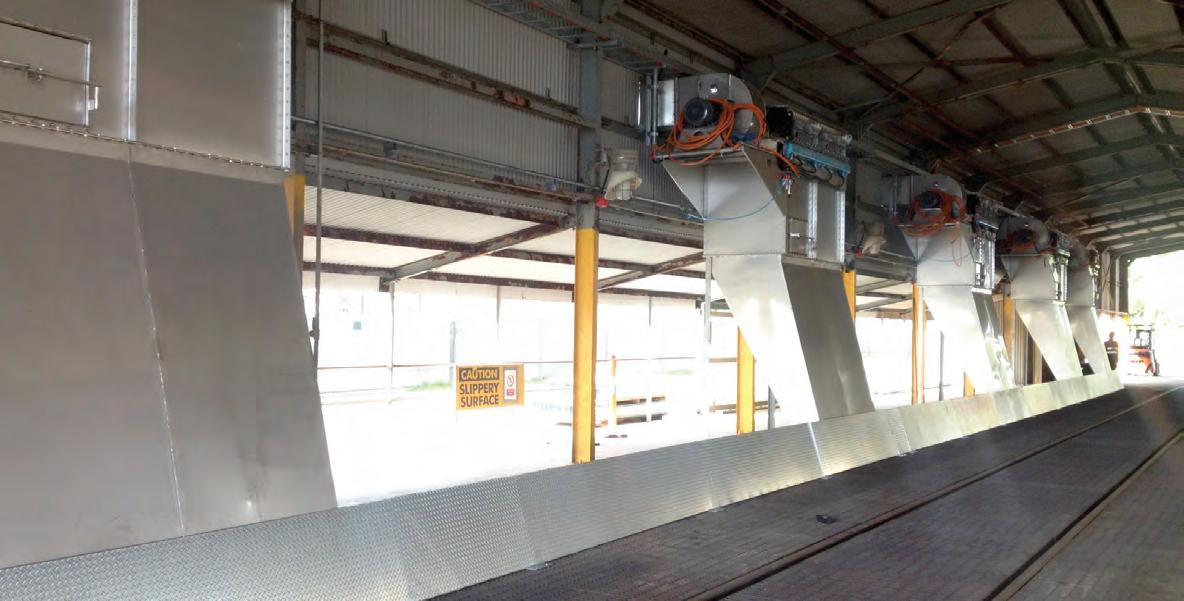
5 minute read
How to know when a hopper is full
Burnley Baffles is a system that restricts air flow.
WITH 60 YEARS OF SUCCESSFUL DUST COLLECTION PROJECTS, MIDECO IS WELL PLACED TO SOLVE EVEN THE MOST CHALLENGING DUST COLLECTION AND EXTRACTION SYSTEM PROBLEM.
Mideco’s dust collection solutions are industry leading and highly effective. The company prides itself on the partnerships it forms solving dust problems for clients from all over the world.
The company’s Burnley Baffles solution is a well-established dust suppression system with hundreds of installations in Australia and around the world.
Burnley Baffles are installed at facilities in the United States, Canada, New Zealand, China, United Kingdom and Ireland.
According to Mideco director Melton White, there is both a question and a rule that are rarely understood and virtually never applied to dust management with regards to bulk materials-receiving hoppers.
The question is, when is a hopper full? The fact is that air extraction cannot ever be directed.
White says the answer to the question of, ‘when is a hopper full?’ is simple but is often complicated with a tootechnical solution.
“Ask any engineer when a hopper is full and you will get an answer associated with how many cubic metres of product it can hold, or what weight of product it can hold, or when it is ‘full to the top’,” White says.
“To answer the question correctly you have to be able to see what can’t be seen.
“The answer to the question is – a hopper is always full. Sometimes it is full of product, other times it is full of air and then other times it’s a combination of both. But regardless, it is always full.”
White says that air extraction can never be properly directed and uses the example of a pedestal fan to make his point.
“Almost all of us have a pedestal fan at home, we tend to put it in the corner of the room and when the air comes in contact with us, it cools us. But where does that air come from?” White asks.
“If we put our hand in front of the fan, the airstream is easy to feel; it’s a column of air blowing out. But if we put our hand behind it, nothing can be felt, or at best we can feel the hairs on the back of our hand moving a little.
“The same can be said for a straw. If we blow down it and hold our finger an inch from the end, we can easily feel the airstream hit our finger. If we suck up through it holding our finger in the same
location, we cannot feel the air at all.
“This is because suction or extraction is rarely understood, when anything sucks it causes a pocket of low pressure; from there, atmosphere pushes in from all directions to fill it. All directions mean just that – every direction equally.”
To illustrate the point more clearly, White references a straw and encourages people to think in only two dimensions instead of three.
“If we think there are 360 degrees around the open end of the straw, our finger is in line with about 30 degrees, thus 330 degrees are free to flow, this includes perfectly parallel to the outside of the straw and around and into the end. We cannot feel the flow. Then remember the third dimension, there are 129,600 angles available, of which say 900 angles are in line with our finger,” White says
“Thus, you cannot feel the airflow at all. Then remember, in the real world there are three dimensions. The same applies for the pedestal fan and right the way up infinitely.
“A jet engine does not suck its way forward – it is propelled by thrust, by the air out the positive-pressure end.”
White says to apply this example when putting product into a hopper. Because the product is heavier than the air that is already in the hopper, he explains that the air is pushed out as a result.
“In this case that means up and out into the environment,” White says. “The problem is, it flows against the product flow and liberates the lighter particles within the product. That is the dust.”
White says the solution is a combination of understanding the answer to the question – when is a hopper full? – and controlling the suction flow.
Mideco’s Burnley Baffles is a system that restricts air flow out of or into the hopper, but still allows product to flow into it.
The system consists of a set of modules that fill the open inlet face of a hopper. Each module contains a set of blades that pivots to allow the material flow into the hopper.
The baffles strip the air moving through the hopper off the pieces of grain or ore because the air pressure on all sides of baffles is all but constant.
As the air is not heavy enough to open the blades, only the product enters the hopper while the dust is kept below the blades.
“So, working in reverse and applying suction to the hopper, by applying a dust collector to it, with a restriction in regard to where the air comes from means the hopper is always at a slightly lower pressure than atmosphere,” White says.
“Air is always flowing down from the working environment into it. Then when the product is dropped into it and starts to push the air out, it does not come out. Instead, it flows towards the negative pressure which is the bag house.
“Therefore, if the air is not flowing up and through the product flow to get out, there is no dust.”
The Burnley Baffles, by themselves, can eliminate up to 80 per cent of the dust escaping the hopper enclosure. Combined with a dust collector, the percentage eliminated can be up to 100 per cent.
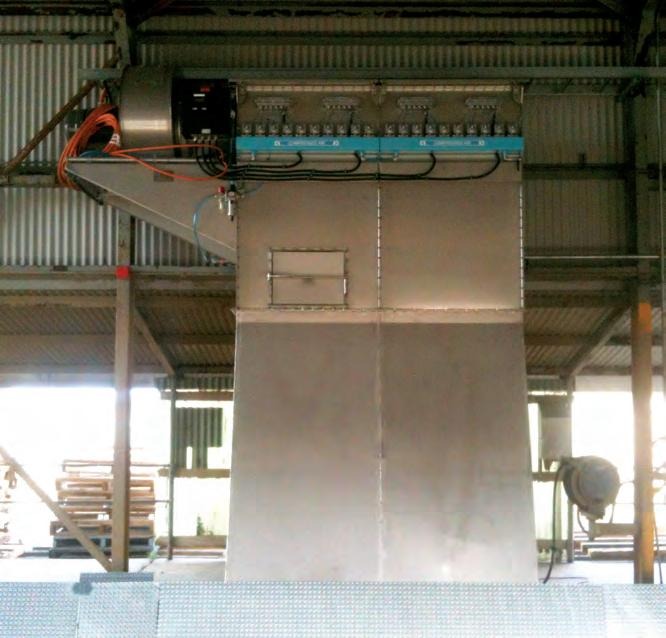
Burnley Baffles are installed at facilities all over the world.