
28 minute read
Trailer Building Materials/Components
Delivering lightweight ultra quads with SAF-Holland
DURAQUIP BANKED ON SAF-HOLLAND AXLES AND SUSPENSION TO PRODUCE A FLEET OF LIGHTWEIGHT LONG HAUL ULTRA QUAD SIDE TIPPERS FOR HEAVY HAULAGE APPLICATION IN WESTERN AUSTRALIA.
Heavy-duty transport vehicle and equipment manufacturer, Duraquip, has delivered a number of ultra quad combinations for David Campbell Transport (DCT) recently. The new lightweight long haul ultra quad side-tipper fleet is an addition to DCT’s existing fleet that is in use for its mining operations in the Pilbara region in northern WA. Duraquip specialises in heavy-duty transport solutions for the mining, agricultural, industrial, and earthmoving sectors across Australia. For the past 15 years its portfolio has included off-road floats, dollies, trailers, liquid tankers and side-tippers for logistics and material handling applications. However, this order marks Duraquip’s move into the iron ore ultra quad market. Mining applications can be as tough as it can get and demand rugged units that tick all the right boxes on the efficiency, safety and durability list. But one of the requisites on this order from DCT was to make lightweight units that deliver better performance standard for multi-combinations. So, when it came to choosing the axles and suspension, Duraquip recommended going with SAF-Holland. “It’s a lightweight suspension but to be able to get these trailers to do the job you would need to meet certain performance criteria, so a fairly stringent PerformanceBased Standard (PBS) assessment was required, and the SAF-Holland product met the performance requirement in the PBS modelling,” says Tony Richardson, Duraquip’s design and sales support manager for Perth metro division. The new ultra-quad combinations feature a tri-axle group on the lead trailer and quad axles including a rear self-steering SAF axle on the following three trailers to ensure an acceptable swept path on turns. The SAF self-steering axle has a weight capacity of nine tonnes and an additional weight of 136kg in comparison with the corresponding rigid axle. The SAF steering axle results in less tyre wear, lower fuel consumption, a high level of driving comfort, optimal manoeuvrability due to precise tracking and a higher resale value of the trailer. Meanwhile, the SAF rear steer axles enables the ultra-quad axle trailers to track exceptionally well both on straight highway stretches and around the corners. The stabilisation damper provides weight optimised steering stabilisation to improve handling on straight and winding roads. The stabilisation damper is suspended on the axle body on one side and on the steering tie rod on the other. It is either pressed (shortened) or pulled (lengthened) depending on the direction of the steering knuckles’ movement. The unique design of this damper means that its internal spiral spring is always compressed during both movements. As the side force decreases,
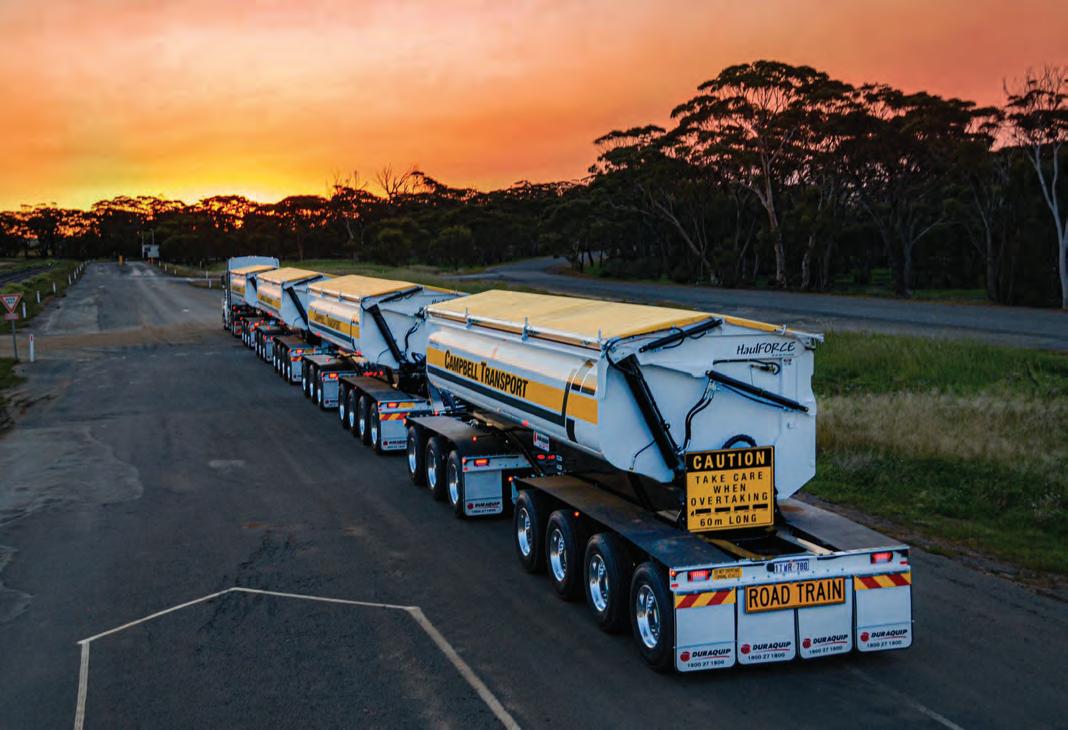
Ultra quad side tippers fitted with SAF-Holland axles and suspension.
the spring force proportionally increases, forcing the steering knuckles back into the straight-ahead position. The DCT units feature 14 degrees of steering angle. SAF self-steering axles are capable of achieving a steering angle of up to 20 degrees based on the track, spring centres and type of wheels installed. An electropneumatic locking mechanism, which is easily controlled by the trailer EBS unit, makes reversing possible by setting the selfsteering axle to rigid. A cathodic dip coating process on particularly exposed parts such as axles and hubs ensures that all SAF axles offer long-term corrosion protection. “Although we mainly left it to SAF-Holland to best explain the features of their product to the Campbell Transport team, one of the main reasons we recommended SAF-Holland for this order was a quick lead time,” Tony says. “With the current state of things with the pandemic that makes it quicker for us with our job. We have been sourcing products from SAF Holland for four years and in that time, we’ve had no major issues. They have good products that are fit for the purpose. Their team has been on top of any issue that we may have encountered. Currently we source around three-four products from them. We started out sourcing heavy-duty off-road axles and suspension, which are both great products. In the recent times though we mainly go to them for lightweight spring suspension and disc brake axles for side tippers. They also have a very good warranty offering with their products.” Duraquip has delivered over half of the order to DCT, where the units will join over 500 trailers and 90 prime movers already at work for the WA-based business. DCT operates from various depots across the state in applications as diverse as mining, heavy haulage, grain, refrigerated, livestock carrying and compost. Designed especially for use in the iron ore mining and transport division, these ultra-quad heavyduty combinations are all geared up for a tough road ahead.
Contact
SAF-Holland Australia P: 1300 131 613 W: www.safholland.com.au
RIDE PERFORMANCE SPECIALIST, MONROE AUSTRALIA, BRINGS ITS BUILT TO LAST TECHNOLOGY TO THE HEAVY DUTY TRUCK AND TRAILER INDUSTRY.
In another strong commitment to Australian manufacturing, Monroe launches its heavy duty truck and trailer shock absorber range to be manufactured at its Adelaide plant. Bucking the trend against local manufacturing, Monroe has re-tooled its plant and re-skilled its enthusiastic workforce to ensure that premium quality Australian made heavy duty ride performance products are designed, manufactured and rigorously tested locally to assure they meet the demanding requirements of the local heavy duty truck and trailer industry. Monroe Australia has made this important local manufacturing decision to ensure that its range of heavy duty trailer ride performance products exceed the toughest requirements of this most challenging environment. This includes the sourcing of premium quality Australian materials to meet Monroe’s heavy duty customers’ requirements for optimum reliable performance and longer life. The rationale behind this Monroe Australia initiative included supporting the company’s loyal and highly experienced Adelaide plant workforce, further developing the plant’s manufacturing capabilities and to provide new local employment opportunities. The quality that is synonymous with all Monroe ride performance products is assured with this locally designed and manufactured Heavy Duty Trailer range. All ride performance products in the range are made using the latest IS09001 Quality System manufacturing processes and to ISO140001 environmental standards, along with design validation testing in compliance with the latest ISO9001-2015 standards. Monroe’s local manufacturing also delivers major design and performance advantages for all products included in the Monroe Magnum Heavy Duty Truck & Trailer range. All reserve and pressure tubes are made from Monroe Australia’s own tube mill with locally sourced material, producing high frequency welded tube at speeds in excess of 100 metres per minute. “Local manufacturing ensures we have the right design and quality to meet the demands of the local environment, which are some of the harshest conditions in the world,” says Monroe Australia Plant Manager, Pat Larobina. Custom designed rebound and compression valving, and mirror finished hardened inner tubes are some of the unique manufacturing advantages of this Aussie made heavy duty commercial vehicle range. Each Monroe Magnum heavy duty trailer shock absorber is also 100 per cent damping force performance tested to ensure that they optimised for their specific trailer application. “Australian manufacturing of our heavy duty Monroe Magnum shock absorber range has been met with
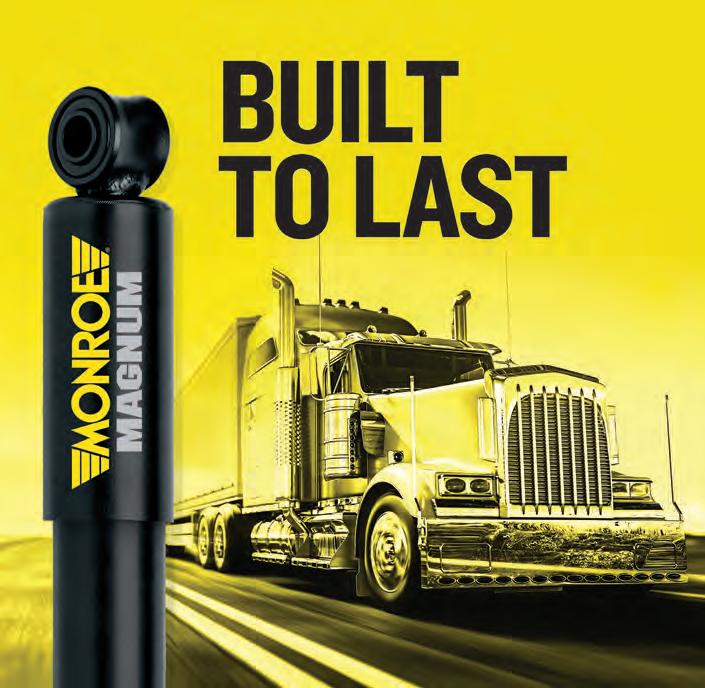
positive feedback from the commercial transport industry including truck drivers, mechanics and distributors, the majority of which have a strong footprint across this country and in New Zealand,” says Chad Torok, Monroe Commercial National Sales Manager. “Our commitment to local manufacturing is also seen as a firm assurance to deliver high quality suspension components that are specifically fit for purpose in meeting our unique Australian heavy duty transport conditions.” To find out more about Monroe’s locally manufactured heavy duty shock absorbertruck and trailer range contact your local Monroe State/Territory Manager, visit www.monroe.com.au or call the Monroe customer service hotline 1800 088 205.
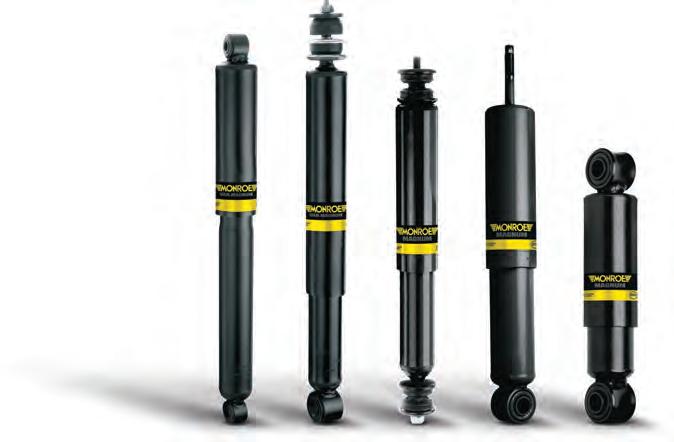
Contact
Monroe Australia Ph: 1800 088 205 Web: www.monroe.com.au
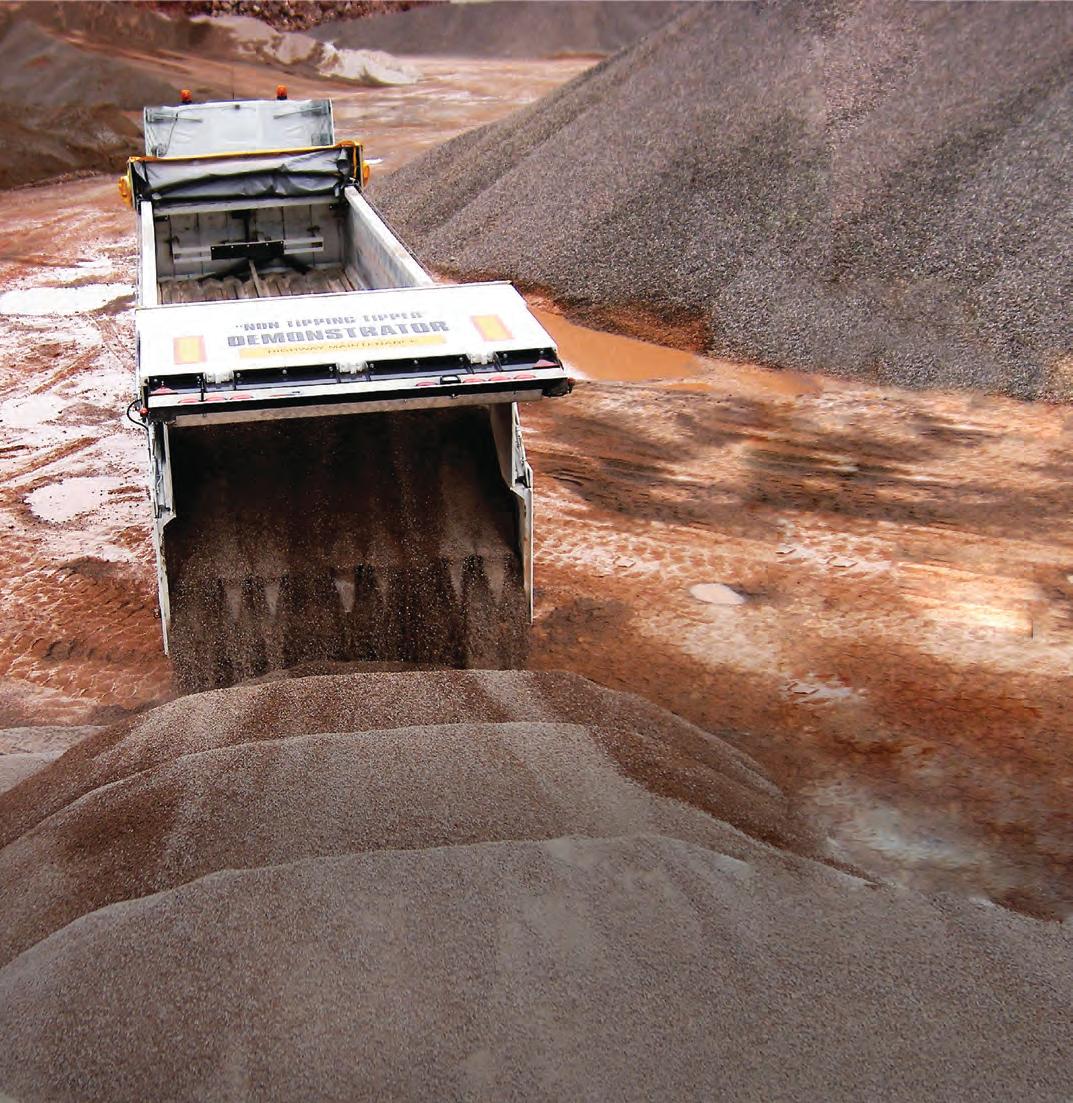

Pumping iron
OPERATING QUAD ROAD TRAINS CARTING IRON ORE IN WESTERN AUSTRALIA’S PILBARA REGION, MGM BULK DEPENDS UPON THE STRENGTH AND RELIABILITY OF JOST’S HEAVY-DUTY JSK39CS BALL-RACE FIFTH WHEEL TO KEEP THE WHEELS TURNING DAY IN AND DAY OUT.
JOST Australia has a long history of building transport components that go the distance under arduous conditions and it’s for this very reason that companies like MGM Bulk continue to use its products. In short, it makes sound business sense. MGM Bulk traces its roots back to the 1950s when Mario Giacci and his family founded a small transport and logistics business at Bunbury in Western Australia. Over the ensuing years it grew into a national business called Giacci Bros. In 2004, Mario Giacci also founded MGM Group, with his daughter Giuditta (Giudi) and son Michael. Over the next decade MGM Group expanded its operations, equipment and resources to become a large established business in its own right. After the sale of Giacci Bros to a public listed company in 2014, MGM added a bulk division to the group known as MGM Bulk, which has experienced significant growth over the last few years, providing bulk haulage and material handling services to a wide range of mining clients all over WA. The company currently manages the logistics of mineral sands, iron ore, lithium, salt, copper concentrate, timber, gravel, limestone and sand. The full fleet of trucks – ranging from semi-trailers to ultra quads – is fitted with driver monitoring technology that includes MTData and DSSI (Seeing Machines). Trailing equipment includes side-tippers, end-tippers, Tautliners, flat decks and tankers. MGM Bulk is currently in the middle of a significant fleet expansion program, with 32 new tri-drive Kenworth C509 prime movers having been delivered from November 2020 to July 2021. Longevity is key in this operation, with MGM Bulk Fleet Manager, Allan Thomas, saying the original C509s the company bought in 2016 now have around 34,000 hours of operation under their belts and are still going strong. Some of the new units have replaced earlier C509s, although the bulk are additional to cater for business growth. A further batch of 19 units are expected to be delivered in the second half of 2021 and into early 2022. Speaking about the JOST JSK39CS fifth wheels installed on the C509s, Allan Thomas says JOST fifth wheels have been a permanent fixture in the MGM Group since the component company opened its Australian operations in 1995. “When JOST first moved into Australia we started using their products and they’ve stood the test of time, so we’ve kept using them,” Allan says. “Wherever we can specify JOST components such as turntables and landing legs that’s what we use.”
A new Kenworth C509.
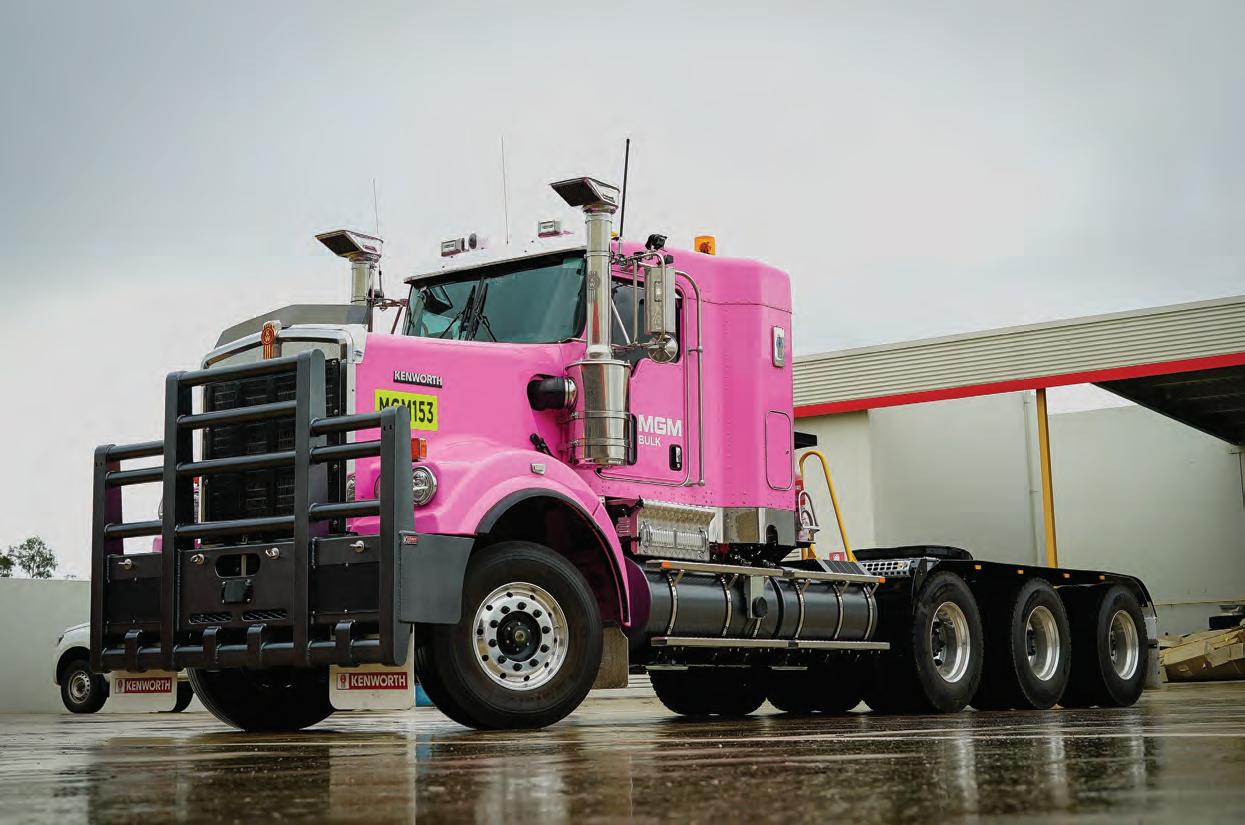
JOST’s JSK39CS heavy-duty fifth wheel is specifically designed for arduous applications including mining, stock crate, fridge van, forestry and other off-road applications. It has a D-Value of 275kN and an imposed load capacity of 26 tonnes. Adding to its longevity are replaceable steel wear plates which bolt onto the top plate. After reaching a minimum thickness limit, the wear plates can be simply unbolted and replaced with new units, thus giving the top plate a virtually unlimited lifespan. Other robust features include manual adjustment of the locking mechanism which provides high reliability and extends the lifecycle of the mechanism. There are also rubber cushion pad mounts which allow a degree of lateral flex of the top plate to help even out the top plate loading and reduce the stresses imposed on the entire unit. The JOST fifth wheels, according to Allan, have a very long lifespan if they are maintained correctly. He also says the process of maintaining and refurbishing them is straightforward, with replacement parts and repair kits readily available, even for the earlier units. “We have some very old units that we have repaired with new jaws and locking bar kits – I’ve never yet seen one thrown in the bin,” he says. “They are user-friendly and very safe, I believe.” MGM Bulk has three branches in WA including its head office at Picton near Bunbury, a branch in Perth and the largest depot at Port Hedland from where the big gear operates. In fact, there are over 60 super- and ultra-quad combinations pulled by the Kenworth C509s with gross combination masses (GCM) of 195 and 210 tonnes respectively, along with respective payload capacities of 140 and 150 tonnes. The tri-drive Kenworth C509 is ideally suited to hauling these colossal weights, featuring Cummins X15 engines rated at 600hp (459kW) at 1,800rpm and 2,050lb/ft (2,779Nm) of torque at 1,200rpm. Along with its loyal adherence to Kenworth trucks and JOST fifth wheels, MGM Bulk has also stuck firmly with Bruce Rock Engineering (BRE) side-tippers and dollies which make up all the quad road train combinations in the northwest operation. As for the drivers, the company has not been immune from the industry-wide shortage of skilled operators. JOST Australia, along with its highly durable fifth wheels and landing legs, have served the company extremely well for more than 25 years. In an operation where harsh operating conditions and high weights dictate the need for ultrarobust equipment, Allan contends that the company has never had any cause to re-evaluate its dedication to a brand it knows and trusts.
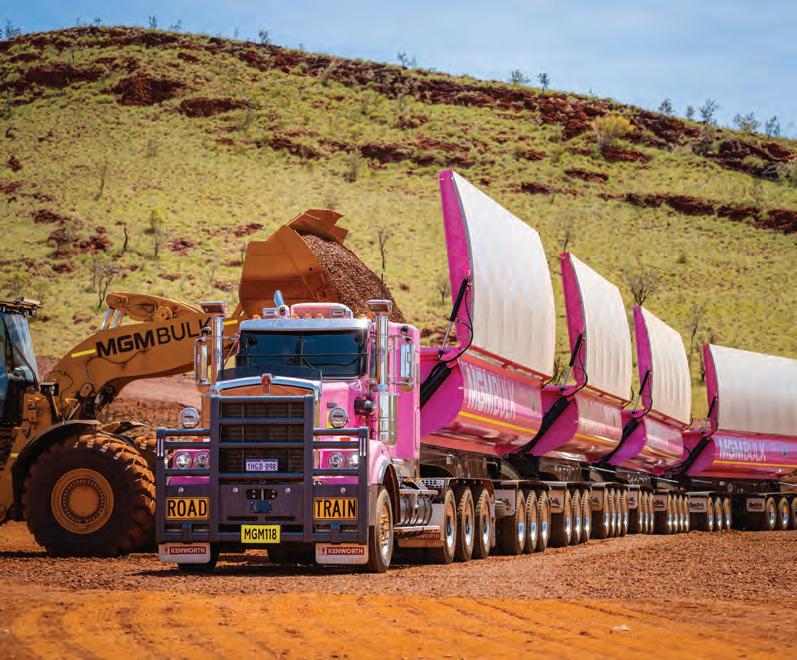
MGM Bulk Pilbara road train.
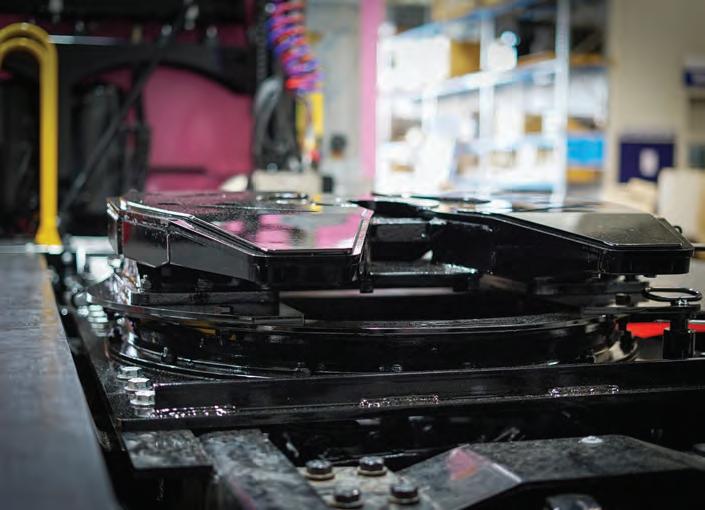
Contact
JOST Australia Ph: 1800 811 487 Web: www.jostaustralia.com.au
Powerdown on shock absorbers and tyre wear
SUPERSHOCK WITH ENVEERO IS POWERDOWN AUSTRALIA’S LATEST INNOVATION FEATURING EXCELLENT SHEAR STABILITY, LONGER LIFESPAN AND MORE.
Everyone in the transport industry knows that tyres are vital to the safe and efficient operation of any freight or transport vehicle. The most commonly accepted reason for excessive tyre wear and premature failure is under or over inflation. This can result in fast and uneven treadwear, compromised vehicle handling and excessive heat build. However, incorrect inflation is not the only contributing factor to tyre wear. Tyres are connected to the vehicle chassis via the axle and suspension module and the movement of the vehicle’s suspension is controlled by the shock absorber. Contrary to their name shock absorbers do not ‘absorb shock’ they control the movement of a vehicles springs and suspension and thus improve wheel ground contact. This is why it is so important to change shock absorbers regularly to help reduce tyre wear. Worn out shock absorbers or units which are not designed for Australian roads will allow the tyre to bounce on the road surface in an uncontrolled manner. This will result in flat patches or ‘scalloping’ on the tread surface of the tyre. This type of wear is inconsistent due to the tyre scuffing the road surface, where as a consistent wear pattern could be the result of an alignment problem or a worn suspension bush. Evaluation of shock absorber condition can be hard without specialised testing equipment, but a basic inspection of shocks for oil leaks, warped or damaged bushes and uneven tyre wear can provide some vital clues and insight about the condition of shock absorbers. This is why ride control engineers recommend the replacement of worn shock absorbers and struts at predetermined kilometres or time period as part of regular servicing of your vehicle. From on vehicle data collection, shock absorbers will on average conduct 1,100 cycles every kilometre. Over the longer term this equates to in excess of 20,000,000 cycles every 20,000 kilometres. With every cycle, internal components wear and fatigue while the oil properties also begin to break down. Utilising dynometer testing, the impact of these wear factors is evident in the considerable reduction, sometimes in excess of 50 per cent, in damping forces generated under the same testing conditions. Powerdown’s latest innovation Supershock with Enveero inside has excellent shear stability; having a higher resistance of changing viscosity when under mechanical stress, due to the longer synthesised hydrocarbon molecules that forms a strong chain. This leads to less mechanical wear on the damper valving components, giving them a longer lifespan. Powerdown Supershock with Enveero inside brings together years of experience in the design and development of shock absorbers specifically for Australia’s harsh operating conditions. The multiple features that set it apart in the market, include: • A large bore size, of 45mm diameter • Enveero inside, which is a synthesized, ultra high performance, environmentally friendly shock absorber fluid designed and developed in Australia by Powerdown • Low pressure gas to keep the unit operating at lower temperatures • Advanced low friction seals, to keep the dust out, providing longer shock absorber life • Increased body size for extra fluid capacity to aid in cooling • An exclusive on vehicle ride height indicator (only available on some
applications) • High tensile strength • Hydraulic stop / recoil cut off, to help increase longevity and reduce fatigue on the shock absorber; and • DU bush in rod guide, which helps to reduce friction and wear when side loading occurs. Powerdown’s Supershock with Enveero inside will go beyond helping drivers and fleets drive safer for longer. Replacing the shock absorbers on vehicles will not only have a noticeable effect on driver control and comfort, but they will also help improve braking and handling, making the vehicle safer and easier to drive. Supershock with Enveero inside will be available for purchase from December 2021,to find your nearest distributor visit www.powerdown.com.au or call our team on 02 4949 0000.
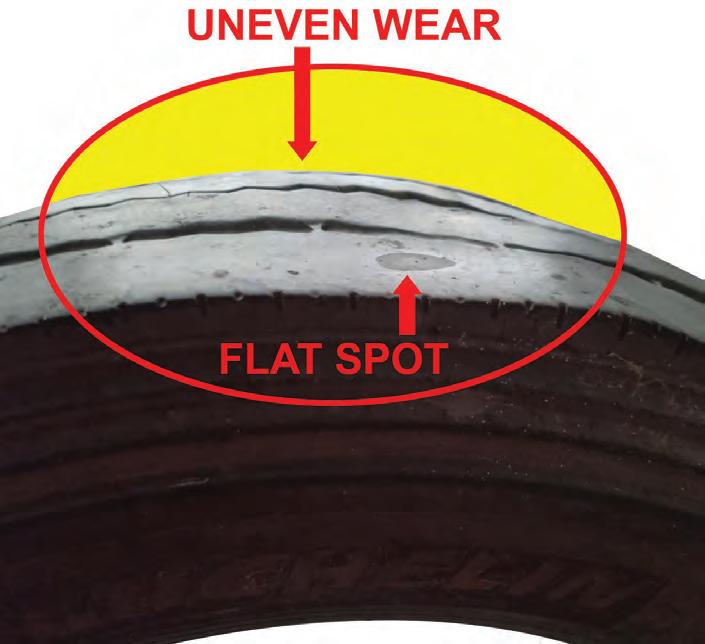
Contact
Powerdown Australia Ph: 02 4949 0000 Web: www.powerdown.com.au Examples of uneven tyre wear and flat spot caused by faulty shock absorbers.
monroe.com.au
BUILT TO LAST
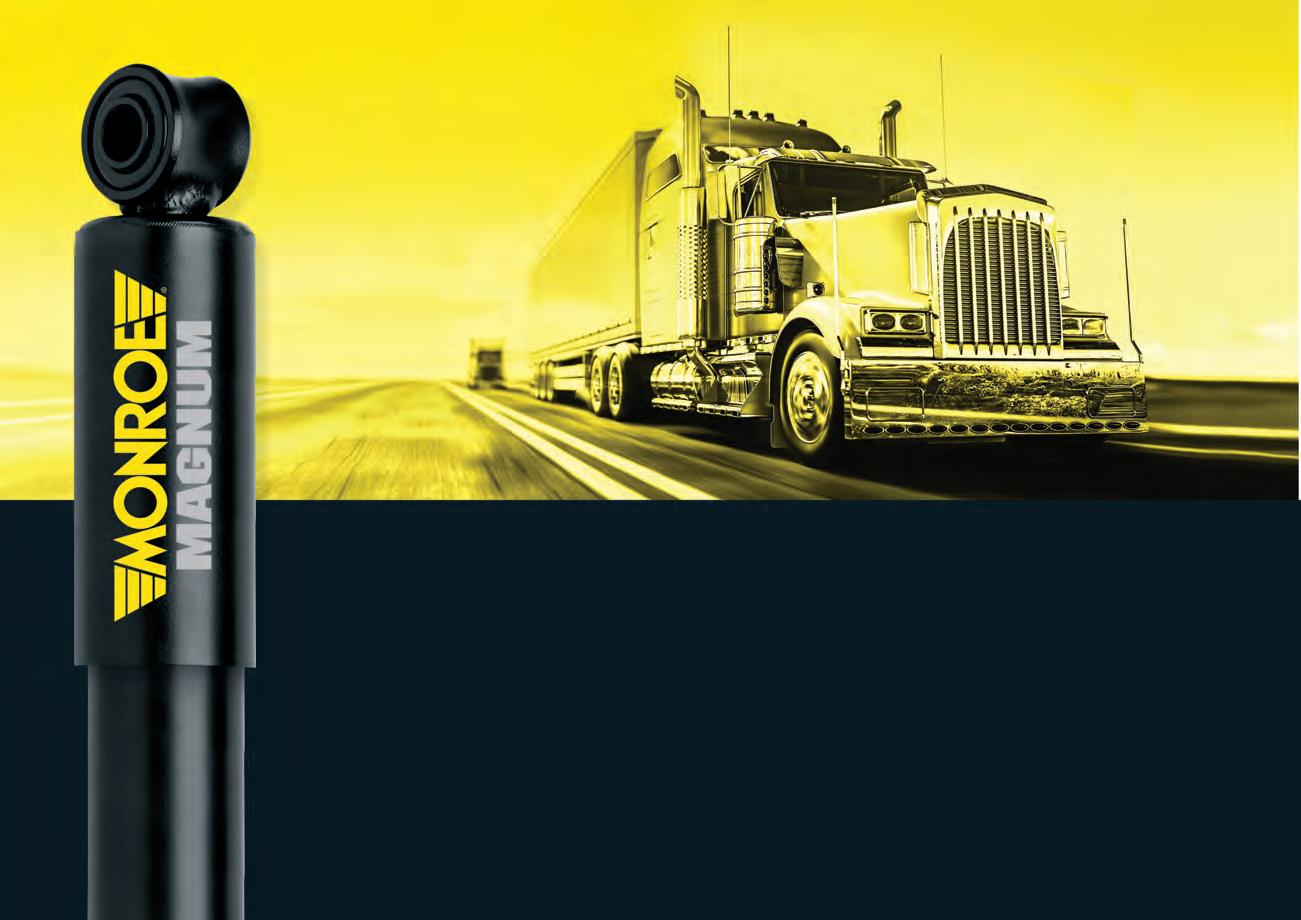
Double action valving system in bump & rebound High Temp resistant hydraulic fluid Hydraulic lock-out piston for improved safety Single bonded bushing for improved durability
Founded by Dino Bertone, EBS Perth is a Knorr-Bremse TruckServices Service Partner that delivers comprehensive support with EBS service, repairs and installations.
Servicing EBS in the West

OVER THE LAST 20 YEARS DINO BERTONE HAS BUILT A SUCCESSFUL ENTERPRISE CATERING FOR THE AUTO ELECTRICAL AND EBS NEEDS OF TRANSPORT OPERATORS IN THE VAST STATE OF WESTERN AUSTRALIA. MORE RECENTLY, DINO PARTNERED WITH TRAILER BRAKING SPECIALIST, KNORR-BREMSE, TO PROVIDE A ONE-STOP-SHOP FOR INSTALLATIONS, SERVICING AND REPAIRS OF SOPHISTICATED EBS EQUIPMENT AND OTHER TECHNOLOGY ON HEAVY TRUCKS AND TRAILERS.
Being invited to become a Knorr-Bremse TruckServices Service Partner in WA was a crowning achievement for Dino Bertone, who has spent the better part of two decades learning all there is to know about EBS (Electronic Braking Systems) while building his business, EBS Perth and Auto Electrical. Having grown up in Perth, Dino started an auto electrical apprenticeship in 1998 and, eager to learn more about truck and trailer braking systems, undertook additional learning in control systems, electronics and pneumatics. Prior to starting his apprenticeship, Dino already had some knowledge of auto electrical systems as he had done plenty of work experience and worked with auto electricians in his school holidays. During his apprenticeship he was awarded Apprentice of the Year in 2000 in Auto Electrical at the South East College of TAFE. Dino also won the Perth regional Workskills competition and then went on to represent his state in the Australian Workskills competition in Adelaide in 2001 where he finished as a finalist. After completing his apprenticeship, Dino worked on heavy vehicles in a range of transport fields including general freight. He was also heavily involved in the fuel industry and as EBS started becoming mainstream on fuel tankers he began filling a need for maintenance of the systems. As such, he became licenced to work on tankers used to haul regular liquid fuels as well as those used for carting gases in the form of LPG, LNG and CNG. Dino also gained his Multi-Combination driver’s licence and Dangerous Goods licence which enabled him to test drive the heavy vehicles to ascertain that issues had been rectified. Dino’s next move was to start his own business called EBS Perth & Auto Electrical, as he realised that there was a significant opportunity in this space and was keen to help truck operators with their EBS needs. “I discovered there were relatively few people with the knowledge and expertise to do this type of work, so I decided I would fill this niche and learnt all there was to know about EBS,” Dino says. As for his initial connection with KnorrBremse, Dino says in trying to diagnose a problem with a truck’s EBS in 2013 he contacted an engineer at Knorr-Bremse who was pleasantly surprised at how much he knew about Knorr-Bremse EBS. “He asked me how I knew so much about their products and EBS in general and I explained that I had been diagnosing faults and doing installations for a number of years and had learned as much as I could along the way,” Dino says. As it turned out, Dino’s enthusiasm and expertise with EBS was just what Knorr-Bremse had been looking for, and the
Fast Fact
EBS Perth & Auto Electrical is an authorised service partner for KnorrBremse in the state of Western Australia. The owner of the business, Dino Bertone, has a broad and deep knowledge of EBS that ensures issues are sorted pronto.
company made him an offer to become one of its service partners in Western Australia. Not surprisingly, Dino grabbed this opportunity with both hands and has worked closely with Knorr-Bremse ever since. Also unsurprisingly, his business has thrived as a result. “Over the intervening years I was introduced to more people at Knorr-Bremse and every time I found issues in a system I was working on, I would consult with them and sometimes fly over to Melbourne so we could work things out together in the workshop,” Dino says. Having now had seven years of doing this, Dino and his company are considered an important go-to service provider for specialised technical support of KnorrBremse EBS in WA. Dino explains that he tries to stay one step ahead of the technology development to ensure he is right up to date with the servicing and diagnostic procedures. “During my time in the fuel and gas industries I made lots of contacts so many of my current clients are from these industries,” Dino says. “I have CNG, LNG and LPG tickets and I’ve also had the opportunity to work closely with software engineers who used to work for a leading global auto manufacturer. This involved learning a lot about CAN bus which is a major component of EBS.” A Controller Area Network (CAN bus) is a robust vehicle bus standard designed to allow microcontrollers and devices to communicate with each other’s applications without a host computer. Dino says that CAN bus systems are generally quite reliable but that problems can arise if aftermarket systems are added without sufficient preparation or testing. He also says his exposure to different
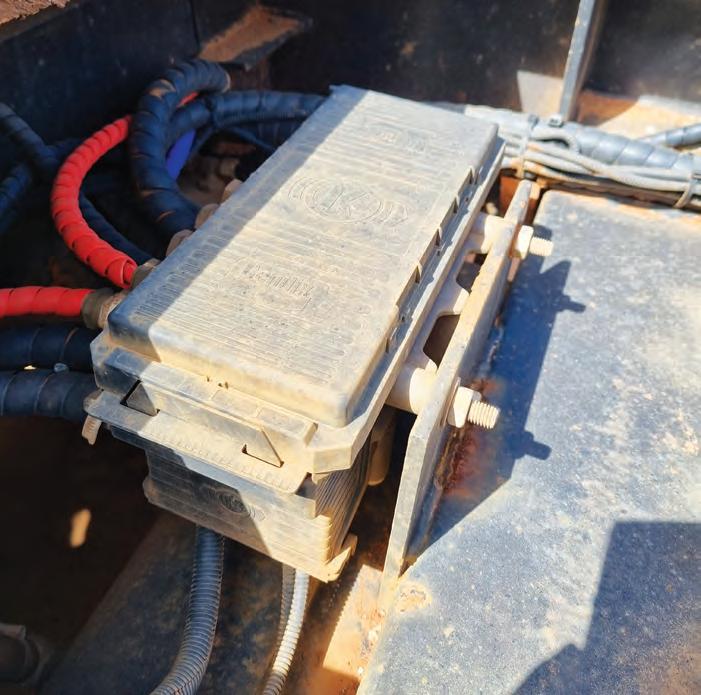
EBS Perth caters for customers in metropolitan Perth as well as in farflung mining communities in places like Kalgoorlie and Port Hedland. Rugged and reliable. Knorr-Bremse EBS features CAN bus communication between the various components.

modes of transport from early in his career – including cars, trucks and marine – has given him a broad perspective on electronics across a wide range of vehicles and vessels. “The owners of the business where I did my apprenticeship were right into yachting so I was able to learn about how to deal with electrolysis problems,” he says. “I was always interested in mechanical and electrical systems and I would always annoy people by asking lots of questions so I could learn as much as possible.” These days Dino’s company comprises himself and one tradesman with Dino saying he is deliberately keeping the operation small so that it remains a specialised service. “It’s important to stay specialised in this field because you can have 10 trailers side-by-side and each one could have a different EBS configuration that you have to know how to manage,” he says. “EBS valves can be programmed in different ways so it’s essential to have the broad product knowledge to enable the job to be done correctly and efficiently.” As such, Dino and his employee are kept on their toes looking after the complete EBS needs of customers from metropolitan Perth to far-flung mining communities in places like Port Hedland and Kalgoorlie. At the same time, Knorr-Bremse is assured its customers’ sophisticated EBS equipment is in the safest of hands in terms of service, repairs and installations in the state of Western Australia.
Contact
Knorr-Bremse Australia
23-29 Factory Street Granville NSW 2142 Toll Free: 1300 309 991 Email: cvs.aus@knorr-bremse.com Website: www.knorr-bremse.com.au
EBS Perth and Auto Electrical
Dino Bertone 0410 512 879
MTA25 axles have been trialing successfully on Australian roads for more than six months.
End to end solutions

MERITOR AUSTRALIA HAS INTRODUCED THE MTA25 TRAILER AXLE AND SUSPENSION SYSTEM BECOMING THE FIRST IN THE AUSTRALIAN MARKET TO OFFER AN END-TO-END PACKAGE OF STEER, DRIVE AND TRAILER AXLES FOR HEAVY VEHICLES.
A leading global supplier of drivetrain, mobility, braking and aftermarket solutions for commercial vehicle and industrial markets, Meritor, has over a 100-year legacy of providing innovative products that offer superior performance, efficiency and reliability. With its head office in Michigan, US, the business serves commercial truck, trailer, off-highway, defence, specialty and aftermarket customers in more than 70 countries. In Australia, Meritor also has a proud heritage of local manufacturing stretching back over 50 years. Originally incorporated in Australia as a division of Rockwell, the Meritor production facility in Sunshine, Melbourne has been continuously operating since 1970, producing locally manufactured drive and steer axles that are the axle of choice for many of the Australian heavy duty truck brands. Meritor’s success with these products has been forged on a reputation for quality, industry leading local application engineering expertise and superior locally based customer support. It was therefore only logical that as the company sought further opportunities for growth they should look to apply this model for success within the trailer market.
The MTA system
Having evaluated the options available from their parent company in the US, where trailer axles has long been offered as a part of the Meritor product range, the local team settled on the MTA (Meritor Trailing Arm) trailer axle as most suited for Australasian conditions. In North America this axle has proven itself over many years and millions of kilometres where it is sold primarily into demanding vocational applications such as logging and tipper work. However, after extensive evaluation of the Australian market and our unique road and application conditions, the team at Meritor Australia strongly believed the MTA would perform well across a multitude of our applications. This decision was reinforced by some extensive in-house durability testing that showed the MTA axle had superior life to axles offered by a recognised competitor with a significant presence in the Australian trailer market today. So, with commonality between truck and trailer front of mind, the local team working on the project put together an MTA package that features trusted Meritor Q+ brakes with
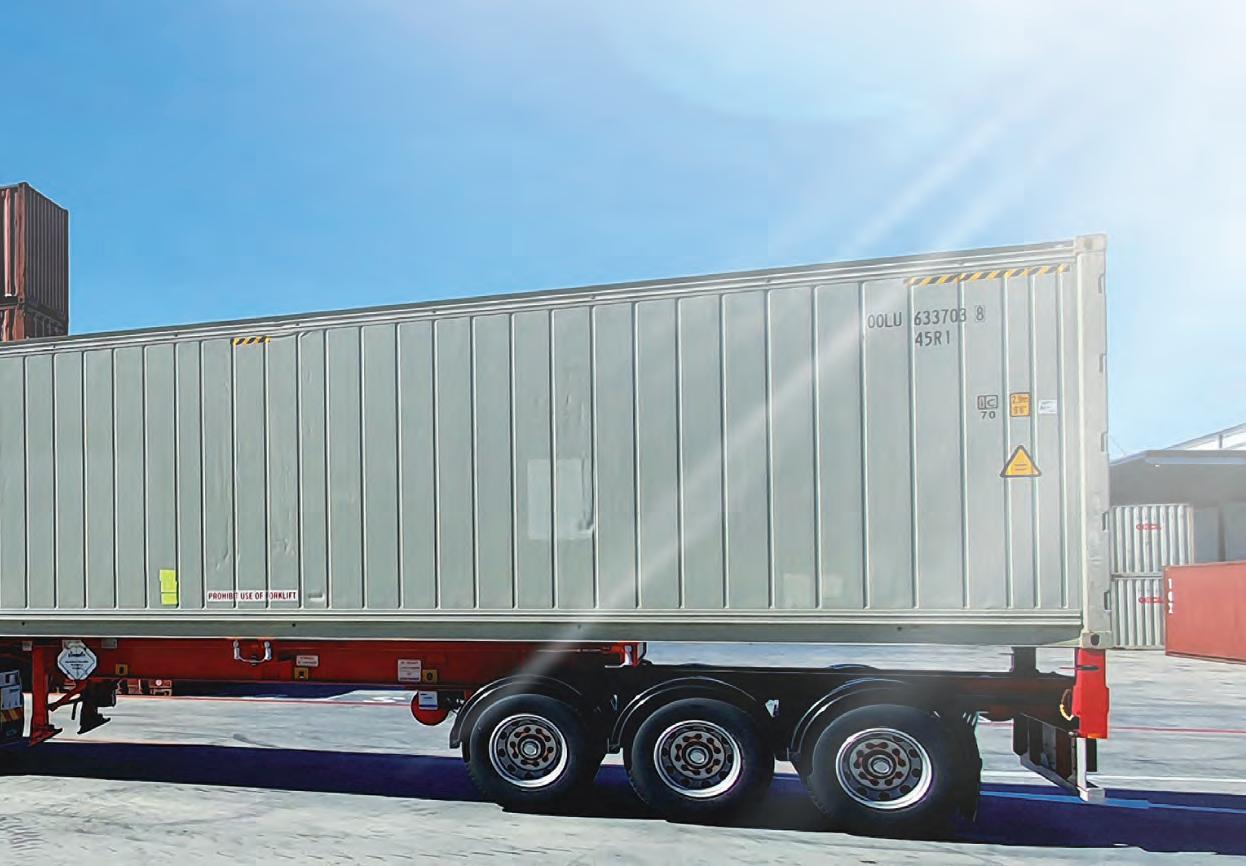
lightweight X30 drum or the Meritor EX family disc brakes – all with the same ease of serviceability, reliability, and parts availability found in Meritor Australia truck drivetrain products today. The result is a product that offers outstanding durability (single piece formed axle, axle wrap design, patented pivot bushing), serviceable design (quick cam replacement without removing the hub, easy installation axle pack bearings) and lightweight (integrated suspension, stamped spider and single piston disc brake). The team at Meritor Australia aimed to lower Total Cost of Ownership (TCO) and make fleet maintenance simple. Now, with over six months of successful trials on Australian roads, the firm is confident it has a product that delivers on this promise. The MTA axle’s major components are manufactured in North America, with the final assembly and configuration of axles taking place in Australia. While Meritor acknowledges it is still gearing up to compete in the Australian trailer market it also understands the dynamic nature of the trailer industry and the needs of local operators. Meritor prides itself on managing a just-in-time (JIT) inventory system that ensures lead times for products is well within the trailer build time. Parts for the MTA trailer axles will be shipped from Meritor’s dedicated 5,000-square-metre parts warehouse in Derrimut, Melbourne, and will be available via the same channels as Meritor’s current drive and steer axles which includes most major OEM truck dealer networks and encompasses over 300 outlets across Australia and New Zealand. Additional technical and sales support will be provided by a dedicated aftermarket customer call centre at Derrimut as well as a team of field-based Meritor Driveforce representatives.

Contact
Meritor Australia Web: www.meritor.com E: sales.sunshine@meritor.com
Production of a trial MTA25 axle at Meritor in Sunshine, Victoria.
XLent sealing
LIKE ITS PREDECESSOR, THE SKF SCOTSEAL CLASSIC, SKF’S SCOTSEAL PLUS XL SEAL OFFERS EVEN BETTER LEVEL OF PROTECTION, LONGER LIFE IN CONTAMINATED CONDITIONS, HIGH TEMPERATURE RESISTANCE AND EASY APPLICATION FOR ALL HEAVY VEHICLES.
Industry estimates suggest that up to 90 per cent of premature wheel bearing failures are due poor bearing adjustment and improper seal installation and subsequent leakage of lubricant. Quality sealing solutions can eliminate the risk of such leakages and continue to remain the main performance differentiator for hub bearing unit applications in all types of vehicles, including heavy duty and offroad vehicles. SKF Scotseal, a trusted industry name for over 30 years, offers sealing solutions that are proven to be dependable and long-lasting. Designed to retain oil and grease, SKF Scotseals are available in a variety of styles and sizes for applications in steer, drive or trailer axles.
SKF Scotseal range
The original self-contained oil type seal, SKF Scotseal Classic has proven its quality and long-life service in the trucking industry in the past three decades. SKF Scotseal Longlife, based on the Classic version, is designed to go to even longer intervals between services. SKF Scotseal Plus provides the same unitised advantages plus offers easy, hand installation. Designed with extended life capabilities, SKF Scotseal Plus XL offers maximum sealing life under virtually all driving conditions. The latest offering, SKF Scotseal X-Treme, provides improved reliability and extended service life under the harshest operating conditions for the vehicle service market, as well as OE truck and trailer manufacturers. Built upon the success of SKF Scotseal Classic, SKF Scotseal Longlife seals in and out with four sealing lips including: spring-loaded primary sealing lip that is factory pre-lubed, radial dirt lip, axial dirt lip, and outer bumper lip that acts
Scotseal Plus XL.
Material
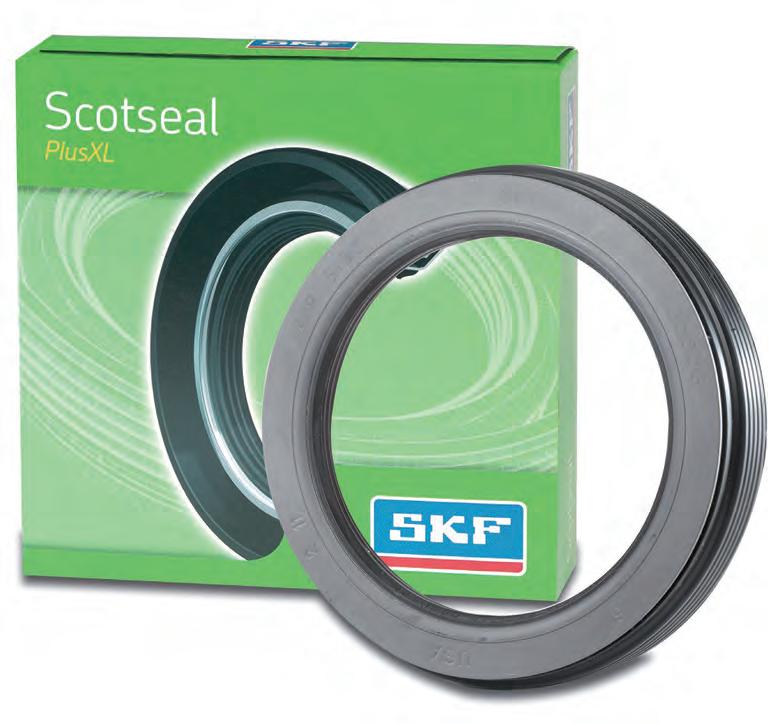
Plus XL
HNBR/EPDM/NBR
Temp
-40˚C to 149˚C Exclusion Excellent Abrasion resistance Excellent
Suitable for oil / grease
Both Extended life Yes Synthetic fluid compatibility Excellent Installation No special tools Front P/N 35058 Drive P/N 47692 Trailer TN P/N 46300 Trailer TP P/N 42627 Trailer 20,000# axle 40129
Scotseal range.
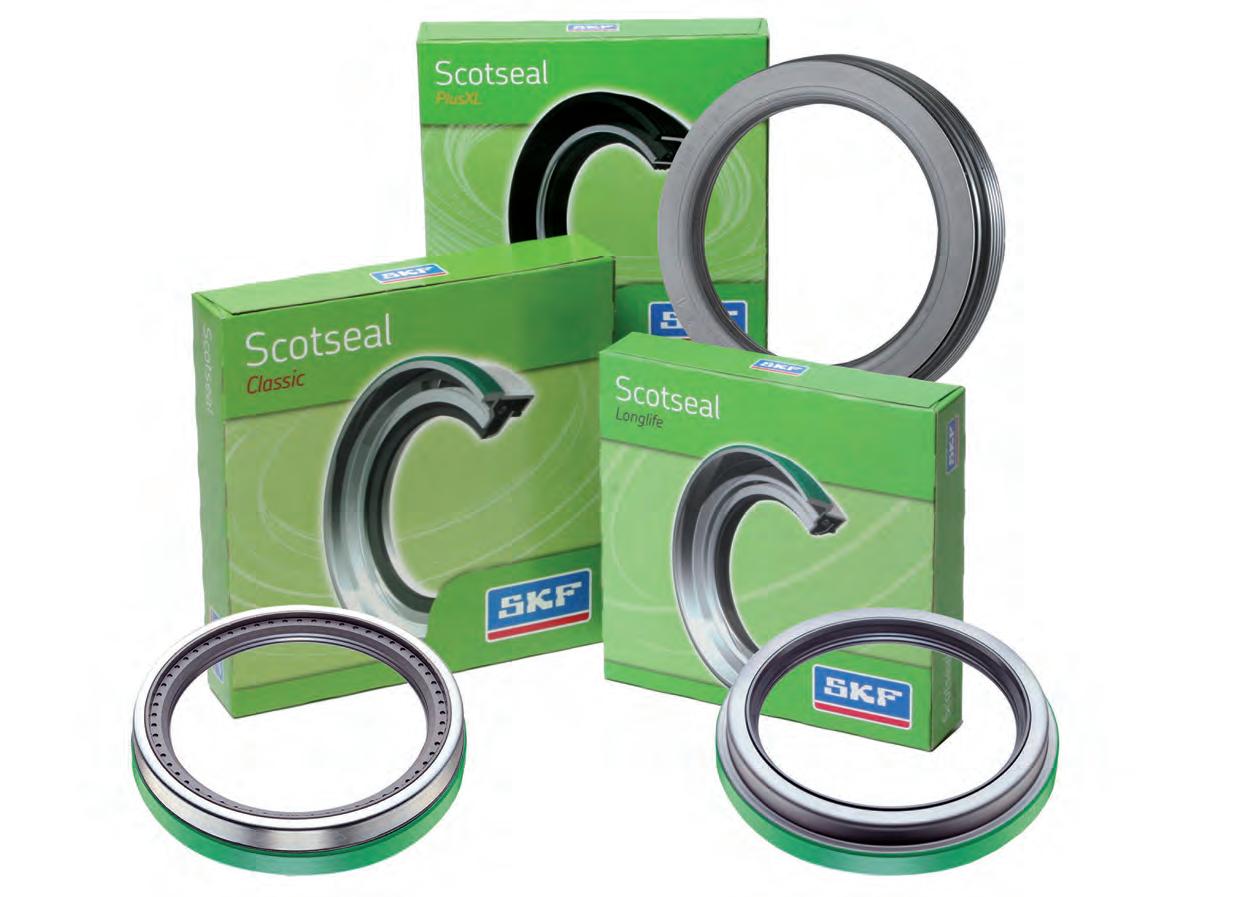
as preliminary dirt excluder. The SKF Longlife with its newly formulated material has superior tolerance and resistance to high temperatures. The special formulated polymer is compatible with all known synthetic lubricants, this combined with advanced seal design makes it suitable for extreme conditions and extends seal life. SKF Scotseal Plus XL offers maximum sealing under frequent braking applications, extreme harsh and heat generating environments, and protects against dust and water ingress. As a result, it is preferred by many OE truck and trailer manufacturers and the standard seal in pre-assembled hubs, due to its proven history of high performance. The advanced HNBR (Hydrogenated Nitrile Butadiene Rubber) material provides extended service life of the wheel end components. It also provides heat resistance up to 149 degrees Celsius as well as broad compatibility with synthetic lubrication fluids. The unitised design provides fresh running surface for sealing lips and keeps out road contaminants for better protection. The ‘fat footprint’ with adhesive type properties locks onto the spindle making a perfect seal even on a worn spindle. Like Longlife, the Plus XL seals in and out with four sealing lips including the springloaded primary sealing lip with patented Waveseal design that sweeps oil back to the bearings. SKF Scotseal Plus XL is easily installed without special tools, helping to eliminate costly do-overs and extending wheel end life. SKF Scotseal Plus XL seals are designed by highly trained wheel end SKF engineers. Competitors trying to duplicate SKF seal geometry cannot replicate the capabilities of the original SKF Scotseal designs. . Elastomeric formulation along with the high tolerances and finishes and manufacturing quality controls put together with the design features produce a seal that cannot be duplicated. Contact SKF for genuine, premium quality SKF Scotseals.
Contact
SKF Australia 17-21 Stamford Road Oakleigh VIC 3166 Ph: 03 92690700 E: skf.marketing.australia@skf.com Web: www.vsm.skf.com