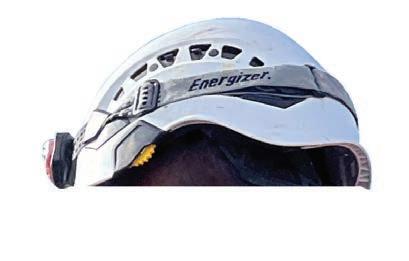
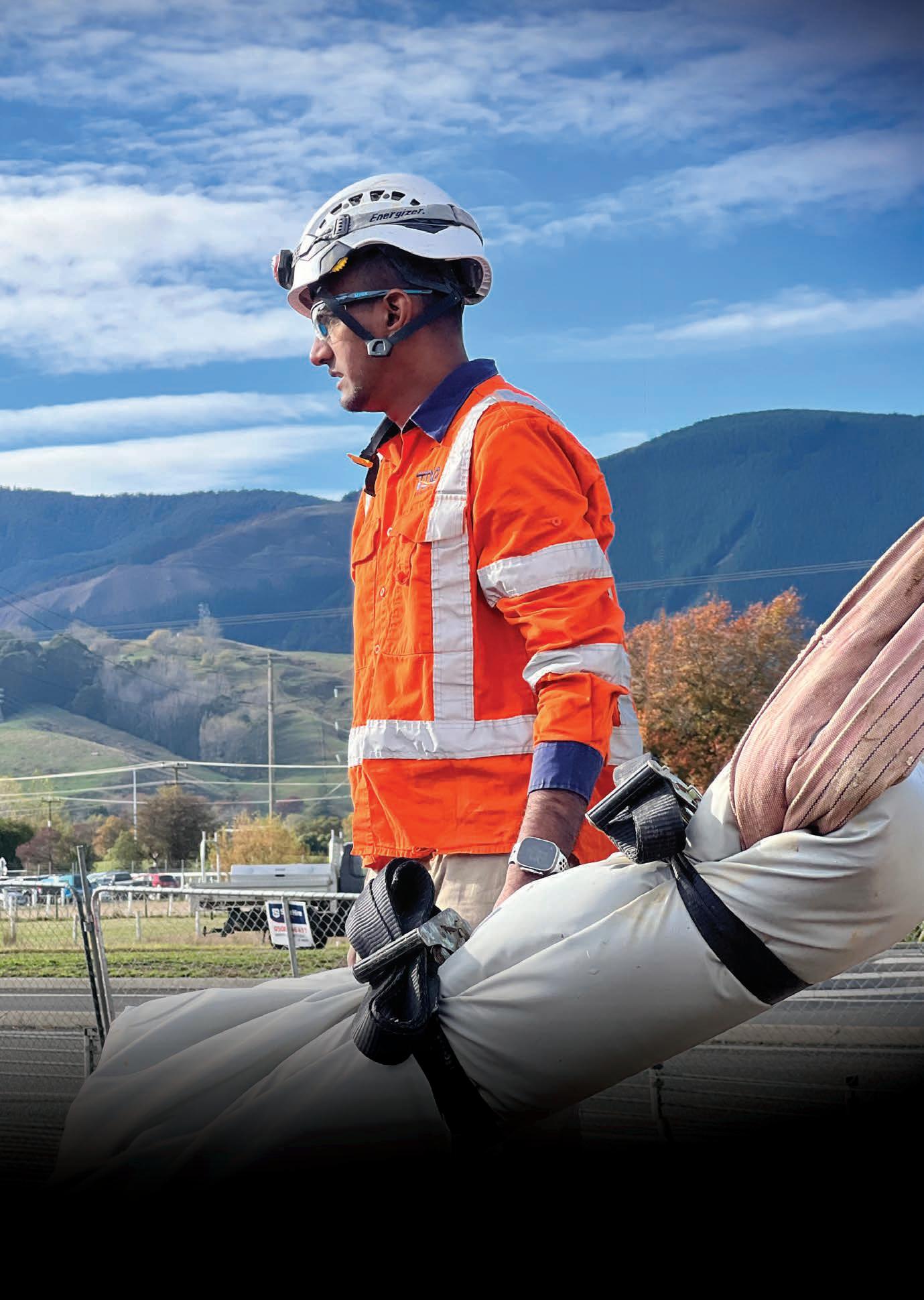
How SAERTEX-LINER led to project success
Trenchless technology shines in New Zealand | A rising force in infrastructure maintenance | Partnered for success | New ways of working puts communities first
“Knowing we made people’s lives easier while we were working, that’s the real win”
– Reece Paulzen, Interflow
We’re Creating the Future of Water by finding new ways of working that put communities first
This magazine is the official journal of the Australasian Society for Trenchless Technology (ASTT) and is distributed to members and other interested parties throughout Australia and the AsiaPacific. It is also available on subscription.
The publishers welcome editorial contributions from interested parties. However, neither the publishers nor the ASTT accept responsibility for the content of these contributions and the views contained therein are not necessarily the views of the publishers or the ASTT. Neither the publishers nor the ASTT accept responsibility for any claims made by advertisers. All communications should be directed to the publishers.
Unless explicitly stated otherwise in writing, by providing editorial material to Prime Creative Media (PCM), including text and images, you are providing permission for that material to be subsequently used by PCM, whole or in part, edited or unchanged, alone or in combination with other material in any publication or format in print or online or howsoever distributed, whether produced by PCM and its agents and associates or another party to whom PCM has provided permission.
CEO
John Murphy
CHIEF OPERATING OFFICER
Christine Clancy christine.clancy@primecreative.com.au
MANAGING EDITOR
Molly Hancock
molly.hancock@primecreative.com.au
EDITORIAL
Tim Bond tim.bond@primecreative.com.au
Zihan Zhang
zihan.zhang@primecreative.com.au
BUSINESS DEVELOPMENT
Nick Lovering nick.lovering@primecreative.com.au
HEAD OF DESIGN
Blake Storey blake.storey@primecreative.com.au
DESIGNER
Blake Storey
COPYRIGHT
Trenchless Australasia is owned by Prime Creative Media and published by John Murphy. All material in Trenchless Australasia is copyright and no part may be reproduced or copied in any form or by any means (graphic, electronic or mechanical including information and retrieval systems) without written permission of the publisher.
The Editor welcomes contributions but reserves the right to accept or reject any material. While every effort has been made to ensure the accuracy of information, Prime Creative Media will not accept responsibility for errors or omissions or for any consequences arising from reliance on information published. The opinions expressed in Trenchless Australasia are not necessarily the opinions of, or endorsed by the publisher unless otherwise stated.
© Copyright Prime Creative Media, 2021
ARTICLES
All articles submitted for publication become the property of the publisher. The Editor reserves the right to adjust any article to conform with the magazine format.
Head Office
379 Docklands Dr, Docklands VIC 3008 Ph: +61 3 9690 8766 enquiries@primecreative.com.au www.primecreative.com.au
Sydney Office
Suite 11.01, Level 11, 201 Miller St, NorthSydney, 2060
Molly Hancock
In this edition of Trenchless Australasia, we turn our focus to New Zealand, a country renowned for its impressive trenchless projects and innovative infrastructure solutions.
New Zealand’s commitment to trenchless technology is evident in its impressive track record of projects that have profoundly impacted its infrastructure and development. With its delicate ecosystems, native wildlife, and pristine waterways, traditional open-cut methods would pose significant risks. This is why trenchless technology is not just a choice but a necessity in a country with such diverse and breathtaking landscapes.
In this October issue, we will explore the advanced trenchless techniques being utilised to tackle the challenges posed by New Zealand’s varied terrain.
Whether in vibrant urban centres or remote rural areas, trenchless methods are proving their worth by minimizing disruption to both people and the environment. Expect to find detailed case studies showcasing the real-world application of these methods across
different projects in New Zealand. If you’re involved or contribute to New Zealand’s trenchless industry, this edition provides an opportunity to raise awareness of companies’ capabilities and the roles they play in contributing to one of the world’s most advanced construction sectors.
The front cover of this edition highlights a project in New Zealand, where TDG Environmental delivered its first pressure installation project using a SAERTEXLINER, which Pipe Core is the local distributor for.
This project not only benefits the local community by enhancing infrastructure resilience, but also sets a precedent for future projects across Aotearoa New Zealand, demonstrating the importance of innovative and sustainable solutions in infrastructure renewal. Discover how New Zealand is setting new standards in trenchless technology.
Molly Hancock Managing Editor molly.hancock@primecreative.com.au
0800 93 7473 hynds.co.nz
THE AUSTRALASIAN SOCIETY FOR TRENCHLESS TECHNOLOGY
ABN 43 893 870 966 18 Frinton Place Greenwood, WA 6024 www.astt.com.au
President: Ben Crosby
Secretary: Trevor Gosatti
Vice President: Blair Telfer
COUNCILLORS
Western Australia: Aizezi Jiang
Queensland: Ben Crosby
New South Wales: Jason Marshal
Victoria: Ash Hamer
South Australia: Shaun Melville
New Zealand: Blair Telfer
Northern Territory: Luke Woodward
Tasmania: Vacant
As we navigate the evolving landscape of infrastructure development, trenchless technology stands out as a beacon of innovation and efficiency. This cutting-edge approach is revolutionizing the way we manage our underground utilities, offering significant advantages over traditional methods.
In New Zealand, trenchless technology is becoming increasingly integral to our infrastructure projects, driven by its ability to minimise surface disruption, reduce environmental impact, and enhance project speed and cost-effectiveness.
Our recent projects exemplify the transformative potential of trenchless methods. From the successful installation of new pipelines in urban areas to the seamless replacement of aging infrastructure, these techniques are not only improving
the resilience of our networks but also fostering sustainability.
The reduced need for extensive excavation translates to less disruption for communities and a lower environmental footprint, aligning with our commitment to responsible development.
Looking ahead, it is crucial that we continue to embrace and invest in these innovative solutions. By doing so, we ensure that New Zealand remains at the forefront of modern infrastructure practices, paving the way for a more efficient, sustainable, and resilient future.
Let us champion trenchless technology as a key driver in our nation’s progress and success.
Ben Crosby ASTT President
CDS is a Horizontal Directional Drilling (HDD) contracting company, who has specialised in the trenchless installation of pipework across New Zealand since 1992. CDS’s main focus is on stormwater, wastewater and water pipelines. We are known for successfully undertaking projects that are challenging and that require close collaboration with clients and design engineers to find innovative solutions.
CDS HDD Design Ltd are a specialist engineering design consultancy focused on Horizontal Directional Drilling (HDD) pipeline projects. Our goal is to promote the use of HDD and advance local industry knowledge in this field. We produce market leading design services through our in-depth understanding of the advantages, limitations and risks of this trenchless method. Our team of experienced chartered professional engineers and HDD specialists, offer turnkey design solutions or can tailor a package to suit your requirements.
MARC CARMODY marc@cdsnz.co.nz
+64 21 902 164
ANTHONY CLOUGH anthony@cdsnz.co.nz
+64 21 853 909
cdsnz.co.nz cdsdesign.co.nz
New Members
On behalf of the ASTT, I extend a warm welcome to the following new members:
Asset Owners – Australia
Barwon Water – Mohit Soni
Silver Corporate Members – Australia Ready Group Pty Ltd – (Shane Holt) –24 months
Individual Members – Australia
Grant Tighe from Confluence Water Ben Worst from Minitap Chris Fraraccio from Global Pipe Graham Coles from Nortrop Consulting Engineers
Individual Members – New Zealand
Cam Wilks from Pattle Delamore Partners
Omar Al-Karbouli from New Zealand Lining Ltd
Young Professional Individual Members – Australia
Romy Wolstencroft from GHD
Young Professional Individual Members – New Zealand
Natasha Bycroft from Pattle Delamore Partners
ASTT at Water NZ
The ASTT was part of the Water NZ Conference and Exhibition held in Hamilton, New Zealand from the September 25 2024 to September 27 2024.
The ASTT provided a dedicated trenchless technology stream as part of the conference with an industry presentation from the ASTT and technical papers presented on trenchless technologies from various speakers. A number of ASTT members were also part of the exhibition. This is part of the longstanding relationship with the Water NZ Association, and we are appreciative of this industry for the opportunity to further promote trenchless technology.
It was planned to hold an ASTT training course (Introduction to Trenchless Technologies) leading up to the event for interested persons but unfortunately this was postponed. We intend to schedule this course in Auckland at another time soon.
New ISTT website to benefit ASTT Members
The International Society for Trenchless Technology (ISTT) recently committed to develop a new website for the ISTT and has engaged EventMagix, based in Turkey, to complete the development of the new website and an advanced database to complement the website and its services.
The new website will contain many new features for the Affiliated Societies and their members, hopefully providing many more opportunities to promote trenchless technologies around the world.
Some of the new features include:
• A corporate booth facility for existing corporate members where the entity’s products and services can be displayed via video, brochures and WhatsApp.
• The ability to “upgrade” the basic corporate booth to a higher level virtual corporate booth providing the corporate entity to promote its goods and services to a global audience. The additional features include video, brochures, presentations, business cards, WhatsApp and other media.
• The option of a corporate upgrade is proposed to be offered through Affiliate Societies.
• The website will have enhanced “Charts and Description” pages highlighting the benefits of trenchless technologies to industry.
• Enhanced pages providing past conference papers, etc will be provided.
• A next level database facility will assist Affiliate Societies to have member data
included and allow members in the database to access all the features.
• It is planned for a single sign on for the member login process.
• The database will allow a more improved search function for corporates and the goods and services they offer to industry.
The ASTT, and more importantly its members, will benefit from the development of this new website, expected to become available in November 2024. As more information becomes available the ASTT will inform its members of the new benefits being provided.
ASTT supports No-Dig Asia Pacific International Conference
The ASTT is happy to support the first NoDig Asia Pacific International Conference and Exhibition 2024 to be held in Hong Kong at the Hong Kong Polytechnic University on October 31—November 1 2024.
The conference and exhibition is being organised by the China Hong Kong Society for Trenchless Technology (CHKSTT) and supported by the ISTT and will be an important event for the Asia Pacific region.
As part of the Asia Pacific region, the ASTT strongly supports this event and encourages any ASTT members interested to participate.
Interested members can either contact the conference organisers directly or through the ASTT Secretary at secretary@ astt.com.au who can assist.
This event promises to be a comprehensive forum for discussing the latest trends and innovations in trenchless technology in the region and would be an opportunity for ASTT members looking to expand into the Asia Pacific region with their goods and services to gain exposure.
Trevor Gosatti ASTT Secretary
With a focus on safety, innovation and collaborative delivery, Rob Carr and March Construction have achieved outstanding outcomes in water, wastewater and energy infrastructure projects respectively in Australia and New Zealand and together as a joint venture in New Zealand. Both Rob Carr and March, are a part of Soletanche Bachy a world leader in foundation and soil technologies and subsidiary of VINCI, a global player in construction across more than 100 countries. With outstanding capabilities to manage the complexities of any project, Rob Carr and March have the people, knowledge and experience to deliver success.
robcarr.com.au
marchcon.co.nz
A new tunnel boring machine (TBM) will be deployed for Snowy 2.0 to help keep the project on its delivery timeline.
Snowy Hydro CEO Dennis Barnes said the new TBM will be the fourth for the project and its addition will help address the current tunnelling challenges.
“We’ve always known the fault zone was there and I’ve said in the past we will need to take action,” Barnes said.
“While the fault zone is not a surprise, further ground testing since the project reset has revealed it is far more geologically challenging than earlier investigations indicated.
“We’ve carefully considered a range of options to get through the fault zone and overcome the initial design immaturity. Bringing in a fourth machine is the best way to keep the Snowy 2.0 on track for its target completion date of December 2028.”
A modification for the project has been submitted to the NSW Department of Planning, Housing and Infrastructure, which seeks approval for a change to construction methods within its work zone.
“We’re mindful that we are building Snowy 2.0 in a precious and protected national park. We have worked diligently to arrive at a proposal that does not step outside our existing construction area or increase our already approved impacts,” Barnes said.
The 24km Sydney Metro West project has achieved a slew of tunnelling milestones, including the arrival of two mega tunnel boring machines (TBMs) at Sydney Olympic Park.
TBM Betty, named after Olympic champion Betty Cuthbert, was first to arrive at Sydney Olympic Park in June and was followed by TBM Dorothy, named after human rights activist Dorothy Buckland-Fuller, on 29 July.
The TBMs spent 10 months completing the 4.6km tunnels from Clyde to reach Sydney Olympic Park.
TBMs Betty and Dorothy have excavated approximately 857,500 tonnes of material, to complete the first leg in the journey and have installed more than 32,600 concrete precast segments to line the new tunnel walls.
In the coming months, the TBMs will be disassembled, lifted out of the station box and transported on trucks back to Clyde, where they will be relaunched in the opposite direction towards Westmead.
TBM Betty has already returned to Clyde, while TBM Dorothy’s disassembly is ongoing. Both TBMs are expected to arrive at Westmead in mid-2025.
The focus at Sydney Olympic Park will now shift to the opposite end of the 200-metre-long, 37-metre-wide, and 27-metre-deep station box, where TBMs Beatrice and Daphne are due to break through in late 2024.
Empire Infrastructure and Rob Carr are helping to deliver a $90 million upgrade to Sydney’s North West Growth Area (NWGA).
Rob Carr has been awarded a microtunnelling contract through Confluence Water for the NWGA project, a major upgrade in collaboration with Sydney Water.
“It has been a great opportunity for Empire Infrastructure to supply pipes to Rob Carr for the NWGA project,” Empire Infrastructure told Trenchless Australasia
“The project includes almost 700m of DN1200 and DN500 CP&P Reinforced Concrete Jacking Pipes.
“We are looking forward to seeing the completion of this section of works in the not-too-distant future.”
Rob Carr General Manager Angelo Soumboulidis praised Empire Infrastructure for its role in the New South Wales project.
“Our experience with Empire Infrastructure is always exceptional. The pipe is reliable and of high quality,” he said.
“Empire Infrastructure’s customer service ultimately exceeds our expectations every time.”
Watercare has begun the final stage of the Huia 1 watermain replacement in Epsom, New Zealand.
The water corporation announced it would use sliplining to pull a 630mm diameter pipe through the existing Huia 1 pipeline.
“This section of the pipeline carries less water than the sections west of Epsom, so we can install a smaller pipe using trenchless technology instead of open cut excavation,” Watercare project manager Tim Manning said. The new Huia 1 watermain stretches over
15km between Epsom and Auckland’s western reservoirs in Titirangi and will supply drinking water to 20 per cent of Auckland’s population. It will replace the existing Huia 1 pipeline, which – at 76 years old – is nearing the end of its design life.
The Pioneer-Burdekin pumped hydro project in Queensland has reached a new milestone, with more than 50 boreholes drilled so far.
Queensland Premier Steven Miles made the announcement noting that more than five kilometres of core samples have been collected.
“With every drill and borehole, PioneerBurdekin powers up more regional jobs for small businesses like Twin Hills Engineering and Drilling, with benefits to the community to continue for decades to come,” Miles said.
“This nation-leading project will ensure we lock in a clean economy future for Queensland’s industrial heartland.
“Reaching this 5km geotechnical milestone is proof that we’re not just planning for the future—we’re delivering it.”
Queensland Hydro’s Pioneer-Burdekin Project will store the excess energy collected from household solar, for use at night when the sun isn’t shining, the wind isn’t blowing and when energy usage is at its peak.
Mackay company Twin Hills Engineering and Drilling is undertaking the works and estimates they are injecting more than $20,000 a week into the region through purchases relating to the project.
TDG Environmental has pulled off its first pressure installation with SAERTEX-LINER in New Zealand.
TDG Environmental delivered its rst pressure installation project using SAERTEX-LINER® in May 2024, positioning the company as a leader in pressure pipeline renewal for New Zealand.
Over eight days, TDG Environmental, one of the largest and most experienced specialist providers of asset renewal in New Zealand, tackled two sections of a 4km DN450 asbestos cement pipe using trenchless UV relining technology.
is project was part of the larger, multiyear works and rehabilitation of the Nelson Regional Sewer System (NRSS) Rising Main duplicate project being delivered by Nelson Regional Sewerage Business Unit (NRSBU).
e project was managed by the client, NRSBU, with support from Beca as the consultant and designers. Hunter Civil was selected as the main contractor for the project, covering the area from the Beach Road pump station to Saxton Creek.
TDG Environmental was chosen as subcontractors to Hunter Civil and was responsible for the trenchless renewal of two critical sections of a rising main which had been decommissioned 15 years earlier due to insu cient capacity.
“A new pipe had been managing the out ow of the Richmond area to the Bell Island Wastewater Treatment Plant,” TDG Environmental General Manager Simon Ganley said.
To help reduce the overall project cost and avoid costly and highly disruptive trenching under the main transport route between Nelson and Richmond, the NRSBU decided to reline the old pipe and bring it back online.
e renewal of the pressurised pipe was crucial to meet the future demands of the growing population and mitigate wet weather over ows. Once in operation, the pipeline would need to withstand operating pressures of 6 bar with a ow rate up to 500l/s.
e renewal involved two segments which ran under State Highway 6, 252m and 140m long, and would require a fully structural solution due to the deteriorated state of the host pipe.
TDG Environmental selected SAERTEXLINER MULTI Type S+XR Pressure, one of the few options on the market suitable for fully deteriorated pipes.
is liner is Class A classi ed according to DIN EN ISO 11295, meaning it is independent and fully structural.
“ e liner is tight- tted and absorbs inner and outer loads independently,” SAERTEX multiCom® Business Development Manager Katharina Helming said.
“It can also withstand operating pressures up to 33 bar in accordance with the diameter, making it a versatile UV-CIPP solution.
“Additionally, the liner has an expected technical design life of 50-years and a smooth surface, which, coupled with low wall thickness, ensure maximum ow rate in supply pipes.”
TDG Environmental participated in SAERTEX multiCom Certi ed Installer training for gravity and pressure pipe liner installation in March 2022, conducted by SAERTEX multiCom and coordinated by the local distributor Pipe Core.
“Our team was very impressed by the quality of the theoretical and practical training for applications in gravity and pressure pipe systems. We were grateful for this opportunity and commend the e orts of everyone involved in bettering industry standards,” Ganley said.
Since the training, TDG Environmental has completed many successful projects using this leading manufacturer’s product.
To support the successful delivery of the project, John Lampe, the SAERTEX multiCom application engineer who conducted the original training, also attended the groundbreaking project in New Zealand.
“It was very good having John Lampe onsite, especially for the consistency between the training and how the project was delivered on-site,” Ganley said.
“He is very knowledgeable and very familiar with the product.”
With a team of seven, the renewal was completed over eight days, starting with one day of high-pressure water cleaning.
“ e rst liner was installed over three days, following cleaning, camera inspection, and relining,” Ganley said.
e second install, the longer of the two lines, took ve days, using a brand-new UV curing cable.
“Pressure checks went well,” Ganley said.
“Both liners were installed successfully, achieving the speci ed 9-bar test pressure.”
NRSBU’s extensive planning ensured the project’s safe execution with minimal impact to the adjacent Waimea Inlet, an ecologically signi cant area and early consultation with the eight Te Tau Ihi iwi ensured they were well informed and understood the objective to reduce the frequency of wastewater over ows.
e collaboration between clients and contractors was pivotal in delivering this project with minimal disruption to tra c on State Highway 6, demonstrating a commitment to mitigating community impact.
e renewed pipeline that was brought back into service will lower the costs associated with reticulation and treatment and minimises over ow risks. e increased capacity facilitates easier maintenance of the assets, ensuring reliability even when sections are o ine for repairs.
is project not only bene ts the local community by enhancing infrastructure resilience, but also sets a precedent for future projects across Aotearoa New Zealand, demonstrating the importance of innovative and sustainable solutions in infrastructure renewal.
TDG Environmental’s successful completion of this challenging project underscores its expertise and capability in the pressure installation space and highlights its commitment to innovation, quality, and industry leadership, positioning it as a trusted partner for future infrastructure challenges.
For more information, visit tdgenvironmental.com and pipecore.com.au
A look at what projects were completed using trenchless technology in the past year.
Trenchless methods are increasingly popular in New Zealand for a range of civil infrastructure projects.
Watercare completes East Coast Bays sewer link
Measuring 1.75km in length and 800mm in diameter, the $21.5 million pipeline was constructed to handle the increased volumes of wastewater pumped from the new Mairangi Bay Pump Station to the Rosedale Wastewater Treatment Plant.
e new pump station pumps up to 625L per second – double the capacity of its predecessor.
e East Coast Bays link sewer went into service in July and has been performing as expected.
“Using this drilling method [HDD] allowed the pipeline to be installed directly beneath the road and under houses, eliminating the need for excavation and prolonged tra c disruptions,”
Watercare Project Manager Dirk Du Plessis said.
“It meant we could get the job done at pace and to a higher quality too.
“HDD is also better for the environment than open trenching as it lessens the impact on the surrounding residential assets.”
Breakthrough at Central Interceptor tunnel
A microtunnel boring machine has broken through a concrete shaft wall at a Central Interceptor project construction site to complete the second of two link sewers.
e 2.8m diameter cutterhead broke through at the Norgrove Ave, Mt Albert site,
making a major milestone for the New Zealand wastewater infrastructure project.
Link Sewer B is just over one kilometre long and intersects the main Central Interceptor tunnel and together with Link Sewer C, the link sewers will collect combined wastewater and stormwater ows from West Auckland.
“ e microtunnelling teams, together with our own Watercare engineers have consistently performed above expectations,” Central Interceptor Chief Program Delivery O cer Shayne Cunis said.
“ ey have completed more than four kilometres of tunnelling safely and expertly, including a particularly long challenging single drive, with a lefthand bend.”
A section of the Central Interceptor tunnel will go live before the end of 2024. e project is due for completion in 2026.
Sliplining delivers Huia 1 water main project
In August, Watercare commenced the nal stage of the Huia 1 watermain replacement in Epsom, New Zealand.
e water corporation announced it would use sliplining to pull a 630mm diameter pipe through the existing Huia 1 pipeline.
“ is section of the pipeline carries less water than the sections west of Epsom, so we can install a smaller pipe using trenchless technology instead of open cut excavation,”
Watercare Project Manager Tim Manning said.
e new Huia 1 watermain stretches over 15km between Epsom and Auckland’s western reservoirs in Titirangi and will supply drinking water to 20 per cent of Auckland’s population.
It will replace the existing Huia 1 pipeline, which – at 76 years old – is nearing the end of its design life.
CDS and Watercare replace failed water main
CDS and Watercare used HDD to deliver a $6.74 million project to replace the Glenbrook Beach watermain in April 2024.
e original pipeline experienced a joint failure in January 2023, when half a kilometre of pipe dislodged and oated to the top of Taihiki Estuary.
Watercare Project Manager Sean McHenry said twin pipelines will be installed to provide additional redundancy. ese will be constructed under the estuary using horizontal directional drilling.
“Using HDD to install the pipelines instead of anchoring them to the seabed using concrete weights will reduce soil disturbance to the riverbed and environmental erosion,” McHenry said.
“Installing them this way is less risky and has better health and safety outcomes as it eliminates the need for manually anchoring the pipelines to the estuary bed.”
Construction partner CDS will station a drill rig on the reserve.
“We’ll drill twin 300mm holes four metres apart to the reception pits on the other side of the estuary at Waiau Pa on Wharf Road,” McHenry said.
“ e drill rig stationed at the reserve at Tahuna Minhinnick Drive will pull the new polyethylene pipelines through the 300mm holes underneath the estuary from its assembly point in Waiau Pa.”
New Zealand has an Infrastructure need. Whether it be asset renewal or for growth or for productivity. Whether it is roads, water (all three of them) or energy we have a need. Whether we have the revenue, taxes or rates or third-party partners (PPP), to pay for it or not – we have a need.
But we’re in a recession with an austerity budget.
Politicking aside, the need versus reality is making it a tough time here in New Zealand at the present, there is little doubt on that. There is a massive need, everyone agrees, but little to no money flowing through the economy to pay for it.
As and when the money starts to flow, trenchless will have our part to play in the solutions. Whether it be tunnels for roads, drilling/microtunnelling for new assets, renewals to get more life/service from existing assets – trenchless is, or should be, a tool in every asset owners’ arsenal.
So, how do we, as an industry, ‘rise the tide’ for trenchless? We all prosper and
improve our positions, commercial or otherwise. By delivering what our clients want – cost effective solutions. Yes, we can deliver high-quality, high-performance work but equally we must deliver at the value our clients want.
This does not mean sub standard workmanship or below par quality – don’t let less revenue lower our standards. We will be successful by delivering cost effective outcomes. We know the benefits trenchless offers and brings - less disruption, lower costs, less carbon for climate change, “more for less” - but with our reputation held high.
It is in these tougher times we need to support our fellow trenchless practitioners; we need to deliver cost effective solutions and outcomes for our clients. We need to continue to invest in our workforce, in training, in retention so when the wave breaks, we are ready to seize the opportunities. Easier said than done, I wholly appreciate.
Yes, it is tough; yes, it is hard – but that’s where we thrive – that’s where our resilience and Kiwi ingenuity, number eight wire mentality, comes to the fore. This is what we do! So, lets show the infrastructure industry what we can offer and deliver.
I, and the whole ASTT Council and members, are here to advocate, promote, support you and for the industry. Please reach out to me where and how I can assist and support. That’s what I and the Council are here for.
And my last final word – look after yourselves, your whanau, your workmates. Check in on one another; please don’t be afraid/shy/embarrassed to ask for help. We can’t help anyone else if we aren’t there.
I look forward to catching up with as many of you as I can at WaterNZ and other trenchless events. Kia Kaha – stay strong.
Blair Telfer ASTT New Zealand Councillor
Hynds Pipe Systems’ innovative range of industry leading low carbon products is delivering performance and sustainability in a significant infrastructure project on Auckland’s North Shore.
New Zealand’s rst low carbon concrete jacking pipe is currently being installed in Albany as part of the Greville Road Stormwater Culvert Upgrade.
e project was identi ed as an emergency works project by Auckland Council’s Healthy Waters after the major
Auckland oods in January 2023. e existing Greville Road culvert consists of a 1950 mm diameter corrugated steel pipe that conveys ow from an inlet located within a basin north of Greville Road. e pipe stretches across a key arterial road (Greville Road), that connects to the Northern Motorway and Albany
Expressway, and under Rosedale Land ll where it connects into a 1950 mm concrete pipe. e culvert had failed at the inlet on the northern side of Greville Road.
Although the initial scope was to excavate and remove the collapsed culvert and replace it with a temporary shaft, a collaborative decision was made by Auckland Council and McConnell Dowell to design and construct the shaft to accommodate the permanent inlet at the same time. e reason for this solution was to avoid any reworking later in the project, saving time in the construction program.
Healthy Waters, McConnell Dowell and Hynds Pipe Systems collaborated in a joint workshop on low carbon pipe options, jacking pipe requirements and procurement timelines. Ultimately, it was decided to proceed with HyndsLC (Low Carbon) 2100mm diameter Hyforce® Butt Joint Concrete Jacking Pipes with a xed stainless steel jacking band.
Karun Kumar, Tunnels Project Engineer for McConnell Dowell, said the early engagement with all parties ensured a smooth process and procurement was able to be fast tracked given the urgency of the project.
“We made the decision to incorporate low carbon concrete in the design of the pipes. It was important that the design of the jacking pipes allowed for the push of 1400 tonnes
which also coincides with the maximum thrust force of our jacking frame,” Kumar said.
“We were able to deliver the lowest carbon option that met the project requirements for the material strength, program and cost. e 92 Hynds pipes will save approximately 62 tonnes of CO2 emissions which is a 16 per cent reduction in the standard pipe range.”
e rst phase of the project to unblock the culvert began last March. At the beginning of this year, the project team mobilised the land ll site which accommodates the launch shaft for the Micro-Tunnel Boring Machine (mTBM).
e mTBM will install a 2100mm ID stormwater pipeline in two tunnelling drives.
e rst will complete 220m in the rst drive and 50m in the second drive.
Hynds was able to deliver the HyndsLC pipes in the same timeframe and meeting the same engineering speci cations as the standard o ering, making life easy for the project team on-site. By conforming to the same engineering speci cations, the low carbon pipes have the same durability and design life as the standard options, meeting Healthy Waters’ long-term sustainability goals.
Gerhard Van Rooyen, Project Manager for Healthy Waters, emphasised Auckland Council’s commitment to sustainability.
“We are actively seeking opportunities to incorporate low carbon products into our projects. By closely collaborating with our supply chain and project teams, we can ensure these outcomes are realised, allowing us to deliver sustainable stormwater infrastructure that enhances Auckland’s resilience,” Van Rooyen said.
Todd Randell, Trenchless and Pipelines Specialist for Hynds Pipe Systems, said being able to o er a bespoke solution was a game changer for the project.
“ e jacking pipe used in this project is actually a lower carbon than we would normally produce,” he said.
“To meet the speci cations, we substituted raw materials – concrete, cement and steel –and chose from our diverse supply chain the lowest carbon producers that we work with.
“Without compromising the quality or durability we have been able to adopt a sustainable outcome for the future.”
e HyndsLC range is manufactured at the company’s state-of-the-art facility at Pōkeno which embraces new technology and production processes, all underpinned by leading edge sustainability practices.
Jackson MacFarlane, Group Sustainability Manager at Hynds, said the company is committed to lowering the carbon footprint of all its product ranges as well as across operations nationally.
“We are expanding our low carbon concrete product range across the country and working
with our customers to develop products that meet their sustainability needs. As part of this commitment, we are also engaging with our key supply partners to bring them on the journey and o er the best solutions possible,” he said.
“Delivering e ective and sustainable infrastructure products is all part of our goal to improve the resilience of communities across New Zealand.”
is collaborative approach with the client, consultants and designers has already made a positive impact on the overall program and provided a cost-e ective solution.
e Greville Road Stormwater Culvert Upgrade project is expected to be completed by mid-2025. At L&D Micro Tunnelling we specialize in laser guided boring. Our Tunnel bore machines use a vacuum extraction system where all spoil is sucked into interceptor tanks for easy disposal with no mess. All our heads are hydraulically driven and guided by a high accuracy laser to achieve precision over long distances.
J&R Contracting, with the help of All Drill, has delivered a critical water main project in Auckland.
All Drill NZ (ADNZ) is a long-time supply partner of the New Zealand drilling industry. Providing everything from onsite and technical support, training, mud schools, uid designs, drilling uids and tooling, ADNZ is supporting the horizontal directional drilling (HDD) sector across the country.
Founded by John Familton, ADNZ was built on the pillars of honesty, quality and reliability. And if you ask J&R Contracting Project Supervisor Ben Noakes about it, he’ll tell you that ADNZ embodies these principles.
“ADNZ supplies us whatever we need in terms of HDD, whether that’s reamers, drill heads, drill mud, or more,” Noakes said.
“ e service is primo – John has so much experience in the industry and is extremely handy.”
J&R recently tapped into John’s resourcefulness to help deliver the Richardson Road water main project in Mt Roskill, Auckland.
Utilising ADNZ HDD reamers and drill uid, J&R recently completed a single 210m drill shot to install a 500mm water main at depths of up to 6.5m.
Noakes said the project presented a number of technical challenges, such as variable ground conditions.
“Ground conditions were a challenge. We entered in solid, stable ground and then as we got down to 4m , we’re working in mud.
“We had to utilise a larger D100 drill rig and went through about 150 cubic metres of drill uid.
“In the end we removed almost 200 cubic metres of slurry, which is quite a lot.”
e project’s location also posed challenges of its own. As the work took place along a residential street, space was limited.
Due to site constraints, a drill uid recycling plant was established in the middle of the drill shot, where uid was mixed before being pumped 150m to the delivery tank.
“Another challenge was that the project took place outside of a primary school,” Noakes said.
“ e good thing was, we were able to align the timeframe of the project with school holidays. We got in and out before school went back.”
e Richardson Road project was a success, delivered on budget, within a tight timeframe,
and without issue from pilot to pullback.
“ e highlight for me was that, from pilot to pullback, everything went according to plan,” Noakes said.
is project is far from the rst that ADNZ and J&R have collaborated on. Indeed, the two companies have more than a decade of partnership.
“ADNZ is a very reliable supply partner,” Noakes said. “Often, John and the team are able to get equipment to site on the same day you call them.
“Sometimes with other suppliers based outside of Auckland, delivery can take a couple of days. But by this time, you’ve just made do with the tools available and nished the job.
“ e valuable thing about ADNZ is that service is fast and reliable.”
With the successful execution of the Richardson Road project, ADNZ and J&R Contracting have deepened their working relationship.
Together, the two companies will continue to deliver critical infrastructure projects to New Zealand.
Modular System: Easily configurable for various pipe sizes and inspection challenges.
Reliable Design: Built to endure harsh conditions and reduce downtime.
Contact SECA today to learn how the ROVION HD can revolutionise your sewer inspections.
With its bespoke glass reinforced plastic pipe lining, Channeline has helped fortify a major sewer transmission line in New Zealand for decades to come.
When Auckland’s Orakei Main Sewer collapsed in September 2023, Watercare Services called on civil engineering company March Cato to respond.
As one of the major city’s main sewer transmission lines, the task of repairing the pipeline demanded speed, precision and lasting quality.
And for that, March Cato and Watercare turned to Channeline.
Since the 1980s, Channeline has provided bespoke structural glass reinforced plastic (GRP) lining systems.
Channeline’s GRP solution is a fully structural rehabilitation solution for the trenchless rehabilitation of sewers, tunnels, culverts, stormwater and other buried structures. Its strength lies in its versatility and customisation, which is what made it a perfect t for the Orakei Main Sewer Project.
To carry out the rehabilitation works, March Cato designed a custom 35-tonne reinforced workstation, which was lowered by crane over the location of the collapse.
Here, March Cato was able to clear the debris in the sewer, and then begin to rehabilitate 120m of sewer. is was done in two drives both upstream and downstream of the breach.
e sewer was a unique egg shape with a 2.3m by 1.5m diameter, which is where Channeline’s custom GRP lining truly shone.
“It was a totally bespoke solution that Channeline provided to us,” March Cato Project Manager Daniel Cato told Trenchless Australasia
“ at’s the beauty of Channeline liners –they were made to a custom pro le with a very quick turnaround.”
Channeline can custom design and manufacture fully-structural lining systems in any shape and any size, making it an ideal partner for any contracting company working in the civil infrastructure space.
“ e company was great to deal with, coaching us through the installation process and providing an on-site expert,” Cato said.
“ e liners mated together nicely, and we were able to successfully line the sewer in live ow.”
Many trenchless operations take place in urban areas where space is limited. Indeed, the Orakei Main Sewer Project was no exception. is is where the lightweight construction of Channeline lining played a key role.
“One major bene t of using Channeline lining is that they are considerably lighter than typical liners,” Cato said.
“ is meant we were able to use a smaller crane to lower these components down into the workspace.”
Despite the light weight, Channeline GRP lining sacri ces nothing in strength, and can return even the most heavily used pipelines to serviceability for many decades.
e rst two layers of Channeline GRP lining, which are the surface and barrier layers, incorporate a corrosion barrier. is is manufactured from high-grade surface veil, precisely impregnated with resin, followed by several layers of multi-axial engineered fabric and glass bres.
As part of the process, the next layer is a central core, composed of sand and resin, which is evenly applied to the exact thickness required.
e following layers are formed using multi-axial fabric, glass bres and resin. is outer surface is treated with a bonded aggregate to enhance adhesion to the annular grout.
All of this comes together to form a strong lining system that is resistant to chemicals, corrosion, UV and extreme temperatures.
With the successful repair of this 120m section of the Orakei Main Sewer, Watercare and March Cato now turn their attention to the subsequent stages of the renewal works, which includes a signi cant 720m drive.
Once again, the company will combine its engineering know-how with Channeline’s unique and versatile lining solution.
A major project delivered by CDS New Zealand has shown that horizontal directional drilling is a robust and environmentally friendly solution to complex pipeline projects.
When a 200mm network watermain in South Auckland failed, utility company Watercare knew it had to act quickly.
e pipeline supplied drinking water to around 357 homes in the Glenbrook Beach region – an area experiencing rapid population growth.
But the pipe, which was anchored to the seabed, was subject to signi cant tidal in uence. Over time, this compromised its integrity.
“ e original pipeline experienced a joint failure that led to half a kilometre of pipe dislodging and oating to the surface of the Taihiki Estuary,” Watercare Design Manager Calvin McCluckie told Trenchless Australasia
“ is emergency prompted Watercare to establish a temporary solution, and subsequently, a permanent replacement project was conceived to ensure a resilient long-term water supply for the Glenbrook Beach area.”
To deliver such an outcome, Watercare partnered with CDS New Zealand Ltd, an expert in horizontal directional drilling (HDD).
“ e project was quite complex, entailing three parallel 750m crossings beneath the Taihiki Estuary,” CDS Engineer Marc Carmody said.
By engaging the services of Highside Drilling Services, CDS achieved added con dence in the pilot bore steering capability utilising the ParaTrack 2 guidance system.
Environmental features such as cli s, as well as the length of the crossings, also forced CDS to think laterally. Rather than following the old pipeline alignment – which would have been the easy decision – CDS opted to chart a new and slightly longer alignment that kept the project clear of a cli , keeping contractors and future maintenance workers safe.
“Another challenge we faced was the length of the crossing, which would have put more pull force on the relatively small bore pipe than we were comfortable with,” Carmody said.
“To remedy this, CDS calculated pipe pull forces and switched to a larger, non-typical pressure rating, PN25 pipe, which was strong enough to safely handle the crossing.”
Rising to the challenge, CDS mobilised to site in April, with the nal crossing installed in early September. e company expects the pipeline to be operational by the end of October.
CDS ensured the project was suitably sta ed and resourced including the establishment of its GoodEng HDD Maxi Rig, which provides a torque of 110,000 newton-metres with a maximum pull force of 3500-kilonewtons.
“It’s been refreshing having CDS as head contractor, as HDD specialists are usually called in as sub-contractors,” Carmody said.
“What made this project so e ective was the early implementation of our team from the design phase, allowing us to be part of the geotechnical scoping work and for HDD to be designed into the project from the very start.
“ is meant that potential risks were e ectively identi ed and managed.”
Each crossing had its own unique ground conditions ranging from gravel to clay. e team was able to tweak their approach in each instance, keeping the project progressing smoothly.
CDS understands the importance of good HDD drilling uid design.
Using specialists, as well as its own experienced team, ensured the uid properties were optimised for both hole cleaning function and to minimise circulating pressures, even as conditions changed downhole.
Watercare Project Manager Sean McHenry knew HDD was the right tool for the job.
“HDD was selected for its ability to minimise environmental disturbance by allowing the pipeline to be installed deep beneath the estuary bed, reducing the risk of erosion and the likelihood of future pipeline failures,” he said.
“Additionally, since the Taihiki Estuary is popular among locals for water activities, HDD guarantees that the pipeline remains safely buried, eliminating the risk of damage
from boat anchors or other activities that may have contributed to the previous pipe failure.”
McHenry also said that CDS’ ability to engage and work with other stakeholders was crucial in delivering the project.
HDD enabled CDS and Watercare to deliver a low-impact, environmentally friendly, and future-proof solution to the locals of Glenbrook Beach.
“ is project is an investment in future of Glenbrook Beach, providing a resilient infrastructure that will support future growth and development in the region,” McHenry said.
The Subsite® Marksman HDD Guidance System provides superior performance in high-interference environments with the industry’s widest range of frequencies in a single beacon. Easy to use with your choice of user interface, the Marksman View features intuitive graphics and clear data, and with a simple single toggle control you’re more productive from day one.
NordiTube and PipeWorks provide New Zealand network owners with the full solution to their ageing pipe networks.
With more than 40 years as a global manufacturer of rehabilitation solutions, NordiTube Technologies has brought the next level of pressure and gravity liners to New Zealand with its local partner, PipeWorks.
Starting with its roots in Belgium, NordiTube Technologies quickly expanded to become a market leader in Europe, North America, and Asia, providing pressure rehabilitation solutions for the water, gas, industry and sewer-main markets.
Now, 40 years later, NordiTube Technologies has manufacturing facilities in Europe, Vietnam, America, and China.
e company reaches its customers globally with fast and e ective lead times, local technical support o ces, and local partners. is includes NordiTube having an o ce in Adelaide and Sydney for the Australian and New Zealand markets.
For more than 20 years, PipeWorks has provided customers with rehabilitation solutions for their networks.
In 2024, NordiTube and PipeWorks teamed up to reduce water loss and protect the environment from pollutants by providing New Zealand municipalities with solutions that allow them to repair their aging pipe
infrastructure quickly, cost-e ectively, and with minimum damage to the environment and community.
e companies accomplish this by providing the full solution from start to nish – advising and then providing customers with a full line of solutions for their water, wastewater, stormwater, oil, and industry pipeline assets.
A agship solution for network operators worldwide is the Nordi ow, a new pressure pipe within the old pipe.
e Nordi ow is a trenchless cured-in-place (CIPP) pipe solution.
Network operators face issues with budget and time restrictions, as well as community and environmental impacts when maintaining their pipe network.
When integrating the Nordi ow system into their ageing network, network operators can expect 30–70 per cent of the cost of replacement and up to ve times faster reinstatement of the network.
Additionally, there will be no disruption to the community or damage to underground or aboveground assets. Increases in hydraulic capacity are also possible with NordiFlow’s smooth inner PE surface.
e Nordi ow comes in sizes DN1501400 and is used for water and sewer mains and high temperature lines, and is AS/ NZS 4020 approved and under the WSAA appraisal (PA2303).
In Auckland, PipeWorks utilised this gamechanging solution in the city’s network.
e section posed a challenge for the designers because the pipe was parallel to a
busy intersection. e line was located under a pedestrian footpath with several residential driveways, which meant that open-dig pipe replacement was immediately out of the question because of the cost, time, and damage to the community.
NordiTube and Pipeworks identi ed the network operator’s problem in their network, o ered the best solution, designed the Nordi ow to match a minimum 50-year lifetime in the network, manufactured, sent, and then installed the Nordi ow to reinstate the network. is whole process happened in less than a month.
PipeWorks will continue to provide innovative NordiTube rehabilitation solutions to the New Zealand communities.
For more information, visit norditube.com and brianperrycivil.co.nz
DISCOVER THE FUTURE WITH BOTHAR, A GLOBAL TRENCHLESS CONSTRUCTION EXPERT.
Ensure your project is delivered safely, sustainably, and successfully.
Bothar possesses comprehensive trenchless solutions alongside expertise in shaft construction and civil capabilities.
With over 30 years’ experience, Bothar is your partner for the delivery of complex infrastructure solutions.
Our Services
•Vermeer Axis Laser Guided Systems
•Auger Boring
•Direct Pipe Installations
•Shaft Construction
•Herrenknecht AVN MTBMs
•Bothar Built EPB - TBMs
•Open Face TBMs
•Tunnel Boring & Pipe Jacking
Founded in 1985, CDS New Zealand has established itself as a leading name in directional drilling, setting industry standards across the region.
As a family-owned business, CDS New Zealand attributes its success to a focus on international development and technological innovation.
To further enhance its trenchless capabilities and operational excellence, CDS recently invested in the American Auger M300DH Cleaning System, supplied by CEA NZ.
According to Daniel Clough, Director at CDS, the company identi ed the need for a recycling unit with small footprint to be utilised on medium sized HDD projects.
“ e known American Augers build quality and fact it was tted with a Derrick Hyperpool shaker made the M300DH a clear choice,” Clough said.
e relatively smaller footprint of the M300DH reduces mobilisation costs.
As a result, CDS is now recycling uid on projects where previously they would have used a pump-and-dump approach.
“ e M300DH has resulted in less trucking of chemical to site, less water trucked to site, and we are not tying up our vacuum trucks to dispose of large volumes of waste uid,” Clough said.
“ is is making our projects greener with a reduced carbon footprint and at the same time more pro table. It has allowed us free up resources for other tasks like hydro excavation
service location so has a bene cial ow on e ect to the rest of our business.”
Just like Clough said, M300DH’s upgraded Hyperpool® shaker from Derrick® ensures ultra-clean performance, enhancing production while prolonging the life of drilling packages.
is technology-driven approach underscores CDS’ dedication to clean production and e ective uid management, both crucial aspects of modern trenchless operations.
Equally impressive is the system’s uid management capabilities. With three centrifugal pumps, the M300DH guarantees optimal ow and pressure, providing ondemand drilling uid.
e M300DH Cleaning System has already become a valuable asset for CDS’s operations.
CDS recently ran the M300DH on a project in Auckland, installing pipe lengths ranging from 220m – 260m in high plasticity clays and clayey silts.
In these conditions it is critical that the operators can pump enough uid to dilute the return solids concentration and keep downhole pressures low to prevent hydro-fracture. e M300DH processing capacity gave them the freedom to pump the volume of drilling uid that is required while maintaining production rates.
Its advanced cleaning and uid management systems have led to reduced equipment wear and increased uptime.
In other occasions, M300DH’s versatility allows adaptation to various job sites, and compatibility with any drill brand ensures seamless integration with existing eets.
According to Clough, CDS has been recycling its drilling uids for close to 15 years to great success, and the addition of the M300DH has been impressive to say the least.
“We are getting dry cuttings and less uid retained on cuttings means less disposal volume and trucking,” he said.
“ e processing capacity ensured that we didn’t experience any non-productive time waiting for uid.”
By investing in the M300DH, CDS not only strengthened its market position but also exempli ed the innovative edge that CEA NZ’s distributed products bring to the trenchless industry.
e company’s ongoing commitment to excellence and safety not only underscores its role in strengthening companies like CDS, it enhances operational e ciency and success in the New Zealand and Australia’s trenchless sector.
In a significant development for the country’s water infrastructure sector, Nuflow New Zealand has expanded its operations to encompass nine franchises across the North and South islands.
This growth is not just a testament to the company’s success but also indicative of the increasing demand for innovative pipe repair and relining solutions throughout the country. As Nu ow celebrates 20 years of servicing the Australasia region, this expansion marks a new chapter in the company’s storied history.
Nationwide coverage
Nu ow’s strategic expansion now covers key regions including Northland, Auckland North Shore, Auckland City, Hawkes Bay/Gisborne, Palmerston North, Wellington, Nelson, Christchurch, and Dunedin. Its widespread presence ensures that communities across New Zealand can access cutting-edge pipe rehabilitation services that are leading the market.
Expertise and capacity
With 14 teams of trained and accredited CIPP (cured-in-place pipe) installation technicians, Nu ow has positioned itself as a leader in the eld. e company’s robust workforce allows it to meet the high demand for infrastructure maintenance and improvement across diverse geographical areas.
Comprehensive service offering
Nu ow New Zealand’s service portfolio is impressively comprehensive, addressing a wide array of infrastructure needs:
• Pipe relining for sewer, stormwater, and pressure pipes
• Manhole rehabilitation
• Pits, chambers and pump stations
• SIPP (spray-in-place pipe) solutions
• In-pipe lining solutions
• UV Large bore DN 150 to DN 1200
• Fire mains
• Rising sewer mains
• Trade waste – high temp acid resistance lining solutions DN 40
• Potable water CIPP lining solutions for water mains
• Nu Coat SIPP lining solutions
is extensive range of services demonstrates their commitment to providing holistic solutions for water infrastructure challenges, supported by Nu ow’s sophisticated and tailored approach to service delivery. Nu ow’s liner design thickness guideline allows the company to capture site-speci c information, enabling bespoke lining solutions in complex circumstances. It also utilises a quality assurance app to ensure that each job
meets the high standards upon completion. is consistent attention to detail ensures that each project receives a custom- t solution, optimising both e ciency and e ectiveness.
Looking ahead
Nu ow New Zealand’s expansion is more than just corporate growth; it represents a signi cant step forward in the nation’s ability to maintain and improve its critical water infrastructure. As urban development continues and existing
e cient, and environmentally friendly pipe rehabilitation solutions is only set to increase. e company’s success and expansion strategy could serve other players in the utility sector.
By joining the Nu ow network, they can drive innovation and improvement within their business and the industry as a whole.
As the industry looks to the future of New Zealand’s water infrastructure, Nu ow is con dent it will play a crucial role in ensuring
of vital water systems. Its growth is not just good news for the company, but for the entire nation’s infrastructure resilience.
Find your local Nuflow
Find a Nu ow near you and access a large local network of trained, accredited technicians with years of experience and the backing of an extensive support network.
Projects in highly populated areas give rise to unique challenges, but the right machinery can ensure the job gets done quickly and without disruption.
Whether it be new developments or upgrades to existing infrastructure, large-scale infrastructure and utility projects within built-up suburbs are common. ey often require contractors to operate within strict time, space and noise restrictions, and choosing the right equipment is imperative to minimising impacts on the surrounding community.
Small but mighty
Vermeer’s D23x30DR S3 is the perfect machine for projects with tight jobsites because of its powerful engine and compact footprint.
Weighing in at 7666kg, it is the lightest rock drill in its class – and with a width of just 141cm, it measures in at 62.2cm narrower than its closest competitor. Its small size and light weight enable the D23x30DR S3 to manoeuvre built-up areas with ease.
Continuing the legacy of the S3 badge, the D23x30DR S3 o ers speed, simplicity and (low) sound. e combination of the latest dual-rod technology and a 100hp engine means that the D23x30DR S3 can drill through even the toughest rock.
Additionally, with an operator ear noise level of 80.3 dB(A), the D23x30DR S3 is quieter than a blender, and is sure not to bother the neighbours.
Skytech Group’s D23x30DR S3 in action
As a leading NBN works provider, Skytech Group works predominantly in established neighbourhoods and recently purchased another drill, Vermeer’s D23x30DR S3, to support its urban NBN projects.
e company chose to purchase a D23x30DR S3 after careful consideration between other options on the market because it was well suited for both current and future projects.
“ e D23x30DR S3 presented as a highly capable rock drilling machine that still maintained a small enough footprint to ensure an optimised site set-up for our clients,” Skytech Group’s General Manager Marc Rodrigues said.
One of the bene ts of the D23x30DR S3 is that it can balance capability and power to drill in rock conditions and is nimble enough to set up in typical suburban areas.
“ e D23x30DR S3 has been used on our projects to install 63mm and 110mm communications conduit,” Rodrigues said. “Its dual rod feature enables us to grind
through rock underground and accomplish jobs otherwise not possible with conventional clay drills.”
Additionally, Rodrigues said that the small footprint and high capability of the D23x30DR S3 allows Skytech Group to execute projects in high-density areas with limited access that, without it, would require larger machines.
“ e D23x30DR S3 enables the site set-up to be compact and as low impact as possible to surrounding residents and businesses, because we can tailor our plan to adapt to the situation and still achieve our desired outcome,” he said.
With a range of Vermeer machines in the company’s eet of equipment, Rodrigues said that Vermeer’s customer support played an important role in the decision to purchase the D23x30DR S3.
“From sales to maintenance, they have been with us to advise and showcase how to unlock the machine’s potential,” he said.
“ at’s just another reason we’re so happy with our choice.”
For more information, call 1300 VERMEER or visit vermeeraustralia.com.au
Any shape, any size
Channeline’s bespoke GRP lining systems can precisely fit any existing structure, offering a fullystructural trenchless solution to improve performance and extend infrastructure life for 150 years.
channeline.com
In a move to strengthen its trenchless technology offerings, CE Civil has acquired the GRUNDODRILL 18ACS from TRACTO Australia.
For over 20 years, CE Civil has built a solid reputation by specialising in civil construction within the utilities sector, covering communications, water, power, and gas.
CE Civil Chief Executive O cer Chris O’Grady told Trenchless Australasia that the company’s approach to trenchless technology has evolved signi cantly in recent years.
“We used to outsource our trenchless technology, but since COVID-19, we’ve launched our own internal trenchless department, and it’s branded as CE Trenchless,” he said.
“As civil construction continues in the coming years, we see trenchless as a more aggressive solution in Australia.”
O’Grady said the decision to invest in the GRUNDODRILL 18ACS was driven by the need for a reliable solution to tackle challenging geological conditions.
“TRACTO’s track record and the track record of the GRUNDODRILL 18ACS in penetrating rock is really strong,” he said.
“We got this drill speci cally as our rock solution. We know other companies that use the drill, and they have great feedback.”
e GRUNDODRILL 18ACS is renowned for its performance in rock drilling, a critical factor for CE Civil as they continue to take on projects with demanding conditions.
Dubbed as the ‘King of Rock’, the GRUNDODRILL 18ACS makes an impact in all kinds of soil.
It has a fully automatic operation which ensures minimal downtime and relief for the machine operator.
With the acquisition of GRUNDODRILL 18ACS, CE Civil aims to enhance its operational e ciency and deliver high-quality results, particularly in areas where traditional methods might falter.
O’Grady said it has already proven its worth.
“We’ve used the machine across a few projects,” he said.
“We hit some pretty serious rock in Mount Martha and Sunbury, and the drill was fantastic.”
When asked why CE Civil chose to work with TRACTO Australia, O’Grady highlighted the exceptional service and support provided by the company.
“ e testing that TRACTO does, and their service is fantastic,” he said.
“ ey really follow through with everything.
ey’re always there if we have any questions.” e geographical distance between TRACTO Australia’s headquarters in Queensland and CE Civil’s base in Victoria has not been a barrier.
“Being that they are based in Queensland and we’re in Victoria, there’s no real gap because they have a presence here in Victoria and they have service partners here as well,” O’Grady said. is continues to be a hallmark of the
company’s services, according to TRACTO Australia Sales Manager Daniel Toms.
“TRACTO Australia works as more than a supplier and we always aim to provide the best after sales support,” Toms said.
“For us, the sale is only the rst step in our partnerships with customers, and the real work starts when the drill is delivered.” is close working relationship ensures that CE Civil can rely on TRACTO not just for equipment, but for ongoing support, further solidifying their partnership.
As CE Civil continues to expand its trenchless technology capabilities, the acquisition of the GRUNDODRILL 18ACS represents just the beginning. e company’s forward-thinking approach and investment in machinery such as the GRUNDODRILL 18ACS, positions CE Civil as a leader in the horizontal directional drilling industry.
The trenchless technology industry is advancing, and PACE Drilling is leading the charge.
Founded in 2004, Pace Drilling is well known as one of the most respected and reliable horizontal directional drilling (HDD) specialists in New South Wales.
With a reputation for providing cost-e ective and quality solutions to their extensive customer base, the team at Pace Drilling work tirelessly to meet the challenges each construction job requires. e company has the expertise and equipment to get the job done quickly and e ciently.
With a proven track record of completing complex bore projects using its AT32 and AT60 rigs, PACE Drilling noticed an increasing demand for larger pipeline installations over longer distances.
To meet this challenge head-on, they turned to Ditch Witch CEA, the national distributor of Ditch Witch products in Australia, for the powerful AT120 as the solution.
O ering a remarkable 120,000 pounds of pullback force, the AT120 ensures con dence and reliability in undertaking even the most challenging projects. Its introduction has signi cantly enhanced productivity at PACE Drilling.
e increased inner rod rotational torque has made drilling through rock strata more e cient, especially during pilot shots.
Additionally, the machine’s power has streamlined the process of opening larger diameter holes, contributing to a more e ective operation overall.
PACE Drilling recently faced a demanding project involving a pipeline installation during a night-time shutdown of a heavily tra cked road.
Given the limited timeframe and the need for minimal disruption, the AT120 proved indispensable.
Its robust capabilities ensured the installation was completed smoothly, minimising impact on the public and environment.
e AT120’s rapid carriage speed and dual rod box design have been transformative, setting
a new standard in operational e ciency in trenchless technology.
Additionally, the enhanced inner and outer rod rotational torque has played a critical role in boosting productivity, particularly in challenging drilling conditions.
Marking a substantial advancement from the AT60, the AT120’s state-of-the-art operator cabin o ers an improved, user-friendly experience, signi cantly enhancing operator comfort and overall work ow.
Despite its compact footprint, the AT120 delivers a formidable 120,000 pounds of thrust, meeting the demands of complex projects while minimising environmental and public impact. is versatility has expanded PACE Drilling’s project portfolio, allowing the company to undertake larger-scale operations that were previously beyond reach.
Compliance with environmental standards is crucial, particularly when working with tierone clients.
e AT120’s Stage V Cummins engine meets these stringent requirements, o ering exceptional fuel e ciency and quiet operation — vital attributes in maintaining the company’s commitment to sustainability.
According to Pace Drilling, the operators
have praised the AT120 for its quiet and spacious operating station, which o ers maximum visibility.
ese design elements not only improve the user experience but also contribute to safer and more e cient operations.
e VAM (Virtually Assisted Makeup/ breakout) technology has been a game-changer in maximising rod life and expediting rod makeup.
A spokesperson from Pace Drilling told Trenchless Australasia that the most notable bene t has been the increased production rate.
“Completing projects ahead of schedule has enabled PACE Drilling to move on to new assignments more swiftly, translating into tangible cost savings and heightened operational e ciency,” the spokesperson said.
With over two decades of partnership with Ditch Witch, PACE Drilling has always relied on equipment that combines high performance with unmatched reliability.
e brand’s consistent support, service, and the reliability of its products have been fundamental in building this enduring partnership.
For more information, visit ditchwitchcea.net.au
kwik-ZIP spacers were utilised on a major water infrastructure project in NSW.
Contracting company Jonishan recently utilised kwik-ZIP HDXT-103 spacers to facilitate the slip-lining of a 914mm Sintakote® mild steel cement lined carrier pipe into a 1200mm reinforced concrete jacking pipe casing. e work was conducted for the Upper South Creek treated water main. is installation was part of the larger Upper South Creek (USC) project, which was implemented to improve environmental ows by transferring treated water from the new advanced water recycling centre (AWRC) to local waterways. e AWRC and USC project are Sydney Water’s largest infrastructure investment in Western Sydney.
Whilst this installation was fully grouted, the HDXT spacers adequately supported the pipe and water for the life of the installation. is is no small task, as the pipe weight
is a signi cant 292kg/m when empty and 880kg/m when full.
But the HDXT’s unique load-sharing design maximises the load bearing capacity of each runner and reduces point loading, helping it safely and reliably bear the weight of piping.
In the world of civil infrastructure, delays are extremely costly. Fortunately, kwik-ZIP spacers can be e ciently installed without the use of any special tools, setup equipment, or the requirement to pre-wrap pipe.
“ e kwik-Zip spacers were very simple and easy to install,” Jonishan Project Engineer Malvin Malicdem said.
In addition to being simple to use, kwikZIP spacers have no metal parts and are made from kwik-ZIP’s engineered thermoplastic blend that is exible, extremely tough and has a low co-e cient of friction.
e kwik-ZIP HDXT series o ers noncorroding, non-metallic, heavy-duty bow spring casing spacers for horizontal pipe-inpipe and open bore applications, which can help extend the life of pipelines.
“Although spacers are usually a small part of the overall pipe installation process, correctly designed and tted spacers can signi cantly increase the life expectancy of the carrier pipe by assisting to keep them free from corrosion as well as remove the potential for damage during installation,” kwik-ZIP Managing Director Jason Linaker said.
In the case of the USC project, the fusionbonded coating on Sintakote® piping was crucial for corrosion prevention and must stay undamaged to work e ectively.
Here, kwik-ZIP spacers not only provided protection but also featured integrated rubber
grip pads, preventing slippage and preserving the coating’s integrity.
In Australia, kwik-ZIP’s HD, HDXT and HDX series of spacers have been successfully appraised by the Water Services Association of Australia (WSAA) against the requirements of WSAA product speci cation number PS-324 (casing spacers).
e WSA PS-324 product speci cation prescribes casings spacer requirements for correct protection of carrier pipes when installed inside casings.
Meeting this rigorous standard means that all of kwik-ZIP’s spacer series meet speci cation requirements and quality assurances demanded by the utilities market.
kwik-ZIP’s large range of spacers can cater to a wide range of carrier and casing pipe size combinations as well as providing exibility to deal with project alterations for any of its customers.
more information, visit kwikzip.com or email sales@kwikzip.com
ASOE has established an array of trenchless pipe rehabilitation solutions tailored for pressure pipe systems. Among these innovations is the Pipe-in Liner, a Flexible Fabric Reinforced Pipe (FFRP).
WHY CHOOSE ASOE
ENHANCED DURABILITY
OPTIMAL FLEXIBILITY
MAINTAINS SHAPE
INCREASED CAPABILITIES
ABRASION-RESISTANT
HIGH BURST PRESSURE
LONG DESIGN LIFE OF 50 YEARS
STREAMLINED INSTALLATION
COMPLIANT WITH SEVERAL STANDARDS,
IMPREG UV-curing equipment, guided by the steady hand of TDM Group Australia, has delivered a technically challenging pipeline project on the central coast of NSW.
The coastal region of NSW is no stranger to heavy rainfall and ooding. at’s why proper drainage is a vital part of the state’s infrastructure.
When one of these critical drainage systems neared the end of its operational lifespan, TDM Pipeline Solutions (TDM PS) was called in to help.
e drainage pipe in question ran underneath a highway in a bush-choked valley – an important road for NSW inhabitants.
TDM PS Business Development Manager Calyn Wilkinson said the pipeline was old and in need of repair, with displaced joints and in ltration at multiple points along the pipe.
“It’s an important drainage system which prevents water from ooding the roadway, so it was critical to repair it e ciently and in a way that lasts,” he said.
To that end, TDM PS turned to its long-time supply partner IMPREG.
“We utilised IMPREG’s fully structural UVcured GL16 liner at DN [diameter nominal] 900 and 8.3mm thickness,” Wilkinson said.
IMPREG is one of the world’s leading manufacturers of cured-in-place-pipe (CIPP) liner systems for UV-curing.
e company’s GL16 liner was developed for all common pipes from DN 150 to 2000 for sustainable and e cient trenchless rehabilitation.
Boasting over 100 years of design life, high quality UV resins, easy installation, and extreme durability even under tough conditions, it’s not hard to see why IMPREG is one of the liner brands that TDM PS uses.
Yet despite the quality of tools in TDM PS’s kit, the relining project presented some technical challenges.
“ e pipe was 5m below the level of the road, and access to both the upstream and downstream sides was 20m o the road through bushland,” Wilkinson said.
“To deliver the project, we utilised a 32-tonne crane to lower the liner equipment down to the access point.
“As we were working in a waterfall area, we also had to create a temporary dam and pump out the water to another area.” anks to the combined ingenuity and expertise of TDM PS and IMPREG, the project was executed without any issues.
“It was a very successful installation that the client was pleased with,” Wilkinson said.
“We were able to restore the drain to its full strength and serviceability for decades to come.”
With the delivery of this latest project, TDM PS has laid more than 4km of IMPREG liner. Wilkinson said one of the best things about working with IMPREG is having direct access
to the supplier, rather than dealing with a thirdparty distributor.
“IMPREG has a relatively fast response time, providing us with fully structural liner designs that meet the client’s criteria,” he said.
“Communication is another strength. If we’re trying to meet tight deadlines, IMPREG is always on deck to help us get what we need, when we need it.”
For IMPREG, the respect is mutual.
“We always enjoy the opportunity to work closely with TDM PS, which excels in providing solutions for di cult installations with a great end result,” IMPREG Country Manager Colin Murphy said.
With the backing of IMPREG, TDM PS is delivering high quality pipeline projects around Australia.
“We’re a solutions-based business that delivers a high standard of work,” Wilkinson said.
“Some projects might seem impossible, but there’s always a potential solution that we try and provide for our clients.”
Loaded with 120,000 lbs (533.8 kN) of pullback/thrust and 15,500 ft-lbs (21015 N·m) of rotational torque, the AT120 not only opens you up to new types of jobs but moves through long bores and large diameter installs with eye-popping power.
Featuring All Terrain technology, a 280-hp (209 kW) Cummins® engine that reduces environmental impact without losing any power, and 3,000 ft·lbs (4067 N·m) of inner rotational torque providing a 50% increase over its predecessor the AT120 provides additional power to drill through the toughest terrain around.
Like to know more?
The Southern Growth Area has been designated by the rural city of Wangaratta as a primary zone for residential development.
This pivotal area, currently in its nascent stages of growth, requires extensive infrastructure upgrades to accommodate the projected population surge.
North East Water has mandated the installation of several new sewer pipelines to support this expansion, integral to managing future housing and community needs.
Adept Civil, a premier civil and water infrastructure contractor based in Victoria, has been selected for this critical task.
e project encompasses the construction of key sewer pipelines, including a 1000m long, 250mm diameter sewer rising main extending from the Salisbury Street sewer pump station along Salisbury Street to Cribbes Road.
Additional works include 710m of gravity sewer pipe varying from 225mm to 300mm diameter west of Salisbury Street and 560m of 300mm diameter gravity sewer pipe along Cribbes Road and Rattray Avenue.
Adept Civil was appointed by Longford Civil, the principal contractor, to undertake the microtunnelling works along Salisbury Street and Rattray Avenue.
e scope of the contract involved approximately 350m of 324mm glass reinforced plastic (GRP) pipe installation at various depths.
Adept Civil’s reputation for collaboration and its adeptness at integrating client requirements were pivotal in securing this contract.
e company’s expertise in microtunnelling was crucial for the project’s success.
For the precise execution of this project, Adept Civil employed the Axis GB812 laserguided boring system. is choice was instrumental in achieving accurate grade drilling and e cient material extraction, minimising environmental impact and community disruption.
One of the signi cant challenges encountered was the installation of the
DN324mm GRP gravity sewer along Cribbes Road, which was completed using microtunnelling due to the pipeline’s alignment in the nature strip.
is method e ectively reduced disturbances to residents, mitigated tra c disruptions, and minimised the impact on existing services, vegetation, and infrastructure.
e use of the Axis boring system, with its advanced precision and vacuum extraction capabilities, further ensured a seamless execution.
Established in 1999, Adept Civil has grown into a leading civil infrastructure contractor.
With over 40 professionals, the company is renowned for exceptional civil project delivery and stringent safety and quality standards.
e company specialises in water and sewerage pipelines, pump stations, and associated services, consistently meeting industrial codes.
Adept Civil’s commitment to safety, environment, and ISO certi cations positions it as a trusted infrastructure partner.
e company holds accreditation from major water authorities including City West Water, Yarra Valley Water, South East Water, and Melbourne Water.
Additionally, Adept Civil is a Civil Contractors Federation Victoria Branch member and VICROADS accredited, re ecting extensive industry recognition.
For more information, visit adeptcivilgroup.com.au
Bothar Group operates at the forefront of trenchless technology, providing solutions-based services that address some of the most challenging infrastructure projects across the globe.
With a focus on delivering complex trenchless solutions, Bothar Group leverages decades of experience, a robust safety culture, and an extensive eet of specialised equipment. Its ability to execute intricate projects in demanding environments has earned them a solid reputation as a trusted partner in subsurface engineering and infrastructure development.
A testament to Bothar’s capabilities is the company’s ongoing Kemps Creek Project in New South Wales.
is dual pressure water main project is a remarkable example of Bothar’s commitment to excellence and innovation in challenging environments.
Utilising a Bothar-built Earth Pressure Balance Tunnel Boring Machine (EPB-
TBM) with a DN1200 (1450mm OD) con guration, the project involves the construction of dual pressure water mains, each housed within DN1200 RCJP enveloper pipes. e project includes twin drives of 270m and 165m, demonstrating the precision and reliability of Bothar’s technology.
e Kemps Creek Project is particularly noteworthy for the complex, water-charged ground conditions it navigates, providing an ideal platform for Bothar to showcase its advanced trenchless technology and engineering expertise. e project traverses environmentally sensitive areas and zones with high tra c volumes, requiring meticulous planning and execution to minimise community impact.
Additionally, the longer twin drives necessitate the use of multiple interjacks, adding another layer of complexity that highlights Bothar’s ability to successfully navigate challenging projects.
Bothar’s extensive portfolio of subsurface engineering equipment is designed to meet the demands of every complex project.
e company’s eet includes Herrenknecht AVN Machines, Vermeer Laser Guided Vacuum Systems, Bothar-built EPBTBMs, open face TBMs, auger boring machines (ABMs), pipe jacking capabilities, shaft construction, and direct pipe installation (DPI).
is diverse array of equipment enables Bothar to tailor its approach to each unique project, ensuring the highest standards of quality and safety.
Bothar’s work on the Kemps Creek Project is a prime example of its leadership in the trenchless solutions industry.
e company’s ability to deliver complex infrastructure projects with precision, while navigating challenging environments, helps reinforce the company as a go-to partner for large-scale engineering endeavours. As it continues to push the boundaries of what is possible in subsurface engineering, Bothar remains committed to innovation, safety, and excellence in every project it undertakes.
For more information, visit botharboring.com
In a rapidly evolving industry, Edge Underground continues to thrive by embracing innovation and consistently delivering high-quality solutions.
Over the past several months, the company has achieved multiple consecutive record-breaking months in terms of revenue, a testament to its ability to stay ahead in the competitive microtunnelling sector.
Driving success through innovation
Founder of Edge Underground and Chief Executive O cer of OptionX Group Stuart Harrison said the growth of microtunnelling as a preferred method for pipeline installation has been instrumental in Edge Underground’s success.
“As industries increasingly recognise the bene ts of this technology, projects that were once unsuitable for trenchless methods are becoming viable due to advances in technology and equipment,” he said.
Edge Underground’s ability to continuously innovate has not only set it apart from its competitors but has also helped it to expand its capabilities. e company is known for tackling unique challenges head-on, with a strong emphasis on research and development.
Turning negatives into positives
e COVID-19 pandemic posed signi cant challenges for many businesses, including Edge Underground. With travel restrictions in place, Harrison, as the company’s owner and leading expert, was unable to be present on every site to provide solutions. However, this challenge proved to be a turning point for the company.
e lockdowns showcased the depth of expertise within the Edge Underground team, proving they had reached a new level of understanding.
“Our on-site experts, in consultation with industry leaders, successfully utilised technology to manage site requirements remotely – a system that is now enabling the company to further expand its network,” Harrison said.
Determined to turn the negatives of the pandemic into positives, Edge Underground identi ed its supply chain and equipment availability as critical areas for improvement. is led to the acquisition of Bournedrill, and the formation of OptionX Group, a key strategic move that ensured Edge Underground could provide solutions at the highest level, regardless of international conditions.
Following the pandemic, many companies became comfortable with delays and extended timelines, but Edge Underground resisted this trend. Its close partnership with Bournedrill has meant solutions are readily available, allowing the company to respond quickly and e ciently to any challenge.
Edge Underground’s dedication to custom solutions has been a cornerstone of its success. On a recent project requiring canopy tube installation, every part of the solution was manufactured at Bournedrill, demonstrating the company’s ability to create tailored solutions in-house.
In another project with challenging ground conditions, it was the upgrades made at Bournedrill on the AXIS machine, featuring AdaptX’s patented technology, that enabled the Edge Underground team to achieve success where others may have struggled. is dedication to innovation doesn’t stop at technology. e Edge Underground team has spent the last decade conducting research and development on Riteline and AdaptX, with an ongoing commitment to improving processes and pushing the boundaries of what’s possible in microtunnelling.
e team is constantly challenging the way things are done today, always striving for better, more e cient methods. ey are committed to shaping the future direction of the microtunnelling industry, and their reputation as problem-solvers is well-earned.
Edge Underground’s belief in trenchless technology as the future of pipeline installation goes beyond strong – it’s unwavering.
perform in a timely and cost-e ective manner. Edge Underground is dedicated to overcoming these limitations, always asking how it can reduce costs and improve e ciency. In fact, the company has hinted at upcoming timeand money-saving solutions that will further cement its position as a leader in the industry.
As Edge Underground continues to grow, the company is expanding its footprint across Australia, with bases in Melbourne, Sydney, Gold Coast, and Townsville. Its focus is on better serving its customer base, both nationally and internationally, through its network.
e company is also heavily involved in research and development, with OptionX Group currently supporting 11 active research and development projects. Edge Underground’s team remains eager to push the boundaries of what’s possible, always looking for motivated individuals to join the ranks and contribute to its innovative culture.
With its focus on continuous improvement, innovation, and problem-solving, Edge Underground is not only shaping the future of the microtunnelling industry but also rede ning what’s possible in trenchless technology.
Head to the next job, thanks to Smart Lock's innovative expanding and locking system.
In urban infrastructure, maintaining the functionality of underground drainage and sewage systems is crucial.
Over time, concrete pipes can su er from signi cant blockages due to mineral deposits, roots, and other obstructions that hinder water ow.
This was the challenge faced when rock-hard mineral sediments formed extensive blockages in concrete pipelines, severely restricting the ow of combined sewage.
e IBAK MicroGator GT Lite, equipped with advanced ultra-high-pressure water jetting technology, emerged as a powerful and precise solution to restore these pipelines to full operational capacity.
The challenge: Rock-hard mineral deposits and root infestation
Concrete pipes, running beneath roads and other non-accessible areas, faced severe obstruction due to natural spring water carrying mineral deposits that settled and hardened in the pipe’s invert.
ese rock-like layers had built up over time, blocking nearly 50 per cent of the pipe’s capacity.
In some instances, lime deposits had sintered to almost two-thirds of the pipe’s height, creating an extremely hard barrier.
Left unchecked, these deposits would lead to complete pipe closure. Complicating the issue further, roots had in ltrated the pipes, forming a dense, tangled mass that needed to be removed to prevent further sewage backup.
Given the location of these pipes, excavation was not an option, and any solution needed to be both non-invasive and highly e ective. Traditional methods like mechanical cutting alone could not provide a long-term solution without risking damage to the pipe structure.
is is where the MicroGator GT Lite’s advanced water jetting technology proved invaluable.
The solution: Ultra-high-pressure water jetting with precision control
As part of the company’s products, the IBAK MicroGator GT Lite employs robot-guided ultra-
high-pressure water jetting technology to address these complex challenges. is method allows for the removal of extensive mineral deposits, roots, and other blockages in a fast, economical, and pipe-friendly manner.
Operating typically at 2500 bar and 26 litres per minute, the system uses among others a rotating falch X-Jet cross jet head that delivers a strong shearing force, breaking apart even the hardest deposits without damaging the pipe wall.
e key to the IBAK MicroGator GT Lite’s systems e ciency lies not only in its power but also in its precision.
e IBAK control system allows operators to set parameters with extreme accuracy, ensuring that the water jet targets only the unwanted deposits, leaving the pipe structure intact.
In addition, the ability to adjust the angle of incidence of the nozzles further enhances this precision for customers, focusing the water jets on the areas that require removal while protecting the integrity of the surrounding pipe.
To ensure that the cleaning process is both e ective and safe, the IBAK MicroGator GT Lite is equipped with an observation camera system. is camera provides operators with a clear, real-time view of the work area, allowing them to monitor the progress and make adjustments as necessary.
e visual monitoring ensures that the entire process remains controlled and that all blockages are removed without risking damage to the pipes. is combination of high-pressure water jetting and live visual control makes the GT Lite a highly e ective tool for restoring pipelines.
Compared to traditional mechanical cutting methods, controlled water jetting o ers several key advantages for large-scale blockages. First, it is a more economical option, especially when dealing with extensive deposits of a solid character, such as lime or mineral sediments. Additionally, water jetting is a highly e cient method for cleaning in areas with limited water availability, as the technology operates with low ow but high performance, maximizing resource use.
e ability to ne-tune the system’s parameters ensures that the cleaning process is not only thorough but also safe for the pipe infrastructure, which is critical when dealing with concrete pipes sintered with lime deposits or roots.
In cases where pipes are heavily obstructed over long distances, water jetting technology proves to be a superior alternative, o ering greater e ciency and less risk than mechanical cutting alone.
Water jetting as an optimal solution
e IBAK MicroGator GT Lite demonstrates the power of controlled ultra-high-pressure water jetting technology in solving complex pipe blockage issues. By o ering a noninvasive, economical, and highly e cient method of removing rock-hard mineral deposits and root masses, the GT Lite represents a signi cant advancement in pipeline maintenance technology. With its precise control system, integrated observation camera for visual monitoring, and the ability to adapt to various blockage types, this technology is a practical and
reliable supplement to traditional robotic cutting methods. In areas where extensive solid deposits pose a threat to pipeline functionality, ultra-high-pressure water jetting o ers an optimal solution-combining power, precision, and cost-e ectiveness to keep vital infrastructure owing smoothly.
e MicroGator GT will be presented with the UHP application at the AUSJET trade fair at stand number B26.
For more information, visit ibak-australia.com.au
The robot allows for easy switching between detailed cutting and grinding tasks to highpressure blasting.
TDG Environmental elevates operations with SECA’s cutting-edge solutions.
SECA, a leader in underground solutions, continues to push boundaries, providing innovative technologies that rede ne trenchless repair. One such partnership
services across both Australia and New Zealand. Specialising in a comprehensive range of services, including service locating, non-destructive digging (hydro-excavation),
cutter to a high-pressure water (HPW) cutter, providing TDG’s operators with unmatched versatility. e robot allows for easy switching between detailed cutting and grinding tasks to high-pressure blasting, making it a powerful tool for removing stubborn materials such as concrete and grout from pipelines. is exibility is invaluable on the job site, where quick adaptations to changing conditions can make the di erence between project success and delays.
TDG has experienced rsthand how the robot’s production rates far exceed those of traditional cutting and grinding robots, making it the ideal tool for many challenging tasks.
One recent project in Brisbane’s Central Business District showcased the e ectiveness of the Sewer Robotics HPW Robot. TDG was tasked with removing cementitious material that had accidentally entered a pipeline, posing a signi cant challenge for the customer.
anks to the HPW module, TDG swiftly cleared the material, delivering cost savings and ensuring the project was completed on time.
TDG’s ongoing collaboration with SECA has been signi cant in the company’s expansion and success across Australia and New Zealand. As TDG underwent a national rebranding and expanded to 25-plus locations, SECA provided essential support, including training on new technologies like the Sewer Robotics HPW Robot. “ e support and training provided by SECA have been invaluable, especially during our expansion. eir expertise has enabled us to o er even more comprehensive trenchless services to our clients,” a TDG representative explained.
Looking ahead, TDG is excited to continue working with SECA as they explore new
ways to maintain and rehabilitate aging pipe networks. With teams already operational in Queensland, New South Wales, Victoria, South Australia, and New Zealand, TDG plans to leverage their partnership with SECA to bring advanced solutions to even more challenging projects across the region.
TDG’s commitment to innovation, combined with SECA’s state-of-the-art technology, is driving the future of trenchless repair. As infrastructure continues to age, maintaining the integrity of underground systems will be essential, and the combined expertise of SECA and TDG will play a pivotal role in safeguarding the environment and ensuring long-term operational success.
For more information, contact SECA’s National Trenchless BDM Brendan Howarth at brendan. howarth@seca.com.au or TDGs General Manager Business Development
Jesse Brown on 0423 854 692
Smart Lock products have played a key role in pipeline repair works in west Sydney.
As Australia’s pipeline network grows, many of these assets, old and new, are in need of repair or maintenance. Sometimes, this can mean tearing out and replacing the pipeline altogether, but this is costly and, in residential or commercial areas, is a signi cant logistical challenge.
at’s why more asset owners are turning to pipeline rehabilitation as an alternative, restoring these critical assets to service for decades to come.
Scan the QR code to find out more.
When ageing water mains in the heart of Melbourne needed attention, new ways of working were needed to deliver a low-impact, cost-effective renewal.
Along South Yarra’s busy Chapel Street ran two cast iron cement lined water mains dating back to the early 1920s. A burst on one of the mains put it in a highrisk category and it was agged for renewal.
Delivery partner Inter ow was engaged by South East Water to renew both mains to ensure certainty of supply for their customers into the future.
What followed was an award-winning project that demonstrates what can be achieved for our communities and our networks when the status quo is challenged.
South Yarra is vibrant inner-city suburb of Melbourne, south-east of the city’s main business district.
e area surrounding the work zones has seen extensive development in recent years. e street is a mix of shops, cafés and businesses at street level, with apartment buildings towering overhead.
On paper this was a straightforward project. Both mains could be renewed by digging them up and replacing them, working at night to reduce the impact on tra c.
Inter ow and South East Water understood that the real marker of success was the impact works had on the 12,000 people and businesses that rely on Chapel Street’s water mains for their supply.
At the time of tender, Inter ow submitted an alternate proposal designed to leverage the bene ts of trenchless renewal technologies to reduce the impact of the renewal works on residents and the business community.
e two organisations collaborated closely during the project to ensure any proposed solutions balanced community and network needs.
“Our goal is always to deliver a better, more sustainable water network for our customers and community, while minimising disruption,” Matthew Snell, General Manager Liveable Water Solutions said.
“ rough our partnership with Inter ow we were able nd new, innovative ways to safely deliver this important project and provide ongoing reliability for the South Yarra community and business owners.”
While there are many examples of proactive problem solving during the Chapel Street renewal project, two were key to delivering exceptional customer outcomes.
Enabling a trenchless approach
e west-side 100mm main was to be renewed with a 150mm pipe (to meet growth demands) and the 300mm east-side main with a like-forlike size.
Inter ow identi ed an opportunity to renew the larger eastern water main using a low impact trenchless approach. e challenge: the cast iron pipe had been lined with cement in the late 1970s, reducing its diameter such that preferred methods like slip lining weren’t practical.
“ ere just wouldn’t have been enough capacity to support the network,” Inter ow Project Manager Reece Paulzen said.
“But if we could gure out a way to remove the cement liner, then slip lining would become a viable option.”
e inspiration for a bespoke cement liner removal process came from a di erent part of Inter ow’s operations.
“High-pressure water jetting is a normal part of our wastewater services,” Paulzen said.
“It’s used to clear signi cant blockages in sewer pipes, like tree roots, or to grind down junctions that will get in the way of lining.
“We understood that in theory it should be possible to break down a cement liner in a water pipe too.”
With South East Water’s support, Inter ow
began trials in its Scoresby yard. e delivery team used some cast iron cement lined pipe removed on another project to test its idea.
What resulted was a process that used ultrahigh-pressure water (up to 15,000psi) and custom cleaning heads to pulverise the cement liner. e cement, along with the water, was ushed through removed using a hydro truck. Afterwards, all 485m of the eastern water main was slip lined with a 280mm (outer diameter) HDPE water pipe.
A revolutionary working window Chapel Street is a four-lane road with trams operating in both directions and a clearway during peak times. 20,000 vehicles use it daily.
Nightworks are e ective for managing tra c impacts, however in this case the e ect of noise on residents was a greater concern.
e delivery team realised that by challenging the norm, they could reduce the chance of community fatigue brought on by long project timelines and disruptive works.
Working with the Department of Transport, the team secured a 7am to 10pm working window with permission to occupy the clearway with a site compound outside these times. e process was uncharted territory for both Inter ow and South East Water and took six months to obtain. e permit eliminated almost all nightworks and allowed two back-to-back shifts each workday, which were bene cial to both the community and
the construction program. Signi cant time was saved by avoiding the need to establish and demobilise the site at every shift.
A long-term collaborative relationship between Inter ow and South East Water was the foundation for success on Chapel Street. By putting community needs rst and actively problem solving, the desired outcomes were achieved with minimal impact.
“ e Chapel Street renewal project has mitigated the risk presented by an ageing asset,” Snell said.
“Now that the project is complete, our customers can be con dent that their community will bene t from reliable,
high-quality water infrastructure well into the future.”
Innovation brings bene ts beyond the problem they are created to solve. For asset owners across the country, the project shows that trenchless solutions can be designed for the most challenging conditions.
Investing upfront in developing these solutions saved South East Water time and money. However, on Chapel Street, it was the community that came out on top.
“We’re all about improving lives,” Paulzen said. “Knowing we made people’s lives easier while we were working, that’s the real win.”
T: (03) 9863 9530 or 0416087254
Email: info@adeptcivilgroup.com quentin@adeptcivilgroup.com www.adeptcivilgroup.com.au
A complex infrastructure project requiring meticulous services at the Port of Melbourne was no problem for civil and drainage specialists M. Tucker & Sons.
Port of Melbourne is Australia’s largest capital city container and general cargo port, handling more than one-third of the nation’s container trade.
Located in the heart of Melbourne, among growing communities, vital industrial precincts and transport corridors, the port operates 24 hours a day, 365 days a year.
Recently, civil infrastructure company BildGroup commissioned M. Tucker to undertake a project involving the cleaning, inspection, and modi cation of a DN600mm drain at Swanson Dock, within Port of Melbourne.
e project kicked o with the mobilisation of M. Tucker’s expert drain cleaning crew to Swanson Dock.
Utilising a KOR Cappellotto high-pressure water jetting system, the team meticulously cleaned the DN600mm drain. is initial phase was crucial in ensuring that all debris and obstructions were removed, facilitating a clear passage for subsequent inspections.
Following the thorough cleaning, a CCTV inspection was conducted using the state-ofthe-art iPEK Rovion CCTV sewer camera from SECA, which allowed the team to identify any structural defects, blockages, or areas of concern.
e detailed assessment was instrumental in understanding the precise state of the infrastructure.
Following this, the M. Tucker team used a KRE robotic cutter, equipped with a
grinding disk, to remove intruding materials from the pipe.
One of the pivotal aspects of the project was the decision to divert the pipe around the defect. is required non-destructive digging (NDD) to ensure this was done safely and e ectively.
Under the directions from BildGroup, M. Tucker’s NDD team mobilised, where they performed vacuum excavation.
is method allowed them to expose the pipe without causing damage, ensuring that the integrity of the surrounding infrastructure was maintained.
NDD operations were carried out with a stringent adherence to safety and compliance standards. e company coordinated closely with Bild Group to secure all necessary permits and approvals.
is meticulous approach ensured that all activities were conducted in accordance with local regulations, safeguarding both the workers and the environment.
While methods such as NDD are e cient alternatives to mechanical excavation, the resultant waste products are a top priority when considering waste management practices.
With its slurry bins, environmental responsibility is a cornerstone of M Tucker’s operations.
During the NDD activities across the project, Category C waste was generated, necessitating careful handling and disposal.
M. Tucker collected all such waste and transported it to their designated waste slurry bins on-site. is process was conducted in strict compliance with environmental regulations and guidelines, ensuring that no harm was done to the surrounding ecosystem.
e nal step in the waste management process involved the use of M. Tucker’s hook lift truck to dispose of the waste at an EPAlicensed facility.
e process is completed through the company’s EPA licenced waste disposal facility based at M. Tucker’s headquarters in Mount Evelyn, east of Melbourne.
e facility includes a washing and sizing plant that allows sand and aggregate to be recycled from the waste, which can then be repurposed into other products such as concrete.
e environmentally friendly concrete is made up from 70 per cent reclaimed materials in 2532mpa paving mix.
e use of recycled sand and aggregate reduces
the need for traditional quarry materials, which are becoming increasingly constrained due to high demand and depletion of natural resources.
e reuse of these materials also helps to reduce the carbon footprint and closes the recycling loop.
is not only showcased the company’s commitment to the environment, but also highlighted the seamless integration of its services – from inspection, to cleaning and nally, waste disposal.
e completion of this project stands as a testament to M. Tucker’s expertise, versatility and dedication.
e company’s use of advanced technologies, such as high-pressure water jetting, CCTV inspection, and robotic cutters, along with its adherence to safety and environmental standards, ensured the e cient and safe execution of the project.
e decision to redirect pipe around the found defect, facilitated by M. Tucker’s NDD services, showcases the synergy between innovative solutions and safe, practical outcomes.
When it comes to complex civil projects, M. Tucker continues to set a high standard with its versatile services across all aspects of drainage maintenance and renewal.
For more information, visit mtuckerandsons.com
Like to know more?
The Sydney Metro West project has achieved a slew of tunnelling milestones in recent months.
The Sydney Metro West project is a new 24km underground metro railway set to double rail capacity between Parramatta and the Sydney CBD, strengthening the city’s infrastructure for generations to come. is signi cant infrastructure investment will provide fast, reliable metro services with fully accessible stations, link new communities to rail services and support employment growth and housing supply.
e project is expected to create about 10,000 direct and 70,000 indirect jobs during construction.
Stations have been con rmed at Westmead, Parramatta, Sydney Olympic Park, North Strath eld, Burwood North, Five Dock, e Bays, Pyrmont and Hunter Street in the Sydney CBD.
Two potential station locations are being investigated west of Sydney Olympic Park, including one at Rosehill Gardens which could support a signi cant increase in housing.
e project employed two autonomous mega tunnel boring machines (TBMs), the rst of their kind ever used in Australia, to carry out tunnelling works.
e TBMs are installed with arti cial intelligence software, which has the capability
to automatically steer, operate and monitor the machine.
Tunnelling roughly 180m per week, the 1200-tonne machines spent 10 months completing the 4.6km tunnels from Clyde to reach Sydney Olympic Park.
TBM Betty, named after Olympic champion Betty Cuthbert, was rst to arrive at Sydney Olympic Park in June and was followed by TBM Dorothy, named after human rights activist Dorothy BucklandFuller, on 29 July.
TBMs Betty and Dorothy excavated approximately 857,500 tonnes of material, to complete the rst leg in the journey and have installed more than 32,600 concrete precast segments to line the new tunnel walls.
In the coming months, the TBMs will be disassembled, lifted out of the station box and transported on trucks back to Clyde, where they will be relaunched in the opposite direction towards Westmead.
Both TBMs are expected to arrive at Westmead in mid-2025.
e focus at Sydney Olympic Park will now shift to the opposite end of the 200m-long, 37m-wide, and 27m-deep station box. Here, two more TMBs, named Beatrice and
Daphne, are currently digging their way through an 11km section between e Bays and Sydney Olympic Park.
e project’s newest addition, TBM Jessie is tunnelling from e Bays towards the Sydney CBD. is machine has excavated 230m of tunnel since its launch in May.
e nal TBM for the project is expected to begin the second under-harbour tunnel later this year.
“We have welcomed the world’s fastest athletes and biggest rockstars to Sydney Olympic Park, and now it is time Metro West’s superstar TBMs to headline here in Sydney’s west,” NSW Minister for Transport Jo Haylen said.
“Sydney’s brand-new rail line will give sports and entertainment fans unrivalled access to this part of town and signi cantly enhance transport options during major events.
“Metro West’s TBMs are digging dual tunnels as part of our government’s $19 billion investment in extending Metro across Sydney and continuing the state’s infrastructure pipeline.”
Sydney Metro West is targeting an opening date of 2032.
The Australasian Society for Trenchless Technology is a non-profit organisation. Corporate or individual membership is open to all who are concerned with the provision of gas, water, sewage, drainage, telecommunications and electrical services.
Corporate and Individual Memberships are available and benefits include:
• Annual subscription to Trenchless Australasia magazine and the Australasian Trenchless Directory
• Discount rates at national conferences and exhibitions, and ISTT International No-Dig exhibitions
• A communication network to keep abreast of the advancement of the science and practices of Trenchless Technology throughout the world.
No-Dig Down Under is the Southern Hemisphere’s only large-scale conference and exhibition dedicated to trenchless technology. The exciting event returns in 2025.
Organised in partnership with the Australasian Society for Trenchless Technology (ASTT), No-Dig Down Under has grown over the years to become the second-largest no-dig technology event in the world and is now considered a ‘must-attend’ for all industry professionals.
Sustainability and innovation are the themes of this year’s event, two principles exempli ed by gold sponsor Pipe Core.
“As a gold sponsor, it’s imperative for us to connect with customers and our industry,” Pipe Core Chief Executive O cer Jason Marshall said.
“Our customers range from plumbers and drainers, lining contractors, infrastructure specialists and asset owners.
“No-Dig Down Under allows us to share what we’re doing and the innovation we are bringing to the industry. Technology constantly changes, so No-Dig Down Under is an e cient way to connect and communicate with the market.”
Founded in 2008, Pipe Core has witnessed and been part of this technological transformation.
Trenchless technology was once considered a novelty in the water and pipeline industry, or at least that was the case when Marshall rst entered the market over 20 years ago.
“Trenchless techniques were very early in their life cycle but are now mainstream options for infrastructure renewal,” he said.
“ e evolution towards ultra-violet (UV) technologies is the biggest change I’ve seen, and one of the reasons Pipe Core is investing in its product o ering to support the industry’s move towards this technology.” is shift highlights innovation within the water and pipeline industries.
Many installers have pivoted their onsite delivery processes to pass on e ciency gains and quality improvements to their end customers.
“One of these e ciency gains is seen through access to pre-manufactured materials for UV relining installation. e move away from onsite liner preparation has gone a long way to helping operators achieve consistent high-quality results and reduce time on-site,” Marshall said.
“We’re also seeing a lot more CCTV inspection technology and robotics in the industry. Arti cial intelligence (AI) and the Internet of ings (IoT) are also an important part of the trenchless future.”
One highlight of No-Dig Down Under will be numerous exhibitors discussing their sustainability practices. Pipe Core will support these initiatives by showcasing its partnerships with companies independently adopting sustainable practices.
Pipe Core’s many suppliers align with key sustainability themes, such as eliminating single-use plastics, energy consumption, carbon reduction, and social impact, which
contribute signi cantly to environmental and social responsibility.
“Trenchless technology is an inherently sustainable renewal option,” Marshall said.
“We’ve worked closely with our suppliers to ensure best practices in all areas, especially with manufacturers like SAERTEX multiCom GmbH, who o er products with a technical service life of 100 years.”
No-Dig Down Under has an exciting technical program lined up, inviting speakers from around Australia and the globe to present papers covering case studies, new and emerging technologies, challenging projects and environments, industry skills and training, risk management and more.
Fortunately for attendees, continuing professional development hours can be claimed for attending this conference through Engineers Australia. e training courses and technical program are supported by an exhibition hall extending over 4500 square metres, featuring exhibitors from all sectors of the industry. ree sponsored social functions will be held, including the prestigious ASTT Gala Dinner and Awards Evening, providing attendees with networking opportunities in a variety of settings with industry professionals.
For more information, visit nodigdownunder.com
Showcase your solutions to the region’s best database of trenchless decision makers and industry experts through the weekly Trenchless Australasia e-newsletter.
Sent directly into the inboxes of 6,000+ trenchless professionals, the Trenchless Australasia e-news connects your brand with one of the world’s largest no-dig databases.
Secure your partnership through this channel and elevate your brand among top industry professionals.
Contact Trenchless Australasia Business
Development Manager Nick Lovering at nick.lovering@primecreative.com.au
Gold Corporate Members
DirectBor Australia
Herrenknecht AG
J&R Contracting Limited
Kellogg Brown & Root
Silver Corporate Members
Aaro Group
Abergeldie Rehabilitation Pty Ltd
ACP Australian Custom Pipes
Adept Drainage Pty Ltd
AECOM New Zealand Limited
AHD Trenchless
Applied Felts
Aqua Assets
AQUATEK Fluid Systems
Atteris Pty Ltd
Aurecon
Ausinland Pty Ltd
Aussie Trenchless Supplies Pty Ltd
Australian Pipeline Management Pty Ltd
Austunnel Pty Ltd
Ballarat Underroad Boring and Excavations Pty Ltd
BG Risk Solutions
Blick Group
Bortec Laser Bore Pty Ltd
BRP Corporation Pty Ltd
Bullseye Boring
CEA
CC Group
CDS New Zealand Ltd
Channeline International
D.J. Mac Cormick Contractors
DCS Manufacturing Pty Ltd
Derby Rubber Products
Digital Control - Australia
Directhitt Trenchless Pty Ltd
Diversified Services Australia
DM Civil
Dormway Pty Ltd
Draintech Solutions
Drillers World Australia
Dunstans
E&CC
Edge Underground
ELB Equipment Pty Ltd
Empire Infrastructure
Fulton Hogan
Fulton Hogan Construction Pty Ltd
Asset Owners
Auckland Council
Barwon Water
Watercare Services Ltd
Michels Trenchless Pty. Ltd.
OptionX Group
Orion Consulting
Rangedale Rehabilitation and Renewals Pty Ltd
Systra Bamser
Future-Proof Solutions
GCE Contractors Pty Ltd
GN Solids Control
Golder
Hard Metals Australia Pty Limited
HDI Lucas
Holcim (Australia) Pty Ltd
Hynds Pipe Systems Ltd
IMPREG (AUSTRALIA) PTY LTD
Independent Sewer Consulting Services Pty Ltd
Insituform
Insituform Pacific Pty Ltd
Interflow Pty Ltd
Iplex Pipelines Australia
JB Trenchless Pty Ltd
kwik-ZIP Spacers
Kynection
L P Pipe Civil
LKL International Pty Ltd
M. Tucker & Sons Pty Ltd
March Cato Ltd
Matamata Directional Drilling
Maxibor Australia Pty Limited
McBerns Innovative Solutions
McConnell Dowell Constructors (Aust) Pty Ltd
McElroy Manufacturing Inc.
McMillen Jacobs Associates (NZ)
Melbourne Water
Metrocorp Technologies
Mudex
Mullane Trenchless Pipeline Solutions Pty Ltd
NEWest Alliance
NordiTube AUS Pty Ltd
Nu Flow Technologies 2000 Pty Ltd
Pezzimenti Laserbore Pty Ltd
Pezzimenti Trenchless Pty Ltd
Pezzimenti Tunnelbore Pty Ltd.
Pipe Core Pty Ltd
Pipe Doctor Australia Pty Ltd
Pipe Technologies Ltd
Greater Western Water
Knox City Council
Bowley Plumbing Services
EnviroPacific- SOLVE
Tunnelling Solutions
Veolia
WSP New Zealand Ltd
Water Corporation
Pipe Tek
Pipeline Drillers Group
Pipe Pro Drilling
PipeWorks
PLUMBLOGIC
Prime Creative Media
Prime Horizontal Pty Ltd
Qalchek Pty Ltd
Qenos Pty Ltd
R & R McClure Excavations
Raedlinger Primus Line Pty Ltd
Ravago NZ Ltd
RBM Plumbing and Drainage Pty Ltd
Ready Group Pty Ltd
Rob Carr Pty Ltd
Rose Atkins Rimmer (Infrastructure) Pty Ltd
RPC Pipe Systems
SA Water
SASTTI Joint Venture
Schauenburg MAB
SEKISUI Rib Loc Australia Pty Ltd
SEQ Trenchless
Sewer Equipment Company (Aust)
SLB-M-I SWACO
Smythe Contractors Limited
STRABAG
Sydney Water
TDG Environmental (NZ)
TDM Pipeline Solutions
TRACTO-TECHNIK Australia Pty Ltd
Trenchless Advisor Pty Ltd
UEA Pty Ltd
Vacvator
Vector Magnetics
Vermeer Australia
Vertical Horizonz Australia
Veolia (NZ)
Vinidex Pty Limited
Warren Smith & Partners
Yarra Valley Water
Zhangzhou Anyue Advanced Materials
Technology Co. Ltd
The Australasian Society of Trenchless Technology (ASTT) is a non-pro t organisation comprising of members throughout Australia and New Zealand.
e successful establishment of the trenchless industry in Australasia has been supported and promoted by the peak industry organisation, the ASTT, since it was established in 1991.
e society works tirelessly to promote the use of trenchless technology in Australasia, lobbying government and client organisations to highlight the advantages of using trenchless technology and the bene ts of training for industry.
Membership is open to all who are concerned with the provision of gas, water, sewerage, drainage, roads, telecommunications and electrical services.
ASTT membership provides trenchless professionals the tools and services they need to be better informed and better connected in this industry.
e ASTT is part of the International Society for Trenchless Technology (ISTT), an a liation of societies in more than 30 countries worldwide.
Membership applications
e ASTT currently o ers seven levels of membership available to all residents of
Australia and New Zealand or anyone who is also a nancial member of an existing ISTT a liated society.
The benefits of Membership depending upon category can include:
Up to 10 people from your organisation may be included in your membership and are entitled to receive the below bene ts:
• Acknowledgment of your company in every edition of the Trenchless Australasia magazine.
• An annual subscription to Trenchless Australasia magazine (six issues per year).
• An annual subscription to ISTT’s Trenchless Works
• A company listing in the Australasian Trenchless Directory (print and digital).
• Opportunity to promote your membership of the association by including the ASTT logo on your business communications and website.
• Access to guidelines and standards.
• Discount rates (normally 10 per cent) at national conferences and exhibitions.
• Discount rates (normally 10 per cent) at international conferences and exhibitions.
• Discount rates (normally 10 per cent) at trenchless forums.
• Opportunity to become involved in our Special Interest Groups which
are technical divisions of the ASTT representing speci c trenchless sectors.
• Special o ers and links with international organisations including the ISTT.
• Opportunity to nominate for ASTT and ISTT awards.
• Free access to ISTT past conference proceedings.
• A communication network to keep abreast of the advancement of the science and practices of trenchless technology throughout the world.
• Discounted rates at international No-Digs and national events including No-Dig Down Under.
Visit the ASTT website on www.astt.com.au and check out the membership bene ts that apply for each category.
Your membership request will be emailed directly to the ASTT for processing. You will receive an invoice based on the information you supply. Acceptance does not take e ect until payment is received in full.
For more information, visit astt.com.au or email secretary@astt.com.au
Trenchless Australasia is tracking new appointments in Australia and New Zealand’s trenchless industries. Read all about the latest people moves.
Lance McDonald has moved into the role of HDD Operations Manager at Boretech Contracting, with a focus on the mining division.
“Boretech Contracting’s primary focus is to install underground infrastructure by way of HDD works,” he said.
“We are expanding further into the mining market, which brings with it challenges like remote worksites, weather and difficult ground conditions.
“With my previous experience, I’ve come on board to help our guys deliver safe and efficient works.”
McDonald, who has worked in the HDD industry since the early 2000s, said he has had dealings with Boretech throughout his career, and so was eager to work together in a more permanent capacity.
“There is a lot to look forward to in this role: the challenges of running remote jobs, bringing my own style of leadership to the group, assisting with the growth of others within this organisation, and having some good laughs along the way.”
Joe Callaghan has started a new position at Melbourne Water as Project Manager –High Risk.
Callaghan is an experienced construction management professional with experience providing complete leadership and support within project management teams.
Prior to joining Melbourne Water, Callaghan worked at Service Steam in various roles including Project Construction Supervisor, Construction Coordinator and Project Assistant. He also worked at construction, maintenance and drainage company Rangedale as Project Manager before he moved onto asset maintenance specialist TDG Environmental, where he worked as Project Manager for over one year.
Tony Wilson has joined Vacuum Truck Supplies as a Sales Representative. Since 1998, Vacuum Truck Supplies (VTS) has been a leader in quality, design and engineering of vacuum tankers. The company deals exclusively in vacuum trucks, trailers and portables and also stocks and supply vacuum pumps and components for the liquid waste, mining and hydro-excavation industries. Wilson is an experienced Transport Manager with a demonstrated history of working in the environmental services industry.
Previously, he worked as a Transport Manager for over 26 years at Worth Recycling before joining Toxfree as an Equipment Manager.
He then worked at KOR for three years as a Business Development Manager for NSW and the ACT. His next role was at Pipe Management Australia as National Fleet and Equipment Manager before moving into his new role at VTS.
If your company has recently employed a new person within your business you would like profiled in ‘People on the move’, send details of the career news alongside a high-res photo to Managing Editor Molly Hancock at molly.hancock@primecreative.com.au
ALL TORQUE - IN THE BEST KIND OF WAY.
The the D23x30 S3 Navigator®️ horizontal directional drill is one of the quietest drills on the HDD market. With a 100 hp (74.6 kW) Tier 4 Final or Tier 3 (EU Stage IIIA) engine optional, the D23x30 S3 offers speed and power in a short, narrow footprint to help increase productivity when working in compact urban or commercial job sites. Get in touch with your local HDD specialists today.