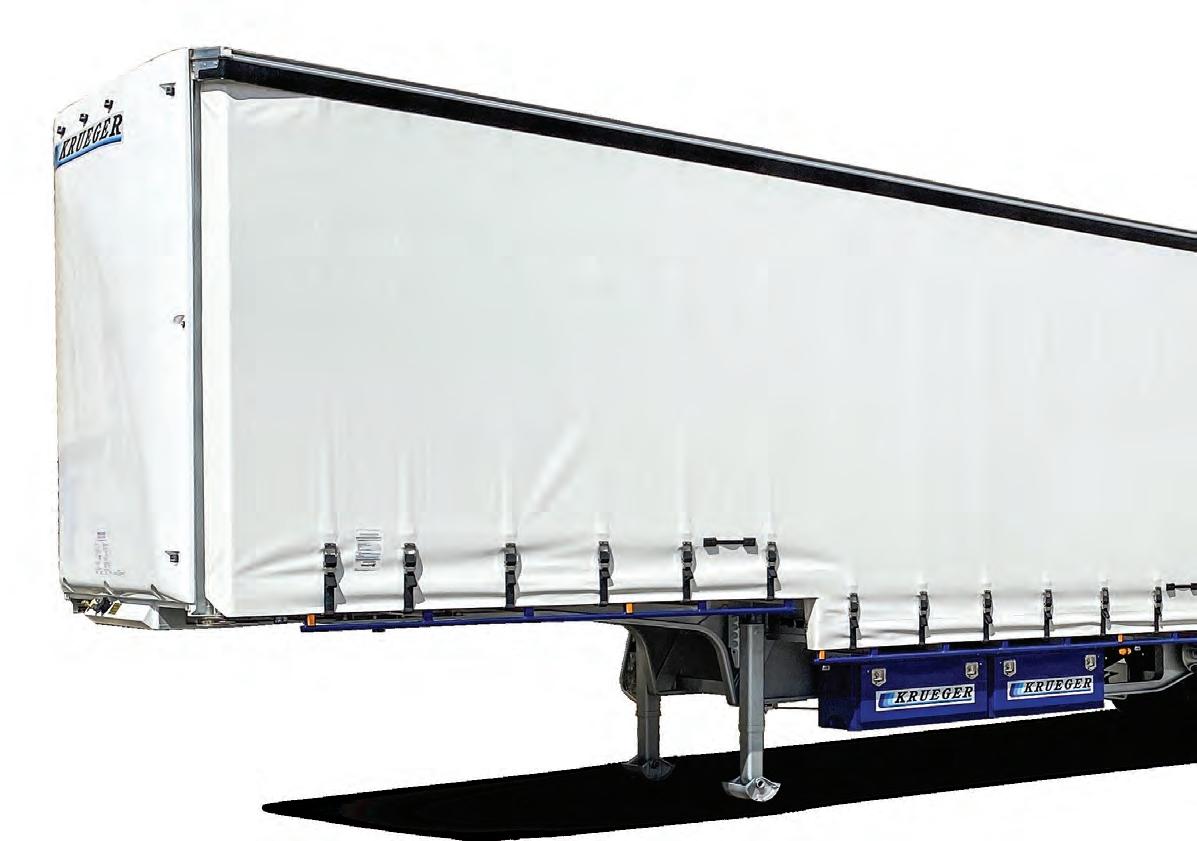
11 minute read
Trailer Builder
Krueger delivers robust Kurtainers for east coast operations
VICTORIAN FREIGHT CARRIER, TRAIANON TRANSPORT, MAINTAINS A MODERN AND RELIABLE FLEET THANKS TO ITS ONGOING INVESTMENT IN KURTAINERS FROM KRUEGER TRANSPORT EQUIPMENT.
A family owned and operated in business in Bacchus Marsh, Victoria, Traianon Transport has supported local industry since 1979. What started as a local beer run with a Bedford has today grown to 15 trucks and a mix of single and B-double trailer combinations. “We provide palletised full load local and intra/interstate freight services to leading Australian businesses ranging from packaging, paper reels, food/ beverage products, racking and other retail products,” says Anthony Traianon. “Our fleet typically comprises single and B-double trailers in mezzanine, straight and drop deck combinations and frequently travel the east coast of Australia (New South Wales, Queensland, Victoria) and South Australia, as well as many regional places in between Mildura (VIC), Laura (SA), Newcastle (NSW), Tumut (NSW), Canberra (NSW) and Sunshine Coast (QLD). We take pride in reliable and quality service always ensuring we deliver a high level of service from booking to delivery.” Since 1998, Traianon Transport has worked with trailer manufacturer Krueger Transport Equipment and uses its Kurtainer models including mezz deck, drop deck and straight deck. The most recent Krueger trailers to join the fleet include a tri-axle 48’ 24-pallet drop deck Kurtainer with load restraint curtains and a tri-axle 45’ 22-pallet drop deck Kurtainer with load restraint curtains. The load restraint technology that Krueger provides is the result of three-plus decades invested in the design and extensive testing and validation of curtain rollers, roof tracks, sliding side posts (a Krueger first) and
Fast Fact
For more than 40 years, Krueger Transport Equipment’s expertise in technical development and manufacturing has resulted in the production of remarkably versatile trailers that deliver peak operational performance.
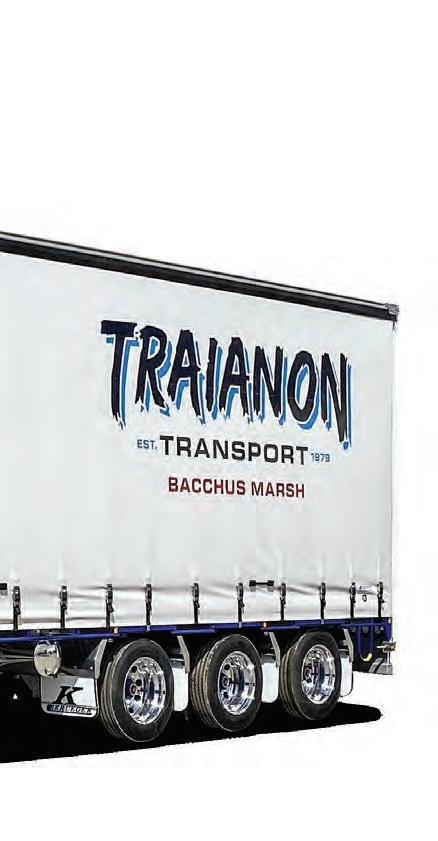
curtain ratchet for superior tension. “Our latest Krueger trailers were purchased to replace some of our old equipment,” Anthony says. “The most important part about investing in Krueger trailers is their quality – they withstand the test of time. Krueger recently refurbished a 2001 build and it is still in our fleet today.” Krueger trailers, according to Anthony, are also easy to use. “They are all round a good quality trailer that never lets you down and if you do need something you never have to wait as their service and parts are outstanding. We can’t fault the workmanship.” To complement its manufacturing capabilities, Krueger also assists heavy vehicle operations with an extensive national support network which includes fixed price servicing, spare parts, refurbishments, smash and damage repairs as well as chassis and body conversions for all trailer types. Krueger also provides full technical service and parts support via a dedicated Australia-wide network. Onsite and emergency vehicle support is also available via Krueger. Lesley says Krueger have been exceptional to work with. “Whether we are speaking with sales, service or parts there are never any problems, even with short notice they are always happy to accommodate. We wouldn’t hesitate to recommend Krueger in any department and we will certainly be using them again in the future.” Anthony defers to Krueger’s team for the first service and for anything the company is unable to do in-house. “It is important for us to support another Australian owned and operated business,” Anthony says. “And to keep these quality trailers being made right here in Victoria.”
Fast Fact
As Krueger produces equipment for a range of applications, from industrial machinery cartage to general freight haulage, fleets can specify precisely what they need and rely on Krueger Transport Equipment to deliver.
Contact
Krueger Transport Equipment 275 Fitzgerald Road, Derrimut VIC 3030 Ph: 03 8331 6100 Web: www.krueger.com.au
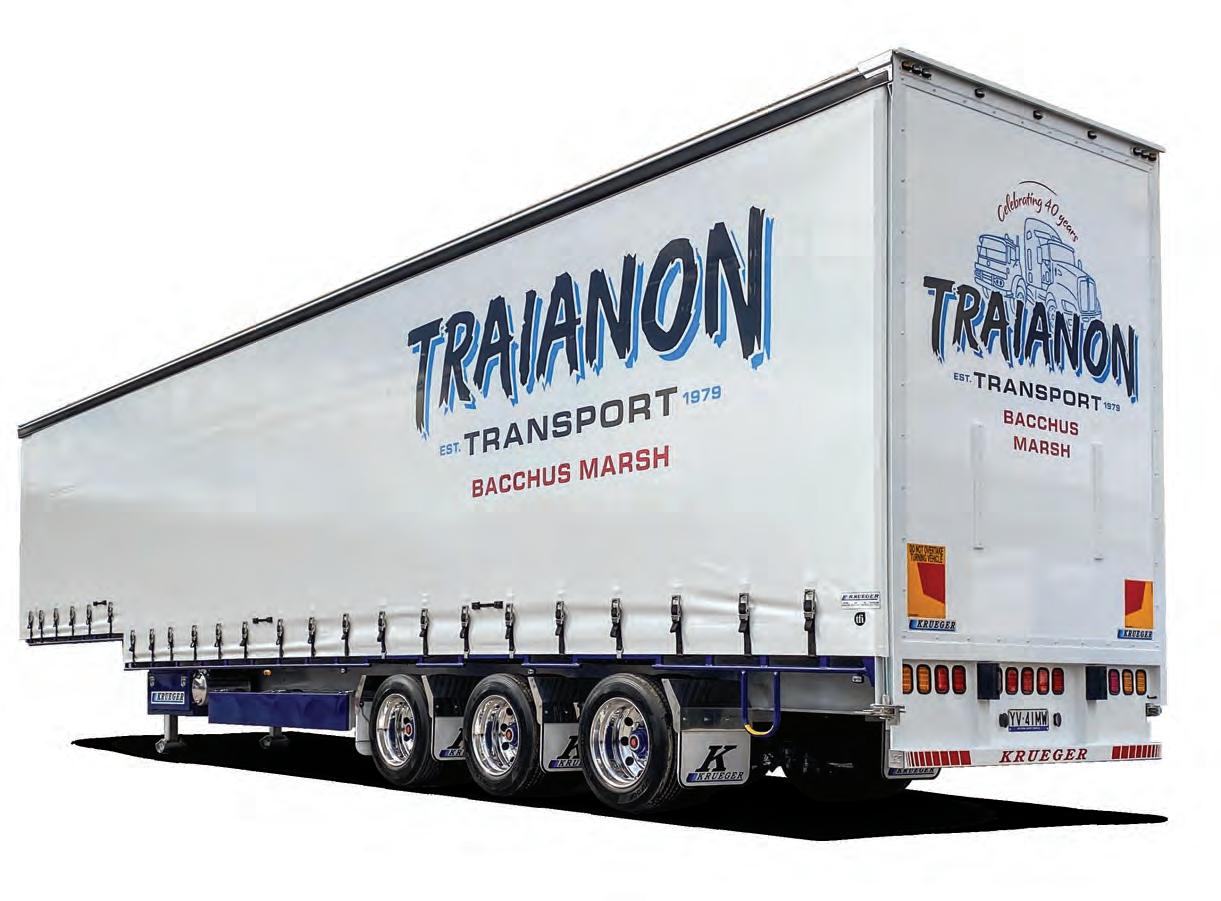
A comprehensive service offering
RENOWNED, THROUGH THEIR BRANDS DRAKE TRAILERS AND O’PHEE TRAILERS, FOR BUILDING SOME OF THE TOUGHEST ON- AND OFF-ROAD TRAILERS KNOWN TO MAN, THE DRAKE GROUP IS KEEN TO GET THE WORD OUT THAT IT ALSO HAS A DEPARTMENT DEDICATED TO THE EXPERT SERVICING, REPAIR AND REFURBISHMENT OF ITS OWN AS WELL AS OTHER BRANDS OF TRAILERS.
While their inherently robust design and construction endows them with a remarkably long lifespan, there eventually comes a time when every Drake Group trailer will require an overhaul to give it a new lease on life. What better place to take it for this type of work than the company that knows their trailers inside out and back to front – The Drake Group itself. The company has a dedicated team of skilled technicians assigned to these tasks, with this department headed up by Branch Manager Service and Repairs, Troy Uhle looking after the east coast and Hugh Markey in the West. Troy has been in the role since the beginning of this year, having taken the reins from long-serving and recently retired Drake Group employee, Steve Collins, who notched up 19 years with the company. “I look after our Wacol (QLD) branch as well as our far-reaching service network which covers all of the eastern states and South Australia,” Troy says. “My Colleague Hugh Markey looks after Western Australia from our branch in Welshpool (Perth) and remote service offerings across the state. “We have preferred repairers in places like Mackay, Sydney and Victoria and we have a field service team that we send to South Australia on a week-on, week-off basis to cater to the needs of our clients in that state.” The Service and Repair division at The Drake Group’s Wacol facility has 12 full-time employees – including three boilermakers, six trailer fitters, an apprentice, a tradesperson’s assistant (TA) and a parts interpreter. The team manages everything from minor services through to complete overhauls, which may involve renewing entire suspension and braking systems before the complete unit is sandblasted and painted. The end result is a trailer that, regardless of its age, is returned to ‘as new’ condition for its owner. Troy mentions that he worked for several months with Steve Collins prior to his
The Drake Group’s comprehensive service offering includes qualified field service technicians and fully kitted out service trucks. retirement to ensure a smooth transition and he says it was a pleasure working with and learning from someone with such a wealth of knowledge. “I had three months working with Steve, which was a great handover period,” he says. Speaking further about his new role, Troy says the company is on a mission to raise awareness of its top-shelf service and repair capabilities that are not restricted to Drake and O’Phee trailer owners. “Most people in the industry are aware of Drake as a trailer manufacturer but our service and repair side is less well known, despite the fact that it has now been running for close to three years.” Prior to forming its own service and repair division, The Drake Group engaged a contractor to manage these tasks, but with the business continuing to expand it was deemed necessary to bring these operations in-house with the formation of a dedicated division. A value-added aspect of the operation that has the potential to significantly speed up the repair process is a service-exchange program recently implemented which entails the stocking of commonly replaced components that have been refurbished and are therefore ready to be fitted to trailers. “We established this system around six months ago, involving the rebuilding of major components like suspension and steering rams which are then put into stock ready for when they are needed,” Troy says. “The chrome plating on the rods eventually reaches the end of its service life after thousands of operating hours in the harshest of conditions, which then leads to seal
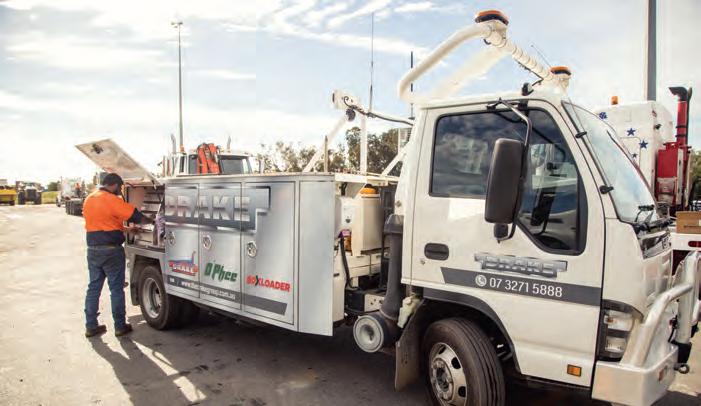
The robust design and build of Drake Trailers allow full refurbishment of older units back to as-new condition.
In addition to repairs and servicing, The Drake Group offers a full refurb service on all brands of trailers.
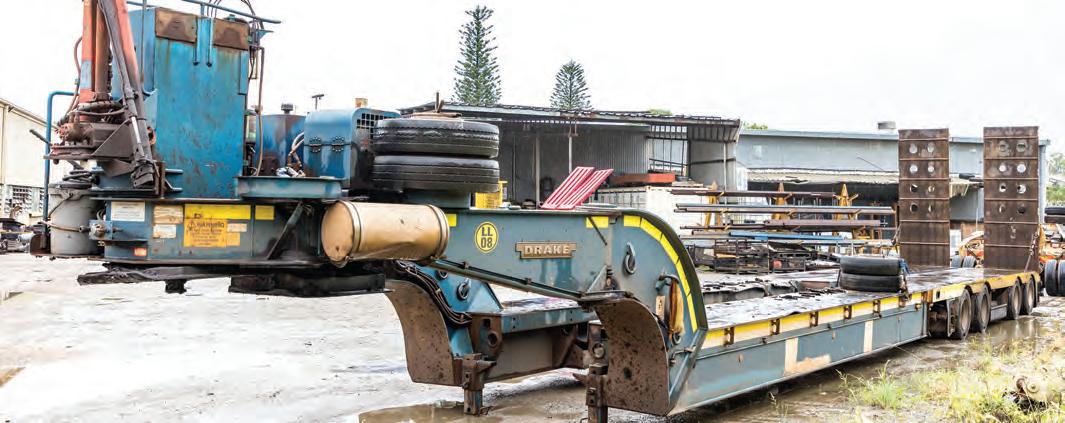
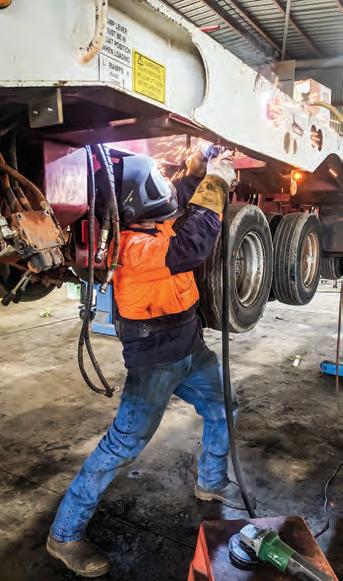
To expedite repair times, The Drake Group now has a service exchange program for components such as hydraulic suspension units. failure,” he explains. “Since the re-chroming process can take up to three weeks, it makes sense to have those parts sitting on the shelf, preassembled and ready to be fitted to the customer’s trailer. Troy explains that the division’s workshop also stocks its own fastmoving new parts such as brake linings and drums that are used on a daily basis. “Having the right stock on hand is critical to our operations due to much of our work being turned around in one or two days,” he says. “We are aiming to increase the volume of our servicing work because of the fast turnaround time in contrast with a full refurb which can take up to three weeks. “We want to get our name out into the marketplace to let people know that we have the expertise and capacity to handle the servicing and refurbishment of their heavy haulage trailers.” Troy explains that plans are afoot for future expansion of The Drake Group’s Service and Repair division, with the current workshop space of 1,000m2 and the same amount of outdoor hardstand area fast being outgrown. “We are aiming to build a new purpose-built workshop with drive-through access to help streamline the processes of servicing and getting trailers in and out in the most timely manner,” Troy says. No doubt, once this is completed The Drake Group will be even better equipped to cater for a considerably larger number of clients in respect to all their trailer servicing, repair and refurb requirements.
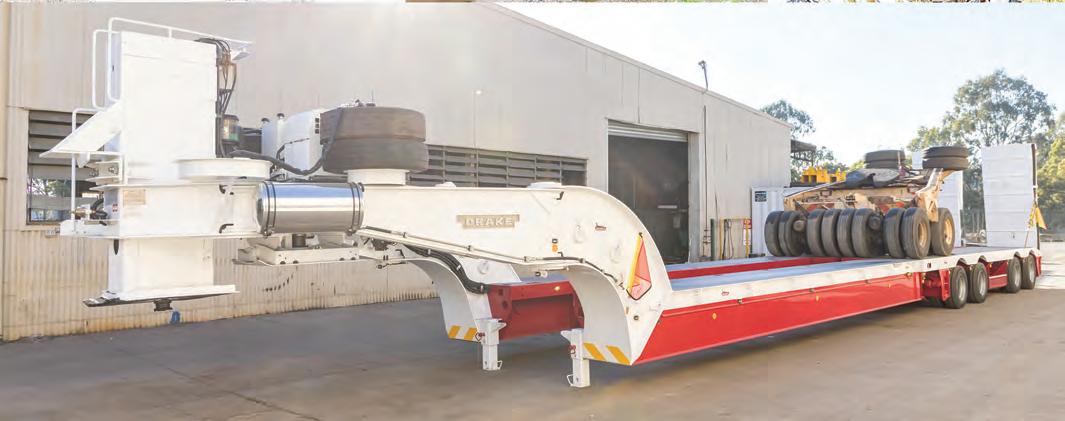
Contact
The Drake Group of Companies 19 Formation St Wacol QLD 4076 Western Australia Branch 95-97 McDowell St Welspool Ph: 1300 240 835 Web: www.thedrakegroup.com.au
The personal touch
FOR MORE THAN A DECADE, WESTERN AUSTRALIAN TRANSPORT SPECIALIST, FREIGHT LINES GROUP, HAS RELIED ON VAWDREY AUSTRALIA FOR EFFICIENT AND RELIABLE TRAILERS WHICH ARE OFTEN SET UP AS POCKET ROAD TRAIN COMBINATIONS AND RE-CONFIGURED FOR OPTIMAL FLEET UTILITY.
In the 1960s, a humble freight company commenced operations in Esperance to Perth. By the 1980s, it established a fuel distribution arm along with fresh fruit and vegetable operations. The business collectively known as Freight Lines Group (FLG) has since expanded into mining, bulk commodities, agriculture and specialised freight, boasting a team of about 210 staff. “The fuel business sold and then Harding Transport was born with the fruit and vege distribution – this evolved over time to the company that I took sole ownership of in 2010,” says FLG Managing Director, Michael Harding. “In 2003, I took over FLG in partnership with Colin Danks and then I purchased Colin’s share around 2010.” Today, the business specialises in general, bulk, express, freezer and machinery freight along with storage and distribution. Over the years, FLG has opened depots in Albany, Geraldton, Kalgoorlie, Ravensthorpe and Esperance – bolstering its presence in regional Western Australia operating alongside its major Perth distribution centre. With a fleet of 140 prime movers and more than 450 trailers, FLG can dedicate equipment for the length of a contract or supply as required for loads as they are scheduled. All trailers, drop decks, curtainsiders, mill ball trailers and skels for mill ball containers, reefers and bulk trailers ride on airbag suspension. “We have worked with the team at Vawdrey Australia for about 12 years now,” Michael says. “To me, it is extremely important to build long-term relationships with companies and Vawdrey has really given

To me, it is extremely important to build long-term relationships with companies and Vawdrey has really given us this in spades.
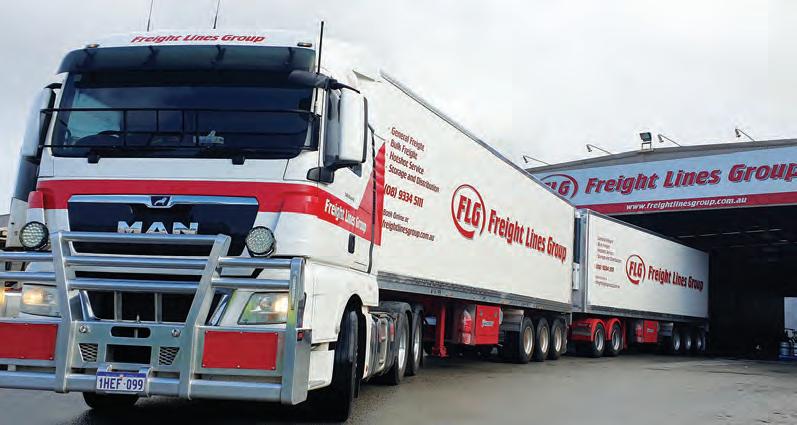
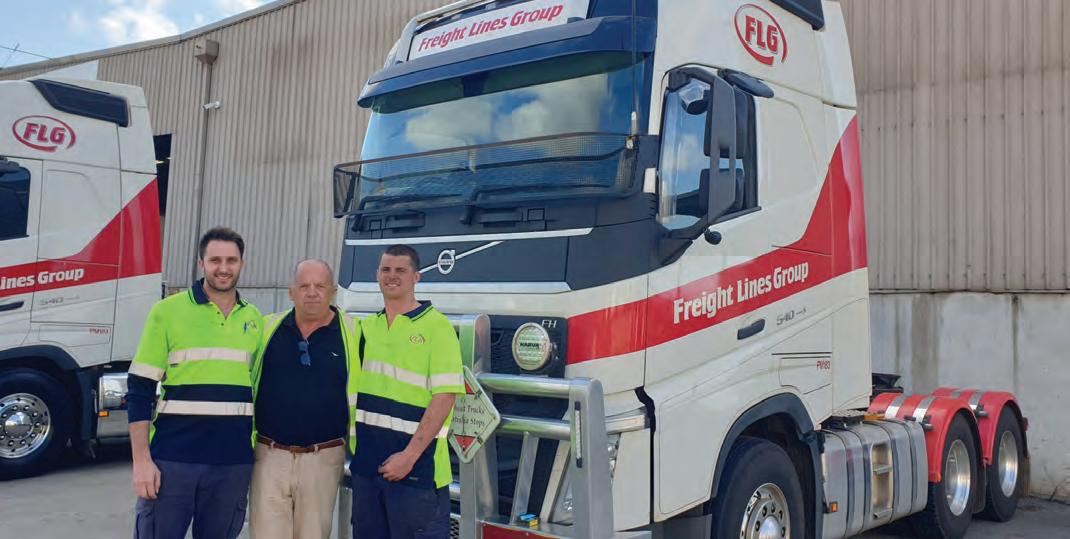
Chris Harding, Michael Harding and Matt Harding.
us this in spades. Their Titeliners and Iceliners are great, reliable products with excellent backup service.” The most important features of the Vawdrey Titeliner and Iceliner trailers, according to Michael, are their ease of use, the quality of the builds and the fact that he has never had an issue with them. Vawdrey’s Titeliner is a sturdy curtainsider ideal for running freight day in, day out throughout Western Australia. Similarly, the Iceliner – locally engineered and manufactured for distribution and heavy duty applications – epitomises peak performance in terms of thermal efficiency and high productivity. The trailers that FLG specifies from Vawdrey are standard specification however they are often used in pocket road train configurations for greater flexibility. “Our Vawdrey trailers always perform well,” Michael says. “The efficiency gains we see are from the flexibility of sending multiple trailers at a time to regional areas. Our fleet travels all over Western Australia and providing essential services to our customers.”
Contact
Vawdrey Australia 1-53 Quantum Close Dandenong South VIC 3175 Ph: 03 9797 3700 Web: www.vawdrey.com.au
High productivity vehicle at a Freight Lines Group depot.