
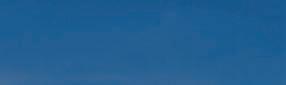
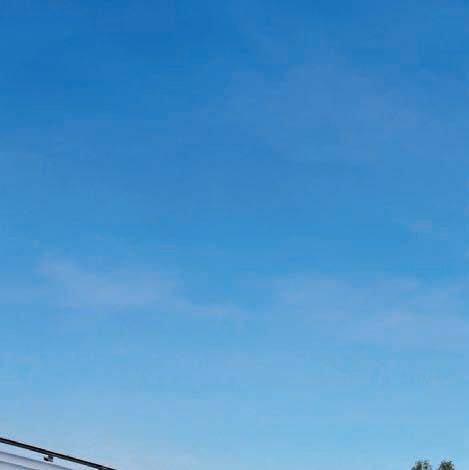


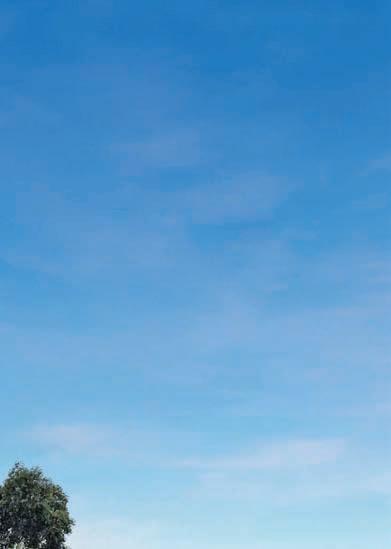
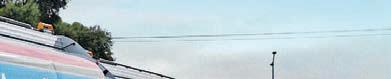

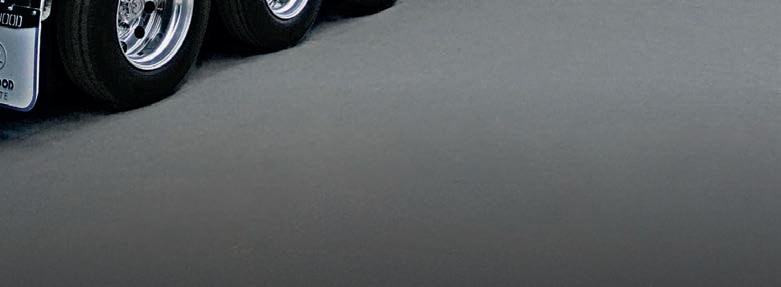



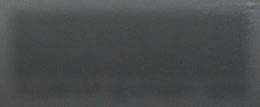

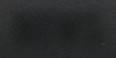



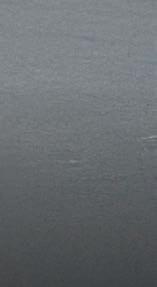


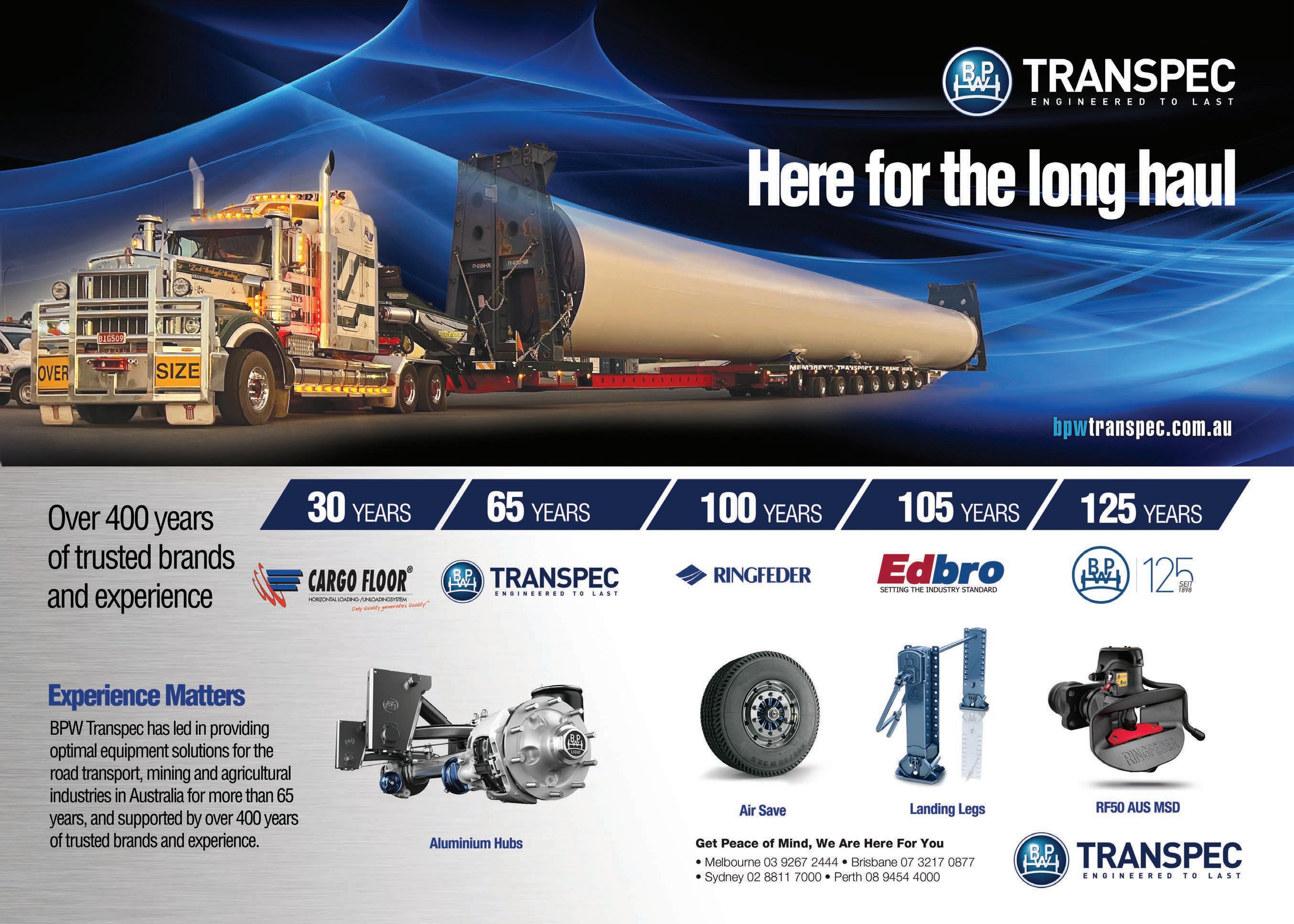
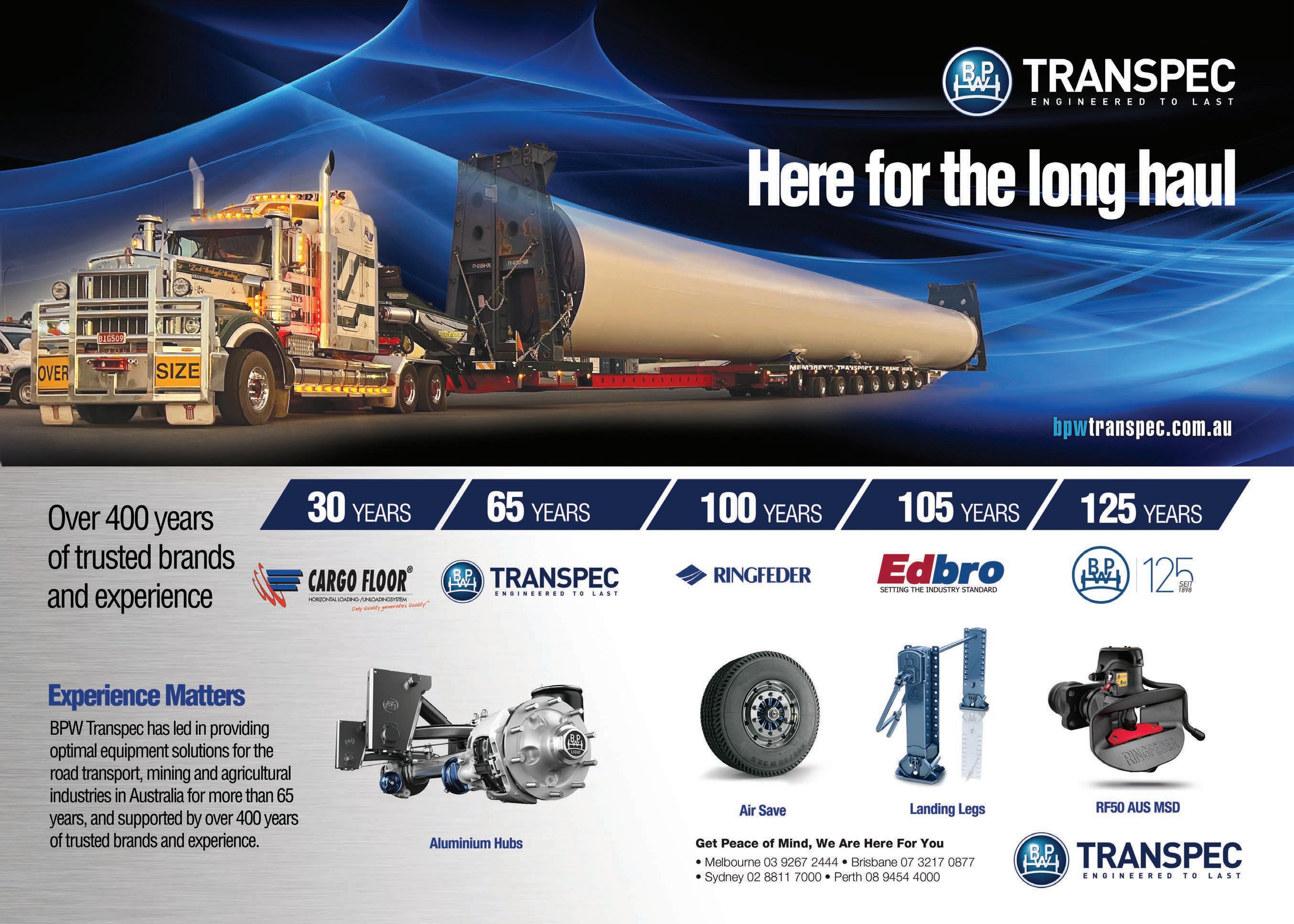
PUBLISHER
John Murphy
john.murphy@primecreative.com.au
MANAGING EDITOR
Luke Applebee luke.applebee@primecreative.com.au
EDITOR
Peter White peter.white@primecreative.com.au
JOURNALIST
Sean Gustini sean.gustini@primecreative.com.au
CONTRIBUTOR
William Craske william.craske@primecreative.com.au
ADVERTISING
Con Zarocostas: 0422 222 822 conzarocostas@primecreative.com.au
Ashley Blachford: 0425 699 819 ashley.blachford@primecreative.com.au
DESIGN
Alejandro Molano
HEAD OF DESIGN
Blake Storey
CLIENT SUCCESS MANAGER
Isabella Fulford isabella.fulford@primecreative.com.au
HEAD OFFICE
Prime Creative Pty Ltd
379 Docklands Drive Docklands VIC 3008 Australia
SUBSCRIPTIONS
03 9690 8766 subscriptions@primecreative.com.au
Trailer Magazine is available by subscription from the publisher.
Annual rates: AUS $99.00 (inc GST). For overseas subscriptions, airmail postage should be added to the subscription rate. The right of refusal is reserved by the publisher.
ARTICLES
All articles submitted for publication become the property of the publisher. The Editor reserves the right to adjust any article to conform with the magazine format.
COPYRIGHT
Trailer Magazine is owned by Prime Creative and published by John Murphy.
All material in Trailer Magazine is copyright and no part may be reproduced or copied in any form or by any means (graphic, electronic or mechanical including information and retrieval systems) without written permission of the publisher. The Editor welcomes contributions but reserves the right to accept or reject any material.
While every e ort has been made to ensure the accuracy of information Prime Creative will not accept responsibility for errors or omissions or for any consequences arising from reliance on information published. The opinions expressed in Trailer Magazine are not necessarily the opinions of, or endorsed by the publisher unless otherwise stated.
O cially endorsed by the VTA
The recent tariffs enacted by President of the possible effects they will have in Australia. More specifically, how will they will impact our economy and the thriving trailer manufacturing industry that our country admirably keeps intact onshore?
Trump has established a record of putting America first in trade. In his first term he threatened to impose tariffs on Mexico in an effort to help secure the United States border, and when the US faced a global oversupply of steel and aluminium in 2018 he quickly implemented tariffs (25 per cent for steel and 10 per cent for aluminium) from most countries. However, it was later announced that Australia, a free trade partner, would be exempted from those regulations.
Based on the first wave of taxes imposed this year in Trump’s second term (a 25 per cent additional tariff on imports from Canada and Mexico and a 10 per cent additional tariff on imports from China), many local economists believe global trade could be disrupted, with the extra pressure to be passed onto Australian exports and industries.
“Given that China is a major export market for Australian firms, such an event would have negative consequences for the Australian economy,” said UNSW Business School Professor of Economics, Richard Holden, ahead of the China tariffs being actioned.
Trump has since announced a 25 per cent tariff on all foreign steel and aluminium imports into the US, without exceptions or exemptions for any country at the time of writing. Policymakers and government will need to consider how to shield the Australian
economy from the expected impact.
“Our nation requires steel and aluminium to be made in America, not in foreign lands,” Trump told the media while signing the executive order.
Cue the domino effect. Should steel and aluminium manufacturers/suppliers be impaired by the tariffs in their margins, additional costs, as a result, will be passed onto trailer builders and the end users. And with the materials being more expensive for buyers, it’s fair to assume that they will see a decrease in demand. While Australia was able to obtain an exemption from the US tariffs last time, our diplomatic relations are going to be tested if we’re to have any chance of repeating this.
The good news, however, is that Australia’s trailer manufacturing industry is still as strong as ever. According to IBISWorld, the market size of the motor vehicle body and trailer manufacturing industry is currently valued at $6.1 billion and it has been growing at a steady compound annual growth rate (CAGR) of 0.6 per cent since 2019. It will be interesting to see how this plays out across industry in the short- and longterm. There’s no reason to believe solid compound growth can’t be maintained if the high levels of innovation and reliability associated with industry are allowed to continue.
Modern politics and its fallout can create fluid situations, and as we have already seen, things can move fast, especially under this administration.
Western Australia 5 Freight Road, Kenwick WA, 6107
Tel -(08) 9350 6470
8 Industry news
Business partnerships, people movements, developments that bolster freight productivity and more.
18Economy
DP World and NSW Ports have announced a $400 million co-investment.
20Refrigerated transport equipment
Learn more about the refrigerated capabilities of Carrier Transicold and Scully RSV.
24Trailer builder
Australia’s trailer manufacturing industry is as strong as ever.
34Hooklifts & skip loaders
Allied Waste Concepts has deployed a new unit fitted with Hyva hooklifts from JOST.
38Trailer building materials/components
A showcase of the products and services that keep trailers on the move.
52ALRTA
The Australian Livestock and Rural Transporters Association celebrates its 40th anniversary this year.
54Haulmax Tyres Trailer Builder Showcase
A list of Australian manufacturers across all major categories from general freight to heavy haulage to tankers.
64Infrastructure spotlight
What you need to know about Australia’s biggest road projects this month.
66World map
A trio of industry heavyweights are joining forces to begin work on a groundbreaking initiative aimed at making e-trailers more e cient.
68Fleet of the month
D&G Logistics isn’t letting a di cult market get in the way of its rapid expansion.
70What’s on
Upcoming shows and field days.
“
Attention to detail is paramount when managing demanding and diverse freight tasks which is why we invest in Australian made, safety optimised and durable equipment from Vawdrey.
“
K&S FREIGHTERS MANAGING DIRECTOR AND CEO, Paul Sarant.
The National Heavy Vehicle Regulator (NHVR), together with the state and local governments, have delivered on a set of heavy vehicle productivity initiatives to support safer and more efficient heavy vehicle movements in South Australia.
The NHVR has introduced three Oversize Overmass (OSOM) trial notices to replace the need for the heavy vehicle industry to apply for permits on key routes.
SA Minister for Infrastructure and Transport, Tom Koutsantonis, said he was pleased to see the changes come into effect after making the request to the NHVR to reduce heavy vehicle access permits in the state.
“Streamlining heavy vehicle access by transitioning permits to notices will allow operators to travel more efficiently, and I thank the NHVR for their enthusiastic response to improve access to routes subject to multiple heavy vehicle access permits,” he said.
“Today’s announcement is part one of a multi-stage plan to drastically reduce the need for thousands of heavy vehicle permits in South Australia.
“These outcomes show how the NHVR
and state and local government are listening to industry about what needs to be done to continue to achieve improved heavy vehicle safety and productivity outcomes.”
Former NHVR CEO, Sal Petroccitto, said the new OSOM trial notices would allow access to load carrying vehicles with greater mass and dimension limits than previously authorised.
“What this will mean is a more streamlined process for operators, with larger and heavier movements of indivisible loads now either requiring no permit, or consent from less road managers than before,” he said.
“I’d like to thank Minister Koutsantonis for his continued support of the heavy vehicle industry, and his recognition
BevChain has unveiled its newest distribution centre (DC) in Kemps Creek, New South Wales.
The new location arrives as BevChain continues to grow in the beverage category after opening DCs in Maddington, Western Australia, Laverton, Victoria.
A new site in South Australia will soon follow.
The 43,000-square-metre DC is home to valued customers including Coles Liquor Group, Brown Brothers, Bacardi, Fiji Water, Drinksworks, Taylors Wines and South Trade.
Designed with the future in mind, the Kemps Creek DC delivers to BevChain’s current and anticipated needs.
“The DC delivers exactly what we need today, and everything we’ll need for tomorrow,” said Coles Liquor Head of
Supply Chain, Andy Hampson.
of the important contribution it makes to the South Australian economy and the communities.”
Over the next 12 months the NHVR, South Australian Department of Infrastructure and Transport (DIT) and other participating road managers will assess how effective the trial notices have been in supporting heavy vehicle productivity and safety.
Future stages of the multi-stage plan will focus on reviewing South Australia’s Performance-Based Standards (PBS) combinations, livestock transport mass exemptions, and tri-drive prime mover access arrangements.
The review will also address specialpurpose combinations, ensuring alignment with evolving industry needs.
“Our vision is to be the go-to drinks retailer for any occasion, and our supply chain is a big enabler of this.
“The DC caters to the seasonality that’s part and parcel of the beverage industry, as well as our ambitious growth plans.
“Our stores benefit from our ability to meet the Christmas peak, with product readily available.”
Location wise, the DC is close to key suppliers and major transport routes which increases efficiency for Linfox and BevChain.
In addition, the facility was designed and built to achieve 5 Star Green Star certification from the Green Building Council of Australia, reflecting Linfox and BevChain’s commitment to act sustainably.
It includes a 750kW solar PV system;
electric vehicle charging capability for trucks, material handling equipment and passenger vehicles; rainwater harvesting and landscaping irrigation; and operational waste management plan towards zero waste to landfill.
“The ability to share resources makes us incredibly agile, with enormous benefits for lead time, shelf availability, efficiency and overall value,” said Linfox President BevChain and New Zealand, Misha Shliapnikoff.
“Our customers are increasingly committed to reducing their scope two and three emissions.
“We work closely with our customers to meet our shared sustainability goals. It’s not only beneficial for the environment and our communities, but it also makes good business sense.”
Mineral Resources (MinRes) has marked a new milestone at Onslow Iron with the final crushing plant constructed and truck load out circuit operational at Ken’s Bore.
The project now boasts three modular crushing plants which have been designed and developed in-house.
Operated by CSI Mining Services, a wholly owned subsidiary of MinRes, the modular crushers consume less energy and deliver significantly lower dust and noise emissions.
Each crushing plant has a capacity of 12.5 million tonnes per annum (Mtpa) and will support the project’s ramp up to nameplate capacity of 35Mtpa.
The truck load out circuit will help optimise the haulage operation, which is underpinned by MinRes’ dedicated, private haul road running from Ken’s Bore to the Port of Ashburton.
Delivering a more efficient way of loading MinRes’ custom-designed road trains, the circuit features a bucket-wheel reclaimer loading ore onto a conveyor belt feeding product into trailers from above.
In May 2024, the project delivered first ore on ship ahead of schedule and has steadily been increasing volumes since.
MinRes Executive General Manager Onslow, Mike Tonkin, said the two latest pieces of plant would bolster the project’s
National transport company, TFMXpress, has announced the launch of its new purpose-built depot in Perth, Western Australia.
The new 10,000-square-metre depot further enhances TFMXpress’ ability to deliver its freight services with improved connectivity, state-of-the-art infrastructure and expanded capabilities.
It includes a range of features such as full drive around access as well as multiple recessed loading docks and roller doors for efficient unloading and loading of vehicles.
ongoing ramp up.
“Commissioning the third crushing plant allows us to significantly increase our crushing capacity and add to our stockpiles at Ken’s Bore,” he said.
“Similarly, the truck load out facility provides greater efficiencies to our haulage operation, allowing us to reduce loading times and increase the number of trucks transporting ore to the Port of Ashburton for export.
“Both pieces of infrastructure demonstrate the in-house capability within the MinRes business and I congratulate everyone involved in the safe delivery of our crushers and truck load out facility.”
TFMXPress said the significant investment enhances its ability to deliver efficiently across WA and beyond.
“This expansion is a significant step in our mission to provide even greater support to Australian businesses freight solutions across the country,” the company said in a statement online.
“With the demand for reliable freight solutions growing, our Perth depot ensures that TFMXpress remains well-positioned to meet those needs while helping local businesses thrive.
“As we continue to expand, we remain committed to providing the same level of personalised, customerfocused service that TFMXpress is known for.”
According to TFMXpress, the size of the new location will help ensure greater volume of deliveries in order to provide customers with reliable, ontime service.
In addition, the facility also links Perth to TFMXpress’ extensive national network of depots and services.
Qube has opened a new bulk storage facility in Picton, Western Australia.
With the capacity to store over 300kt of bulk minerals for export, the additional new bulk warehouse will be utilised for Iluka Resources’ significant operations across the South West region, boosting Picton’s under coverage storage capacity to 30,000 square metres.
Qube Bulk Director, Todd Emmert, was joined by Federal Member for Forrest, Nola Marino, Mayor of Bunbury, Jason Disan Miguell, Iluka Resources South West Operations Manager, Garry Green, and long term WA shed building partner, Q-Design, for a ribbon-cutting ceremony on the new building on 30 January.
“As a long-term local employer, with over
400 employees across the south west, Qube is focused on unlocking opportunities for current and aspiring importers and exporters,” Emmert said.
“Iluka is a great Australian company with large scale operations across WA including Narngulu, Catby and Capel.
“We are proud to support Iluka in their operations and ambitious endeavours.”
A major job-creating road project in Perth’s south has reached a critical milestone with a contract now awarded.
The $1 billion Tonkin Highway Extension and Thomas Road Upgrade Project will see the transformation of the southeast of Perth, delivering a 14-kilometre extension of Tonkin Highway as well as major upgrades to Thomas Road.
The extension will include including a four-lane dual carriageway from Thomas Road to the South Western Highway and a number of gradeseparated interchanges, underpasses and roundabouts.
The project will also cater for the recreation needs of the area with several equine underpasses and a new principal shared path along the entire 14-kilometre extension.
It will also benefit local communities in Byford, Armadale, Kelmscott and Gosnells which currently contend with large volumes of heavy vehicles on local roads.
The contract for Perth’s Tonkin Highway Road project has been awarded to the Tonkin Extension Alliance consortium which includes BMD, Civcon Civil and Project Management, Georgiou Group, BG&E and GHD.
Upgrades to Thomas Road will include duplication of 4.5 kilometres between Kargotich Road and South Western Highway, new principal shared path and upgrades to a number of local intersections including Kardan Boulevard, Masters Road and Plaistowe Boulevard.
According to Federal Minister for Infrastructure, Transport, Regional
Development and Local Government, Catherine King, the extension will directly increase road efficiency in the area.
“This project will deliver significant benefits to Western Australia’s freight and logistics network, by creating a high-standard north-south transport link, improving road safety, freight efficiency, and connectivity for residents, businesses, and commuters,” she said.
“The project is part of a broader investment to the Tonkin Highway that will deliver a high-standard north-south transport link, including key upgrades such as the Tonkin Highway Gap.”
This sentiment was echoed by Federal Member for Burt, Matt Keogh, who particularly addressed the easing of
The Ollera Creek Bridge has re-opened for all traffic following its recent collapse into floodwaters.
Priority works to deliver an interim repair solution for the bridge have been finished.
While future additional work will be required, the opening of the Ollera Creek Bridge has been fast-tracked to facilitate
freight movement prior to expected further flooding impacts north of Ingham.
“Teams on the ground have worked around the clock in inclement weather over several days to fast-track the repairs, and we celebrate and thank them for their hard work in managing to re-open the bridge and restore this vital connection for the community,” Transport
heavy vehicle road congestion as a key benefit for local residents.
“Extending Tonkin Highway will get trucks off South Western Highway, which will support this rapidly growing area, giving this community the roads they deserve,” he said.
“This will make a huge difference to everyday life – whether it’s dropping the kids at school or going up to the city, this is a game changing project for the southeastern suburbs.”
Construction of the project is scheduled to commence in mid-2025 with completion anticipated by late-2028 and is set to support around 4,400 direct and indirect jobs, marking a significant boost for the local economy.
and Main Roads Queensland said in a statement online.
“The bridge, which serves as a key link for vehicles travelling between Townsville and Ingham and surrounds is now accessible to the general public, after opening to essential freight, supply and emergency vehicles at 8pm last night [10 February].”
Logistics business, Northline, has moved into a new $16 million national service centre in Kent Town, South Australia. Following the company’s opening of a new $38 million depot in Brisbane at the end of last year, the latest growth phase
IT and logistics has never been stronger,” he said.
“This growth and our relocation to a new, custom designed service centre allows us to invest in the right people and technologies to strengthen our position in the market.”
JOST has announced its successful acquisition of global hydraulics company, Hyva.
The acquisition marks a significant milestone in the growth journey of JOST, strengthening its position as a leading supplier for on-highway and offhighway applications in the commercial vehicle industry.
By joining forces with Hyva, JOST enhances its regional presence –particularly in Asia and the Americas – and enters new market segments.
Hyva’s brand, recognised for its technological leadership and strong market position (40 per cent in hydraulic tipping cylinders), complements JOST’s existing offerings.
“With the Hyva brand as part of the JOST World, we are strengthening our business structure, customer base, and market positioning,” said JOST CEO, Joachim Dürr.
“Together, we will expand our global footprint, enrich our portfolio for transport and agriculture businesses, and boost our potential in the infrastructure industry.”
Customers will reportedly benefit from the comprehensive range of products, expertise and service across the globe, ensuring streamlined processes, consistent quality and access to specialised knowledge tailored to meet diverse regional needs.
By pooling R&D expertise, JOST and Hyva will also create an innovation platform focused on automated and digital solutions to meet emerging industry trends and evolving customer needs.
The combined strength of both brands elevates their global positioning, driving competitiveness and market leadership.
Hyva CEO, Alex Tan, said that joining the
JOST World represents an exciting new chapter for Hyva.
“Our shared commitment to advancing technology and providing reliable and innovative solutions for transportation, agriculture, construction, mining and environmental applications creates a strong foundation for mutual success,” he said.
“Together, we will drive growth and deliver even greater value to our customers globally.”
The acquisition was first announced in September last year when JOST revealed its intention to significantly broaden its worldwide product portfolio by purchasing Hyva.
Team Global Express and leading Chinese logistics provider, SF Express, have entered a partnership to drive increased bilateral trade, improve market access and deliver cost-of-living benefits for Australian consumers.
The partnership will enable customers to access integrated solutions that seamlessly combine Team Global Express’ multimodal network of rail, road, air and sea in Australia with SF Express’ technological capabilities and extensive aviation and road express network in China.
It will enhance cross-border trade opportunities – providing Australian businesses with faster and more efficient access to the world’s largest consumer market while offering Australian consumers greater choice and value.
Team Global Express Group CEO, Christine Holgate, said the partnership will strengthen the Australia-China trade lane and create new delivery opportunities.
“Australian businesses are in a prime position to benefit from China’s growing
demand for high-quality goods and services,” she said.
“This partnership not only strengthens our economic ties with China but also brings tangible benefits to Australian consumers through greater access to affordable and diverse products.”
The collaboration offers business greater access to China’s vast market, at the same time as leveraging the advantages from the China-Australia Free Trade Agreement (ChAFTA) to enable local exporters to increase their market share in China by benefiting from reduced tariffs on critical export sectors, such as wine, beef and lithium.
As the demand for high-quality Australian products grows across various categories, food and perishable goods in particular are poised to benefit from the faster and more efficient multimodal transportation solutions that this partnership offers.
Australian companies – especially small and medium enterprises (SMEs) – will also now have more opportunities to engage with Chinese markets, driving innovation,
creating jobs and boosting overall economic growth.
The partnership will also help Australian consumers by improving the speed, cost and reliability of imported goods.
With access to a broader range of products from China, Team Global Express claims that Australian shoppers can expect increased competition, potentially leading to lower prices on everyday goods.
“We are thrilled to partner with SF Express to enhance our international logistics capabilities and nurture the robust trading relationship between Australia and China,” Holgate said.
“Our collaboration will enable us to provide more efficient services to our customers, while fostering economic growth through integrated import and export solutions to our nation’s largest bilateral trading partner.
“By leveraging SF Express’ extensive infrastructure and expertise in China, we can better serve Australian businesses and consumers engaged in cross-border e-commerce.”
Qube Bulk has announced a contract with South Australian business Agfert Fertilizers.
The arrangement will help support growers on the Eyre Peninsula.
Qube will manage import arrangements through Whyalla Port for Agfert.
Fertiliser unloaded at Whyalla Port will be road transported by the Qube Bulk team to Agfert Fertilizers’ new distribution centre in Cowell, an hour away by road.
“Whilst we have a clear focus on our core business products at Whyalla, the diversification into the agriculture sector is exciting,” said Regional Manager, Brett MacDonald.
“Qube operates stevedoring and marine services in the ag sector right across the nation, so it’s nice to add this port to that list.”
The first cargo is due to arrive this month.
The end of 2024 saw Australia Post hit a new milestone for its busiest peak period, overseeing nearly 103 million parcels delivered between 1 November and 31 December, according to its latest quarterly Inside Australian Online Shopping Report.
Over these two months, 2,800 parcels were delivered to Australian households every minute in November and December. 7.6 million Australian households reportedly made at least one online purchase in November and December, showing a 2.4 per cent increase from last year.
According to Australia Post Executive General Manager of Parcel, Post and eCommerce Services, Gary Starr, Australia Post’s busiest day was on 9 December, when it delivered over 3 million parcels.
“The record volume of deliveries reflects Australia Post’s ongoing investment into new and upgraded parcel facilities, technology and fleet as well as a commitment to improving services for online shoppers,” he said.
“While we are proud of what we have achieved, we can always do better, and we’ll reflect on this peak to start planning for the next.”
Across Australia, Health and Wellness proved the most popular shopping category, reportedly growing by 20.5 per cent in the number of online purchases year-on-year (YoY), followed closely by Athleisure and Tools & Garden increasing by 15.8 per cent and 14.6 per cent, respectively.
Despite online sales increasing around the
country, the Northern Territory, Tasmania and South Australia saw the strongest yearon-year growth, with purchases from online sales events growing by 12.4 per cent, 11.44 per cent and 8.9 per cent, respectively.
Additionally, the top three suburbs for online shopping in Australia were Mackay and Toowoomba in Queensland, and Point Cook in Victoria.
The total number of parcels delivered between last November and December, up 3.1 per cent from last year, has been attributed to consumers turning to cyber sales following cost-of-living pressures and high inflation, fuelling a spike in
Emerald Carrying Company has appointed a new group CEO.
The appointment comes from within the company with Arron Johnson promoted internally to oversee both Emerald Carrying Company and Monaro Fuel Haulage.
“I’m not one for big announcements, but I wanted to share some news,” Johnson said in a statement online.
“After three and a half years as the Group General Manager, Greg Haylock
and the Haylock family has given me the opportunity to step into the role of Group Chief Executive Officer.”
Johnson became Group General Manager in August, 2021 having worked as the Northern Regional Manager previously.
“I’ll be honest – titles have never been what drives me,” he said.
“What does matter to me is the outstanding people I work with, the trust we build, and the results we deliver together.
online shopping activity.
Starr attributes the spike to Australia Post’s ability to anticipate consumer needs when making deliveries for online purchases.
“Consumers are more empowered than ever to manage their delivery experience,” he said.
“We’ve listened and understand their need for more reliability, simplicity and speed when ordering online, which has ultimately shaped the success of our best peak yet.”
The AusPost app was used by 4.6 million users to track their parcels between November and December, with a record 57 million visits in the latter month alone.
“That underpinned by our family values has always been the backbone of our company, and it’s something I plan to keep at the heart of what we do moving forward.”
Emerald Carrying Company was established in 1965 by Bill and Joan Haylock and today remains a family-owned and operated business specialising in bulk liquids transport and general freight.
The business acquired Monaro Fuel Haulage in 2016.
Global logistics provider, DB Schenker, has opened a new facility in Sydney’s west.
The 17,000-square-metre warehouse has been built to a 5 Star Green Star rating, designed to meet the highest standards of sustainability and operational efficiency.
This certification indicates that the site is future ready, protecting the community’s biodiversity and ecosystems, and contributing to market transformation and a sustainable economy.
Features of the site include solar panels and water heating, as well as rainwater collection and reuse.
Facilities also encourage emission reduced commuting through electric vehicle charging stations, bicycle parking and car share spaces.
As it looks to increase its presence across Australia and New Zealand, DB Schenker is introducing initiatives to pursue its broader sustainability ambitions across all sites and future facilities.
our dedication to serving the region by providing the right space and operational facilities in much needed locations for our customers, teams, and the community,” said Craig Davison, CEO Australia and New Zealand Cluster.
fitout allows us to better serve our customers in the Hi-Tech Electronic segment with improved efficiency and reliability.”
DP World and NSW Ports have announced a $400 million co-investment which will more than double the logistics company’s annual handling capacity and enhance Sydney as a key hub for trans-pacific trade.
DP World and NSW Ports are co-investing $400 million to extend the rail terminal at Port Botany in Sydney which will transform its logistics capability and reinforce the city’s position as a vital gateway for international trade.
NSW Ports is contributing $148 million for the new facility which will service both the Container Terminal and the Logistics Park. The project – which will start on site in June and take two years to compete – will see the addition of five new rail sidings to accommodate 600-metre-long regional trains.
According to DP World, this milestone marks a significant step in shifting freight from road to rail, reducing emissions and improving air quality.
“Our investment in this new port-centric logistics infrastructure will deliver more capacity, superior agility, seamless integration of processes, increased productivity and added reliability,” said DP World Executive Vice President, Nicolaj Noes. “We cannot wait for our present and future customers to reap the benefits of this world-class facility, which accelerates the shift of freight from road to rail while reducing carbon emissions and improving Sydney’s air quality at the same time.”
Key benefits of this initiative include:
• Enhanced capacity: annual rail capacity for DP World’s terminal will more than double, increasing from 400,000 TEUs to one million TEUs.
• Environmental impact: reduction in truck movements and carbon emissions, supporting Sydney’s sustainability objectives.
• Economic growth: improved logistics efficiency will deliver growth across key sectors from agriculture, manufacturing,
FebMarSepOctNovDecJan2025 AprMayJunJulAug
construction to retail and e-commerce, while driving sustainable job creation across New South Wales.
“This collaboration with DP World to deliver a new, enhanced, rail terminal continues the growth of on-dock rail capacity at Port Botany to service the state’s import and export trade,” said NSW Ports CEO, Marika Calfas. “This new rail terminal will enable more containers to be moved by rail, reducing the growth of trucks on roads and will deliver greater efficiency for the state’s container supply chains.
“Port Botany is uniquely the only port in Australia with on-dock rail within each container terminal, connected to an extensive network of metropolitan and regional intermodal terminals including by dedicated freight rail.”
The investment at Port Botany is the latest example of DP World investing in its
intermodal rail capabilities across several continents as it extends its reach into the global supply chain. Port Botany is NSW’s container port and has Australia’s largest common user bulk liquids facility. Handling 2.8 million TEUs annually, it contributes $10.7 billion to NSW’s Gross State Product each year. It is the only port in Australia with on-dock rail at all three of its container terminals and is directly connected, including via dedicated freight rail, to a network of metropolitan intermodal terminals and regional intermodal terminals.
Within the port, DP World operates the 20-hectare Sydney Logistics Park, the largest in the city with a capacity of more than 18,500 TEUs, offering services including warehousing, bonded storage quarantine activities, reefer monitoring and storage as well as container maintenance and repair.
CoolWay Trans has deployed another Carrier Transicold Vector HE19 multi-temperature refrigeration unit which has bolstered its cold chain logistics operations with great efficiencies and technological functions.
CoolWay Trans has made ripples in the refrigerated transport sector during its 10-plus years of operations. Founded in 2014, the family business has thrived in servicing Australia’s cold chain logistics needs while growing its national footprint to operate distribution centres in all the country’s capital cities.
When CoolWay Trans was last featured in Trailer (March 2024), the company had undergone big changes. A relocation into a new and second site in Glendenning and the delivery of five B-doubles were the latest developments for the fleet at the time.
The new year has clearly continued the company’s prosperous trajectory, with CoolWay Trans since further expanding its physical capabilities and value offering. And according to CoolWay
Trans Managing Director, Sunny Ahmed, the business isn’t showing any signs of slowing down.
“The company is going bonkers at the moment,” he says. “It has been growing by 30 per cent from last year.”
This 30-per cent growth is clearly shown in the current size of CoolWay Trans’ fleet. Twenty-two prime movers from last year have since become 36, and are now met with four additional B-double sets, a 26-pallet quad trailer and a gargantuan 32-pallet super quad trailer. Sunny attributes CoolWay Trans’ continued success to two key factors. The first is the business’ committed servicing of smaller enterprises and niche markets – entrenched in family values of loyalty, trust and integrity, CoolWay Trans has enthusiastically maintained positive
working relationships with those that propped it up with business in its early days.
“As a business, we’re looking to deliver quality service to our customers,” he says. “We try to stay away from big and corporate businesses so the small familyowned businesses receive support.
“We still deal with our very first customers, even 10 years on. It’s hard work, delivering juice buckets and ramen noodle soup into their shops, but those guys gave us our very first job. So, if they ever have a problem, we’ll get it sorted.
That’s what we do.”
The second factor contributing to CoolWay Trans’ continued success is its longstanding relationship with Carrier Transicold. Having officially partnered close to 10 years ago, Carrier’s
refrigeration technology has been intertwined with CoolWay Trans’ cold chain logistics capabilities ever since.
Drawn to both the company’s high cooling efficiency and values-driven customer service, Sunny has chosen Carrier time and time again as one of his desired collaborators in the industry.
“Carrier is a corporate business but it will treat you like a family,” he says. “When you need them and call them, they’ll always answer the phone, and that’s what we appreciate. They’re loyal to us and they get the job done which is what we want.
“Time is of the essence in the refrigerated transport industry. You need to get products out as quickly as possible, particularly if fridges break down on you. Carrier is reliable and we’ve stuck with them because of that.”
trailer configurations to meet their specific needs, while a multi-temp unit is perfect for the transportation of sensitive goods, intensive urban distribution, multiple door openings and loads of different types. In addition, different temperatures can be assigned to different sections of the trailer, allowing for total controlled separation when carrying different products.
This performance and versatility of the Vector HE19 has resulted in great efficiency throughout many dimensions of CoolWay Trans’ operations. The Vector HE19 multi-temp refrigeration’s added capability, for example, enables the transporter to make certain deliveries in one trip rather than two or more, thereby reducing the use of its other fleet vehicles and the various costs that come with additional truck and trailer journeys.
Additionally, the implementation of the Carrier Vector HE19 unit provides great environmental benefits. Though controlling multiple temperature zones like two fridges, the energy use of one multi-temp refrigeration unit is not noticeably different to a single-temp design. This advantage serves a particularly important role in the transport industry which is currently seeking ways to reduce its carbon footprint. By using the highly efficient Vector HE19, operators can benefit from improved fuel consumption by up to 30 per cent, reduced unit weight by 10 per cent and a noise emission lowered by 3 dB(A).
The combination of these benefits has provided Sunny and CoolWay Trans with the highest quality of transport and delivery capabilities.
“The Vector HE19 is so unbelievably efficient,” he says. “The ability to carry split loads gives us a much greater opportunity to service more customers, and the reduced environmental impact is so important for our industry, too. These kinds of capabilities are why we choose Carrier.”
The latest iteration of this partnership has come with CoolWay Trans’ new super quad 32-pallet trailer which is fitted with a Carrier Vector HE19 multitemp unit. The Vector HE19 refrigeration unit with E-Drive all-electric technology enables high performance cooling capabilities with maximum capacity and Contact
While CoolWay Trans is implementing its new trailer for deliveries between depots and distribution centres only, the company still enjoys massive savings in fuel and maintenance costs by being able to send fewer vehicles out for these freight tasks at a time. And, by not having to operate separate refrigerated
‘Tis
Scully RSV’s cold chain logistics capabilities were put to the test over last year’s manic Christmas season which saw peak demand for refrigerated goods and a strategically prepared fleet rollout from the company.
Scully RSV has come a long way from its humble beginnings. Founded as a family business in 1993, the company worked aggressively to respond to the great demand in the market of cold chain logistics, looking to break through a plethora of barriers to provide an essential service to customers around Australia.
Over time, Scully RSV’s service offering and constant ambition grew the business into a bigger and better operation, expanding its presence with large distribution and manufacturing facilities across states and boasting a fleet of over 1,000 refrigerated transport vehicles for hire.
Two thousand twenty-four proved to be yet another year of critical success for Scully RSV, setting the scene for major growth while proving its operational capacity. The Christmas holiday period,
according to Scully RSV National Sales and Business Development Manager, Glenn Smith, was the year’s peak for logistical demand and saw the company service a massive undertaking.
“We service some of the nation’s largest logistics providers, particularly during the Christmas peak season,” he says. “During this time, the volume being moved in the industry significantly increases.
“These logistics customers come to us for a solution to give them the equipment they need so that they can move highly demanded products. We play an integral role in enabling these deliveries of refrigerated goods that people want over Christmas time.”
Scully RSV’s refrigerated truck fleet mainly carries fresh produce such as meat and poultry, seafood, certain fruits and vegetables and a variety of dairy products. And although these products are always in
demand, they experience a particular spike over the holidays.
While this increase in demand for logistical services and deliveries could prove overwhelming to some, Scully RSV has worked meticulously to refine and prepare its service offering while rapidly growing as a company. Combining its operational capabilities and past experiences, the business has developed an ironclad process of rolling out its fleet to ensure the smooth navigation of the holiday season’s logistical frenzy.
Glenn believes this diligent planning and invaluable experience sets Scully RSV apart and acts as a vital ingredient to its successful Christmas period – with last year’s one being the busiest ever.
“We undertake a number of processes in advance of peak periods like Christmas,” he says. “Our fleet team thoroughly checks that everything is in order because we know that
all of our vehicles will go out to customers who need to be able to deliver the high volumes that come through.
“We’ve been doing this for a long time and the years of experience in our management team can be measured in the hundreds, so we know when the delivery volumes will increase. We get ahead of the curve and prepare ourselves so we can service demand efficiently and safely.”
Because of this extensive experience in dealing with periods of high logistical demand, Scully RSV is able to effectively anticipate the physical hotspots that the demand can be connected to. According to Glenn, areas with higher populations typically require a strong logistical presence as a greater concentration of people want more refrigerated goods.
Partnering with organisations like OzHarvest and Food Bank, to name a couple, Scully RSV provides assistance in supplying food and other goods to these communities. The company’s relationships with these initiatives are particularly strengthened over the Christmas period when a greater number of people in these communities tend to need food assistance.
Scully RSV’s commitment to community partnerships stems from its strong family values which have remained core principles that guide the company’s business operations and mission.
“We’re very keen on making sure we participate on the ground in the communities that we service,” Glenn says. “Having commenced as a family business and having carried those family values through to our management structure today, it is extremely important to us to employ local people and to engage with charities and community organisations in the places we operate. This is an essential investment that Scully RSV will continue to make.”
the addition of another branch will be determined by where the demand can be found.
“We follow our customers where they take us,” Glenn says. “We built a customer base in Perth and quickly expanded our operations to keep up with the growth, and the same thing happened in Melbourne and Sydney in Scully RSV’s early days. Now our customers have most recently taken us to Adelaide, so we put a branch there to support that.
“We go where the demand is, and we fill that gap by putting operations on the ground to service our customers right.”
The 2024 Christmas period required a large cold chain logistics provider that was up to the task of connecting customers with their desired refrigerated goods. As a powerhouse of the sector, Scully RSV naturally filled this role and provided a consolidated service for the transport industry, ensuring these essential goods got to the right people in time for the holidays.
In addition to this focus on metropolitan areas, Scully RSV is equally committed to servicing more regional areas of the country, many of which do not have as much infrastructure to hold refrigerated goods. As part of servicing these regional areas with cold chain logistics solutions, Scully RSV is also heavily involved in a range of community partnerships which focus on delivering the food and community services required. Contact
Coming off the intense period of sustained demand last Christmas, Scully RSV is looking to expand its outreach further across Australia. Last year saw the company open its newest branch in Adelaide, and
Ph: 1800 728 559
Web: www.scullyrsv.com.au
Higher Mass Limits, has provided a great return on investment.
Family-owned and operated since the 1960s, APCO Service Stations is a key player within its industry with a large focus on local people, great food and coffee and fuel at the right price.
With 27 stores around Australia and growing, APCO has developed a fair understanding of the importance of reliable and high-quality fuel since its inception more than six decades ago. And, to maintain its standards, the business runs a fleet of five permanent B-double tankers and a single tanker from its Geelong, Victoria, base to deliver fuel to its service station network throughout the country.
The Holmwood Highgate fleet works on a 24/7 basis, with four drivers allocated for each combination working on 12-hour rotating shifts. On average, the fleet travels approximately 30,000 kilometres throughout Victoria a week, with contractors
also delivering to sites in Mildura, Victoria, and Wagga Wagga, New South Wales, which are the furthest from the company’s home base.
APCO has just deployed a new 23-metre B-double from Holmwood to bolster these operations. With high volume sales at its various sites, APCO Service Stations Logistics Manager, Scott Curtis, says the unit is key in helping the fleet deliver fuel to these locations.
“These deliveries have traditionally been sent on 19-metre or 20-metre B-doubles, but we are now able to access some of the sites with the new 23-metre one,” he says.
The new B-double tanker features a three-compartment lead trailer and a five-compartment rear trailer, with all the compartments allowing for a safe fill of 8,300 litres of fuel. Thanks to its steerable rear axles, APCO is able to
carry the payload of a traditional 25-metre combination and in addition gets a “brilliant turning circle” which makes entries and exits to sites much more easier.
“We are also trialling using Hendrickson suspension and axles on this unit,” Scott says. “Along with alloy hubs and disc brakes, it has resulted in a tare weight saving of 400 kilograms.
“We had the ladder on the rear trailer mounted on the front of the barrel to get a nice, clear area for advertising as well. This provided a fantastic opportunity for our APCO Foundation to advertise and get the word out with a bold pink message across the rear of the barrel.”
APCO now standardises getting the barrels painted silver prior to the APCO stripes and signage being applied.
“We find the painted barrels do not show the dirt as much and are easier to clean,”
Scott says. “We’ve found that the quality and finish of Holmwood’s tankers is excellent.”
The new tanker combination has been active for over a month now, and Scott says the drivers have been very happy with its on-road handling.
“It sits on the road nicely and is easy to operate,” he says. “It can travel up to 10,000 kilometres a week in busy times when it’s on the long-distance work. For instance, if it does two Wodonga trips out of Geelong in 24 hours, it does just over 1,500 kilometres.
“Based on these figures, we would expect the unit to travel 450,000 kilometres annually.”
Through the National Heavy Vehicle Accreditation Scheme’s (NHVAS) Mass Management accreditation, APCO is also able to operate under Higher Mass Limits (HML). The new B-double has been running at a Gross Combination Mass (GCM) of 68.5 tonnes, resulting in a payload of around 46 tonnes and a series of benefits.
“We’ve gotten the payload of a 25-metre combination on this one while still being at 23 metres,” Scott says. “Plus, with the steerable rear axles, we are able to get it into sites you wouldn’t be able to access with a standard 25-metre unit. There are no Performance-Based Standards (PBS) requirements either so it is quick and simple to get on the road.”
According to Scott, the reason APCO went with Holmwood for this unit is the same as it’s been for every purchase since the first –the outstanding quality he’s become familiar with.
“We chose Holmwood to build this B-double as the quality and finish is excellent,” he says. “I worked with Wayne Sloane on the design of the unit and he listened to our requirements and made sure everything that we wanted was included in the build.
“The quality of the Holmwood product is excellent. We have had minimal downtime with the Holmwood tankers in our fleet and we’ve found that the product holds up better. We still have a 19-metre model from 2003 still in service which is testament to that.”
Working with Wayne, Scott says, has also been a major highlight of his Holmwood purchases.
“Wayne has been great to deal with when I’ve been looking for a quote or wanted to run a concept or idea past him,” he says. “Even if we haven’t got anything on the order books, he will always call in just to see how things are going.”
In addition, Holmwood’s service department plays a pivotal role in the maintenance of APCO’s B-double tanker fleet. All of its trailers are serviced monthly
and also undergo an annual major service from the trailer builder.
By collaborating with Holmwood for these processes, Scott is able to keep on top of all maintenance protocols. Just as important, he’s reminded that he truly is a valued customer.
“We prepare a 12-month plan for service in conjunction with Holmwood’s service staff so that nothing gets missed,” he says. “Due to the high utilisation of the fleet, Holmwood assists to keep it serviced and safe. They carry out all the six-month Safe Loading Pass (SLP) inspections for us and they also operate an excellent 24/7 breakdown service which is handy as our fleet works at all hours.
“We get the feeling that we are an important customer when dealing with the Holmwood team and their Operations Manager, Clayton Stephens, and that’s a great way to feel. So, we have a great relationship with Holmwood because they have always put in the extra effort for us to keep our fleet on the road. They are always incredibly busy, but nothing is ever too much trouble for them.”
Contact Holmwood Highgate
Ph: 03 9936 0360 | 07 3440 9000
Web: www.holmwoodhighgate.com.au
Norman Carriers is celebrating its 75th anniversary with a new delivery of Performance-Based Standards skels from Freighter Group which are improving efficiency across the business.
Norman Carriers is a family-owned Australian company which was established in 1949 primarily as a port logistics transport company. Seventy-five years down the track, the business has since expanded into a larger entity with further capabilities in the fields of warehousing and custom freight solutions, all while keeping its heritage of port operations intact.
Norman Carriers has come a long way since founder, Norman Hearnden, opened its doors all those years ago. The business has experienced significant growth over the years through a series of expansion phases and business developments which have turned it into a one-stop shop for freight handling solutions. This is testament to the hard work and dedication of not only Norman who set the business up for
success, but his son, Graham, who followed in his footsteps and then passed the reins to his own son, Gareth, who now leads the business with the same values established by his grandfather.
“We’re honoured about where we are now, and it does come from collaboration over the years with partners, family and friends,” says Norman Carriers Safety and Compliance Officer, Richard Wyles.
“As a business, this milestone is the beginning of our future growth throughout Australia. We’ve just opened up a new office in Sydney, and that’s the start of our expansion across the eastern seaboard and eventually into Western Australia.”
The aforementioned growth which Norman Carriers has experienced along the way, Richard says, has been a key highlight for the company. Across its five warehouses in New South Wales and Victoria, Norman Carriers has significantly increased its capacity for palletised storage and custom freight while truly becoming a force to be reckoned with – its recent developments including acquisitions of Transfleet Tranport last year have led to very strong year-on-year (YOY) growth increases of 60 per cent annually since 2021.
The amount of success seen in recent times has, as expected, resulted in higher demand. And to cater for this, the fleet specifically turned to Freighter Group for new fleet investments. The latest is an order of Performance-Based Standards (PBS) skels which, operating at Higher Mass Limits (HML), were designed specifically with improved productivity in mind. The delivery consisted of a triaxle A-double skel combination and two single quad-axle skels, with one being a retractable version.
“It was all about maximising the amount of weight we could carry on the road,” Richard says. “We got the retractable version for better flexibility because it would allow us to carry heavier 20’ shipping containers and still have the ability to back up to a loading dock by retracting the trailer.”
Having the skels in the fleet, Richard says, has unlocked the ability for Norman Carriers to handle up to 32-tonne containers to sites without needing subcontractors and third parties involved – giving it complete control over every delivery.
“We used to have to outsource a different trailer that could take the weight to meet our sideloader mid-transit, but now that we can take that heavier weight, it’s reduced our subcontractor costs significantly,” he says. “We’ve now got that in-house and can do it ourselves, and that was a key focus.”
Depending on the prime mover, the Freighter A-double skel has a Gross Combination Mass (GCM) of 91 tonnes and payload capacity of up to 60 tonnes. Meanwhile the Freighter retractable skel,
in a single semi combination, can run with a GCM of up to 50.5 tonnes and a payload of up to 33 tonnes.
The trailers have been given the task of carting heavy cargo from the wharf precinct in Melbourne back to Norman Carriers’ depots. Based on their operations so far, they have been performing extremely well.
“We haven’t had any issues with them at all,” Richard says. “We’re very happy with the new assets and we’ve been putting them to good use. The A-double combination is on the road every day from four o’clock in the morning through till midnight, and it’s getting a good workout in its travels.
“The product is a quality build. The craftsmanship is really good, and that’s another one of the reasons why we went with Freighter. We’re after a quality product that is going to take the mass that we need and has the support in the background, and Freighter Group has the skill, knowledge base and partnerships to ensure that a seamless solution is provided.”
According to Richard, feedback from the drivers has been nothing but positive. The new skel trailers have already become renowned within the fleet for handling really well thanks to the steerable axles fitted.
The high productivity skel trailers have paid off for Norman Carriers by bolstering its transport operations and improving efficiency across the business. Richard hands it to Freighter Group for not only providing such a successful solution but being completely transparent and accommodating while doing so.
“Freighter Group is excellent to deal with,” he says. “They are very proactive, and the level of communication that supported us through the sales and delivery process was great.
“What’s important about the order was the communication that our salesman, Heath Menhennet, and their PBS Engineering team provided. They were always keeping us informed about what stage we were at and the expected delivery timelines, and they also accommodated quick swap-arounds – we had the single skels scheduled to come first but then we managed to swap them around and get the A-double first. So, we were able to make little tweaks like that through the process because they were very accommodating.”
This “second-to-none” service is ultimately what has constructed such a close collaboration between Norman Carriers and Freighter Group over many years.
“We’ve had a longstanding relationship with Freighter Group,” Richard says. “We actually invited the guys from Freighter to our 75th anniversary party, so it was really nice to see them there. They’ve always been quite responsive to our needs and have provided the support and understanding we’ve needed through the processes, so we’re looking forward to some more purchases in the future. We’re not going to slow down, so as we expand we’ll always reach out to Freighter Group.”
Contact
Freighter Group
Ph: 03 5339 0300
Web: www.freighter.com.au
Vawdrey’s Auto Lock Air mezzanine deck solution has become a standard feature in ATT Logistics’ fleet of Titeliners due to its ability to significantly improve productivity and safety.
ATT Logistics commenced its operations more than 35 years ago as Amalgamated Couriers & Taxi Trucks and is now known as one of Brisbane’s largest logistics operators, with locations throughout Victoria and New South Wales as well.
The fleet specialises in the transport of fast-moving consumer goods (FMCG) and providing contract logistics capabilities for its blue-chip client base along with distribution and warehouse services available too. These include warehouse storage and distribution, supply chain solutions, cross-docking, container consolidating and de-consolidating and much more.
“Our mission is to become the favourite partner and supporter of Australia’s leading retailers, with safety being a part of everything we do,” says ATT Logistics Director, Garry Clarke. “We’ve been expanding fairly well with growth seen year after year.”
ATT Logistics’ first growth phase saw the company expand its operations in Melbourne in 2017 with the opening of its Keysborough location. From there, it opened a Sydney site in Yennora in 2020.
While there’s been a lot of change at ATT Logistics and more to follow (plans to further expand into Adelaide and Perth are currently in progress), the business has retained a lot of factors along the way. This, Garry says, is something very important to the heart of it.
“Our organisation has a balanced growth plan that involves further collaboration with its existing customers while ensuring that new relationships are in line with the core offerings of our business,” he says. “Even though our company has grown over the last few decades, we’ve retained our balance of organisational size with a personal touch. We’ve had some of our customers for 19 years now, and to stay with them and have that longevity means
we’re doing something right.”
ATT Logistics’ relationship with Australian trailer manufacturer, Vawdrey, is a prime example of this commitment to retaining partnerships.
“We have a great relationship with Vawdrey,” Garry says. “They’re very responsive and if we need equipment they make sure we get it in time. If we’ve got a very tight lead time on a new contract, they’ll bend over backwards to make sure we hit the targets.
“Vawdrey is at the forefront with technology, too. They’ve always got new things to show you which is important, so it’s a very good relationship.”
ATT Logistics began dealing with Vawdrey shortly after its inception when it was time to start purchasing new trailers. Since then, the company has established an extensive fleet of 250 trailers all from Vawdrey which include standard B-doubles, Titeliners, refrigerated trailers,
48’ flat tops and mezzanine drop decks. Remaining with ATT Logistics through thick and thin, they have each played a significant role by catering to the increased demand seen as the company has continued to grow.
“They have been very reliable,” Garry says. “They’re built robust, so they’re strong and very hard to hurt. They’ve been really good.”
The trailers operate predominantly throughout metropolitan areas in Melbourne, Brisbane and Sydney. They travel from Brisbane to Newcastle every day, as well as to and from Mildura within Melbourne and as far as Canberra within their Sydney routes.
ATT Logistics’ latest trailer delivery consists of three 48’ mezzanine deck Titeliners each fitted with Vawdrey’s Auto Lock Air mezzanine deck solution, a feature which is spec’d as standard on all of the fleet’s mezzanine floor trailers. The units arrived towards the end of last year and according to Garry have been performing exceptionally.
“The new trailers have been very good, they don’t give us any dramas at all,” he says. “We use the Auto Lock systems because we want to be safer, and we want our drivers to know that. They are
much easier than having to move decks manually, so they’re a great safety feature for our fleet.”
Vawdrey’s Auto Lock Air mezzanine deck solution allows operators to raise or lower decks via a forklift without having to climb the trailer platform and handle them manually. The system also increases pallet capacities for businesses by providing maximum flexibility in transit, resulting in better efficiency and higher payloads.
In addition, it is also able to significantly reduce the amount of time it takes to change deck positions in a trailer – unlocking a whole other level of productivity. Garry himself is a big fan of it.
“I like it, it’s really good,” he says. “It’s pretty safe and easy to use, so it’s a really good setup.”
The productivity and safety benefits of the system have been two major advantages for ATT Logistics.
“The guys are unloading twice the product when they get into the larger warehouses,” Garry says. “So, while they are cringing at the fact that they have to do more work, it means we are a lot more productive.
“The Auto Lock solution is also reducing damage to the product because there’s plenty of room in the trailers and you can fit different configurations of pallets in
them. That’s definitely been a big benefit for the business.”
In terms of the success that ATT Logistics has experienced in recent years, Garry attributes a lot of it to the trailers that have been able to keep up with the increased demand. This, he says, is also testament to Vawdrey itself.
“Our Vawdrey trailers have certainly catered to the growth experienced,” he says. “We’ve bought a fair few trailers over the time, so they grow with us.”
Garry also commends Vawdrey and the people behind it for supporting ATT Logistics to no end.
“Vawdrey’s aftersales service is impeccable,” he says. “Nothing’s a problem when it comes to that. Vawdrey is very flexible and they’ll work with you to find a solution.
“They’re very trustworthy, and I’ve just stayed with them because they’ve never let me down. We build a relationship with every supplier we have, and we’ve had this relationship for years.
“You can rely on Vawdrey, and that is very important in our game.”
Contact Vawdrey Australia
1-53 Quantum Close Dandenong South, VIC 3175
Ph: 03 9797 3700
Web: www.vawdrey.com.au
KingKira Group has taken delivery of a new scrap tipper road train from Bruce Rock Engineering to service Western Australia’s mining and resource industries.
KingKira Group is a 100-per cent female Aboriginal-owned business that has operated in the Pilbara region of Western Australia for over a decade. Founded by Tammy O’Connor in 2014, the company has worked diligently to provide practical and environmentally sustainable waste management solutions for the mining sector.
These solutions, shaped by core beliefs of respect, innovation, sustainability and empowerment, are delivered through the company’s own integrated environmental sciences framework which considers the handling of total waste management, recycling and industrial services in ways that uphold the natural health of the land local companies operate in.
KingKira Group’s waste management work has proven extremely successful in the Pilbara region, securing longterm contracts with Tier One mining companies and growing both presence and operational capacity. The business now oversees waste management across over 15 mine sites throughout the state,
according to KingKira Group Manager of Environmental Services, Mick Garkaklis.
“The company has experienced significant growth over the past decade,” he says. “This sustained success has facilitated our expansion, with support depots now strategically located in Port Hedland, Newman and Karratha.”
KingKira Group’s success has also necessitated an expansion of its fleet and equipment to better deliver on the value offering of total waste management.
Looking for a versatile vehicle boasting the top quality required for its delivery of sustainable waste management solutions, the company has partnered up with state-local manufacturer, Bruce Rock Engineering (BRE).
BRE’s reputation as a reliable Australian brand as well as its own manufacturing locations which closely aligned with that of KingKira Group’s depots led to the fleet approaching the trailer builder for a collaboration.
“BRE is a well-established Western Australian brand,” he says. “Their state-
of-the-art facilities reflect the company’s strong commitment to product quality, service excellence and client satisfaction.
“We are pleased to have engaged with BRE for the construction of our first fleet of scrap tipper trailers.”
The new scrap tipper trailers in question are scheduled to be rolled out in the Pilbara region and will be applied to the transportation of bulk scrap metal (both ferrous and non-ferrous-based materials) from mine sites to a resource recovery yard in Port Hedland for additional processing before being exported. This process is a key example of the company’s recycling program and overall goal of ensuring sustainable engagement with waste.
The scrap tipper trailers were spec’d with various features to address their loading and weight capabilities. More specifically, KingKira Group approached BRE Sales Manager, Peter Oliver, to discuss the exact designs needed to create a fleet of vehicles able to safely handle the heavy waste from mining and
resource companies.
According to Peter, the design of the trailers has achieved a level of stability and control due to their Electronic Braking System (EBS) braking fittings which are weighed down by the implementation of SAF-Holland airbag suspension.
Additionally, the vehicles were further fitted with weight scales and a quickdrop function to ensure convenience and safety when loading and transporting waste.
“With the weight scales which we put on the trailers as well as the dollies, operators can see exactly how much weight they’re putting on without having to run in and across a weighbridge,” he says. “As for the quick-drop function, if the trailer starts to lean while it is tipping, operators can flick a switch on the truck which lowers the body at twice the speed of a normal trailer.”
BRE also fitted the scrap tipper trailers with side-swing tailgates to ease the delivering of scrap metal to the recycling
facility, ensuring no material would be trapped inside the back of the trailers during unloading.
Mick expresses excitement for the partnership between KingKira Group and BRE – two companies which both stand to strengthen their operational capabilities and brands and hope for it to set a precedent of further collaboration on new initiatives.
In addition to enjoying similarities in site locations and functionality, the partnership between KingKira Group and BRE is further underpinned by their business values which come together to create an exciting synergy. BRE’s manufacturing revolves around the delivery of consistent and high-quality products which build the brand’s trust and accountability for consumers, while KingKira Group’s approach is entrenched in its identity and values, prioritising inclusivity, sustainability and plans for sustainable growth among individuals and communities.
“Bruce Rock Engineering is centred on operational excellence and KingKira Group focuses on transformative, progressive growth,” Mick says. “It is this dynamic partnership that will ensure stakeholder expectations are consistently met.”
KingKira’s inclusive and sustainable approach to waste management in the Pilbara region has proven successful for more than 10 years, prioritising empowering waste solutions which recognise the land’s traditional ownership and cultural significance.
This approach has been amplified with the help of BRE’s delivery of scrap tipper trailers. Together, the two companies have strengthened their capabilities and ensured diligent waste management in WA’s mining and resource sectors.
Contact
Bruce Rock Engineering
15 Swan Street, WA 6418
Ph: 08 9061 1253
Web: www.brucerockengineering.com.au
A fleet of 120 trailers has shown Compliant Asset Rentals the true value of utilising Moore Trailers equipment.
Compliant Asset Rentals is a company based in Torrington, Queensland, which supplies solutions to the transport industry in the form of trailers and prime movers for hire. It came about during the onset of Covid-19 on the back of Pengelly Trucks and Trailers, a truck sales business which had the chance to expand further in the market and took the shot.
“We wanted to venture into hire because we saw the opportunity for customers that had short-term contracts,” says Compliant Asset Rentals Operations Manager, Matt Cruickshank. “A lot of people had uncertainty about the longevity of their contracts particularly during the Covid period, so we started with four second-
hand prime movers and we’ve since grown to a fleet of 80 to 100 trucks and over 300 trailers.”
Compliant Asset Rentals’ business model is pretty straight forward. Customers come to the company with a list of what they require, and if Matt and his team don’t have something, they will source it. This is where Moore Trailers, the fleet’s predominant brand of trailers, plays such a critical role.
“Once we started in the rental game and needed to source trailers, they were the obvious choice,” Matt says. “They’re good guys for a start, but they’re also local and they build a good quality product at a fair price.
“Reactivity is also a big thing in our
business because we need to source equipment to a deadline most of the time. Moore Trailers has certainly been able to perform the best and particularly during the Covid period when equipment was very hard to source.”
Compliant Asset Rentals has now accumulated 120 Moore trailers and dollies. The latest to join the fleet are 10 new water tankers as well as a road train of flat tops, and there’s new trailers coming in all of the time – Compliant Asset Rentals has an ongoing order arrangement with Moore Trailers which sees it constantly replacing older equipment with new units to cater for the market’s demand.
Throughout this developing relationship,
Moore Trailers has also been working very closely with Compliant Asset Rentals to get the specifications exactly as the company and its customers need them.
“Our orders are now a running spec that we ask for each time,” Matt says. “We put a lot of work into our tankers in particular to get them to the spec that we require.
“Our flat tops and side tippers are the same, so it makes it very easy for us as well as Moore Trailers as a manufacturer if we’re just simply repeating the last order every time.”
Moore Trailers’ local proximity and its flexibility with accommodating to customer requirements are two key factors which drew Compliant Asset Rentals to it. And, the fact that there’s been “nothing but positive feedback” from its own clients, Matt says, has been a big bonus.
“This is very important, because if the customer is happy with the equipment we provide then they’re more likely to keep it and call us again,” he says. “That customer satisfaction is pretty much
guaranteed with Moore Trailers.
“If we have a project deadline to meet or if we need to customise the design to a degree, they will work with us to achieve it. It’s never a drama to change things on the fly, because Moore Trailers works with us to achieve what our customers expect from us.”
For Compliant Asset Rentals, it seems the “obvious choice” in Moore Trailers was the right choice.
Ph: 07 4693 1088
Web: www.mooretrailers.com.au
Following JOST’s acquisition of Hyva, Allied Waste Concepts has deployed a new unit fitted with hooklifts from the company into its waste operations.
Global transport component manufacturer, JOST, just recently announced its acquisition of international hydraulics solutions provider, Hyva, early in February.
After months of negotiations and awaited approval, the acquisition will see Hyva’s operations in over 110 countries – including Australia – fall under JOST ownership, consolidating its outreach and product servicing around the world.
The acquisition marks a significant milestone in the growth journey of JOST, strengthening its position as a leading supplier for on-highway and off-highway applications in the commercial vehicle industry. By joining forces with Hyva, JOST has enhanced its regional presence and entered new market segments.
Among the various local companies already intertwined with Hyva’s products and servicing was Allied Waste Concepts, a company which has been handling the
transport of contaminated waste for over 20 years.
Founded in 2004 by the Briggs and Buxton families, the family operation had observed what it felt was a severe disconnect between the large promises of companies to consumers and their actual value offerings. Looking to fill this gap with its tight-knit values of hard work, loyalty and transparency, Allied Waste Concepts began the collection and transport of both EPA and non-EPA waste with its one truck around Brooklyn, Victoria.
In the following years, Allied Waste Concepts’ waste transport capabilities grew steadily, a testament to its meticulous and values-fuelled business approach which, according to Director of Business, Doug Briggs, will remain integral to the business in spite of its increasing size.
“When Allied Waste Concepts was born, there was a need in the industry for
businesses that would do what they said they would do,” he says. “Allied Waste Concepts has been built on that. It has been built on giving proper service and will continue to do so.”
This sentiment was echoed by Allied Waste Concepts General Manager and one of Doug’s Sons, Jay Briggs.
“Our family’s values are present in everything we do,” he says.
Guided by these core principles, Allied Waste Concepts now boasts a much bigger operation consisting of a seventruck fleet with an eighth on the way, and a large staff of personnel ensuring the business runs smoothly.
In tandem with the fleet’s physical growth, its waste transport capabilities have been bolstered by the company’s relationship with international transport equipment solutions manufacturer, Hyva. Initially connected to Allied Waste
Concepts by recommendation from Tevfik Onguc at Scania following the purchase of the business’ first truck, Hyva has supplied Allied Waste Concepts with state-of-the-art hooklifts and customer service for nearly five years.
“The first time we ventured into the Hyva hooklift was off a recommendation from Scania,” Jay says. “Since then, our relationship with Hyva has been fantastic. Murray and Richard from the company have been awesome to deal with. They always answer the phone if we have any rare issues or breakages, and they’ll give us prompt advice on how to fix or rectify them.”
Hyva hooklifts have been spec’d on Allied Waste Concepts’ last three trucks and they have just been fitted to the fleet’s newest one which arrived at the end of February. The addition of these hooklifts provide the units with a much greater ability to pick up and transport a variety of waste items.
The multi-rail hooklifts feature manually adjustable 1,450mm and 1,570mm pick-up hooks with a pnuematic locking safety latch. These enable the truck to lift waste bins to a higher elevation than previously possible and to turn the bins to a greater tilt angle than before, allowing for the collection of more waste types. Liquid waste, collected from sludge bins, can be
emptied out and collected with greater ease due to the trucks’ new elevation and angle capacity provided by the hooklifts.
These new capabilities allow Allied Waste Concepts’ combinations to service a greater number of segments and collect a wider range of waste. According to Jay, the company’s overall reach and value proposition has been significantly amplified by the installation of Hyva hooklifts.
“Hyva’s hooklifts help us to service all areas of the market,” he says. “In addition to the extra rail widths and bin heights that we can access to transport more waste, we also have the flexibility to move materials that we haven’t previously been equipped to move.
“The hooklifts also provide our trucks with greater stability when lifting waste due to their solid locking system.”
Allied Waste Concepts’ implementation of Hyva hooklifts brings the company great operational benefits and access to quality product servicing.
“I think it’s going to be business as usual for our company,” Jay says. “The JOST brand has a greater capability to hold more stock and will have more branches to access for product availability or service. That will be very exciting. But otherwise, we’re just going to continue with the work we have set out to do.”
Allied Waste Concepts’ headquarters in Brooklyn is well-positioned to receive servicing and product parts from numerous JOST dealerships. These open channels will help the company to consolidate its transport services over time with the supply of equipment and servicing.
Allied Waste Concepts has operated a smooth and efficient waste transport operation with the help of Hyva hooklifts, developing a strong working relationship over nearly five years.
JOST itself is excited over the Hyva acquisition and the beginning of dealings with Allied Waste Concepts. JOST General Manager of Sales and Marketing, Corey Povey, acknowledges the involved history between both companies from when JOST Australia was a distributor for Hyva around 25 years ago.
“JOST and Hyva both have a strong brand reputation and excellent product range,” he says. “We look forward to providing national support to the Hyva team and help the business grow further, especially in the recycling sector.”
Contact
JOST Australia
Ph: 1800 811 487
Web: www.jostaustralia.com.au
E: sales@jostaustralia.com.au
Holmwood Highgate is a leader in the tanker manufacturing industry, renowned for its diverse range of capabilities. With cutting-edge technology and a commitment to innovation, we specialize in creating tankers that cater to various sectors, including oil, gas, and chemical transport. Our expert team blends engineering excellence with sustainability practices, ensuring each tanker is built for efficiency, longevity and safety. From bespoke designs to robust production processes, Holmwood Highgate, and it’s associated brands, are dedicated to delivering high-quality solutions that meet the evolving needs of our global clients.
With growth in our brands we have seen the expansion into local firsts and industry demanding transportation systems. We offer various applications for bulk liquid, gas, bitumen, food, ANE and more to cover Australia’s ever growing need and hunger for unique transportation options.
BITUMEN TANKERS
AMMONIUM NITRATE EMULSION
FOOD AND MILK
INDUSTRIAL GASES - (LPG & CRYOGENIC)
DRY BULK
AVIATION FUEL
COMMERICAL GRADE FUEL
Queensland 07 3440 9000 20-26 Burchill Street, Loganholme, QLD, 4129
Victoria 03 9936 0360
425 Fitzgerald Road, Derrimut, VIC, 3026
Convair Engineering executes high-quality tankers to completion by specifying Rhino Guards’ stainless steel mudguards as standard on all of its builds.
Convair Engineering is a trailer builder based in Epping, Victoria. Founded in 1993, it has specialised in the design, manufacture and supply of pneumatic dry bulk tankers for over 30 years. The company also constructs ISOtainers and onsite storage tankers from steel and aluminium which it imports for the food, chemical, construction materials and oil and gas industries.
The key to being a reputable manufacturer within the road transport industry is not only having a highquality product that will withstand the
environments and operating conditions it’s thrown into, but one that customers will be completely happy with. And, by selecting Rhino Guards as the exclusive supplier for its stainless steel mudguards, this, according to Convair Engineering Sales and Business Development Manager, Steve Gnafakis, has been achieved.
“When Rhino approached us, we were pretty impressed with the quality of their product – especially the mudguards, so we started using them,” he says. “We’ve been using them ever since, and we’ve
received some really good feedback from our customers.”
Convair Engineering was introduced to the Rhino product around one year ago. Steve says the business was starting to have some issues with another product at the time, and the quality and finish of Rhino’s stainless steel guards was what carried Convair Engineering over the finish line.
“What impressed us from the get-go was the smooth finish,” he says. “It has no ripples on it, and it’s also quite strong and doesn’t tear easily. That was what got us the line.”
Convair Engineering has since gone full bore with Rhino, fitting its stainless steel guards as standard to every unit it builds. Steve says the feedback he’s received from the workshop is that they’re very easy to fit, and the praise doesn’t just end there.
“The customer feedback has been really positive as well,” he says. “The issue with our previous guards was initially brought up from our customers who weren’t happy with the finish, and that’s what really prompted us to start looking into alternatives.
Annealed (BA) to manufacture its stainless guards which gives them ultimate durability and finish. More specifically, 1.2mm-thick stainless steel is utilised, which is more robust that thinner products offered and not as heavy as thicker options – striking the optimal balance between strength and weight.
Rhino’s BA has a smooth, bright, reflective finish typically produced by cold rolling followed by annealing in a protective atmosphere in order to prevent oxidation and scaling during
want everything to look good, and this has definitely helped us with the finishing off of the tankers.
“You often get customers who will walk around and pinpoint every single blemish when picking up a new tanker, so having a mudguard that is smooth and shiny helps us out because it means we have no issues and that we get positive feedback.”
On top of all this, Steve also has extreme confidence in Rhino’s customer service abilities.
“I personally haven’t had any problems,
Knorr-Bremse has relocated into a new state-of-the-art facility in Dandenong South, Victoria, successfully consolidating its operations and upscaling its production in one fell swoop.
Knorr-Bremse’s 120-year history began in Berlin, Germany. Founded by Georg Knorr in 1905, the company entered the commercial vehicle systems market with a design for the pioneering K1 freight train rapid release brake. Following a string of breakthrough inventions, successful patent filings, an expanded product line and international outreach eventually spanning 30 countries – including Australia through its arrival in 1987 – Knorr-Bremse remains a manufacturing powerhouse in today’s competitive market.
On a more domestic scale, Knorr-Bremse Australia has also enjoyed continued success. Operating within the country for nearly 40 years, the division has amassed over 450 employees across six sites. However, the company outgrew its two production sites in Granville, New South Wales, and Keysborough, Victoria, as the business sustained its growth. This ultimately led to its move into one
consolidated facility which will propel the business into the future and accommodate the growth expected in the years to come.
“The CVS business has had some really good growth over the last 10 years,” says Knorr-Bremse General Manager for the Commercial Vehicle Systems (CVS) division in Australia, Michael Roche. “If I look back to 2015, our turnover has grown by nearly 150 per cent since then. We’ve outgrown the facilities that we were previously in.”
Knorr-Bremse Australia’s expansions have enabled the company to consolidate all facets of its business under one roof in Victoria. The new Dandenong South site consists of a 2,500-square-metre warehouse with an additional 367 square metres of office space.
“We’ve consolidated all of our business and put it into a bigger one-site facility where we can now distribute all of our parts and do all of our production, kitting
and configuration activities out of the same location,” Michael says. “We chose this site because it’s closer to the transport hub in Melbourne where the majority of our customer base, being trailer and prime mover OEMs, are. So, we can optimise our processes and service our customers more effectively out of this one facility.”
In addition to this, the location gives Knorr-Bremse better opportunities to develop products locally, test technologies in-house and train customers on its offerings.
“That was taken into consideration with the move,” says Knorr-Bremse Technical Operations Manager for the CVS division, Ronnie John. “We have a dedicated space for in-house testing. Moving forward, we want to transform it into a training room with technology which our engineers will be able to trial and test, as well as using it to train external service partners and customers.”
Meanwhile, Knorr-Bremse’s Granville site continues to house the rail and HVAC divisions, with CVS retaining a smaller administrative presence there. Ronnie explains that this shift played a key role in the design of the new facility in Dandenong South.
“It was a blessing for us to be in the previous facility as we were able to understand the restrictions of what we had and what we couldn’t do,” he says. “Once we started migrating to the new site, we made sure we took those restrictions into consideration.
“We strategically allocated fast-moving goods to easily accessible areas and optimised our operations to be more efficient and user-friendly. This allows us to work more effectively with a strong focus on improving overall productivity and ensuring a smooth workflow.”
Prior to the move, Michael, Ronnie and the Knorr-Bremse team had discussions on an ongoing basis to understand where the business was growing. With space being the biggest constraint, it was clear to them that notable investments would be needed.
“We’ve made a significant investment into this brand-new, state-of-the-art facility”, Michael says, “and we will continue to invest in our business, whether that’s through our people, tools, resources or new technologies.
“We’ll upgrade to cutting-edge racking and shuttle systems, and beyond that, we’ll invest into ourselves from a green perspective. For example, we’re exploring the installation of solar panels on the roof to ensure we operate as a sustainable business.”
Ronnie attests to the company’s shift to more sustainable practices, explaining that the new site presented a great way to
“We did a lot of things to incorporate more efficient and eco-friendly features when we initially moved,” he says. “When adding the lighting, for example, we made sure they were LED.
“Waste reduction is another one of our main concerns, so we implemented recycling programs and we’re also reducing excess packaging.”
In addition to amplifying production and distribution capabilities for the company, Knorr-Bremse’s myriad investments into the new Dandenong South site stand to deliver numerous benefits for customers. The facility’s new size advantage provides the ability for the company to better manage its internal processes and prepare parts for delivery at a much faster rate, without needing to divert attention to other product manufacturing like at the previous site.
This streamlined process enables a better response to urgent customer requirements, as Knorr-Bremse is able to focus entirely on relevant orders that come through and is much more adaptable to sudden changes in production.
manufacturing scale is an impressive achievement in its own right, the fact that its occurrence aligns with a major anniversary makes the success that much sweeter for Knorr-Bremse.
“Knorr-Bremse is celebrating its 120th anniversary this year, so it’s exciting that we’ve been able to expand this year,”
Michael says. “It’s a milestone year for us, but it’s also the milestone of being able to control our own business, processes and systems in order to continue on the same growth trajectory we’ve been on.”
The relocation of Knorr-Bremse’s headquarters in Australia is a testament to the company’s growth and relentless ambition to drive progress. Equipped with the right resources and a committed team in place, Knorr-Bremse is well-positioned to continue advancing in the commercial vehicle systems sector – it won’t be pumping the brakes any time soon.
Contact Knorr-Bremse truck.knorr-bremse.com/en/au/
Capral Aluminium has shared a near 50-year history with Muscat Trailers, providing essential materials and services to the manufacturer’s quality builds.
Muscat Trailers’ family operation has navigated five decades of the competitive trailer manufacturing industry. Initially conceptualised by Maurice Azzopardi, the company’s true form was developed with the collaboration of Paul Muscat in New South Wales during the mid-1960s.
Its first factory, restored from an old chicken shed with dirt floors, was the site of the company’s then-handful of trailer designs. Muscat Trailers has since grown into a formidable manufacturer in the industry, having manufactured close to 6,000 trailers and now sporting over 20 designs built by a large and loyal team.
In this time, Maurice passed the business operations to his son, Troy, who has been in close proximity with the company since
he was a child and has enjoyed a firsthand view of its growth.
“I was coming to work with my dad at the age of four or five, driving forklifts and everything that I wasn’t allowed to do,” he says. “The business has grown humbly and slowly from then.
“It was always the vision of my dad and his partner to do things with a hands-on approach and be in control of what’s happening. That’s the way I feel. My whole vision is moving forward – I want to be in control of what we want to supply to the market.”
This hands-on approach has defined Muscat Trailers’ manufacturing process, allowing it to create its products with certain unique touches and finesses to
reward customers and meet their specific needs. The process is one of delegation, in which, following a customer’s order, 3D models are created, drawn and sent to separate workshops for aluminium, steel, fit outs and installs to be produced before being combined and sent off.
The unique orders that Muscat Trailers fulfil often result in design and production amendments – something which Capral Aluminium, the company’s aluminium supplier, is adept at handling.
“It’s important for us to work with suppliers that have the ability to be adaptive, to make quick changes and complement what others build,” Troy says. “Capral is very good at that.”
Muscat Trailers has enjoyed a relationship
with Capral effectively since its inception back in the 1960s. The supply of Capral’s aluminium and extrusions over the decades to follow have been integral to Muscat Trailers’ production process, with each trailer containing roughly two-and-ahalf tonnes of aluminium according to Troy.
Capral also supplies all of the aluminium rolled products, sheet, plate and treadplate used by Troy and the team in the construction of Muscat trailers.
Troy has observed that trailer design and manufacturing has shifted – while precise and surgically designed products were once in vogue, customers are expressing interest in more craftsmanship within their trailers, preferring a personal touch to manufacturing. In response to this, Muscat Trailers has developed its trademark rippled aluminium extrusions which, locally produced by Capral, create a key differentiator for a Muscat trailer with their more intimately-designed feel.
“The ripples in the side of the extrusion of a Muscat trailer is unique to us,” Troy says. “It’s like our tattoo.”
Capral’s material and engineering involvement in Muscat Trailers’ manufacturing process is further bolstered
by its customer service. The supplier’s ability to hold stock is greatly beneficial, enabling the accommodation of any customer order delays or changes.
“The holding of stock gives us the ability to forecast and plan our work, knowing the material is going to be there when we need it,” Troy says. “Capral is really good and very fair to work with.”
An equally important aspect of Muscat Trailers’ manufacturing capabilities come from the staff that the company sources. Troy’s employee base has become very diverse in the wake of domestic shortages, but he has found this variety has brought operational advantages for Muscat Trailers.
“With the short skill set available, we’ve got a lot of foreign workers that bring in a really unique element and have helped produce a good product,” he says. “But more than that, they’ve brought a lot of cultural diversity within the workplace, which I feel is good.”
Muscat Trailers’ decades of business have been defined by its strong relationships. In addition to the company’s cultural diversity which has been cultivated to serve the brand, its near 50-year relationship with Capral is a focal point of its operations, yielding a myriad of benefits for both parties.
From material supply to engineering capabilities, Capral and Muscat Trailers’ collaborations have been marked by quality, reliability and efficiency.
Contact
Capral Aluminium
Ph: 1800 258 646
Web: www.capral.com.au
In the transport industry, every decision impacts the bottom line. Tyres are no exception.
For Australian transport operators, selecting the right tyres is critical to efficiency, safety and cost savings. Haulmax Tyres’ products have been engineered to handle the toughest conditions, ensuring fleets stay on the road longer and perform at their best.
But Haulmax itself is more than just tyres. It’s a complete ecosystem, integrating a national tyre solutions and support network and cutting-edge technology to optimise fleet operations. And for trailer builders, its purpose-built trailer tyres set the benchmark for reliability and cost efficiency.
Haulmax tyres are designed to thrive in the demanding Australian transport environment, offering application-specific solutions that maximise durability and performance. With a focus on reducing operating costs and increasing longevity, Haulmax provides application-specific engineering tailored to handle Australian highways, outback roads and heavy loads; ultimate durability with reinforced casing construction for extended tyre life; and industry-leading warranty and CPK guarantee for protection and peace of mind with every tyre.
“Trailer tyres bear the brunt of transport loads, making their performance and longevity essential,” says Australian Tyre Traders National Marketing and Communications Manager, Daniel Sapsead. “Haulmax Tyres offers a range of trailer-specific solutions, including the ATT101 and ATT105-Pilbara, engineered for efficiency and endurance.”
Haulmax ATT101 is a robust, highperformance trailer tyre designed for longevity, stability and efficiency. Built to excel in linehaul, it delivers superior wear resistance and durability for fleets covering long distances. Meanwhile Haulmax ATT105-Pilbara, being purposebuilt for Australia’s harshest routes, is designed specifically for extreme conditions, delivering superior resistance
to wear and optimised performance in tough environments.
standards, they exceed them,” Daniel says. “That’s why leading trailer manufacturers and transport operators trust Haulmax Tyres.”
A great tyre is only as good as the service backing it. That’s where Haulmax Wingman comes in. With over 550 partners nationwide, Haulmax Wingman provides fleet operators with consistent, high-quality support wherever they operate. From multiple-depot servicing to linehaul and local support, Haulmax Wingman ensures that fleets get the best possible return on their tyre investment.
But tyre performance isn’t just about rubber on the road – it’s also about datadriven insights. Haulmax Tech Solutions goes beyond traditional Tyre Pressure Monitoring Systems (TPMS) to deliver realtime monitoring, proactive maintenance alerts and GPS tracking.
With Haulmax Tech Solutions, fleet operators can expect: • Reduced downtime: Proactive alerts for pressure loss, hub overheating and potential wheel loss.
Fleet operators face increasing pressure to reduce costs, enhance safety and improve efficiency. According to Daniel, the Haulmax ecosystem – spanning tyres, national service and smart technology – delivers real-world solutions to these challenges.
“For trailer builders, choosing Haulmax means choosing proven performance, industry-leading support and data-driven efficiency,” he says. “We recently asked Vawdrey Australia Director, Paul Vawdrey, about which of his customers use Haulmax tyres, and his response was, ‘The smart ones’.
“So, whether you’re designing trailers for interstate transport or off-road haulage, Haulmax Tyres ensures every journey is safer, smarter and more profitable.”
Contact Haulmax Tyres
Ph: 1300 677 524
Web: www.haulmaxtyres.com.au
Deck
Coldcore
Etnyre
Titan
PBS
E-Plas’ QuickSilver Heavy Duty floor liner option has gained quite the momentum since it arrived in the Australian market last year.
Allow QuickSilver Heavy Duty to reintroduce itself. Last year, E-Plas launched a brand-new floor liner to the Australian market in partnership with Mitsubishi Chemical Advanced Materials (MCAM) which, having already demonstrated its dominance throughout Europe and the United States in global applications, was destined for Australia.
Building on the expertise behind the standard QuickSilver product, QuickSilver Heavy Duty was specifically designed for high-demanding tipping operations to offer operators a more durable and longer-lasting truck liner.
“We identified a very specific wear and flow issue that we wanted to address,” says E-Plas National Operations Manager, Rupin Joshi. “The standard QuickSilver truck lining was already a premium product, however we wanted to better address the specific needs of a niche group within that market.
“We wanted to come up with something that would give customers experiencing extreme wear issues better extended life.”
The end result is QuickSilver Heavy Duty, a product that was specifically designed for purpose in applications which require a lot of abrasive product to be transported over a number of trips.
The main benefit of QuickSilver Heavy Duty is that it can handle extreme abrasion under high intensity tipping, with wear capacity and flow improvements also being key advantages of its use. The new liner to the QuickSilver range, as a result, is the perfect solution for applications where wear is the issue due to the number of trips completed or the abrasiveness of the material used.
QuickSilver Heavy Duty is ideally suited to the intense demands of Australia’s heavy vehicle users and has already proven itself in such applications overseas. For example, E-Plas and MCAM compared QuickSilver with a wear resistant steel liner with a customer which was looking to save weight while getting a similar product lifespan. According to
MCAM, QuickSilver Heavy Duty achieved both of these factors – the product has already lasted double the time which the wear resistant steel liner material did and is still in its application.
E-Plas and MCAM recently conducted another case study which compared the classic QuickSilver with QuickSilver Heavy Duty liners through the applications a customer which was transporting a very abrasive material. The results found that Heavy Duty lasts approximately 30-per cent longer than the classic QuickSilver.
The product was also trialled in another case study in Switzerland where the customer was very impressed with its performance.
“The customer told me, ‘I have tried every liner that is available, but nothing
performs like QuickSilver Heavy Duty from a wear point of view’,” says MCAM Linings Sales and Marketing Manager, Orson Yong. “The drivers also confirmed that it unloaded better than anything else.”
According to E-Plas, operators can gain a significant increase in payload each trip when using QuickSilver Heavy Duty over standard steel as well. And when looking at the material able to be transported in each load, it has found that Heavy Duty can increase carrying capacities while also decreasing workloads due to less cleaning necessary. The latter is ultimately a result of its flow improvements.
That being said, QuickSilver Heavy Duty has made quite the impression since its launch in Australia with there
now being several applications of it within the country.
According to Rupin, one local customer found that their standard aluminium liners weren’t lasting long and the more abrasive-resistant Heavy Duty material seemed to solve their problem.
“We’ve been monitoring the use on that particular vehicle and everything has been going well,” he says. “The install was finished early this year, so although it’s only been in operation for a short time, the early signs are looking positive.
“We have another customer in Victoria who has used it in a pretty highdemanding application as well and they are very happy with the product’s performance, reporting no issues.”
QuickSilver Heavy Duty was first developed by MCAM in the United States. The international company was founded in the 1960s and with its expertise in the field, it saw the need to add to the QuickSilver range with an option dedicated to abrasive bulk materials.
According to Orson, the original objective was for it to take over the very demanding jobs which the standard QuickSilver product wasn’t coping in. It’s had a snowball effect since then in the global market and now Australia, and the snowball isn’t slowing down.
“It has been holding up really well, and the customers using QuickSilver Heavy Duty are constantly giving us feedback that they are very satisfied with its performance,” he says. “The performance metrics are very justifiable for them. While Heavy Duty is at a higher price, its performance outweighs the price difference.”
The QuickSilver Heavy Duty liner is especially well-suited for the construction, quarries, mining and glass recycling industries due to its ability to handle high intensity tipping of highly abrasive and high impact materials. Available in 12mm-thick coils, it is most efficient for sand, gravel, rock, recycled glass and construction rubble applications which require eight or more trips per day. For applications that require less loads, QuickSilver classic, also supplied in 12mm-thick coils, remains a perfect choice. On top of that, the Heavy Duty variant is available in custom lengths and sizes upon requests.
The relationship between MCAM and E-Plas dates back to when the plastic specialist first arrived in the Australian
market. MCAM has remained by its side ever since and continues to play a key role in E-Plas’ operations down under.
“We are so pleased that we have the privilege to work with E-Plas in the Australian market,” Orson says.
“As a global company, we have lots of experience and case studies – whether it be success stories or failure stories – that we bring to the table, and that will go a long way in working to the benefit of the customers in Australia.
“So, we are not here just to supply a product to our distributor and push it out to the customer. We are here to provide a solution that is consistent. We’re always spending time to look at the problem and coming up with an engineered solution.”
Contact E-Plas
Ph: 03 8361 1791
Web: www.eplas.com.au
Calibre Steel has supplied businesses across Australia with top quality steel plate products for many years – its experience with managing steel plate supply chains being an integral part of the value offering.
Calibre Steel is a renowned distributor, processor and stockist of steel plate, catering to a wide range of industries across Australia. With dedicated facilities in Melbourne, Sydney, and Perth, Calibre Steel provides essential steel plate products for manufacturing and fabrication customers nationally.
The company offers an extensive selection of steel plate products complemented by value-added processing services. The product range includes Australian-made structural steel plate, laser plate and quench-and-tempered steel plate products, including key brands XLERPLATE steel and TRU-SPEC steel made by BlueScope and BISALLOY products manufactured by Bisalloy Steel. In addition, Calibre Steel possesses significant expertise in international supply chains, enabling the sourcing of high-quality products from global steel mills to meet specific customer requirements.
Calibre Steel has several strategicallylocated warehouses designed to securely store products and protect them from the elements. And, the company’s use
of overhead crane systems ensures the safe and efficient handling of steel plates, guaranteeing that each product is delivered in optimal condition. This dedication to precision and quality enables Calibre Steel to be a trusted partner for trailer manufacturers, supplying the materials needed to meet the most demanding specifications.
In addition to its premium steel plate products, Calibre Steel offers a comprehensive suite of value-added processing services designed to streamline customer manufacturing and fabrication processes in alignment with industryspecific requirements. These capabilities include plasma and oxy cutting, bevelling, ultrasonic testing and robust material traceability, all underpinned by strict adherence to compliance standards.
Calibre Steel’s comprehensive products and services are delivered by a dedicated, highly skilled team, committed to providing exceptional customer service.
As highlighted by Customer Relationship Manager, Maddie Dharmapala, this unwavering commitment to quality ensures
that every client receives tailored solutions that exceed expectations.
“Our team is dedicated to providing exceptional service in steel plate supply to the transport manufacturing sector,” she says. “We have a wealth of knowledge and experience in our team and we have a deep understanding of steel plate management, whether it is offering the best range of products or collaborating closely with customers to deliver value-add processing services tailored to suit their specific needs.
“We are committed to supporting our customers’ business objectives and fostering partnerships based on mutual understanding. Our focus is on attention to detail and responding swiftly to ensure the delivery of outstanding results.”
Calibre Steel remains a leading supplier of steel plate, with its experienced team continuously developing tailored supply solutions to meet the unique needs of each customer.
Contact Calibre Steel Web: www.calibresteel.com.au
Celebrating its 50th anniversary this year, heavy transport industry supplier, Tramanco, pays respect to its history, its flagship product and the loyal customers who made it all possible.
Tramanco’s history is a classic success story. Founded in May 1975 by Roger Sack out of his friend’s suburban workshop in Goodna, Queensland, Tramanco was initially just a small-scale manufacturer for the heavy vehicle industry. Its technical direction was informed by Roger’s own experience working for various engineering divisions in the prime mover manufacturing sector which proved extremely successful for the company.
Six months after its establishment, Tramanco’s operations relocated to a larger site in Rocklea. According to Roger, this move enabled its manufacturing capabilities to expand and its product offering to grow as a result.
“We expanded our capabilities and continued to offer truck engineering conversions like wheelbase alterations, lazy axles, twin steers and tandem and tri-drive set ups,” he says. “We also ventured into converting 4x2 and 6x4 trucks to all-wheel drive, as well as adapting Ford tractors for underground mining operations at Mount Isa mines.”
Tramanco’s growing innovative momentum led Roger to pursue the development of accurate on-board weighing solutions after noticing an increasing demand for them – a development which would eventuate in the creation of the CHEK-WAY ELIMINATOR and KWIK-CHEK.
Committing to properly servicing this increasing demand, Roger and the company underwent extensive research to look for unique and meaningful ways to tap into the market.
“After exploring options from the United Kingdom, Europe and the United States, we thought that the existing systems fell short for Australian conditions,” he says. “This was especially the case with B-doubles. However, driven by necessity, collaboration with our customers and a commitment to improvement, we
enhanced these systems.”
This enhancement led to the introduction of a handheld remote with a dot matrix display to make multicombination truck weighing more efficient.
Building on this efficiency, the 1980s saw Tramanco leveraging microprocessor technology – eventually leading to the development of the company’s own refined weighing systems which also incorporated its patented RAW DATA function. By 1981, these systems had been road tested and proven, and required upscaled production to keep up with the growing demand.
Following the closure of its local printed circuit board supplier shortly afterwards, Tramanco took the full scale of manufacturing into its own hands. Thus, the CHEK-WAY ELIMINATOR was officially born, followed by KWIK-CHEK.
The CHEK-WAY ELIMINATOR offers weighing solutions for vehicles across a myriad of industries such as transport, mining, agriculture and waste collection. KWIK-CHEK is made of the same components and is suited to trucks of different sizes – 4x2, 4x4, 6x2, 8x4 and
10x4. It also features the option to link trailers via Bluetooth in order to function as standalone weighing systems.
The outreach of both the CHEK-WAY ELIMINATOR and KWIK-CHEK has connected Tramanco with a wide range of customers who have since remained loyal to the brand. According to Roger, these customers have always been at the forefront of his mission for the last 50 years.
“From day one, our focus has always been on delivering exceptional customer service,” he says. “Without their unwavering support since our first birthday on 14 May 1975, we wouldn’t be celebrating an incredible milestone. Their trust and partnership have been the foundation of our journey.”
Tramanco’s 50-year tenure in the world of heavy transport manufacturing has been one of great success. The company has amassed great production capabilities, influence and customers. With no apparent end in sight, Tramanco is ready for another 50.
Contact
Tramanco
Ph: +617 3892 2311
Web: www.tramanco.com.au
The Australian Livestock and Rural Transporters Association is celebrating its 40th anniversary this year – a significant milestone for the organisation and the transport industry it has relentlessly served.
Two thousand twenty-five marks 40 years in which the Australian Livestock and Rural Transport Association (ALRTA) has been representing and supporting rural operators within Australia’s transport industry. The achievement is a remarkable feat for the association which began on 9 October 1985 when a group of transporters met in Sydney and created what was called the Australian Livestock Transporters Association (ALTA) at the time.
The ALTA was founded with the mission to unify and advocate for rural transporters across Australia. The first meeting, led by Livestock Transporters Association of Queensland President, Bruce McIver, and Livestock Transporters Association of Western Australia President, Jack Mitchell, brought together operators with one objective – to create a national voice for the industry and unify rural transporters across Australia.
“Queensland and Western Australia were the first states to start,” says ALRTA President, Gerard Johnson. “The other states followed suit, and the ALRTA formed afterwards to look at the federal issues that affected all of the states.”
ALRTA’s strength lies in its grassroots foundation. The association has always been led by people directly involved in the industry, ensuring the association stays practical, relevant and committed to the real needs of its members. This, Gerard says, has been critical to its resilience.
“We’re a very strong organisation, and I think that’s mainly due to the passion of the people involved,” he says. “The members that make up the association are all very hands-on in the industry, and I think that’s been the driving success behind the ALRTA.”
Frasers Livestock Transport is one of these members – the company played a significant part in the establishment of the ALRTA and is still heavily involved with the association to this day.
“It’s important that the people representing an industry are working in it, and the ALRTA has got skin in the game,” says Frasers Livestock Transport Director, Ross Fraser. “The early days weren’t without any challenges, but Queensland livestock carriers were instrumental in providing the financial backing to set the ALRTA up.”
According to Ross, the initial forming of the ALRTA really set the mark for what it is today. He explains that the original members, including himself, put a lot of practices and procedures in place which have helped change the face of transport in Australia.
“The ALRTA has been a huge success, and the basis under which we set it up 40 years ago is one of the reasons why,” he says. “The 40th anniversary is a great milestone and it’s testament to the support
that the industry has given the association over the years.”
As the ALRTA celebrates four decades of operation, it reflects on the dedication of those who started ALRTA, the progress made along the way and the ongoing mission to support the transporters who play such a vital role in rural Australia.
“It’s an honour to be President of the ALRTA, especially when you look at some of the people that have been involved over the years,” Gerard says. “We’ve always tried to do the right thing for the industry, and that’s what we’ll continue to do in order to get the best outcome for our members.”
Contact Australian Livestock and Rural Transporters Association
Ph: 02 6247 5434
Web: www.alrta.org.au
For your convenience, we present to you a contact list of all participating trailer builders. Whether you would like to place an order for trailing equipment or learn more about a trailer manufacturer’s expertise and capabilities, see below for their details.
AAA Trailers
41 Ricky Way
Epping VIC 3076
Ph: 1300 333 888
Web: www.aaatrailers.com.au
Absolute Trailer Solutions
94 Second Ave (Old Stanthorpe Rd)
Warwick QLD 4370
Ph: 07 4661 5966
Web: www.atrailer.com.au
ADCO Trailers
54 Barrow Road
Spring Farm NSW 2570
PH: 02 4658 2844
Web: www.adcotrailers.com.au
Air & Gas Industries
19 Industrial Avenue
Wacol QLD 4076
Ph: 07 3271 5899
Web: www.airgas.com.au
AJ Stock
3 Visor Court
Holden Hill SA 5088
PH: 08 8263 4233
Web: www.ajstock.com.au
Aldom Transport Engineering
280 Cormack Road
Wingfield SA 5013
Ph: 08 8346 3711
Web: www.aldom.com.au
Allroads Transport Engineers
65 Copal Road
Willyung WA 6330
Ph: 08 9844 3883
Web: www.allroads.com.au
Alltruck Bodies
245 Frankston-Dandenong Road
Dandenong VIC 3175
Ph: 03 9791 2144
Web: www.alltruckbodies.com.au
BArends Trailers
189-191 Thomas Street
Murray Bridge SA 5253
Ph: 0427 823 481
Web: www.arendstrailers.com.au
ATB Engineering
4/225 Leitchs Road
Brendale
QLD 4500
Ph: 07 3205 2268
ATE Tankers
9-35 Vella Drive
Sunshine West VIC 3020
Ph: 03 9310 2722
Web: www.atetankers.com.au
Austate Enterprises
15 Swaffham Road
Minto NSW 2566
Ph: 02 8795 0600
Web: www.austateservices.com.au
Australian Trailer Manufacturers
39 Middle Road
Trafalgar VIC 3824
Ph: 03 5633 3450
Web: www.austrailer.com.au
AZMEB
85 Radius Drive
Larapinta QLD 4110
Ph: 07 3726 1166
Web: www.fwr.com.au
Bailey’s Body Builders
2 Browning Road
Armadale WA 6112
Ph: 08 9399 5485
Web: www.baileysbodybuilders.com.au
Barker Trailers
44 Clancys Lane
Woodend VIC 3442
Ph: 03 5427 9999
Web: www.barkertrailers.com.au
Barry Stoodley
32 Tikalara Street
Regency Park SA 5010
Ph: 08 8340 2033
Web: www.barrystoodley.com.au
Base Fabrications
37 Weston Street
Naval Base WA 6165
Ph: 08 9437 9381
Web: www.basefabrications.com.au
Beavertail Trailers
30-32 Grandlee Drive
Wendouree VIC 3355
Ph: 03 5336 2555
Web: www.beavertrailers.com.au
Boomerang Engineering
14 Wheeler Street
Belmont WA 6104
Ph: 08 9277 2522
Web: www.boomerangengineering.com.au
Borcat Trailers
477 Victoria Steet
Wetherill Park NSW 2164
Ph: 02 9631 9594
Web: www.borcat.com.au
Bozmac
96 Lower Mt. Road
Harvey Bay QLD 4655
Ph: 07 4124 5425
Web: www.bozmac.com.au
Brentwood Trailers
4 Harris Street
Port Kembla NSW 2505
Ph: 02 4276 2030
Web: www.brentwoodtrailers.com.au
Brimarco
17-19 Coronet Street
Wendouree VIC 3355
Ph: 03 5339 1000
Web: www.brimarco.com.au
Bruce Rock Engineering
15 Swan Street
Bruce Rock WA 6418
Ph: 08 9061 1253
Web: www.brucerockengineering.com.au
Bulk Transport Equipment
12-16 Fowler Road
Dandenong South VIC 3175
Ph: 03 9794 0330
Web: www.bte.net.au
CByford Equipment
Business Park Cobb Highway
Moama NSW 2731
Ph: 03 5482 0666
Web: www.byfordequipment.com.au
Byrne Trailers
278 Hammond Avenue
Wagga Wagga NSW 2650
Ph: 02 6923 7300
Web: www.byrnetrailers.com.au
Cain Equipment
Building 6/102-128 Bridge Rd
Keysborough VIC 3173
Ph: 1800 462 246
Web: www.cainequip.com.au
Capital Body Works
50 Belmore Street
Tamworth NSW 2340
Ph: 02 6765 5944
Web: www.capitalbodyworks.com.au
Chassis Line
18 Carrington Road
Toowoomba QLD 4350
Ph: 07 4633 1466
Web: www.chassisline.com.au
Chris’s Body Builders
2-24 Burwood Avenue
North Sunshine VIC 3020
Ph: 03 9311 6124
Web: www.chrissbodybuilders.com.au
CIMC Vehicle Australia
20 Whitfield Boulevard
Cranbourne West VIC 3977
Ph: 1300 202 462
Web: www.cimc.com.au
Coastal Transport Engineering
1 Glendale Close
Denmark WA 6333
Ph: 08 9842 6050
Web: www.coastaltransportengineering.com.au
Convair
91-93 Miller Street
Epping VIC 3076
Ph: 03 9408 7255
Web: www.convair.com.au
CTE – Custom Transport Equipment
73 Wellwood Road
Drouin VIC 3818
Ph: 03 5625 5408
Web: www.ctequip.com.au
Custom Quip Engineering
73 Logistics Boulevard
Kenwick WA 6107
Ph: 08 9258 9688
Web: www.customquip.com.au
Damouni Tipper Bodies
Freighter
233-243 Learmonth Road
Wendouree VIC 3355
Ph: 03 5339 0300
Web: www.freighter.com.au
Freightmaster Semi Trailers
D F21 Brett Drive
Carrum Downs VIC 3201
Ph: 03 9775 0909
Web: damounitipperbodies.wixsite.com/website
Drake Trailers
19 Formation Street
Wacol QLD 4076
Ph: 07 3271 5888
Web: www.thedrakegroup.com.au
Duraquip
PO Box 1/102 Cecil St
Gnowangerup WA 6335
Ph: 1800 197 873
Web: www.duraquip.com.au
Ekebol
E1 Industrial Avenue
Kunda Park QLD 4556
Ph: 07 5445 4755
Web: www.ekebol.com
Elphinestone Engineering
36 Tasman Highway
Triabunna TAS 7190
Ph: 03 6257 3242
Web: www.elph.com.au
Euro Pantech
E: dave@europantech.net
Ballarat VIC 3350
Web: www.europantech.com.au
Felco Manufacturing
9 Production Court
Wilsonton Toowoomba QLD 4350
Ph: 07 4630 2213
Web: www.felco.net.au
Firmus Group
2-2 Progress Court
Laverton North VIC 3026
Ph: 1300 294 253
Web: www.firmusgroup.com.au
Fleetrite
5 Stark Court
Harristown QLD 4350
Ph: 0439 735 031
Web: www.fleetrite.com.au
G566 Waterloo Corner Road
Burton SA 5110
Ph: 08 8280 6475
Web: www.freightmastertrailers.com.au
FTE
9 Healey Road
Dandenong South VIC 3175
Ph: 03 9794 7466
Web: www.fte.com.au
FWR Australia
85 Radius Drive
Larapinta QLD 4110
Ph: 07 3726 1166
Web: www.fwr.com.au
G H Varley
21 School Drive
Tomago NSW 2322
Ph: 02 4964 0499
Web: www.varleygroup.com
General Transport Equipment
159 McDowell Street
Kewdale WA 6105
Ph: 08 9352 4000
Web: www.gtetrailers.com.au
Gippsland Body Builders
5 Darcan Way
Drouin VIC 3818
Ph: 03 5625 5580
Web: www.gippslandbodybuilders.com.au
GLT
2/39 Silica Street
Carole Park QLD 4300
Ph: 1300 731 442
Web: www.glttrailers.au
Graystar Trailers
219 Dundas Street
Preston VIC 3072
Ph: 03 9484 4568
Web: www.graystartrailers.com.au
Hamelex White
H233-243 Learmonth Road
Wendouree VIC 3355
Ph: 03 5339 0300
Web: www.freighter.com.au
Hammar Australia
9 Cunneen Street
Mulgrave NSW 2756
Ph: 02 4577 7700
Web: www.hammarlift.com/au
Harris Trailers
1/28 Bluett Drive
Smeaton Grange NSW 2567
Ph: 02 9186 3791
Web: www.harris-trailers.au
Haulmark Trailers
1848 Ipswich Road
Rocklea QLD 4106
Ph: 07 3277 3666
Web: www.haulmark.com.au
Heath Busch Trailers
Lot 1, Wambianna Street
Brocklehurst NSW 2830
Ph: 02 6888 5100
Web: www.heathbuschtrailers.com.au
Hercules Engineering
87 Canterbury Road
Kilsyth VIC 3137
Ph: 03 9728 2111
Web: www.hercqld.com.au
Hockney & Co
425 Fitzgerald Road
Derrimut VIC 3026
Ph: 03 9936 0360
Web: www.hockneyandco.com.au
Holmwood Group
20-26 Burchill Street
Loganholme QLD 4129
Ph: 07 3440 9000
Web: www.holmwoodgroup.com.au
Howard Porter
134 Barrington Street
Spearwood WA 6163
Ph: 08 9418 0000
Web: www.howardporter.com.au
Jamieson
714-720 Port Wakefield Road
Parafield Gardens SA 5107
Ph: 1300 526 437
Web: www.jamieson.com.au
JG Schulz
199-201 Cormack Road
Wingfield SA 5013
Ph: 08 8262 2447
Web: www.schulz.com.au
MLKKennedy Trailers
131 Forge Creedk Road
Bairnsdale VIC 3875
Ph: 03 5152 6362
Web: wwww.kennedytrailers.com.au
Krueger Transport Equipment
275 Fitzgerald Road
Derrimut VIC 3030
Ph: 03 8331 6100
Web: www.krueger.com.au
Lustec
Gate 3, 250 Karrabin Rosewood Road
Karrabin QLD 4306
Ph: 0477 498 185
Web: www.lustec.com.au
Lusty EMS
233-243 Learmonth Road
Wendouree VIC 3355
Ph: 03 5339 0300
Web: www.maxitrans.com
M&S Truck Bodies
4 Harris Street
Port Kembla NSW 2505
Ph: 02 4274 3003
Web: www.mstruckbodies.com.au
M&T Trailers
35 Redden Street
Cairns QLD 4870
Ph: 07 4035 1644
Web: www.mttrailers.com.au
Matrix Engineering Australia
16 Kirkcaldy Street
South Bathurst NSW 2795
Ph: 0417 669 987
Web: www.matrixeng.com.au
Maxi-CUBE
233-243 Learmonth Road
Wendouree VIC 3355
Ph: 03 5339 0300
Web: www.freighter.com.au
Mick Murray Welding
11 Forge Court
Bohle QLD 4818
Ph: 07 4728 7088
Web: www.mmwnt.com
Midland
3 Billy Mac Place
Parkes NSW 2870
Ph: 1300 301 570
Web: www.midlandind.com.au
Modern Transport Engineers Australia
15 Millennium Place
Tingalpa QLD 4173
Ph: 07 3393 5100
Web: www.modtrans.com.au
Moore Trailers
58 French Road
Pittsworth QLD 4356
Ph: 07 4693 1088
Web: www.mooretrailers.com.au
Muscat Trailers
7 Graham Hill Road
Narellan NSW 2567
Ph: 02 4648 2101
Web: www.muscattrailers.com.au
NCC Trailers
19 Jordan Close
Altona VIC 3018
Ph: 0434 365 161
Web: www.nccmaintenance.com.au
North Star Transport Equipment
4990 Murray Valley Highway
Strathmerton VIC 3641
Ph: 03 5874 5484
Web: www.northstarindustries.com.au
O’Phee Trailers
19 Formation Street
Wacol QLD 4076
Ph: 07 3271 5888
Web: www.the drakegroup.com.au
Peak Engineering Transport Services
1675 Ipswich-Boonah Road
Peak Crossing QLD 4306
Ph: 07 5467 2211
Web: www.peakeng.com.au
Pumpa Manufacturing
140 Karinie Street
Swan Hill VIC 3585
Ph: 03 5032 1916
Web: www.pumpa.net.au
Robuk Engineering
1294 Lytton Road
Hemmant QLD 4174
Ph: 1300 113 627
Web: www.robuk.com.au
Rytrans
2 Bain Court
Toowoomba QLD 4350
Ph: 07 4634 6838
Web: www.rytrans.com.au
Sloanebuilt Trailers
21-33 Dunn Road
Web: www.freighter.com.au S T
Smeaton Grange NSW 2567
Ph: 02 4647 4800
Web: www.sloanebuilt.com.au
Southern Cross Trailers Equipment Group
11 Manthorpe Street
Dry Creek SA 5094
Ph: 08 8405 7600
Web: www.scteg.com.au
Tefco Trailers
24-30 Alexandra Place
Murarrie QLD 4172
Ph: 07 3390 7007
Web: www.tefco.com.au
Tieman Tankers
180 Northbourne Road
Campbellfield VIC 3061
Ph: 03 9469 6700
Web: www.tieman.com.au
TopStart Trailers
2-20 Carter Way
Dandenong South VIC 3175
Ph: 03 9799 6533
Web: www.topstarttrailers.com.au
Trout River
24 National Drive
Hallam VIC 3803
Ph:03 9708 6266
Tru Grit Australia
125 Axis Pl
Larapinta QLD 4110
Ph: 1300 960 690
Web: www.trugrit.au
Ultimate Plant Trailers
U V
11/13 Saunders Street
North Geelong VIC 3215
Ph: 03 5272 2827
Web: www.ultimateplanttrailers.com.au
Vawdrey Australia
1-53 Quantum Close
Dandenong South VIC 3175
Ph: 03 9797 3700
Web: www.vawdrey.com.au
Tasmanian freight route upgrades continue with key bridges
Nine Tasmanian bridges are currently undergoing strengthening works and tenders have opened to strengthen a further 12 bridges as part of a $100 million upgrade to Tasmania’s freight routes.
These projects, jointly funded by the Australian and Tasmanian Governments under the five-year Freight Capacity Upgrade Program, seek to increase the freight capacity of critical and regional freight routes across Tasmania by strengthening or replacing various bridges and improving sections of roads.
Work is now advanced on a package to strengthen nine bridges under a $2.2 million contract awarded to construction company, Fulton Hogan.
Six of the nine bridges – at Agent River, Arthur River, Mole Creek, Leslie Station Creek, Don River and Pardoe Creek – are in the state’s north west.
The remaining bridges are at Wellards Creek, Norfolk Creek and Allans Creek on the Arthur Highway in the state’s south east.
Eight of these nine bridges are currently undergoing work. The ninth, Leslie Station Creek, will will start construction this year.
According to Tasmania Senator Anne Urquhart, the Freight Capacity Upgrade Program is playing a crucial role in stimulating the state’s economy.
“These much-needed bridge strengthening works will increase road and bridge network capability to increase freight productivity for critical state industries such as agriculture and manufacturing,” she said.
The Australian and Western Australian Governments are partnering to deliver a $700 million upgrade to the Kwinana Freeway.
These works will widen the freeway, adding roughly 50 per cent capacity to the upgraded sections, easing congestion for motorists and improving the efficiency of moving freight on a road that typically carries 100,000 vehicles every day.
This investment will also support the operations of the future Westport project which plans to move the state’s container trade from Fremantle to Kwinana and will stimulate WA’s economy in the long-term through the creation of local jobs.
Prime Minister, Anthony Albanese, commented on the importance of this joint investment.
“Western Australia is an economic powerhouse,” he said.
“We want to make sure we are investing in future job creating projects like Westport, while still delivering the immediate congestion benefits for commuters now.”
In total, the Federal Government is investing $9.7 billion towards transport infrastructure projects in the state across many projects outlined by WA Transport Minister, Rita Saffioti.
“The investment will ensure we can continue our Government’s major transformation of the Kwinana Freeway, which has seen the installation of smart freeway technology, the Armadale Road to North Lake Road Bridge Project and widening to large sections,” she said.
The New South Wales Government is investing more than $15 million to deliver a new safer, stronger Warroo Bridge, with construction set to start this month.
Warroo Bridge is a critical connector in the state’s Central West region as it is the only major crossing of the Lachlan Valley Way to the Henry Parkes Way.
The construction work will see a new concrete bridge be built just a few metres upstream from the existing timber truss bridge which, built in 1909, is not suitable for use by modern agricultural equipment or heavy vehicles with higher mass limit loads.
The construction of the new bridge will be safer and will allow for more efficient transport – particularly for freight operators in regional NSW.
“This new Warroo Bridge over the Lachlan River is an important piece of infrastructure that will make life easier for farmers, businesses and families in the Central West,” said Minister for Regional NSW, Tara Moriarty.
“The new bridge will be safer and more reliable than the existing bridge that is now well over 100 years old.”
The existing Warroo Bridge will remain open to traffic throughout the construction of the replacement bridge and will be removed completely once the new bridge is operational.
“The Minns Labor Government is investing in the future of regional NSW by building better bridges that keep communities connected, improve safety and increase efficiency for freight operators,” said NSW Minister for Regional Transport and Roads, Jenny Aitchison.
MaxiTRANS has changed its name to Freighter Group.
The new Freighter Group stands for something more powerful than ever before. It stands for being ready.
Ready to push boundaries, deliver excellence and to help you go further. Be part of a new era in transport.
freighter.com.au
A trio of industry heavyweights are joining forces to begin work on a groundbreaking initiative aimed at making e-trailers more efficient through battery swapping technology.
Charging infrastructure, or lack of it, is a continual bone of contention within the industry as operators do their very best to integrate environmentally sustainable vehicles into their fleets.
Looking to alleviate this problem, Trailer Dynamics, DB Schenker and Contemporary Amperex Technology are putting their research capabilities together by looking at the feasibility of battery swapping technology, and the implementation of battery swapping stations for electric trailers and potentially electrified trucks, across Europe.
“Battery swap technology will play a crucial role in overcoming charging infrastructure challenges and supporting the market ramp-up of zero-tailpipeemission heavy goods transport specifically in Europe,” said Executive Vice President of DB Schenker Europe, Wolfgang Janda, adding that the cooperation sends a strong signal to the European market, demonstrating the participating companies’ dedication to advancing the electrification of heavyduty transport.
The initiative aims to create a swapping system that can be undertaken in five minutes which would, the partners expect, represent a significant step
towards enhancing the efficiency and cost-effectiveness of battery charging for heavy goods traffic, and in turn increase the range and uptime of electric vehicles.
Battery Swapping systems are particularly suited to accommodate the unique and dynamically changing requirements of eTrailer users. The estimated swapping time of five minutes and the selection of multiple battery modules according to the required uses, not only improves the efficiency of the logistics process in electrified heavy goods transportation, but also the commercial parameters.
Key highlights of the project are:
• Increased range and efficiency: By allowing rapid battery swaps, we aim to maximise vehicle uptime and extend operational range.
• Custom Solutions: Tailored battery modules will meet the diverse needs of eTrailer users, reducing reliance on traditional charging infrastructure.
• Fleet Uptime: Higher utilisation of fleet vehicles due to significantly reduced charging time from three hours to five minutes.
Contemporary Amperex Technology or CATL will adapt its battery expertise
to the eTrailer concept and provide essential technical data for the design of the Battery Swapping Stations.
“We are excited to combine our technology and experience with the industry knowledge and operational expertise of DB Schenker and Trailer Dynamics, to accelerate the transition to emission-free transportation in Europe,” said CATL Executive President of Overseas Business, Akin Li.
Trailer Dynamics will oversee the mechanical and electrical integration of the swappable batteries into their eTrailer systems and provide prototype eTrailer models for review.
“The battery swap technology has the potential to maximise the uptime of our vehicles and reduce CO2 emissions throughout Europe,” said the CEO of Trailer Dynamics, Abdullah Jaber.
Meanwhile, DB Schenker will assess suitable locations for testing the battery swapping stations and design a forwardlooking map of potential locations across Europe.
It is expected that the group of companies involved in the project will be successively expanded to include other logistics companies, energy suppliers and service providers.
Brisbane-based transport company, D&G Logistics, isn’t letting a difficult market get in the way of its rapid expansion.
payload capacity and capitalising on the innovations of high-performance freight units when investing in new fleet.
D&G Logistics, established in 2016, has largely flown under the radar since its fruition despite accruing major accounts as a contractor for the likes of Toll, Team Global Express and Linfox. The bulk of new work it has been furnished is in refrigerated transport, a growing sector it has no doubt hitched some future ambitions to.
While the company currently runs a fleet of 60 prime movers, Pantechs are becoming more prominent at dispatch despite nearly 90 per cent of their mobile assets being operated in a standard B-double mezzanine application.
“Everyone is facing challenging times with costs going through the roof,” says D&G Logistics General Manager, Ray Spiteri. “In response to the current economic climate, we’re trying to do things a bit differently.”
The business is now running B-triples, road trains and quads as an outcome of this stagnating inflationary environment. That means adding new lanes, upping
“We’re finding the margin is getting smaller and smaller in regard to earnings,” Ray says. “Our onus is in trying to get customers direct because it makes it a bit more feasible. Running quads and triples that will increase our profit and we can leverage off that and then pass on some of those savings to the customer.”
Part of that is providing a juxtaposition for the customer when it comes to the price of a B-double versus a B-triple. D&G Logistics will reduce that space it carries so the customer has to commit to loading extra.
In maximising the capacity of the goods each truck is assigned, greater opportunities to discount or reduce costs for customers are being found on these bigger combinations. A recently launched ABB-quad road train is now running between Brisbane and Darwin. At present they anticipate approval soon for a permit
to operate a B-triple from Melbourne into Brisbane, the biggest corridor for the business currently.
Meanwhile, on an NHVR gazetted route, D&G Logistics runs its B-doubles out to Gatton where they will hook up additional trailers before advancing into Darwin. The trip takes in total four days.
“We try and leave Friday morning to be over there by Monday,” Ray says. “The thing with Darwin is everyone is pretty good in terms of transit times. We tell the customers five days express, six days general freight. But we get it there within four.
“We’ve been really successful from Brisbane and heading towards North Queensland. We’re looking at opening depots in Cairns, Townsville, Mackay and Rockhampton. It’s quite funny. You could say we’re an interstate company but most of the work that we’re winning is ex Brisbane which is fine for us. It just shows us how much opportunity there is out there in every state.”
Reverse with ease. Drive with con dence.
Enhance safety and control - introducing iReverse, the cutting-edge reversing assist system for trailers.
Providing audible and visual alerts to help drivers detect obstructions when reversing and automatically applying the brakes if an object gets too close, Knorr-Bremse has your back with iReverse. Available today.
Visit our website or contact your local Knorr-Bremse representative for more information. | truck.knorr-bremse.com/en/au/ |
Pencil in some information on dates and venues of various truck shows, field days and road transport industry conferences both locally and internationally.
Got an upcoming event? Then let us know about it – email editor@trailermag.com.au
March
Victoria
Wimmera Machinery Field Days 4-6 March
Horsham, VIC Visit: www.wimmerafielddays.com.au
South Australia
South East Field Days 21-22 March
Lucindale, SA Visit: www.sefd.com.au
Victoria
Farm World 27-29 March
Lardner, VIC Visit: www.lardnerpark.com.au/farmworld
2025 National Rural Carriers Convention 4-5 April
Canberra, ACT
Visit: www.lbrca.org.au/lbrca-events/conferences
Tocal Field Days 2-4 May
Paterson, NSW Visit: www.tocalfielddays.com
Queensland
Brisbane Truck Show 15-18 May
Brisbane, QLD Visit: www.brisbanetruckshow.com.au
National Diesel Dirt and Turf Expo 16-18 May
Sydney, NSW Visit: www.dieseldirtandturf.com.au
Victoria
Elmore Field Days 7-9 October
Elmore, VIC Visit: www.elmorefielddays.com.au
Wandin Silvan Field Days 17-18 October
Wandin, VIC Visit: www.wandinsilvanfielddays.com.au
November
France
Solutrans 18-22 November
Lyon, France Visit: www.solutrans.fr