

The AIR we BREATHE
Keeping workers safe from dust
Face all your challenges with one tool
United. Inspired.
Mobius for Drills
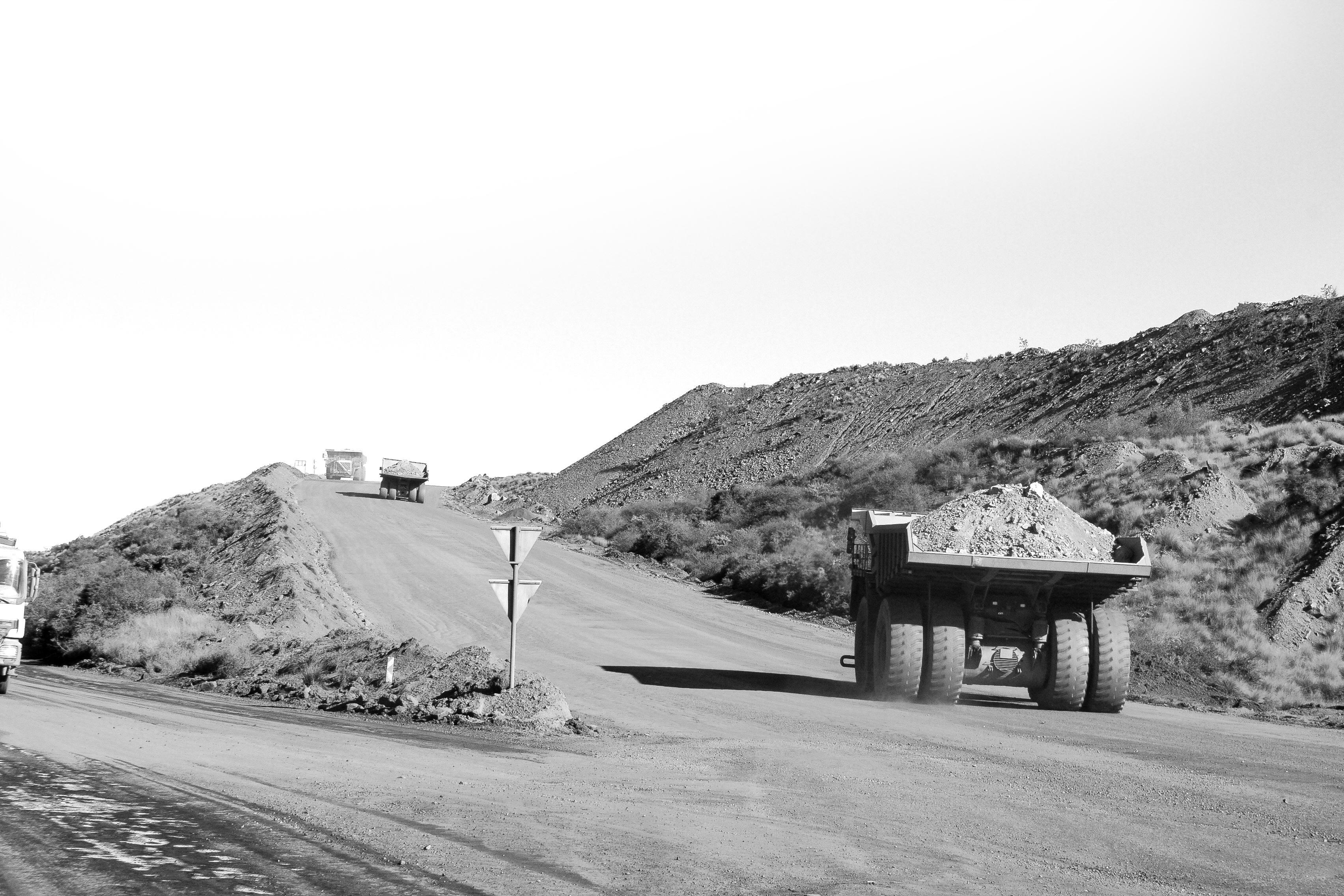
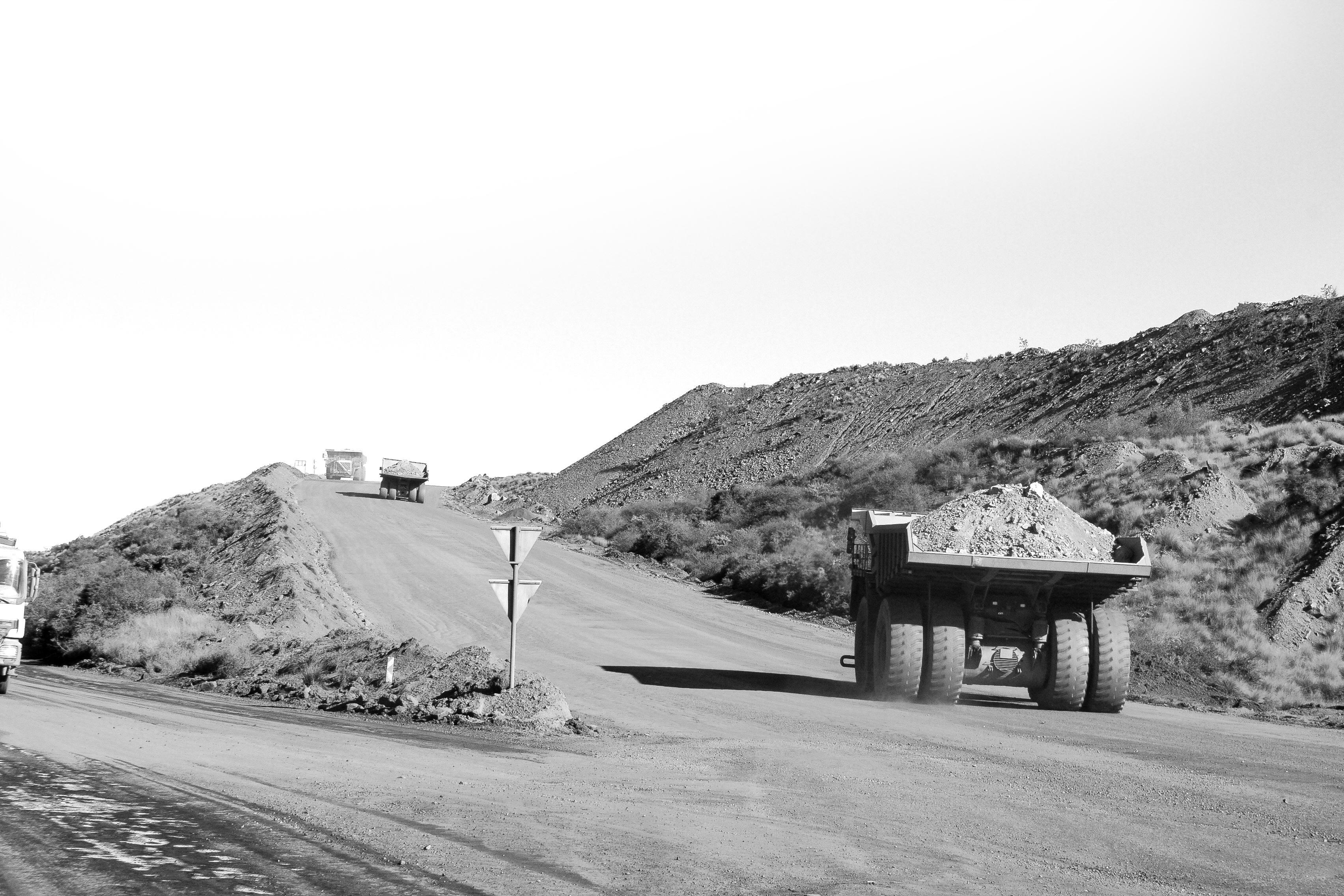
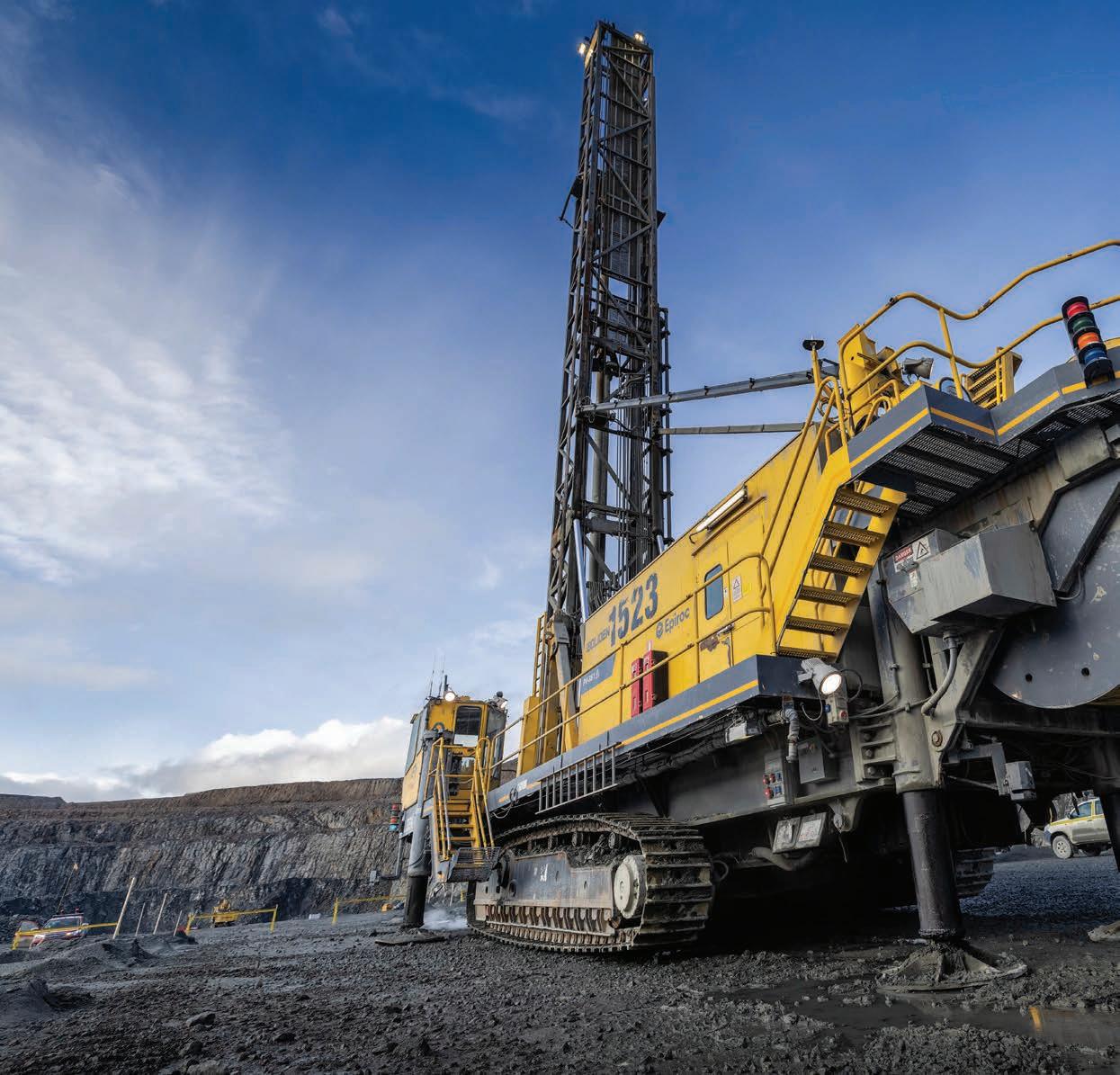
Mobius for Drills seamlessly integrates with drill OEMs and offers a user-friendly interface for effective decision-making. It serves as the main tool for managing drill fleets, providing detailed insights and real-time situational awareness. The system supports semi and fully autonomous drills, enhancing productivity and safety across mining operations. Additionally, it includes applications for blasting, haulage, and dozer operations, all coordinated through the Mobius Traffic Management System.

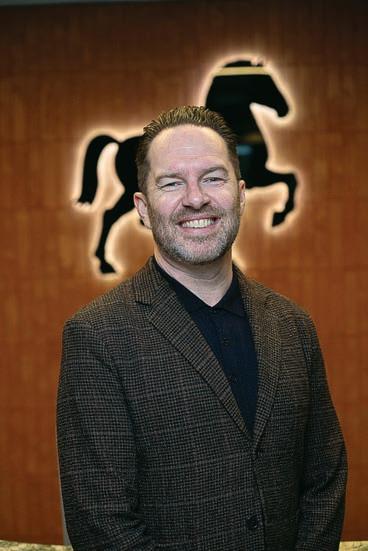
An invisible enemy
MINERS MIGHT NOT ALWAYS BE ABLE TO SEE DUST PARTICLES, BUT THAT DOESN’T MEAN THEY’RE NOT DOING EVERYTHING THEY CAN TO STAY SAFE FROM THEM.
The issue of dust is not a new one for the resources sector. For as long as mines have been extracting ore from the earth, they have battled dust. Dust can wear down equipment, harm vegetation and wildlife, and affect the quality of air, water and soil in an area. But, perhaps most concerning of all, dust can potentially have very harmful effects on the workers on the front lines of the mining industry.
Silicosis, a lung disease caused by inhaling respirable crystalline silica, remains a significant concern in many industries, mining chief among them. Silica dust, often invisible to the naked eye, can stay airborne for long periods and pose a threat to workers’ respiratory health.
Fortunately, the resources sector has made major strides in fighting against the dangers of dust.
OLIVIA THOMSON
Tel: (03) 9690 8766
Email: olivia.thomson@primecreative.com.au
DYLAN BROWN
COO
CHRISTINE CLANCY
MANAGING EDITOR
PAUL HAYES
Tel: (03) 9690 8766
Email: paul.hayes@primecreative.com.a
JOURNALISTS
KELSIE TIBBEN
Tel: (03) 9690 8766
Email: kelsie.tibben@primecreative.com.au
Tel: (03) 9690 8766
Email: dylan.brown@primecreative.com.au
ALEXANDRA EASTWOOD
Tel: (03) 9690 8766
Email: alexandra.eastwood@primecreative.com.au
CLIENT SUCCESS MANAGER
JANINE CLEMENTS
Tel: (02) 9439 7227
Email: janine.clements@primecreative.com.au
From personal protective equipment to suppression agents to better mining techniques to improved ventilation to shorter operating hours, companies across the industry make use of a range of products and services designed to limit dust exposure and keep workers safe. But efforts to protect workers go beyond an on-the-ground approach, and a large part of the answer to the question of dust exposure also lies in legislation.
In 2021, the International Organisation for Standardisation (ISO) released the ISO 23875, which lays out regulations for air quality in operator enclosures. ISO 23875 covers the lifecycle of the machine from design at the original equipment manufacturer level or in the after-market space, and throughout its service life.
ISO 23875 addresses the specific engineering control requirements necessary
to achieve a low level of silica exposure in operator enclosures, addressing air quality throughout the lifecycle of a machine.
The presence of dust is as old as the idea of people digging things out of the earth, but as extraction processes have become ever more sophisticated, so too have dustsuppression techniques. By adhering to up-todate legislation, ensuring health and safety policies are kept relevant and educating employees on how to stay safe in the face of dust, mine sites can go a long way towards ensuring their workers stay protected for longer.
Paul Hayes Managing Editor

RESOURCES GROUP LEAD
JONATHAN DUCKETT
Mob: 0498 091 027
Email: jonathan.duckett@primecreative.com.au
BUSINESS DEVELOPMENT MANAGER
JAKE NIEHUS
Mob: 0466 929 675
Email: jacob.niehus@primecreative.com.au
ART DIRECTOR
PAUL HAYES
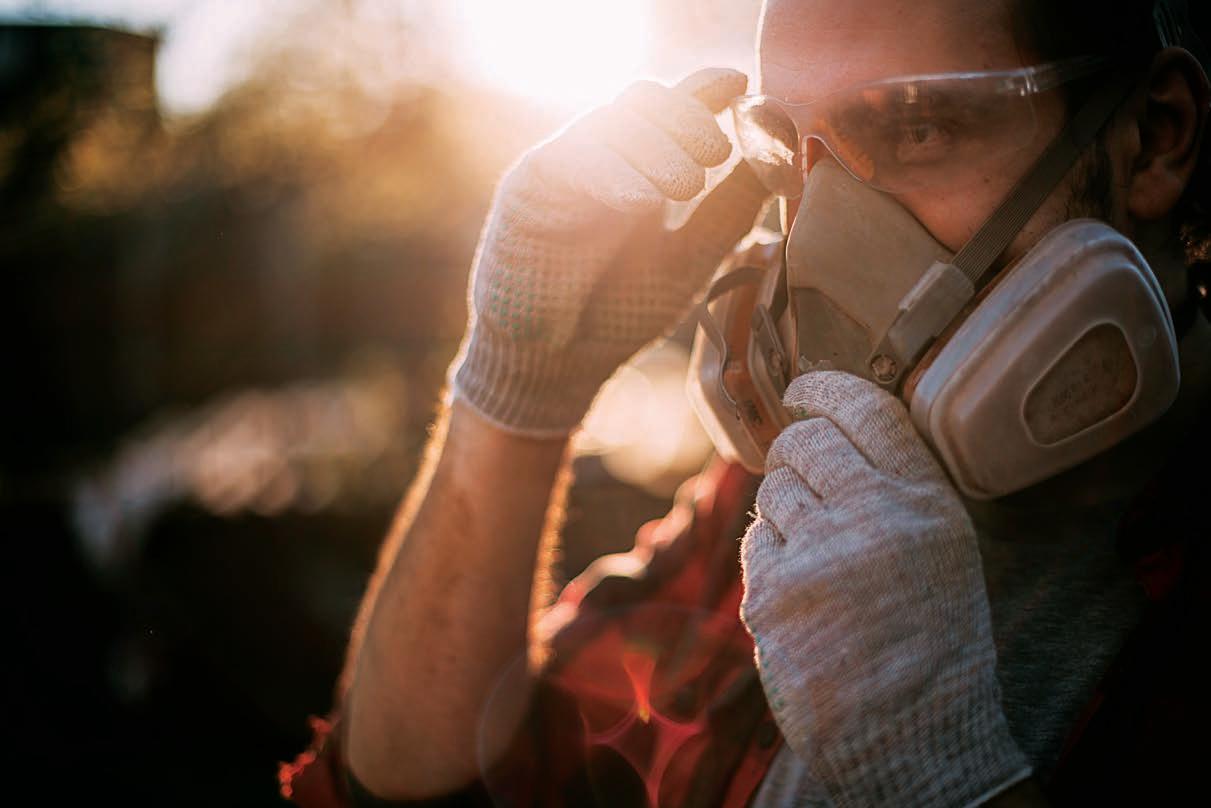
8 Bringing the Grosvenor fire under control: A timeline
Operations at Anglo American’s Grosvenor coal mine were suspended for almost a month after an underground fire broke out and, most importantly, no injuries were reported.
12 Keeping a lid on dust
While dust may be an inevitable part of mining, there are some key measures operators can take to help ensure workers stay safe.
16 Controlling dust, boosting safety
Dust-A-Side Australia wants to lead the charge when it comes to safety and dust control.
18 A greener path
Eco-Road Hero is on a mission to pave a safer, greener, less dusty road on the way to the Australian mining industry’s environmentally conscious future.
24 Next-level dust detection and measurement platform
WaterGasRenew’s new condition-monitoring range captures real-time data in one easy-to-use platform.
34 Ensuring safety while supporting mental health
Safety Mate’s Skytec 3030V respirator is protecting workers when they need it most. 36

36 Measuring workplace training results
Martin Engineering asks the question: Is your goal to get a return on your investment when undertaking required training hours?
40 MinRes Air lifts off Mineral Resources is on a mission to reinvent the FIFO experience.
46 Acting against welding fume
Apex Welding Safety’s AeroGuard air monitor can help operators keep their finger on the pulse when it comes to welding fume.

OCTOBER IS MENTAL HEALTH MONTH
SAFETY MATE OFFER THEIR BLACK DOG PRODUCT
RANGE TO SUPPORT BLACK DOG INSTITUTE
Safety Mate is proud to support Black Dog Institute who strive to provide better mental health and transform the mental health system. As the only medical research in Australia to investigate mental health across the lifespan, Black Dog Institute have the power to create better mental health for all Australians.
20% of Australians will experience symptoms of mental illness each year, and more than half of these people won’t seek help.
Through their partnership, Safety Mate are providing vital funds to Black Dog Institute, helping them to drive positive and evidence informed change in mental health where its needed most.

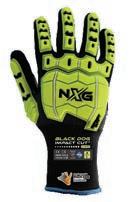
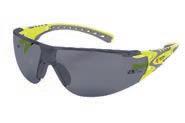
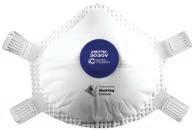
BLACK DOG CUT D GLOVE
• Lightweight cut level D
• Touchscreen compatible
• Comfortable and durable
• $1 per pair donated to Black Dog Institute
BLACK DOG IMPACT CUT F
• Lightweight cut level F
• Excellent fit, breathability and comfort
• Touchscreen compatible
• Soft and flexible TPR impact protection
• Durable and breathable nitrile coating
• $1 per pair donated to Black Dog Institute
BLACK DOG STREAM EVO
• Maximum comfort and protection
• Tecton 400™ Anti-scratch and Anti-fog
• Soft, adjustable, anti-slip nose bridge
• 50c per pair donated to Black Dog Institute
SKYTEC 3030V
• Market first and only full foam face seal – ensuring excellent face fit testing results, and comfort
• Four point headstrap adjustment
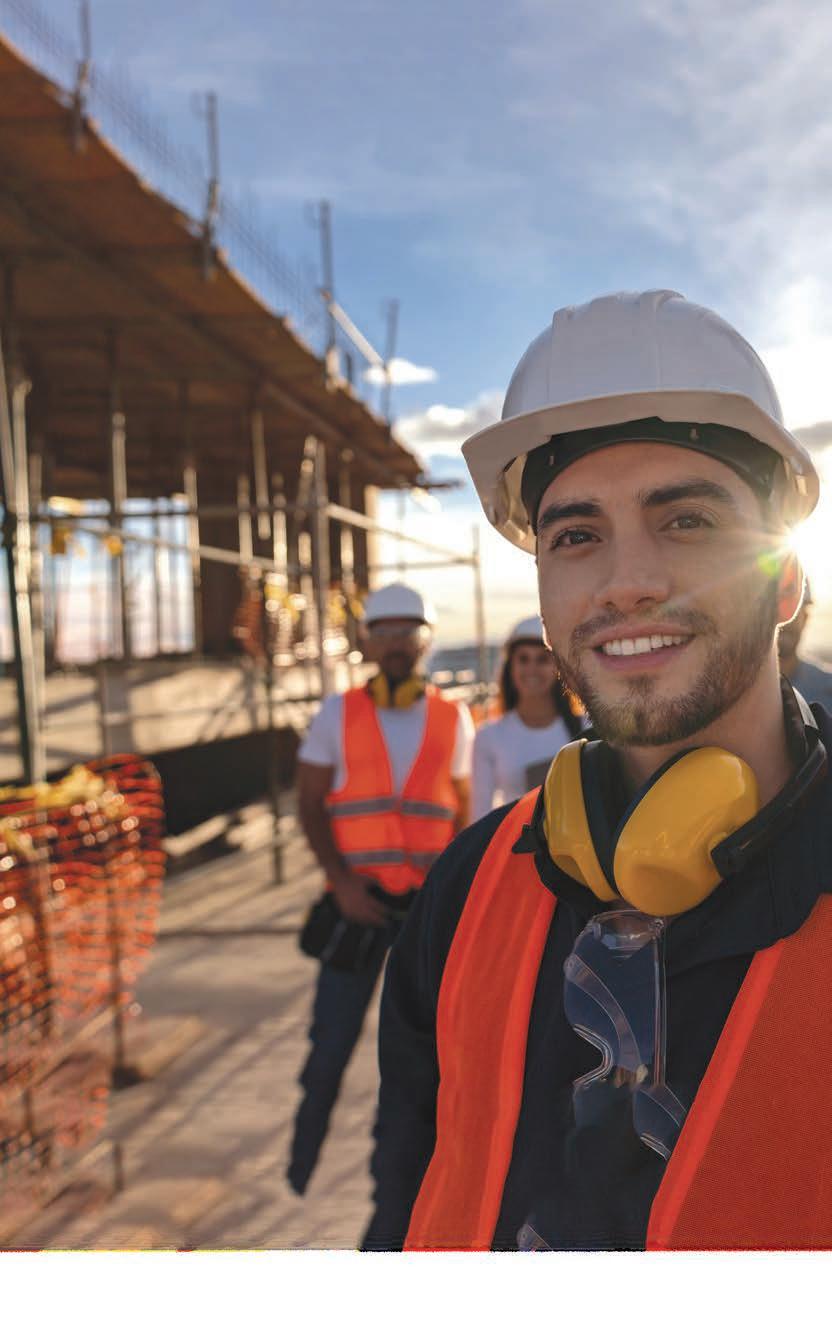
• Low breathing resistance valve
• Also available in smaller size (3030V-S)
• 50c per mask donated to Black Dog Institute
About Black Dog Institute
The Black Dog Institute is a not-for-profit facility for diagnosis, treatment and prevention of mental illnesses such as depression, anxiety and bipolar disorder. Their aim is to create a mentally healthier world for everyone.
SCAN FOR MORE INFO AND TRIAL SAMPLES
Products
THE ESS EZI-GUARD SYSTEM
The ESS EZI-GUARD system is a versatile, easy-to-install solution featuring brackets, lightweight panels, and standard structural tubing. This modular ‘off-the-shelf’ system adapts to nearly any application, exceeding the guard design requirements of AS4024.3610:2015.
Key features include:
• quick and easy retrofit capabilities
• simple removal for maintenance
• strong yet lightweight panels
• corrosion resistance
• availability in a variety of materials
• options for barricade form
• standard colours in ‘safety yellow’ or black.
The ESS EZI-GUARD is designed for ease of handling and adaptability, making it a reliable choice for diverse applications.
• esseng.com.au

BOLLÉ SAFETY GLASSES
Bollé Tryon glasses are available in three versions: safety spectacles, OTG, and prescription. The glasses are ultra-wrap-around with a sporty design and are non-slip, providing a safer experience.
Like many Bollé products, the Tryon range is available in clear, smoke, copper, cobalt flash and polarised lenses, making them suited to use throughout a range of industries. The cobalt flash lenses are suitable to use outdoors and indoors, as they protect the wearer from heat, while the copper lenses are ideal for activities that require exposure to alternating high and low light. The Tryon glasses combine style, innovation and protection to provide the wearer with the maximum comfort and safety.
•
THE BLACK DOG IMPACT CUT F SAFETY GLOVES
Known as being super lightweight, the Black Dog Cut D gloves are made from a breathable nitrile coating and lightweight liner, providing comfort, durability and highquality cut resistance, a key benefit when working within tough mining conditions. The gloves are also renowned for their breathability, compatibility with touchscreens, and having a certified Made In Green label by Oeko-Tex.
The Black Dog Impact Cut F safety gloves have also received the Made In Green label and provide users with maximum cut level F protection, durability, breathability and touch screen compatibility. In addition, they also provide flexible but tough impact protection for pinch and impact situations.
For every pair of Black Dog gloves sold, Safety Mate donates $1.00 to the Black Dog sInstitute.
• bolle-safety.com/au/industrial/glasses/safety-glasses/tryon-TRYON_INDUSTRIAL.html
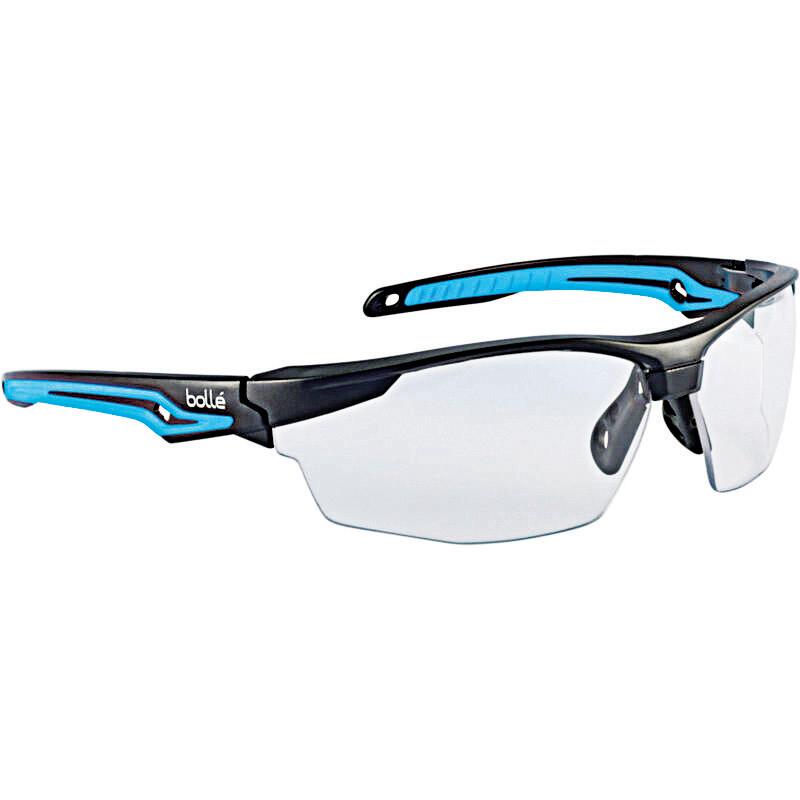

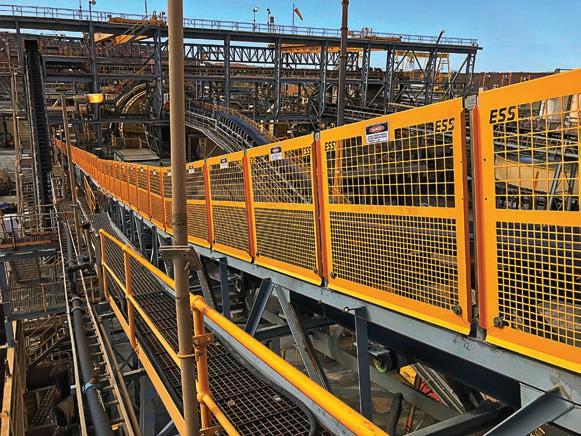
Image: Bollé
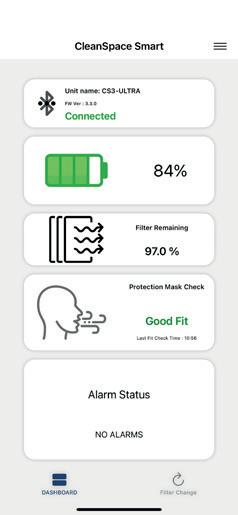
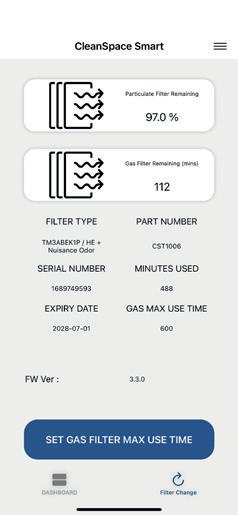
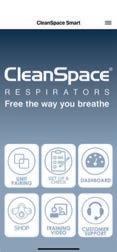
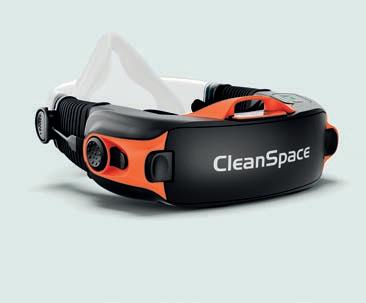
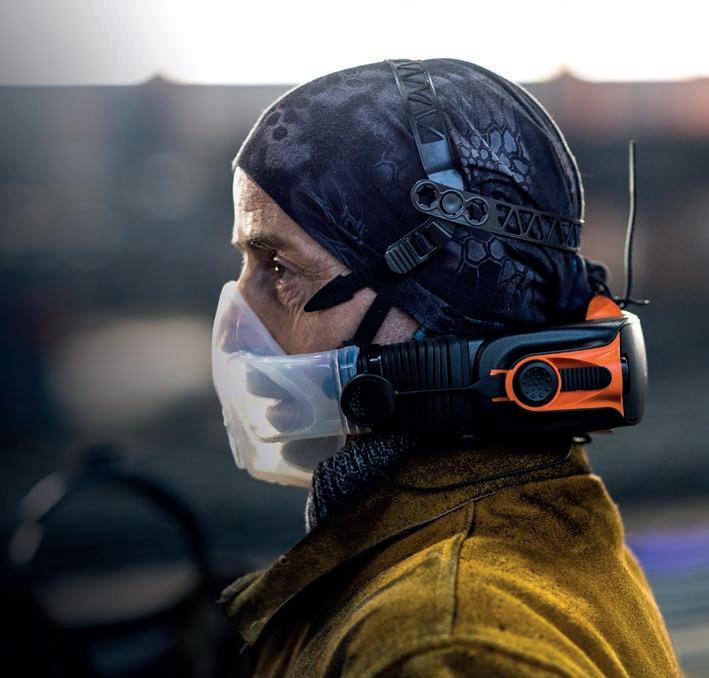
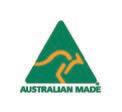
Bringing the Grosvenor fire under control: A timeline
OPERATIONS AT ANGLO AMERICAN’S GROSVENOR COAL MINE WERE SUSPENDED FOR ALMOST A MONTH AFTER AN UNDERGROUND FIRE BROKE OUT AND, MOST IMPORTANTLY, NO INJURIES WERE REPORTED. SAFE TO WORK BREAKS IT DOWN.
Afire at any mine site can have dire consequences, but a fire at an underground coal mine, where the process produces a number of gasses, can be catastrophic. According to Resources Safety and Health Queensland (RHSQ), highly flammable gasses like methane, hydrogen sulphide, and carbon monoxide collect in pockets along a coal seam and, when released, those gasses can trigger an explosion.
While modern coal mining enjoys the benefit of practices and technologies that minimise the likelihood of a gas fire, the risk remains prevalent in the industry.
This fear was realised by Anglo American earlier this year when an underground fire broke out at its Grosvenor coal mine in central Queensland in late June.
JUNE 29
Anglo was quick to act once the alarm had been sounded, prioritising the safety of the 150 underground workers on-site at the time the fire broke out.
“All emergency protocols were followed and the workforce was safely evacuated from the mine without injury,” Anglo said in a statement at the time.
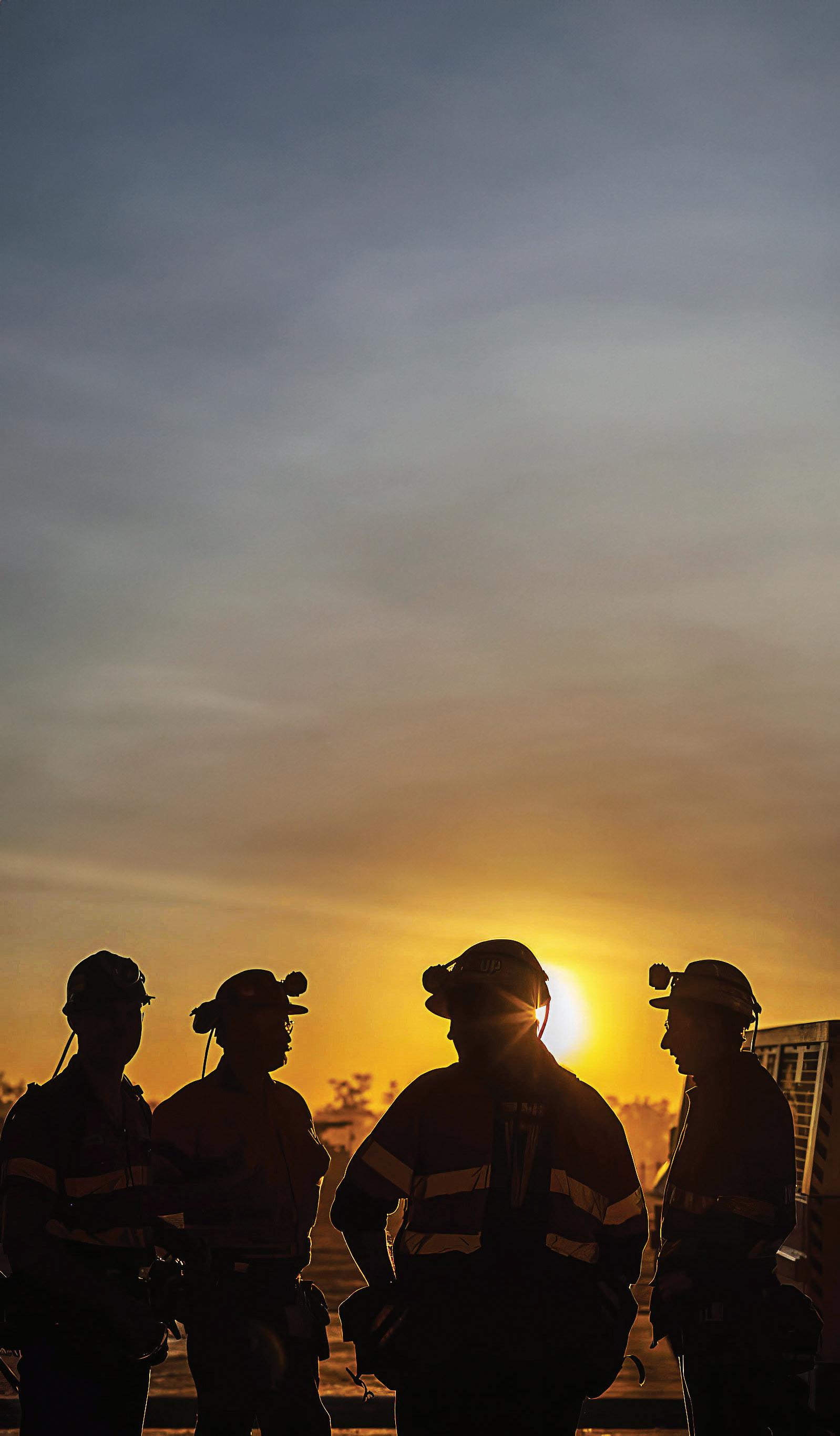
Anglo called in RHSQ to help secure the scene, and aid was immediately sent to the site.
JULY 4
Five days after the fire initially broke out, Anglo revealed the efforts it was making to quell the flames.
Work to extinguish the fire began immediately, but the process wasn’t as straightforward as one might hope. With a complex network of tunnels extending 500m underground, quashing the fire quickly and safely was a difficult proposition.
Rushing to close off all entrances to the mine could have resulted in an
Workers at the Grosvenor mine.
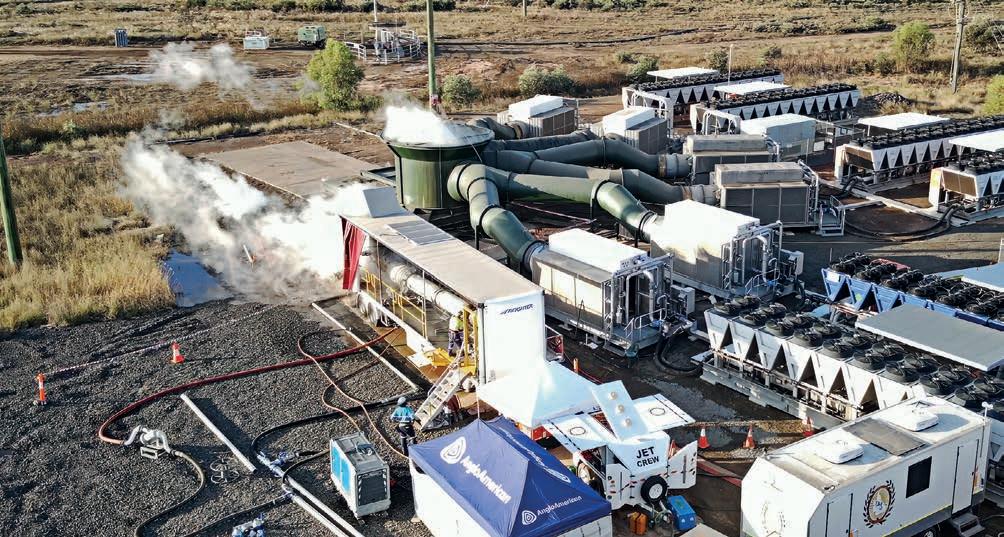
explosion if gas was recirculated back towards the fire.
Efforts began with the use of a Gorniczy Agregat Gasniczy (GAG), which in Polish roughly translates to “mine fire suppression apparatus”. The GAG was connected to ventilation shafts on-site, sending inert gas into the mine.
A high-pressure jet-engine, the GAG generates large volumes of low-oxygen inert gas to extinguish the fire and make the underground atmosphere safe, using a mix of inert gas and water vapour.
“The Queensland Mines Rescue Service’s mine inertisation unit, a specialist team of mines rescue personnel from coal mines across Queensland, operates this high-tech machine,” Anglo said.
“The mines rescue response on display has been a true testament to the spirit of teamwork and collaboration that exists in the mining industry.”
As for the Moranbah area surrounding the mine, Anglo was confident there was no danger to local people.
“All monitors are reporting readings within acceptable limits, indicating no impact on community health from
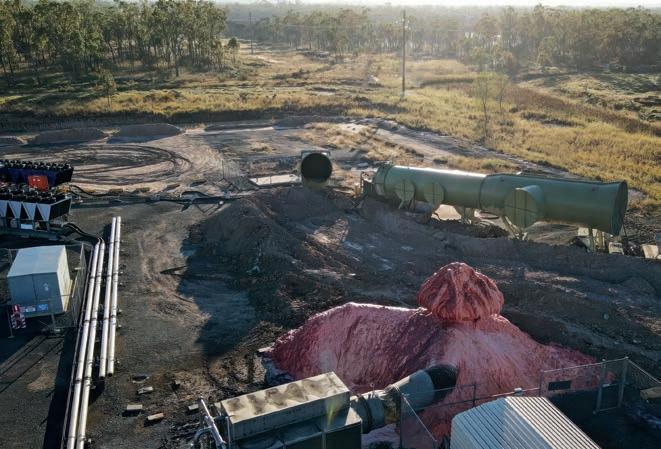
smoke or airborne contaminants,” the company said.
Anglo also called in the help of a remote-controlled dozer from its Dawson mine in Kianga, Queensland. The dozer was used to safely approach on-site ventilation shafts at Grosvenor to assist with temporary seal efforts by pushing dirt into the shaft, sealing off the fire’s oxygen supply.
“An operator controls the dozer remotely using hand-held controls,” Anglo said. “It first needs to remove
the shaft housing above ground level so it can gain access to the shaft into the underground area to plug.”
Anglo also used Rocsil foam, a phenolic resin product, to help with the temporary seal of a number of ventilation shafts.
“This product is a mix of resin and a catalyst that produces an immediate foaming reaction, followed by a rapid expansion to as much as 35 times its original volume,” the company said.
“It is effective in helping us create a temporary seal.”
A GAG jet engine was a key component of Anglo’s incident response.
Anglo used Rocsil foam to help with the temporary seal of a number of ventilation shafts.
Industry safety
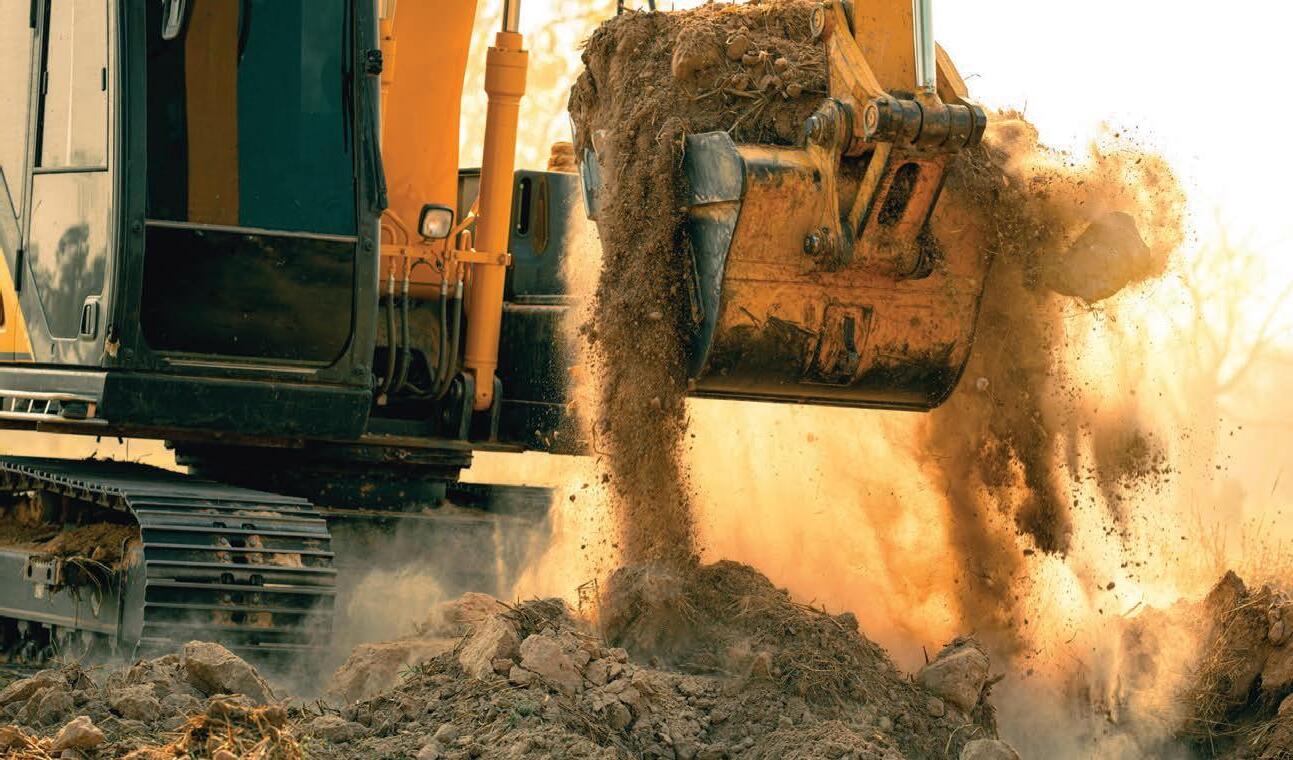
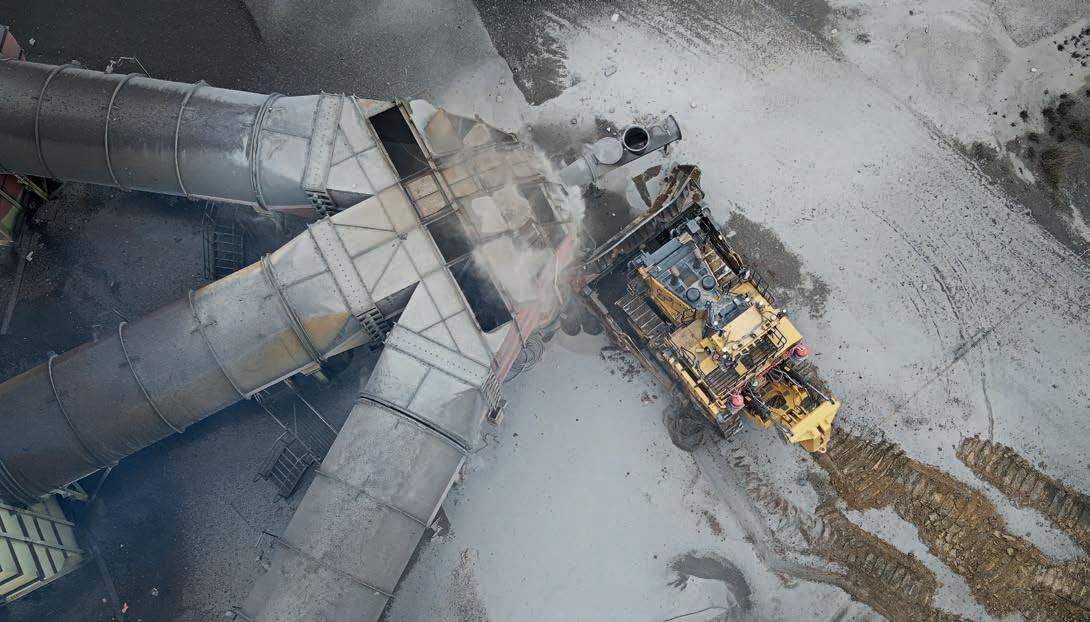
JULY 8
As efforts to safely staunch the fire continued, Anglo took steps to safeguard its 1400-person workforce from the challenges arising from the mine’s temporary closure.
This was revealed by Anglo in a joint statement with the Isaac Regional Council, the Mining and Energy Union, the Electrical Trades Union, the Collieries Staff and Officials Association, and the Australian Manufacturing Workers Union.
“Grosvenor mine is a significant employer in the Moranbah region, and we recognise its positive impact reaches far beyond the mine gates,” Anglo said.
“We’ve established an industryfirst working group consisting of senior leaders from Anglo American Steelmaking Coal and senior representatives from all unions covering the company’s operations in Queensland.
“The group’s objective is to support the long-term sustainability of the Grosvenor mine workforce.”
Anglo has made clear it is committed to working with unions to create continuous job opportunities and minimise uncertainty for its affected workforce. This involved a pay extension from July 15 to August 31 for all employees and embedded contractors working full-time at Grosvenor in operations or staff roles.
“Our priority is to provide added security for the Grosvenor workforce while we fully stabilise the mine to then begin assessing all options going forward,” Anglo said.
JULY
25
It was during Anglo American’s 2024–25 financial year results presentation that chief executive Duncan Wanblad confirmed the fire was out.
“Gas, temperature and drone monitoring suggest that the fire has now been extinguished,” he said. “We are developing plans with the authorities to examine the workplace in order to understand the cause and extent of the damage.”
Anglo said fallout from the fire will likely impact production for several
“All emergency protocols were followed and the workforce was safely evacuated from the mine without injury.”
months to come, but there is hope that damage can be contained, leading to a steady recovery for Grosvenor.
Despite damage to the mine itself, Anglo’s quick response helped to extinguish the fire in less than a month and led the 150 workers on-site at the time to safety with zero injuries.
The company’s effort resulted in a best-case scenario for the mine and its workers amid an extreme situation, helping to set an example to the industry at large that when disaster strikes, a quick response and a commitment to workers will lead to a light at the end of the tunnel.
Anglo’s remote-controlled dozer on loan from its Dawson mine.
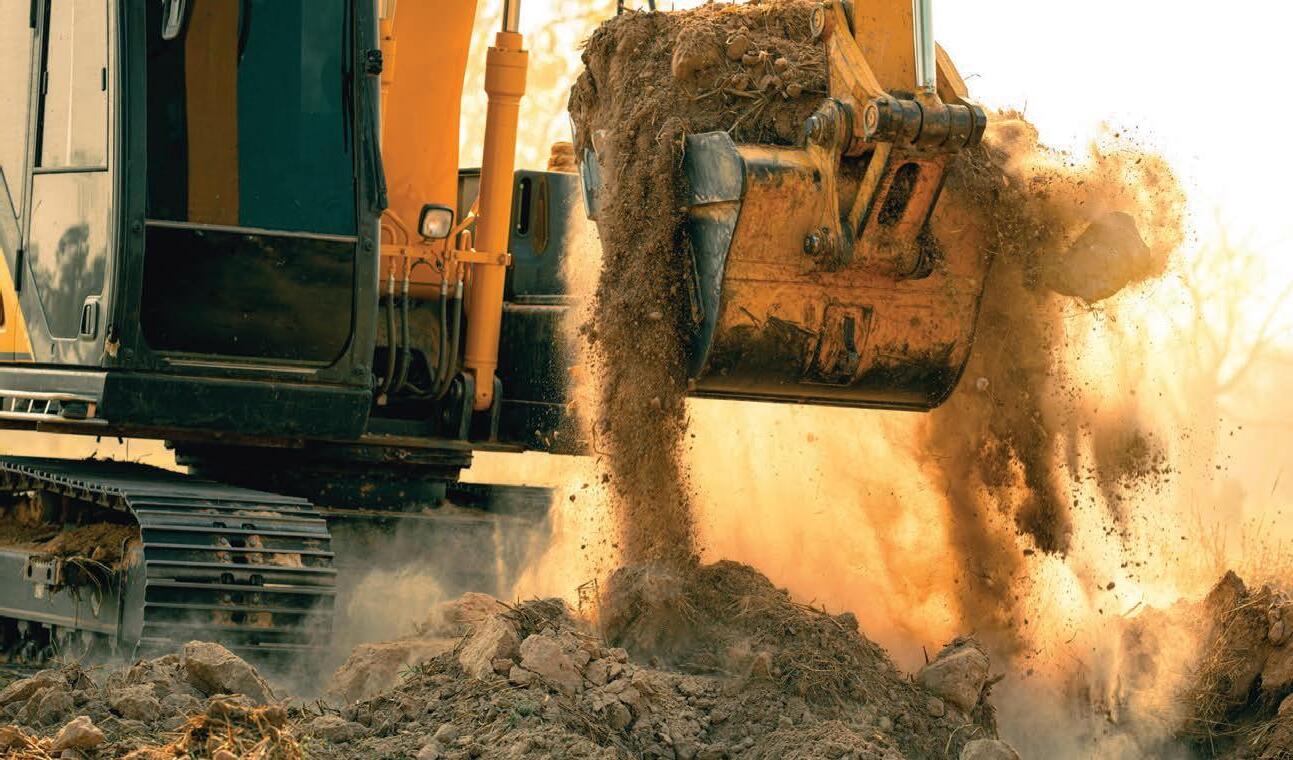
Your gateway to severe environment intelligence
Safeguard your workforce and enhance operational efficiency with dAlert
Industries that operate in severe environments, such as mining, construction, and agriculture, rely on accurate and trustworthy data. dAlert’s state-of-the-art environmental analytics equipment empowers you to make informed decisions that protect your people, optimise your operations, and solve environmental challenges.
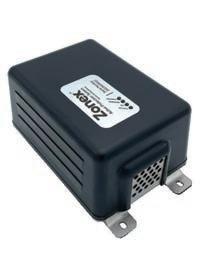
Zonex∞ monitors and alerts to changing air particulate levels in real time, promoting a healthier and safer work atmosphere.
• Prioritises operator well-being and contributes to operational efficiency.
• Engineered with the highest standards
• Supports compliance with ISO 23875

iDAT integrates advanced vibration analysis capabilities within a rugged, self-contained unit.
• Equipped with a 3-axis accelerometer and temperature sensor
• Precise vibration analysis
• Integrated Gateway Solution
Enginex
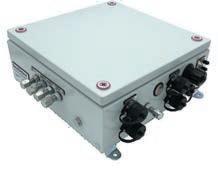
Enginex∞ is a cutting-edge air sampling device specifically designed for protection of diesel engines against “dusting”.
• Measures particulate quantities and sizes in filtered air samples.
• Provides regular and real time insight into air composition
• Proactive monitoring to mitigate the risk of excessive particulate contamination.
RoadGuard
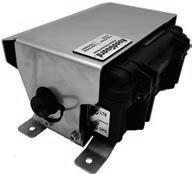
RoadGuard detects when severe road conditions are having an adverse effect on plant and equipment.
• Real-Time continuous monitoring
• Prompt Identification of road hazards
• Route optimisation and proactive maintenance
Zonex∞
Keeping a lid on dust
WHILE DUST MAY BE AN INEVITABLE PART OF MINING, THERE ARE SOME KEY MEASURES OPERATORS CAN TAKE TO HELP ENSURE WORKERS STAY SAFE.
Dust on a mine site can be more hazardous than it first appears. And excessive dust is more than just a nuisance; it can significantly impact air quality for workers who spend up to 10 hours at a time in these environments across the span of a shift.
According to Resources Safety and Health Queensland, exposure to harmful levels of respirable dust can lead to a range of lung diseases. These include forms of pneumoconiosis, chronic obstructive pulmonary disease, and lung cancer – collectively known as mine dust lung diseases.
The most well-known form of pneumoconiosis is silicosis, which is caused by exposure to silica dust.
So how can operations mitigate exposure to dust and
ensure their employees remain safe? A significant part of the answer lies in the legislation.
In 2021, the International Organisation for Standardisation (ISO) released the ISO 23875, a document that lays out the latest regulations for air quality in operator enclosures. ISO 23875 covers the lifecycle of a machine from design at the original equipment manufacturer (OEM) level or in the after-market space, and throughout its service life.
The standard requires the use of effective engineering controls, which are validated by performance tests of the cab.
ISO 23875 is the only standard that addresses the specific engineering control requirements necessary to achieve a low level of silica exposure in operator enclosures,
addressing air quality throughout the lifecycle of a machine.
“ISO 23875 is unique in the world of standards, as it was the product of 20 years of research and global collaboration between the best and brightest in the cab air quality space that included occupational hygienists, machine manufactures, end-users, regulators, researchers, and academics from 10 countries,” SyKlone International project lead ISO 23875 Jeff Moredock said.
“It is the roadmap to the future of cab air quality and compliance with the lowered silica exposure limit.”
Safe Work Australia also has limits around dust exposure.
The workplace exposure standard for respirable coal dust has been reduced from three milligrams per cubic metre (mg/m3) to 1.5 mg/m3.

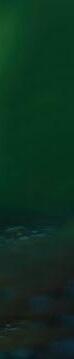
Keeping operators out of dust clouds is vital.
The new standard was agreed following an expert review commissioned by Safe Work Australia as part of efforts to provide workers better protection from the adverse health effects associated with dust.
As part of Safe Work Australia’s ‘Clean Air. Clear Lungs.’ campaign, operators are advised to take a stepby-step approach to managing risks. These include identifying hazards, assessing and controlling risks, and reviewing control measures.
“You should always aim to eliminate risks, as this is the best way to manage risk,” Safe Work Australia said.
“If you can’t eliminate risks, you must minimise risks so far as is reasonably practicable.
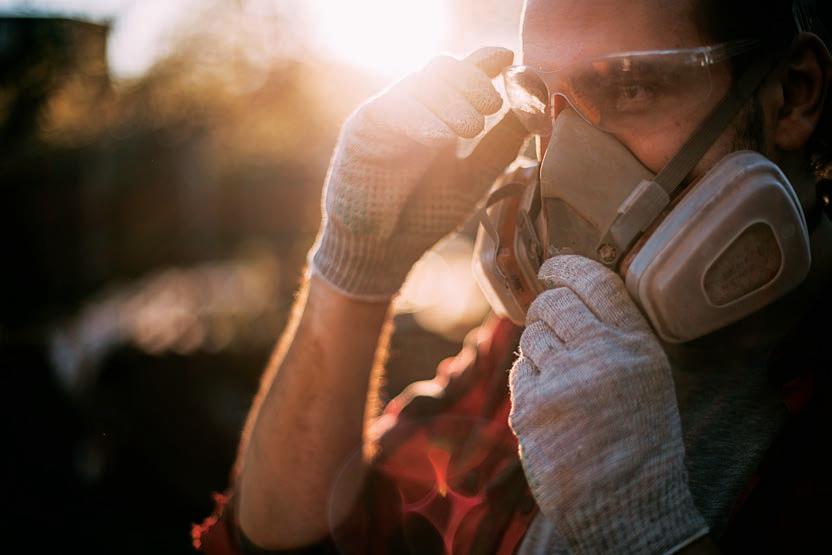
“Use the hierarchy of control measures to control risks and reduce exposure to hazards.”
According to Safe Work Australia, the highest level of protection
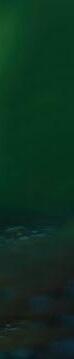

for eliminating risks such as dust is to substitute the hazard with a safer alternative. If this can’t be achieved, it’s recommended to reduce the exposure to hazards using administrative controls, and then use personal protective equipment (PPE).
A primary danger of respirable dust is its size. Smaller than a human hair, respirable dust can’t be seen with the naked eye, so people might not realise how much they’re inhaling.
Thankfully, modern mining techniques mean suppressing these tiny particles is easier than ever.

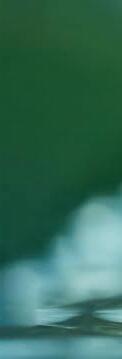
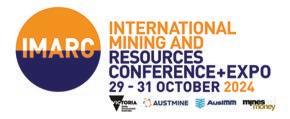
Properly fitted masking up can help miners stay safe on-site.
Feature Dust suppression
One way to mitigate dust exposure is by upgrading a mine’s engineering controls. Sprays on stockpiles, roads, machinery and cutting equipment wet the dust particles and make them heavier, forcing them to fall to the ground before they can be inhaled.
Adjusting ventilation rates for maximum efficiency is also recommended, as well as enclosing cabins where possible, ensuring seals are well-maintained.
Operator positioning also plays a part in keeping miners safe from dust.
The Queensland Department of Natural Resources and Mines recommends any task that has the potential to place coal mine workers on the return side of the shearer should be reviewed and controlled.
The department recommends pairing this positioning change with regular job rotation so an employee is not in the same space for an extended period of time.
While these measures, along with engineering changes and adherence to legislation, should be top-of-mind for mine sites, PPE similarly goes a long way in helping to keep miners safe.
“Before using PPE, you need to do a risk assessment to see what other controls can and should be used,” Safe Work Australia said.
“PPE should only be considered after implementing substitution, isolation, engineering and administrative controls.
“As [dust] particles are very small, workers should be provided with appropriate respiratory protective equipment [RPE].
“As everyone’s face is a different size and shape, there is no ‘one size fits all’ respirator. Fit-testing is essential to make sure the RPE works correctly and is comfortable to wear with other PPE that may be needed for the task.”
The New South Wales Resources Regulator advises mine operators review and verify the adequacy of their hazard management plan for airborne contaminants, including the hierarchy of controls, mine ventilation, and supply of PPE.
“Workers must utilise the lower order control of wearing … RPE to complement higher order controls in the workplace,” the regulator said.
“Existing and former mine workers are encouraged to attend periodic health screening and to contact their medical practitioner if they have any concerns about their respiratory health.”
For as long as mines have been extracting ore from the earth, they have battled dust. But by adhering to legislation, ensuring health and safety policies are relevant, and educating employees on how to stay safe in the face of dust, mine sites can go a long way to making sure their workers stay protected for longer.
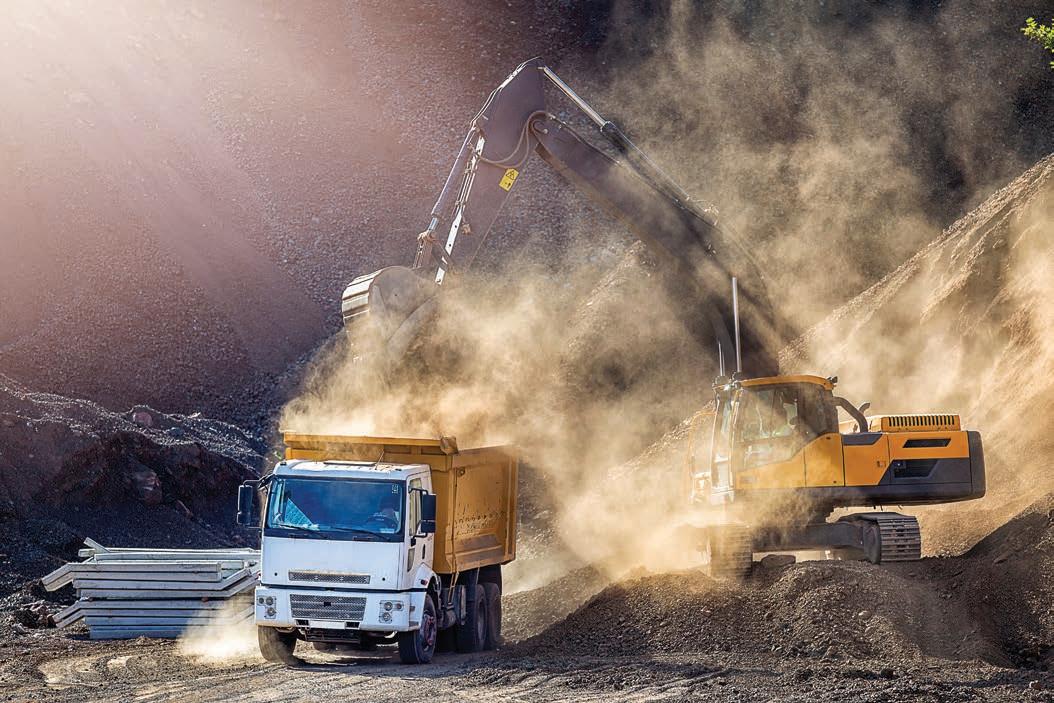

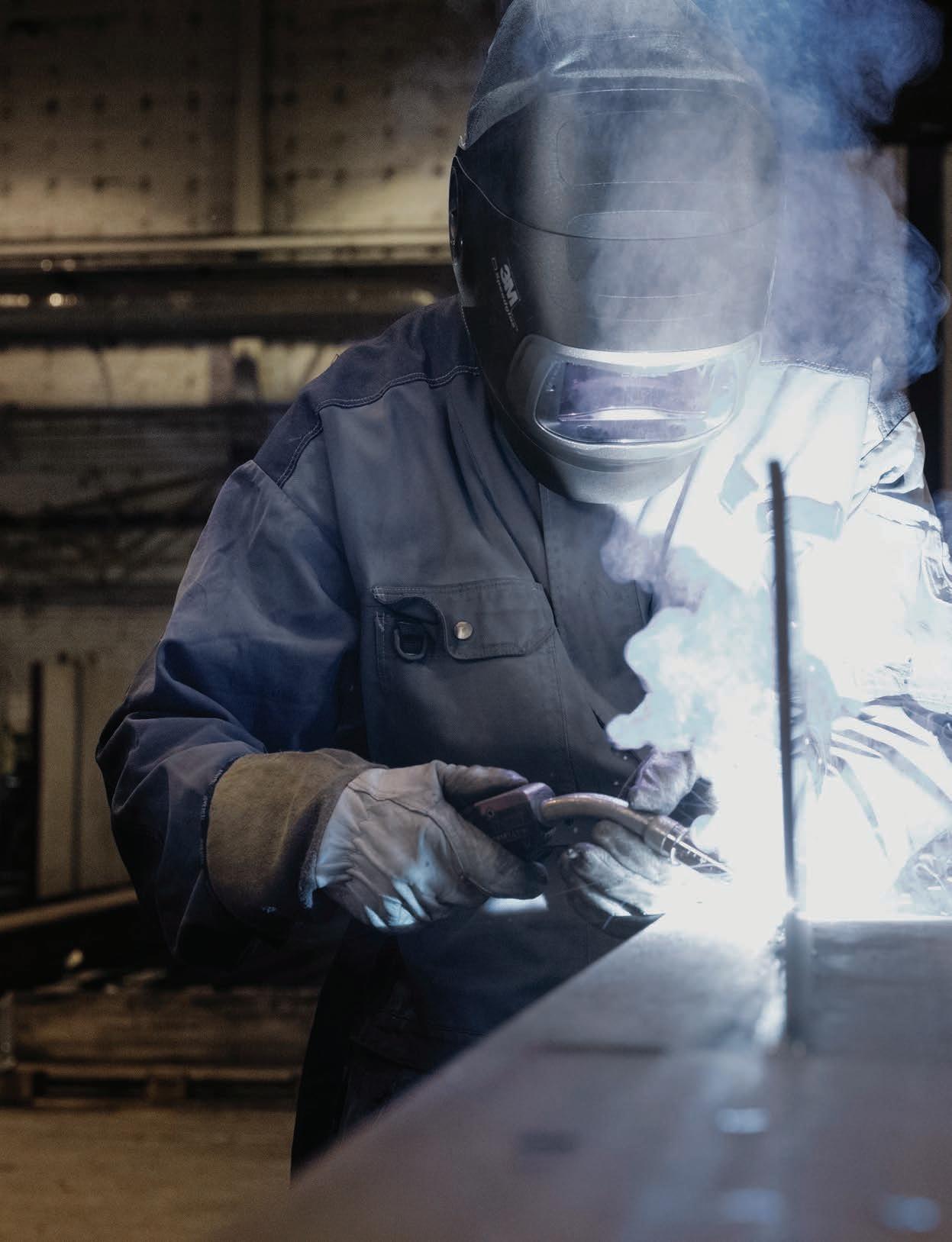
Dust is common on a mine site, but there are measures that can help workers stay safe.
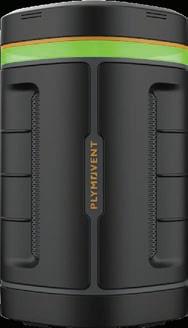



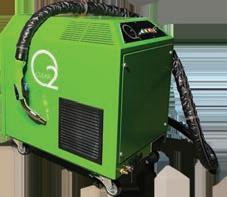
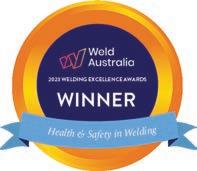
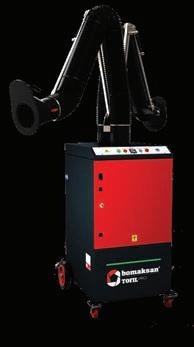
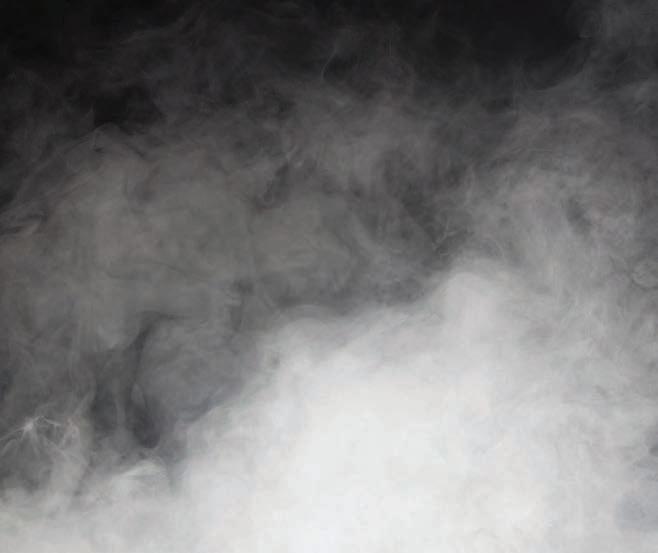
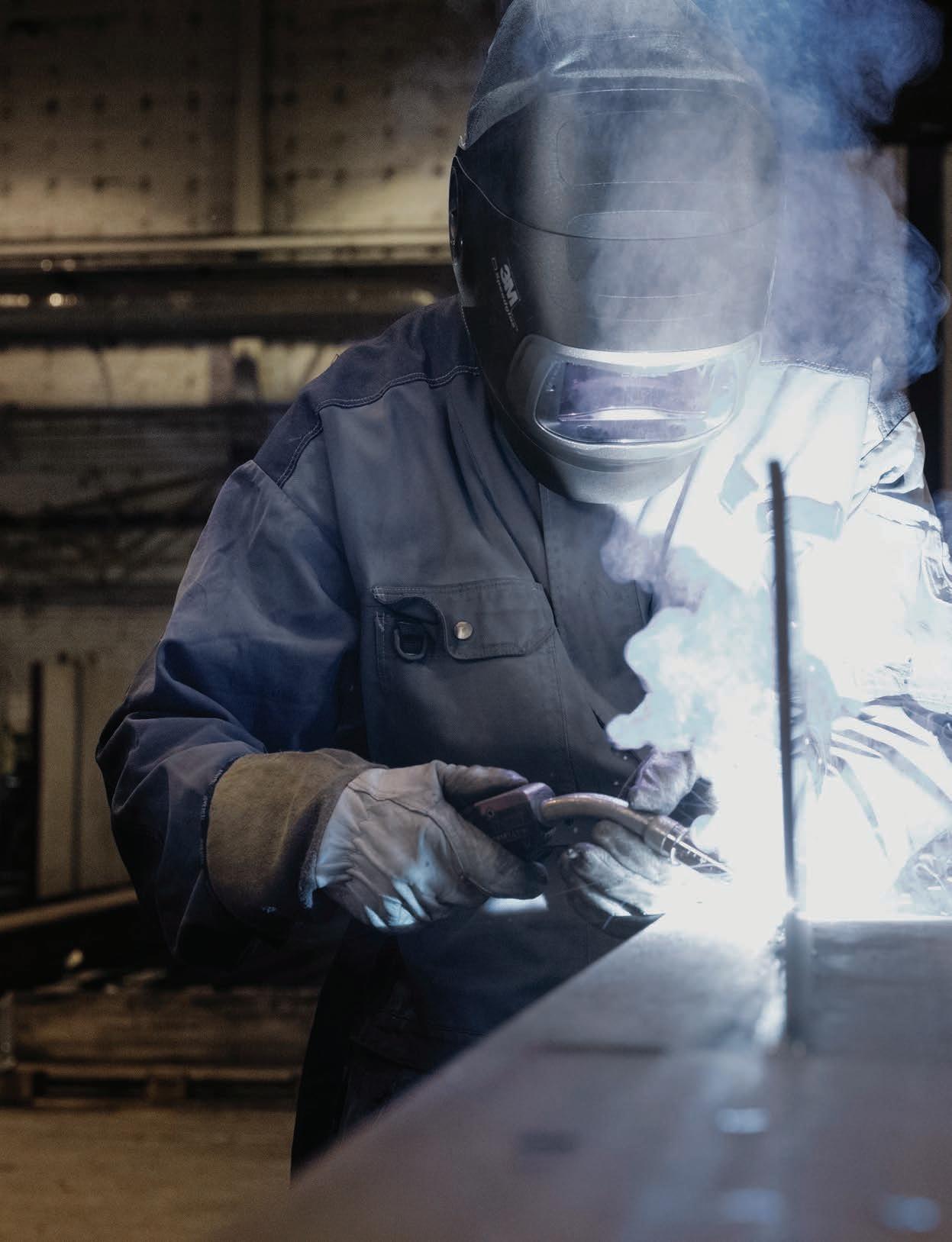
Controlling dust, boosting safety: Dust-A-Side Australia
DUST-A-SIDE AUSTRALIA WANTS TO LEAD THE CHARGE WHEN IT COMES TO SAFETY AND DUST CONTROL.
In the dynamic mining environment, ensuring safety via effective dust control is paramount.
Dust-A-Side Australia is one company aiming to be at the forefront of combating this challenge by leveraging decades of experience and a global network to deliver innovative solutions that prioritise health and operational efficiency.
The company’s approach to dust control goes beyond traditional methods like the application of water.
“The costs associated with relying on water for dust control can be quite high, not to mention the fact that wet roads create other dangers, including vehicle instability and slippage,” DustA-Side Australia managing director Shaun Cockman told Safe to Work.
Dust-A-Side Australia employs advanced dust suppressants with
binding properties, eliminating the need for constant re-watering and reducing the risk of slippery surfaces.
The company’s flagship suppressant – DAS Product – has been successfully applied around the world for more than four decades. This emulsion of bitumen in water is specifically designed and formulated to physically bind road materials together and suppress dust.
This method not only mitigates road damage and the formation of potholes but helps to enhance production efficiency by minimising downtime.
“Understanding that effective dust control requires a holistic perspective, we implement solutions across all stages of mining and construction processes,” Cockman said. “This includes not just haul roads but also production and processing plants,
where workers are directly exposed to dust in confined spaces.”
Dust-A-Side Australia’s standard and custom-designed dust suppression systems have proven to reduce respirable dust by over 80 per cent in key areas such as run of mine and tip areas, crushing plants, and stockpile feeds.
The company’s haul road maintenance programs and technologies have been found to reduce operational dust levels by more than 90 per cent.
“In a recent trial at an open-cut mine, we could demonstrate the efficacy of our HydroTac solution, for instance, which is a biodegradable dust binder,” Cockman said. “The project saw an average dust reduction of 80 per cent on service roads and 50 per cent on heavy vehicle access
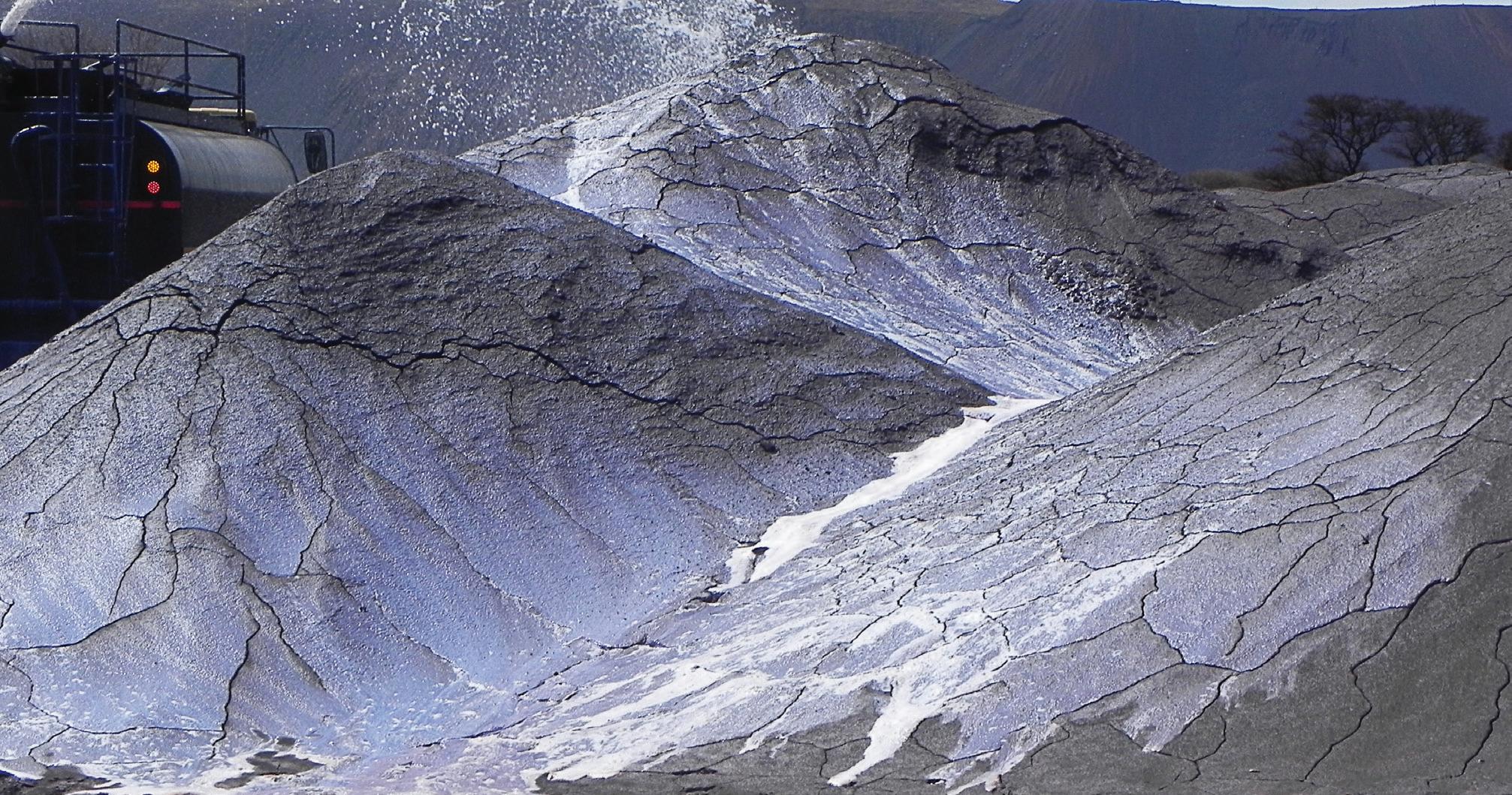
Dust-A-Side has solutions to reduce respirable dust in run of mine and tip areas, crushing plants, and stockpile feeds. Images:
roads.”
Cockman said Dust-A-Side Australia is able to help a site reduce equipment usage by 70 per cent, highlighting the operational efficiency and cost savings achieved.
“HydroTac not only reduced fugitive dust but also improved road performance and safety,” he said.
To further enhance dust control, the company uses next-generation monitoring software that enables the real-time analysis and identification of haul road defects.
This proactive approach is designed to ensure dust levels are consistently within safe limits, thereby protecting workers’ health and improving overall site safety.
Another standout technologies the company offer is its high-pressure dust suppression systems.
Unlike traditional low-pressure water sprays, these systems use a fine atomised mist to capture and subdue airborne dust particles. This includes

including PM10-sized dust, which are particles with a diameter of 10 micrometres or less, which means they are small enough to pass through the throat and nose and enter the lungs.
This method is highly effective, reducing PM10 dust levels by over 80 per cent and significantly improving both safety and environmental outcomes.
And the company’s commitment to safety extends beyond dust control.
Dust-A-Side Australia aims to ensure its clients can meet stringent occupational exposure limits for coal and silica dust, safeguarding the wellbeing of their workforce.
As part of Colas Group, DustA-Side Australia is supported by a strong upstream industrial network. Operating in 50 countries across five continents, the group carries out more than 50,000 projects each year with over 65,000 employees.
BME

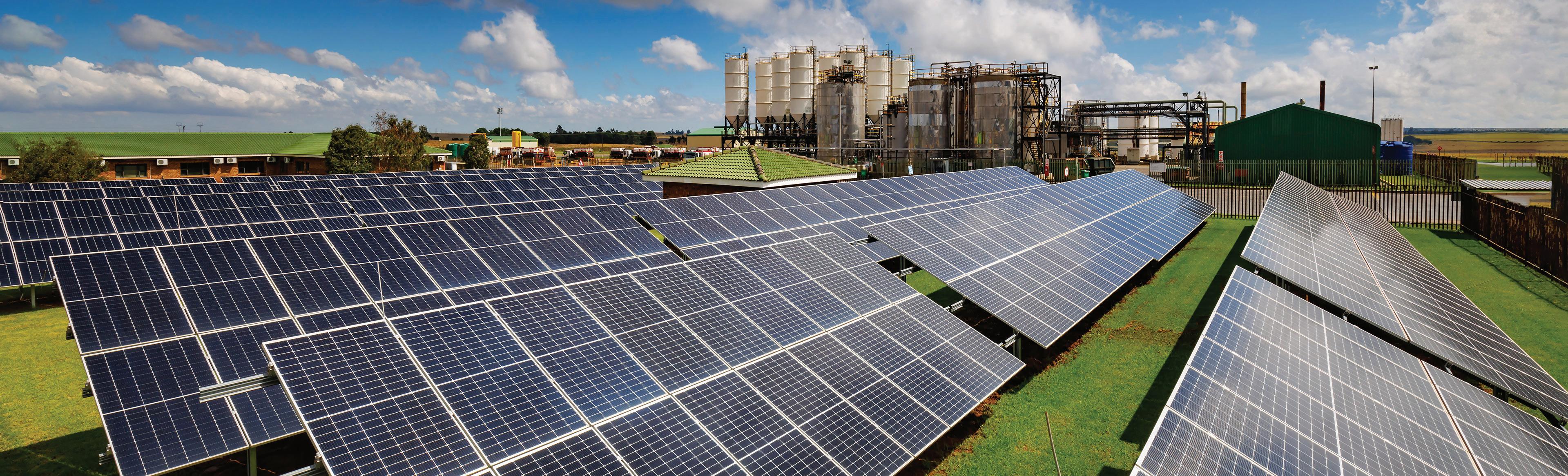

Dust-A-Side’s solutions have been found to reduce operational dust levels by more than 90 per cent.
Dust suppression
Precision blasting
BME TAKES A HOLISTIC APPROACH TO OPTIMISING ITS BLASTS TO LIMIT DUST AND FUMES.
Though mine blasting may look like a chaotic explosion of rock, the reality is very different. The process is a delicate and highly engineered one that involves balancing factors such as dust, fumes, noise and vibration.
Explosives and dust go handin-hand, but the technical experts at BME have blast design down to an exact science to minimise the impact on workers and the surrounding environment.
“It is a given that dust will be generated during blasting,” BME technical manager Hennie Van Niekerk told Safe to Work.
“The goal is to limit the height to which dust particles rise, as well as the distance they travel before falling to the ground.”
Blast design is a key step in the explosive process and takes into consideration factors such as increased stemming length, which is the length of inert material at the top empty part of the blast hole, and minimising explosives’ energy exposure to open air.
By designing blasts to restrict vertical displacement, the likelihood of rocks and dust being ejected high into the air is reduced.
“When rocks are displaced vertically, they tend to break into finer particles that contribute to dust,” Van Niekerk said. “Since dust particles are heavier than air, they will gradually fall back to the earth.
“By limiting the height that dust particles reach during the blast, these particles will remain within the blast zone, thereby reducing dust contamination over a larger area.”
But no matter how well a blast is designed, conditions on the day play a major role in a blast’s outcome.
Van Niekerk said a key question BME technicians ask themselves is, “what needs to be protected from dust pollution?”
“On blast day, wind speed and direction play a major role when initiating a blast,” he said. “The direction and distance to sensitive areas needs to be considered.
“It is essential to avoid blasting when the wind will blow dust towards the sensitive area.”
Some other considerations when looking to minimise dust when using explosives include limiting the size of the blast and reducing the charge per hole by drilling a greater number of smaller holes, providing better explosives distribution.
Ultimately, however, there is a balance that needs to be struck to ensure an optimised blast is achieved.
“There is a trade-off between controlled blasting, optimal blast results, and total drill and blast cost,” Van Niekerk said. “The objective is to find the acceptable balance between the three to satisfy all stakeholders and produce the optimal result.
“The customer need and environmental concerns will be considered during the blast design phase to produce a result that conforms to operational requirements and minimising environmental impact.”
While dust is a key consideration in BME’s designs, NOx (nitrous oxide) fumes are another critical aspect of the blasting process to which the company’s technical experts are particularly attentive.
The release of fumes during blasting in mining operations primarily occurs due to the chemical reactions involved in detonating explosives.
The ideal detonation results in complete combustion, producing relatively harmless gases such as

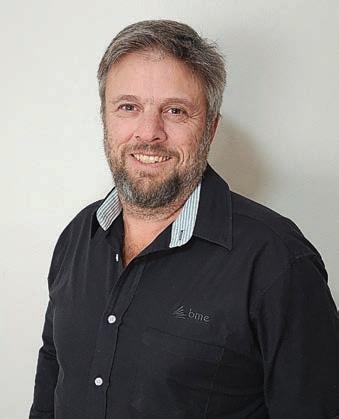
or partial detonation, resulting in the production of these harmful gases.
If the detonation environment lacks sufficient oxygen, not all fuel in the explosive may burn completely, leading to incomplete combustion.
In addition, improper mixing, the condition of the explosive, the method of initiation, temperature
BME technical manager Hennie Van Niekerk.

The goal in blasting is to limit the height to which particles rise.

eliminate the risk of fumes before the explosion begins.
Typical explosives content includes ammonium nitrate and diesel in its make-up due to these being relatively safe to handle and transport compared to other
explosive systems. But ammonium nitrate by itself is not waterproof, with moisture quickly breaking down its chemical composition, leading to a combustion imbalance.
The technical experts at BME developed a solution to this common issue – a dual-salt emulsion system containing ammonium nitrate and calcium nitrate. Together, these salts create an improved water and thermal resistance.
BME international systems and field services manager Tom Dermody said the company’s dual-salt emulsion is a powerful explosive that is less harmful to the environment and worker health.
“These emulsions create a more stable and efficient explosive material,” Dermody told Safe to Work
“The combination of these salts provides high energy output and improves rock fragmentation during blasting, resulting in superior blast performance.”
Not only does this create a more powerful blast but BME is also able to increase the efficiency of its explosions, with benefits to health and the environment.
“As a dual-salt emulsion system, BME’s explosive is more environmentally friendly and produces fewer toxic by-products due to its efficient detonation properties,” Dermody said. “BME’s dual-salt emulsions offer enhanced performance and increased safety, making them suitable for challenging and diverse environments.”
Combined with BME’s extensive dust suppression measures and condition monitoring, the solution has been making waves in the mining industry.
Whether it is designing blasts down to the smallest of factors or developing solutions to material challenges, BME is helping operators extract the ore they seek while keeping workers and the environment safe.
BME international systems and field services manager Tom Dermody.
A greener path
ECO-ROAD HERO IS ON A MISSION TO PAVE A SAFER, GREENER, LESS DUSTY ROAD ON THE WAY TO THE AUSTRALIAN MINING INDUSTRY’S ENVIRONMENTALLY CONSCIOUS FUTURE.
Eco-Road Hero director Ivan Heron knows dusty roads.
With a career in one of Australia’s largest mining companies spanning almost a quarter of a century, Heron has seen his fair share of dirt roads become all but invisible thanks to the plumes kicked up by massive haul trucks.
But when it comes to dust, compromised visibility is just one of the dangers faced by Australia’s miners. Poor air quality can have major impacts on worker health, especially over an extended period of exposure.
This ongoing problem inspired Heron to found Eco-Road Hero and become the Australian distributor of dust-suppression solutions from Canadian-based Cypher Environmental.
These solutions include the likes of Dust/Blokr and Road//Stabilizr, which are offering operators a green, dualaction solution to mine-site dust woes.
“Dust/Blokr is a formulation of sugars and starches made from 95 per cent renewable materials,” Heron told Safe to Work. “That’s what initially drew me to Cypher Environmental’s products, which provide a groundbreaking alternative to traditional road salts that leaves zero environmental impact behind.
“The product is added to a water truck and sprayed on the surface of a dusty road, creating a far more effective suppressant than water alone.”
Dust/Blokr’s semi-soluble nature minimises the need for frequent reapplication, helping to maintain dust
control even in challenging conditions like heavy rainfall or dry spells on any soil type, including gravel roads.
Road//Stabilizr, on the other hand, aims to tackle dust at the source as a long-term soil-stabilisation solution for roads that require continual maintenance due to wet weather and marginal road materials.
“Road//Stabilizr a biodegradable, non-toxic, non-corrosive biological catalyst-based product mixed into dirt when roads are being made, particularly those made with higher amounts of clay,” Heron said.
“The combination of catalysts and other ingredients makes the clay stronger and work to keep water out, creating a stronger, more reliable base less likely to kick up dust.”

Dust/Blokr in action.

If a road is in bad shape, a fleet’s fuel consumption can easily increase by thousands of litres a year.
“Cypher Environmental measured fuel consumption before and after the implementation of its products at a major coal mine overseas producing over 20 million tonnes of coal per year,” Heron said. “The mine reported that they have saved 17.4 per cent in fuel. With increasing diesel prices … not only did they see massive fuel savings, but dust in the pit was reduced by over 50 per cent.”
With mines across Australia striving to meet higher environmental standards by reducing dust and fuel consumption, Heron said Eco-Road Hero can help operators take the next leap.
“These products are so gentle on the environment they’ve been used in the Canadian Arctic, where people rely on foraging for food,” Heron said.
“They’re also hugely popular for dust suppression in thoroughbred racing and other sensitive settings like the Alpine Shire. Dust/Blokr, for example, has been approved by the stewards in NSW horse racing due to the fact it has no impact on the health or performance of the equine athletes.”
Since launching Dust/Blokr and Road//Stabilizr in Australia, Eco-
Road Hero has continued to broaden its focus.
“Instead of simply providing these game-changing products, EcoRoad Hero can provide consultation in road design and ongoing road maintenance,” Heron said.
“A mine’s dirt roads can be a bit of an area of lower operational focus, but our mission is to show operators the huge benefits that can come from taking a proactive approach.”
Eco-Road Hero has seen success across a range of industries, but mining is where the company is keen to focus its energies into the future.
“A major Victorian gold mine has seen great success with Dust Blokr,” Heron said. “The main access to their plant is about two kilometres of dirt road, so you can imagine it gets a lot of traffic.
“The operator has been very happy with the product’s performance, and we’ve been able to satisfy their environmental expectations and save them costs on fuel and maintenance.”
As it does with all customers, EcoRoad Hero provided the gold mine with a ‘technology transfer pack’, which details every aspect of its product’s application, from the ratio of Dust/Blokr to water to the speed at which water trucks need to drive along the road to optimise its performance.
Heron said it is essential that customers have the correct procedures in place to get the most out of Eco-Road Hero’s offering for years to come.
“Part of our package is providing ongoing support to our customers, meaning we regularly check in on the product’s performance and collect data on how the road is tracking,” he said. “That way we can help operators save costs, protect the environment, and keep their workers safe into the future.
“It’s all part of our mission to bring safer, greener, more accessible solutions to Australia’s mines.”

Dust/Blokr is a formulation of sugars and starches made from 95 per cent renewable materials.
Dust/Blokr is added to a water truck and sprayed on the surface of a dusty road.
Dust suppression
Ensuring smooth operations
JSG INDUSTRIAL SYSTEMS IS BOOSTING EQUIPMENT LONGEVITY THROUGH THE DISTRIBUTION OF SKF’S SINGLE-LINE AND PROGRESSIVE LUBRICATION SYSTEMS.
Mining companies are always looking for ways to maximise equipment lifespan and minimise downtime, and this is especially true in remote working areas that contain high dust levels.
To help boost equipment durability when working in these kinds of environments, miners can utilise an automatic lubrication system that distributes lubricant to moving parts such as bearings, pins and bushings to reduce friction between surfaces that rub against each other.
When the bearing and seal manufacturing company SKF acquired Lincoln in 2010, it combined more than 300 years of experience in managing lubrication and reducing friction and wear. The acquisition led to SKF taking over Lincoln’s international distribution channels, which included Australianbased JSG Industrial Systems.
JSG Industrial Systems product sales manager – lubrication equipment Branco Zivic told Safe to Work that automating and monitoring lubrication informs preventive maintenance and planning, helping to ensure worker safety while minimising unplanned downtime.
“A lubrication system eliminates the need to access hazardous areas to manually lubricate equipment including conveyors, conveyor shuttles, belt feeders, screens, crushers and mills,” Zivic said.
JSG distributes SKF’s automatic single-line and progressive lubrication systems to a range of industries.
SKF’s single-line lubrication systems involve a central pump station that automatically delivers lubricant through a supply line to the metering device.
Backed by integrated system control and monitoring capabilities, each metering device serves only one
Automatic lubrication systems distribute lubricant to moving parts of machinery.
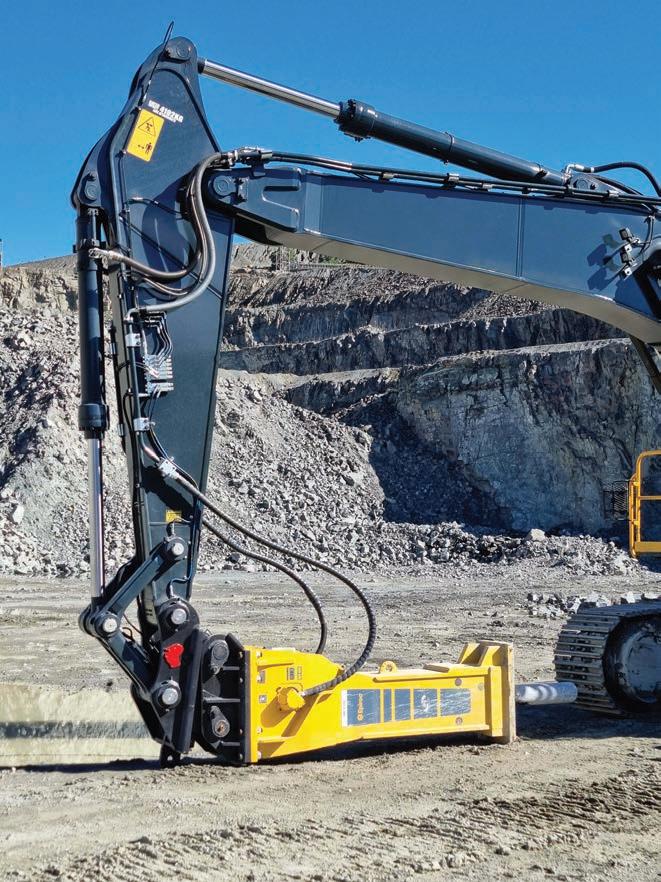
“The single-line lubrication systems are reliable, simple to install and maintain, with an easy system expansion,” Zivic said.
“They are suitable for almost all lubricants and can pump long distances and, within a wide temperature range and system, continue to operate if one point becomes blocked. Injectors are also available in preset and adjustable models for defined or customised metering.”
to a metering device. This provides continuous lubrication while the pump is operating.
“The progressive lubrication systems provide easy system monitoring and simple blockage control, as well as integrated system control and monitoring,” Zivic said.
“They are also effective in harsh environments that are dirty, wet or humid, while having the ability to work temperatures from -40 to 70º Celsius.”
Images: JSG Industrial Systems
According to Zivic, SKF’s automatic lubrication systems have been a hit with customers.
“One quarrying customer was converted from manual lubrication when he saw first-hand the result of the automatic lubrication systems on his equipment,” Zivic said.
“The system worked well in providing a seal on his pins and bushes, as well as providing lubrication as he used the equipment. It also served to provide a barrier to sand and dirt ingress into his pins, providing gains in machine availability and reduced his overall maintenance costs.”
With so many products and brands on offer, JSG is dedicated to providing its customers with the finest aftermarket support.
“In each of the geographic areas we support, we have a network of carefully selected platform partners,” Zivic said. “These qualified professionals provide
local area support to all our valued end-user customers.
“Each platform partner has access to our online system, which gives them 24–7 visibility of service sheets and technical libraries that may be required in the lifetime of your product.
“Once systems are installed and commissioned, our platform partners
assist with ongoing training, servicing, upgrades and maintenance.”
JSG’s portfolio means it can find the right product for the right application.
“The extensive research and development capabilities of SKF ensures we have the latest innovations as we move into a smart product era of connectivity and wireless technology,” Zivic said.

TRACKED CARRIER.
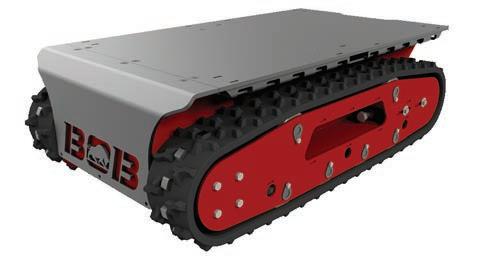

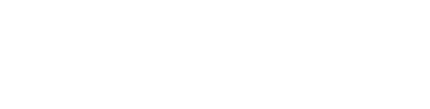










Automatic lubrication systems help ensure worker safety.
Dust suppression
Next-level dust detection and measurement platform
WATERGASRENEW’S NEW CONDITIONMONITORING RANGE CAPTURES REAL-TIME DATA IN
ONE EASY-TO-USE PLATFORM.
Harmful particles don’t exactly knock on the door before making themselves known. By the time a worker begins to cough, dust might have already begun to cause damage.
Evolving air quality standards mean the Australian mining industry needs to be on the front foot when it comes to compliance. That’s why operators need proactive controls like real-time alerts when dust reaches harmful levels.
WaterGasRenew (WGR) has announced a new range of products designed to monitor and provide operators with critical information regarding equipment in harsh, dusty, and heavy industries.
“We are thrilled to introduce our groundbreaking dAlert product range,” WGR chief executive officer Bob Dixon told Safe to Work. “Our commitment to providing innovative solutions for our customers has driven us to focus on a range of products that address the unique challenges faced by heavy industries.
“By offering plug-and-play capabilities, we are simplifying the process of data collection and analysis, empowering our clients to achieve new levels of safety and efficiency.”
WGR’s dAlert range of products offers an integrated platform of sensors that communicate to deliver
a one-stop shop for air quality data. The platform tracks critical factors like CO2, gas, Air Quality Index, particle size, concentration and count, humidity, air pressure and temperature to offer operators a complete view of working conditions.
As soon as the platform detects a workplace environment that needs attention, dAlert’s monitors send warnings to operators, supervisors and workers. Anyone with access can quickly zero in on areas of concern or specific particle counts, with dAlert providing in-depth data on particles of less than half a micron.

becoming a go-to resource for operators looking to evaluate and monitor workplaces to keep people safe and healthy in dusty environments.
“dAlert is perfect for any heavyduty industry, from construction to quarrying,” Dixon said.
“But the mining sector is our major focus, where we believe will achieve great results in helping operators successfully monitor air quality.”
dAlert is the culmination of four key products capable of harnessing the power of complete condition-
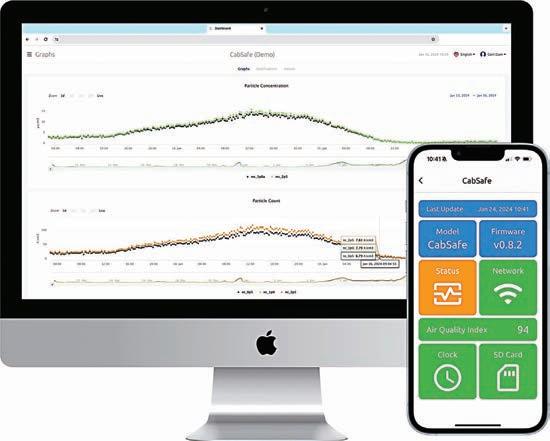
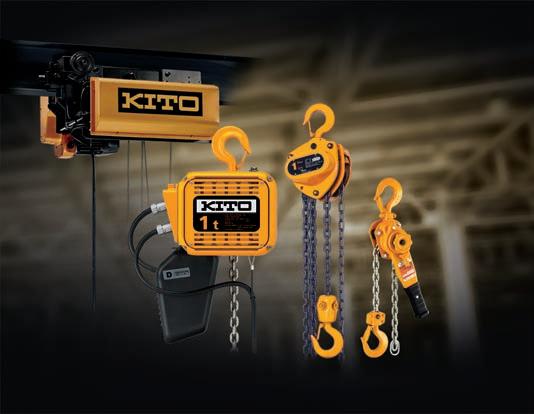
Under the dAlert umbrella, Zonex can work alone or with its companion products iDat, RoadGuard and Enginex to offer safer, more efficient operations.
The dAlert platform tracks critical factors to offer operators a complete view of working conditions.

workplace, that monitors changing air particulate levels in real-time applications like machine run-time hours, pressures and data meshing,
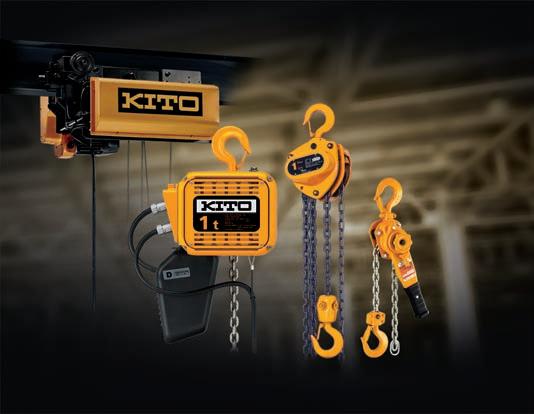
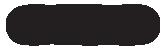
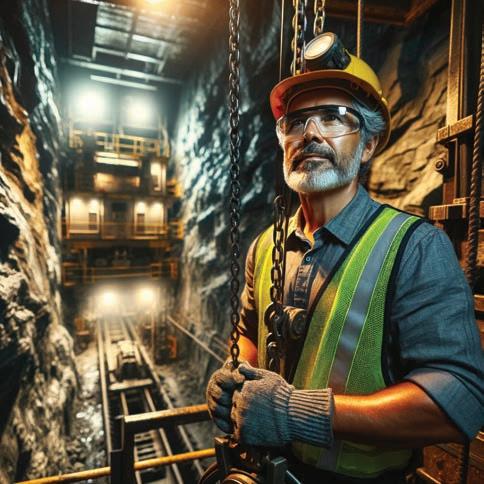
as well as vibration, temperature and noise measurement.
Enginex is an advanced airsampling device that protects diesel engines by measuring dust particulate quantities in the engine intake air. Like Zonex, Enginex provides realtime filter performance insights, ensuring proactive monitoring against contamination.
RoadGuard is a unique device that detects when severe road conditions are having an adverse effect on plant and equipment. A key feature of this device is its ability to log a GPS location and photograph the road condition to enable rapid rectification.
WGR’s product range, as well as the dAlert platform, can be tailored into a configuration suited to any operation.
“Quite often when you buy equipment to record data or information, there’s a lot of integration required, and the equipment itself has its own systems which need to be
Dust suppression
considered when you try to integrate other equipment,” Dixon said.
“The beauty of the dAlert products is that they’re all plug-andplay; there’s not a significant amount of time you spend in terms of systems or data integration.”
Today, dAlert is a sophisticated, interconnected range built to tackle any mining condition challenge, but the platform’s rapid expansion started with a single idea.
WGR quickly found that Zonex, a “tiny-but-mighty” device that fits in the palm of a hand, was capable of more than had ever been anticipated.
“Workers could be in dusty or enclosed environments for more than 10 hours a day, exposed to a whole range of changing conditions like dust, temperature, humidity and vibration,” Dixon said.
“By passing air from a workplace environment through the Zonex device, we are able to give workers critical information instantly.”
As word about Zonex got out, WGR was suddenly being asked to implement the device in all sorts of applications to measure dust.
Some of these applications saw Zonex bolted to the back of a truck, where it measured plumes of dust coming off the truck’s tyres, mounted inside electrical enclosures and monitoring workplaces and specific activities to assist in work method redesign.
“It’s certainly becoming a useful compliance and measurement tool,” Dixon said. “By using Zonex’s GPS and getting the readings off each unit mounted on the trucks, we can mesh together all the readings and warn the mine when there is an exceedance so they can implement dust suppression measures like wetting down specific areas of the haul road.”
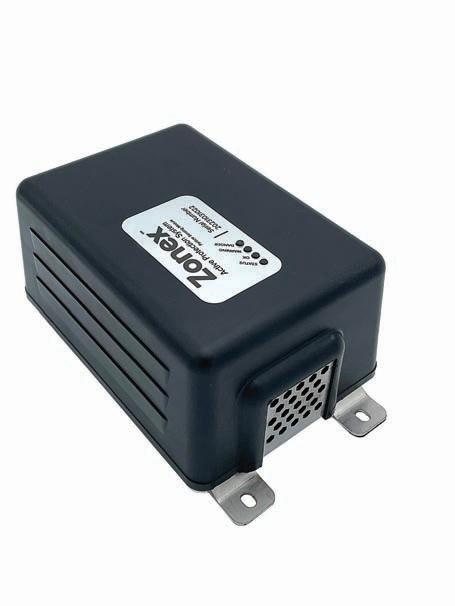
Because the unit can have either a permanent power supply for fixed applications or battery power, it can be easily repositioned to measure multiple locations quickly when determining dust origins, impact of extraction, or dust dispersion systems.
Under the dAlert umbrella, Zonex can work alone or with its companion products iDat, RoadGuard and Enginex to offer safer, more efficient operations.
WaterGasRenew’s Zonex monitors changing air particulate levels in real-time and provides alerts when thresholds are exceeded.
“When foreign particles get into equipment, it leads to machinery breakdown, downtime in productivity, and heavy maintenance costs,” Dixon said.
“The solutions we’re bringing out are designed to provide the intelligence to be able to monitor the safety of the operator, but also look at the efficiency and reliability of the equipment to minimise downtime and increase and improve productivity.”

“As we talk to customers, we learn more about what their requirements are and incorporate those into new development we undertake,” Dixon said. “We want to know our customers’ pain points and challenges, and work with them to come up with the right solution that will help them solve the issues they’re facing.
“The feedback we’ve had from customers is that we’re not just solving their initial problem but the versatility of products like Zonex is providing solutions for a range of other challenges they hadn’t anticipated.”
With air-quality regulations continuing to ramp up across Australia, it’s solutions like Zonex that are helping operators step into a new era of technology-driven safety and efficiency.
“By taking a holistic approach to condition monitoring, we can offer a simple, accessible, cost-effective solution to the challenges arising from excessive dust and decreased air quality,” Dixon said.
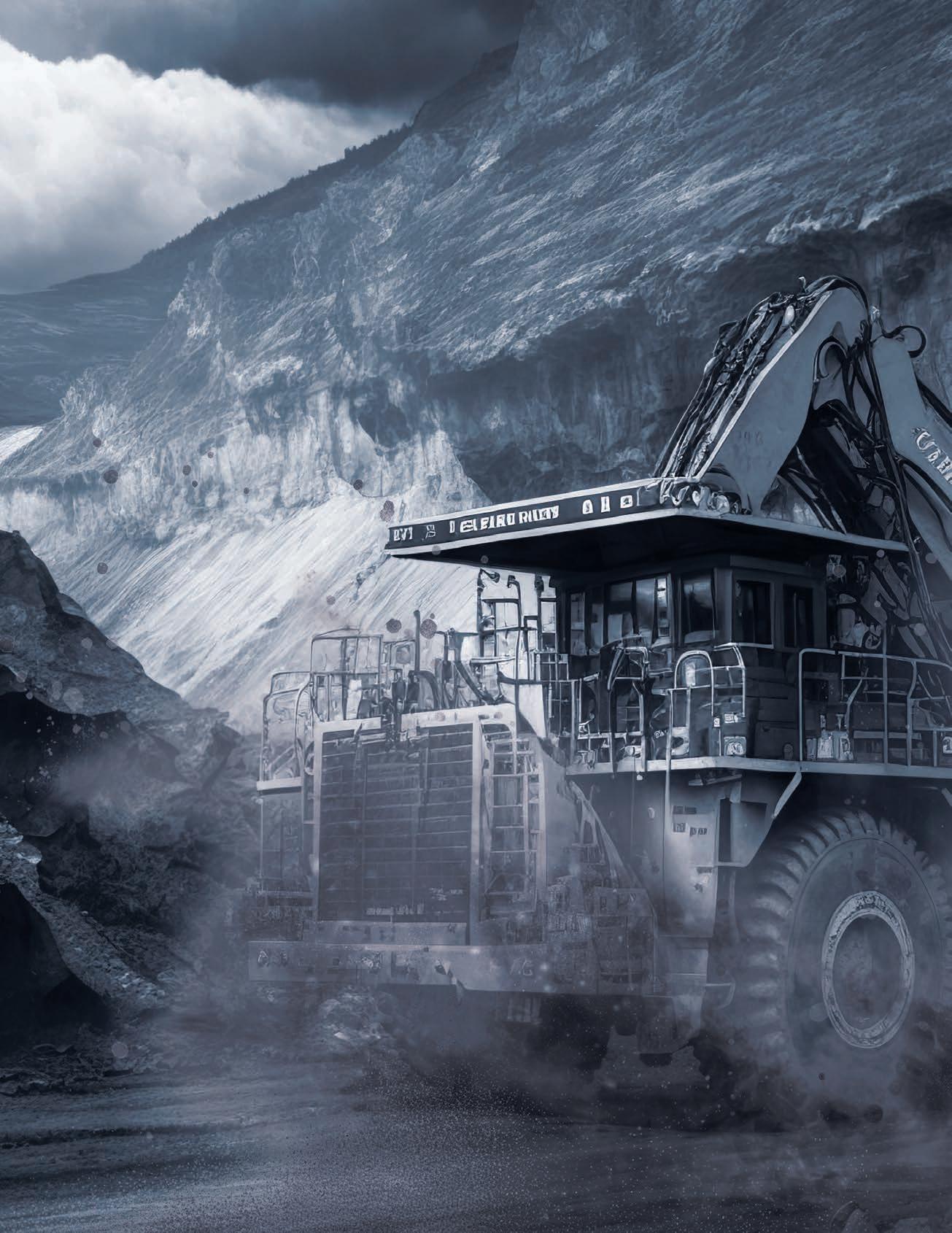
As word about Zonex got out, WGR was suddenly being asked to implement the device in all sorts of applications to measure dust.
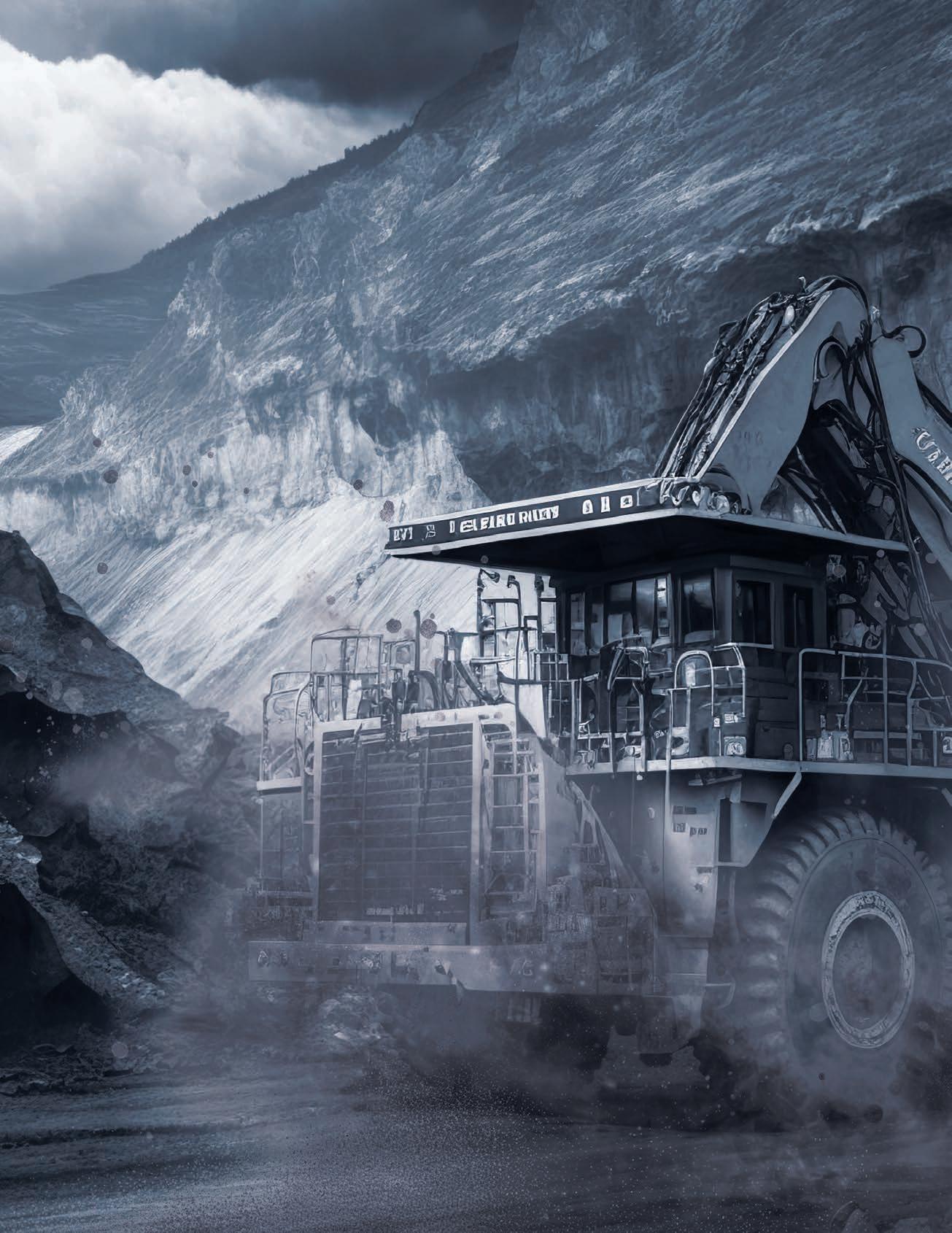
Protect heavy mobile equipment operators from Black Lung, Silicosis and other lung related occupational diseases.
ISO AS 23875
STANDARD FOR CAB AIR QUALITY
ISO AS 23875 is an international standard that creates a consistent approach to designing, testing, operating,and maintaining operator enclosures with respect to air quality.
United Safety operates and distributes the Sy-Klone product across Australia on a national scale. For enquires, please contact us at:
P: 1800 424 889
E: sales@ussc.com.au
W: unitedsafteycorporation.com.au
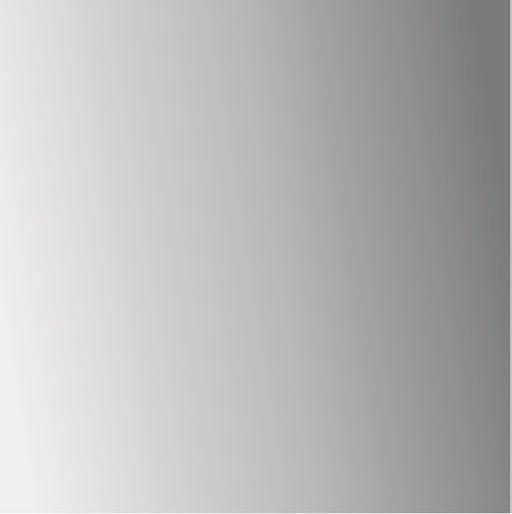
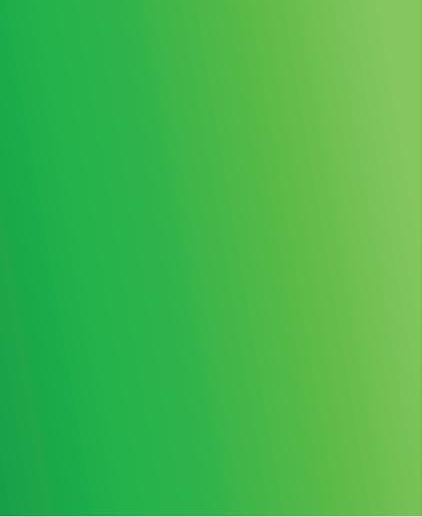
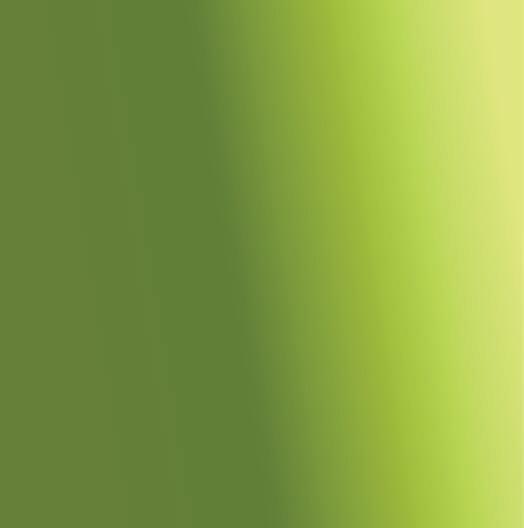
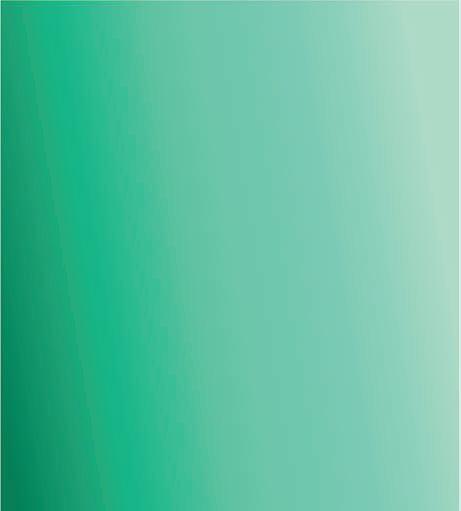
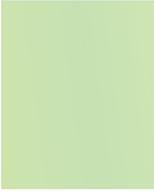
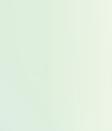
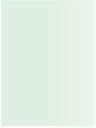
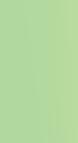
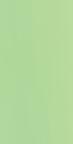
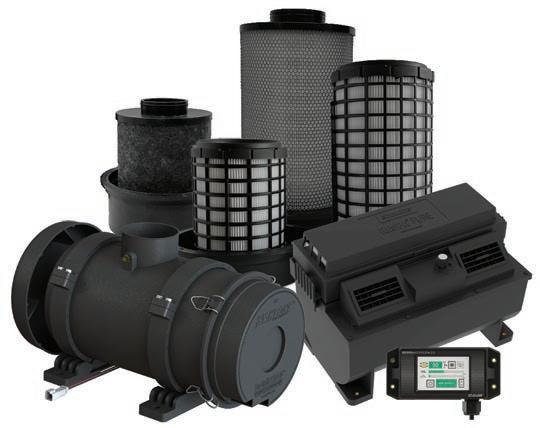
Dust suppression
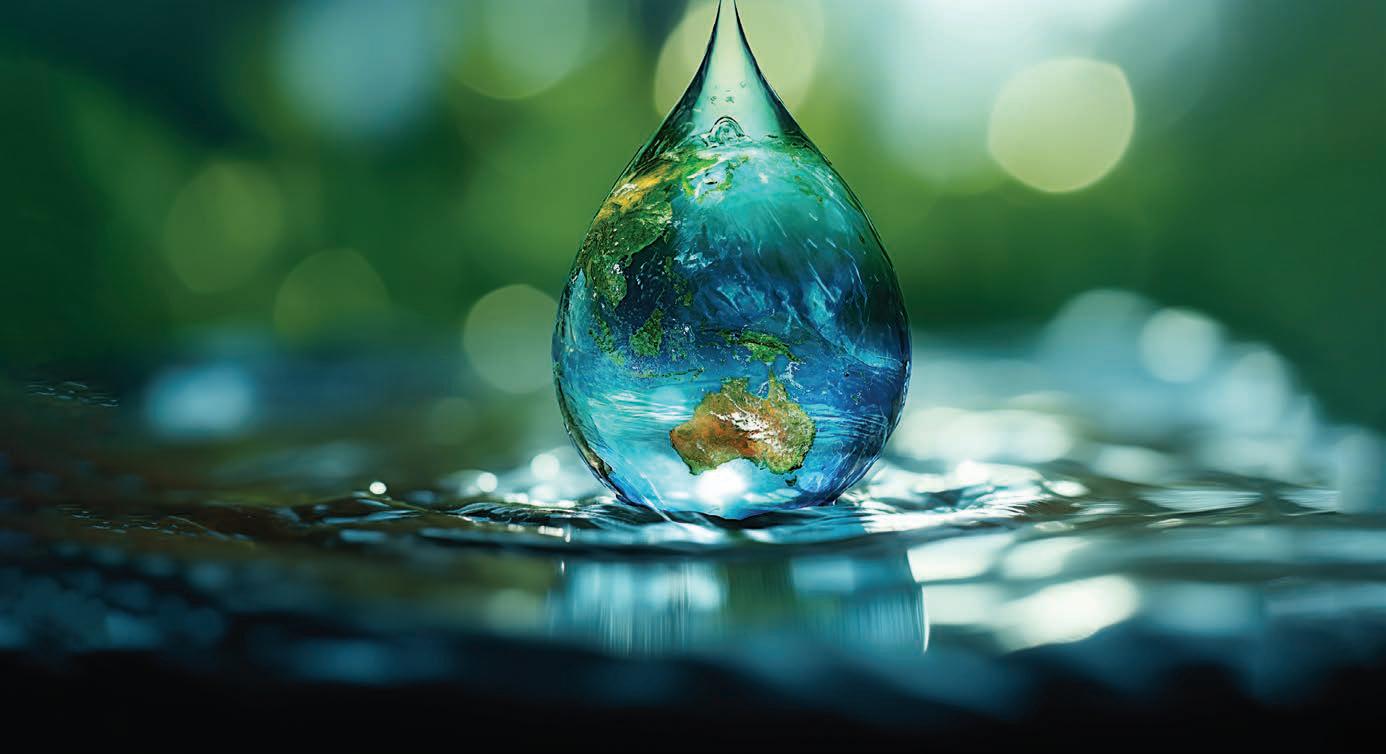
A natural way to improve performance
BIND-X IS BRINGING A DUST CONTROL SOLUTION TO AUSTRALIAN SHORES THAT COULD SAVE MEGATONNES OF CO2.
As issues like water scarcity and overuse are becoming more prevalent, mining companies across Australia are looking for solutions to cut back unnecessary usage.
A major source of water usage on a mine site comes from spraying down haul roads to reduce dust. Though reducing dust is essential, and a safety, efficiency and legislative requirement, using water alone is only temporary, and can be costly and inefficient. According to Bind-X founder and chief executive officer Martin Spitznagel, more than 70 per cent of Australian mines still only use water to control dust on their roads, a situation he calls “unnecessary”.
“It is also unnecessary to rely on dust control solutions with a high environmental impact while striving for more responsible practices,” Spitznagel told Safe to Work. “In 2021, polymeric and petroleum-
based emulsions accounted for approximately 70 per cent of the Australian dust-suppressant market.
“That stands in contrast to the mining sector being under increasing pressure to reduce carbon emissions and enhance environmental performance.
“This is where Bind-X can make a difference for Australian mines. We have developed a portfolio of biological dust solutions that help mines save up to 90 per cent of water that they would otherwise use for dust suppression but with no environmental downsides.
“It further reduces operational costs and contributes to the industry’s decarbonisation goals.”
Bind-X is a biotech company specialised in developing and producing biological binders. Its mission is to improve sustainability of the mining industry with biotechnology, and Spitznagel said the
company is primed to save Australia’s mines megatonnes of CO2.
“Bind-X’s biological dust control portfolio is engineered to meet the different specifications of tackling dust on heavy-trafficked haul roads, on secondary roads with lower traffic, and on stockpiles and tailings,” he said.
But what exactly are biological binders?
“In short, they are a new category of dust control products and a proven alternative to polymers, bitumenbased products, chlorides and lignin sulfonates,” Spitznagel said.
Bind-X’s biological binders utilise a process found in nature where a bio-geochemical process solidifies the soil matrix. Applied on mining roads, it creates a solid layer as hard as cement but with adapted material properties.
Spitznagel said the process is as environmentally friendly as it is effective.
Bind-X aims to help Australian mines reduce their water consumption.
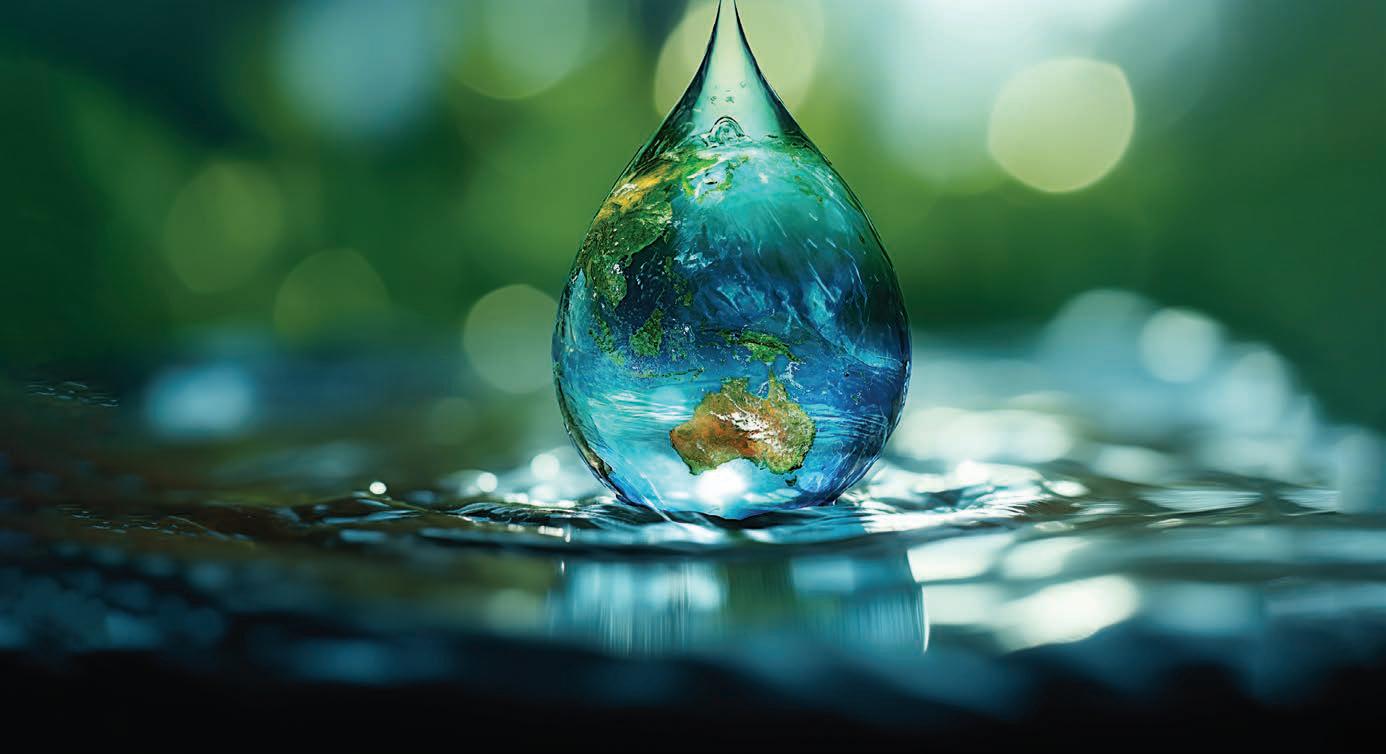
“As a result, even the finest fugitive particles are trapped and bound, which is especially vital in addressing harmful fine dust and combating silicosis and other respiratory diseases,” Spitznagel said.
Together with its clients, Bind-X first analyses the biggest sources of dust within operations and puts that in relation to environmental conditions and existing equipment.
Further collecting non-confidential information (such as fuel cost) will enable Bind-X to calculate the direct benefits of using Bind-X products regarding improvements on water, cost and CO2.
The company’s operational team then recommends the most suitable product from the Bind-X portfolio, and the best form to deliver the product to site and apply.
“What makes our products unique is that they combine superior performance with no downsides to the environment,” Spitznagel said.
“Their new mode of action leads to improved application frequencies and therewith tangible water and diesel savings and thus CO2 improvements.

“For instance, with our primary road product, we want to offer the industry for the first time a proven
is the complete opposite,” Spitznagel said. “It is 100 per cent biodegradable over time, and is completely non-toxic to workers, animals and plants.”
Bind-X has been working with Australian partners for the last two years and is currently establishing a local presence and team.
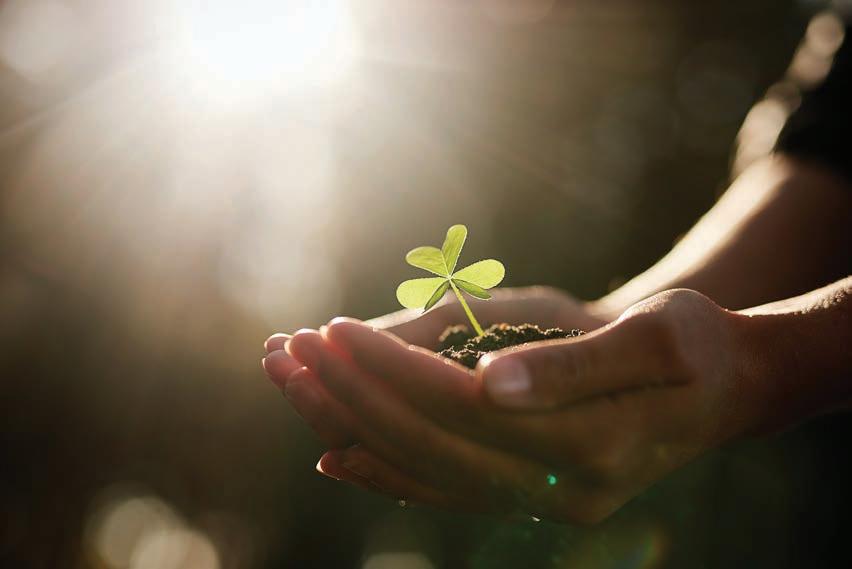
Bind-X’s mission is to improve sustainability, profitability and innovation in the mining industry.
“In the first quarter of 2025, we will have our production facility in WA running to deliver Australian-made products with shortened lead times,” Spitznagel said. “We will also enter the best partnerships in logistics.”
Part of that service is Bind-X’s commitment to delivering ongoing operational support to its customers, assisting them to get the maximum value out of their infrastructure.
The company is bringing with it an established footprint overseas, having recently won the Eramet Responsible Mining Challenge for a solution it implemented at an African mine.
The Eramet Responsible Mining Challenge is an initiative to reward innovative technologies that bring industries closer to net-zero goals.
According to Bind-X, the mine at which its biological binder was implemented saw dust fallout cut by two thirds, an 85 per cent reduction in water usage, and a 94 per cent reduction in CO2 emissions linked to its previous dust-control measures.
“Our team is ready to assist Australian mines to implement our new way of dust control and transition towards more sustainable mining,” Spitznagel said. “It’s about sharing our knowledge for substantiable practices in road construction.”
Bind-X’s solution creates a solid layer on mine roads as hard as cement.
Dust suppression
United on a clean-air front
UNITED SAFETY AND SURVIVABILITY CORPORATION IS A PRODUCT PARTNER OF SY-KLONE INTERNATIONAL TO HELP PROTECT AUSTRALIA’S MINERS FROM THE HAZARDS OF RESPIRABLE DUST.
Since its launch into the mining sector in 2004, United Safety and Survivability Corporation has been on a mission to take the industry’s safety standards to the next level. In partnership with SyKlone International, United Safety and Survivability is doing just that thanks to the Sy-Klone Cab Air Quality system.
The system works by drawing air into a powered pre-cleaning filter and pressuriser, where any debris is ejected to deliver fresh, clean air into an enclosed cab on a mobile plant.
Designed for dust-heavy mining environments, the system alerts the operator to changes in pressure, CO2 and particulate concentration, or when the filter needs to be changed in order to keep the solution working as effectively as possible.
“One of the biggest benefits of the system is its ability to dramatically reduce the egress of dust into the cabin,” United Safety and Survivability
United Safety and Survivability supplies
general manager Matthew Jarrett told Safe to Work.
“Operators are reporting dust-free cabins and seeing great results from the longevity of the system’s filters.”
Each filter is designed with an ejection port, whereby more than 90 per cent of respirable particulate is removed prior to the air passing through the main filter.
“This dramatically increases the life of the Sy-Klone filters to almost double that of our competitors,” Jarrett said.
Innovations like these, according to Jarrett, are supported by the bedrock of the International Standardisation Organisation Australian Standard (ISO/ AS) 23875 design principles that led to the development of the Sy-Klone Cab Air Quality system:
• Defined CO2 principles – maintain defined levels of ambient CO2 plus 400 parts per million
• Define fresh and recirculation system efficiency – maximum respirable particulate matter concentration less than 25 micrograms per cubic metre
• Increase filter efficiency requirements – a filter that meets more stringent test criteria will be required in ISO 23875-compliant operator enclosures
• Define pressurisation requirements – pressure shall be 20 Pascals (Pa) or higher (minimum sustained pressure) and not exceed 200Pa (maximum sustained pressure), minimum sustained pressure is required when the machine key moves to the “on” position
• Real-time monitoring requirements – cab pressurisation and CO2 levels monitored by permanently installed monitoring system
Published in February 2021 and updated in 2022, ISO/AS 23875 is a new global standard that unifies
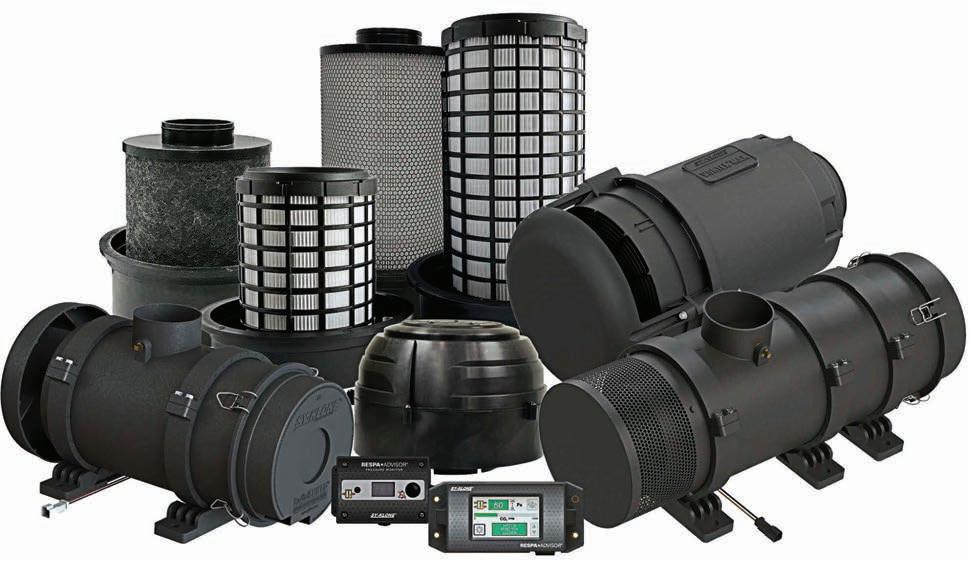

Images:
Sy-Klone International
Sy-Klone products that aim to improve air quality for Australia’s miners.
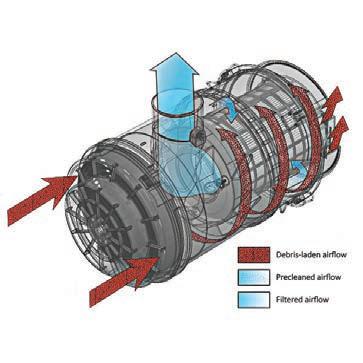
the design, testing, operation and maintenance of air-quality control systems for heavy machinery cabs and other operator enclosures, particularly in the mining industry.
Adherence to the requirements and testing methods set out in the standard aims to support the safety of machine operators, improve productivity, promote operator
alertness, and enable companies to reach occupational exposure reduction goals.
“Once you implement the SyKlone Cab Air Quality system onto a machine, you’re building an environment that incorporates these five engineering principles,” Jarrett said. “The Sy-Klone system actually goes above and beyond the ISO/AS 23875 standard with its real-time particulate monitoring, which is a game-changer for the mining industry.”
Jarrett said the ability to bring SyKlone Cab Air Quality Solutions to the Australian mining sector requires a close and collaborative partnership between Sy-Klone International and United Safety and Survivability.
“This partnership includes components, equipment and methods to assure compliance to ISO/AS 23875 and the creation of a haven for operators of heavy equipment and light transportation vehicles
within mine sites,” he said. “It is our combined abilities that allows the partnership to protect the operator inside the cab and during time spent in transportation.
“We are committed to delivering the most innovative and reliable safety and survivability solutions our customers can trust to protect life and property.”
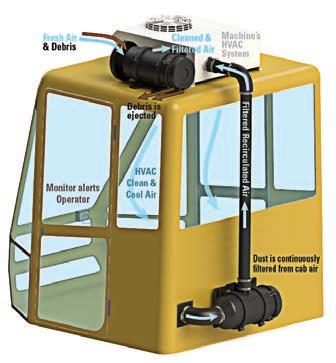

The Sy-Klone Cab Air Quality filter’s ejection port removes more than 90 per cent of debris before reaching the main filter.
The Sy-Klone Cab Air Quality system.
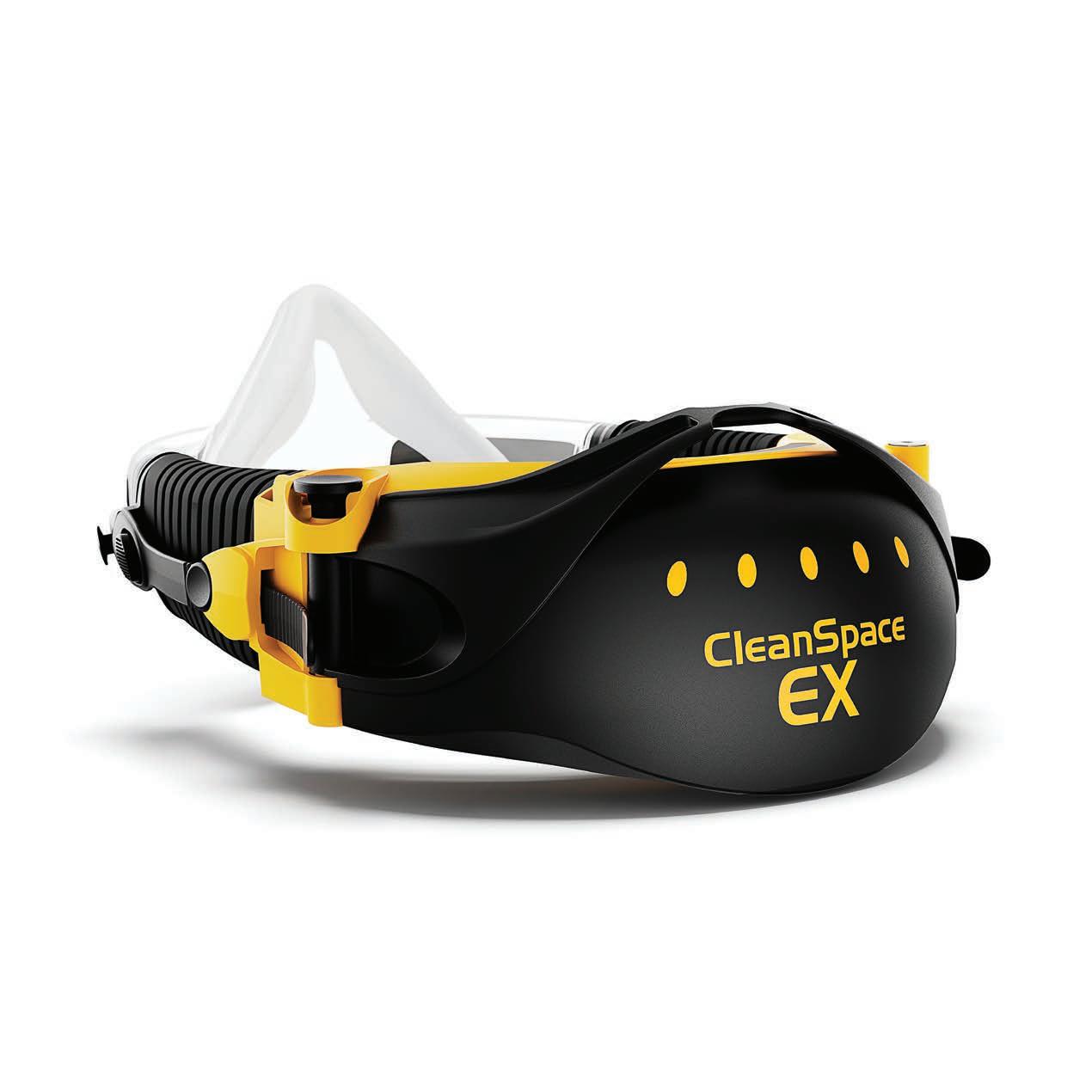
Safeguarding miners from silica dust
PROACTIVE PREVENTION IS KEY TO MITIGATING SILICA DUST EXPOSURE AND ENSURING MINERS’ SAFETY.
When rocks with crystalline silica are cut, drilled or disturbed, silica dust forms. And if this airborne dust is inhaled, it can potentially lead to serious health complications.
The respirable dust particles are so small that they are invisible under normal lighting conditions. This extremely small size also means they can easily be breathed deep into the lungs. Silicosis, an irreversible lung disease, occurs when silica particles cause lung inflammation and scarring, reducing lung capacity. Prolonged exposure also increases the risk of respiratory diseases such as chronic obstructive pulmonary disease and lung cancer. It is therefore vital that mining companies prioritise dust control through the implementation of engineering solutions, administrative controls, and the use of personal protective equipment (PPE).
THE IMPORTANCE OF HIERARCHY OF CONTROLS
The hierarchy of control framework is crucial for minimising hazardous substance exposure, including silica dust.
Elimination
The most effective control measure is to eliminate hazardous processes or materials. While it may not always be feasible to entirely remove silica dust from mining, eliminating processes that generate dust can significantly reduce the associated risks.
Substitution
Where complete elimination is not possible, substituting hazardous materials or processes with less hazardous alternatives can help reduce risks.
Engineering controls
These controls involve physical modifications to the workplace
designed to isolate workers from exposure. Examples include the installation of water sprays and ventilation systems to suppress and remove airborne silica dust.
Administrative controls
Implementing policies and procedures to limit workers’ exposure time to silica dust is crucial. This includes practices such as rotating shifts, scheduling adequate breaks, and designing work processes to minimise dust generation.
Personal protective equipment
PPE serves as a “last line of defence” against silica dust exposure. When other control measures cannot fully eliminate the risk, highquality respirators are crucial for safeguarding workers. Choosing PPE that addresses hazards and suits the work environment’s needs is essential.
ADVANCED RESPIRATORY PROTECTION
CleanSpace, an Australian company established in 2009, aims to lead innovation in preparatory protection

Images: CleanSpace
The CleanSpace Ex.
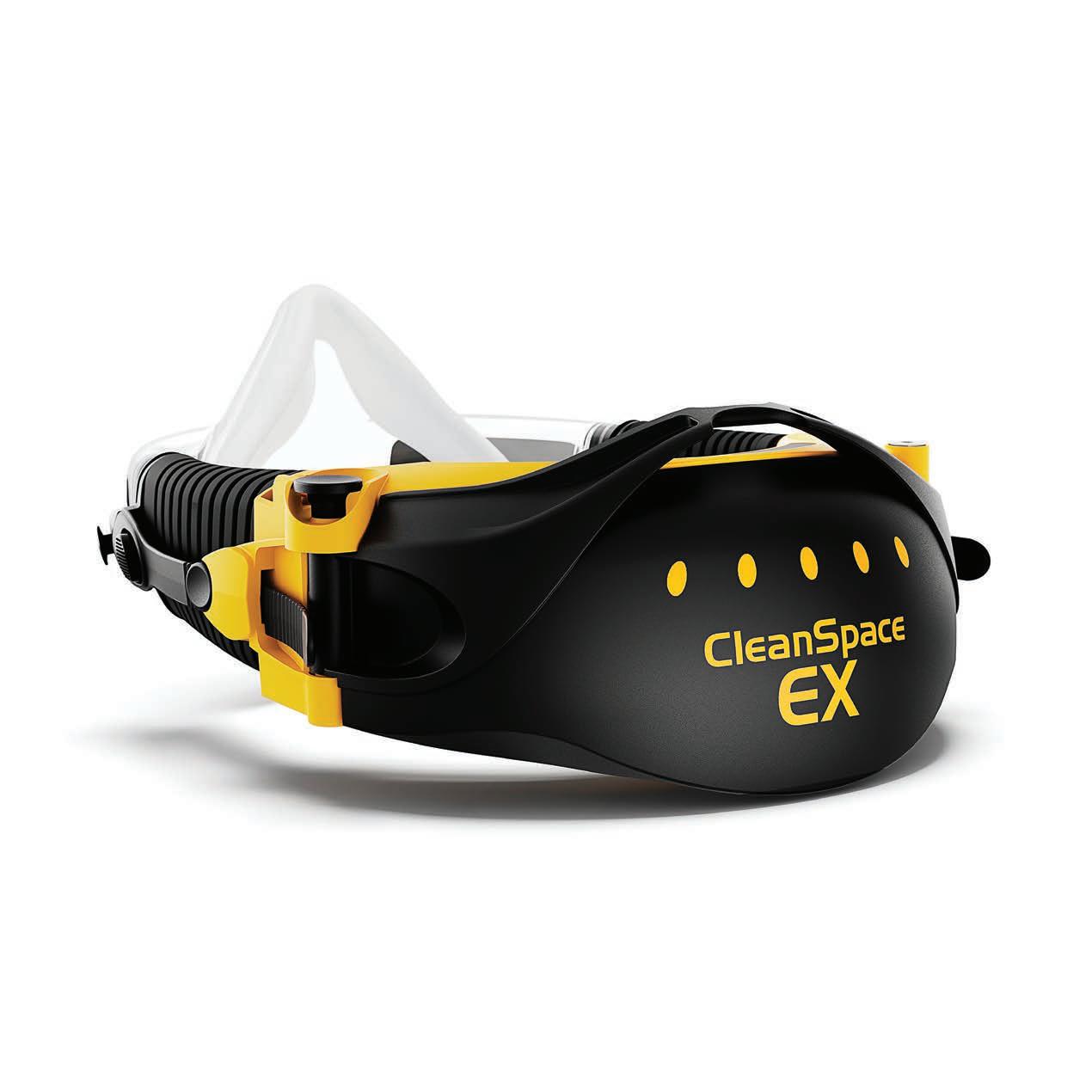
for mining. It offers intelligent, user-friendly powered airpurifying respirators that are effective and easy to use.
CleanSpace CST ULTRA is one of the company’s leading respirator models, incorporating features such as Bluetooth connectivity and real-time compliance reporting.
This respirator is designed to be lightweight, compact –with no hoses or battery pack – and comfortable, making it more ideally suited for workers who need to carry out physically demanding tasks.
According to CleanSpace, the CST ULTRA’s battery can last up to 14 hours (at moderate work rates at sea level), depending on factors like filter type, filter loading, mask seal, work rate and altitude.
Thanks to its fast-charging capabilities, the CST ULTRA helps to ensure workers are continuously protected throughout their shifts.
The device also provides real-time data on protection levels, battery status and filter usage, helping site managers ensure comprehensive reporting for compliance management.
Another respirator in the company’s arsenal is CleanSpace EX, designed for potentially explosive environments and certified for use in underground mining in Australia. Weighing in at less than 500g and with a battery that lasts for up to eight hours depending on work conditions, the respirator is particularly suited for underground coal mines where methane presents a significant explosion risk.
CleanSpace is dedicated to creating high-quality respiratory protection solutions.
Recognising the crucial need to protect the health of miners, CleanSpace equipment is designed to be highly effective and comfortable.
CleanSpace’s mission is to assist mining operations in upholding stringent safety standards and shielding their workers from the hazards of silica dust exposure.

KEEP YOUR DUST DOWN
Fine particles of dust pose a serious health risk, especially when fine particles are inhaled. Other safety risks include the increased risk of slips, trips and falls in areas of poor visibility caused by dust.
Dust is a significant operating, environmental and occupational hazard unacceptable to the modern Bulk Materials Handling Industry.
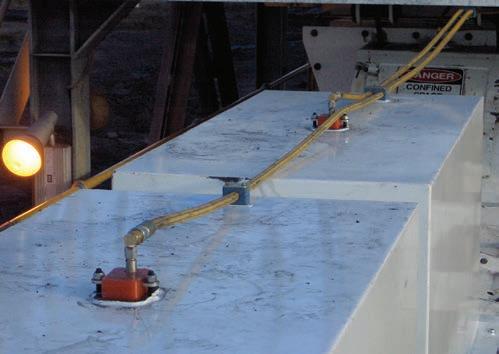
The Quickfit nozzle is part of the ESS Dust Suppression System designed to dramatically reduce the dust emissions generated as part of materials handling processes.
ESS Dust Suppression systems are suitable for most applications where the process will allow for small amounts of added moisture.
ESS Dust Suppression System utilising Quickfit Nozzles are
• Easy to Install and maintain – with service occurring outside the structure
• Low Maintenance – by using filters to reduce blockages
• Low Water Consumption Units – using 2 litres of water a minute over a range of pressures. Making it suitable for drier environments
• Designed in Kit Forms – available in kits of 2, 4 or 6
• Tailored to suit your sites needs

The CleanSpace CST ULTRA in action.
Dust suppression
Ensuring worker safety while supporting mental health
SAFETY MATE’S SKYTEC
3030V RESPIRATOR IS PROTECTING WORKERS WHEN THEY NEED IT MOST.
When Safety Mate introduced the Skytec 3030V respirator, it did so with the aim of protecting workers from harmful airborne particles like silica dust. Silicosis, a lung disease caused by inhaling respirable crystalline silica, remains a significant concern in many industries. Silica dust, often invisible to the naked eye, can stay airborne for long periods, posing a
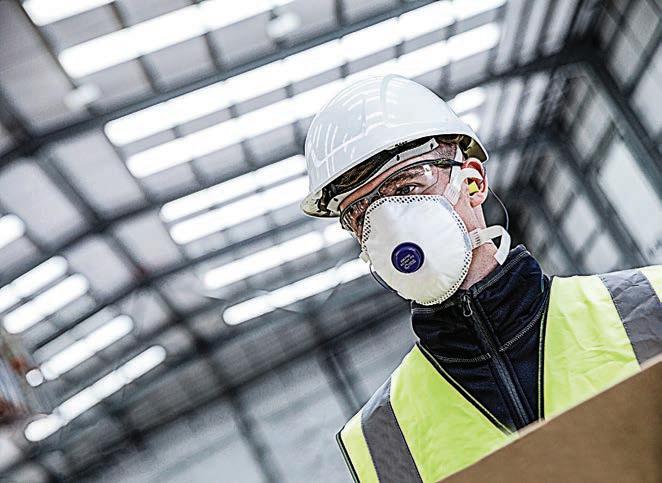
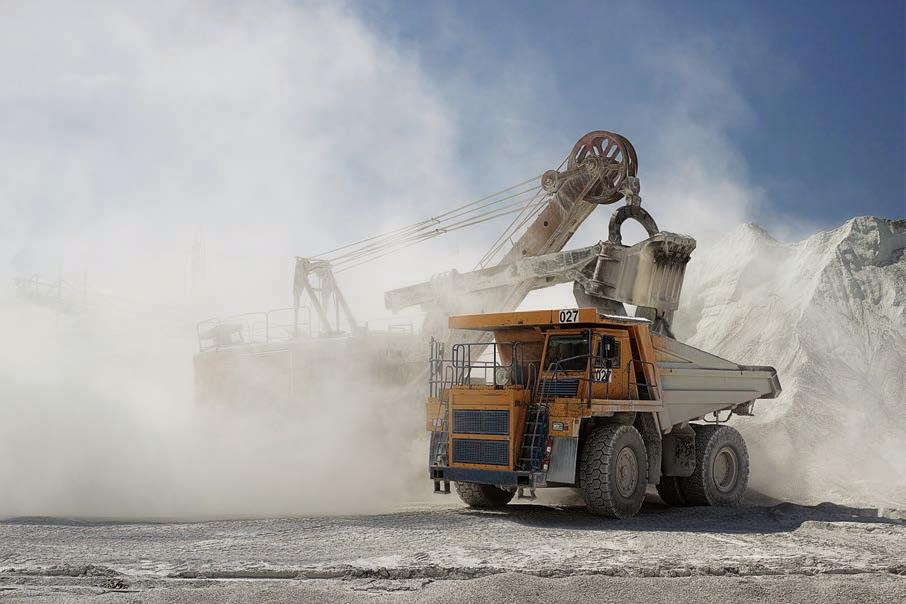
threat to workers’ respiratory health. Inhaling certain kinds of dust can lead to pneumoconioses, a group of lung diseases – long called black lung disease for coal miners– and its causes and effects have been understood for decades, with relevant regulation evolving in turn.
While it is estimated up to 600,000 Australian workers are potentially exposed to silica dust each year across a range of industries, silicosis only recently started becoming more regulated.
It is against this backdrop that products like the Skytec 3030V respirator become so important as a reliable safety solution.
This P2-graded respirator is designed to safeguard workers from silicosis and harmful welding fumes, making it essential in industries such as mining and construction.
“The 3030V disposable respirators offer an outstanding level of protection

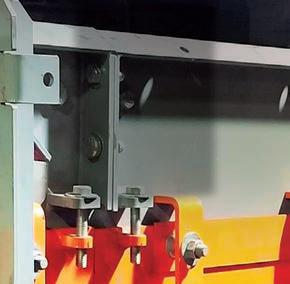
Safety Mate’s Skytec 3030V respirator.
The Skytec 3030V respirator is ideal for challenging work conditions.
demonstrated when conducting facefit testing,” Safety Mate director Clint Tee told Safe to Work.
According to Tee, the respirator’s lightweight outer shell is designed to ensure comfort during extended use, making it ideal for challenging work conditions.
“The Skytec 3030V provides a full foam face seal, providing unparalleled comfort and fit, making long hours of wear surprisingly comfortable” he said. “With adjustable head straps and the full foam face seal, the Skytec 3030V adapts to every face shape, ensuring maximum protection and a perfect fit for anyone.
“This adaptability makes it a versatile choice for diverse work environments and user needs.”
Safety Mate has been proactive in offering top-tier respiratory protective equipment (RPE) as Australia prepares to implement
stricter regulations on silica exposure, including the ban on engineered stone benchtops.
But Safety Mate understands that protecting physical wellbeing is only part of the equation when it comes to keeping workers safe across the mining industry.
That’s why the company partners with the Black Dog Institute, a non-profit organisation dedicated to mental health research and awareness.
Safety Mate launched the Black Dog range of personal protective equipment, where a portion of proceeds from each sale goes towards life-saving research.
The Skytec 3030V respirator, a cornerstone of the Black Dog range, not only meets safety standards but embodies Safety Mate’s broader mission to enhance worker safety and promote mental health awareness.
08-02_SafeToWork_InsertV1.pdf 1 8/5/24 2:40 PM
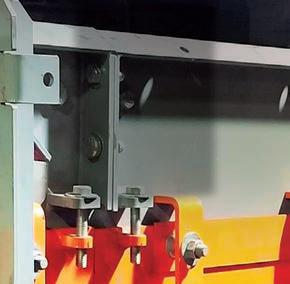

“Our Black Dog product range is more than just personal protection –it’s a symbol of support and awareness for mental health,” Tee said.
“This initiative ensures that with every purchase of Black Dog products, donations are channelled directly towards the institute, bolstering efforts in diagnosis, treatment and prevention of mental illnesses.”
Recognising the challenges within heavy industries, where workers have been found to face a higher risk of mental health issues, Safety Mate’s initiative is a step towards comprehensive worker support.
“Understanding the link between mental health and workplace productivity, we’ve forged a meaningful partnership with the Black Dog Institute,” Tee said.
“This is just another way that Safety Mate is supporting workers both onsite and in their personal lives.”
KEEPING YOUR FUGITIVE MATERIAL UNDER CONTROL

ugitive material in any form can be extremely dangerous — to workers’ health, to belt conveyor components, to your bottom line. Martin’s transfer point associated products (such as belt support, sealing and tracking) minimize spillage and airborne dust problems. When bulk material transfer systems are properly designed and maintained, overall operations run cleaner, safer and more efficiently. Think Clean ®
Impact Cradles
Apron Seal Skirts
Belt Trackers
Dust Curtains
Training and education
Measuring workplace training results
MARTIN ENGINEERING ASKS THE QUESTION: IS YOUR GOAL TO GET A RETURN ON YOUR INVESTMENT WHEN UNDERTAKING REQUIRED TRAINING HOURS?
Training employees can lead to significant improvements in production, maintenance labour, risk avoidance and cashflow.
Training should be robust enough to break the “we’ve always done it that way” mentality and encourage creativity in problem-solving with safety at the forefront of the design. Companies that place a priority on safety – and address fugitive material problems seriously –can benefit from fewer safety incidents, less regulatory oversight and higher productivity and profits.
Martin Engineering’s online Foundations Learning Centre draws from the collective knowledge and expertise gathered over nearly 80 years of solving bulk handling challenges. Aimed at apprentice technicians and experienced engineers alike, the non-commercial information is offered at no charge and, as an extension of the Foundations training curriculum, the Learning Centre uses a mix of text, photos, videos, webinars, online events and live experts available to answer questions. Everyone who operates, cleans or maintains conveyors should be trained in the hazards of belt conveyors and bulk material handling. Operators and cleaning crews should have a basic understanding of normal conveyor operation and common problems so they can be aware there are ways to reduce day-to-day problems such as spillage and belt wander.
Basic training includes topics such as guarding, identifying problems and safe work practices. Appropriate safety training emphasises how the belt can store elastic energy, even
when lock-out, tag-out procedures are followed, and why additional securing of the belt is required.
And with the retirement of many experienced operators and mechanics, coupled with the difficulty in finding new workers, it becomes critical that new employees understand the basics of conveyor design and operation.
Engineering and maintenance staff should be additionally trained in fundamental conveyor design concepts so they can analyse causeand-effect relationships.
Visible signs of poor conveyor operation are often not the root cause of the problem. For example, using guide rollers to force the belt to track does not address the fundamental reason for the belt mistracking and usually results in belt-edge damage.
Training can often be on a specific piece of equipment, with the goal of creating trainers who can
educate the rest of the maintenance department. This approach works well with certain types of equipment but ends up with one or two motivated and well-versed technicians who can troubleshoot.
A mechanic trained in installing problem-solving components can run into myriad physical constraints. Firstly, the original conveyor design and subsequent modifications can make it impossible to install equipment according to the manufacturer’s instructions without a complete redesign. Secondly, structural obstructions or conveyor arrangements often don’t allow enough room for installation, clear views for inspection or access for safe and easy maintenance according to industry standards.
Conveyor design training for engineers and mechanics is critical so they can diagnose problems with an understanding of fundamental

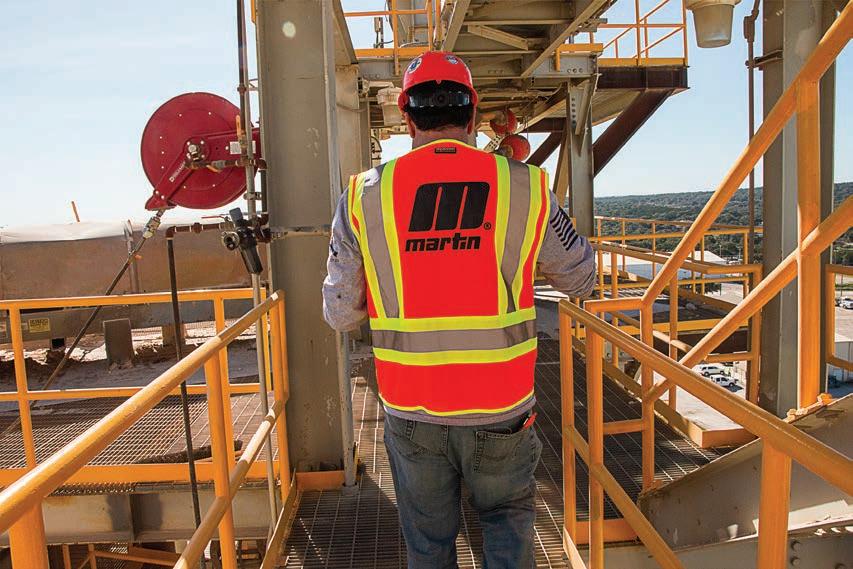
and capacity exceed the original design specifications.
No two conveyors are identical and even side-by-side twin conveyors can act differently. So adhering to standard design methods allows one technician to make these slight adjustments and another technician to recognise the intentions even without the prior technician present.
TRAINING FOR RESULTS
Training alone rarely results in meaningful actions to improve conveyor performance. When management understands the clear links between safety, cleanliness and productivity, it is much easier to turn training into results.
There are many variations, but most success stories have common threads:
• Basic training in conveyor hazards and the methods for controlling fugitive materials
• Training in conveyor design fundamentals and the root causes of common problems
• Management participation in the training to show support
• A pilot program and measured results
• A long-term plan implemented from a successful pilot program
before the training help the instructor focus on site-specific problems. The goal is for the instructor to have actual examples to show the class that their problems are not necessarily unique.
The first day of training usually starts with reviewing typical problems and getting people in the class to talk about their specific challenges. The class then identifies a couple of problem conveyors and the splits into small teams – each team can look at
the same problem or select different ones. Photos and videos of the issues are taken to be used in the problemsolving discussions.
The rest of day one and the start of day two can be spent reviewing basic design principles that relate to the problem conveyors. The discussion can centre on possible root causes and solutions.
Once the teams reach an agreement on a way forward, they prepare a short presentation with the help of the instructor, using their actual conveyor problems and the knowledge they gained. The presentations may also include an estimate of the cost of the proposed solutions.
At the end of day two, management is invited to listen to team presentations and solutions. By participating in the presentations, management shows a commitment to making improvements and has an opportunity to ask questions, while the trainees, by making the presentations, show the knowledge they gained and support for the proposed solutions.
It is critical at this step that the members of management who attend the presentations have the authority to act on the proposals and are willing to potentially commit to a pilot program to prove theoretical results can be turned into reality.
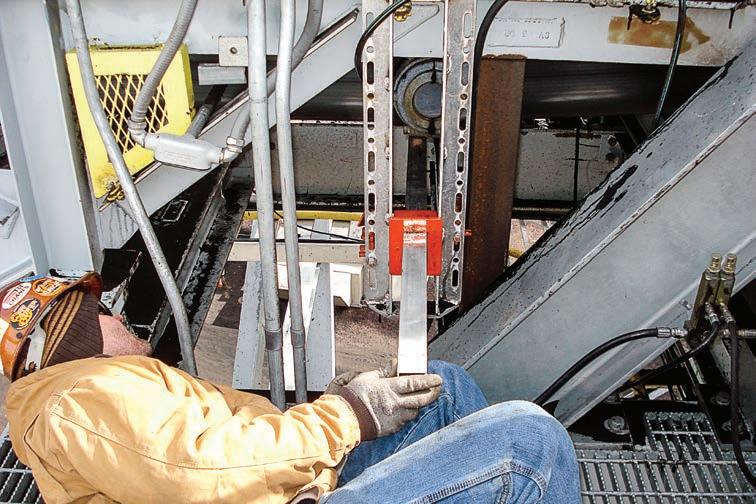
A professional safety inspection considers a third-party perspective that can be overlooked.
The Martin Conveyor Belt Carryback Gauge estimates carryback on the return side of a belt.
Training and education
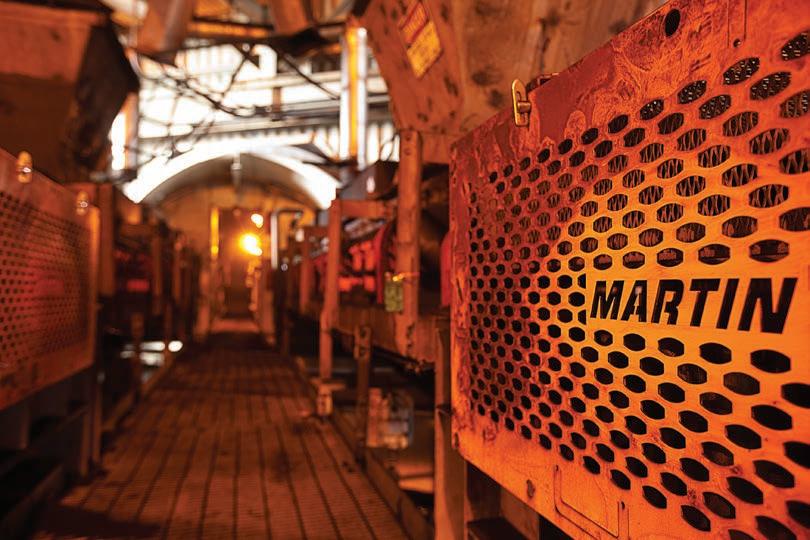
PILOT PROGRAM
One or more conveyors are selected for a trial. While it’s normal to use the “worst” conveyor, keep in mind half measures don’t get half results, so it’s key to consider a project’s scope.
Once a conveyor (or conveyors) has been selected, detailed proposals for retrofit can be obtained. An experienced person from the selected equipment supplier should overview the designs, offer feedback, and supervise the installation. Sufficient downtime must be allocated to properly modify the conveyor.
Measuring results from improvements is important but relatively straightforward.
Photos and videos of before and after must be taken, dust levels are measured using common instrumentation, spillage can be measured with buckets or trays in appropriate locations, and carryback is measured by placing a tarp under several return idlers close to the discharge pulley. The collected fugitive materials are weighed for comparison after the conveyor has been modified.
Dust and spillage sampling locations should be marked so tests can be accurately repeated after retrofitting and an improvement percentage can be calculated.
The length of time for collecting samples can vary from a day to a week and should give a good representation of the average or typical operating environment and weather conditions.
It is important to keep the dust monitor running even if the conveyor is running empty, as maximum fugitive dust levels are often detected when running conveyors empty long enough that the carryback dries out and becomes airborne.
The results of the pilot program are usually immediately noticeable, but there is a temptation to assume the problem has been fixed and to revert
back to delaying maintenance without follow-up maintenance, causing the results to deteriorate.
The test period should therefore extend to the next scheduled maintenance shutdown, with periodic inspections and adjustments made by the equipment supplier in the interim to ensure optimum efficiency.
THE PAYBACK ON TRAINING
To demonstrate the benefit of safety to a company’s bottom line, the Occupational Safety and Health Administration’s (OSHA) online tool, ‘$afety Pays,’ uses company-specific economic information to assess the potential economic impact of occupational injuries on that firm’s profitability.
The program estimates direct and indirect costs and weighs them against financial details supplied by the company.
Experience has shown the motivation to take action developed in the classroom often defaults back to prior habits. A production-at-all-costs approach means problems and safety concerns may never go away, and employees have to accept the poor performance and added risks, which demoralises morale.
It is incumbent upon management to take the safety and maintenance training as seriously as the staff, listen to the concerns of employees and fix the problem the first time.
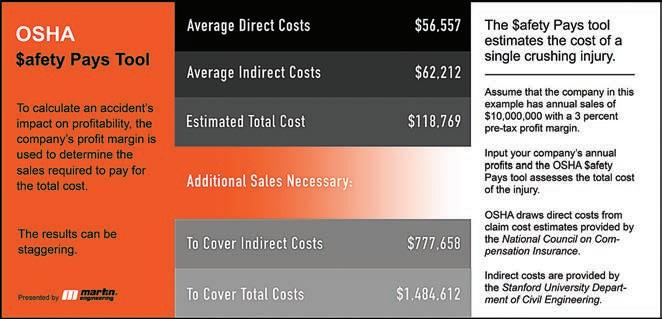

A properly engineered conveyor system will help to maximise productivity and safety.
OSHA’s ‘$afety Pays’ tool uses economic information to assess potential impact of occupational injuries.

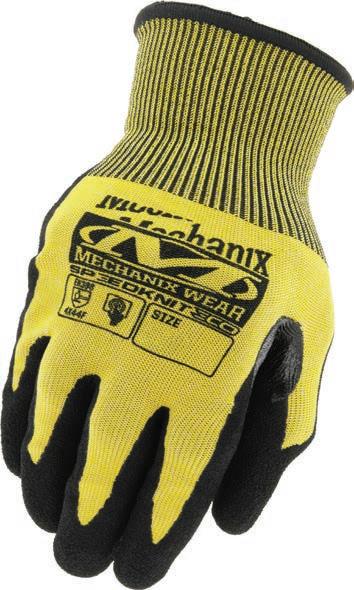
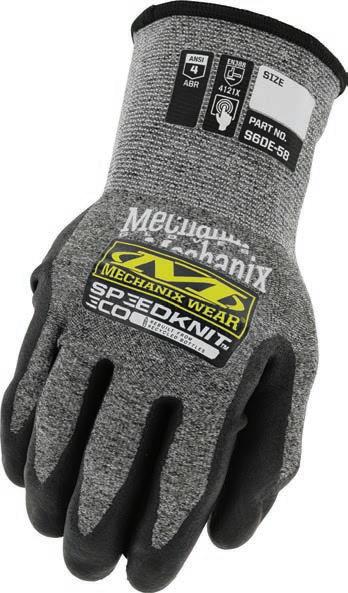
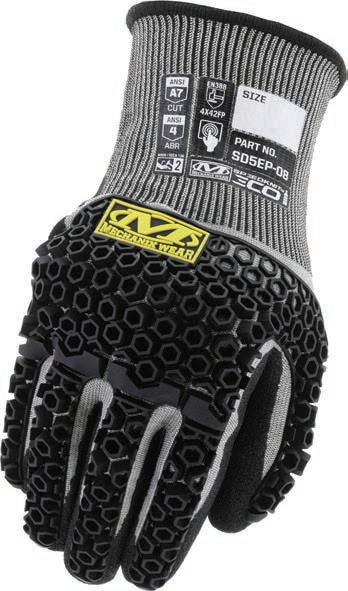
PROTECTION SUSTAINABILITY AND
THE LEADING BRAND IN AUTOMOTIVE, HOME IMPROVEMENT, AND LAW ENFORCEMENT IS NOW BRINGING TRUSTED PROTECTION TO MINING AND INDUSTRIAL SECTORS.
We offer the widest size range (XXS to XXXL) for the perfect fit. Recycled materials certified by the Global Recycling Standard - Full recyclability through Upparel. Superior comfort and fit, reducing the need to remove gloves. Dual protection against cuts and impacts*. Touchscreen capability for seamless smart device use. *Features vary by product.
Our sustainable models use recycled materials and are fully recyclable through Upparel. Protect your hands and the planet with Mechanix Wear.
Fly-in, fly-out
MinRes Air lifts off
MINERAL RESOURCES IS ON A MISSION TO REINVENT THE FIFO EXPERIENCE.
It’s no secret that fly-in, fly-out (FIFO) work can be tough. But as leaders in Australia’s mining industry look to improve working conditions and mental health outcomes, FIFO is an area of the sector that is flying to new levels of comfort and stability.
With initiatives from majors like BHP and Fortescue seeing millions being invested into levelling up the worker experience, it could be argued that there’s never been a better time to be a FIFO worker.
Mineral Resources (MinRes) is one operator taking its FIFO focus to another level. The iron ore miner’s new internal airline, MinRes Air, officially took to the skies for the first time in July, with an inaugural flight landing in the Pilbara region of Western Australia.
The flight transported MinRes FIFO employees and contractors from Brisbane Airport to the company’s Wodgina and Ken’s Bore mine sites.
Miners would previously have to make round-about trips to get to the sites, but the direct weekly flights
shave off hours or even days off the time east-coast workers have to spend away from their families, while also significantly reducing the cost of travel.
The first A319 aircraft to launch in MinRes’ new initiative completed the 3600km cross-country journey from Brisbane to Wodgina in five hours and 40 minutes.
And workers flew in style, with the aircraft having been refurbished to provide an extra 25cm of legroom to ensure maximum comfort.
After originally planning to carry 138 passengers, MinRes reduced the number to 108 to provide the additional legroom.
The service is also staffed by a highly experienced team of pilots, cabin crew, engineers and ground staff who have flown and worked across Australia and around the world.
“MinRes Air is one of the ways we are redefining the fly-in, fly-out employee experience by setting a new standard in the resources industry for
facilities, food and flights,” MinRes people facilities and logistics executive general manager Bethanie Ibrahim said at the time of the inaugural flight.
“This industry-first investment will improve safety and productivity by ensuring our people travel to and from site as quickly, conveniently and comfortably as possible.
“Our focus is on providing more flight flexibility to our remote operations and allowing our people to travel to and from site at attractive times five days a week.”
For initial flights while MinRes Air was being developed, the miner had been partnering with Skytraders, an Australian-owned airline that operated the Brisbane–Pilbara route for MinRes from January until the new airline was ready to launch.
Now that the first phase of the MinRes Air service has been rolled out, the weekly direct flights to and from Brisbane are expected to significantly reduce the travel time and cost for
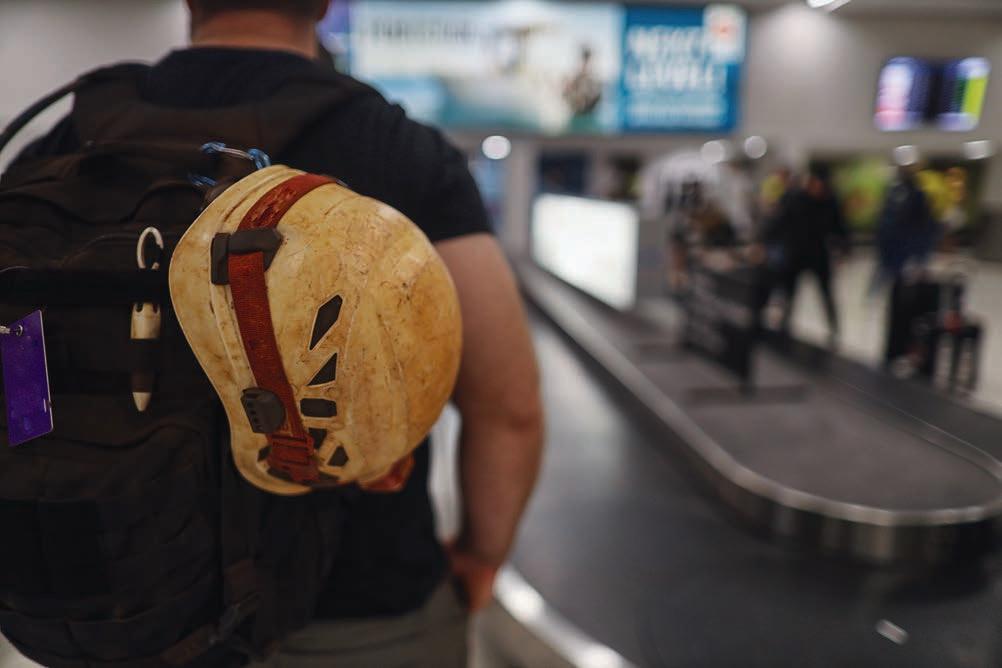

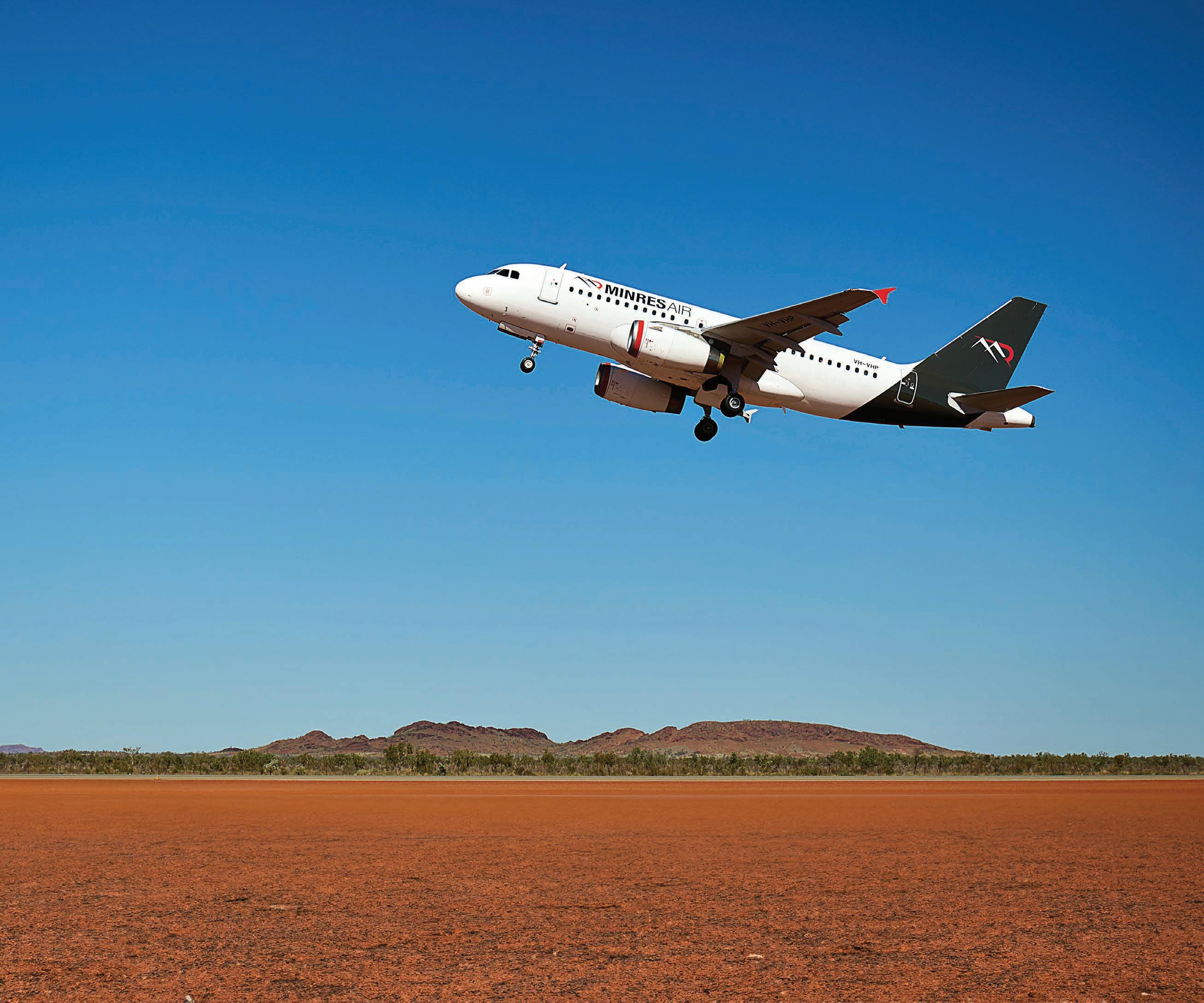
The MinRes aircraft feature a decreased capacity to allow more room for passengers.
MinRes employees and contractors who live in Queensland or elsewhere on the east coast. In the second phase of the rollout, which is anticipated in the near future, flights between the MinRes Air terminal at Perth Airport and Ken’s Bore will launch to service the Onslow Iron project in WA.
Onslow Iron delivered its first shipment in May and is on track to ramp up to nameplate capacity of 35 million tonnes per year by June 2025, drawing more employees from across Australia.
“Seeing the MinRes colours proudly displayed on an aircraft is an incredibly
EXTEND LIFE & ENHANCE EFFICIENCY
exciting milestone for the business,” Ibrahim said.
“We have assembled an outstanding team that has decades of experience in the aviation sector and [we] look forward to our first Perth flights taking off soon.”

SKF Automatic Lubrication
Systems
Minimise downtime and extend equipment lifespan, even in the harshest environments, with SKF’s reliable single-line and progressive automatic lubrication systems. Our systems deliver cutting-edge technology that protects your machinery and enhances performance, backed by expert support every step of the way. Our strength comes from high-quality distribution partners who manage installation, service, technical support & training nationwide.
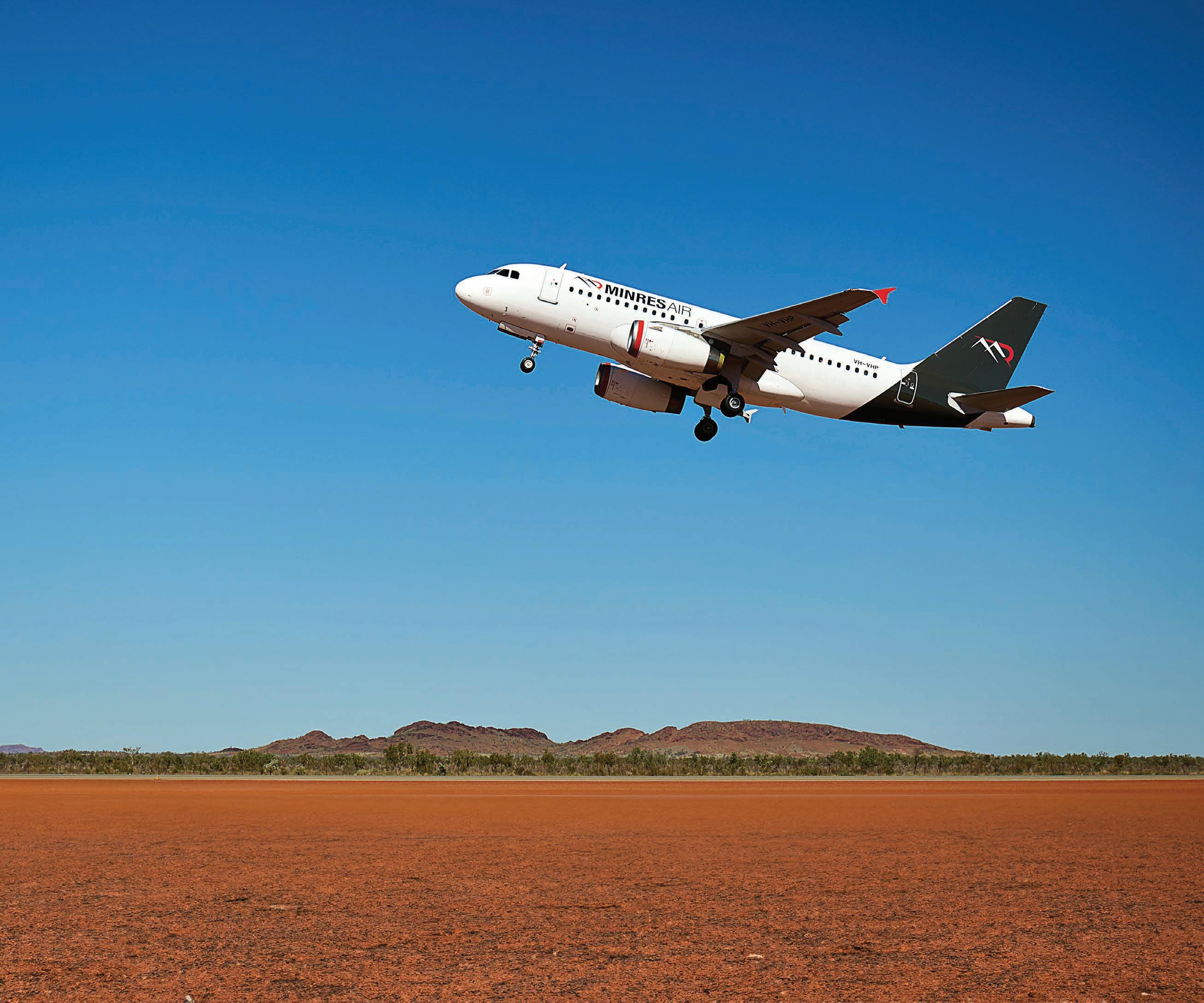
The inaugural MinRes Air flight as it departed Wodgina mine site in the Pilbara.
More than just a guard
DIACON AUSTRALIA TAKES PRIDE IN BEING AN INNOVATOR OF THE PLASTIC CONVEYOR IMPROVEMENT SYSTEM, SETTING AN INDUSTRY BENCHMARK.
The Diacon name has become synonymous with industry standards in safety, quality and efficiency across manufacturing, mining and logistics sectors nationwide.
Diacon Australia has aimed to redefine the operation of conveyorbased systems by enhancing demarcation and fall protection to minimise risks to workforce and machinery. Supported by a proven 20-year track record, a commitment to zero harm underscores the company’s proactive approach to the prevention of workplace injuries.
“We are really proud of the contributions and advancements Diacon has made,” Diacon managing director Brendan Refalo said.

“It’s why we’re the trusted suppliers and industry leaders of plastic guarding systems.”
Diacon Australia’s offerings have a number of key benefits:
ost-effective custom labelling o need to paint ustralian made and owned
“Diacon Australia’s commitment to ongoing research and responsiveness to industry needs drives continuous product innovation and advancement, resulting in an entire suite of conveyor improvement product solutions,” Refalo said.
A site’s conveyor productivity can be significantly enhanced thanks to Diacon’s innovations in spillage reduction, quick access for idler changeout, and lightweight componentry eliminating the need for cranes and additional people during maintenance activities.
“The features of our comprehensive conveyor improvement system – the Diacon hungry board, Diacon safety panel, Diacon conveyor guards, and Diacon hoods – collectively enhance workplace safety and productivity through one unique solution.
“Our products are 100 per cent Australian-owned and manufactured to the highest quality,
• Easy to install, remove and maintain
• Quality build, strong in structure
• Customisable to any specifications
• 100 per cent corrosion-free
• Up to four times lighter than steel
• Mounted using ‘hook, hang and lock’ system
• Safer during operations and maintenance periods
• Sound-deadening qualities
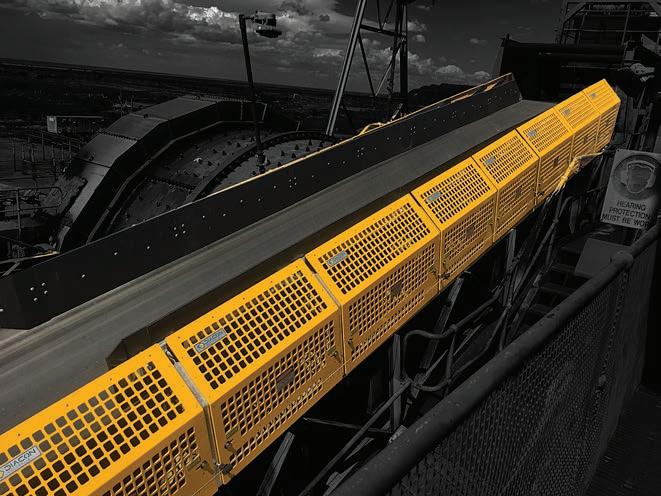
“Diacon’s approach to improved conveyor safety is achieved through uniquely designed industry-compliant guarding that is exceptionally lightweight and can be safely stored when not in use on the nearby handrail,” Refalo said.
“Our strong reputation is built on our dedication to understanding clients’ needs and our proactive approach to continued advancements in product evolution.
“Our success as market leaders is thanks to the extraordinary relationships we’ve developed with our clients and distribution partners, and their understanding that we’re more than just a guarding product.
“Diacon Australia is dedicated to developing the latest design, engineering, and manufacturing techniques to stay ahead of industry demands.
“By staying adaptable and responsive to evolving needs, we’ve consistently driven the industry expectations for safety, productivity, and efficiency as market leaders.’
Diacon is a trusted supplier of plastic guarding systems for conveyors.
Diacon aims to stay on the cuttingedge of technological innovation.


Looking back to stay ahead
AUSPROOF IS CELEBRATING 30 YEARS OF POWERING AUSTRALIA’S MINES WITH ITS RANGE OF ELECTRIC CABLE COUPLERS.
When you’re servicing a major industry like mining, it pays to be based in the right place.
AusProof makes its home in the heart of the Queensland coal mining industry: Gladstone.
And as a manufacturer of electric cable coupler solutions for Australia’s coal mines, managing director Aston Marks said it has been the perfect place for AusProof to stay on the cutting-edge of product development.
“We’re incredibly selective with our range,” Marks told Safe to Work. “By focusing on continually developing our key products, we can continue to grow with the industry.”
But AusProof isn’t just focused on Australia. The company’s couplers have elevated operations in Africa, the US, the UK, South America, and parts of New Zealand and Asia.

which can in turn have explosive consequences in a coal mine.
But AusProof’s removable flange means an Allen key and a few minutes are all that’s required to re-fit a new flange as soon as a scratch is detected, keeping the system flameproof while operations continue running.
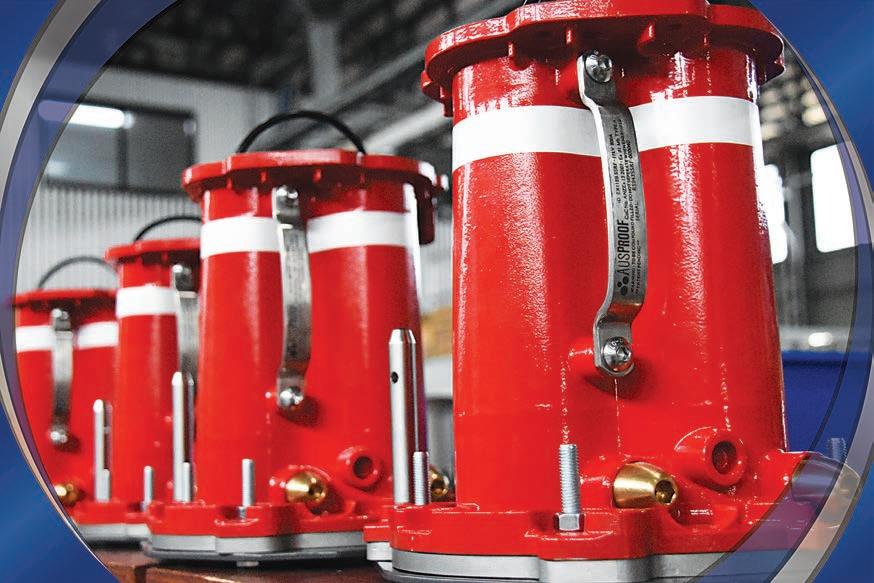
“Our specifically-designed coupler is used in 99 per cent of Australian operations today,” Marks said. “It changed the game when it comes to safety and cost savings when it was launched, and nothing has been able to rival it since, save for our own innovations to optimise it further.”
Features on AusProof products like replaceable flameproof paths, insulation that extinguishes arcs and faults, full phase-to-phase segregation with earth, and prevention of hot joints are part of the company’s focus on health and safety.
It’s innovations like these that Marks said represent a prime example of AusProof’s ethos that more can always be done.
“Another solution can always be designed, another improvement can always be made,” he said, “AusProof is committed to manufacturing products that are modern, reliable, durable and, above all, safe.”
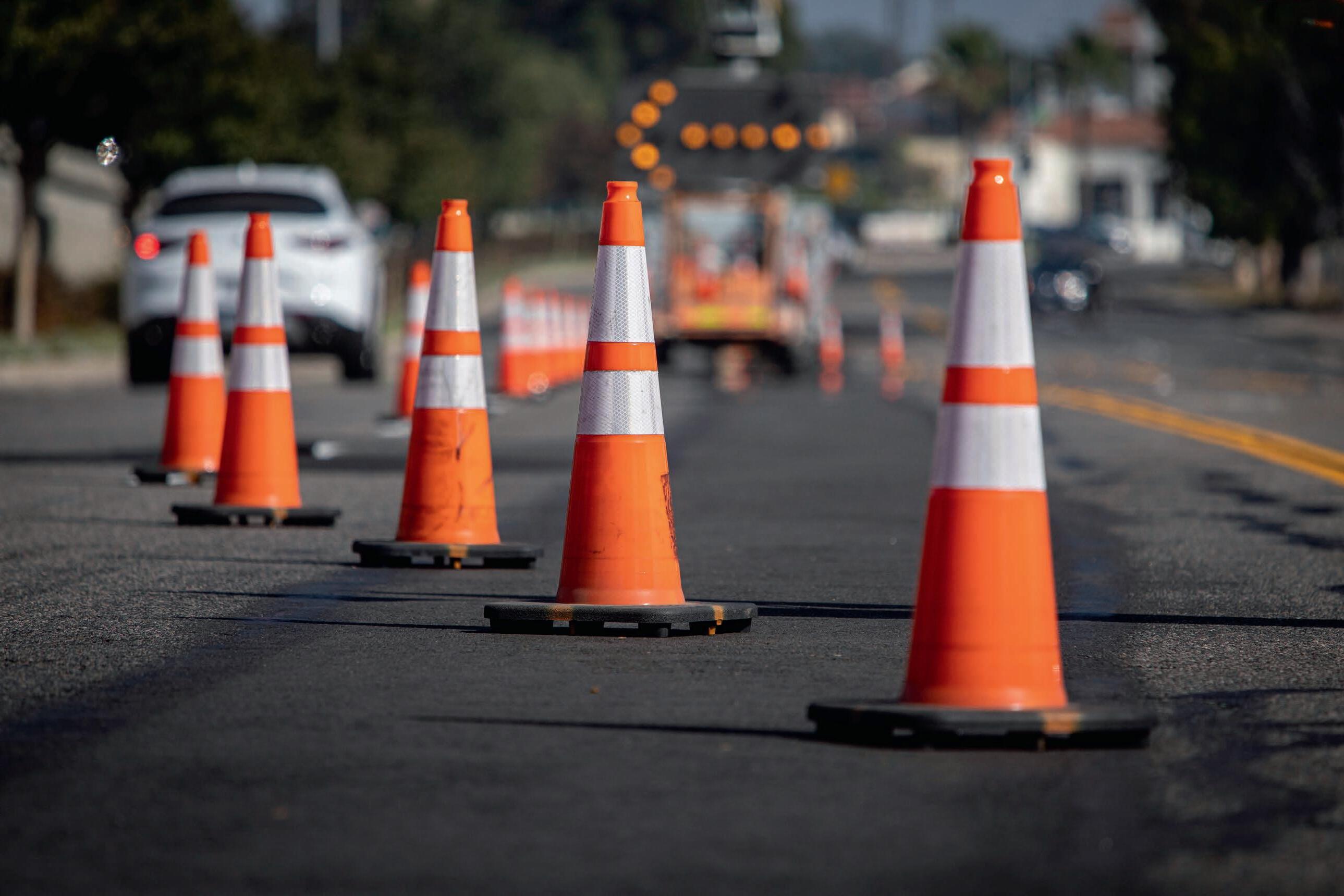
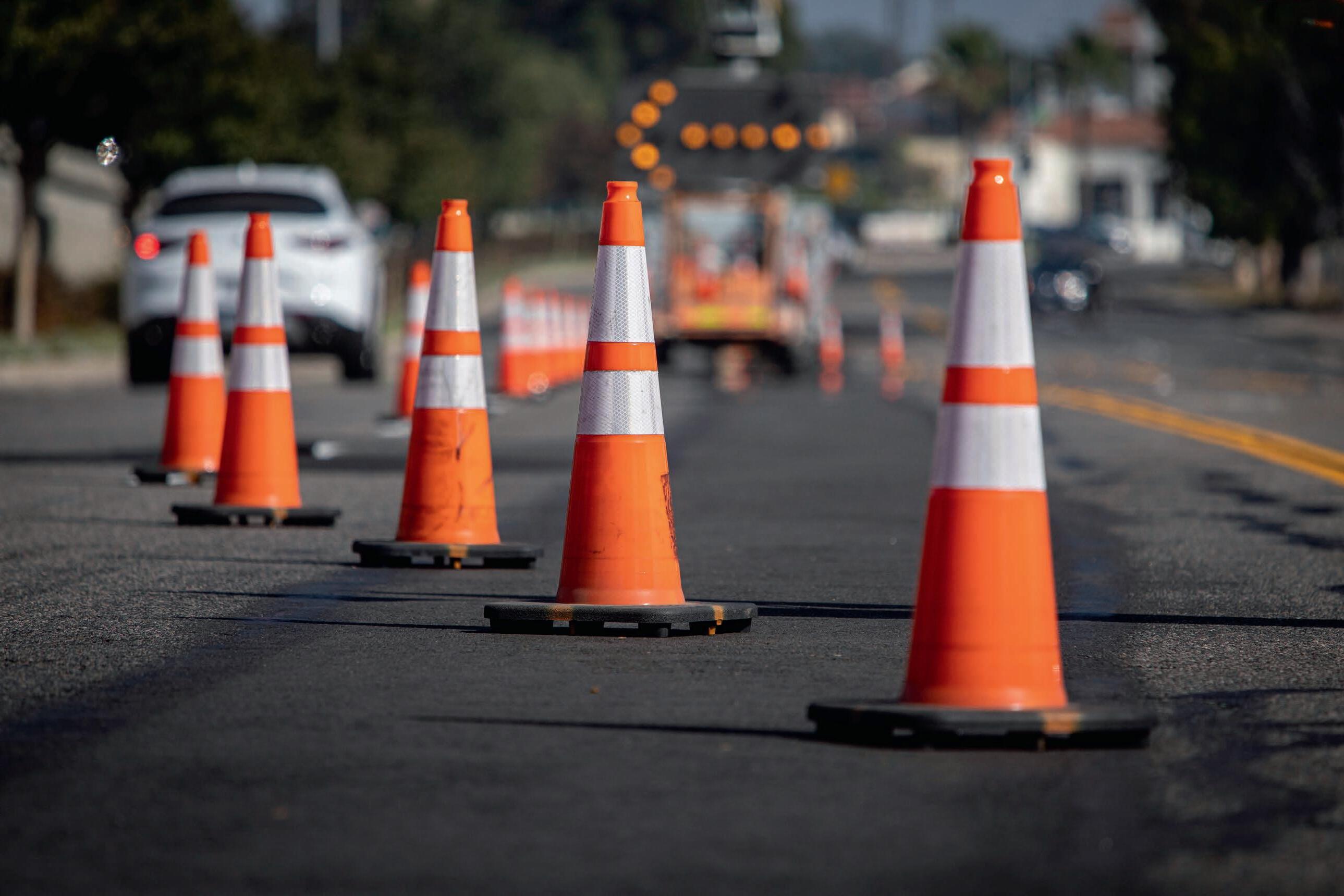
AusProof is celebrating 30 years of quality cable coupler design and development.
AusProof’s Ex118BSSRF ready for shipping.
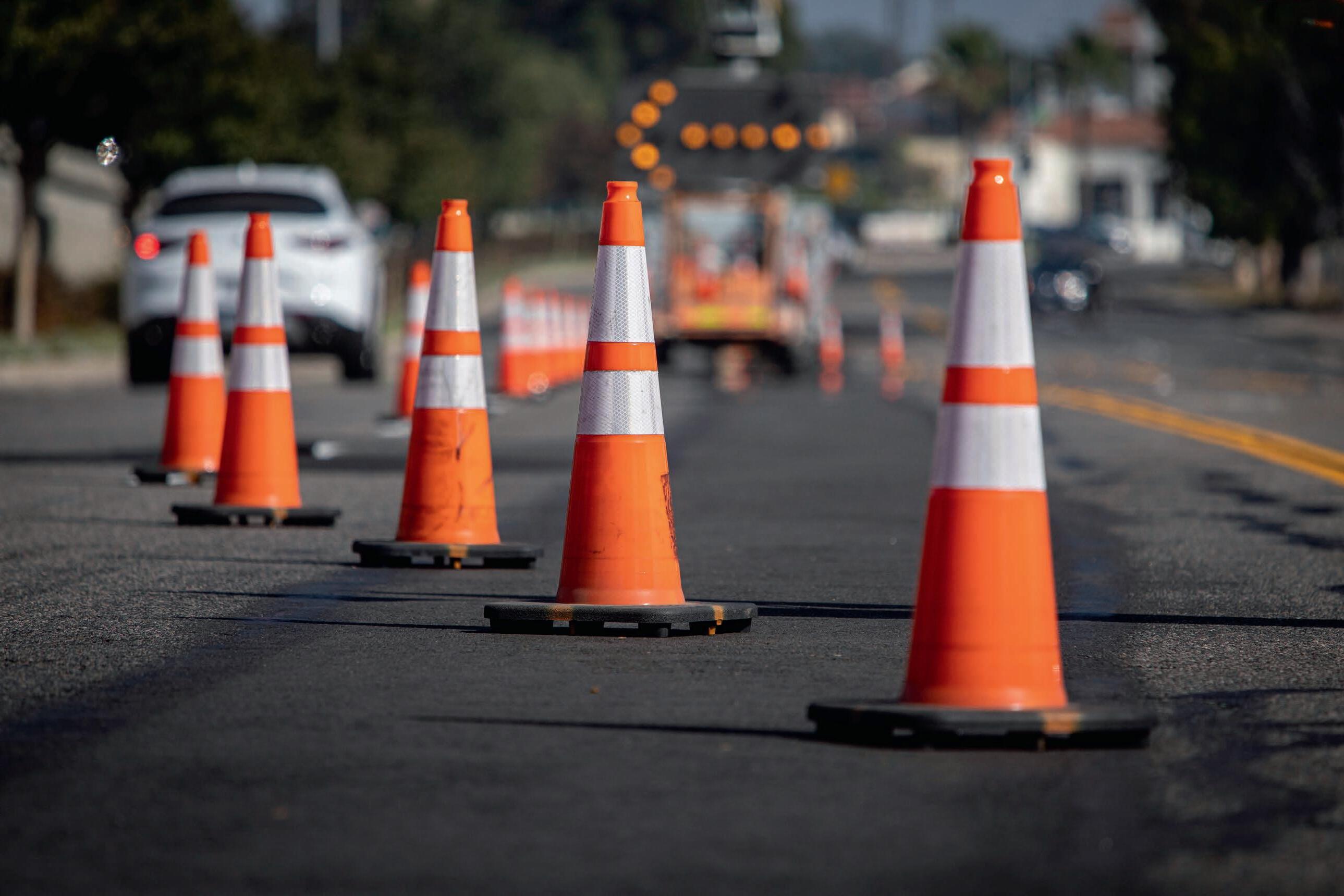
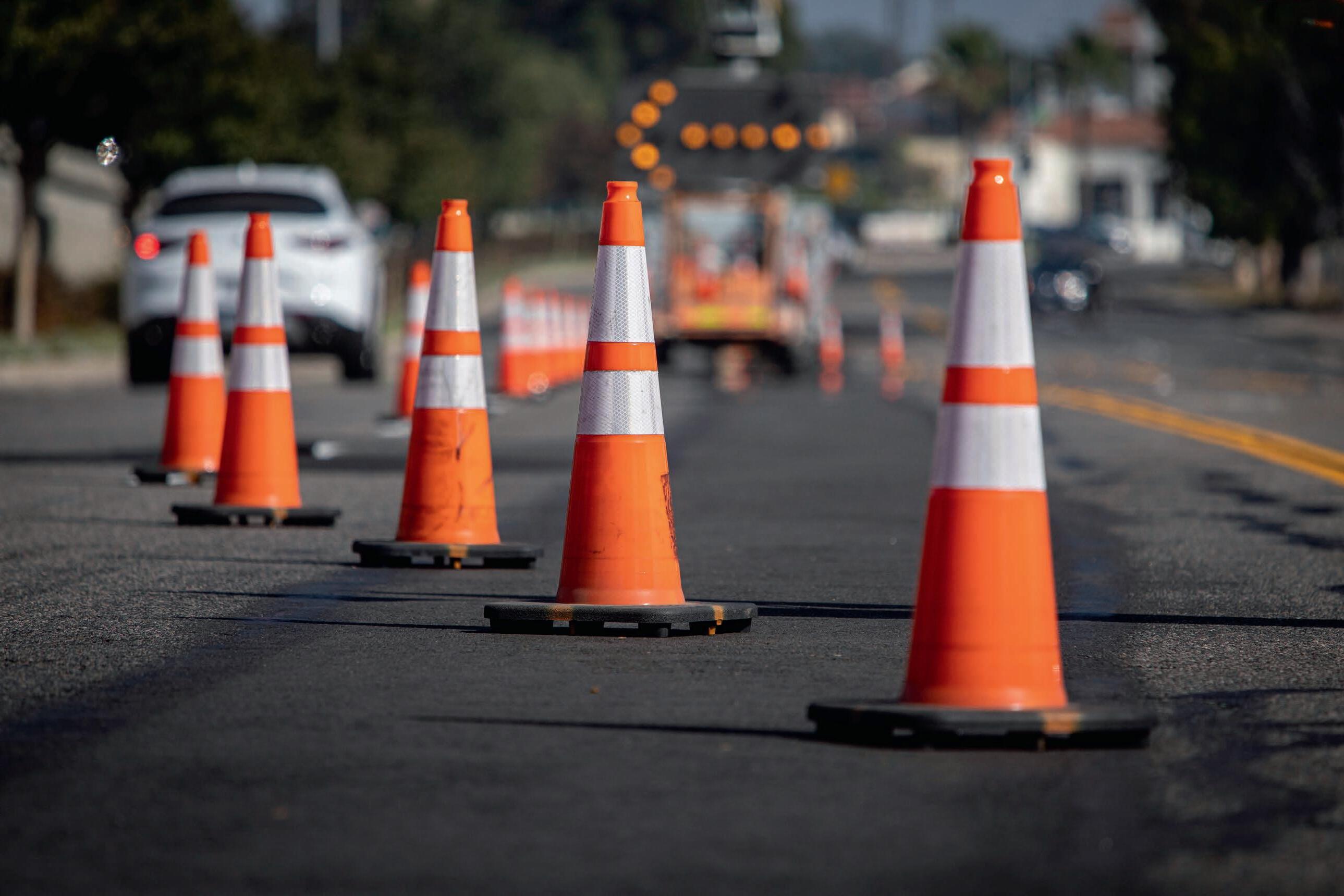
Air quality
Take action against welding fume exposure
WHILE THE RISKS POSED BY WELDING FUME ARE SERIOUS, KEEPING SAFE CAN BE STRAIGHTFORWARD.
In January 2024, Work Health and Safety Ministers agreed to an 80 per cent reduction to the Workplace Exposure Standard (WES) for welding fume from five milligrams per cubic metre (mg/m3) of air to 1mg/m3.
All Australian workplaces must now comply with this new lower limit by law, sending a clear message to the welding industry that welding fume is serious, and action is required.
This message has in turn encouraged welding businesses to review their risk assessments, revise their welding fume control measures, and work towards minimising exposure to as low as reasonably practicable.
So what are the key considerations to ensure a workplace is up to standard?
MONITOR WELDING FUME
Firstly, it is important for employers to gauge the effectiveness of their current welding fume control framework.
The AeroGuard Air Monitor can measure the welding fume level in a workplace in real-time. This allows businesses to understand the quality of their workshop air in relation to the NEW Workplace Exposure Standard for Welding Fume (1mg/m³).
The AeroGuard is equipped with a diverse array of sensors capable of detecting a variety of pollutants and climate factors that impact comfort and wellbeing:
• Particulate matter (eg welding fume)
• Volatile organic compounds
• Carbon dioxide
• Temperature
• Humidity
• Sound
• Atmospheric pressure
• Indoor Air Quality Index

A 360° LED ring keeps users perpetually updated by alternating between green (good), yellow (moderate) and red (unhealthy) according to the air quality in their work environment.
As a result, with an AeroGuard at their disposal, businesses are well placed to identify the risks to their workers and optimise their welding fume control measures accordingly.
PROTECTING WELDERS
The important point to understand is that while the risk posed by welding fume is serious, keeping welders safe can be straightforward.
Welding helmets with integrated Powered Air Purifying Respirators (PAPR) have been established as “the most widely used form of respiratory protection amongst welders in Australia and New Zealand”.1.
This widespread trust in powered air systems has been reinforced by the results of an independent scientific study comparing the relative effectiveness of common welding fume product controls.
Among many eye-opening findings from the study, perhaps the most notable was that PAPR welding helmets demonstrated an Effective Protection Factor (EPF) of at least 2600 – a level of performance 52 times better than the Required Minimum Protection Factor (RMPF) of 50 specified in the Australian and New Zealand standard for respiratory protection (AS/NZS1715:2009)2
This EPF equates to a reduction in welding fume exposure of at least 99.96 per cent; as such, the powered air welding helmet used in the study emerged as by far the most effective control measure in protecting the welder from welding fume exposure when compared to on-gun fume extraction or hooded capture Local Exhaust Ventilation (LEV). 2
A welding helmet with an integrated PAPR also provides protection to the welder’s eyes and face from radiation, heat, sparks, splatter, and foreign objects.
Based on the results of the study, PAPR welding helmets should be considered a priority in
The AeroGuard Air Monitor.
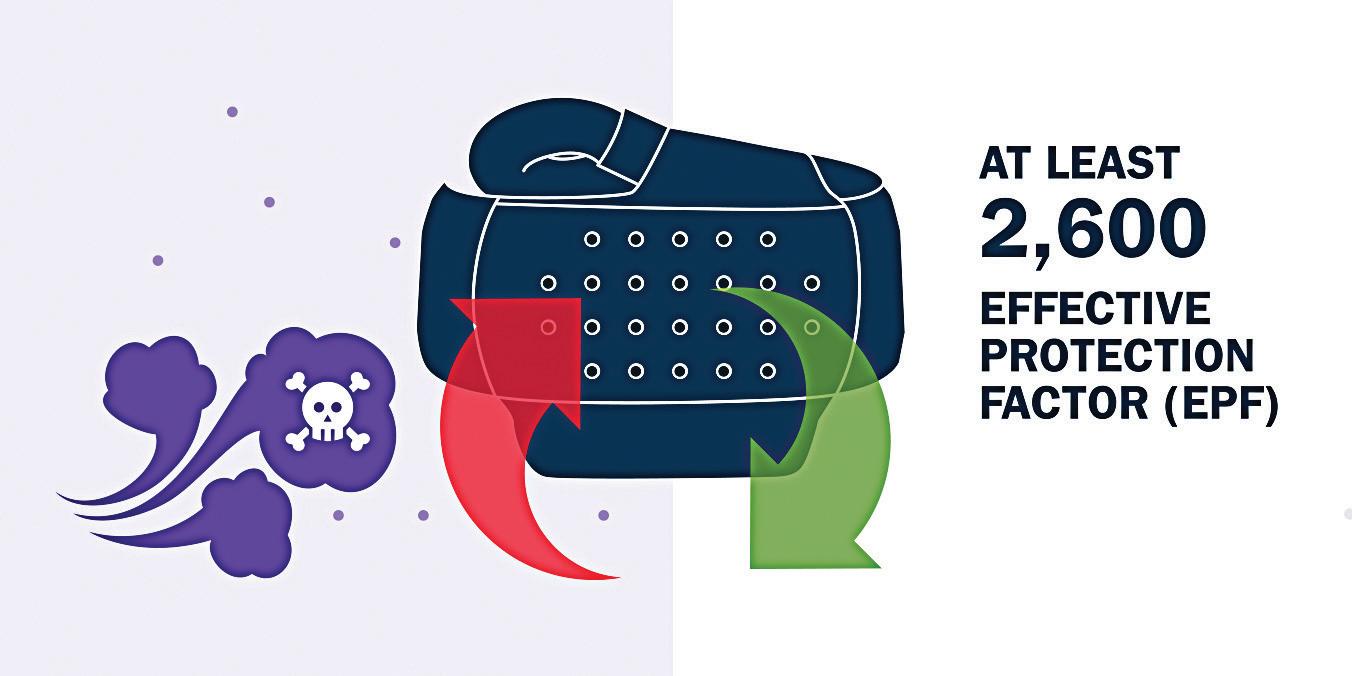
situations where the welder is the only person requiring protection against welding fumes, in environments with good ventilation.
PROTECT SURROUNDING WORKERS
Given the fact a welding fume particle that is 0.5 micrometres in size can take two days to reach the floor from a height of 1.5m, it is apparent that the air in welding environments can contain respiratory hazards long after welding has been completed.
It is an employer’s legal responsibility to reduce welding fume exposure to
as low as reasonably practicable for all persons, not just the welder.
On-gun fume extraction and hooded capture LEV are two common methods used to capture welding fume directly at the source and remove it from the environment altogether; the most effective way to ensure surrounding workers are not exposed.
Per the aforementioned study, on-gun fume extraction was found to remove 33 per cent more welding fume from the environment than its hooded capture counterpart.
On-gun fume extractors also boast the added benefit of following the
According to a 2023 scientific study, on-gun fume extraction was found to remove 33 per cent more welding fume from the environment when compared to hooded capture LEV.
The study found PAPR welding helmets have demonstrated an effective protection factor 52 times better than the required minimum protection factor.
welder as they move, while fixed LEV hooded capture requires the welder to be perfectly positioned relative to the capture hood and for the welder and welding arc location to remain relatively stationary.
What’s more, on-gun technology has now evolved to address criticisms that the guns were too heavy, cumbersome, inconsistent, and interfering with the shielding gas.
Consequently, when the priority is capturing welding fume at the source to protect all workers in the workplace, on-gun fume extraction (if suitable for the application*) should be used in tandem with PAPR welding helmets.
* Please note that on-gun fume extraction is not compatible with all applications (eg MMA stick welding).
1 Welding Fume Product Controls Survey, AWS, June 2023 (560 respondents).
2 2023 Peter Knott, Georgia Csorba, Dustin Bennett, Ryan Kift. Welding fume; a comparison study of industry used control methods. Safety Journal.
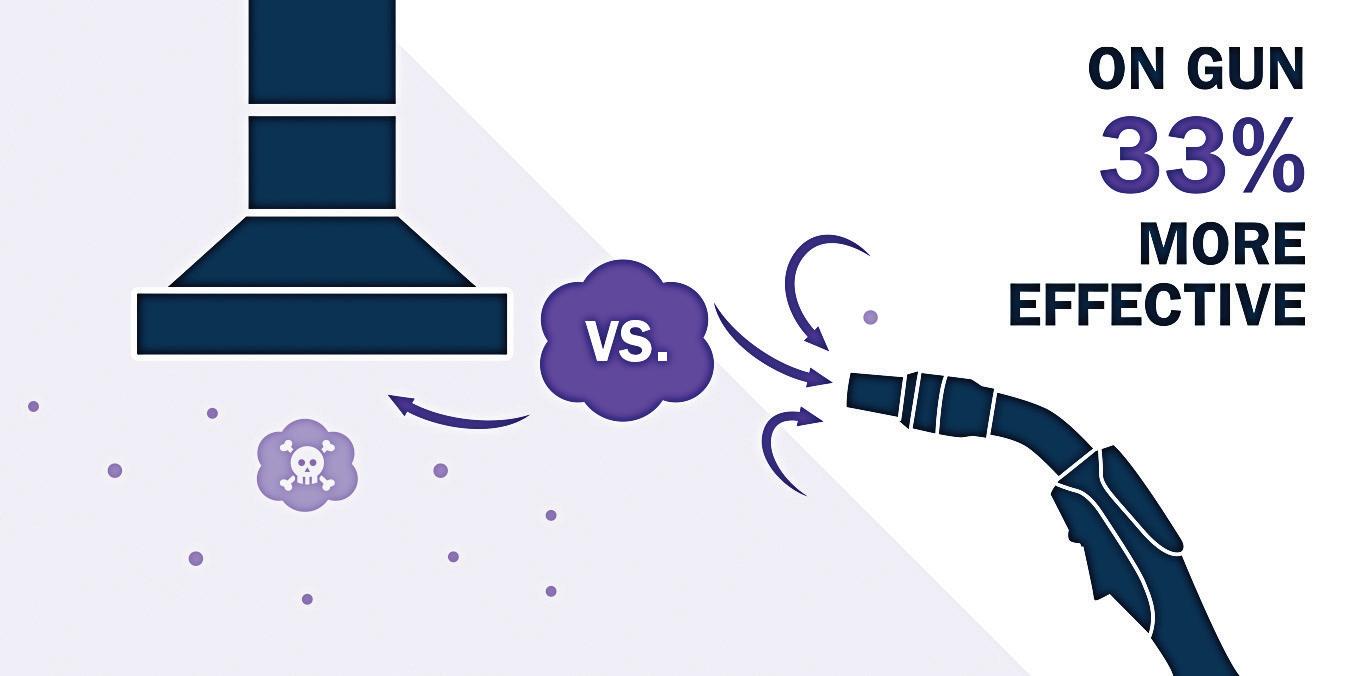
Taking collision avoidance to the next level
EPIROC IS SIMPLIFYING SAFETY ABOVE AND BELOW THE GROUND.

Pretty much everywhere you walk on a mine site, there is a potential hazard.
While the industry is full of processes, risk assessments and preventive measures to better enforce workplace safety, incidents will unfortunately still take place. According to Safe Work Australia, vehicle incidents and being hit by moving objects accounted for more than half of all worker fatalities in 2022.
To reduce workplace accidents and fatalities, mining operations can implement a collision avoidance system (CAS) that is simple and robust.
Enter Epiroc’s Titan CAS.
Currently in its fourth generation, the Titan CAS symbolises Epiroc’s ambition to drive digital innovation in the mining industry.
“Titan is a robust and versatile solution designed to enhance safety
in mining operations,” Epiroc global director product management Hans Wahlquist told Safe to Work
“Developed and refined over 10 years in harsh South African mining conditions, it offers a comprehensive range of sensor technologies that allow operators to effectively manage proximity risks between vehicles and pedestrians across both underground and surface mining environments.”
The Titan CAS has been designed so it can be utilised on all mining machines and across all systems.
“The Titan CAS provides realtime alerts, advice and intervention for dangerous proximity situations straight from the control room to the cockpit, empowering operators to make informed decisions and take appropriate action to avoid collisions,” Wahlquist said.
“Special proximity tags are also available for pedestrians,
further enhancing overall safety by alerting them whenever a proximity situation occurs.”
Titan detects collisions while also acting as the central interface, coordinating and sending out information when miners need it most.
“Epiroc’s Titan CAS automatically takes control of the machine to slow down and stop it if the operator is unable to do so, providing an unparalleled level of safety,” Wahlquist said.
“It also offers a variety of available technologies, including low-frequency, time-of-flight, global positioning system [GPS], and artificial intelligence [AI] cameras, allowing for customisation and optimisation to suit each operation’s specific risk requirements.”
Underground miners have to contend with tighter spaces and less time to act when obstacles occur,
Images: Epiroc
Collision avoidance includes potential vehicleto-vehicle and person-to-vehicle incidents.
while surface mining can be just a fraught with stray personnel and more vehicles reaching higher speeds.
Through its communication and positioning capabilities, Titan can monitor vehicle-to-vehicle (V2V), vehicle-to-pedestrian (V2P), and vehicle-to-equipment (V2E) proximity risks across an entire mining operation, whether underground or on the surface.
“In surface mining, positioning can often be solved by using available technology like GPS, while communication is quite straightforward, using modern mobile phone [LTE] technology,” he said. “V2V, V2P and V2E might need various technologies to perform well.
“In underground mining, positioning is much trickier to solve and sometimes needs a variety of technologies to enable the right accuracy for specific use cases. Most common in today’s underground mines are Wi-Fi or Wi-Fi and Bluetooth. Communication in underground mines is made predominately by Wi-Fi or LTE.
“By enabling usage of multitechnology, multi-vendor solutions for both communication and positioning, we can optimise a solution based on the customer needs.”
While collision avoidance is an essential technology on any modern mine site, it is not a silver bullet.
Epiroc’s Mobilaris Onboard solution can be applied to Titan to maintain a lookout for immediate danger while it does the heavy lifting of site-wide traffic management.
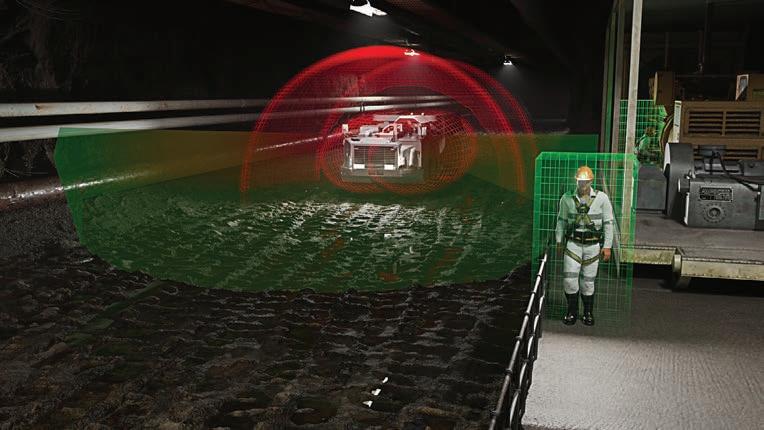
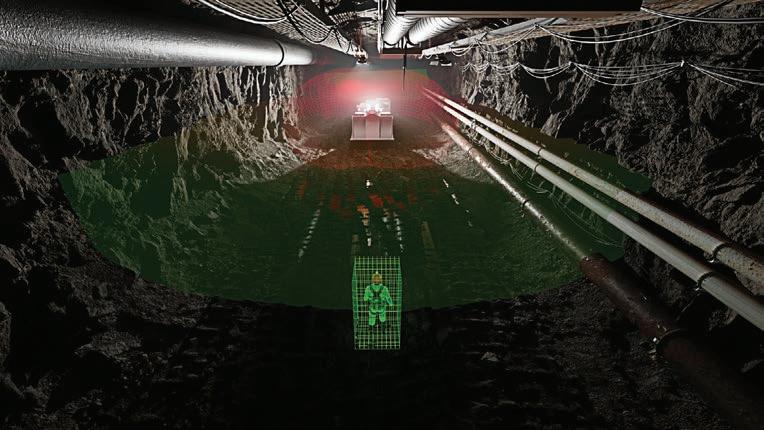
would probably not avoid metal-tometal at such speeds.
Mobilaris provides navigation in an underground mine even without any network coverage, as well as early warnings for any incoming vehicles within a 600m range.
Wahlquist said the solution doesn’t replace common sense but is a vital tool that even allows users who have never set foot on site before to navigate with ease.
“Imagine two trucks driving quite fast – say, 30k/ph – towards each other near a tight corner. A CAS solution will not solve that situation,” he said. “Even if you had CAS level nine, which is an automatic brake, it
“Now imagine a vehicle with only Mobilaris Onboard. That will warn you about incoming collisions far in advance, giving you time to decide if you want to proceed driving or find the best parking bay quickly, but it won’t warn you for a pedestrian walking close to your vehicle.
“That’s why we combine the two state-of-the-art solutions and create the best of both worlds.”
Wahlquist said combining Titan and Mobilaris has resulted in significant safety and productivity enhancements.
“The early warnings for incoming traffic makes driving safer and
increases productivity, as it leads to better traffic flows with fewer unplanned stops or congestions. Some mines have measured this and seen a huge improvement in haulage tonnes,” he said. “For the driver, the work environment gets much less stressed and it leads to much less chatter on the radio.”
Epiroc’s digital division is growing rapidly as technologies continue to develop. The company has made a number of recent acquisitions like the Titan CAS and Mobilaris that have the potential to create similar synergies on sites across Australia.
It’s that kind of innovation that puts mines in the path of success.
Epiroc is working to simplify collision avoidance above and below the ground.
Effective collision avoidance is vital in a dynamic mining environment.
Like a beast
NIVEK INDUSTRIES’ BEAST OF BURDEN – BOB –HEAVY-LOAD CARRIERS CAN BE ADAPTED TO MEET MINING CUSTOMERS’ SPECIFIC
REQUIREMENTS.
Since the release of its Tracked Elevated Device (TED) in 2011, Nivek Industries’ has significantly grown its product portfolio.
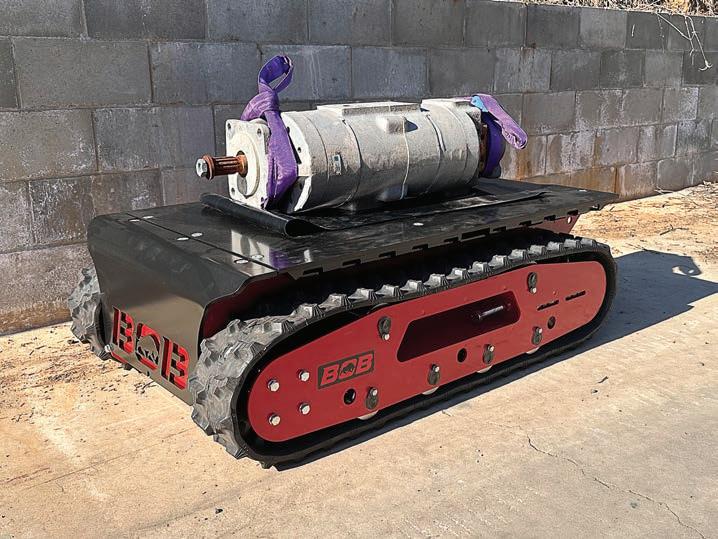
“The TED alone has over 40 different attachments, and we have a bigger version of the TED, the Big TED, for heavier loads,” Nivek general manager Derrick Cant told Safe to Work.
“We have two lift assist arms, the LA40 and the LA-80, with a lifting capacity of 40kg and 80kg, respectively.”
To take its range to the next level, Nivek has spent the last 12 months developing a new range of low-profile heavy-load carriers named the Beast of Burden (BOB). Designed to carry heavy loads for long distances, BOB is a mobile, remote-controlled and allterrain tracked carrier.
Currently available in 500kg (the 0.5T model), 1500kg (the 1.5T model) and 5000kg (the 5T model), each BOB carrier has been built to comply with three key Australian standards: AS1170.0, AS1170.1 and AS4100.
The 0.5T and 1.5T models are powered by dual 48-volt lithium batteries that provide 4.6 kilowatt hours (kWh) of power to the 3.5kW electric motor power unit, in turn driving the two independent hydraulic drive motors.
The 5T model is fully electric, incorporating dual electric drive motors and a battery supply of up to 14kWh.
“Besides the working load limits, the main differences between the
0.5T and 1.5T machines are the type of tracks it utilises, rubber and steel, respectively,” Cant said.
“The 0.5T BOB with rubber tracks is designed to carry loads that are too heavy or awkward to lift manually and to areas where a forklift is unable to reach. The rubber tracks also allow the 0.5T to climb a staircase.
“The 1.5T BOB with its increased carrying capacity is designed to carry heavier loads to areas a forklift is unable to reach. Its increased capacity and small footprint make it a useful carrier.
“The 5T BOB is designed to carry extremely heavy components around the worksite. With its manoeuvrability and large battery system, operators can transport those large components around the workshop safely.”
Wireless remote control allows BOB operators to stand clear of the load being carried, helping to ensure safety and visibility as they move around to obtain the best view.
Known for the durability, both electric motors in the BOB machine allow it to produce enough torque to ensure heavy loads can be carried across various types of tough terrain.
“The BOB was developed to compliment the TED range to provide a long-distance carrying option, something the TED is unable to provide,” Cant said.
BOB carriers are built to handle heavy loads in various types of tough terrain.
“BOB is more than just a carrier.”
BOB machines are fitted with an auxiliary (AUX) power outlet, which allows the carrier to be modified with custom-made smart attachments to suit a variety of tasks and requirements, demonstrating versatility and flexibility. BOB is essentially a mobile, adaptable, powerhouse, capable of undertaking a wide variety of jobs.
BOB 5T has been successfully utilised at a Chilean mine site to transport a four-tonne valve during a regular maintenance changeout.
The task usually requires a full team and three shifts to complete. However, the customer was able to complete the task in half the time when using BOB 5T.
To further enhance the BOB range for its customers, Nivek is developing several new multi-purpose attachments for the 0.5T, 1.5T and 5T models.
The company is even looking to create BOB models that can carry 10,000kg and 20,000kg.
“Nivek designs and builds products that can be adapted to suit customer requirements,” Cant said.
“This has been done deliberately to allow us to develop specific attachments to meet individual customer needs without having to fully develop an entirely new machine.”
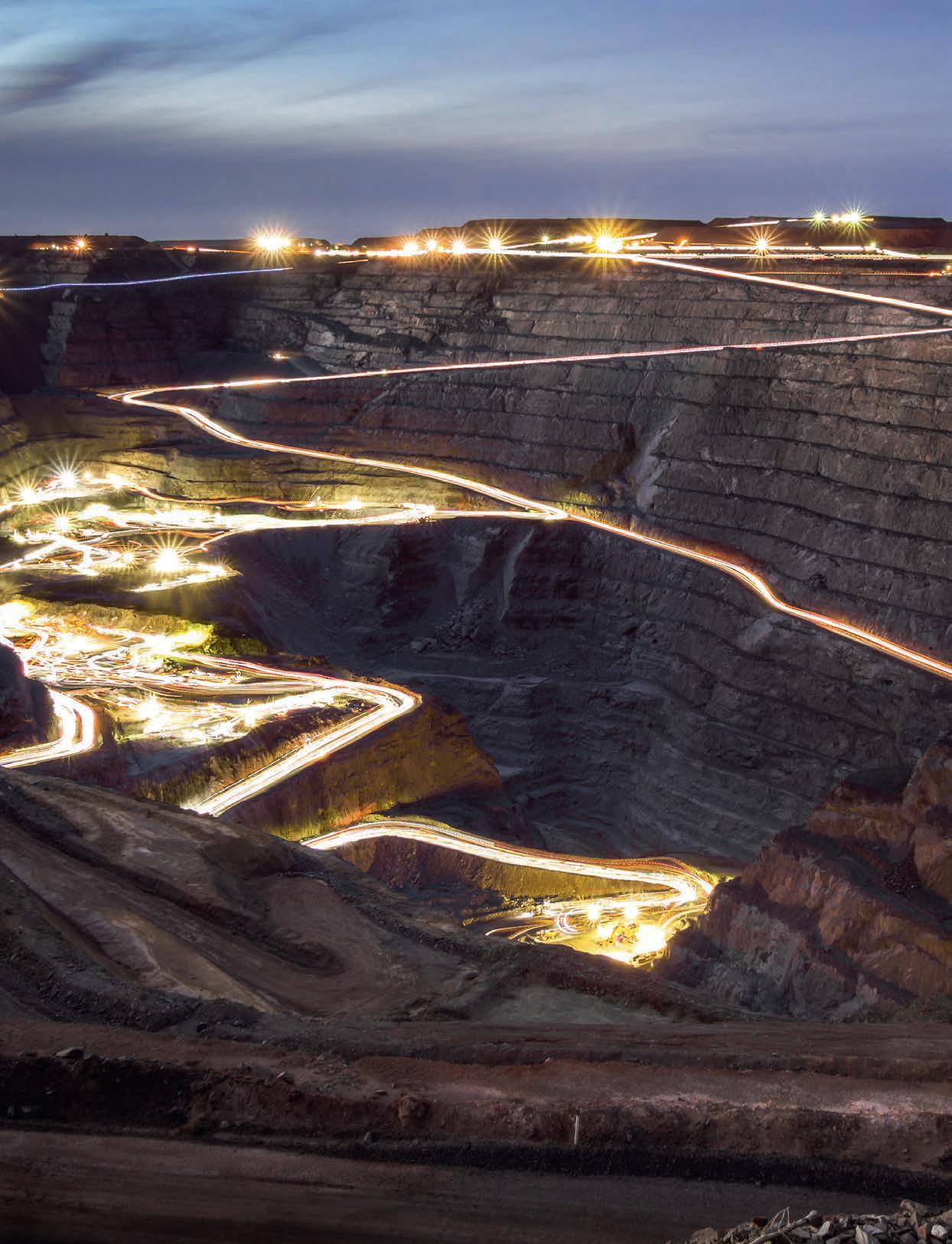
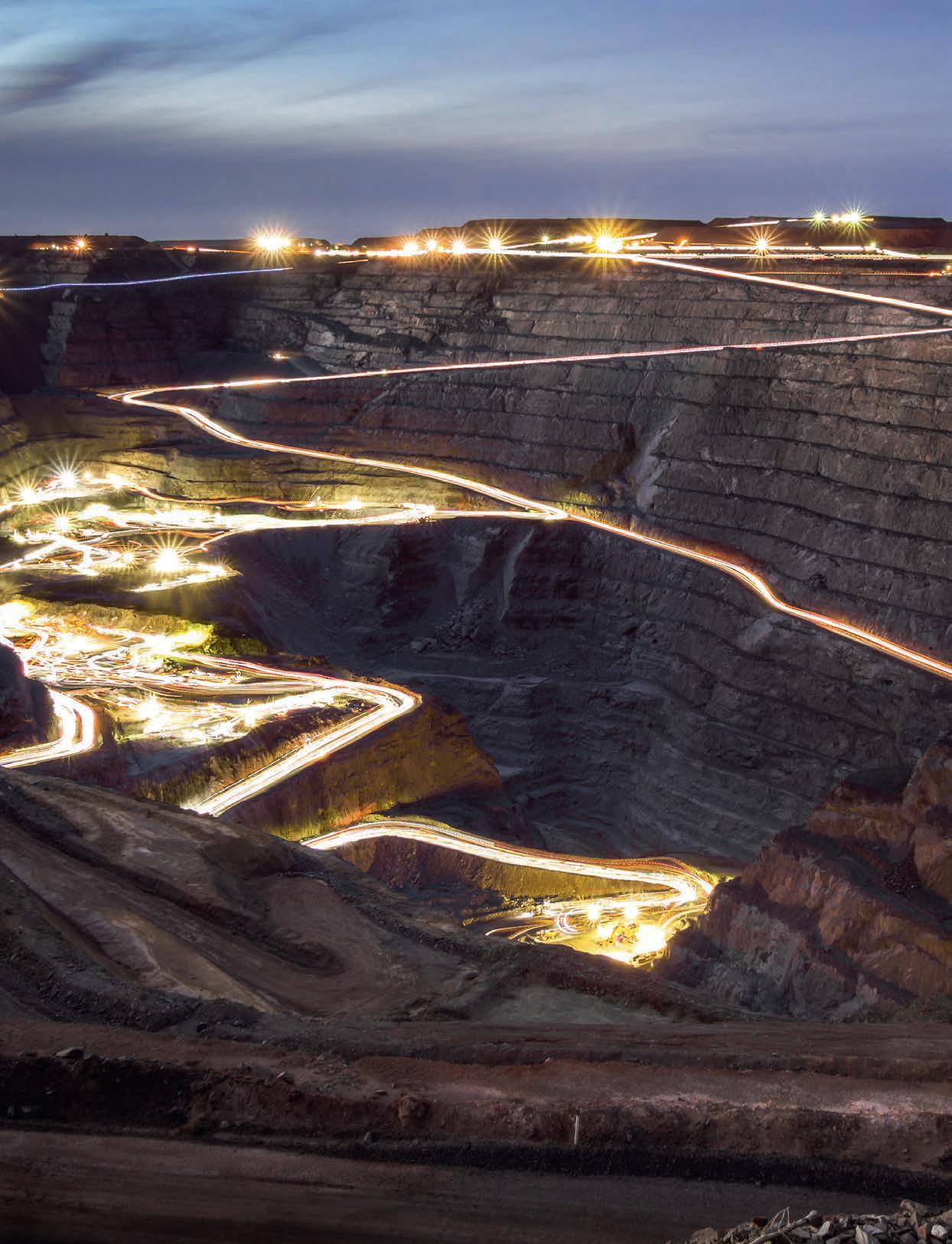
AIMEX PROVIDES AN UNMATCHED OPPORTUNITY TO CONNECT AND DO BUSINESS WITH LEADING MINING SUPPLIERS FROM AROUND THE WORLD.
Protection and sustainability hand-in-hand
MECHANIX WEAR IS ON A MISSION TO PROTECT MINERS WHILE BOOSTING LONG-TERM SAVINGS AND SUSTAINABILITY FOR AUSTRALIA’S MINES.
Investing in high-quality personal protective equipment (PPE) is one of the most essential aspects of keeping workers safe. Quality PPE like the gloves offered by Mechanix Wear allows workers to get on with the job. Each pair is crafted to stand up to the test of harsh conditions while maintaining integrity and staying comfortable, promoting all-day wear.
Mechanix Wear prides itself on its acute understanding of the hazards workers face.
“Our gloves provide superior protection against cuts and impacts, two of the most common hand injuries in the mining and industrial sectors,” Mechanix Wear told Safe to Work
“The size range, from XXS to XXXL, ensures a perfect fit for every worker, enhancing comfort and reducing the likelihood of gloves being removed during critical tasks.”
But protecting hands is only part of Mechanix Wear’s mission. The company is equally committed to protecting the planet.
By working with Mechanix Wear, customers can take advantage of the company’s comprehensive waste management solutions. Mechanix Wear assists its customers in setting up recycling programs, provides guidance on proper disposal, and offers take-back programs to ensure gloves are recycled efficiently.
This proactive approach to waste management helps Mechanix Wear customers reduce their environmental impact and aligns with broader corporate sustainability goals.
“Our Speedknit Eco gloves are made from recycled materials and are fully recyclable through Upparel at the
end of their lifecycle,” the company said. “This 360° approach to sustainability means that every glove we produce not only provides topnotch protection but also contributes to a healthier environment.
“This is a key differentiator for Mechanix Wear. While some focus on biodegradability – which doesn’t prevent products from ending up in landfills and lacks auditability – Mechanix Wear takes a different approach.
“Our strategy focuses on completely eliminating gloves from ending up in landfills, ensuring a process that is 100 per cent auditable.
“By choosing Mechanix Wear, companies can ensure they are reducing their environmental impact while maintaining the highest standards of worker safety.”
As part of its commitment to environmental responsibility, Mechanix Wear carries the Global Recycling Standard logo, verifying that its products are made from recycled materials and its manufacturing processes meet stringent environmental and social criteria.
“To ensure you are working with genuinely sustainable products, always look for the Global Recycling Standard logo and request to see certification documents,” the company said.
“Mechanix Wear provides these certifications, giving you confidence that our claims are backed by rigorous standards.”
Mechanix Wear offers a comprehensive solution for companies in the mining and industrial sectors looking to enhance safety and sustainability.
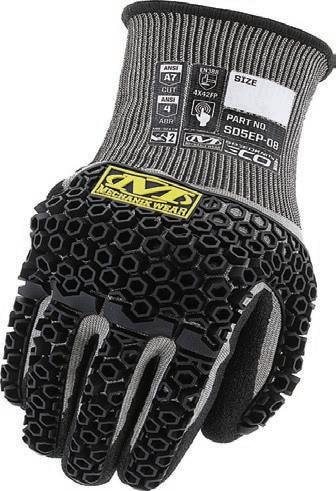
replacements.
By choosing Mechanix Wear, companies are on track to achieve significant cost savings through reduced consumption of PPE and lower logistics costs.
The ultimate goal of any PPE company is to ensure workers can perform their tasks safely and efficiently, and Mechanix Wear is confident its gloves provide “unparalleled” protection and comfort. Its approach to PPE combines hand protection with a strong commitment to environmental sustainability.
Mechanix Wear gloves are designed reduce consumption and waste, and are backed by reputable certifications and comprehensive waste-management solutions.
“Protecting hands and the planet is not just a slogan for us; it’s a core part of our mission,” Mechanix Wear said.
“By choosing Mechanix Wear, companies can be confident they are making a responsible and sustainable choice that benefits both their workers and the environment.”
Image: Mechanix Wear
Mechanix Wear’s gloves last longer and reduce the need for frequent
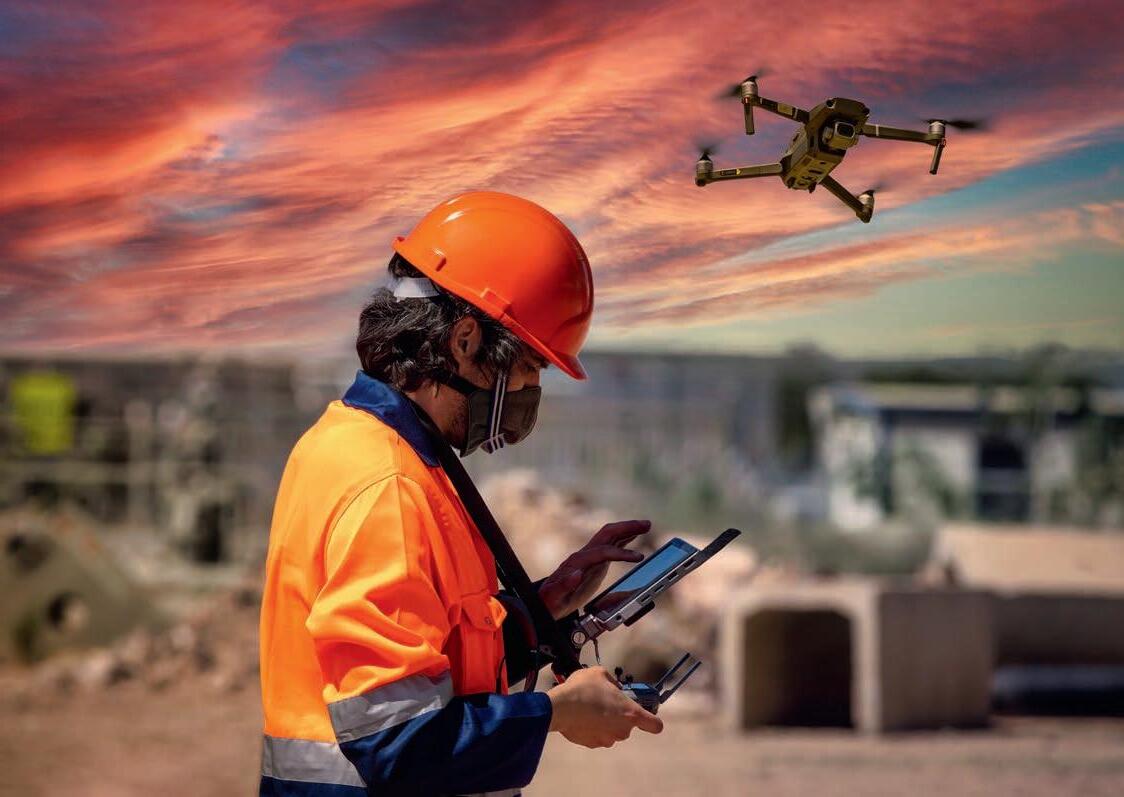
9–10 October 2024 Perth Convention & Exhibition Centre
Featuring a highly targeted conference, seminar series, and 100+ leading mining suppliers.
Ensuring safety and efficiency
IN
THE
HIGH-STAKES WORLD OF MINING, RELIABLE
COMMUNICATION ISN’T JUST A CONVENIENCE –IT’S A LIFELINE.

Very high frequency terrestrial trunked radio (VHF TETRA) has emerged as a “game-changer” in the way mining companies approach communication challenges.
COMMUNICATION CHALLENGES AND RISKS IN MINING
Operating in mining environments presents a host of communication challenges that impact efficiency and safety. The remote locations of many mining sites, coupled with expansive and rugged terrain featuring underground tunnels, deep pits and rocky landscapes, pose significant obstacles to signal transmission.
Mines are inherently hazardous environments due to risks like cave-ins, explosions, dust, and toxic substances. Users often face signal degradation, limited coverage, and connectivity issues, especially in remote or underground areas.
Electromagnetic interference (EMI) from heavy machinery and equipment is a significant issue, disrupting wireless signals.
Multi-path propagation exacerbates communication problems, causing signal distortion and fading as radio waves bounce off surfaces such as walls and machinery, particularly in underground mines with reflective surfaces.
Compliance with safety regulations, such as those set by regulatory bodies like the Mine Safety and Health Administration (MSHA), is essential. These standards govern transmitter power levels, antenna installations, and frequency usage to help mitigate interference and uphold worker safety.
VHF TETRA presents a solution for large-scale mining environments by consolidating multiple networks into a single system that operates above and below ground.
Above ground, VHF signals travel far in open areas, providing a costeffective and reliable communication solution with clear audio, even in noisy conditions. Below ground, the ability to propagate signals in tunnels via a leaky feeder makes it well suited to complex underground networks.
VHF TETRA is safe, reliable and robust. The system is built to withstand the mining environment, offering interference resistance to explosives, dirt, dust and heavy machinery. Its reliability helps to improve personnel safety, providing prompt alerts for evacuations or coordinated rescue efforts.
VHF TETRA can also be costeffective. It requires minimal infrastructure and maintenance and can help streamline workflows and boost productivity, making it a more sustainable choice for long-term deployment in mining operations.
Sepura’s VHF TETRA radios have been described as a “game-changer”.
Images:
Sepura
SEPURA’S VHF TETRA SOLUTION FOR MINING
Recognising the unique communication needs of the resources sector, Sepura has developed a suite of TETRA products tailored specifically for mining environments: the SC Series.
“Combining the reliability and security of TETRA with the longer range signal propagation at VHF frequencies plus the powerful audio processing of the SC Series radios sets a new standard for communication excellence in the mining industry,” Sepura said.
According to Sepura, the SC Series allows mining organisations to establish a robust VHF TETRA solution with many benefits:
Enhanced
VHF solutions provide enhanced coverage in expansive outdoor areas, underground tunnels using leaky feeder, and complex terrains.
Streamlined infrastructure
Extended coverage means fewer communication infrastructures are needed, resulting in reduced set-up and maintenance costs, as well as quicker deployment across sites.
GNSS location services
Integrated GNSS (global navigation satellite system) services allows for tracking, triggers and emergency response, improving situational awareness and safety.
Rugged design
Built to endure mining conditions, with magnetic shielding to mitigate metal dust build-up, the radios are equipped with water and dust-resistant technology. Their inherent haptics are designed for use with gloved hands, ensuring performance in all conditions.
Versatile communication modes
Access various communication modes like SMS, SDS, direct (DMO), trunked (TMO), and gateway operation, along with feature-rich applications for enhanced functionality.
Efficiency and safety features
AppSPACE links teams, devices and systems by transmitting operational data across TETRA, Wi-Fi and Bluetooth. This connectivity allows for streamlined workflows and ensures crucial situational awareness information reaches the appropriate individuals quickly.
AppSPACE allows customised applications to be added to radios already in the field without disrupting any critical TETRA communications.
Emergency response capability
Features like Man-Down and Lone Worker help keep workers safe by detecting emergencies, and the SmartView app locates individuals in an emergency.
Streamline processes
The AutoMate app automates tasks, helping mining companies streamline processes, improve worker
safety, and protect valuable assets. RadioAsset allows fleet managers to access crucial information such as software versions and battery manufacture dates, providing valuable maintenance information, as well as the ability to run an audit to keep track of the products.
Wireless programming
Over-the-Air Programming allows for secure configuration updates and asset management over approved Wi-Fi networks, simplifying maintenance and upgrades.
“VHF TETRA stands as a gamechanger for mining safety, offering unparalleled reliability, coverage and functionality tailored to the unique demands of the industry,” Sepura said.
“With Sepura’s innovative VHF TETRA solutions, mining operations can achieve new levels of efficiency, productivity and, above all, safety.”
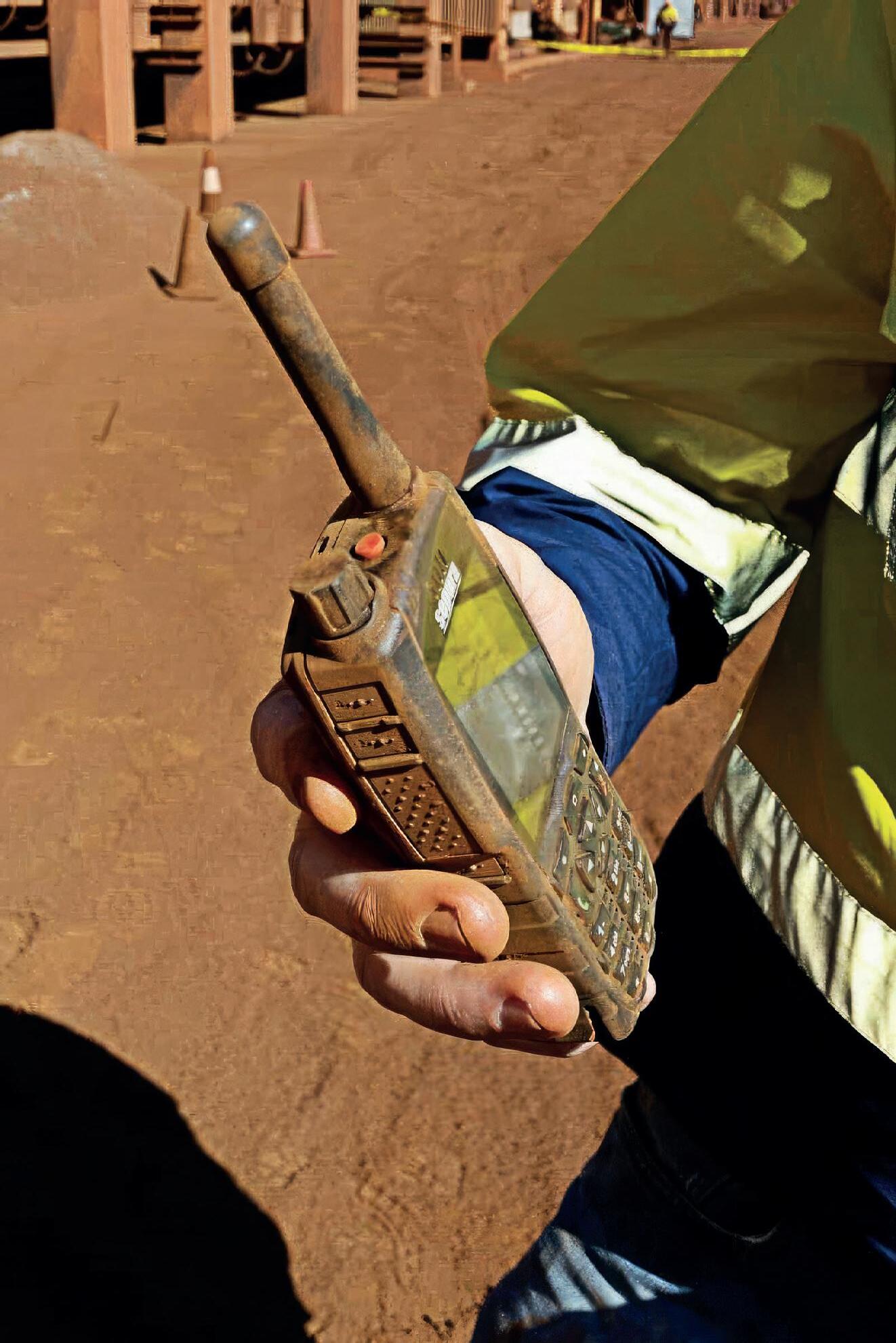
Sepura’s radios feature waterand dust-resistant technology.
Events
QMIHSC 2024 took place on the Gold Coast from August 18–21.
A safety ripple effect
THE 35TH QUEENSLAND MINING INDUSTRY HEALTH AND SAFETY CONFERENCE SHOWCASED THE BEST IN SAFETY TECHNOLOGY AND WORKPLACE CULTURE.
Since its first iteration more than three decades ago, the Queensland Mining Industry Health and Safety Conference (QMIHSC) has grown to become a leading event on the industry calendar.
After nearly two years of recovery, Jones started his career in commercial real estate. While he has seen great success in that field, Jones was motivated to make a difference in the health and safety space.
were valuable lessons from his story that needed to be shared on a wider scale.
“It was at the 2023 conference where I decided to throw my hat into the ring to be selected as a keynote speaker in 2024,” Jones said.
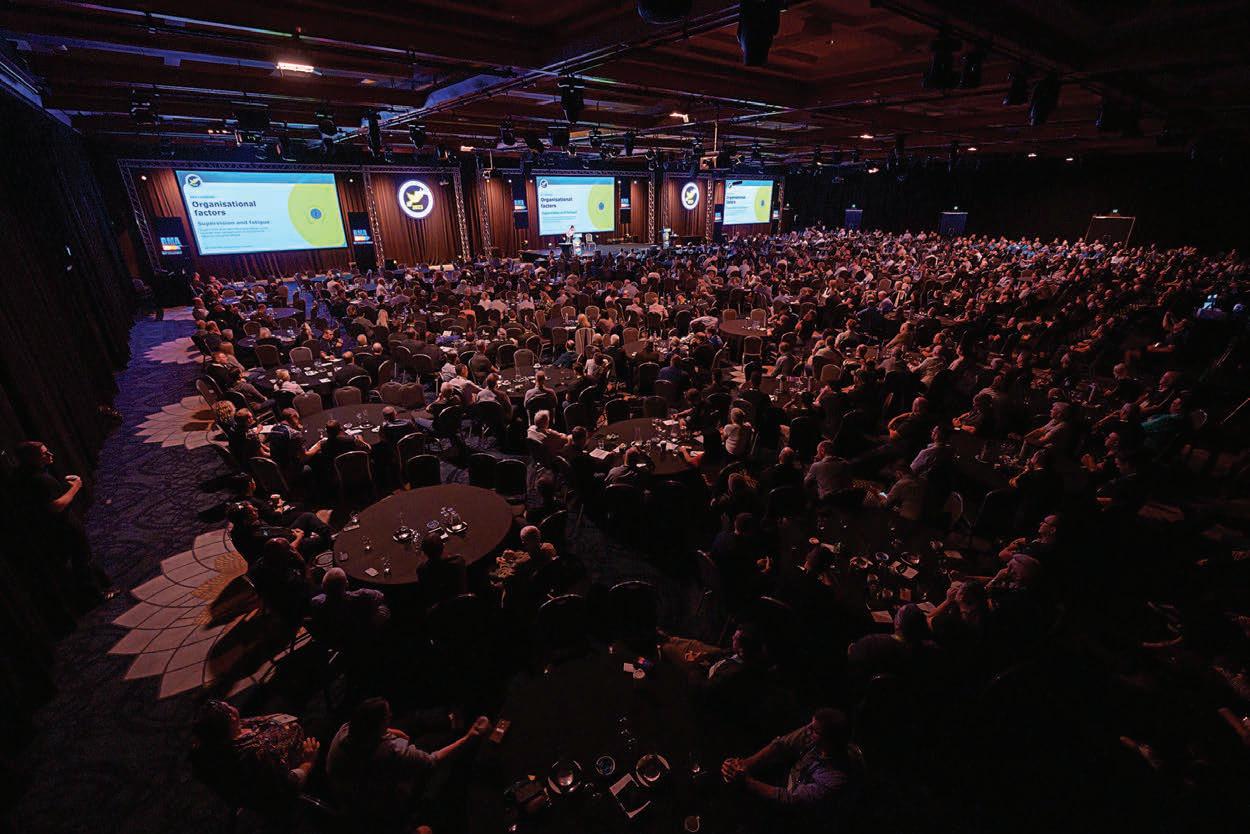
The annual conference provides the resources sector with opportunities to exchange information, form connections and foster proactive health and safety management techniques.
And the 2024 event more than lived up to this vision.
Held at the Star Gold Coast from August 18–21, this year’s QMIHSC had the theme of ‘Back to the future’, which explored whether the relative simplicity of the past can work in harmony with advancements in the present to create a safer future.
“This year’s content was relevant to industry’s changing health, wellbeing and safety landscape, covering current and future matters and catering to our diverse delegate cohort,” QMIHSC chair Larnie Mackay told Safe to Work
“I returned to the industry in 2023 where the main focus was to

“Extended interactions between our keynotes and delegates were positively embraced last year and this continued in 2024, with opportunities available to engage one-on-one.
“We encouraged delegates to share knowledge, expertise and insights into important health and safety matters with keynotes speakers and other delegates.”
Jones’ presentation at this year’s QMIHSC, ‘Ripple effect’, shed a light on the issues that contributed to his accident and how it changed his life, as well as others around him.
“By sharing my vulnerabilities with the industry, I hope to break down the stigma surrounding poor mental health and show others that we don’t need to be ashamed of having mental health issues and hide them but instead face them head on and be open with our families and work mates,” Jones said.
“Talking about these issues is one of our best solutions.”
Jones believes safety is more than a series of policies and procedures.

Josh Jones was among these keynote speakers. Beginning life in the industry as an apprentice diesel fitter in 2012, Jones’ mining career was cut short after a 2015 accident left him an amputee and resulted in the death of a colleague.
“I was invited to the 2023 QMIHSC as a guest by the Thiess safety team. I was impressed with the industry knowledge and innovative technologies in the safety space and was keen to be a part of it.”
The 2023 QMIHSC theme of ‘Inside looking out’ made Jones realise there
“We need to make safety personal and give our workers more ownership over their wellbeing,” he said. “We all have a part to play in improving safety across the industry and I feel that accountability is a huge step in moving in the right direction.
“We need to build more trust between our colleagues on-site. This is a vital component to creating a safer environment, as if we have colleagues that aren’t taking accountability for their actions, it will cause serious damage to the trust between workers.
“Everyone needs to remember that getting home to our families at the end of each day is not a given. The equipment we are surrounded by daily has potential to cause serious harm and we must not forget that.”

QMIHSC is Australia’s largest mining safety conference.
The event included critical safety lessons that can be employed in the mining industry.
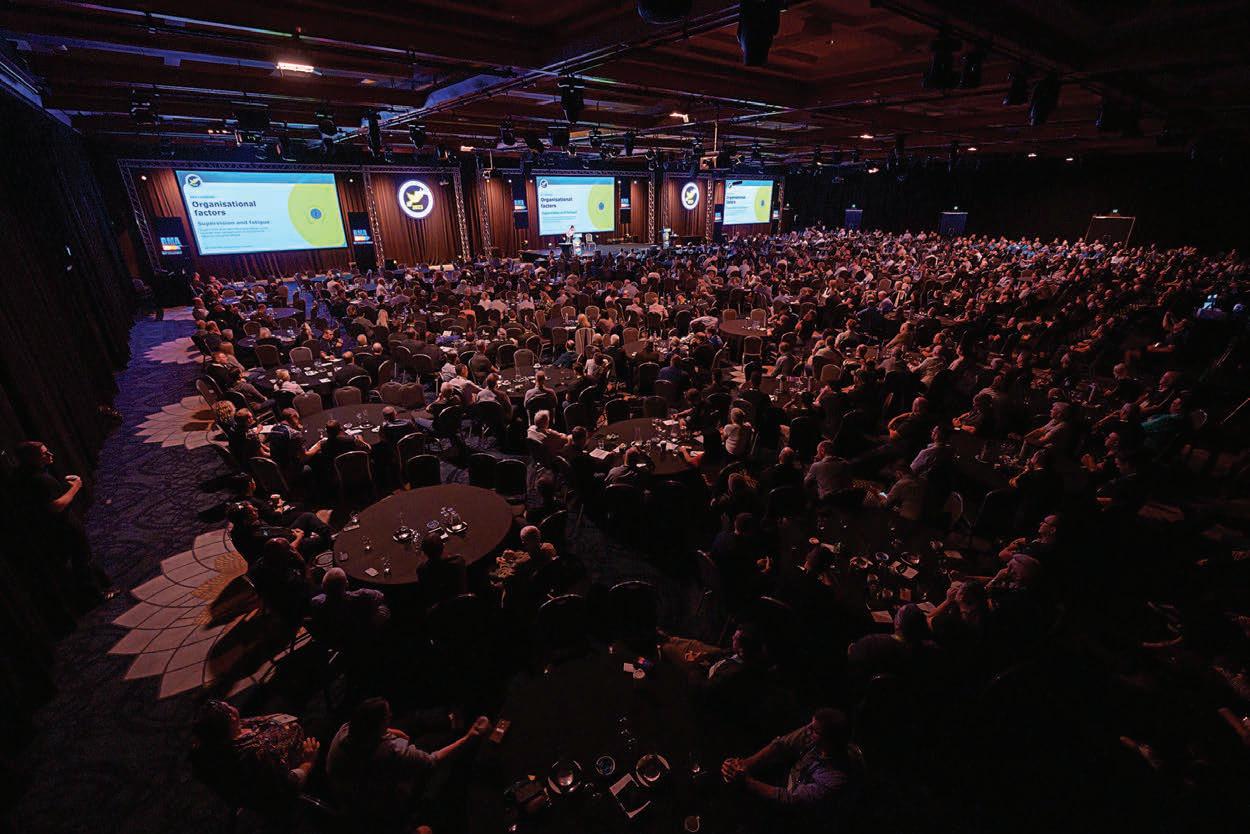

Events
QMIHSC 2024 took place on the Gold Coast from August 18–21.
A safety ripple effect
THE 35TH QUEENSLAND MINING INDUSTRY HEALTH AND SAFETY CONFERENCE SHOWCASED THE BEST IN SAFETY TECHNOLOGY AND WORKPLACE CULTURE.
Since its first iteration more than three decades ago, the Queensland Mining Industry Health and Safety Conference (QMIHSC) has grown to become a leading event on the industry calendar.
After nearly two years of recovery, Jones started his career in commercial real estate. While he has seen great success in that field, Jones was motivated to make a difference in the health and safety space.
were valuable lessons from his story that needed to be shared on a wider scale.
“It was at the 2023 conference where I decided to throw my hat into the ring to be selected as a keynote speaker in 2024,” Jones said.
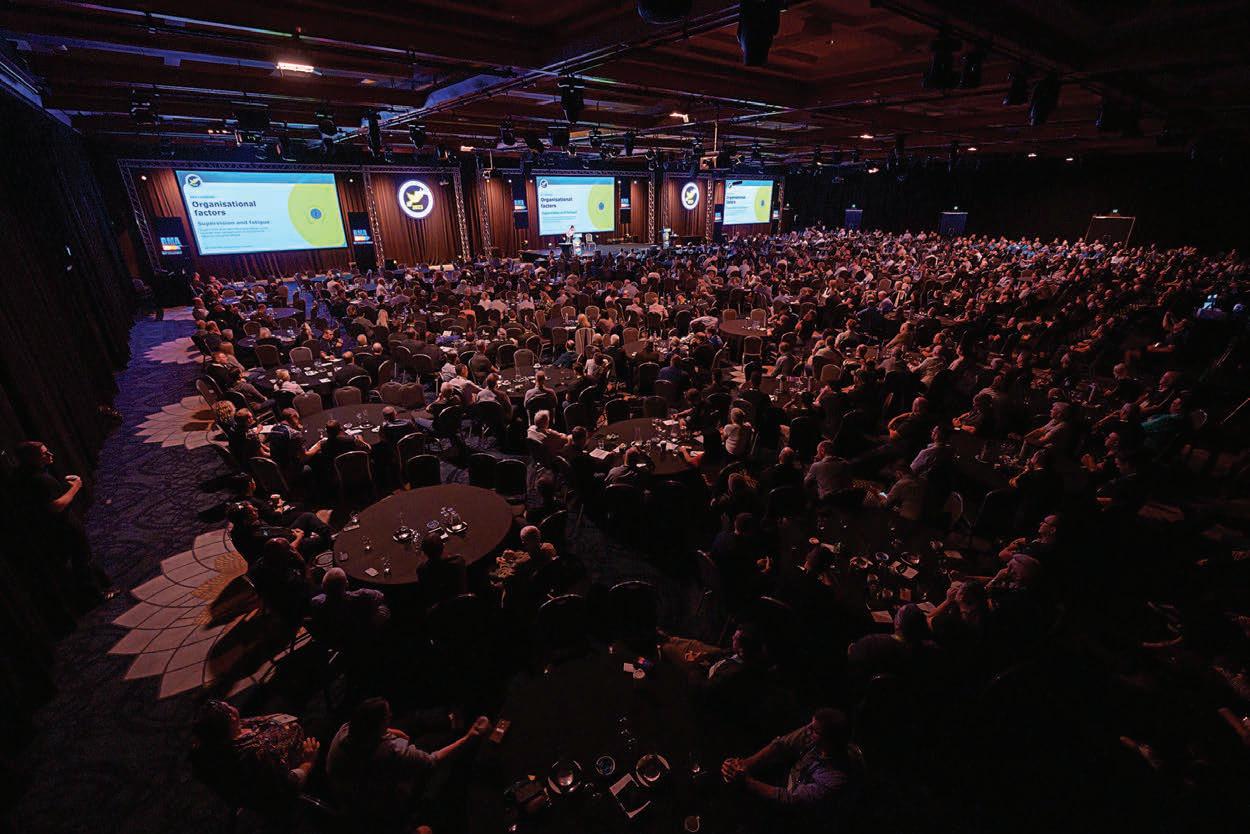
The annual conference provides the resources sector with opportunities to exchange information, form connections and foster proactive health and safety management techniques.
And the 2024 event more than lived up to this vision.
Held at the Star Gold Coast from August 18–21, this year’s QMIHSC had the theme of ‘Back to the future’, which explored whether the relative simplicity of the past can work in harmony with advancements in the present to create a safer future.
“This year’s content was relevant to industry’s changing health, wellbeing and safety landscape, covering current and future matters and catering to our diverse delegate cohort,” QMIHSC chair Larnie Mackay told Safe to Work
“I returned to the industry in 2023 where the main focus was to

“Extended interactions between our keynotes and delegates were positively embraced last year and this continued in 2024, with opportunities available to engage one-on-one.
“We encouraged delegates to share knowledge, expertise and insights into important health and safety matters with keynotes speakers and other delegates.”
Jones’ presentation at this year’s QMIHSC, ‘Ripple effect’, shed a light on the issues that contributed to his accident and how it changed his life, as well as others around him.
“By sharing my vulnerabilities with the industry, I hope to break down the stigma surrounding poor mental health and show others that we don’t need to be ashamed of having mental health issues and hide them but instead face them head on and be open with our families and work mates,” Jones said.
“Talking about these issues is one of our best solutions.”
Jones believes safety is more than a series of policies and procedures.

Josh Jones was among these keynote speakers. Beginning life in the industry as an apprentice diesel fitter in 2012, Jones’ mining career was cut short after a 2015 accident left him an amputee and resulted in the death of a colleague.
“I was invited to the 2023 QMIHSC as a guest by the Thiess safety team. I was impressed with the industry knowledge and innovative technologies in the safety space and was keen to be a part of it.”
The 2023 QMIHSC theme of ‘Inside looking out’ made Jones realise there
“We need to make safety personal and give our workers more ownership over their wellbeing,” he said. “We all have a part to play in improving safety across the industry and I feel that accountability is a huge step in moving in the right direction.
“We need to build more trust between our colleagues on-site. This is a vital component to creating a safer environment, as if we have colleagues that aren’t taking accountability for their actions, it will cause serious damage to the trust between workers.
“Everyone needs to remember that getting home to our families at the end of each day is not a given. The equipment we are surrounded by daily has potential to cause serious harm and we must not forget that.”

QMIHSC is Australia’s largest mining safety conference.
The event included critical safety lessons that can be employed in the mining industry.
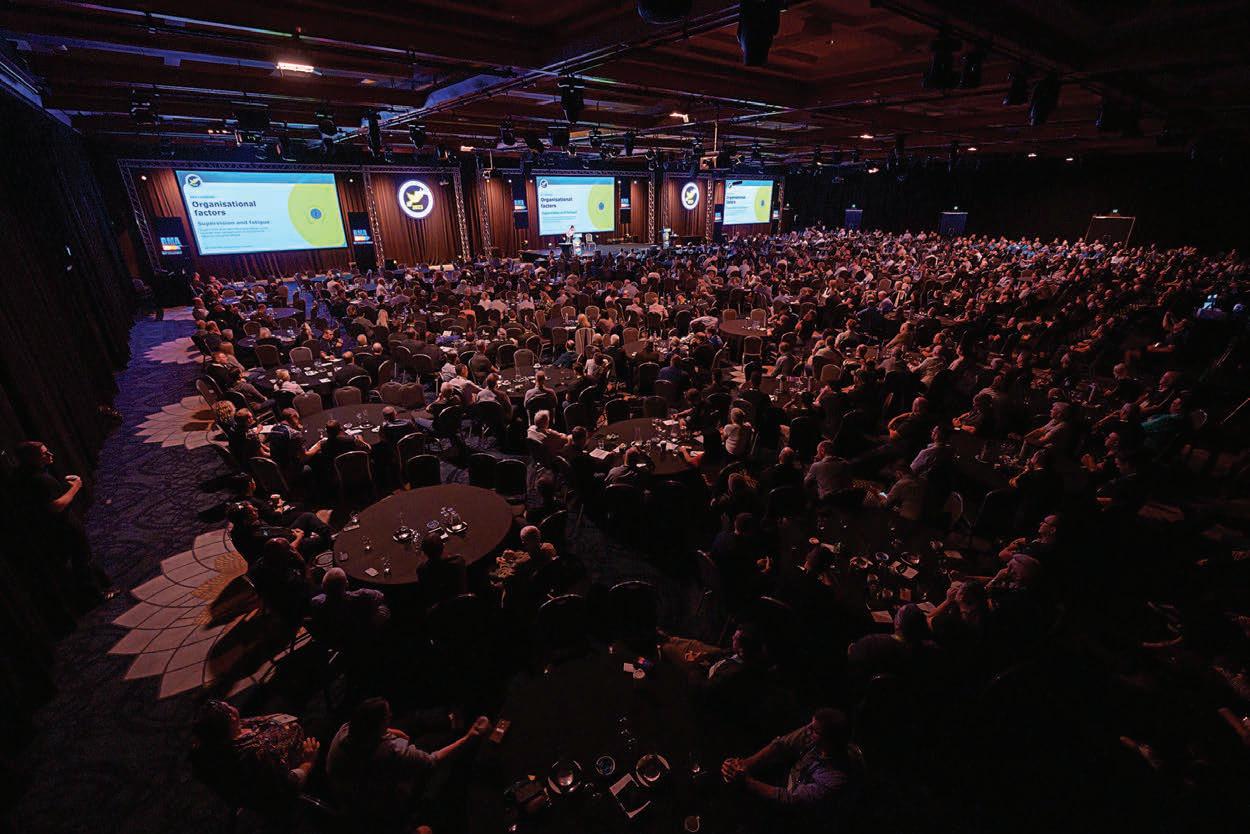




Events
Tracking excellence at WA Mining
SOME OF THE BIGGEST NAMES IN THE INDUSTRY WILL TAKE TO THE STAGE AT THE UPCOMING WA MINING CONFERENCE AND EXHIBITION IN PERTH.
Set to be held at the Perth Convention and Exhibition Centre from October 9–10, the 2024 WA Mining Conference and Exhibition (WA Mining) will showcase the state’s critical role in the resource industry’s digital evolution.
A panel discussion with Rio Tinto and material tracking technology specialist Track’em is set to be a highlight of an impressive speaker line-up at the event.
The Track’em Track and Trace platform at Rio Tinto Iron Ore has offered the major miner an end-toend solution for the tracking of goods from vendors to end-users. It uses scanning technology to offer reliable status, location, and delivery date visibility throughout the supply chain.
Created in collaboration with Rio Tinto’s Perth-based team, the platform integrates with the miner’s third-party logistics partners to link its Pilbara operations, including mine sites, subplants, administration centres and other hubs, into one platform for better management and tracking of materials.
The Rio Tinto–Track’em panel will discuss options to empower operational excellence, which Rio asset management supply chain manager and panel participant Chris Brown describes as being a case of “having the right information to the right people at the right time”.
“It’s about knowing where parts are, understanding where they should be, and having people ... be able to move those parts where they needed the first time, every time,” he said.
Brown believes events like WA Mining are a vital opportunity for people across the sector to share experiences and foster connections.
“Presenting at the conference gives us the chance to highlight a great partnership that we’ve had with a local IT vendor who’s been able to work with us to develop an integrated solution and engage with others in the industry,” Brown said.
Track’em is equally excited to be taking part.
“The panel at WA Mining is an exciting opportunity for people who will be attending, and we want to make it an interactive experience,” Track’em founder and chief executive officer Kashif Saleem said. “People love stories and I think this case study and panel discussion is a good opportunity to tell a great story.”
Elsewhere, speakers include WA Minister for Mines and Petroleum David Michael, as well as representatives from MEC Mining, the Minerals Council of Australia, the Chamber of Commerce, and Industry WA. Presentations will examine opportunities such as decarbonisation, tech-driven operations, and a circular economy for critical minerals.
The conference will run alongside a free exhibition and seminar series, with insights from government, miners and industry decision-makers.
WA Mining will be held at the Perth Convention and Exhibition Centre from October 9–10. For more information, visit waminingexpo.com.au/attend
More than 40 speakers are on the docket to share case studies and thought leadership.
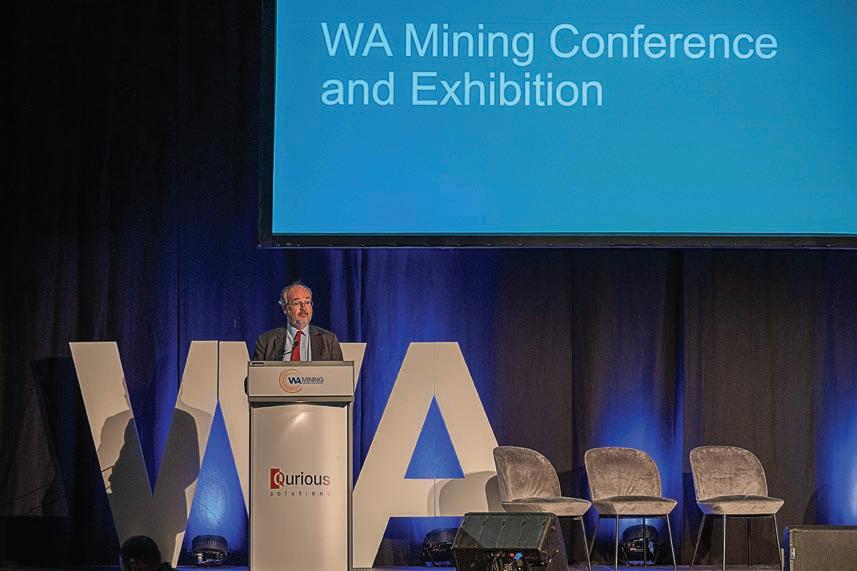

WA Mining 2023 was a big success, with industry majors from across the sector.
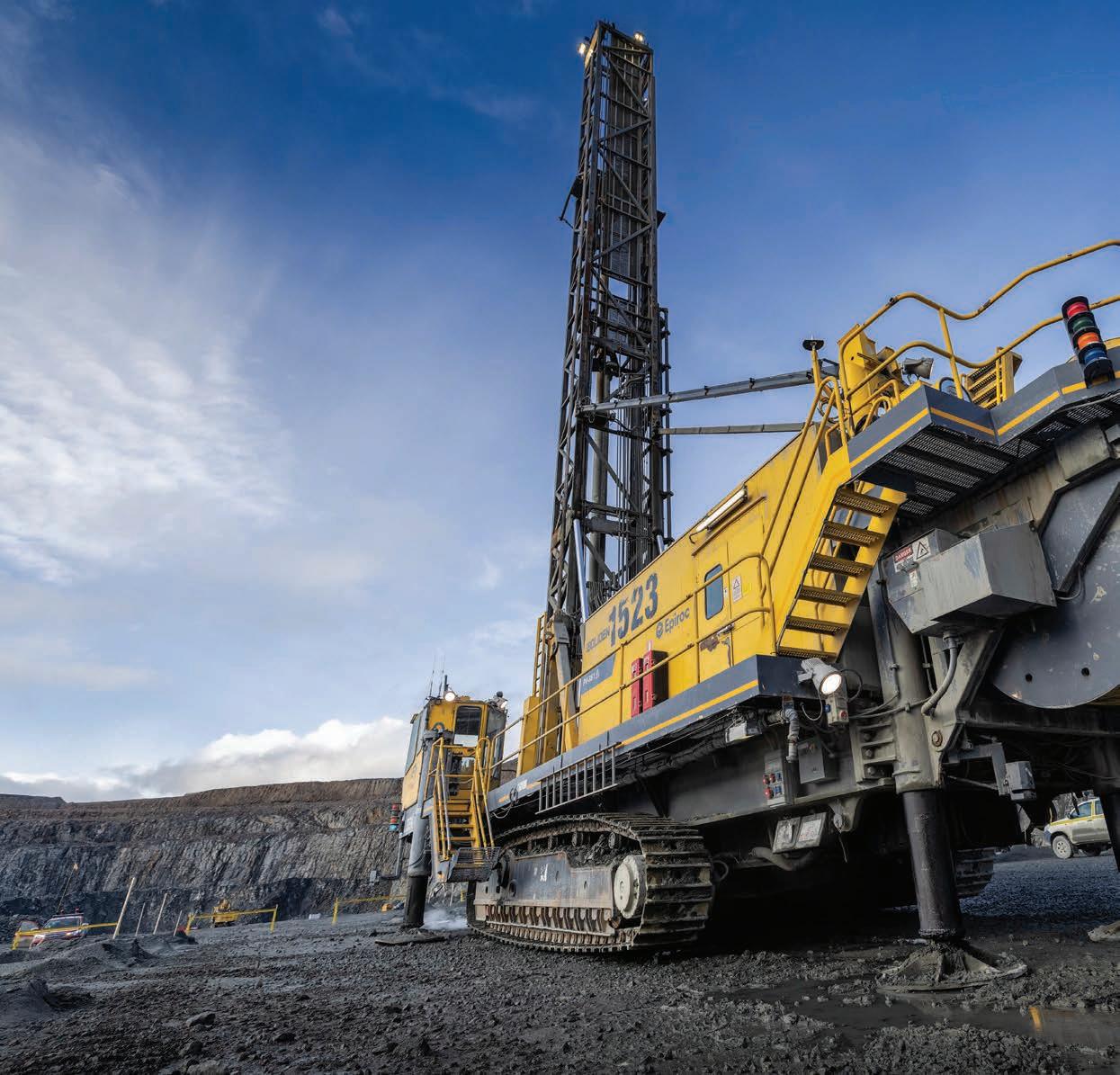
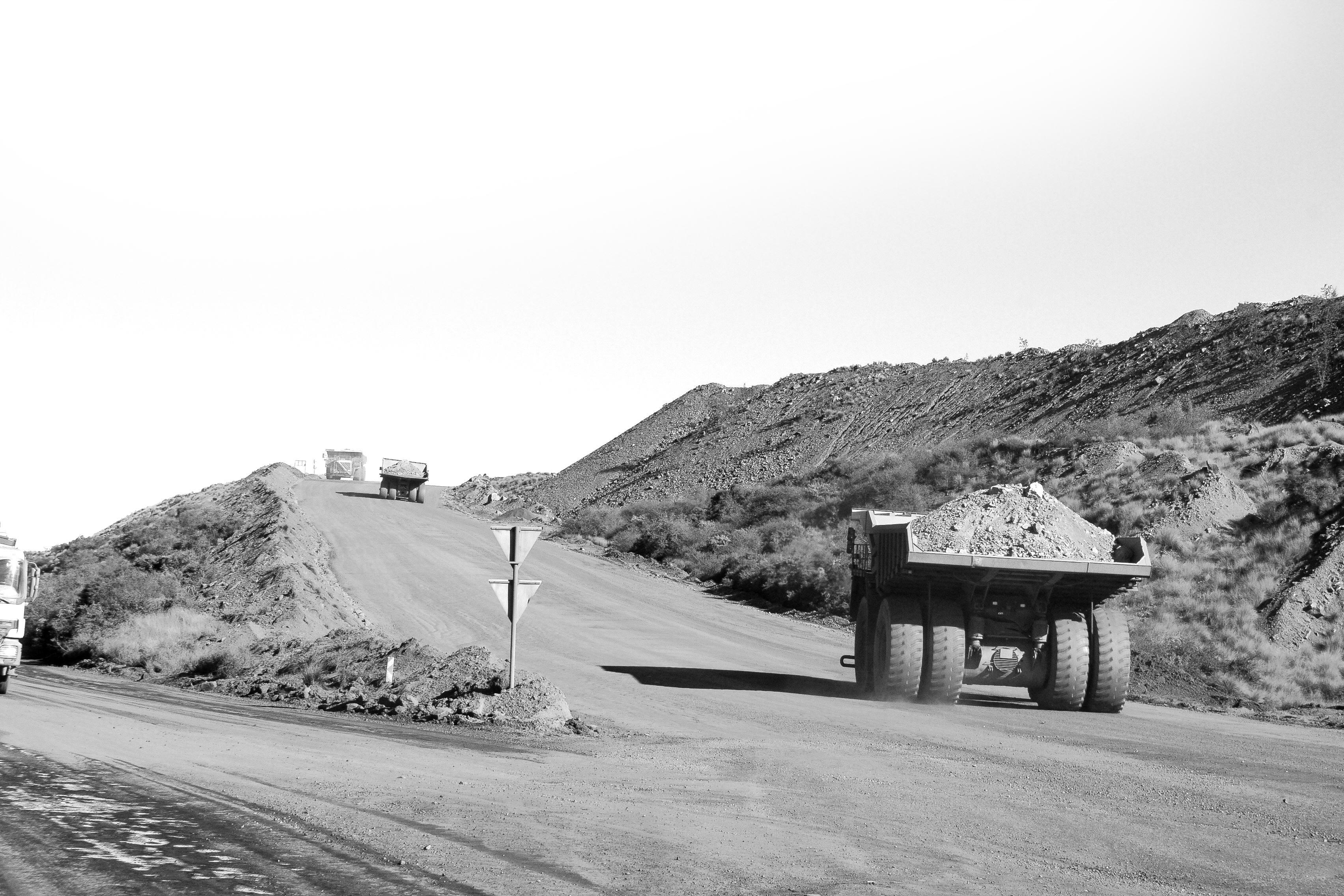
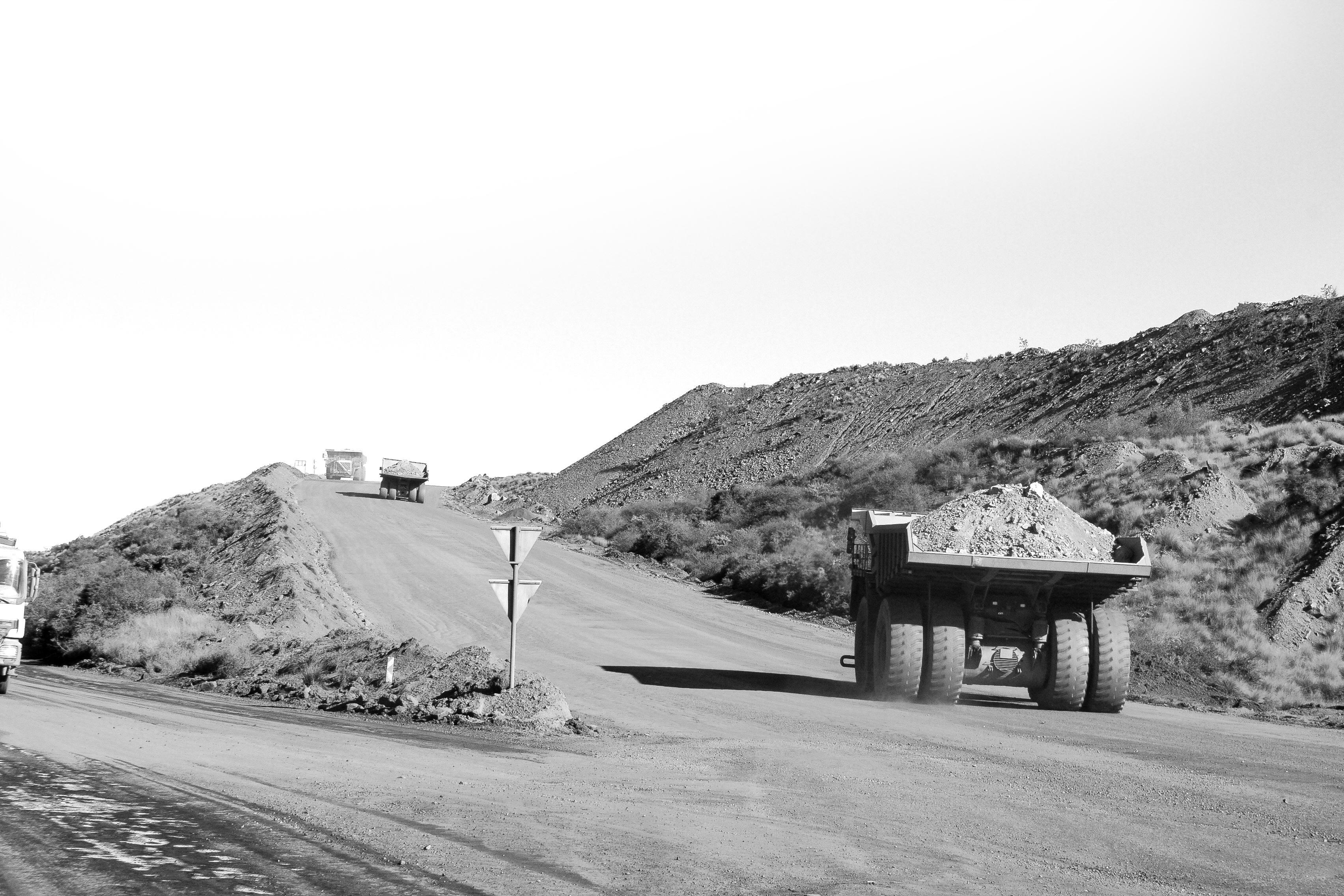
Control Dust Reduce Costs Increase Production Deliver Sustainability
With decades of experience, Dust-A-Side Australia are industry leaders in dust and erosion control, road management, dust suppression systems and environmental solutions. Our services are designed to make workplaces safer and healthier for workers, more productive and efficient for our clients and more sustainable for the local environment.
Environmentally Friendly Dust Suppression
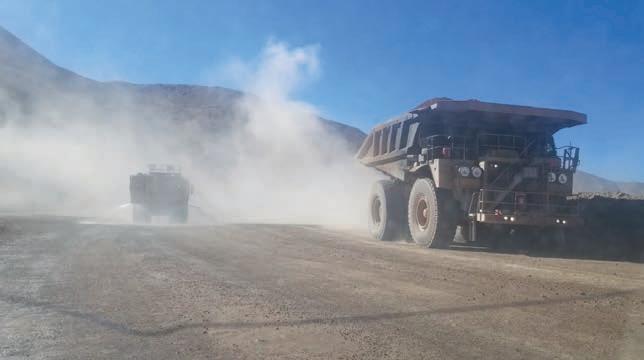
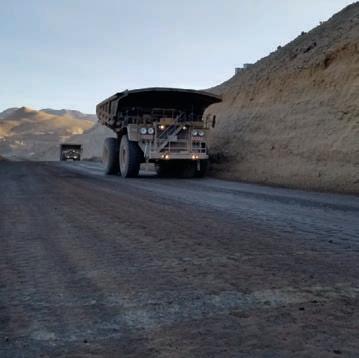
•
•
•
•
•
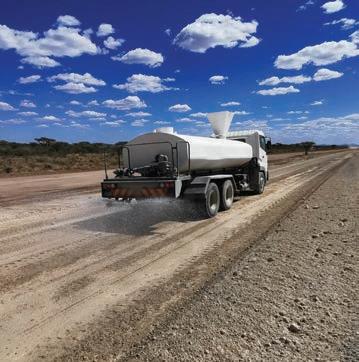
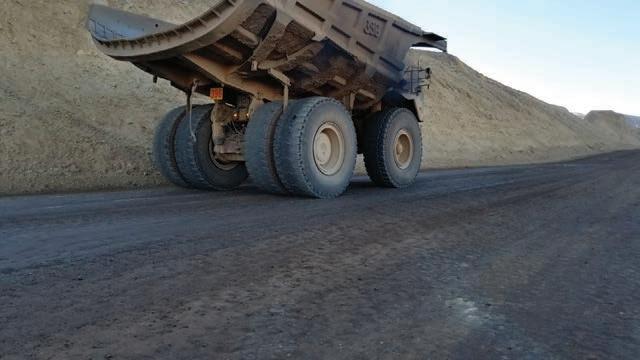
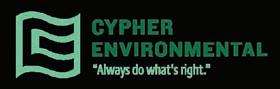
