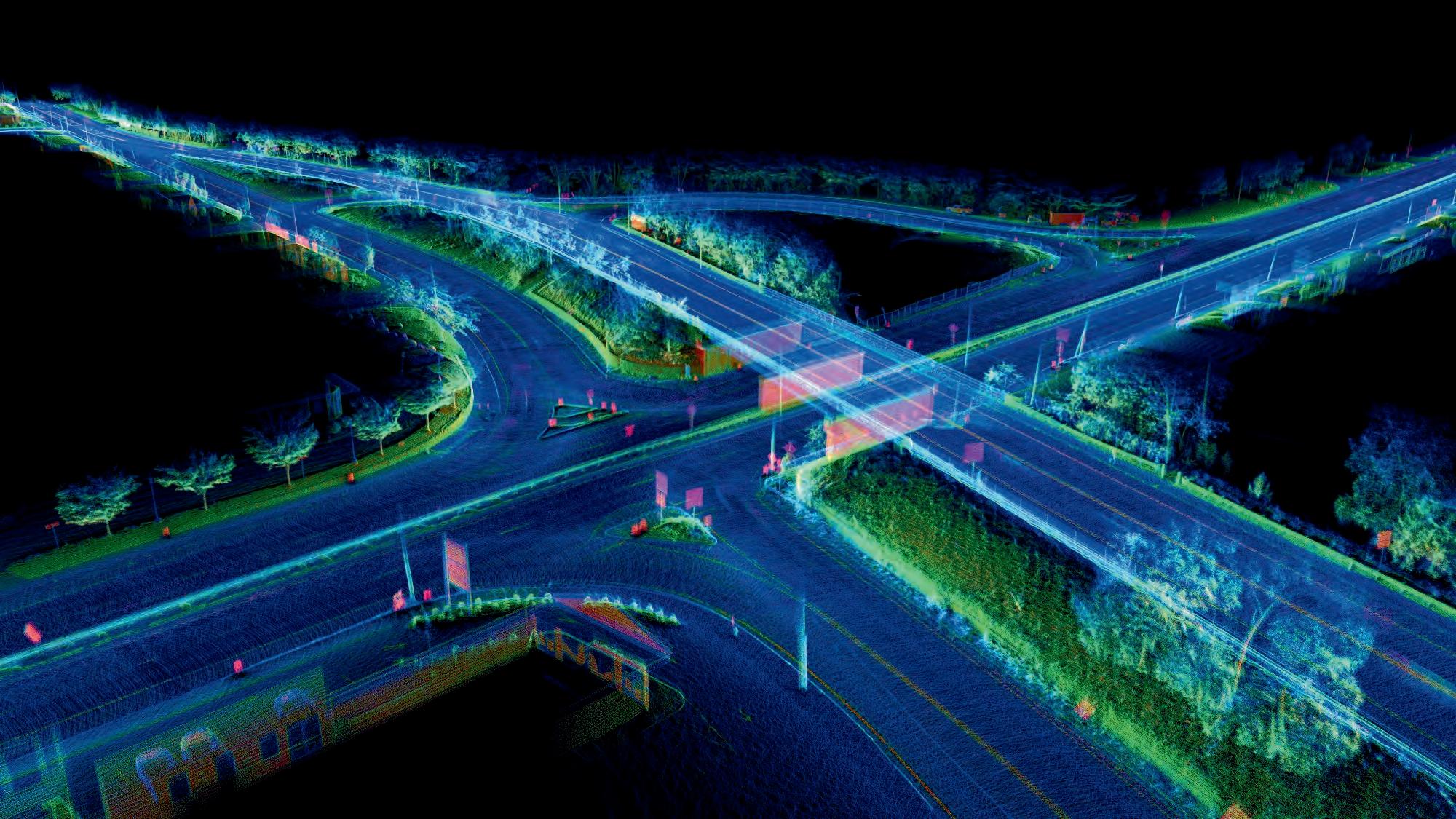
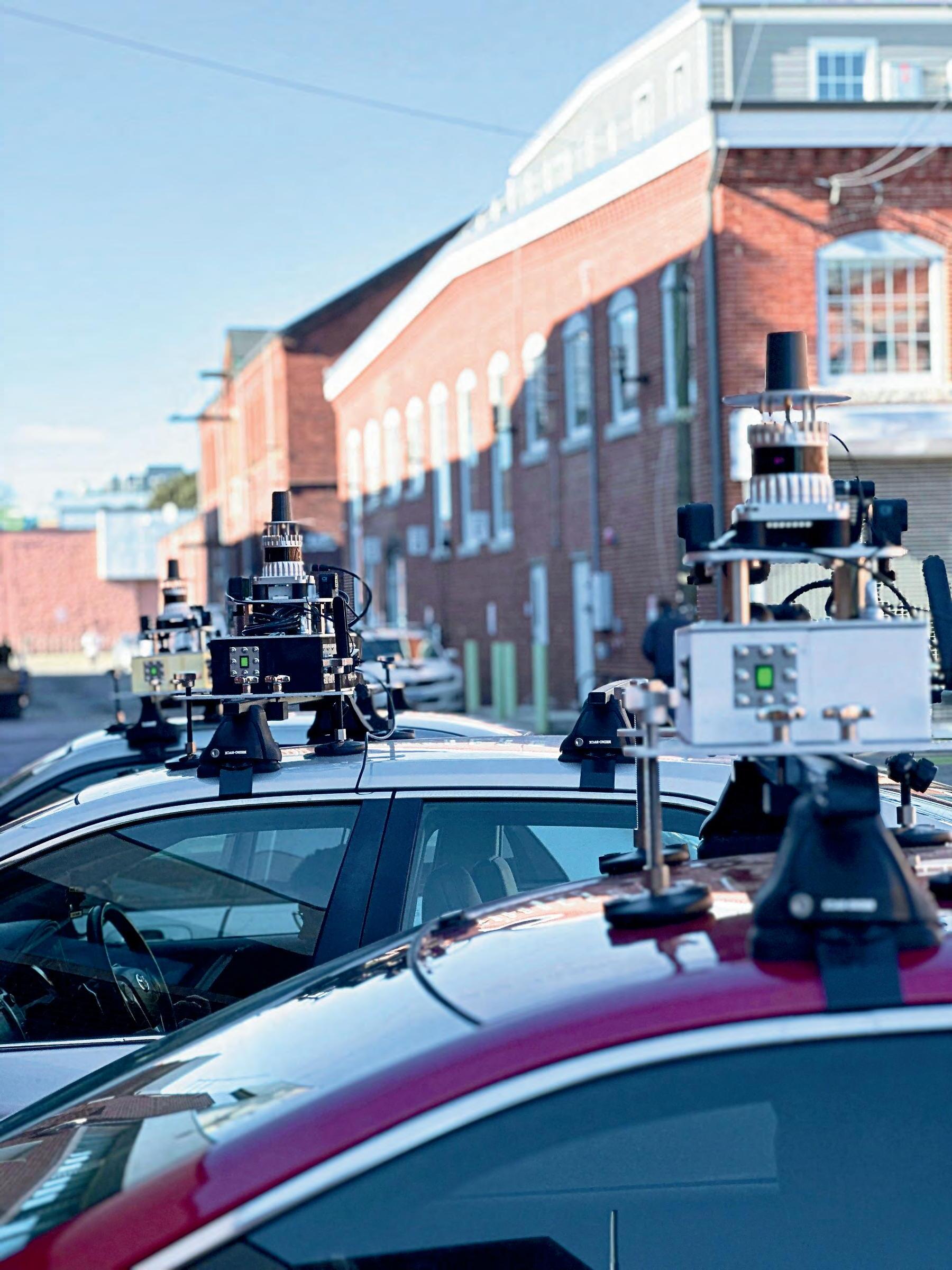
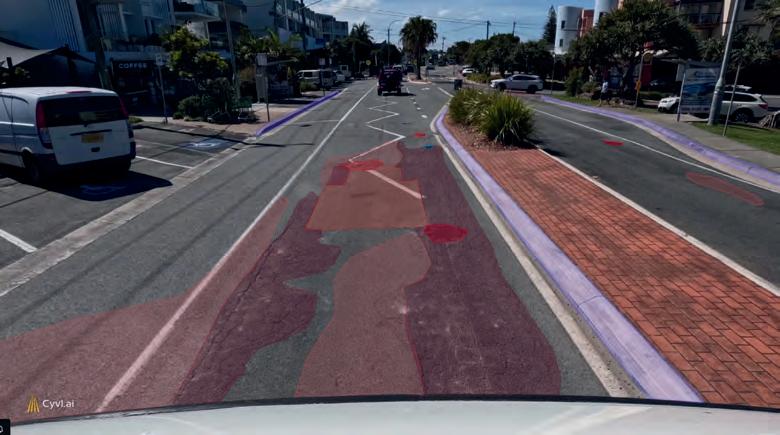
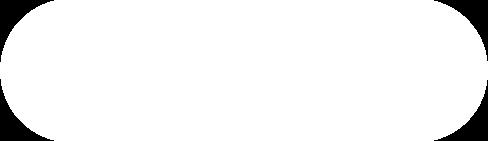
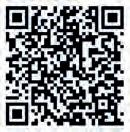
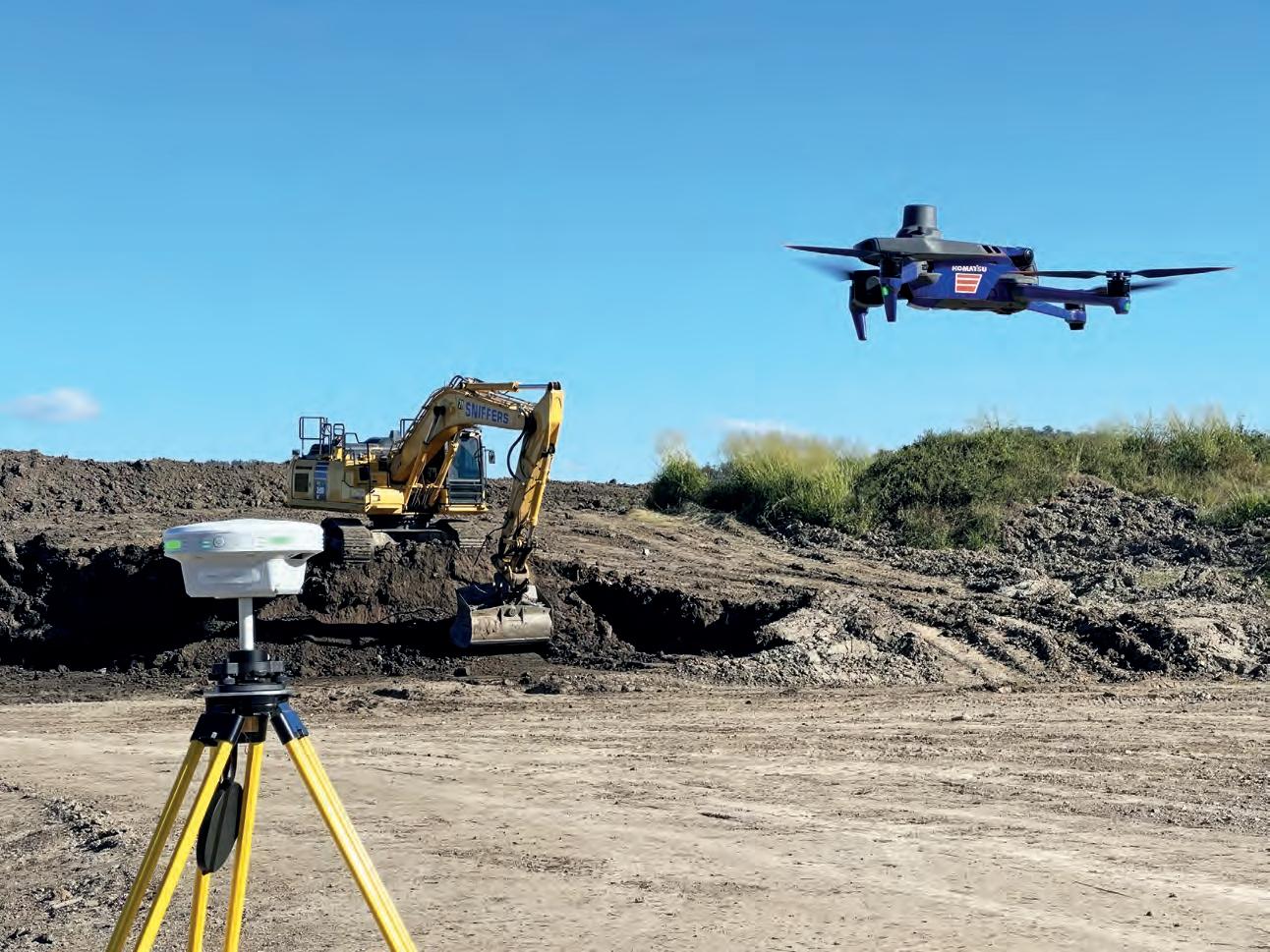
IN THE SKY YOUR EYE
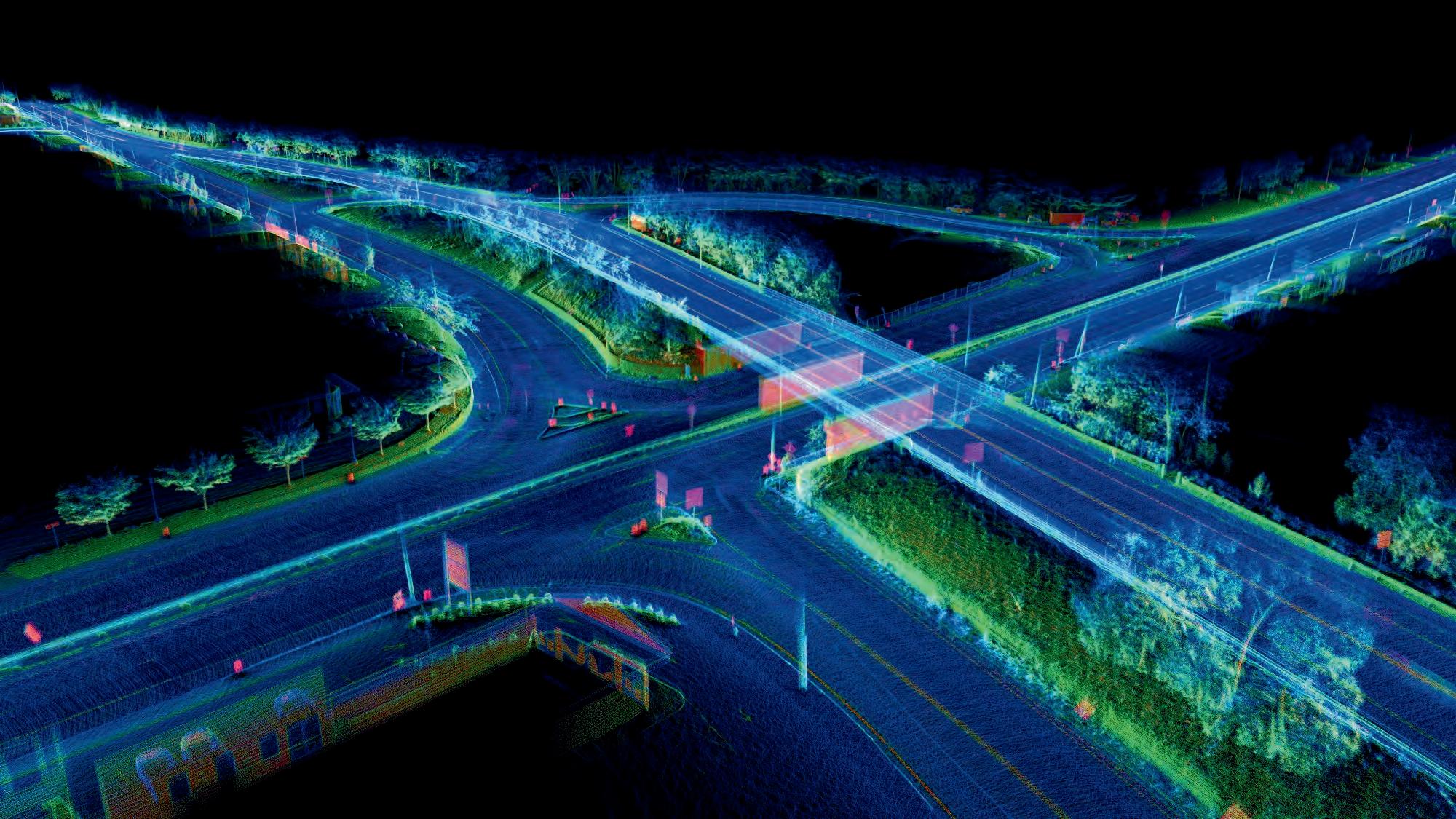
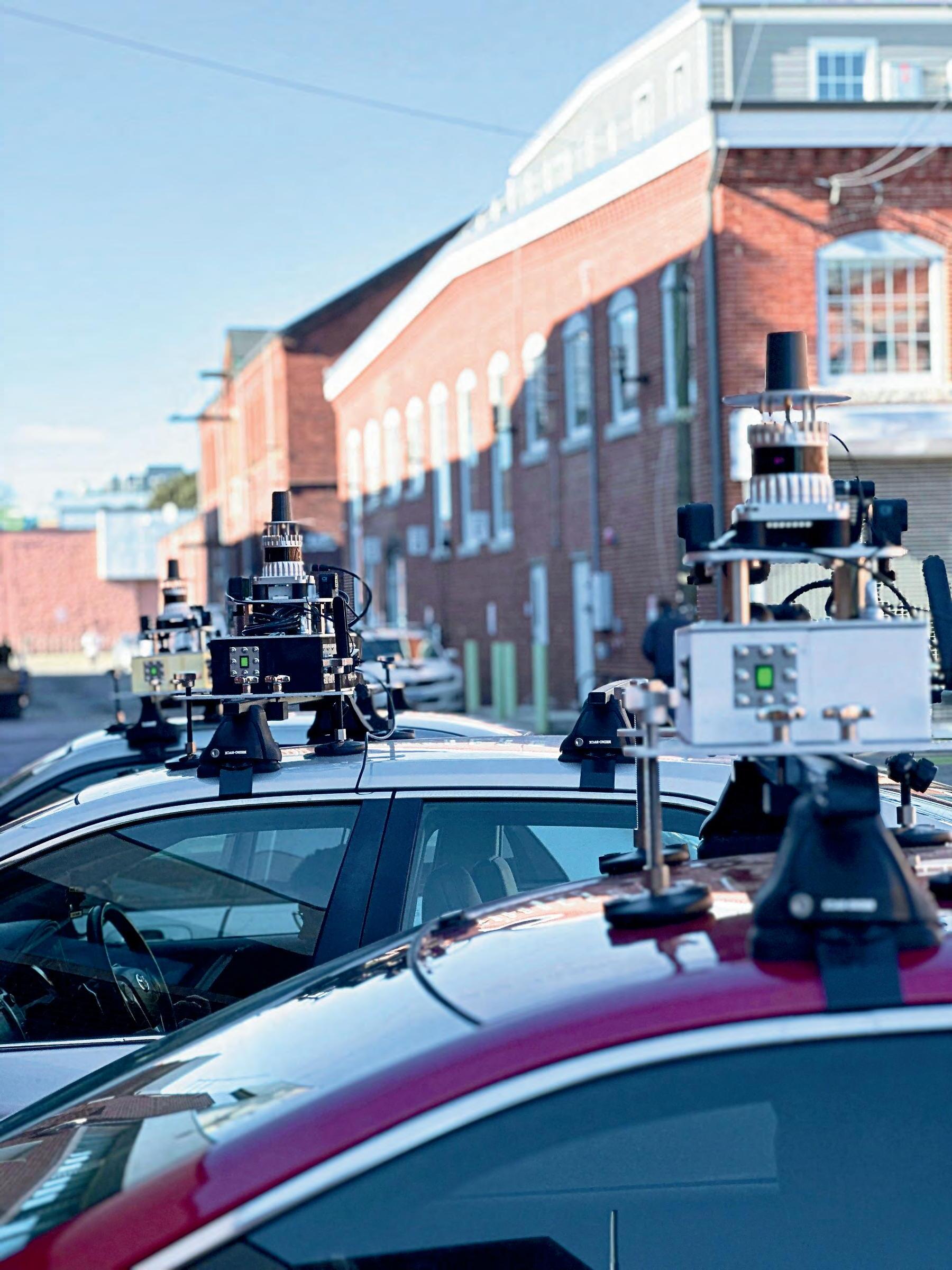
KOMATSU’S SMART CONSTRUCTION EDGE 2 SOLUTION IS TRANSFORMING CONVENTIONAL SURVEYING METHODS, OFFERING A MORE EFFICIENT AND SAFER ALTERNATIVE. KOMATSU PRODUCT MANAGER JAMES MACKENZIE EXPLAINS.
Cthe price may seem too good to be true. But Komatsu’s Edge 2 is making this a reality.
Komatsu Product Manager James Mackenzie says Komatsu’s Smart Construction Edge 2 will transform the way aerials surveying is conducted across a number of sectors specifically related to earthworks.
“Traditional aerial surveying requires using a survey-grade drone, a GPS device to record data during the flight, and placing numerous markers around the site,” he explains. “Afterward, you’d need to upload the images to a cloud processing platform and wait several hours for processing.”
Komatsu’s Edge 2 makes this process much easier and streamlined, potentially providing a 60 per cent faster surveying experience when compared to traditional methods.
“In the past 10 years, this space has
evolved rapidly,” Mackenzie says. “And the Edge 2 is a perfect example of that.”
Komatsu’s Edge 2 is technically a GNSS (Global Navigation Satellite Systems) device and processing unit in one. What this means, is that the operator can benefit from rapid processing on site, rather than having to leave and transfer the recorded data. That way users can return to the office equipped with detailed, accurate and ready to use data.
“We can also set the Edge 2 up so that the data is transferred back to our Cloud Smart Construction Dashboard, all with the click of a button. That way you don’t have to process or move that data across to a USB. It’s all about limiting the number of times that our customers need to press buttons,” Mackenzie says.
“The Edge 2 is quicker and easier, allowing our customers to plan today to work out exactly where they want to be tomorrow.”
On top of providing high quality images from a bird’s eye view, the Edge 2 has capability to remove objects thanks to
its fully inbuilt, AI (Artificial Intelligence)supported system. All these associated features can help project managers and other stakeholders to have more accurate insights into project progress, allowing them to make more frequent changes to satisfy project parameters.
“We refer to the Edge 2 as the ‘everyday drone’. While the Edge 2 is processing, you can drive to the next site to make sure that you can survey daily, every second day or as frequent as you like,” he says.
“Previously, surveyors recorded data at the end of each month, which could be too late to address delays in tracking earthwork progress. However, with faster processing times, you can survey more often using the Edge 2, and quickly identify if you’re falling behind schedule. You can view your progress more rapidly than ever.
“An example could be during earthworks. You can conduct an aerial survey before starting, after stripping the topsoil, and at each lift layer and unsuitable material
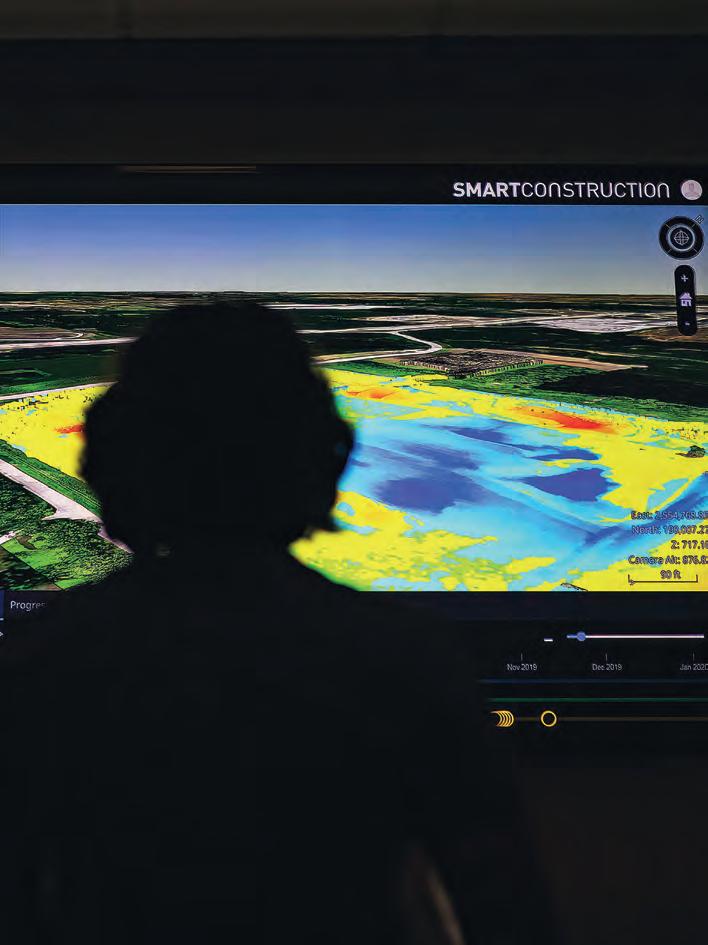
that delay work. The project maintains a digital, work-in-progress 3D model of all operational layers, which can be used for compliance sign-off and project completion. What used to be a costly and time-consuming bottleneck with traditional surveying is now made efficient with Edge 2.”
Edge 2 can also be used as a ‘base station’, as Mackenzie explains.
“GPS devices require a base station to achieve survey-grade accuracy with a drone or rover,” he explains. “The Edge 2 provides RTK (Real-Time Kinematics) corrections to the drone or rover and can also record RINEX data for PPK (PostProcessing Kinematics), making it a highly versatile solution.
“Komatsu machines, like our intelligent machine series of excavators and dozers, SmartConstruction 3D-MG and other compatible GPS machinery can also use that correction to work in RTK if the operator wishes. Once it’s been turned on as a base station to broadcast correction
assist operators.
“There are aviation rules and regulations that must be followed. We assist customers by connecting them with the right resources to get compliant. We have commercial agreements in place to provide everything from hardware, licensing, management platforms and training. We are helping our customers get started smoothly,” Mackenzie says.
“For those eager to begin but not yet licensed, we also offer drone services through our SMEs until they achieve compliance.
“The latest drone we recommend is the DJI Mavic 3 Enterprise. It is highly advanced, featuring onboard sensors that detect solid objects to help prevent collisions. One feature that has really impressed me is its ability to sense the gradient and elevation of the terrain below, allowing the drone to maintain a consistent height relative to the ground. This ensures a more uniform Ground Sample Distance (GSD). It’s incredibly intelligent.”
Another major benefit of the Edge 2 is its ability to take surveyors out of harm’s way while enabling them to conduct their assessments easier and quicker.
“It completely removes the need
“I’M SEEING A BIG UPTAKE IN AERIAL SURVEYING AS MORE AND MORE PEOPLE ARE ABLE TO SEE THE TECHNOLOGY AND THE BENEFITS THAT IT PROVIDES.”
data, unlimited devices can connect and use that service.”
RTK effectively takes signals from the GNSS and uses a correction stream capable of providing users with one to two centimetre horizontal accuracy and two to three centimetre vertical accuracy. This also provides greater autonomy for drone operation.
“You can design your flight parameters and a polygon of the area, and the drone can use that information to go out and take the images by itself,” Mackenzie says. “All you need to know is the barriers you want to set, along with the height.”
SAFETY AND EXPERIENCE
For those who may consider their lack of drone operation experience to be a barrier, Mackenzie says Komatsu has a variety of support services and training available. The Edge 2 also has a number of features that are designed to
for surveyors to walk around and near machinery and removes the chances of injury with unstable or steep terrain. The Edge 2 is a massive upgrade on walking surveying production and safety.”
Mackenzie says he’s excited to allow more construction companies to harness all that the Edge 2 has to offer, adding that the long-term return on investment has the potential to be substantial.
“I’m seeing a big uptake in aerial surveying as more and more people are able to see the technology and the benefits that it provides,” Mackenzie says. “It’s now user friendly and affordable. Ten years ago, it would’ve been very expensive to purchase this type of technology.
“I reckon nine out of ten people who have been fortunate to see the drone data and the Edge 2 in action have expressed interest. The appetite is there, customers just need to see our demonstrations of Edge 2.”
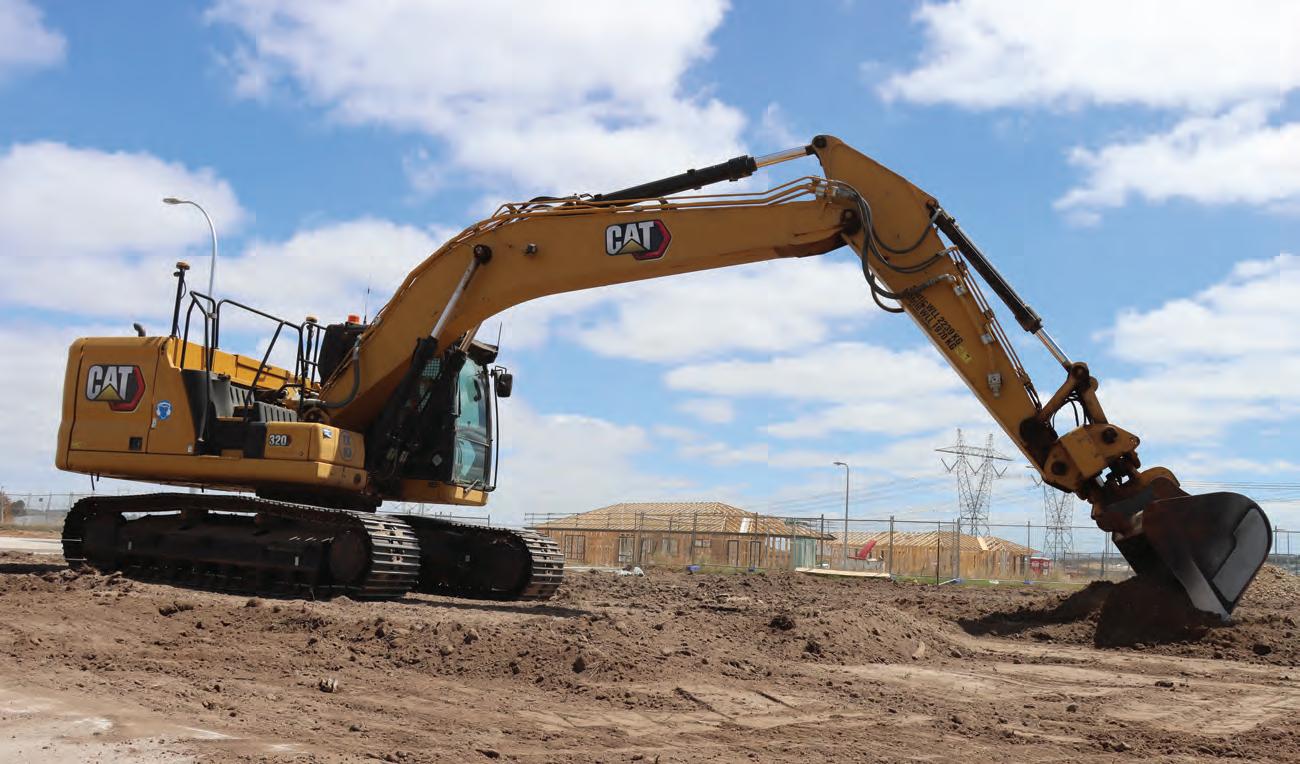
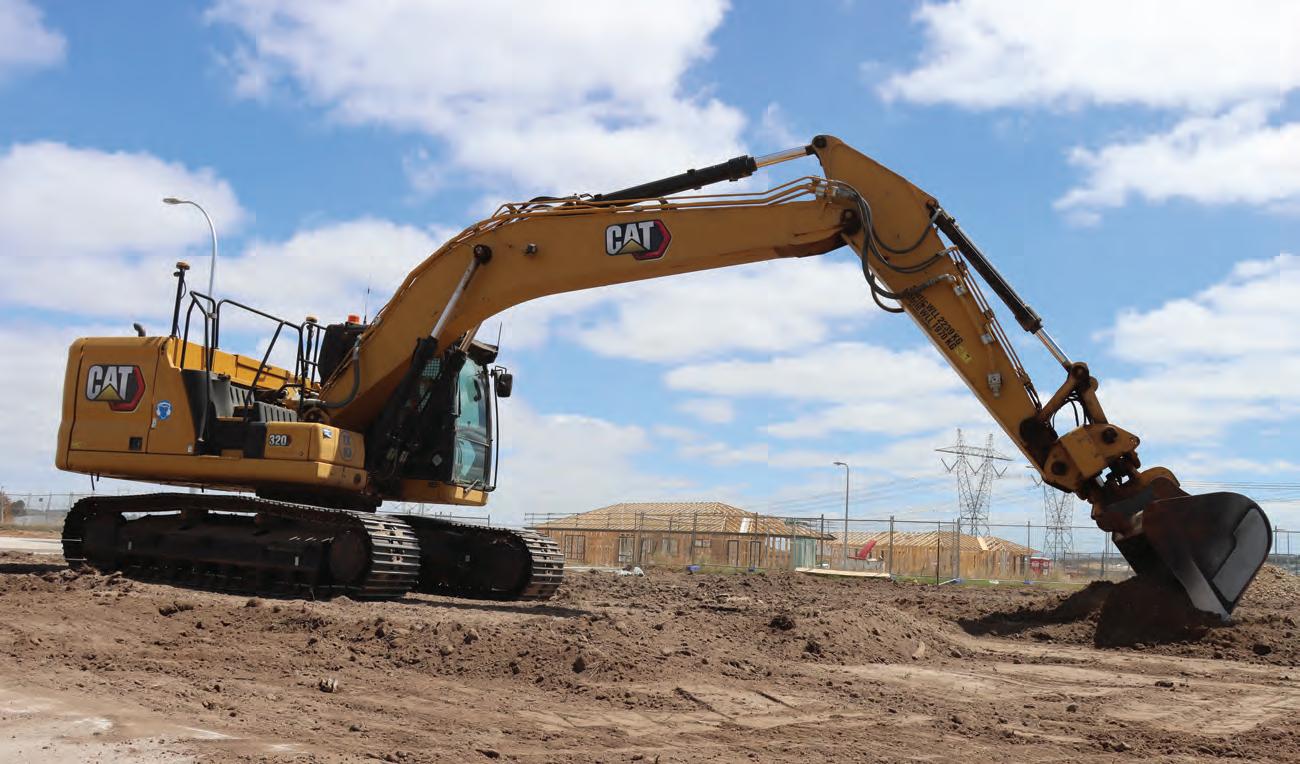
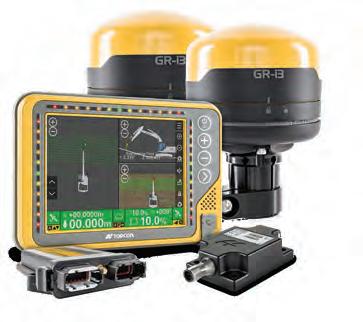

GETTING THE JOB DONE
HOLZ HEAVY HAULAGE’S HEAVY LOAD TRANSPORT EXPERTISE IS BACKED BY ITS LEADERS GUARANTEE OF PROFESSIONAL SERVICE AND TRANSPORT OPTIONS VIRTUALLY AUSTRALIA-WIDE. COVERING AN ENTIRE NATION
ISN’T EASY, BUT OEM MANUFACTURER TRT IS HELPING TO EASE THE BURDEN.
The story of Holz Heavy Haulage is grounded in determination and hard work. Qualities that have endured to this day.
Holz Heavy Haulage, an Australian and family-owned business based in Razorback, New South Wales, delivers specialised heavy haulage services.
Founder Wayne Holz started with just one truck and trailer, slowly increasing the size and variety of his machinery fleet over time, while also building up his rapport and reputation throughout the heavy haulage sector.
As he explains, the early days were tough work, filled with sacrifices and challenges. But Holz says it’s all been worthwhile.
“In 1998 we got our first truck and our first trailer, and I went out to work, doing
as many hours as I was legally allowed to,” he says. “For those first two years I was on the road quite a lot. My wife was raising the kids as I was usually away. That’s when we first started to grow.
“We grew and I was able to purchase more and more trailers and add them to the fleet.”
At the time, Holz was carefully considering different trailer manufacturers to find the best possible ‘bang for buck’.
“I was putting the word out and purchasing more trailers. It was actually one of my clients who mentioned that I should take a look at the TRT product. There were quite a few brands around, but I thought ‘why not?’
“I was introduced to TRT in 2005. We had our first talks shortly after and we’ve
partnered with them – and had a great relationship – ever since,” he says. “We purchased our first TRT unit in 2009.”
Holz Heavy Haulage now has nine trailers and three dollies from TRT, including TRT Low loaders Quad, 3x8, 5x8 trailers and TRT Dolly trailers.
Jeremy Carden, Trailer Sales – TRT, who deals directly with the team at Holz Heavy Haulage, says the partnership goes back years, with both parties loyal and trusting.
“It’s definitely more than just a typical customer relationship, it’s a proper partnership. Both Wayne and his wife Maree have come to New Zealand a few times. It’s a very close relationship that we’re more than happy to have,” he says.
“We’re really looking forward to having them again in the future, too.”
TRT has a wide range of low loader trailers catered to the Australian market, ranging from Dollies, Rows of Eight and Quad Floats right up to its impressive ESS Modular Platform trailers. Customers can also select from a range of axle configurations and other features.
Well known for their fit-for-purpose design, as well as robust construction, TRT trailers are designed and manufactured in-house and include the latest trailer technology, such as electronic steering systems.
Carden says the experts at TRT can find the best possible trailer to cater for the individual needs of each of its customers, helping to simplify the movement of plant and equipment.
“Wayne wants to be able to move everything and anything up to the legal requirements, that’s why our trailers are so effective. The general strength and durability of TRT trailers is what stands out,” he says. “One of the biggest things that differentiate TRT trailers
Below: Holz Heavy Haulage now has 12 TRT units within its growing fleet.
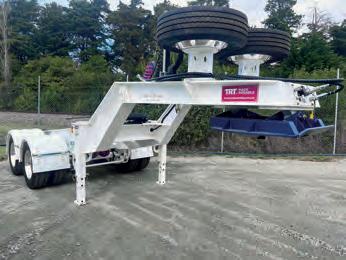
from others is that we offer double acting hydraulic suspension. Others offer the standard single-acting type, which means that the suspension control is only powered in one direction. This can lead to excessive manual labour, in the form of axle pins, along with difficulties in changing tyres and more.
“Wayne’s trailers are all really high ‘spec’. All his trailers have auto greasing systems on them, they also have heavy duty rubber conveyor belts that are deployed in a way that they don’t get ripped off. We also offer deck protection systems with different materials. We’ll pretty much try anything, depending on what the customer wants.”
TRT has also achieved a world-first in the heavy haulage market with the introduction of ESS Platform trailers, which are simply SPMT’s (Self-Propelled Modular Transporters) capable of highway speeds. This design grants additional flexibility for the operator by allowing them to add or remove axle modules from the platform trailer efficiently to suit the payload.
Holz says that right from the initial meeting, he knew that TRT would be his future trailer builder of choice.
“We have used a few other brands in the past,” Holz says. “But TRT’s trailers stand above the rest. It’s very user friendly and accessible for our drivers.
“The other great thing about TRT’s products is the access to spare parts and support. Normally if I need something, it’s shipped to me within two days. We keep a fair amount of stock from TRT in our workshop in case we need something.”
He says another major benefit of TRT’s product is the resell value of each unit, a testament to the robustness and durability of the TRT brand.
“We’ll continue to grow with TRT. Once we get to a point where we’ve got enough to move on to a newer unit, we know that we can sell what we were using and still recover a lot of that money,” Holz says. “The resale value has always been there with the TRT product.”
FAMILY FIRST
With an increasing number of TRT units and growing size of the fleet overall, Holz Heavy Haulage recently underwent a major expansion to its facilities to better cater for future demand.
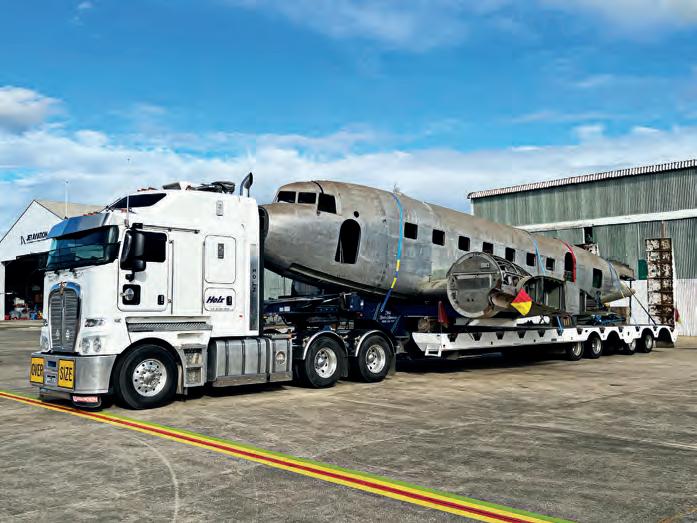
from our original home address to a new maintenance workshop with brand new facilities,” Holz says. “It’s already been a great asset, being an easier place to work and having centralised our services in one location.
“We have 14 semi-trailers on the road – so 14 prime movers on the road at any one time – which all work from our Picton yard now, with all of our servicing done there as well.”
Holz says being a family-owned business ensures that all staff members are working towards a collective goal, with many family members taking up essential positions within the company.
“Because we’re family, we all pull in the same direction. We know what each other’s thinking and we’re not afraid to bounce ideas off each other,” he says.
“We all want the same outcome. We’re growing the business together, instead of just being here to get a wage.”
As the proud Founder and Director of an Australian and family-owned business, Holz says setting up the next generation for success fills him with the greatest satisfaction.
“I’m very proud that my family is coming through and into the business. Without family, the business wouldn’t succeed. They’ve got the ability to keep the growth we’ve got going, it’s on them now,” he says.
“They’re the ones who are going to be hitting the ground running and I can sit back and watch them build upon what we’ve already got.
As an experienced provider, Holz
is capable of moving objects of all sizes to many different regions across the country.
As
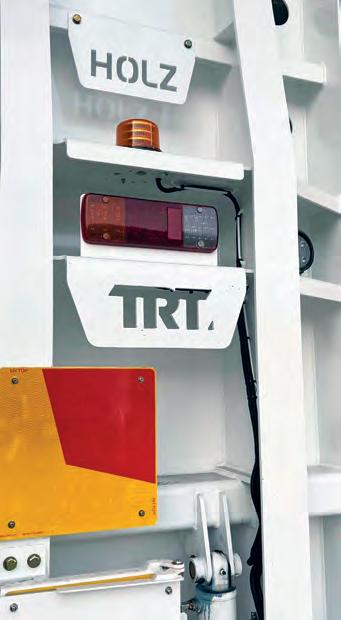
“Growth is always there for the taking. At the moment we just need to wait for the economy to change in New South Wales and Australia-wide.”
He adds that the support of the wider Holz family, the company’s growing capabilities and the trust provided by TRT, holds Holz Heavy Haulage in great stead for future success.
“It’s our serviceability, reliability and passion to push further that’s been the biggest drivers of growth for us,” Holz says.
“It’s also those long-term relationships and building up a rapport with a lot of our customers that’s helped to get us to where we are today.”
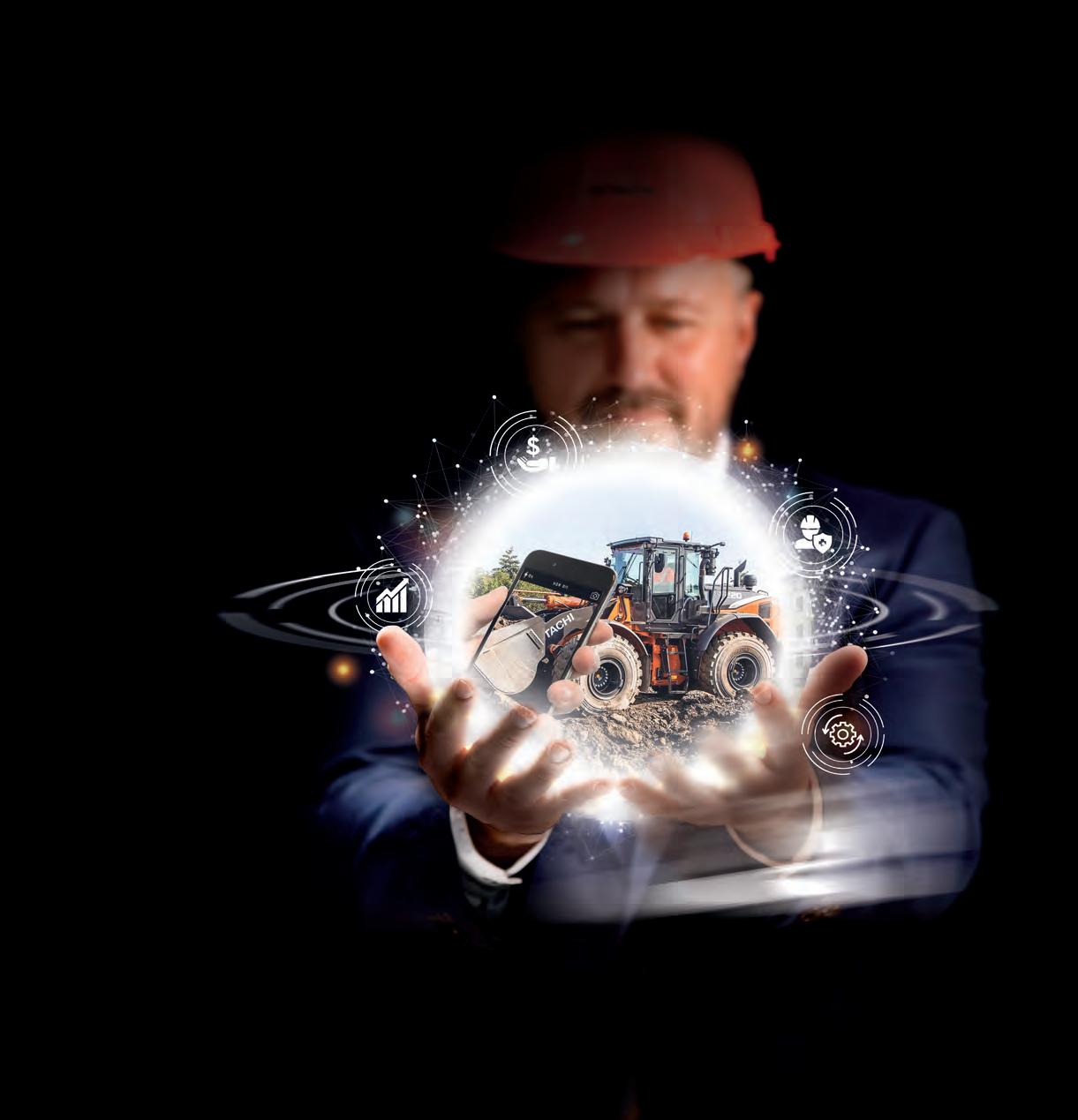
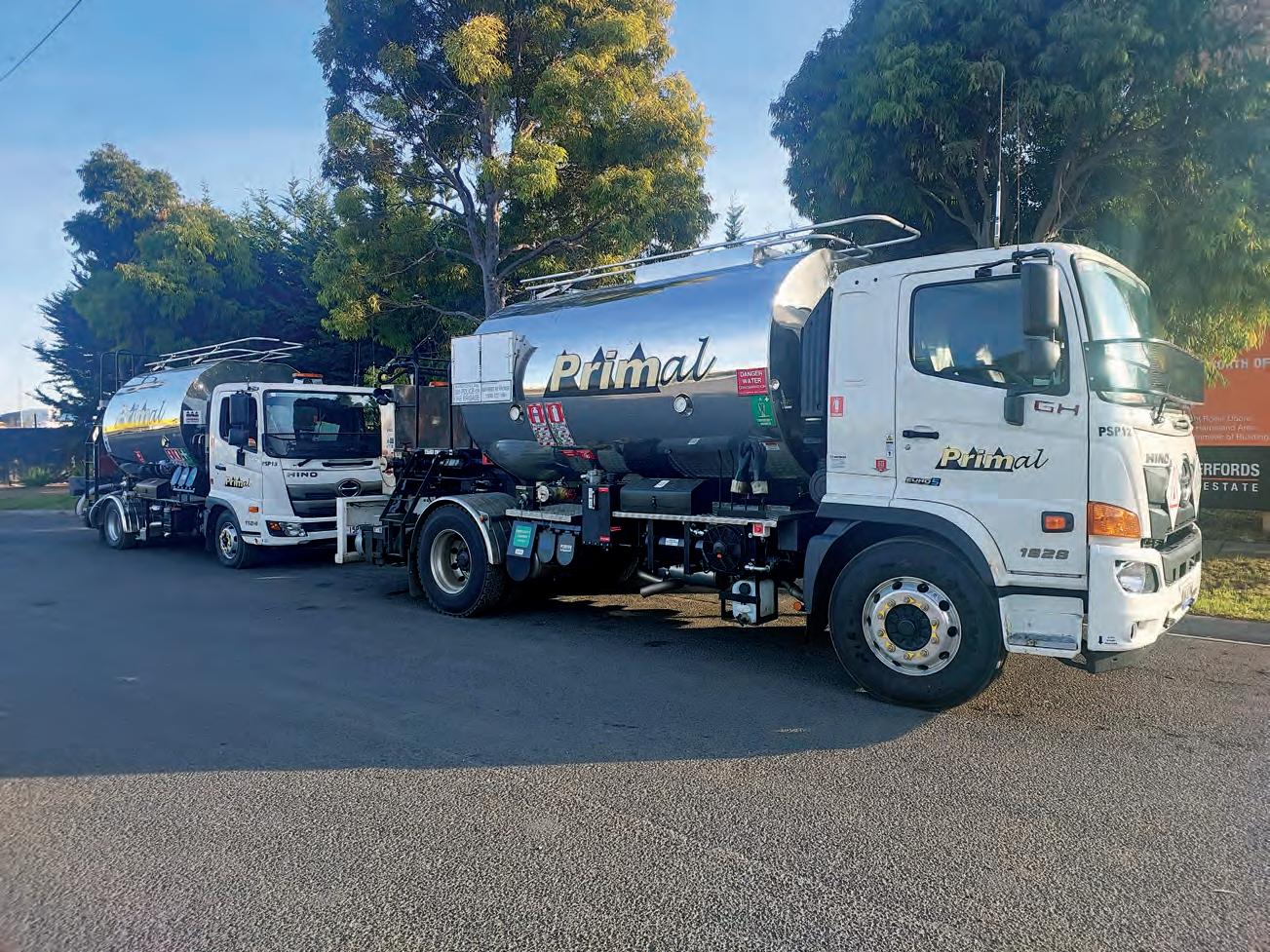
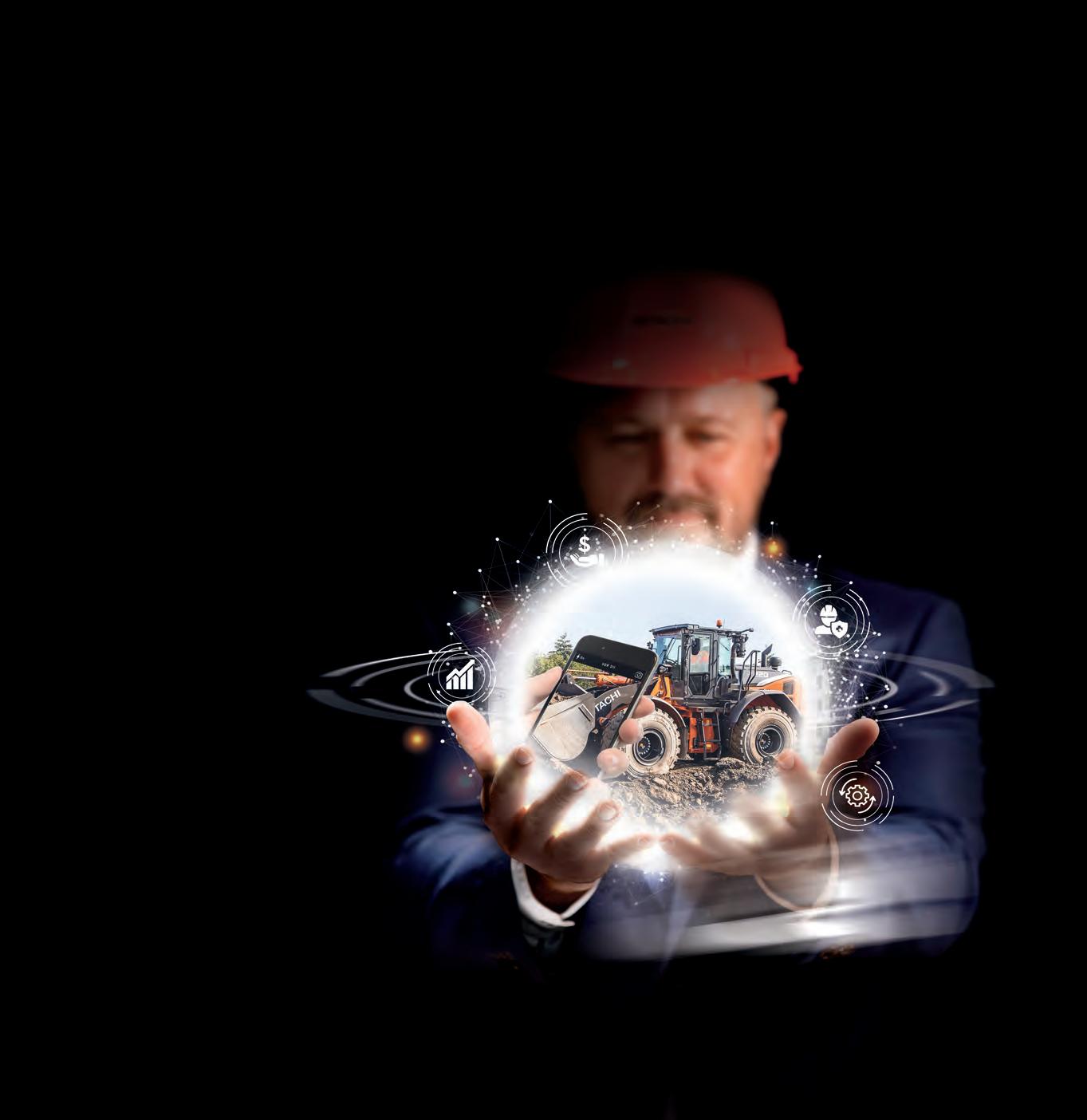
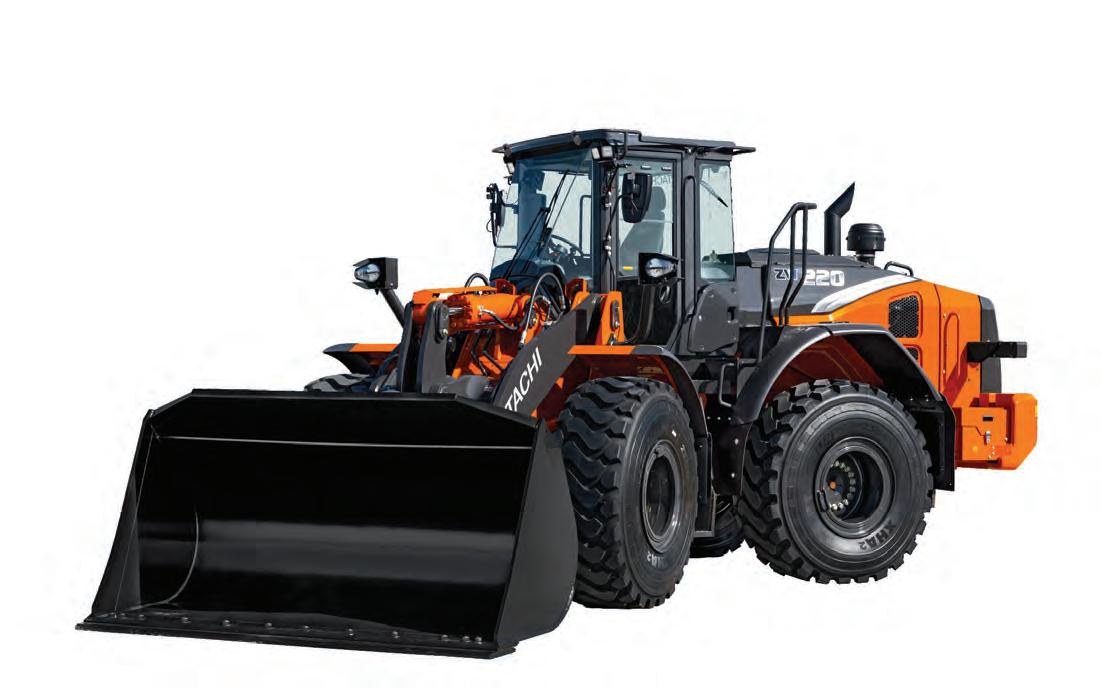
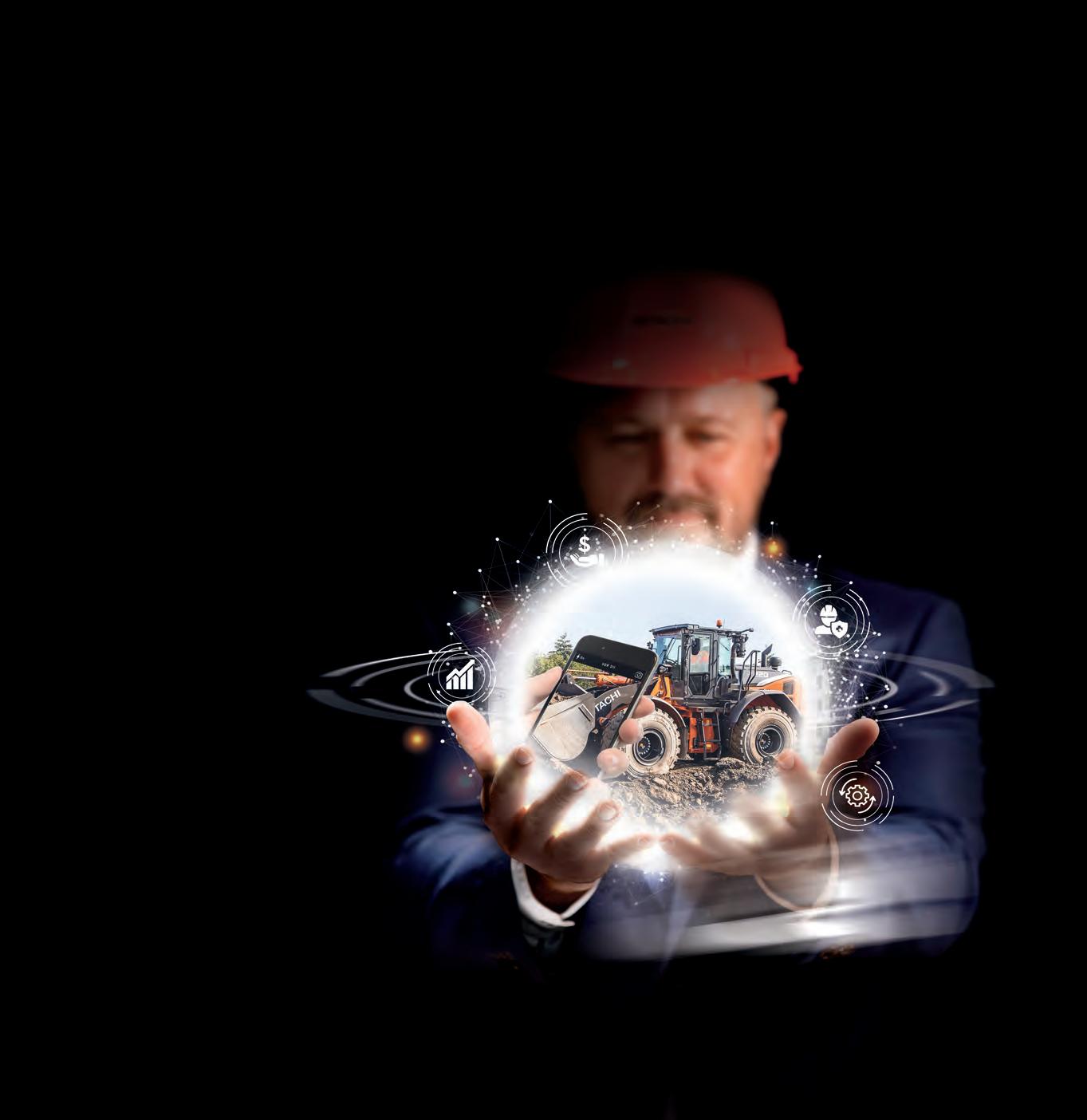
YEARS IN THE MAKING
PRIMAL SURFACING HAS BENEFITTED FROM A LONG-STANDING PARTNERSHIP WITH SPECIALISED ROADING EQUIPMENT (SRE) FOR ITS MACHINERY NEEDS. NOW THE GROUP IS ADDING TWO NEW SRE SPRAYERS, MARKING A CONTINUATION OF THIS DECADE-LONG CONNECTION.
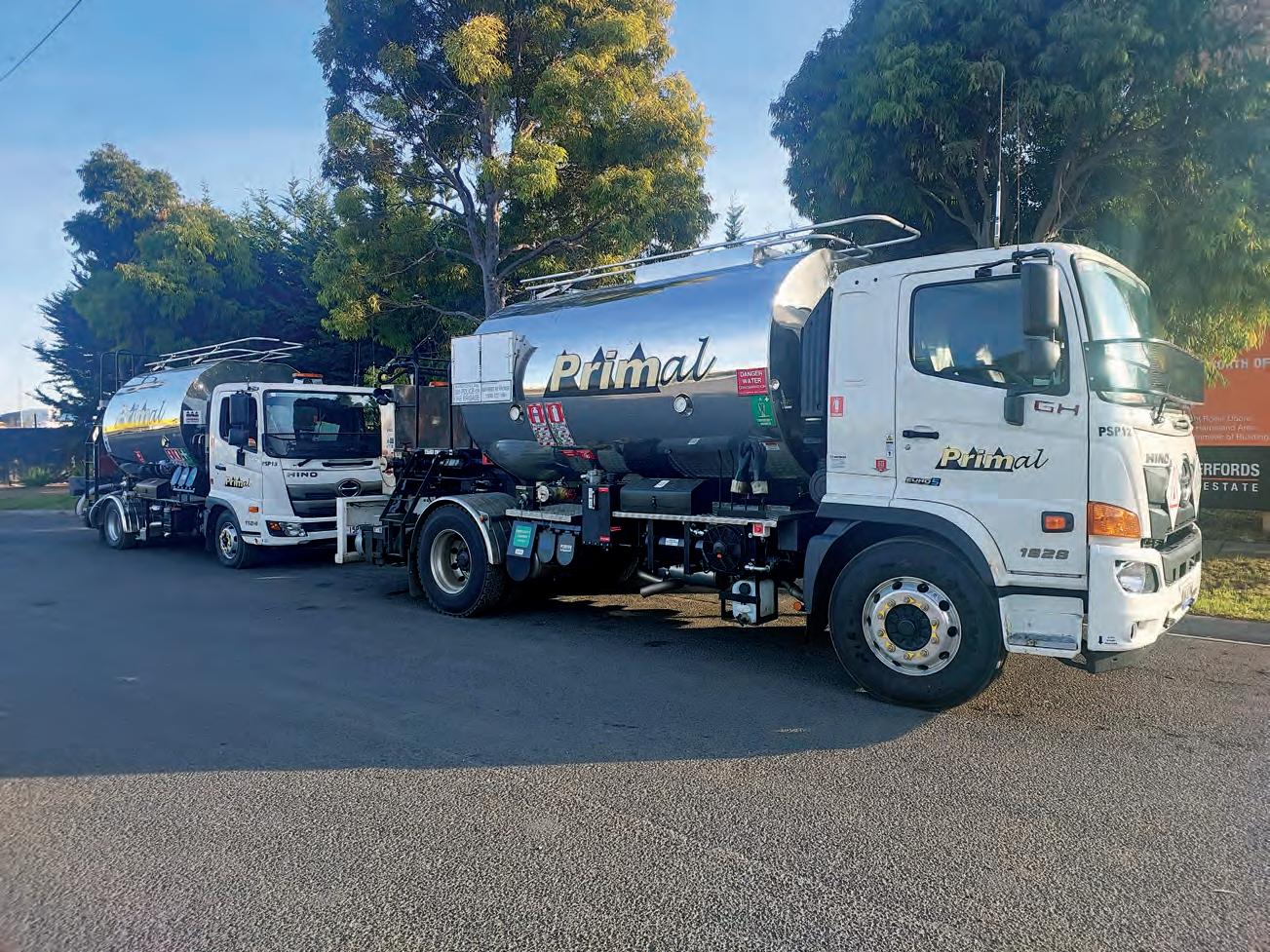
Primal Surfacing (part of the VSA Roads Group) is regarded as one of the leading providers of road construction and maintenance services around the country. A big part of maintaining this reputation is its frequent upkeep and updates of its machinery fleet.
The company’s success is rooted in its history of incorporating new technology and equipment. So much so, that the company claims to have the youngest fleet, containing the most advanced equipment in Australia – the result of a more than $5 million investment in capital equipment during the past few years.
Primal Surfacing regularly touches base with the sector to learn more about the latest machinery available. One manufacturer that’s long been on Primal Surfacing’s radar is Specialised Roading Equipment (SRE).
Located in New Zealand, SRE manufactures a range of telescopic bitumen sprayers for all kinds of materials and applications, such as hot bitumen and emulsion spraying.
VSA Managing Director Justin Bartlett says the affiliation with SRE started when Primal Surfacing was looking to strengthen its machinery fleet.
“Our relationship with SRE began 12 years ago when we purchased a 12,000-litre sprayer,” he says. “That was a big step for us, it was the first time that we went down the path of having a sprayer with a telescopic spray bar, as opposed to the traditional Australian methods of having vertically raised bars that are built in segments.”
This first venture into the telescopic sprayer space opened many doors for Primal Surfacing, namely around increased efficiency and productivity. Importantly, SRE’s units also ticked the boxes when it came to reliability and output.
“With every job, there’s a lot of moving parts. The cost of a spray ceiling crew per hour is very expensive, so you can’t have pieces of the production process breaking down, because if one piece stops, everything else stops,” Bartlett says. “That’s why we’ve got well-equipped workshops, highly-skilled staff and our significant investment in equipment. When our equipment rolls out the gate, we know that we’re going to get a decent day’s work in.”
Bartlett says acquiring a telescopic sprayer was high on Primal Surfacing’s priority list.
“When you compare the telescopic spray bar design to a conventional Australian
bar, the telescopic can be moved in and out quickly, so it makes for a far more efficient job. When you’re doing maximum and minimum widths, works in courts and projects such as that, having that greater control and ability to move quickly is really useful,” Bartlett says.
“We were able to place an order for righthand drive trucks that were made to an Australian standard and were ready to roll on Australia’s road network. For us it was a no-brainer.”
Such has been the robustness and reliability of SRE’s units, Primal Surfacing still operates the very first sprayer it purchased from SRE. Now Primal Surfacing has added an additional two SRE units to its growing fleet.
Simon Mckinnon, Workshop Manager at VSA Group, says the lead times for the equipment, as well as prompt support and responses, have been key reasons for Primal Surfacing’s continued interest – and recent purchase.
“The speed in which they could deliver the trucks was definitely a factor in us purchasing the first SRE unit,” he says. “As we were getting closer to replacing our ageing fleet, our smaller units were doing most of the work in metropolitan areas, which
Primal is a proud and loyal customer of SRE, having had a relationship that’s gone on for longer than a decade.

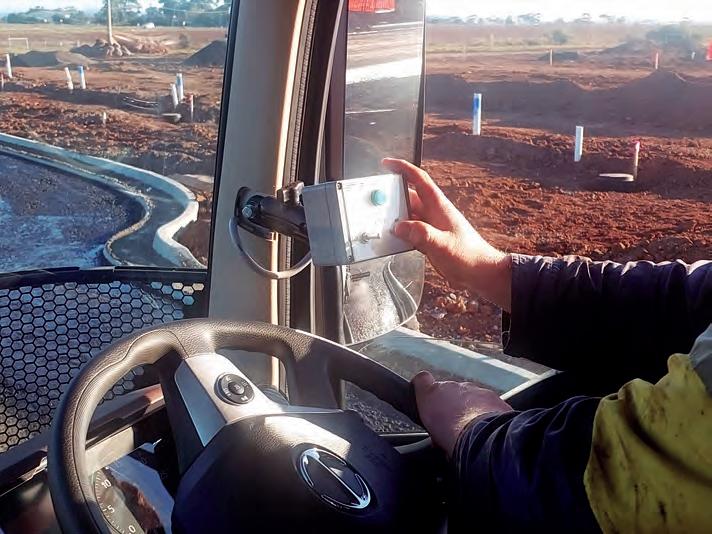
“That means that we needed sprayers that had a shorter wheelbase, smaller volume tanks, but highly flexible spray bars. That’s why we went the way of SRE.
“The relationship we have with Chris (Kaelin, SRE Business Development Manager) is great, if we ever have any questions or if there’s any issues, he’s usually able to jump right on it.”
TECHNOLOGICAL INNOVATION
Bartlett says there were several reasons for adding another two SRE sprayers. On top of the renowned support, and relative proximity of SRE being based in New Zealand, another big plus for Primal Surfacing has been the technological capabilities of SRE’s units.
“Not only did we see a telescopic spray bar that we were comfortable with, but we also saw an operating system that was very appealing. It’s a system that’s flexible and
SRE’s telescopic sprayers come with a variety of technological features aimed at making operation as simple as possible for the user.
every application can have its own slight nuances,” he says.
“We’re able to say to SRE ‘we want your operating system to do X, Y and Z’ and they’ve been more than happy to accommodate.”
SRE’s telescopic bitumen sprayers are some of the most technologically advanced in the market.
With an integrated computer control system, all spraying functions are done inside the cab on SRE’s intuitive cab touchscreen or operational remotes.
And that’s not all. SRE also has a real time job data transfer system, which provides customers and project stakeholders with spray reports providing accurate productivity and performance data, aiding administration and management.
As Mckinnon explains, SRE’s technology also makes remote support a breeze.
“SRE can dial into the truck from New Zealand, so if we’re having trouble with something, SRE can see via the truck modem what we’ve sprayed, where and when. It’s a big feature for us and a great feature to aid the country-to-country communication,” he says.
“It solves a lot of problems straight away. They can change the program and the settings remotely, just with a phone call. They can see the onboard diagnostics, which allows SRE to guide our mechanics to resolve any issues. If that doesn’t work, one of their technicians has been happy to fly over and pay us a visit to smooth things over.”
Chris Kaelin and the team at SRE have also provided additional training services to ensure that Primal Surfacing’s operators can optimise their time and output in the units. They have also been present throughout the initial and subsequent unit calibrations.
Plant and Equipment Engineer Syed Ahmad Raza says he’s established a good rapport with the SRE team in a short period of time.
“Considering I’ve only been contacting them for a few months, the feedback and the prompt responses have been really good. It’s a relationship that’s grown gradually in the past few years and continues to grow today,” he says.
“We want to push our technology forward, and SRE giving us good products and support plays a big part in that. If there’s an opportunity through the online diagnostic system to increase or add to what we’ve already got, they work with us to make sure we can benefit. We want our machinery to be up to date with modern standards, with SRE we can exceed those standards.”
Mckinnon and Bartlett say they’re both looking forward to seeing what the two new units are capable of, with both already hearing positive feedback from operators.
“I’d like to see the years tick by and us still using these same models. I’m looking forward to seeing these units pay for themselves and start earning their keep. Now we’ll see what they can do for the next 10-15 years at least,” Mckinnon says.
Bartlett says there may also be plans in the future to replace one of the company’s larger sprayer units, but for now the two SRE units will lead the way.
“Both of our operators who have had a go at the new units say they’re getting better and better every day. The more time they spend in them, the more productive they’re becoming,” he says.
“They’re making a big difference already.”
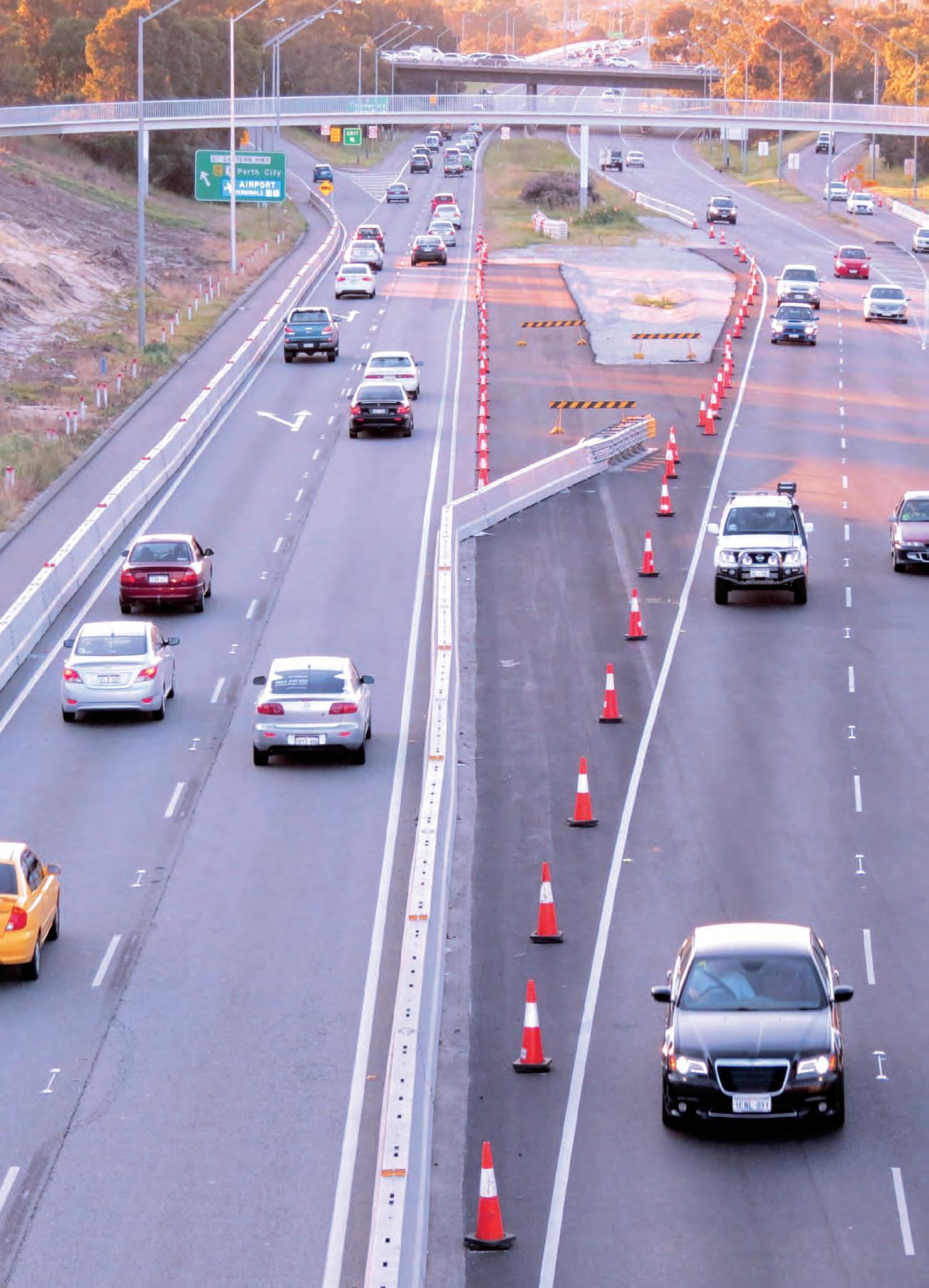

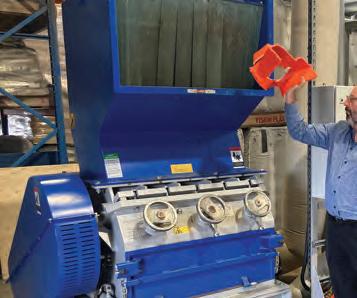
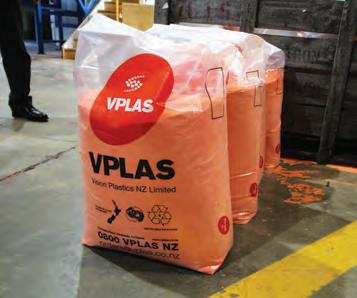
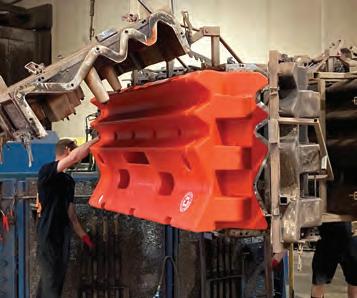
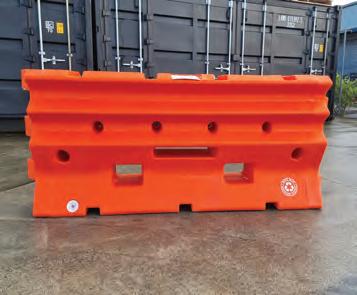
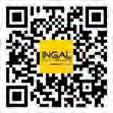
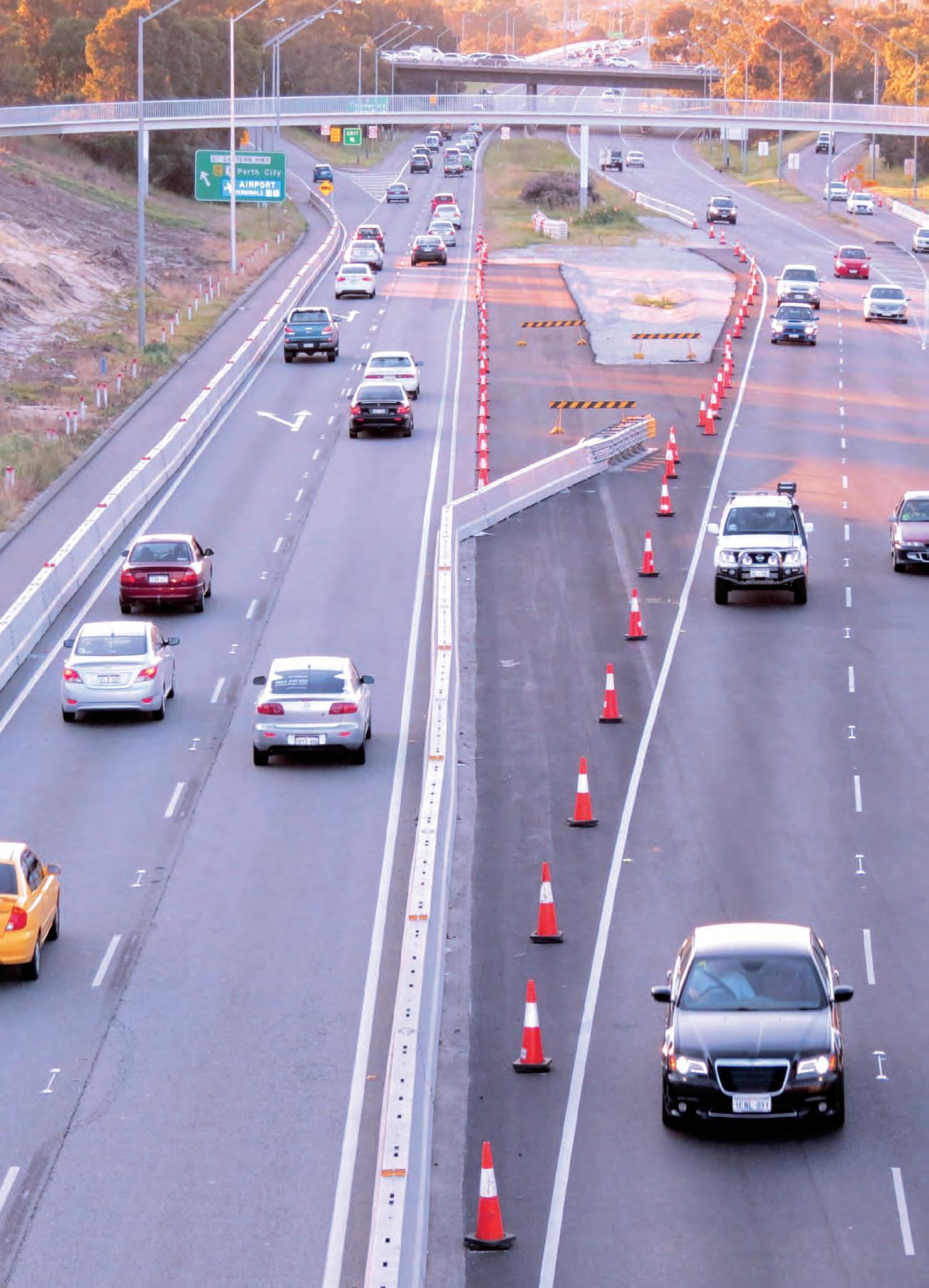
CHANGING LANES
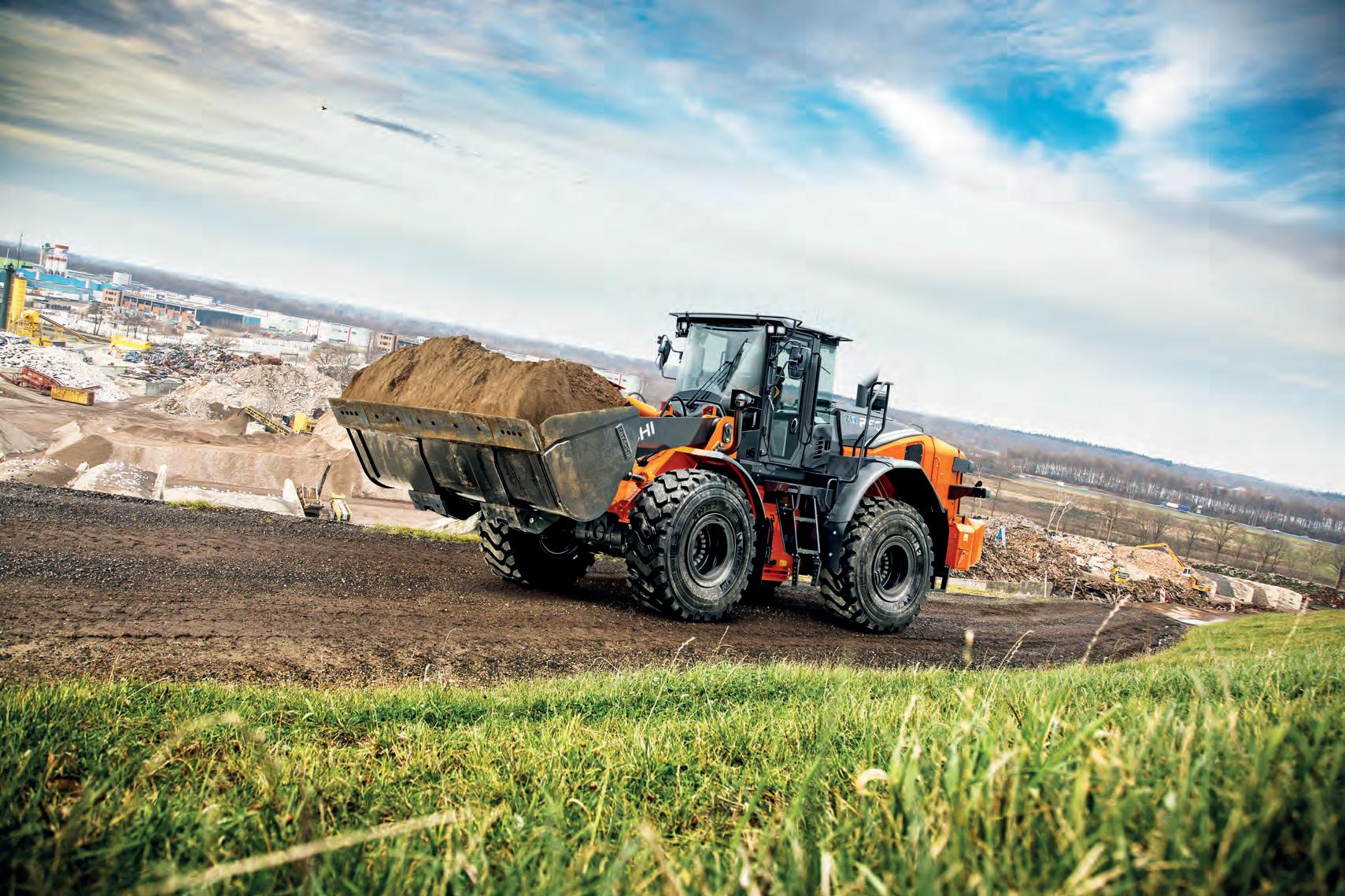
HITACHI CONSTRUCTION MACHINERY IS EXPANDING ITS WHEEL LOADER RANGE, DEVELOPING A LINE SUITABLE FOR INFRASTRUCTURE AND RAIL WORKS. DAVID GALLINA, NATIONAL PRODUCT MANAGER, EXPLAINS WHAT THIS SHIFT IN FOCUS MEANS FOR CUSTOMERS.
David Gallina, National Product Manager –Hitachi.
For those in the agricultural, waste, mining and construction sectors, the iconic orange livery of Hitachi Construction Machinery is an easily identifiable landmark of project sites.
The construction machinery manufacturer is now welcoming brandnew units to its “Orange Family”, growing its strong foothold in a number of different industries.
It’s also entering and strengthening its position in other growing sectors, some of which are new to the company.
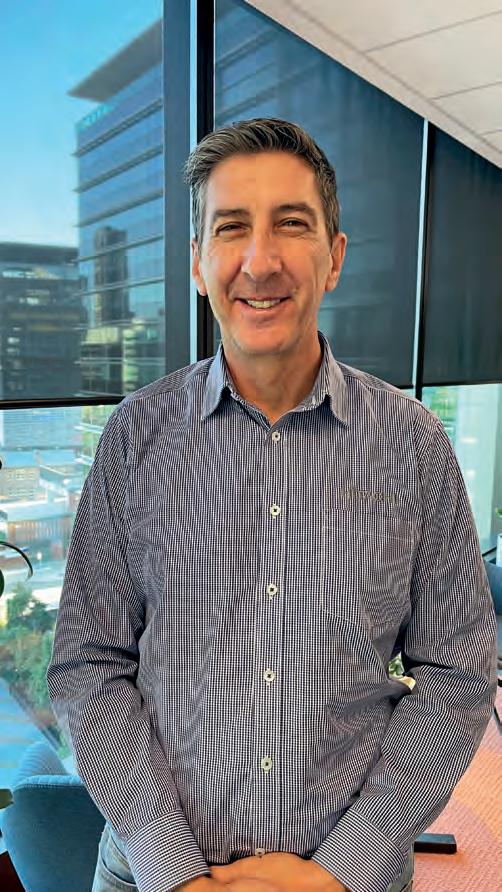
Hitachi is eyeing fresh horizons for its new ZW-7-wheel loader range, with aspirations of growing its portfolio in the rail maintenance space.
As David Gallina, explains, it’s more of a natural shift, considering Hitachi’s previous success in the rail sector.
“We already provide rail maintenance excavators, so we view the new wheel loader range as a complement to our existing excavators, which have successfully established themselves in the market,” he says. “We’ve successfully established a foothold in the agriculture and recycling industries. Going into rail maintenance and infrastructure industries with the ZW-7 range is just another step in expanding our portfolio of industry segments that we believe we can be successful in.”
Gallina says the shift of focus to the rail sector isn’t completely out of the blue for the ZW-7 wheel loader range.
So, how, and why are these machines so well suited to the rail sector?
The ZW-7 range seamlessly integrates into any rail maintenance machinery fleet, featuring enhancements such as a wider tread width, exceptional stability and capacity, compatibility with various attachments and loader forks, increased horsepower and torque, and improved transmissions.
Gallina says the ZW250-7 is among the standout models that are already well suited for the rail sector.
“We see the ZW250-7 in particular as being a workhorse for the rail sector, a machine that can go up against the best of them,” he says. “We offer a machine that’s as capable, if not better and safer in the rail space, than what’s currently available.”
Gallina says the feedback he’s received predominantly centres around performance, comfort, visibility and safety.
“It’s a smarter machine, better for your bottom line, more productive, very comfortable and very quiet,” he says.
“We’ve sold a number of units already and the feedback has been exceptional.
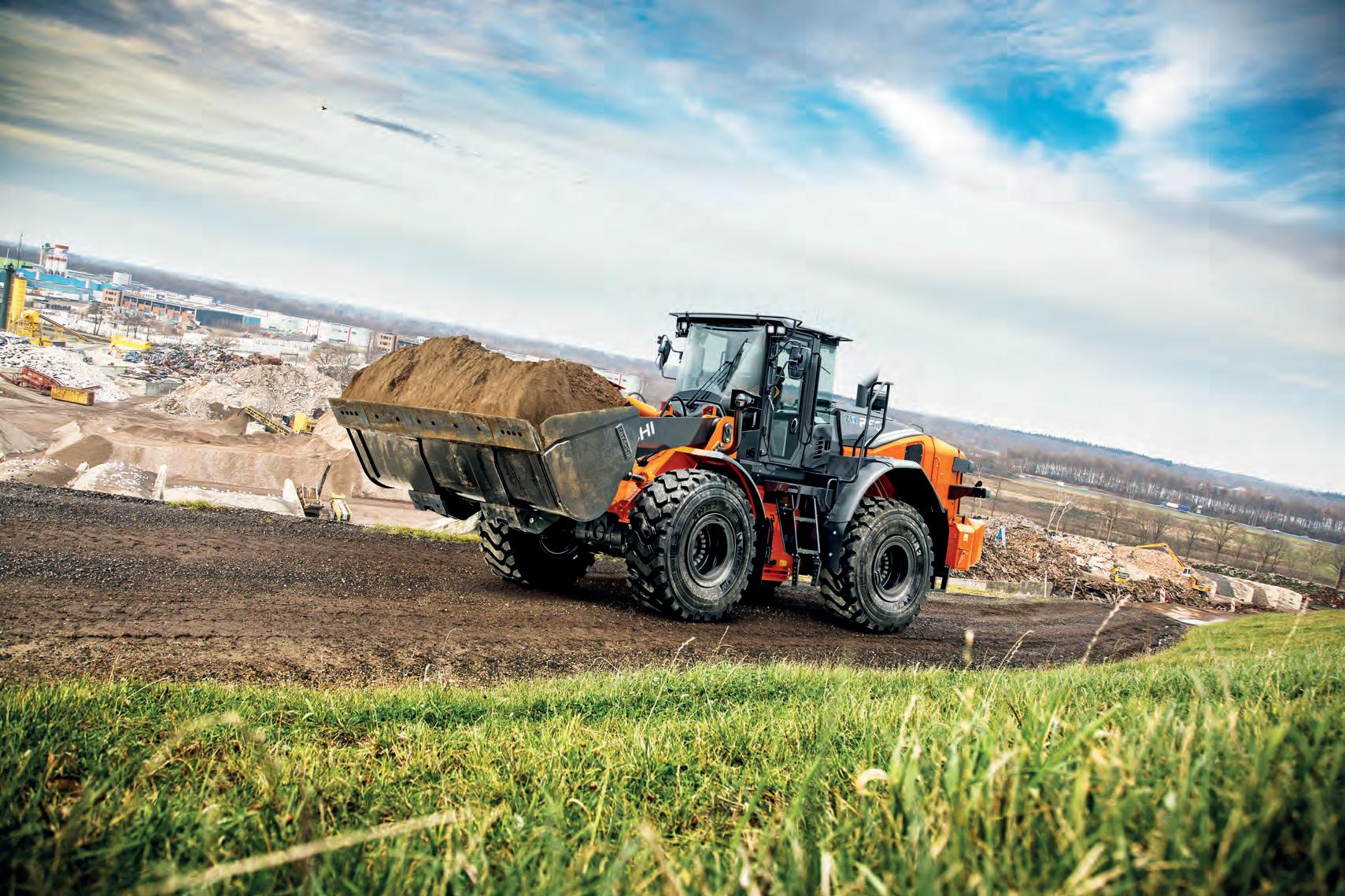
A lot of the feedback has even exceeded our expectations.”
Changes to the European-styled and designed interior of the cab are all aimed at ensuring the operator feels refreshed and comfortable at the end of the day.
An improved seat, low noise and vibration levels, along with a fully adjustable armrest and ergonomic multifunction lever, all contribute to a more comfortable experience.
The comfort of the ZW-7 range is matched by its innovation, with a userfriendly controller and high-resolution screen helping to optimise control of the machine for the operator. In a flash, operators can help to save time and fuel through the approach speed control feature.
They can also load trucks accurately, thanks to a payload monitoring system, again helping to save time and money.
Handy for the rail sector, the ZW-7 range also features an auto powerup function, which detects when the machine is ascending rail embankments and automatically increases the engine RPM while delaying gear shifts.
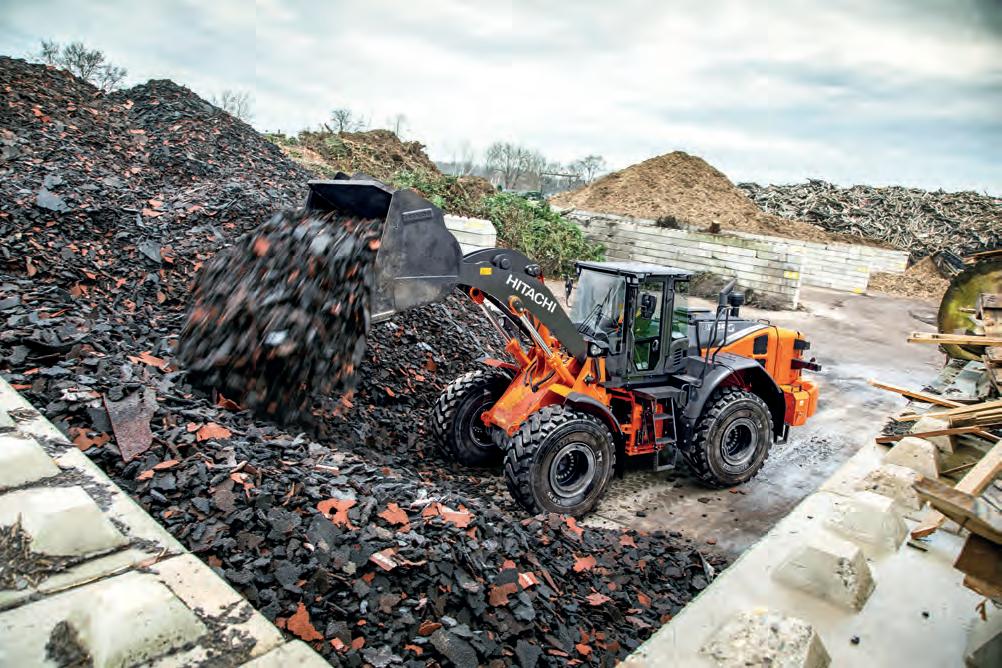
camera, the rear object detection system, the integrated controls, it just makes the operator’s life a lot easier.”
To help optimise these features, Gallina and the team also provide training and on-boarding sessions for newer operators, as well as experienced operators new to Hitachi machinery.
These features and more are centred on making each project as simple as possible, helping to reduce stress and fatigue for the operator, as Gallina explains.
“If you can keep an operator happy and refreshed at the end of each day, they’re more likely to stay with the business long-term,” Gallina says. “For business owners today, they’re most likely to purchase a machine that an operator wants, because it’s hard to find and keep experienced operators.
“That’s why the operator has a larger influence on purchasing decisions these days. With this machine, they’ve got the ultimate control over their own comfort and safety. Features like the onboard scales, the bird’s-eye view (270 degree)
“We offer in-depth training and familiarisation services to ensure that the operators and owners can maximise their return on their purchase in terms of profitability and output,” Gallina says.
“It’s to make sure that at the end of the day, the operator can have a firm grasp on the basics.”
Gallina says the immediate popularity of the ZW-7 range since being introduced to Australia, as well as Hitachi’s experience in delivering innovative construction machinery, will support the company as it tackles the challenges presented by its new sectors of interest.
“Operators tend to buy what they’re used to and what they’re comfortable with,” Gallina says.
“That presents a challenge, but it’s an exciting prospect and we’re going to have a go.
“Before it might’ve been challenging to break into the sector, but now we’ve got the machinery to do it.”
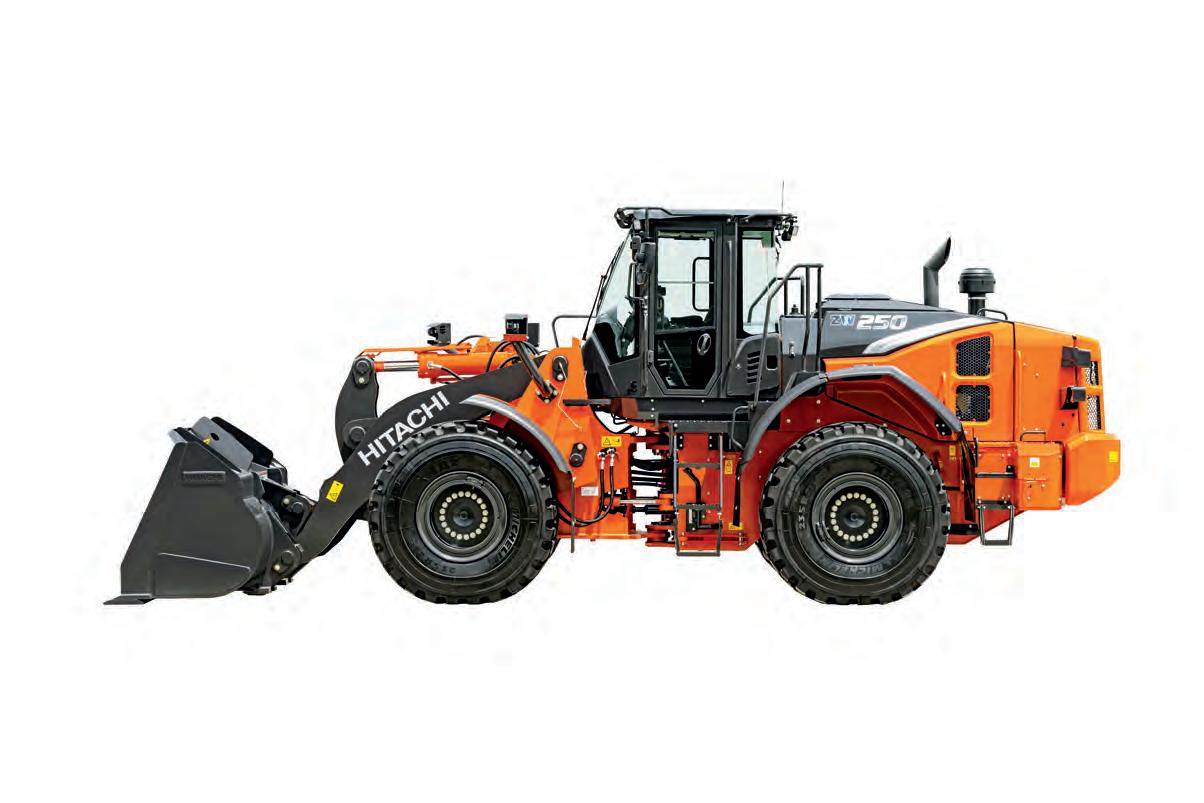
“FOR BUSINESS OWNERS TODAY, THEY’RE MOST LIKELY TO PURCHASE A MACHINE THAT AN OPERATOR WANTS, BECAUSE IT’S HARD TO FIND AND KEEP EXPERIENCED OPERATORS.”
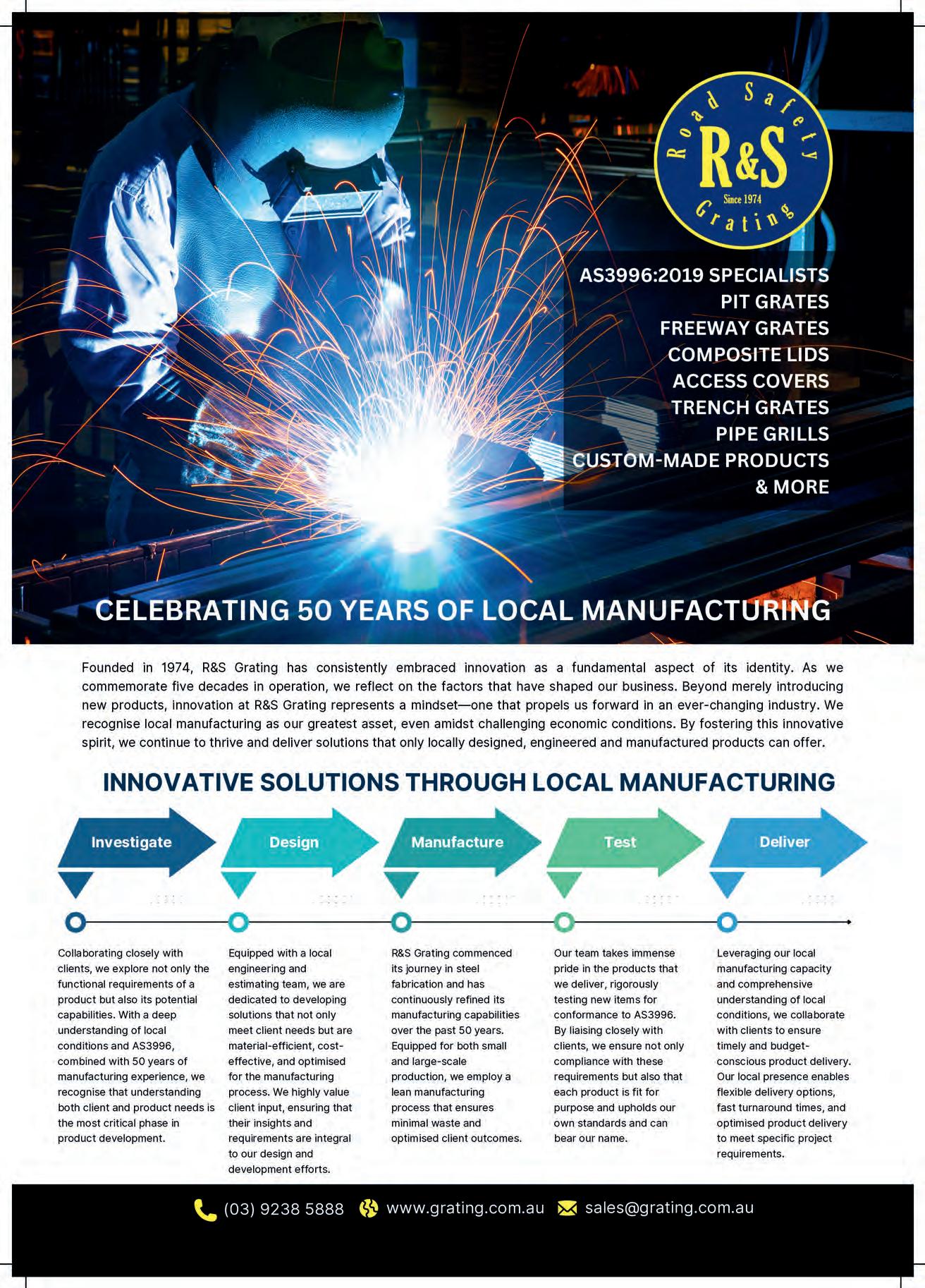
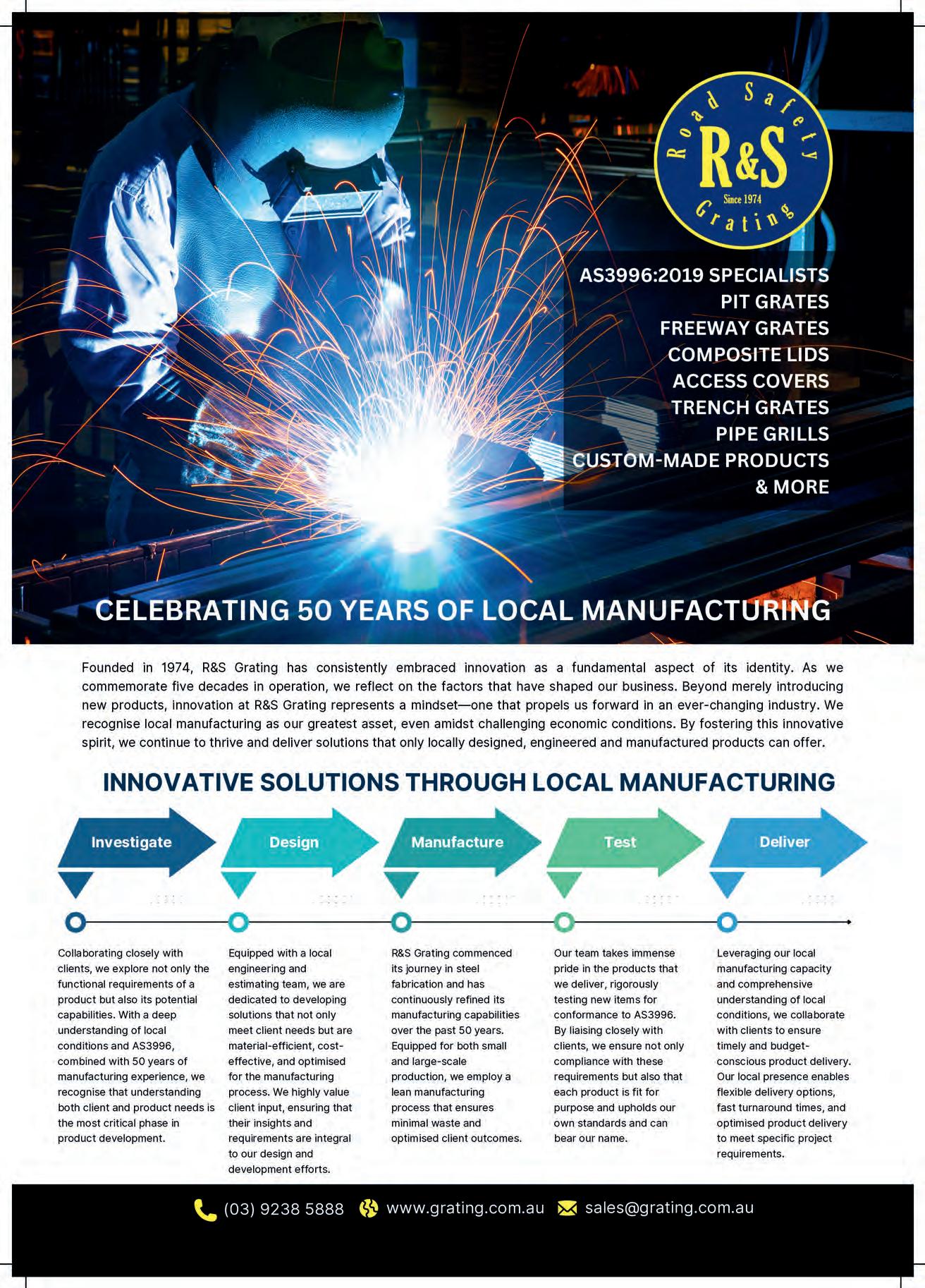
FOR SAFETY ONE DIRECTION
QUALITY
FABRICATION & ENGINEERING’S ROAD ANT IS HELPING TO INSPIRE THE DEVELOPMENT OF SAFER AND MORE SUSTAINABLE ROAD CONSTRUCTION MACHINERY, WITH THE FORWARD-MOVING AGGREGATE SPREADER STILL CHANGING THE GAME.
For years, reversing tippers were the preferred, and at times the only, option for aggregate spreading on a large scale.
Glaring safety concerns, particularly with reversing and blind spots, were at times overlooked due to a lack of alternative solutions.
Quality Fabrication & Engineering General Manager Glenn Hardiman says the introduction and continued success of the forward-moving aggregate spreader signifies a change throughout the sector.
“Our customers have found that spreading from the rear cabin in a forwards direction is much more comfortable and safer for their operators,” he says. “I don’t think people realise the stress involved for the operator if they’re required to reverse with a conventional vehicle. It’s so hard for them to see what they’re doing with only their mirrors.
“The Road Ant helps to alleviate some of that stress.”
The Road Ant features both a front and rear cabin, with full operation of the truck, spreader and safety controls from either end, eliminating the need to spread in ‘reverse’. The rear cabin is also dual control, enabling operation from either the left or right-hand side for a clear view of the spread line, also making it ideal for training new drivers.
“The feedback that we’ve had is that operators of the Road Ant are relieved that they’ve got a machine now with a clear line of sight and far greater visibility. It helps to make their daily activity so much simpler,” Hardiman says. “Thanks to the Road Ant, operators can say goodbye to blind spots.”
On top of offering independent driving control from both ends of the machine, the Road Ant can be fitted to a variety of cab chassis and to date have been fitted to Hino, Volvo, Isuzu, Iveco and DAF.
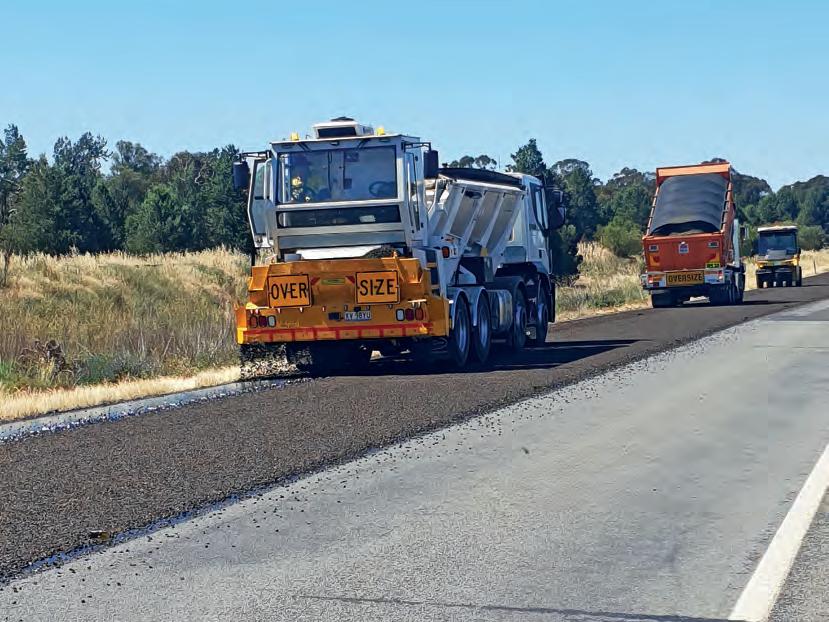
Operationally, the Road Ant conveys the aggregate from the Trout River moving floor body, underneath the cabin and into the Trout River 10 gate chip spreader. Reaching 2.5 metres as standard, the spreader can service widths of up to 2.95 metres, with extensions, or 3.4 metres with additional extensions, making the machine suited to arterial and local roads.
It’s features like this that have led to interest at a state government level. Hardiman says Quality Fabrication & Engineering recently conducted field tests as part of a presentation to Transport for NSW, which has expressed interest in forward-moving aggregate spreaders.
“We’ve had more and more interest interstate, it’s encouraging to see the Road Ant is gathering such interest in New South Wales and South Australia,” he says.
“People can be hesitant about accepting a new concept and question how it’s going
to work. But we’ve now got 24 units on the road, and it’s become obvious that they’re reliable, accepted and clearly now the preferred choice for forward aggregate spreader vehicles.”
This interest is not only off the back of the potential safety of the machine, but also its sustainability capabilities.
GREENER AND CLEANER
“The outstanding factor is the aggregate and stone that it can save. Because we’ve got very accurate measuring in the spreader, there isn’t excess stone laid out unnecessarily, which would otherwise just be swept off the road and onto the shoulder,” Hardiman says. “That gives you big savings in terms of wasted aggregate.”
The Road Ant is a robust and durable design, increasing the sustainability of a business, because it can run the machine for longer, with reduced maintenance intervals.
Greater visibility and significant standard spreading widths are just some of the reasons why the Road Ant is now among the preferred options for forward-moving aggregate spreading.
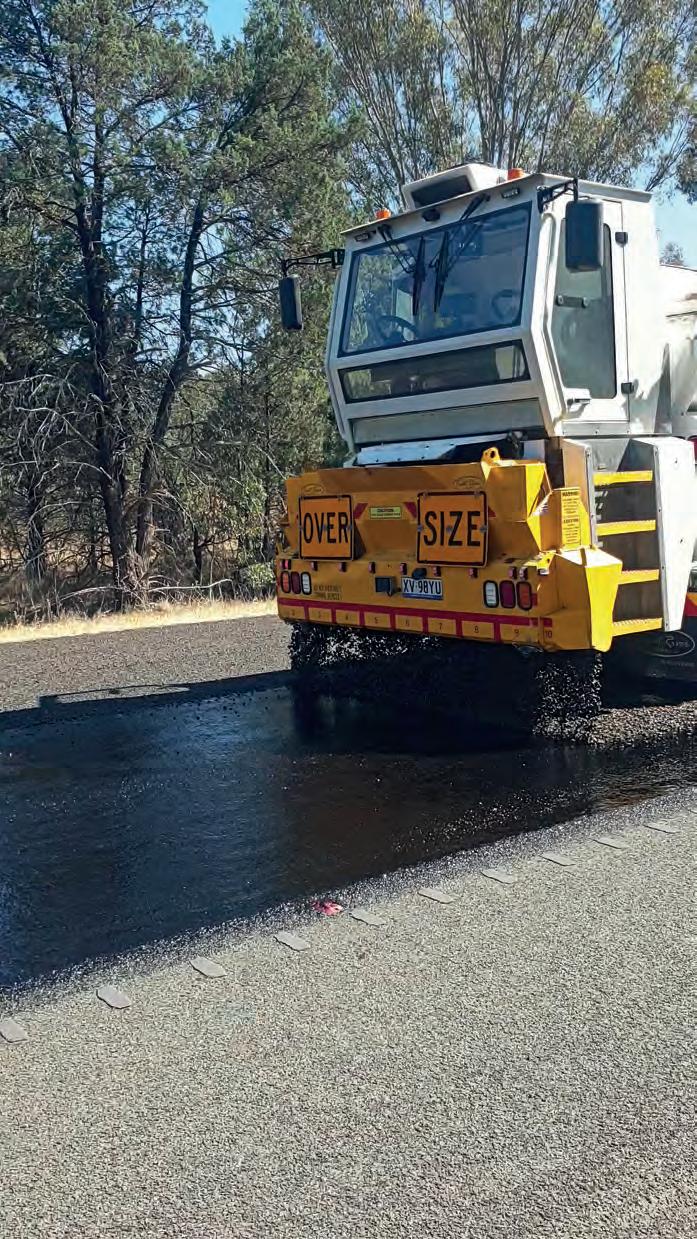
“We’ve designed the unit in such a way that if the customer decides to change their truck, upgrade or renew their prime mover, all of the functionality can easily be fitted to another unit,” Hardiman says.
“We expect to get 10, 15 even potentially 20 years out of our spreaders, which in itself is a great saving.”
This longevity is also backed up by the Road Ant’s “bang for buck”, with flexibility within the design that enables the machine to be used 365 days a year.
“Our units are designed to do more than just spread aggregate. Even in the colder times of the year, the Road Ant can still be used for transporting other products. It can also be used for asphalt supply, dressing road shoulders or bulk material transportation,” Hardiman says.
“We were very conscious of the limitations that could come with having a purposebuilt machine that can only carry out one process. It was always our intention to try and make the unit as versatile as we could. That’s a concept that’s been refined over time, now it performs better than we hoped for.”
This year marks a big one for Quality Fabrication & Engineering and the Road Ant, with on-going sales and a future pipeline which looks promising. Hardiman says that no matter what the future has in store, the Road Ant is already viewed internally and externally as a success.
“We’re pleased that the “forward-moving” concept is getting wide acceptance, not only for its safety and sustainability features, but also for its ability to help drivers and operators reduce the inherent stress of their occupations,” Hardiman says.
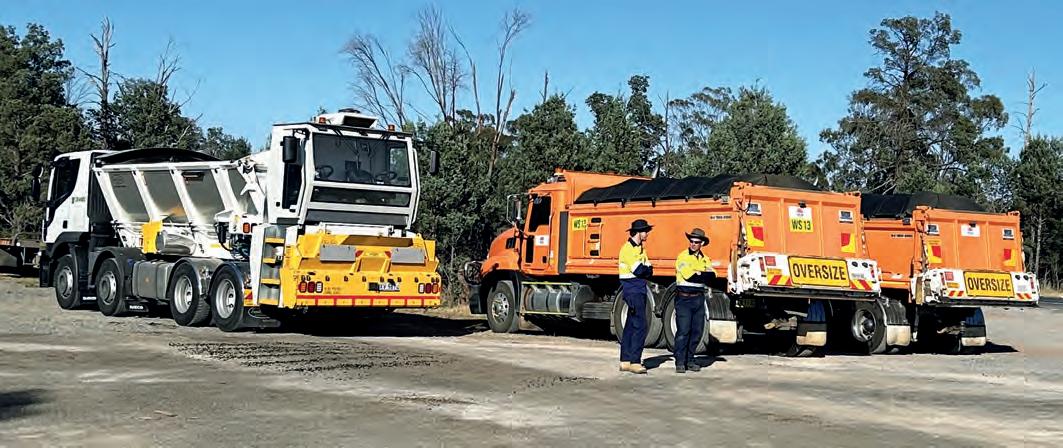
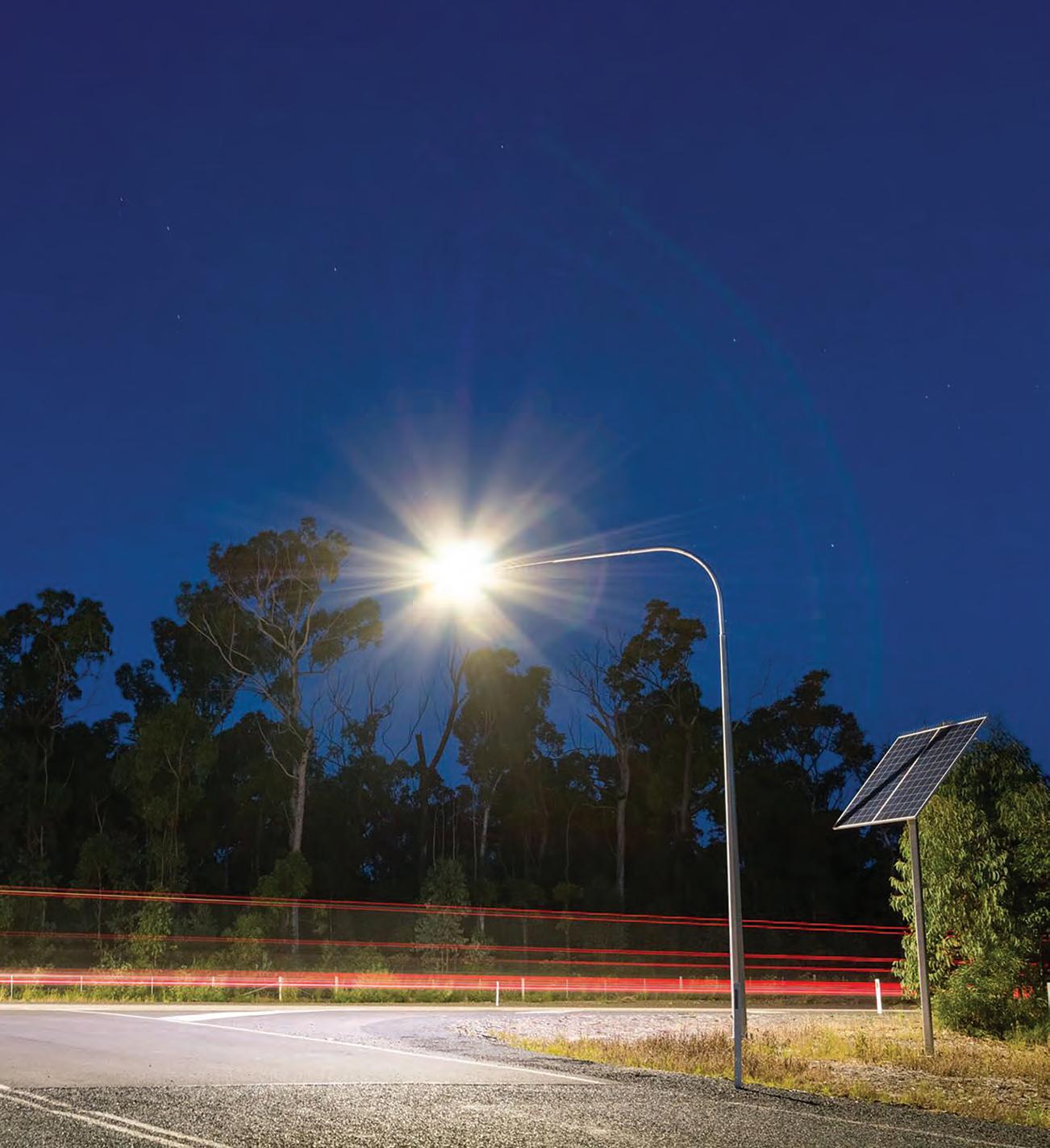
INDUSTRIAL GRADE SOLAR LIGHTING
Australia’s most trusted solar lighting for roads, public spaces and infrastructure projects
Roads and Infrastructure projects can’t afford to risk unreliable lighting. Have confidence your lighting won’t let you down. Get
Designed and developed in Australia for Australia’s harsh conditions and worst-case weather
100% compliant with Australian and New Zealand lighting and safety standards
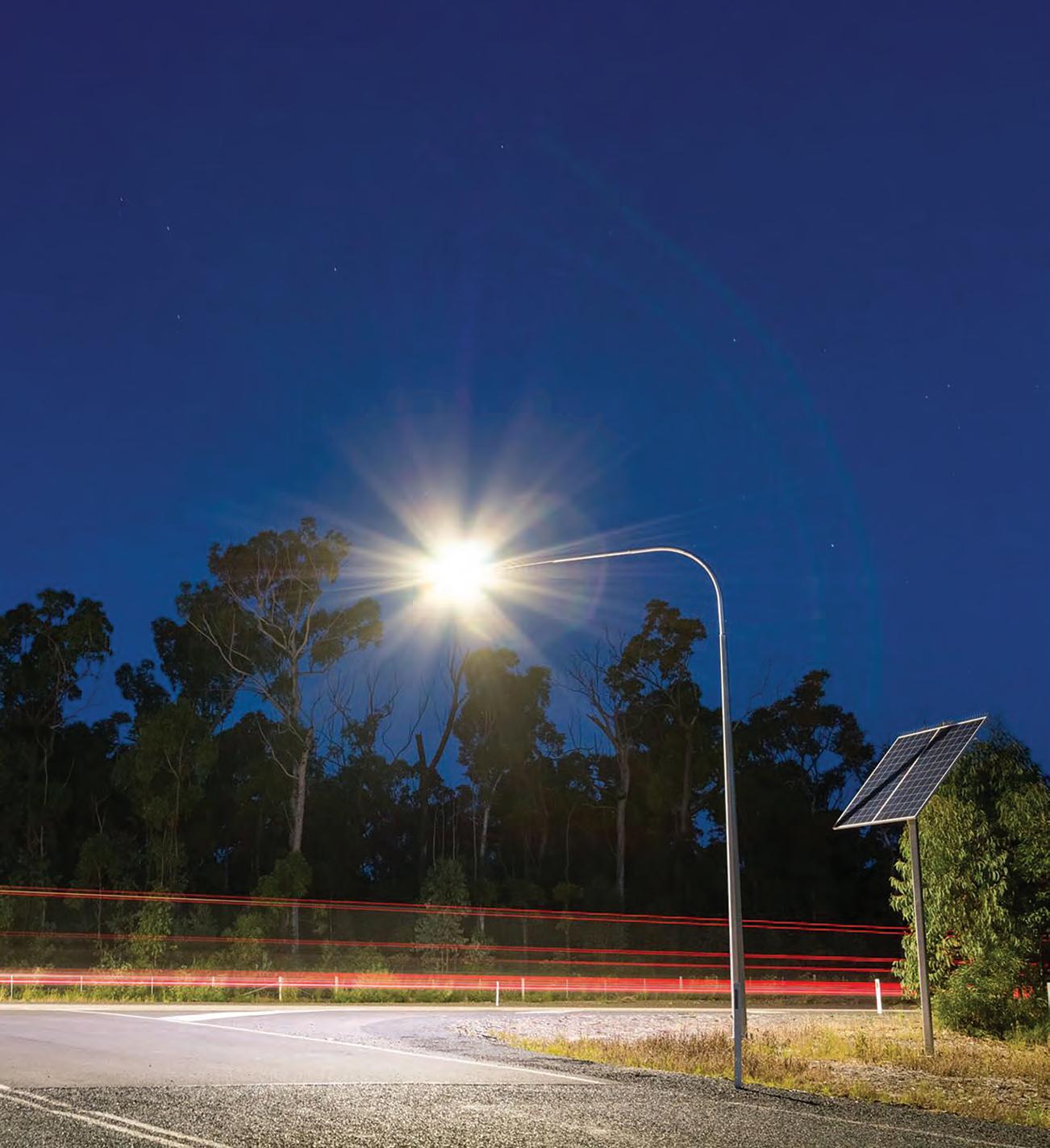
Highly reliable all-night light, even when the sun isn’t shining
Save with no upfront trenching or cabling, no ongoing electricity costs and minimal maintenance
20+ year design life, 10-year warranties and additional performance guarantees
No noise, fumes, glare or ongoing diesel usage
Safeguard your installation with Garland’s Rodent-Proof Fibre Optic Cable.
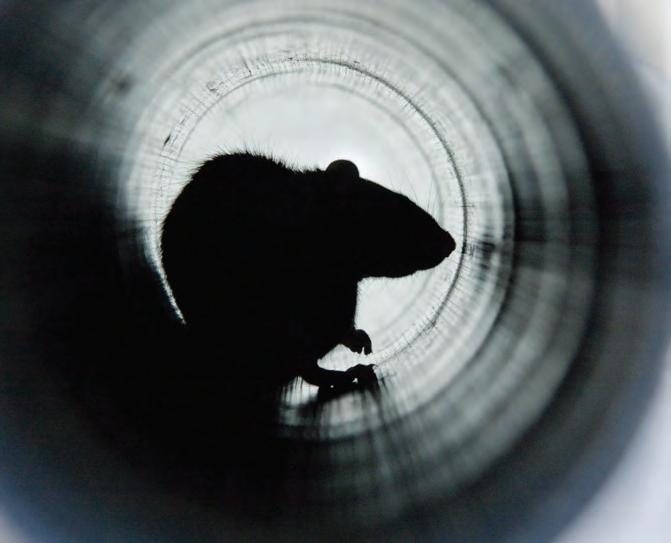
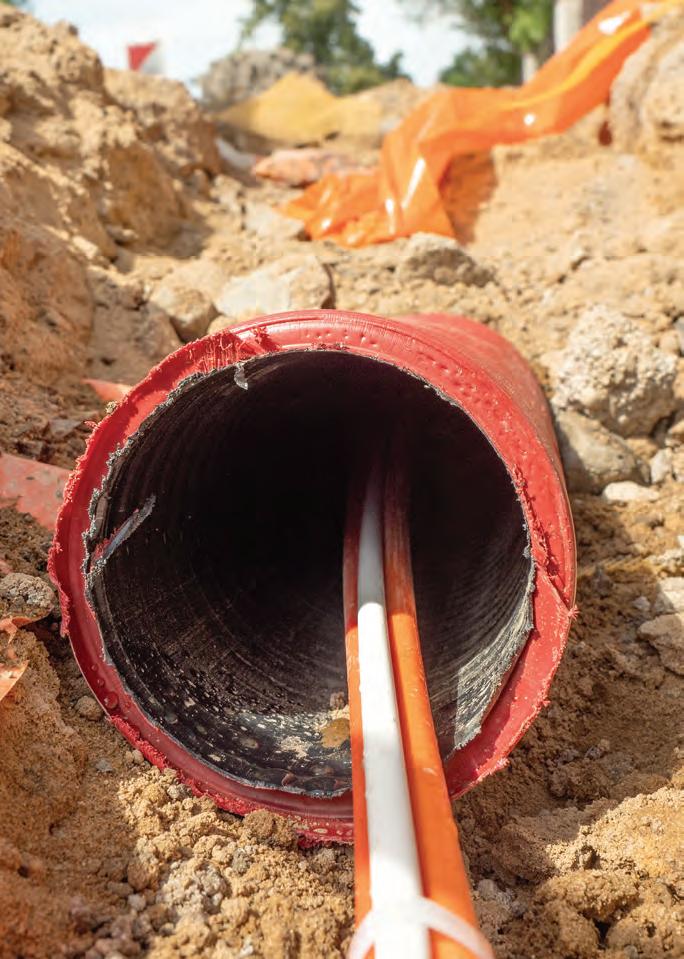
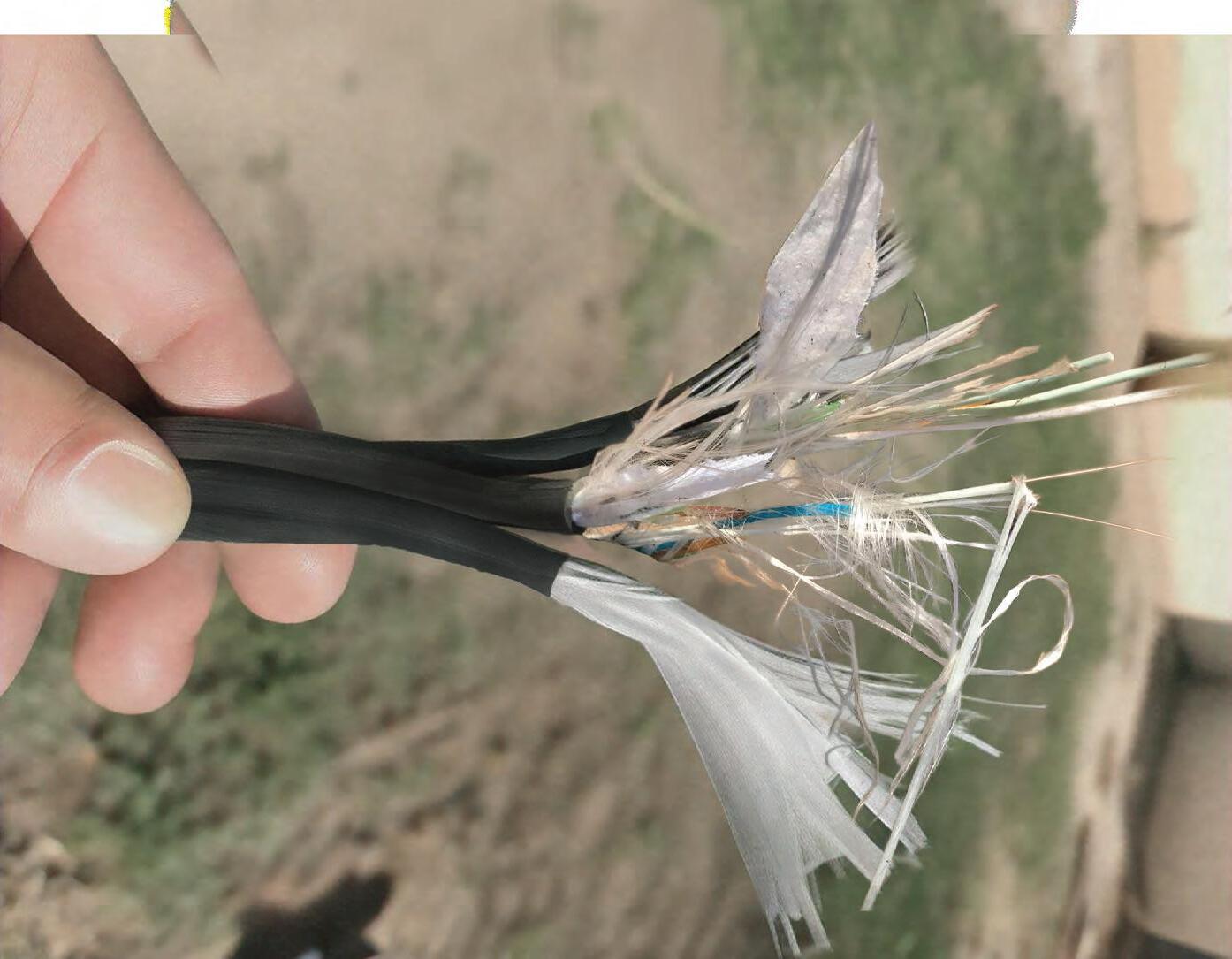
Rodent attack is a major problem for optical fibre cables installed underground in unsealed or non-metallic conduits. Garland’s GLT-AZB Series Loose Tube cable has non-metallic design, making it suitable for use near power cables and in areas of high lightning strike rates.
Designed to b e environmentally friendly w ithout the u se of da ngerous c hemical ag ents, this product range offers the protection needed for your fibre optic installation.
o For use in ducts or direct burial applications
o Available from fibre counts of 6 up to 144
o Complies with TMR Queensland requirement
Garland has been manufacturing quality cables for over 45 years. We’re owned, made and distributed by Madison Express, so get in touch with our friendly team for bespoke solutions and quality cable, made to last.
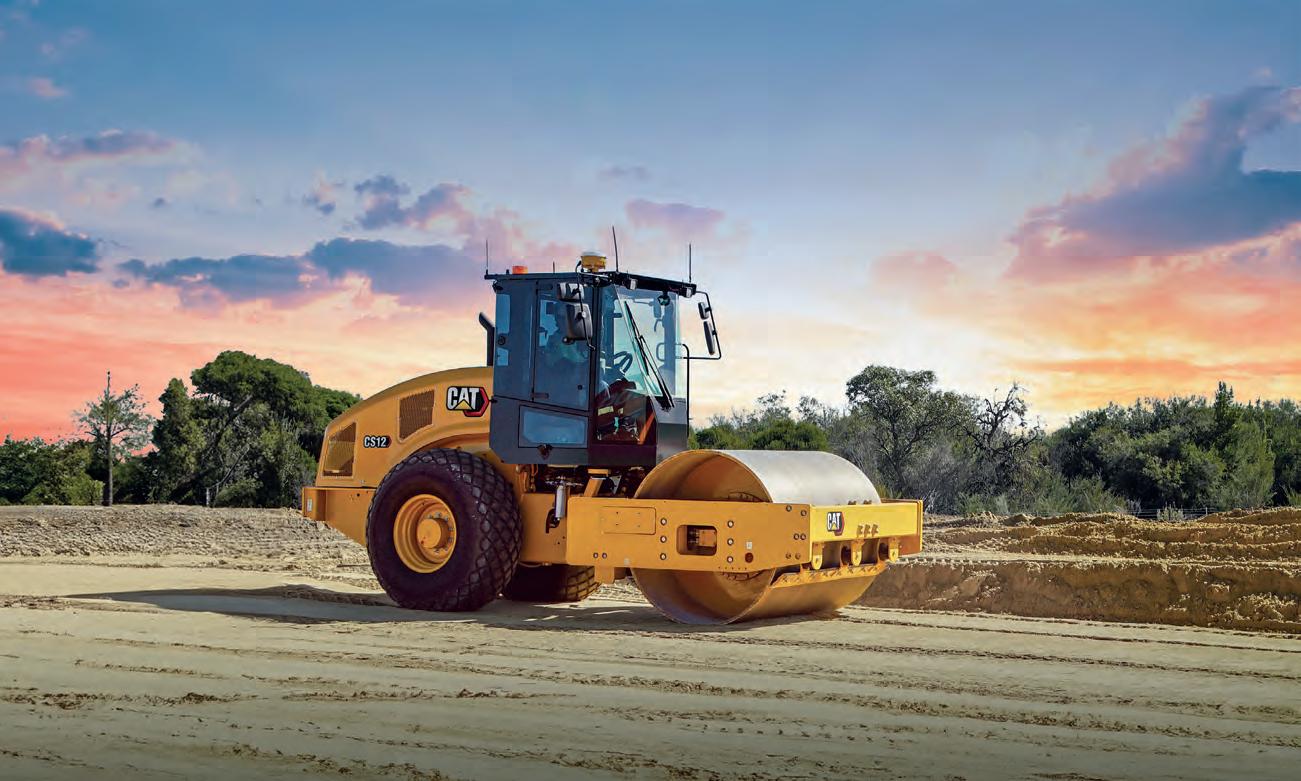
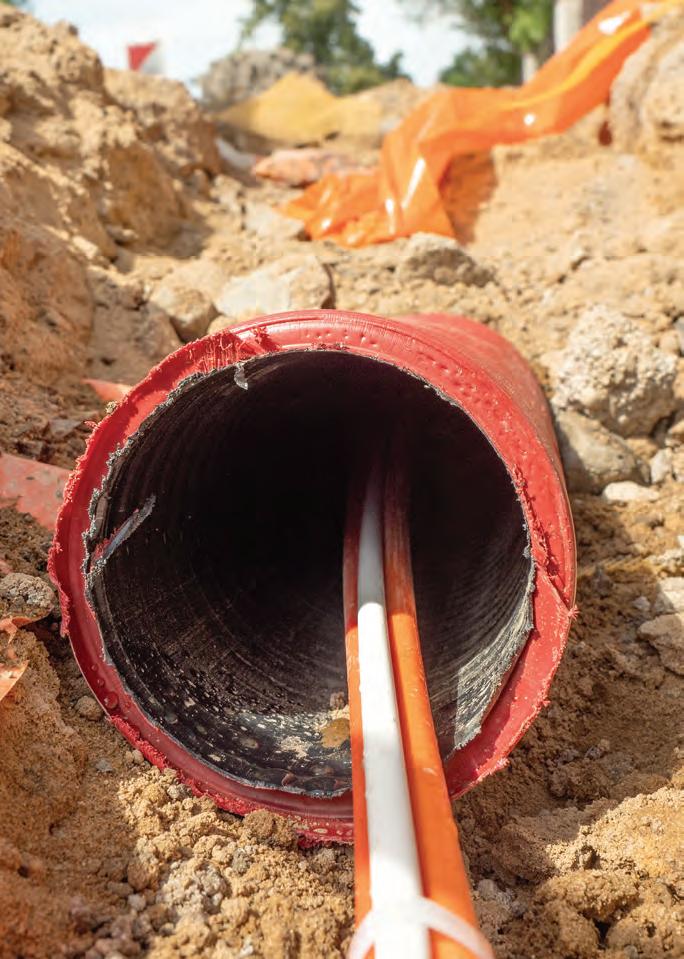
SAME QUALITY NEW NAMES,
CATERPILLAR IS RENAMING SEVERAL MACHINES IN ITS VIBRATORY SOIL COMPACTOR RANGE AS PART OF A RENEWED APPROACH TO ITS NOMENCLATURE.
DEAN
ALLEY, TERRITORY MANAGER FOR ANZ EXPLAINS WHAT THESE CHANGES ARE AND HOW THEY’LL BENEFIT THE INDUSTRY.
New names, same great performance. That’s Caterpillar’s mantra as it welcomes new changes for its vibratory soil compactors.
Following both external and internal feedback, Caterpillar has introduced a number of model name changes to its existing range, hoping to better align soil compactor model names with weight classes.
As Dean Alley, Territory Manager for ANZ explains, it’s a change that’s already been widely accepted and welcomed across the board.
“It’s a more common-sense approach to machinery classification, easing the confusion for our customers, as well as our dealers and representatives. It just means the names are more meaningful, especially to people who might be new to the market,” he says.
“We have kept the same letters in our nomenclature with the CP still standing for Compactor Pad Foot and CS referring to our Compactor Smooth Drum.
“It’s just a simple change in numbers, but one thing that hasn’t changed is our great machines. Each unit still has the
great features and benefits that CAT is known for.”
The nomenclature change aims to make it easier for customers and contractors to select the machine that best suits their project or application needs.
An example of these changes can be seen from CAT’s smaller soil compactor range such as the CP44B and CS44B – which has now changed to the CP7 and CS7 respectively – better reflecting the seven tonne models, an ideal machine for tackling smaller jobs with maximum productivity.
For the markets most common size, CAT’s CS12 (formally the CS56B) is a popular model for medium weight applications, providing greater versatility and consistency than its predecessors.
The CS12 (formally the CS56B) is among CAT’s flagship units within the vibratory soil compactor range and is the premium version of the CS13GC (previously referred to as the CS12GC). As Alley explains, the performance difference between the two models is all about the machines climb ability.
“The premium unit has a dual pump, as opposed to the GC, which just has a single
pump, meaning it can climb very steep inclines. That’s particularly important if you’re working in forestry, as well as construction applications that require steeper incline climbs larger than 30 per cent grade,” he says.
“The CS12 is a game changer and one of the few machines in the market that can work in those types of projects at this size. It’s a monster of a machine when it comes to compaction and climb-ability.
“It’s got a great extended service life, with its sealed for life, maintenance free centre hitch and an outstanding and reliable vibratory pod system, letting it give great reliability out in the field. There’s nothing that comes close in the 12-tonne space.”
Alley says identifying the most suitable machine is the first and most important step.
“We’ve got a soil compactor range that’s perfect for the different types of road projects that you’d see in Australia,” Alley says. “Now with the name changes, identifying what machine you need for the job at hand will be much easier.”
For those who need, or prefer, an even larger solution, CAT’s large vibratory soil
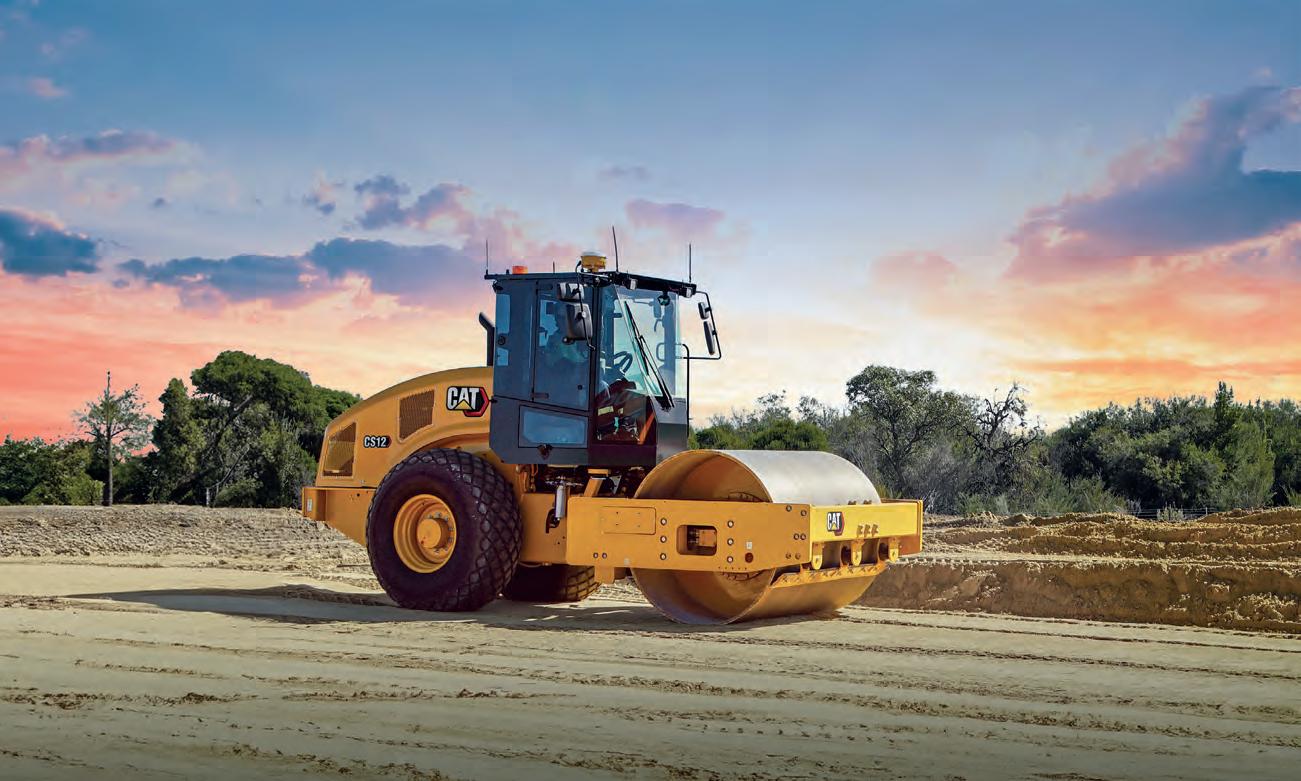
“THROUGH OUR CONNECT OFFERING, WE’RE NOW ALSO ABLE TO SEND OUR COMPACTION DATA THROUGH THE CLOUD VIA OUR VISIONLINK PORTAL INTO THE PROJECT MANAGER’S OFFICE.”
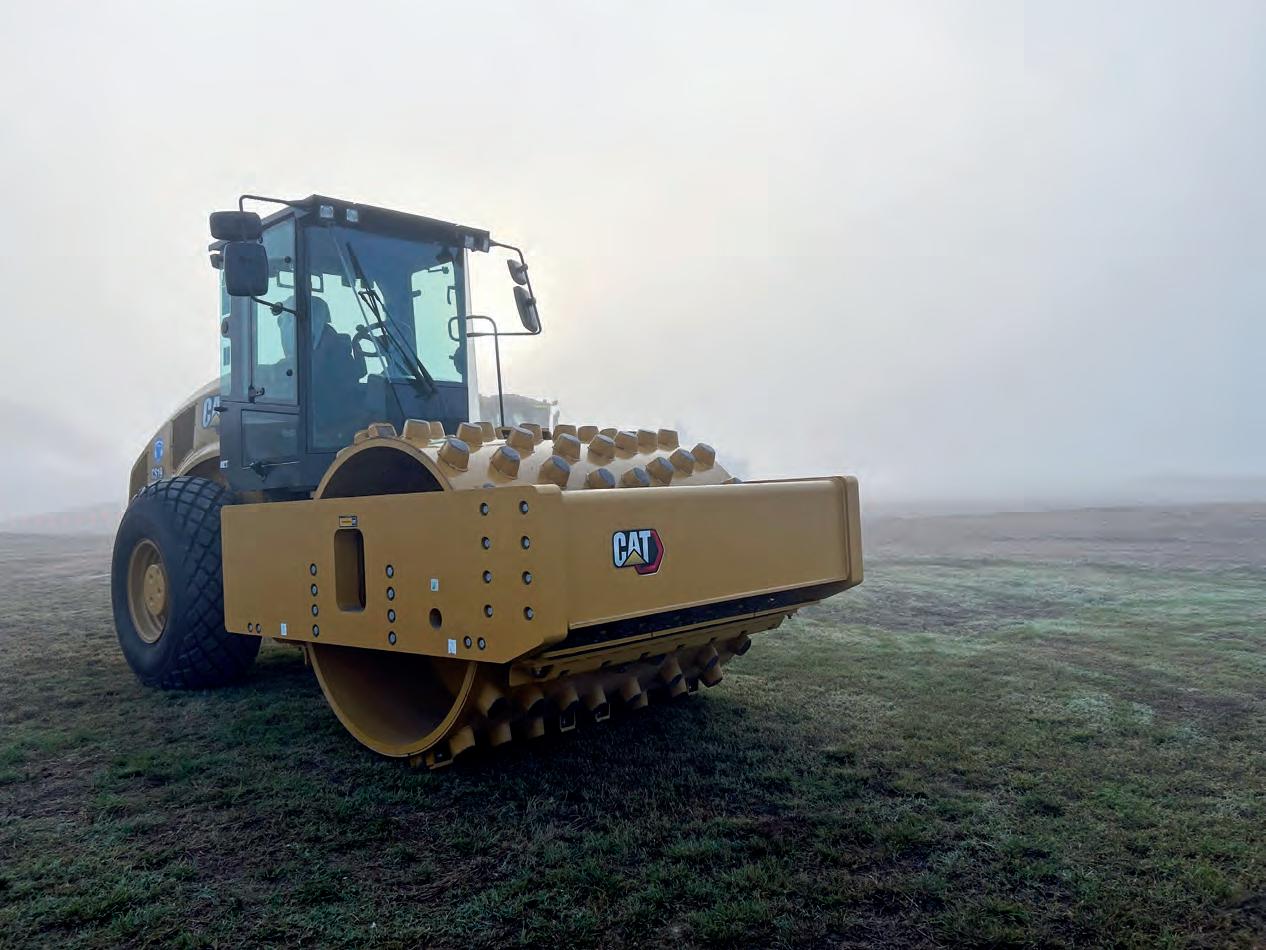
compactors, ranging from 15 to 20 tonnes provide more horsepower and ability to complete tough compaction jobs with fewer passes.
The CP14, CS14, CP16, CS16, CP17, CS19 and CS20 (formally the CP68, CS68, CP74B, CS74B, CP76B, CS78B and CS79B) are ideal for thicker material lifts.
CAT’s impressive intelligent compaction, provided by its suite of best-in-class technology, focuses on improving the efficiency of each pass, while also providing greater accuracy for soil stiffness.
“With CAT technology, we have three different levels. Our first level of intelligent compaction is MDP (Machine Drive Power), which is our patented soil stiffness measuring system. We’re the only manufacturer in the market that has this type of system that uses rolling resistance as a measure. This enables the operator to know when they’ve reached maximum soil stiffness, or more importantly when it hasn’t been achieved and requires investigations,” Alley says.
CAT’s second level, compaction mapping, helps to optimise the accuracy and productivity of each pass for the operator by using the machine’s GNSS and RTK position location, for an accuracy of two centimetres.
“The mapping system can either be used as an MDP or as a pass count feature, depending on material type and site requirements,” Alley says. “We’re
starting to see more and more projects have this requirement across Australia, benefitting both the project itself as well as the contractor.”
The third level enables both machine-tomachine communication and also sends compaction data to the cloud for near live monitoring through VisionLink portal.
Why is this important? Machine-tomachine communication allows operators to see the progress of other machines working on the same project.
This ensures the lifts are not over compacted by another machine going over the same ground as well as saving fuel.
“Through our connect offering, we’re now also able to send our compaction data through the cloud via our VisionLink portal into the project manager’s office. This enables project stakeholders to be kept updated on compaction progress, as well as when/if compaction requirements haven’t been reached,” Alley says.
Intelligent compaction has been proven to maximise compaction efficiency, reduce fuel
CAT’s vibratory soil compactor range comes with a variety of transformative technologies to aid efficiency and output.
burn, vastly increase accuracy and ensures quality on each pass.
“Over compaction is just as bad as under compaction, because you don’t want to smash your aggregate, lose your grade and then the capacity to compact,” Alley says.
“These technologies are for the operator, the site supervisors and the engineers to enable them to report and visualise the quality and uniformity of the work across the entire site. This data is then collected, analysed and used for documentation, or to simply uncover hidden in-efficiencies.”
With a technology and vibratory soil compactor range that continues to grow, as well as a renewed focus on nomenclature, Alley says CAT is well placed to cater for the changing needs of the industry.
“It’s going to make a big difference not only for us, but also all our current and prospective customers,” he says.
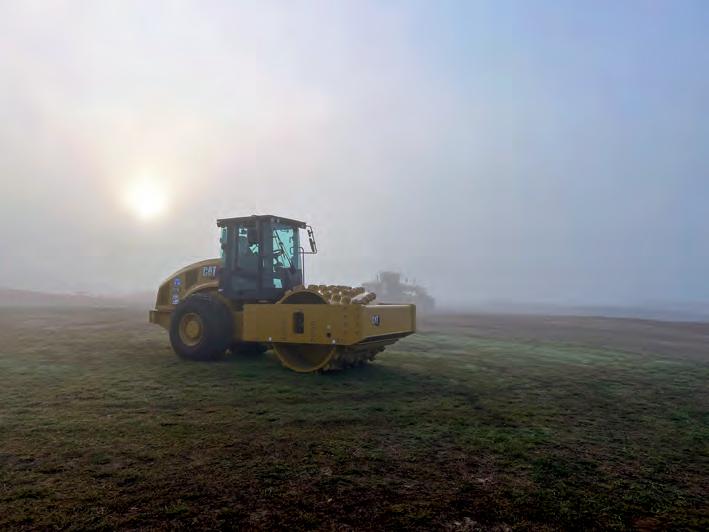
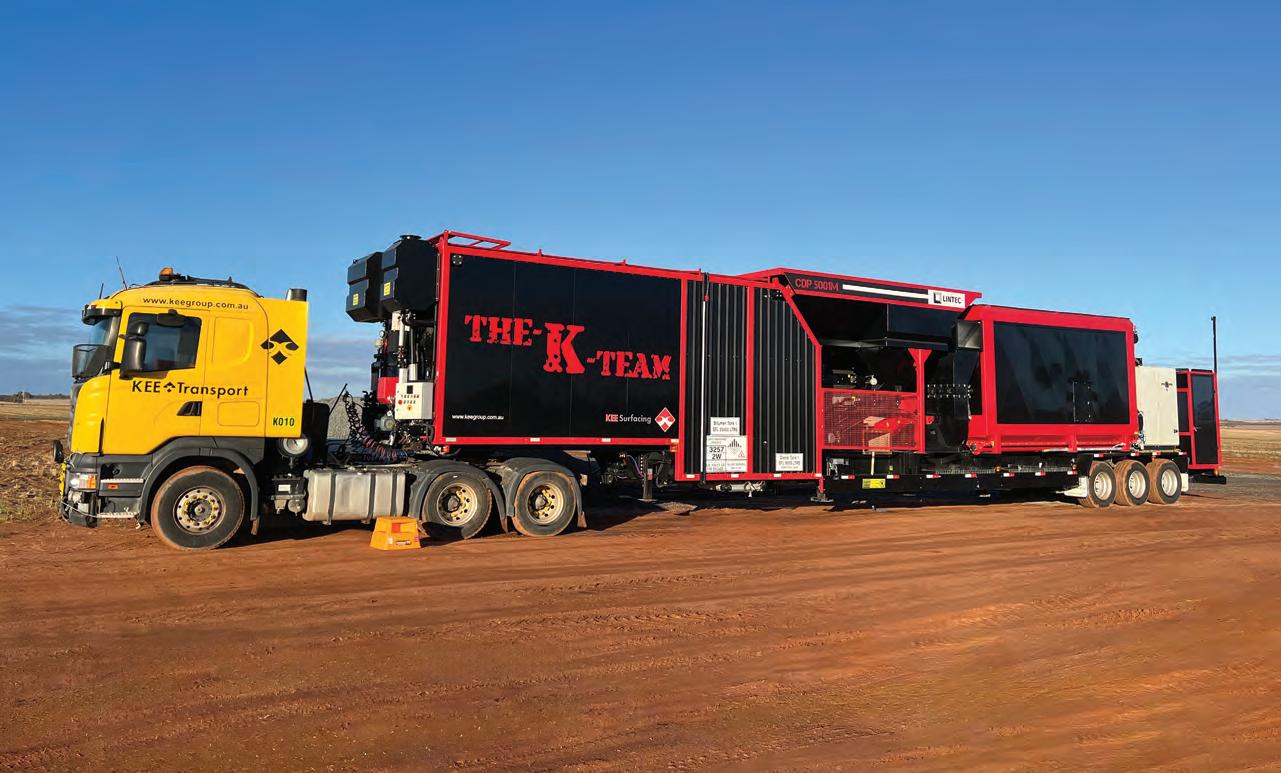
“Nothing’s changed from our perspective except for the model names.
“We’re still really well placed in the Australian market.”
The nomenclature changes aim to make things simpler for customers and Caterpillar representatives.
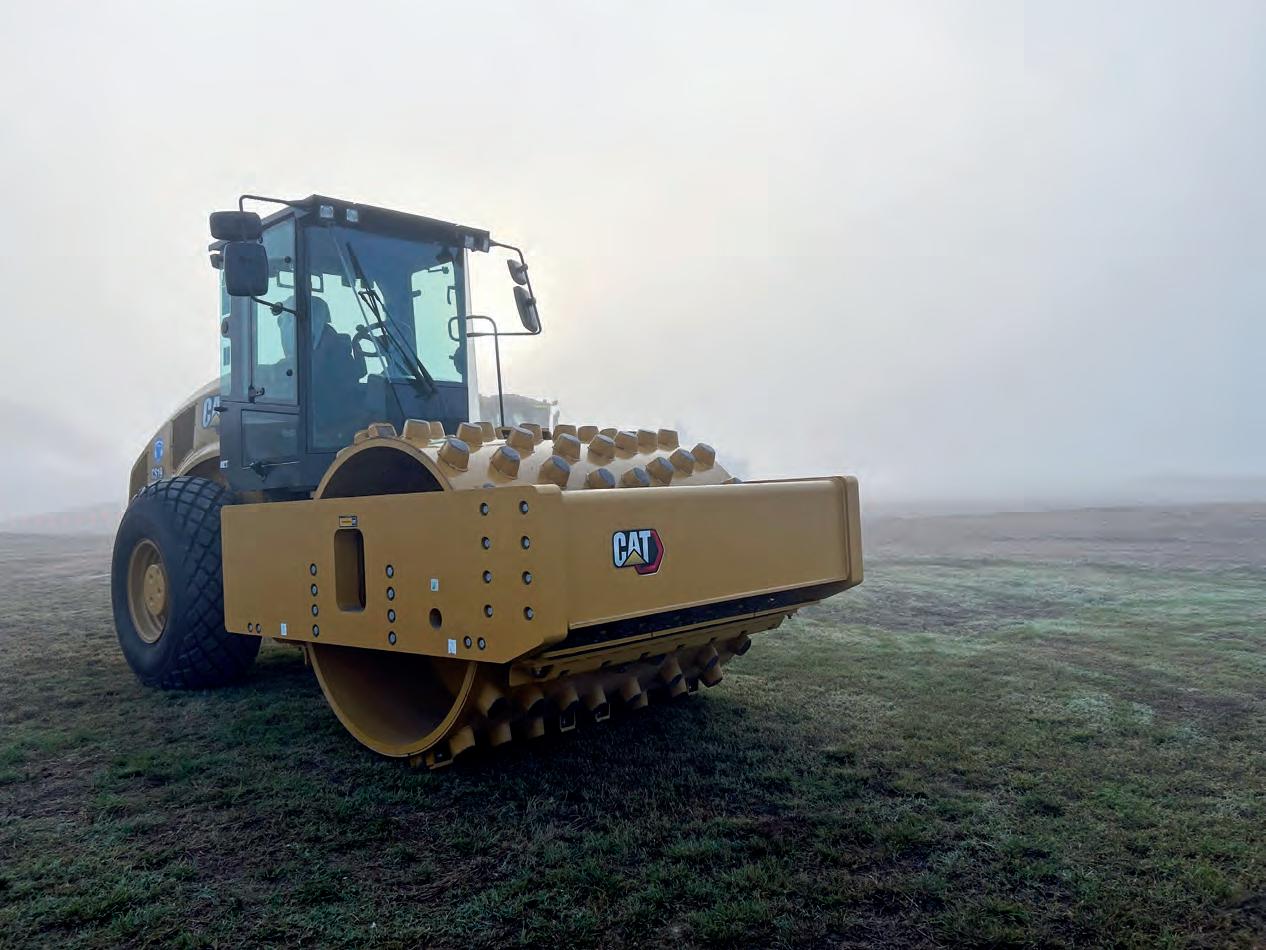
Mobility Redefined.
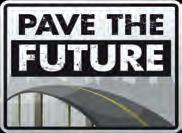
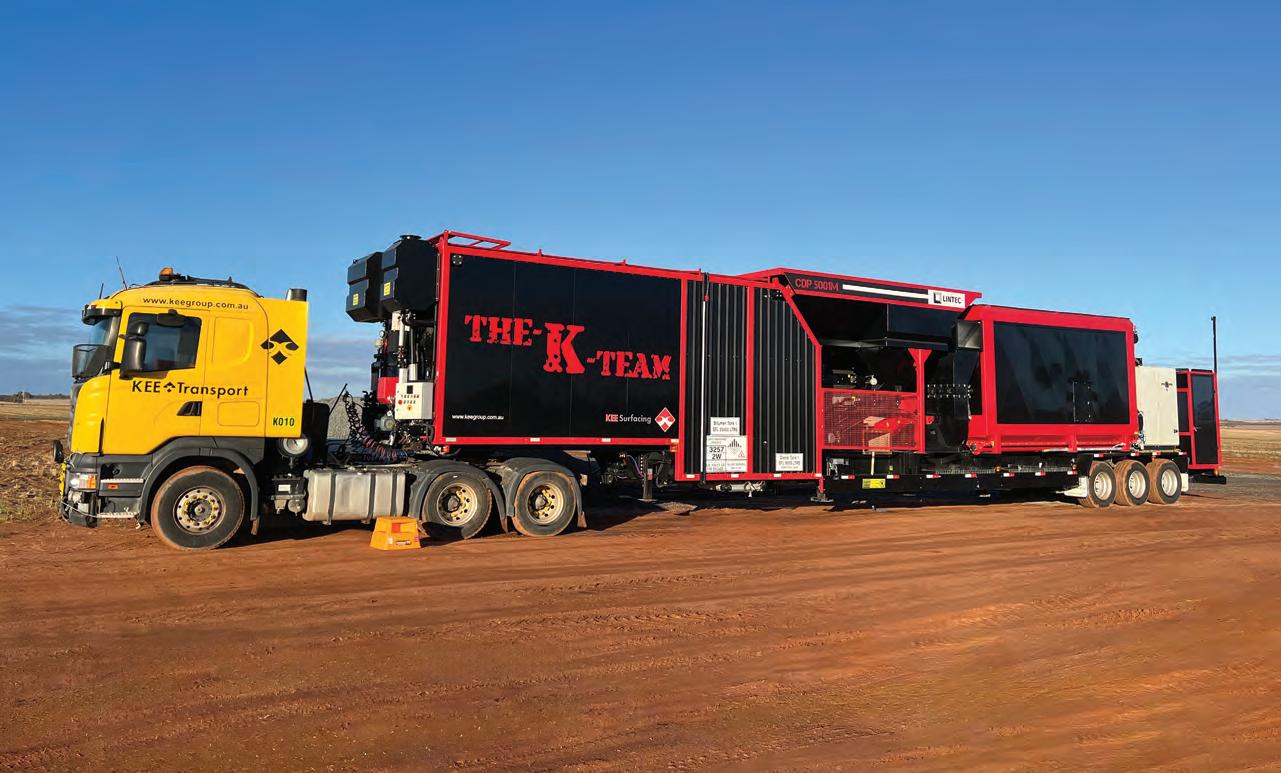
Unlock new levels of efficiency and mobility !
Our cutting-edge Lintec CDP5001M Mobile Continuous Asphalt Mixing Plant has been engineered for superior performance. The CDP asphalt mixing plant delivers top-quality asphalt production quickly and directly at your job site. Say goodbye to transportation delays and hello to seamless, on-the-go operations. Elevate your projects with our innovative solutions and experience true mobility redefined. — Your road to success starts here.
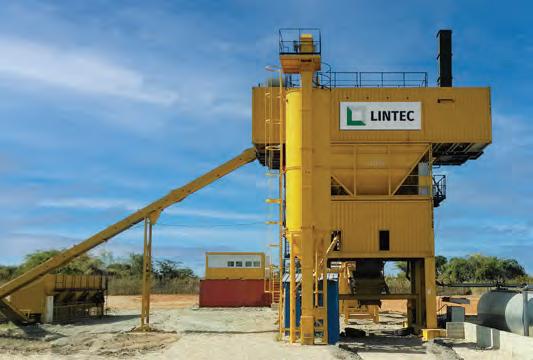
Seamless Mobility, Effortless Installation.
The Lintec CSD2500B Containerised Asphalt Mixing Plant features modular construction, fully enclosed in 100% ISO certified sea containers. It offers lower energy consumption per ton and reduced maintenance costs. The design allows for easy transportation and rapid installation, making it ideal for projects of all sizes.
Aftersales Services Available!
Our dedicated after-sales team located nationwide offers industryleading service for your asphalt mixing and concrete batching plants, ensuring maximum efficiency and reliability, and minimising downtime.
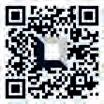
www.lintec-linnhoff.cominfo@lintec-linnhoff.com
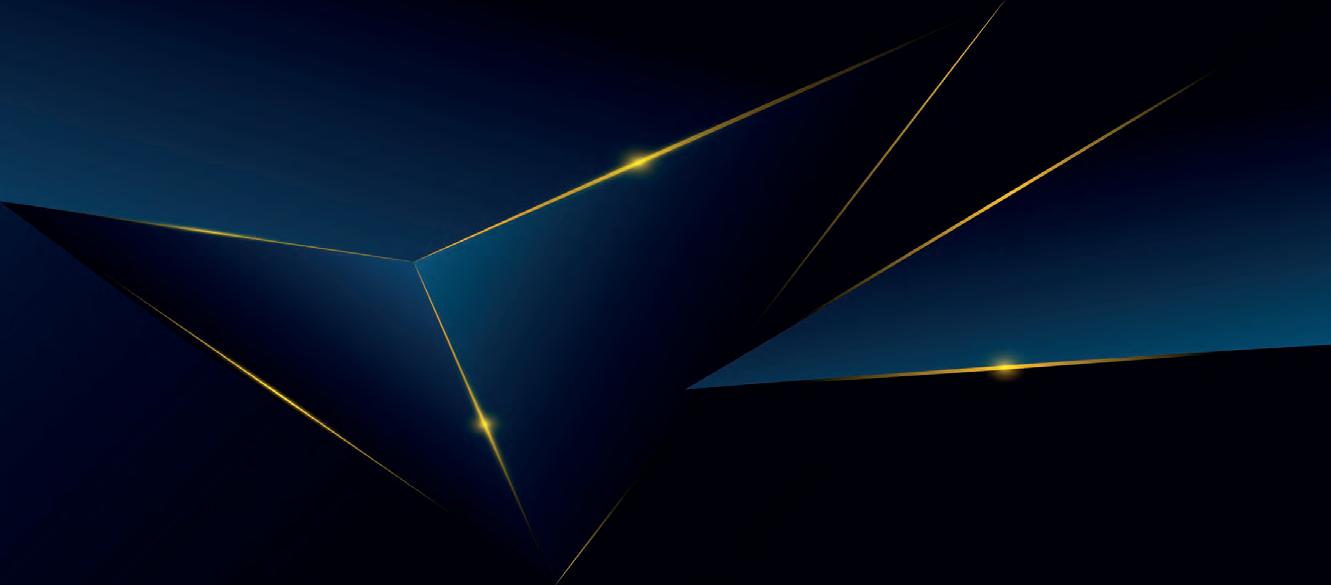

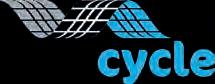
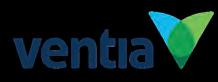
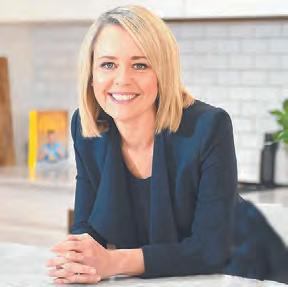
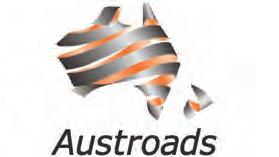

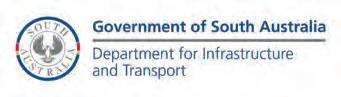
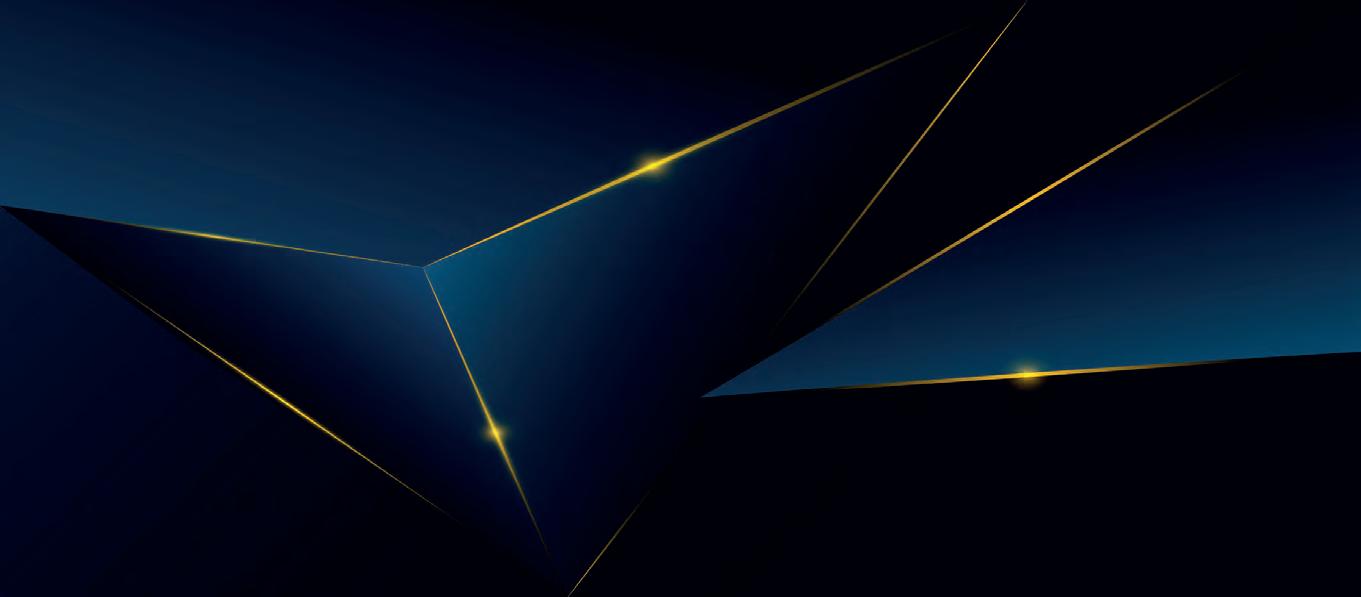
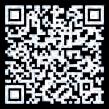
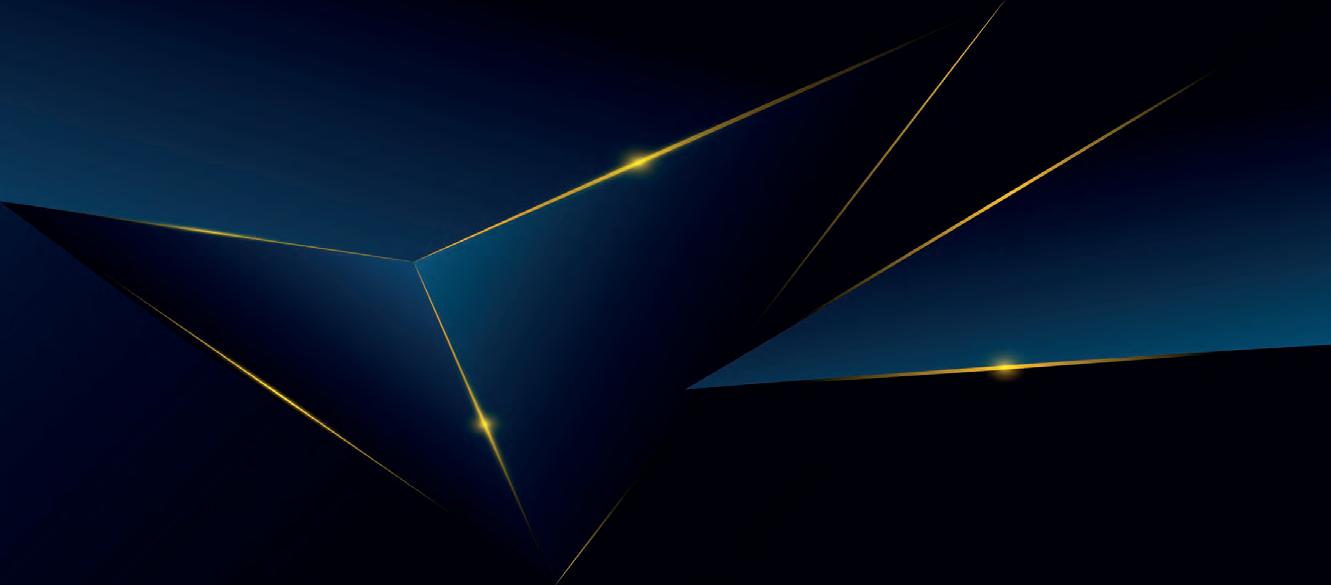
CLEVER CONNECTIONS
MADISON EXPRESS CONTINUES TO GROW AND IMPROVE ITS IMPRESSIVE COLLECTION OF GARLAND BRANDED CABLE AND CONNECTIVITY PRODUCTS, DESIGNED TO BOTH OUTLIVE AND PREVENT IMPACTS FROM LOCAL FAUNA.
When considering or observing infrastructure development, it’s easy to look up to view construction in progress and admire the capabilities of both people and equipment.
It goes without saying that infrastructure development is a complicated prospect, filled with many moving parts. But if one was to consider the surface below their feet, they’d discover the importance of what can be an under-appreciated component of transport and infrastructure development.
Fibre optical cables play an essential role in connecting vital technologies and services to routes that we use daily.
For Madison Express, connectivity through cable is as essential as it gets, which is reflected in the company’s vast offerings throughout the infrastructure sector. As National Product Manager George Karanikolaou explains.
“In the infrastructure space, you’ve got your small day-to-day projects and the larger projects, with every project in between often having completely different requirements and standards that we need to adhere to,” he says.
Karanikolaou says these varying specifications frequently occur when multinational companies implement a design that was developed overseas, incorporating international – rather than Australian –specifications and guidelines.
Regardless of the project requirements or specifications, Madison Express has a long history of catering for and tailoring its products for infrastructure projects of all sizes.
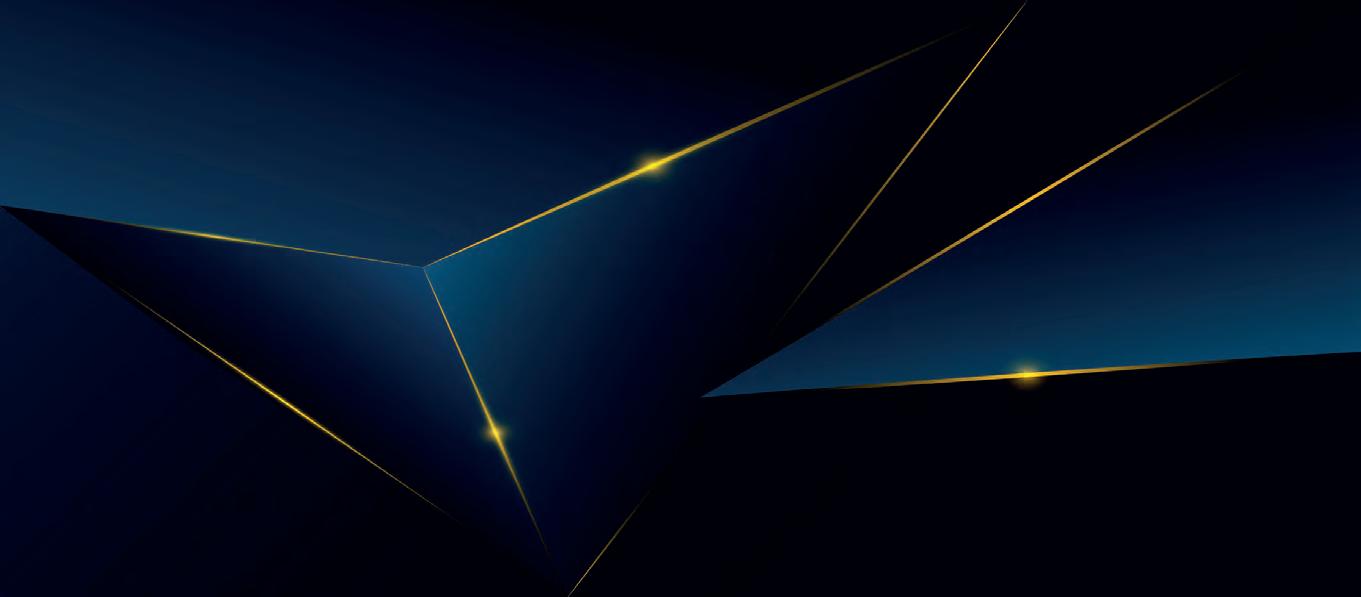
Karanikolaou says varying requirements can at times be a challenge. But with more than 40 years in cable design and manufacturing, he says each test is an opportunity to learn and expand.
“We’re great at being able to identify and communicate those conflicts and come up with a design that will be fit for purpose and satisfy the needs of the customer, those are
the things that we pride ourselves on,” he says.
“That means that our product portfolio is always expanding, because every time you go to a project, there’s something new that we’ll find or learn that we’re able to do.
“You’ve got to ask questions and then come up with a creative solution and a compromise that works for everyone. Especially on state or Federal government projects, you need to tick all of those boxes.”
Karanikolaou adds that Madison Express’ flexibility and willingness to customise its products is just one of the many reasons why large infrastructure contractors keep coming back for more.
“We can design and tune cables to make sure that compromises are minimised. The second thing is our deliveries, it’s in our name, there’s an implication that we can deliver quickly. Regardless of the case, we’re very open with our customers on every step of the supply process, from manufacture, to shipping and delivery at the customers location” he says.
“We also don’t have a lot of add on charges considering the amount of customisation that’s allowed throughout the process. Other organisations will have additional charges for doing this or that. That’s not our way, we have a set price and present that upfront.”
PEST PROOF
A big benefit of Madison Express’ product range is its ability to design fibre cable solutions that can withstand both flora and fauna, as well as mother nature.
From water protective designs to specially designed fire alarm cables, Madison Express already has a variety of products that have been developed as a result of market feedback and the demands of niche applications.
One of the company’s latest innovations similarly was derived from market feedback, which reflected the lack of suitable
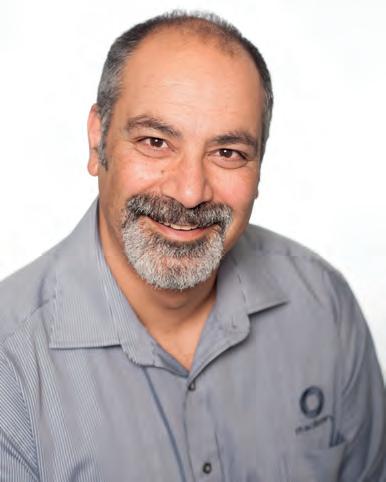
options made to cope with pests. As Karanikolaou explains.
“There’s strong rodent populations throughout the country,” he says. “If you’re putting fibre anywhere that’s accessible by rodents, there’s a high enough risk that it’s going to be attacked. “
“Bridges and roads these days have a lot of cabling, connecting speed cameras, monitoring systems, sensors and more back to control rooms. A lot of devices that transport authorities are using need cabling for it to exist and with a lot of roadways there’s typically large conduits that can inadvertently provide access for rodents to fibre cabling.”
Karanikolaou says tunnels becoming a primary solution for improving the efficiency and safety of transport solutions will also heighten the need for systems that can withstand rodent attacks.
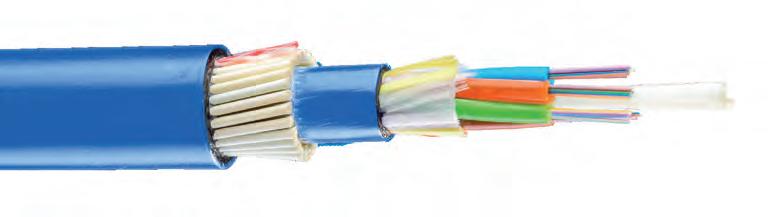
“Tunnels are dark, protected and damp areas and perfect for rodent populations, which is why we’re seeing more and more demand for this type of product in tunnel applications,” he says.
Regardless of the application or environment, rodent proof fibre cabling will likely be a primary option for infrastructure development. So much so, that Queensland Transport and Main Roads established a standard for rodent proof fibre, which Madison Express now satisfies.
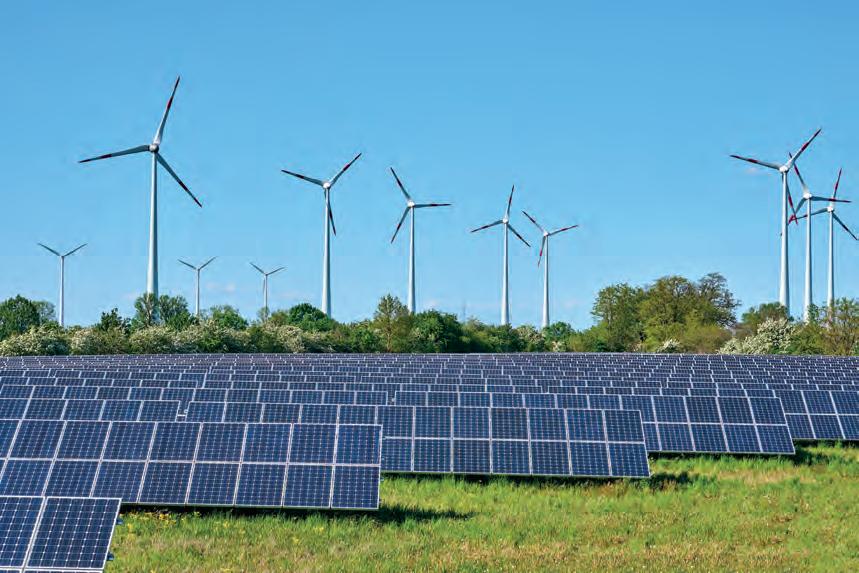
So, what exactly is Madison Express’ solution?
“There’s a number of different options. There’s steel tape or steel wires used as armouring around the cable. That’s not so popular in Australia, as metallic armoured communications cables need to be segregated from power cables and a transport authority isn’t going to dig two separate conduits for ‘comms’ and power,” Karanikolaou says.
“Our approach uses glass reinforced plastic as an armour around the fibre cable, which we believe is the best and most appropriate alternative.”
Madison Express’ optical fibre cable includes
both termite and rodent barriers as well as two High Density Polythene jackets. Placing the termite barrier under the rodent barrier ensures that rodent attacks don’t decrease the cables resistance to termites.
On top of its performance characteristics, Madison Express’ solution is also a considered choice when it comes to potential long-term impacts on the environment and local flora and fauna.
“There’s other solutions that use a chemical additive to deter rodents from accessing fibre, but we’ve taken a stand for a number of years and it’s our view that this approach can have negative effects on both the environment, as
well as safety,” Karanikolaou says.
“There’s often issues with keeping those types of compounds inside the material, as they can start to leach out into the environment. It might be preventing rodents from attacking your fibre, but the long-term effects on local fauna wildlife is something that needs to be considered.”
Karanikolaou adds that chemical additives can also pose serious risks if exposed to technicians, who could suffer dermatological impacts .
By preferring a glass reinforced plastic armouring rather than other options, Madison Express’ solution can minimise rodent damage on fibre cables while also having minimal impacts on the local environment and community.
“More and more people are starting to recognise our knowledge, skill and ability to deliver suitable solutions in this space,” Karanikolaou says. “The possibility of further expanding and improving our current portfolio is a really exciting prospect and one that will only help us to provide more suitable products to the market.”


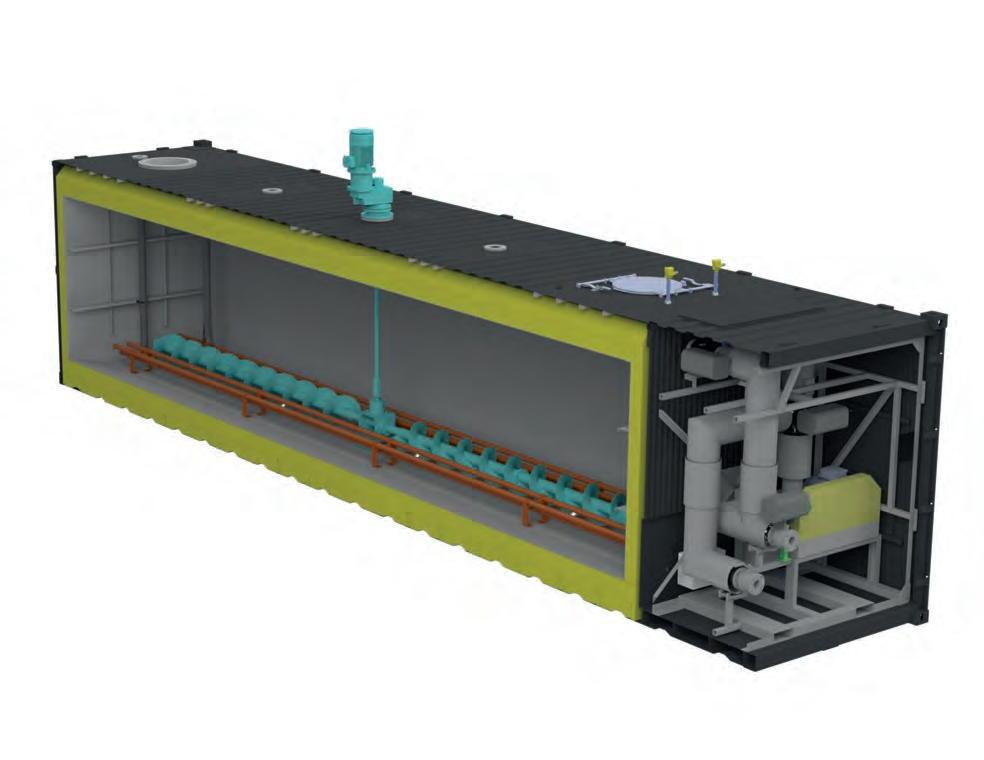
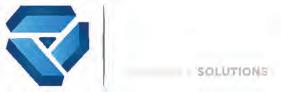
NATIONAL ROADS & TRAFFIC EXPO:
BUILDING ROADS FOR A CONNECTED FUTURE
EVER WANTED TO CONNECT AND LEARN MORE ABOUT THE INFRASTRUCTURE SECTOR? THE 2024 NATIONAL ROADS & TRAFFIC EXPO IS PROVIDING AN OPPORTUNITY FOR JUST THAT. WE FIND OUT WHAT’S IN STORE FOR ATTENDEES AND EXHIBITORS AT ONE OF THE SECTOR’S MOST ESTABLISHED AND RENOWNED CONFERENCES.
Taking place on 30 and 31 October at the Melbourne Convention & Exhibition Centre, the National Roads & Traffic Expo is Australia’s largest and only event dedicated to the entire roads and traffic management industry, covering everything from road design and procurement to construction, maintenance, and operations.
Attendees and exhibitors at the upcoming National Roads & Traffic Expo will have an unparalleled opportunity – across two days – to connect with key decision-makers, industry innovators and policy leaders who are shaping the future of the $40-50 billion road infrastructure sector.
The expo brings together professionals from across the supply chain, from top-tier executives to on-site engineers, creating the ultimate platform for business, networking, and knowledge sharing.
It also serves as a hub for federal and state transport agencies, local governments, and industry partners to collaborate and build stronger connections within Australia’s transport infrastructure network.
SPEAKERS AND CONTENT
Attendees will have the opportunity to hear from industry leaders and experts across seven conference tracks, covering a diverse range of critical topics including traffic management, road safety, transport planning, networks, parking, sustainability, and material innovation.
Key areas such as road construction, engineering, maintenance, procurement, supply chain, people culture, and workplace dynamics will also be explored.
The sessions will offer insights into the latest trends, challenges, and innovations, including strategies for enhancing road user behaviour and traffic controller safety, the integration of AI-powered technologies
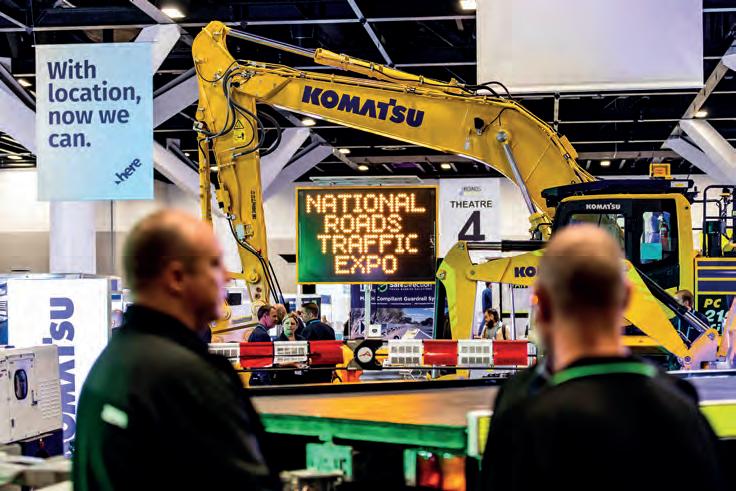
for next-generation transportation, and the creation of sustainable and accessible transport networks.
Additionally, digital engineering will be discussed as a tool to improve efficiency, safety, and cost-effectiveness in road infrastructure, while fostering innovation in road network management.
NEW HORIZONS
Speaking exclusively with Roads & Infrastructure Magazine, Abby Gale Zipagan, Marketing Manager for the event says this year’s expo is shaping up to be the biggest and best yet.
“For 2024, we’ve made several exciting updates to elevate the National Roads & Traffic Expo,” Zipagan says. “One of the most significant changes is relocating the event to Melbourne, a vibrant hub for innovation, infrastructure, and connectivity. This new venue will better accommodate our expanding audience and exhibitor base, making it an ideal setting for this year’s event.
“We’re also broadening the scope of the exhibition, bringing in additional sectors like smart transportation, road safety, advanced materials, and sustainability solutions.”
Another key focus will be on digital transformation, with dedicated sessions exploring the role of AI (Artificial Intelligence) data analytics, and IoT (Internet of Things) in modernising road and traffic management.
“To further enhance engagement, we’re introducing new networking opportunities, including tailored roundtables and oneon-one meetings to help foster stronger industry relationships,” Zipagan says.
“In addition to these features, we’re welcoming an exciting line-up of new speakers from both government and industry, who will share their perspectives on the future of roads and traffic across Australia.”
Want to find out more? Visit the National Roads & Traffic Expo 2024 website and register for FREE now: https://www.terrapinn.com/roads/pcrai
ONE STOP-SHOP FOR TRENCHLESS TECHNOLOGY
THE 2025 NO DIG DOWN UNDER CONFERENCE, THE LARGEST TECHNOLOGY EVENT IN THE SOUTHERN HEMISPHERE, WILL PROVIDE THE SECTOR WITH MODERN SOLUTIONS TO TACKLE ISSUES ASSOCIATED WITH MAJOR INFRASTRUCTURE WORKS.
No-Dig Down Under is the southern hemisphere’s only large-scale conference and exhibition dedicated to trenchless technology and it’s set to come back even bigger and better in 2025.
Trenchless technology is important for installing new services, as well as rehabilitating and maintaining existing pipelines and infrastructure, without having to dig multiple trenches, disturbing traffic, business and residential locations.
With major utilities located underground and requiring ongoing upkeep and extension, No-Dig Down Under is a crucial event for local government representatives and those involved in planning decisions for major infrastructure projects.
Trenchless renewal technology provider, Pipe Core, is consistently making waves as an industry leader in this space and is proud to be a gold sponsor for the event.
Pipe Core distributes premium CIPP pipe relining equipment and consumables, including drain cleaning, inspection equipment, as well as cutting-edge UV technologies.
Leading the initiative is Jason Marshall, who joined Pipe Core in 2023 as Chief Executive Officer.
“Our customers range from plumbers and drainers, lining contractors, infrastructure specialists and asset owners,” he says.
“With technology constantly changing, No-Dig Down Under is an efficient way to connect and communicate with the market, allowing us to share what we’re doing and the innovation we are bringing to the industry.”
Marshall says attendees can look forward to the numerous exhibitors discussing their sustainability practices.
“Trenchless technology is an inherently sustainable renewal option,” says Marshall. “Pipe Core will leverage the No-Dig Down Under platform to support these initiatives and highlight its supplier partnerships, where sustainability practices are independently adopted.”
He adds, “Pipe Core’s suppliers align with key sustainability themes such as cutting single-
use plastics, minimising energy consumption, reducing carbon emissions, and enhancing social impact, all of which contribute to environmental and social responsibility.”
Marshall says Pipe Core has worked closely with suppliers to ensure best practices across all areas.
“Especially with manufacturers like SAERTEX multiCom GmbH, who offer products with a technical service life of 100 years,” he says.
The No-Dig conference promises to bring attendees the very latest information about products designed to make trenchless installation and rehabilitation easier and more efficient.
A range of training courses on trenchless methods will be presented prior to the conference and will be led by industry leaders from Australia and overseas, providing value to anyone who encounters trenchless technologies as part of their roles.
The technical program invites speakers from around Australia and the globe to present papers covering case studies, new and emerging technologies, challenging projects and environments, industry skills and training, risk management and more.
The training courses and technical program are supported by an exhibition hall extending over 4500 square metres, featuring exhibitors from all sectors of the industry. Finally, three
including the prestigious Australasian Society for Trenchless Technology (ASTT) Gala Dinner and Awards Evening, providing attendees with networking opportunities in a variety of settings with industry professionals.
Organised in partnership with the ASTT, NoDig Down Under has grown over the years to become the second largest no-dig technology event in the world and is now considered a ‘must-attend’ for all industry professionals.
The ASTT is the peak body for trenchless technology in Australasia, providing advocacy, leadership, support and educational opportunities for organisations and individuals involved in trenchless technology.
For 30 years, the ASTT has provided members with access to the latest technological advancements, technical information, and educational opportunities through Trenchless Australasia magazine, the No-Dig Down Under conference, as well as providing access to industry tools, technical forums and webinars.
Gold sponsors have already been announced, with Pipe Core, Rob Carr and Vermeer Australia leading the way.
Now you have the opportunity to sponsor or exhibit at the event, which is set to be the largest yet.
To find out more about the upcoming NDDU Conference, make sure to visit:
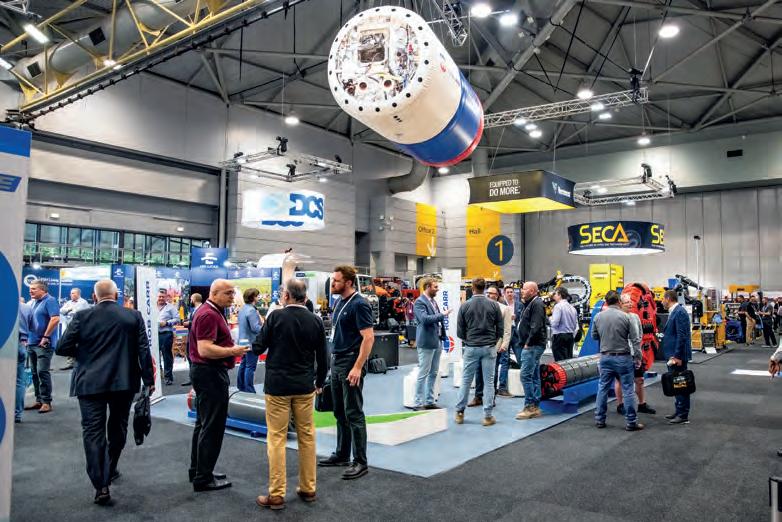
ADVOCATING FOR A GREENER FUTURE
ROADS
& INFRASTRUCTURE MAGAZINE SPEAKS WITH THE NEW CEO AND LEADERSHIP TEAM OF AUSTSTAB TO LEARN WHAT’S IN STORE FOR THE FUTURE OF THE ORGANISATION AND ITS MEMBERS.
The use of sustainable pavements, now more than ever, is a crucial component for the future of Australia’s infrastructure sector.
As one of the biggest contributors to carbon dioxide emissions on a sector-to-sector basis, the infrastructure sector is especially responsible for influencing positive change.
A reduction in funding for pavement and road projects, as well as on-going materials and skilled personnel shortages have created challenges to achieving sustainable outcomes. Organisations such as AustStab are helping to provide the light at the end of the tunnel.
As the only member-driven industry association in the world for pavement recycling and stabilisation, AustStab is the peak industry body representing a broad member base including contractors, material suppliers, consultants, asset owners and plant manufacturers.
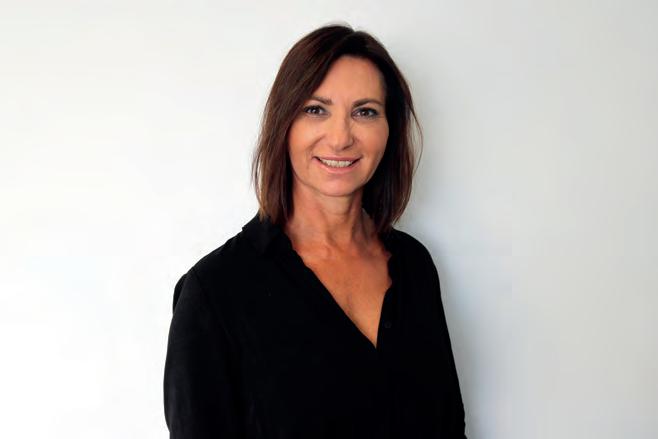
AustStab’s impact on the sector shouldn’t be understated, with the progression and development of sustainable pavement solutions largely being influenced by the association’s support and commitment to greener and cleaner project outcomes.
Its many members are helping to push progress and messaging around the importance of recycled pavements and road rehabilitation.
Newly appointed Chief Executive Officer Tanja Conners says AustStab is an essential body for the infrastructure sector, providing platforms for industry innovation and the advancement of products and methods.
“Organisations like AustStab are essential for the betterment of the pavement recycling and stabilisation industry,” she says. “They provide leadership, promote innovation, ensure high standards, and represent the industry’s interests, all of which contribute to the sector’s sustainability, growth, and success.”
ROLE TO PLAY
AustStab’s primary goals focus on advancing the pavement recycling and stabilisation industry in Australia.
One of the many ways it goes about achieving this is by promoting sustainable practices. AustStab advocates for the adoption
standards, with the association developing and promoting best practices, guidelines and standards that enhance the quality and durability of pavements. This includes providing training and certification programs to ensure industry professionals are equipped with the latest knowledge and skills.
Daniel Orris, AustStab President says now is the time to inspire positive and sustainable outcomes for society as a whole.
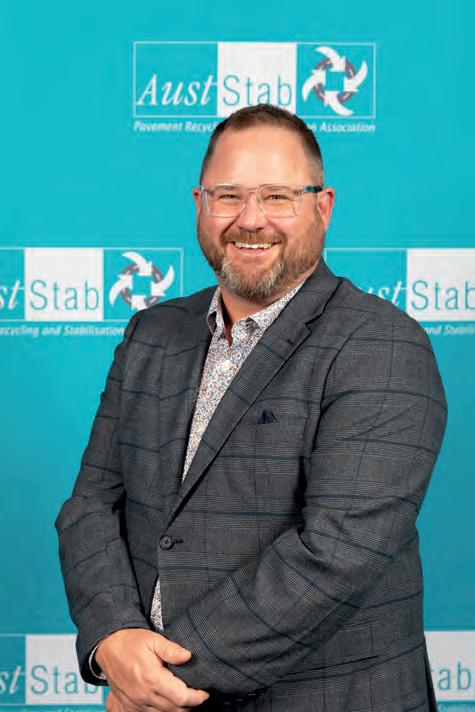
“Our industry is in a unique position to help society and government through a range of current challenges and opportunities,” he says.
“Whether it’s more sustainable infrastructure, cost effective solutions that can lower construction and rehabilitation costs, or enhancing asset performance and life through more resilient solutions.”
Brad Brown, AustStab Vice President says it’s about nurturing such advancement and providing the right tools and facilities to achieve greater outcomes.
“AustStab provides a space for the whole industry to come together to collaborate with the common goal of promoting the use of pavement stabilisation and recycling to achieve sustainable outcomes for asset owners,” he says.
“AustStab represents contractors and suppliers engaged in the road stabilisation and pavement recycling industry, with relationships with all state road authorities, Austroads, the National Road Transport Organisation and Local Government Engineering groups.”
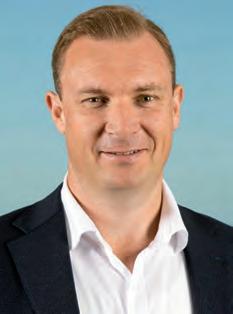
With its key focus on creating opportunities and better methods for use by future generations, AustStab always has one eye on the future. Its ongoing collaboration, evident by its relationships with state transport road authorities, is a key element in leading the industry towards a more sustainable future.
Despite being around for close to 30 years, AustStab is still finding new ways to make an impact. The organisation has already hit a number of milestones in 2024 and under the new leadership of Conners, is set to introduce fresh strategic directions while building on the solid foundation established by previous management.
Brown says this new direction will not only complement what the organisation has already achieved, but strengthen areas to ensure that AustStab can continue to service its members.
“I’m excited for the direction of AustStab under our new CEO Tanja Conners as we build on the great work that’s gone before us from previous management and industry contributors,” he says.
Conners says AustStab is gearing up for several key initiatives, including planning for the 2025 Conference following the success of the recent Brisbane event.
“The focus will be on expanding education capabilities and certification programs, intensifying advocacy efforts and continuing to promote sustainability within the industry,” she says. “AustStab will also support research and innovation projects and host various networking events to foster collaboration among industry stakeholders, positioning the industry as a leader in sustainable infrastructure development.”
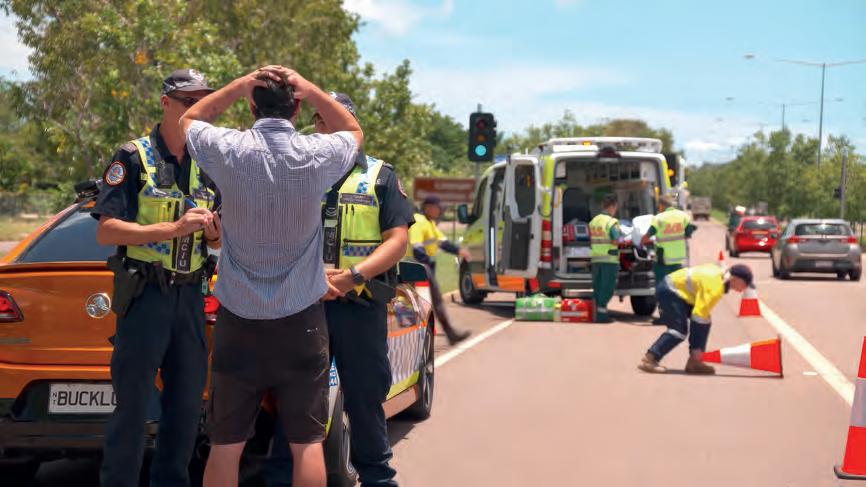
SURVEY SHINES LIGHT ON SAFETY
THE TRAFFIC MANAGEMENT ASSOCIATION OF AUSTRALIA (TMAA) HAS RELEASED ITS 2024 NATIONAL TRAFFIC CONTROLLER SAFETY SURVEY, A COMPREHENSIVE STUDY SHEDDING LIGHT ON THE EXPERIENCES AND CONCERNS OF THESE ESSENTIAL WORKERS ACROSS THE COUNTRY.
As the national peak body for the traffic management industry in Australia, the Traffic Management Association of Australia (TMAA) strives to create a safe and zero-harm industry across the country.
In doing so, the TMAA conducts and releases an annual survey to provide industry members with some critical safety insights.
This year’s report gathered data from over 1500 respondents and builds upon the foundation of the TMAA’s 2023 survey, with a 500 per cent increase in participation.
The survey offers a more robust and detailed picture of the safety landscape facing traffic controllers, by providing a wealth of information about the experiences and perceptions experienced by professionals nationwide.
A notable shift in demographics from last year’s survey shows a larger representation of both men and women, with a more diverse age range and a spread of experience across various industries.
Matthew Bereni, Chief Executive Officer, TMAA says this survey data will ultimately
lead to improvements in the safety of traffic controllers on the ground, a top priority for TMAA.
“We’re doing our part by developing a critical benchmarking dataset, which allows us to advocate more effectively and run an informed advocacy program,” he says.
“We’re constantly in conversations with decision-makers at all levels of government, pushing for policy or regulatory changes. However, meaningful change doesn’t happen without data to back it up.
“That’s why our focus has been on creating and delivering the evidence that supports long-term change.”
A SNAPSHOT OF SAFETY
With an average rating of 7.1 out of 10, traffic controllers generally reported feeling safer in 2024 compared to 2023. However, the survey revealed a consistent national trend, with a range of significant concerns emerging.
These include a culture of disrespect, with verbal abuse from road users remaining a persistent issue.
Fifty-four per cent of traffic controllers reported verbal abuse on a weekly basis, with nine per cent reporting physical assault in the past year, highlighting the need for public education campaigns that emphasise respect for workers.
Addressing driver behaviour was also a key issue which emerged from the results, with the frequency of drivers refusing to stop at traffic control sites proving alarming. Results showed 53 per cent of traffic controllers encountered drivers refusing to stop at least once a week.
Additionally, 49 per cent of respondents reported nearly being struck by a distracted driver, and 44 per cent had near misses due to speeding vehicles. This underscores the need for more stringent enforcement of traffic
laws, increased public awareness campaigns, and improved safety protocols. While also highlighting the need for a multi-pronged approach and informed the creation of three advocacy goals.
Bereni says although current feedback indicates positive progress, there is more to be done.
“The feedback we’ve received from traffic controllers themselves is encouraging – many are telling us that they feel safer in their workplace compared to last year,” he says.
“But on the other hand, when we look at the broader road safety statistics for 2024, the numbers are concerning.
“It shows that while we’ve made some headway, there is still significant work to be done to ensure the safety of both traffic controllers and road users. The journey is far from over.”
The findings provide critical data for TMAA in creating evidence-based policies aimed at creating safer working environments for traffic controllers and improving road safety for all.
The first is Unified National Training Standards which work towards harmonising training standards across states and territories to ensure consistent high-quality training.
The TMAA believes Unified National Training Standards will ensure that all traffic controllers are equipped with the knowledge and skills necessary to navigate a complex and often challenging environment.
A better enforcement of road rules is the second goal, as survey responses highlighted the importance of consistent and strict enforcement of traffic laws.
The TMAA believes the stringent enforcement of speed limits and traffic restrictions around traffic management sites is necessary.
The survey results also highlighted the need for public education of drivers, the third advocacy goal outlined by the TMAA.
Comprehensive public awareness campaigns are vital on educating the public about the dangers facing traffic controllers and to foster a culture of respect and understanding.
The TMAA has expressed its commitment to leveraging the insights from this survey in its advocacy program, and will continue to work with government bodies, industry partners, and the public to achieve advocacy goals.
“Meaningful change doesn’t happen without data to back it up,” Bereni says.
“That’s why our focus has been on creating and delivering the evidence that supports long-term change. This data will ultimately lead to improvements in the safety of traffic controllers on the ground, which is our top priority.”
ENHANCING SAFETY AROUND MOBILE PLANT AND EQUIPMENT
THE
AUSTRALIAN FLEXIBLE PAVEMENT ASSOCIATION’S NATIONAL WORKER ON FOOT AWARENESS COURSE IS THE SECTOR’S OPPORTUNITY TO INVEST IN THE SAFETY AND WELL-BEING OF ITS WORKFORCE, REDUCING RISK AND POTENTIALLY SAVING LIVES.
Across the road construction and maintenance sector, safety is not just a priority – it’s a foundational commitment, particularly when working in close proximity to mobile plant and equipment. Recent data highlights the critical need for enhanced safety measures and training for workers on foot near these powerful machines.
To address these concerns, AfPA (the Australian Flexible Pavement Association) has introduced the National Worker on Foot Awareness online course, a specialised program that exemplifies AfPA’s unwavering dedication to improving safety protocols and ensuring a secure work environment for all individuals on site.
The demand for improved safety training is underscored by statistics from Safe Work Australia, revealing a concerning pattern: mobile plant and equipment are disproportionately involved in hazardous incidents on construction sites.
In the 2021-22 financial year, 3840 serious claims were linked to mobile plant machinery, including 10 fatalities.
These figures demonstrate the necessity for targeted, high-quality safety training and effective protocols tailored to the risks associated with mobile plant operations. This course meets that need head-on.
Mobile plant machinery is integral to road construction and maintenance projects, including equipment such as excavators, graders, profilers, pavers, and rollers.
The size, movement, and operational complexity of these machines introduce substantial risks for workers on foot.
The congested and dynamic nature of construction sites further amplifies these risks, posing challenges in visibility and communication between workers and machinery operators.
AfPA’s course addresses these challenges directly, equipping participants with the knowledge and skills needed to prevent accidents and ensure smooth operations.
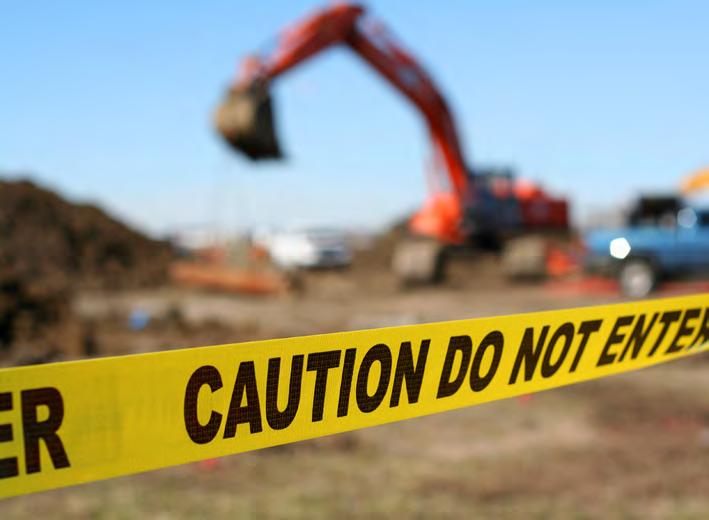
to accidents such as being struck by moving machinery, run over, or injured by falling objects.
Given the dynamic nature of construction sites, it is imperative for workers to be wellversed in safety protocols and to remain vigilant about their surroundings.
The National Worker on Foot Awareness Course is an opportunity to invest in the safety and well-being of a workforce, reducing risk and potentially saving lives.
The Primary goal of the course is incident prevention. It includes strategies for establishing safe zones around mobile plant machinery, conducting regular safety checks, and implementing site-specific safety protocols.
Additionally, participants will learn effective response techniques for emergencies, equipping them to react promptly and appropriately in the event of an incident. These critical skills could be the difference between a near-miss and a serious injury.
Importantly, the course also provides industry specific content, giving a detailed understanding of mobile plant machinery commonly used in road construction and maintenance.
Participants will gain insights into machine movements, associated hazards, and best practices for mitigating these risks.
This foundational knowledge is essential
By enrolling, you are ensuring your team is equipped with the latest industry knowledge to stay safe and productive.
The last focus is effective communication strategies, with communication being crucial for site safety.
The course emphasises Positive Communication (PosCom), training participants on using communication tools and techniques to ensure awareness of each other’s movements among all site personnel.
This is not just training – it’s a strategy for success in high-risk environments.
Whether you’re a small contractor or a large organisation, this course adapts to your needs, offering unparalleled value and effectiveness to suit multiple requirements.
Enrolling in this course demonstrates a proactive commitment to risk management and safety for employers and workers alike. Given the significant risks associated with working near mobile plant machinery, The National Worker on Foot Awareness Course by AfPA offers an indispensable solution for addressing these risks and elevating safety standards on construction sites.
The National Worker on Foot Awareness course is planned to roll out online by the end of October.
Keep an eye on the AfPA social channels for updates.
CONTRACTS IN BRIEF
ROADS & INFRASTRUCTURE PROVIDES AN UPDATE ON SOME OF THE CONTRACTS AND TENDERS RECENTLY AWARDED OR PUT TO MARKET ACROSS THE AUSTRALIAN
INFRASTRUCTURE SECTOR.
QUEENSLAND
UGL wins second stage works on the Western Downs Battery
UGL has been appointed a works package to design and construct the second stage of the Western Downs Battery in Queensland. The contract, which is for renewable energy producers Neoen, consists of the installation of a 270 MW / 540 MWh Battery Energy Storage System and the high voltage infrastructure to connect it to the grid at Neoen’s Western Downs Green Power Hub. The BESS (Battery Energy Storage System) will consist of 140 Tesla Megapack 2XL units and is expected to start operations in 2026. UGL is also currently constructing the first stage of the Western Downs Battery (also sized at 270 MW/540 MWh), which is expected to start operations later this year. Following construction, both batteries will work alongside Neoen’s 460 MWp Western Downs solar farm at the same site and allow stored energy to be transmitted into the electricity network. Neoen also has a history of completing battery projects in Australia. The company’s 150 MW Hornsdale Power Reserve, more commonly known as the ‘Tesla Big Battery’, has been in operation in South Australia since 2017. Its 300 MW Victorian Big Battery, currently in operation near Geelong, is one of the world’s largest batteries. UGL will commence work on the project in the coming weeks, with an aim to commence operations in 2026.
Two tenders released for Direct Sunshine Coast Rail
Line
Two new tenders for the Direct Sunshine Coast Rail Line project in Queensland have now been released to market, coinciding with the opening of a brand new information and engagement centre for the community to learn more about the project and associated works. For the two tenders for the major rail project, QLD TMR is seeking engineering teams and procurement specialists to assist in finalising the reference design and support procurement activities for the project. This will enable Transport and Main Roads to call for detailed quotes from the construction industry in 2025 ahead of major construction in 2026. The Direct Sunshine Coast Rail Line is a proposed 37.8 kilometre rail extension between Beerwah and Maroochydore to increase public transport opportunities and improve connectivity to Moreton Bay, Brisbane and beyond. The first stage of the Direct Sunshine Coast Rail Line project will deliver a new 19-kilometre link between Beerwah and Caloundra (by 2032), new stations at Aura and Caloundra and an upgraded station at Beerwah. The new information centre will serve as a hub for locals to talk directly with project representatives and view maps, displays, concept images, timelines and detailed information about the Direct Sunshine Coast Rail Line as
the project progresses through planning and delivery. Geotechnical investigations from Beerwah to Birtinya are getting underway. The geotechnical activity will help to provide more certainty about ground conditions along the corridor. These investigations will better inform environmental approvals, the design process and help contractors to price the project with more certainty.
VICTORIA
Preferred contractors announced for $785M Melton Station, LXRP works Contracts have been awarded to two project alliances to deliver four level crossing removals at Coburns and Exford roads in Melton, and Ferris and Hopkins roads in Truganina, as well as the new Melton Station. A $560 million contract has been awarded to John Holland, Kellogg Brown and Root (KBR), Metro Trains Melbourne, V/Line, and the Level Crossing Removal Project. This alliance will deliver the new Melton Station and remove the level crossings at Coburns and Exford roads by constructing a rail bridge. Additionally, a $229 million contract has been awarded to an alliance comprising Fulton Hogan, Metro Trains Melbourne, V/Line, and the Level Crossing Removal Project. This team will deliver new road bridges to get remove the level crossings at Ferris Road, Melton, and Hopkins Road, Truganina. The removal of the Melton level crossings will also see the introduction of larger nine-car VLocity trains as part of the $650 million Melton Line Upgrade, boosting passenger capacity by 50 per cent. The new Melton Station will have an expansive pedestrian walkway, pick-up and drop-off zones, a new relocated bus interchange, and platform accessibility via lifts and stairs. It will also feature an air-conditioned waiting room, a staffed ticket office, and lighting and security cameras throughout the area. The new Melton Station will also feature two additional platforms to accommodate Ballarat train services. Crews have been on site testing ground conditions with geotechnical drills and preparing for construction, paving the way for a workforce of 550 construction workers from recent crossing removal projects, with works set to begin later this year. Final designs for all four level crossing removals and the new Melton Station will be released later in 2024. These level crossings are on track to be removed in 2026.
SOUTH AUSTRALIA
Bardavcol awarded contract on T2Dlinked intersection upgrade South Australian company Bardavcol has been awarded the contract for major works on the $85 million Marion Road and Sir Donald Bradman Drive intersection upgrade. The
works aim to provide better traffic flow through the major commuter roads between the city and airport, both during and after construction of the River Torrens to Darlington Project. The jointly funded project will include new turning lanes on Sir Donald Bradman Drive in both directions, along with an extended left-turn lane on Marion Road (northbound) heading west onto Sir Donald Bradman Drive. Both the Federal and South Australian governments will contribute $42.5 million to the project, which will include new public spaces around the intersection and other improvements such as new LED road lighting, asphalt, drainage, kerbing and gutters. New bicycle lanes will be installed on all approaches, with pedestrian crossings to be upgraded to improve safety for cyclists and pedestrians to encourage active travel. Marion Road and Sir Donald Bradman Drive are major commuter, freight and public transport routes, with about 60,000 vehicles passing through the intersection every day. The intersection upgrade is one of several enhancements to intersections and roadways in the areas surrounding the T2D Project.
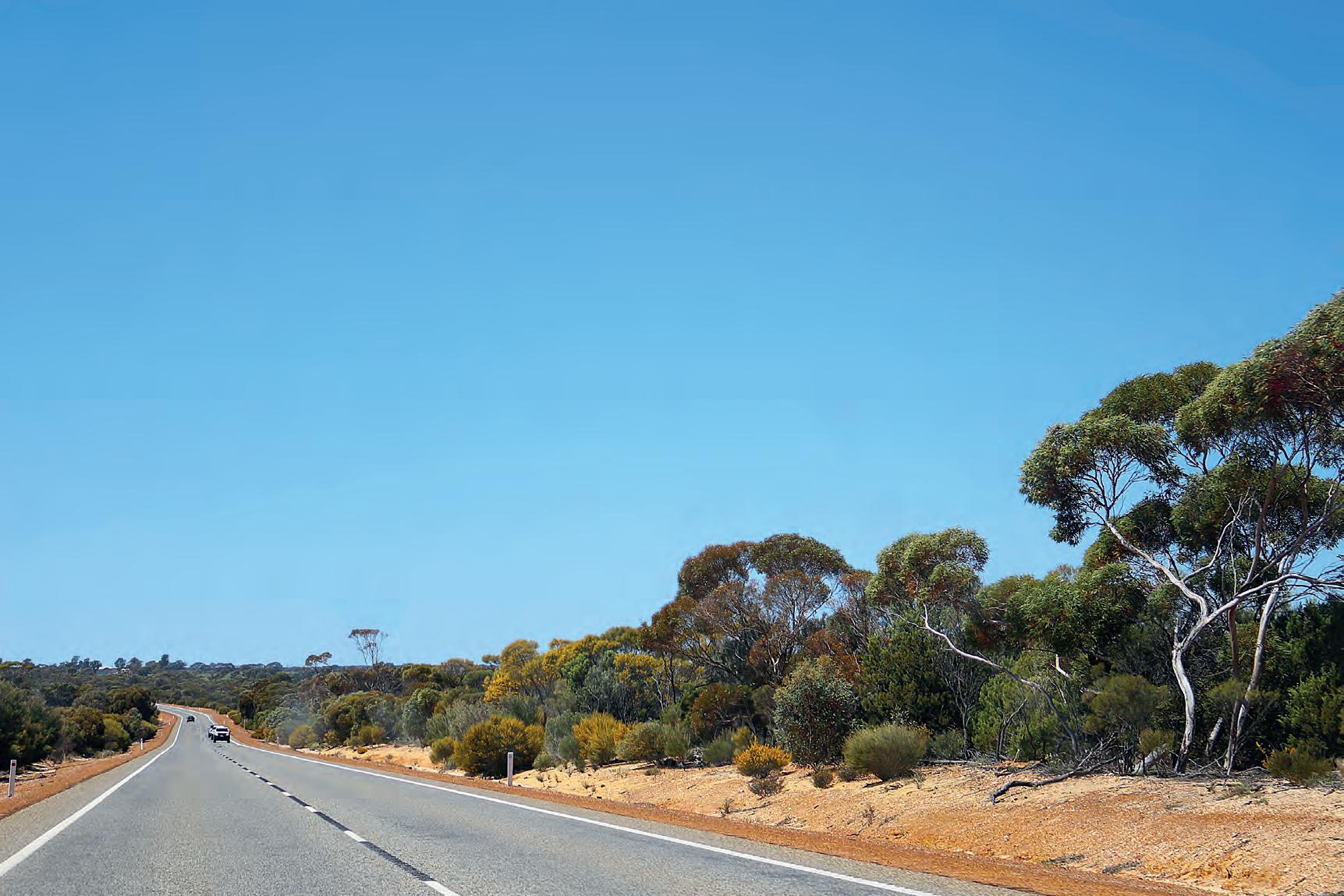
Preferred alliance revealed for North South Corridor works
The final stage of the North South Corridor in South Australia has reached a major milestone, with the preferred alliance partner now selected to deliver the state’s largest ever infrastructure project. The preferred consortium comprises of John Holland, Bouygues Construction, Arcadis Australia, Jacobs and Ventia. The North South Corridor will be the major route for north and south-bound traffic, including freight vehicles, running between Gawler and Old Noarlunga, a distance of 78 kilometres. The project is made up of a number of different works packages, such as the River Torrens to Darlington Project, which is the final 10.5-kilometre section of the North South Corridor. The River Torrens to Darlington Project (T2D project) will allow motorists to avoid 21 existing sets of traffic lights between the River Torrens and Darlington and will complete the non-stop 78-kilometre North-South Corridor between Gawler and Old Noarlunga. The consortium’s tender detailed a plan to procure three Tunnel Boring Machines (TBMs), instead of the two previously anticipated – which will mean both north and south tunnels can be constructed concurrently. The three TBMs that will be used to excavate the T2D tunnels will be purpose-built for the local conditions they will encounter on the project.
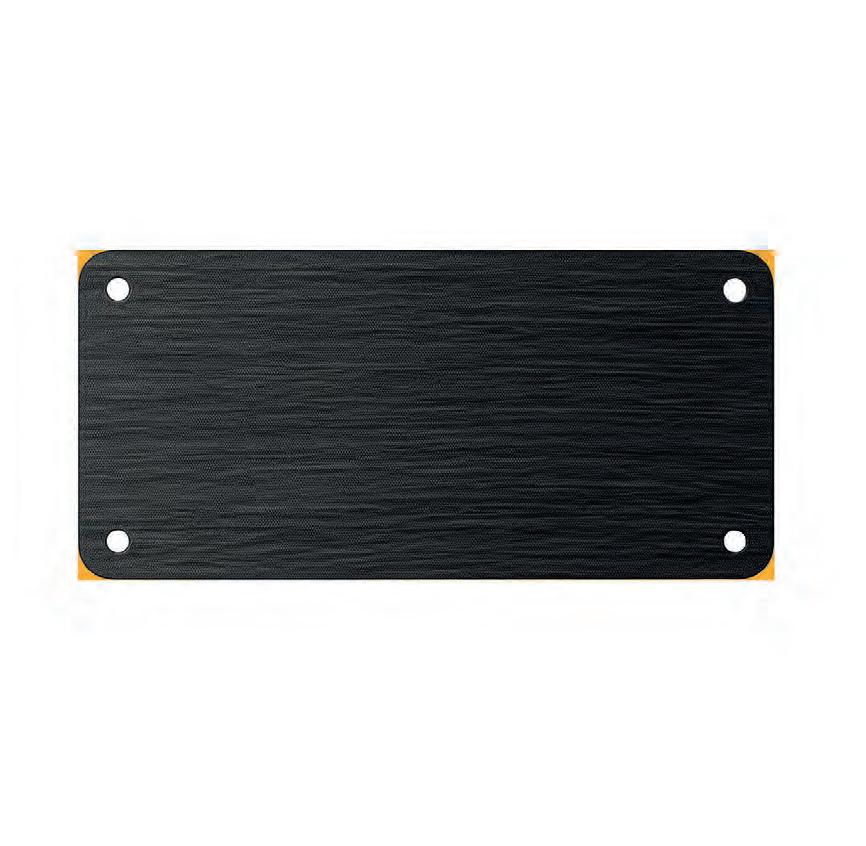
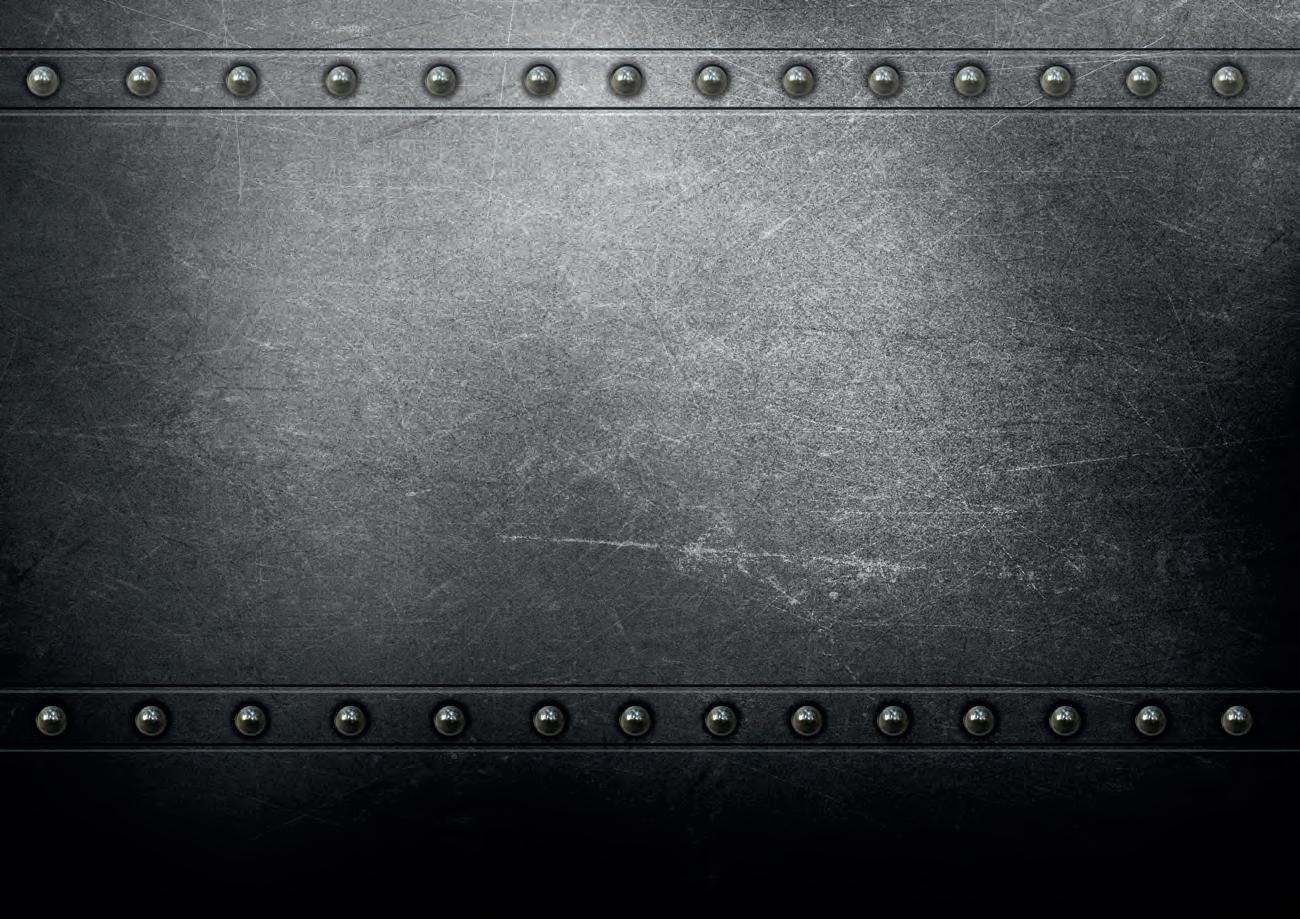
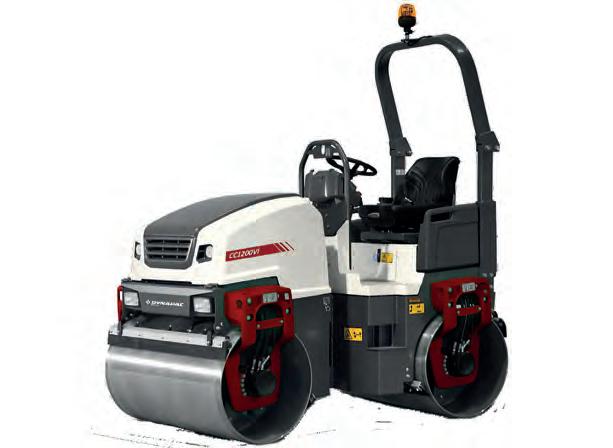
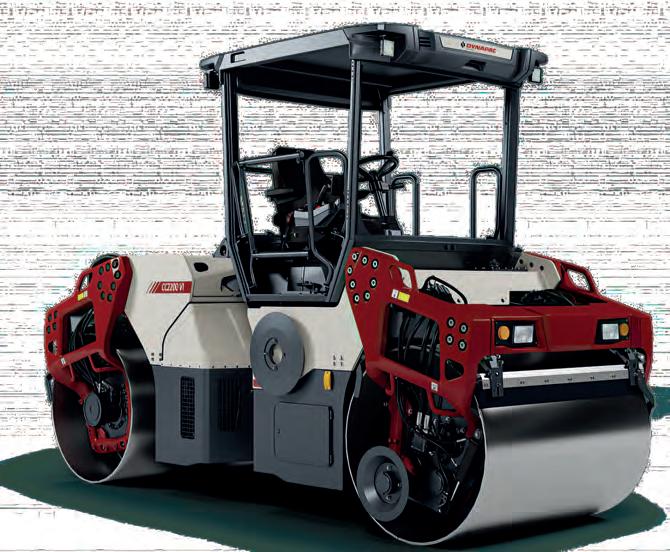

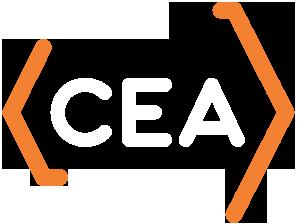
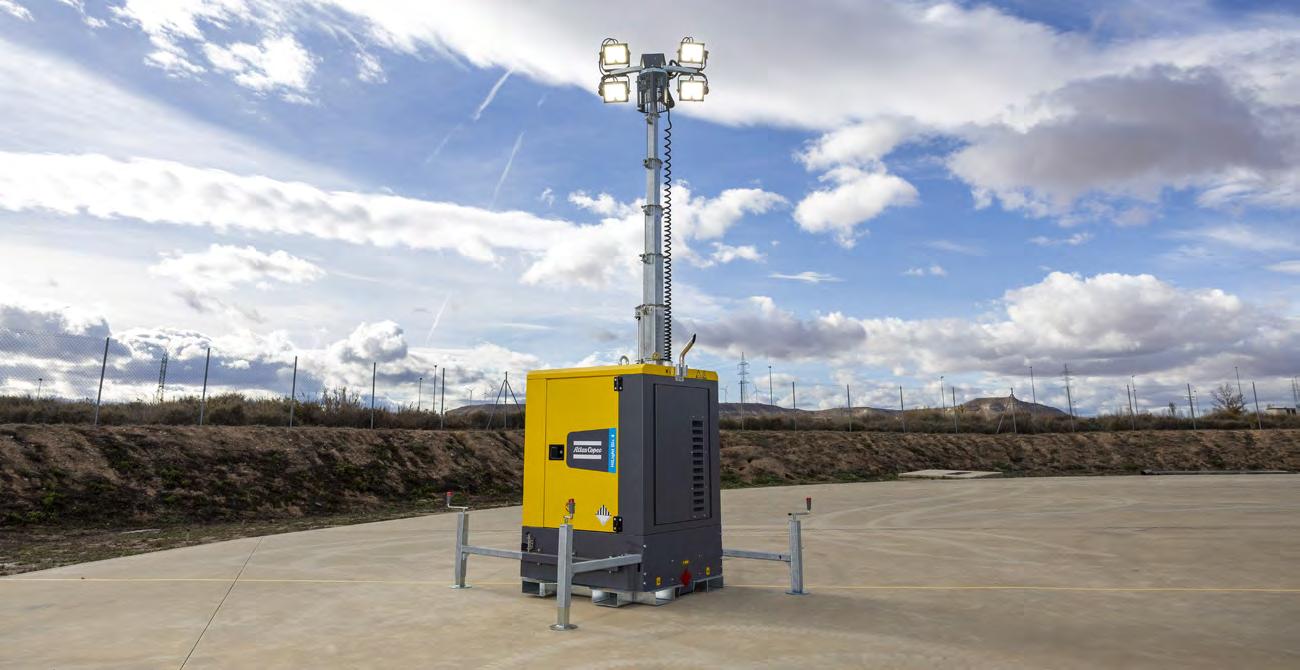
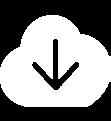
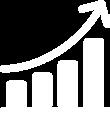
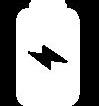
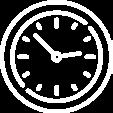
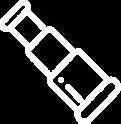
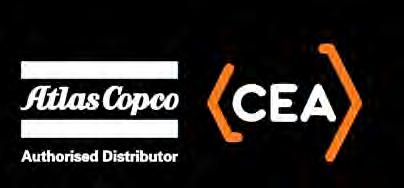
As pure as it gets
Our dedication goes beyond quality bitumen; it’s a journey towards establishing sustainable roads for generations to come.
SAMI Bitumen Technologies is committed to using HSE-compliant materials in all products.
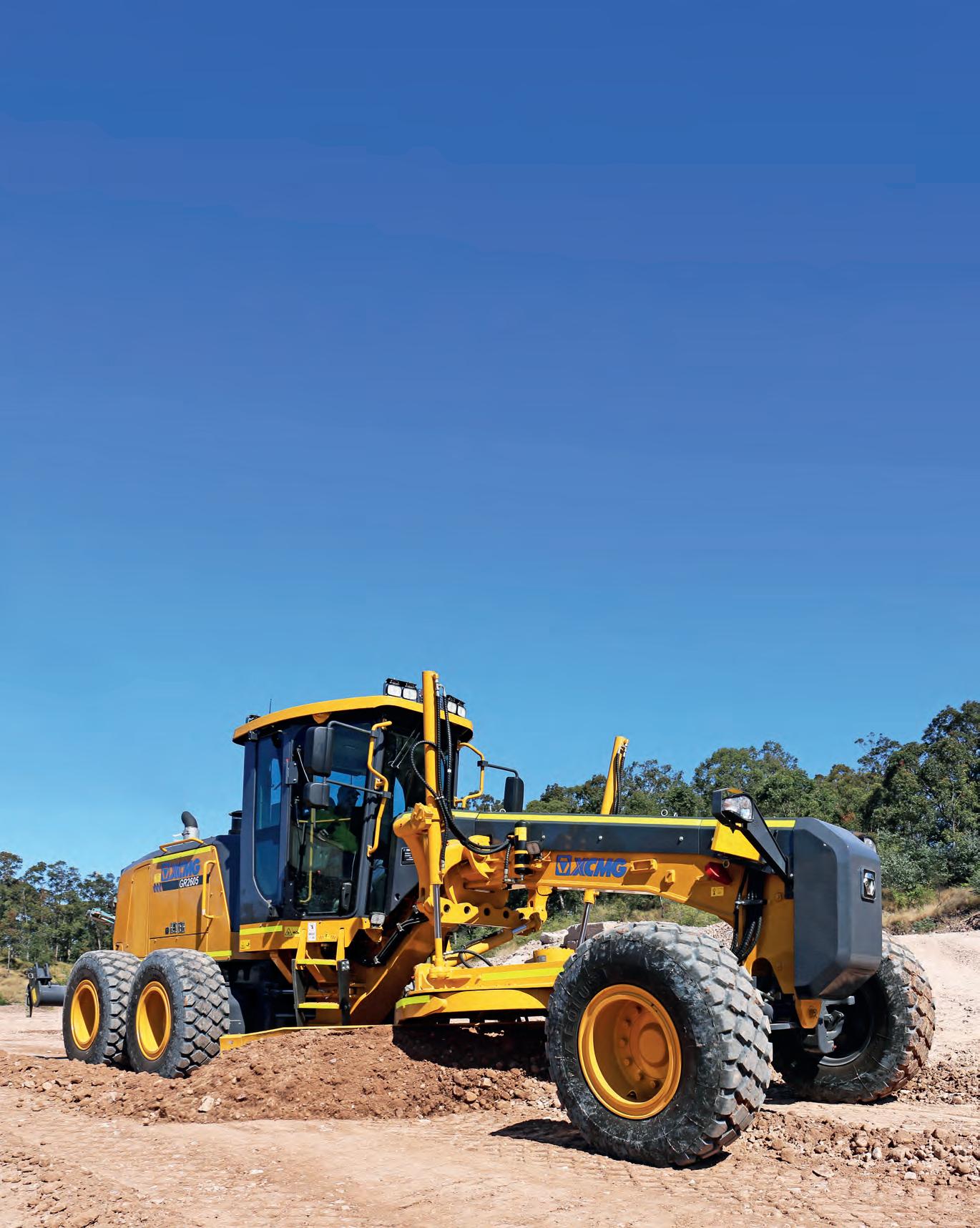
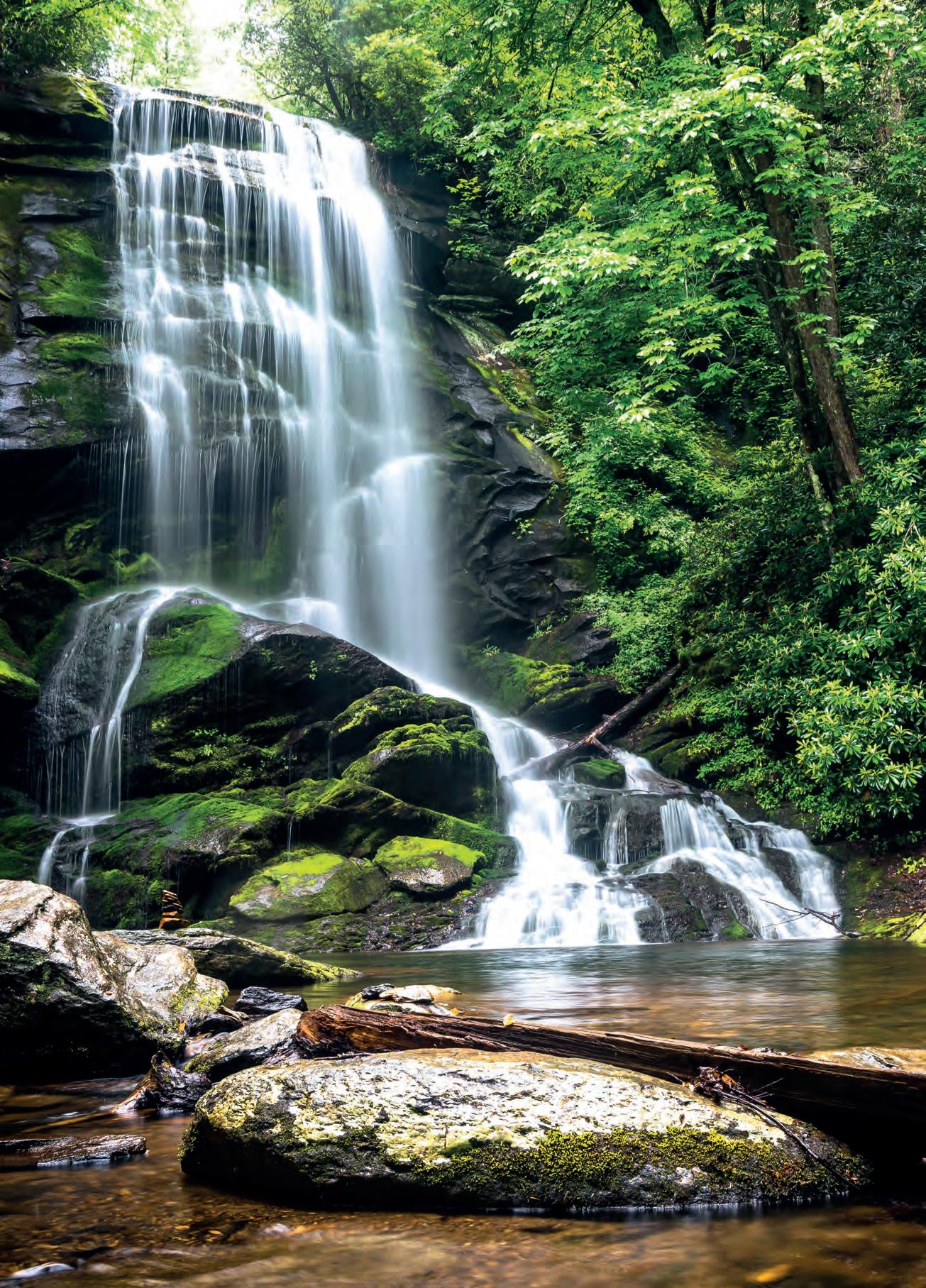