
3 minute read
Sydney’s forgotten ghost tunnels all powered up with guided boring breakthrough
from Trenchless Apr 2022
by Prime Group
Directhitt Trenchless has completed a project for Laing O’Rourke at Sydney’s Central Station by installing critical electrical infrastructure for the new Sydney Metro.

As part of the biggest upgrade to Sydney’s busiest railway station in decades, Directhitt Trenchless were contracted to supply and install four DN 630 HDPE liners and PVC electrical conduits to provide 33KV power to the new underground Metro station. e boreholes constructed by Directhitt, connected the 27 m deep metro station box level B2 to an existing ghost tunnel, which was built in the 1920s as part of the Eastern Suburbs Railway line for Bondi and the Illawarra. However, it was never completed. Platforms 26 and 27 have sat unused since and will now house 17 new communications and power rooms to support the new Sydney Metro at Central Station. e 90 m long microtunnells were constructed using an Akkerman Guided Boring Rig, which used a Pilot Tube and Laser Guidance System to accurately drill the pilot hole to line and grade in Class II Hawkesbury Sandstone.
e con ned site prevented the use of a typical HDD rig set up, so Directhitt chose to use a Guided Boring rig with a compact 3 m jacking frame. e Akkerman dual-wall pilot tube design allows the pilot tubes to be installed with pinpoint accuracy while reducing pressures necessary for the long installations. e annular space between the inner and outer tube was used to pump drilling uid lubricants to the Tri-Hawk drill bit. e inner tube is treated for corrosion

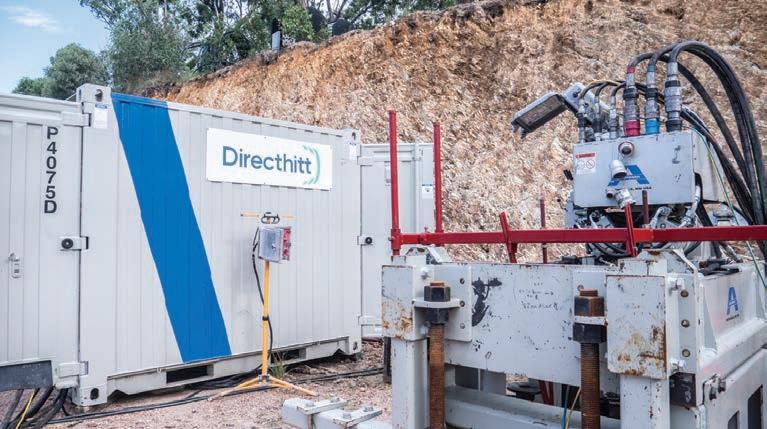
Directhitt chose to use a Guided Boring rig with a compact 3 m jacking frame for the project.
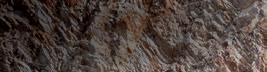

Testing and commissioning of the Akkerman system at the Directhitt yard prior to mobilisation to Sydney.
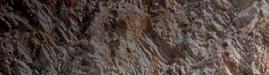
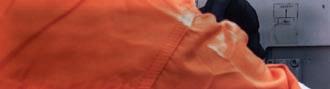
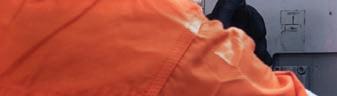
Directhitt crew testing the guidance system. The rugged monitor and controls are purpose-built specifi cally for pilot tube installation to avoid any contact with the theodolite once set-up.


resistance and sealed for a clear site path to the target located directly behind the steering head and 165 mm drill bit. Once the pilot hole was completed the boreholes were then enlarged to 710 mm before the HDPE liners were fusion butt welded and installed into the boreholes, using the jacking frame. Given the con ned site, the DN 630 HDPE liners were welded and pushed into the boreholes one section at a time.
Directhitt then installed the DN 280 PVC Electrical ducts into the HDPE liners and grouted the PVC duct annulas with a low thermal resistivity cementitious grout before nal testing and commissioning of the conduits was completed. e project presented many challenges for Directhitt to overcome, with COVID-19 shutdowns, border closures and managing crews in working bubbles to maintain a COVID-free workplace. Together, with the site access restrictions presenting constant challenges for the crew, Directhitt stepped up to the challenge and completed the project successfully. e addition of the pilot tube system to Directhitt’s trenchless capabilities allows for the provision of varied and hybrid trenchless solutions utilising the best of grade control and accuracy from the Akkerman system with trusted hole opening technology and drilling uid management from the HDD industry.
For more details contact Eamon Foley on 0419 794336 or info@directhitt.com.au or visit our website at wwww.directhitt.com.au
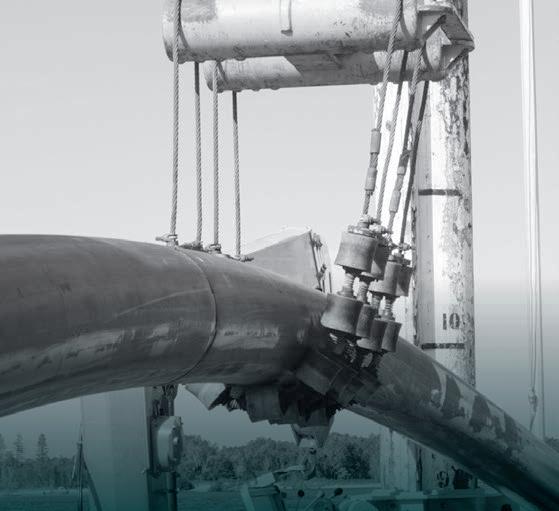
INTRODUCING
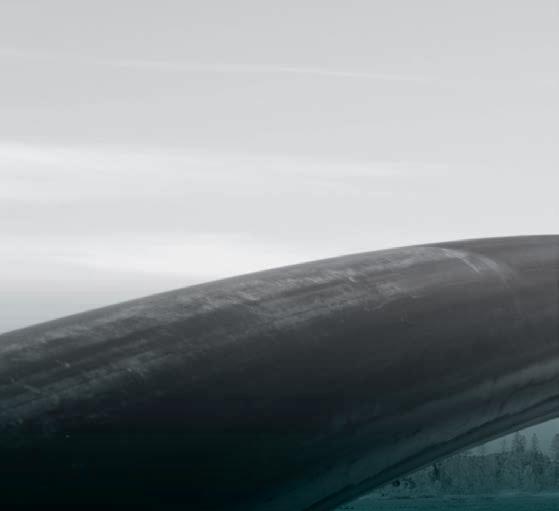
Market Leaders in Trenchless Technology. Yes, we’re direct.
If you’d like to know more about the potential of trenchless solutions including Horizontal Directional Drilling or Laser-Guided Microtunnelling for your next project, get intouch with a professional or visit our new website.