
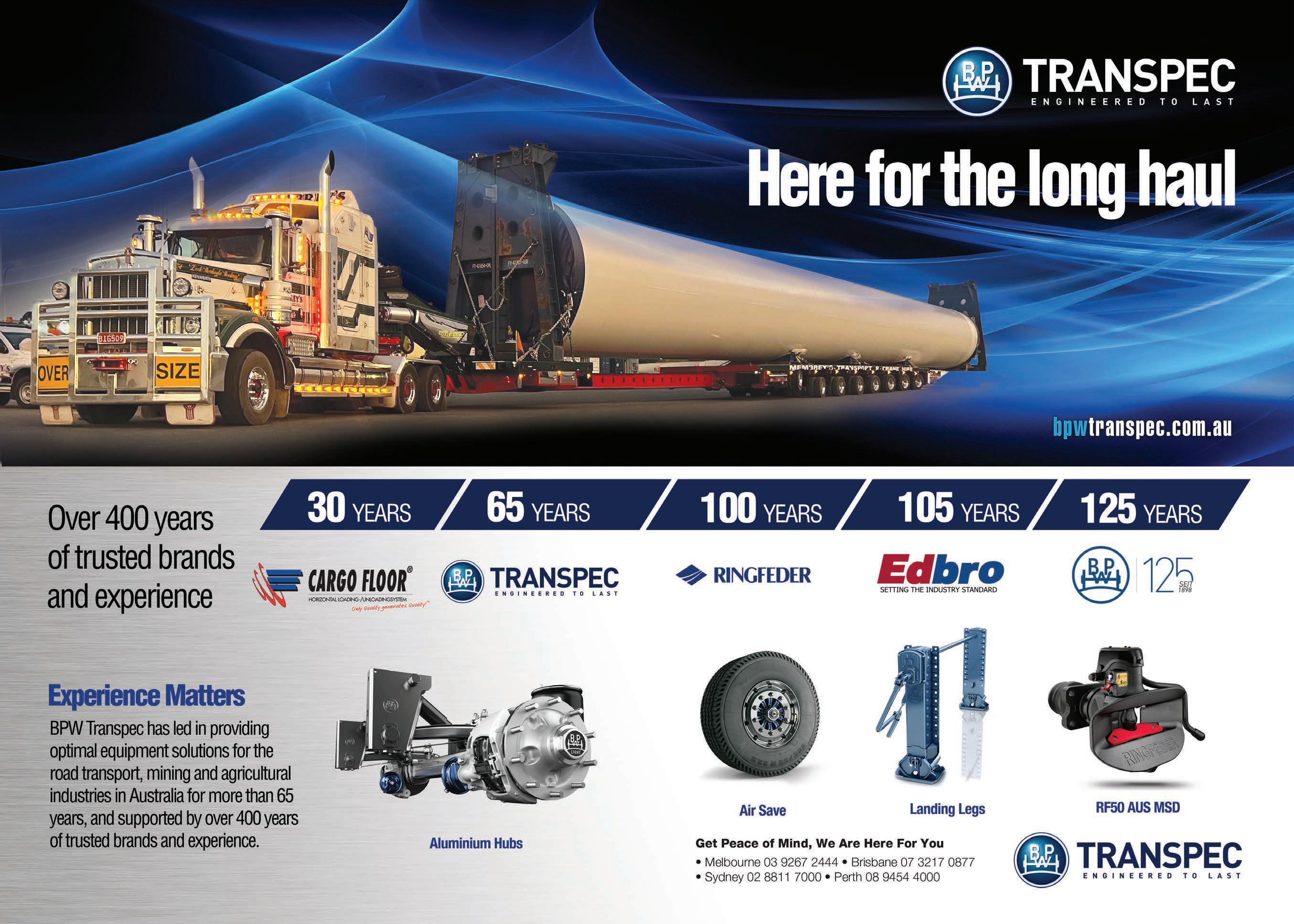
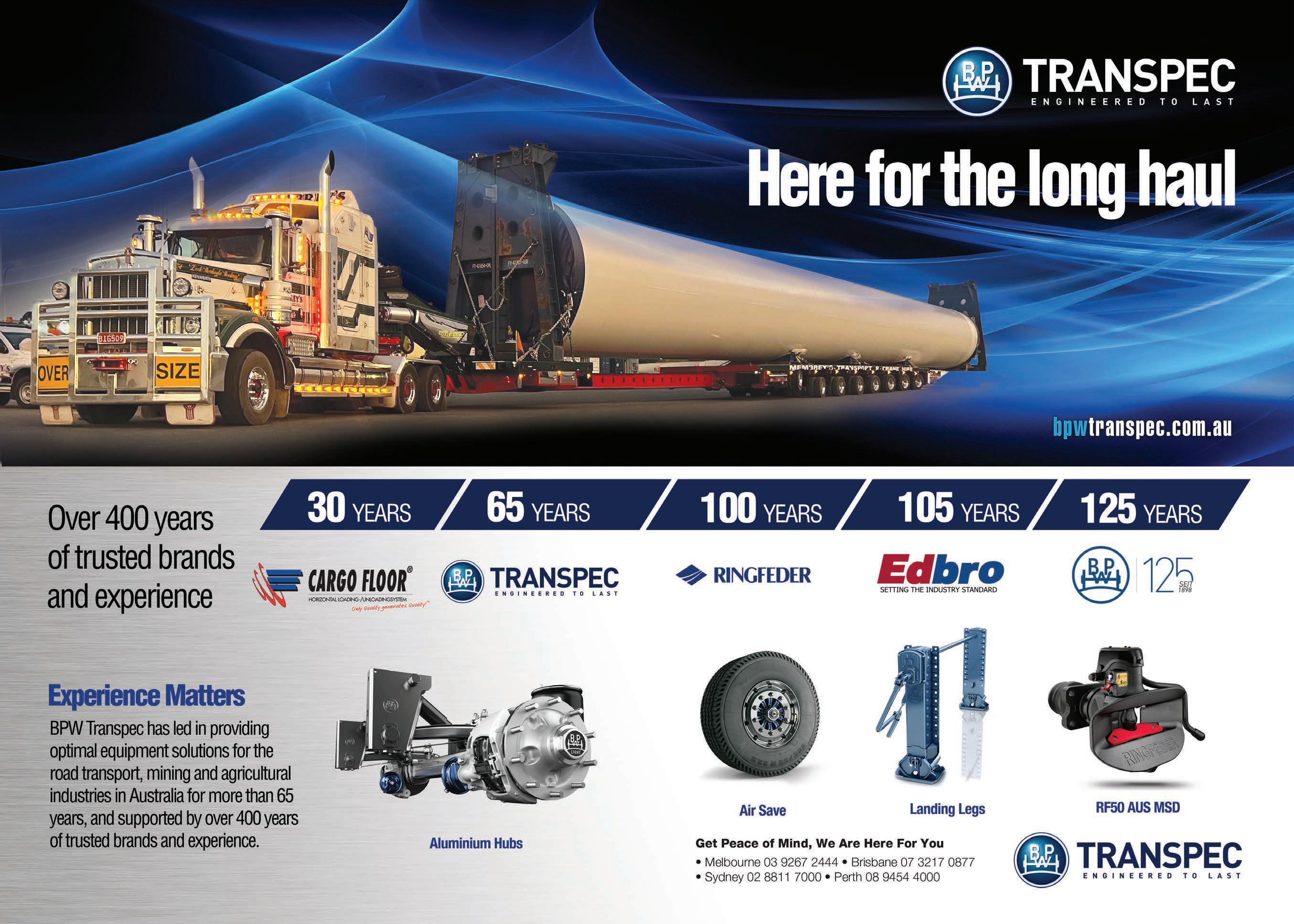
PUBLISHER
John Murphy john.murphy@primecreative.com.au
MANAGING EDITOR
Luke Applebee luke.applebee@primecreative.com.au
EDITOR
Peter White peter.white@primecreative.com.au
JOURNALIST
Sean Gustini sean.gustini@primecreative.com.au
CONTRIBUTOR
William Craske william.craske@primecreative.com.au
ADVERTISING
Con Zarocostas: 0422 222 822 conzarocostas@primecreative.com.au
Ashley Blachford: 0425 699 819 ashley.blachford@primecreative.com.au
DESIGN
Daz Woolley/Alejandro Molano
ART DIRECTOR Blake Storey
CLIENT SUCCESS MANAGER
Salma Kennedy salma.kennedy@primecreative.com.au
HEAD OFFICE
Prime Creative Pty Ltd
379 Docklands Drive Docklands VIC 3008 Australia
SUBSCRIPTIONS
03 9690 8766 subscriptions@primecreative.com.au
Trailer Magazine is available by subscription from the publisher.
Annual rates: AUS $99.00 (inc GST). For overseas subscriptions, airmail postage should be added to the subscription rate. The right of refusal is reserved by the publisher.
ARTICLES
All articles submitted for publication become the property of the publisher. The Editor reserves the right to adjust any article to conform with the magazine format.
COPYRIGHT
Trailer Magazine is owned by Prime Creative and published by John Murphy.
All material in Trailer Magazine is copyright and no part may be reproduced or copied in any form or by any means (graphic, electronic or mechanical including information and retrieval systems) without written permission of the publisher. The Editor welcomes contributions but reserves the right to accept or reject any material.
While every e ort has been made to ensure the accuracy of information Prime Creative will not accept responsibility for errors or omissions or for any consequences arising from reliance on information published. The opinions expressed in Trailer Magazine are not necessarily the opinions of, or endorsed by the publisher unless otherwise stated.
O cially endorsed by the VTA
This month, MEGATRANS returns to Melbourne – and it’s bigger than ever. For those who may not know, MEGATRANS is Australia’s largest integrated conference and exhibition dedicated to the logistics industry. Part of Prime Creative Media, MEGATRANS continues to play a crucial role in encouraging innovation and sustainability within the supply chain, and this year, it will focus on fleets of the future and the zero carbon warehouse, as well as traceable supply chain and cold chain solutions by bringing together companies which offer zero carbon solutions.
The 2024 expo, taking place between 18-19 September at the Melbourne Convention and Exhibition Centre, will be showcasing cutting-edge technologies and services in these areas that are pivotal to advancing the sustainable supply chain, with products and services ranging from state-ofthe-art transportation technologies to innovative warehousing solutions.
In addition to the show floor, it will feature a conference including several speakers from different organisations such as TOLL Group, Deloitte, JLL and more to discuss issues that are shaping the future.
Show Director, Lauren Chartres, said MEGATRANS will have something for everyone.
“This event is not just a platform for showcasing products and services
but a hub for knowledge-sharing and networking among industry decisionmakers,” she said.
Speaking of exciting things, this month we bring to you the annual Trailer Rigid Body Builder Showcase – this time sponsored by our good friends at E-Plas. The showcase is the only published list of all leading manufacturers in the country and their build capabilities, and it’s a great resource if you’re looking to invest in new equipment or just want to check out what’s available in the market.
Some other highlights of this edition include Krueger’s new partnership with Calibre Steel in our Trailer builder section which you can read about on page 26, Lactalis Australia’s (the leading dairy company which offers Pauls Milk, Ice Break iced coffee, Oak and Breaka flavoured milk products and more) fleet renewal program with Scully RSV on page 30, and for our Tasmanian readers, Bass Strait Transport’s new B-double drop deck fitted with a series of JOST products on page 40.
Back to MEGATRANS, though – if you’re reading this and you’d like to attend, it’s not too late. You can lock yourself in by visiting www.megatrans. com.au/register.
Business partnerships, people movements, developments that bolster freight productivity and more.
20 Economy
Australia Post has increased its production of renewable electricity by more than 27 per cent.
22 Rigid bodies
Bruce Rock Engineering has rebranded its reefer trailer o ering in partnership with one of North America’s largest trailer builders, Wabash National.
24 Trailer builder
Australia’s trailer manufacturing industry is as strong as ever.
30 Rentals/leasing
Lactalis Australia banks on Scully RSV for its fleet renewal program and Rentco celebrates its 30th anniversary.
34 Axles & suspension
Market Express and LUSTEC are gaining significantly through high-quality axles and suspensions.
38 Trailer building materials/components
A showcase of the products and services that keep trailers on the move.
44 E-Plas Rigid Body Builder Showcase
The only published list of all leading manufacturers in the country that specialise in rigid bodies.
52 Infrastructure spotlight
What you need to know about Australia’s biggest road projects this month.
54 World map
A new report detailing what the biggest challenges the US will face when transitioning its heavy vehicle to fleet to zero emissions has been released.
56 Fleet of the month
Jarratt Transport Solutions has launched four new prime movers and B-triple road trains.
58 What’s on Upcoming shows and field days.
After a two-year wait, Australia’s largest integrated conference and exhibition dedicated to the logistics industry is returning to Melbourne.
MEGATRANS’ previous events have attracted thousands of attendees, providing a platform for leaders across the supply chain to discuss the future of the logistics industry.
The event is being held 18-19 September (9.30am – 4.30pm) at the Melbourne Convention & Exhibition Centre.
Attendees can expect to see a range of fleets, manufacturers and suppliers including Schmitz Cargobull, E-Plas and VISY Logistics.
The combined conference, exhibition and jobs pavilion will provide a space for industry experts to champion their services as well as network and exchange solutions.
Many of the exhibitors, like Australian Truck Radio, have organised interactive displays.
Prime Creative Media Managing Editor – Commercial Transport, Luke Applebee, will be at the Australian Truck Radio stand and encourages event attendees to stop by for a chat.
“With Manager and Producer Simon Smith at the helm, Australian Truck Radio runs a music-based format with loads of industry news, interviews and insights
that truckies can ‘lock on and leave on’ – 24 hours a day, seven days a week,” said Applebee.
“Our programming is driven by the hottest country tunes and the greatest classic rock bangers along with the best mix of the ’70s, ’80s and ’90s.
“We keep drivers engaged and informed for upwards of six hours at a time and improve road safety by doing what we do best.
“If you happen to be at MEGATRANS this year, come and visit the Australian Truck Radio stand. I’ll be there with microphones ready to record.”
The official opening breakfast will feature a key address by Victorian Minister for Roads and Road Safety and Ports and Freight, Melissa Horne.
Hosted by the Victorian Transport Association (VTA), it will be held before the expo from 7:30-9:30am on 18 September.
Tickets for the breakfast must be booked through the VTA website.
MEGATRANS will be collocated with The Australian Bulk Handling Expo and the associated Mercury Awards.
Also, new to the program is the MHD Sustainable Warehouse award.
This award is designed to celebrate sustainable practices and green facilities amid current efforts to reduce emissions. Current nominees’ initiatives
include water and temperature conservation, solar arrays, LED lighting, on site batteries and low-carbon concrete.
Companies are invited to submit their nominations directly to MHD. The winner will be announced at the exhibition.
The theme for this year’s event is sustainability. This refers not only to the environmental context, but also to ensuring the viability of the industry’s future.
From traceable and transparent supply chains to sustainable warehouses and upgraded fleets, forward-thinking companies are innovating solutions to reduce emissions while saving on costs. Supply chains are essential. The goal is to make sure they can last.
“Making sure the entire supply chain is resilient is really the main theme of the show,” said Prime Creative Media Events Manager, Lauren Chartres.
“Not just sustainability in terms of decarbonisation, though that is important, especially in terms of the transport sector, but also sustainability in terms of upskilling the workforce and having a skilled workforce in place.
“And then there are sustainable facilities, too, whether that’s retrofitting them to reduce emissions or building new facilities to accommodate future growth.”
Earlier this year, Australia Post opened a new $12 million parcel facility on the Gold Coast, cementing its long-term investment in the region.
Built to accommodate increased parcel growth, the modern 15,087-squaremetre facility was designed to improve turnaround times and help process up to 6,000 parcels per hour, 75,000 parcels a day and up to 90,000 during peak periods like Christmas.
The new state-of-the-art facility integrates cutting-edge sortation technology, enabling increased visibility of customer parcels moving throughout the network and seamlessly integrating Australia Post’s suite of services including Express Post, Parcel Post, StarTrack Premium and its newest next day delivery service, Australia Post Metro, to provide a better experience for customers.
In a first for Australia Post, the facility has also achieved an accredited 5 Star Green Star rating, featuring a 99kW solar system capable of powering up to 30 per cent of the total load for the facility in an effort to reduce carbon emissions.
Queensland Minister for Communications, Michelle Rowland,
and Australia Post Executive General Manager Network Operations, Rod Barnes, were onsite to unveil the facility.
Barnes said the multi-million-dollar investment into the Gold Coast and its surrounds, including parts of northern New South Wales such as Tweed Heads and Murwillumbah, reflects Australia Post’s commitment to improving services for the community.
“As one of Queensland’s biggest cities, we’ve seen parcel volumes increase by 97 per cent since 2019, with data indicating almost 280,000 Gold Coast households shopped online in the past year,” he said.
“This increased demand has seen the Gold Coast become our largest posting zone outside the major capitals, with substantial inbound and outbound product.
JOST Australia Regional Sales Manager Victoria, Graham Cox, is celebrating 10 years at the company.
Cox’s journey with JOST, the company said, is a testament to dedication and growth.
Starting at the business as Warehouse Leading Hand, he moved through roles in customer service to his positions as Sales Representative and then Area Sales Manager.
Cox now leads JOST Australia’s Victorian sales team as Regional Sales Manager.
“Throughout his career, Graham has consistently provided customers with the exceptional JOST experience, embodying the company’s core values in every role he’s held,” JOST said in a statement online.
“His enthusiasm for seizing opportunities and his commitment to fostering a learning environment make him a true team player, always bringing others along on the journey of growth and development.”
“This new facility will expedite processing and improve turnaround times, ensuring quicker delivery of parcels to our customers’ doorsteps.”
Rowland said the important investment in parcel delivery infrastructure will ensure that Australia Post is wellequipped to handle the growing increase in demand for parcels.
“Australia Post is a cherished national institution that supports communities, businesses and our economy – and the Government is committed to supporting the organisation to modernise to meet the expectations of Australians,” she said.
“This state-of-the-art facility will help ensure consumers and businesses on the Gold Coast and across Queensland are well-served by Australia Post.
“Australia Post’s facility investment and the Government’s modernisation agenda will help ensure the business is well positioned to meet the challenges and needs of the future.”
The opening also commemorates 50 years of StarTrack, with the new facility enabling StarTrack to collect from over 250 customers daily and servicing an average of 25,000 delivery points within the Premium network.
Reflecting on his time at JOST, Cox said he has enjoyed working with like-minded people who have a passion and belief in the products which JOST supplies.
The opportunity to progress in the business with the knowledge and skill sets learned from within, he said, has also been memorable.
“I would like to thank the people who gave me the opportunity to start at JOST, and those who have mentored me through my journey at JOST Australia and continue to do so,” Cox said.
“I’m looking forward to the progress of
JOST technology products like sensor systems, Loc-Light and more so KKS auto coupling systems, [as well as] new products JOST will release to market and the expansion into a new Melbourne facility in the future.”
FedEx recently opened its new state-ofthe-art sortation and distribution facility in Coffs Harbour, New South Wales.
According to FedEx, the facility will support economic growth in the region as well as small and medium businesses looking to expand their domestic and international reach.
It spans over 2,400 square metres and is equipped with advanced material handling and sortation technology to safely and efficiently sort up to 1,300 packages per hour.
“This advanced facility represents a significant milestone in our commitment to enhancing our value proposition in Australia, and creating greater access for customers while supporting the ongoing economic growth of regions like Coffs Harbour,” said FedEx Australasia Vice President, Peter Langley.
“By investing in infrastructure
enhancements and service improvements in Australia, we enable faster and more efficient freight movement across the country.
“This expansion will not only strengthen our regional network and overall service offerings, but it also empowers local businesses to retain or even gain market share by providing the best possible last-mile delivery experience for their customers.”
Strategically located near the Pacific Highway, the new facility provides easy access for express pick-up and delivery services across Coffs Harbour and surrounding areas, including Grafton to the north and Eungai Creek to the south.
It also serves as a domestic and international collection point, providing seamless end-to-end transportation services for local importers and exporters.
• CLIPLOCK features a TWO-STAGE locking mechanism. The industry standard and the Optional innovative GP LOCKING CLIP & LOCKING GROOVE (PATENT PENDING).
• Prevents incomplete coupling connections and unintentional disconnection of Trailer Airline Couplings.
• A dangling Locking Clip will alert the driver that the Coupling Connection may not be securely connected.
• Ensures positive and secure connection of the Trailer Airline Couplings.
makes it easy to quickly see any connection issues. CLIPLOCK features an ‘OPTIONAL’ New innovative second stage locking system exclusive to GP Truck Products.
The National Heavy Vehicle Regulator (NHVR) has released new guidance in a move to support industry uptake of rapidly emerging Fatigue and Distraction Detection Technologies (FDDT).
Described as a ‘big step forward’ in fatigue safety, the guidelines come in response to industry feedback which highlighted the need for greater clarification on the use of FDDTs.
Driver fatigue is a leading factor in truck crashes according to the NHVR. Under Australian law fatigue management is considered the responsibility of all parties in the supply chain. Most FDDTs are designed to improve these safety outcomes by delivering an immediate alert to a driver when it senses potential fatigue or distraction.
The latest fatigue safety guidelines are reported to address the regulatory responsibilities of companies responding to FDDT alerts and how to support an effective rollout of the technology among drivers and companies.
“We know industry is supportive of
FDDT but is also eager for greater guidance on how to effectively implement it and to better understand their regulatory responsibilities in managing FDDT alerts and data,” said NHVR CEO, Sal Petroccitto.
“The NHVR studies on FDDT continually show the importance of the positive relationship between the company and driver and having an absolute authority to stop driving as key to improving safety.
“FDDT has been proven to play an influential role in reducing driver fatigue and distraction – and is a clear demonstration of how industry continues to innovate with safety technologies.”
South Australian Road Transport Association Executive Director, Steve Shearer, said Australian roads will be safer by providing operators with the tools and knowledge to effectively manage fatigue and distraction.
“There is little information available to industry on how to effectively use FDDT, which we know saves lives,” said Shearer.
“The benefit of the good practice
Australia Post and IKEA have announced a new strategic partnership, entering into a three-year agreement to further expand IKEA’s delivery footprint in Australia.
Starting this October, Australia Post will become IKEA’s primary e-commerce fulfilment partner for small and medium parcels, accounting for approximately 65 per cent of IKEA Australia’s total parcel orders.
Australia Post is projected to deliver over 250,000 IKEA parcels each year under the agreement, offering both Parcel Post and Express Post delivery options for customers across the country.
“Australia Post is proud to be chosen as IKEA Australia’s trusted delivery partner,” said Australia Post CEO and Managing Director, Paul Graham.
“With our robust infrastructure and commitment to reliability and efficiency for customers, we have built the largest delivery network in the country.”
With 23 per cent of all IKEA Australia parcel orders delivered to areas outside the reach of metropolitan stores, Australia Post will support the expansion of IKEA deliveries across its extensive network.
IKEA customers can expect to receive their deliveries from widespread Australia Post collection points and at convenient locations such as local post offices.
“We look forward to supporting the continued growth and momentum of this iconic brand as they expand their customer reach in Australia through our extensive delivery capabilities,” Graham said.
Sustainable delivery solutions also underpin the partnership, with Australia Post operating the country’s largest electric delivery vehicle fleet which will contribute to IKEA Australia’s goal to provide zero-emission deliveries.
“As an omnichannel retailer, our goal is to bring IKEA to more people, in more
guidance is it includes sample templates from transport companies using the technology, meaning they have been tested in the real world.
“We can continue to learn a lot about fatigue management from this technology as we get better at identifying and working with drivers to address the signs and cause of fatigue.”
Key features of the FDDT good practice guidance material:
• An overview of the safety benefits and types of technologies available
• Practical instructions on how to install, set-up and maintain FDDTs
• Information and fillable templates on how to meet your safety duties under the HVNL
• Fatigue and distraction event procedures and processes to reasonably respond to alerts
A set of guidelines providing a starting point on good practice options and a guidance summary are available on the NHVR website.
ways and in more places, making it easier and more convenient than ever before for Australians to shop with us to create homes they love,” said IKEA Australia CEO and Chief Sustainability Officer, Mirja Viinanen.
“We’re famous for our flatpack furniture, however what our customers don’t always realise is much of the IKEA home furnishing range is available to them in a parcel via the post. Partnering with Australia’s largest delivery provider allows us to greatly enhance our accessibility for our customers in this way.
“We are excited to work together with such a highly trusted brand as Australia Post, who shares our values when it comes to excellence in customer experience and a dedication to sustainability and look forward to a successful new partnership.”
Linfox is celebrating a partnership with Coles which started more than 60 years ago and has expanded further since.
Linfox, according to the company, has supported Coles’ growth from almost the beginning – through a supply chain partnership which began in the 1960s, around the time when Coles opened Australia’s first freestanding supermarket.
Overtime, the partnership has thrived alongside the growth of Coles which now houses an extensive national footprint of around 1,800 supermarkets and liquor stores.
“The Linfox and Coles partnership continues to grow stronger,” said Linfox General Manager Coles, Tim Trewin.
“Linfox has invested significantly in fleet, security, people and infrastructure.
“With an additional 80 prime movers, almost 350 trailers and more than 500 team members, we are well-equipped to uphold our high level of service and safety for Coles.”
As of July this year, Linfox was also awarded the management of Coles’ secondary transport services out of four distribution centres (DCs) in Victoria and two in Queensland, including the new automated DC in Redbank.
The arrangement sees Linfox manage Coles’ secondary freight along the east coast, streamlining operations and increasing efficiencies across the network.
“The strength of our relationship is built on our commitment to supporting Coles in meeting its customers’ expectations of value, quality, convenience, and great service,” said Linfox President Retail, Simon Livingstone.
“Coles also continues to entrust Linfox with the management of Coles’ Truganina Regional DC and Somerton National DC in Victoria.
“These significant ambient operations jointly employ more than 1,500 people, who manage approximately 18,000 stock keeping units.”
To celebrate the successful commencement of the secondary transport operations across Coles’ four Victorian sites, Linfox founder, Lindsay Fox, recently visited the Coles Truganina team with Linfox ANZ CEO, Mark Mazurek, Livingstone and NSW team members as well.
“Since 1963, Coles has been judging Linfox by its actions,” Fox said.
“We’ve grown together and shared in each other’s success.”
State-of-the-art sensor technology to be trialled in Sydney will scan trucks in real time and use connected warning signage to divert drivers of overheight vehicles from their routes.
The trial is part of the NSW Government’s ongoing crusade to reduce disruption from overheight incidents that has seen tunnel closure minutes in the Sydney Harbour Tunnel cut by 80 per cent.
The automatic system will give drivers an accurate real-time height reading on their vehicle, giving heavy vehicle drivers time to change their route to avoid dangerous tunnel incidents that can cause systemwide disruptions to Sydney’s road network and damage to critical infrastructure.
In an ‘Australian first’, Transport for NSW has combined the light detection and ranging (LiDAR) scanning technology with automatic number plate recognition (ANPR) software.
The six-month trial, announced last month, will see trucks taller than four meters scanned as they pass under the sensor, and their height and number plate information will be gathered and instantaneously displayed to drivers on the overhead Variable Message Sign (VMS).
“This Australian-first scanning technology takes the guesswork out of load heights with real-time accurate calculations that allow drivers to act immediately and head off overheight incidents,” said NSW Minister for Roads, John Graham.
“The NSW Government remains resolute in its commitment to stopping overheight trucks from shutting down our city and inconveniencing motorists.
“This new technology on trial will help us strengthen the approach even further.”
Graham claims the technology is an awareness rather than enforcement tool, arming drivers with the right information so they can make the right decisions on the road.
The first site is now live on the southbound lanes of the M1 Pacific Motorway at the Mount White Heavy Vehicle Safety Station which is operated by the National Heavy Vehicle Regulator (NHVR).
“The NHVR supports the investment
by NSW Government into the use of new technologies like LiDAR scanning and ANPR software to help industry and ultimately drive greater safety and productivity outcomes,” said NHVR CEO, Sal Petroccitto.
“This system not only enhances road safety but also underscores our commitment to fostering innovation within the heavy vehicle industry.
“We are proud to continue our collaboration with Transport for NSW to reduce overheight incidents and ensure safer road transport for all.”
The NSW Government has introduced a zero-tolerance approach to overheight trucks, including six-month registration bans for offending trucks – sending the message to truck owners and trucking companies that it is their responsibility to manage, along with drivers.
This crackdown, in combination with the work of the industry-wide Overheight Truck Taskforce launched in June 2023, resulted in a dramatic drop in overheight incidents in Sydney tunnels.
According to the NSW Government, in the first six months of the taskforce’s operation (July to December 2023) there was a 67 per cent decrease in total closure time minutes and a 32 per cent reduction in incidents, the lowest level in seven years.
Over the same period, the Sydney Harbour Tunnel, the most disrupted route, saw an 80 per cent reduction in closure minutes and a 58 per cent reduction in incidents.
The reduction in incidents has continued across the network in 2024, with 26 recorded overheight incidents between January and June – 62 per cent fewer than the same period in 2023.
“Responding to overheight incidents comes at a huge resource and productivity cost – not to mention resulting delays and damage,” said Transport for NSW Executive Director Customer Journey Management, Craig Moran.
“Following the conclusion of the taskforce’s successful approach, Transport [for NSW] is taking the learnings forward to ensure our road network is safe, efficient and reliable.”
A-League club Adelaide United has announced the continuation of its partnership with South Australian linehaul provider, TML Transport, for the 2024/25 soccer season.
Following this extended partnership, the TML Transport logo will continue to be clearly displayed on the front of the team’s shorts in all UTE A-League matches in the season.
TML, based in Two Wells, SA, offers an extensive range of trucking linehaul services across the country.
Adelaide United Head of Commercial, Fabrizio Petrone, expressed his joy in renewing the team’s agreement with TML Transport.
“We’re thrilled to continue our partnership with TML as we embark on an exciting new season,” he said.
“Their commitment to excellence and shared values make them an ideal partner for us and we are delighted to have them on board again.”
TML Transport owner, Lewis Magro, similarly shared his enthusiasm for the partnership.
“We’re really excited to carry on our association with Adelaide United for the 2024/25 season,” he said.
“As a proudly South Australian owned and operated company with a national reach, TML Transport is a perfect match for the club.
“We’re eager to continue working together and supporting Adelaide United’s ongoing success.”
Americold Logistics has begun work on its newest development project in Australia.
Americold is investing $55 million in expanding its temperature-controlled facility in Prospect, New South Wales.
The facility will offer more cold storage capacity and flexibility for its newest and existing customers in Sydney.
“This is a significant achievement for Americold and our valued retail, QSR and FMCG customers,” said Americold Logistics President of International, Richard Winnall.
“We are responding to our customers’ future growth needs by bringing on temperature-controlled capacity to a high-demand market and growing market in Sydney.
“Americold is privileged to carry out our vision of assisting our clients in feeding the world, and this growth is evidence of that dedication.”
Coles has opened its second Automated Distribution Centre (ADC) as part of a more than $1 billion investment in technology led innovation.
The Kemps Creek, New South Wales, facility was officially opened on 6 August by Coles Group Chairman, James Graham, and CEO, Leah Weckert.
Located 40 kilometres west of the Sydney CBD, the ADC has been designed to provide better availability for customers and create safer, more efficient outcomes for team members and suppliers.
The site spans 187,000 square metres – the equivalent size of around 25 rugby league fields.
With a building size of 66,000 square metres, Coles claims it’s one of the ‘biggest and most productive’ automated distribution centres in the world.
Once operating at full capacity, the Kemps Creek facility will service 229 NSW and Australian Capital Territory stores, with the ability to process more than four million cartons per week.
This is the equivalent of 32 million
products sold in stores, and over the course of a year, around 1.6 billion sales units.
At the opening, Graham said he was extremely pleased to see the major investment in Coles’ supply chain come to fruition.
“Over 4,400 people contributed more than 1.8 million working hours to building the site, installing the automation and getting the system ready for operation –it is an achievement that everyone should be very proud of,” he said.
This is the second of two Witron facilities Coles has opened and is part of the company’s single biggest capital investment in its 110-year history.
The first ADC opened in Redbank, Queensland, in May last year and has since processed more than 140 million cartons, with customers in Queensland and northern NSW seeing a 20 per cent improvement in availability compared to other stores.
“Today marks a key milestone on our roadmap to enhance our supply chain and improve our operating efficiency,
New South Wales’ premier vehicle safety facility will be quadrupling in size, with $30 million being invested by the State Government to significantly expand it.
Paving the way for new highway speed and heavy vehicle testing, the investment follows the purchase of 100 hectares of farmland adjacent to the existing Future Mobility Testing and Research Centre (FMTRC) site in Cudal.
Planned works will include the expansion and construction of a 4.4-kilometre loop track as well as a new heavy vehicle skid pad which will support the team in increasing safety testing and research.
This work involves enacting real-world scenarios at the centre to test vehicle safety features that help prevent crashes.
“The need for a new heavy vehicle testing space in the southern hemisphere was a key finding from extensive engagement with vehicle manufacturers,
developers and researchers to map the future for the Cudal site,” said NSW Minister for Roads, John Graham.
“As light vehicles continue to become more advanced, there is also a need to uplift testing capabilities to keep up with new, increasingly automated, technology.”
The new Cudal track will let the team test new driver assist systems in real-world scenarios, including heavy laden B-doubles travelling at highway speeds, and situations involving headon approaches and merging safety with cars, trucks and motorcycles.
According to the NSW Government, the FMTRC site is the only Governmentowned and operated testing centre of its kind in the world.
Since being established in 2019, the facility has delivered more than 85 test and research programs.
Transport for NSW will now begin
with a world-class facility that will deliver improved availability for our NSW customers,” Weckert said.
“We have seen great improvements in availability for our customers in Queensland and Northern New South Wales following the opening of Redbank ADC in Queensland last year – and I’m excited to see this second ADC bring these same benefits to NSW.
“This facility also delivers a stepchange for the safety of our team, with the elimination of around 16 million kilograms of manual handling every week.”
The Kemps Creek ADC is fitted with a 3.5-megawatt solar solution on the roof which is among the largest rooftop solar solution in the Coles network, with Coles Group to be powered by 100 per cent renewable energy by the end of financial year 2025.
It is also half the footprint of the current two distribution centres in NSW, due to the utilisation of the 36-metre building height which is almost three times taller than Coles’ current DCs.
planning and community consultation for the design of the new loop track, with construction set to commence in 2025.
“This expansion is an investment in regional NSW, and this cutting-edge facility attracts clients from across the globe, making NSW a leader in testing road safety aspects of autonomous vehicles that will save lives,” said NSW Minister for Regional Transport and Roads, Jenny Aitchison.
“Vehicle safety is a critical part of making our roads safer and independent modelling has shown that vehicle safety improvements have saved more than 700 lives over the past decade.”
Brisbane-based refrigerated transport company, SLR Trans, is celebrating 10 years of operations.
SLR Trans began in 2014 as a small business averaging 200 deliveries a week.
With steady growth ever since, SLR Trans has expanded into a national transport provider while committing to providing a superior service for its customers.
SLR Trans COO, Aumar Moosa, told Trailer the 10-year anniversary marks a significant milestone in the company’s journey – signifying a decade of dedication, growth and resilience in the competitive road transport industry.
team and reinforce its commitment to providing reliable and efficient logistics solutions.”
According to Moosa, SLR Trans has sustained its success over the past decade through a combination of key factors – such as understanding and prioritising the needs of clients to develop strong and lasting relationships, ensuring repeat business and customer loyalty and collaborating with other reputable businesses and stakeholders in the industry.
“These elements have collectively contributed to the sustained success of SLR Trans,” he said.
“At SLR Trans, we are focused on
service excellence.”
Looking ahead, Moosa said SLR Trans is focused on maintaining and enhancing the quality of service for its existing customers while keeping the doors open for any new clients who needs transport and warehousing solutions.
“We understand the importance of sustaining the reliability standards that have built our reputation over the past decade,” he said.
“Additionally, SLR Trans is committed to giving back to the community and engaging in meaningful collaborations which involves identifying ways to contribute positively to society, whether
Construction of Toll Group’s new cuttingedge healthcare facility at the Melbourne Airport Business Park has been completed.
The 10,000-square-metre temperaturecontrolled facility was custom built to support the operations of leading global biotechnology company, CSL Seqirus, which is situated on the adjoining site.
Toll is a leading supply chain partner to CSL Seqirus which produces influenza vaccines, antivenoms and blood plasma to Australia and the rest of the world.
Melbourne Airport Program Manager, Cesar Gomez, said the new facility is a significant addition to Toll’s extensive network servicing the healthcare industry.
“Toll Healthcare’s new facility has received one of the highest ratings from customer auditors in the region and is
well on track to receive an A1 compliance rating from the Therapeutic Goods Administration,” he said.
“Its advanced specifications on security, mechanical systems and electrical redundancy are critical for the nature of their operations.”
Constructed by CMW Design & Construct, Gomez explained the facility’s development also had a heavy focus on sustainability – targeting a 5 Star Green Star building certification.
“This building is set to be the first within the Melbourne Airport Business Park to achieve such a significant accreditation,” he said.
Construction of the new facility was first announced earlier this year, where it was reported that the $20 million facility would eventually become Toll’s largest healthcare site in Victoria.
Tunnel works have commenced for the North East Link Project which is expected to get thousands of trucks off local Melbourne roads.
Two tunnel boring machines (TBM) are being used in the project, with the first now digging a 6.5-kilometre tunnel between suburbs Watsonia and Bulleen which will reportedly reduce travel times by 35 minutes and remove 15,000 trucks from local roads.
The TBM is the first of two massive machines that will dig up to 15 metres per day and up to 45 metres underground.
The 4,000-tonne machines will also install tunnel walls made of approximately 44,000 individual concrete segments made locally in Benalla.
“Victoria’s missing link has been talked about for decades,” said Minister for Transport Infrastructure, Danny Pearson.
“We’re getting on with building it to make sure our freeways are keeping up with our growing state.”
More than 100 tunnel workers have undergone specialised underground training at the Victorian Tunnelling Centre to work below ground, with the tunnels to be built using 100-per cent renewable electricity.
The project has employed more than
6,700 people and will create 12,000 jobs before its completion in 2028.
The Australian Government has made a total contribution of $5 billion to the project following an additional pledge of $3.25 billion at the 2024-25 Budget, with the Victorian Government providing the rest of the project’s funding.
“This shows the Commonwealth is once again partnering with Victorian
infrastructure, in job creation and in building the economy, as we deliver this important project for our local community,” said Federal Member for Jagajaga, Kate Thwaites.
The final assembly of the two machines was announced earlier this year, when it was revealed that they would be launched in the months to follow.
The National Heavy Vehicle Regulator
(NHVR) has registered the Mobile Crane Industry Code of Practice following extensive stakeholder consultation in a bid to assist industry with identifying potential hazards and reducing risk.
In partnership with The Crane Industry Council of Australia (CICA), the NHVR has developed a practical guide aimed at assisting parties in the Chain of Responsibility (CoR) to comply with their Primary Duty obligations under the Heavy Vehicle National Law (HVNL).
NHVR Chief Safety and Productivity Officer, David Hourigan, said Codes of Practice are not designed to be exhaustive, but to alert operators in an industry to relevant hazards along with recommendations on how to manage those risks.
“Mobile cranes play a crucial role in the completion of construction and infrastructure projects across the country, but we also know there are unique hazards and risks associated with mobile cranes compared with other types of heavy vehicles,” he said.
“Often of substantial mass and dimensions, mobile cranes are regularly required in high-traffic urban areas, with operators and drivers also potentially faced with tight deadlines on high-
pressure and dynamic construction sites.
“We are pleased to have worked closely with industry on the new Mobile Crane Industry Code of Practice, including in partnership with CICA, and obtaining input from industry through public forums and feedback on a draft Code of Practice.”
Under the HVNL, parties in the Chain of Responsibility (CoR) are required to ensure the safety of the heavy vehicle transport activities they control or
influence under their Primary Duty obligation.
“That is why a Code such as this can be such a helpful and important tool – here you have relevant potential risks and hazards outlined, along with recommendations for how to eliminate or minimise them,” Hourigan said.
“This Code won’t just be relevant for crane companies – construction companies, civil contractors, builders, suppliers and other businesses may be CoR parties within this industry.”
One of Australia Post’s largest and newest solar array systems – supporting the Kemps Creek Parcel Facility in New South Wales – has generated enough electricity in its first year of operation to power 292 four-person homes.
As the Kemps Creek location marks its one-year anniversary, the 1,500-kilowatt solar system has generated enough electricity to cover 30 per cent of all electricity used at the facility.
More than 3,400 panels positioned on the facility’s roof support Australia Post’s Kemps Creek operations including new, state-of-the-art sortation equipment and charging stations for electric vehicles (EVs). Constructed to meet the needs of Western Sydney’s growing population, the massive 33,680-square-metre Kemps Creek facility is the size of 4.5 soccer fields and can process up to 200,000 parcels per day with a maximum hourly throughput of 20,000.
Across the facility’s delivery catchment (an area comprising 46 Western Sydney postcodes) the total number of online purchases grew by 81 per cent from 2019 to 2023. The number of households shopping online grew by 21 per cent over the same period, a figure reflecting both population growth and e-commerce trends accelerated by the pandemic.
Kemps Creek’s huge solar array is on track to deliver a long-term carbon emissions saving of 1,680 tonnes carbon dioxide equivalent per year by avoiding the use of grid-sourced electricity. Like many homes, the solar system at
GDP growth rate March 2024
Kemps Creek exports some electricity to the grid at times of peak generation, while drawing from the grid at times where solar is not produced. In addition, five per cent of all car spaces at the facility now have provision for EV charging, while motion-sensor LED lighting is also installed to boost energy efficiency.
Australia Post Executive General Manager Network Operations, Rod Barnes, said the facility’s cutting-edge technology was benefitting not only the environment but customers in one of Sydney’s major growth corridors.
“Western Sydney with its booming population was a very strategic point for us to increase our presence and
this is paying off in efficiency gains and less on-road time by positioning parcel delivery drivers closer to the homes and businesses they deliver to each day,” he said. “More broadly, over the past three years in New South Wales the number of parcels we process each day has risen by 305,000 – the result of new facility builds or upgrades at 17 sites.
“One year on from launch our team is taking pride in seeing such a significant proportion of electricity usage covered by solar.”
Australia Post operates the country’s largest fleet of electric delivery vehicles – 37 per cent of its total fleet and nearly half of all delivery rounds – and continues to procure more.
For quite some time, Bruce Rock Engineering (BRE) has found triumph with its specialty in PerformanceBased Standards (PBS) and tipper combinations for the bulk commodity logistics sector. Although, as the sole Australian distributor of Wabash National’s dry and refrigerated trailers from the United States, the company has shown that when new opportunities arise, it’s able to not only adapt but excel.
BRE has been partnering with Wabash for over 10 years now. The collaboration initially involved bringing its completed Arctic Lite refrigerated trailers down under through roll-on, roll-off (RORO) and to Australian specifications, but it has since expanded into a whole new range of reefers and further innovation.
“We originally partnered with Wabash for market supply between 2010 to 2014
after the global financial crisis boom, which provided us the extra capacity to complement our own locally made product,” says BRE Managing Director, Damion Verhoogt. “Using Wabash’s R&D projects, we identified that their composite van panel resource would be a huge potential for our market with tare weight and thermal efficiency improvements.”
Since Wabash first developed its innovative Cold Core Moulded Structural Composite (MSC) van panel technology in 2019, BRE has been importing the material in flat pack form to assemble onto its chassis in Western Australia for dry and refrigerated trailers.
Now known as Cold Core EcoNex, the reefer range includes full-length chassis for road train compatibility which are engineered and manufactured to BRE’s exacting standards.
“We get an EcoNex panel that is built to our dimensional specifications which we put on our local built full-length chassis,” Damion says. “We then build the box up and complete it to customer requirements.
“This has allowed us to have another string to our bow in our product range. We are very active in the bulk tipper market with side and end tippers, so venturing into refrigerated trailers has allowed us to expand our market and industry while still maintaining our road train focus.”
The Cold Core EcoNex reefer range is made up of two primary models, the Acutherm Refrigerated Freight Body and Acutherm Refrigerated Van, which are available in a variety of sizes and configurations and are worthy choices when it comes to protecting products and maximising operating efficiency.
The brand-new Acutherm Refrigerated Van with EcoNex technology.
“We’re on our second generation of Cold Core composite vans using the latest of Wabash’s composite panel technology and a lot of small improvements and learnings over the first series,” Damion says. “Our largest volumes are 45’ road train freezer vans, but we also do 12-pallet rollback A trailers and 48’ to 53’ singles. We’ve got some Performance-Based Standards (PBS) super B and B-triple combinations as well, so we basically do anything we can cater for.”
The Acutherm Refrigerated Freight Body, BRE claims, is setting ‘breakthrough performance standards’ with up to 30 per cent more thermal efficiency in a body that is up to 15 per cent lighter compared to conventional reefers.
Its standard features include a seamless exterior which enables
smooth, full-wall decaling; stainless steel rear frame for added durability; one piece header system which eliminates corner caps and increases front wall strength and a smooth, seamless interior liner for a consistently flat and brighter food grade surface.
Meanwhile, BRE says the Acutherm Refrigerated Van also sets standards while helping fleets meet ambitious sustainability goals, thanks to its unique longer lasting and lightweight properties that were designed to increase revenues from first to final mile.
“The original Cold Core MSC has been a game-changer with 25 per cent better thermal efficiency than the Wabash conventional Arctic Lite reefer,” Damion says. “This gain is increased to 50 per cent better than some rivals, which is based on field test data, not just theory.”
The new and improved Cold Core EcoNex product builds on the already established series with improved door seal arrangements which are more ergonomic and user-friendly and allow for better operator comfort, as well as a new internal scuff package that is more durable.
The EcoNex material was designed and tested to operate under the harshest of conditions – typified by midsummer temperatures in excess of 50°C – and is made of a foam-insulated core with a polymer fibre-reinforced shell and a protective gel coat surface.
The internal wall and ceiling line of materials have also been upgraded to be more resistant to punctures and abrasions, and on top of that, Damion says BRE has introduced additional options for polished base rail extrusions as well as some “other bling for operators who want the shiny bits”.
“The build quality is exceptional, but the biggest thing is thermal efficiency and tare weight,” he says. “That all leads to a lower carbon footprint, less reefer hours, more payload when loaded, less diesel burnt in the truck when empty and less rolling resistance carting around dead weight.
“So, thermal performance and tare weight are probably our main points of difference in market, and there’s more of a focus on this with the green carbon push that’s happening.”
Wabash and BRE’s joint-project is now in full-effect, with the updated versions currently in production at BRE’s WA
facilities. As Damion details, a new 45’ road train unit has just been built and is being rolled out to a customer, with others following suit.
“The trailer that we’ve just finished building incorporates all of the upgrades and improvements over the Cold Core MSC product,” he says. “We’ve got some more of them in production now, and they will be our primary refrigerated reefer offering going forward.”
Contact Bruce Rock Engineering 15 Swan Street, WA 6418
Ph: 08 9061 1253
Web: www.brucerockengineering.com.au
ORIX Rental has added five Dangerous Goodsrated 40’ skel trailers from CIMC Vehicle Australia to its growing and versatile national rental fleet.
Rental and leasing giant, ORIX Rental, has been operating in Australia for over 35 years, offering a wide range of vehicles and trailers to meet the needs of businesses large and small.
Over the last decade, ORIX Rental has continued to grow with new locations and fleet additions for the light commercial and heavy commercial space, all while listening to its customers and understanding where their pain points are to tailor a rental solution.
“We’re one of the largest rental and leasing companies in Australia for passenger, light and heavy commercial vehicles, and that allows us to provide a full-service solution to our customers,” says ORIX Australia General Manager Rental and Mobility, Grant Harrison. “We can provide operating leases as well as options to buy, so there’s long-term options as well as short-term options as part of a complete service for our customers.”
Through its latest trailer delivery from CIMC, ORIX Rental has added
five new 40’ skel trailers to its fleet which have been designed specifically with versatility in mind, making them suitable for a wide range of practical applications.
They join ORIX Rental’s large rental fleet of CIMC skels built to its standard Dangerous Goods (DG) specification featuring three-way twist lock pins, Ringfeder couplings, side loader pads and shipping tie downs, with Performance-Based Standards (PBS) capabilities too.
“The DG rating is critical for us because it gives our customers the versatility to move different boxes around, using DG-rated equipment,” Grant says. “They’re designed to be as vanilla and versatile as possible to enable many applications as possible.
“The trailers can be used in various configurations such as singles, road trains and A-doubles. This flexibility not only enhances safety but also boosts efficiency, making them a valuable addition to our fleet.”
Grant says the new trailers have
proven to be extremely reliable and worthy for ORIX Rental through their rental operations.
“We’ve been very pleased with their performance,” he says. “They represent great value, and we’ve received very positive feedback from our customers. They handle exceptionally well and have resulted in improvements in safety and operational versatility.
“We’ve had CIMC trailers in our fleet for many years and they have been reliable in every application our customers have used them in, whether it be on-road and partial offroad applications or in general freight corridors from ports to distribution centres.”
ORIX Rental’s fleet of CIMC trailers have been heavily involved with the transport industry as well as the renewable sector and in operations across a variety of other industries. Therefore, Grant explains it is essential that ORIX Rental has an OEM it can rely on to supply a fleet of trailers that will deliver on a large scale.
“Acquiring trailers through CIMC supports our goal of providing highquality and versatile trailers to our customers,” he says. “We look at wholeof-life costs for these types of assets, and as a rental provider, we have high expectations to meet the demands of our customers.
“CIMC understands these requirements and is always willing to collaborate with us. Their responsiveness and flexibility ensure we can provide our customers with reliable and flexible trailers, helping us maintain our high standards and meet industry demands effectively.”
According to Grant, the efficiencies CIMC provides in terms of trailer configurations and its ability to work with ORIX Rental’s own customers has also been key.
CIMC has a diverse range of trailers in stock, with a product portfolio of curtainsiders, flat tops and skels built to extremely high quality and in fast turnaround times – often for customers looking for new equipment within six months.
In addition to its dedication to building exceptional equipment at an affordable price, CIMC is also committed to serving its customers both before and after their purchases have been made – a factor which benefits ORIX Rental significantly.
“That’s the type of support that we’re after,” Grant says. “It’s the type of support that our customers expect from us, and it’s the comfort we need to know we will be supported by our partners. It also gives us a lot of comfort knowing that our customers are getting the value out of their
rental product.
“CIMC have also been highly responsive to our requests, and this adds to the CIMC value offered. We’re here for the long-term, and as such, we’re looking to develop long-term mutually beneficial relationships.”
As ORIX Rental’s most recent skel units prove their worth in fleets around Australia, Grant says the business will continue to place its trust in CIMC for its trailer offering. ORIX Rental is expecting another batch of orders from CIMC which will primarily include drop decks, flat tops, skels and B-double curtainsiders, ensuring it
continues to meet the diverse needs of its customers.
“With the support of CIMC, we can continue to grow our rental fleet and invest heavily to ensure our customers have access to safe, quality, modern and reliable equipment,” he says.
“This commitment allows us to meet the evolving needs of our customers and maintain our position as a trusted provider in the industry.”
Contact
CIMC Vehicle Australia
Ph: 1300 202 462
Web: www.cimc.com.au
Krueger has joint forces with Calibre Steel to continue to bring high-quality trailers constructed with Australian-made products and materials to market, only now with greater flexibility.
Krueger has a history of contributing many product innovations to Australia’s transport industry, and with a clear commitment to quality and efficiency, it continually pushes the boundaries in an effort to deliver the very best to its customers.
The business has done this for the entirety of its proud 45-year history.
Although recently, it embarked upon a new partnership with leading steel supplier, Calibre Steel, in an arrangement that will increase efficiency for Krueger while allowing it to access some of the industry’s best products and personalised steel supply.
As part of the arrangement, Krueger has moved the majority of its steel procurement to Calibre Steel so that it can continue to access BlueScope Australian-made steel and offer the highquality trailers and short lead times it has become renowned for.
“Steel is our single biggest and most important commodity,” says Krueger Director of Engineering and Supply Chain, Steven Teofilo. “It forms the backbone of every trailer, so we go through so much of it.
“The partnership with Calibre Steel is
more than just steel supply. They’ve got a lot of knowledge across their expert team, and they help us solve problems as a real one-stop shop solutions provider.”
The partnership sees Calibre Steel supply Australian-made 250 and 350-grade TRU-SPEC steel to Krueger in various dimensions for use across all of its product lines, ensuring consistency and reliability.
“TRU-SPEC is BlueScope’s cleanest and highest-grade steel that we use for laser cutting,” Steven says. “It’s the best of the best in the BlueScope range, and when we talk about the quality of Krueger products, that’s where we’re starting – with the best steel we can get our hands on.
“We start with the best steel so customers know exactly what they’re getting, where it’s coming from and so we can put assurance behind what’s going into our product.”
Under the arrangement, Krueger can call on Calibre Steel’s in-house secondary processing capabilities including plasma and oxy cutting. Due to the supplier’s involvement, once a delivery arrives onsite there is much less
handling and processing required from Krueger’s end, resulting in more efficient manufacturing.
Another key benefit of the collaboration is Calibre Steel’s close proximity to Krueger’s manufacturing facility which results in reduced material transportation costs and greater on-call access to Calibre Steel’s specialist account service team – all this while still enabling Krueger to source the same high-quality Australian-made steel plate products it has utilised for decades.
“Calibre Steel is based in an adjoining suburb to us, meaning that transportation is greatly reduced with as little as 10 minutes’ travel,” Steven says. “Multiply these time savings across a schedule of regular deliveries and the efficiency gains really add up.”
Calibre Steel is also geared up to provide Just in time (JIT) delivery, project management and forecasting as required. Importantly, all supplied steel is quality assured with full traceability, ensuring Krueger continues to enjoy a premium reputation in the transport industry.
“As a manufacturer, it’s important to continuously identify processes
and techniques that grow our competitiveness,” Steven says. “Efficiencies could come through new technologies, such as our new state-ofthe-art fibre laser cutting machine which we introduced last year, or via logistics and supply chain improvements such as those provided by Calibre Steel.”
In addition to locally made steel plate products, Calibre Steel also has access to some of the highest quality global steel mills which provide even greater scope for Krueger to continue to look into more product innovations – with the possibility of exploring different grades in the future should the need arise.
Calibre Steel Customer Relationship Manager, Maddie Dharmapala, who has extensive experience in the steel industry and works closely with the Krueger team, says the opportunity to partner with Krueger on such a large scale has been very exciting.
“Krueger is well known and highly regarded in the road freight industry for its quality trailing stock, innovative trailer designs and modern manufacturing processes,” she says. “It’s extremely rewarding for Calibre Steel to partner with such an operation and assist the company in reaching its corporate goals.”
In addition to reducing steel transportation costs and providing Krueger with secondary processing capabilities in the form of weld packs, Maddie says another area in which Calibre Steel adds value to Krueger’s operations is through its customer service and support.
“Calibre Steel’s transport team is well qualified and extremely knowledgeable of the industry,” she says. “This understanding sees us ideally placed to provide Krueger with the best service on material selection as well as high levels of overall support. We’re only a 10-minute drive away, very accessible and eager to help.”
As well as its ability to supply quality Australian steel structural plate and laser plate, Calibre Steel also holds local stock of quench and tempered products made by BISALLOY Steel. In addition, a vast global network of partner producers allows the company to source more specialised steel and alloy products for clients that may require these materials.
“They’ve got a very wide and large network, not just in Australia but globally,” Steven says. “If there’s
something that’s not even available in Australia, they can reach out to mills all around the world for it – and they’ve helped us with things like that.”
With Calibre Steel heavily involved in its supply chain, Krueger can guarantee its customers ultimate adaptability and customisation in their trailer builds.
“If customers are looking for something custom, we can reach out to Calibre Steel and they’ll be there,” Steven says. “If customers have really strict requirements, this is where Calibre really shines. They can help find what we need, wherever it’s coming from, and get it to us in a really short time.”
Contact
Krueger Transport Equipment
Ph: 03 9366 2133
Web: www.krueger.com.au
AAA Trailers continues to help shape the landscape of the Australian transport industry – for over a decade, it has contributed to this effort by delivering high-quality, purpose-built truck trailers to clients nationwide.
AAA Trailers’ steadfast commitment to quality, trust and client satisfaction has cemented its reputation as an industry leader, as the business upholds the highest standards of safety, reliability and performance with each and every trailer manufactured.
Now, with its new and expansive location in Ingleburn, New South Wales, AAA Trailers is poised to elevate its capabilities within the region even further.
“The new Ingleburn site represents a major milestone for AAA Trailers,” says AAA Trailers Director, Daniel Bull. “This move is about two things – expanding our footprint and enhancing our ability to serve clients in NSW better.”
The Ingleburn site offers quick access to major transport routes such as the M5 Motorway and Hume Highway, ensuring that clients can easily reach it.
This strategic positioning, according to Daniel, therefore reduces transit times and improves overall efficiency while also adding a boost to its delivery capabilities.
“With streamlined logistics and faster access to major roads, we can now deliver trailers faster than ever before,” he says. “This means less waiting
time for clients and a more responsive service for all.”
The new warehouse spans an impressive 10,960 square metres and allows AAA Trailers to maintain a larger inventory. It also ensures it has the trailers clients need and when they need them.
The warehouse features six containersized roller shutter doors providing easy access for loading and unloading and a seamless flow of operations, reducing wait times and enhancing productivity.
The internal clearances of the warehouse range from 4.8m to 8.0m, accommodating a variety of trailer sizes and types. This flexibility allows AAA Trailers to store
and manage a diverse range of trailers efficiently.
Weather can often be a significant challenge in the transport industry, but the new facility addresses this with a 1,300-square-metre all-weather loading and unloading awning. This ensures that operations can continue smoothly, regardless of weather conditions.
In addition, the secure all-weather level yard, which covers approximately 7,500 square metres, further improves AAA Trailers’ capability to keep trailers safe and secure in any weather.
Another one of the location’s standout features is its complete drive-around
access. This design substantially improves manoeuvrability for large trucks and trailers, and is expected to result in smoother, faster and safer day-today operations by reducing the risk of accidents and getting clients their new trailers as promptly as possible.
The Ingleburn facility is also equipped with a larger power supply and highpressure gas supply, meaning AAA Trailers can operate at peak efficiency and support advanced machinery and equipment. The modern office component, approximately 454 square metres, provides a comfortable and efficient workspace for staff to be more productive and deliver better service to clients.
Outside, the new location boasts a large yard area and forecourt which was designed specifically for easy truck manoeuvrability.
“This feature is valuable in making sure that clients can move their trailers with ease and safely, should they decide to pick up their trailers in the warehouse,” Daniel says. “Additionally, the very spacious parking area ensures that everyone, from staff to customers, can park conveniently.”
AAA Trailers’ focus has always been on delivering high-quality truck trailers that help clients maximise their operational efficiency and ensure reliable performance on the road. The new
Ingleburn location is a testament to this commitment. With its strategic positioning, state-of-the-art facilities and improved infrastructure, AAA Trailers is now better equipped than ever to meet the everchanging needs of its clients. Therefore, the business’ extensive inventory of trailers is now more accessible and even more comprehensive with the increased capacity.
“This ensures that AAA Trailers can provide the right trailer at the right time,” Daniel says. “It also reduces the likelihood of some trailers being out of stock, which typically takes months to replenish, thus minimising delays for clients.
“Moreover, the enhanced loading
and unloading facilities mean quicker turnaround times, allowing clients to get on the road faster.”
For AAA Trailers, this expansion is not just about growing its footprint but about ultimately enhancing its ability to serve clients. With improved access, state-of-the-art facilities and a continued commitment to quality and reliability, AAA Trailers is poised to deliver even greater value to the Australian transport industry.
Contact
AAA Trailers
Ph: 1300 333 888
Web: www.aaatrailers.com.au
With a new fleet of custom-built refrigerated trailers leased through Scully RSV, Lactalis Australia has been able to transform its operations of delivering some of the nation’s most favoured dairy products much more efficiently.
Lactalis Australia has become a favourite among Australian households over the years, with its Pauls, Zymil, Ice Break, OAK, Breaka and Vaalia dairy product lines being popular choices for many. The business is owned and operated by Lactalis Group, the giant global business which is among the world’s largest fresh dairy companies with over 250 production sites and 80,000 employees across 94 countries, and thus it benefits from the significant multinational scale and ambition the parent company has achieved since establishing in 1933.
One of Lactalis Australia’s key commitments is providing exceptional products and services to its customers through efficient, agile and sustainable logistics, and in recent times, the key to this has been its partnership with Scully RSV.
At the end of 2022, Lactalis signed a five-year contract extension with Scully RSV on the back of a fleet renewal program the year prior for the hire of a rental trailer fleet in its three Queensland, New South
Wales and Victoria operations. As part of the contract, Scully RSV would be responsible for replacing 20 aged assets of Lactalis’ Victorian fleet with brand-new trailers built to a custom specification, which, upon deployment, would carry 3.8 million litres of flavoured milk products per week in 200 deliveries through Melbourne’s central metropolitan and Victorian regional areas.
In order to achieve this, Scully RSV worked directly with Lactalis and its preferred trailer OEM, Vawdrey, on a design that addressed a number of unique challenges in the fleet’s Victorian distribution centres and daily operations.
Two years down the track, the transition is now complete and the results have been significant. Lactalis Australia National Transport Operations Manager, Andrew Karetai, says the program has been very successful, resulting in a range of benefits –primarily reliability across the fleet.
“Getting from point A to point B and knowing that our cold chain and product
integrity is being maintained is paramount to our business,” he says. “As a transport operations manager, that is my goal – to ensure that product reaches the customer in a saleable, safe, compliant manner.
“With Scully RSV, we’ve got that reliability and confidence in the fleet. The build and design of the trailers are specific to our needs in terms of strength, durability, cleanability as well as trackability. And at any given time, we can log in and see exactly where these trailers are, what temperature they’re running at and if there’s any issues. These are all critical components of our food safety management system that extend beyond the walls of the distribution centres and production facilities.”
The trailers, set up as B-double combinations, were spec’d with a number of unique features for Lactalis’ direct needs. Their ThermoKing A500 refrigeration systems in the new trailers, as Andrew explains, have been a massive investment for Lactalis by providing reliable, consistent and energyefficient cooling to protect the business’ precious freight while at the same achieving enormous reductions in fuel consumption.
“We’ve gone from using about 3.6 litres of fuel per hour down to around 1.6-1.8 litres per hour,” he says. “So, our fuel consumption is through the floor.”
Working hand-in-hand with the fridge motors, the trailers were designed with insulated roller doors which prevent the rears of the units from overheating. In this space, they also feature switches which
automatically turn the fridges off when the doors are open.
The trailers have a tall aperture at the back which allows Lactalis to double-stack pallets – maximising payload and reducing the number of trips travelled annually. In the rear, electric standby power outlets were also installed to allow efficient access while in dock and limit use of diesel.
and reduced fuel usage) by specifying alloy wheels and removing features such as bar boxes and toolboxes.
“The specifics of the trailers are paramount for us making sure that we’ve got the right equipment for the task that we’re doing,” Andrew says. “Scully RSV’s ability to nurture that and make it into what we’ve got in front of us is really important. They’re definitely
“We’ve gone from using about 3.6 litres of fuel per hour down to around 1.6 to 1.8. Our fuel consumption is through the floor.”
Other important features include e-track rails which provide Lactalis with flexibility in terms of load restraint options, special order load locking rails for effective restraint of loaded milk crates, strategically located work lamps on all A trailers to assist with hooking up of B trailers at night, steel and non-slip flooring inside the vehicles for easy cleaning and maintenance and rear under-run bars with increased ground clearance to prevent damage to both the trailers and loading docks at Lactalis’ major distribution centres in Victoria.
Lactalis’ attention to detail also came down to the location of the kingpins on all of the B trailers, which were moved for flexibility and to cater for the driveways at Lactalis’ sites which have extreme entry and exit angles.
In addition, Lactalis was also able to achieve significant weight reductions (as well as further contributions to greater payloads
the special features that are helping us get through days, weeks and years of good operations.”
According to Andrew, the attention to each and every crevice of the trailers’ design has already paid off in the on-road performance of the units deployed so far.
“We saw repair and maintenance spend drop by 38-odd per cent once we got a full fleet coming on board,” he says. “We’ve been able to maximise our payload so that we can increase the weight carried per load, which has reduced the number of trips taken each week. We’ve also seen a dramatic reduction in fuel spend based on the efficiencies of the fridge motors on the trailers.”
As a result, Andrew says the trailers are paramount to Lactalis and it getting its products to the market.
“If we didn’t have a strong, reliable fleet, we wouldn’t deliver,” he says. “Our KPI is
on-time delivery (OTD), and our national OTD sits at 96.3 per cent for the last month which is really strong. We’re sitting at about 99.8 per cent for our Queensland operations and NSW and Victoria are in the high 90s, based on a good, stable fleet delivering the product.
“We’re not seeing fridge failures, product temperature abuse or anything which would cause a disruption to our supply chain. So, that level of performance and consistency is paramount to us building trust within our network and with our customers, and maintaining that through having a good, solid trailer fleet.”
For Lactalis, safety is a huge priority. As Andrew puts it, whether workers are a cleaner or a truck driver, there is safety system in place to ensure they get home in the same manner that they arrive at work in. Scully RSV, in this regard, has been vital to Lactalis.
“Part of that is having the right equipment to do the task well and ensuring that the equipment we provide our people with is designed specifically for the task and has all of the right features to complete the job safely,” he says. “Our trailer fleet is exactly that. So, as a partner in that space, Scully RSV has really come on board for the journey.”
Contact
Scully RSV
Ph: 1800 728 559
Web: www.scullyrsv.com.au
For three decades, Rentco has empowered businesses across Australia’s transport industry by providing high quality rental transport equipment that they can rely on.
Thirty years ago in April of 1994, Rentco commenced its business in Kewdale, Western Australia. Initially focused on supplying trailers to the agricultural industry, the company quickly expanded to meet the growing demand for a diverse range of rental products.
Through its commitment to compliance, reliability and investment in high quality equipment and technology, Rentco has established itself as a key player in the heavy duty truck and trailer industry.
“It all started with a business that wasn’t doing very well,” says Rentco founder and Managing Director, Bob Shier. “We bought some equipment and rebuilt the business back up to a reasonable size, and it just kept growing. The more equipment we added, the more the business expanded – especially along the east coast. This growth prompted us to go nationwide.”
Bob attributes much of Rentco’s success to this strategic move. While WA wasn’t particularly rental-orientated, Bob says, the east coast was more receptive to rental businesses.
“Once we expanded to the east coast, we found a favourable market with several small rental companies already in operation,” he says. “It was a good opportunity for us to join in.”
Opening branches in Queensland, New South Wales, Victoria, Darwin, Townsville and Adelaide allowed Rentco to gain valuable insights and grow into a prominent national rental company.
“Moving to the east coast was a significant step for us,” Bob says. “We learned a lot in the early days.”
Rentco’s unique business model, which Bob says was relatively new to the Australian market at the time, also contributed to its success.
“We bought equipment based on job needs rather than waiting for leases,” he says. “We made equipment available like in the construction equipment industry, ready for immediate use.”
Over the past three decades, Rentco has continued to adapt and remain
competitive. Increasing volumes and deep knowledge of equipment have been key to its strategy.
“We don’t just rent equipment, we understand what our clients need and have become a solutions provider,” Bob says. “Rentco will continue to grow while adopting better practices in the rental market.”
As part of its expansion, Rentco plans to upgrade several branches along the east coast to handle more equipment. The company is also closely monitoring the electric vehicle market.
Rentco also recently acquired its first twelve fully electric terminal tractors, and Bob is keen to explore further opportunities in this area.
“We’re watching the electric vehicle market closely,” he says. “While Australia isn’t fully ready for heavy-duty electric vehicles yet, we’re watching, learning and prepared to expand when the time
is right.”
Additionally, strategic fleet acquisitions are a possibility for Rentco.
“If there are fleets in need of management, we can take on specialised units to help them run their business better,” Bob says. “We already manage fleets for our customers.”
Looking ahead, Rentco aims to continue contributing to Australia’s transport sector by sharing the knowledge it has accumulated over the past 30 years.
“We keep up with new concepts, rules and laws, and we pass that information on to our clients,” Bob says. “It’s a big achievement, starting from nothing. We’re very happy with the business and eager to see it grow.”
Contact
Rentco
Ph: 08 9353 9999
Web: www.rentco.com.au
B-DOUBLE DROP DECK CURTAINSIDER
• Full mezz deck
• Hanging gates, toolboxes & provision for tow coupling
• Locally supplied curtains
B-DOUBLE FLAT DECK CURTAINSIDER
• Rear doors
• Gates, toolboxes & provision for tow coupling
• Locally supplied curtains
45’ Drop Deck with BiFold Ramp
• 12V Power Pack
• 3 Way Twist locks
• Machinery tie-down points in floor
40’ DROP DECK SKELETAL TRAILER
• 3 way twist locks
• Dangerous goods rated
• Container tilt airbag fitted
13.7-21.5m Extendable Flat Top
• 3 Way Twist locks
• Pneumatic warning flags
• Provision for tow coupling
40’ 3 WAY SKELETAL
• Standar & lightweight designs
• Side loader pads
• Provision for tow coupling
• CIMC has a long term commitment to Australia by investing in infrastructure to provide high quality products, support and service.
• Local production capacity for Semi-Trailers and Tankers with CNC cutter, welding machines and start-of-the-art heated paint shop.
• Comprehensive parts store stocking genuine CIMC parts, along with additional OEM sourced items.
• Dedicated service & repairs workshop.
• Total site area 51,000 sqm, with a 13,000 sqm workshop.
Melbourne CIMC TRAILERS 1300 202 462
Whitfield Blvd, Cranbourne Brisbane CIMC TRAILERS 0423 795 649 68 Tile Street, Wacol Perth GTE 08 9352 4000 159 McDowell Street, Kewdale
The Newell Highway is a major road connection between Queensland, New South Wales and Victoria, and for freight operators, it is a direct link to getting products from warehouse to market. The highway is the longest of its kind in NSW, stretching over 1,060 kilometres from the Victorian border to the Queensland border, yet for many is notorious due to its rough surfaces.
Market Express, a family-owned transport and logistics company based in Leeton, NSW, often travels along the Newell Highway in its operations of carting frozen and general freight between Leeton, Brisbane and Sydney – its fleet of quadaxle trailers drive through the route twice a week, averaging around 5,500 kilometres for both times.
Although, by specifying BPW Transpec axles and suspensions as standard on all of its trailers, the business is able to ensure that its products get to their end destination in the same condition they leave Leeton in.
“By using BPW Transpec axles and suspensions, we get better wear and tear, our maintenance costs are lower and the product in the trailers isn’t damaged, meaning we don’t have any extra insurance costs,” says Market Express Director,
Ralph Ierano. “At the end of the day, in the transport game – where our profit margins are under single digits – you’ve got to do whatever you can to differentiate yourself to your competitors.
“The number one thing is look after your customer’s product. If you can get your product to market and to customers in good condition, they’re going to keep using your services.”
For Market Express, this has been seen through the loyalty of its customers who have stayed with the business since it began almost 50 years ago.
“We’ve got customers that have been with us since day one,” Ralph says. “Next year, they’ll have been with us for 50 years. That just speaks for itself. If you pay a little bit more for the products you use and you get the right results out of the equipment, you’ll get clients looking after you.”
Market Express first started out in 1975 carting fruit and vegetables. The business was started by Ralph’s brother Mick, who thought farming was a bit slow at the time and decided to buy a truck and cart produce for the market.
Ralph joined his brother four years later in 1979 and purchased two new trucks, and from there, things began to evolve for the business. After a short stint with
a Canberra-based transport company in 1983, the brothers went back out on their own and focused on doing work for a couple of core growers until the time for more fleet equipment arrived.
“We started to look at quad-axle trailers in 2015,” Ralph says. “We didn’t want to go to B-doubles because our work was predominantly too many pick-ups and drops. It was hard enough getting drivers to do that sort of work with single trailers, let alone B-doubles, so that’s why we looked at quad trailers.”
Ralph and Mick went on to purchase their first quads and have now accumulated 20 of them.
The latest quad additions are two twin tandem split configurations from Lucar which are operating on BPW AL2 AM-D30 air suspension with 10/285 PCD drum brake axles and BPW steer axles in the first and fourth axle rows. The brake control equipment is a BPW Transpec Electronic Braking System (EBS) with the added option of ‘tail-guard’ reverse sensors.
“We spent three to six months working on the design and engineering of them, and we got the first ones on the road three months ago,” Ralph says. “The drivers think the split configurations are better than the closed quads. They ride better which
is better for the freight, so it’s a win-win situation. At the end of the day, if your product rides better it’s going to have less damage and you’re going to have less complaints from customers.”
Market Express was first introduced to BPW Transpec through some secondhand trailers Ralph and Mick purchased in the early days which came with its axles and suspensions. They were both impressed with how the units handled with the products, and so when it came to purchasing more trailers, they carried the components over.
That was over 20 years ago now, and the fleet has stuck with BPW Transpec for every order since.
“We’ve always preferred BPW Transpec,” Ralph says. “They’re a bit more expensive, but they are a lot better to run with less hassles. We find that they’re easier to work on and you get better wear and tear out of them.
“The old saying is you get what you pay for. They’re just a better option because they’re a bit more heavy-duty. So, at the end of the day, even though they might be five to 10 per cent dearer, you get that back
in your maintenance costs and additional running out of them.”
Aside to the quality of the product, Ralph has found BPW Transpec’s aftersales service and support to be highly advantageous. As he explains, BPW Transpec regularly visits and sends its trainer and consultants out to Market Express’ warehouse to conduct training programs, and by helping his mechanics understand the axles and suspensions it makes it a lot easier for them to be maintained.
But ultimately, choosing BPW Transpec time and time again has always come down to the success Market Express has seen with the product.
“If you keep the customer happy and give them the service that they want, they’ll keep coming back to you,” Ralph says. “If you keep damaging their product, they’re going to look for an alternative.
“If you have increased productivity, less damage and lower maintenance costs, you can’t get much better than that. And that’s what we find with BPW Transpec.”
Contact
BPW Transpec
Ph: 03 9267 2444
Web: www.bpwtranspec.com.au
Australian trailer builder, LUSTEC, is utilising a complete fit-out of Fuwa K Hitch axles, suspensions and components to launch its new range of side tippers.
LUSTEC is an Australian business with an extensive history in the local trailer manufacturing industry. On the back of family-owned and operated business, Lusty, LUSTEC emerged and has become renowned for designing and building heavy vehicles of the highest quality.
“I started building low loaders with my father, John, back in 1996 and I’ve been building them ever since,” says LUSTEC owner, Chris Lusty. “I’ve been in the industry since then and I’ve won design awards for major Australian trailer manufacturers.
“In 2019 I decided it was time for me to have a crack myself, and I’m proud of where I’ve come from. I’m the third
generation of the family and I still work closely with my father.”
While low loaders are the main types of trailers which Chris has specialised in, LUSTEC is now entering a new venture with side tipper models.
“One thing about low loaders is they just don’t wear out – the first one that my father built in 1984 is still on the road,” he says. “But, we’re moving into side tippers now.
“We were looking for a product range with a little bit more turnover and side tippers seemed to be the best option for us. Side tippers were something I wanted to add to my range. With changes in the market, especially along the east coast,
I see a huge opportunity for them.”
Chris and the team started designing their new side tippers this time last year, and the first ones have now been built and are ready to go. Over the next couple of years, Chris says there’s going to be a heavy push to get them off the ground.
Using Chris’ lifetime of experience in designing and manufacturing classleading trailers, the cutting-edge steel body side tippers are being crafted with precision engineering and innovation, and like all of LUSTEC’s trailers, will be made up completely with Fuwa K Hitch components.
The trailers themselves were designed
with a distinctive body to incorporate a functional and streamlined look. They feature a unique hinge design to increase door speed while also allowing the hydraulic cylinders to sit vertically, resulting in more room in the tipper bodies.
LUSTEC also spent a lot of time to ensure the trailers would be built with serviceability in mind, leading to less downtime for maintenance and repairs once put into action.
“Most side tipper designs have a lot of hoses everywhere, but I wanted to be able to run cat tracks and just tidy everything up,” Chris says. “So, we’ve managed to tidy all of our lines up and make them look a lot cleaner.”
The running gear on the trailers includes Fuwa K Hitch suspension, axles, turntables and ballraces – giving Chris the confidence to launch the new product range in a competitive market.
“Fuwa K Hitch is our base product, it’s what we spec all of our trailers on,” he says. “We do give customers the option for other products, but Fuwa K Hitch is our standard one and what we like to use in all of our designs from our air bag trailers through to our hydraulic and spring suspension trailers.”
Fuwa K Hitch’s 19.5” drum brake axles, steer axles, disc brakes, KT suspension, fifth wheels and landing legs have always been heavily featured on each of LUSTEC’s trailer builds. Although its 20” drum brakes and Weweler air suspension will be dedicated to the new side tippers, joining the rest of the standard components.
“We started using Fuwa K Hitch when they first started in Queensland, which was around 20 years ago,” Chris says. “They’ve been good value to us ever since.”
During this time, price and service, according to Chris, have been driving factors.
“Fuwa K Hitch’s price in the market is great, and their service to us has always been excellent,” he says. “I like a lot of their designs and the way they do things, especially with their forged axles, rigid arm designs and KT suspension which work well with our trailers. Their turntables are also very robust.”
By relying on Fuwa K Hitch for all of his trailer component requirements over the years, Chris’ business has gained significantly.
“As part of our relationship, Fuwa K Hitch has supplied us with information which has allowed us to get all of their designs into our trailers,” he says.
“Having that information and being able to get it into all of our models just makes thing work seamlessly. We’ve seen this with the steer axles – we’ve got a lot of moving parts, but we’ve been able to make sure everything works without any interferences.”
“There’s also been a couple of projects, especially on our rows of eight trailers, where Fuwa K Hitch designed products for us to fit in our trailers. We have fitted prototype suspension arms in our trailers for them over the years as well.”
Little to no warranty issues has also been an advantage and the main reason
LUSTEC continues to use Fuwa K Hitch.
“The products are standing up to what people ask them to do,” Chris says.
“Ninety per cent of people are extremely happy with their gear.
“Fuwa K Hitch has grown to be a market leader in the axle space. Through their product being the most used axles in our trailer builds, they’ve proven to be reliable with great spare parts support. So, the partnership has worked well for us. The fact that Fuwa K Hitch is local, has products in stock and can cater to us is beneficial.”
Contact
Fuwa K Hitch
Ph: 07 3372 2223
Web: www.khitch.com.au
GP Truck Products is taking another crack at uncompromised performance with its latest innovation, CLIPLOCK , which will be arriving very soon.
GP Truck Products is a Melbourne-based supplier/manufacturer of air brake fittings and truck and trailer components ranging from Suzi coils to trailer couplings, air brake filtration systems and associated products. Since forming in 2002 on the back of General Pneumatics, the business division has expanded time and time again and is now recognised within the market for its commitment to offering unique and high-quality products.
“We’ve always been an innovative company,” says General Pneumatics Managing Director, Joe Borg. “We design
products and are very selective as to what we take on to make sure that they are fit for purpose.”
GP Truck Products’ latest innovation, CLIPLOCK, is an innovative trailer coupling which was specifically designed to ensure positive and secure connections of trailer airline couplings while preventing unintentional decoupling.
CLIPLOCK features a unique two-stage locking mechanism in the form of an optional stainless steel locking clip and locking groove, as well as a unique bright yellow cable which acts as a visual lock
indicator. Connected to the locking clip, the visual lock indicator makes it easy for operators to quickly notice potential connection issues – if the yellow cord and locking clip is dangling, it means that the coupling may not be securely connected.
In addition, if the locking clip cannot be inserted into the locking groove of the coupling, it means the male and female couplings haven’t been connected properly. CLIPLOCK, Joe says, is therefore an added layer of protection for fleets.
“We’ve machined a special groove into the coupling to accommodate the innovative locking clip that stops the locking collar from coming back and releasing,” he says.
Ultimately, Joe says this puts the minds of end users at ease.
“We’re bringing this product to the market because of unintentional coupling disconnections,” he says.
As Joe reveals, CLIPLOCK will be arriving in the market this month, with several organisations already enquiring and testing to make it a standard feature across their fleets.
Contact
GP Truck Products
Ph: 03 9580 1811
Web: www.gptruckproducts.com.au
Rentco, the first Australian Rental Fleet to bring to market the R/H Drive fully electric terminal tractor, the long awaited Terberg TY200-EV.
After testing the first 12 units to be delivered into Australia we are very happy with the results and these have proven to be the most comfortable carbon free emission option we can deliver to market.
The first four units were delivered in July of this year and have been tested by some of the counties largest freight companies in some of the busiest depots we have in Australia, with another 4 arriving this year and the remaining 4 will be delivered in Feb 2024. These 12 full electric terminal tractors will bolster what is already the largest terminal tractor fleet in the country.
Rentco takes its responsibility to a more sustainable future and reducing carbon emissions very seriously and is leading the way by delivering a ready to go true 100% electric terminal tractor to Australia’s transport industry. For Terberg Rental enquiries, contact Paul Scott: Tel: 0407 456 463 Email: paul.scott@rentco.com.au
Bass Strait Transport, under the umbrella of Tasmania’s De Bruyn’s Transport, has been operating since 1998 with transport and freight forwarding solutions in and out of Victoria.
The group maintains a fleet of over 300 curtainsiders, skels, tankers and flat top trailers, with 98 per cent of the units being fitted out with JOST products such as fifth wheels, ballraces, landing legs and kingpins.
De Bruyn’s Transport Managing Director, John DeBruyn, who has been with the business for over 40 years, has seen the JOST products applied as standard himself for a quarter of a century.
“We’ve used JOST products for at least the last 25 years,” he says. “They’re good products which work well and are safe, so we standardised them.
“Once we get a good run out of something, we stick with it. We’d have to have a really big disaster for us to change.”
From a maintenance perspective, standardising JOST equipment has
kept Bass Strait Transport’s costs down due to familiarity with the product –the employees, as John explains, are working with the same sort of equipment week in and week out and have therefore become very efficient in this area.
“We’ve got a substantial fleet of trucks and trailers and we do all of our own maintenance,” he says. “So, we really focus on standardisation to make sure that the maintenance task is really efficient. Our workers are also trained by JOST, meaning they are right across the products.”
This also benefits the drivers as every truck and trailer in the business is exactly the same.
Bass Strait Transport’s latest addition to the fleet is a B-double drop deck curtainsider from Barker Trailers. The unit, spec’d with mezzanine floors to maximise cubic capacity, carries general freight from Melbourne to Hobart and is one of eight identical combinations at the company.
“They perform really well,” John says.
“Together with the JOST products, we haven’t had any problems with them at all. They’re maintained and we get a really good run out of them.”
Like Bass Strait Transport, Barker Trailers also standardises JOST’s fifth wheels, landing legs and kingpins on all of its builds. It does this to maintain the all-round reliability they have been recognised for over the last five decades.
Celebrating 50 years in the industry this year, Barker Trailers has consistently demonstrated a strong commitment to the transport industry, and in saying that, it has earned a reputation for constructing high-quality products as part of its unwavering dedication to ensuring every trailer manufactured meets the highest levels of excellence.
Part of Barker Trailers’ success comes down to its long-term partnership with JOST. JOST is renowned for its varying top-tier transport products, and for over 30 years, its fifth wheels, landing legs and kingpins have been standard fitment on all of Barker’s trailers – a testament to
their reliability and superior quality.
“I think quality and durability will always have a place in the market, and JOST products have that reputation of high quality which aligns with our values,” says Barker Trailers Managing Director, Scott Barker. “I have always valued the responsiveness and knowledge of JOST, and from a customer perspective, a lot of people specifically ask for JOST fifth wheels.”
Barker Trailers’ partnership with JOST is built on mutual trust and years of successful collaboration. According
to Barker Trailers Procurement and IT Manager, Russell Thomas, its components enhance the overall quality and reliability of Barker Trailers’ combinations, allowing the business to offer top-notch products to its customers.
“Our customers praise JOST products for their reliability, performance and longevity,” he says. “The high standards upheld by JOST complement the quality of Barker Trailers, adding significant value and contributing to customer satisfaction and loyalty.”
As Barker Trailers celebrates 50 years of excellence, it commends JOST, a company that has delivered for it in more ways than one for decades.
“We know that if our customers have an issue with a JOST product, which is very rarely the case, they will easily be able to get the part that they need,” he says. “Then, and more importantly, they will be able to spend more time on the road and making money.
“JOST’s reliability reflects well on us as a manufacturer of quality products which partners with a supplier that shares the same unwavering vision.”
Another standout aspect of Barker Trailers’ dealings with JOST has been the exceptional responsiveness and service received.
“They always answer the phone and react quickly to any issues, even when the fault lies with us,” Russel says. “This level of support ensures that we can deliver the best possible service to our customers.”
As a family and a team, Barker Trailers takes immense pride in its work.
Choosing JOST as its preferred supplier, Scott says, has demonstrated that in the long run.
“JOST is very aligned with us in the fact that their equipment is able to cope in just about all conditions,” says Barker Trailers Data and Cost Analyst, Ross Barker. “With JOST, there is great versatility because their products are suitable for all of our applications. We don’t need to alternate between suppliers depending on the design because they usually have a ready-made solution.
“Their product is well-regarded, and because of that, we know we’re quoting superior equipment at a price point that keeps us competitive in the market.”
Ross says JOST’s product range is simple yet diverse enough to cater directly to Barker Trailers’ needs. In addition, its national presence means Barker Trailers and its customers such as Bass Strait Transport can rely on JOST at all times.
“Our long-term partnership with JOST exemplifies our commitment to delivering the best products and services to our customers, ensuring a bright and successful future for both companies,” he says. “We look forward to continuing our tradition of innovation and strong partnerships.”
Contact
JOST Australia
Ph: 1800 811 487
Web: www.jostaustralia.com.au
In the road transport industry, maximum payload every trip means the difference between a profit or a loss. For operators and fleets, ensuring that payloads are optimal is beneficial for increased efficiencies and therefore productivity across the board.
In this area, accurate on-board weighing systems or weighbridges are advantageous. Tramanco, a family-owned Brisbane-based business established in 1975, manufactures a range of Static and On-Board Mass (OBM) weighing systems and specialises in this field precisely. Its flagship electronic weighing and data logging systems, particularly CHEKWAY and KWIK-CHEK, are engineered to allow operators to weigh any type of vehicle regardless of their make, model or size.
“Tramanco’s systems are internally monitored for accuracy, damage and tampering every 30 seconds and any discrepancies are reported in real-time with GPS location and speed,” says Tramanco owner, Roger Sack. “So, they allow the driver to confidently load to maximum payload every trip by relying on the displayed weights they are seeing.”
Both systems share common
components and can be used with load cells, air and hydraulic pressure transducers, bending beam transducers and deflection or movement transducers of any type.
Tramanco prides itself for having quality Australian products which, from day one, were designed for Australian roads, loads and conditions. It also writes its own software and, in addition, has several extra programs for a variety of operations such as load/deliver to monitor different products as they are being loaded and then unloaded.
Tramanco also provides 100-per-cent spare parts back-up, as well as immediate service reports for mass quality records which are unique to CHEK-WAY.
“This means the operator can be assured that our scales are accurate, and a problem can be diagnosed in real time and then scheduled for repairs,” Roger says.
Without a reliable OBM system or weighbridge to count on, operators are often left guessing what their loads are. So, what do you do if you are overloaded on one trailer or worse, underloaded on both?
“Remember, only six tonnes of the total load is your profit if you are fully
loaded to 60 tonnes,” Roger says. “What happens if you are down say, three tonnes? Do you just go and hope you don’t get pulled over and weighed, or do you tip another two or three tonnes off the overloaded trailer so that you are just running for the experience?
“The same applies to small trucks such as a 4.5-tonne 4x2 as well – it is just the size of the loss which is involved in the transaction.”
Size, as Roger notes, does matter. To ensure that your payload on any size vehicle remains legal, constant and profitable on every trip, the solution is to invest in quality weighing systems like the ones available from Tramanco.
“Accuracy, longevity, and quality are never accidents, they are the results of intelligent effort,” he says. “Quality is that indefinable element which can never be inserted into a product once it has been made, or into a service once it has been given. Nor can it be removed. So always buy quality as it is the only thing that lasts.”
Contact Tramanco
Ph: 07 3892 2311
Web: www.tramanco.com.au
Skel trailers
Evolution side tippers
Road train dollies
trailers side tippers train dollies
Flat tops, drop decks
Flat tops, drop decks and extendables
Deck wideners and extendables
End tippers, bulk and TaREX quarry bodies
End tippers, TaREX quarry bodies
Coldcore refrigerated and dry vans
Coldcore dry vans
Etnyre live bottom trailers
Etnyre
Titan walking floor and belly dumper trailers
Titan floor and dumper trailers
PBS specials: super quad & super triple
PBS specials: super quad triple
being almost zero growth in new registrations, it’s clear that demand is keeping up.
ARTSA-i Data believes there’s still a chance to achieve the heights Australia’s manufacturing industry saw in financial years 2022 and 2023 by the end of this year. If the second half of 2024 maintains the momentum experienced during the first quarter, it claims we will be heading towards a similar calendar year performance to the last one.
That being said, we bring to you the 2024 E-Plas Rigid Body Builder Showcase, a list of all the OEMs in this space with heavy and medium rigid manufacturing capabilities which will be playing a role in hopefully bringing this year’s data back up to the levels experienced in recent times.
auSTATE Services
15 Swaffham Road
Minto NSW 2566
Ph: 02 8795 0600
Web: www.austateservices.com.au
Byrne Trailers
278 Hammond Avenue
Wagga Wagga NSW 2650
Ph: 02 6923 7300
Web: www.byrnetrailers.com.au
Cain Equipment Australia
6/102-128 Bridge Road
Keysborough VIC 3173
Ph: 1800 462 246
Web : www.cainequip.com.au
CE Body Builders/Major Motors
57 Wandeara Crescent
Mundaring WA 6073
Ph: 08 9295 6636
Web: www.cebodybuilders.com.au
CIMC Vehicle Australia
20 Whitfield Boulevard
Cranbourne West VIC 3977
Ph: 03 9797 2100
Web: www.cimc.com.au
Cook’s Body Works
144 Cochranes Road
Moorabbin VIC 3189
Ph: 03 9555 4166
Web: www.cooksbodyworks.com.au
Byford Equipment
Moama Business Park, Cobb Highway
Moama NSW 2731
Ph: 03 5482 0610
Web: www.byfordequipment.com.au
Custom Transport Equipment
73 Wellwood Road
Drouin VIC 3818
Ph: 03 5625 5408
Web: www.ctequip.com.au
Elphinstone Engineering
36 Tasman Highway
Triabunna TAS 7190
Ph: 1800 030 019
Web: www.elph.com.au
Eurocold
100 McPhee Drive
Berrinba QLD 4117 07 3569 2858
Web: www.eurocold.com.au
Fibreglass Transport Equipment
9 Healey Road
Dandenong South VIC 3175
Ph: 03 9794 7466
Web: www.fte.com.au
Furina Truck Bodies
13 Broadhurst Road
Ingleburn NSW 2565
Ph: 02 9829 2572
Web: www.furinabodies.com.au
Scully RSV
88 Grindle Road
Rocklea QLD 4106
Ph: 1800 728 559
Web: www.scullyrsv.com.au
Shakanda Engineering
16-18 Sanders Street
Korumburra VIC 3950
Ph: 03 5662 3144
Web: www.shakandaaustralia.com
Shephard Transport Equipment
31 Arc Place
Larapinta QLD 4110
Ph: 07 3711 0400
Web: www.ste.com.au
Sloanebuilt Trailers
21-33 Dunn Road
Smeaton Grange NSW 2567
Ph: 02 4647 4800
Web: www.sloanebuilt.com.au
Southern Cross Trailers
9-15 Manthorpe Street
Dry Creek SA 5094
Ph: 08 8405 7600
Web: www.scteg.com.au
Starworx
5A Westwood Drive
Ravenhall VIC 3023
Ph: 03 9958 9750
Web: www.starworx.net.au
The Drake Group
19 Formation Street
Wacol QLD 4076
Ph: 07 3271 5888
Web: www.thedrakegroup.com.au
Tieman Tankers
180-186 Northbourne Road
Campbellfield VIC 3061
Ph: 03 9469 6700
Web: www.tieman.com.au
Transport Refrigeration Services (TRS)
3 Distillers Place
Huntingwood NSW 2148
Ph: 1800 317 510
Web: www.trsservice.com.au
Vawdrey
1-53 Quantum Close
Dandenong South VIC 3175
Ph: 03 9797 3700
Web: www.vawdrey.com.au
Hey legend, we're Dan and Ed, Co-founders and Directors of TradeMutt and TIACS. After launching our workwear company, we saw the need to break down barriers preventing Australians from accessing mental health counselling.
We met on a building site in Brisbane, both starting work for a builder on the same day. Our bond formed over laughs and tackling a tough job, which became crucial when Dan received heartbreaking news about his best mate's suicide. This deeply affected both of us, which led to Ed stepping up as my main support.
In our conversations, we realised that mental health discussions were too heavy and hard to approach. That's why we decided to change the conversation by using job site safety gear to start discussions. This fresh approach aimed to make talking about mental health simpler and less intimidating, led to the creation of TradeMutt.
Then in 2020, we took things up a notch and launched TIACS. A professional, confidential and free mental health counselling service for the blue collar community and their loved ones.
Ed & Dan Founders
TIACS provides professional, free text and phone mental health counselling to tradies, truckies, farmers, blue collar workers and their loved ones Australia wide.
A new report detailing what the biggest challenges the US will face when transitioning its heavy vehicle to fleet to zero emissions has been released at the same time transport industry leaders are weighing-in, and it seems to come down to dollars.
In what could be described as a candid speech at this year’s Advanced Clean Transportation expo in Las Vegas, JB Hunt Transport Services President, Shelley Simpson, told attendees that it is estimated the United States would have to increase its electricity production by 40 per cent to charge all registered vehicles in the country.
“Who’s willing to give their electricity up to power their home, for us to charge our entire fleet?” she asked the audience. “Imagine what it would take to power all the electric vehicles in the US, in addition to all the passenger vehicles.”
Simpson reiterated that clean energy is a positive movement that the industry needs, but in order for it to reach its overarching goal of reducing transportation-related emissions, something needs to change.
“We have pressures that we’re all facing, and those pressures are affecting our businesses, our decisions and the future of our industry,” she said. “The reason that we’re feeling this tension is because there’s a misalignment of sustainable technology, policies to regulate emissions and an economic case for incorporating emerging technology.”
According to a recent US study, it is the economic case that Simpson points to that will be the biggest hurdle. The Forecasting a Realistic Electricity Infrastructure
Buildout for Medium- & Heavy-Duty Battery Electric Vehicles report claims that the charging infrastructure required to electrify all medium- and heavy-duty vehicles and charge point operators in the US is expected to cost $620 billion USD.
In addition to this, onsite charging infrastructure for the medium duty segment is forecast to cost $496 billion USD, however heavy-duty vehicles call for more significant infrastructure – an average investment of $145,000 USD as opposed to $54,000 USD per medium duty vehicle.
A further $69 billion USD is needed for reliable on-route charging for high mileage vehicles. Meanwhile, long-haul vehicles would need a dense highway charging network at a cost of $57 billion USD, although this development would be constrained by the capabilities of the transmission grid infrastructure.
Much of the pressure fleets are feeling comes, in part, from a combination of rigid deadlines at both the state and federal levels in the form of the California Air Resources Board’s Advanced Clean Fleet rule and U.S. Environmental Protection Agency’s latest emission standards for heavy-duty vehicles. In response, the report highlights the need for greater cross-industry collaboration in regard to electrification.
It recommends a phased electrification
approach with an initial focus on the medium-duty segment, which would then be followed by technology and infrastructure improvements for heavyduty and long-haul.
The report also found that while medium-duty vehicles will face fewer roadblocks, economic and operational constraints make electrification very challenging for the heavy-duty segment. Furthermore, the study outlined the significant improvements in battery range and charging infrastructure capabilities that would be needed to support a path for the electrification of long-haul vehicles.
Roland Berger Senior Partner, Dr Wilfried Aulbur, said fleets will need to look at how they operate and adjust, industry and government will need to cooperate, and there needs to be an ‘openness’ to alternative technology paths to decarbonising the heavy-duty segment.
“It also is clear that an industry with a yearly turnover of about $800 billion USD and a profit margin around 5.0 per cent cannot invest $620 billion USD without financial support or a significant increase in freight rates,” he said.
For its part, JB Hunt recently announced an ambitious goal to reduce carbon emission intensity by 32 per cent by the year 2034, focusing on alternative power equipment, biogenic fuel and improved fuel economy.
Queensland-based transport company, Jarratt Transport Solutions, was started in February of 2011 by Phil Jarratt and his wife, Jodie, after they sold their first transport company in 2007 and returned to the market following demand from their previous clients.
Carrying over their motivation for safety, compliance and customer service, Phil and Jodie began once more with an even stronger focus on providing complete transport solutions around Australia.
Just recently, Jarratt Transport Solutions completed another fleet expansion round with the delivery of four new Kenworth T610SAR prime movers for B-triple road train applications.
The new trucks join an identical fleet of eight Kenworth T610SARs which travel from Far North Queensland to central South Australia carting cotton, citrus, wind and solar farms freight and power and infrastructure goods.
According to Phil, they have been performing faultlessly in their operations so far.
Pencil in some information on dates and venues of various truck shows, field days and road transport industry conferences both locally and internationally.
Got an upcoming event? Then let us know about it – email editor@trailermag.com.au
September
Western Australia
Newdegate Machinery Field Days 4–5 September
Newdegate, WA
Visit: www.newdegatemachineryfielddays. com/the-field-days
New South Wales
Henty Machinery Field Days 17–19 September Henty, NSW
Visit: www.hmfd.com.au
Victoria
The MHD Mercury Awards 18 September Melbourne, VIC Visit: www.mercuryawards.com.au
Germany
IAA Transportation 17–22 September Hanover, Germany
Visit: www.iaa-transportation.com/en
Victoria
MEGATRANS
18–19 September
Melbourne, VIC
Visit: www.megatrans.com.au
Queensland
Agrotrend 2024 20–21 September
Bundaberg, QLD
Visit: www.agrotrend.com.au
October
Victoria
Elmore Field days 1–3 October
Elmore, VIC
Visit: www.elmorefielddays.com.au
Wandin Silvan Field Days 11–12 October
Melbourne, VIC
Visit: www.wandinsilvanfielddays.com.au