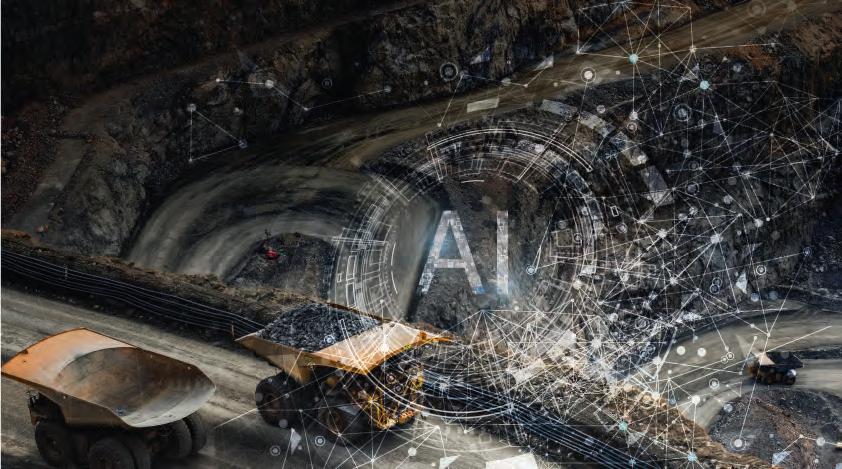
4 minute read
Smarter, safer AI-driven mining fleets
THE DEPLOYMENT OF ADVANCED DATA ANALYTICS, ARTIFICIAL INTELLIGENCE AND INCREASED CONNECTIVITY THROUGH THE INTERNET OF THINGS ARE KEY DRIVERS OF THE DIGITAL REVOLUTION IN THE MINING SECTOR. ONE AREA WHERE MACHINE LEARNING CAN PLAY A BIG ROLE IS FLEET MANAGEMENT.
The Australian mining industry has one of the highest fatality and injury rates of any industry. A combined total of 2808 working days per year are lost due to injuries alone.
This makes it easy to see why mining companies have a lot to gain from this advanced technology and why rates of adoption continue to grow.
There’s an urgency to ensure mine site safety and maintain regulatory compliance, which has resulted in a need for mining companies to become more proactive in managing daily operations to mitigate risk.
WHY AI IS THE FUTURE OF FLEET MANAGEMENT
The use of artificial intelligence (AI) can allow for a deeper analysis of fleet operations as well as more accurate and specific predictions than have been seen before.
Thanks to AI, mining fleets can improve the accuracy of telematicsderived data related to driver behaviour, asset tracking, fleet utilisation and overall fleet operations which, in turn, can improve site safety, driver safety, productivity and cost-efficiency.
AUTOMATED DECISION MAKING
AI-driven automated decision-making is also becoming more common when it comes to fleet-maintenance issues.
Many fleets today practice preventive maintenance – for instance, sending a notification or alert every 10,000 kilometres to change the vehicle oil to prevent future engine problems.
By analysing engine data, fleet information can get more precise and predictive than ever before.
Not every vehicle needs its oil changed at 10,000 kilometres – where, how and how frequently depends on factors like the way a vehicle is driven and the condition of the oil.
Telematics data pulled from the engine and analysed can give a more precise picture and enable fleets to predict exactly when maintenance is needed to suit a particular circumstance.
Users can see how such a process would lead to better efficiency, greater vehicle uptime and increased productivity. Preventive fleet maintenance is where AI really shines.
AI enables deeper analysis of fleet operations as well as more accurate and specific predictions in mining operations.
MAKING FLEETS SAFER
Another feature of AI that could help in making mine fleets safer is facial recognition.
In-cab cameras are a big growth area in telematics. According to Berg Insight, the market for video telematics will grow by 22.2 per cent between 2020 and 2025, to 3.2 million subscribers.
Video telematics can reduce collisions by 60 per cent and the related costs by 75 per cent.
Visual evidence collected by in-cab cameras is a powerful tool for insurance claims and driver safety training.
What’s more, video telematics is increasingly being used in combination with AI technology to help provide visual context.
This helps to determine the circumstances around specific events such as on-site crashes.
AI-powered video eliminates the time-consuming task of sifting through hours of footage to find the precise event a fleet manager needs to review and makes any video snippet available in near real-time.
The technology has garnered a significant reputation for its ability to increase safety and efficiency within fleets of all sorts, making AI ideal for the mining industry.
In-cab cameras can also provide important proactive safety benefits – models that can detect a driver falling asleep while driving or an imminent crash that then triggers audible in-cab warnings to help prevent a crash from occurring.
Machine vision technology, powered by AI, can also be used to streamline driver ID and security processes.
For instance, facial recognition can be used to unlock or start vehicles (to prevent, for example, unauthorised usage), or enable auto-login to the telematics system.
CHALLENGES THAT AI-POWERED VIDEO CAN HELP MINING OPERATORS TO SOLVE
The benefits of using AI-powered technology include (but are not limited to): • Reduction in speeding through increased awareness of road safety behaviours. • Identifying at-risk drivers and taking relevant actions to assist them. • Locating drivers at all times. • Providing direct real-time feedback for operators and their control centres on road conditions. • Reducing fuel usage, thus lessening environmental impact.
Using AI alongside video telematics can help manage driver distraction, fatigue and other potential safety threats in real-time to prevent potential crashes and the resultant injuries.
Safety incidents can be significantly reduced through the identification and monitoring of high-risk drivers, locations, times and shifts.
In turn, action plans can be implemented to train drivers on how to avoid safety hazards, allowing for improvement to take place on a continuous basis for long-term results.
The more data users have, the smarter they can be about making decisions that improve performance, efficiency and most of all safety.
Generating actionable insights will be the key to success in this brave new world of AI-enabled fleet management.
EZI-ON, EZI-OFF EZI-GUARD
Moving parts and pinch points pose a serious danger to people who work around machinery. While most machinery guards eliminate incidents around moving parts, it is often heavy and cumbersome enough to become a manual handling hazard.

The patented ESS EZI-GUARD system comprises of a range of versatile, easy to install brackets, lightweight panels and standard structural tubing which forms an ‘off the shelf’ system that can be adapted to almost any application.
The EZI-GUARD System has been developed to exceed the guard design requirements of AS4024.3610:2015.
The patented ESS EZI-GUARD is; • Quick and easy to retrofit • Easy to remove for maintenance • Modular ‘off the shelf’ design • Corrosion Resistant
• Strong but lightweight panels • Easily handled • Available in a variety of materials • Available in barricade form
• Coloured Safety Yellow or black as standard
