
4 minute read
Safety with a dash of innovation
from STW Jul 2021
by Prime Group
Mining equipment Safety with a dash of innovation
THYSSENKRUPP INDUSTRIAL SOLUTIONS HAS MAINTAINED A STRONG FOOTHOLD IN THE MINING INDUSTRY BACKED BY A TRACK RECORD OF DELIVERING SAFE AND FORWARD-THINKING PRODUCTS THAT STEM FROM THE CULTURE OF ITS EMPLOYEES.
There are many ways that original equipment manufacturers can claim to develop safer products.
However, thyssenkrupp’s proven method of creating mining machinery under the baton of its strong safety culture has cemented the company’s long lineage of safe, productive and reliable equipment. thyssenkrupp health, safety, environmental and quality (HSEQ) manager Jeremy Walden says there is no single method for achieving this.
“There is no one silver bullet. At thyssenkrupp, it is a combination of factors,” Walden tells Safe to Work.
This includes design review and feedback during the engineering phase of a project, implementing feedback learnt from previous projects, adopting client initiatives, reviewing market and product safety information, communication and collaboration between thyssenkrupp (local and global) and its customers, and drawing on internal talent, experience and knowledge from the company.
Accidents at a mine site can often lead to significant production losses – or at the very worst, fatality – so thyssenkrupp ensures its range of equipment and services match the stringent guidelines enforced across Australia. thyssenkrupp matches Australia’s high safety standards for workplaces, which Walden says is another important factor of the company’s success in the country.
“We definitely put in a lot of effort to maintain that,” he says. “thyssenkrupp replicates the same high standard even if the safety expectations of another country that we operate in are different. That doesn’t mean we drop our standard – we conduct global, internal meetings so the same standard is rolled out no matter where in the world we operate.” thyssenkrupp employs 104,000 people across 140 countries. Walden says the company’s safety culture is constantly evolving, and it continually looks for ways to enhance and refine its practices.
This has been achieved through the driving factors of hazard identification and controls, as well as safe work behaviours.
“I would describe thyssenkrupp’s safety culture as positive and evolving, relying on the individual efforts to maintain the team performance,” Walden says. “Hazard identification and risk assessment has always been there as part of the company, and what thyssenkrupp has done more recently is that it has made it more of a focus as clients have made it more of a focus.
“Globally, thyssenkrupp is quite active at communicating health, safety and environment topics, safety shares and promote initiatives such as the annual ‘we care’ event – a week-long event that promotes a particular nominated topic across the globe.” thyssenkrupp’s mining solutions, including its bucket wheel excavators, stackers, shiploaders, crushers and belt conveyors, all exhibit the company’s attention to detail.
“We’re always trying to optimise the design in a cost-effective way,” Walden says. “You must always stick to good quality, and I think that’s an area that thyssenkrupp does well with its products.
“For our teams and safety of personnel, we’ll keep communicating on safety, sharing and improving systems of work, while we identify our hazards and build on the positive safe work behaviours exhibited by our experienced teams.” thyssenkrupp believes that automation, regular maintenance and a rethinking of designs can mitigate error and prevent personnel from hurting themselves on site.
“thyssenkrupp aims to mitigate these existing risks by improving and expanding its automation offerings, continue and expand its maintenance portfolio and follow continual improvement as required by its ISO:9001 Quality System Certification,” Walden says.
thyssenkrupp retains high safety standards across all countries it operates in.
As the use of automation ramps up on mine sites, Walden says that a stronger focus on this area is likely for the industry as it aims to manage potential hazards on site and deliver higher efficiency.
“In thyssenkrupp, there’s a big push for automation. We’re just removing people from harm’s way or elements of the process,” Walden says.
“Through automation, workers don’t need to be in certain environments because the machines are programmed to do certain things, so you can get the machines to run their program with little input from external people and take them out of that process.”
Walden believes the industry is still a long way from fully automated machinery, however, self-diagnosis is on the horizon.
He says the focus is to introduce automation on a lot of equipment so the machines are more efficient and run 24/7.
“This will include developments in the coming years leading into machines that carry out basic maintenance within their own ecosystem, and reduced exposure to risk for the operators and personnel,” he says. “There will always be a need for people or humans. We’re a long way off from removing people from involvement with these machines.”
By delivering a focus on safety culture and continuing to innovate with its products, thyssenkrupp expresses the vigour of safety in the mining industry through its range of solutions.

thyssenkrupps expects the rapid uptake of automation to continue in mining.
SILEX+ SMALL
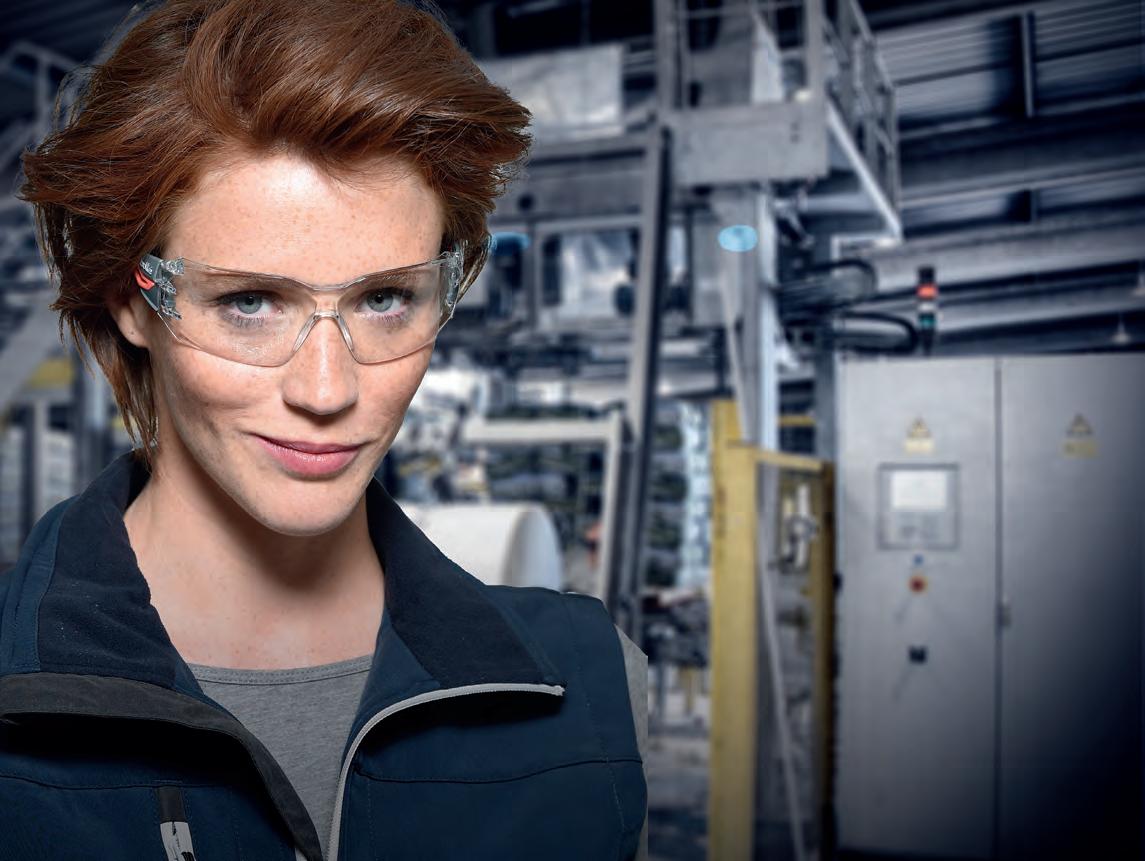
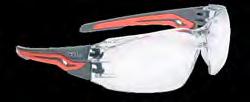

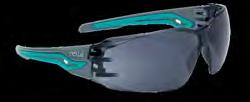