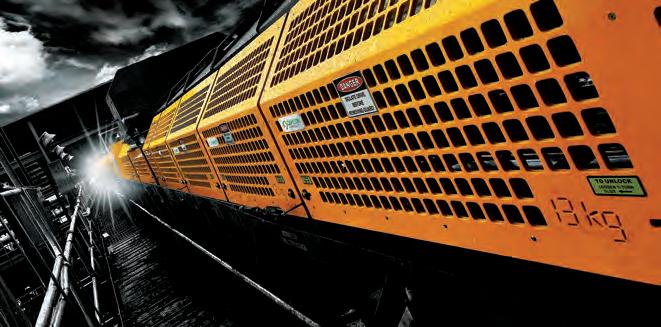
4 minute read
Diacon advancing safety in 2022
Materials Handling Diacon advancing safety in 2022
DIACON AUSTRALIA IS REVOLUTIONISING THE CONVEYOR GUARD INDUSTRY, WITH ITS PLASTIC MESH CONVEYOR GUARDING PROVIDING A SAFER ALTERNATIVE TO STEEL GUARDING THAT WILL OUTLAST AND OUTPERFORM.
Diacon Australia has its priorities in check, with its main goal to eliminate conveyor belt injuries on mine sites.
Where there are conveyor belts, there must be safety guarding for those belts, and traditionally the industry has opted for steel guarding fabricated on-site out of steel mesh.
Diacon established its plastic guarding as an alternative to steel, originating from the sugar industry in Diacon’s hometown of Mackay in Queensland.
“The big thing about our Diacon guarding - it’s lightweight, it’s durable, it’s corrosion-free and it’s safe. It stops people from being able to access a belt and either be pulled into or be hurt by that belt,” Diacon Australia general manager Matt Kennett says.
“Sugar is an extremely corrosive substance, so we wanted to come up with a system that could outlast the steel guarding, which we have.”
The plastic guarding has moved far beyond its original use in Mackay’s sugar industry, with Diacon servicing mine sites across every state in Australia, in Papua New Guinea, New Caledonia, Indonesia and the United Kingdom.
With safety at the forefront of Diacon Australia’s ethos, its plastic guarding hits the mark, with its lightweight design suitable for a one-man job and a system customised to fit the exact belt it is being used on.
“That’s probably one of the biggest things Diacon has got too, we’re pretty much a one-stop shop from design, to manufacture, to install,” Kennett tells Safe to Work.
“When we’re asked by a mine, we go and have a look at their conveyor systems, we scan their belts with 3D scanning, and then we design our system around their belt.
“Then we will manufacture the guarding, and we will go out with a team to do the site install.”
Steel guarding created on-site out of steel mesh is heavy and bulky, which creates several safety issues.
It takes two to three people to take it down when you need to do maintenance on the conveyor, whereas with Diacon, one person can lift the guarding by themselves.
“All our guarding hangs on handrails, it’s all safely hung, so there’s no issue of anything being able to fall over or taking up area on the walkways, and it’s also a lot lighter,” Kennett says.
“A standard steel mesh guard could be 30+ kilograms, whereas one of our biggest guards might be a maximum of 16 kilograms.”
Diacon Australia is positive for the year ahead, with an even stronger push for safety and innovation on the cards for 2022.
The company is well and truly spreading globally, with further plans to grow across the world.
However, Diacon stresses the importance of supporting Australian businesses in the wake of the pandemic as life returns to somewhat normal.
“I think it’s extremely important to support local, we are proudly Australian owned and operated,” Kennett says.
“You’ve got to look after your own backyard and that’s what we want to do.”
Not only will 2022 see a growth with Diacon’s existing products; the Diacon
Diacon conveyor guards are designed and manufactured in Australia.
Conveyor Guard, the Diacon Hungry Board and the Diacon Safety Panel, but there is also a new product set for release in the first quarter of the year.
The new range of guarding is currently in the trial phase at a mine site in the Bowen Basin, and in a sugar mill in Mackay.
The new product will keep the same lightweight design that Diacon plastic conveyor guards are famous for but will increase the visibility of the guarding.
“It will be just as robust, and it’s coming from listening to what our customers want and working with our customers to come up with some new solutions for them,” Kennett says.
“That’s one great thing about Diacon - how adaptive we are to our customers’ needs.
“All of our guarding is customised because no two conveyor belts are the same, and we understand that, and that’s what we do.”
The more and more guarding that Diacon is getting out into mine sites, the more people are realising that there is an alternative to steel mesh guarding that is safer because it’s lightweight, easy to use, and it’s tailored to suit site-specific situations and applications.
Diacon Australia has also put in the hard yards to refine their processes and improve the plastic quality to be able to last in the varied environments of the mine sites.
“Out in the Bowen Basin you get such harsh environments from 50+ degrees in summertime down to well in the negatives, so you’ve got to have a product that can withstand all those temperatures,” Kennett says.
Kennett praises his team at Diacon for how they’ve fared throughout the pandemic, and for how resilient they have become as a company, saying 2022 is onwards and upwards for them as they continue to help keep mine sites and workers safe.
“The number one goal is to make sure workers are going home to their families at night-time,” Kennett says.
“When they’re doing maintenance on the conveyor itself, there’s no room for them to hurt themselves with our guarding.
“Our aim is to build long-term
Diacon’s plastic guarding is lightweight, durable, corrosion-free and safe.
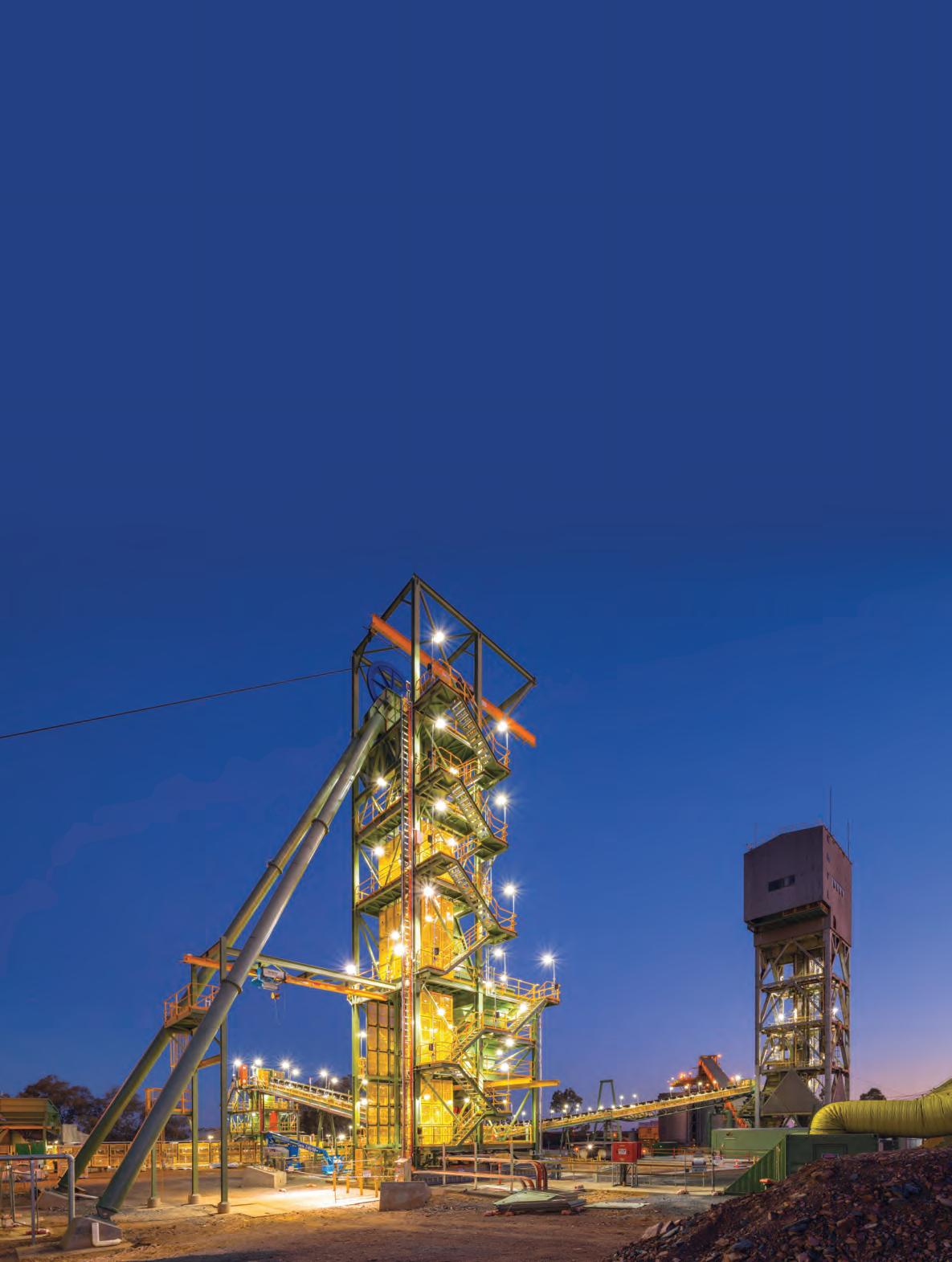