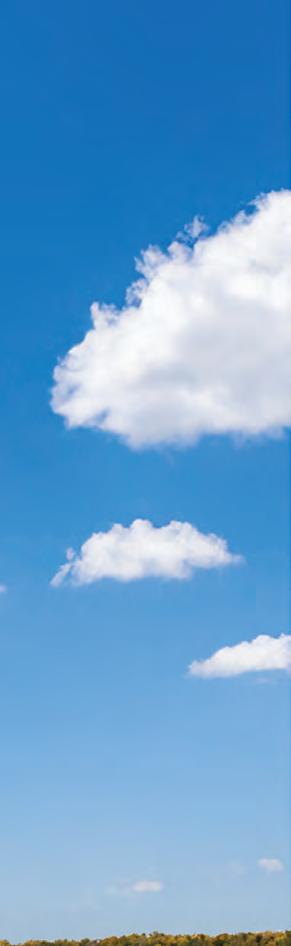
The switch to green
One of Australia’s largest infrastructure providers is making sustainable changes across the board
Future-proofing for millions
Inside one of Victoria’s largest ever infrastructure endeavours, the Level Crossing Removal Project
One of Australia’s largest infrastructure providers is making sustainable changes across the board
Inside one of Victoria’s largest ever infrastructure endeavours, the Level Crossing Removal Project
Stabilised Pavements of Australia sheds light on what it takes to be a pioneer and innovator across four decades
14 Family-led excellence
For 40 years, Stabilised Pavements of Australia has pioneered the development of sustainable solutions for the sector.
17 Youth future focus
Two members of the Suburban Rail Loop’s youth panel reflect on their feedback on the future of Victoria’s transport system.
20 Snowy 2.0 project progress
How the Snowy 2.0 project is catering for future renewable energy demand.
22 The right switch
Fulton Hogan is making a number of operational changes, in a bid to make its business more sustainable.
27 Greener, cleaner, smarter
The NuMIXER bitumen softener is giving operators more sustainable and robust outcomes, creating more consistency for bitumen.
30 Resourceful recycling
ResourceCo is transforming construction and demolition waste back into high quality products for the construction sector.
34 Durability meets sustainability
SAMI Bitumen Technologies is helping to inspire and influence greener outcomes for transport.
38 145 years of sustainability
Leaders from Alex Fraser reflect on the company’s recent 145th anniversary.
40 Overt culvert innovation
Mainmark’s Teretek and Terefil are helping contractors to support and fill culverts.
43 Electric excellence
Inside JCB’s foray and establishment in the electric machinery and equipment market.
46 Making a big impression
BOMAG rollers are helping a local equipment hire business to prosper.
48 Master productivity
Caterpillar is introducing its latest construction machinery technology.
50 Building Australia’s future
A National Precast member is at the forefront of delivering innovative infrastructure solutions.
52 Breaking down the LXRP
An update on the Level Crossing Removal Project in Victoria.
56 Creating opportunity
The importance of treating off-the-road tyres properly, to minimise environmental impacts.
58 Contracts & Tenders
Smart Construction Edge 2 simplifies drone-based aerial surveying.
Eliminate the need for Ground Control Points and process data rapidly, onboard, in the field.
Komatsu’s Edge 2 technology makes aerial surveying a hassle-free and essential part of daily work life.
Learn more
Call us today on 1300 445 978 to find out more.
WE’RE ALMOST AT THE FINISH LINE for what has been a massive 2024 for the sector. With this in mind, many of the people and companies I’ve talked to this month are in a reflective mood, with some celebrating milestones, others assessing the highs and lows of what has been – at times – a challenging year for some.
For this month’s cover story, we sat down with Warren Smith and Tom Wilmot of Stabilised Pavements of Australia (SPA). The company is celebrating its 40th anniversary this year, having made a monumental impact on the infrastructure and pavement sectors in that time. The company has been the developer, key representative and soundboard for the stabilised pavement space, influencing positive change across a number of different areas, with sustainability always a focal point. Smith and Wilmot shed light on what it’s taken to get to this point, while also looking back (and forward) on what has been a four decade friendship between the pair.
Another of the biggest innovators in the space, Alex Fraser, is celebrating a significant milestone, recently achieving 145 years of providing greener outcomes for road and infrastructure projects right across Australia. We speak with a number of individuals who reflect on the achievement and the accomplishments that have been made along the way, as well as the company’s future, with further innovation in the pipeline.
Fulton Hogan is another company that’s playing its part, with internal and external sustainability objectives inspiring eco-friendly changes to the way the company operates. Fulton Hogan is making the switch from diesel to natural gas to power a number of its asphalt plants in South East Queensland. This is on top of changes that are being made across the board at the company to minimise its carbon footprint.
CEA/JCB is developing more and more electric options for its machinery fleet, identifying that electric and battery powered equipment is the future. We take a peek behind the curtains to see what’s currently available, as well as what the company is working on, as it aspires to support the sustainability goals of its customers.
This and so much more, in the November edition of Roads & Infrastructure Magazine.
Happy reading!
Tom O’Keane Roads & Infrastructure Magazine
COO
Christine Clancy christine.clancy@primecreative.com.au
PUBLISHER
Sarah Baker sarah.baker@primecreative.com.au
MANAGING EDITOR
Lisa Korycki lisa.korycki@primecreative.com.au
EDITOR
Tom O’Keane tom.okeane@primecreative.com.au
JOURNALIST
Jennifer Pittorino jennifer.pittorino@primecreative.com.au
HEAD OF DESIGN
Blake Storey
ART DIRECTOR Bea Barthelson
BUSINESS DEVELOPMENT MANAGER
Brad Marshall brad.marshall@primecreative.com.au
CLIENT SUCCESS MANAGER
Salma Kennedy salma.kennedy@primecreative.com.au
HEAD OFFICE
Prime Creative Pty Ltd
379 Docklands Drive, Docklands VIC 3008 Australia p: +61 3 9690 8766 enquiries@primecreative.com.au www.roadsonline.com.au
SUBSCRIPTIONS +61 3 9690 8766 subscriptions@primecreative.com.au
Roads & Infrastructure Australia is available by subscription from the publisher. The rights of refusal are reserved by the publisher.
ARTICLES
All articles submitted for publication become the property of the publisher. The Editor reserves the right to adjust any article to conform with the magazine format.
COVER IMAGE
Stabilised Pavements of Australia.
COPYRIGHT
Roads & Infrastructure Australia is owned and published by Prime Creative Media. All material in Roads & Infrastructure Australia is copyright and no part may be reproduced or copied in any form or by any means (graphic, electronic or mechanical including information and retrieval systems) without the written permission of the publisher. The Editor welcomes contributions but reserves the right to accept or reject any material. While every effort has been made to ensure the accuracy of information, Prime Creative Media will not accept responsibility for errors or omissions or for any consequences arising from reliance on information published. The opinions expressed in Roads & Infrastructure Australia are not necessarily the opinions of, or endorsed by the publisher unless otherwise stated.
Sometimes you want the latest tech. Sometimes you just want the essentials done exceptionally well. That’s why we offer distinct levels of innovation, comfort, and performance so you can get done faster, more efficiently, and on budget.
Melbourne’s West Gate Tunnel Project is nearing ever closer to completion, as an extra lane on the M80 entry ramp begins construction to widen the West Gate Freeway from eight to 12 lanes.
The West Gate Freeway carries 200,000 vehicles each day and is a critical link in Melbourne’s transport network, but one incident is enough to
One section of the new 23-kilometre alignment at Western Sydney Airport has been completed, taking the metro railway over the Warragamba pipelines.
The 3.5-kilometre viaduct structure between Orchard Hills and Luddenham will be a critical part of the alignment, implemented to take metro services over key locations including the Warragamba pipelines, Blaxland Creek, and Luddenham Road.
The Sydney Metro railway will become the transport spine for Greater Western Sydney, connecting communities and travellers with the new Western Sydney International (Nancy-Bird Walton) Airport. Working closely with WaterNSW, it took crews one month to construct a twospan section of elevated viaduct over the two pipelines, which will be responsible for transferring 80 per cent of Sydney’s water from Warragamba Dam to filtration
bring traffic to a standstill.
Widening the West Gate Freeway from eight to 12 through lanes will help to ease congestion, while supporting the state’s growing population.
In October, the West Gate Freeway Williamstown Road citybound exit ramp was closed until mid-November to install a new walking and cycling bridge over
the top of the ramp.
A s ection of Footscray Road eastbound was closed for most of October as crews edged closer to finishing the new 2.5 kilometre cycling super-highway above Footscray Road.
The West Gate Tunnel Project will deliver an alternative to the West Gate Bridge, removing 9000 trucks a day off local roads by providing a second river crossing and creating 14 kilometres of new walking and cycling paths.
Express lanes from the M80 Ring Road interchange to the West Gate Bridge will reduce congestion for vehicles heading to the south of the city and out to the south eastern suburbs. The widened West Gate Freeway will also include a new tunnel entry to the city and exit to the west.
Trucks will save up to 50 per cent travel time through direct freeway connections to the Port, and new ramps from the West Gate Freeway to Hyde Street.
plants for treatment.
A total of 26 segments, each weighing up to 65 tonnes, were installed up to 15.3 metres above the pipelines, following a significant amount of preparation to strengthen the ground around the pipelines. Rigorous vibration and settlement monitoring were implemented throughout construction activities to ensure the pipelines remained unaffected, while a crane was used to support the segments while they were lifted and positioned.
Only 18 per cent of the viaduct remains
concrete segments at a facility just outside Newcastle now complete. The final 208 segments will be installed over the coming months. Major tunnelling to build the 9.8-kilometres of twin tunnels that take the metro line underground between Orchard Hills and St Marys in the north and Airport Business Park and Bradfield in the south was completed in June 2024. By the end of 2024, the majority of the viaduct and sections of the alignment at ground level will be finished, making way for the commencement of tracklaying.
Receive up to $2.5K in Fuel Cards with purchase on selected JCB Skid Steers* & FUEL UP ON SAVINGS!
HURRY OFFER VALID UNTIL 31 DECEMBER 2024
Before you buy a skid steer you need to know it’s going to be tough enough to perform in a variety of conditions. Fortunately, with JCB strength and durability come as standard.
Benefitting from JCB’s unique PowerBoom design, a single-sided reinforced high tensile strength steel boom that features 20% more steel than its competitors, JCB’s skid steer range is built to tackle tough jobs that require a compact machine with heavy duty features.
Safety is also a key priority and with exclusive left-hand-side entry operators can access the JCB skid steer without having to climb over large attachments or under an unsupported boom, and with a 270° field of vision the range offers up to 60% better visibility than rival machines. For the ultimate in versatile performance the JCB skid steer range offers endless possibilities.
To find out more and take advantage of this great offer speak to your local JCB CEA dealer today!
The first sod turn on the Singleton bypass in New South Wales has marked the beginning of major construction on the $700 million project, which is Singleton’s biggest infrastructure project to date.
The Federal Government’s $560 million contribution and the New South Wales Government’s $140 million contribution will remove one of the Hunter region’s most notorious bottlenecks and around
The Coomera Connector bridge between Brisbane and the Gold Coast has hit major construction milestones across all three packages of the project, with stage one expected to open to traffic in sections from late 2025.
Jointly funded by the Federal and Queensland governments, the $3.026 billion, one kilometre bridge that spans the Coomera River, Hope Island Road and Saltwater Creek is taking shape, with 350 bridge girders installed and 13 bridge deck concrete pours completed so far. Further installations began from midSeptember on the 50 girders required for the overpass and pedestrian bridges over Helensvale Road.
15,000 vehicles each day from the Singleton
Contractor Acciona Constructions Australia has finalised the design of the project, which when completed will aid motorists in avoiding five sets of traffic lights.
Six bridges will be built as part of the project, including four across the Hunter River floodplain, as well as a northbound climbing lane which will allow heavy
vehicles to climb the hill between Gowrie Gates and the northern connection.
Following additional investigations and constructive engagement with the community, stakeholder and property owners, the design has been further refined to include modifying the southern connection and reconfiguring the Putty Road interchange.
The Singleton Bypass is expected to open to traffic in late 2026.
The Coomera Connector is a future state-controlled north-south transport corridor between Loganholme and Nerang. Image: QLD Department of Transport and Main Roads.
one North package, where crews have been busy laying more than 1500 metres of asphalt.
This included the first section of the main motorway alignment near McPhail Road and in areas for future widening around the Helensvale Road interchange and Shipper Drive.
More than one million working hours have been clocked by crews on the Stage
While bridge construction and asphalt laying continues in these
areas, work on the Coomera Link Road section is due to begin, where a new signalised intersection will be installed at the Foxwell Road and Shipper Drive roundabout.
Set up of the site compound on the South package is underway and heavy vehicle access has been constructed at Boulton Drive to allow preloading works to start in the coming months.
The Urban Design and Landscape Plan for the Eastern Freeway Upgrades in Victoria have been approved, marking a major milestone for the project.
The Eastern Freeway upgrades will include new express lanes, new traffic management technology and Melbourne’s first dedicated busway, connecting the new North East Link tunnels in Bulleen to the M80 Ring Road in Greensborough.
In response to community feedback through the project’s Environment Effects Statement, the Urban Design and Landscape Plan (UDLP) exhibited for comment in October 2023 and included a range of responses.
The first stage of the Eastern Freeway Upgrades from Burke Road to Tram Road will deliver six new express lanes for faster trips, new Eastern Busway lanes connecting with two park and rides at Bulleen and Doncaster, 11 kilometres of
walking and cycling paths and 1.8 million new trees and plants.
It will also include one kilometre of new and upgraded noise walls and 43,700 square metres of revitalised Valda Wetlands, with more space for trees and plants at Koonung Creek Reserve near Doncaster Road and more trees for screening and shade along Koonung Creek Trail near Elgar Road.
While the plan was on exhibition, it was viewed online more than 7000 times, over 140 people visited an information display, and 130 submissions were received.
In response to submissions, the final UDLP now includes further improvements to the design including
an extra 1.2 kilometres of upgrades to the main Koonung Creek Trail, better bike connections at Doncaster Road to Doncaster Park & Ride, improved Heyington Avenue bridge design at Valda Wetlands and new connections to Koonung Creek Trail in Bulleen and Doncaster.
Additional upgrades for Koonung Creek Reserve and parklands include extra fitness equipment, extra barbecue and rest areas and more bike repair stations and drinking fountains.
With the Urban Design and Landscape Plan now approved, locals will see construction work on the Eastern Freeway Upgrades continue to move forward.
Major works on the $1.162 billion Gympie Bypass in Queensland have been completed.
The project has involved constructing a new 26-kilometre, four-lane divided highway between the existing Bruce
Highway interchange at Woondum, just south of Gympie, and Curra.
It is the final section of a 62-kilometre, $2.549 billion program of works to upgrade the Bruce Highway between Cooroy and Curra.
The project will improve traffic flow, as the upgrade will avoid 53 intersections (including nine signalised intersections) and 106 property accesses that contribute to current safety and congestion issues on the Bruce Highway. It will also help to improve safety and capacity through the separation of long-distance traffic from local traffic. This will reduce traffic volumes on the highway travelling through Gympie, with around 50 per cent fewer heavy vehicles.
The $1.162 billion Gympie Bypass is jointly funded, with the Federal Government committing $929.6 million and the Queensland Government contributing $232.4 million.
Construction of the overall Cooroy to Curra program began in September 2009.
Works on the new Dubbo Bridge are pushing ahead, with a third of the concrete deck now in place for the $263.2 million structure on the Newell Highway in New South Wales.
The New Dubbo Bridge will provide a second high level river crossing in Dubbo during flood events and will deliver a reliable connection for local, commuter and heavy freight traffic throughout the region.
The 660-metre bridge will connect the western side of the Macquarie River to River Street, travelling over the flood plain west of the river.
The decking is being built in sections, with each section involving the pouring of about 105 cubic metres of concrete to provide a deck slab of up to 25 centimetres in depth.
The deck pours will be carried out progressively while the rest of the bridge takes shape, with the final deck pour expected in mid-2025.
Once the concrete deck is completed, the final step in building the bridge surface will be to add an eight centimetre thick layer of asphalt.
Pile driving was recently completed
along the entire length of the new structure which crosses the Macquarie River and a section of the floodplain east of the river.
Construction is also underway for the
network of roads that will link the bridge to the Dubbo road network, including road widening work at the intersections of Whylandra and Thompson streets and River and Bourke streets.
reducing congestion and improving travel times in the area.
The Victoria Park-Canning Level Crossing Removal Project represents the most significant upgrade ever undertaken on the 131-year-old Armadale Line, creating six hectares of new public open space for the community.
The project will remove six level crossings, raising the rail over the road at Mint/Archer Street, Oats Street, Welshpool Road, Hamilton Street, Wharf Street and William Street.
New modern elevated stations are being built at Carlisle, Oats Street, Queens Park, Cannington and Beckenham stations, with Welshpool Station to be closed permanently.
The Federal and Victorian governments have both committed $87.5 million to the project.
FOR 40 YEARS, STABILISED PAVEMENTS OF AUSTRALIA (SPA) HAS PIONEERED THE DEVELOPMENT OF INNOVATIVE AND SUSTAINABLE SOLUTIONS FOR THE ROADS SECTOR. DIRECTORS, REVOLUTIONARIES AND GOOD FRIENDS WARREN SMITH AND TOM WILMOT REFLECT ON THE COMPANY’S ACHIEVEMENTS AND PROVIDE SOME INSIGHT INTO SPA’S BRIGHT FUTURE.
Despite being four decades ago, many of the events of 1984 still influence our lives daily.
It was the year Steve Jobs first launched the Macintosh personal computer in the United States, the year that the one-dollar coin was first introduced in Australia and the year that Ghostbusters smashed domestic box office records.
For Warren Smith and Tom Wilmot, 1984 is also fondly remembered for the foundation of one of Australia’s most influential players in the pavement stabilisation space.
A united desire and hunger to improve outcomes for the roads and infrastructure sectors, as well as a lack of alternative solutions in the market at the time, gave way for the launch of Stabilised Pavements of Australia (SPA) and its focus on pavement recycling.
Smith, a Director of the company alongside Wilmot, says SPA’s early days were about making connections and aiming to influence a greener and greater future for the industry as a whole.
“It all started with our passion for recycling,” he says. “Over the years we’ve brushed shoulders with people who share that passion. That’s led to opportunities and the building of relationships with suppliers.”
SPA has been influential across pavement recycling and insitu stabilisation, road reconstruction, profiling, spray sealing and more, often developing solutions that are later adopted as standard across the roads sector.
The company has experience completing a variety of road construction projects. It’s also often the voice for the pavement sector, helping to represent and advocate
for improved outcomes. Just one example of SPA’s support for the industry is its partnership with AustStab – the Pavement Recycling and Stabilisation Association.
As a founding member, SPA is a keen supporter of AustStab’s efforts to create sustainable roads for future generations, as the only member-driven industry association in the world for pavement recycling and stabilisation.
Every day SPA is recycling the roads of local councils, helping to save money and disruption for the community while having minimum effects on the environment. Similarly, SPA is continually delivering major infrastructure projects.
SPA contributes to both Federal and State government projects, delivering over 130 kilometres of shoulder widening for VicRoads in 2020-21 alone.
The company’s expertise and track record in delivering projects for both the public and private sectors are just some of the reasons why SPA has been so successful.
Back to the future, SPA’s first pioneering reclaimer/stabiliser in the early days.
Reflecting on SPA’s 40th year anniversary, Smith says that without family, the company wouldn’t be where it is today.
“When I look back, it was a lot of hard work, and everyone contributed so much. All of us were doing that little bit extra to help the business,” he says.
“Even though we now have hundreds of employees, we’re still a family. The door’s always open. Doesn’t matter if it’s a health issue or something financial, our employees know that we’re happy to lend a hand.”
Smith says SPA has been instrumental when it comes to product development and regulation, thanks to the experience of its team and access to best-in-class facilities.
introduce new blends and improvements to foaming agents,” he says. “We’ve not only worked for SPA, but we’ve also worked really closely with our suppliers and brought them along with us.”
A core pillar and constant of SPA’s growth has been the organisation’s commitment to community and family, reflecting the attitudes of both Smith and Wilmot.
A big focus of SPA’s senior leadership team has been treating its employees like its customers – with respect, understanding and trust, helping to provide greater growth opportunities for the company.
“That loyalty is reciprocated by a lot of our employees, which also passes down to our customers,” Wilmot says. “We’ve built up that base of trust and created an environment where we’ve got people who are all like-minded, who want to do the right thing and are hard working.
“Our senior management predominantly consists of people who started with us on site, which goes to show that they’ve got a real understanding of the sector. That depth goes right across the business.
“They know what’s required and what it takes, and that experience is passed from the field to our offices. We’re passionate about the whole process and the sector. We never let a customer down and we don’t let our suppliers down.”
This is seen as step-by-step progress by SPA, ensuring that its solutions and specifications can provide positive outcomes for generations to come.
“A lot of our innovation isn’t just something out of the blue that’s totally different from everything else we’ve done.” Wilmot says.
“A lot of it comes from improving existing processes.
“We’ve spent a lot of our time improving our spreading techniques, improving our mixing ability and refining our mixes. We’ve made big strides in those areas.”
Having a diverse team with a variety of backgrounds and experience levels also contributes to continuing success, as Smith explains.
“It’s about innovating all the time and that’s supported by the environment that we’ve established where there are no dumb questions or ideas,” he says.
“We’ve found a nice blend between people who have been at the company for a long time and new, young people who are coming in. That cross-section is where our idea generation excels.”
David Berg, SPA Executive Director, shares the same sentiment.
“I joined SPA in year 1988 and have enjoyed being part of the growth to a national business, building a formidable team whilst encouraging the family ethos taken up eagerly by the team”.
Another major highlight throughout SPA’s 40-year journey has been the friendship between Smith and Wilmot. This decadeslong friendship has consisted of many tough decisions and “gambles”, all of which have helped to shape the company that SPA is today.
“It’s a pretty unique partnership,” Wilmot says. “We’ve learnt each other’s strengths and weaknesses. If I have a particular view and Warren (Smith) has another, we’ll usually meet halfway and that’s worked very well for us for years.
“Being able to work so well together, in combination has been one of our greatest strengths and it’s something that I’m very proud of.”
Both close friends say they’ve benefitted from challenging and pushing each other, an ethos that they’ve both instilled in SPA today.
“If you’re standing still, you’re going backwards,” Smith says. “You’ve got to keep on moving.”
“Everyone within our environment is a part of that process of continual improvement. That’s what excites me the most, that we’ve got so many inspired and intelligent individuals who will help to paint a brighter future going forward.
“That passion towards recycling, sustainability and cutting emissions will be fundamental to that future.”
TRT ESS* Platform Trailers give our customers a better return on investment from day one.
TRT’s all-axle intuitive steering package delivers faster maneuverability and unmatched control. All hydraulic functions are operated via proportional remote control, and with our modular quick-connect coupling system, you save both time and money.
Our gear lasts longer, pays for itself sooner, and has a lower operational cost.
*Electronic Steering System
TWO MEMBERS OF THE SUBURBAN RAIL LOOP (SRL)’S YOUTH PANEL REFLECT ON THEIR TIME PROVIDING FEEDBACK ON THE FUTURE OF VICTORIA’S TRANSPORT SYSTEM.
By 2050, Melbourne will be a city of nine million people, the current size of London.
Growing with the people, the city is changing to accommodate the needs of the future population.
As both a transport and urban planning project, Suburban Rail Loop (SRL) will deliver better transport, connecting suburbs and linking every major train service from the Frankston Line, in the east, to the Werribee Line in the west, via the Melbourne Airport.
SRL will support the delivery of more homes on the doorstep of public transport, services, jobs, schools, parks and cafés, greater connecting Victorians to employment, hospitals, universities and one another.
As part of Victoria’s Big Build, the Victorian Government is building Suburban Rail Loop (SRL) East from Cheltenham to Box Hill.
To help guide the project in the right direction for future generations, young Victorians were given the opportunity to provide their feedback on the SRL East underground stations, through the SRL Youth Panel, established in early 2024.
Following an expressions of interest process, the SRL Youth Panel – a group of 13 members aged 18 to 24-years-old –have been meeting regularly since March, discussing how best to increase housing supply and choice across Melbourne.
Two of those members included medical students Arvin Banerjee, a 24-year-old from Mount Waverley and Sophie Skuza, a 22-year-old from Clayton.
Both Sophie and Arvin came across the callout for the youth panel on Facebook and with an existing passion for change, both jumped at the opportunity to help.
Banerjee’s passion for improving the
application to the youth panel.
“The ability to get around and easily meet up with friends, family and the community is important and the SRL is a big part of that,” says Banerjee. “Everyone is really excited for the Sydney Metro, but I am looking forward to the SRL which is the Melbourne equivalent of what it can provide.”
The SRL youth panel is one of many projects Skuza has worked on in addition to her many advocacies through university.
“When I saw this opportunity I jumped on it because I love the thought of being able to shape change,” says Skuza.
“A lot of young people, including myself, have a lot of concerns around climate change and housing, so knowing this project is aiming to address those topics is important to me, and I wanted to be able to have a say in that.”
The panel discussions provided an opportunity for the community to have more in-depth conversations and provide feedback on a range of topics.
This feedback will be used to inform the draft structure plans and planning scheme amendments that will be exhibited later this year or in early 2025, when communities will have another opportunity to provide feedback.
correlated with the broad strokes of the project and what the panel wanted SRL to provide.
“One of the things we did was craft a vision for what we want the entire corridor of SRL to look like,” he says.
“Most things we touched on revolved around stations. We discussed how important it was for stations to have their own unique identity.
“SRL should develop and increase the attractiveness of the precincts around each station. For example, Anzac Station has been designed well, making the station itself an attractive place to be in and visit.”
Skuza says the value of cars within society dominated most of the conversation topics.
“We often discussed car spaces provided with apartments and how many cars we want to see on our roads,” she says.
“Some believed we should aim to remove as many cars as possible off the road and discourage car use as much as possible. Whereas some believed cars are important in our society, and that we should continue to promote their use.
“Other notable topics of conversation included increasing the amount of green space around stations, the importance of having diverse housing options, as well
as increased access to bus services and tram extensions.”
The future of housing is a question that plays on the minds of many, including both Skuza and Banerjee.
“Precinct development, zoning and housing is a particular concern for me,” says Skuza.
“I feel a lot of anxiety around finding housing in the future. But I do take a lot of comfort in knowing that the aim of this project is to help develop housing around these precincts and increase access to housing options for future generations.”
Similarly to Skuza, Banerjee worries if he’ll live in the same place he grew up.
“How can we grow up where our family, friends and community are without pushing other people out as well?” he says.
For this reason, Banerjee says the panel wishes to increase the housing supply by densifying housing around the SRL stations.
“We also discussed how many car parks should be supplied with apartments,” he says.
“Some of us thought that there should be less to encourage people to bike and to walk in their local areas. Whereas some people thought that there should be ample car parks for people to have the ability to drive or use the SRL.”
With the project due for completion in 10 years’ time, Skuza says it is important for today’s youth to be involved in planning for the next generation.
“Once completed it will connect a lot of universities, which is something I have struggled with as a medical student,” she says.
“I’ve had a lot of trouble commuting to placement at different hospitals, so
having the train line would make a huge difference because it will connect different hospital precincts like Eastern Health and Monash Health.
“SRL has the potential impact to mitigate the effects of climate change by taking cars off the road and that is something that will predominantly affect future generations.”
Although the number of attendees differed weekly, Banerjee says the diverse group of 13 provided a range of opinions and discussions.
“We had a lot of diversity with gender, location and demographics,” he says.
“Some of the panel had lived in the city for a long time, some were from the outer suburbs, and some moved from country Victoria.
“No matter where we were from, we all had similar experiences and frustrations with
current public transport and the general road infrastructure systems, which is why we wanted to contribute to the SRL.”
The panels’ common goal to better the state’s future set the precedent for respecting each other’s differing opinions, which Banerjee says promoted healthy debate.
“Panel members were able to self-regulate how much they were putting their hands up to talk, but we also had two great panel adjudicators who helped move the discussion along,” he says.
“We had differing opinions but given that we all have a similar goal, it was generally not difficult to get the conversation going.
“We all remembered we were there because we loved the idea of SRL, and we bonded over the opportunity for positive change.”
Lissa van Camp, Suburban Rail Loop Authority Executive General Manager, Land, Planning, Environment and Sustainability, says a key part of managing the future growth of the SRL is incorporating the community’s perspective.
“The Youth Panel is a unique chance for young Victorians to help shape the future of our city by having their say on plans for more housing, businesses and green spaces around the six new SRL East stations,” she says.
“Today’s young people will see the full benefits of Suburban Rail Loop.
“More housing choice around the stations means homebuyers have a better chance of owning a place near where they grew up –and more options for work, education and healthcare nearby.”
SINCE 2019, THE SNOWY MOUNTAINS IN NEW SOUTH WALES HAVE HOUSED THE SNOWY 2.0 TEAM AS THEY VENTURE ON AN ALMOST DECADE LONG PROJECT TO CONNECT TWO EXISTING DAMS OWNED BY ENERGY BUSINESS SNOWYHYDRO.
For 75 years, SnowyHydro has remained one of Australia’s leading integrated energy providers. The company ensures energy security and supports the transition to renewables through its Snowy Scheme.
The Snowy Scheme consists of eight power stations, 16 major dams, 80 kilometres of aqueducts and 145 kilometres of interconnected tunnels, sitting in the heart of Kosciuszko National Park in New South Wales.
Snowy Hydro manages 6400 hectares of the park and around 24,000 hectares of freehold land, including 600 kilometres of foreshore around storages including Jindabyne, Eucumbene and Tantangara.
Through the Snowy Scheme, Snowy Hydro has combined its power with gas and dieselfired peaking generators, distributing more than 5500 megawatts of generating capacity across New South Wales, Victoria and South Australia.
To continue the innovation of renewable energy across the south of Australia, SnowyHydro created Snowy 2.0.
In 2019, SnowyHydro commenced construction of the Snowy 2.0 project, which aimed to link two existing dams, Tantangara and Talbingo, through a 27 kilometre
underground tunnel and a new underground power station.
The Snowy 2.0 project is the next chapter in the Snowy Scheme’s history, a large-scale renewable energy project that will provide on-demand energy and storage to Australia’s southern states.
Once operational, rain and melted snow will fill one of two dams. When energy is required, the gates will open to allow water to flow through the middle where an underground pumped-hydro power station will generate power when water passes through it. It will provide on-demand power while reusing or ‘recycling’ the water in a closed loop.
Water will be pumped to the upper dam when there is surplus renewable energy production and the demand for energy is low, and then released back to the lower dam to generate energy when electricity demand is high.
The renewable energy efficiency will be maximised by using solar and wind energy to pump water to the higher dam, to be stored for later use.
It’s touted as the cheapest, most efficient way to provide large-scale energy storage –the equivalent of 2700 of South Australia’s ‘big batteries’.
The water then continues downstream where it is later released for uses such as irrigation for farms and environmental flows.
Four years away from expected completion, Snowy 2.0 will provide an additional 2200 megawatts of dispatchable, on-demand generating capacity and approximately 350,000 megawatt hours of large-scale storage
to the National Electricity Market – enough energy storage to power three million homes over the course of a week.
Planning and environmental approvals were received in 2020 from both the Federal and New South Wales governments. These approvals allowed construction to start on the project’s underground power station, waterways and access tunnels, as well as other supporting infrastructure.
As of July 2024, the Snowy 2.0 team has completed 570,000 cubic metres of excavation of the Talbingo intake, where water will exit and enter the tailrace tunnel, connecting the lower Talbingo reservoir to the underground power station.
Excavation of the Marica surge shaft has reached 95 metres. Once complete it will be one of the largest shafts of its type in the world. The 28 metre-wide and 250-metredeep surge shaft will be used for water storage and pressure relief when the power station starts up to absorb the momentum. Mechanical excavation including rock breakers and excavators continues, with drill and blast methods also being used.
Excavation of the gate shaft at Tantangara is now complete, with drill and blast work to excavate the transition tunnels linking it and the intake well advanced. The gate shaft is used to stop and start the flow of water into the headrace tunnel and power station for maintenance purposes, or in the case of an emergency.
TBM’S CELEBRATE WOMEN IN STEM
The main mode of machinery being used on the Snowy 2.0 project is the three Tunnel Boring Machines (TBM), named Florence, Lady Eileen Hudson and Kirsten.
Florence is 142 metres long and has an 11-metre diameter, as high as a three-storey building. This TBM is currently excavating the 16-kilometre headrace tunnel, which will connect the underground power station to the upper Tantangara reservoir.
Following a seven-week operation to use ultra-high pressure water jetting to remove very hard rock preventing the TBM from progressing, TBM Florence restarted excavation in July this year.
TBM Lady Eileen Hudson completed the 2.8-kilometre main access tunnel to the power station and is now excavating the sixkilometre tailrace tunnel.
The machine is progressing well and is approximately 3.0 kilometres into the tailrace
tunnel which will connect the underground power station to the lower Talbingo reservoir.
Kirsten was the TBM to complete the 2.9 kilometre emergency, cable and ventilation tunnel. It is now excavating the 1.6 kilometre Inclined Pressure Shaft (IPS – connecting the underground power station to the headrace tunnel that leads to the upper Tantangara reservoir).
TBM Kirsten has installed 14 trial tunnel lining rings in the IPS using locally manufactured concrete segments specifically designed for the high-water pressures that will be experienced in the IPS.
TBM’s Kirsten and Florence were named by students in the Snowy Mountains, who nominated groundbreaking Australian women in science, technology, engineering and maths (STEM) for the Snowy 2.0 TBM naming competition.
The winners were astrophysicist Kisten Banks and Australia’s first electrical engineer Florence Violet McKenzie. Lady Eileen Hudson made an enormous contribution as ambassador to the Snowy Scheme during its construction, along with her husband Sir William Hudson, the first Commissioner of the Snowy Mountains Hydroelectric Authority.
Since the project’s announcement in 2018, thousands of jobs have been created to deliver the project spanning nine years.
In 2021, construction of the 126-bed
Upon completion, the
accommodation development in Cooma was completed to house Snowy 2.0 workers.
The accommodation houses 140 modular units, accommodation for 90 single rooms and 26 self-contained units, communal facilities, parking and landscaping. More than 3000 people were building Snowy 2.0 as of August this year, with 1950 total camp beds available at Lobs Hole, Tantangara, Marica and Cooma available.
The Snowy 2.0 team is currently transporting power station components to site. The first power to come from Snowy 2.0 is expected in 2027, followed by the completion of the project in 2028.
WITH REAL AND MEANINGFUL REDUCTIONS AT FRONT OF MIND, FULTON HOGAN IS TRANSITIONING A NUMBER OF ITS ASPHALT PLANTS IN SOUTH EAST QUEENSLAND FROM DIESEL TO NATURAL GAS. RORY BRACKEN, HEAD OF CARBON AND CIRCULAR ECONOMY – FULTON HOGAN, EXPLAINS HOW THIS CHANGE WILL PROVIDE GREENER OUTCOMES FOR YEARS TO COME.
Resource use, carbon reduction, biodiversity and environment protection have long been pillars of Fulton Hogan’s efforts to create, connect and care for its local communities in an environmentally conscious way.
The company has also never been shy of setting itself significant goals.
Fulton Hogan builds essential infrastructure connecting communities across Australia and New Zealand. Building and maintaining bridges, airports and ports, and the nation’s communication networks generates carbon.
As demand for resilient infrastructure intensifies, so too does the need for it to be built in ways that are sustainable and in line with a net zero future.
So, while Fulton Hogan continues to build resilient infrastructure, the team understands the need to reduce carbon emissions by creating real reductions across its business.
Keeping it real and finding and funding solutions that reduce emissions in a meaningful way is a core philosophy.
As Rory Bracken, Head of Carbon and Circular Economy – Fulton Hogan explains, the drive to achieve better sustainable outcomes has led to greater internal analysis and improved sustainability results.
“Fulton Hogan has a scope 1 and 2 carbon reduction target of 30 per cent below 202021 levels by 2030. As an emissions intensive industry it is incumbent upon us to search out and investigate solutions that could support us to meet that target,” he says.
“Our view of the emissions reduction goal is that we wanted to engineer-out the carbon and look at existing technological
opportunities that would reduce our carbon footprint overall.”
Sustainability has long been intrinsic to Fulton Hogan’s operations. So has the perspectives and opinions of its staff, another factor that contributed to Fulton Hogan’s aspiration for greener outcomes.
“Through a number of staff surveys, it has been abundantly clear that there is a desire for greater sustainability outcomes from all of our staff, regardless of age or demographic,” Bracken says.
“Our team genuinely wants to see us doing our bit for the environment, for sustainability and for carbon reduction. They’ve been very clear that they want to see more tangible action on the ground.”
As part of its ambitious target, Fulton Hogan looked internally to identify areas that presented scope for improvement from a carbon reduction and business case
perspective. One of the most glaring was the company’s strong network of asphalt manufacturing facilities.
“Some of the biggest emitters within the business are our asphalt plants. Some of our plants, especially in Queensland, continue to run the burner on diesel. Diesel works fine from an asphalt manufacturing perspective, but it’s relatively carbon
intensive compared to other options out there,” Bracken says.
Per Business Wire, the global market for asphalt is projected to hit 183 million tonnes by 2027. Asphalt is clearly an essential material for the infrastructure sector.
Companies sector-wide are now looking at alternative methods of production to minimise asphalt’s environmental impact.
Fulton Hogan is at the front of the pack, pioneering sustainable change in this space.
Shortly after identifying the opportunity for change, Fulton Hogan underwent a thorough evaluation process, assessing the potential environmental and operational benefits of using alternative fuel sources for its asphalt manufacturing facility in Ormeau, South East Queensland.
As Bracken explains, natural gas was a clear standout quite early.
“Working through all of those checks and balances we discovered that natural gas was as good, if not better than conventional diesel as a fuel option,” he says.
“It’s a less carbon intensive fuel that’s available right now and is ultimately a very
practical and direct replacement for diesel in our plants. Most, if not all asphalt plants can accept natural gas with only minor upgrades,” he says.
Fulton Hogan’s switch to natural gas in Ormeau was only finalised a few months ago and is already providing 25 per cent less carbon intensity during production, Bracken says. The expectation is that natural gas will provide carbon savings in excess of 1600tCO 2 annually.
The change also aligns with a number of other Fulton Hogan asphalt manufacturing facilities across Australia, particularly in Victoria.
“Most of our other asphalt plants are already on natural gas. It’s the least carbon intensive fuel currently available that’s cost competitive and practical for our operations,” Bracken says.
“As most of our Queensland facilities run on diesel, natural gas was an obvious place to start.”
He says that on top of its apparent sustainability improvements, natural gas has also provided several operational and safety improvements to Fulton Hogan’s Ormeau site.
diesel and other hydrocarbon-based fuels, because it’s in a pipeline and it’s always on, which removes the risk of running out of capacity and delivery volumes,” Bracken says. “It’s available 24/7, whenever you need it. From a maintenance perspective, you don’t have any of the particulate build-up in the burner either. It also doesn’t take up much room on site, which is important for asphalt manufacturing facilities, where space is always at a premium.”
Bracken says he’s optimistic for the future of renewable energy sources, with Fulton Hogan constantly eyeing potential technologies and methodologies to utilise in future.
little to no disruption to the surrounding site, even throughout installation.
“We’ve never had any real issues with supply or demand. From a historical and long-term perspective, we were very comfortable with making the switch to natural gas because when we turned it on, we knew that we’d have gas readily available,” he says.
“It was a straightforward process, as the infrastructure that’s required for natural gas isn’t that significant.”
Fulton Hogan has already begun the transition to natural gas at its Narangba site, north of Brisbane, which is the next focus of its fuel transition program. Investigations are underway around transitioning additional facilities where viable, following the success at Ormeau.
As Bracken adds, natural gas could and should be considered a primary transitional fuel source in the future.
“As an existing, lower carbon-intensive fuel for asphalt plants, natural gas is a great opportunity to take up if it’s available.”
willing to change and adapt as technology and methods improve, understanding that natural gas may not always be the answer.
“We understand that natural gas is a transitional fuel providing support in our 2030 reduction and 2050 net zero carbon goals. Fulton Hogan understands that natural gas is not the final solution and that energy efficiency and electrification of
Hogan’s sustainable initiatives, including the use of Australian generated tyre derived materials and utilisation of over 500kWhp solar power installed at facilities around the country, as the company pushes closer towards its goal of being a net zero business by 2050.
“We are also proud of our Victorian Power Purchase Agreement that covers 100 per
“IT’S A GREAT THING THAT WE’RE DOING AND LAST YEAR SAVED OVER 8000TCO² FROM BEING EMITTED INTO THE ATMOSPHERE FROM PURCHASING GREEN ELECTRICITY.”
processes should continue where feasible. It also understands that where lower emission gases such as biomethane or hydrogen or liquid fuels such as renewable diesel become viable, they should be utilised in preference to non-renewable fuel sources.
“Our transition is ongoing as other fuel sources become viable. There are also other opportunities out there now that are competitive, which could help us to reduce our carbon emissions by over 30,000 tCO² annually,” he says.
cent of our facilities across our internal supply chain, from quarries, asphalt plants, bitumen blending, through to our offices and on site grid connected construction facilities. It’s a great thing that we’re doing and last year saved over 8000tCO2 from being emitted into the atmosphere from purchasing green electricity,” Bracken says.
“That’s what I’m most excited about, those tangible opportunities that we can make the most of today, and the sustainable innovations that are coming tomorrow.”
We raise, re-level & re-support sunken concrete, roads and buildings.
At Tyrecycle, we are committed to recycling end-of-life tyres otherwise destined for landfill. We are paving the way to produce more Crumbed Rubber Asphalt to cater to growing domestic demand with over $40 million invested in setting up new and upgrading plants, creating long term value for all stakeholders.
SRIPATH’S NUMIXER BITUMEN SOFTENER IS HELPING TO COMBAT THE GROWING ISSUE OF BITUMEN QUALITY VARIABILITY, WHILE ALSO BEING A FRIEND TO THE ENVIRONMENT. SEEM TOO GOOD TO BE TRUE? AS SRIPATH’S TEAM EXPLAIN, THIS SOLUTION IS REAL AND AVAILABLE NOW.
Sripath Technologies has long been an ally of the environment.
Acknowledging that it produces products that will inevitably impact the environment in some way, the company is determined to maximise sustainability gains wherever and whenever possible.
Deepak Madan, Chief Operating Officer – Sripath, says a passion for developing sustainable solutions has been intrinsic to the company’s success, with carbon reduction opportunities always front of mind during product design and delivery.
A big part of this focus is being open with customers, with a robust package of Environmental Product Declarations
(EPD) and sustainability reports ensuring that customers – and Sripath itself – can be fully aware of the environmental impacts of manufacturing, distributing and using the company’s products.
“Sripath has elected to embrace transparency as a key aspect of our business strategy,” Madan says. “Sustainability is an integral part of our corporate DNA.”
Sripath supports the adoption of enhanced circular economy concepts with minimal waste, with the company’s research and development team incorporating sustainability into every stage of a product’s development.
Sripath’s sustainable bitumen softener
NuMIXER is another tool in the company’s eco-friendly arsenal.
NATURALLY ENHANCING PROPERTIES
Sripath Technologies’ NuMIXER is a sustainable bitumen softener, produced from a blend of prime green bio-based oils, sourced from renewable crops that do not negatively affect food sources and production.
Sustainably sourced, NuMIXER also helps to reduce the user’s overall carbon footprint through multiple facets.
The product can be used and shipped at ambient temperatures, while also reducing energy consumption and lower greenhouse gas emissions.
NuMIXER also helps to tackle what is a growing issue in the sector. Bitumen quality variability is increasingly prevalent, with differing suppliers, transport methods and production processes leading to batches with fluctuating properties.
“Customers in Australia and New Zealand increasingly rely on imported bitumen. There used to be a time where refineries in the region were refining crude oil and producing bitumen of consistent quality,” he says.
“Now refineries around the globe are buying crude oil on the open market based on availability and price.
“They adjust their process to derive the best value-added fuel refining crude oil and producing bitumen of consistent quality.”
He says many bitumen suppliers and/ or users are using a range of additives to adjust the properties and performance of bitumen in an effort to mitigate the inherent variability in quality as a result.
“We’re even seeing customers in South Africa that are starting to feel the pinch because they’re not refining anymore and needing to import,” Madan says.
“They’re starting to realise that they need to change their mindset, from expecting the bitumen supplier to take care of the quality, to being able to take care of the quality themselves.”
It’s here that NuMIXER excels. As Krishna Srinivasan, President – Sripath Technologies explains, few products can help to improve the consistency, longterm performance and sustainability of bitumen simultaneously.
“NuMIXER is designed with sustainability at the forefront,” he says.
“It is an innovative bitumen softener, designed as an additive to help mitigate the inherent variability in the quality of bitumen that is fast becoming a global issue.
“It’s clearly an effective alternative to petrochemical oil-based products. NuMIXER not only mitigates the property deficiencies of bitumen and promotes durability, but also helps customers lower their overall carbon footprint and meet their net zero carbon goals.”
NuMIXER achieves this by decreasing
“NUMIXER, OUR ENVIRONMENTALLY-FRIENDLY BITUMEN SOFTENER, IS FAST BECOMING THE ADDITIVE OF CHOICE TO HELP ADJUST AND MANAGE THE PERFORMANCE PROPERTIES OF BITUMEN.”
stiffness and increasing the compliance value (m-Value) in poor quality binders while improving failure, fatigue and cracking resistance.
NuMIXER also helps to expand the low temperature range of bitumen.
This is achieved in part due to the product’s high potential to reduce the viscosity of bitumen. As an example, a five per cent NuMIXER addition can reduce bitumen viscosity by about 5-15 per cent.
Ravi Rajagopalan, General Manager, Sripath Asia-Pac, says NuMIXER has proven to be popular across the globe for close to a decade, due to its reliability and enhanced performance. Now, the next step is further use and growth across Australasia, as Rajagopalan explains.
“Increasingly, the bitumen and asphalt industry in Australia and New Zealand is embracing net zero carbon goals and focusing on sustainability,” he says. “NuMIXER, our environmentally-
friendly bitumen softener, is fast becoming the additive of choice to help adjust and manage the performance properties of bitumen.”
As with the majority of Sripath Technologies’ products, customers can view the full EPD for the NuMIXER to learn more about its sustainability properties and performance. As Madan explains.
“A big part of our sustainability strategy is continuous improvement. To go through the process of completing our EPDs allowed us to look right from the ground up, all the way through our supply chain, taking every step very seriously along the way,” he says.
“We provide easy access to all of our EPDs and Sustainability Reports, including NuMIXER, on our website.
“We have a robust pipeline of new product and technological development underway. Now, more than ever, sustainability is at the forefront of those new developments.”
FOUNDED ON THE PREMISE THAT THERE’S NO SUCH THING AS WASTE, RESOURCECO HAS FIRMLY SET ITS SIGHTS ON THE DECARBONISATION OF INFRASTRUCTURE DEVELOPMENT AND HEAVY INDUSTRIES THROUGH INNOVATIVE RESOURCE RECOVERY.
There’s not much that ResourceCo doesn’t recycle. From construction and demolition waste, commercial and industrial waste to soils and tyres, the company lives its commitment in making sure that waste is never wasted.
What most might view as ‘waste’, ResourceCo sees opportunity; resources that need not be sent to landfill – if the right mindset is applied.
In three decades, the company has repurposed more than 60 million tonnes of ‘waste’. In doing so, it has helped its customers leave a lighter carbon footprint with the abatement of over 2.5 million tonnes of greenhouse gas emissions.
Today, ResourceCo is one of the most diverse recyclers in the country, providing landfill avoiding resource recovery services alongside sustainable recycled products to multinational companies.
From tier one contractors all the way through to small business and independent operators, ResourceCo offers multifaceted
resource recovery services, with several sites holding the capacity to undergo cross functional operations.
It organises itself under four main pillars –recycling and waste, energy, soil reuse and recycling and tyre recycling.
With a national network of services and processing capabilities. Tyrecycle is one of Australia’s leading collectors and recyclers of end-of-life tyres.
Jim Fairweather, Tyrecycle’s Chief Executive Officer, says Tyrecycle’s offtake partners include Australia’s leading road surface finishers, who increasingly use the company’s highly refined crumb rubber.
“It goes without saying, when it comes to road infrastructure in Australia, quality is paramount, and we pride ourselves on the quality products we supply into the sector,” says Fairweather.
“What is also becoming increasingly important is sustainable infrastructure.”
Fairweather says every tonne of Tyrecycle’s crumb rubber used in asphalt mixes represents a potential greenhouse gas saving of 2463 kilograms of carbon dioxide emissions.
Meaning, decarbonised infrastructure outcomes have shifted from a ‘nice to have’ to a ‘must have’.
“We’ve seen a real uplift in the Australian crumb rubber market,” he says.
“In recent years our crumb capacity has tripled to 30,000 tonnes. Last year we achieved approximately 20,000 tonnes per annum sold domestically.
“We have plans in place to push that up to 30,000 tonnes per year, off the back of domestic demand.”
Annually, Tyrecycle collects in the order of 20 million tyres, to put that into perspective, if every tyre were to be lined up next to each other, the total length would equate to a return trip from Perth to Sydney.
In addition to crumb and granules,
a low recycling rate, which in the eyes of the teams at ResourceCo and Tyrecycle, presents an exciting opportunity.
“Currently approximately only one per cent of mining tyres are recycled, the rest are buried in pits or left on site,” he says.
“We are working closely with the resources industry as we build Australia’s first dedicated OTR tyre recycling plant in Port Hedland, Western Australia.
“It will be a game changer for the industry and will be operational by mid-November.”
Tyrecycle manufactures tyre-derived fuel (TDF), an alternative fuel source that’s decarbonising heavy industries.
TDF is utilised to displace the use of fossil fuels in high-energy consuming industries, such as in kilns in the production of cement.
Fairweather says most of the fuel is sent to Japan and Korea, who are actively looking for non-fossil fuel energy sources.
“Not only does our TDF reduce an industrial reliance on fossil fuels, its high calorific value means it also emits significantly lower levels of carbon dioxide,” he says.
“Meaning TDF has a better carbon dioxide equivalent emissions profile than the typical fuels consumed by our customers.”
On the continued growth path, Tyrecycle is focusing significant energy on the recycling of mining truck tyres. Fairweather says these off the road (OTR) tyres have
The cornerstone of ResourceCo’s resource recovery heritage is the sorting, refining and remanufacturing of C&D (Construction and Demolition) waste into a wide array of products to be used for civil construction applications.
Brad Lemmon, ResourceCo Recycling and Waste Chief Executive Officer, says the company receives more than one million tonnes of C&D waste each year, 99 per cent of which is recycled into new products for various markets.
“ResourceCo offers a genuine one stop shop service to the civil infrastructure sector,” says Lemmon.
“Trucks arrive at our strategically located sites, loaded with C&D material to tip off, when they leave the same trucks can be loaded with high quality products, ready for supply to the same or another site” he says.
ResourceCo is continuing to build on its capability of offering the market
rubble and aggregate products that meet technical specification.
In acknowledging the evolving requirement for infrastructure projects to have greater sustainability outcomes, Lemmon says ResourceCo is adding to its offering. Sites are now contributing to a project’s Green Star Building accreditation, along with outgoing products having Environmental Product Declarations (EPD).
“Our customers place a genuine value in landfill diversion services and materials that meet technical and sustainability requirements,” he says.
“This is why we’ve worked with the likes of renowned sustainability consultants thinkstep and PINDA Life Cycle Thinking, who have assessed and verified the environmental footprint of ResourceCo’s products. This includes the potential of global warming and land use impacts which are associated with the company’s products.
“With many products already registered with EPD Australasia, ResourceCo is demonstrating how we can genuinely and verifiably help our customers achieve sustainability benefits for their projects.”
ResourceCo’s C&D waste disposal service is complemented by its commercial and industrial (C&I) waste management services.
Henry Anning, Chief Executive Officer of ResourceCo’s Energy business says ResourceCo’s landfill diversion of C&I waste maximises the inherit value of all material. This is achieved through mechanical sorting and separation methods, ensuring
that waste is segregated into different material streams.
“Lighter than C&D waste, due to its highly variable composition, C&I waste is often, and easily sent to landfill,” he says.
“That’s where we step in, we sort the material to extract glass, metals, timber and inert fractions for further recycling.”
Anning says the company then refines residual material further to produce an alternate fuel source for high energy consuming industries.
“Our processes yield an approximate 95 per cent landfill diversion rate which is great for our customers and the environment,” he says. “This alternate fuel source not only avoids an end of life in landfill, but directly aids in the development of more sustainable infrastructure. Using our fuel reduces our customers’ emissions, giving them the ability to have a more sustainable product and service to offer to the market.”
Whether the task is transforming waste soil into products for new markets or relocating materials directly for reuse, Steve Harrison, ResourceCo Soil Reuse and Recycling Chief Executive Officer, says ResourceCo demonstrates a unique ability to manage a wide range of soil needs.
“Our soil reuse and recycling services provide reusable, structural and sustainable soil export and import solutions across the country,” he says.
Harrison says the company prides itself on the live tracking of end-to-end material movement linking drivers to solution sites. This chain of custody service can
be integrated into customer portals and adds to the company’s continued soilbased innovations.
With a demonstrated track record of successfully delivering some of Australia’s largest road infrastructure projects, including the WestConnex project in Sydney and the North East Link project in Melbourne, the soil reuse and recycling team has a solid foundation to leverage further growth.
“In addition to bulk excavation material movement, we supply and manage the placement of fill materials that are reused in rehabilitation projects, such as in quarries, agricultural or land improvement projects,” Harrison says.
By applying ResourceCo’s groupwide philosophy of maximising the potential of all resources, Harrison
operations have evolved significantly in recent years.
“By adopting the methodologies of sorting, screening and treating the soils we handle, we are now in the space of manufacturing different types of commodities, ready for resupply into the market,” he says.
“When it comes to soil, we’re committed to doing as much as we can for our customers. We export soil, we sort it, sift it and blend it. We select the best products for our customers’ needs and, if part of a rehabilitation project, we oversee the placement of material too.”
Harrison says the capability to give soil new life strongly aligns with and complements ResourceCo’s other materials recycling operations.
The basis of ResourceCo’s growth, regardless of its various operations, has always focused on working closely with its customers to understand their waste disposal and product supply needs.
“It doesn’t matter which part of ResourceCo’s operations someone looks at, providing efficient and sustainable outcomes for our customers is central to what we do,” says Harrison.
Adapting to the changing needs of the markets within which ResourceCo operates, Harrison says the company will continue to work with infrastructure partners to expand on its sustainability and performance standards.
“Wherever we can, we try and refine our processes to ensure that the changing needs of the market are always met,”
HAMIDREZA SAHEBZAMANI, KANJANA YINDEE
n the dynamic field of road construction, where escalating demands, increasing traffic loads, and extreme environmental conditions intersect, the combination of innovation and sustainability is no longer a luxury, but a priority.
As the globe struggles with the intensifying threats of global warming and the imperative to limit carbon emissions, the road construction industry faces a dual challenge: to revolutionise its practices while responsibly using limited resources.
Innovative products and construction methodologies that can withstand heavy loads and harsh climates, yet minimise environmental impact, are crucial for sustainable development. Using green materials, recycling existing road surfaces, reducing pavement thickness, increasing the longevity of road lifespan, and energyefficient construction techniques are examples of sustainable innovations that not only preserve the environment, but also ensure resilience and cost-effectiveness.
Prioritising sustainability and innovation in road construction not only aligns with global environmental targets, but also delivers tangible benefits by creating infrastructure that can endure the test of time and adapt to future demands.
SAMI Bitumen Technologies, established in 1978, has been a pioneer in the Australian roads industry, meeting the market demand for advanced bitumen technology. The company prides itself on providing a reliable
and consistent full range of high-quality bituminous products for the construction of critical infrastructure, suitable for projects such as highways, bridges, runways, and local roads.
SAMI’s commitment to sustainability is ingrained in its operations, as it continually strives to develop environmentally friendly solutions that contribute to the long-term durability of Australia’s road network.
SAMI’s R&D sustainability initiatives are built on three key pillars. The first is encouraging the use of cold technologies in pavement construction and maintenance.
The second is the development of highperformance binders that enable roads to last longer with reduced thickness. The third and final pillar is advancing low-carbon emission products.
The utilisation of cold technologies has the potential to greatly reduce the carbon footprint associated with pavement construction and maintenance. As part of SAMI’s development strategies, there is a focus on the development and promotion of new, specialised high-performance emulsions. These emulsions play a vital role in enhancing the performance of pavement materials, while also contributing to sustainable and environmentally friendly construction practices. By embracing these innovative technologies and advancements in emulsion formulations, SAMI aims
to further minimise the environmental impact of the construction industry while delivering high-quality and durable pavement solutions.
Australia boasts one of the largest road networks per capita globally, spanning over 870,000 kilometres. Approximately 40 per cent of this network is paved using various bituminous products. These road surfaces typically involve essential applications such as prime coats, initial seals, SAMI seals, and spray seals. However, it is unfortunate that a significant quantity of cutback products are still utilised.
Surprisingly, the road industry in Australia consumes a high amount, approximately 12,000 tonnes, of kerosene and 15,000 tonnes of diesel each year in the production process, excluding the fuels themselves.
Australia remains one of the largest consumers of cutback products globally, despite being one of the pioneering countries to adopt bitumen emulsion approximately 100 years ago. Regardless of the underlying reasons, the current outcome is undesirable, emphasising the need for a change in mindset. This significant quantity could be greatly reduced by replacing cutbacks with bitumen emulsions, resulting in an annual decrease of approximately 12,300 tonnes of CO2e emissions, according to the AfPA (Australian Flexible Pavement Association) LCA (Life Cycle Analysis) calculator.
Bitumen emulsions play a crucial role in
various aspects of flexible or composite pavement construction, maintenance, and preservation. From the base layers, where emulsions (ETB) can be used to treat base courses, to surface layers where structural cold wearing courses known as grave emulsions can be applied, they offer a wide range of benefits.
Emulsions serve as penetrating prime coats, primer seals, and tack coats with high shear strength. They can be sprayed as fog seals, rejuvenating/enrichment seals, or scrub seals to extend the lifespan of aged surfaces and effectively seal them to prevent water penetration.
The use of bitumen emulsion in the world has always been growing due to the expansion of road construction and maintenance activities, as well as its substitution for cutback products and conventional hot applications. According to the key figures from IBEF (International Federation of Bitumen Emulsion) in 2022, the global consumption of bitumen emulsion amounted to 10 million tonnes, accounting for eight per cent of the total global bitumen consumption.
SAMI Bitumen Technologies has been a pioneer in bitumen emulsion innovations and production for nearly half a century. SAMI offers a range of unique products tailored for various applications.
Two well-known emulsion primes from SAMI are SAMIprime K2 and K2P, which are commonly used as prime coats for granular, stabilised, and concrete base
spray sealing applications.
SAMIflex covers a range of highperformance polymer-modified emulsions suitable for spray sealing and Stress Alleviating Membrane Interlayers. These examples exemplify SAMI’s commitment to research, development, and promotion of bitumen emulsion within the industry, bridging the gap between Australia and global standards.
SAMIfilla EC is a specially formulated, highly polymer-modified emulsion with a thixotropic effect, capable of filling cracks without the need for heating.
The development of high-performance binders is a critical aspect of constructing sustainable and long-lasting roads, summarised in the strategic approach in this pillar. The logic behind this strategy is straightforward yet reflective: the most
higher carbon emissions from vehicles when compared to driving on smooth roads. As such, ensuring that a road is as smooth as possible is an essential consideration in sustainable road design and construction. In response to the demand for more sustainable and durable road materials, SAMI has introduced a product known as I-Brid. This highly modified binder represents a significant innovation in road construction materials. It is a hybrid binder that incorporates a mix of additives from various sources, fitted to enhance the pavement’s performance. I-Brid’s unique formulation delivers superior resistance to rutting, which is the permanent deformation of the road surface under the stress of traffic loads, particularly in hot weather.
Additionally, the binder exhibits excellent fatigue resistance, meaning that it can withstand repeated loading from traffic without cracking prematurely. The
“SAMI BITUMEN TECHNOLOGIES HAS BEEN A PIONEER IN BITUMEN EMULSION INNOVATIONS AND PRODUCTION FOR NEARLY HALF A CENTURY.”
sustainable road is the one that lasts the longest. It is counterproductive to build roads with minimal carbon footprints if they degrade quickly and require frequent repairs or replacements. Therefore, the durability and longevity of the pavements are of utmost importance when considering the sustainability of road infrastructure.
importance of such a property cannot be overstated, as roads that resist fatigue maintain their integrity for longer periods, reducing the need for maintenance and the resources associated with it.
Moisture sensitivity and fuel resistance are other critical properties addressed by the I-Brid binder. By resisting the damaging effects of water and fuel spillages, the road’s remains consistent regardless of exposure to
by reducing the thickness of pavements. This approach has been recognised as a significant arm in the pursuit of sustainability. France has long been utilising high-modulus asphalt with EME2 binders, a durable and long-lasting pavement structure.
Through the promotion of EME2 and the development of the I-Brid binder, SAMI is contributing to the construction of roads, airports, ports, and racetracks that not only have a reduced environmental impact during their construction phase, but also promote sustainability through their enhanced durability, longevity, and reduced maintenance requirements.
This innovative material answers the pressing need for infrastructural solutions that are both environmentally responsible and economically viable, ensuring that the roads that are built today can serve the needs of tomorrow without compromising the planet’s health.
The third pillar of SAMI’s sustainability initiative emphasises the adoption of low-carbon emission products, a step that reflects a critical awareness of environmental responsibility within the industry. Central to this endeavour is the introduction of SAMIGreen, a groundbreaking product line that incorporates partially biogenic additives. The development of SAMIGreen is the result of extensive research dedicated to identifying a biogenic source that maintains the binder’s performance both in short and long-term ageing.
sustainability and product efficacy,
SAMIGreen binders represent a significant innovation. These binders can be formulated into various grades of Polymer Modified Bitumen (PMB) suitable for diverse applications in asphalt and spray seal projects. Furthermore, they have been smoothly emulsified to craft low-carbon polymer-modified emulsions.
A remarkable feature of SAMIGreen is its technical profile, which mirrors that of traditional binders while cutting the carbon footprint by more than 50 per cent. This substantial reduction illustrates SAMI’s commitment to cutting-edge, ecofriendly products. The whole-life embodied carbon of the pavement is considered when designing SAMIGreen. This means that by using SAMIGreen, the quality and technical performance of the road will not be compromised, and the road will remain as long-lasting as it should be.
Hybrid modifications of bitumen are a relatively new concept in bitumen modification, where two or more different additives with different natures are used as modifiers in bitumen. This allows the sector to take advantage of the different benefits offered by each additive while limiting their disadvantages.
One popular method of hybrid modification is the simultaneous use of crumb rubber and elastomeric additives. This approach helps maintain the desired technical properties while reducing the need for elastomeric additives, which typically have a carbon footprint of over 5000 kilograms of CO2e per tonne of product.
tyres, SAMI aligns with the principles of the circular economy. Furthermore, crumb rubber has a significantly lower carbon footprint compared to elastomeric additives and even pure bitumen in the Australian context, with emissions of 376 kilograms CO2e per tonne for crumb rubber versus 425 kilograms CO2e per tonne for bitumen.
Crumbflex is a hybrid polymer-modified binder developed by SAMI, which incorporates both elastomeric additives and crumb rubber simultaneously. This binder can be produced in various grades of modification, offering the same technical properties as traditional PMBs but with approximately 10 per cent less carbon footprint.
By combining Crumbflex with SAMIGreen products, the company can maximise the advantages of low-carbon footprint products while ensuring the preservation of desired technical properties. The unique engineering composition of elastomeric additives, crumb rubber, and biogenic additives has resulted in a polymer modified binder with an impressive 70 per cent reduction in carbon footprint.
Innovation is at the heart of SAMI’s success story. Over the years, the company has invested heavily in research and development, pushing the boundaries of bitumen technology to provide cuttingedge solutions to its customers.
The company’s forward-thinking approach enables it to adapt to the ever-evolving needs of the road industry, delivering innovative products that enhance the
Leading local trailer solutions supplier, MaxiTRANS, has changed its name to Freighter Group.
The new Freighter Group stands for something more powerful than ever before. It stands for being ready.
Ready to push boundaries, deliver excellence and to help you go further. Be part of a new era in transport. freighter.com.au
AS ALEX FRASER CELEBRATES ITS 145TH ANNIVERSARY, ROADS AND INFRASTRUCTURE REFLECTS ON THE COMPANY’S JOURNEY TO BECOMING ONE OF AUSTRALIA’S LEADING PROVIDERS OF RECYCLED CONSTRUCTION MATERIALS.
Alex Fraser is one of a few Australian companies to have 145 years of operation behind them. An extraordinary milestone and long history of success, which Alex Fraser attributes to its investment in its people and its business.
With a diverse team of people and a network of recycling facilities and asphalt plants across Brisbane and Melbourne, Alex Fraser has recovered and recycled more than 58 million tonnes of concrete, brick, rock, asphalt, and glass. All used to produce specification products needed to build greener roads and infrastructure.
Established in 1879, Alex Fraser was a founding member of a metal broker firm in Queen Street, Melbourne, run by the
Alex Fraser’s recycling and asphalt operations work with local governments, contractors and asset owners to build greener roads throughout Melbourne and Brisbane, reducing the carbon footprint of construction by up to 65 per cent.
By choosing Alex Fraser’s Green Roads Construction Materials, developers and government have helped to save carbon emissions and reduce heavy vehicle traffic.
In 2019, Alex Fraser invested in Victoria’s first licensed glass recycling plant at its Western Sustainable Supply Hub, with capacity to process more than 150,000 tonnes of glass per year, equating to around four million
of recycled glass, asphalt, and plastics into sustainable Green Roads asphalt mixes. It also launched its first Sustainable Supply Hub in Melbourne’s west, integrating the asphalt plant, glass plant and a construction and demolition (C&D) plant to recycle high volume waste into quality construction materials.
One year later in 2020, Alex Fraser’s Clarinda Recycling Facility installed an additive bin – partly funded by Sustainability Victoria’s Resource Recovery Infrastructure Fund grant – used to blend recycled glass sand and brick into a new, sustainable roadbase product. Melbourne’s northern suburbs were the next destination for a new facility, when Alex Fraser commissioned its new asphalt plant
new rock crushing plant, was commissioned in June this year, with further additions due for completion in 2025. The plant is expected to process up to one million tonnes of recycled products, including paddock rock and reclaimed asphalt pavement.
The end product also feeds Alex Fraser’s neighbouring Epping Asphalt Plant to produce high-recycled sustainable asphalt, containing up to 70 per cent recycled materials.
Alex Fraser Managing Director Peter Murphy says the hub will maximise sustainability outcomes for Melbourne’s north, boosting the current recyclable market.
“Our facilities are customers’ one-stop shops to recycle construction material including paddock rock, brick, concrete and asphalt profilings, and to source highrecycled construction materials and lowercarbon asphalt,” he says.
Murphy says Alex Fraser’s innovations are instrumental in fostering a safe environment while maximising operational efficiency in the plant.
“Process improvement is constant and soon we’ll see the introduction of more technology supporting material detection and sorting accuracy, which will also reduce manual handling,” he says.
Quintessential to Alex Fraser’s identity is its tagline ‘Building Greener Roads’, which has become synonymous with improving sustainability outcomes on large infrastructure projects. Through the implementation of the Victorian
Government’s Recycled First Policy, Alex Fraser was well-positioned to supply quality, recycled construction materials and support Victoria’s Big Build, with recycled content proactively considered in bid and tender requests.
In 2023, Alex Fraser supplied more than 465,000 tonnes of its Green Roads Construction Materials, contributing to an expansive list of works across the Level Crossing Removal Project and the Big Build, including the Sunbury and Epping road redevelopments.
Specifications that clearly support the use of recycled materials have proven to be critical to standardising the industry’s uptake of circular construction products. With innovation at the forefront of operations for Alex Fraser, trials like ‘Recycled Tyres
for Sustainable Roads’ demonstrate how the use of recovered carbon black (rCB) in asphalt can be built to build greener roads for Victoria.
Alex Fraser’s Green Roads Recycled Glass Sand is another example of innovation and has been extensively used in compliance with VicRoads.
Murphy says that collaboration supports Alex Fraser’s commitment to sustainability.
“Collaborations, such as partnerships with infrastructure agencies, ecologiQ and our long-standing customers have been the key to increasing the use of recycled materials in infrastructure projects, contributing to a more sustainable and thriving circular economy,” he says.
Alex Fraser’s fierce advocacy and knack for pushing the envelope is a sure sign of the company’s continued success in being a leader, and pioneer in the recycling space.
FOR OVER THREE DECADES, MAINMARK HAS BEEN ONE OF THE LEADING PROVIDERS OF REHABILITATION AND MAINTENANCE SERVICES FOR CULVERTS AND OTHER HORIZONTAL INFRASTRUCTURE ACROSS AUSTRALIA AND INTERNATIONALLY. ROADS & INFRASTRUCTURE SITS DOWN WITH TOM BAILEY, INFRASTRUCTURE & MINING MANAGER, NSW/ACT – MAINMARK, TO LEARN MORE.
Although often overlooked by the general public, culverts are crucial in maintaining the efficiency and safety of critical infrastructure connections such as bridges, roads, and railways.
Typically constructed from concrete box sections, corrugated steel, or concrete pipes, culverts are engineered to manage stormwater runoff by controlling water flow beneath these vital transport corridors. Many also provide safe passage
for wildlife. Their design and maintenance must adhere to stringent standards to protect waterways and ecosystems and the communities and infrastructure that rely on them.
Leaking pipes and culverts beneath roads can lead to significant damage, including the formation of potholes, cracks, and road settlement. As water erodes the subbase and subgrade materials, roads can develop uneven surfaces or even collapse, increasing
the risk of dangerous driving conditions.
In more severe cases, erosion can create sinkholes, posing serious vehicle safety hazards. These issues compromise road safety and lead to costly repairs and disruptions. For railways, similar problems arise when erosion weakens the ground beneath tracks, potentially causing subsidence, track misalignment, and derailment risks.
In addition to direct road and railway damage, leaking culverts and pipes can disrupt utility lines that run alongside or beneath transport infrastructure, leading to service outages and further complicating repairs.
The cost of frequent maintenance and emergency repairs escalates as persistent leaks weaken these structures, reducing their lifespan. Proactive maintenance, such as utilising Teretek® resin injection, can prevent such issues, ensuring that roads, railways, and their surrounding infrastructure remain safe, functional, and long-lasting.
This is where Mainmark’s expertise comes into play. As specialists in ground engineering and asset preservation, Mainmark brings extensive experience and a proven track record in culvert maintenance and rehabilitation.
Tom Bailey, Infrastructure & Mining Manager NSW/ACT – Mainmark, says deteriorating culverts can negatively impact the integrity of surrounding infrastructure.
Teretek Resin Injection offers a fast, non-disruptive, and cost-effective solution for filling voids, re-levelling subsided structures, and improving ground stability. This technology, which has been tested and adopted by infrastructure authorities across Australia, is used to strengthen the areas around culverts and the supporting soils.
According to Bailey, injecting the resin into these areas helps fill voids, reinforce the ground, and prevent potential structural failures. Additionally, the weakened soils beneath roads can be treated, subsidence corrected, and road levels restored. The entire process can be conducted either from above, where access is limited, or from within the affected structure itself.
Mainmark’s team carefully assesses each situation, drilling a series of holes based on a predetermined injection sequence to ensure the material is applied to the most effective areas. The results are equally effective whether applied above ground or from within the structure.
Most projects can be completed in just a day or two, with very little operational interruption, allowing the community to quickly regain access to the crucial roadway with minimal disruption.
Since Teretek does not negatively affect groundwater, soil, or local wildlife, the work can be conducted without any impact on the surrounding environment.
Mainmark received a Good Design Award in the Engineering Design category for its innovative solution in repairing and futureproofing vital drainage culverts on the Toowoomba Bypass, a major Queensland infrastructure project aimed at improving freight connections and reducing local road congestion.
Mainmark also offers an efficient solution for abandoning culverts or pipes in place with its innovative Terefil technology.
Terefil is a lightweight cellular concrete (LCC) created by combining cement and sand (or just cement) with highly airentrained slurry, achieving a cast density range of 500 to 1200 kilograms/metres³. This air entrainment, produced by introducing preformed foam with encapsulated bubbles, results in a pumpable, free-flowing material that solidifies into a lightweight, stable fill upon curing.
Terefil is ideal for culvert and pipe abandonment due to its ease of application and unique properties. When pumped into culverts or pipes, it completely fills the space, solidifies, and forms a stable structure that prevents future collapse or voids, ensuring long-term integrity beneath roads and railways.
costs, making it a cost-effective option.
Additionally, Terefil is environmentally friendly, using fewer raw materials and contributing to sustainable infrastructure solutions. These benefits make Terefil a preferred choice for projects that require stable, long-lasting abandonment and filling solutions. According to Bailey, Mainmark Australia collaborates closely with asset owners and project stakeholders to identify the fastest and most efficient solutions for every situation.
“No matter the circumstances, the result is the same,” he says. “With our expertise dating back to 1989, we understand what it takes to restore, extend the lifespan, and repair damage to critical infrastructure.”
He emphasises that these outcomes are achieved with significantly less cost, time, and disruption compared to conventional methods – an important factor, especially for high-traffic road and rail networks.
And Mainmark isn’t stopping there.
“Holistically, as a business, we’re innovators. We’re constantly looking at improving our methodologies and our
technologies,” Bailey says.
“We’re constantly working with other specialists in the no dig and trenchless technology space. It’s great to have the opportunity to make a difference by extending the lifespan of infrastructure. With population growth and ageing infrastructure, it’s an issue that isn’t going away.
“It’s a growing area and a growing need. It’s exciting to be able to help asset owners and entities.”
For more information on Mainmark’s innovative Teretek & Terefil technologies, visit www.mainmark.com
Enrol today - afpa.asn.au/registrations/
IN CREATING THE JCB E-TECH RANGE, JCB HAS REDISCOVERED THE POWER IN INNOVATION, PRIORITISING THE DELIVERY OF NET-ZERO TARGETS.
JCB has pioneered a range of 100 per cent electric machinery as it works towards a more sustainable future.
Just as electric vehicles on roads are becoming routine, the use of electric machinery in green construction and agriculture is also on the rise.
JCB has perfected its electric machinery with zero emissions, displaying many benefits over its diesel counterparts, allowing its customers to meet their sustainability goals without compromising performance.
Clients in the construction industry have welcomed the rise of electric machines which benefit not only the environment, but also individuals and the wider community.
The range of JCB E-TECH machines offers customers a sustainable and ecofriendly solution for their construction equipment needs.
The machines available in the Australian range include a telehandler, site dumper, mini excavator, dumpster, teletruk, powerpack, wheel loader, articulated boom and access lifts.
Greg Sealey, JCB CEA National
Wholegoods Manager says making the transition to electric-powered machinery offers municipalities the chance to enjoy a range of benefits including quieter operation, minimal service requirements, cleaner air quality in urban areas and reduced carbon emissions.
“Our range offers not only advantageous environmental benefits, but also enhanced efficiency in daily operations and lower long-term operating costs,” says Sealey.
“JCB is focused on building a future where innovation meets sustainability, with machines that are designed to not only shape the world but also to protect it.”
In early 2021, JCB revealed its first ever hydrogen engine using and adapting engine technology, the hydrogen combustion engine delivers power in the same way as a diesel engine – but importantly with zero carbon dioxide at point of use.
Sealey says JCB’s focus on clean energy remains paramount whether the focus is on equipment or broader construction sites and projects.
“JCB is dedicated to creating sustainable
solutions that leave a positive impact on our planet,” he says.
“JCB’s investment in the electric range is a great example of how industry can make this happen.”
When choosing from JCB’s electric range, potential customers are making the active decision to reduce harmful emissions and lessen their environmental impact.
This can be done through the E-TECH’s range promising zero emissions of carbon dioxide, nitrous oxide and particulates into the atmosphere.
Sealey says power remained a focal point when JCB engineers created the line, using powerful Lithium-Ion technology which can power up to three hours of use on a single charge.
“In creating the E-TECH range, JCB wanted to remove as many barriers as possible when it comes to making the switch from standard diesel machinery to the electric range,” Sealey says.
“When designing the range, JCB made sure its electric charging solutions were simple to use and delivered enough power to keep operators productive in any environment.
“That is why they also designed a universal
fast charger which is compatible with JCB’s 100 per cent electric, zero emissions E-TECH range, eliminating the need for multiple charging solutions.”
Machines can be charged in as little as 2.5 hours, with fast charging options available to get machines ready for work even faster.
In addition to rapid charging times, there are no engine revs with the electric range, resulting in reduced noise levels.
“This makes the range ideal for noisesensitive environments such as residential areas. It also means work can continue after hours when working towards a deadline,” he says.
“Clients gain the freedom to work anywhere, anytime with our E-TECH range, whether it be indoors, outdoors or underground.”
Sealey also says due to the low noise levels, zero emissions, and lack of electrical wire hazards, customers can now work more safely onsite.
The Telehandler 525-60E, which is part of JCB’s E-TECH range, works safely and efficiently on-site with adaptive load control to prevent tipping. With a lift capacity of 2500 kilograms at full height, 720 kilograms at full reach and a max lift capacity of 2000 kilograms, the telehandler has the strength of its diesel counterpart while having the added benefit of zero emissions, low noise levels, and many other innovative features.
Like the JCB wheel loader, the Site Dumper 1TE is a fully electric machine that challenges perceptions of where site dumpers can
operate. With seven kilowatt continuous and 20 kilowatt peak power, the 1TE matches the power of a diesel one tonne dumper. The machine can operate indoors and in noise sensitive environments due to its near silent operations and powerful LED work lights which allows for ‘out-ofhours’ working.
Accompanying the Site Dumper ITE is the award-winning Mini Excavator 19C-1E. It delivers the same power as the diesel model, only with zero emissions and low noise levels. With a maximum dig depth and dump height of 2.81 metres, the 19C-1E is ideal for indoor and urban settings. The 19C-1E has maintenance free batteries,
and high carrying capacity of 500 kilograms the electric dumpster works in harmony with the E-TECH mini.
To complete the electric range, customers have the choice of two teletruk models, the Teletruk 30-19E and 35-22E. The JCB electric Teletruk telescopic forward reach range is designed to deliver maximum power when space is at a premium. Equipped with a telescopic boom, small turning circle and single side loading ability, the 30-19E allows operators to do more materials handling work.
Assisting with all operations is the JCB Access range. This range includes the electric scissor range, developed to
A municipal works, civil and commercial construction event.
17-18 September 2025, MCEC
In September 2025, a new event will be landing at the Melbourne Convention and Exhibition Centre. Converge will bring together leading decision makers in the Municipal Works, Civil and Commercial Construction space, to share the tools, ideas and technologies that are shaping these sectors.
BOMAG SINGLE DRUM ROLLERS HAVE ADDED EVEN MORE FIREPOWER TO THOMAS KINGSLEY RESOURCES’ (TKR) IMPRESSIVE EQUIPMENT HIRE RANGE. BUT WHAT MAKES THEM DIFFERENT? TKR DIRECTOR JAMES ANDERSON EXPLAINS.
largest providers of wet and dry hire equipment to the civil construction industry across Queensland and northern New South Wales,” he says. “We have a broad range of equipment and quality brands across rollers, excavators, dozers and graders that make up our fleet.”
As part of this push, TKR has made a commitment to constantly assess the latest machinery that the sector has to offer, to ensure that it can stay up to date and even ahead of industry standards.
“A few years ago, we decided to add compaction equipment to our fleet, due
respected and reliable compaction equipment manufacturer. This led TKR to BOMAG equipment.
Five years ago, TKR engaged Tutt Bryant Equipment (Australian National BOMAG distributor) to learn more about the supplier’s range of single drum rolling equipment.
This connection, which began after one of Anderson’s former machinery supplier contacts made the switch to Tutt Bryant, has grown considerably. TKR is now one
internal roads.”
Anderson says that from TKR’s existing range, BOMAG’s 13 tonne option stands out as a market favourite.
“It’s a great all-rounder, with good size,” he says. “It’s also got what’s known as the ‘ECONOMIZER’, which indicates to operators when they’ve reached optimum compaction. It makes compacting over areas much easier and more accurate.
“The Economiser can also help less experienced operators become more efficient as a result.”
Another highlight of the BOMAG range
is the BW 213 D-5 single drum roller. Capable of achieving 2130 millimetres of compaction, and powered by a 103 kilowatt, Duetz TCD 2012 L04 2V engine, the BW 213 D-5 is suitable for a variety of project applications and sizes.
The BW 213 D-5 is just one of BOMAG’s fifth generation rollers that are built to cater to construction site needs.
Understanding that specifications and project scenarios can differ greatly, BOMAG’s range aims to enable the operator to tackle every type of project, thanks to several features.
One is VARIOCONTROL, a feature that enables the drum to vibrate linearly, allowing the drum to also adapt in realtime to the surface.
Rollers equipped with VARIOCONTROL can achieve maximum power where conventional designs can’t, while also providing greater depth effect and eliminating over-compaction, all in less passes.
Another is BOMAG’s TERRAMETER. This measuring feature enables the single drum rollers to become rolling pressure plates, meaning the operator can benefit from more accurate readings in real time. This helps to increase the accuracy of compaction, meaning operators can work toward the required stiffness level outlined by the client or project manager.
“The feedback that we’ve had from customers has been overwhelmingly positive when it comes to the Sumitomo and the BOMAG brands,” Anderson says. “We often hear that they’re simple machines to operate, they’re robust and the backup support service provided by Tutt Bryant is a big plus for operators, and ourselves.
“At times they bend over backwards to provide us with the support we need. If we ever need urgent parts, one of their parts managers usually runs it down to us, we’re only about five minutes away from each other.”
And to ensure that clients get the right machine for the right job, TKR’s experienced team, made up of individuals who used to be operators themselves, can guide customers in the right direction.
“The knowledge within our management team, who have experience in operating machinery and running projects, goes a long way when pairing the right machine for the right application,” Anderson says. This is particularly important for
“IT’S ALSO GOT WHAT’S KNOWN AS THE ‘ECONOMIZER’, WHICH INDICATES TO OPERATORS WHEN THEY’VE REACHED OPTIMUM COMPACTION. IT MAKES COMPACTING OVER AREAS MUCH EASIER AND MORE ACCURATE.”
many of TKR’s clients who are currently engaged on major infrastructure works, such as the Cross River Rail and the Coomera Connector, as the region prepares for the upcoming Brisbane 2032 Olympic and Paralympic Games.
“We’re on pretty much all the major infrastructure projects in South East Queensland,” Anderson says. “There’re heaps of tenders out there and our clients are tendering on different aspects of these works. Next year looks set to be a big year in the major infrastructure project space.
“We’re a preferred provider because we focus on the specialised side of machinery for these projects. Whether it’s attachments for different projects or
intelligent machine control, we provide that as part of our complete package. The rollers play a key role in us having the ability to provide the whole package.”
John Glossat, National Business Development Manager – Tutt Bryant Equipment, says there’s plenty to come in the rolling space for both existing and future customers.
“We have many longstanding customers, one of the biggest aspects that’s helped us to grow over 80 years to establish a massive Australian footprint in the supply, support, parts and service of compaction and construction machinery,” he says.
“There’s massive deals right now, so don’t forget to contact your local Tutt Bryant Equipment branch.”
CATERPILLAR IS INTRODUCING THE LATEST CONSTRUCTION MACHINERY TECHNOLOGY, DESIGNED TO INCREASE PERFORMANCE AND ACCURACY.
Caterpillar has revolutionised the operation of motor graders with the introduction of joystick controls and a suite of advanced machine control solutions, delivering enhanced operability and boosting productivity.
More than a decade ago, Cat introduced three-axis joystick control for steering, blade and transmission control on its all-new M Series. The new technology machine with electro over hydraulic (EH) joysticks has proven to reduce operator fatigue, allowing easier multi-function work compared to traditional lever controlled hydraulic systems. This new EH control system was the enabler for greater
machine control automated technologies, but Caterpillar’s legacy in advanced technologies started way before this.
Back in the mid-1960s Cat Motor Graders developed a grade control option called ABC (Automatic Blade Control) that included a simple stringline follower to control blade elevation. A very basic system compared to today’s digital computing systems that include high-powered electronic control modules.
Cat Motor Graders design have had significant developments over the years with integrated systems much desired by its customers instead of bolt-on aftermarket attachments. The EH controls
introduced with the M Series allowed for advancements in integrated Grade control technology with the 2D Cross Slope option available factory installed.
With 2D Cross Slope, operators benefit in having autonomy in maintaining the desired cross slope in a road without the need of external grade slope checkers. This feature, although an option, was found to be accepted by over 90 per cent of Cat’s customers as a minimum requirement.
The Cat Grade 2D Cross Slope gives the operator guidance or automatic control to maintain road slope to design on one side of the blade. For road maintenance applications this results in greater accuracy,
and more timely completion of the job, without relying on support personnel to check grade.
For more complex road and infrastructure designs with curves, slopes and contours, customers typically install aftermarket 3D Grade control technology. This higher technology automatically controls blade height and horizontal positioning, all accurate to the millimetre.
Whilst these aftermarket 3D Control systems can grade to design with millimetre accuracy, its recommended to limit steering, drawbar, circle and moldboard operation to stay accurate to grade.
The 3D aftermarket systems include long masts attached to the blade with GPS receivers mounted to the top. Caution needs to be exercised to prevent masts damaging the cab or impact to masts from overhead obstructions.
These heavy masts and antennas are typically removed at the end of the shift for security and transport.
With this knowledge of machine operation limitations and issues associated with long blade masts, Caterpillar has developed Grade 3D without mast mounted GNSS (Global Navigation Satellite System) antennas. More than four years ago, the Cat 3D GNSS Mastless option was introduced to the market on the T4f emissions-built Motor Grader product, with the take-up of this option significantly exceeding Cat’s expectations. This new mastless grade technology has recently been introduced to the T3 emissions versions also.
With no masts to interfere with visibility, and the ability to use full machine functionality without compromise to grade tolerance, greater productivity and more applications can be achieved. Wheel lean, drawbar offsets and frame articulation can be positioned without restriction from masts or cables, expanding the use of the grader in many new applications that were difficult with blade mounted masts. This is particularly useful in environments such as side slopes and drains, where guidance was not previously effective due to the mast restrictions.
The Cat 3D GNSS Mastless technology reduces operator inputs and, due to its high accuracy, reduces the number of passes to finish the job – saving time and money. The operator also benefits from a new 10 inch
touch screen display with fast performance.
The Grade display puts the design plan clearly in front of the operator, giving them greater autonomy with the ability to create in-field design and modify existing plans on the go, directly on the screen, without reliance on electronic design file transfer.
The grade technology is operated via control switches integrated with advanced control joysticks, meaning there’s no need for the operator to remove their hand from the controls, allowing for seamless operation.
E-fence is included as standard, and when activated, the E-fence system sets automatic boundaries to prevent the
moldboard from contacting the tyres and ladder. Plus, it prevents contact between the linkbar and top drawbar. The machine protects itself, freeing the operator to devote full attention to the tasks at hand.
Cat 3D GNSS Mastless is factory fitted and fully calibrated for optimal performance, and all supported with factory warranty and backing of the CAT dealer network.
The integration of 3D antennas into the cab roof and front frame gives a better line of sight, and with ease of transport, Cat’s new Mastless Grade 3D option is leading the way; setting a course for its customers to be more successful.
For half a century, a long-standing Master Precaster member of National Precast, Reinforced Earth, has been at the forefront of delivering innovative infrastructure solutions across the country. Since its inception in 1974, the company has led the adoption of reinforced earth technology, a technique originally developed in France during the 1960s. This revolutionary construction method has been instrumental in transforming Australia’s infrastructure landscape, enabling the creation of robust, long-lasting structures across various sectors.
“Our team takes immense pride in having been a part of Australia’s infrastructure evolution over the past 50 years,” says Reinforced Earth Managing Director, Riccardo Musella. “Our technology has not only stood the test of time, but has also adapted to meet the ever-changing needs of modern infrastructure.”
HOW REINFORCED EARTH TECHNOLOGY WORKS
capacity. This technique has been widely used in the construction of retaining walls, bridge abutments and embankments. The method is particularly effective in challenging geotechnical conditions, providing a cost-effective solution that reduces the need for traditional concreteheavy construction methods.
According to National Precast Chief Executive Officer Sarah Bachmann, precast concrete plays a crucial role in reinforced earth solutions, by providing durable and modular components that enhance the structural integrity of various infrastructure projects. In these applications, precast concrete panels are often used to form retaining walls, bridge abutments and other key elements that support the load-bearing capabilities of reinforced earth systems.
“The precision and consistency of precast concrete ensure a high-quality finish, while its ability to be manufactured off-site reduces construction time and costs,” Bachmann says.
Precast elements are combined with soil reinforced by steel strips or geosynthetics, creating a robust and flexible system that can withstand significant loads and environmental conditions, making it ideal
for long-lasting infrastructure in challenging geotechnical areas.
“Our precast elements use locally sourced materials and we reduce the overall amount of concrete required, which helps with both cost and sustainability,” Musella says. “It’s a win-win for our clients and the environment.”
Reinforced Earth services offer significant
Earth specialises in tailoring infrastructure solutions for local communities and governments.
environmental benefits, reducing the need for excessive concrete and lowering the carbon footprint of infrastructure projects.
The use of locally sourced materials and advanced design techniques means these systems require minimal maintenance over their lifespan, contributing to longterm sustainability.
“Our focus has always been on delivering durable infrastructure that lasts, while also reducing the environmental impact,” Musella says. “We’re proud to have pioneered solutions that benefit both the economy and the planet.”
Since the introduction of the reinforced earth method to Australia, Reinforced Earth has been involved in over 1000 projects nationwide. The company’s first major project was constructing retaining walls for the Hume Highway in the 1970s, which remains a crucial transport corridor today. Over the decades, the company has become a trusted solution for major infrastructure works across roads, rail, ports and even mining operations.
One standout project is the M7 Motorway in Sydney, where over 100,000 square metres of precast concrete retaining walls
were supplied. These retaining structures have supported the motorway’s expansion while blending seamlessly with the surrounding landscape. As infrastructure demands grow, Reinforced Earth continues to evolve its offerings, incorporating new technologies and materials. The company remains committed to leading the charge in developing sustainable and innovative infrastructure solutions.
“We’re excited about our future in Australia,” Musella says. “As we continue to innovate, our
Earth has been designing and constructing civil infrastructure projects for 50 years.
goal is to deliver resilient infrastructure that meets the challenges of tomorrow.”
For the past 50 years, the company has played a vital role in shaping Australia’s infrastructure, from urban centres to remote regions. As the company looks to the future, reinforced earth technology will continue to be a key part of Australia’s infrastructure solutions, ensuring communities can rely on strong, sustainable, and cost-effective infrastructure for decades to come.
& INFRASTRUCTURE
MAGAZINE PROVIDES AN UPDATE ON THE LEVEL CROSSING REMOVAL PROJECT IN VICTORIA, WHICH REPRESENTS ONE OF THE LARGEST PACKAGES OF CONSTRUCTION WORKS EVER SEEN IN THE STATE.
In May 2015 the Victorian Government announced it would establish The Level Crossing Removal Project (LXRP) to oversee one of the largest rail infrastructure projects in the state’s history.
Central to the project is the removal of 110 dangerous and congested level crossings across Melbourne by 2030. In addition to these works, other projects include rail network upgrades such as new train stations, track duplication and train stabling yards.
The LXRP is part of the Victorian Infrastructure Delivery Authority, which delivers major rail and road projects across the state, forming Victoria’s Big Build.
So far 84 level crossings have been removed and the Lilydale Line is the first rail line in Melbourne to be level crossing free.
The Cranbourne, Pakenham and Sunbury line will join next year, while the Frankston Line will be boom gate-free in 2029 and the Werribee Line in 2030.
Improving safety for road users and pedestrians in Melbourne is one of the reasons for the LXRP, which will be achieved by removing the danger of trains sharing a level crossing with vehicles and pedestrians.
The LXRP will also make travel easier for commuters, motorists and those who utilise active transport by eliminating delays caused by boom gate down time. This will help to reduce the build of traffic, therefore also reducing travel times and uncertainty around the state’s metropolitan road network.
The construction industry has flourished over the past nine years, with thousands of jobs created to complete the works.
Works have not only included removing level crossings, but also building new stations and creating new public spaces.
The train lines at Sunbury, Werribee, Frankston, Cranbourne, Pakenham and Lilydale each boast a unique design at the site, adding value to the community and commuters.
Removing dangerous crossings has allowed new open space and new shared walking and cycling paths to be created, while previously bland spaces have
Work is nearly completed on the Pakenham Line as level crossings at Main Street, McGregor Road and Racecourse Road have now all been removed and replaced by a 2.5-kilometre section of elevated rail.
New stations at Pakenham and East Pakenham have been open since July 2024, with works underway under the rail line to create community spaces, the equivalent of six Melbourne Cricket Grounds in size.
Emma Vulin, Member for Pakenham, says the works will modernise the town.
“Removing these three level crossings will make Pakenham a better place to be by improving safety, creating better access in and out of the town centre and more open space for everyone to enjoy,” she says.
The new open space will feature a barbecue area, a half basketball court, playgrounds, bicycle hoops, a bicycle repair station, parklands, seating and garden beds, ready for use in spring 2024.
The new station in Pakenham includes 300 car parks as well as bike facilities, bus bays and dedicated pick-up and drop-off zones close to the station.
Despite all projects having fixed technical requirements in relation to design solutions, the LXRP has actively collaborated with the community on negotiable elements including open spaces, landscaping, station precincts and public art.
One great example has been students at St Margaret’s Berwick Grammar creating six unique artworks in term one of 2022
for display at Berwick Station as part of the Clyde Road level
removal project. Students from Year six and nine collaborated on the pieces, taking inspiration from a range of sources such as Van Gogh’s Starry Night, through to the school colours and emblems.
Sunbury local and Yorta Yorta, Gunaikurnai and Gunditjmara artist Teena Moffatt also shared her talents to the level crossing project in Sunbury, creating the artwork for the Gap Road rail bridge.
The Gap Road level crossing located in the heart of Sunbury was removed, with a road under rail design built in its place.
“REMOVING THESE THREE LEVEL CROSSINGS WILL MAKE PAKENHAM A BETTER PLACE TO BE BY IMPROVING SAFETY, CREATING BETTER ACCESS IN AND OUT OF THE TOWN CENTRE AND MORE OPEN SPACE FOR EVERYONE TO ENJOY.”
The artwork’s custom-designed perforated panels were installed on both sides of the rail bridge.
Moffatt’s artwork references the volcanic plains of the western district, the ancient presence of Mount Holden hovering over Sunbury, Jackson’s Creek winding through local valleys and the unique features of the Organ Pipes and Rosette Rock.
“My art connects my past, present and future,” says Moffatt.
“I do my work in honour of my grandmothers and grandfathers, my family and my bloodlines; to ensure my children feel a strong connection to their people and our traditional ways.”
The removal of level crossings at Dublin Road, Ringwood East and Coolstore Road, Croydon made the Lilydale Line Melbourne’s first rail line to be boom gate free.
Two more dangerous level crossings were also removed at Union Road, Surrey Hills and Mont Albert Road, replaced with a brand-new Union Station which opened in May 2023.
In its works, the LXRP strives to deliver sustainable infrastructure that supports safe and healthy Victorian communities into the future.
To achieve this goal, the LXRP focuses on using materials efficiently and implementing sustainable alternatives where possible, while designing green space with people and wildlife in mind.
It also aims to create energy efficient infrastructure and minimise the energy used in construction. While also assessing climate change risks to reduce the environmental impact through smart design.
One sustainability highlight has been the works at Union Station, which since its opening has received two honours for its sustainability.
In April 2024, it received the highest sustainability rating, a Six-Star Green Star certification by the Green Building Council of Australia, joining the ranks of “world leadership” in building design and construction, scoring highly in the areas of emissions, transport, building materials and innovation.
Two months later in June, the station was awarded the highest ever sustainability
rating for a Victorian rail project. The Infrastructure Sustainability Council (ISC) awarded the precinct an “As Built” score of 101 points, judged across a range of sustainability measures, including environmental management and the use of technological advances to set new engineering benchmarks.
Level Crossing Removal Project Program Director Steve Brown says the certification recognised the project team’s commitment to providing the community with a state-ofthe-art transport facility.
“Being recognised as a world leader in sustainability is a huge achievement and a reflection of the project team’s innovation and dedication to deliver improved transport infrastructure with lasting environmental benefits,” he says.
Works on the Cranbourne Line Upgrade have been completed, with eight kilometres of duplicated track between Cranbourne and Dandenong, and a new Merinda Park Station in Lyndhurst open to passengers.
The track duplication has allowed more services to be introduced on the Cranbourne Line, including a 10-minute average frequency in the morning peak.
Level crossings have been removed at Evans Road, Lyndhurst, Greens Road, Dandenong South and Camms Road, Cranbourne, with Webster Street, Dandenong to be removed by 2025.
Throughout the works, the LXRP has provided a range of employment opportunities across many business areas.
This is offered through a range of employment programs that aim to provide people who are starting in their careers with an opportunity to gain experience through ‘hands on’ work.
One Civil Engineer, Samrawit, was hoping to get a start in Victoria’s booming construction industry after migrating from Ethiopia with her husband on skilled migrant visas in 2023.
Samrawit’s first opportunity to break into the industry came through the Victorian Government’s GROW program which led her to secure an internship with the LXRP and work on a range of projects.
The Government’s GROW program is designed to introduce people from marginalised and disadvantaged
Both projects celebrate local Indigenous culture with the inclusion of design elements that reflect Traditional Owners’ connection to country.
Member for Mordialloc Tim Richardson says the progress made has been exciting.
“With the removal of these dangerous and congested level crossings we’re seeing improved safety, reducing congestion and the creation of better connections for our community,” he says. “We’ve seen so much investment on the Frankston Line, but there is more work to be done.”
Moving out west, works on the Werribee Line continue with the removal of four level crossings completed and a further three on the way, making the line boom gate free by 2030.
A new rail bridge has been built over Werribee Street, allowing for both freight and passenger trains, while future works will include a new Spotswood Station and a new road bridge at Maidstone Street, Altona. Throughout LXRP’s journey, an approach towards innovation has been constantly evolving.
With this in mind, the LXRP salvaged materials from many project sites and
“BEING RECOGNISED AS A WORLD LEADER IN SUSTAINABILITY IS A HUGE ACHIEVEMENT AND A REFLECTION OF THE PROJECT TEAM’S INNOVATION AND DEDICATION TO DELIVER IMPROVED TRANSPORT INFRASTRUCTURE WITH LASTING ENVIRONMENTAL BENEFITS.”
backgrounds to employment and training opportunities and pathways, delivered by the Training for the Future initiative, as part of the LXRP.
On the Frankston Line, all level crossings on the line are set to go by 2029, changing the way people live, work and travel.
As part of these level crossing removals, new stations will be built at Highett, Mordialloc, Aspendale and Seaford.
Through these works the LXRP is working to reconnect communities and create public spaces that will leave a long-lasting legacy for Melbourne. This is done through work in urban design.
Urban design is the practice of making these precincts work for the community, including elements like architecture, green space and pathways.
Two level crossings in Seaford Road and Carrum were recognised at the 2024 VIC Landscape Architecture Awards for shaping resilient, culturally conscious, climate positive and inspiring places.
repurposed them to become part of the $88 million redevelopment of Werribee Open Range Zoo.
Rail track, including 1.5 kilometres replaced as part of the Werribee Street Level Crossing Removal Project, and elevator cable will be used to construct the perimeter fencing for several animal facilities.
Other material donated includes salvaged timber, 20 gum tree stumps from Old Geelong Road, Cherry Street and Werribee Street projects, as well as two kilometres of rail track from the Coburg and Preston projects.
Member for Williamstown, Melissa Horne, says the removal of the level crossings along the Werribee Line is a fantastic investment for the west.
“I look forward to seeing these dangerous and congested level crossings gone for good from our community,” she says.
Works across projects continues, with 26 level crossings still on the horizon for removal by 2030.
THE MANAGEMENT, RECOVERY, AND REUSE OF OFF-THEROAD (OTR) TYRES HAS BECOME AN IMPORTANT TOPIC. AS THE AUSTRALIAN FLEXIBLE PAVEMENT ASSOCIATION WRITES, MORE WORK NEEDS – AND IS – BEING DONE TO COUNTER THE CARBON IMPACTS OF THIS MATERIAL.
Off-the-Road (OTR) tyres are an essential component in industries like mining, agriculture, and construction, where heavy-duty machinery operates in rugged conditions. These massive tyres, which are designed to withstand extreme pressure and harsh environment, pose a significant environmental challenge once they reach the end of their lifecycle.
Across Australia 130,000 tonnes of OTR reach their end of life each year, with only 10 per cent being recovered and the rest mostly buried, stockpiled or sent to landfill (Tyre Stewardship Australia, 2023). This is below the Federal Government’s 2030 target of 80 per cent recovery rate for all waste streams.
OTR tyres are not easily recycled due to their size and the locations where they are used. While automotive tyres are typically in metropolitan areas and easily recovered, most OTR tyres are used in remote areas of Australia, far from established processing facilities.
Due to limited recycling services and transportation distances, many OTR tyres are buried or stockpiled on-site, resulting in waste and potential negative impacts on the environment and community. From a report published by Tyre Stewardship Australia (TSA) in 2023, Western Australia and Queensland are the largest OTR tyre generators.
One of the solutions to reuse end of life tyres is to use the rubber in roading applications. Crumb rubber technology is well known in Australia and already widely adopted for spray sealing applications. CR-modified binders are manufactured by adding the rubber from processed tyres to a conventional bitumen to enhance the bitumen elastic and durability properties.
The use of the rubber from end-of-life tyres as an elastomeric modifier for bitumen represents a high value recycling opportunity. In the past years, due to the joint effort of TSA, various state road authorities, AfPA and Austroads, several research and field projects
are being promoted to ensure broader adoption of crumb rubber in road pavement applications.
A recent project funded by the TSA investigated the opportunity to create a circular economy in Queensland by repurposing waste tyres from the construction industry into valuable resource for reuse. The project, led by the former AfPA Director of Technology, Anna D’Angelo, in collaboration with Sunshine Coast Council and Boral Asphalt, assessed the constructability and performance of Crumb
Rubber Gap Graded (GGA) mixes using crumb rubber manufactured from 100 per cent OTR tyres. The OTR tyres for the project were sourced internally by Boral from its West Burleigh Quarry site, and the crumb rubber manufactured by Carroll Engineering.
The chemical analysis and binder tests, performed by RMIT University, showed that the OTR crumb rubber had slightly more natural rubber and less synthetic rubber compared to standard crumb rubber, and could be effectively used in bitumen blends. In addition, the binder samples were also analysed using a Suntest Atlas weathering chamber to compare the ageing due to solar radiation.
The UVA (Ultraviolet A) and UVB (Ultraviolet B) radiation data collected daily in Sunshine Coast in 2022 by the Australian Radiation Protection and Nuclear Safety Agency (ARPANSA) were used to calculate the total UV radiant exposure, considering a clear sky (i.e., worst-case scenario).
Results showed that the unmodified C320 was severely affected by photo-oxidative ageing to a much larger extent than the CRmodified binder. Further testing showed that the ageing of the CR-modified binder, due to UV damage, is significantly less than that of conventional bitumen, showing that the addition of crumb rubber slows down the deterioration of the base binder. Less UV damage entails greater resistance
to environmental cracking and, overall, longer road durability. This aspect is especially relevant for local council roads where most damage is caused by environmental factors rather than traffic loads.
Asphalt mixes using the OTR crumb rubber bitumen manufactured by Puma Bitumen, were laid on different road types and were tailored to the needs of the Sunshine Coast Regional Council with respect to suitable applications for collector roads, residential streets, and rural residential street applications and as an alternative to the conventional dense graded asphalt.
The performance testing conducted on the asphalt mixes showed improved cracking resistance and reduced UV damage compared to unmodified bitumen.
Anna D’Angelo – former AfPA Executive Director Technology – Leadership says the project provided an opportunity to demonstrate that crumb rubber derived from OTR tyres can be interchanged with common crumb rubber in bitumen blends and confirmed the industry’s readiness and capability to manufacture and pave CR asphalt mixes.
“The project, an example of a circular economy approach and industry collaboration, demonstrated a viable solution to recycling end-of-life OTR tyres essential for the transition of society towards a more sustainable future.”
ROADS & INFRASTRUCTURE PROVIDES AN UPDATE ON SOME OF THE CONTRACTS AND TENDERS RECENTLY AWARDED OR PUT TO MARKET ACROSS THE AUSTRALIAN INFRASTRUCTURE SECTOR.
Major Road Projects Victoria has awarded a construction contract to upgrade the busy Clyde Road, in Melbourne’s south-east. Seymour Whyte has been awarded the works which include a 1.2-kilometre upgrade for the busy Clyde Road/Princes Freeway intersection in Berwick, southeast Melbourne. The upgrade aims to relieve bottlenecks by improving traffic flow, while making journeys safer and more reliable. This will be achieved by improving freeway access, adding additional lanes between the Princes Freeway and Kangan Drive, and widening the existing Clyde Road bridge over the freeway. The project also includes upgrading the Clyde Road/Kangan Drive intersection; constructing new and upgrading existing shared walking and cycling paths; and installing new street lighting, road signage, drainage; and landscaping. This project also has a Recycled First Plan, which prioritises using recycled content in construction materials, further contributing to lowering carbon emissions and promoting a circular economy. Clyde Road is an access route to the Berwick Health and Education Precinct, a growing ‘knowledge hub’ that includes key institutions such as Casey Hospital, St John of God Hospital, Chisholm TAFE, Federation University, and the Berwick Railway Station. The planned upgrades will support the precinct’s ongoing expansion, facilitate better connectivity, and accommodate future growth in the area. Construction has started, with completion scheduled for 2027.
$190M in works packages awarded for Borumba Pumped Hydro Queensland Hydro has announced the successful tenderers for three major works packages for the Borumba Pumped Hydro project. Borumba Pumped Hydro is a major, 2000 megawatt renewable energy project at Lake Borumba, located near Imbil, west of the Sunshine Coast. The existing lower reservoir (Lake Borumba) will be expanded with a new dam wall downstream from the current Borumba Dam. A second reservoir will be constructed at a higher altitude. An underground powerhouse will link the two reservoirs together. When electricity is required, water will be released from the upper reservoir through underground turbines via tunnels to the lower reservoir. Water2Wire Joint Venture (JV) have been appointed as Dams Designer Delivery Partner, with packages totalling $40 million awarded to advance the
design and engineering of both the upper and lower reservoirs. Water2Wire JV will be responsible for leading the engineering and design for the Borumba Project’s seven proposed dams which involve six new dams to form a new upper reservoir, and one new dam wall and spillway immediately downstream from the existing Borumba Dam. The replacement dam wall will see Lake Borumba increase its capacity providing security to the proposed energy storage scheme. AFRY-Aurecon JV were awarded the $39.9 million Pumped Hydro Energy Storage (PHES) Designer package. The package will see AFRY-Aurecon advance the front-end engineering design documentation, focusing on the technical elements of the pumped hydro scheme itself – such as the interplay between the turbines, cavern design, tunnel waterway design, and other equipment. Decmil have been awarded a contract totalling approximately $111M to design and construct two temporary worker camps on the site of the Borumba Project. The best practice camps will be able to house up to 336 workers each, with each location containing a wellness room, gym facility, running track, social room, laundry facilities making workers on one of Queensland’s most important infrastructure projects feel right at home.
The design has been completed, with construction given the green light to begin in 2025 for works to improve safety and congestion related issues presented by the Coopers Plains rail level crossing in Queensland. The $399 million project will improve safety and congestion by building a new elevated three-way intersection over the rail crossing, connecting Boundary Road and Orange Grove Road. New active transport facilities will also be built including connections for bike riding and dedicated pedestrian footpaths. The project means better train services for rail passengers, and travel times for drivers by allowing for the through-flow of trains and cars without a level crossing. TMR will now go to procurement, with construction companies asked to register their interest in building the new rail overpass, by late-September 2024.
A contractor has been selected to deliver
enabling works for the second stage of the Parramatta Light Rail in Sydney. John Holland will deliver the works that will include a public and active transport bridge linking Wentworth Point and Melrose Park across the Parramatta River. The second stage of the Parramatta Light Rail will deliver 14 stops over a new 10-kilometre two-way track. It will connect the Parramatta CBD to Ermington, Melrose Park, Wentworth Point and Sydney Olympic Park. It will also connect to Sydney Metro West, the heavy rail in Parramatta and Sydney Olympic Park, and ferry services at Rydalmere and Sydney Olympic Park. Parramatta Light Rail Stage 2 will also provide a total of 9.5 kilometres of integrated active transport (including 8.5 kilometres of new shared paths) to support healthy, liveable and connected communities. The project will be staged. The first stage is the delivery of the new public and active transport bridge over Parramatta River between Wentworth Point and Melrose Park, including approaches on either side of the river – totalling 1.3 kilometres. The NSW Government committed $602.4 million in the 2022-23 NSW Budget towards the delivery of the Enabling Works. The new bridge will connect communities on the north and south of the river, and will feature an innovative, long-span cast in situ balanced cantilever design. The design means the bridge will only have two piers in the river, minimising disruption to boats and other waterway users and protecting the sensitive marine environment. Organisations were shortlisted to tender for the delivery of the enabling works package and the request for tender was issued on 14 November 2023.
This included a CPB Contractors Pty Ltd and McConnell Dowell Constructors (Australia) Pty Ltd joint venture, as well as a Fulton Hogan Construction Pty Ltd and SRG Global joint venture, and of course the successful John Holland tender. This is the first critical stage of works for the light rail extension which, when complete, will connect communities on the Olympic Peninsula with Greater Parramatta. This project is one of a number of projects that John Holland is delivering in western Sydney, including the M7-M12 Integration project and the Upper South Creek Advanced Water Recycling Centre.