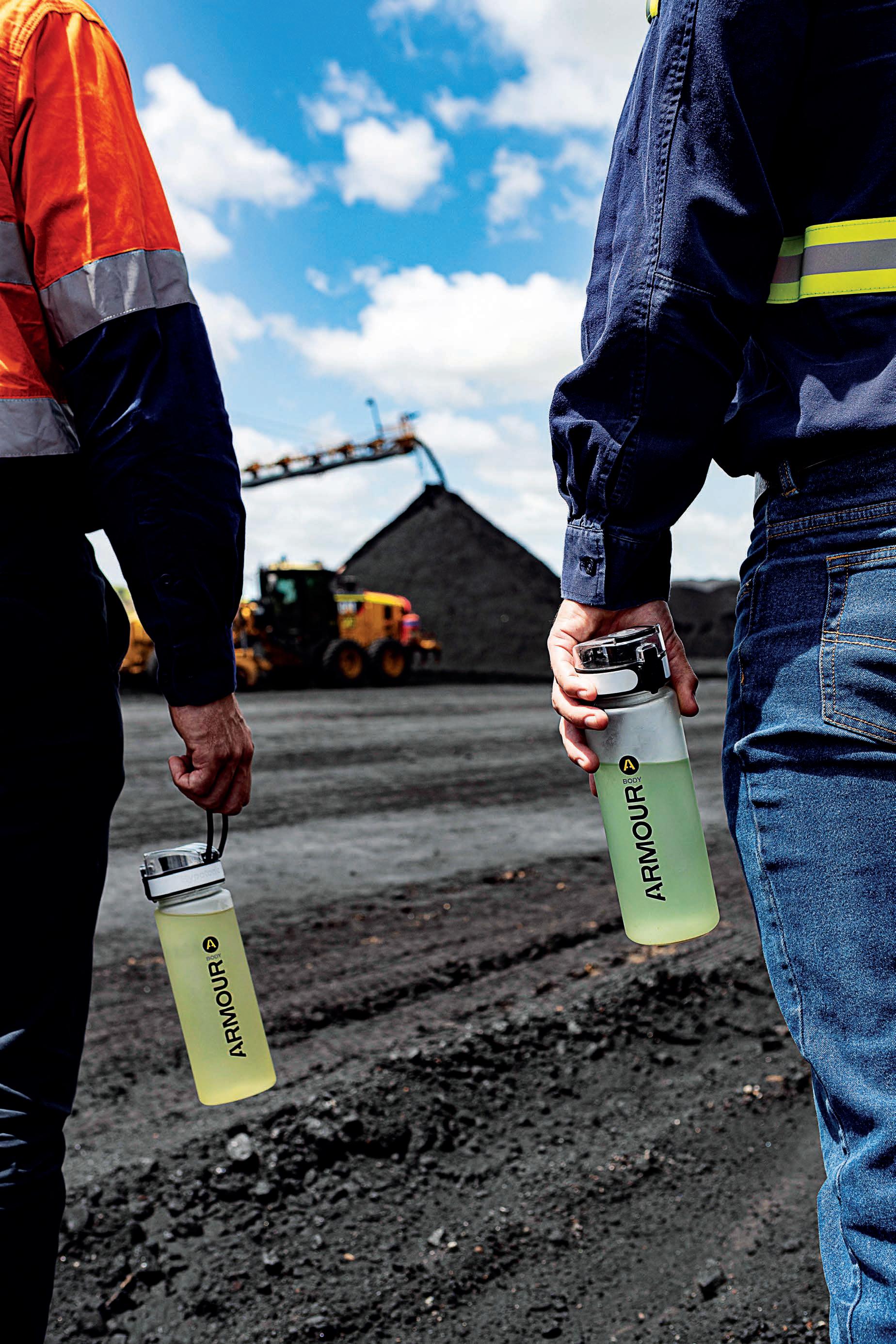
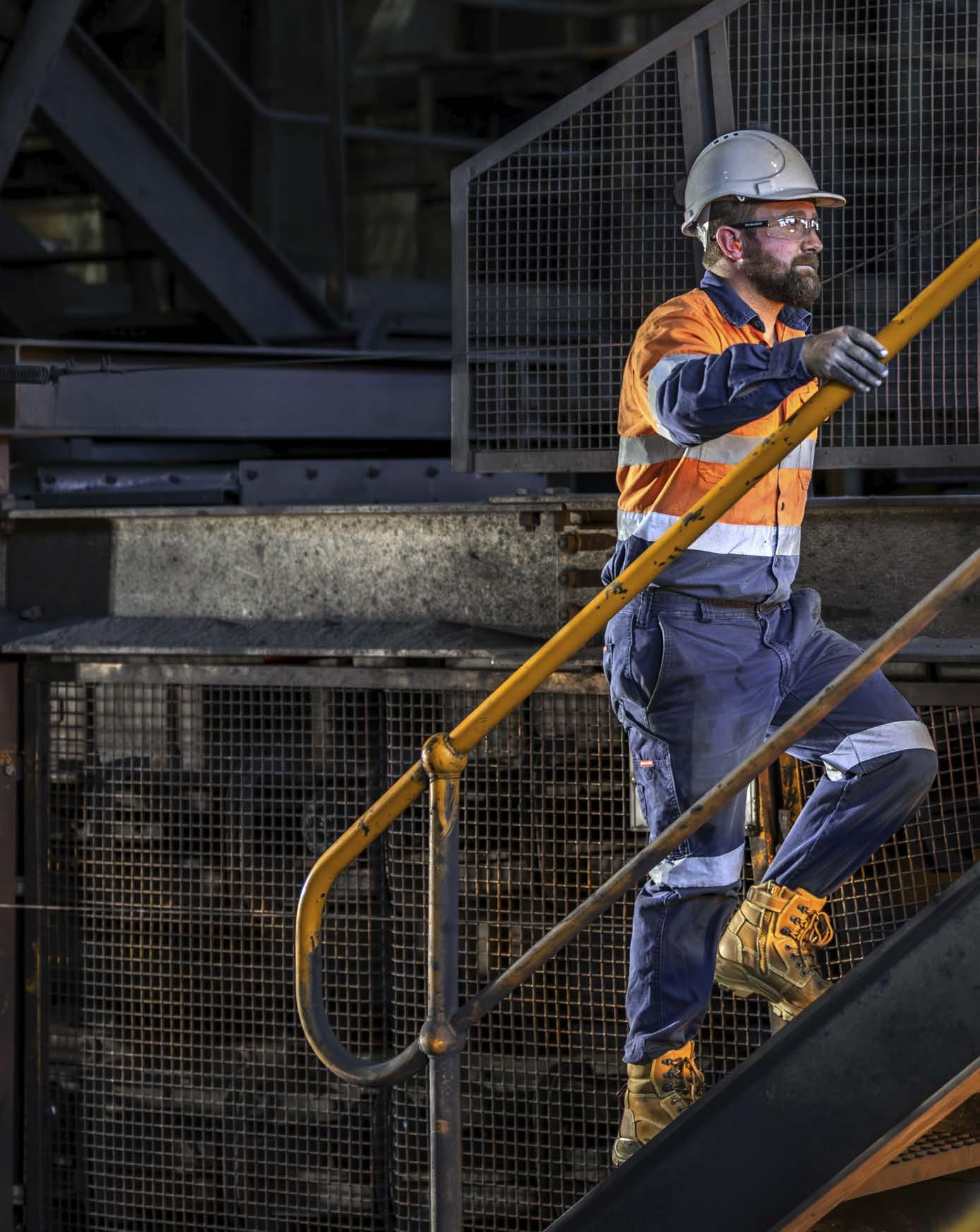
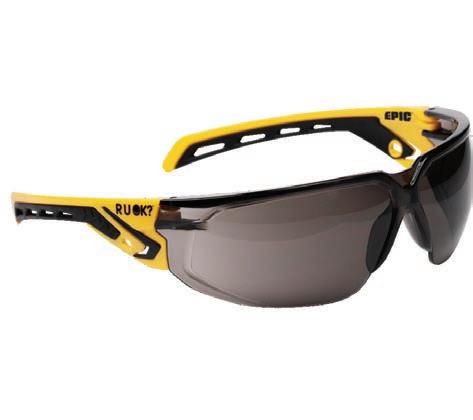
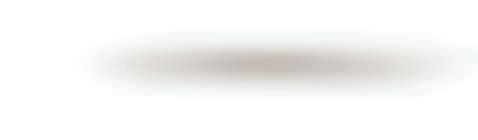
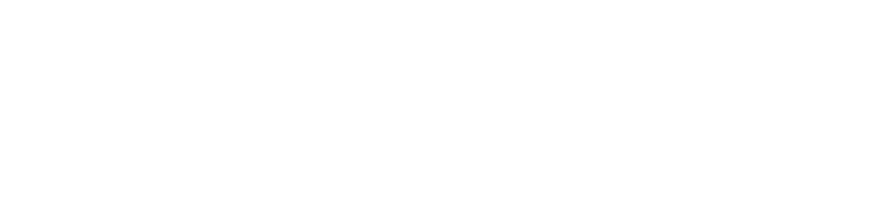
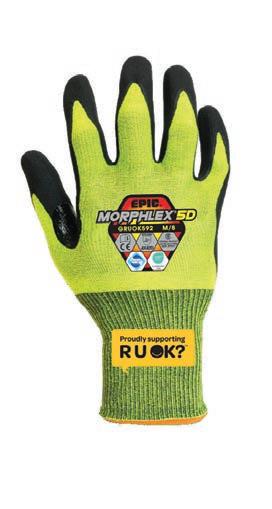
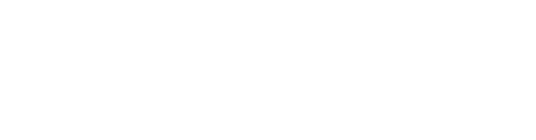
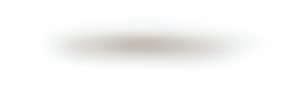
Reach out to your work mates. Look out for your work mates.
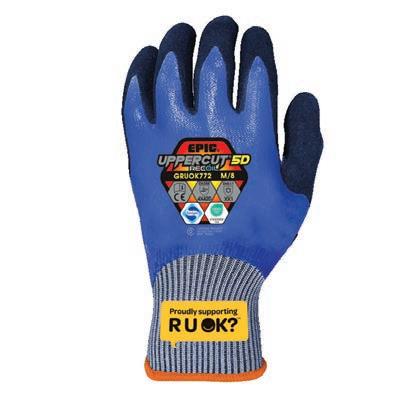
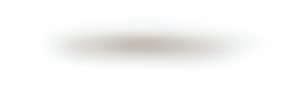
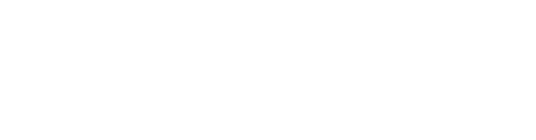
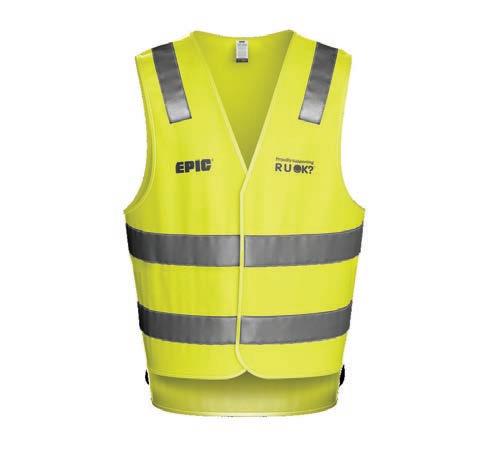

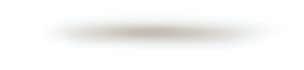
Make sure your work mates are seen and heard. Give your work mates a hand.
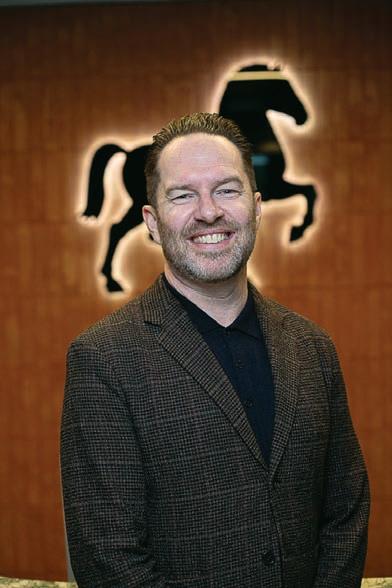
Reach out to your work mates. Look out for your work mates.
Make sure your work mates are seen and heard. Give your work mates a hand.
PAUL HAYES
thriving workforce.
That workforce needs a lot of considerations to truly thrive – and they aren’t all the most obvious.
Hydration, sleep, nutrition, air quality, respiratory health, filtration and mental health are just a few of the critical areas quickly coming into focus for mining companies looking to support their employees in continued success.
These elements are crystallising into innovations, initiatives, services and technologies that are changing the game when it comes to keeping employees in tip-top physical and mental health.
This issue of Safe to Work examines some of the innovators who are rising to the top of their respective fields in employee wellbeing and creating a foundation for a flourishing resources industry into the future.
Whether helping workers breathe easier, sleep better or be treated as the industrial athletes they are, the industry
players in these pages are truly making a difference at sites across Australia.
Elsewhere in this issue, we take a look at some of the most critical emerging trends affecting miners in the realm of health and safety.
This includes a new global genderneutral paid parental leave initiative, groundbreaking research into mental health and helping fly-in, fly-out workers get a better night’s sleep, as well as a deep dive into how training might just be one of the most important ways a mine site can stay injury-free.
The world of health and wellbeing has officially collided with Australian mining, opening the door for a workforce that is more equipped than ever to take on the all the challenges and opportunities the industry has to offer.
Paul Hayes Managing Editor
products that feature natural formulas with no artificial colours, sweeteners, or flavours.
Body Armour harnesses he power of advanced clinical research, carefully selecting ingredients backed by data to create products that deliver genuine and tangible health and performance results.
COO
CHRISTINE CLANCY
MANAGING EDITOR
PAUL HAYES
Tel: (03) 9690 8766
Email: paul.hayes@primecreative.com.a
ASSISTANT EDITOR
KELSIE TIBBEN
Tel: (03) 9690 8766
Email: kelsie.tibben@primecreative.com.au
JOURNALIST
ALEXANDRA EASTWOOD
Tel: (03) 9690 8766
Email: alexandra.eastwood@primecreative.com.au
JOSEPH MISURACA
Tel: (03) 9690 8766
Email: joseph.misuraca@primecreative.com.au
CLIENT SUCCESS MANAGER
JANINE CLEMENTS
Tel: (02) 9439 7227
Email: janine.clements@primecreative.com.au
RESOURCES GROUP LEAD
JONATHAN DUCKETT
Mob: 0498 091 027
Email: jonathan.duckett@primecreative.com.au
BUSINESS DEVELOPMENT MANAGER
JAKE NIEHUS
Mob: 0466 929 675
Email: jacob.niehus@primecreative.com.au ART DIRECTOR
8 Is your mine up to scratch?
With 2025 now well underway, the NSW Resources Regulator spoke to Safe to Work about its new set of compliance priorities for the state’s mines.
14 Industrial athletes rise up Body Armour director Toni McQuinn outlines how today’s heavy-industry workers should be supported in their health and recovery as the ‘industrial athletes’ they are.
26 Leading worker wellbeing
Research has found a significant link between ‘transformational leadership’ and improved employee psychological wellbeing and safety culture.
36 Why the right mining boots are critical
For those working in the mining sector, getting the correct safety footwear is about much more than choosing a comfortable pair of boots.
28 Remote work done differently
Anglo American has successfully implemented remote-controlled operations at its underground coal mines in Queensland’s Bowen Basin.
22 Waking up to worker safety
The latest solution from Ethos Health helps miners track their fatigue levels and unlock new levels of productivity.
30 Fighting FIFO fatigue
A new study from Edith Cowan University has discovered methods FIFO workers can use to get better sleep while on-site.
Mine safety is about more than technology. Change management and data insights are important, too. Hexagon integrates systems for collision avoidance, operator alertness and vehicle intervention into your mining workflows. On top of that, we partner with customers to engage and re-engage operators in a cycle of continuous improvement. Our solutions are OEM-agnostic, smart enough to adapt to mixed fleets and diverse sites while helping you to exceed safety and productivity standards.
One partner. For the life of your mine.
COAL REVEALS HOW IT HAS KEPT ITS NARRABRI OPERATIONS INJURY FREE FOR OVER 5000 DAYS – THE EQUIVALENT OF 13.5 YEARS.
Whitehaven Coal celebrated a major milestone in January, marking 5000 days without a lost time injury (LTI) at its Narrabri coal handling and preparation plant in New South Wales.
The Narrabri mine is Whitehaven’s only underground operation and employs around 500 people, the majority of which live locally. The mine is approved to produce 11 million tonnes per annum of high-quality thermal coal from its fully automated longwall until 2031.
The new safety record is equivalent to more than 13.5 years without an LTI, and 60 months free of total recordable injuries.
keeping up its trend of protecting its workers into the future.
“We’re committed to driving continuous improvement in our approach to health and safety outcomes,” Howland told Safe to Work. “As we look ahead to 2025, we will continue to take a proactive approach to managing risks and focus on the controls that are most critical to protecting the health and safety of our people.
Howland said the milestone shows unwavering commitment to safety and care from every member of the team.
“We look forward to building on our positive track record to ensure our people get home safe and healthy after work every day,” Howland said.
“This remarkable achievement is a testament to the proactive safety culture we’ve worked so hard to build.”
Howland emphasised that the feat is also a reflection of how the team members look out for each other, ensuring safety is always a top priority – whether at work or at home.
“This success is the result of everyone’s diligence, vigilance, and dedication,” he said.
“Whether it’s the crews operating on the front lines, maintaining equipment or supporting operations, our commitment to safety ensures that we continue to thrive without incident.”
Whitehaven is seeking to extend the
Whitehaven’s new safety record is equivalent to more than 13.5 years without an LTI.
The NSW Department of Planning, Industry and Environment has previously recommended the project is in the public interest and approvable subject to conditions, and the project was approved by the NSW Independent Planning Commission in April 2022.
The project was approved by the Federal Government in September 2024, subject to conditions, in accordance with the Environment Protection and Biodiversity Conservation Act 1999 (Cth)
Whitehaven is proposing to extend the operation by extracting coal to the south of the existing mine, which would in turn extend the life of the mine from 2031 to 2044, providing continued employment for hundreds of locals.
Stage three would also allow for the socioeconomic benefits associated with the mine, including spending with local businesses and royalty payments to the NSW
Government, to continue for more than a decade.
These benefits are estimated to be in the region of $599 million across the state, as well as $317 million in direct wages to the local community.
An additional $259 million in royalties will be paid to the NSW Government, as well as a further $247 million spent with local suppliers.
Notably, stage three will see coal be extracted using the
underground longwall mining method already used successfully and safely at the mine, and using the established surface infrastructure, including the existing coal handling preparation plant, rail loop, box cut and offices.
This automated longwall method has already proven to be effective at keeping miners safe for more than 13 years, longer than the proposed extension to the mine’s life.
The New South Wales Resources Regulator has turned its attention to increasing safety compliance across a range of key areas.
Every six to 12 months, the Regulator refreshes its priorities in an effort to maintain safety, sustainability and regulatory adherence within the mining sector.
These priorities are shaped by incident data, compliance assessments and an analysis of mine hazards and risk profiles.
“The Regulator’s compliance priorities are published to increase transparency, community and industry confidence in regulatory activities and increase levels of voluntary compliance,” NSW Resources Regulator executive director Peter Day told Safe to Work
“The findings and analysis of trends are published on the NSW Resources website at the completion of each targeted assessment.”
The publication of compliance priorities is designed to provide transparency and ensure industry confidence in the Regulator’s activities. By identifying key risks and compliance gaps, the Regulator aims to drive voluntary compliance and improve overall safety within NSW mining operations.
“By targeting key areas of risk and supervision management across NSW mines and quarries, we’re ensuring the safety of workers, regardless of tasks they are carrying out,” Day said.
“Our inspectors are dedicated to preventing incidents and increasing health and safety management education, engaging directly with operators and ensuring risks are effectively controlled.”
The Regulator takes a proactive and risk-based approach to enforcement, aiming to ensure the mining industry meets its legal obligations. The priorities outline the key expectations for compliance, enforcement processes and regulatory methods.
Assessment programs play a central role in ensuring that mine sites are effectively managing principal hazards. These programs involve both scheduled and unannounced visits, allowing inspectors to assess compliance under real operating conditions.
“Producing and sharing these types of reports on our activities demonstrates our consistent and responsive regulatory approach,” Day said. “It builds industry confidence that our compliance activities are robust and comprehensive.”
The July–December 2024 compliance program has been completed, with individual reports on targeted assessment programs set to be released soon.
“Generally speaking, our compliance priorities are set out to ensure a safe, sustainable and innovative mining industry in NSW,” Day said.
“These priorities help us provide information and guidance about safety, environmental and other regulatory obligations, highlight best practice and make regulation transparent.”
than just standard; they are crucial in helping to ensure that mine sites adhere to safety standards and compliance obligations.
January–June 2025 include a major review of the NSW mining competency system, which has remained largely unchanged since the 1990s. The review aims to assess and recommend improvements to ensure the system remains fit for purpose.
development of the Roads or Other Vehicle Operating Areas Technical Reference Guide (TRG) for surface mines. The Regulator is seeking industry feedback on the guide, which will provide a framework for managing vehicle interactions on mine sites.
the assessment of risk management at mine sites and the supervision of tailings dams.
2024, 31 incidents across open-cut and underground mines identified inadequate hazard identification or control or supervision as contributing factors. In the same period, assessments resulted in 80 notices which referenced supervision or risk management.
cut activities in 2025, NSW Regulator inspectors will be visiting coal and metalliferous mines, with a focus on risk management and supervision.
unannounced on backshifts and weekends to include work undertaken
outside of production areas and target plant or machine shut-down work.
A total of three tailings failures occurred internationally in the 12 months to November 2024.
According to Day, the possibility of catastrophic failure remains a credible risk to workers.
“A safe tailings dam is dependent on effective critical controls, maintained to an adequate standard,” Day said. “As part of the planned inspection activities on tailings storage facilities and
signs of early failure and to protect workers on and below dam walls.”
Inspectors will be attending tailings dams and emplacement areas focusing on principal hazard management plans, dam break studies, failure mode analysis and monitoring system effectiveness in installation, maintenance and escalation.
Mine operators can take steps to ensure they meet compliance expectations by reviewing standardised assessment criteria and making necessary improvements based on feedback from targeted assessments.
“Mines should be aware that all inspections under a targeted assessment program involve
a standard set of assessment criteria, which is transparent,” Day said. “This ensures consistency across all the inspections.
“At the conclusion of each targeted assessment, the mine is provided feedback on their current compliance and areas for improvement.”
The Regulator also offers industry resources, including fact sheets, reports and training materials, which are available on its website. This includes the results of previous compliance priority investigations.
With the publication of its compliance priorities for 2025, the NSW Resources Regulator remains committed to ensuring mine operators meet their obligations and that industry safety continues to improve.
Regulator assessments will be made unannounced on backshifts and weekends.
GRX25 builds on the legacy of the Austmine Conference, which has long been a cornerstone of mining innovation.
GRX25 WILL SHOWCASE AUSTRALIA’S TECHNOLOGY LEADERSHIP AND INNOVATIVE SOLUTIONS SET TO SHAPE THE FUTURE OF THE GLOBAL RESOURCES SECTOR.
The Global Resources Innovation Expo (GRX) is debuting in Brisbane from May 20–22, representing a dynamic collaboration between Austmine and AusIMM.
This partnership merges the strengths of two leading industry associations to deliver a global platform for innovation and discussion in the resources sector.
GRX25 builds on the legacy of the Austmine Conference, which has long been a cornerstone of mining innovation. The key theme of the event is “embracing a new era”, as the conference is rebranded to reflect the dynamic changes currently happening in the industry.
This evolution promises to amplify the event’s impact by bringing together a broader and more diverse audience under the banner of “by industry, for industry”.
Austmine chief executive officer Chris Gibbs Stewart said she is proud that the conference has become the leading innovation events on the global mining calendar.
“Since its inception in 2005, we have showcased world-leading
METS [mining equipment, technology and services] organisations with a directed focus on driving the importance of innovation in our industry,” she said.
“Our partnership with the AusIMM allows us to amplify aligned messages and offer greater relevance to a global audience.
“Through this collaboration, we are uniting our powerful communities to drive important conversations, showcase innovation, and elevate the industry to greater heights.”
The joint effort between Austmine and AusIMM is designed to unite their respective networks to spark conversations, foster collaboration, and propel the resources industry forward.
GRX25 will serve as a deep dive into how new technology can improve efficiency, safety and performance in this new era.
The event will be an opportunity to learn from industry pioneers and examine how other professionals are leading change, driving innovation, enhancing environmental sustainability and fostering resilient communities around the world.
The program includes five plenary presentations and multiple breakout sessions, as well as opportunities to network alongside the chance to explore the exhibition floor and engage with industry peers.
By leveraging each organisation’s expertise and influence, the event aims to enhance the reach and relevance of Australia’s mining innovations on a global scale.
Attendees can expect a showcase of cutting-edge technologies, thought-provoking presentations, and networking opportunities designed to tackle industry challenges and drive progress. GRX25 will also provide a platform for international collaboration, strengthening Australia’s position as a leader in mining and resources innovation.
With the inaugural event just months away, industry players are already preparing to leverage this opportunity for growth, knowledge-sharing, and the exchange of best practices.
GRX25 is set to be a transformative event for Australia’s mining and resources sectors, cementing its place as a key milestone in the global industry calendar.
PREMIUM RECOVERY AND PERFORMANCE SOLUTIONS SPECIFICALLY DESIGNED FOR HEAVY INDUSTRY
MAKING SURE EMPLOYEES ARE PHYSICALLY AND MENTALLY HEALTHY IS A CORNERSTONE FOR MANY OF AUSTRALIA’S MINING COMPANIES.
Keeping healthy doesn’t just mean regular gym sessions and a balanced diet.
In the mining industry, where workers are often away from family and friends for extended periods of time, keeping mentally healthy is just as important.
Recognising this situation, some of Australia’s biggest mining companies have dedicated considerable resources to setting up wellbeing initiatives designed to improve the physical, mental and emotional health of each employee.
Safe to Work takes a look at the initiatives that three of the country’s major miners have in place.
MINERAL RESOURCES
Mineral Resources (MinRes) employs a team of on-site health and wellbeing advisors who are responsible for a range of health-focused initiatives to support, maintain and improve employee health. The program covers physical and mental health, injury prevention and management, and lifestyle and social wellbeing.
“MinRes considers mental health as important as physical health and critical to employee engagement and productivity,” the company said. “With over 80 per cent of our employees working remotely across our operational sites, our people and their families may face challenges to their mental health.
“Our Mental Health Framework helps guide MinRes’ vision to be a recognised employer of choice, prioritising positive mental health and wellbeing alongside physical health and safety.”
In 2022, MinRes opened a health centre at its Walters Drive headquarters in Western Australia to provide even more comprehensive healthcare services to its employees.
Not only does the centre house a team of counsellors and mental health professionals, it also employs general practitioners who can administer vaccines, arrange specialist referrals and order pathology and radiology tests to keep MinRes workers in tip-top shape.
Like MinRes, Rio Tinto places a strong emphasis on the success of its employees on and off site.
The iron ore major offers initiatives designed to promote holistic wellness, from mental health support services to physical fitness programs.
In 2023, Rio Tinto expanded its mental health resources with the introduction of on-site counsellors at its key locations. It also introduced 24-hour access to confidential helplines to support employees facing challenges in their professional and personal lives.
“Caring for each other is one our values – it is part of who we are and the way we work, every shift, every day,” Rio Tinto said.
“Nothing is more important than the safety and wellbeing of our employees, contractors and communities.”
Rio Tinto supports global mental health campaigns such as R U OK? Day and World Mental Health Day in September and October, respectively. The company places a large emphasis on storytelling, with anyone from graduates to executive team members encouraged to speak up about their struggles and successes.
People experiencing mental health issues are also encouraged to reach out to peer supporters –employees who have put up their
hands to listen to their colleagues and help them access professional services should they need it.
“As a peer supporter, I help people around our site who are struggling with problems,” Rio Tinto mobile mining equipment fitter and peer supporter Taurai said.
“We spend two thirds of the year on a worksite, so it’s important people have a support network inside work.”
BHP has been working to make mental health a company priority since 2015, with a big focus on acknowledging, supporting and destigmatising those experiencing these types of issues.
The company dedicates the entire month of May to Mental Health Month. Every year, team members across the Big Australian’s operations participate in the campaign, which aims to promote open conversations, reduce stigma and empower people to manage and prioritise their mental health.
“At BHP, we’re committed to supporting mental wellness in our workforce and those in the
communities in which we operate,” BHP chief executive officer Mike Henry said.
“A number of years ago, we asked our employees and contractors what more we could do to better support them and their mental wellbeing. The conversations that followed … led us to some important insights and actions.
“We have developed a suite of mental health initiatives and tools to support our workforce and their families. We have embedded our mental health framework into our management rhythms and routines and we regularly monitor our progress.”
November is also a special month for BHP as the company participates in Movember, a charity working to change the face of men’s mental and physical health. Since 2017, BHP has raised more than $2.1 million for the Movember Campaign.
These comprehensive approaches from MinRes, Rio Tinto and BHP have helped to set a benchmark for the mining industry, fostering supportive workplaces where the physical, mental and emotional health of employees can thrive.
BODY ARMOUR DIRECTOR TONI MCQUINN OUTLINES HOW TODAY’S HEAVY-INDUSTRY WORKERS SHOULD BE SUPPORTED IN THEIR HEALTH AND RECOVERY AS THE
Aprofessional sports athlete is often compared to a computer chip. Optimised, highly sensitive and calibrated to perform at the peak of what is humanly possible under extreme circumstances.
It makes sense, then, that these athletes take their health seriously
‘INDUSTRIAL ATHLETES’ THEY ARE.
and ensure every aspect of their nutrition, hydration and recovery is carefully analysed and optimised to achieve peak performance. Modern science drives the composition of their solutions, looking at what goes into athletes’ bodies to help them run faster, jump higher or lift heavier, while ensuring long-term health is not at risk
In contrast, workers in heavy industries, such as those in the mining and resources sector, are regularly exposed to physically demanding and/or high-risk tasks that demand sustained focus, quick decisionmaking and physical endurance. Even a slight decrease in these capabilities can mean the difference between a
safe work environment and a potential safety incident. They too are regularly asked to perform under tough conditions across extended periods.
It stands to reason, therefore, that industrial workers should be treated with the same level of attention to ensure their health is in tip-top condition and their safety risk profile reduced at every possible opportunity.
While ‘industrial athletes’ are often provided recovery solutions such as hydration products, the quality of their composition can often be subpar, with the long-term effects rarely scrutinised. What’s more, training on the fundamentals regarding recovery and the links between nutrition and performance are often under-applied.
Body Armour is an industrial hydration, nutrition and sleepsupport company dedicated to raising awareness and improving the health and wellbeing of Australia’s heavyindustry workers.
The company’s Hydration+ range is formulated with five key electrolytes, a vitamin complex and nootropics, served in several formats, including healthy cordials, icy poles, carbonated cans and powders designed for mine workers to grab and go in the form that suits them best.
Body Armour’s Sleep blend is made up of nine active ingredients, including natural sedatives, is mixed into water and taken before bed, aiming to support industrial athletes contending with the physical and mental demands of long shifts and irregular schedules.
The Body Armour team ensures its research is peer-reviewed, working with trusted third-party partners in the pharmaceutical, food and sports industries to stay on the cutting-edge of nutrition and recovery investigative analysis.
Safe to Work sat down with Body Armour director Toni McQuinn to explore the question: why aren’t we investing the same level of resources into the hydration, nutrition and recovery of industrial athletes as we do for sports athletes?
“I’ve always found it surprising that workforce education on nutrition, and
its direct impact on performance, isn’t a core pillar of site safety strategies,” McQuinn said.
“A drop in cognitive function, energy levels, or reaction time doesn’t just reduce productivity; it increases an individual’s safety risk.
“Beyond safety concerns, the evidence is clear: effective recovery and optimal nutrition lead to enhanced performance and productivity.
“Given these direct benefits, organisations should view this as a critical strategy under their productivity and safety pillars, a very small investment in the workforce that ultimately drives better outcomes for both individuals and the business.”
What do mining companies and their industrial athletes need to know when it comes to optimal performance?
McQuinn emphasised the importance of understanding the
modern industrial athletes are given the best shot at long-term success. He broke down key biological steps of the recovery process:
Sweat depletes water and electrolytes, disrupting hydration and cellular function. Water consumption balanced with essential salts enables the body’s rehydration.
Physical activity depletes glycogen stores, which are replenished after exercise using absorbed carbohydrates.
Heavy physical activity causes microtears in muscles, repaired through protein synthesis using amino acids.
Physical exertion generates free radicals, causing oxidative stress and inflammation that can be reduced through the consumption of antioxidants like vitamin C.
Effective recovery protocols can mitigate the immune system suppression caused by prolonged physical stress, making the body less
recovery protocols to operate at maximum capacity. While there is a broad spectrum of nutrients essential for bodily function, McQuinn argues that their application must be tailored to the environment, conditions and tasks an individual faces.
McQuinn outlined some of the key nutrients industrial athletes need to understand:
blend of electrolytes,” McQuinn said. “This replenishes what is lost through sweat and ensures sustained hydration without relying on sugary additives.”
B-complex vitamins (B1, B2, B3, B5, B6, B7, B9, and B12) are essential for energy metabolism, helping convert food into usable energy. They also support brain function and combat fatigue.
Body Armour products include the full B-vitamins complex in clinically effective doses that are developed with heavy-industry workers in mind to enhance energy levels and cognitive clarity throughout long shifts.
Amino acids are the building blocks of protein, crucial for muscle recovery, repair and endurance.
Amino acids like L-Glutamine are present in Body Armour recovery products to aid in muscle repair and reduce downtime between shifts.
Antioxidants combat oxidative stress caused by physical exertion and environmental factors, reducing inflammation, improving recovery and enhancing immune defence.
Natural antioxidants are included in Body Armour products to protect workers from wear and tear while promoting long-term health.
Magnesium supports over 300 biochemical reactions in the body. It plays a pivotal role in energy production, muscle contraction and relaxation, and sleep quality. It is a mineral that helps to combat cramping.
Body Armour’s range provides magnesium and calcium in bioavailable forms, addressing deficiencies in industrial athletes and improving muscle recovery and relaxation after intense physical activity.
Low-GI (glycaemic index) carbohydrates provide a steady release of energy, preventing spikes
Electrolytes are vital for muscle function, nerve signalling, hydration regulation and overall body performance.
and crashes often associated with high-sugar snacks or drinks.
Body Armour products avoid high sugar content and focus on clean, sustained energy sources to keep workers energised and focused throughout long shifts.
A ‘nootropic’ is the term given to any substance that has been proven to improve cognitive function, including memory, focus, mental clarity, and overall brain performance. They are typically plant-derived.
“By incorporating the right nootropics into daily routine, industrial athletes can enhance their cognitive function, reduce mental fatigue, and stay focused and alert throughout long and challenging shifts.”
McQuinn said artificial colours have typically been used by the food industry to make liquids and solids look more appealing to the eye. But recent studies have shown they pose significant long-term health risks
when consumed in the quantities typical for industrial athletes.
“We raise this as a concern in our hydration solutions due to the volume a typical heavy industry operator consumes daily, weekly and yearly,” McQuinn said. “Compounding effects can be devastating and irreversible.”
Thaumatin is a natural, plant-derived sweetener extracted from the katemfe fruit, native to West Africa.
Unlike synthetic sweeteners like sucralose, thaumatin has a negligible effect on blood sugar levels, making it a better choice for those consuming regular volumes of hydration drinks, managing their glucose intake, or who follow low-carb diets.
Body Armour uses thaumatin over other sweeteners in its hydration products as part of its commitment to providing natural, high-quality products that prioritise health and performance.
“It’s also non-cariogenic, meaning it won’t contribute to tooth decay,” McQuinn said.
The science of recovery can seem complicated, but McQuinn believes it doesn’t have to be. Body Armour’s focus is to formulate solutions to take the guesswork out of supporting optimal recovery and overall health.
Body Armour is determined to empower industrial athletes and employers with the tools and knowledge to make decisions that will lead to better health outcomes, higher rates of wellbeing, and increased productivity and performance.
“One of our core pillars is harnessing clinically advanced research and modern science to guide our product development and the educational content we provide,” McQuinn said. “Our experienced team of chemists and naturopaths bring deep expertise to everything we do, ensuring our offerings are grounded in cutting-edge knowledge.
“Today’s industrial workers should be treated like the high-performing athletes they are and given adequate tools to recover so they can continue performing at optimal levels.”
An esteemed product and service level provider to the mining industry since 2007, Industree Group has built its reputation on providing personal protective equipment (PPE) and safety solutions to the sector.
“Our mission is to deliver innovative, fit-for-purpose safety solutions that enhance workplace protection and compliance while prioritising comfort and performance,” Industree Group marketing director Chris Foster told Safe to Work
Among its PPE offerings, Industree Group also offers innovative recycling programs to help mining
companies reduce waste and improve sustainability via its epicycle PPE recycling and repurposing program.
Also on offer is Industree Group’s comprehensive Respirator Fit Testing programs, helping to ensure workers receive the correct fit for their respiratory equipment to maximise safety and compliance.
“By providing cutting-edge safety solutions, fit-testing programs and sustainability initiatives, Industree Group helps mining companies protect their workforce, improve compliance and enhance operational efficiency and meet ESG [environmental, social and governance] goals,” Foster said.
A commitment to innovation and safety is central to Industree Group’s mission to help mining operations run smoothly while prioritising worker wellbeing.
“In the Australian mining sector, Industree Group has established strong partnerships with key industry players to supply advanced safety products tailored to the harsh and demanding conditions of mining operations,” Foster said.
“From protective clothing and respiratory solutions to footwear and hand protection, our products are designed to meet and exceed Australian safety standards.”
Industree Group’s extensive product range and services have enhanced personal safety for decades by improving operational efficiency and supported compliance with industry regulations.
But safety doesn’t stop at PPE.
“Beyond product supply, we actively engage with industry partners to support safety initiatives and best practices within the mining sector,” Foster said.
“Through our partnership with R U OK? we promote a culture where people feel confident asking and answering this simple yet important question among workers in high-risk, high stress industries.”
R U OK? is a national suicideprevention charity that encourages people to stay connected and have conversations that can help others through difficult times. Industree Group’s partnership with the charity is an especially important one for the business and has become part of its daily culture.
“Industree Group has developed co-branded R U OK? workwear and PPE, reinforcing the importance of checking in with colleagues on-site any day,” Foster said.
“The ever-growing product range includes safety glasses, gloves, safety vests and respirators with many more products to come. A portion of each sale goes to R U OK? to support and fund free resources that increase
the willingness and confidence of all Australians to recognise the signs someone is struggling, start a genuine conversation and lend appropriate support.”
Foster said the partnership ensures that regular, genuine conversations become a standard part of workplace safety, encouraging workers to check in on their colleagues and seek support when needed.
“By integrating the R U OK? message into the everyday work environment, Industree Group is driving meaningful change in industries where mental health awareness is critical and massively underrepresented” he said.
“Customers appreciate the dual purpose of the R U OK? product range – providing premium protection and quality while also fostering a culture of care and support in high-risk industries.
“Many businesses report an increase in mental health awareness and open conversations among teams, demonstrating the success of this initiative.”
Foster said customer feedback on the partnership has emphasised to Industree just how important these kinds of partnerships and initiatives are.
“One customer introduced the R U OK? PPE range along with their mental health training sessions and said the response has been overwhelmingly positive,” he said. “It’s a great way to keep the conversation going year-round.
“Another said they love that part of the proceeds go towards supporting R U OK? initiatives, saying it feels good knowing their PPE investment is making a difference beyond site safety alone.”
As Industree Group moves into 2025, the company is looking forward to continuing its focus on the health and wellbeing of the mining industry.
“Industree Group remains committed to innovation and sustainability, with a strong focus on new product development, eco-
friendly initiatives, and expanding worker wellbeing through our partnership with R U OK?,” Foster said.
“Our 2025 objectives are designed to enhance workplace safety while driving positive change across industries like mining, construction, infrastructure and manufacturing.”
With its high-quality, innovative and customisable safety products and solutions, there’s little doubt that Industree Group stands out as a go-to provider for the mining industry.
“Our commitment to cuttingedge technology, worker wellbeing and sustainability ensures that businesses receive the best in both protection and performance,” Foster said.
“Our commitment to customisation, advanced technology and industry partnerships makes us a trusted partner for businesses seeking nextlevel personal and workplace safety.”
Kathy Hubble has more than three decades’ experience in the medical field as a clinical nurse consultant in chronic pain management and psychology.
She has seen first-hand how chronic pain can have severe and long-lasting impacts on a person’s life. In particular, Hubble has seen how workplace injuries or chronic pain being managed by those in heavy industries like mining can affect not only people’s lives but their careers.
She has also worked as a returnto-work technical specialist and senior claims manager in the insurance sector.
This mix of experience has seen Hubble develop a specific interest in helping those with chronic pain and workplace injuries navigate not only their own healing journey but the healthcare journey.
“I’ve seen the good, the bad and the ugly of treatments and the management of chronic pain in all domains,” she told Safe to Work
Hubble said she found those who were under workers compensation, or some form of income protection claim, often had worse health outcomes than their non-workplacerelated injury counterparts.
These challenges inspired Hubble to develop a non-medicinal system that could be accessed by patients dealing with chronic pain.
“We wanted to supply these individuals with an evidence-based platform that would allow them to access a behavioural program based on what is being administered in pain clinics,” she said. “We developed an app that can be accessed instantly on any device and provide tailored care for patients at any stage of their healing process.”
The Amelio Health app uses a patient’s own data to develop its programs. By using a wearable device like a smart watch, users can input live data that alerts the platform to their present state. The platform is proving beneficial for industries like mining,
where remote sites can make it difficult for patients to receive consistent, tailored care.
“One of the biggest challenges encountered by miners is access,” Hubble said. “With the Amelio Health app, we can develop behavioural feedback through wearable devices that is sent through notifications to alert these workers to changes in their body immediately, rather than having to go off-site to receive health advice.”
Every module on the Amelio Health app has been mapped back to the core competencies for the International Association for the Study of Pain (IASP), a global leader in the study and practice of pain management.
IASP brings together scientists, clinicians, healthcare providers and policymakers from around the world in pursuit of their mission to help those in pain. Its competencies are considered the global standard for effective healthcare.
Hubble said the app is also based on Bloom’s taxonomy of learning theory, a set of three hierarchical models used to classify educational learning objectives into levels of complexity and specificity. The three lists cover learning objectives in cognitive, affective and sensory domains, namely thinking skills, emotional responses, and physical skills.
“As people’s knowledge increases, it changes their behaviour, which can have positive effects on their function and pain scores,” Hubble said.
A common treatment for chronic pain is opioids which, aside from being potentially addictive, can have lasting impacts on the body. Hubble said that, over time, opioid use can create hypersensitivity in the nervous system that continues to create pain long after the initial injury has healed.
Through 24-hour monitoring, app users can quickly pick up on early indicators of opioid over-use based on their oxygen saturation.
“We’ve been operating with much success in the UK for a few years now, and we have launched in the US and Australia, where people are already
seeing the benefits of the app,” Hubble said. “Our goal is to identify and reduce the suffering of those with chronic pain and who might be at risk from over-prescription.
“The Amelio Health app was able to identify dangerously low oxygen levels in one of our clients who had been prescribed three different opioids by her general practitioner.”
Hubble said fly-in, fly-out (FIFO) workers in the mining industry are under a lot of pressure to balance their work and home life, creating psychological stress. When this is coupled with chronic pain or illness, opioid dependency can become more of a risk.
“It’s critical that we find these people early in the process after their injury so we can help prevent them going down the pathway of using opioids that can ultimately make their chronic pain issues worse,” she said.
The Amelio Health app is biopsychosocially-based, combining the data from wearables, pain diaries, mindfulness techniques, behavioural changes, and sleep prioritisation. It’s designed to empower patients with the knowledge and tools they need to become an active participant in their healing and pain management.
Embedded into the app’s behavioural program, health professionals and rehabilitation consultants can see their patient’s live
data being tracked in real-time and follow their progress.
Amelio is also in the process of developing a new app that takes a completely AI-driven approach to healthcare. This multi-tiered app will soon be available to the public and features data-driven health coaches who can help users through their pain management programs.
Amelio has also developed a simple screening tool based on data collected from the company’s pain management program. By collecting this data over long periods, Hubble said it can present employers with strategies that can help them prevent incidents that lead to injury or ongoing chronic pain before they occur.
“We want to become even more intuitive in terms of the data we use so that we can eventually predict who is likely to develop a chronic pain problem based on a range of databacked parameters,” she said.
“This will help to reduce costs across the board for employers, insurance companies, and employees alike, as we will be able to help workers recover effectively before an ongoing problem develops.
“This groundbreaking digital health solution provides good evidence supporting a shift away from the mainstream approach to managing chronic pain toward a system based on outcomes.”
Since its inception in 2009, Ethos Health has been pioneering workplace health and safety solutions.
Based in Newcastle, New South Wales, the company has been improving health outcomes and operational efficiencies through technology-driven solutions. With a focus on high-risk industries like mining, Ethos Health is dedicated to fostering safer, healthier and more productive workplaces.
Ethos Health provides an extensive range of services and technologies designed to address critical human factors that impact workplace health and safety. These include fatigue management, injury prevention, lifestyle disease mitigation, and mental health support.
The company’s approach is rooted in collaboration, ensuring its solutions align with the needs of the workforce – including those on a mine site.
“People are often surprised when they hear about our services to mining clients,” Ethos Health chief executive officer Trent Watson told Safe to Work “They say it must be hard to engage them in health initiatives.
“I haven’t met a worker yet that wants to be involved in a workplace that is unhealthy, unhappy or unsafe. Miners are no different.”
Watson emphasised the company’s purpose is to keep people healthy, happy and safe.
“We start off from an aligned position with the workforce and see ourselves as working together with miners to find strategies that positively impact their health,” he said.
Whether reducing injury risks, ensuring workers remain alert on long
shifts, or fostering mental and physical wellbeing, Ethos Health’s passion for improving workplace conditions is at the core of its offerings.
“When people are healthy, happy and safe, they work better, and that’s good for the worker and the business,” Watson said.
The Australian resources sector has long been a leader in workplace safety initiatives, setting high standards across heavy industry.
Ethos Health has contributed to this progress over the past 16 years, evolving its solutions in collaboration with the workforce to ensure meaningful impact.
“We develop and adapt our solutions in consultation with the workforce and make a point to provide services that also benefit workers in their homes,” Watson said.
“I would like to think our customers use Ethos Health because of our industry knowledge, our ability to provide innovation, and customer-
focused solutions that keep people healthy, happy, safe and productive at work and at home.”
One of the strongest indicators of Ethos Health’s impact is the continued trust and engagement of its clients.
“I think the best feedback we get is the relationships we have formed, the recurring work, and the utilisation of our technology by customers in mining and across other industries over many years,” Watson said.
“We have a saying at Ethos Health that ‘feedback is a gift’. We accept any feedback we can get from our customers. Good or bad, we utilise it accordingly – this allows us to continually innovate, adapt and improve.”
Ethos Health’s workplace health and safety specialists identify areas of concern and design tailored solutions and support
their clients through implementation and monitoring.
One standout service is Ethos Health’s fatigue management. The company works closely with mining clients to identify and mitigate fatigue risks, designing effective management systems and procedures, including:
• fatigue risk assessment and mitigation strategies
• development and refinement of fatigue management procedures
• implementation and monitoring via training and software solutions.
Central to this approach is FatigueTech, an app designed to automate and enhance workplace fatigue risk management.
“FatigueTech consolidates work-hour monitoring, practical risk assessment tools, personal fatigue assessment and support, journey management, and team compliance functions into a single app,” Watson said.
“Through real-time insights and automated tools, FatigueTech turns fatigue risk into an opportunity
to enhance safety, compliance and efficiency.”
The technology has already gained traction, with a range of mining clients using it on a daily basis. FatigueTech was recently recognised through an innovation award by Transport for NSW.
“We believe our FatigueTech software has the capability to change the way we view fatigue risk management,” Watson said.
“Rather than see it as a problem, we believe the real insights gained from using FatigueTech will transform it into an opportunity to enhance safety, compliance, and efficiency.”
Watson said Ethos Health wants to use tools like FatigueTech to “revolutionise” the delivery of healthcare and become a global leader in tech-enabled, patient-centric health services.
“Whether it’s preventing injuries, helping workers stay safe on long shifts or supporting their overall wellbeing, we know we can make a real difference,” he said.
“This passion for improving the health and safety of workers is at the core of our products and services, which are designed to ensure that workers are not only safe but also at their best, both mentally and physically.”
Safety Mate has been a trusted supplier of safety gloves and eyewear to a range of industries for more than two decades.
But the company isn’t just focused on physical protection; it also emphasises the importance of mental wellbeing and support.
As part of an ongoing commitment to improving mental health, Safety Mate is a proud partner of Black Dog Institute, a critical medical research institute that investigates mental health across the lifespan – from childhood to adulthood.
“Since 2021, Safety Mate and Black Dog Institute have worked closely on initiatives to support Safety Mate’s customers and the broader mining and construction sector,” Safety Mate director Clint Tee told Safe to Work. “This partnership also included participating in one of Black Dog
Institute’s workplace mental health training programs that is backed by research and delivered by experts.
“The program is designed to build employees’ awareness and understanding of their own mental health and how to have conversations with others.”
The collaboration centres around Safety Mate’s ‘Black Dog’ product range, which supports Black Dog Institute’s work in the mental health space.
The range includes five signature products: three safety gloves, the Black Dog Stream Evo safety glasses and the Skytec 3030V P2 respirators. A portion of profits are channelled directly towards the Institute, bolstering efforts in diagnosis, treatment and prevention of mental illnesses.
“All Australians deserve to feel safe at work, and that includes our
mental safety as well as our physical safety,” Black Dog Institute senior research fellow Dr Mark Deady told Safe to Work.
“Most people will spend more than a third of their adult lives working, and this could be even higher in roles that require regular travel or FIFO [fly-in, fly-out] schedules, so we know that mental health at work is closely connected to overall wellbeing.
“Increasing understanding of the signs and symptoms of mental ill-health is one of the first steps to building better mental health at work. It’s encouraging to see organisations like Safety Mate support their people by providing these important training opportunities.”
Each pair of gloves in the Black Dog range have been designed with comfort and durability in mind.
Known for being especially lightweight, the Black Dog Cut D safety gloves provide a high-quality cut level D resistance for those working in tough conditions.
The gloves are also renowned for having a certified ‘Made in Green’ label by Oeko-Tex, a certification that is a traceable product label for safe and sustainably produced products.
The label signifies environmentally friendly manufacturing, social responsibility, safe work environments, and materials free from harmful substances. It helps to assure consumers their products come from facilities that prioritise ecological and ethical standards.
According to Safety Mate, it is the first glove company to achieve such a label.
“This accomplishment highlights our commitment to leading the way in sustainable practices, demonstrating our commitment to environmentally conscious methods and ethical production standards,” Tee said.
Like the Cut D gloves, the Black Dog Impact Cut F gloves are renowned for their breathability, fit and comfort. Both gloves types feature a breathable nitrile coating and lightweight liner, while the Impact Cut F safety gloves have also received the Made in Green label.
Cut D and Cut F are joined by the Black Dog Impact Cut D Grip safety gloves. Built with level D cut resistance, these gloves are covered with the SuperGrip heavy-duty nitrile coating for maximum liquid- and oilresistant grip.
All Black Dog gloves are made with high-quality materials and are touchscreen compatible and soft in feel. For every pair sold, Safety Mate donates $1 to Black Dog Institute.
The Black Dog Stream EVO safety glasses were designed with high performance and maximum comfort and protection in mind.
Built with premium anti-scratch and anti-fog protection, the Stream EVO glasses feature helpful safety features such as a UV400 rating, lateral protection, slim temples for comfort when worn with ear protectors, and an adjustable anti-slip nose bridge. They are also soft and adjustable, and feature TempFLEX temple tips for a comfortable and secure fit.
The Stream EVO range replaces individual plastic packaging with a reusable microfibre storage pouch made from recycled materials.
Available in clear, grey and LED polycarbonate lens, the Stream EVO glasses are 100 per cent metalfree and feature slim temples to enhance comfort while worn with ear defenders.
There is also a foam gasket and adjustable headband available for additional protection.
For every pair of Black Dog Stream EVO safety glasses sold, Safety Mate donates $0.50 to Black Dog Institute.
The Skytec Black Dog 3030V is a P2certified respirator designed to protect workers against silicosis, harmful welding fumes and similar respirable hazards – essential in the wideranging environments of mining.
The respirator provides a fullfoam face seal and first-rate face
extended use. Further adding to the comfort is the respirator’s lightweight outer shell designed for challenging work conditions.
Featuring a four-point head strap adjustment and a pre-formed nose bridge, the Skytec Black Dog 3030V can be adapted to all face shapes, reducing the need for regular adjustments.
“The 3030V disposable respirators offer an outstanding level of protection demonstrated when conducting face fit-testing,” Tee said.
“The Skytec 3030V provides a fullfoam face seal, providing unparalleled comfort and fit, making long hours of wear surprisingly comfortable. Its adaptability makes it a versatile choice for diverse work environments and user needs.”
The respirator is also available in the smaller Skytec Black Dog 3030V-S.
Since forming its partnership with Black Dog Institute, Safety Mate has surpassed $1 million in donations to the organisation.
Tee said the Black Dog product range is more than just personal protection equipment; it symbolises mental health support and awareness.
“If we can contribute through a collaboration like this, we can help provide mental health information and resources to those that need it,” he said.
RESEARCH HAS FOUND A SIGNIFICANT LINK BETWEEN ‘TRANSFORMATIONAL LEADERSHIP’ AND IMPROVED EMPLOYEE PSYCHOLOGICAL WELLBEING
AND SAFETY CULTURE.
The idea of ‘transformational leadership’ has emerged as the most effective management style for developing workplace safety culture and enhancing employee psychological wellbeing, according to new research published in the International Journal of Occupational Safety and Ergonomics
The study (true to the tradition of highly specific academic titles) is called ‘The impact of leadership on workplace safety climate and employees’ wellbeing with particular focus on transformational leadership’.
Research from the study found that organisations have a need to prioritise leadership approaches that foster safety compliance and employee wellbeing, particularly in high-risk industries. Researchers evaluated more than 350 studies published between 2013 and 2023, comparing different leadership styles and how they affected employee wellbeing. This led to the crowning of transformational leadership as the optimal style.
A term thought first to have been coined in the 1970s, transformational leadership involves leaders focusing on individual employee development.
Transformational leaders know how to encourage, inspire and motivate employees to perform in ways that create meaningful change.
The result is an engaged workforce that’s empowered to innovate and help shape an organisation’s future success.
University of Doha for Science and Technology department of environmental health and safety and the study’s lead researcher Dr Haruna Musa Moda said transformational leadership has significant positive effects on workplace safety culture.
“Several factors are said to contribute to the rise of workplacerelated accidents, including poor safety attitudes and behaviour, exposure to various forms of pollutants, workload, leadership attitude and commitment towards the promotion of safety within the organisation,” Moda said.
“Interest regarding the associated impact of leadership style on employee safety and wellbeing across organisational settings is on the rise.”
The research demonstrated that safety-specific transformational leadership is particularly effective in improving safety outcomes.
Study co-author Dr Lekha Kozhiparambath emphasised that successful implementation requires comprehensive organisational commitment.
“It is reasonable to conclude that employees are more likely to exude positive behaviour where they believe their safety is valued by the organisation, hence the need for managers or supervisors who take their safety and wellbeing more seriously,” Kozhiparambath said.
The study found that effective leadership in safety contexts can be achieved by “either serving as a role model, engaging followers in collective problem-solving or demonstrating empathy towards subordinate wellbeing”.
“Transformational leadership characteristics and behaviour have long been established as having the ability to engage followers and gain their willingness to voluntarily take part in safety-related tasks,” it stated.
In heavy industries like mining, transformational leadership can empower workers with the support they need achieve a greater sense of wellbeing and contribute proactively to a safer workplace.
Mining is a tough job, and workers often deal with daily pain. Now you can get a 'Pain Team in Your Pocket' to help with everything from daily pain to chronic pain after surgery, injury, or illness like cancer.
Learn about the nervous system and how it sustains pain, and use your health data to manage and reduce it.
ANGLO AMERICAN HAS SUCCESSFULLY IMPLEMENTED REMOTE-CONTROLLED OPERATIONS AT ITS UNDERGROUND COAL MINES IN QUEENSLAND’S BOWEN BASIN.
Underground mining has traditionally relied heavily on hands-on methods of extracting minerals, often involving workers operating machinery on-site in confined spaces and hazardous conditions.
While automation gained momentum in other industries over the decades, mining operations still required a high level of direct human involvement – and many still do.
But today’s mining landscape is shifting as companies look to integrate automation and remote operation into their daily processes in more integral ways, aiming to improve efficiency and safety in their workforces.
The shift represents a significant change in how mines are managed, with an emphasis on reducing exposure to hazardous environments while optimising efficiency.
part of this transition. These centres enable Anglo to fully remove workers from underground environments.
In Queensland’s Bowen Basin, Anglo American has been developing and implementing remote operation technology across its underground coal mines with much success.
Anglo has five steelmaking coal mines in the Bowen Basin, along with additional joint venture interests in steelmaking coal and manganese, and base metals exploration projects in Queensland.
The past decade has seen the miner focus on automation, data analytics and digitalisation, gradually introducing new systems to reshape its approach to underground mining, culminating in making all of its Bowen Basin mines fully autonomous.
The introduction of remote operation centres (ROCs) across these company’s mining sites has been a key
Anglo recently celebrated a key milestone across its Bowen Basin mines with a 22,500-hour reduction in workers exposed to hazardous underground conditions.
Prior to Anglo’s focus on autonomous mining, the San Juan Mine in the US was reportedly the only known site to have successfully implemented sustainable remote mining operations. Expanding similar technology to multiple sites in Australia reflects the growing role of automation in the mining industry.
But the shift to remote operations has not been without challenges for Anglo, requiring the development of new technologies and operational processes. The transition has involved the implementation of more than 1000 new system initiatives over the past 10 years. Each development has
introduced new obstacles, requiring further technological advancements to meet the specific demands of underground coal mining.
While automation has reduced the need for direct human involvement in certain tasks, the company has emphasised that workforce expertise remains essential to mining operations.
According to Anglo head of operations Matt Cooper, experienced workers continue to play a critical role in the success of remote operations.
“Our people are irreplaceable, and we are equipping them to grow with the industry, preserving a legacy of knowledge that will always be essential to our success,” Cooper said.
“By developing state-of-the-art technologies and prioritising the wellbeing of our workforce through a collaborative approach, our steelmaking coal mines in Australia have emerged as leaders in the industry, reshaping the future of
As mining technology evolves, employees are being equipped with new skills to manage and operate automated systems. Anglo American has taken steps to ensure that long-standing knowledge within the workforce is not lost but instead integrated into the development and refinement of new technologies.
Anglo American Australia automation superintendent Matthew Wakeford said the rapid pace of technological innovation – especially in areas like data analytics, automation and digitalisation – had unlocked incredible opportunities for the mining sector to be safer, more productive and more sustainable.
“At Anglo American, we have reimagined mines where our people can remotely manage operations from a safe distance, using real-time data to make informed decisions,” Wakeford said.
Beyond the introduction of ROCs, the company has been trialling tele-remote dozer technology at its Capcoal Complex near Middlemount, Queensland.
The pilot program involves retrofitting a stockpile dozer with WiFi-enabled technology, allowing it to
The company expects that once fully implemented, the technology will reduce in-cab dozer exposure time by 45,000–75,000 hours annually.
Dozer operators are currently undergoing training to transition from manual to remote operation. The system is designed to provide operators with a similar level of awareness and control as they would have when operating a dozer in person.
The set-up includes six onboard cameras, external cameras around stockpiles and microphones that transmit sound back to the operator.
Feedback from workers has led to further refinements, with the company now exploring additional enhancements such as movement feedback through controls to improve the user experience.
“In pursuit of safety and efficiency, the mining industry has been a constant driver of innovation for generations,” Capcoal general manager George Karooz said.
“Operating our fleet of dozers from a safe distance will reduce the number of hours in the cab and fully remove our operators from the dozer seat in what is another significant advancement in autonomous mining.”
The pilot project currently involves a single dozer, but there are plans to retrofit another 13 across Capcoal and Moranbah operations.
The rollout of tele-remote dozers is expected to further reduce worker exposure to potential hazards, particularly those associated with concealed stockpile voids.
Anglo’s broader approach to automation has also included the implementation of personal proximity detection systems in underground mining, designed to enhance safety by reducing the risk of worker–machine interactions. These technologies form part of a wider effort to improve operational safety while maintaining productivity.
The past decade has seen significant developments in remote operations and automation in the mining sector. As these technologies continue to evolve, mining companies will likely need to balance innovation with workforce adaptation, ensuring that operational knowledge is retained and applied alongside emerging systems.
Anglo American is one miner proving the integration can make operations not only safer but more efficient and profitable, as well an empowering workers with new skills that will serve them in mining’s digital age.
The isolated natured of mine sites across Australia, combined with the 24–7 nature of the industry, often makes it difficult for employees on-site to get adequate shuteye.
Fly-in, fly-out (FIFO) workers regularly take on long shifts with irregular schedules, making it difficult to maintain the consistent eight-hour sleep schedule they need.
The remoteness of mines can add to the complexity, with workers usually having to adapt to different environmental conditions that can disrupt sleep, including seemingly simple things like new and varying sounds and temperatures.
Some studies have shown that FIFO workers average between 5.5–7.3 hours of sleep, leading to insufficient rest and affected physical and mental health. This can in turn impair cognitive function, reduce alertness and increase the risk of workplace accidents.
New research from Edith Cowan University (ECU) has explored how FIFO mining shift workers can get a better night’s sleep – and ‘sleep hygiene’ plays a key role.
Sleep hygiene includes habits and sleep environment factors that can positively influence sleep, including a healthy diet, physical exercise and limited screen time.
“From extensive research on sleep in humans we know that sleep is very important for many aspects of our life such as our health, wellbeing, and daytime functioning,” ECU PhD candidate and lead study author Philipp Beranek told Safe to Work
“Mining companies are already doing a lot to reduce fatigue-related incidents, with many companies tackling poor sleep.
“While avoiding shift work seems to be an obvious way to improve the mining shift workers sleep, this is not feasible. Therefore, it is important to investigate avenues to improve the mining shift worker’s sleep without interfering with mining operation.”
FIFO workers often average between 5.5–7.3 hours of sleep a night.
workers could get their 40 winks – but that doesn’t just mean showering at night instead of in the morning.
“Sleep hygiene involves behavioural aspects like avoiding caffeine close to bedtime and sleep environment factors like keeping a cool bedroom that can help us get better sleep,” he said.
“Numerous studies, conducted in other populations, have shown that better sleep hygiene [engaging in sleep-supporting behaviours and have a sleep-conducive bedroom] is linked to better sleep.”
Image: Gorodenkoff/shutterstock.com
The study unequivocally found that mining shift workers that have a better sleep hygiene experience better sleep health, indicating that those who are looking to rest better should implement such strategies.
“Particular attention should be given to having a regular sleep schedule, a sleep-conducive sleep environment, good mental health, and limited time in bed extensions,” Beranek said.
According to Beranek, the study was the first to investigate the
context of FIFO workers.
“Shift work causing sleep difficulties has been observed in many industries, such as the healthcare industry,” he said.
“However, sleep research in Australia’s mining industry is very limited, unfortunately.
“Therefore, in our recently published research article we investigated whether this previously observed relationship between sleep hygiene and sleep also exists in Australia’s mining industry, potentially indicating that mining shift workers may be able to improve their sleep by improving their sleep hygiene.”
The study also found that better sleep health was found in those who:
• have a more regular sleep schedule experience
• experience a more comfortable bed and bedroom
• think/plan/worry less and are less angry/stressed/nervous when they go to bed.
Another key finding was that those who spend too much time in bed experience worse sleep health.
“Shift workers often experience sleep disruptions because they are unable to allocate a constant and specific time for sleeping, and their body clock is often not adjusted for this,” Beranek said.
“If you are working the night shift, it requires you to go to bed at a time when your brain and body usually are awake and set to function.
“FIFO workers have long shifts, yet they are still required to do all the normal things as well, like having dinner, washing their clothes, doing exercise or even commute from the mine site. It makes it difficult to manage sufficient sleep within that 24-hour period.”
The temperature of the environment in which miners work can also contribute to a poor night’s sleep. In the Pilbara region of Western Australia, nighttime temperatures can reach up to 28°C.
“[Hot weather] can lead to elevated room temperatures, which potentially disrupt the sleep of night shift workers who sleep during daytime,” Beranek said. “To help, set the air-conditioning between 16 and 20°C.”
But it isn’t all up to the individual. There are things mining companies can do on an organisational level that can help their FIFO workforce sleep better.
Beranek also recommends a more comfortable pillow, a consistent bedtime and wake-up time, and practising mindfulness or meditation.
“At the organisational level, mining camp providers can consider evaluating existing accommodations and make improvements where needed, like blocking out light,” Beranek said.
“Further, those evaluations could inform the design of future mining
camps to create a sleep-conducive environment from the beginning.”
Beranek also recommends mining companies provide their workforce with education to help them make informed decisions.
“Education on sleep health can increase an employee’s sleep knowledge and provide practices to improve sleep if needed,” he said. “At an individual level, shift workers can implement a bedtime routine that prepares them for going to sleep.”
Improving sleep hygiene is one of the most effective ways for FIFO workers to manage the inherent challenges of shift work and remote environments.
By making small, consistent changes like maintaining a comfortable sleep environment and establish regular sleep routines, shift workers can make a significant difference in their overall wellbeing.
If employers take it a step further and ensure their employees’ accommodation supports quality rest, FIFO workers will be better prepared for the day ahead. By taking proactive steps, companies and employees can create a culture that prioritises rest and recovery.
With the right habits, quality sleep doesn’t have to feel like a luxury for FIFO workers.
8-9
In the 1990s, Pru Giagtzis was working as a safety professional for one of the world’s biggest miners, but a new opportunity led her to help develop an entirely original system of incident investigation.
When the executive team behind Giagtzis’ employer identified issues with the quality of investigations at the time, it formed a group to review its practices and develop a uniform methodology across the business.
Based on the work of James Reason’s ‘Swiss Cheese Model’ of accident causation, which emphasises active failures and
to implement a new structure of incident investigation.
The early iteration of the system was a major success across the global network of sites operated by the miner, as well as its broader operations, including downstream steelmaking, transport and logistics. It was from this project that the ICAM methodology was born.
ICAM – incident cause analysis method – is a systematic framework used for investigating and analysing incidents in high-risk industries like mining. It is now also used in industries like aviation, healthcare
factors of incidents and develop effective solutions to reduce the likelihood of recurrence.
Key principles of the ICAM system:
• Systems thinking – focuses on understanding the incident within the context of the organisational system, recognising how various factors interact to create risks
• Human factors – recognises that human errors are often symptoms of deeper issues in processes, training, equipment or culture
• Proactive solutions – aims to generate actionable recommendations that address
Giagtzis is now a senior investigator for ICAM Australia, an organisation formed in 2020 with the aim of providing specialist and tailored investigation solutions.
“I have been involved in training ICAM across industry sectors and have led or been part of hundreds of investigations,” Giagtzis told Safe to Work.
“ICAM Australia employs experienced safety professionals and investigators who collectively have 150 years-plus experience in the domestic and international mining sector.
“Our team members were involved in the initial development of the system and have been providing training and investigation services since ICAM was first introduced into the mining sector in the early 2000s.”
ICAM Australia’s key objective is working with industry to increase training delivered to frontline management and operational personnel so the knowledge and principles that come from the methodology are integrated into everyday operational practices.
“We believe this will drive a change from a reactive to proactive use of the ICAM methodology to improve safety outcomes,” Giagtzis said.
Why is this shift so critical?
Giagtzis believes the changing tide of the mining industry will call for a stronger foundation of safety.
“Ongoing skills shortages and a trend towards migrant workforces will require greater safety knowledge and awareness,” she said. “This could introduce a new complexity to training delivery, especially around literacy and language.”
Giagtzis is concerned by findings from ICAM data that found inadequate training to be a key factor in a large portion of mining incidents.
“Contributing factors related to training are one of the key causations we see in almost every ICAM investigation,” she said. “From my experience, improving work health and safety training and competency training is vital to reducing the number of incidents in the mining industry.
“One of the real challenges for miners is that without effective and timely training, a functional safe system of work is unachievable.”
ICAM training is focused on understanding the key principles of the model and ensuring participants have the practical skills to apply those principles in investigations.
“All of our team members are passionate about developing capacity in industry to use the ICAM tool to enhance risk management and further safety improvement,” Giagtzis said.
“We are passionate about ensuring that we give participants the tools, knowledge and skills to not only effectively investigate but also apply the principles outside of the investigation process.”
A key component of the ICAM methodology includes an inherent critical-risk-management way of thinking. This is a fundamental principle instilled in all who undertake training in the system.
“From my experience delivering ICAM training, the methodology changes the thinking of participants,” Giagtzis said. “Because we predominantly train leaders and safety professionals, post-training we see a shift in thinking towards proactive risk management prior to incidents occurring despite the methodology being aimed at reactive investigations.
“Over the years, I don’t know how many times I’ve heard participants tell me that post-ICAMtraining the way that they practised safety changed from a reactive to proactive risk thinking.”
According to Giagtzis, the benefits that recipients of ICAM training have reported include reduced workers’ compensation costs, improved workplace morale, stronger corporate governance, and improved safety and operational efficiency.
“I feel my greatest achievement comes from the impact I’ve seen within operations after we have completed ICAM investigations, and we see meaningful change in the risk-management processes of the mining organisation,” she said.
“More importantly, we see a change in the thinking of the people involved in the investigation process and changes in culture around peoplefocused investigation outcomes such as blame towards a riskbased causation thinking, which promotes effective and long-term preventive controls.
“I’m proud that I was, and continue to be, part of something that is now used worldwide as a proven investigation technique.”
IS ABOUT MUCH MORE THAN CHOOSING A COMFORTABLE PAIR OF BOOTS.
From offshore gas exploration to open pits to deep underground, the Australian resources industry has a diverse range of job roles that require many different types of fit-for-purpose safety boots.
Environmental conditions also vary significantly – wet and muddy to dusty and rocky and everything in between – and all sites have distinct challenges that demand specialised safety gear.
Taking a generic approach could ultimately leave workers at
For an industry that prioritises safety and technology in its operations, mining workers can often end up wearing uncomfortable or inappropriate footwear.
For example, faced with wet and boggy conditions, underground miners may resort to wearing gumboots that are far from ideal when it comes to fit, cushioning and shock absorption.
Blundstone business development specialist Steve Broadbent has seen his share of tough site conditions. He
not only comfortable for long days at work but provided the right protection
water and sludge, on very uneven surfaces, so he needed a waterproof, supportive safety boot to handle those conditions,” Broadbent told Safe to Work
“His Blundstone 980 specialist underground mining boots were doing an excellent job in this environment to keep the miner’s feet dry and his ankles supported.”
It’s not just workers on the front lines that need a tailored solution – any engineer, drill operator, truck driver or process operator needs safety footwear that suits their individual requirements. However, this vast range of work roles coupled with different environmental hazards in different areas can be a challenge for work, health and safety (WHS) officers and procurement teams when outfitting their staff.
The solution is to find a comprehensive range of boots with tailored safety features that are made from tough, battle-tested materials to protect in the most extreme environments.
Enter Blundstone mining boots.
Broadbent said Blundstone has long prioritised manufacturing and technological leadership, delivering specific features such as waterproofing, chemical resistance, heat resistance and slip resistance to meet the demands of various roles.
“The mining industry is evolving rapidly and Blundstone is prioritising innovation to ensure every worker is protected,” Broadbent said.
“Designed with advanced technology and tested for the harshest conditions, our mining safety footwear provides comfortable, supportive and lightweight protection for workers, and long-term value for procurement teams.
“This reduces overall personal protective equipment [PPE] costs while keeping staff fully protected with the best safety footwear on the market.”
This long-term durability and comfort can also heavily reduce worker fatigue and musculoskeletal foot pain, a positive for the worker and the company’s bottom line.
A comfortable, fit-for-purpose pair of boots can contribute to a reduction in lost work hours caused by lower limb pain, slips, trips and falls.
ROTOFLEX MAX #9099
The all-purpose powerhouse of Blundstone’s RotoFlex range, the MAX #9099 aims to combine style with top-tier safety.
This boot features ultra waterrepellent AquaShield leather and a fully waterproof Sympatex membrane (bootie) designed to conquer any terrain and meet every challenge.
A GripTek MAX Sole, made from advanced Vibram Rubber TC4+, provides traction, protection and support and provides heat resistance to 300°C.
It is also fuel oil resistant and offers strong abrasion, cut and slip resistance to keep teams safe on-site.
ROTOFLEX #9161
“The RotoFlex #9161 is packed from top to toe with premium comfort and safety,” Broadbent said.
“It is designed to provide protection in environments where there is potential for hazardous liquid chemical exposure.”
Offering abrasion, cut and slip resistance, the GRIPTEK XHD biomechanically engineered rubber (PUR) outsole is designed for optimum grip and stability. It is also heat resistant to 300°C and is fuel oil resistant.
The #9161 is also tested for limited contact with common chemicals including methanol (A), dichloromethane (D), sodium hydroxide at 40 per cent concentration (K) and isopropanol (Q).
Both the #9099 and #9161 offer a FORTASHIELD broad-fitting, cut-resistant steel toe cap, an AIRCELL zoned airflow footbed, and a SOFTCELL comfort system to increase stability, balance, comfort and manoeuvrability.
With a well-earned legacy of crafting quality, safe footwear for more than 150 years, Blundstone is able to offer a wide range of high-quality Australian-designed safety boots to cover the diverse range of jobs right across the resources sector, including underground mining boots, waterproof boots, chemical-resistant boots, smelter boots, and many more.
For the first time in its storied history, Asia-Pacific’s International Mining Exhibition (AIMEX) is set to take place in Adelaide.
This historic relocation marks a new chapter for one of the mining industry’s most influential events, bringing together key players, groundbreaking innovations, and industry-defining discussions.
With industry giants already securing their place, AIMEX 2025 is shaping up to be the most impactful edition yet.
Among the companies confirmed for the event are XCMG/BROOKS, ifm, Motion, Flexco, TriCab, Milwaukee Tool, Netzsch Australia, Vayeron and MaxMine.
As the event expands on a successful 2024 edition, exhibitors
and attendees alike are recognising the unparalleled opportunities AIMEX offers for networking, collaboration and showcasing cutting-edge mining technologies and innovations.
“The excitement around AIMEX 2025 has been incredible,” Prime Creative Media mining events
an event that not only highlights innovation but also strengthens connections across the sector.”
Beyond industry advancements, AIMEX 2025 is dedicated to supporting those who keep the mining community thriving.
The event has partnered with the Royal Flying Doctor Service (RFDS),
an organisation that delivers vital healthcare to remote and rural areas.
“The RFDS is a lifeline for many communities, including those that support Australia’s mining industry,” Todesco said.
“It’s an honour for AIMEX to contribute to its mission and help ensure continued access to essential health services.”
Adding to the excitement, AIMEX 2025 will host the prestigious Australian Mining Prospect Awards, celebrating excellence across the industry.
Held on the second night of the event, this black-tie gala recognises achievements in categories such as Indigenous and Community Engagement, Mine Project Success of the Year, and Outstanding Mine Performance.
“The Prospect Awards are a key moment to celebrate the individuals and organisations shaping the future
Networking, collaboration and showcasing cutting-edge mining technologies are at the heart of AIMEX.
of mining,” Todesco said. “This year, we’re raising the bar with an expanded program that will highlight the very best in the industry.”
AIMEX 2025 is set to be one of the most significant mining events of the year, featuring cutting-edge exhibits,
expert presentations and unrivalled networking opportunities.
With a line-up of industry-advancing thought leadership and innovations, don’t miss out on a chance to be part of mining’s next great chapter.
AIMEX 2025 will be held at Adelaide Showground from 23–25 September.
Maintenance and repair are constants on a mine site, often with multiple projects underway at once, and can be carried out while full-scale operations continue.
Mine operators do everything in their power to keep workers safe during these works, but having so many moving parts and people in play can pose a variety of challenges.
While maintenance is being carried out in a certain area, it’s often essential that energy sources be managed effectively so potential issues like shocks, arc flashes, or the release of liquids or steam can be avoided.
If another worker who is unaware the works are being carried out comes along and re-engages those energy sources, it can lead to potentially severe consequences for those involved.
To protect workers performing maintenance, sites can implement a ‘lockout–tagout’ system where lockout equipment, such as a safety padlock, secures an energy isolating device while a tagout, such as a tag, warns employees not to use the equipment. This aims to prevent unintended reenergising and start-up of equipment.
Mayo Hardware has been the exclusive wholesaler of Master Lock products in Australia for nearly 100
years. Master Lock’s safety locks and devices are some of the tools with which mine sites across the country have been able to prevent damage to machinery and injuries to people.
“The SafeSite program by Mayo Hardware is a free-of-charge service offer that works with end users to ensure they receive the best advice and solution tailored to their needs,” Mayo Hardware product manager Jason Vandenberg told Safe to Work.
“The goal is simply to make it easier for people to do the right thing, ensuring protection is achieved efficiently and willingly, rather than it being a burden that people would rather do without.”
Vandenberg emphasised that the SafeSite program has been a “game-changer” for sites looking to improve their lockout–tagout isolation safety practices.
“Many companies are happy to just sell products, but our customers demand more than that; they want a partnership where they can have their say so their site’s specific needs are heard and met,” he said.
“The SafeSite program acknowledges that safety is more than just product – it includes training, culture, behaviour and procedures. Mayo Hardware has representatives in each Australian state who are never far away from being able to conduct site visits and talk through best practice.”
The SafeSite program has been successful in providing tools and products to protect miners during their operations, but it’s just one facet of Mayo’s approach to protecting miners on-site.
As the Australian wholesaler of ATG Gloves, Mayo is also helping protect workers while they perform heavyduty, hands-on work.
“Like Master Lock, ATG Gloves are considered global market leaders in the coated seamless knitted glove market and can be found on most mine sites in Australia,” Vandenberg said.
By taking a holistic approach to safety through the SafeSite program, Mayo and ATG have diligently worked to ensure users understand what makes the gloves different, as well as making it easier for workers to quickly select the right gloves for the job.
“Using the wrong gloves increases the risk of injury,” Vandenberg said. “Gloves that are incorrectly sized are uncomfortable and prohibit performance. As soon as a glove is removed, your hand is no longer protected.
“Comfort is the key to compliance. Many sites have trialled other gloves, but due to worker discord come back to ATG – their comfort is unsurpassed with the inclusion of ADAPT technology keeping hands up to 65 per cent cooler.
“They are also extremely durable, meaning they last longer than regular gloves making them economical over the course of their life.”
Whether implementing a lockout–tagout system or introducing ATG gloves, Mayo regularly checks in on its customers to make sure everything is going smoothly.
“We review how everything is going in six to 12 months to ensure changes made have worked or, if not, implement additions and improvements” Vandenberg said.
“We have a procedure-writing partner that can do a free desktop audit on existing lockout–tagout procedures, and we can quickly put together glove matrices and education posters encouraging worker education and compliance.”
Master Lock is further looking to make things easier for mine sites with its Bluetooth-connected padlocks and lock boxes that can be controlled by a mobile phone app.
“They’re a great way to streamline and manage access control, especially in areas where many keys are used, remote locations, or where contractor access is constant,” Vandenberg said.
“No more lost keys or forgotten codes; permanent or temporary access can be granted to those who need it from anywhere. Detailed access history is kept so you can easily see who accessed the device and when.
“Master Lock also has a connected lockout program – cLOTO – enabling users to digitally transform their lockout programs by bringing safety, accountability and innovation together on a desktop or mobile device.”
This versatility allows users to streamline processes, assign and track procedures and make real-time decisions when they matter most.
“We will continue working with mine sites to make it easier to keep people safe,” Vandenberg said. “Having a positive impact on a site’s health and safety culture is paramount.”
ViPR’s advanced AI algorithm searches and cross-references critical safety information based on the user’s job role.
A NEW AI-DRIVEN SAFETY APP IS HELPING RISK AWARENESS BECOME SECOND NATURE FOR AUSTRALIAN MINERS.
ViPR Australia was founded with a clear mission: to stop workplace accidents by proactively enhancing worker awareness of job-related risks.
The company’s journey began when its founder Michael Jones witnessed first-hand the impact of workplace incidents – not just on individuals, but on families, teams and entire businesses.
This experience sparked a critical question: why aren’t we doing more to stop this before it happens?
Determined to find a smarter, more effective approach to workplace safety, Jones set out to create ViPR – a platform that uses artificial intelligence (AI) to make risk awareness second nature.
By equipping workers with real-time, job-specific safety information, ViPR can help them make informed decisions that prevent accidents before they occur.
“Our goal is to create a culture where safety is proactive, intuitive and truly impactful,” Jones told Safe to Work.
ViPR is an advanced AI-driven safety technology designed to be a worker’s real-time safety companion on-site. It is designed to ensure hazard identification and critical safety information from regulators and manufacturers are delivered instantly to workers in the
field, where timely information is most crucial.
“What sets ViPR apart is its intelligent adaptability,” Jones said.
“Instead of generic safety updates, its advanced AI algorithm searches and cross-references critical safety information based on the user’s job role, location, type of mining operation, and specific tasks being performed.
“This ensures that workers receive highly relevant, site-specific information about potential risks before they escalate, factoring in conditions like environmental hazards and machinery-specific dangers.”
ViPR prioritises simplicity and usability. The interface is designed to be intuitive, so workers can access vital safety information quickly and efficiently, without navigating complex systems or unnecessary details.
By making safety information smarter, faster and more targeted, ViPR aims to empower workers to make informed decisions in real-time.
For Jones, ViPR isn’t intended to replace any systems currently
in use in the workplace. Rather, it’s designed to enhance and work as a kind of personal assistant, providing information that may not have previously been encountered.
“ViPR is designed for people, not just protocols,” Jones said.
“Unlike traditional safety software, it doesn’t require users to have prior knowledge of mining, safety or risk management, nor does it demand extensive data entry before becoming effective.
“ViPR works straight out of the box, analysing risks and delivering actionable insights immediately.
“Whether you’re a seasoned manager or a worker new to the field, ViPR provides instant, relevant safety information, making it more than just a tool – it’s a true safety partner and pocket assistant.”
Jones has a vision to see ViPR set a new standard for safety across all industries. The goal is to keep the platform on the cutting edge by continuing to advance its AI capabilities and taking on feedback from users.
“ViPR’s growth will be shaped by real-world feedback,” Jones said. “As more industries adopt the platform, we’re focusing on refining the tool to make predictions even more personal and adapting the system for diverse work environments, not just mining.
“Our goal is to ensure ViPR stays ahead of emerging risks and remains a practical, game-changing solution for industries across the country ensuring the information remains relevant and easy to access at all times.”
Jones believes workplace safety isn’t just about compliance; it’s about protecting people and creating a culture where everyone feels valued and supported.
“ViPR isn’t just a tool; it’s a mindset shift,” he said. “We’re proud to partner with companies that share our vision for smarter, safer workplaces, and we’re excited to see how ViPR can make a real difference on the ground.
“At its core, ViPR is about keeping people safe so they can go home at the end of the day.
“That’s a mission worth standing behind.”
“Our goal is to create a culture where safety is proactive, intuitive and truly impactful.”
Working at heights presents unique challenges, particularly in the case of safety management. Regular equipment inspection is vital to ensuring safe and compliant work environments.
Without proper oversight of equipment such as harnesses, ropes, carabiners and anchor points, workers
inspection protocols to uphold safety standards. WAHA secretary and strategic programs manager Deborah Chick shared the critical aspects of equipment inspection with Safe to Work
In any work environment that involves heights, faulty or worn-out equipment
heights is safe, reliable and compliant with the relevant standards.
Regular equipment checks not only protect workers but also help organisations avoid legal repercussions from non-compliance with safety regulations.
Some key reasons why equipment inspections are essential:
• Preventing equipment failure –regular checks identify wear and tear before it becomes a hazard. suring compliance – inspections are often required to comply with national and international
inimising liability – ensuring all equipment is up to date reduces legal and financial risks.
orker confidence – employees feel safer knowing the equipment they are using is regularly inspected
When working at heights, there are several key pieces of equipment that must undergo regular inspections.
Each type has specific wear indicators and usage thresholds, making it vital to be familiar with the
Personal protective equipment (PPE) arnesses – inspections should look for frayed webbing, damage to buckles and signs of excessive wear; ensure labels with weight limits and manufacturing dates
anyards and shock absorbers –check for cuts, burns or chemical exposure, and test shock absorbers for signs of activation
Create a checklist
Use a standardised checklist to ensure all components are reviewed during inspections. WAHA provides templates for its members that can be customised for specific equipment types.
Document the inspection
Documentation is critical to tracking the lifecycle and maintenance history of each piece of equipment. Record the inspection date, the condition of the equipment, any issues found, and the actions taken.
Involve a competent person
A competent person should carry out inspections, which means a person who has, through a combination of training, qualification and experience, acquired knowledge and skills enabling that person to correctly perform a specified task.
Take equipment out of service if necessary
If any issues are identified that compromise safety, the equipment must be removed from service immediately and either repaired or replaced.
• Helmets – should be inspected for cracks, internal padding wear and damage to chin straps
Anchors and connectors
• Anchor points – ensure fixed or portable anchor points used for rope access or fall arrest systems are securely installed, undamaged and tested for load capacity
• Carabiners and hooks – examine for wear on gate mechanisms, corrosion and deformation, ensuring they lock and unlock smoothly
Ropes and cables
• Lifelines and safety ropes – inspect for abrasions, cuts and signs of UV degradation; ropes should be checked for contamination from chemicals or moisture, which could compromise strength.
• Fall arrest blocks – ensure the casing is intact and the retraction mechanism is functioning properly, and check for internal damage, particularly after a fall arrest
According to guidelines provided by WAHA and other safety organisations, inspections must occur at regular intervals that vary based on usage frequency and environmental conditions.
Workers should perform an inspection of each item of personal and common use equipment before and after each use per AS/NZS 1891.4 section 9.2. This simple step can detect obvious issues, such as broken or missing components.
For high-use or critical equipment, formal inspections should be carried
out by a competent person at least every six to 12 months. These inspections are more thorough, often involving disassembly and testing.
Any equipment involved in a fall or other significant incident must be inspected before being put back into service. In some cases, the equipment may need to be retired if its integrity has been compromised.
Regular equipment inspections are not just about ticking off a regulatory requirement – they are about ensuring the safety and wellbeing of every worker operating at heights.
By adopting a proactive approach to equipment inspection and maintenance, mines will not only comply with WAHA and other industry regulations but also foster a culture of safety that can prevent lifethreatening accidents.
Designed to foster business connections, share industry insights and provide a worldclass networking experience, the 2025 PNG Industrial and Mining Resources Exhibition and Conference (PNG Expo) is set to build on the success of previous years.
Held at the Stanley Hotel, a premier business venue in the heart of Port Moresby, PNG Expo 2025 will ensure a seamless experience for delegates by keeping all aspects of the event – exhibitions, conferences, and networking sessions – within one convenient location.
With exhibitors such as Metso, Blackwoods, Sandvik, Dreager, Lincom and Putzmeister already having secured their spots, this year’s PNG Expo is expected to be a mustattend event of the year for those in the sector.
The exhibition will feature a carefully curated floorplan designed to facilitate high-value business interactions between key mining industry buyers and suppliers. Running alongside the
Beyond the exhibition and speaker sessions, PNG Expo 2025 offers a premium networking experience designed to help delegates maximise their time in Port Moresby.
The event will officially kick off with an exclusive welcome drinks reception, set against the stunning backdrop of the local skyline.
Prime Creative Media general manager of events Siobhan Rocks reflected on the success of the 2024 event, which featured a similar networking opportunity.
The networking opportunities continue as the event progresses. Delegates can meet and collaborate throughout the exhibition, at conference sessions and during casual encounters around the Stanley Hotel’s business facilities. The gala dinner, which marks the
conclusion of the PNG Expo, is set to be an unforgettable evening of celebration, networking and entertainment. This exclusive event brings together industry leaders, decision-makers and business representatives to celebrate the everevolving mining industry.
Rocks said the 2024 gala dinner played a crucial role in enhancing the overall PNG Expo experience.
“It was a fantastic way to round out two days of business and networking,” she said. “Attendees got to sit down with people they had met at the event, strengthen their connections over a five-star meal, and enjoy speeches and entertainment that truly celebrated the industry.”
This year’s gala dinner will be even bigger and better, ensuring an unparalleled experience for all who attend.
With major industry names already securing their participation, now is the time to lock in a spot at this year’s PNG Expo. Whether looking to exhibit, attend or sponsor, this event promises to be a game-changer for those in the mining and resources industries.
The 2025 PNG Expo will be held at the Stanley Hotel in Port Moresby from July 2–3.
Mining has long been a cornerstone of Australia’s economy, supporting jobs, industries and communities across the country. The sector plays a critical role in providing essential resources to global markets.
As the industry evolves, so too does its approach to workforce wellbeing, with an increasing focus on ensuring employees have the support they need to maintain a healthy and balanced work life.
In recent years, mental health and wellbeing have become key considerations for mining companies, industry bodies and governments.
The nature of mining – often involving long shifts, remote locations, and fly-in, fly-out (FIFO) work arrangements – can present unique lifestyle challenges. Many workers spend extended periods away from family, friends and other support networks, and adjusting to the demands of the job can require resilience and adaptability.
While the industry has long recognised the importance of physical safety, there is now a growing emphasis on fostering a positive work environment that supports mental and physical wellbeing.
A number of initiatives have been introduced to support a healthier and safer working environments for mining employees.
One such initiative has come from the Western Australian Government, which, through the Minerals Research Institute of Western Australia (MRIWA), has introduced a raft of PhD scholarships as part of its Mental Awareness, Respect and Safety (MARS) Program.
These scholarships aim to encourage innovative research into workplace wellbeing, psychological safety and other factors that contribute to a positive and productive mining environment.
The MARS Program was established in December 2021 and is an inter-agency collaboration involving the Department of Energy,
Mines, Industry Regulation and Safety (DEMIRS), the Mental Health Commission, the Equal Opportunity Commission, and the Department of Communities. Its primary aim is to address mental health, workplace culture and safety issues within the WA mining industry.
The scholarships awarded through the program seek to generate new research that will provide insights into workplace experiences, safety practices and mental wellbeing in the mining and resources industry. Activities include:
• exploring how psychological capital can be leveraged to improve psychological safety in the Western Australian mining industry context by Ronald James at Edith Cowan University (ECU)
• assessing a range of occupational hygiene dust sampling devices to determine their suitability for riskbased exposure measurements in Australian mining operations by Benjamin Walsh at ECU xamining the significant impacts of psychosocial risk factors on workforce sustainability and workers’ behaviours in the mining industry by Nousheen Fatima at ECU esearch into understanding how leaders construct and deliver effective safety stories and capture the impact on safety outcomes by Patrick Benetti at the University of Western Australia.
The recipients of these scholarships will play a crucial role in WA’s research ecosystem, working alongside industry professionals and academic experts to develop strategies that contribute to a positive work environment in mining. Their research is expected to provide evidence-based insights that can inform industry practices and workplace policies, helping to ensure As the mining industry evolves, there is growing understanding of the importance of a strong mental health culture on-site.
The scholarships aim to encourage innovative research into mining mental health.
that mining operations continue to evolve in a way that prioritises worker wellbeing.
The program has also funded the establishment of the MARS Centre at ECU. This multidisciplinary centre brings together expertise from ECU’s School of Business and Law and the School of Medical and Health Sciences with the aim of improving safety and wellbeing in the mining sector.
WA Mines and Petroleum Minister David Michael said the scholarships are key to positioning the state as a global leader in mental health in the mining sector.
“This research will help drive innovative solutions and support sustainable workforce practices,” Michael said. “The WA Government is proud to invest in the next generation of researchers whose work will
directly contribute to improving safety outcomes and fostering healthier, more inclusive workplace cultures across the mining industry.
“By supporting minerals research through initiatives like the MARS Program, we are reinforcing the importance of workplace health and safety in Western Australia’s mining sector.”
WA Training and Workforce Development Minister Simone McGurk believes the scholarships are an example of the state’s commitment to continuous improvement.
“The mining industry has come a long way in recent years when it comes to addressing issues around the health and wellbeing of workers, but there is more to be done,” McGurk said.
“These scholarships will be important to advance mental health
initiatives and to shape strategies that put the wellbeing of workers first.”
As the industry continues to grow and adapt, initiatives like the MARS Program PhD scholarships provide an opportunity to explore new ways of fostering a supportive and inclusive mining culture.
With a focus on practical, research-driven solutions, these scholarships represent another step in ensuring that mining remains a strong, safe and sustainable industry for the future.
Through collaborative efforts between researchers, industry leaders and policymakers, the sector is working towards a more comprehensive approach to workplace health and safety, balancing operational demands with the wellbeing of its workforce.
The WHS Show will bring together industry leaders and safety professionals to address key workplace safety challenges.
THE MELBOURNE AND SYDNEY WHS SHOWS WILL RETURN IN 2025, OFFERING CRUCIAL INSIGHTS INTO THE LATEST WORK AND GENERAL SAFETY INNOVATIONS.
This year’s Workplace Health and Safety Show (WHS Show), to be held in Melbourne on May 21–22 and in Sydney on October 22–23, will bring together industry leaders and safety professionals to address key workplace safety challenges.
Mine safety is expected to be a significant focus at both shows, with exhibitors and presentations dedicated to addressing hazards unique to the sector.
Given the high-risk nature of mining, innovations in personal protective equipment (PPE), hazard monitoring and safety technology will be among the highlights.
All attendees can expect to be presented with demonstrations of an array of cutting-edge solutions, including in the areas of advanced respiratory protection and enhanced visibility workwear, two of the most critical safety measures for underground and openpit operations.
“These new safety technologies and products are set to make a massive difference in the industry, with this year’s WHS Show demonstrating more than ever before,” WHS Show portfolio director Stephen Blackie said.
“It’s more than just a show about workplace safety; it’s a reminder that employers have a legal responsibility and a moral obligation to their workforces to create an environment where they can arrive to work, do a job well, and leave safe at night.
“With over 180 suppliers primed to explain and demonstrate the latest tech available in the safety industry, we have this year’s safety innovations covered.”
The WHS Show will also feature seminars from safety experts discussing best practices for the mining industry. At the Melbourne event alone, 75 industry experts will deliver over 40 hours of combined educational content.
Presentations on mental health initiatives will also be a must-see, with the sector increasing its focus
on psychological safety and workplace culture. Key insights to improve mental health support in high-pressure mining environments will be explored as part of broader discussions on improving employee retention and overall safety performance.
Technological advancements in emergency response and evacuation planning will be another focal point, with exhibitors providing insights on simulation tools and communication systems that enable faster, more effective responses to critical incidents in mining environments.
With safety regulations continuously evolving, the WHS Show offers mining industry professionals the opportunity to stay on top of compliance requirements and adopt best practices to protect their workforce.
For those in mining, attending the shows in Melbourne or Sydney presents unique opportunities to explore new safety innovations and gain actionable insights to boost workplace safety.
Mould can cling to particles in the air, making dust suppression efforts key.
THE MINING GUIDELINES ARE CLEAR WHEN IT COMES TO EXPOSURE STANDARDS FOR RESPIRABLE HAZARDS SUCH AS DUST OR SILICA, BUT LIMITS FOR MOULD ARE A BIT MORE COMPLICATED.
Mould is common in everyday life, found in leftovers at the back of the fridge, in the grout of a share-house shower, and even floating in the air we breathe. Just as mould can easily be found around the house, it can also be seen (or unseen) at mine sites across Australia.
Anywhere there is moisture, there is the potential for mould. Many types of mould are harmless, but there are also toxic species that make vigilance from mining companies especially important.
The Australian Institute for Occupational Hygienists (AIOH) is working to draw more attention to the challenges of mould on mine sites and what companies can do to limit
exposure to workers. AIOH certified occupational hygienist Ash BossHandley said that because there are no official exposure limits for mould, it’s up to experts to determine the level of risk.
“We really rely on our professional judgement to determine acceptable levels based on a range of factors,” Boss-Handley told Safe to Work.
“Mould is everywhere, spores are invisible in the air, in soil and on surfaces, but if you can see mould growing indoors, that’s a pretty good indication there’s a problem.”
According to Boss-Handley, moisture and ventilation represent perhaps the two biggest factors that will affect the prevalence of mould in mines.
Mould growth in fly-in, fly-out (FIFO) camps can be common if there are leaks, ineffective ventilation or standing water around amenities.
Dust can also be a significant culprit, as mould binds to particles in the air which are then inhaled, making ventilation and dust suppression efforts crucial.
Exposure to mould can cause lung irritation, wheezing, coughing and shortness of breath, with a small number of mould species causing more serious issues.
A common type of mould is Aspergillus, a genus that covers about 200 different species. A small number of those species cause a disease called Aspergillosis, which occurs
when the mould enters the lungs and causes significant health issues like a reduction in lung function.
“It’s cases like that where people can get quite frightened, because they might assume any spore of mould is going to cause these issues,” BossHandley said.
“But the reality is there’s a huge proportion of mould that is more or less benign and just kind of exist naturally in the air or in soil.
“Our objective is always to just eliminate excess mould as much as possible. If we know there is an issue where visible mould growth is identified, it’s important to get rid of that mould irrespective of whether we think it is a toxic variety.”
How can mining companies keep mould to a minimum?
The risk is well known, meaning most Australian miners have controls in place to reduce the likelihood of excessive growth. Workers will generally already be wearing personal protective equipment (PPE) like respirators that will serve to protect them from stray spores, and most mines will monitor their ventilation systems diligently to ensure fresh air is provided to work areas.
Boss-Handley recommends simply wiping away visible mould from non-porous materials.
When it comes to removing mould, Boss-Handley emphasised it doesn’t
“If you see mould, remove it as soon as you can,” she said. “If you notice mould on something nonporous, simply wiping it away with a damp cloth may suffice, there’s no need to use harsh chemicals, which may compound respiratory issues.
“If there is visible mould on a porous surface such as clothing or cardboard, it will have already taken root in the pores of the material, meaning the best course of action is
If there is concern of excessive mould growth in an area, BossHandley recommends calling in a professional.
“As occupational hygienists, we can use our experience, expertise and professional equipment to attend a site and assess the affected area,” she said.
“That way, we are able to determine the larger systems that might be at play in allowing mould to grow and give recommendations on how to prevent future growth.”
On a mine site, like in all environments, there are countless mould spores present completely invisible to the naked eye, most of which will not lead to mould growth or cause illness.
If mine sites uphold the controls they have in place to tackle mould and keep a watchful eye, BossHandley said there should be little cause for alarm.
“Reducing moisture sources and maintaining airflow are the keyways mould growth can be kept to a minimum,” she said.
“Ensuring miners are safe from the respiratory effects can be straightforward as long as workers and mining companies collaborate to remove mould as soon as possible.”
All workers were safely evacuated from the mine with no injuries reported.
AN INVESTIGATION IS UNDERWAY INTO THE CAUSE OF AN UNDERGROUND MINE FIRE AT PERILYA’S BROKEN HILL MINE IN JANUARY.
The New South Wales Resources Regulator has launched a causal investigation into the factors that led to an underground mine fire at Perilya’s historic Broken Hill zinc-leadsilver mine in January.
The fire originally started on Sunday January 12 and was extinguished by the early hours of January 13 but restarted a short time later. It was extinguished for good later that week. All workers were safely evacuated from the mine with no injuries reported.
The incident took place at level 23 underground at the site’s southern operations, which is about 980m below the surface.
Workers were using chemical and mechanical ground support to remediate an area in the haulage shaft at the time, due to a wedge failure of rock intersecting the haulage shaft and the level 23 platform.
The chemical ground stabiliser is a two-part chemical classified as a polymeric or polyurethane chemical. When both reagents (typically an isocyanate and a polyol) are mixed, self-heating occurs.
Heating is usually managed through careful application in correct mixing ratios of the chemicals, or by using chemicals that do not significantly self-heat.
During the stabilisation process, workers reported fumes and vapour. All workers who were underground at the time retreated from work areas to fresh-air bases and awaited rescue or clearance until the fumes subsided. But the fumes and vapour failed to subside, and in that time the area ignited.
Most workers were able to safely exit the mine unassisted; however, five workers stayed in a fresh-air base for several hours until it was deemed safe by the mine’s emergency rescue team for them to safely retreat.
A preliminary investigation of the incident did not identify any material breaches of the Work Health and Safety Act 2011, and the Regulator has no intention of conducting any further investigation into any potential non-compliance issues or taking any prosecutorial enforcement action.
A causal investigation team will comprise representatives from the Regulator, Perilya and other stakeholders who may be able to provide expert insight and advice.
Together, it is hoped the team will be able to fully understand of the causes of the incident and publish corresponding lessons to the mining industry as a whole.
While the elements at play that led up to the fire’s ignition are clear, determining exactly how the fire broke out will be the first step towards preventing similar incidents occurring at other sites in the future.
SEPTEMBER 2025 23-25
As Australia’s longest running mining show, Asia-Pacific’s International Mining Exhibition (AIMEX) has a long, established history of showcasing and supporting the latest trends and developments in the industry.
AIMEX is relocating and will call South Australia home for the next 10 years, following market feedback and strong support from the local government and key mining players.
The move marks an exciting new chapter for the event and the region’s resource sector, with the state leading the way in future-focused mining.
AIMEX offers unparalleled opportunities to connect with Australia’s largest community of mining suppliers and professionals in an environment that stimulates innovation and collaboration.
SANDVIK HAS INTRODUCED A NEW PARENTAL LEAVE POLICY IN AN EFFORT TO SUPPORT EVERY PARENT IN THE COMPANY, NO MATTER THEIR GENDER.
Sandvik Group is working to turn a traditional gender norm on its head.
Under a new directive, every new parent who has completed their first 12 months as a Sandvik employee will be guaranteed 14 weeks of paid leave.
It’s a move set to transform the way parental leave is managed and is a key element in Sandvik’s commitment to promote diversity, equity and inclusion (DEI), as well as employee wellbeing.
“Sandvik’s gender-neutral parental leave initiative stems from our commitment to fostering an inclusive and equitable workplace,” Sandvik Group executive vicepresident and head of HR Björn Axelsson told Safe to Work
“Recognising the need for a standardised, family-friendly approach, we introduced a global parental leave benefit to provide all employees – regardless of gender or parental status – equal access to paid leave when welcoming a child.”
The program has already been rolled out in more than 20 countries, including Canada, Croatia, Poland and Latvia. Full implementation is expected by June 2025.
“Early feedback has been overwhelmingly positive,” Axelsson said. “Employees appreciate the equitable approach, which removes traditional barriers associated with parental leave.
“By ensuring that all eligible employees – whether biological parents, adoptive parents, or those using surrogacy – have access to 14 weeks [98 calendar days] of paid leave at 90 per cent of their base salary, we expect to see improvements in employee wellbeing, retention and overall job satisfaction.
“Additionally, by encouraging more fathers and non-birthing parents to take leave, we anticipate a positive cultural shift in gender roles at home and in the workplace.”
With centres in 170 countries, Sandvik employs a total of 41,000 people worldwide. While all are now eligible for the parental leave, and even though Sandvik encourages its employees to make use of this opportunity, the new benefit is completely voluntary, with the company leaving it up to each family to decide what is best for them.
“The mining industry has traditionally been male-dominated and gender equality remains a challenge,”
Axelsson said. “By taking a bold step toward inclusivity with our genderneutral parental leave policy, we hope to set an example for the industry.
“The initiative from Sandvik demonstrates that prioritising employee wellbeing and gender equity is not just the right thing to do – it also strengthens company culture, improves retention, and enhances overall business performance.
“We anticipate that other industry leaders will see the benefits of such policies and consider similar measures to support their employees, ultimately driving meaningful change across the sector.”
Beyond its parental leave initiative, Sandvik actively promotes DEI through various programs, including leadership development programs aimed at increasing gender diversity in management roles, mentorship and sponsorship initiatives to support underrepresented employees.
“At Sandvik, we believe that fostering an inclusive work culture requires more than just policies – it requires a commitment to change,” Axelsson said.
“Our gender-neutral parental leave initiative is a reflection of this commitment, and we encourage other companies to take similar steps. By prioritising equity and supporting employees through all stages of life, we create a workplace where people feel valued, engaged, and motivated to perform at their best.
“This initiative is just one step in our ongoing journey toward greater inclusivity, and we look forward to seeing its positive impact across Sandvik and beyond.”
Sandvik president and chief executive officer Stefan Widing said it was his own experience of being able to spend time at home with his sons that drove his views on inclusive parental leave.
“Offering all employees the same opportunity is something I’m personally committed to,” Widing said. “I believe that work–life balance is key to both personal wellbeing and professional success.
“I’m happy we can now offer this benefit to all employees, and I consider it especially important that men take this opportunity.”
Sandvik Manufacturing Solutions head of HR Nidhi Gokhale said the company hopes the new benefit will allow its employees to focus on their growing families.
“We believe in and we support our people, so they can bring their best to both work and home,” Gokhale said.
“However, in many places, especially for fathers, parental leave is limited or non-existent. By launching this global benefit, Sandvik takes one big step forward in our commitment to inclusion
and supporting our employees’ health and wellbeing. We’re not the first company to introduce this, but we’re among the few offering such comprehensive support for families.”
Opremier resources events, WA Mining Conference and Exhibition (WA Mining), is set to make its return in 2025, bringing together industry leaders, innovators, and decision-makers at the forefront of industry innovation.
The event remains a must-attend for professionals looking to stay ahead in an industry that is evolving at an unprecedented pace.
Alongside a comprehensive exhibition, the highly anticipated paid conference will once again feature renowned industry experts tackling critical sector-wide challenges and presenting case studies on the latest trends shaping the Australian mining landscape.
Prime Creative Media mining events marketing manager Rebecca Todesco expressed excitement about building on the achievements of the previous event.
breaking attendance with over 3000 visitors, 48 per cent of whom held purchasing authority,” Todesco said.
“This motivated us to create an even bigger and better experience in 2025, facilitating meaningful connections between buyers, sellers and suppliers.”
With major corporations moving quickly to secure their role in the industry’s evolution, leading names such as Komatsu, Blackwoods, Denver Technology, Martin Engineering, Pinnacle Hire, and VIPER Metrics have already confirmed their participation in this year’s event.
Western Australia has long been the heart of the country’s mining industry and, in recent years, has solidified its position as a leader in innovation. Not just the beating heart of Australia’s mining industry, WA is widely recognised as a global leader in the resources sector, with a diverse range of minerals and energy commodities.
The state produces more than 50 different minerals, including iron ore, gold, alumina and nickel, all of which are essential to various industries.
Some of the world’s largest mining companies operate in WA, exporting these resources through major ports that are among the busiest in the world.
Despite the significant mining activity across the state, large areas remain underexplored, making WA both a centre of established industry expertise and a key frontier for future mineral discoveries.
The 2024 WA Mining event was a roaring success which, as Todesco highlighted, was dominated by local attendees.
“A remarkable 92 per cent of visitors coming from the state, showing WA remains a pivotal force in the mining industry,” Todesco said.
“By hosting the event in Perth, we’re strengthening ties between the country’s mining capital and businesses from across Australia.”
SAFETY MATE OFFER THEIR BLACK DOG PRODUCT RANGE TO SUPPORT THE WORK OF BLACK DOG
The Black Dog Institute is Australia’s only medical research institute dedicated to mental health across all ages. They use ‘translational research’ – combining studies, education programs, digital tools, clinical services, and public resources – to discover new solutions, foster connections, and create real world change.
Mental health is becoming widely acknowledged as an important component in business stability, workforce and even productivity. 20% of Australians will experience symptoms of mental illness each year. The Black Dog Institute does important work in this space.
BLACK DOG CUT D GLOVE
• Lightweight cut level D
• Touchscreen compatible
• Comfortable and durable
• $1 per pair donated to Black Dog Institute
BLACK DOG IMPACT CUT F
• Lightweight cut level F
• Excellent fit, breathability and comfort
• Touchscreen compatible
• Soft and flexible TPR impact protection
• Durable and breathable nitrile coating
• $1 per pair donated to Black Dog Institute
BLACK DOG STREAM EVO
• Maximum comfort and protection
• Tecton 400™ Anti-scratch and Anti-fog
• Soft, adjustable, anti-slip nose bridge
• 50c per pair donated to Black Dog Institute
SKYTEC 3030V
• Market first and only full foam face seal – ensuring excellent face fit testing results, and comfort
• Four point headstrap adjustment
• Low breathing resistance valve
• Also available in smaller size (3030V-S)
• 50c per mask donated to Black Dog Institute
The Black Dog Institute is a not-for-profit facility for diagnosis, treatment and prevention of mental illnesses such as depression, anxiety and bipolar disorder. Their aim is to create a mentally healthier world for everyone.