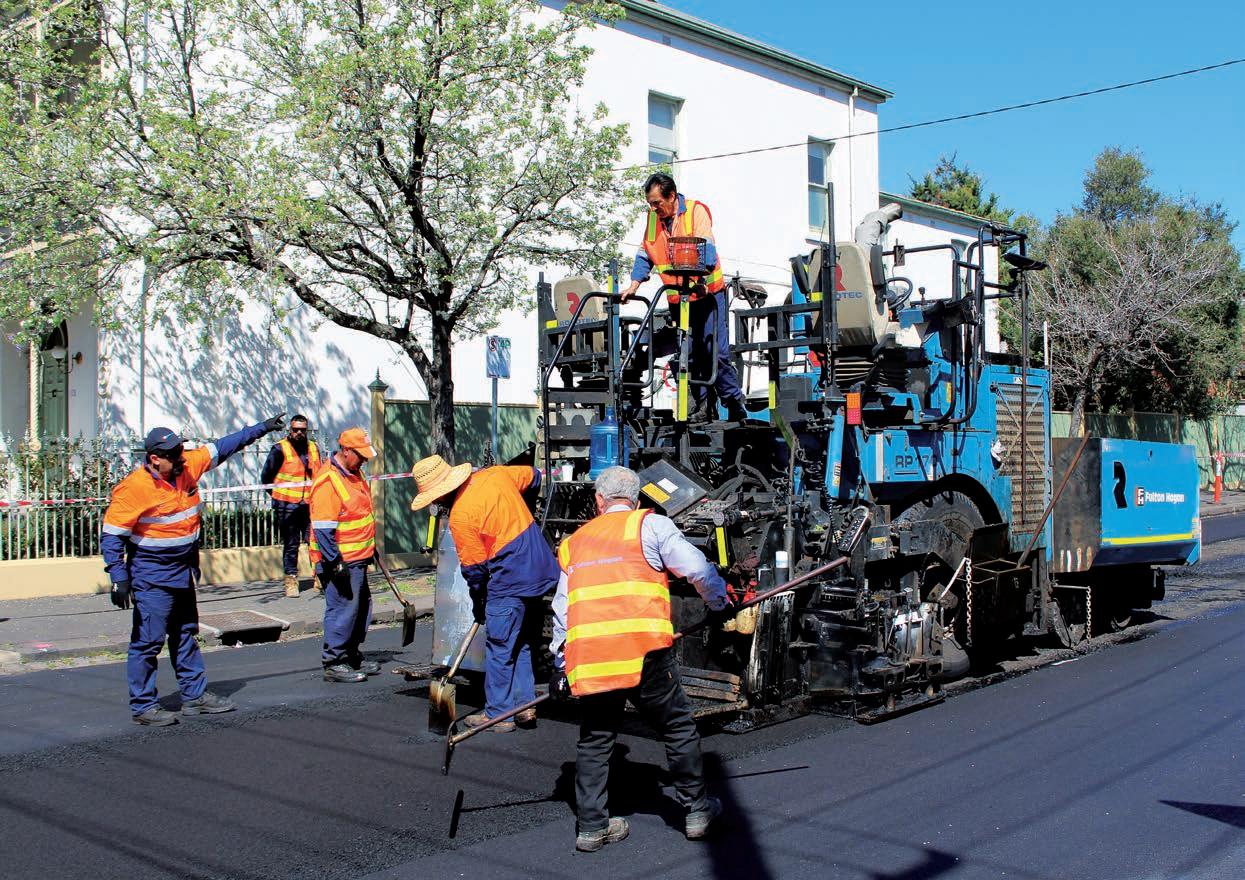
8 minute read
Plastiphalt road
Mozart Street in St Kilda, Melbourne was resurfaced with 800 kilograms of plastic last year.
PLASTIPHALT SETS NEW STANDARD FOR GREENER ROADS
A REVOLUTIONARY NEW ASPHALT PRODUCT THAT USES A PREVIOUSLY UNIDENTIFIED SOURCE OF RECYCLED PLASTIC IS SET TO SIGNIFICANTLY REDUCE THE AMOUNT OF WASTE DUMPED IN AUSTRALIA’S LANDFILLS.
The scourge of plastic pollution in rivers and oceans worldwide is a well-known concern, as nearly three-quarters of the waste along Australian coastlines is plastic, according to CSIRO.
The ubiquitous material, which has increased 20-fold in the past century, is predicted by the World Economic Forum to double again in the next 20 years.
Moreover, research into the implications of microplastics – tiny pieces of plastic less than five millimetres long – on human health is still being conducted.
While some plastic alternatives are readily identifiable, the historical blend of various plastics in manufacturing has thrown a curveball at its direct remanufacturing. Additionally, international restrictions on waste exports have challenged the commercial viability of plastics recycling.
Consequently, the roads sector has been inspired to play its part in the waste crisis, finding local solutions to an international problem.
Last year, leading infrastructure and civil construction company Fulton Hogan developed a groundbreaking proprietary product called PlastiPhalt. The innovative, environmentally friendly asphalt pavement contains shredded plastic and has already been laid on several council roads.
Recycled plastic has been incorporated into asphalt for Australian roads by the industry previously. Building on these efforts has been about innovation, with Fulton Hogan sourcing plastic from a number of strategic supply sources. This has allowed the company to provide the right mix of product to manufacture PlastiPhalt to a high level of performance that meets Austroads guidelines.
Now, Fulton Hogan has identified a new source of recycled plastic which was previously consigned to landfill. They are utilising recycled automotive plastic as the key ingredient, which has become
an increasing global problem due to an increased demand for fuel efficient vehicles.
Working with local recycling partners, Fulton Hogan takes automotive plastic waste and shreds it before combining it with a specially selected binder to produce PlastiPhalt.
Apart from the environmental benefits of reducing waste to landfill, extensive testing at laboratories accredited by Australia’s National Association of Testing Authorities (NATA) has shown that PlastiPhalt is significantly more durable than normal asphalt mixes.
Fulton Hogan’s Australian Chief Executive Officer of Infrastructure Services Matthew MacMahon says the fact that PlastiPhalt lasts significantly longer than traditional asphalt products also has valuable environmental and community benefits.
“Apart from the obvious benefits of recycling materials that would otherwise clutter up Australia’s landfills, testing has proved that PlastiPhalt is actually significantly more durable than traditional asphalt. That means that we will need to repair the road surface less often, which has a clear benefit to the community,” Mr. MacMahon says.
“As a family business, Fulton Hogan is committed to ensuring the work we do today will make a real difference to the lives of our people and customers, the communities they call home, and the world we will live in tomorrow.”
Through its PlastiPhalt mix design, Mr. MacMahon says Fulton Hogan has also found a solution to the issue of microplastics.
Mr. MacMahon says that in some cases, these small plastic particles can be released as the road surface degrades over time, potentially clogging waterways and becoming an environmental issue for marine life. He says the manner in which PlastiPhalt is produced, however, ensures that no microplastics are released.
Noriko Wood, Materials Engineer at Fulton Hogan, says that the recycled plastic within the polymer modified binder is milled and melted so the plastic is fully dissolved into the chemical matrix of the bitumen. This, she says, forms a homogenous mixture and the plastic
actually becomes part of the bitumen. As a result, there are no particles of plastic present, and no way for them to strip out of the pavement.
As an experienced engineer, Ms. Wood conducted extensive testing in the lab to ensure PlastiPhalt meets rigorous NATA standards, including in rut resistance, durability and fatigue properties.
“Because we had to adapt the manufacturing process to accommodate recycled plastic, it meant that we had to think really deeply about the best way we could do it to avoid microplastics entering the environment,” Ms. Wood says.
The absence of microplastics in the product was one of the reasons the City of Port Phillip chose to become the first Victorian council to conduct a major trial of PlastiPhalt in late 2019. Initial successful trials of the new product were conducted by Fulton Hogan in a select number of locations around Australia and New Zealand. From there, Mozart Street in St Kilda, Melbourne was resurfaced successfully with asphalt which incorporated 800 kilograms of plastic. In all, a 2000 m² section of road was resurfaced using 224 tonnes of PlastiPhalt
City of Port Phillip Mayor Dick Gross and Fulton
Hogan Australian Chief Executive Officer of Infrastructure Services Matthew MacMahon are proud to play a key part in the project.

The plastic is fully dissolved into the chemical matrix of the bitumen to form a homogenous mixture.
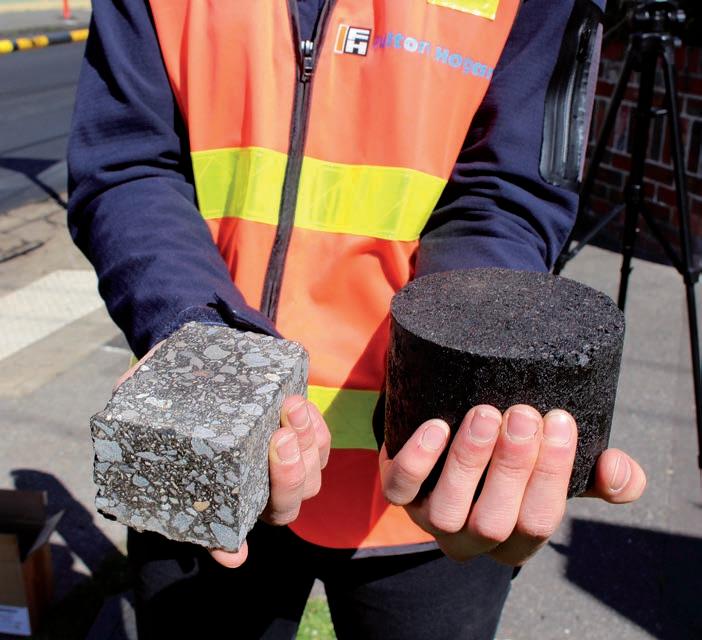
and the City of Port Phillip was excited to trial the new greener road alternative.
“Our council is continually looking at ways of increasing and encouraging sustainability,” explained City of Port Phillip Mayor Cr Dick Gross when announcing the trial.
“If we get the results we are expecting, this is a win for our community and the environment.
“It’s also a great example of how creating a circular economy for recyclables can breathe new life into waste that would otherwise go to landfill.”
After outstanding initial results from the Mozart Street trial, the City of Port Phillip has since scheduled additional projects using PlastiPhalt and other Victorian councils have swiftly followed suit. Frankston City Council successfully trialled the new asphalt product in Seaford, incorporating 500 kilograms of recycled plastic into the new road surface. The Greater City of Dandenong has also relaid a 4300m² section of road in Westall using 376 tonnes of PlastiPhalt.
The first official trial of PlastiPhalt on Victoria’s major road network has since been successfully conducted through Fulton Hogan’s maintenance alliance with Regional Roads Victoria (RRV), with more than three tonnes of recycled plastic used to resurface a 1.5-kilometre section of the iconic Great Ocean Road coastal route near Lorne.
“This project will save an amount of plastic equal to about 300,000 plastic bottles from entering landfill,” RRV’s Regional Director (South West) Emma Miller-Olsen explained.
“We’re constantly looking for ways to improve the sustainability of our road building and repair practices, and this represents a significant step forward for us in terms of using recyclable materials, particularly when we’re improving the Great Ocean Road – one of the state’s most famous assets.”
Fulton Hogan is also looking at other methods of further reducing the carbon footprint of road projects by incorporating Recycled Asphalt Products (RAP) as a percentage of the PlastiPhalt, and producing the mix at lower temperatures.
As an example, approximately 20 per cent of the PlastiPhalt used in the Frankston City Council trial was composed of RAP which had been recycled from old road surfaces in the region. The mix used in Seaford was also done as a ‘warm mix’ rather than a ‘hot mix’. This means the asphalt mix was heated to a lower temperature, reducing carbon emissions by approximately 30 per cent.
As part of Fulton Hogan’s holistic approach to providing greener alternatives for road projects, locally sourced RAP and recycled plastic is used wherever possible in order to limit emissions generated by transporting materials. Between January and March 2020, the City of Greater Geelong will use PlastiPhalt to resurface 1100 metres of three road surfaces in their first trial of the new product. The 3500 kilograms of recycled plastic will be provided by a local Geelong business, while the 20 per cent RAP used will also be sourced from local Fulton Hogan stockpiles.
Ms. Wood says that to date, more than 4000 tonnes of PlastiPhalt has been laid in Victoria alone, with works also taking place in Queensland, SA and WA.
“We’re working with the Department of Transport to gain approval, which means that the number of roads we could use it on will be expanded,” she says.
“We’re also looking to incorporate it as much as possible across Australia on local government and other road projects.”
Mr. MacMahon says that ultimately, introducing new products that can’t themselves be recycled as part of the circular economy is a short-sighted approach. Importantly, the PlastiPhalt surface can itself also be recycled as RAP in years to come.
“Fulton Hogan is confident that this type of product is the way of the future for Australian road maintenance and will fast become the product of choice for councils and road authorities around the country,” he says.
Find out more about PlastiPhalt® by visiting the Fulton Hogan website at www.fultonhogan.com
Industry Awards Gala Dinners
Industry Award presentation dinner dates: Nomination submission closing dates:
: 29th May : 05th June : 12th June : 19th June : 26th June : 24th July : 14th Aug
South Australia
Queensland Western Australia New South Wales
Tasmania Northern Territory Victoria/National 01st May : 08th May : 15th May : 22nd May : 29th May : 26th June : 10th July :
More details on www.aapa.asn.au/events/
