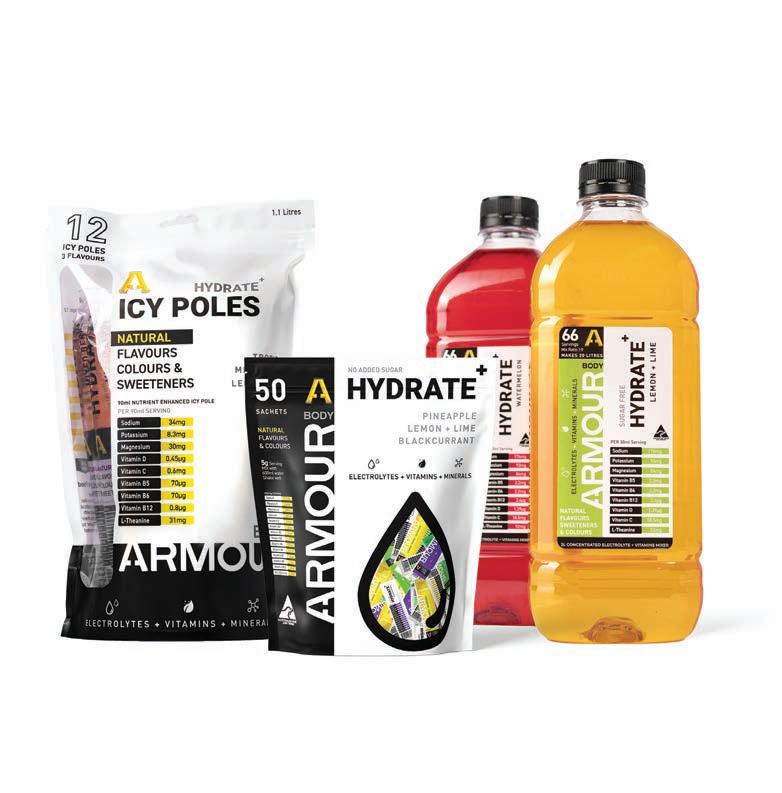

Pushing the boundaries on style and innovation, the NEW Navigator X offers a protective eyewear solution without compromise. Featuring the iconic wayfarer design, high quality materials and specialist lens options, the Navigator X is the next level for style & safety.
+ Market first HD lens dramatically improves clarity and contrast, heightens colours whilst relaxing the eye
+ Made using ethically sourced Bio-Based materials
+ Premium UV400 FLOW-TEC Anti-Fog and Anti-Scratch lenses (including polarised and mirrored)
Safety Mate’s latest innovation is the new NXG GreenTekTM environmentally conscious range of gloves which are manufactured using up to 50% recycled yarn. Every pair of GreenTekTM gloves repurposes one to two plastic bottles.
CERTIFIED CARBON NEUTRAL BY SGS
The GreenTek™ glove range has been certified as carbon neutral by SGS. These gloves meet stringent requirements for achieving and maintaining carbon neutrality.
Gloves that help the environment without compromising performance
Working together to reduce plastic waste and carbon emissions
PAUL HAYES
THE NEW YEAR HAS OFFICIALLY BEGUN, BRINGING WITH IT A FRESH OUTLOOK ON HOW WORKERS CAN STAY SAFE AT EVERY STAGE OF MINING.
here’s no shortage of heavyduty equipment on a mine site.
minerals.
But under the demands of such a heavy industry, critical equipment is in constant need of more than a little tender love and care.
In all the activity of drilling and hauling, mine maintenance is often overlooked when it comes to safety. In this issue of Safe to Work, we take a look at the technology, initiatives and products that are keeping workers just as safe when the mining stops.
Whether it’s next-generation guards changing the way conveyor maintenance is done, heavy lifting equipment taking the burden out of equipment repair, or a data suite rethinking operational intelligence, one thing is for certain: it’s a new era of safer maintenance in 2025.
Elsewhere in this issue we welcome a new association partner, the Australian Institute of Health and Safety (AIHS). As a national advocate for workplace health and safety, the AIHS has a long
legacy providing workers with the critical information and resources they need to ensure they’re safe on the job.
Now the association is bringing its wealth of health and safety knowledge to the pages of Safe to Work.
We sat down with AIHS chair Cameron Montgomery to discuss the institute’s campaign to make key work health and safety Standards free for miners.
Whether mining deep underground or extracting ore from the surface, no worker should be without the very best safety knowledge and innovations keeping them protected.
As a new year of mine safety dawns, so too does the opportunity to look to new and exciting innovations and find out what the future holds.
Paul Hayes Managing Editor
Aptella proudly distributes machine control and positioning systems across Australia and south -east Asia.
Its extensive portfolio offers miners complementary solutions from leading technology innovators, helping to bring the latest innovations to Australian shores.
From fleet management and highprecision machine guidance to 3D laser scanners and remotely piloted aircraft, Aptella offers a comprehensive suite of solutions.
Through long-term partnerships, Aptella supports and advises its customers on the best solution for their needs, enabling them to push the boundaries of what was previously thought possible with automation and positioning technology products and systems.
Aptella seamlessly integrates advanced hardware systems with sophisticated software platforms, empowering customers to analyse, monitor and design with a new level of efficiency.
Offering a full spectrum of instruments and systems supported by reliable service and industry expertise, Aptella aims to ensure its customers have the comprehensive support they need for any project.
COO
CHRISTINE CLANCY
MANAGING EDITOR
PAUL HAYES
Tel: (03) 9690 8766
Email: paul.hayes@primecreative.com.a
JOURNALISTS
KELSIE TIBBEN
Tel: (03) 9690 8766
Email: kelsie.tibben@primecreative.com.au
OLIVIA THOMSON
Tel: (03) 9690 8766
Email: olivia.thomson@primecreative.com.au
DYLAN BROWN
Tel: (03) 9690 8766
Email: dylan.brown@primecreative.com.au
ALEXANDRA EASTWOOD
Tel: (03) 9690 8766
Email: alexandra.eastwood@primecreative.com.au
CLIENT SUCCESS MANAGER
JANINE CLEMENTS
Tel: (02) 9439 7227
Email: janine.clements@primecreative.com.au
RESOURCES GROUP LEAD
JONATHAN DUCKETT
Mob: 0498 091 027
Email: jonathan.duckett@primecreative.com.au
BUSINESS DEVELOPMENT MANAGER
JAKE NIEHUS
Mob: 0466 929 675
10 Maintaining mines
How can companies ensure maintenance is carried out efficiently and safely?
22 Data done differently
Aptella is on a mission to help Australian miners get home safe every day.
32 Preventing future fires
12 Beast mode
The latest release from Nivek Industries is making a name for itself in heavy-duty maintenance.
18 A force of nature
Earthquakes, lightning strikes and windstorms; BHP has seen it all.
24 Should WHS Standards be free?
It’s an issue much bigger than saving a buck.
26 Finding the missing link
Why poor nutrition could be mining’s biggest safety and productivity risk.
The NSW Resources Regulator told Safe to Work how miners can reduce the risk of another Grosvenor-style fire.
48 Keeping a lid on fumes
The new Speedglas welding helmets feature never-beforeseen technology.
50 Simplifying sun safety
One young sparkie’s invention is keeping miners safe in the sun.
KALIUM LAKES MADE A SERIES OF CHANGES TO THE TYRE-CHANGING PROCESS ON ITS MINE EQUIPMENT AFTER A WORKER WAS INJURED BY AN EXPLODING ROAD TRAIN TYRE.
It all started in July 2022, when an incident occurred on an access road at the Kalium Lakes Beyondie mine around 160 kilometres south-east of Newman, Western Australia.
A road train was parked off an access road after the driver heard a noise coming from the truck. Two workers travelled from the mine site to attend to the vehicle and, after diagnosing the issue, began greasing the pivot points.
During this process, one of the men noticed the truck had a flat inner tyre on the rear axle that had come off its bead. Upon completing the initial repair work, the workers turned their attention to the deflated tyre.
As the workers were reinflating the tyre, it exploded. An investigation revealed they had both been standing in the line of fire in front of the tyre at the time, due to being provided with a 1m inflation hose.
The percussive blast propelled one of the workers backwards, knocking him unconscious for around four minutes. The force blew off his safety glasses and hard hat, tore his shirt and caused numerous small wounds.
The worker had been contracted by K19 Mining to provide services at Beyondie but had not received any training prior to the incident beyond a basic site induction and did not complete a job hazard analysis prior to fixing the tyre.
WorkSafe commissioner Sally North said he is lucky to be alive.
“It is common industry knowledge that a tyre explosion can result in a sudden release of stored energy known as a percussive blast,” North said.
“Workers should not be in the line of fire when reinflating tyres and should be using tyre cages in a controlled environment.
“There are a number of measures K19 Mining could have taken to significantly reduce the risk to the workers.”
Both K19 and Kalium Lakes have taken measures to protect workers performing tyre maintenance in the future.
K19 purchased 15m air hoses to allow workers to stand further away, replacing the 1m hoses that led to
the incident and effectively keeping workers out of the line of fire.
Kalium Lakes has implemented a new procedure that requires tyre reinflation to occur in K19’s on-site workshop. The miner has also ensured tyre cages are available in the area.
Designed for the safe inflation of tyres, the cages are constructed to absorb energy from a tyre failure or explosion.
By making targeted changes, Kalium Lakes and K19 have forged a path forward to a safer, more effective future of tyre maintenance.
NEW Speedglas™ PAPR with 30% lower starting price point * !
The new 3M™ Speedglas™ G5-03 Pro Air with Heavy-Duty Adflo™ PAPR gives professional welders the ultimate in comfort, protection, and adaptability in a lightweight fixed front welding helmet. *Compared to 3M™ Speedglas™ Welding Helmet G5-01
NEW TAP Technology: Tap to access weld, cut, and grind settings
Control the airflow inside your helmet for optimal comfort 73 x 109mm viewing area with SideWindows & True-View optics
Configurable extra head and neck coverage options (e.g. leather) 12-hour Adflo PAPR supplies at least 50 times cleaner air (RMPF= 50)
Optional task light specifically designed for welding
BHP PRESIDENT GERALDINE SLATTERY PROVIDED SAFE TO WORK WITH SOME INSIGHTS ON WHAT THE FUTURE OF MINE SAFETY MIGHT BRING.
With another year officially in the books, the Australian resources industry is preparing for a fresh start – and miners are no doubt keen to keep their slates clean and injury-free.
As growing forces like the global energy transition ramp up, so too does the need for more mines to keep pace with the demand for essential metals and minerals.
More mines mean more workers. Western Australia’s mining industry alone supported a record 134,871 full time miners in the 2023–24 financial year – a number that is expected to explode in the coming decades.
But as new graduates enter the industry, there are concerns about how a new, untested generation will be kept safe on the job.
Speaking at the Melbourne Mining Club Luncheon in December, BHP president Geraldine Slattery told the audience that Australia’s skills and talent are “under threat”.
“We must be champions of more competitive settings,” she said. “We cannot change the rocks we have, but we can change the enablers and settings in their discovery, extraction and development.”
According to Slattery, nearly half of the global skilled engineering workforce is set to retire in the next decade, which means majors like
BHP are preparing for an even more pressing skills drought than the sector is already facing.
As the everyday risks of mining, industry-wide skills shortages, new technological advances, and a drive to increase productivity coincide, it begs the question: how will miners continue to keep workers safe?
Speaking with Safe to Work after the Melbourne Mining Club event, Slattery said increasing productivity and investing in new technologies like artificial intelligence (AI) will be key drivers of not only attracting new talent to the sector but also keeping them safe.
“Creating a safe workplace and getting people home safe is table
stakes in attracting people and keeping people [in the sector],” Slattery told Safe to Work
“Technology is actually our friend in this area. Autonomous haulage is removing people from pit environments and interacting with vehicles, and there’s many more examples.
“I think in terms of how we bring that to life … you need to have the right skills the right regulatory environment needs to support that. That’s the goal for an ecosystem that makes it sustainable.
“Technology and productivity and safety very much go hand in hand. If anything, it’s a need for us.”
But technology won’t be the only driver of safety in 2025, just as hazards presented from mining practices won’t be the only challenge. The push to establish a psychosocially safe workplace will continue to be a key trend sweeping the resources industry in the year to come.
WA passed the Industrial Relations Legislation Amendment Bill 2024 in November 2024, with the majority of changes set to come into effect from January 31 2025.
Under the new reforms, individual public and private sector workers who are bullied or sexually harassed at work can make an application to the WA Industrial Relations Commission (WAIRC) for an order to stop said bullying or sexual harassment.
The ‘stop bullying and sexual harassment’ provisions provide the WAIRC with the power to address a worker’s allegations directly and promptly. This can include ordering compensation to be paid to the worker being harassed.
Rio Tinto is one mining major determined to lead the way in the psychosocial safety space, having recently delivered a progress review on its work to deliver sustained workplace cultural change across its global operations.
An initial ‘Everyday Respect’ report was undertaken in 2022, which outlined 26 recommendations for Rio Tinto to improve workplace culture. Two years into a long-term cultural change program, a review has found
that progress is being made with promising signs of improved culture, innovation and performance.
The latest progress review found the 26 recommendations have been largely implemented with longer-term actions ongoing.
Around half of the 11,600 survey respondents reported a perceived improvement in relation to bullying (50 per cent), sexual harassment (47 per cent) and racism (46 per cent).
A majority of respondents expressed confidence the company will make a meaningful difference in these areas in coming years and felt ‘Everyday Respect’ is now widely considered a normal conversation within the company, which is a critical step for culture change.
Rio chief executive Jakob Stausholm said the company will continue to lead the industry into a new era of psychosocial safety where all miners feel mentally and physically safe at work.
“I want to thank everyone across our business who has shown the courage to speak up, as your honesty will guide our ongoing efforts to become an organisation where every day is safe, respectful, and productive for everyone,” Stausholm said.
“The review also shows that while progress is being made, achieving the sustained change we want to see in our culture will require ongoing focus and effort.
“We will stay the course.”
Keeping equipment clean can be an overlooked aspect of machine maintenance.
MAINTENANCE IS UNIVERSALLY UNDERSTOOD TO BE A CRUCIAL ASPECT ON ANY MINE, BUT HOW CAN COMPANIES ENSURE IT IS DONE EFFICIENTLY AND SAFELY?
Making sure workers have the correct personal protective equipment (PPE) and are up to date on their certifications are two of the most important safety aspects on a mine site.
But there is another, less discussed safety requirement that regularly saves lives: maintenance.
If done correctly, machine maintenance can lead to a longer life for the asset, as well as a longer life for those around it. Regular inspections and maintenance are essential in preventing equipment failures which can result in serious accidents and even fatalities.
Safe to Work takes a look at some of the key considerations miners should take into account when conducting maintenance.
In a world of wear-and-tear problems, the simple notion of machine
cleanliness can easily be overlooked. But ensuring machines are clear of dirt and grime is one of the most important upkeep activities.
The first step of many regular maintenance assessments is a visual inspection. This can be harder to achieve when a machine is dirty, meaning a potential hazard is more likely to be missed.
Dirty machines are also more likely to break down, halting production and creating a potential safety hazard.
“Cleaning plays a vital role in equipment upkeep, ensuring optimal performance and reducing the risk of malfunctions or accidents,” industrial cleaning company SCS Group said.
“Regular cleaning removes dirt, grease and debris that can compromise the functionality and safety of machinery. By prioritising equipment cleaning, mining companies can enhance worker safety.”
Good housekeeping around the machines can also prevent trips, slips and falls.
The right protective equipment is essential everywhere on a mine site, including when employees are conducting maintenance.
With machines regularly standing more than 10m tall, it is imperative that employees not only wear the correct PPE to work at heights but also know how to use it. The same goes for those working with electrical components.
Equipment maintenance can also lend itself to working in tight spaces, which makes appropriate hand protection is essential. The wrist and hand were the most common site of injury in 2023, making up 38 per cent of all work-related hospitalisation in Australia.
Maintenance is essential to a mine for both productivity and safety reasons.
Hand impact and crush injuries, which occur when a worker’s hand is trapped between two objects, were by far the most common at 56 per cent.
The right work glove when undertaking maintenance activities must be comfortable, fit well, protect against task-specific hazards and provide good grip.
Regular maintenance is safe maintenance, so it’s important for mines to stay up to date on scheduled machine servicing.
Missing a regularly scheduled maintenance interval might not sound like a big deal at first, but it can have far-reaching ramifications. A crucial problem might be missed that leads to significant safety hazards down the track.
Scheduled maintenance also allows mines to reduce downtime, which can occur if a piece of equipment unexpectedly stops working.
“Consistent preventive maintenance helps to ensure the equipment is regularly inspected and serviced so that it operates at optimal performance,” McLanahan director of global sales – mining Lee Hillyer said.
“It helps identify and address potential problems before they lead to failure, minimising the risk of unplanned downtime and expensive repairs or replacements.
“A maintenance strategy should be determined based on the needs of each specific site, using the maintenance guidelines in the equipment manual as a baseline for the minimum requirements.”
Many wouldn’t think twice about jumping on a ladder to change a light bulb at home, but even small maintenance tasks like these should be approached with caution on a mine site. It’s important that every employee who undertakes on-site maintenance work is appropriately trained and educated in the task.
According to workplace operations company SafetyCulture, experience is often the difference between a prolonged equipment outage and a short one.
“Maintenance training is an important part of any business, particularly in ensuring workplace safety and equipment efficiency and condition,” the company said.
“Before properly performing maintenance tasks, training is essential to make sure your employees are aware of the right safety procedures before, during and after work. Regular maintenance training also helps ensure that workers are updated on any possible changes in practices.”
It’s also important that mines hold refresher courses for those with maintenance certifications, as systems and equipment change over time.
Approaching maintenance onsite can seem daunting, but with the correct procedures in place, miners can ensure every employee gets home safely at the end of the day.
Mine maintenance has come a long way over the years, with new and emerging innovations making the practice easier and safer by the day.
But there’s no getting around the fact mining is a heavy-duty industry that requires the maintenance of multitonne equipment – a necessary but often dangerous undertaking.
Putting workers in harm’s way is exactly what a mine wants to avoid, yet personnel still have to contend with lifting or working under extreme loads.
Nivek Industries first tackled this issue in 2008 when development began on the company’s Tracked Elevated Device (TED), a remotecontrolled all-terrain hydraulic belly plate jack designed for applications where a crane or forklift is not viable.
Since it was launched in 2011, TED has undergone multiple upgrades and enhancements and now has more than 40 attachments available to increase its versatility.
The success of TED inspired the Nivek team to keep innovating to improve the experience of workers at mine sites across Australia and around the world.
This has led to the development of the company’s Beast of Burden (BOB), an all-terrain remote-controlled carrier with the ability to track loads across long distances of rough terrain.
Currently available in 500kg (the 0.5T model), 1500kg (the 1.5T model) and 5000kg (the 5T model), each BOB carrier has been built to comply with three key Australian
standards: AS1170.0, AS1170.1 and AS4100.
“Besides the working load limits, the main differences between the 0.5T and 1.5T machines are the type of tracks it utilises, rubber and steel, respectively,” Nivek general manager Derrick Cant told Safe to Work.
“The 0.5T BOB with rubber tracks is designed to carry loads that are too heavy or awkward to lift manually and access areas where a forklift is unable to reach. The rubber tracks also allow the 0.5T to climb a staircase.
“The 1.5T BOB, with its increased carrying capacity, is designed to carry heavier loads to areas other machinery is unable to reach. Its increased capacity and small footprint make it a useful carrier.
“The 5T BOB is designed to carry extremely heavy components around
the worksite. With its manoeuvrability and large battery system, operators can transport those large components around the workshop safely.”
Nivek BOB Tracked Carriers are fitted with an auxiliary power outlet that allows the carrier to be modified with custom-made smart attachments to suit a variety of tasks and requirements.
With the ability to be adapted to a range of situations, BOB is well on its way to joining TED among the ranks of industry mainstays.
“Nivek designs and builds products that can be adapted to suit customer requirements,” Cant said. “This allows us to develop specific attachments to meet individual customer needs
without having to fully develop an entirely new machine.”
The company’s drive to innovate doesn’t stop with BOB’s versatility. Nivek is also helping mines make an impact in the sustainability arena with the aid of greener power solutions.
The 0.5T and 1.5T models are powered by dual 48-volt lithium batteries that provide 4.6 kilowatt hours (kWh) of power to the 3.5kW electric motor power unit, in turn driving two independent hydraulic drive motors.
The fully electric 5T model incorporates dual electric-drive motors and a battery supply of up to 14kWh.
Known for durability, both electric motors allow BOB to produce enough torque to ensure heavy loads can
be carried across various types of tough terrain.
“BOB is more than just a carrier – it’s essentially a mobile, adaptable powerhouse capable of undertaking a wide variety of jobs,” Cant said.
“I was recently at a mine site in Western Australia where workers were having to carry 60kg pumps up to 100m over rough terrain. This is the perfect application for BOB, which can handle any surface and comes with a variety of custom-made smart attachments that help it take on any task.”
Nivek has more attachments in the works to increase BOB’s versatility and is even looking to create BOB models that can carry up to 10,000–20,000kg.
All of this innovation is coming out of the company’s research and development (R&D) facility in Singleton, New South Wales.
“Most of our ideas for attachments and developments come from our end users,” Cant said. “They’ll often send us the specifications for an area where they’re having an issue and we’ll look at how we can solve it safely and efficiently using BOB or TED or another suitable product.
“There’s probably a million jobs BOB can do, and we’re only thinking of 20 of them. It’s through our customers using BOB that we can see all the ways it can make an impact on a site and drive that impact even further.”
Diacon conveyor guards are easily replaced thanks to the company keeping a record of every guard ever made.
AUSTRALIA’S CONVEYOR GUARD SYSTEM IS TAKING THE HASSLE OUT OF MAINTENANCE.
Conveyors can be fickle beasts, with falling rock and hazardous materials causing all manner of issues that need to be addressed quickly and effectively.
For any conveying application at a mine site, steel conveyor guards have long been accepted as the go-to standard. But Diacon Australia is on a mission to shift that status quo through its high-quality plastic alternative that delivers significant benefits beyond protecting workers.
Unlike traditional steel guarding solutions, the Diacon conveyor system uses a light-weight plastic mesh to provide corrosion-free guarding. The system has been making waves in the mining and resources sectors since it was launched in 2010.
“We are really proud of the contributions and advancements Diacon has made,” Diacon managing DIACON
director Brendan Refalo told Safe to Work.
“The features of our comprehensive conveyor improvement system – the Diacon hungry board, Diacon safety panel, Diacon conveyor guards and Diacon hoods – collectively enhance workplace safety and productivity through one unique solution.
“Our products are 100 per cent Australian-owned, manufactured to the highest quality and developed to handle the harshest of work environments. It’s why we’re the trusted suppliers and industry leaders of plastic guarding systems.”
Diacon Australia’s conveyor guard system has a number of key benefits:
• Easy to install, remove and maintain
• Quality build, strong in structure
• Customisable to any specifications
• One hundred per cent corrosion-free
• Up to four times lighter than steel
• Sound-deadening qualities
• Safer during operations and maintenance periods
• Long-life UV protection
• Cost-effective custom labelling
• No need to paint
• Australian made and owned
These features have led to Diacon becoming a leader in conveyor guarding, but it’s the system’s ‘hook, hang and lock’ mechanism that is changing the maintenance game.
“The guards are simple to install,” Refalo said. “They mount on custommade bosses attached to brackets and have a unique slide-lock system that locks the guard into position, in accordance with Australian safety standards.”
The slide-lock mechanism is captive within the guard, so it can’t get lost or come free and fall, a critical feature as conveyor belts are often high above ground.
“When the guards are removed from the mounting system, they can actually be hung on a nearby handrail,” Refalo said. “When most workers see this for the first time, they think, ‘How easy is that?’, and it keeps the guard off the ground ensuring it doesn’t become a trip hazard.”
Being able to store the guards on handrails during maintenance is one of
materials, and on most occasions will readily bounce back into shape after impact. Even if a panel has been badly damaged, it can be replaced at minimal cost and no extra maintenance downtime.
By retaining details of every panel guard it has ever made, Diacon is able to promptly reproduce any guard according to its original
from robust, impact-resistant
engraved on the inside of the guard, Diacon will have a replacement ready for installation during the mine’s very next maintenance shutdown.
“Our strong reputation is built on our dedication to understanding clients’ needs and our proactive approach to continued advancements in product evolution,” Refalo said.
“Our success as market leaders is thanks to the extraordinary relationships we’ve developed with our clients and distribution partners, and their understanding that we’re more than just a guarding product.”
By staying on the cutting edge of product design, Refalo said Diacon is able to bring next-generation innovations to the Australian mining industry that aim to make processes like maintenance hassle-free.
“Diacon Australia is dedicated to developing the latest design, engineering and manufacturing techniques to stay ahead of industry demands,” he said.
“By staying adaptable and responsive to evolving needs, we’ve consistently driven industry expectations for safety, productivity and efficiency as market leaders.”
XMPRO’S INTELLIGENT BUSINESS OPERATIONS SUITE CAN HELP MINERS PREDICT UNWANTED EVENTS BEFORE THEY OCCUR.
There is no question the future of mining rests on ones and zeroes just as much as it does ore in the ground.
But as new technologies develop, it’s not just the way mining is done that will continue to evolve. The way mining is not done is becoming just as pivotal to the industry’s technology revolution.
Maintenance is no longer just something that happens when machines break down. The emergence of artificial intelligence (AI) means operations can gather data 24–7 to help them make the most of the time spent with tools down.
XMPro has been helping Australia’s Tier 1 mines to get the most out of their operations since it broke into the industry in 2009. Bringing an engineering perspective to creating AI maintenance solutions for miners, XMPro has been able to understand the processes and workflows of sites on a deeper level.
XMPro chief executive officer Pieter van Schalkwyk said the company’s innovative Intelligent Business Operations Suite (iBOS) brings together a range of technologies like AI and digital twins into one easy-touse platform.
The integrated platform aims to empower organisations with realtime insights, recommendations and automated actions, creating a common operating picture across strategic, tactical and operational levels.
“We can bring in real-time data from the multitude of systems in operation on a mine site to orchestrate and manage key events that may be happening or are likely to happen with equipment,” van Schalkwyk told Safe to Work.
“We combine that data and analytics with the expertise of engineers to provide prescriptive recommendations to miners.”
By integrating real-time sensory data from across a mining operation with advanced AI processing, miners can shift their operations from reactive to predictive with the touch of a button.
The iBOS is able to anticipate equipment failure and optimise maintenance to address the root of the issue before it ever becomes a problem.
For example, the mining industry relies heavily on mobile assets, such as haul trucks, loaders and drilling rigs, which are crucial for the extraction and transportation of materials. The operational efficiency of these mobile assets can directly impact productivity and cost management.
Mobile equipment in mining operations is subject to demanding conditions and intensive use, leading to deterioration that can culminate in unanticipated equipment failures.
With detailed visualisations of asset locations and statuses, operators can quickly identify and address
issues thanks to iBOS. With built-in AI diagnostic capabilities, it can make intelligent, tailored recommendations that act as a digital consultant that already knows all the ins and outs of an operation.
According to van Schalkwyk, when developing the iBOS it was essential that any engineer on-site would be able to access the platform and find the information they need without getting bogged down in code.
“We want to make sure people have the right tools in the right part of the mining process to get the job done as safely and efficiently as possible,” he said.
This is done by using the iBOS platform’s AI pilots to marry realtime and historical data to unlock operational insights like never before.
This bird’s eye approach allows maintenance operations to be optimised, minimising downtime and maximising productivity and sustainability.
“iBOS can help miners see if their processes are actually delivering the outcomes they’re trying to achieve,” van Schalkwyk said. “Every application on the platform is built around solving a business problem and tracking how it is making a difference.”
When it comes to safety, van Schalkwyk said the iBOS’ magic comes from giving mines a new level of visibility.
“This type of technology gives you the context of machinery in relation to everything that sits around it, equipping miners with the right briefs so they can respond accordingly,” he said. “For example, if sensors pick up that a piece of equipment is becoming excessively hot and a work order comes up on another machine nearby, iBOS will send a proximity alert that stops the worker from entering an unsafe environment.”
The iBOS was recently deployed at mine with more than 50 conveyors operating 1.2km underground. The mine was having trouble with its conveyors and losing production to downtime. XMPro got to work immediately and over the first five months of implementation added an additional 44,000 tonnes of material back into production.
“The iBOS isn’t another technology that beeps constantly and is difficult to use,” van Schalkwyk said.
“We’re bringing the power of AI and data to the fingertips of miners through an intuitive platform they can rely on.”
BHP FACED ALL MANNER OF WILD WEATHER CHALLENGES ACROSS ITS OPERATIONS IN 2024, SOME OF WHICH PROVED EVEN A GIANT ISN’T IMMUNE TO THE ELEMENTS.
BHP saw its share of safety events in 2024.
Earthquakes, lightning strikes and windstorms causing power outages and challenges at its mines across the country put the Big Australian’s emergency response plans to the test.
As BHP prepares to meet new challenges head-on in 2025, Safe to Work examines the safety obstacles the major miner overcame in 2024.
BHP Mitsubishi Alliance’s (BMA) Peak Downs is one of five metallurgical coal operations in Queensland’s Bowen Basin and is well known for employing some of the biggest mining trucks in the world.
Electrical storms are not uncommon in the Bowen Basin, and Peak Downs is no stranger to lightning strikes.
A storm caused damage to infrastructure at BMA’s Peak Downs coal mine in 2020, and while no one was injured, the incident drew the attention of the state’s safety regulator. In October 2023, Resources, Safety
and Health Queensland coal chief inspector Jacques le Roux handed down directives that would see operations cease during lightning storms where strikes are detected within 16km of the mine.
The directives were issued under Queensland’s Coal Mining Safety and Health Act 1999 and relate to the operator of Peak Downs, BM Alliance Coal Operations’ Severe Weather Policy and associated Trigger Action Response Plan (TARP).
The aim of the TARP is to set out action to be taken in response to three different levels of lightning proximity.
Level 1 is activated when lightning is within 60–30km of mine, Level 2 when it is within 30–16km, and Level 3 when it is less than 16km from mine.
Regardless of the actions taken at each of these levels, BM’s response allows for operations to continue throughout all three.
According to le Roux’s orders, BM would have to stop operating at Level 2 in response to two main concerns.
The first was that heavy mobile equipment (HME) tyres filled with
air are in danger of exploding when struck by lightning.
Queensland Industrial Relations Commission President Peter Davis, who heard BM’s appeal, had a solution.
“It is common ground that if a truck suffers a lightning strike, there is a danger that air-filled tyres will explode as the electric current passes through them to earth,” Davis said in his decision, according to the Queensland Law Society Proctor. “It is also common ground that nitrogen-filled tyres will not explode.
“The answer to this problem is to fill the tyres with nitrogen rather than air, which contains oxygen. This avoids the tyres exploding.”
The second concern le Roux brought to the Commission was the risk of electrocution to workers operating HME if it is struck by lightning.
BMA argued heavy mobile equipment struck by lightning operate as perfect Faraday cages, completely protecting workers from electrical charge.
A key decision will see BMA’s Peak Downs continue operating safely during lightning storms.
Davis agreed, emphasising it was common ground that HME could be struck by lightning when operating in coal mines in the Bowen Basin.
“It is also common ground that, as a matter of physics, a metal vessel [such as a truck], when struck by lightning, operates [not necessarily perfectly] as a Faraday cage so that lightning which hits the HME will tend not to pass into and through the occupant of the vehicle but will pass across the metal surfaces of the vehicle into the earth,” he said.
Davis said the Act described an acceptable level of risk as being “within acceptable limits” and “as low as reasonably achievable”.
“It is common ground that if a truck suffers a lightning strike, there is a danger that air-filled tyres will explode as the electric current passes through them to earth.”
“Those two considerations are quite different,” he said. “Some operations may be such that whatever safety measures are taken the risk cannot be brought ‘within acceptable limits’ and therefore operations must cease.
“Mr le Roux considers that operating HMEs at Level 3 conditions is such an example. BM says that operating HMEs at Level 3 conditions
is within acceptable limits of risk, provided that the tyres are filled with nitrogen.
“If that is so then the question becomes, by reference to all precautions taken, whether ‘the risk is as low as reasonably achievable’.”
Davis believes that if HME tyres at Peak Downs are filled with nitrogen, they will have met the requirement of the Act requiring the risk to be as low as reasonably achievable.
In his decision, Davis stayed the directives requiring the mine to stop production during lightning storms, allowing Peak Downs to continue operating until a formal decision can be handed down in the future.
Peak Downs produced around 29 million tonnes of metallurgical coal in the 2022–23 financial year (FY23), a figure that would be impacted by avoidable shutdowns
affecting hundreds of vehicles over Queensland’s six-month storm season (November 1 – April 30).
The Queensland Industrial Relations Commission’s decision will allow BMA to maintain strong production numbers while continuing to keep its workers safe.
BHP’s Mt Arthur coal mine near Muswellbrook in the Upper Hunter region of New South Wales was near the epicentre of multiple earthquakes in 2024.
A magnitude-4.7 quake struck the area in August, followed by a magnitude-4.5 in early September and a magnitude-4.2 in November.
GeoScience Australia senior seismologist Dr Hadi Ghasemi told the ABC there was ongoing activity in the region, labelling it an “earthquake swarm”.
“In earthquake swarms, you have a series of the earthquakes with similar size magnitudes – it’s not like an aftershock sequence,” Ghasemi said at the time of the second earthquake.
“In this region, since the magnitude-4.7 in August, we’ve
recorded over 50 earthquakes, four of them with magnitudes larger than 4, including the recent one.”
Ghasemi said more quakes may be on the way for the miner in 2025.
“All of the previous magnitude-4 ones in this region, they were followed by smaller aftershocks,” he said.
“But then again, with the swarm activity this kind of activity may continue for months or even years to come.”
BHP paused operations to conduct inspections after each incident, confirming that no injuries to its 2000-strong workforce or damage to equipment had been recorded, with strong infrastructure and safety protocols keeping workers out of the fray.
Olympic Dam in South Australia is one of the world’s most significant deposits of copper, gold and uranium.
Located 560km north of Adelaide, Olympic Dam is made up of underground and surface operations and operates a fully integrated processing facility.
Parts of SA were lashed by extreme wind in the second half of 2024, which caused a power outage at Olympic Dam. Gusts were reported to be in excess of 130km per hour in some areas, with more than 130,000 lightning strikes recorded in the region in one 24-hour period in mid-October.
SA Energy Minister Tom Koutsantonis announced at the time that BHP’s Olympic Dam was heavily affected, with the mine shuttered for several days.
“They’ve got their critical power needs covered, but mining operations won’t be allowed to continue because of ventilation issues,” Koutsantonis said.
Ventilation is critical in a mine not only for air quality but to ensure harmful gasses and fumes can’t trigger a fire or explosion.
“All of the safety issues are in place to make sure that the smelter can remain operational and warm,” Koutsantonis said. “We’re working very, very hard to make sure they get back online as fast as possible.”
A BHP spokesperson said electrical storms in SA’s north had caused structural damage to transmission
lines, including the two lines that supply Olympic Dam.
“ElectraNet crews are working to restore power as soon as possible, and we are working with them to better understand the scale of the impact and recovery timelines,” the spokesperson said at the time. “In the interim, backup generation and business continuity plans are in place.”
Power outages can pose significant safety risks on a mine site. With operations fully underway, a sudden stop of major equipment and processing infrastructure can put workers at risk.
As a mix of underground and surface mines, Olympic Dam has plans in place to remove miners from potentially dangerous situations as much as possible. This involves taking underground miners out of the line of fire by employing an autonomous train system that delivers ore to the surface.
this that will be part of BHP’s future safety approach.
It’s technological innovations like
With autonomous haulage and artificial intelligence (AI) hazard avoidance technologies implemented
across its operations Australia-wide, as well as a strong foundation of emergency response plans, BHP is well placed to drive a new era of safety in the mining sector in 2025.
While safety has come a long way in the mining industry, there’s no denying there are many dangers in the profession. People can make mistakes, but when near giant equipment hauling tonnes of rock, mistakes can be costly.
An automation and positioning specialist, Aptella has been developing and distributing new solutions to avoid collisions on mine sites across Australia and south-east Asia for more than 15 years.
With the emergence of innovations like artificial intelligence (AI) and hazard avoidance technologies, the task of monitoring safe work procedures is steadily moving out of the hands of people and passed to trusted technologies.
Machine learning enables users to use insight from millions of data points on a single screen and make
decisions backed by processing power previously unthinkable to humans.
One supplier of such technology is determined to see Australia’s mines come along the journey to a safer, more technologically integrated future.
Aptella recently joined forces with international technology giant Torsa to distribute a new collision avoidance technology to Australian mines.
Traditional collision avoidance systems often rely on a wearable tag or device that positions miners in reference to machines, sending alerts when they get too close.
But with the Torsa Collision Avoidance technology, a predictive algorithm monitors and analyses interactions between vehicles and personnel with centimetre-level precision, without the need for any wearables.
Aptella mining product manager Denzil Khan said
Torsa is an industry leader in collision avoidance.
“Collision avoidance isn’t just about identifying risk, it’s about taking corrective action,” Khan told Safe to Work. “By using a multi-sensor approach, Torsa can identify not only vehicles in the vicinity, but those out of the line of sight that pose an unseen risk to miners.”
Torsa Collision Avoidance takes these points of data and processes them in real time to provide an educated alert to operators.
“Whether a machine or person – moving or stationary – the solution is able to determine exactly what’s happening,” Khan said. “It’s drumming up a lot of interest in both the surface and underground sectors, as it’s usually difficult to have highly accurate collision avoidance technology so far below the surface.
“Torsa incorporates not only productive mining equipment but also all ancillary equipment, meaning miners have complete coverage across their fleet and workforce, helping them ensure everyone goes home safely every day.”
While Torsa is seeing great success across the industry, there’s another technology in Aptella’s distribution repertoire taking the industry by storm: Blindsight.
Brought to the market by heavy industry software expert Presien, Blindsight boasts AI capabilities pretrained for industrial applications.
The technology works by detecting a potentially dangerous on-site situation about to unfold and alerting the operator, calling their attention to the risk before it turns into a costly accident.
But that’s not what sets Blindsight apart, according to Aptella mining executive manager Andrew Granger.
“The real differentiator is that it’s an integrated system that has a full reporting suite on the back end,” Granger told Safe to Work.
“A standalone system doesn’t offer visibility of what’s going on, whereas an integrated system with comprehensive real-time reporting
managers and supervisors to see behaviours or habits that may be compromising safety.”
Blindsight gives users access to a full spectrum of data, including automated health and safety reports, so elements like safety metrics and site performance can be quantified with the tap of a finger.
Granger said Blindsight can also be tailored to each site’s requirements, no matter the equipment they have in operation.
“If you need a certain cone, for example, recognised on one site but not on another, the AI can be trained and developed to alert accordingly,” he said. “We’re finding huge success with leading mining companies across Australia around those highrisk areas where there are larger machines operating alongside smaller equipment and personnel.
“Unfortunately, there are ongoing instances where workers are being hit by unseen plant they didn’t know was moving, so having the Blindsight system in place is alerting operators very quickly and eliminating the risk.”
With new technologies increasingly incorporating AI, Granger and Khan agree miners can be confident in Aptella’s long history delivering top-tier solutions that make a difference on-site.
“The AI boom has been happening for a little while now, but for Aptella, it’s about using the data we’re gathering to create even more value for our customers,” Khan said.
Granger said this data can help miners not only on their journey to keep workers safe, but to increase productivity and profitability.
“We’re working to produce better software, better hardware and better value,” he said.
“By partnering with developers like Torsa and Presien, we can offer Australian mines a leg up into a safer, more productive, data-driven era.”
THE AUSTRALIAN INSTITUTE OF HEALTH AND SAFETY IS CALLING FOR MANDATORY WORKPLACE HEALTH AND SAFETY STANDARDS TO BE FREE – BUT THE ISSUE IS BIGGER THAN SAVING A BUCK.
The phrase ‘cost-of-living’ has rolled off the tongue of almost every Australian in the past 12 months. And as households across the country tighten their belts, so too do the nation’s businesses.
The mining industry is a huge contributor to the Australian economy, but increasing costs are making it difficult for emerging miners to gain a foothold. While no miner, big or small, would ever sacrifice safety in the cost crunch, there are growing concerns of an emerging barrier to accessing critical safety information.
Work health and safety (WHS) Standards are the guidelines, procedures and specifications that help businesses stay safe, consistent and reliable.
The Standards are not laws, so there is no specific requirement for businesses to conform to their guidance, but things get complicated when a Standard is referenced in legislation.
In 2011, Safe Work Australia developed a single set of WHS laws to be implemented across Australia. These are known as the model WHS laws.
The model WHS laws have become legally binding in New South Wales, Queensland, Tasmania, South Australia, the Northern Territory and the Australian Capital Territory, but not Victoria or Western Australia.
WA passed a version of the model WHS Act in November 2020, but it will not be operational until certain regulations are finalised.
If a specific Standard is enshrined in these or any laws, businesses are required to conform, and therefore must purchase the Standard.
These Standards can cost miners hundreds or thousands of dollars, which could otherwise be spent on critical personnel or equipment.
There are currently 17 Australian Standards referenced in the model WHS laws set out by Safe Work Australia, which must be purchased, but dozens more are relevant to mining operations that are not mandatory.
Some of the mandatory Standards include regulation around pressure equipment, respiratory protective devices, electrical installations and personal equipment for working at height – just a few of the common and recurring practices with which those who work in the mining industry will be familiar.
This situation begs the question: if a Standard is enforceable by law, should it be available free of charge?
According to the Australian Institute of Health and Safety (AIHS), the answer is yes.
“We currently have an environment where cost pressures on businesses are significant,” AIHS chair Cameron Montgomery told Safe to Work. “Our concern is that businesses may forgo critical safety information because the cost becomes a barrier.”
For the AIHS, it’s not about making all Standards free; it’s about making sure businesses are given access to essential safety information that is relevant to them.
Montgomery believes any Standards referred to in legislation should not sit behind a paywall and should be freely available to those tasked with adhering to them.
“These documents are crucial to ensuring workplaces are safe and productive,” he said.
“Our members are telling us that free access to Standards would help to reduce the regulatory burden faced by business owners and safety professionals.”
According to Montgomery, most of the original pricing for Standards was set based on the number of physical pages printed. Nowadays, however, Standards are distributed digitally.
“At a minimum, costs should be reduced to reflect that,” he said.
The AIHS is currently campaigning to make mandatory Standards free for all businesses, calling on all levels of government to play their part in ensuring the minimum standards of safety can be met across Australia.
Montgomery said a precedent for cutting costs was set last year when several Standards were made free of charge – but the fact they did not relate to commercial use meant they were irrelevant to businesses.
“It’s not just business owners impacted by these costs,” he said. “For health and safety professionals, accessing the necessary Standards across several industries and jurisdictions can be a significant cost burden to maintaining current knowledge.
“It’s time these costs were removed to help businesses meet their obligations to operate safely and productively without having to be further out of pocket.
“Everybody deserves to go to work safe and come home safe.”
In heavy industries like mining, the margin for error is often razor thin. Small impairments in physical or cognitive function such as fatigue, delayed reactions or lapses in focus can have catastrophic consequences. The good news is that these risks can be mitigated. With modern science and a growing body of research, there are clear and actionable ways to improve safety through better nutrition and recovery practices.
company founded by four friends united by a shared obsession with nutrition and performance, and a vision to create real change.
experience in the mining and construction industries, the founders saw a gap in the market for recovery and performance solutions that are
genuinely effective and free from hidden toxins, harmful chemicals and misleading marketing.
“Our mission stems from a simple belief: nutrition free from harmful chemicals and effective recovery are the most important pillars of optimal performance,” Body Armour director Toni McQuinn told Safe to Work. “We are committed to shining a spotlight on the harmful chemicals still present in many recovery and
Equipped with this knowledge, he believes miners will be able to make more informed decisions about what products they choose to consume, ultimately supporting the health and performance of the industry at large.
“During my 15 years in the industry, managing human resources functions and collaborating closely with HSE [health, safety and environment] teams, I’ve witnessed exceptional efforts placed on the latest technologies, systems and processes to keep our workforce safe,” McQuinn said.
“However, one critical aspect often overlooked – the role of nutrition and recovery in safety-critical factors like focus, muscle movement, reaction time, sustained energy and mental strength. We do it very well for sports, so why not for operators executing challenging tasks in difficult conditions?
“These factors, which are pivotal for performing highstakes tasks, often lacked proper education and integration into safety strategies.”
McQuinn said this issue is compounded by the quality of recovery solutions traditionally available to the industry.
“Many have been formulated with excessive sugar and harmful chemicals, including artificial colours that have been linked to serious long-term health impacts, directly contradicting their intended purpose of promoting health and performance,” he said.
“At Body Armour, our mission is to serve employers who are committed to protecting and empowering their workforce.”
The company’s range of health and wellness products is tailored to meet the unique needs of industries like mining where focus, endurance and recovery are critical to safety and productivity.
“Guided by advanced clinical research and modern science, we develop solutions that enhance the body’s ability to perform and recover effectively,” McQuinn said.
“Among our range, our hydration and sleep solutions provide tangible health benefits that directly translate into optimal focus, muscle movement, sustained energy, and improved recovery for workers in physically demanding environments.”
With cordials, icy poles and powders that can be mixed into water available through Body Armour’s Hydration+ range, miners are able to grab and go with whichever form of hydration suits them best.
The range was designed to eliminate unhealthy ingredients like
sugar and artificial additives, offering miners an alternative to traditional hydration products that support longterm health.
“Our Hydration+ range is a robust recovery solution designed to support workers who face extreme physical exertion and environmental stressors, such as heat, long shifts and demanding tasks,” McQuinn said.
“Through five key electrolytes, a vitamin complex and nootropics, our hydration range is designed not only mitigate heat stress, dehydration, cramping and muscle fatigue but also to maintain energy levels and focus.
“By providing a clean, toxin-free alternative to traditional hydration solutions, Body Armour ensures that workers can stay hydrated without the harmful chemicals found in many conventional products.”
Adequate sleep is often overlooked, yet it plays a critical role in recovery, cognitive function and overall performance.
The Body Armour Sleep support targets workers who struggle with long shifts and irregular schedules.
Body Armour Sleep targets workers who struggle with the physical and mental demands of long shifts and irregular schedules.
“Our formula is designed to enhance the natural sleep cycle, promoting deeper, more restorative sleep, particularly during the crucial REM [rapid eye movement] and deep sleep stages,” McQuinn said. “This ensures workers can recover effectively and perform optimally during the day.”
The Body Armour Sleep blend is one solution to a reliance on chemicals like sleeping tablets, which can have serious adverse effects on performance.
“Body Armour Sleep is formulated with nine active ingredients, including some of the most potent natural sedatives, to enhance the body’s natural restorative processes,” McQuinn said.
During Body Armour’s site visits across Australia delivering educational
content on body functioning, nutrition and performance, McQuinn has seen firsthand the appetite from both employers and their workforces to better understand the fundamentals of nutrition and its link to overall health.
“We’re also seeing HSE teams asking more critical questions about the composition of products and solutions provided to the workforce,” he said. “It’s encouraging to witness this focus moving beyond cost to value, recognising the role that proper nutrition and recovery play in safety, performance and overall wellbeing.
“These are all excellent steps in the right direction.”
By working with employers and collaborating with HSE teams to take a holistic approach to health, Body Armour is on a mission to change the way sites tackle worker wellbeing.
“While most companies focus solely on rehydration, Body Armour takes a broader approach by targeting overall performance,” McQuinn said.
“Our formulations are designed to provide all essential electrolytes, minerals, vitamins and nootropics necessary for optimal recovery and peak functionality, far beyond mere replenishment.”
Partnership is a cornerstone of the way Body Armour operates and the company has received glowing feedback from its hands-on approach.
“Customer service is a core metric for us, and we actively gather feedback to drive our continuous improvement objectives,” McQuinn said.
“We’ve been fortunate to receive outstanding feedback from several mining and heavy industry sites.”
As part of these partnerships, Body Armour has provided comprehensive support with access to educational resources in areas like heat stress management, fatigue management protocols, nutritional frameworks, hydration protocols and other key wellness topics.
The company follows this support with on-the-ground training for the entire workforce, ensuring every individual receives the tools and knowledge they need to make informed decisions about their health and performance.
With a team made up of experienced nutritionists, chemists and naturopaths, Body Armour has a line-up of experts primed support the company’s mission and provide expert
guidance to ensure that safety and performance are maximised through proper nutrition and recovery.
Body Armour experts are also directly accessible for one-on-one consultation through the company’s online platforms, allowing partnered sites to offer their workforce an avenue for questions.
“We’re also proudly Australianowned and operated, with all our manufacturing taking place in our Brisbane and Melbourne labs,” McQuinn said.
“This gives us complete control over quality, ensures consistent supply and top quality customer service, and reinforces our ability to deliver products tailored to the demands of Australian industries.”
Looking to the year ahead, McQuinn said Body Armour will continue working with miners to raise awareness about the critical need to incorporate nutrition education and training into safety strategies.
“With Body Armour, you’re not just investing in a product,” he said. “You’re gaining a partner dedicated to delivering innovative performance solutions that prioritise health, safety and sustainability.”
No
Smart tradies choose smart solutions.
140 YEARS.
Back in 1887, one Englishman’s quest for gold in Ballarat didn’t pan out as he’d hoped.
Like so many young men and women at the time, James Oliver traversed an entire ocean to reach Australian shores in search of fortune. But while many daring miners struck success, Oliver was not one of them.
A shoemaker by trade, he fell back on what he knew best and began making boots for local farmers and miners instead. What was borne out of one failure would soon become one of Australia’s longest-running success stories.
As the company grew and expanded across the country, Oliver Bootmakers became a name associated with high-quality, reliable work boots for busy feet.
Not only known for its quality, Oliver Footwear has always aimed to be on the forefront of delivering the latest research and developments in protective footwear to miners.
The company is now looking to the future.
Oliver Footwear’s product development manager Brett Huggins is confident the bootmaker will continue its legacy of setting new trends of innovation.
“Oliver Footwear is very much a source of, and an adapter to, new technologies that can improve certain features of our footwear,” Huggins told Safe to Work.
“Miners are in their boots for 12 hours a day in some of the worst conditions that you can imagine, so it’s essential their boots offer protection
technologies on offer.”
The AT 55 Series and AT 65 Series are Oliver Footwear’s premium miningfocused work boot range, highly specialised with a range of in-built features developed specifically for Australian miners.
Boasting resistance to heat, cuts, slips, sole penetration, static, abrasion, oil, fat and acid, these boots mean serious business.
The AT 65 Series was specifically created in consultation with the coal mining industry to offer even more targeted protection underground.
“A high-leg mining boot, the AT 65791 is built for the harsh, changeable conditions faced by coal miners,” Huggins said.
“It has a completely waterproof lining that doesn’t allow any water to go through, even if the if the leather outer gets wet.”
Huggins said the boot’s abrasionresistance works to protect the whole foot, thanks to a special Oliver technology.
“In addition, we have features like our METprotect metatarsal guard, which provides an additional layer of shock-absorbing material to create a unique protective shield for the foot.”
While steel caps protect the toes, METprotect extends protection from the back of the toe cap to where the foot raises from the ankle. It offers protection from any rolling objects like rocks or debris that get past the toe.
“Traditionally, metatarsal guards were very rigid and stiff and made from metal or hard plastic plates sewn into leather pockets along the boot,” Huggins said. “They were very cumbersome and uncomfortable to wear for long periods of time.”
Oliver Footwear’s engineers were able to develop the METprotect technology using a soft, high-impact foam called ‘Poron’ that deadens the blow from impacts.
“It’s a soft pad of foam that sits over the top of the foot and absorbs about 95 per cent of all impact,” Huggins said. “It’s very lightweight and flexible, so when you’re wearing it, it feels
unrestrictive; however, under impact, it hardens to protect the foot.”
Another innovation to come out of the Oliver workshop is the company’s nitrile rubber soles, which are resistant to surface temperatures of up to 300°C. Because they’re designed to endure harsh conditions, the soles feature high abrasion resistance and penetration protection that stops nails or any sharp objects coming up through the sole of the foot.
Not only does Oliver Footwear work to meet rigorous Australian workplace safety standards, the company is also actively involved in creating them. It is heavily involved in consultation with the mining industry at large, as well as with Australian and international workplace safety standard bodies.
Huggins himself was the chair of the Australian Standards Committee for safety footwear for 15 years.
“These committees are structured to include various user groups that wear different safety boots and report on their effectiveness,” Huggins said. “By being involved in the process, we can stay abreast of international trends and work collaboratively with those user groups to determine what’s best for the industry.”
But while safety is always central to Oliver Footwear’s practices, it’s not the only priority in which the company strives to excel.
“When it comes to mining boots, it’s all about toughness on the outside and comfort on the inside,” Huggins said. “That means keeping your feet dry, which our boots achieve by not only being 100 per cent waterproof, but also through our moisture-wicking lining, which absorbs moisture from the foot directly, keeping feet fresh and dry all day.
“But one of the biggest comfort features that we have within the Oliver footwear ranges is our COMFORTcushion impact absorption system, which provides superior cushioning, helping to reduce foot, leg and back fatigue.”
The AT 55 Series and AT 65 Series are equipped with the NANOlite footbed, comprising multiple layers
of urethane foam that massage your feet as you walk, promoting greater blood flow and helping to reduce fatigue. A perforated foam air control layer also enhances air circulation, reducing odour.
“We have spent a lot of time on creating what we think is a very comfortable boot, while not neglecting the physical environment and making sure that it protects the wearer,” Huggins said. “Feedback we get regularly is that the boots don’t need to be worn in; they can be worn straight out of the box, and customers are confident they will be comfortable from day one.”
Oliver Footwear has a national network of distributors the company works with to determine the specific needs of each site at which its boots are deployed.
By taking into consideration the mine’s location, its workforce, the resources it mines and the processes it uses, Oliver Footwear is able to recommend specific boots that will be the best fit for the mine. From there, the company offers mines a trial of the boots so they can assess the wear and make a decision with confidence.
Almost 140 years after James Oliver traded gold for leather, the company has continued to evolve alongside Australia’s mining industry.
“We’ve been around for a long time, and we’re tried and tested – over the years we’ve proven time and time again we’re a brand people can trust,” Huggins said. “We want to support the industry by being a solutions provider for the footwear needs of Australia’s mines.”
One of those solutions is set to be launched next year in the form of expanding the company’s range of women’s work boots.
“We already have a comprehensive women’s safety footwear range, but we’re looking to offer a female counterpart to our AT 55 Series to offer female miners the very best in on-site foot protection,” Huggins said. “As more women enter the industry, we see the need to offer safety footwear designed for female feet, not just a scaled-down version of men’s boots.”
As the industry evolves, Huggins said Oliver Footwear will continue to make these kinds of strides.
“We’re always prepared to look into the specific needs of a site and innovate new developments and technologies,” he said.
“Our promise to the industry is to offer comfort, durability and performance – it’s the foundation of everything we do at Oliver Footwear and will continue to be, as the mining industry enters this new chapter.”
FOLLOWING THE 2024 GROSVENOR COAL MINE FIRE, SAFE TO WORK SAT DOWN WITH A STATE RESOURCES REGULATOR TO DISCUSS ELIMINATING SIMILAR RISKS IN THE FUTURE.
For most of July 2024, a fire blazed underground at Anglo American’s Grosvenor coal mine in Queensland, prompting one regulator to investigate the potential risk at other mines.
On June 29, gas ignited in the tail gate of the underground longwall at Grosvenor and all mine personnel were quickly evacuated. Efforts to put out the fire continued until July 25, when Anglo chief executive Duncan Wanblad confirmed it had been staunched.
Anglo immediately called in Resources Safety and Health Queensland (RSHQ) to investigate when the fire broke out, and RSHQ in turn notified the New South Wales Resources Regulator.
In response, the NSW Resources Regulator carried out an inspection program to assess the risk of similar incidents at underground coal mines in the state.
The Regulator said the implementation of planned assessment programs for mines and petroleum sites is a crucial element in an incidentprevention strategy.
“The Regulator carried out this inspection program with the purpose of assessing the status of risk-control management and incident mitigation to prevent an ignition event similar to the Queensland incident occurring in a NSW underground coal mine,” NSW Resources Regulator deputy chief inspector Dwaine Jones told Safe to Work.
“Safety management is a key fundamental in a high-risk mining environment, precautions can be taken to ensure worker safety.
“The Regulator is dedicated to ensuring mine operators are
doing everything they can to protect workers.”
Without detailed information on how the Grosvenor fire broke out, the Regulator considered the mines’ handling of ventilation, gas drainage, frictional ignition and spontaneous combustion, as well as the use of polymeric chemicals in underground coal mines, post-incident monitoring and emergency sealing.
“These assessments were undertaken between July and August 2024 and specifically targeted eight underground coal mines with longwall mining operations and methane present as a seam gas,” Jones said.
“The Regulator’s assessment reviewed ignition sources, ventilation and gas management controls and post-incident responses for mine monitoring and sealing.
“To ensure each site was being assessed in the same way, specific criteria questions were developed for a control documentation assessment [CDA] and a control implementation assessment [CIA] questionnaire review at each site.”
Of the eight mines investigated, all had appropriate controls and postincident monitoring, as well as good knowledge of their spontaneous combustion potential.
However, 43 of the 464 individual findings from the investigation required enforcement action, with a total 18 notices issued to seven mines in the program.
Of the areas investigated, the Regulator released recommendations for three key pinch points:
• Coal mine operators injecting polymerics in coal for strata support should consider the reaction temperature of the product in relation to the thermal runaway temperature of the in-situ coal
• Coal mine operators should review their plans for emergency sealing considering the sequence of sealing, potential for explosions, resistance of seals to an overpressure event and the maintenance of seals
• Post-incident monitoring arrangements should include tube bundle monitoring at strategic locations
As a result of the assessment program, there were 18 Work Health and Safety Act
The NSW Resources Regulator said the coal mines assessed were committed to working together.
Efforts to put out the 2024 Grosvenor coal mine fire included sealing the exits to cut off oxygen.
compliance notices issued to seven of the eight assessed coal mines. Some sites were issued multiple notices.
“A key finding was that all assessed mines had appropriate ventilation design systems for longwall operations,” Jones said.
“There were a variety of ventilation system techniques used to suit the individual circumstances.
“All coal mines assessed had existing risk-management systems in place to control and mitigate the potential for a gas explosion and proactive systems to respond in the event of a gas ignition.”
When it came time to undertake the targeted investigations, Jones said all coal mines involved were more than happy to undertake site assessments and responded appropriately to specific site enforcement notices.
“Proactive and responsive site management to prevent a gas ignition in an underground coal mine environment is crucial to maintaining a safe workplace for all workers,” he said.
“While it was encouraging to see all assessed mines had a good knowledge of the risks associated with gas ignition and mitigation controls and appropriate response actions, it is crucial that management systems are diligently reviewed for effective operational outcomes.”
A fire at any mine site is dangerous, but the nature of coal mines means operators need to take extra care to ensure workers are kept safe from the risk of uncontrolled fire or explosion.
Coal mine fires can blaze for months, years – even centuries – if left to burn. it is therefore critical that operators have a plan in place to stop fires before they can even start, and to have effective controls in place in the event that one does break out.
Thankfully, incidents like the fire at Grosvenor are rare, but it is still the duty coal miners to remain diligent every second of operation to eliminate the risk.
The NSW Resources Regulator’s report shows miners take this responsibility seriously and are more than willing to work with industry bodies to keep a lid on fires now and into the future.
As we reach the peak of the summer season, miners across Australia are in need of quality eye protection that keeps them safe not only on the ground, but also from the sun.
According to the Australian Cancer Council, exposure to UV radiation over long periods can result in serious damage including squamous cell cancers on the surface of the eye. And this is compounded by the fact Australian miners are at risk of eye injuries in their day-to-day duties.
Around 50,000 eye injuries are reported in Australia every year, according to Federal Government statutory authority Comcare. What’s more, eight per cent of all workplace injuries are related to eye damage,
with an estimated 60 per cent of all such injuries occurring in the mining, construction, agriculture and forestry industries.
Between the sun’s rays and the risks on the ground, protective eyewear is a must.
But traditional eye protection like safety glasses is often uncomfortable to wear, requiring constant adjustment lest a full day’s wear lead to pinching or headaches.
In addition, conventional safety glasses aren’t exactly known to be stylish, another factor that is unlikely to inspire effective use of personal protective equipment (PPE) over a long shift in the sun.
That’s why the creators of Navigator X are determined to change the game.
“Too often, we’d see people on work sites take a pair of safety glasses and find the closest mirror to see how they looked,” Safety Mate said. “It became clear that people wanted more than safety and performance –they wanted style, too.
“And you’d better believe we went for the trifecta: looks, performance and safety, all wrapped into one.”
Safety Mate teamed up with Riley Eyewear five years ago to deliver a solution to all of these issues with its Navigator range of safety glasses.
The companies worked together for more than a year on the range to ensure it ticked all the boxes.
Now, Safety Mate and Riley Eyewear are back with their latest range: Navigator X.
The range features anti-fog and anti-scratch capabilities thanks to Riley Eyewear’s FlowTec dual-lens coating, which protect the wearer’s eyes from some of the harshest industrial and hazardous environments.
This special coating also provides 100 per cent UVA and UVB coverage, ensuring miners have clear vision no matter how bright it gets, with each lens engineered to filter some of the highest energy wavelengths of visible light up to 400 nanometres.
The range is available in seven different lenses: clear, polarised, grey, LED, emerald revo, arctic blue revo, and the market-first HD. They will also soon be available in prescription.
Navigator X eyewear is designed to eliminate discomfort to pressure points on the head and face so workers can wear the glasses for prolonged periods without constant adjustments.
This is thanks to the range’s rubberised, non-slip nosepiece and
flexible side arms tips that sit gently but securely in place all day.
Navigator X glasses also feature a transparent frame and side shield for increased peripheral visibility and reduced risk from side impacts – a critical feature on a mine site, where optimum visibility is essential.
“For a long time, safety didn’t go hand-in-hand with looking and feeling good,” Safety Mate said. “We wanted to challenge that idea, so we got on with it and now offer some of the most cutting-edge, best-looking safety glasses in the industry.
“The range you see today is the result extensive research and development by specialist product designers and safety experts with decades of experience.
“In other words, it’s pretty damn good.”
Each pair of Navigator X glasses has been manufactured from ethically sourced bio-based materials, reducing carbon emissions during
the manufacturing process. Glasses in the Navigator X range are built to handle tough conditions – just like their wearers – and are designed to meet the world’s highest safety standards, including AS/NZS, EN166, ANSI Z87.1.
By wearing Navigator X glasses, workers can rest assured they’re protected by world-class engineering and design.
“Together, we pushed the boundaries of what safety eyewear could look like,” Safety Mate said. “We’re talking best-in-class manufacturing, zero compromise on safety, and a second-tonone attention to detail.
“This hunger for innovation continues to drive the company today.”
Safety Mate has raised the bar on what safety eyewear can be, and it’s far from finished.
The Navigator X range is proof that safety glasses can be as stylish as they are functional, offering a glimpse into the future where innovation, protection, and style converge to usher in a new era of safety eyewear.
Training helps to ensure employees understand their legal obligations.
THE WORKING AT HEIGHT ASSOCIATION BELIEVES EFFECTIVE TRAINING IS PERHAPS THE MOST IMPORTANT STEP IN KEEPING WORKERS SAFE.
Working at height is one of the most hazardous tasks facing people onsite – and not just in the mining sector.
According to data from Safe Work Australia, falling from a height was the second-largest contributor to workplace fatalities in 2023, a sobering statistic that underscores the need for comprehensive safety protocols.
In many countries, including Australia, workplace safety laws mandate that workers exposed to heights undergo appropriate training to ensure workers are competent. Compliance with these regulations is not just about avoiding fines or penalties; it’s about safeguarding lives.
Australia’s Work Health and Safety Act outlines stringent requirements for businesses to ensure workers are competent to perform high-risk tasks. Effective training helps to ensure employees understand these legal obligations and can apply safe work practices in the field.
Organisations like the Working at Height Association (WAHA) are dedicated to improving industry standards and promoting the importance of training in this highrisk practice. WAHA secretary and strategic problems manager Deborah Chick believes training is one of the most critical safety measures available.
“Working at height involves a complex array of hazards, from unstable surfaces and weather conditions to the misuse of
equipment,” Chick told Safe to Work. “Comprehensive training programs teach workers to identify these risks, assess potential dangers, and implement controls to mitigate them.
“With this knowledge, workers are better equipped to handle the unpredictable nature of working at height, minimising the likelihood of accidents.”
Chick said training for the effective use of personal protective equipment (PPE) is a cornerstone of working at height safely. Harnesses, lanyards, anchors and fall-arrest systems are critical for protecting workers from injury or death in case of a fall.
However, Chick emphasised the fact that PPE is only as effective as the user’s knowledge of how to use it properly.
“Training ensures that workers understand the types of PPE available, how to inspect their gear, and how to correctly wear and use it for maximum safety,” she said. “Regular refresher courses ensure that workers stay updated on new technologies and safety equipment.”
Training provides workers with the practical skills needed to perform tasks safely at height, and these courses often include hands-on practice in real-world scenarios, which boosts worker competence and confidence. When workers feel confident in their abilities, Chick said they are less likely to make errors that can lead to accidents.
“Proper training can transform a potentially hazardous job into a manageable, routine task by fostering a sense of professionalism and selfassurance in workers,” she said.
A well-trained workforce is a safer workforce. Studies show that companies with robust safety programs have fewer incidents and injuries compared to those that do not
encouraging workers to take responsibility for their own safety and that of their colleagues,” Chick said. “This proactive approach leads to fewer workplace accidents and injuries, resulting in better outcomes for both employees and employers.”
Preventing falls is always a top priority, but it is equally important to prepare for emergencies. In the event of an accident, a fast and effective response can be the difference between life and death.
Training workers in rescue operations helps to ensure they know how to react quickly, efficiently and safely in case of a fall. This training covers the use of equipment such as rescue kits and proper techniques for retrieving a fallen worker, minimising the time between an incident and medical intervention.
While investing in training programs might seem like an added expense, it can be a long-term costsaving measure.
“Injuries and fatalities due to falls from heights can lead to significant financial losses for businesses through medical costs, legal fees, insurance premiums and downtime,” Chick said.
“By reducing the likelihood of incidents, training can protect businesses from these financial risks, while also ensuring the wellbeing of their workforce.”
There are also immediate productivity gains as a result of a more competent, aware and effective workforce. The ability to navigate a space more efficiently can lead directly to safer and greater output.
“Training is essential to protect workers from the dangers of falls and ensure compliance with safety regulations,” Chick said.
“It helps in hazard recognition and proper use of PPE, and instils a culture of safety and preparedness.
“By investing in quality training programs, businesses can not only protect their employees but also foster a more productive and secure working environment.”
The emphasis on continuous learning and upskilling within the Australian mining sector is vital. As advancements in safety practices and technology continue to evolve, training is an ongoing necessity for all who work at height.
Known as Australia’s longestrunning mining event, AsiaPacific’s International Mining Exhibition (AIMEX) has a rich history of supporting industry trends, innovations and developments by bringing leading local and international mining suppliers and professionals under one roof.
As those in the industry look towards AIMEX 2025, they can expect a shake-up worthy of such a cuttingedge event.
A strong bid from the South Australian Government will see AIMEX make a new home in Adelaide for the next 10 years. Adding one of Australia’s premier mining events to its repertoire is the icing on the cake for a state strengthening its position as one of the fastest growing mining markets in the world, with the event set to generate more than $250 million for SA’s economy over the next decade.
“With our natural advantages and ingenuity, South Australia has the potential to lead the world in decarbonisation of critical minerals, including green steel and copper,” SA Premier Peter Malinauskas said.
“We have a compelling story to tell, and AIMEX being hosted in Adelaide for the next decade provides a strong platform to do just that.”
What’s more, AIMEX is now under the ownership of Prime Creative Media, enabling the event to provide the best possible showcase for the technology, equipment and services empowering the next generation of mining and exploration.
Prime Creative Media general manager of events Siobhan Rocks said AIMEX’s move to SA was made based on exhibitor and partner feedback, with support from key mining players operating in the state.
“We’re maintaining AIMEX’s global reputation as a leading mining event in the Asia-Pacific region,” Rocks said.
“For the past 40 years, AIMEX has taken place in New South Wales, a heavy coal mining region.
“As the world decarbonises, we felt it was important to have AIMEX’s new location reflect a change in industry – South Australia has a progressive and forward-thinking mining sector, as well as the green resources needed to build critical infrastructure.”
AIMEX 2025 will feature a freeto-attend conference full of industry insights, case studies and thought leaders discussing current and future mining developments.
Businesses will have the opportunity to promote their emerging technologies at the Transformative Technology Pavilion, and leading miners can showcase their achievements while promoting themselves as an employer of choice at the Mining Pavilion.
Recent technological advancements will also be highlighted at AIMEX’s Research and Development Hub.
The AIMEX ‘meet the buyer’ program is also set to return, connecting mining companies with suppliers and helping decisionmakers find the best solutions for their needs.
From welcome drinks to exhibitor functions, AIMEX 2025 will offer endless opportunities for visitors and exhibitors from around the world to connect face-to-face.
AIMEX 2025 will take place at the Adelaide Showgrounds from September 23–25.
Edith Cowan University’s Mental Awareness, Respect and Safety (MARS) Centre has become a mainstay in the mining industry.
Each year, the centre partners with a handful of Australia’s most well-known miners to promote mentally healthy workplaces, build a culture of safety and respect, and prepare for workplace safety in future mining.
In November 2024, Liontown Resources was one of these partners looking to improve the mental health and wellbeing of its fly-in, fly-out (FIFO) workforce.
While the broader FIFO workforce is an integral part of the mining sector, it is also the most likely to experience psychological distress.
A 2018 study from the Centre for Transformative Work Design found that one third of FIFO workers reported experiencing high or very high psychological distress – and that number is continuing to climb.
A 2024 study by the University of Western Australia and MATES in Construction showed people in FIFO roles were at a significantly greater risk of psychological distress – a sobering 2.4 per cent of FIFO workers had attempted suicide in the previous 12 months, compared to 0.3 per cent of the general population.
Recognising that something needs to change, Liontown took the opportunity to partner with the MARS Centre.
Between March and April 2024, researchers explored how a sense of team belonging can influence the wellbeing of workers on remote mine sites, including those at Liontown’s Kathleen Valley lithium operation in WA.
The researchers collected survey data from 72 Liontown employees and contractors that provided valuable insights into overall wellbeing and team dynamics.
Key findings revealed that the Kathleen Valley community reported
psychological distress levels consistent with the mining industry but higher than the general Australian population, reinforcing the need to be proactive in supporting the mental health of FIFO workers.
Positively, 72 per cent of respondents reported feeling moderate to high belongingness at Kathleen Valley, which was correlated to better wellbeing.
Liontown work health and safety manager Hayden Spencer said the results demonstrated the impact of prioritising supportive team environments.
“It was great to get involved in research that concentrated on the positives to working away,” Spencer said. “For some people, their team is the reason they go to work and they get to build friendships that outlast the mine life. However, we still have a lot of work to do in this space and will ensure that we include our contract partners in this as much as possible.”
enhance the wellbeing of its community using evidence-based recommendations tailored to its operation, engaging with its contractors to address their unique needs, and providing training for leaders to support their teams.
The MARS Centre is also working to create a standardised survey tool for the mining industry to measure psychosocial safety, providing recommended actions based on the scores.
The tool is expected to be rolled out across the mining sector this year.
Liontown’s partnership coincided with the MARS Centre’s first research showcase, held in Perth in November.
The showcase featured a number of research projects around emerging technologies, critical safety improvements, the wellbeing of FIFO miners, advancing diversity and inclusion in the mining industry, and the impact of welding fumes on workers.
is an opportunity to share some of the exciting work with are doing with industry to support a culture of safety and respect and foster mentally healthy workplaces,” MARS Centre deputy director Kate Blackwood said.
Emerging mining technologies were a particular focus of the showcase.
“The true value of technological advancements hinges on effectively managing and implementing workplace changes,” Edith Cowan University senior lecturer Eden Li said.
“Adopting human-centred principles and regularly evaluating practices allows organisations to design workplaces where technology enhances workers’ wellbeing rather than detracting from it.”
Research conducted by Dr Judy Lundy, Dr Uma Jogulu and Edith Cowan University student Amy Chapple showcased how building inclusive and diverse workplaces could positively influence respectful
and healthy relationships and workplace relationships.
The study evaluated how a specially designed diversity and inclusion (D&I) capability maturity model could assist the resources industry to develop a culture geared more toward inclusion.
“Our research team have been thrilled with the openness of research participants to share their insights to inform current state assessments and to use this as a baseline for improvement,” Lundy said.
“We’ve found the assessment tool and process have been extremely valuable in raising awareness of the importance of D&I and the D&I concepts and to help provide a line of sight of where to go next in building capability maturity.”
In a responding to recent legislative changes that extend the duty of care for organisations to protect workers from psychological harm, the MARS Centre is also working to
co-design interventions that build leaders’ capabilities in the practice of psychosocial risk management.
This research includes the design, implementation and evaluation of a psychosocial safety climate intervention to promote healthy work and wellbeing at a systems level.
“A further study tests the efficacy of an intervention that enhances organisational capability in addressing workplace bullying and incivility in the sector as an organisational priority addressed proactively, rather than an interpersonal issue dealt with reactively,” Edith Cowan University professor Tim Bentley said.
“Our MARS researchers are also working with mining organisations to enhance organisational capability in diversity and inclusion, towards building a culture of respect and advancing critical outcomes, such as diversity management maturity and the performance and retention of sector staff.”
The MARS Centre continues to be proactive in its research as it seeks to contribute to the goal of creating a mentally healthy FIFO sector.
“Mining is a great industry, and we want to foster an environment based
on healthy, sustainable work where people from all backgrounds can grow and thrive,” Bentley said.
“If we can help contribute to that by helping to lift work health and safety capabilities in the sector, and helping people tackle the challenges around managing psychosocial hazards, then I think the industry’s future will look so much brighter.
“It’s important to look across the broader system and see how different factors interact to produce negative outcomes that we sometimes see in the workplace.
“Conversations around mental health and issues facing people from diverse backgrounds looking to enter the industry need to be at the fore.”
As Australia’s longest running mining show, Asia-Pacific’s International Mining Exhibition (AIMEX) has a long, established history of showcasing and supporting the latest trends and developments in the industry.
AIMEX is relocating and will call South Australia home for the next 10 years, following market feedback and strong support from the local government and key mining players.
The move marks an exciting new chapter for the event and the region’s resource sector, with the state leading the way in future-focused mining.
AIMEX offers unparalleled opportunities to connect with Australia’s largest community of mining suppliers and professionals in an environment that stimulates innovation and collaboration.
Acquisitions, new innovations and expansions were just some of the milestones ticked off mine technology provider Hexagon’s 2024 bucket list.
Known for its cutting-edge mining technologies including artificial intelligence (AI), collision avoidance and mine planning, Hexagon is one of the industry’s most ambitious pioneers when it comes to mine efficiency and safety.
Hexagon’s Mining division celebrates a decade of operation in February this year. While the industry giant tends to focus on automation technologies powering the future of mining, the anniversary is a reminder that it has a rich, historical legacy of products that have changed how mining is done.
Hexagon MinePlan, for example, dates all the way back to 1970 when Dr Fred Banfield, widely considered the godfather of mine planning, began applying computers to analyse mine plans.
Jon Olson, the architect of the world’s first fleet management system in 1981, also developed the foundational elements of Hexagon’s fleet management system.
SAFEmine, with its collision avoidance system, was among the first mining-related acquisitions by Hexagon, followed soon after by the acquisition of fatigue monitoring specialists Guardvant.
Hexagon’s continued development of these systems for operator alertness, personnel protection and vehicle intervention has given its customers full visibility on issues unseen by siloed solutions.
With the mining industry’s pace of progress reaching a stratospheric trajectory, Hexagon is continually
challenged not just to innovate, but to ensure its systems work together to offer miners the best possible support. The company has continuously embraced that challenge since launching its mining business 10 years ago.
As a new year gets underway, Safe to Work caught up with Hexagon’s Mining division executive vice president Dave Goddard to talk transitions, trends and the future of mining.
What movements did Hexagon make in 2024 that have set the company up for success in 2025?
Hexagon’s Mining division completed a year of firsts in 2024.
We released an AI-powered 3D blast movement solution, deployed innovative underground safety systems and introduced 4D radar in our collision avoidance solution.
We helped Ma’aden create the Middle East’s first digital mine and acquired indurad, a leader in industrial radar systems.
Elsewhere, we brought safety insights to market, as well as upgrades and enhancements to our Collision Avoidance System (CAS) and Operator Alertness System (OAS).
In the mine planning realm, we debuted AI-driven blast movement monitoring with Hexagon Blast Movement Intelligence, and within fleet management, we released an updated version of Hexagon OP Pro with fleet analytics capabilities.
Through our earlier acquisition of HARD-LINE, we introduced new applications of teleoperations beyond
underground and across the mine, for example by enabling Brazil’s first teleoperated eight-by-four mining trucks.
What trends do you see emerging in the industry that will play out across 2025?
At a macro level, we expect miners to be cautious with new investments and continue to find creative ways to extract value from their existing assets.
As average grades decrease and talent continues its scarcity, Hexagon’s technologies and solutions become even more critical to improving production efficiency and enhancing safety.
Can you tell us about Hexagon’s acquisition of indurad?
The acquisition of indurad and its autonomous haulage subsidiary
xtonomy was an important step towards realising Hexagon’s vision of fully connected and integrated mine workflows.
indurad’s unique offering of one-, two- and three-dimensional radars and real-time location systems solutions expands our portfolio in collision avoidance, positioning, digitalisation, process optimisation and automation.
indurad’s proven ability to understand unique problems that customers are trying to solve from pit to port, complemented with its radar expertise, enables digital twins that are otherwise next to impossible to achieve with other sensors.
How will this acquisition enable Hexagon to continue driving safety in Australian mines?
The indurad acquisition is part of a bigger safety journey Hexagon is on with its customers.
Technology is just one layer of mine safety. Change management and data insights are also important layers.
Neither Hexagon’s CAS nor OAS stand alone as 100 per cent effective. Even when both solutions are combined, operators must still be engaged and re-engaged in a cycle of continuous improvement.
That’s the power of safety layers and navigating the EMESRT (Earth Moving Equipment Safety Round Table) Levels 1 to 9 as a cyclical process.
Autonomy in mining is more than just deploying the latest sensors and machine learning algorithms. It’s about orchestrating the fleet and understanding the broader mission and daily production goal.
Each truck’s payload, its interaction with other equipment and its ultimate destination are all critical.
Hexagon’s solutions for safety, productivity and autonomy will continue to ensure that every truck arrives at the right place, at the right time, with the right payload.
What other key acquisitions and technologies are setting the company up for a successful 2025?
Besides indurad, the integration of HARD-LINE highlights and further reinforces our position as the most comprehensive provider of solutions that enable customers to become increasingly connected and autonomous.
For example, customers using Hexagon CAS can now easily enhance that solution by integrating TeleOp and/or the radio remote control systems developed by HARD-LINE for another layer of protection.
This will see greater protection for miners in areas where operators may inadvertently get too close to a remotely operated machine. CAS is deployed in more than 100 mine sites worldwide, including open-pit and underground operations.
What is Hexagon’s overall outlook on mine safety in 2025?
Hexagon began 2025 with 65,000 CAS units deployed, the largest global install base on the market.
Our customers can expect an integrated safety ecosystem of solutions that unify collision avoidance, operator alertness and intervention systems.
Beyond this cohesive safety and productivity platform is a missioncentric approach to autonomy that ensures vehicles don’t just operate safely but contribute to optimised production by managing payloads,
traffic rules and destination timing. Our solutions are OEM (original equipment manufacturer) agnostic and flexible enough to adapt to mixed fleets and varied site conditions while maintaining consistent safety and productivity standards.
How will Hexagon continue to support the industry in 2025?
Safety is central to Hexagon’s ethos.
Hexagon is focused on providing the flexibility for our customers to use OEM-agnostic solutions while they navigate the journey to autonomous operation, all the while optimising their safety and productivity with data insights every step of the way.
More broadly, our solutions are actively used in North and South America, Australia, Africa and other major mining geographies.
Each of these regions presents unique operational challenges, from safety and productivity to regulatory requirements.
By leveraging our global expertise and local knowledge, Hexagon can tailor solutions to deliver optimal outcomes and make a positive impact wherever we’re engaged with customers.
G5-03 SERIES INCLUDES THREE ALL-NEW WELDING HELMET PLATFORMS COMBINING SIGNATURE SPEEDGLAS FEATURES WITH NEW TECHNOLOGY.
Trust in a brand cannot be built overnight. It takes years to become known and even longer to be trusted.
In 1981, 3M Speedglas released the first ever auto-darkening welding helmet and has aimed to consistently set the benchmark ever since. This has culminated in Speedglas Generation 5 (G5), which represents the pinnacle in welding helmet innovation and leads the pack in terms of vision, comfort, safety and performance.
Speedglas G5-03 is the latest addition to the series, following the precedent set by the heavyduty Speedglas G5-01 and curved Speedglas G5-02.
At the forefront of this new G5-03 range is the 3M Speedglas G503 Pro Air Welding Helmet, a slim and lightweight respiratory helmet featuring the latest technology from 3M Speedglas.
The G5-03 Pro Air is over 10 per cent lighter than the Speedglas G501 welding helmet and has a lower starting price point.
The G5-03 Pro Air is a fixed-front welding helmet; however, new TAP technology, Speedglas True-View optics and an optional task light can combine to optimise the helmet for grinding even in low light conditions.
The unique TAP function enables the welder to seamlessly switch between weld and grind modes
simply by tapping on the outside of the helmet, even with a gloved hand.
With an expansive welding lens viewing area, peripheral side windows and impressive optical quality, the G5-03 Pro Air gives welders exceptional views, according to 3M Speedglas.
Users have a choice between three unique welding lens options:
• G5 -03VC (73x109mm): Shades 3/5, 8-14, TAP technology, variable dark state colours
• G5 -03TW (73x109mm): Shades 2.5/5, 8-13, TAP technology
• G5-03NC (55x107mm): Shades 3/5, 8-12
What’s more, the G5-03 Pro Air Welding Helmet comes standard
with the heavy duty Adflo powered air purifying respirator (PAPR) featuring a 12-hour battery runtime for continuous respiratory protection during long shifts.
The Adflo PAPR delivers a constant flow of clean air directly into the breathing zone, while welders can adjust the movement and direction of this airflow within the helmet via climate control.
The G5-03 Pro Air also empowers welders to configure and customise their protection with a range of extended head and neck coverage options and optional accessories to offer a more secure and comfortable welding experience.
A heavy-duty Adflo PAPR backpack is also available to provide improved comfort and balance during extended welding applications in hard-wearing environments.
The Speedglas G5-03 Pro Air with Adflo PAPR has been designed to minimise hazards and maximise performance for professional welders – and the same can be said for its G5-03 counterparts.
The first of these is the Speedglas G5-03 Pro Welding Helmet, which aims to set a new standard for nonrespiratory welding helmets.
Many of the leading benefits showcased in the G5-03 Pro Air carry
over to the G5-03 Pro, including TAP technology, True-View, side windows, configurable head and neck coverage and the optional task light. The same three welding lens variants are also available.
The Speedglas G5-03 Pro is also designed to allow welders to customise the fit of their helmet to their specific preference. To achieve this, the ergonomic head harness boasts six points of adjustment for even weight distribution and optimal comfort.
The result of these combined benefits is a highly versatile welding helmet that eliminates any need for compromise when it comes to comfort, performance or safety.
For those who have been holding out for a premium helmet at a budgetfriendly price point, the Speedglas G5-03E Welding Helmet is a slim, lightweight, comfortable solution with precision True-View optics for a brighter, more realistic view of welds.
The G5-03E Welding Helmet delivers quality and comfort at an affordable price, featuring a large 55x107mm welding lens viewing area with shade three grind mode, shade five cut mode, the most commonly used dark shades (8-12) and arc detection down to one ampere.
For those new to Speedglas technology, the G5-03E helmet serves as the perfect entry point into one of the world’s leading brands in welder’s personal protective equipment.
ustralian miners are no stranger to the sun. With many of the country’s mines located in some of its hottest, sunniest places, surface miners are at particular risk.
According to the Cancer Council, around two thirds of Australians will be diagnosed with some form of skin cancer during their lifetime. Skin cancer accounts for around 80 per cent of all newly diagnosed cancers, and the majority of those – an estimated 95 per cent – are caused by sun exposure.
But skin cancer isn’t what led young Queensland electrician Sean Conneely to develop his sun-blocking solution.
“I was a domestic electrician for many years, which involved a lot of switchboard upgrades,” Conneely told Safe to Work. “You could be out in the sun for hours, sometimes all day, with no option but to stay out there
In 2020, following one too many hot days in the Queensland sun, Conneely decided enough was enough. After a few initial prototypes made in the downstairs car park of his apartment building, Conneely developed the first iteration of what would go on to become one of Australia’s bestselling sun-protection solutions, the Trade Shade.
A portable sun protection solution, the Trade Shade combines a strong magnetic base with an adjustable umbrella holder. The magnets are encased in rubber to ensure any surface remains scratch-free.
It was during his initial research for the Trade Shade that Conneely discovered just how dangerous exposure to the sun was for workers
“If you don’t get it early, skin cancer can turn into this big thing that it doesn’t need to,” he said. “Tradies are
in the sun all the time, so they can often neglect it, but we need to make it less taboo to go get a skin check and prioritise looking after ourselves working outdoors.”
Conneely himself had a close call when he had a suspicious spot removed during a skin check. The spot was benign, but the sun safety seed was already planted.
“The first prototype was developed from parts from the local hardware shop and involved some late nights cutting steel pipe with an angle grinder after I finished work for the day,” Conneely said.
“I started using it at work and a few of my mates saw it and wanted one for themselves, and everything just snowballed from there.”
Conneely spent the next six months perfecting his design, teaching himself how to develop a website, building a fulfillment process and getting comfortable in front of the camera for his growing social media platform, all while continuing his full-time job as an electrician.
“The Trade Shade as it is today is compatible with most umbrellas on the market,” Conneely said. “It has an adjustable mechanism that allows the holder to be continually adjusted to protect workers as the sun moves, or from any direction rain might be coming in.”
As word got out, orders for the Trade Shade continued to grow. With mates working at mines across Queensland and Western Australia taking Conneely’s innovation to site, it wasn’t long before those orders started to come from the state’s mining majors.
“It spread like wildfire,” Conneely said. “The only real competition out there is the gazebo, which is bulky to carry around and time consuming to set up. It’s not really practical on
a busy mine site where you’re going from job to job and have limited space in your service vehicle.
until late into the night, and rinse and repeat the next day.”
For Conneely, it’s all worth it to know he’s keeping workers protected from the harsh Australian sun.
a few seconds to stick it to the closest metallic surface and get to work with hands-free protection from the sun.”
After two years working on the Trade Shade, Conneely went parttime on the tools to focus more energy on the exploding business, finally leaving altogether in December last year.
“I was getting up at five in the morning for work, then getting home at three or four in the afternoon and packaging up orders and racing to the post office before it closed,” Conneely said. “Then I would get to work on the website and answering emails
One mine in particular has seen great success in using the Trade Shade.
“The Trade Shade has been a gamechanger in enhancing sun safety across our mining projects,” Queensland project manager R. Doo said. “It’s durable, easy-to-install design provides crucial shade coverage in areas where workers previously had limited protection from the harsh sun.
“By reducing direct UV exposure, the Trade Shade has significantly improved workplace safety, comfort and morale.
“We’ve noticed a decrease in heat-related fatigue and better compliance with sun safety protocols, ultimately contributing to increased productivity and worker wellbeing.
“If you’re looking for a reliable, longlasting solution to protect your team and meet sun safety requirements, the Trade Shade is a must-have investment. Its robust construction, adaptability to any site, and ability to withstand tough conditions make it the ideal choice for industries like ours.”
With more developments in the pipeline, Conneely is looking to the future. And with stockists in every Australian state and territory, he has plans to take the Trade Shade worldwide.
“We want to get sun protection to as many mine workers and tradies across the world as possible, not just Aussies,” he said. “Our mission is to spread the word about staying safe in the sun and the importance of looking after yourself while you work.”
FOOT HEALTH MIGHT NOT SOUND LIKE A MINER’S TOP PRIORITY, BUT PODIATRIST
AMANDA TAYLOR SAID IT’S THE FOUNDATION OF A LONG CAREER.
Left unchecked, foot issues can cause long-term issues.
Anyone who has ever worked a 12-hour shift will tell you all they can think about at the end is getting off their feet.
But come the next morning, cramped toes and aching arches are all but forgotten as the demands of the day dawn again.
Maybe it’s because busy miners are too run off their feet to really think about them longer than it takes to put on a pair of socks, but feet have been overlooked for too long.
Wodonga Podiatry podiatrist Amanda Taylor agrees. She told Safe to Work that strained lower limbs, ankles and feet can result in a variety of foot problems beyond general aches and pains, including serious conditions like plantar heel pain, joint inflammation, tendinopathies and bone stress fractures.
“Standing for long periods can also affect the blood circulation, leading to swollen legs, varicose veins, or worse, deep vein thrombosis (DVT),” Taylor said.
“Miners often face these circulatory issues because they lack the ability to move around frequently enough to stimulate healthy blood flow, and standing on hard surfaces all day can put extra pressure on veins.”
Stringent work safety laws require miners to wear protective safety footwear accredited to Australian standards.
Examples of safety features include steel toe caps or mid and sole properties that insulate against environmental hazards such as temperature and/or high voltage electricity.
But Taylor said such design properties make the footwear heavy and can lead to fatigue.
“As no one foot is the same, fit issues are common and ill-fitting footwear often causes or exacerbates foot and lower limb pathologies,” she said. “Pressure on nails can cause ingrown toenails or nail infections and high pressure on joints can cause callous or corns.”
So what can miners do? Taylor is confident there’s a lot more to be done.
To begin with, miners should ensure their safety footwear fits properly.
“I know it sounds logical but so often we think we are a particular size
in a shoe so we default to that when purchasing or requesting footwear,” Taylor said. “But footwear sizes are not regulated across footwear brands.
“Don’t assume your size – or worse – have someone assume it for you.”
Taylor said regular stretching and exercise can improve the load tolerance of our joints and tendons.
“Strengthening needs to be gradual – don’t rush in and overdo it,” she said. “It’s best to have a heath professional or your podiatrist guide you with your foot and lower limb exercises.”
Standing still for long periods can lead to poor circulation and muscle fatigue.
“Take short breaks to walk around, stretch, or change posture frequently to keep blood flowing and reduce pressure on the feet,” Taylor said. “Even small movements like shifting weight from one foot to the other can make a difference.”
Keeping the feet clean and dry can prevent fungal and bacterial infections, blisters and odour.
It’s also important to change socks regularly and even consider moisturewicking fabrics to prevent dampness.
Adding insoles or orthodics can help to distribute weight more evenly across the feet.
Insoles designed for high-impact or heavy-duty use can reduce pressure on the soles and joints, improving comfort over long shifts.
Believe it or not, maintaining proper hydration and nutrition is essential for foot health.
“Dehydration can worsen circulation problems and increase muscle cramps and fatigue,” Taylor said. “A diet rich in vitamins and minerals like calcium, magnesium and potassium can support foot health.”
Taylor said there’s a key message miners shouldn’t overlook:
“Inspect your feet daily,” she said. “Look at the integrity and general health of your skin. Check between your toes. Look for pressure areas or skin lesions, changes in joints.
“Seek help early if you have pain or notice something new or different.”
If there are any concerns or anything out of the ordinary, Taylor said it’s essential to speak to a podiatrist as soon as possible.
“They are qualified to identify health conditions that place your feet at risk and can help prevent complications,” she said. “They are trained to diagnose and manage numerous conditions that can affect the health of your feet including joint and soft tissue problems, skin and nail conditions and problems with your gait.”
While many may take their feet for granted, it’s far better to address a foot-related issue before it sweeps you off your feet – and not in a good way.
By getting on the front foot of feet health, miners can rest easy knowing they have two strong foundations set for a long career free from tired, aching feet.
Legionnaires’ disease is a severe form of pneumonia that can be deadly.
THE AUSTRALIAN INSTITUTE OF OCCUPATIONAL HYGIENISTS SAID THERE ARE A RANGE OF ACTIONS MINERS CAN TAKE TO COMBAT OUTBREAKS OF LEGIONNAIRES’ DISEASE ON-SITE.
While silicosis is currently at the forefront of people’s minds when it comes to diseases of which miners need to be aware, there are common health risks to which no industry is immune.
Legionnaires’ disease is known for resurfacing in the news every so often, but it can be more serious than an occasional nuisance.
A severe form of pneumonia, Legionnaires’ can be deadly if left untreated. In Australia, there are an average of 400 reported cases of the disease every year.
The Australian Institute of Occupational Hygienists (AIOH) is working to empower miners with the tools they need to stop legionella bacteria becoming a problem in the first place.
HOW ARE MINERS AT RISK?
Legionella – the bacteria that causes Legionnaires’ – is found naturally in soil, freshwater and even compost and potting mix. In the right conditions, the bacteria can blossom in potable water storage tanks, water distribution pipework, cooling towers and water recirculation systems where nutrient sources like dust, dirt and algae can support its growth. In water temperatures between 20–50°C, legionella can bloom basically anywhere there is standing moisture.
All up, that means lots of places on a mine site.
“Water is used in many different ways in a mining environment, so there are plenty of opportunities for legionella bacteria to grow to high numbers,” principal occupational hygienist Nicola Power
told Safe to Work on behalf of the AIOH.
“The most common source of legionella bacteria exposure is contaminated or poorly maintained cooling towers, because the exposure pathway is from mist, and bacteria can travel long distances in the air. There are many reported cases of contamination each year, and multiple cases of Legionnaires’ disease in miners have been reported.”
But cooling towers are not the only source of contamination.
An underground miner in Western Australia contracted Legionnaires’ disease in 2020 from an underground wash bay where the miner had used high-pressure water-blasting equipment to clean heavy machinery.
According to the WA Government’s notifiable infectious disease
dashboard, men are 3.1 times more at risk of contracting Legionnaires’. There are also an average of 72 cases reported in WA every year, despite the disease being difficult to diagnose.
Water reticulation systems, as well as recycled and natural source waters used for dust-suppression, drilling, vehicle wash-down and irrigation, can all present an exposure risk if not properly managed.
Sprinkler systems, safety showers and fire water systems are often overlooked because they’re rarely used, giving bacteria an opportunity to grow.
Even areas like stagnant bodies of water, particularly underground, can present a risk if conditions are right.
“One of the greatest risks for miners, believe it or not, is actually onsite showers, evaporative air-cooling systems and misting machines, which inherently provide a lovely, warm environment for bacteria,” Power said. “In mining camps, plumbing is often above-ground, where hot weather can create the perfect temperature for legionella bacteria to thrive.
“The other big risk factor is processes that create water mist, like dust suppression, drill sprays and high-pressure washing.”
While regulation will vary from state to state, all mines in Australia are required to have management plans in place for preventing risk to health.
Power said all mines should include routine treatment for, and monitoring of legionella in their site emergency response plan or water management plan.
“To prevent outbreaks of Legionnaires’ disease, all water sources on-site need to be managed,” she said. “Good system design and maintenance are the most important factors in preventing legionella growth.”
Power also warned against assuming site water sampling will be enough.
“Water sampling and analysis will take seven to 10 days to detect and
report legionella bacteria,” she said. “This is typically too late to respond to any risk.”
Power said responses to the detection of legionella should include:
• interim exposure controls, such as equipment shutdown, exclusion zones or use of respiratory protective equipment (RPE)
• investigation of the source
• identifying factors that contributed to its growth
• assessing whether controls such as cleaning and maintenance have failed
• determining the extent of affected systems
• taking action to prevent future growth, such as cleaning to remove bacteria on surfaces and in biofilm, and disinfection.
Occupational hygienists like Power can help with identifying such risks and help mines determine suitable controls to prevent the growth of legionella, as well as undertaking water monitoring.
As part of these controls, miners should first identify all sources of onsite water mists and aerosols and try to design systems that don’t create
an environment in which bacteria will thrive.
If such systems are unable to be designed out, then miners should assess exposure levels of mists and aerosols and review risk management strategies for the tasks and activities that generate them. These strategies may include using alternate, clean water sources, keeping water moving and at safe temperatures and using extraction ventilation.
Power said water treatment plant operators should be well trained and resourced with a strategy in place to monitor for the bacteria.
“This includes carrying out appropriate planned maintenance, remedial treatment or corrective actions to prevent legionella as necessary – chlorinated water is not immune to legionella bacteria growth so the key to prevention is ‘CCC’ – clean, cool and constantly moving water in your water pipes and tanks,” she said.
By adopting these processes and controls and ensuring they are diligently implemented, mines can stay on track to keeping their sites legionella-free.
After a whirlwind two-day event in July 2024, the stage has once again been set for the PNG Industrial and Mining Resources Exhibition and Conference (PNG Expo) to shine a light on the resources sector in 2025.
Due to be held at the Stanley Hotel in Port Moresby from 2–3 July, the 2025 PNG Expo is set to light up the stage like never before.
“We came away from the 2024 PNG Expo with some key lessons that we can apply to our 2025 program,” Prime Creative Media general manager of events Siobhan Rocks said.
“We’re looking forward to welcoming more attendees, exhibitors and speakers to the Stanley Hotel in July 2025.”
Like last year, the 2025 PNG Expo will feature several key networking events that attendees can use to get to know each other. These include the welcome drinks and gala dinner.
“Both of these events sold out quickly last year, as everyone was eager to connect and catch up before the conference and exhibition began,” Rocks said.
“The dinner at the end of day one was a good opportunity to speak about the presentations from the day and learn what everyone was looking forward to as we entered day two.”
TriCab, a silver sponsor of the 2024 event, has renewed its support for 2025, reflecting its premiumquality products with a premiumquality event.
“At TriCab we pride ourselves on supplying premium, high-performance flexible cables and accessories that reflect our values of innovation and quality,” TriCab Queensland state manager Shane Plumridge said.
“Providing engineered cable solutions, which save our customers
time and cost, is where we make our difference. At TriCab, we listen and respond to a range of customer needs, remaining innovative in our operations to ensure we can meet demands of all markets, existing and emerging.”
Plumridge said the company was proud to be a silver sponsor at the 2024 event, where it was able to
showcase its products and people to attendees.
“The ability to see people from the local area in the one place all with the same values, who were looking for new and innovative products and services, was a tribute to the organisers,” Plumridge said.
“It gave TriCab the ability to expose our vision of demonstrating our capabilities in the growing PNG sector.”
Plumridge is encouraging others to attend the 2025 event.
“Events like the PNG Expo are vital in bringing like-minded consumers and suppliers together in the one space, where it is mutually beneficial to all parties in a relaxed and safe environment.”
The 2025 PNG Industrial and Mining Resources Exhibition and Conference will be held at the Stanley Hotel in Port Moresby from 2–3 July.
At Body Armour, we have researched all of our ingredients, including the colours in our formulations, to ensure the utmost safety of our consumers purposefully avoiding questionable colours to help optimise performance.
Discover the natural sweetness of thaumatin, a superior alternative to sucralose Sourced from the Katemfe fruit, thaumatin is a protein-based sweetener that delivers an intense,
Our formulation provides a combination of Sodium, Potassium, Magnesium, Calcium and Chloride to replace electrolytes lost in sweat and ensure maximum performance onsite
Synergistic Ingredients
Laden with synergistic ingredients like Vitamins B, C and D along with Sea Buckthorn, L-Glutamine and L-Theanine, a nootropic to help increase mental sharpness and alleviate muscle fatigue