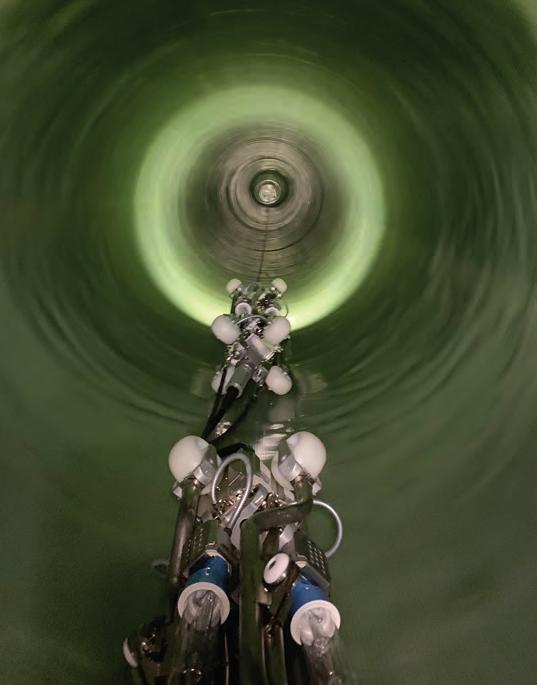
2 minute read
IMPREG prepares for the future of CIPP
As a company that makes the impossible possible, IMPREG develops and produces cured-in-place pipe (CIPP) liner systems using a high-tech process for trenchless pipes and sewer rehabilitation.
With its future-oriented CIPP liners based on fibreglass material, IMPREG masters even the largest dimensions and highly complex remits.
Ensuring maximum quality at all times, general manager Michael Ellenrieder says it is thanks to its innovative products and insight.
“Our activities are always resource-saving and environmentally conscious. Our success proves us right. IMPREG CIPP liner systems for UV curing are used all over the world,” he says.
“We are a reliable solution partners at all times, and commit ourselves to the highest future-proofed quality and to environmentally conscious conduct.”
The IMPREG liner was developed for all common pipes from DN150 up to DN2000. As a result of quality materials and a new fibreglass design, the IMPREG liner can produce more finely nuanced gradations of wall thickness.
The Australian outlet is currently stocking sizes from DN150-DN600. Ellenrieder says local customers can receive their order within 3-5 business days and also benefit from IMPREG’s on-site technical support for installation.
“Efficient, future-proof, and environmentally friendly, IMPREG’s innovative CIPP liners and pipe rehabilitation solutions ensure a reliable and sustaining working life for all pipelines,” he says.
As one of the world’s leading manufacturers of high-tech CIPP Liner systems for UV-curing, IMPREG has made a decisive contribution to trenchless pipe rehabilitation technology for over 40 years.
Ellenrieder says as part of its proven track-record, the company was awarded the tender for rehabilitation of sewer mains by in-situ relining works by a regional NSW council.
IMPREG’s valued client in regional NSW secured the contract following the council seeking tender submissions from suitably qualified and experienced contractors.
The works to be executed under this contract consist of all work associated with the pipe cleaning, CCTV inspection, design, manufacture, supply, delivery to site, installation, and testing of an acceptable sewer liner to the sewer mains as specified in the asset index and plans.
Outlined in the tender, the conduits to be rehabilitated are predominantly DN150 gravity mains with potential for some DN225 and DN300 gravity mains.
As part of the contract, IMPREG will rehabilitate 8 km of DN and 1 km of DN.
Ellenrieder says the the project also involves a large civil component including installation of new manholes and digging up unrepairable sections of pipe.
Since its foundation in 1999, IMPREG has employed innovative technology and pioneering ideas.
In the recent history, it has made the company synonymous with advanced technology in modern sewer rehabilitation. IMPREG now stands for quality and service throughout the world.
In addition, Ellenrieder says to guarantee the quality of its trenchless CIPP fiberglass liners during their journey from its Virginia plant to the project, the company builds shipping containers for every project.
“Making our crates ensures consistent quality, protects liners from the elements, shields from harmful UV-rays, and helps us keep costs down by not involving a third party crate company,” he says.
The IMPREG liner was developed for all common pipes from DN150 up to DN2000. For more information visit www.impreg.de/en/
