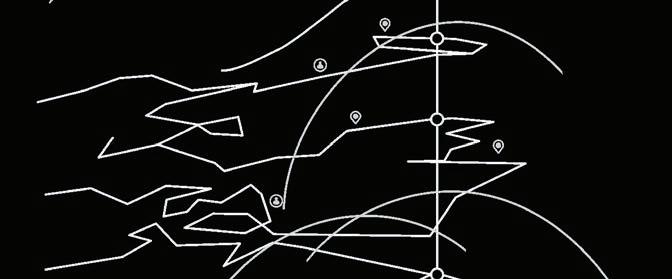
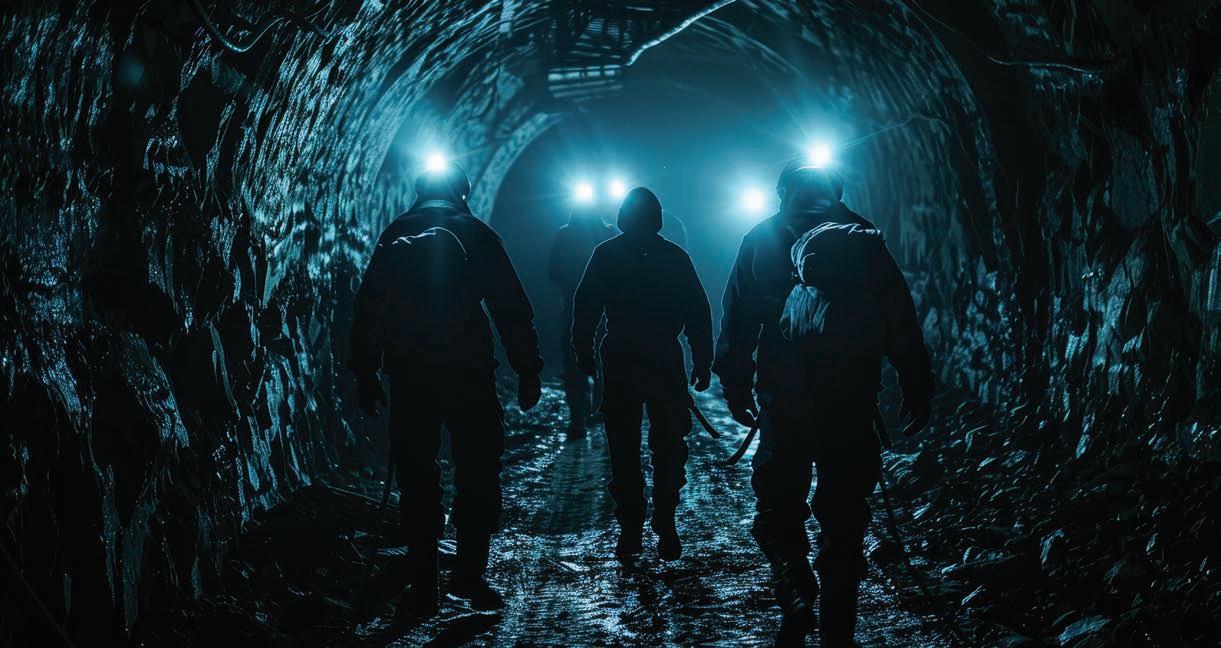
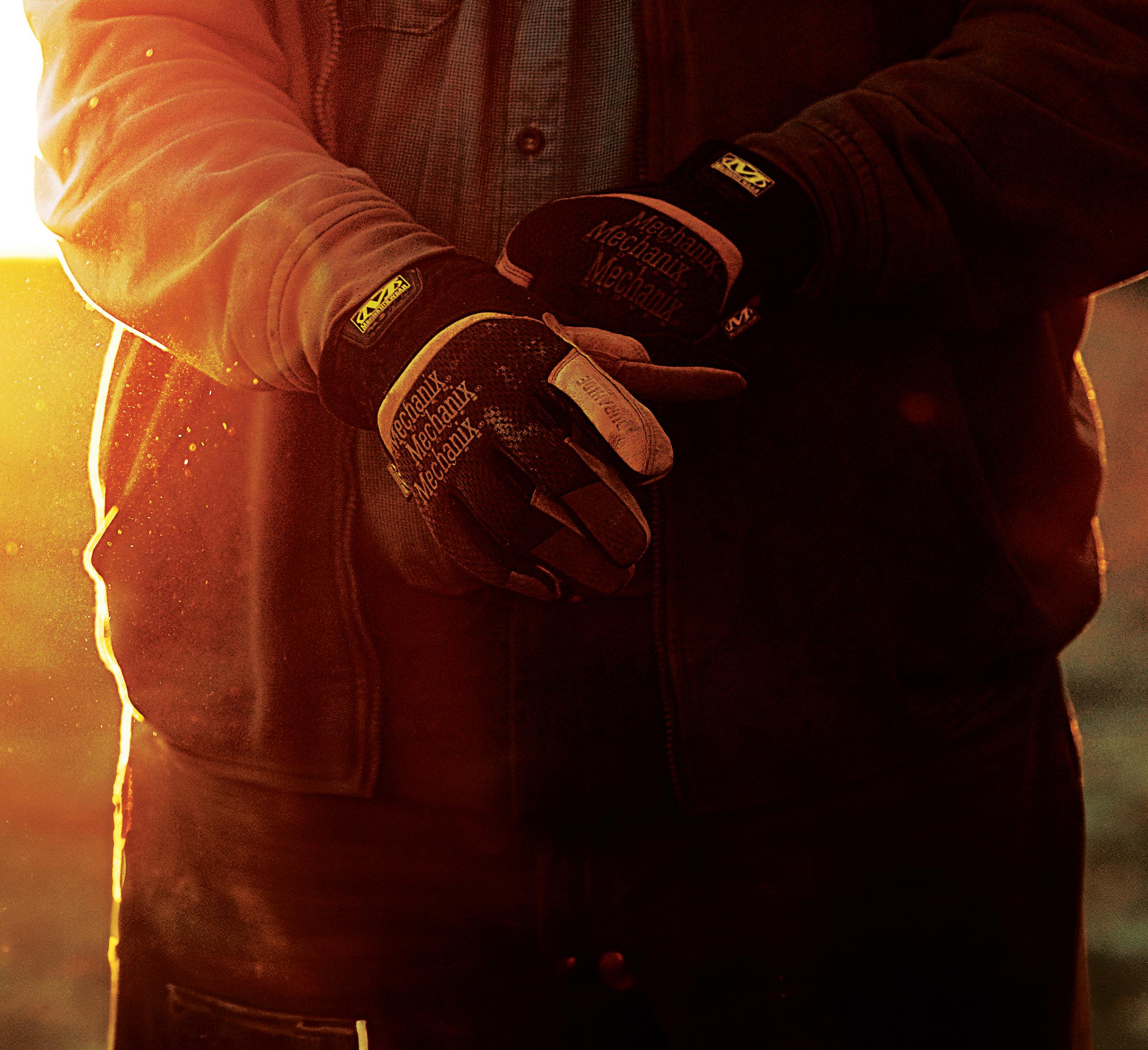

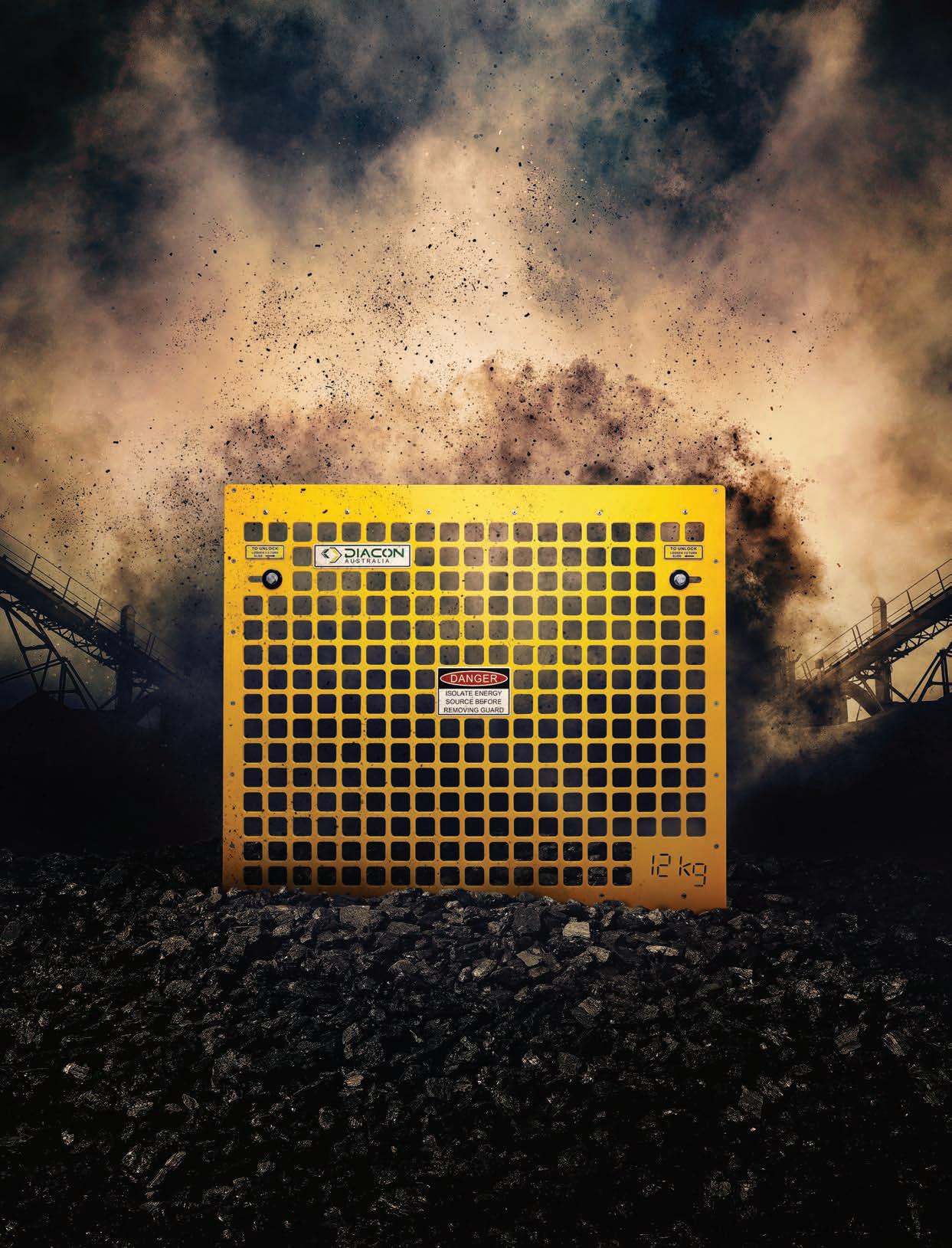
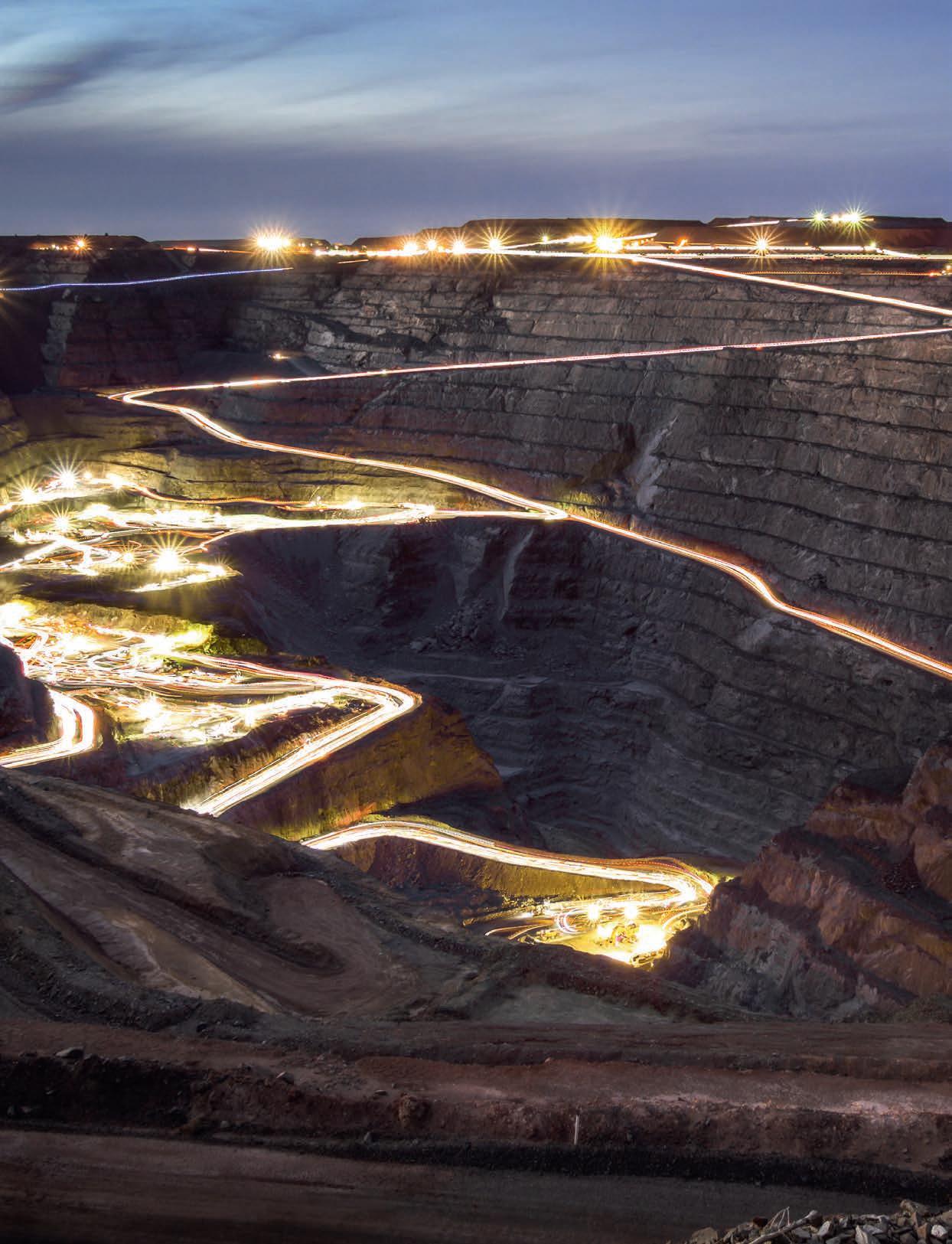
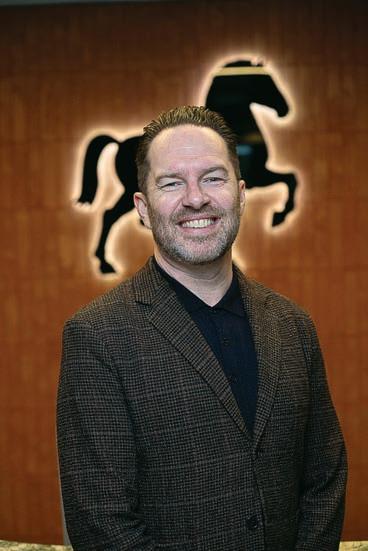
The mining industry has never been more committed to mitigating the hazards that put workers at risk.
As the resources sector has advanced over the years, the machinery that keeps the industry running has had to get a lot larger and more sophisticated than a humble pickaxe.
But while equipment might be bigger, it’s also smarter.
The emergence of hazard avoidance and autonomous technologies is launching the mining industry into a new era of safety, one where people are better protected, with the resulting efficiencies making operations more productive and environmentally friendly.
New studies are showing the uptake of these technologies is progressing at pace, reducing injuries and supporting a greener future for the next generation.
Industry majors are a driving force behind the
COO
CHRISTINE CLANCY
MANAGING EDITOR
PAUL HAYES
Tel: (03) 9690 8766
Email: paul.hayes@primecreative.com.a
JOURNALISTS
KELSIE TIBBEN
Tel: (03) 9690 8766
Email: kelsie.tibben@primecreative.com.au
OLIVIA THOMSON
Tel: (03) 9690 8766
Email: olivia.thomson@primecreative.com.au
DYLAN BROWN
Tel: (03) 9690 8766
Email: dylan.brown@primecreative.com.au
ALEXANDRA EASTWOOD
Tel: (03) 9690 8766
Email: alexandra.eastwood@primecreative.com.au
CLIENT SUCCESS MANAGER
JANINE CLEMENTS
Tel: (02) 9439 7227
Email: janine.clements@primecreative.com.au
development, with the likes of BHP, Rio Tinto and Fortescue partnering with innovators and original equipment manufacturers to lead the charge.
This edition of Safe to Work explores some of the emerging and established technologies driving new frontiers in hazard avoidance.
We delve into where the future of the mining industry is heading thanks to personnel tracking software, artificial intelligence (AI) collision avoidance, and data-driven conveyor guarding.
Elsewhere, we welcome two new association partners striving to create a greater culture of safety in the resources sector.
The Working at Height Association presents a compelling case for a shifted perspective on what it means to stay safe while working at height, and how the best approach may just come from the top down.
Closer to the ground, the Association for Occupational Hygienists offers readers a host of resources to tackle the hazard of silica exposure and examines how the industry is shifting to protect workers from deadly diseases.
Whether working around heavy equipment, suspended from heights, or breathing particles in the air, miners are better protected than ever before from the hazards associated with mining.
By taking a holistic approach to hazard avoidance and autonomous technologies, miners are now in a position to layer safety with environmentally conscious practices, creating a better future for all.
Paul Hayes Managing Editor
RESOURCES GROUP LEAD
JONATHAN DUCKETT
Mob: 0498 091 027
Email: jonathan.duckett@primecreative.com.au
BUSINESS DEVELOPMENT MANAGER
JAKE NIEHUS
Mob: 0466 929 675
Email: jacob.niehus@primecreative.com.au
ART DIRECTOR
Michelle Weston
8 A safety revolution
Cutting-edge hazard avoidance and autonomous technologies are quickly becoming industry mainstays, with some of the biggest names in Australian mining leading the charge towards a safer future.
28 A double HELIX at MINExpo 2024
44 Raising awareness to new heights
The Australian Working at Height Association wants to see the increasing rates of height-related injuries and fatalities slashed.
14 Evolving with industry needs
Diacon Australia has a 20-year legacy of improving industry standards in conveyor safety and efficiency.
20 Safety from the ground and beyond
Epiroc’s Mobilaris Situational
Awareness solution can now be utilised at underground and
The HELIX platform has successfully helped mines across the world streamline their data. Now, MST is back with two key technologies aiming to offer miners even more operational autonomy.
34 Resourcing the industry
Western Australia’s mining sector is flourishing in large part thanks to fly-in, fly-out workers. But for the industry to keep riding on the wings of success, it needs critical resources.
36 A labour of glove
Mechanix Wear gloves are being recycled into the very fabric of a greener future.
48 A future free from silicosis Safe to Work sat down with the Australian Institute of Occupational Hygienists to discuss what can be done to protect workers against the threat of silica exposure.
56 A night to remember
The 2024 Australian Mining Prospect Awards was a night of celebration, recognition and connection for the best and brightest the mining sector has to offer.
BE PART OF OUR TEAM!
RevUp is a new program from Mechanix Wear that aims to revolutionise glove sustainability by providing eco-friendly waste reduction measures for end-of-life safety products. This includes partnering with Upparel to upcycle PPE for reuse and close the sustainability loop.
SCAN TO LEARN MORE
PROTECTION AND SUSTAINABILITY WITHOUT SACRIFICING FIT OR FEEL.
• Superior multi-threat protection
• High breathability and comfort
• Full dexterity and range of motion
• Built from recycled materials
• Significant cost savings
The Kito ER2 electric chain hoist is a heavy-duty solution tailored for mining operations where safety and reliability are essential.
A robust design enables the hoist to handle intense workloads, making it suited for lifting and transporting heavy materials.
Advanced features like an in-built frequency inverter, variable speed control, condition-monitoring with CH meter, and fault detection help to ensure precise load handling and preventive maintenance, minimising accident risks while enhancing productivity. The maintenance-free electromagnetic brake is guaranteed for one million operations, and the nickel-plated load chain provides strong rust and abrasion resistance. With an IP55 rating, the sealed construction protects against dust, debris and moisture, ensuring long-term durability in harsh conditions. Safety is a priority with features such as motor burnout and overheating protection, emergency stop control, and a patented friction clutch for overload protection.
For mining companies prioritising efficiency and worker safety, the Kito ER2 is an ultimate choice.
• kitocrosby.com.au
Fires can cause widespread shutdowns, loss of productivity, and even fatalities in severe cases.
With the MusterFire suppression system, mining operations can anticipate fires before they start, potentially saving millions of dollars in damage and operational downtime.
The real-time diagnostics built into the system’s new module can also add another level of value.
If there is a discharge event, the system can be fully interrogated, allowing for a detailed investigation.
This level of visibility is essential for asset management and understanding what triggered the discharge.
The module works to simplify fault detection, checking system pressure, battery capacity and relay settings.
Importantly, it records event history for up to 150 alarm panels, making it easier for technicians to store information as they move from machine-tomachine and site-to-site.
• musterfire.com
Slip and fall accidents are a major cause of workplace injuries in industrial environments.
Surfaces contaminated by dust, oil, grease or water can quickly become dangerous, especially in facilities with high foot traffic or heavy machinery.
In addition to keeping floors dry, Tennant machines help address the dangers posed by silica dust, a key concern in industrial settings.
The S30’s cab-forward design, coupled with an optional fully pressurised cab, features HEPA-class filtration which provides a filtration efficiency of 99.97 per cent to 0.3 microns.
This technology offers protection for operators and further helps facilities maintain work, health and safety compliance and silica dust exposure plans.
By maintaining dry, debris-free surfaces, businesses can significantly reduce the risk of slips and falls, contributing to a safer work environment for their employees.
• tennantco.com
Systems and technologies designed to increase the safety of people working in and around heavy mobile machinery.
Centralised software platforms for monitoring, training and reporting
Proximity Detection & Collision Avoidance Systems
• HazardAVERT® Electromagnetic
• HazardAITM Artificial intelligence detection systems
• Full Level 9 EMESRT capability
CUTTING-EDGE HAZARD AVOIDANCE AND AUTONOMOUS TECHNOLOGIES ARE QUICKLY BECOMING INDUSTRY MAINSTAYS, WITH SOME OF THE BIGGEST NAMES IN AUSTRALIAN MINING LEADING THE CHARGE TOWARDS A SAFER FUTURE.
The Australian mining industry is in the midst of a technology revolution. The rise of autonomation is sweeping the sector, bringing with it a new frontier of innovation.
These advances have heralded a new era of safety for the resources industry, with workers protected from the hazards of mining like never before.
A 2024 study by GlobalData looked at the adoption of technology at 162 operating mine sites between March and May this year.
The study found record adoption of hazard avoidance and autonomation technology, with underground mines in particular investing more in predictive maintenance, mine communication and electric vehicles.
The ultimate purpose of these technologies comes back to one shared goal: keeping miners safe.
The trend in the uptake of hazard avoidance and autonomous technologies paints a picture of a future mining landscape defined by the use of data to improve safety.
Mining giant Rio Tinto recently accepted its 300th Komatsu autonomous haulage system (AHS) truck at its Pilbara operations in Western Australia.
Komatsu and Rio Tinto initially signed a memorandum of understanding in 2011 to deploy 150 AHS trucks to the Rio Tinto site and that partnership is still going strong 13 years later, with both companies looking to accelerate the pace of mining automation.
“We’ve led the industry in mining automation since 2008, when we commenced the Rio Tinto trial,” Komatsu Australia general manager –mining automation Garry Povah said.
“We delivered the first five AHS trucks to Rio mine sites in Australia in 2011 and it’s incredible to see how much the business has embraced this technology over the years, helping to make their mines safe, and also highly productive.”
Povah said AHS trucks are a crucial solution to mine safety and to addressing labour shortages in the sector.
environments, AHS trucks significantly reduce the risk of accident and injury, while enabling continuous operation that considerably impacts site productivity,” he said.
“The AHS fleets at Rio Tinto sites have completed 8.9 million operating hours and have moved over 4.8 billion tonnes of material, all while improving their sites effective utilisation by 15 per cent – a remarkable feat.”
The 300 AHS trucks are currently spread across 10 of Rio Tinto’s Australian mine sites and contribute to approximately 80 per cent of their daily production capacity.
The Big Australian recently hit a onemillion-metre autonomous drilling milestone at its Mount Arthur South coal mine in New South Wales.
Leading Caterpillar (Cat) dealer WesTrac and major mine services provider Thiess joined forces to reach the milestone, which was achieved using a fleet of three Cat MD series drills running with the Cat MineStar Command autonomous drill system.
Since introducing the technology solution in 2021, Thiess recorded a 20 per cent improvement in drilling performance and an eight per cent reduction in fuel use, with the safety implications of data-driven mining protecting countless workers on the front line.
Thiess head of autonomy and operations technology Trent Smith said the company’s adoption of the technology took into consideration its integration with people and process.
“Working in partnership with WesTrac and Caterpillar, we took a drill that didn’t have any automation capability and went on the journey as
a team to bring through what is now three drills running autonomously with a single controller,” he said.
Thiess upskilled more than 30 of its people at Mount Arthur South, from traditional drill controllers to autonomous operators, and has invested in autonomous mining systems training for more than 500 employees, leading the workforce into a new era of safety and efficiency.
partnership with Liebherr for the delivery of carbon-free autonomous mining solutions.
This will include 360 autonomous battery-electric trucks, 55 electric excavators and 60 batterypowered dozers.
Fortescue founder and executive chair Andrew Forrest was at the event, where the companies also unveiled the jointly developed autonomous battery-electric T 264 truck.
“Partnerships with companies and people like Liebherr and Willi Liebherr – where ambition is backed by action – are critical,” Forrest said.
“This is an important next step in our 2030 Real Zero target –to eliminate emissions from our Australian iron ore operations by the end of the decade.
“Together, we can be the trailblazers who forge the world’s move away from fossil fuels.”
The influx of zero-emission autonomous equipment will represent about two-thirds of the current mining fleet at Fortescue’s operations.
Fortescue and Liebherr have confirmed that their continued cooperation will allow customers to access this ecosystem for their own operations in the coming years.
As this kind of technology becomes more ubiquitous, so too does the opportunity to keep miners out of harm’s way.
Majors like BHP, Rio Tinto and Fortescue are the kind of industry behemoths the sector needs to facilitate the original equipment manufacturer (OEM) innovation that drives the industry forward.
With the evolution of technology pulling workers away from the front line and into new and dynamic roles, mining in Australia is certainly changing – but the future has never looked so safe.
MINE RESCUE COMPETITIONS ARE PROVIDING EMERGENCY RESPONSE TEAMS WITH THE HANDS-ON EXPERIENCE NEEDED TO STAY ON TOP OF WORKPLACE SAFETY.
There’s no doubt safety comes first in the resources industry, but there’s also no shortage of hazards in Australia’s mines that pose a risk to workers.
The industry might have once held a reputation as being one of Australia’s most dangerous, but things are definitely improving.
A 2003 Safe Work Australia study recorded 12.4 deaths for every 100,000 mining.
That number has dropped to just 3.4 in the 21 years since.
Today, mining doesn’t crack Australia’s top six most dangerous professions.
However, that doesn’t mean mine sites are totally risk-free. After all, three deaths per 100,000 workers is still three too many.
Common risks on mine sites can come from interactions with heavy machinery like haul trucks and loaders, from intricate equipment with many moving parts like conveyors and crushers, or from the outbreak of fire, working from height and handling hazardous materials.
The industry is well aware of these potential risks and is always working to improve its response to hazards and emergencies. One way mines stay primed to respond to these hazards is through keeping their emergency response teams well trained.
Many of Australia’s mines have emergency response teams. Generally comprised of volunteer miners, these teams train in a range of scenarios
potential emergencies.
While these teams are essential to keeping their colleagues safe, there are also opportunities for them to shine beyond the site.
The Minerals Council of Australia (MCA) held its 31st Victorian Mine Rescue Competition in Bendigo in August, with teams from Victoria, New South Wales and Tasmania participating in a series of rescue simulations in the weekendlong event.
The event is not only a chance for teams to put their skills to the test but an opportunity for safety personnel from different mines to come together with like-minded colleagues. It is also a celebration of the MCA’s dedication to forging a safer mining community.
MCA executive director James Sorahan takes pride in the organisation’s commitment to safety in the mining industry.
“Safety is our number-one priority, and this training exercise is one of the main ways that we try to achieve this,” he told Safe to Work. “Bringing in that collaborative element and
encouraging the rescue teams to learn from each other at a large-scale mine rescue training exercise is what makes this sort of competition so unique.”
The competition also provides rescue teams the vital opportunity to work with local emergency services.
Emergency services play a critical role in the mining industry, and Sorahan said the MCA works hard to
deepen its understanding of safety and emergency response.
“Having fire, police and ambulance from local commands come to the mines and meet and work with the rescue teams is of enormous value,” he said. “We’re really bringing together all of the mine rescue community in Victoria, including emergency services, government agencies or the
mining community, to all learn from each other over an intense weekend at a local mine site.”
The competition is made up of various rescue simulation scenarios designed to push competitors to
the limit, testing several key aspects of emergency rescue response: fire, first-aid, ropes, underground search and rescue, skills, theory, breathing apparatus, and road crash rescue.
Victoria’s Fosterville mine partnered with the Central Deborah mine to create the rescue drills for this year’s event, with Fosterville’s health, safety and security manager Andrew Mattiske helping to design seven different scenarios.
One of those scenarios involved rescuing injured personnel in an underground mine.
“The teams had to go in and search for them under breathing apparatus,” Mattiske told Safe to Work. “Knowing how to operate breathing apparatus is crucial in mine rescue, where there can be toxic gas leaks, air pollution or particles that are harmful to your lungs.
“Having to save someone while under all that apparatus can be very tricky.”
Another scenario took the form of a vehicle truck collision simulation that involved five passengers who were trapped in a car.
“Teams had to cut the car open and retrieve the people and deal with
their injuries,” Mattiske said. “These types of vehicle-related scenarios are common on mine sites.
“We even had the local police present for this drill because it’s important they know how to respond to vehicle-related incidents on mine sites, too.”
Competitors also got to stretch their underground firefighting skills.
The potential for fires and hazardous gas leaks in mines is more common than one likes to think, as was demonstrated when a fire blazed for almost a month at Anglo American’s Grosvenor underground coal mine in Queensland in July.
With potential safety issues so prevalent, it is vital that rescue teams maintain their skills.
Fosterville’s rescue team, for example, undergoes training at least once a month, keeping its volunteers in tip-top shape for an emergency.
“We recognise the importance of being prepared for any emergency
and having the capacity to respond to these situations,” Mattiske said.
As for the rankings from the event, Tasmanian Cornwall coal mine took home the overall gold, with Ballarat Gold Mine in second place, followed by Costerfield mine in third.
The 2024 Victorian Mine Rescue Competition marked another year of stepping towards better workplace safety, as mine rescue teams left with strengthened skills and memories of an exhilarating weekend.
10% OFF YOURORDERFIRST
Pushing the boundaries on style and innovation, the NEW Navigator X offers a protective eyewear solution without compromise. Featuring the iconic wayfarer design, high quality materials and specialist lens options, the Navigator X is the next level for style & safety.
+ Market first HD lens dramatically improves clarity and contrast, heightens colours whilst relaxing the eye
+ Made using ethically sourced Bio-Based materials
+ Premium UV400 FLOW-TEC Anti-Fog and Anti-Scratch lenses (including polarised and mirrored)
Engineered and manufactured in Australia, Diacon Australia’s innovative and versatile plastic conveyor improvement system stands at the forefront of the industry.
Over a two-decade history, the system has evolved through a commitment to understanding and addressing client needs and insights with precision and authority.
“At Diacon, we believe in not just meeting industry standards but redefining them,” Diacon managing director Brendan Refalo told Safe to Work. “This dedication to excellence ensures that our solutions not only enhance safety and efficiency but also lead the way in sustainable practices.
“In our experience, there is rarely a one-size-fits-all solution in the conveyor industry. It’s this understanding that has allowed us to thrive for 20 years; by listening to our clients and customising our systems to meet their unique needs, we’ve set ourselves apart and continue to lead in innovation and safety.”
With an unwavering commitment to flexibility, Diacon’s innovative plastic improvement system is seamlessly integrated into existing conveyors, showcasing its core strength.
Custom-manufactured bracketry, guards, hungry board, and conveyor hoods are tailored to meet the specific needs of each site, helping to ensure
optimal safety and efficiency in every installation.
The versatile system is suitable for use in the manufacturing industry on moving machines and robotic enclosure applications, while also serving as barrier control for area demarcation in public transport and enhancing safety standards for conveyor belts in the mining and food processing industries.
The process begins with a comprehensive full 3D laser scanning of conveyor structures. Advanced technology allows the creation of detailed 3D models of the conveyor systems. By visualising the entire set-up in a digital format, the
team can identify potential challenges and design solutions that enhance safety and efficiency.
Key features and benefits:
• Effortless installation, removal and maintenance
• Strength and quality
• Fully customisable to meet specific site requirements
• Convenient ‘hook, hang, and lock’ mounting system
• Safety enhancements during operation and maintenance
• Sound-deadening properties
• Long-lasting UV protection
• Custom labelling options
• No painting required
• Australian made and owned
Diacon guards are trusted across a diverse range of industries, providing essential safety and efficiency in the processing of materials such as sugar, grains, salt and coal.
The innovative solutions are designed to meet the specific challenges faced by sectors dealing with heavy and often hazardous materials, including iron ore, copper, zinc, nickel, gold, silver and lithium.
From rock to wood products, Diacon guards enhance operational safety by preventing accidents and minimising downtime.
10-04_SafeToWork_InsertV1.pdf 1 9/18/24 10:47 AM
• 100 per cent corrosion-resistant
• Up to four times lighter than steel
• E xceptionally lightweight and easily stored away
“Our commitment to quality and customisation means that each solution is tailored to the unique requirements of the processing environment,” Refalo said. “With Diacon guards in place, industries operate with confidence, knowing they have the best protection available.”
Martin’s Foundations™ Learning Center provides online, aroundthe-clock access to a wide variety of training modules featuring scores of topics. We also offer an extensive curriculum of webinars, Zoom sessions and in-person classes conducted by factorytrained, certified professionals. These instruction options are provided not only for the training of workers and staff, but also to identify potential dangerous conditions, prevent equipment failure, and reduce unnecessary cleanup costs and unscheduled downtime. Click. Learn. Profit. Go to www.martin-eng.com to find out more.
NIVEK INDUSTRIES ENSURES WORKERS DON’T HAVE TO SHOULDER THE BURDEN OF HEAVY LOADS ALONE.
In 2008, Hunter Valley mine diesel mechanic and fitter Kevin Cant narrowly avoided being crushed by a half-tonne belly plate he was removing from a bulldozer.
Belly plates are prone to slipping when being removed, with injuries like serious crushes not uncommon.
These plates can weigh up to 400kg while empty, but conditions like those at the iron ore mine at which Kevin was working could see the build-up of debris increase the plate’s weight to more than 700kg.
Kevin knew something had to be done to protect others who might not be as lucky as he was. He spent the next three years researching, designing and developing the first prototype of what would become known today at mine sites across Australia as TED.
TED – which stands for Tracked
plate jack designed for applications where a crane or forklift isn’t viable.
With a lifting capacity of up to 800kg, TED aims to remove workers from the hazards associated with suspended loads when working not only on bulldozers, but graders, dump trucks and other mining equipment and earthmoving machinery.
Kevin launched TED under his own company, Nivek Industries, in 2011 and began rolling out the solution to Australian mines.
Two years later, Kevin’s brother joined the new Nivek family. Now the company’s general manager, Derrick Cant told Safe to Work the TED solution was the linchpin that launched an entire brand dedicated to protecting workers in rough Australian mining conditions.
“Kevin built the first TED in his backyard all by hand,” Derrick said.
that specific application.
“But we’ve come a long way since then, with TED undergoing multiple upgrades and enhancements, as well as now having over 40 attachments and counting on offer to increase its versatility.”
One of the major evolutions to come out of TED’s deployment within the mining industry is its heavy-duty brother, Big TED, which was primarily designed to
and manoeuvrability.
Not only do TED and Big TED remove workers from underneath hazardous loads otherwise suspended by chains or come-alongs, they aim to protect workers long-term by eliminating manual handling related issues like back injuries and muscle strain.
“For example, TED can be driven under a dozer and used to raise the table up and support the machine physically, meaning there is no suspension of the load,” Derrick said.
“Then the operator will go in, undo the four bolts in the corner and stand clear before dropping the belly guard down, so they won’t be in the drop zone if it does slip off or all the debris slides out.
“Once the component is lowered, the guard is able to be driven out –rather than dragged, which causes strain on the body – on TED’s tracks to be cleaned, then driven back in to position and lifted back into place.
“It’s a much safer and more efficient process.”
The next innovation to join the Nivek family was the Lift Assist 40 (LA40), which takes the idea of removing heavy loads and applies it to smaller applications.
The LA40, which can be attached to TED, aims to reduce muscle strain and fatigue, as well as chronic musculoskeletal injuries in workers,
by taking the weight of equipment like rattle guns, impact drivers and torque tooling.
The system can hold tools weighing up to 40kg and its articulation joints have been designed to push fingers out rather than pinch, addressing another common hazard within the industry.
Joining the LA40 in removing the need for heavy lifting is TED’s cousin BOB (Beast of Burden), which comes with a load capacity of 0.5 tonnes, 1.5 tonnes or five tonnes.
Like TED, BOB is an all-terrain remote-controlled carrier. But BOB differentiates itself in its ability to track loads across long distances with rough terrain.
“I was recently at a mine site in Western Australia where workers were having to carry 60kg pumps up to 100m over rough terrain,” Derrick said. “This is the perfect application for BOB, which can handle any surface and comes with a variety of custommade smart attachments that help it take on any task.”
Nivek has come a long way since TED was first developed in Kevin’s backyard.
The company now has a research and development (R&D) facility in Singleton, New South Wales, from which the Cant brothers and their team of engineers develop new solutions and work to continually improve their existing products.
And the innovations aren’t slowing down any time soon for Nivek, with a new range already on the horizon for release in 2025.
The REX (Remote EXcavation) range will be a fully electric mini loader capable of working in confined spaces without producing added noise or fumes.
“The REX is narrow enough to fit through a doorway and can be fitted with a live video feed so it can be operated through hazardous areas without having to send in a worker,” Derrick said.
“We see it mainly operating in mines to perform cleaning duties around washeries and conveyor belts, but as we’ve seen with TED and BOB, I’m sure its uses won’t stop there.”
Nivek’s ability to problem-solve and innovate new solutions has seen it become a go-to in the industry for removing the challenges and hazards associated with heavy lifting and suspended loads.
“These solutions mean more people with different abilities and strengths can still get the job done safely and efficiently,” Derrick said. “With operators looking to open up opportunities for a more diverse range of workers, solutions like those from the TED and BOB and the LA40 family can help.
“No matter the challenge, we work to design custom solutions that meet the needs of any site.”
At the heart of every Hexagon solution is safety.
And the company’s underground collision avoidance system (UG CAS) is no different.
Designed to enhance safety and efficiency in underground mining operations, Hexagon UG CAS provides operators with 360° awareness via non-intrusive cabin display units for surrounding vehicles and equipment when travelling at any speed and in all conditions.
The technology allows operators to see not only the location but also the direction of travel of nearby people and other vehicles. The system then uses this information to incorporate path prediction and leverage auditory and vibration alarms that alert drivers to collision risks.
safety with our Hexagon CAS solution, and the in-house expertise behind
that solution applies to Hexagon UG CAS as well,” Hexagon underground portfolio manager Mateus Quintela told Safe to Work
“Hexagon UG CAS is built with a customer-centric mentality, meaning it has an easy interface for the operator to understand, is simple to install, and leverages innovative technologies available in the market.”
UG CAS is part of Hexagon’s expanding autonomous mining portfolio, which is designed to help the industry future-proof operations and address challenges such as operational productivity and decarbonisation.
Also falling under this forwardlooking portfolio is Hexagon’s suite of offerings powered by HARD-LINE, a leading heavy machinery automation company Hexagon acquired in
TeleOp helps to eliminate exposure to common mining hazards.
automation solutions such as TeleOp, an autonomous system that remotely operates heavy machinery from a control station in a safe area on the surface or underground.
TeleOp enhances safety by
the operator to comfortably control the equipment from a distance.
HARD-LINE senior director Ryan Siggelkow told Safe to Work the TeleOp and radio remote control (RRC) systems have already been utilised in several Hexagon applications.
Most recently, Hexagon integrated TeleOp with UG CAS to create a safety powerhouse for underground mining.
“The integration of these two worldclass systems provides an added layer of protection for sites that would like to further de-risk activities underground,” Siggelkow said. “Hexagon’s UG CAS and TeleOp are integrated in a manner that enables each solution to operate alone or in concert with each other.
This means customers can upgrade at any time from a Hexagon UG CAS implementation to add RRC or TeleOp functionality or add CAS to an existing RRC or TeleOp installation.”
Siggelkow said the accuracy and dependability of Hexagon UG CAS will bring users peace of mind.
“Integrating these two systems lays the foundation for the implementation of future technologies like level nine EMESRT (Earth Moving Equipment Safety Round Table) vehicle intervention, and more enhanced autonomous systems,” he said.
“It also enables added functionality, such as collision detection in vehicle-
to-person, vehicle-to-vehicle and vehicle-to-object situations.”
The blend of Hexagon UG CAS with TeleOp capability further reinforces how Hexagon is delivering on its quest to help mines become increasingly connected and autonomous, ensuring a scalable, sustainable future.
Hexagon is here to help miners future-proof operations and address industry challenges.
EPIROC’S MOBILARIS SITUATIONAL AWARENESS SOLUTION CAN NOW BE UTILISED AT UNDERGROUND AND SURFACE MINES.
For over 70 years, Epiroc has been a leading original equipment manufacturer (OEM) to the Australian mining industry.
The secret to its long-standing success? Always innovating its offerings.
In keeping up with recent industry trends, Epiroc is focused on three key technological areas: automation, electrification and digitalisation.
The company believes it is these focal points that will strengthen safety and productivity, while lowering carbon emissions and reducing total operating costs.
That’s why Epiroc created Blast Support, a next-generation safety solution for surface mining.
The digital decision-support tool is designed to ensure safe blasting without losing time and productivity.
Built with 3D visualisation and open space positioning, Blast Support provides the control room with an overview of everyone’s location on-site before blasting.
“Blast Support can tell in realtime whether an area is safe to blast or not,” Epiroc business line manager digitalisation Andreas Prill told Safe to Work. “It works by assigning WiFi or LTE (long-term evolution) tags
to people in the mine and utilising open-space positioning and satellite imaging to create a 3D map of the blast area, including surface blast zones and tunnels.”
Blast Support optimises blast design and execution while ensuring all personnel and equipment are cleared from the area in line with scheduling, reducing time spent looking for personnel prior to blasting.
It also increases productivity and efficiency by monitoring the blast results and performance and optimising the material flow and haulage routes.
Blast Support not only enables the physical safety of workers, but it provides mental stress relief. Encouraging collaboration and coordination by empowering seamless communication, personnel are endowed with real-time information and digital tools. This then allows for clear communication between people in and around the mine, thus helping to reduce stress before and during the blasting process.
Increasing transparency among personnel also lessens the chances or errors or, in worst case scenarios, injuries and fatalities.
Blast Support was created when Epiroc recognised how timeconsuming it is for medium- and largescale mine sites to ensure personnel and assets are clear from the blast.
The OEM took its proven underground safety technology, Mobilaris Situation Awareness, and tailored its features to suit surface mining operations.
Mobilaris Situational Awareness enables the real-time tracking of
people, mobile and fixed assets and vehicles while the status of various operations is monitored within the mine. This not only includes 3D mapping of the blast area but also other hazardous areas, such as where there is a risk of rockfall or land slide, increasing alertness and responsiveness along the entire operation.
Mobilaris Situational Awareness allows traffic to be managed in and
around risk areas, and alerts can be raised when certain thresholds are reached. Ventilation can also be triggered by machines or personnel entering certain areas, which aims to create a safer and more controlled mine operation.
By combining Blast Support with Mobilaris Situation Awareness, users can send zone-based messages, allowing a site operator to map out danger zones, monitor the position
of workers in real-time, and send informed warnings or alarms to those workers to clear the area.
The system is also technologyagnostic, making it compatible with various LTE networks and tags, including Epiroc’s virtual tag, an application for Android smartphones.
“With these two tools, we are able to create different blasting and clearance areas and the system can account for everybody in real-time,” Prill said.
Blast Support being interoperable with third-party communication infrastructure already established at mine sites encourages simple integration and reduced capital expenditure.
“Blast Support reduces time for blasts by ensuring that all personnel and equipment are cleared from the area on time,” Prill said.
“And, most important of all, it provides another layer of safety for workers.”
Blast Support is a modular addition to Mobilaris Situation Awareness.
Epiroc offers various Mobilaris tags that enable the effective localisation of personnel and mobile assets within a Wi-Fi or LTE network.
The position of each tag is determined with special algorithms.
“Blast Support reduces time for blasts by ensuring that all personnel and equipment are cleared from the area on time.”
The tags can be updated remotely over the air whenever needed and are configured, managed and monitored from the Mobilaris Mining Intelligence platform. This range of products aims to improve safety and productivity throughout the shift.
The portfolio comprises a range of technologies such as Blast Support, Mobilaris Situational Awareness, Mobilaris Emergency Support, Mobilaris Onboard, Mobilaris PocketMine, Mobilaris Shift Support, Mobilaris Event Automation and Mobilaris Network Awareness.
Alongside Blast Support and Mobilaris Situational Awareness, Epiroc’s complete Mobilaris surface offering also includes Emergency Support, PocketMine, Event Automation and tags.
With more than 40 Mobilaris Situational Awareness installations completed globally, Epiroc is bringing its proven solutions from underground mines to create new value for surface mines.
“Epiroc has years of experience in underground blast safety, and with Blast Support we have brought this important technology to the surface,” Prill said.
Routinely carrying out maintenance on heavy machinery during his time at several Australian mine sites, heavy plant mechanic Luke Dawson became concerned by the level of risk to which he and his colleagues were exposed on a daily basis.
Pneumatic and hydraulic maintenance of equipment is essential on a mine site, but it can put technicians at risk of crush and fluidinjection injuries.
Dawson began formulating ideas for new technologies that could keep workers out of the line of fire and increase safety standards around live testing machinery.
His developments led to the 2019 establishment of SafeGauge, of which Dawson is founder and managing director.
“It started with a wireless pressure transducer for technicians to read hydraulic pressure away from danger,” Dawson told Safe to Work. “Soon followed the development of other high-demand products including the wireless dial indicator, tachometer, push rod and no-contact laser measurement to safely complete common high-risk maintenance tasks.
“We have grown to a team of 25 today, with a range of skills to engineer, manufacture and supply to the mining industry around the world.”
SafeGauge remains proudly Australian-owned, with sales in over 15 countries and backing by a global distribution network that promotes and supports safer working practices in all heavy industries.
Of all SafeGauge’s innovations, Dawson said the MultiTool Pro is the most advanced tool on the market for live machinery maintenance.
“Up to 12 tools can connect to our MultiTool to test, log data and generate comprehensive reports,” Dawson said. “From two touches of the screen, the user can be testing which, most importantly, makes it easy to use.”
The MultiTool Pro, like all SafeGauge tools, has a specialist wireless capability that allows workers to test equipment remotely, such as from the cabin of a mining machine.
“All tooling is quick-connect to the machine and can be used from up to 100m away,” Dawson said. “This allows even the largest machines in the industry to be maintained from a safe distance.”
SafeGauge’s products are currently used in a variety of applications, mostly on heavy mobile machines including haul trucks, bulldozers, excavators, graders and loaders for any type of live work.
“It could be a quick pressure test of a brake pack, or an in-depth commission of a machine after overhaul,” Dawson said. “Importantly, the flexibility of each product is not brand-specific and will remain agnostic across our entire range.”
Through his industry experience, Dawson has built an understanding and close connection to SafeGauge customers and their needs.
“We listen and design our products from their direct feedback,” he said.
“Having the internal capabilities for the product design, manufacturing and network of credible distributors around the world clearly separates SafeGauge from any competitor, though we also understand we are all working towards the same goal of improving the safety of the mining industry.
“We aim to join forces to help make a greater difference rather than compete.”
throughout their journey to eliminate live work with ongoing product support, team training and servicing,” he said. “Sometimes we don’t have all the answers, but we invest our time to understand the customer’s problem and provide either advice or engineered solutions.
of not needing a user manual, we wanted the products to be intuitive enough for first-time users to understand.”
Interoperability, customer satisfaction and ease of use are central to SafeGauge’s mission to eliminate live work.
This commitment is setting the company up for a future defined by keeping workers and technicians safe on the job.
And SafeGauge isn’t stopping at Australian miners.
The company recently expanded into the US with an office based in Phoenix, Arizona.
And with more and more innovations bearing fruit, Dawson said SafeGauge is looking to expand into other countries.
“We have an exciting product roadmap that solves unique problems,” he said.
“Our most recent product release includes a free mobile application for large companies and individual mechanics and contractors alike to keep their workers safe.”
Dawson said SafeGauge is providing customers their own data in a way that helps improve efficiency and machine availability.
“We are empowering our customers with the technology to test their machines safely and return them back to work in a timely manner,” he said.
“Our goal is to ensure no one has to risk their safety when live testing machinery and we will continue working hard to change industry standards.”
Arecent report from the Australian Resources and Energy Employer Association anticipates an additional 26,810 workers will be needed by 2029 if the mining industry is to keep up with new projects as they emerge.
More workers on more mine sites means more people are at risk of injury and harm by operating in close proximity to major machinery and equipment.
Operators need reliable collision avoidance strategies if they are to keep the ever-growing number of miners safe on the job.
Strata Worldwide has been rising to meet this challenge for over three decades.
The company’s HazardAVERT system is designed to keep workers out of harm’s way by alerting them to approaching machine-to-machine or machine-to-person collisions. When a small receiver device worn by a worker or attached to machinery detects an electromagnetic field around machinery, it immediately communicates the potential danger to the wearer and operator.
HazardAVERT is in widespread use in South Africa and the US, with more than 2000 vehicles and 40,000 miners protected daily. In Australia, largescale deployment of HazardAVERT is currently underway at mines like BHP’s Olympic Dam in South Australia and Coronado Coal’s Mammoth underground mine in Queensland.
The Earth Moving Equipment Safety Round Table’s (EMESRT) has defined a range of collision avoidance levels from one through to nine, each of which indicate a certain level of system capability.
Strata managing director Tony Napier told Safe to Work that HazardAVERT is popular with mines thanks to its level nine machine intervention control capability.
While HazardAVERT’s alerting system falls under level seven, a level nine control means the technology is also able to slow or bring a machine to a complete
stop based on personnel or machinery detection.
“Strata has taken our expertise with level nine control to our HazardAVERT system and now we’re one of the only ones really doing level nine with AI [artificial intelligence] systems,” Napier said.
“The experience we’ve gained from level nine in mining is now allowing us to provide this capability in other industries including construction.”
HazardAVERT has been successfully deployed throughout Australia for more than a decade, bolstered by Strata’s continued research and development (R&D) to make it even more effective.
“We continue to enhance it, and it’s certainly moving ahead in leaps and bounds,” Napier said. “We’re seeing improvements on a monthly or even weekly basis.
“There’s many different technologies out there, but what we offer is one that is proven to do the job.”
Strata’s latest collision avoidance technology, HazardAI, offers EMESRT level seven and level nine protection, but the video-based HazardAI doesn’t require wearables. Rather, it uses
stereoscopic 3D cameras attached to machinery that differentiate between people, machines and obstacles.
HazardAI uses advanced algorithms to analyse collision potential and records and collates data mine operators can then use to address ongoing areas of concern.
“HazardAI can detect people and machines up to 40m away extremely accurately,” Napier said. “We model algorithms based on the environment they’re going to be used in, adding another layer of precision and protection.”
As with HazardAVERT, Strata is dedicated to continually improving HazardAI, with a team of engineers in Australia and the US working to reach the next safety zenith.
“These solutions are industry mainstays,” Napier said. “Whether it’s HazardAVERT, HazardAI or another of our technologies, we’re committed to bringing the latest innovations to the mining industry.”
Tradesales relocatable off-grid solutions including site offices, crib rooms, and toilet blocks for mining and remote locations.
Equipped with solar power, water, and wastewater tanks, these modular containers provide vital infrastructure without relying on the grid. Our designs are tailored to your needs, ensuring comfort, functionality, and compliance with safety regulations.
From heat relief to rapid deployment during shutdowns, Tradesales delivers premium, relocatable infrastructure for seamless, off-grid operations.
Tradesales: No Grid, No Problem
www.tradesales.com.au • 1800 999 521
Industry events are essential for bringing together the best and brightest in the resources sector to showcase their latest innovations. These events are critical to driving the industry forward and keeping Australia’s mines on the cutting-edge.
One mining event behemoth –MINExpo International – gathers industry professionals, experts and decision-makers every four years to collaborate, learn and engage with all facets of the resources sector.
The 2024 iteration in Las Vegas saw next-generation software specialist Mine Site Technologies (MST) take to the floor to launch two new technologies.
After the success of its integrated software platform, HELIX, MST has been developing more solutions to help miners get the most out of their data. After all, more data means safer sites for workers.
HELIX Dispatch and HELIX Telemetry are the highly anticipated fruits of these labours.
Dispatch is designed to manage a site’s entire fleet from the production face to the surface and every point in between.
Using automation features, dispatchers and supervisors can oversee shift plans, monitor equipment performance and address issues as they arise.
This means companies can protect workers using live data including location, time and crew information.
“It’s all about collecting data and providing operational insights that will help mines target the specific areas or processes of their mining operation,” MST product manager Nick Rebeiro told Safe to Work. “The key advantage of HELIX Dispatch over other fleet management software is the automated production tracking capabilities.”
Rebeiro said that without any operator input, miners can track all of the material movements that are completed by the scoops and trucks underground or on the surface.
“We can track from the production face all the way to surface crushers and record material quality and quantity information so you always have a picture of how much material is located in your different production areas,” he said.
“By keeping an eye on where fleets are located and keeping workers safe with a complete picture of the work being performed underground, we can cut downtime, increase productivity and maximise the amount of material extracted from the mine.”
MST had a live demonstration of HELIX Dispatch at MINExpo, which allowed attendees to witness the technology’s potential first-hand.
Now a Komatsu technology brand, MST had HELIX Dispatch incorporated into one of the original equipment
manufacturer’s (OEM) load haul dumps (LHD). MST then simulated a haul cycle for the LHD.
Using the HELIX 3D map, which provides a geospatial digital twin of a mine, MST created a visual representation of the tracked location of the LHD.
“In conjunction with those movements, the equipment operators could see the material movements automatically captured through HELIX Dispatch,” Rebeiro said. “We also took our viewers through several other features of HELIX Dispatch, including operator task lists and workplace safety checklists like those used to complete digital pre-start checks for equipment and general site safety checks.”
Where HELIX Dispatch provides real-time access to production data,
HELIX Telemetry works to gather realtime information that helps operators stay on top of any potential equipment failures that may arise.
This is done through the collection and analysis of sensor and alarm data taken from mining equipment, which is then displayed as actionable insights on dashboards in the broader HELIX platform.
“The whole concept around HELIX Telemetry is preventive maintenance,” Rebeiro said. “By having access to this data live, you may identify something before a problem occurs, helping prevent unplanned equipment downtime and improve operator safety by preventing any failures while the equipment is being operated.”
Rather than waiting for issues to occur, HELIX Telemetry aims to empower miners to plan ahead.
“Generally, downtime caused by a failure is going to result in a longer maintenance period because the cause has to be determined and failed parts may cause damage that needs to be repaired,” Rebeiro said.
“Informed decision-making helps improve your vehicle reliability, because you can schedule maintenance to prevent failures.”
With the data collected by Telemetry, operators receive a snapshot of information in the moment and maintenance technicians can take a deep dive into what is happening to a machine over a longer period.
“You can configure the display of real-time information according to a specific context and geotag all of these sensor and alarm events that occur underground, which helps with root cause analysis for any failures
that have taken place in the mine,” Rebeiro said.
A key feature of the HELIX suite is that it’s an OEM-agnostic solution. Despite being a Komatsu brand, Rebeiro emphasised MST’s mission to develop solutions that can be configured to any mine specification or equipment – an ethos shared by Komatsu.
“We have a very flexible configuration that helps our customers really only pull in the specific sensors and alarm data that’s relevant to them,” he said. “Sometimes it can be an overwhelming amount of data, but what we allow you to do is connect to multiple sensor interfaces, so on any machine you could have transmission, vehicle control, unit and engine interfaces, just to name a few.
“Through our sensor hub, data logger and edge device, we can connect to multiple interfaces and combine data from all three according to the operational context that’s desired.”
Dispatch and Telemetry are the latest innovations to join the HELIX suite, which includes HELIX 3D, the
foundation of the HELIX platform that offers real-time positioning of personnel and equipment in a 3D map for underground and a 2D map for surface operations, and HELIX IoT, which enables long-range communication of sensors across vast geographical areas – but MST isn’t stopping there.
MST product management and marketing general manager Alex Gawad said HELIX has a major future ahead in hazard avoidance and sustainability.
“We have on our near-term roadmap another HELIX module that will be focused on personnel safety around mobile equipment,” Gawad told Safe to Work. “This new module will allow control centre personnel, as well as machine operators, to view in real-time who is around the machine and take precautions if needed to avoid a potential incident.
“We want to bring that transparency and visibility to mine managers and safety managers alike.”
With safety and sustainability key pillars of the future of the Australian mining industry, MST is looking to give
operators a full picture of their sites that they can use to realise that future.
“Electrification is bringing increased safety but also better outcomes for the environment,” Gawad said. “In the future, we want HELIX to provide operators information about the amount of carbon dioxide their equipment is producing, but also data on their electric fleet and how it can be optimised.”
Gawad emphasised MST’s commitment to exploring every avenue when it comes to making mines more productive, energy efficient and, ultimately, safer.
“HELIX is an enterprise platform designed to be interoperable between all of our different products, offering users a mine-wide, one-stopshop solution to data management,” he said.
“With the launch of Telemetry and Dispatch at MINExpo, and our new developments in the works, we are demonstrating that we will continue to look for potential paths to deepen this integration between our products, boost on-site safety and provide additional value for our customers.”
Alot has changed in the last 15 years, whether it be new standards or technologies, or emerging mining practices requiring a new way of thinking.
But through it all Aptella’s mission has remained the same: to protect workers and equipment.
A leading automation and positioning technology specialist, Aptella has been distributing new solutions to mine sites across Australia and south-east Asia since it originally formed as Position Partners in 2008.
One of the most critical ways the company has been able to achieve its mission is through its hazard and collision avoidance technologies.
One such technology Aptella distributes is Blindsight by Sydneybased technology company Presien, which detects a potentially dangerous on-site situation about to unfold and alerts the operator, calling their attention to the risk before it turns into a costly accident.
the full spectrum of data the system captures, including automated health and safety reports. This means elements like safety metrics and site performance can be quantified with the tap of a finger.
and they were looking at what type of implementations and interventions they could put in place based on the data that they were seeing to improve safety and behaviour around heavy equipment,” he said.
Aptella market development manager Nick Corr said Blindsight is an easy-to-use device installed in the cab or on fixed infrastructure. This means customers can be ready to go in a matter of minutes thanks to Presien’s artificial intelligence (AI) coming pretrained for industrial applications.
“The real differentiator with Blindsight is that it’s an integrated system that has a full reporting suite on the back end,” Corr told Safe to Work.
“A stand-alone system doesn’t offer visibility of what’s going on, whereas an integrated system with comprehensive real-time reporting is a game-changer for allowing managers and supervisors to see behaviours or habits that may be compromising safety.”
The Blindsight solution is being used in some of the most significant coal and iron ore mines in Australia.
“One of our customers operates one of Australia’s largest feedlot operations in Queensland,” he said. “They trialled the Blindsight system for six months before making the decision to put it on all their wheel loaders.
“They now have 12 systems fitted and have seen more than a 55 per cent reduction in critical alerts, which has resulted in them being awarded a safety innovation award.”
Crediting the customer’s significant decrease in such alerts to being “on the journey” with a full Blindsight integration, Corr believes there is even more to be gained in the long term than protecting workers or equipment in the moment.
“Some organisations want a setand-forget solution, and that’s fine, but the overall improvement mines can see from embracing an integrated system with this amount of data is massive.”
Aptella recently collaborated with international technology giant Torsa to establish a distribution agreement to bring a new collision avoidance system to Australian mines designed to enhance safety without the need for tags or identifiers.
Using a predictive algorithm, the Torsa solution is able to monitor and analyse interactions between vehicles and personnel with centimetre-level precision. It allows operators to take a holistic approach to mining and consider the context in which their equipment and personnel operate.
Aptella executive manager of mining Andrew Granger believes the Torsa technology marks a pivotal shift for the mining sector.
“It’s well documented that fatalities and incidents have occurred in mine sites across Australia,” Granger said.
“I think anyone that has been to a mine or works in mining knows the sheer size and enormity of these risks.
“While it can be accepted that it is a dangerous environment, it cannot be accepted that we’re not doing anything about it.”
Centralising data on a unified platform, the system acts as a bridge between field personnel and decisionmakers, offering situational awareness and enhanced site-wide safety.
By proactively identifying potential hazards and collisions before they occur, the Torsa system is able to provide real-time alerts, which Aptella product manager for mining Denzil Khan believes is a standout feature.
“The beauty of Torsa is the multisensor approach – intelligently processing sensor data to give accurate alerts, ensuring operators trust the technology and avoiding alert fatigue or unnecessary frustration,” Khan said.
“Torsa’s intelligent processing capabilities allow it to adapt to various operational scenarios.
“This level of sophistication not only enhances safety but streamlines operations, reducing unnecessary distractions for operators that have previously caused frustration and inefficient use of time.”
Another key benefit of Torsa’s technology is its ability to adapt to diverse conditions. It provides customisable alerts and responses tailored to varying environments, aiming to enhance safety and operational efficiency. This flexibility can contribute to optimised workflows, leading to increased productivity and cost savings.
Torsa chief executive officer Juan Raúl Santana called the system “a breakthrough in safety technology”.
“It has the potential to save lives by significantly improving
safety standards across various domains,” Santana said.
“Our system is unique in its ability to detect non-metallic obstacles, including rocks, quarrying fronts and berms, thanks to advanced LiDAR [light detection and ranging] technology.”
Certified to levels seven, eight and nine, Torsa’s collision avoidance system offers full intervention control, customisable to different site requirements and asset types, including draglines, dozers, haul trucks and light vehicles.
“Our goal is to create universally applicable systems, which is why we actively engage with industry forums and standards bodies,” Santana said.
According to Granger, Torsa’s collision avoidance technology allows operators to confidently address environmental challenges while safeguarding their workforce.
“The technology not only signifies a major step forward in safety practices but also promises improved operational efficiency and sustainability across the sector,” he said. “For mining professionals and stakeholders, embracing Torsa technology is not just an option; it is a necessary step towards a safer and more efficient mining operation.”
Granger is confident Aptella technology is a tool that will give future generations more options when it comes to working in the resources sector.
“Often in mining it’s an environment where multiple generations have been in the sector,” he said. “I think technology makes that hugely exciting for the modern generation.
“Systems like these mean that maybe you’re not a truck driver anymore because in the future that’s an autonomous system. But perhaps you’re working on the technical side, running and managing these state-ofthe-art systems.”
With a network across Australia, New Zealand and south-east Asia, Aptella, supported by Mitsui & Co., plans to provide comprehensive sales, deployment, training and technical support under the distribution agreement with Torsa.
“Torsa’s collision avoidance system enhances our safety portfolio and integrates seamlessly with our machine guidance and fleet management solutions,” Granger said. Whether Torsa, Blindsight or another technology in its suite, Aptella is confident it can work with the needs of any mine to keep workers safe when they need it most.
WESTERN AUSTRALIA’S MINING SECTOR IS FLOURISHING IN LARGE PART THANKS TO FLY-IN, FLY-OUT WORKERS. BUT FOR THE INDUSTRY TO KEEP RIDING ON THE WINGS OF SUCCESS, IT NEEDS CRITICAL RESOURCES.
It might sound obvious to say the mining industry is dependent on resources, but the kind of resources underpinning the success of the sector go beyond
For the Shire of Laverton in Western Australia, the regional Laverton airport is a gateway to some of the state’s most industrious mines, including Lynas’ Mt Weld rare earths
The airport is a massive service on which the region’s miners rely, and that’s why Shire of Laverton president Pat Hill said it’s time for an upgrade.
“Over $5 billion in mining wealth
$2.85 million earmarked for a new terminal expected to hold 80 people at any given time set to come online by the end of 2024.
Another $1.3 million will be used to completely reseal the airstrip and parking areas, with the same amount to be spent on new runway turning nodes.
With around $700,000 in landing fees injected into the Shire last
financial year, Hill hopes the upgrades will bring even more FIFO workers to the region in the future.
“We’re doing a lot of improvements and we encourage people to come use it,” Hill said. “We want the airport to be very user-friendly with stateof-the-art facilities that can even be expanded in the future.”
Getting FIFO workers to their destination efficiently and in comfort is essential, but ensuring they are cared for while on site is just as important.
Studies show loneliness and lower mental health can be issues for FIFO workers, who spend a significant time away from their families for work.
This can be an especially pervasive issue for women, who are often considered to be default primary caregivers in their family units, causing increased stress and guilt when they are away.
International confidence coach Erika Cramer is on a mission to give FIFO workers, particularly women, the resources to promote better mental health within themselves and their communities.
In early October, Cramer led a ‘girls’ night out’ hosted by the Shire of Ashburton in WA’s Tom Price, home to Rio Tinto’s Tom Price mine, which aimed to give women a space to share their experiences.
“When a woman’s mental health is better, the whole world is better,” Cramer told Safe to Work
“Having dedicated spaces where we can share things in a community environment is so helpful.”
Cramer has three key pieces of advice for female FIFO workers looking to boost their confidence, which she references from her book, Confidence Feels Like Shit.
“The first is to practice some kind of inquiry, whether it’s journaling or just getting your thoughts down on paper,” she said. “It’s a really powerful practice because it allows us to separate what we think with who we are.
“The second is to lean into community and have conversations. A lot of corporations have women’s arms now, and I think that’s so helpful.
“The third is to have some kind of mentorship, whether it be a therapist or a life coach or even a personal trainer – having someone that is supporting you for better mental health and wellbeing and allowing you space to unpack things is critical.
“I really encourage FIFO workers to speak up and open up.”
Whether internally or on the runway, having an abundance of resources is the key to empowering Australian workers to consider FIFO work.
As the mining industry continues to grow, more workers than ever are going to be needed to fill essential jobs. And with a skills shortage looming, it’s initiatives like those spearheaded by Hill and Cramer that are going to make the difference.
THANKS TO A NEW PARTNERSHIP, MECHANIX WEAR GLOVES ARE BEING RECYCLED INTO THE VERY FABRIC OF A GREENER FUTURE.
Australian regulations regarding the quality of personal protective equipment (PPE) are known to be some of the strongest in the world. Everyone who has worked in the resources industry is well versed in how seriously these regulations are taken, as well as the implications of non-compliance.
But when it comes to regulating what happens to that PPE after use, the lines on what, where and how it can be disposed of responsibly are not so clear cut.
Millions of tonnes of textiles end up in landfill every year, and PPE from all industries is a big contributor.
If the world is to embrace a netzero mentality, it’s going to take those committed to developing a circular economy to push things forward. And part of that is ensuring textiles like PPE don’t become the hurdle that staunches progress into the future.
In a circular economy, materials never become waste and are instead continually reused and recycled. It might sound too good to be true, but thanks to a partnership between global work gloves manufacturer Mechanix Wear and Melbournebased textile recovery and recycling company UPPAREL, Australia’s mines may be one step closer to bringing such a future to fruition.
The partnership has led to the development of the RevUp initiative, which brings together Mechanix Wear’s mission of ‘revolutionising environmental vision’ with the UPPAREL name.
The initiative aims to keep Mechanix Wear gloves, which are used in some the of harshest Australian working conditions, out of landfill.
“RevUp involves Mechanix Wear and its customers sending us their old gloves, which we then turn into functional products,” UPPAREL partnerships manager Riley Aickin said. “We’ve been working on this Mechanix Wear–UPPAREL partnership since early 2024.”
When the gloves arrive at UPPAREL’s facility, they are sorted into two categories.
The first category is gloves that are to be reused, which are circulated through UPPAREL’s 450 charity partners to find their new home.
The second category sees the gloves turned into a host of important products.
While the prevalence of recycled PPE is increasing across Australia, the mining sector’s waste challenges call for a bigger solution than recycled PPE alone. That’s why RevUp looks to turn used Mechanix Wear gloves into products that can be used beyond the mine site.
“The gloves might be shredded to make ‘FluffUP’, which is used to fill things like soft toys, beds or cushions,” Aickin said. “They could also be used to make UPtex, a material from UPPAREL that is made entirely from recycled textiles.
“UPtex can be used to make slippers, desk mats, furniture – the possibilities are endless.”
Mechanix Wear commercial accounts manager Courtney-Jane Wilson said RevUp is a labour of love.
“We wanted to ensure our products are recycled in a 360° manner,” Wilson said.
“That means that not only are they made from recycled materials but they are also able to be recycled at the end of their lives.
“Above all, we wanted a service that had no greenwashing and was genuinely traceable and trackable.”
Wilson said the partnership first began when Mechanix Wear was updating its environmental, social and governance (ESG) goals and felt the changing tide of PPE disposal priorities.
Mechanix Wear saw that its customers wanted to work with companies that had strong ESG goals, especially since it can be hard to find ways to recycle products in Australia.
“We’re an island nation, so our waste problem is heightened,” Wilson said. “If we can’t find a way to recycle, then the problem remains front-of-mind.
“The UPPAREL partnership solves this problem by not only enabling us to have a 360° recyclable product but also through its ease of use.”
On its journey to boost its ESG impact, Mechanix Wear went to great lengths to ensure every part of its gloves are fully recyclable. Operators who to recycle their gloves now just have to box them up and send them to UPPAREL.
Once UPPAREL has the gloves in hand, the recycling process is fully traceable, making it easy for customers to report on their own sustainability goals.
“It’s a positive step forward on all fronts,” Wilson said. “People’s eyes light up when we talk about this because it’s become such a clear need for the industry.”
Mechanix Wear garners no financial gain in the partnership; the win comes from knowing the company is doing its part to make the world a better place.
“This partnership makes it easy for people to change their ways,” Wilson said. “They know they have a sustainable, quality product in Mechanix Wear gloves, and we know our gloves won’t end up in landfill.
“A lot of research went into RevUp, and it’s going to be a game-changer for us and our customers who want to make a difference.”
While recycling PPE is just one rung on the ladder to complete sustainability, it’s a critical step towards a more circular economy. For those looking for a ‘game-changer’, as Wilson puts it, initiatives like RevUp are there to lead the charge into a greener future.
Mining camps have evolved significantly in recent years, with industry leaders investing in new amenities to improve the living conditions for Australia’s fly-in, fly-out (FIFO) workers.
Olympic-sized swimming pools, gyms and cinemas are becoming more common, signalling a shift towards ‘resort-style’ accommodations. Yet despite these advancements, one basic need can remain largely unmet: clean, breathable air.
While mine sites are known for being dusty places with lessthan-desirable air quality, dongas aren’t the clean-aired escape one might hope.
For most workers, a donga is just a bare-bones room to rest their head before they start their next shift. However, these units often lack adequate ventilation, and rather than providing a sanctuary from the dust-filled environment of a mine site, they can expose workers to poor indoor air quality.
Studies show that carbon dioxide (CO2) levels can build up to potentially harmful concentrations if a window or door is not regularly opened, leaving workers vulnerable to fatigue, nausea and even cognitive dysfunction.
While air-conditioning units provide relief from the heat, they often recycle air rather than purify it, leaving harmful contaminants behind.
The implications of prolonged exposure to such poor-quality air are significant. The build-up of CO2 and other particulates can lead not only to physical symptoms but can also negatively impact mental acuity.
Breathing unclean air over long periods can lead to workers facing challenges in concentration, focus and even emotional wellbeing.
Recognising the issues workers face, VBreathe developed a patented, four-layer medical-grade filter and proprietary gel technology, which purifies and sanitises the air and surfaces within mining dongas.
This innovative solution goes beyond traditional air-conditioning systems by actively neutralising bacteria, viruses, and other airborne particles like dust and silica, making the indoor environment safer for workers.
VBreathe’s expansion into the mining sector builds on its success in homes and healthcare facilities, where its technology has proven the company’s ability to transform air quality, benefiting physical and mental health.
This transition to the mining sector is timely, as there is increasing recognition of the importance of air quality in
worker health and productivity. For FIFO workers, having clean air is essential to maintaining energy and mental clarity, both of which can become compromised by prolonged exposure to contaminated air.
VBreathe mining director Jason Benino noted the frequent complaints he hears from workers about the air quality in dongas.
“Many FIFO workers tell us they leave a stint on-site feeling stuffy, like they haven’t had a refreshing sleep in days,” he said. “Our technology provides a cleaner, safer environment, helping workers breathe easier, sleep better, and wake up feeling more refreshed.”
As an Australian company, VBreathe has the flexibility to adapt its services to meet the unique challenges of the mining sector. This adaptability also allows VBreathe to respond rapidly to the evolving needs of the industry, creating solutions that directly address the real-world conditions workers face on-site.
This helps VBreathe set itself apart as a service-focused company, emphasising health and wellbeing.
“By partnering with our mining customers, we’re focused on developing air-quality solutions specifically tailored for mining camp environments,” Benino said.
Through its medical-grade filtration service, VBreathe not only purifies the air entering and exiting the device but also disperses a natural sanitising agent that neutralises bacteria and viruses, including COVID-19, silica and allergens.
An independent study in a mining donga demonstrated that VBreathe reduced particulate levels by 99 per cent in under 60 minutes, lowering concentrations from 110.4 µg/m³ to between 2.1 and 0.8 µg/m³, which represents a significant reduction.
Workers involved in the study reported improved energy levels, better sleep, and reduced fatigue, all of which contribute to higher productivity and overall wellbeing.
VBreathe executive account director Jason Tippett highlighted the importance of prioritising air quality in the mining industry.
“For too long, poor air quality has been normalised in mining,” Tippett said.
“We believe every worker deserves the peace of mind that comes with knowing they’re breathing clean air and that their living space is sanitised.
“Our goal is to provide a solution that increases productivity, efficiency, and workers’ wellbeing and health.”
performance from their workforce to meet production goals.
With the VBreathe air and surface sanitisation service, Australian mining companies have an opportunity to lead the way in promoting a culture of wellness and safety in their camps.
The service offers a transformative approach, emphasising prevention and wellness at a time when mental health and physical safety have become top priorities. By implementing VBreathe, mining camps take a proactive step towards ensuring their workers return home as healthy as they arrived, if not healthier.
Beyond health, VBreathe’ s air and surface sanitisation service also aligns with the mining industry’s broader focus on sustainability.
By helping to create healthier environments, VBreathe contributes to longer-lasting and more productive careers for FIFO workers. This approach supports individual wellbeing while also benefiting mining companies, which rely on consistent
As mining operations continue to demand more from their workers, VBreathe offers a practical, sustainable approach to ensuring workers can breathe easily, sleep better, and return to their shifts feeling recharged.
With cleaner air, safer environments and better health, VBreathe is helping to set a new standard in mining accommodation.
Mines across Australia are on the lookout for solutions that can help reduce their carbon footprint and make operations safer for workers.
The excessive dust kicked up on haul roads can create health hazards and have ecological impacts, making it an obvious target for a system overhaul. But the chemicals often used to wet down roads can be harsh on the environment.
That’s why when one major overseas coal mine wanted to reduce the dust on its haul roads, it turned to a solution making a name for itself in the industry for its greener touch.
Canadian-based dust control expert Cypher Environmental’s Dust/ Blokr solution is an alternative to traditional road salts and aims to leave no environmental impact behind.
A formulation of sugars and starches made from 95 per cent renewable materials, Dust/Blokr is added to a water truck and sprayed on the surface of a dusty road where its semi-soluble nature minimises the need for frequent re-application.
This helps to maintain dust control on any soil type, even in heavy rainfall or dry spells.
Dust/Blokr’s companion product, Road//Stabilizr, is a biodegradable, non-toxic, non-corrosive biological catalyst-based product mixed into dirt when roads are being made to tackle dust at the source by creating a stronger base.
The products are seeing success in a range of global industries looking to reduce dust and are now being implemented across Australia by sole Dust/Blokr and Road//Stabilizr distributor Eco-Road Hero.
Eco-Road Hero director Ivan Heron said the overseas mine was curious about Dust/Blokr and Road//Stabilizr from the beginning.
“They were having trouble with their road conditions and dust, and called in my local colleagues to help,” Heron told Safe to Work. “The local Cypher distributor team, Road Plus, are close colleagues to Eco-Road Hero.
“They were initially engaged to undertake a site demonstration of their capability.
“They improved a short section of road, and this was assessed by the mine operators. The mine then implemented the improvements more broadly in their road network.”
When determining the best course of action for the mine, Heron said the team worked to gather as much information as possible.
“The local team undertook a detailed geotechnical assessment of the mine roads,” he said. “We worked with the mine owners over a period of 18 months to demonstrate and implement the improvements.
“The implementation was done in a way that minimised disruptions to the mining operation.”
This particular coal mine produces over 20 million tonnes of coal a year and uses 200-tonne haul trucks, creating significant dust challenges that impact air quality.
With such a major operation, downtime spent wetting a road or implementing a time-consuming solution wasn’t an option.
“Roads treated with Road// Stabilizr can be used immediately
after application,” Heron said. “The technologies improved the engineering properties of the in-situ road materials and there were significant increases in properties like California bearing ratio [a measure of the strength designed for testing cohesive materials with a particle size less than 19mm] and material density.
“As a result, the roads were more durable and less dusty.”
The results, Heron said, spoke for themselves.
“The mine operator reported a 50 per cent reduction in the dust in the pit,” he said.
“They also measured a fuel saving of 17.4 per cent on their trucks.
“The fuel saving was explained by an improvement in rolling resistance of approximately 0.7 per cent, which sounds modest but is significant in engineering terms.”
Since the implementation of Dust/ Blokr and Road//Stabilizr, Heron said the local distribution team has
fostered an ongoing relationship with the mine.
“We are a solution provider not just a product supplier,” Heron said. “We work with our customers to develop procedures for the application of the two technologies with their equipment and people.
“We use prudent engineering approaches to road challenges in combination with these technologies.”
When it comes to other mines looking to reduce their carbon footprint
Hero takes a holistic approach that considers all facets of an operation.
“There are strong regulator signals for the mining industry to reduce their carbon footprint,” he said. “A road focus can deliver carbon reductions in a way that is very low cost compared to other approaches.
“This approach can be delivered quickly and significantly enhance road, emissions and safety performance.”
The Tracked Elevating Device (TED) is an essential piece of safety gear for anyone working on dozers, graders, dump trucks and other mining and earth-moving machinery.
• Remote-controlled operation
• Adaptable to site conditions
• Safe and efficient to operate
• Versatile attachment range
• Ongoing maintenance and support
• Robust product warranty
COLLABORATION WITH ITS CLIENTS HAS SEEN TRADESALES RELOCATABLE SITE SOLUTIONS BE USED ON MAJOR MINE SITES ACROSS AUSTRALIA FOR YEARS.
In July 2018, a Chilean copper miner struck a 10-year deal with national utility Colbún to provide 550 gigawatt hours of electricity from renewable sources from July 2020.
The deal made the copper mine the first in the Chile to operate on 100 per cent renewable energy.
Closer to home, a major gold mine in Western Australia is working with a key mobile and modular power company to build one of the world’s largest renewable energy microgrids.
The mine will be powered by 20,000 solar panels and backed up by a two megawatt battery system. These devices will be integrated into a natural gas-fuelled generator.
In September 2024, a major iron ore miner announced its climate transition
plan, outlining comprehensive details of how it plans to eliminate fossil fuels from its Australian operations by 2030 using a number of measures, including solar energy.
“While renewables at mine sites are not a new thing, their rollout is investment-intensive and not easy to access should a project enter a new area or if the company needs to rapidly increase the number of facilities,” Tradesales national sales manager Jay McEwen told Safe to Work
“Our relocatable off-grid site offices, crib rooms and toilet blocks help to fill the gap between companies’ renewable ambitions and functionality by allowing them into remote areas without the
need to be connected to the grid –renewable or otherwise.”
Tradesales has been building relocatable site solutions, also known as modified containers, for the mining sector for over a decade. They are now used by Australia’s mining majors, contracting companies and original equipment manufacturers alike.
“We pride ourselves on innovation and we’re always looking to push the boundaries on what we can offer our partners,” McEwen said. “Collaboration with our clients led to the development of the Hydration Station, the Lubestation and numerous other relocatable infrastructure.
“While our modified containers all vary in design and purpose, the thing they all have in common is that they
different area when needed.
“With options like renewable power, battery back-up and water tanks, our range of off-grid solar containers takes this benefit to the next level.”
Mining in Australia can be hot and hard work.
“Off-grid site offices and crib rooms not only act as a central hub for managing activities but also provide a much-needed respite from the elements,” McEwen said.
“The site offices and crib rooms come with powerful air-conditioning, power and inverters to charge appliances and computers, and kitchenettes with wastewater tanks.”
While cool air-conditioning may have once been viewed as optional, WA’s Occupational Safety and Health Act 1984 now requires employers to provide and maintain an environment in which workers are not exposed to hazards. This applies to any safety and health risk, including illness from working in the heat.
Tradesales’ off-grid solutions are used by operators and contractors for exploration work and the construction
of new areas of a site where existing power and water infrastructure may not be available. They are also used when staff numbers are greatly increased for a limited time, such as during a shutdown.
“Shutdowns require companies to rapidly increase the number of people on-site,” McEwen said. “Relocatable off-grid options allow companies to add and remove extra facilities seamlessly.”
Tradesales’ most recent addition to the lineup is the off-grid toilet block.
“In a remote environment such as in mining, traditional toilet blocks come with several challenges – access to power and water, connection to sewerage,” McEwen said.
“Our offering solves these challenges with solar power and an in-built water tank, all sitting on top of a sewerage tank.”
The Tradesales offgrid toilet block features five individual unisex toilet cubicles each with its own external door. Vinyl floor throughout the toilet block allows for easy maintenance and all electrical work is completed to a mine-spec.
In addition, in-built water and sewerage tanks are easily accessible for emptying, refill and upkeep.
“Tradesales has been manufacturing bespoke storage and workplace solutions for the mining industry for over three decades,” McEwen said.
“Due to this experience and our local manufacturing capability, we provide predictable upfront costs, precise timelines, and minimal impact on our client’s operation.”
Tradesales can also out-fit other relocatable site solutions with solar power to help solve numerous energy challenges that
THE AUSTRALIAN WORKING AT HEIGHT ASSOCIATION WANTS TO SEE THE INCREASING RATES OF HEIGHTRELATED INJURIES AND FATALITIES SLASHED.
According to data from the latest Safe Work Australia Work Health and Safety Statistics Australia 2024 report, falling from a height was the second-largest contributor to workplace fatalities in 2023, increasing 71 per cent on the previous year and 32 per cent on the five-year average.
Working at Height Association (WAHA) chief executive officer Scott Barber wants the issue tackled differently to truly see positive changes in these numbers.
“The increasing statistics have been stubbornly consistent,” Barber told Safe to Work. “We need to use all the resources we have at our disposal, including introducing innovation, technologies and learning development, to bring greater safety to every industry.
“If we want to see a change in these numbers, we need to change our approach.”
The WAHA was established in 2009 in response to demand for a peak body to provide information, guidance and support for businesses that need to address working at height issues.
Working at height come with an entirely different set of risks and considerations to keep people safe, which requires an industry presence with the tools to educate workers and operators alike.
The WAHA aims to represent those working at height while bringing industry together with safety professionals and experts who can speak with authority on height-related best practice and misconceptions across industries.
Even the nature of working at height, according to Barber, can be misunderstood.
“It’s not just working environments high up in the air,” he said. “A fall from height refers to falling from one level to another, which can also mean from ground-level down.
“It’s especially applicable to underground work where there’s any kind of void or where you’re working above a false environment.”
Barber spent years in the mining sector working with corporate and site safety and emergency response. He said falls are a pervasive threat encountered in the industry.
“The mining industry tends to address it really well in terms of applying those higher order controls, but when you’re doing shutdown maintenance and construction, the exposures are there,” he said. “You might be dealing with a contractor base where you don’t necessarily have a clear line of sight around their experience and competency,
Addressing the hierarchy of controls is key to keeping workers safe.
which opens up a whole new range of exposures.”
When it comes to increasing worker safety on site, Barber emphasised the most effective measures come from higher up in the controls, rather than better quality harnesses or administration.
“Understanding how the hierarchy of controls is applied is essential,” he said. “If we can actually look at where people are accessing and why, we can look at engineering out those risks
in the initial design phase of new or upgrading projects, so people don’t have to go to those areas or, if they do, they are easily accessible.”
With artificial intelligence (AI) and hazard avoidance technologies becoming more advanced and accessible, keeping workers safe on mine sites digitally has never been more obtainable.
But as much as these technologies may be leading the industry towards a safer future, Barber said there are still considerations to be confronted.
“We’re looking at addressing those competency areas where we have gaps in knowledge,” he said. “Though training may be rigorous, there’s no guarantee the trainee is coming out with skills that are actually relevant to the work they’re going to be doing.
“That’s why the WAHA has developed a learning tool for operations and registered training organisations to ensure that what is being delivered in the theory and practical assessments is clearly understood and workers have
confidence and genuine competency to operate safely in falls environments.”
Barber described the tool as putting trainees on a “personal learning pathway” to competency rather than a “generic learning journey”.
“Our aim is to have a workforce that is operating at a consistently high level, with a clear understanding of the risk and the systems in place to address it within a hierarchy of controls,” he said.
“The learning tool uses an AIbased algorithm that takes 20 points of data a minute to work with users to direct their learning by highlighting gaps in knowledge and addressing that directly. It’s the unconscious incompetency, where you think you know but you’re wrong, which is a key area of concern, and this is what the platform directly addresses.”
A workforce empowered to make better decisions ultimately leads to better outcomes, and the WAHA is determined to put as much knowledge in the hands of workers as possible.
“An empowered workforce also has the confidence to speak up if they see
something that doesn’t look quite right,” Barber said. “They have the language, understanding of the fundamentals and the competence to question existing methodologies and even find a better way of doing the work.”
Ultimately, Barber said collaboration is key.
“I’ve got over 20 years of experience in this space, but I certainly don’t have all the answers,” he said. “Our work with different industry groups and trade associations is critical for us to understand where the gaps are so we can work with those industries to actually find and address issues.
“That helps us design and evolve education and campaign programs to effectively educate people and provide them with resources that they can take into the workplace.
“The latest statistics show there is something missing in our current approach, but we have an opportunity to work with individuals to empower them to make better decisions and make working from height safer for everyone and contribute to a more effective and engaging safety culture.”
THE NAVIGATOR X EYEWEAR RANGE IS KEEPING WORKERS PROTECTED WITHOUT COMPROMISING COMFORT OR STYLE.
Miners face all number of potential hazards on the job, and no matter the situation, eye protection is almost always a must in the roughand-tumble resources sector.
But in the world of personal protective equipment (PPE), eyewear isn’t always comfortable – and it certainly isn’t always stylish.
In recognising the need for eyewear that guarantees safety without compromising comfort or appearance, Safety Mate decided it was time to take Australia’s safety eyewear offering to the next level.
With 20 years of safety experience and a partnership with Riley Eyewear, which itself brings more than 30 years of manufacturing might, Safety Mate is on a mission to push the boundaries of what safety eyewear can be.
After a year working together in research and development, perfecting every detail to meet the highest safety standards, the Navigator X safety eyewear range was born.
Designed with comfort, protection and performance in mind, the Navigator X features first-to-market high-definition (HD) lenses that help improve clarity and contrast while
heightening colours and relaxing the eye.
This is especially important given the challenges of shift-work and constant noise on site. Fatigue is a hazard Safety Mate is determined to reduce with the Navigator X’s ability to take the pressure off busy eyes.
Each pair of Navigator X glasses has also been designed to withstand extreme temperatures and working conditions.
Utilising Riley Eyewear’s cuttingedge FlowTEC technology, Navigator X safety glasses have dual lens coating that is bonded and cured for the life of the product, providing resistance to moisture, scratching and fogging.
Renowned for being flexible, lightweight and adjustable, the Navigator X range is available in seven different lenses: HD, clear,
polarised, grey, LED, emerald revo, and arctic blue revo.
Revo lenses have a reflective coating on their surface and, similar to polarised lenses, reduce the glare of intense sunlight.
The blue-light-blocking lenses from the LED Navigator X glasses aim to improve contrast and reduce eye stress. With a soothing light-brown tint, the glasses significantly lower LED and fluorescent lighting glare, keeping eyes relaxed and focused.
Those with impaired sight will also soon be able to access any pair within the range, with prescription availability in the works.
The FlowTEC coating offers 100 per cent UVA and UVB protection, with each lens engineered to filter some of the highest-energy wavelengths of visible light up to 400 nanometres. This means whether taking a clear pair underground, or sliding on a set with a grey, emerald, or arctic blue finish in
the harsh Australian sun, workers can be confident they are protected from light and debris.
Featuring rubberised, nonslip nosepiece and side-arm tips, Navigator X eyewear removes discomfort to pressure points on the head and face so workers can wear
them for prolonged periods without constant adjustments.
Given mine sites are dynamic places with multi-tonne equipment roving about and constant sensory input, workers need to bring their A-game to every shift to stay safe.
That’s why the Navigator X range features a transparent frame for increased peripheral visibility and a fixed transparent side shield that reduces risk to the wearer from side impacts.
Each pair of Navigator X glasses has been manufactured from ethically sourced bio-based materials, reducing carbon emissions during the manufacturing process and comply with the world’s top three major safety eyewear standards: AS/NZS, EN166, and ANSI Z87.1.
Backed by world-class manufacturing, zero compromise on safety or attention to detail, Navigator X glasses are hitting the trifecta of safety, performance and looks.
SAFE TO WORK SAT DOWN WITH THE AUSTRALIAN INSTITUTE OF OCCUPATIONAL HYGIENISTS TO DISCUSS WHAT CAN BE DONE TO PROTECT WORKERS AGAINST THE THREAT OF SILICA EXPOSURE.
A2022 study from Curtin University estimated that more than half a million Australian workers are currently exposed to silica dust across various industries including mining, quarrying and construction.
The study’s modelling predicts more than 10,000 Australians will develop lung cancer and up to 103,000 workers will be diagnosed with silicosis as the result of their current exposure to silica dust at work.
The Australian Institute of Occupational Hygienists (AIOH) is a non-profit organisation whose members have been assessing the exposure of Australian workers to respiratory hazards for over 40 years.
Occupational hygienists, also called industrial hygienists, are health and safety experts who specialise in the assessment of these workplace exposures and how to combat them.
AIOH members are specially trained to measure silica in the air that workers breathe, interpret the results and advise if the air is safe or not.
“On any given day on mine sites all across the country, AIOH members are there talking to drillers, operators, drivers and the many men and women who work in mining about silica dust,” AIOH immediate past president Tracey Bence told Safe to Work.
“We do this because the AIOH mission is a healthy working environment for all and our purpose is to prevent dust diseases.
AIOH immediate past president Tracey Bence.
“We have known of the dangers of silica for over 500 years and yet silicosis remains incurable.
“The only responsible response to this danger is prevention of
exposure to silica dust at the source and that is what motivates me as a mining hygienist.”
Safe Work Australia sets out the current Workplace Exposure Standards (WES) for the various types of crystalline silica, such as quartz.
Mining-specific regulations have been in place for decades and require mine operators to reduce exposures to silica-containing dust which can be released by drilling, blasting, crushing, processing and transferring rock, ore and mineral concentrates.
From September 1, new work health and safety (WHS) regulations have taken this a step further requiring all workplaces not covered by mining regulations to also protect workers by these controls:
• Isolation from the dust
• Enclosed operator cabins with a high efficiency air filtration
• Wet dust suppression
• On -tool extraction
• Local exhaust ventilation
The WES for quartz – the most common type of silica – is currently 50 micrograms per metre cubed (µg/ m3) of air.
“This amount sounds microscopic but we know that over time it may not be protective enough for miners, tunnellers and all those who work with silica containing materials,” Bence said. “A reduction of the airborne silica WES is expected in 2026.
“Even before any change to the legal limit, all workplaces have a duty to reduce dust levels so far as is reasonably practicable and protect their people from irreversible harm from silica-related diseases such as silicosis, lung cancer and rheumatoid arthritis.”
The AIOH has a dedicated toolkit to help workplaces combat silica exposure. This includes the Breathe Freely Australia website, which was launched in 2019 when diagnoses of rapid onset or accelerated silicosis in engineered stone workers began emerging in Queensland.
Not just focused on silica exposure, Breathe Freely has resources on welding fume, asbestos and other
lung-disease-causing materials. The AIOH provides these free tools and training materials to help workers and employers in mining, quarrying, construction, tunnelling, welding and stone fabrication.
Another approach the AIOH has taken to empower employees to protect their workers is its RESPFIT national respirator protective equipment fit-testing training and accreditation program.
“The whole purpose of RESP-FIT is to assure the competency of the people who perform fit tests so that workers who have to wear respirators can be confident they fit properly to protect them,” Bence said. “But at the AIOH, we are still working hard to get the dust-prevention message out to workplaces: it is not okay to rely solely on respirators to protect us from breathing in silica particles at work.”
This determination led to the creation of the AIOH’s latest line of defence against silicosis, the Silica Resource Hub.
The point of the Silica Hub, Bence said, is to impart the expertise of hygienists to workplaces that might not otherwise be available.
“You can think of the silica hub as the place where occupational hygienists want you to get advice from the ‘people in the know’,” she said.
“We have straightforward and free advice on getting your silica materials tested, when you might need air monitoring, what tasks could lead to over exposure to silica and what dust controls work in the ‘real world’.
“Breathe Freely Australia and the Silica Hub will raise your awareness of this microscopic, fine and mostly invisible dust and what to do to prevent being exposed.
“With crystalline silica being in so many common natural and man-made materials, AIOH wants you to tell all colleagues, kids and tradespeople about a future free of silicosis.
“These are also great training resources for work, health and safety representatives, safety professionals, supervisors, even home renovators and those who ask others to handle crystalline-silicacontaining substances.
“The mining sector has come a long way in protecting its workers from exposure to silicosis, and the recent ban on engineered stone and amendments to the WHS regulations will save lives, but I can see there is still more preventive work to be done.”
With silica awareness provided by the AIOH, Australian industries are another step closer to a future free from silicosis.
MARTIN ENGINEERING EXPLORES HOW A COMBINATION OF PREVENTIVE AND PREDICTIVE MAINTENANCE MAY BE THE BEST APPROACH TO KEEP OPERATIONS RUNNING SMOOTHLY.
Effective upkeep of hightonnage conveyor systems is critical to maintaining production and profitability.
Maintenance repair and operations professionals need a comprehensive plan with a foundation built on workplace safety.
Formulating such a strategy requires an understanding of the advantages and disadvantages of reactive maintenance, preventive maintenance and predictive maintenance. Key to this is establishing goals that include minimising unscheduled downtime, improving safety, raising efficiency and reducing the overall cost of operation to achieve a better return on investment (ROI).
Even today, many companies practice what can be called reactive maintenance on their conveyors, meaning they simply fix whatever breaks.
Components are left to run until they fail and the resulting system downtime is unscheduled, disruptive and expensive.
Among the contributors to the costs of this approach are unplanned production stoppages, ancillary equipment damage (when a broken component damages something else), overtime and emergency service fees.
Other disadvantages include shorter asset life expectancy, since components are not maintained in optimal running condition, as well as uncontrolled budgets and potential safety hazards.
Additionally, technicians tend to take more risks and make more mistakes when under pressure to restore operations in the shortest possible timeframe.
Despite the clear downside of a predominantly reactive maintenance strategy, it’s been estimated that half of all conveyor maintenance activities in the average US facility follow this approach.
One reason this may occur comes down to budget – reactive
maintenance requires less staff, less planning and a lower initial investment. But such a strategy can lead to ineffective planning, insufficient oversight and far less system control.
The deficiencies of reactive maintenance have driven an evolution to a more preventive approach to minimise failures that force unplanned shutdowns for repairs. Guidelines are typically based on time in service or operating hours.
It’s the same approach that consumers use when they take their car in for scheduled oil changes to extend engine life.
Preventive maintenance prolongs component life, increases productivity, improves overall efficiency and reduces maintenance costs.
Bulk handling equipment endures ongoing punishment by transporting millions of tonnes of rock, aggregate and sand in fluctuating weather conditions, potentially creating dust emissions, spillage and carryback
maintenance schedule requires strict adherence and consistent updating.
Some firms take this responsibility in-house, but others find specialist service providers can deliver a better return on their maintenance investment. This can allow them to rely on the expertise of industry experts so their employees can focus on core activities.
Generally triggered by time, metered inspection or common indicators like mistracking and spillage, the preventive maintenance approach to conveyor maintenance assumes that each component has a typical equipment life based on previous similar applications and environments.
Using observation and experience, preventive maintenance determines when relevant parts should be retired, replaced or refurbished, before the expected failure point.
The result can often mean greater safety, higher system efficiency, reduced spillage and better overall system control.
Predictive maintenance directly monitors equipment performance during normal operation with the aim of more accurately anticipating failure.
Relying on sensors and supported by software, information is collected over time and facts are aggregated and fed into an algorithm to deliver a
to stakeholders.
When combined with regular physical inspections, this type of datadriven system can provide far more complete, accurate and actionable information for service technicians and operations personnel.
Some component manufacturers offer structured conveyor inspections and belt cleaner maintenance as part of a managed service relationship.
Their monitoring systems can track component wear and update the service technician and operations team via Wi-Fi or cell phone on upcoming service needs.
The technology will also send an alert through a mobile app in the event of upset conditions, allowing service technicians and plant operators to access real-time data. Emerging systems can even adjust belt cleaner tension automatically.
Highly trained service technicians provide an added set of eyes on the conveyors, travelling to and from the equipment to be serviced and logging details in their reports.
Because technicians see so many different applications, they can often alert operators to problems that general maintenance personnel may overlook or have become accustomed to ignoring.
With factory-direct managed service, the responsibility for maintenance falls on the provider, allowing the staff to focus on other priorities.
Unlike preventive maintenance that is determined by an average or expected life statistic, predictive maintenance is based on the actual condition of the equipment.
Sometimes called ‘conditionbased maintenance’, when predictive analysis identifies a potential issue, the repair can be scheduled at a time that minimises the impact on production.
The benefits of this approach can include further optimised system performance and component life, a reduced need for visual inspection and minimised guesswork through a more automated, analytics-based system. Although it doesn’t fully eliminate the need for personal inspections and maintenance, for conveyor systems that can be miles long and, in some cases, cover difficult terrain, the approach saves time and reduces potential hazards.
A predictive maintenance program starts with data collection and storage, and then proceeds to analysis.
In the past, adding new points of measurement could be a time-consuming and expensive undertaking, but wireless instruments have greatly reduced these costs.
With more readily available data collection, storage and analytics options, some bulk material handlers are recognising that each critical component can and should be monitored and analysed to optimise performance.
Sensors can also feed data to cloudbased software which then broadcasts to mobile applications in the field.
The initial capital expenditure for these systems may appear steep, but cloud-based technology can defray some of the cost of entry.
The potential benefits of extended equipment life, tighter budget forecasting, more reliable maintenance scheduling, increased worker efficiency, decreased downtime and better productivity can all add to a swift ROI.
Unlike preventive maintenance, which relies on wear life determined by manufacturer or operator observations, machine learning can adapt maintenance needs to a specific operation and service environment, fuelled by all previous input.
The benefit can be a tailored experience where equipment seemingly communicates its needs directly to decision-makers.
A recently commercialised example is a belt cleaner position indicator that monitors the blade and tracking and reports its remaining service life.
The device continuously gathers data on primary belt cleaners, notifying factory-trained service technicians and plant operations personnel when retensioning or replacement is required or when abnormal conditions occur.
Managers and service technicians can quickly access information on any networked cleaner via phone or Wi-Fi.
The device delivers critical realtime intelligence and aims to reduce worker exposure to moving conveyors, improving efficiency and safety.
Maintenance planning can be simplified by having detailed information available on demand, allowing service personnel to deliver and install replacement wear parts during scheduled outages.
Relying on actual operating conditions instead of human judgement to monitor blade wear and tension for optimal cleaning performance, the indicator can maximise the blade’s usable surface area and report when a blade is nearing the end of its useful life.
A belt cleaner position indicator that monitors the blade and tracking and reports its remaining service life.
Taking the technology a step further are sensors that constantly monitor blade pressure and inform stakeholders of their status of wear, meaning maintenance personnel no longer need to visit each cleaner and manually re-tension.
This reduces maintenance time while maximising the usable area of every cleaner and takes the concept of preventive maintenance to another level.
Rather than optimising for a process parameter or other metric, the approach can make real-time profitability the priority outcome.
Predictive maintenance has many advantages over preventive maintenance, but in the past, it was often too expensive or impractical to implement this strategy on all but the most critical components.
Now that data collection, storage and analysis is becoming easier and less expensive, additional components and systems are likely to become part of a plant’s conveyor maintenance program.
Bulk material handling systems working in harsh operating environments can experience unexpected failure events that are often difficult to predict when they are caused by random,
abnormal overloads or human error. Maintenance staff need to have some capacity to react to sudden failures.
During unscheduled downtime, managed service providers can take advantage of the outage to maintain or upgrade equipment.
Some service providers are also taking steps to help customers whose facilities have limited access. By partnering with their maintenance staff, service providers can remotely train employees to effectively maintain their conveyor systems, and offer guidelines on preventive maintenance, inspections and replacement blade options.
During this process, factory-direct technicians remain in close contact with periodic check-ins and operate within key parameters with the aim of assuring optimum performance.
With the goal of an efficient and cost-effective maintenance schedule, human labour will always be needed to design and carry out solutions, just like data will always rely on human experience to be properly applied.
That’s why leveraging the benefits of both preventive and predictive maintenance is often the best approach.
Given unscheduled downtime, prematurely degraded wear parts and unnecessary labour can have such a serious impact on the cost of operation, applying each method to a maintenance strategy can maximise the effectiveness of both.
The Queensland Government is funding projects that will generate jobs within a matter of months.
THE MOUNT ISA MINING CORRIDOR IN QUEENSLAND IS SET TO WELCOME THOUSANDS OF NEW MINING JOBS.
Mount Isa is a crown jewel of Queensland’s North West Mineral Province, an area touted to be one of the world’s most mineral-rich regions.
As home to some of the largest copper mining and smelting operations in Australia, Mount Isa has long been a major resources employer. And a new initiative was announced by the Queensland Government in late July is set to bring even more jobs to the region.
Under the new $30 million Mount Isa Mining Acceleration Program, mining projects in the North West Minerals Province that have the potential to generate local jobs within a matter of months are being expedited.
The acceleration program funding will be allocated to three projects:
• H armony Gold’s Eva copper project – $20.7 million
• N orth West Phosphate’s Paradise South phosphate mine –$5.77 million
• Vecco Group’s Vecco critical minerals project – $2.33 million Upon completion, the mines are expected to generate almost 1000 long-term mining jobs, with a peak early works and construction workforce expected to tip 1600 jobs.
“These investments will help unlock opportunities months and years sooner,” Queensland Deputy Premier, Treasurer and Minister for Trade and Investment Cameron Dick said at the time.
“The government has selected these projects to support the people of Mount Isa by providing jobs sooner and diversifying industries and skills across the region.”
EVA COPPER PROJECT
Harmony’s Eva mine, boasting a minimum mine life of 15 years, is expected to be one of the largest copper mines in Queensland. The project will generate approximately 800 construction jobs and create 450 permanent jobs when in operation.
Harmony chief executive officer Peter Steenkamp said the grant was an important contribution to the Eva project’s progress.
“We are thankful to the people and the Queensland Government for this grant, and we reaffirm our commitment to developing the Eva copper mine project in a way that is sustainable and maximises local economic benefits and jobs,” Steenkamp said.
Harmony’s $20.7 million has been earmarked for preparatory works, including building site access
roads, constructing accommodation facilities, fencing, and associated services and infrastructure.
The proposed Paradise South opencut mine has a forecast resource of two million tonnes of phosphate ore per year, with an initial life of at least 20 years.
The mine will include an on-site processing plant to produce phosphate concentrate ready for market.
The mine will generate 74 immediate jobs, with 492 construction jobs and 245 mining operations jobs created by 2026 and, thanks to the funding boost from the Queensland Government, construction is expected to commence within the next year.
Located near Julia Creek, the proposed Vecco critical minerals project will mine vanadium and highpurity alumina, crucial critical minerals that will also support downstream battery production in Townsville.
Once up and running, the project is expected to generate 8000 tonnes per annum (tpa) of vanadium, 4000tpa of high-purity alumina and 600tpa of molybdenum over an initial 17 years.
The Vecco mine will engage 274 operational workers from 2026, while construction starting this year which will generate 300 jobs.
and Critical Minerals Scott Stewart said the North West Minerals Province
Image: Peruphotart/shutterstock.com
More than 2500 jobs are expected to be created between the projects.
has the potential to generate more than $500 billion in returns.
“Queensland’s North West Minerals Province has an abundance of critical minerals that can support Australia’s transition to a clean energy future,” Stewart said when the program was announced.
“This acceleration fund will help get
THE 2024 AUSTRALIAN MINING PROSPECT AWARDS WAS A NIGHT OF CELEBRATION, RECOGNITION AND CONNECTION FOR THE BEST AND BRIGHTEST THE MINING SECTOR HAS TO OFFER.
For more than a decade, the Australian Mining Prospect Awards have recognised those who go above and beyond in the mining industry – and the 2024 iteration, held in Perth on October 9, was no exception.
This year’s Prospect Awards were announced from a new home as part of the WA Mining Conference and Exhibition (WA Mining).
As the only national awards program to examine the mining industry and reward those who are excelling and going above and beyond, it’s fitting that the Prospect Awards took to the stage in WA, where innovation abounds.
Show director Siobhan Rocks was delighted that the 2024 Prospect Awards were held in WA.
“Partnering with sponsors and a world-class judging panel, these prestigious awards recognise leadership across the industry,” Rocks said.
“It is a night celebrating excellence and ingenuity that cannot be missed.”
This year promised to be bigger and better than ever before, with some of the most well-known miners, original equipment manufacturers and innovators across the industry nominated as the best in their class.
Industry association Austmine has been involved with the Prospect Awards since 2017 and returned as the sponsor for the Innovative Mining Solution award at this year’s event.
“Our mission is to advocate and champion the advancement of mining technology and innovation, and this award in particular aligns with our overall mission,” Austmine director marketing, membership and events
it, then you go unnoticed. Stopping, pausing, recognising and rewarding people accordingly is an important thing, and we love being part of the Prospect Awards.”
There were 11 prestigious awards presented on the night, including Excellence in Mine Safety, OH&S, Innovative Mining Solution, and Excellence in Environmental Management and Sustainability.
Winner: Roy Hill
The Excellence in Mine Safety, OH&S award recognises a mine, company or project that has developed or carried out a program that increases safety, removes risk or cuts worker issues.
Roy Hill’s Safer Summer program was the worthy winner of this category. The program was focused on leveraging knowledge-sharing to enhance safety awareness and practices during the high-risk summer period.
This included supporting leadership and bringing awareness to hazard control and the dangers of thermal stress and distractions. Through a targeted and incentivised approach, Roy Hill managed to ensure teams remained focused on the most relevant hazards.
The campaign incorporated monthly focus topics in addition to a competition element, the ‘we care team safety challenge’, which provided an interactive mechanism to encourage teams to share hazard control initiatives.
The decision to reward teams who excelled in the campaign’s focus areas with charitable donations also introduced a unique motivational driver.
Teams that adopted the focus areas of the Safer Summer campaign and
proactively implemented and shared hazard controls were eligible for one of five $5000 prizes to donate to a charity of their choice.
By emphasising teamwork and a collective responsibility to implement and share controls across the business, Roy Hill was able to give participants a deeper sense of purpose and achievement.
The Safer Summer program also included a variety of educational activities and resources such as workshops, training, safety shares, and the innovative use of emerging platforms for sharing new hazard controls.
The diversity of available resources aimed to ensure teams were well-informed about the campaign, with key messages reinforced through continuous learning and acknowledgement of team achievements.
This included significant engagement by the Roy Hill executive team, operational general managers and other senior leaders.
The legacy of the Safer Summer campaign has resulted in a more active hazard control sharing culture at Roy Hill, with teams consistently sharing new hazard controls in meetings and online via the company’s new Hazard Control Shares Viva Engage channel.
Teams are continuously encouraged to share their initiations via this channel, as well as provide feedback or ask questions of their colleagues.
Roy Hill’s chief executive officer and chief operating officer were regular contributors to the Safer Summer Viva channel, posting updates and commenting on posts to drive engagement with the frontline.
The campaign has also enhanced a culture of continuous improvement, with teams actively implementing new controls to help reduce risk.
A triumph on all fronts, the Safer Summer campaign has successfully reduced recordable injuries by 36 per cent compared to the previous summer season.
According to Roy Hill, the campaign’s focus on teamwork, seasonal relevance, engagement, education, effort recognition and ongoing improvement was a key factor in its success.
“The award reflects the ingenuity of our people and a collective commitment to creating a safe and healthy work environment,” Roy Hill said in a LinkedIn post celebrating the win.
“As Frankie Valli and The Four Seasons so eloquently put (it): ‘Oh, what a night’.”
AND COMMUNITY ENGAGEMENT AWARD
(SPONSORED BY SANDVIK)
Winner: Buru Rehab
Recognising collaboration between an Aboriginal-owned business or a community organisation, and mining and minerals processing companies operating within Australia, Buru Rehab was the worthy winner of this award.
Through a partnership with Mineral Resources (MinRes), Buru Rehab was entrusted with a five-year contract to manage road maintenance and civil works at MinRes’ Wodgina lithium mine in Western Australia.
Winner: IGO Limited
Celebrating a significant discovery at either a greenfields or brownfields site, the Discovery of the Year award went home with IGO for the rare mineralisation discovery it made at its Dogleg nickel-copper-cobalt prospect in Western Australia in 2023, potentially leading to multiple new nickel mines in the region.
EXCELLENCE IN ENVIRONMENTAL MANAGEMENT AND SUSTAINABILITY (SPONSORED BY SEFAR)
Attendees were in the presence of some of the Australian mining sector’s best and brightest.
minerals processing operations, Orica Digital Solutions took home this award for its BlastIQ Underground, which provides quality control and improved drill and blast productivity for superior blast outcomes, enabling underground operators to efficiently manage their blasting processing from planning to post-blast analysis.
INNOVATIVE MINING SOLUTION (SPONSORED BY AUSTMINE)
underground coal mine, which saw coal production achieved in March 2023, enabling the mine to meet its first coal train milestone.
PROJECT LEAD OF THE YEAR (SPONSORED BY REGAL REXNORD)
Winner: Claude Mocellin, South32
Winner: BHP West Musgrave project
The Excellence in Environmental Management and Sustainability award recognises a mine that has developed a pioneering program to protect, preserve and/or rehabilitate the natural environment.
BHP’s West Musgrave project in Western Australia took home the award thanks to its land access and disturbance permit (LADP) system. The LADP system facilitates engagement with the Ngaanyatjarra community, the Traditional Owners of the land.
EXCELLENCE IN IIOT APPLICATION (SPONSORED BY IFM)
Winner: Orica Digital Solutions
Recognising an outstanding implementation of Industrial Internet of Things (IIoT) that enhances mining and
Winner: IPI Australia
This award recognises a unique mining solution. IPI Australia took home the prize for its shaft alignment system (SAS) to address common conveyor challenges.
Intended to be a permanent fixture to pulley bearing housings, IPI’s SAS safeguards correct factory seal alignment and eliminate the need for seal adjustment when a pulley is landed on a conveyor structure.
Winner: Robson Civil Projects
Recognising a significant engineering and/or contract mining project that has been undertaken on a mine site, Robson Civil Projects took home this award for the Maxwell underground project at the Muswellbrook
Awarded to an individual who has led a project or mine site to a successful outcome, the Project Lead of the Year category at this year’s Prospect Awards celebrated Claude Mocellin for his leadership in South32’s Dendrobium Area 3C expansion project.
Under Mocellin’s multi-year leadership, the team conducted mock emergency evacuations and rewarded strong safety behaviour, contributing to a program that experienced zero recordable injuries.
AUSTRALIAN MINE OF THE YEAR (SPONSORED BY BONFIGLIOLI)
Winner: Roy Hill
OUTSTANDING MINE PERFORMANCE (SPONSORED BY SEW-EURODRIVE)
Winner: Mineral Resources for its Wodgina and Mt Marion lithium mines
AIMEX PROVIDES AN UNMATCHED OPPORTUNITY TO CONNECT AND DO BUSINESS WITH LEADING MINING SUPPLIERS FROM AROUND THE WORLD.
The ultimate platform for seamless connectivity,
data insights, and optimised underground operations.
HELIX is transforming the mining industry with advanced digital solutions. By seamlessly connecting all aspects of your underground operations, HELIX empowers you with real-time insights to make smarter, faster decisions.
Gain instant access to critical data across your mine. HELIX delivers powerful analytics, enabling you to monitor performance, track assets, and ensure safety with precision and accuracy.
With HELIX, optimise your productivity while enhancing safety. Its robust platform integrates seamlessly with existing systems, reducing downtime and streamlining operations for a higher return on investment.
Built for scalability, HELIX adapts to your needs as your operations grow. Experience the power of a flexible, future-ready platform designed to support the next generation of mining technology.
We specialise in mining and tunneling technology that empowers you to unearth safety and productivity improvements. Over the last 30 years we have consistently delivered innovative solutions that not only address the needs of our customers today, but also their future needs.