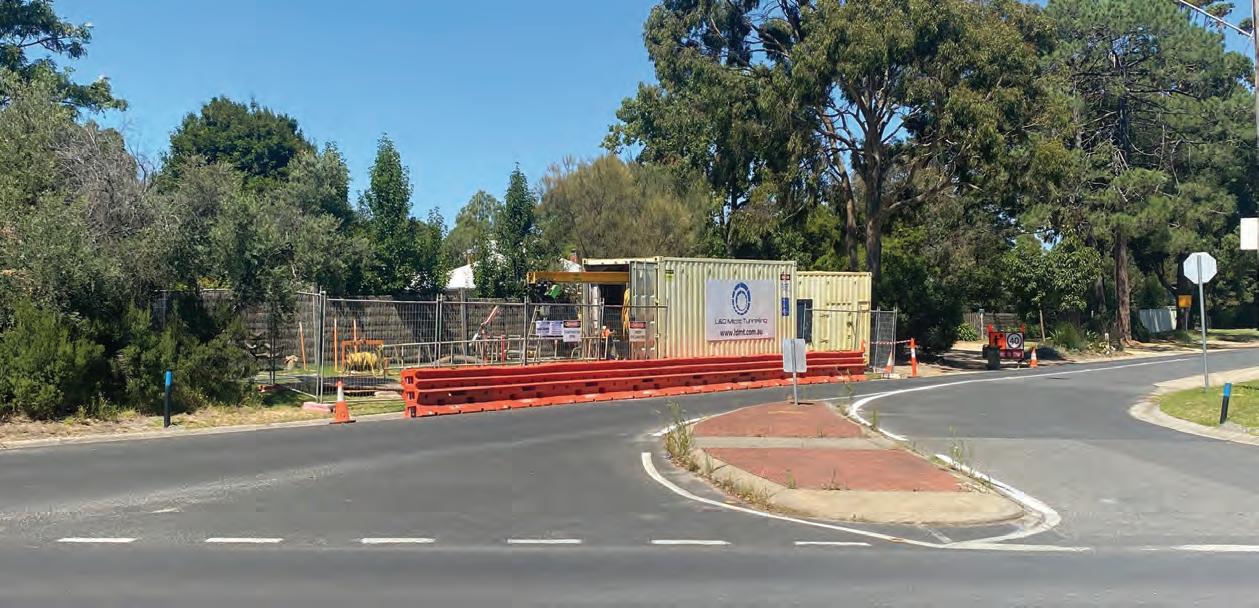
2 minute read
Masters in micro tunnelling deliver peninsula project amid trying times
L&D on Mt Martha Sewer Duplication project.
Masters in microtunnelling deliver peninsula project amid trying times
In the midst of COVID-19, L&D Micro Tunnelling was contracted to bore a length of 900 m for the Mt Martha Sewer Duplication to provide security for the region through seasonal spikes in sewage inflow.
L&D Micro Tunnelling was established in 2015 by business partners Luke Lewis and Christopher Dean. The pair have worked together since 2011, when they were both working for R&C Davies Constructions as construction manager and head of microtunnelling operations respectively.
Combined, the pair have 20 years’ experience in the sewer and water industry, and both understand the need for precision and thoroughness in their line of work.
Today, their company offers a range of services including sleeve boring, free boring, pipe jacking and pilot auger boring, as well as specialist machine hire. Lewis and Dean specialise in high-accuracy laser guided boring, and the company also has three tunnel boring machines (TBMs) operating throughout Victoria with drill heads ranging from DN350 to 600 mm.
L&D was recently awarded a drilling contract to carry out 900 m of tunnelling for the Mt Martha Sewer Duplication in Victoria by client Fulton Hogan, Delplant and Beca (FHDB). In November 2018, the Council of Mornington Peninsula Shire introduced its Wastewater Management Plan 2018-2023 to address the environmental and public health risks posed by residential and commercial wastewater.
The council invested millions into wastewater infrastructure projects to support population growth and protect assets through seasonal spikes in sewage inflows. Works on the Mt Martha Sewer Duplication commenced in January 2021, and the company used a free boring method to bore through sandy clay and rocky ground conditions to depths of 2 - 7 m.
The purpose of the duplication was to relieve the existing sewer, which was under pressure from the demands of the expanding local population. Free boring was decided as the preferred method of boring because the clay ground profile was self-supporting, meaning it wouldn’t require more delicate methods of tunnelling.
While boring was mostly seamless, the deeper sections of the dig at around 7 m posed the greatest challenges, where reefy rock conditions plagued the earth.
The project took around four months to complete and was L&D’s third project for the Fulton Hogan joint venture - testament to the company’s tried and tested methods.
L&D installed 280 HDPE & 376mm HOBAS GRP jacking pipe. The Poly line was welded into full strings along the length of each bore. Once the team had broken through with the drill head, the contractors extracted the head from the retrieval shaft and attached a pull-back tool to install the pipe as they retracted their rods. Centralising clips were installed every metre on the pipe to create an annulus so the pipe could be grout-filled in place after installation.
Cofounder Chris Dean said he was proud of his company’s ability to deliver the project on time and without complication, despite operating under COVID conditions.
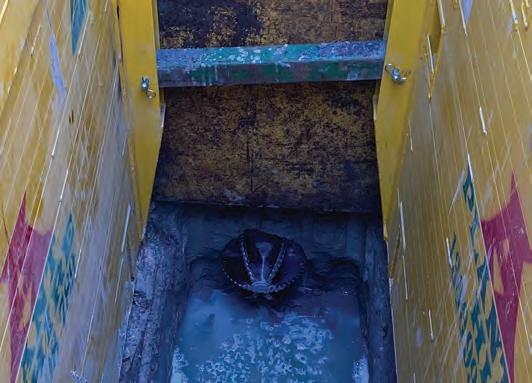
L&D used a free-boring method as ground conditions were self supporting. For more information visit www.ldmt.com.au