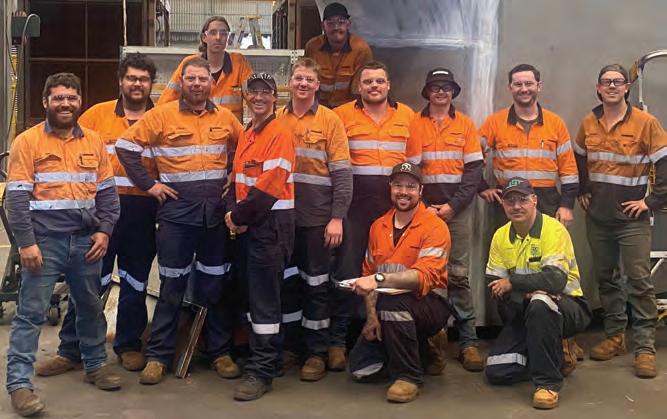
6 minute read
Taking confined spaces training deeper
LIEBHERR-AUSTRALIA HAS LED THE WAY IN MAKING ITS WORKPLACE SAFER BY IDENTIFYING A PRACTICAL SOLUTION TO EMERGENCY TRAINING WHILE ALSO BOOSTING CONFIDENCE AND MORALE.
Liebherr-Australia’s fabrication department in Perth has a tough job.
Working in confined spaces, the team is assigned to conduct inspections and undertake maintenance and repairs on the company’s R 9400 and R 996 hydraulic excavators.
This can often take members of the team to mine sites around Western Australia, including Tom Price, which is one of the hottest parts of the state.
The heat from the equipment, combined with personal protection equipment and the natural warmth of the region, can make working inside the excavator booms incredibly uncomfortable.
However, there was also another significant issue with the work.
It was discovered that standard rescue plans and associated response times with confined space work inside the booms lacked efficiency, resulting in residual risk.
Liebherr-Australia fabrication team member Ben Palmer was instrumental in identifying the need for in-depth requirements regarding boom confined space preparation.
He also maintained an unwavering drive to continue to find a solution and implement new practices to better his team over a four- to five-year period.
Palmer encouraged and led the fabrication team in identifying, developing and implementing confined space rescue plans for excavator attachments.
Due to a swift increase in workload, Palmer became increasingly concerned as the frequency and, in turn, the number of employees required to enter the booms/sticks increased, from just himself and two others to the majority of the team.
Determined to find a solution, Palmer consulted with various levels of the company and industry experts, all the while fostering an environment for solutions to be developed and implemented, while positively influencing a proactive safety culture for the fabrication department and wider Perth branch.
Fabrication supervisor Neil McHugh says discussions around the training started taking place in around 2014.
“While we had identified safety aspects, it didn’t really go deep enough to address what we were doing inside the boom,” McHugh tells Safe to Work.
“So we had to go that little bit further. Most confined spaces are like cylinders and tanks, but this was unique in the way that the internal design of the boom is structured and is inherently a lot more difficult.
“While still compliant, it just wasn’t the most ideal way of training, so we decided to find a better way.
“Finding someone who was able to see what our requirements were and address those as a training provider was quite difficult.”
The company turned to safety training specialists ERGT, located
The Liebherr-Australia Perth fabrication team.
just down the road at the Incident Management Training Centre (within the Perth Safety Training Centre), which is designed to develop incident commanders and their support teams for the effective management of major incidents and emergencies.
From core safety skills to incident response and management, ERGT Australia delivers relevant, engaging training for the resources and mining industry.
The centre uses a realistic and experiential approach to training through simulations and workplace exercises.
ERGT trainer Craig Foley was approached by Liebherr-Australia to assist in developing a plan to incorporate all aspects of incident training.
“When Liebherr-Australia approached us, due to their specialised requirements, they needed to make sure we would be able to help them,” Foley says.
“Once we had a thorough discussion, we knew that we could come up with a training solution.
“So, then it was a matter of sitting down and looking at the compliance side of the training, as well as making sure we could guarantee an outcome of getting someone out if they did get trapped.”
ERGT worked with Perth’s fabrication department to understand what an emergency situation would look like and how to interact with emergency services that arrived at a potential incident.
They then applied that training to how an accident would possibly happen as part of the regular site duties.
Liebherr-Australia fabrication leading hand Tom Waters says the training allowed a greater understanding of what to do in an emergency situation.
“Once we found out the training was actually nationally accredited, we thought we would get everyone involved as it would give confidence that no matter what happens on site, they are going to be able to get someone out,” Waters says.
“It also helped to make us all more confident in actually doing the job, because we knew if anything did go wrong, we had the training and the knowledge of what to do in that situation.”
Prior to this initiative being introduced, training for internal inspections and repairs were limited to industry standard, generic confined space training.
Significant inefficiencies were identified with the type of rescue equipment, suitability of practices, existing work instructions, and the
The teamwork developed has led to stronger morale at Liebherr.
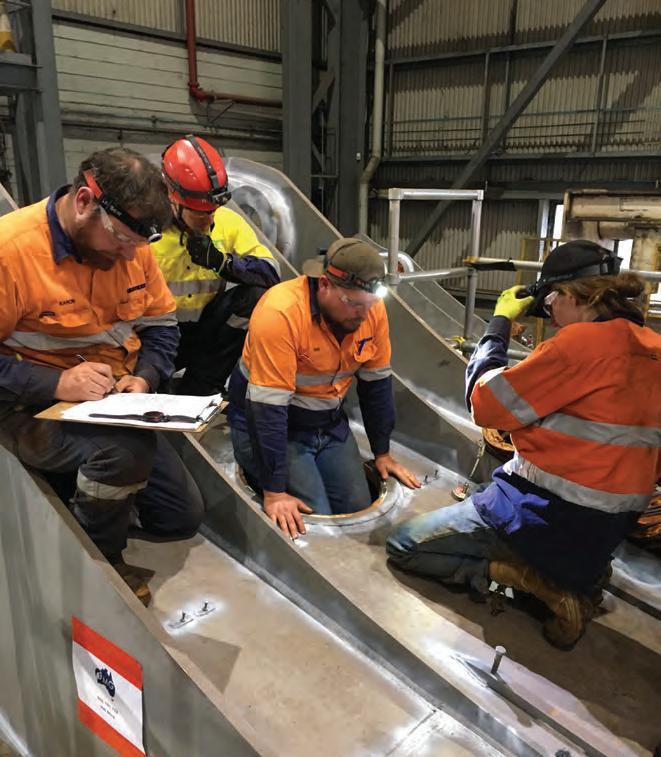
physical ability to rescue a distressed person in an emergency situation.
Liebherr-Australia regional manager Paul Hyham says the company gave its full support to the initiative and encouraged the development of the safety and rescue protocols.
“From an organisation point of view, we always talk about empowerment when it comes to safety,” he says.
“I can’t think of a better real-life example I have seen where great enthusiasm has driven such a valuable outcome.
“It is especially important to us because our workers are at the forefront of potential risk every day: they are the ones who have the experience to be able to make their jobs safer and we empower them to drive the changes they need to.
“You can talk about empowerment all day, but when you actually see an example of what our people have done to deliver an outcome from a
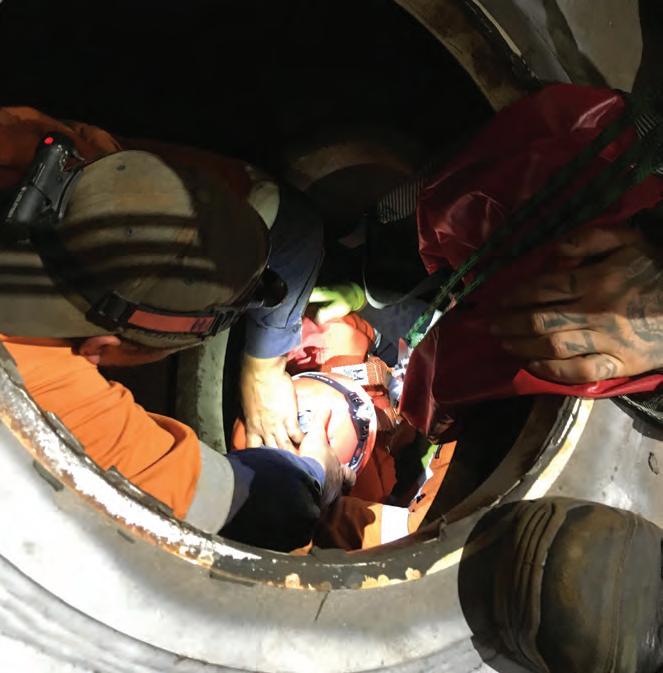
A range of scenarios were included in the training.
Inspections take place in extremely confined spaces. safety perspective, this is an absolute credit to them.”
From the training courses, the fabrication team was able to develop specific rescue plans with support from ERGT and specialist rescue equipment was purchased.
Specialist training was undertaken, with refresher training every six months, including mock rescues of a dummy and a person, which resulted in finalisation of efficient and effective rescue plans for the R 9400 and R 996B excavator booms.
Liebherr-Australia senior health safety and environment advisor Shermin Sarvaryan says the training has also increased the confidence of the original equipment manufacturer’s mining partners.
“Our clients know that when our team goes out on site that they have the knowledge of what to do in an emergency situation,” Sarvaryan says.
“Knowing that when a site’s emergency response teams are going to be dealing with our employees, who have trained for this situation and understand the best practice in terms of rescue, gives them the surety that we can either conduct a safe rescue ourselves, or provide the best advice and support them if needed.
“There is also greater confidence from within the fabrication department: by increasing their ability to solve a complex problem, it not only makes our work practices safer, but provides a more professional service to our customers and further cements the team’s bond.”
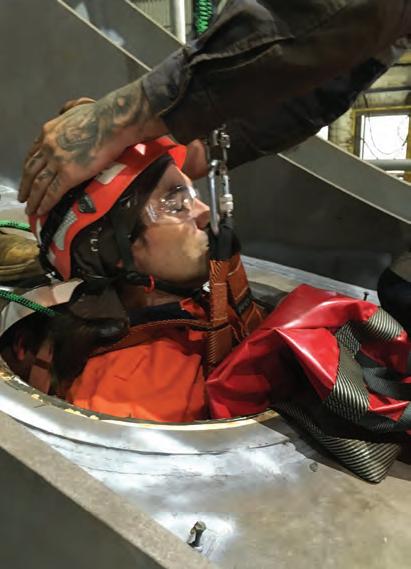