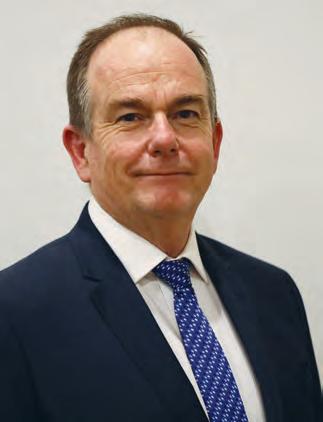
10 minute read
QLD mine trial encourages safer practices
from STW Jul 2021
Q&A QLD coal mine trial encourages safer practices
EACH YEAR, RESOURCES SAFETY AND HEALTH QUEENSLAND CONDUCTS A SIMULATED EMERGENCY EXERCISE AT ONE OF THE STATE’S MINES. QUEENSLAND CHIEF INSPECTOR OF COAL MINES PETER NEWMAN REVIEWS THE LEARNINGS FROM THE SIMULATION AT ANGLO AMERICAN’S MORANBAH NORTH MINE IN 2020.
Knowing what to do during a hazardous situation is crucial to avoiding disaster.
In the mining industry, hands-on learning approaches are being encouraged to ensure workers are prepared to follow the correct procedures and protocol.
Resources Safety and Health Queensland (RSHQ), the state’s independent regulator of worker safety and health in the mining, quarrying, petroleum, gas and explosives industries, has recognised the importance of trialling disaster situations at mine sites.
RSHQ organises simulated emergency exercises at a Queensland underground coal mine site each year, bringing its findings to the rest of the industry to encourage improvements to the health and safety protocol that are followed by mine operators and coal mine workers.
In 2020, a simulation at the Moranbah North coal mine involved an underground loader fire, followed by a fan stoppage that led to a mine evacuation.
A coal mine worker remained missing underground when the evacuation was completed, prompting a mine re-entry by Queensland Mines Rescue.
RSHQ Chief Inspector of Coal Mines Peter Newman tells Safe to Work about the purpose and learnings of the exercise.
What benefits do emergency mine exercises have over other methods of establishing safety-related industry learnings?
One of the key learnings out of the Moura No.2 1994 disaster was that level one exercises were to be run in underground mines each year with level two exercises being run across surface and underground mines each year.
As with level one exercises, the learnings from those other level two exercises are to be shared with the industry.
So why is it different to other safety related industry learnings? It’s validating the learnings being implemented at one underground coal mine each year, through a coordinated external agency validating the mine’s emergency response and management capability.
It’s use of an independent party to test the emergency response capabilities of an organisation as close as possible to an actual disaster condition, providing real-life testing of the mine’s capacity and capability to respond and ensure there is no further loss of life with the incident.
There are safety alert bulletins, seminars and conferences that cover industry learnings, but the level one emergency exercise validates whether learnings from past exercises have been implemented.
The cross-industry stakeholders that we use in the planning and assessment of the exercise, which are people outside of the mine being tested, take their learnings back through to their respective organisations.
Queensland chief inspector of coal mines Peter Newman.
One of the recommendations in the December 2020 report is to enhance communication protocols for mine workers. Could advancements in wearable technology make this easier for mine workers to adopt?
I suppose there’s several new technologies when it comes to communications that have been introduced into mines to enhance those communications protocols.
For a long time in the industry, Wi-Fi and fibre has been available in surface
mines, but now it’s very much being used in underground mines and that certainly enhances the communication networks now available.
It has the ability to introduce more advanced wearable technologies where previously those other technologies weren’t able to be used because the communication platform wasn’t there.
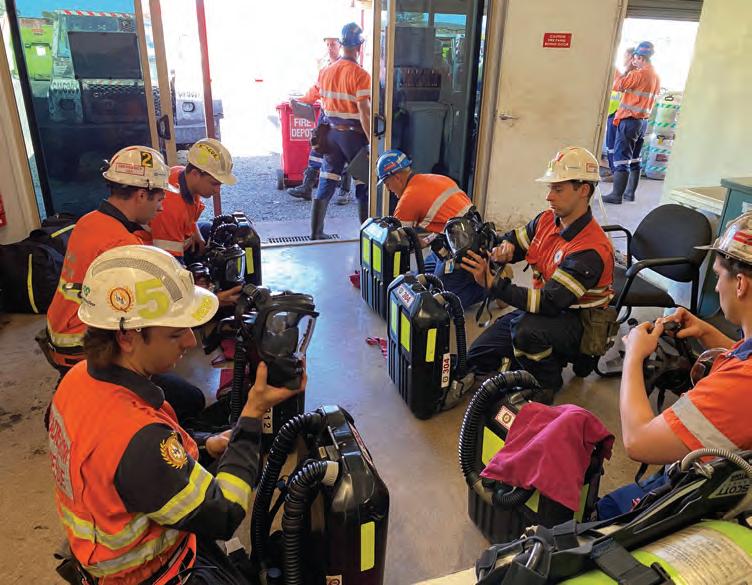
What sort of safety improvements are being encouraged across Queensland’s coal mines?
There are obviously numerous safety improvements being organisationally based or mine-site based.
There are those resulting from the learnings from incidents and near misses, reinforcing the importance of HPI reporting to the regulator so that those learnings can be shared across the industry.
The Brady Report in December 2019 reviewed the learnings from the last 20 years of fatalities and high-potential incidents (HPI) in the industry.
It recommended that the mining industry in Queensland – both coal and mines and quarries – adopt the high reliability organisation philosophy that has been adopted in other high hazard industries.
This change in behaviour of organisations will have a significant impact on the safety performance within the industry.
The industry is in its infancy in terms of adopting that philosophy, but that is one of the significant safety improvements being encouraged across the Queensland resources sector.
The other one is automation in open cut and underground operations, which will ultimately improve predictability in performance, but the human factor is always going to be present there. So, a continued focus on effective supervision will be critical.
The third one is improvement of risk management in the industry. Twenty-two years ago, the regulator introduced risk-based legislation into Queensland. There is a requirement for a refocus of the adequacy of risk management processes, including the cross section of participants, the skills of facilitators and the attention of the identification of hazards and risks and the controls required to prevent harm to mine workers.
Automation is becoming a greater part of the Queensland resources sector, but this does not distract from the requirement for operations to be underpinned by robust risk management processes and effective safety and health management systems.
The simulation involved an underground loader fire and a fan stoppage that led to an evacuation. Image: Anglo American.
The exercise at Moranbah North involved a missing underground coal mine worker. Why was this specific scenario chosen?
It wasn’t chosen specific to a recent incident that’s occurred in the industry. It’s more along the lines that each year a new scenario is developed to test the effectiveness of the mine’s emergency response.
The scenario needs to be unpredictable, involve multiple agencies, provide a level of complexity and really all the components that a real mine incident will present to the mine’s incident management and emergency response teams.
People can become injured, disoriented or overcome by smoke, in a mine disaster scenario. The missing worker was just one part of an incident that may play out in the scenario.
Invariably the underground incident will revolve around a combination of a failure of strata, ventilation, gas and/ or water management, or equipment failure, resulting in falls of ground or a change in the mine environment, fire explosions, flooding or operator injury.
Any one of these events may present an instant response to be managed by the mine.
Each year, one or more of these
events is presented in the level one exercise so that it does very much test the mine’s capability and capacity to respond.
The level one exercises are only undertaken in underground coal mines. The level two exercises in open cut and underground are run by the mine itself rather than an independent body. However, the learnings and experience gained by the mine are as critical for continued industry learnings.
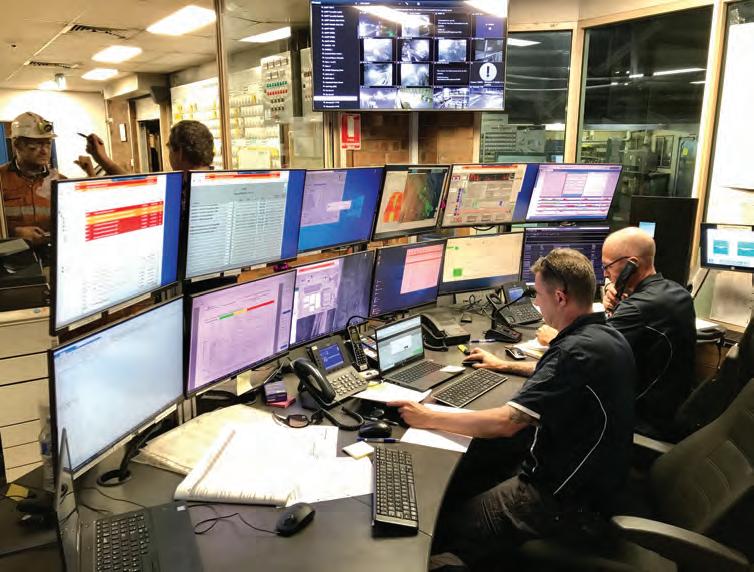
The exercise also found that staff were not adequately trained to use selfcontained self-rescue devices (SCSR). How vital is this training?
There were certain mine workers where there were some failings in terms of the donning of their SCSR.
It has in past years been a common learning that comes across from these exercises – in particular, the transferring from the belt worn to the cache unit.
The training of coal mine workers in emergency response and self-escape is a critical component of the mine safety and health management system.
The level one exercise tests that effectiveness in that training. In the underground scenarios which are also run at level two, those also involve mine workers having to don their selfrescuers, so they get further training in an emergency situations.
The SCSR are a coal mine worker’s means of self-escape. So, at the start of each shift, it’s critical that they check that unit physically, ensuring that it’s ready for use.
The refresher training undertaken by mine workers on an annual basis in terms of donning the SCRS is a critical component of the mine’s safety and health management system.
One of the benefits of the level one and level two exercises is that mine workers get tested in the donning of those rescuer devices.
The learnings demonstrate the importance of refresher training undertaken by mine workers that use emergency response equipment and never take it for granted that it will not be used.
It’s akin to it being a bit too late when you’re in a car crash to check if your seatbelt works.
Moranbah North was used in RSHQ’s simulated emergency exercise. Image: Anglo American.
One area of improvement from the exercise was the briefing of ISHR and mines inspectors. What needs to improve in this space?
The role of the mines inspectors and ISHR is that they play an important role in providing oversight to an emergency situation and an emergency response, while not being involved directly in the incident management team.
They are there to ensure that there is an acceptable level of risk management achieved in all aspects of the response.
In order to do this, it’s important that they are fully briefed on the incident and the response.
When both parties reach the mine at a similar time, these briefings can be undertaken together so that a single, consistent briefing is provided.
In the scenario that occurred, there was some delay between the various parties arriving so there were separate briefing sessions done by separate individuals at the mine.
The briefing certainly needs to be provided by one of the senior mine officials through the mines duty system contained within their incident management team – someone who is informed of the emergency and the response.
The IMT (incident management team) at the mine needs to be left to manage the incident, but the mine also needs to have a dedicated, informed official to brief both the ISHR and mines inspector with accurate and timely information.
To answer what needs to improve in
the space, it is that there is a fully briefed senior official who is briefing the ISHR and the mines inspectors on not only the emergency but also the proposed response.
How has safety protocol improved in Queensland’s resources sector? What still needs to change?
There’s been a number of areas that safety protocols have been improved over the last decade.
However, as an industry, there tends to be variability across operations and organisations, and that continues to be a concern and the subject of chronic unease within the regulator.
There are some best practice operations in certain aspects, while others certainly have other areas of improvement.
In terms of what needs to change, the areas of improvement that the industry is being encouraged to improve, and adopt, include effective supervision, HRO (high reliability organsiation) philosophy and effective risk management.
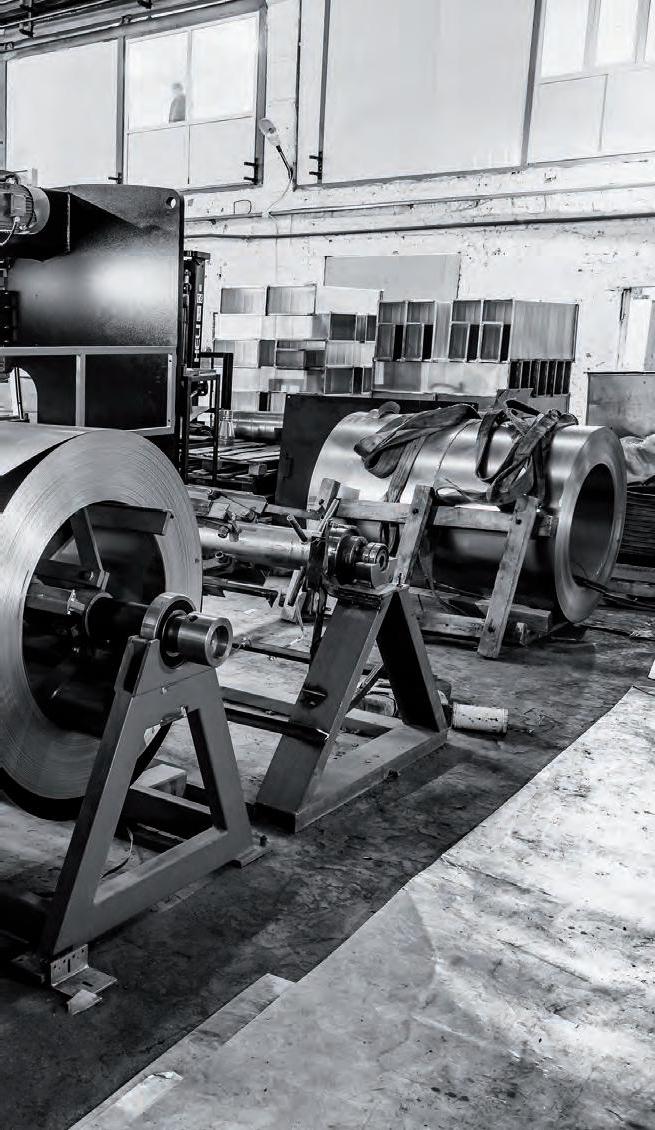
Advancements in mining technology are often associated with improvements to safety outcomes. However, many technologically advanced solutions require specific training. Is this something RSHQ has to consider?
RSHQ has to consider them with respect to mines achieving an acceptable level of risk.
The inspectors within RSHQ need to understand the new technology, so they are informed in terms of the way in which the technology will result in improved health and safety outcomes, and any potential risks that the technology may introduce, and the additional controls required for the implementation of such technology. A good example is the recent introduction of autonomous trucks into the Queensland coal industry and the use of autonomous longwall operations.
These changes see equipment being automated, eliminating the requirement for mine workers to operate the controls. This has the advantage of removing operators from hazardous areas, improving the predictability of equipment operation and movement and hence reducing the risk of operator error, exposure to noise dust, vibration and other hazards. However, the introduction of new technology does not prevent operator interaction with the equipment.
In the surface area, you still need to operate light vehicles, graders and excavators in and around autonomous haulage.
Operating those other pieces of equipment requires a new set of skills and knowledge no different than the longwall where operators will still be working in and around the longwal during certain activities. These skills and knowledge apply to both operators and the regulator.
FEELS LIKE BARE HANDS, BUT IT’S CUT LEVEL 5C
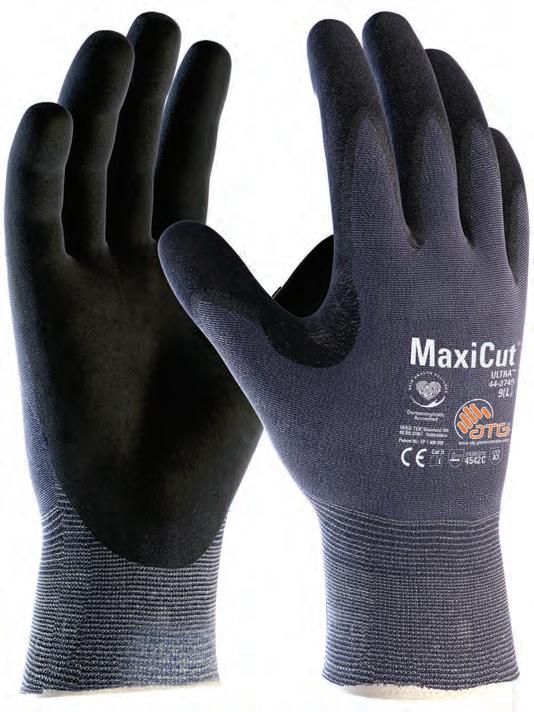
ATG® MaxiCut® Ultra™ gloves provide a high cut-protection solution, while also delivering increased flexibility, comfort and precision handling.