
5 minute read
Seismic roller technology
A SEISMIC SHAKE-UP FOR COMPACTION
DYNAPAC HAS CREATED A NEW COMPACTION TECHNOLOGY TO INCREASE EFFICIENCY, OPERATOR COMFORT AND FUEL EFFICIENCY. RELEASED INTERNATIONALLY IN 2019, THE TECHNOLOGY HAS NOW HIT AUSTRALIAN SHORES.
The idea behind the creation of Dynapac’s newest optimisation technology came at an unexpected moment.
Andreas Persson, Dynapac Calculation Engineer, was watching his daughter on the trampoline when inspiration hit.
Mr. Persson noticed that his daughter jumped much higher when she landed on the upswing of the trampoline.
He realised she gained a maximum height, with the least amount of effort, when she jumped in phase, taking advantage of the natural frequency in the trampoline.
It was this principal that Mr. Persson and Dynapac adapted to create Seismic technology for compaction rollers, which is now patent pending.
Launched at one of the world’s leading construction and machinery fairs in 2019, Dynapac’s Seismic technology has now landed in Australia.
Seismic reads the natural frequency of the soil and determines the optimum frequency for that material to be compacted.
Traditionally for compaction, the
properties of the drum and the ground are viewed as two separate elements that interact to create the compacted surface.
However, Seismic technology enables the drum and ground to work together as one system for improved compaction practices.
For Seismic compaction to be achieved, two specific conditions must be met.
The first is that the machine must read the stiffness properties of the ground in order to interact with it. When these values can be determined, the optimal frequency can be calculated.
Secondly, once the optimal frequency is calculated, the machine must be able to automatically adjust its frequency to adapt to the varying ground properties at all times, as these change.
Construction Equipment Australia’s National Product Manager for Dynapac, Chris Parkin, says Seismic works through the development of a special software algorithm which uses the existing compaction metre on the drum to detect soil frequency and optimises the machine’s vibration frequency.
In addition, a sensor in the vibration motor adaptor detects the position of the exciters. The position of the exciters is important as this expresses the connection between the ground contact force and the indentation of the roller drum.
“At the natural frequency, the drum amplitude is enhanced significantly, since energy is automatically fed to the ground at exactly the right time. This, in turn, maximises the contact force between the drum and the ground, yielding maximised compaction and energy efficiency,” Mr. Parkin says.
“By working in synchronisation with the ground’s natural properties, the machine’s performance is maximised, and less energy is required to achieve the same compaction results.”
Seismic allows the operator to focus on the exact compaction requirements as the system eliminates the need for the operator to guess and manually adjust the vibration frequency on the run.
“By using the speed limiter function, a constant speed and optimal compaction is ensured, thus allowing the operator to focus on meeting the compaction requirements in terms of pass counts and overlapping,” Mr. Parkin says.
Some of Dynapac’s other tools such as the intelligent compaction system “Dynapac Dyn@lyzer” also ensures these requirements are met. One of the main advantages of using the Dynapac Seismic technology is the reduced vibration power and, therefore, energy consumption.
“Lifetime fuel consumption has been estimated to be reduced using Seismic by around seven to nine per cent with vibration power and energy consumption reduced around 20 to 30 per cent,” Mr. Parkin says.
The machine must read the stiffness properties of the ground in order to interact with it.
As the machine vibrates in harmony with the soil, noise is also reduced to a minimum as the soil compacts at a lower frequency, which can provide operators with a more comfortable cabin noise level.
“In addition, thanks to Seismic, the same quality of compaction can, in most cases, be achieved with a reduced number of passes. This means savings in time, a reduction of costs and less wear and tear on our machines,” Mr. Parkin says.
The technology has been laboratory tested with the Royal Institute of Technology in Sweden and field tested with Trafikverket for the Swedish high-speed railway foundations.
Mr. Parkin says conventional vibratory compactors deliver a rapid succession of impacts to the soil surface at either a high or low amplitude, with a set frequency or a frequency that is adjusted manually. He says this would normally be around 30-33 Hertz for soil compaction.
“Dynapac Seismic does it differently. Since the drum and the soil act as one dynamic system, several benefits can be found from the system’s natural frequency. This allows for significantly lower vibration frequencies to be used.
Using the Seismic system, we operate in the range of 20 Hertz instead.”
Seismic technology is best suited to soil compaction for earthworks, but further
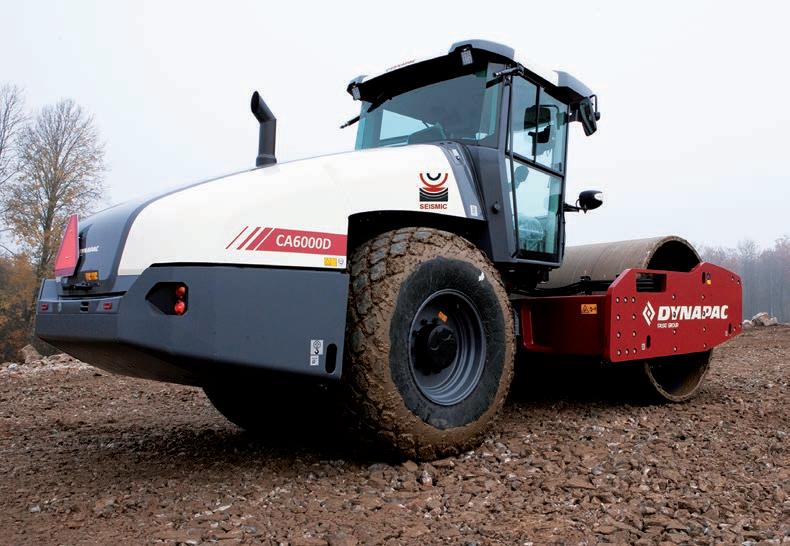
tests are being undertaken to optimise the system for asphalt.
“The measured value that controls the Seismic machine is a composite value of the material underneath the drum up to a certain depth. For very thin layers, typically asphalt wear courses, the technology needs to be refined to work properly,” Mr. Parkin says.
Dynapac is now undertaking research into this to determine the best system for asphalt compaction.
When using Seismic technology, it does not require any additional machine components. It uses all of the same components that have been used in Dynapac rollers for several years. It has simply added an algorithm to let the machine better adapt to the soil.
“Although machine operators have had the possibility to adjust the frequency themselves previously, recognising the dynamic characteristics of a certain soil just by looking at it from inside the cabin is near impossible,” Mr. Parkin says.
“With Dynapac Seismic, the roller automatically determines the natural frequency of the soil and adjusts to it. This saves both time and fuel consumption, makes it easier on the environment and reduces the wear of the machine.”
Seismic technology will be available on the complete soil compaction range CA1500-6500 machines.