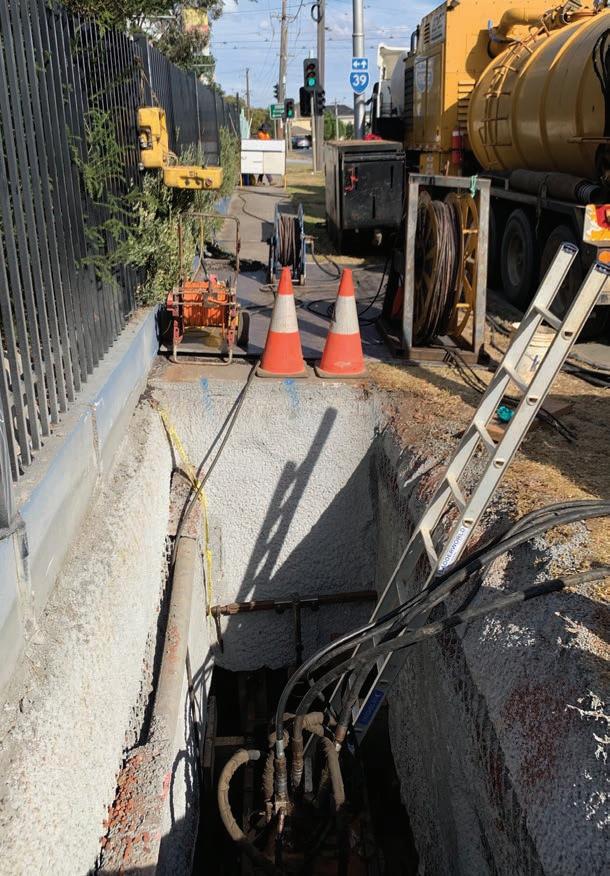
4 minute read
Getting the edge over the competition
With an increasing focus on being environmentally conscious, contractors that can provide a solution that is more earth friendly, while also remaining efficient and cost effective, are keeping themselves a step ahead of the competition.
Edge Underground contracts for the installation of water and sewer pipelines. Managing Director and inventor of the Vermeer AXIS guided boring system Stuart Harrison is very familiar with the benefits of trenchless installation methods over traditional open cut approaches.
Pipeline installation has the potential to be destructive to the surrounding natural and built environment, but trenchless techniques, such as microtunnelling, can help mitigate this. Here are some of the environmental benefits of this method.
Minimal surface disruption One of the major differences between traditional open cut methods and trenchless methods such as microtunnelling is the amount of excavation that needs to take place.
“Traditional open cut methods require a large amount of excavation as trenches need to be dug along the entire length of the pipeline route. This results in a large amount of environmental disruption to flora and fauna, and can be disruptive to the community,” says Mr Harrison.
“Trenchless methods don’t have this problem as they require minimal excavation. For microtunnelling, only a small entry and exit pit needs to be excavated at each end of the pipeline, and the ground between these points is left undisturbed.
“This drastically reduced site footprint means there is less impact to the surrounding environment, flora and fauna.”
Spoil management Spoil management and disposal is critical for any pipeline construction project to meet environmental regulations. Due to the amount of excavation required for open cut installations, mounds of spoil either need to sit at the site or transported out during works and trucked back in for backfilling, and in cases where there is ground contamination, it needs to be disposed of correctly.
Conversely, microtunnelling requires much smaller quantities of incoming and outgoing materials.
“Some microtunnelling machines, such as the AXIS laser guided boring system, use vacuum excavation, which offers improved environmental outcomes,” says Mr Harrison.
“The vacuum excavation method uses a vacuum tank and power unit to help maintain a clean site. During drilling, upon reaching the launch pit, the spoil transitions from the drill casing to a hose that runs up the launch pit to the tank.
“Among other benefits, this eliminates the need to manually handle spoil within the launch pit, which not only reduces manual labour but also provides a cleaner and safer pit environment for personnel to work in.
“There is also a cost-saving benefit of using the vacuum excavation method, as it is able to remove the spoil as it is produced, removing the need to suspend drilling operations so it can be done manually. This reduces project costs and helps ensure the pipeline is completed on time.”
Work safety As microtunnelling requires fewer trenches and uses vacuum excavation methods, it also has the benefit of helping to create a safer working environment. Working within or near excavation projects is considered dangerous due to the risk of potential cave-ins. This is the event of objects falling into the excavated area. These risks increase the deeper the excavation is.
As microtunnelling only requires excavating an entry and exit pit, the risks are much lower when contained to a smaller area.
Reduced emissions Construction activities are one of the main contributors to a country’s overall emissions of greenhouse gases. Both open cut and trenchless
For microtunnelling, only a small entry and exit pit needs to be excavated at each end of the pipeline.
pipeline installations contribute to this as well.
“The AXIS is the only microtunnelling machine on the market that has been proven to have low carbon emissions,” says Mr Harrison.
“During a project in the US which used the AXIS system, Dr Sam Ariaratnam and his team from Arizona State University undertook an emissions study using the ‘E Calc’ emissions calculator. The study compared the results to alternative methods, and the AXIS system conclusively had the least emissions of all of them.
“With countries working towards reducing their overall emissions, the AXIS is able to help project managers and contractors lower their project’s carbon footprint.”
Mr Harrison founded Edge Underground in 2010 after more than 25 years of contracting experience installing sewer and water pipelines. He has travelled the world as a microtunnelling expert, working on equipment research, development and troubleshooting. He is considered a pioneer in the industry and one of the most trusted pipeline contractors.
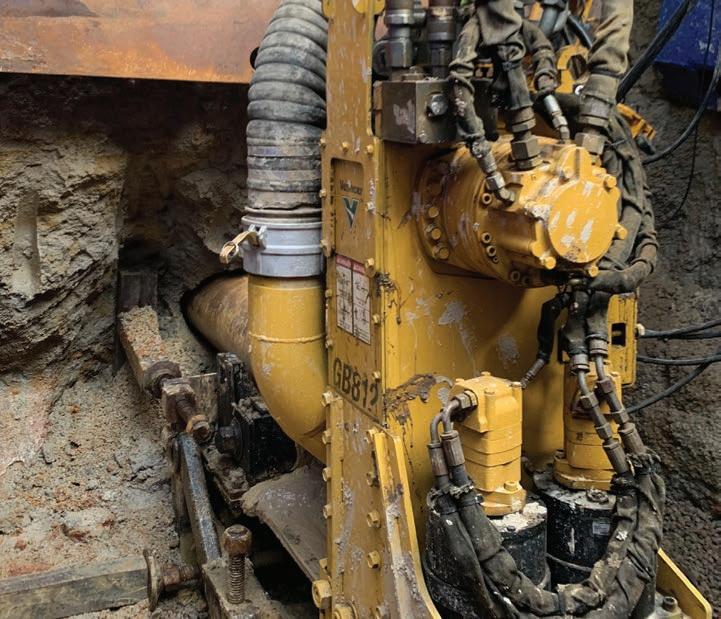
Microtunnelling requires much smaller quantities of incoming and outgoing materials.
For more information visit www.edgeunderground.co
SUPERIOR MANHOLE REHABILITATION TECHNOLOGY
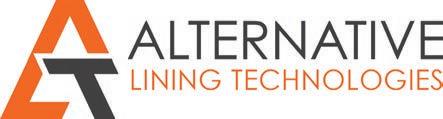
DESIGNED TO LAST MORE THAN 50 YEARS MORE THAN 50 YEARS
Alternative Lining Technologies’ CIPM™ lining systems extend the life of manholes, pump wells and pits by more than 50 years and come with a 20-year warranty as standard. No other rehab system provides the performance and confi dence that performance and confi dence that CIPM™ liners do. Stop infi ltration Stop H2S corrosion Structurally rehabilitate Save time and money


Contact us to learn more about the superior manhole rehabilitation technology Bruce Keys - General Manager | 0418 542 120 | bkeys@altliner.com.au www.altliner.com.au