Down Under
Primus Line celebrates 10 years in Australia

A cutting-edge revolution | More than just technical training | Celebrating 35 years | Making global strides in trenchless technology

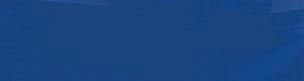
“Proactive trenchless renewals are one of the keys to defending our critical water and wastewater services in a sustainable and costeffective way”
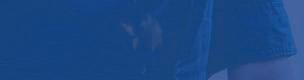
– Will Zillmann, Interflow
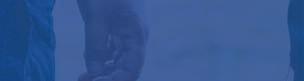

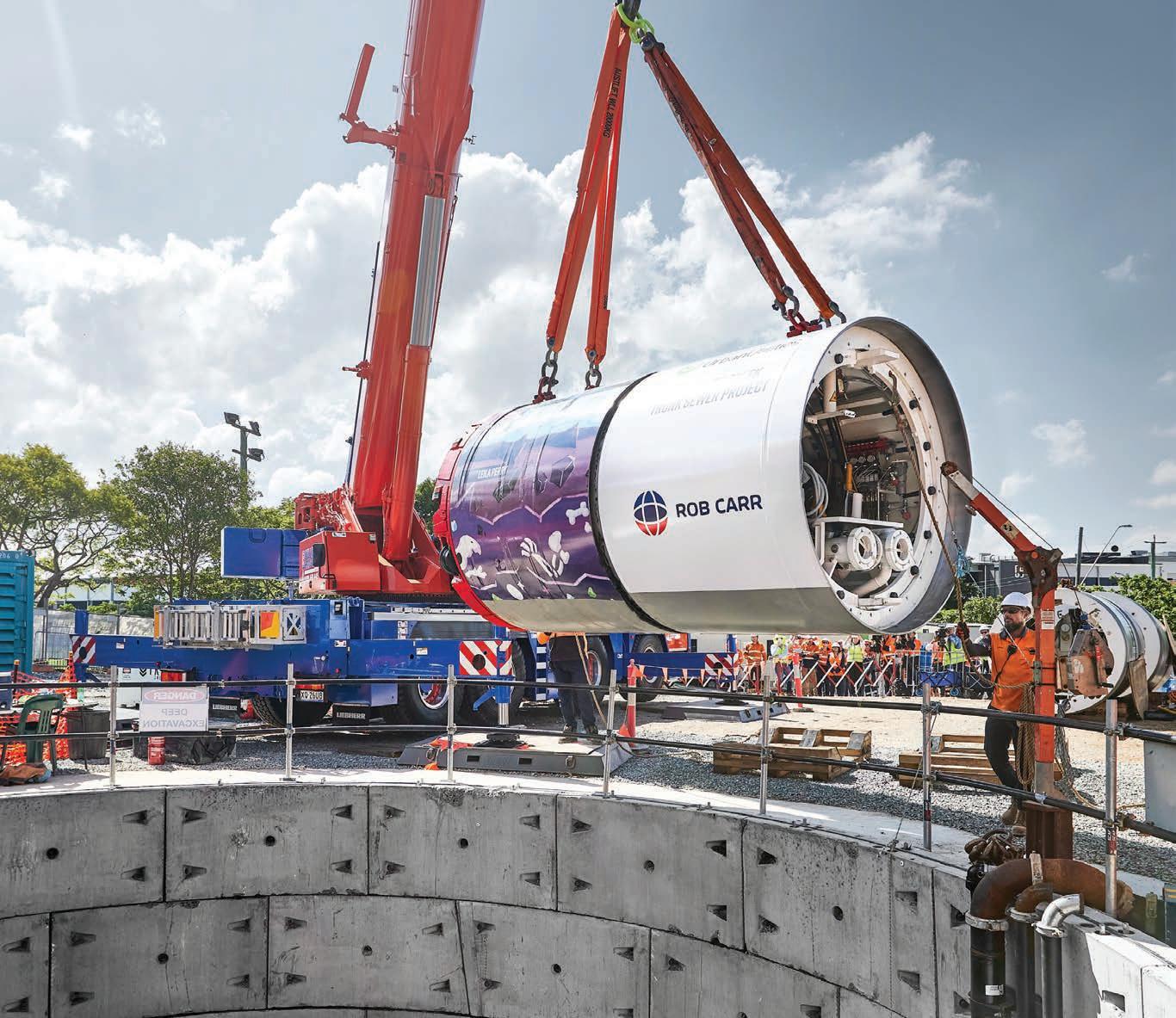
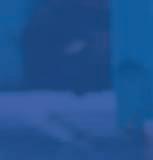
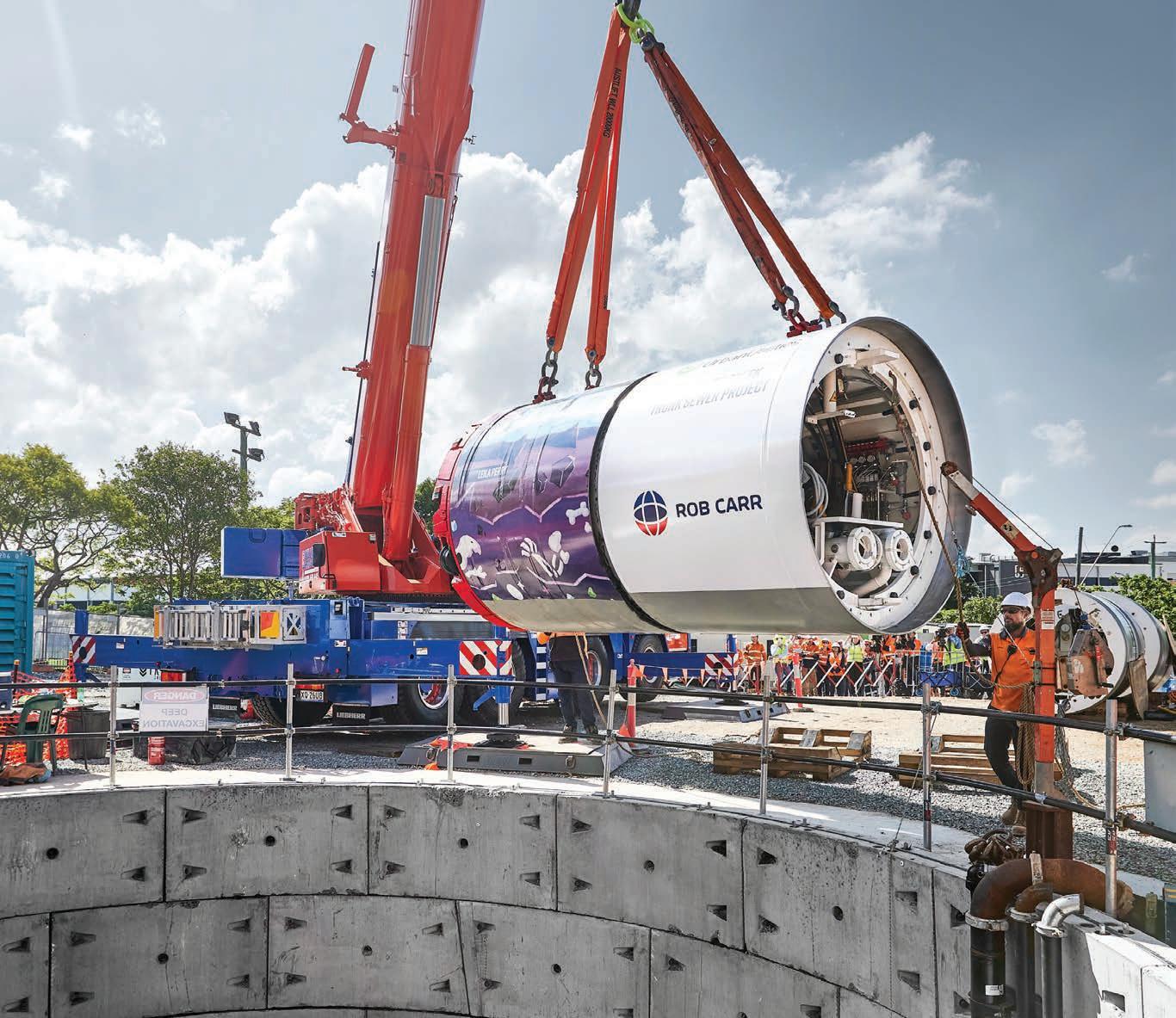

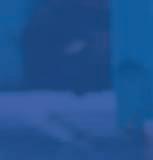
Excellence in tunneling for water, wastewater and energy infrastructure.
With a focus on safety, innovation and collaborative delivery over the last 35 years, Rob Carr has achieved outstanding outcomes in water, wastewater and energy infrastructure projects in both Australia and overseas. Rob Carr is part of Soletanche Bachy a world leader in foundation and soil technologies and subsidiary of VINCI, a global player in construction across more than 100 countries. With outstanding capabilities to manage the complexities of any project, Rob Carr has the people, knowledge and experience to deliver success.


This magazine is the official journal of the Australasian Society for Trenchless Technology (ASTT) and is distributed to members and other interested parties throughout Australia and the AsiaPacific. It is also available on subscription.
The publishers welcome editorial contributions from interested parties. However, neither the publishers nor the ASTT accept responsibility for the content of these contributions and the views contained therein are not necessarily the views of the publishers or the ASTT. Neither the publishers nor the ASTT accept responsibility for any claims made by advertisers. All communications should be directed to the publishers.
Unless explicitly stated otherwise in writing, by providing editorial material to Prime Creative Media (PCM), including text and images, you are providing permission for that material to be subsequently used by PCM, whole or in part, edited or unchanged, alone or in combination with other material in any publication or format in print or online or howsoever distributed, whether produced by PCM and its agents and associates or another party to whom PCM has provided permission.


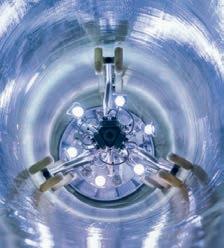
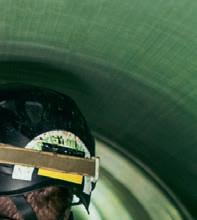
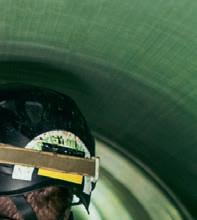
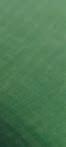
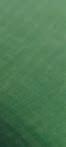

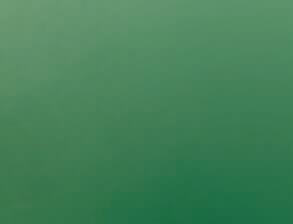

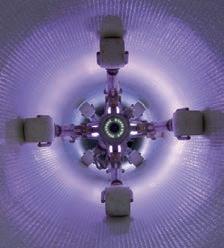

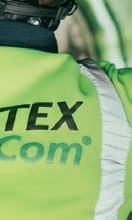

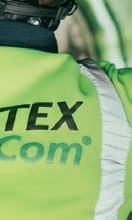
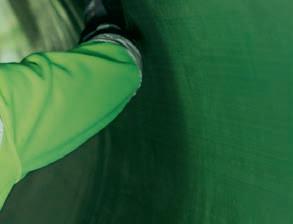

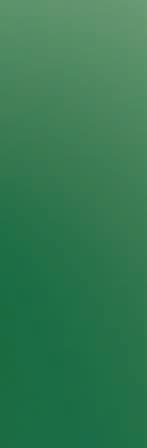
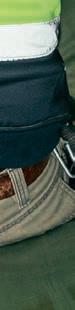
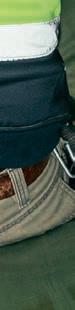
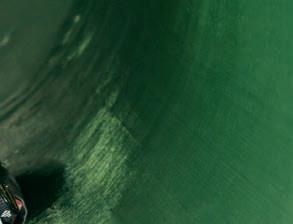
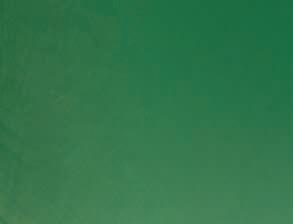
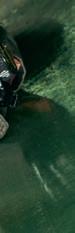
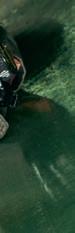


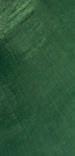
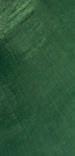
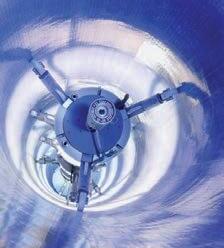






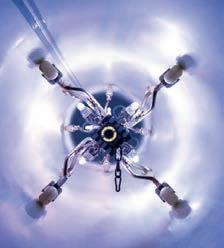
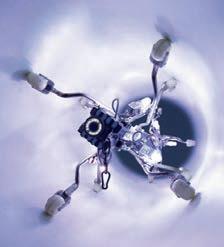
CEO
John Murphy
CHIEF OPERATING OFFICER
Christine Clancy christine.clancy@primecreative.com.au
MANAGING EDITOR
Molly Hancock molly.hancock@primecreative.com.au
EDITORIAL
Tim Bond tim.bond@primecreative.com.au
Darragh Bermingham darragh.bermingham@primecreative.com.au
BUSINESS DEVELOPMENT
Nick Lovering nick.lovering@primecreative.com.au
HEAD OF DESIGN
Blake Storey blake.storey@primecreative.com.au
DESIGNER
Blake Storey
COPYRIGHT
Trenchless Australasia is owned by Prime Creative Media and published by John Murphy. All material in Trenchless Australasia is copyright and no part may be reproduced or copied in any form or by any means (graphic, electronic or mechanical including information and retrieval systems) without written permission of the publisher.
The Editor welcomes contributions but reserves the right to accept or reject any material. While every effort has been made to ensure the accuracy of information, Prime Creative Media will not accept responsibility for errors or omissions or for any consequences arising from reliance on information published. The opinions expressed in Trenchless Australasia are not necessarily the opinions of, or endorsed by the publisher unless otherwise stated.
© Copyright Prime Creative Media, 2021
ARTICLES
All articles submitted for publication become the property of the publisher. The Editor reserves the right to adjust any article to conform with the magazine format.
Head Office
379 Docklands Dr, Docklands VIC 3008 Ph: +61 3 9690 8766 enquiries@primecreative.com.au www.primecreative.com.au
Sydney Office Suite 11.01, Level 11, 201 Miller St, NorthSydney, 2060
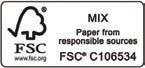
Editor’s letter
Molly Hancock
Welcome to the last edition of Trenchless Australasia for 2024. As Australia continues to grow and evolve, so too does the need for sustainable, efficient, and innovative solutions to infrastructure challenges. One such solution that has proven to be transformative in reducing environmental impact, cost, and disruption is trenchless technology. This cutting-edge approach to installing and maintaining underground infrastructure is revolutionising how we think about everything from water and sewer systems to communication networks and gas pipelines.
However, as the demand for trenchless technology expands, so does the need for a skilled workforce capable of handling its complexities. This is where training and education play a pivotal role. As an industry, we must not only adopt new technologies but also ensure that the workforce is adequately prepared to deploy and maintain them with the highest standards of safety and efficiency.
In Australia, we are fortunate to see an increasing emphasis on trenchless technology training programs, designed to meet the unique demands of our landscape and regulatory environment. From specialised courses offered by universities to the ASTT’s programs, these educational
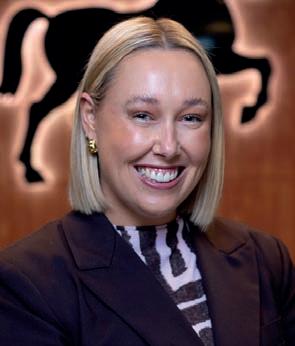
initiatives are bridging the skills gap and preparing the next generation of technicians, engineers, and project managers.
Importantly, trenchless technology is not just about innovation; it’s about sustainability. By minimising the need for open excavation, this technology helps preserve our natural environment, reduces road closures, and limits the impact on local communities.
In this issue, we take a closer look at the state of trenchless technology education in Australia, highlighting the initiatives, partnerships, and success stories that are helping shape the future of the industry. Whether you’re just starting out in your career or looking to expand your expertise, this issue provides valuable insights into how education and training are paving the way for a more efficient, sustainable future in trenchless technology.
The team from Trenchless Australasia thank you for your support during 2024 and wish everyone a happy and safe Christmas and New Year. We look forward to joining you again in 2025.
Happy reading!
Molly Hancock Managing Editor molly.hancock@primecreative.com.au
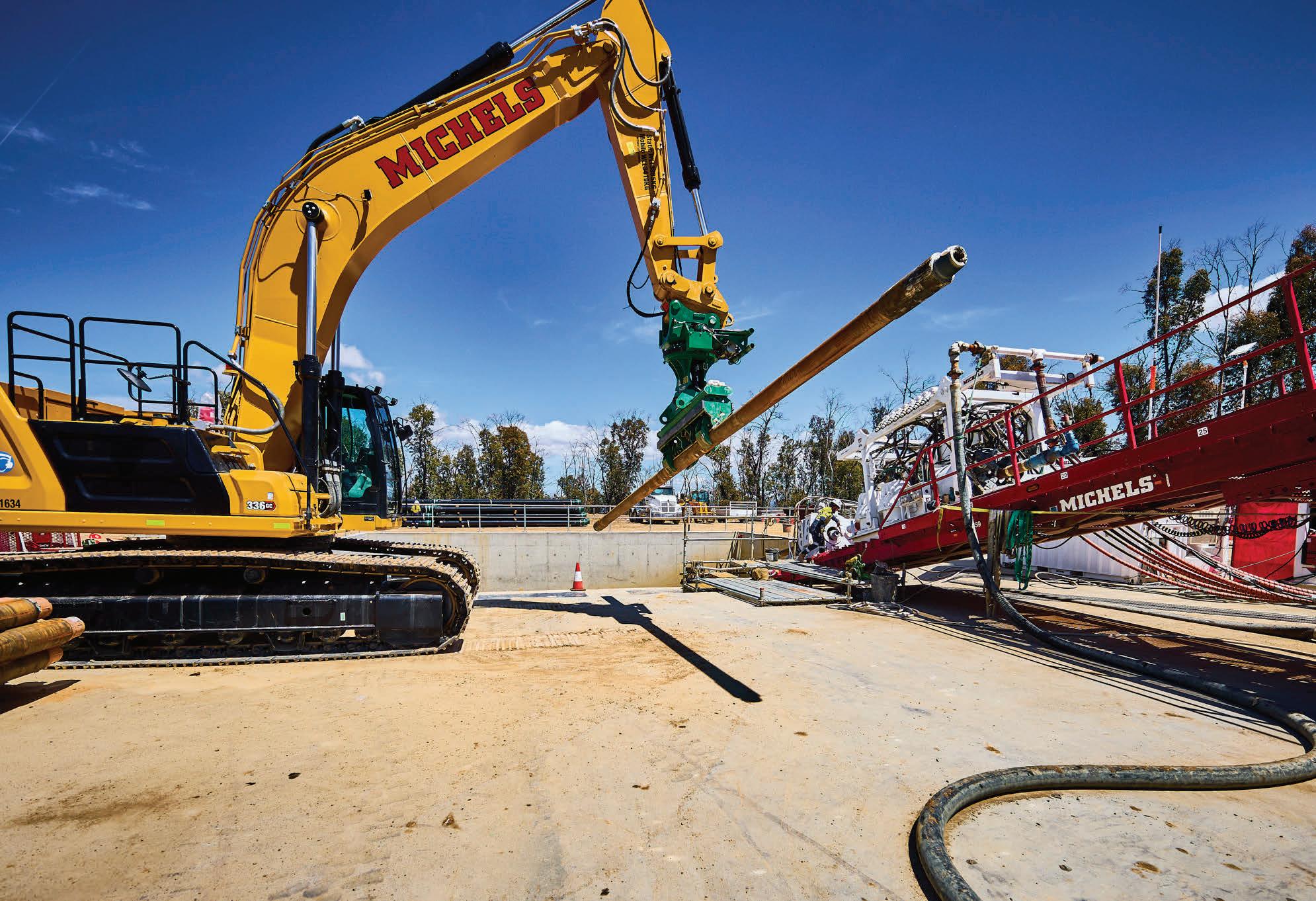
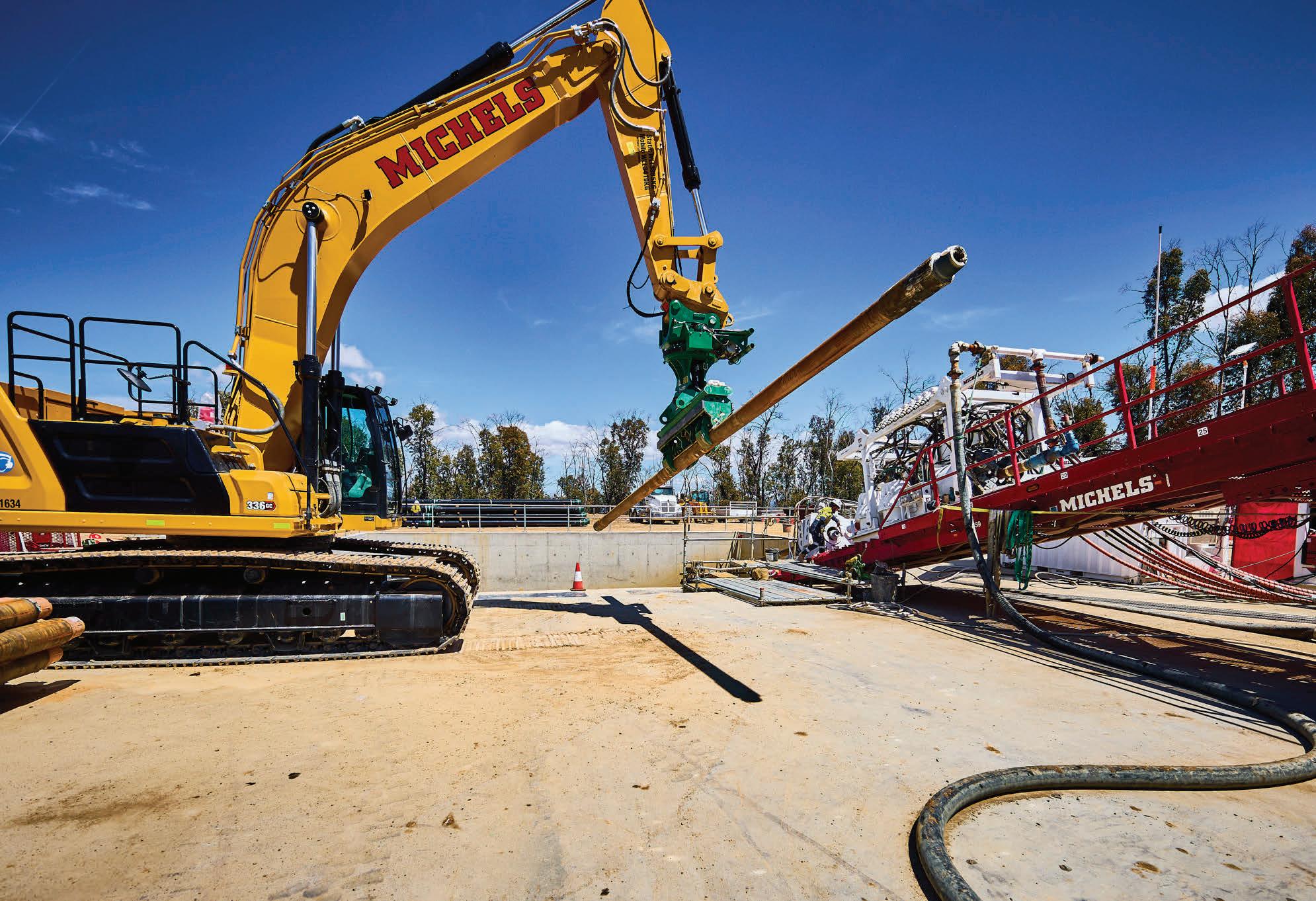


Horizontal Directional Drilling
• Multiple NASTT Project of the Year awards
• Australia-based operations with local resources
• Extensive experience with intersects and long crossings
• Successful 4.7km HDD under waterway
Direct Pipe
• Foremost Direct Pipe Contractor
• Outfalls and shore approaches
• Pipe Installations up to 1.5m
What
we have been up to in Australia
• Completed first of multiple 2,250m HDDs with 590m elevation change
• Longest HDD intersect completed in Australia
• Record-breaking HDD for combined elevation change and length
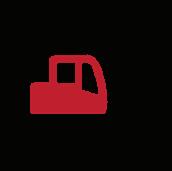
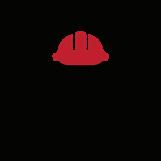
THE AUSTRALASIAN SOCIETY FOR TRENCHLESS TECHNOLOGY
ABN 43 893 870 966
P.O. Box 2242, MALAGA
LPO WA 6944
www.astt.com.au
President: Ben Crosby
Secretary: Trevor Gosatti
Vice President: Blair Telfer
COUNCILLORS
Western Australia: Aizezi Jiang
Queensland: Ben Crosby
New South Wales: Jason Marshal
Victoria: Ash Hamer
South Australia: Shaun Melville
New Zealand: Blair Telfer
Northern Territory: Luke Woodward
Tasmania: Vacant
President’s message
As we approach the end of 2024, it’s a wonderful opportunity to reflect on the exciting milestones and achievements that have defined this year for the ASTT. We have made significant strides in advancing the trenchless technology sector, and I am proud to share some of the highlights with you.
One of the key developments in 2024 has been the expansion of the ASTT Council. This reflects our ongoing commitment to strengthening the leadership and governance of our society, ensuring that we continue to effectively serve our growing membership and industry. Additionally, the commencement of the Young Members initiative has been a key focus. This new program aims to engage the next generation of trenchless professionals, offering them the support, mentorship, and resources needed to thrive in our industry.
We have continued to build and strengthen our relationships with important partners, most notably the Water Services Association of Australia (WSAA) and the North American Society for Trenchless Technology (NASTT). These collaborations are crucial to ensuring that ASTT remains at the forefront of global advancements in trenchless technology. By working together, we can share knowledge, foster innovation, and advocate for the adoption of trenchless methods worldwide.
ASTT is committed to the ongoing development of the workforce within the trenchless technology industry, and in 2024, we made significant progress in this area.
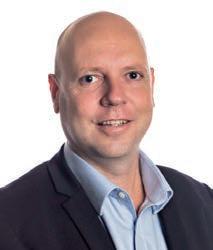
A key highlight has been our collaboration with the University of Technology Sydney (UTS) to introduce a dedicated trenchless technology module into the Masters of Engineering (Tunnelling and Underground) program. This module will provide students with specialised knowledge and practical insights into trenchless methods, helping to build a pipeline of skilled professionals ready to tackle the challenges of underground infrastructure.
Looking forward, we are already planning for some exciting events in 2025 and beyond. The Melbourne No-Dig Down Under 2025 will be a major event on our calendar, bringing together industry leaders, professionals, and innovators to discuss the latest trends and developments in trenchless technology. We are also preparing for the International No-Dig Conference 2026 in New Zealand, which promises to be another key global event for the trenchless community.
I would like to take this opportunity to thank all of our members, partners, and stakeholders for their continued support and dedication to advancing the trenchless technology industry. It is through your efforts that we are able to drive meaningful progress and innovation, and I look forward to continuing this journey together.
Thank you for your continued commitment to ASTT and our shared goals.
Ben Crosby ASTT President
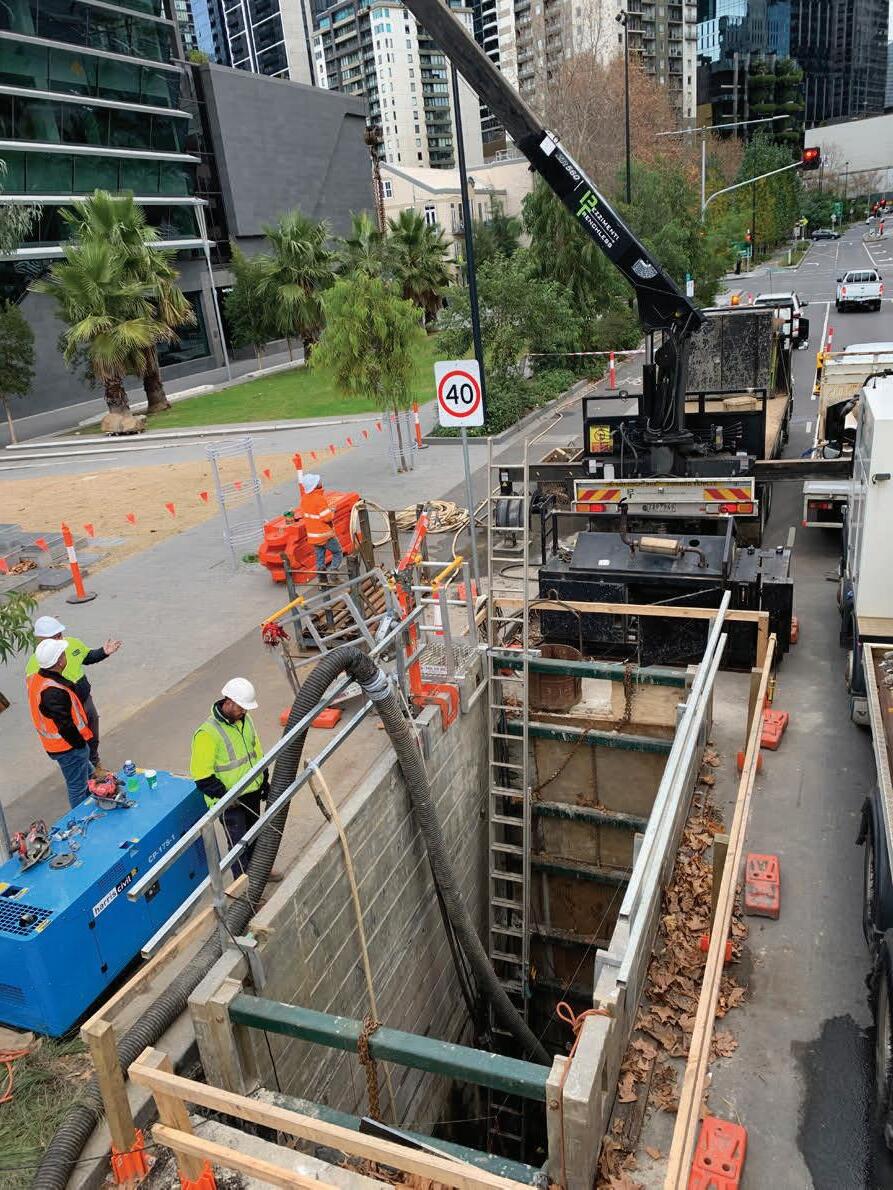

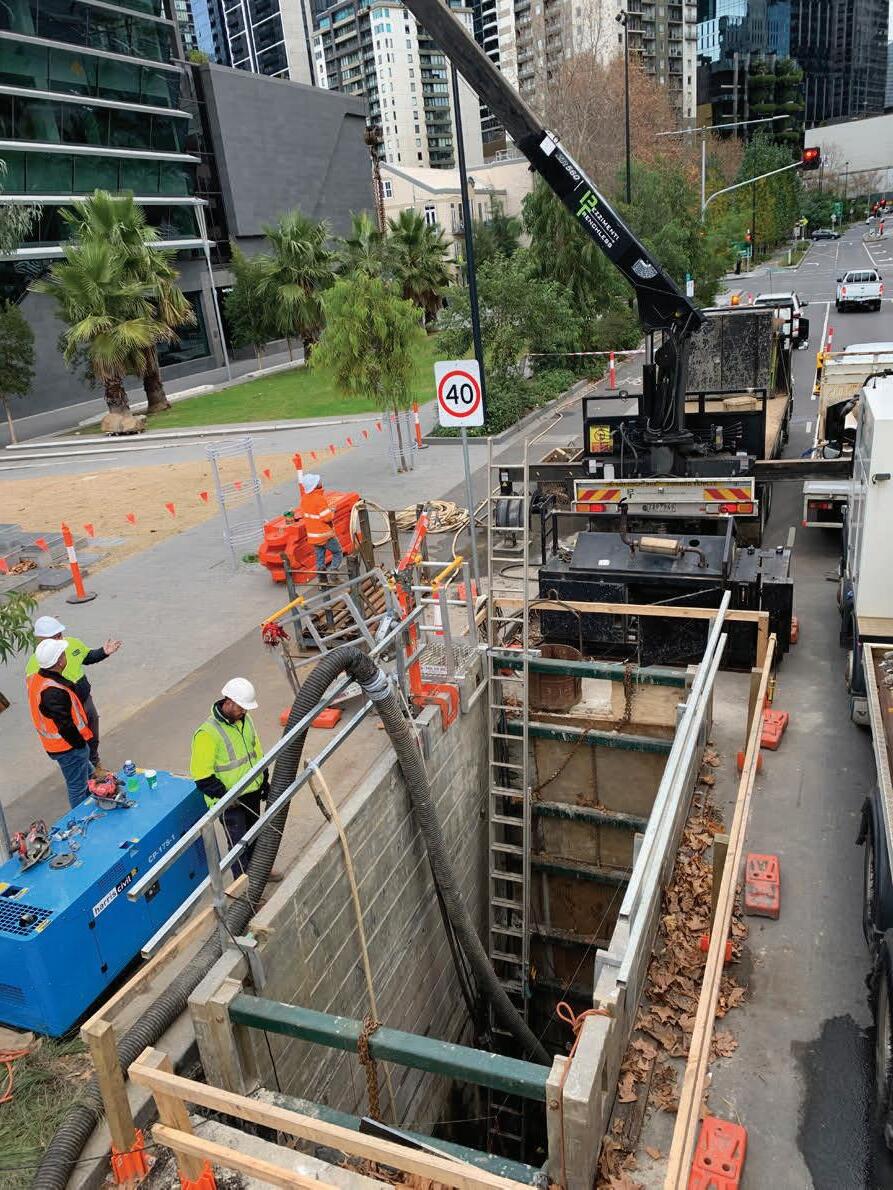




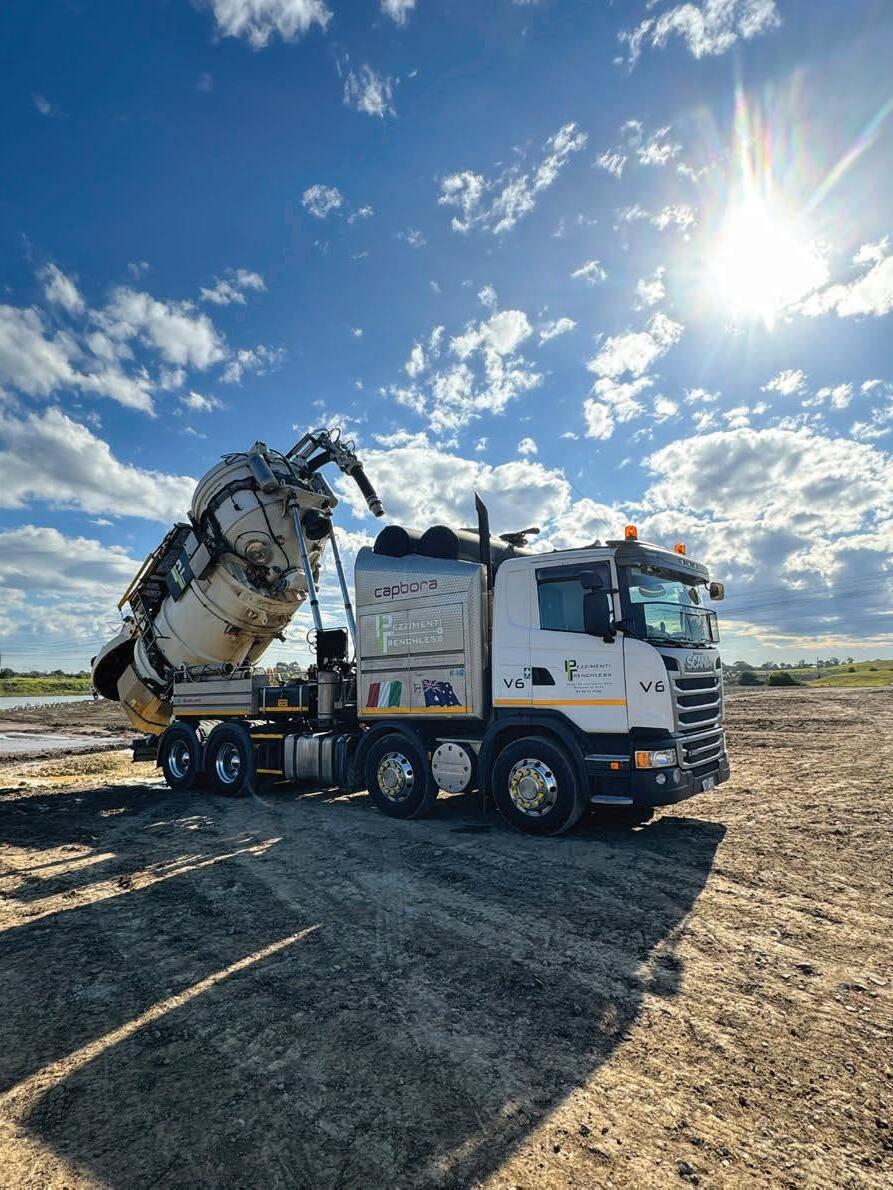
The Pezzimenti name has been synonymous with pipeline construction since 1957 when G. Pezzimenti and Sons began contracting to the Melbourne Metropolitan Board of Works.
Since then, Pezzimenti Trenchless has established itself as a leader in the trenchless industry, using the Pezzimentideveloped laser-guided microtunnelling system to install gravity sewers, water mains, stormwater, gas and electrical conduits ranging in diameters from 325 to 1850mm.
Working with all leading sewer and water contractors and all major water boards throughout Victoria and South Australia.
Secretary’s corner December 2024
New members
On behalf of the ASTT, I extend a warm welcome to the following new members:
Tertiary Education – Australia
ACA Training – (Peter Milne)
Silver Corporate Members – Australia
FJA Consulting Engineers –(Jeremy Hopson)
Individual Members – Australia
Thomas Wood from Egis
Individual Members – New Zealand
Andy Flint from Pipe Care
International No-Dig Conference and Exhibition sponsorship and exhibition opportunities open
In a recent press release the ASTT and Prime Creative Media formally announced that sponsorship and exhibition opportunities were now available for the International No-Dig 2026.
The International No-Dig, the International Society for Trenchless Technology’s (ISTT) annual event, will be held in New Zealand in 2026 following a successful bid by the Australasian Society for Trenchless Technology (ASTT).
The event will be held at the newly built New Zealand International Convention Centre in Auckland from September 2830, 2026. It will be the first time that the prominent global industry event will be held in New Zealand, and will be a fantastic opportunity for the trenchless industry in the region.
For all enquiries visit: no-dignz.com/
ISTT International Council meeting in Dubai
The ISTT held its International Council Meeting (incorporating the AGM) in Dubai,
UAE on 4 November 2024, just prior to the Trenchless Middle East Conference and Exhibition that was being held there.
A number of matters occurred at the meeting including:
• The election of Sam Efrat from SASTT to the position of Vice Chair
• The election of six ISTT Board members (three re-elected terms, three new members)
In addition to the International Council meeting, the ISTT took the opportunity at the Trenchless Middle East event to conduct sessions on the new ISTT website and the new ISTT Strategic Planning initiatives.
It was also great to see a number of ASTT members being represented at the Trenchless Middle East promoting their goods and services to the global markets.
New ISTT website to benefit ASTT members
As mentioned in the last edition of the Trenchless Australasia, the ISTT announced its new website was complete, along with an advanced database to complement the website and its services.
The next step will be for the database and website to be uploaded with data from the 28 affiliated societies of the ISTT so that the website will effectively provide the data portal that it is intended to do going forward.
When most of this data has been uploaded hopefully within weeks, the site will be made “live” and members can then enjoy the benefits of the new site.
The new ISTT website contains many new features for the affiliated societies and their members providing many more opportunities to promote trenchless technologies around the world.
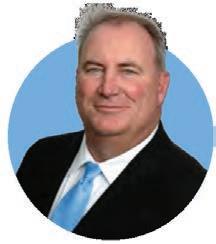
Some of the new features include:
• A corporate booth facility for existing corporate members where the entity’s products and services can be displayed via video, brochures and WhatsApp
• The ability to “upgrade” the basic corporate booth to a higher level virtual corporate booth providing the corporate entity to promote its goods and services to a global audience. The additional features include video, brochures, presentations, business cards, WhatsApp and other media
• The option of a corporate upgrade will be offered through affiliate societies
• The website will have enhanced “Charts & Description” pages highlighting the benefits of trenchless technologies to industry
• Enhanced pages providing past conference papers
• A next level database facility will assist affiliate societies to have member data included and allow members in the database to access all the features of the ISTT website
• It is planned for a single sign on (SSO) for the member login process
• The database will allow a more improved search function for corporates and the goods and services they offer to industry
The ASTT and more importantly its members will benefit from the development of this new website. We look forward to soon communicating the new benefits to its members that they can access.
Trevor Gosatti ASTT Secretary
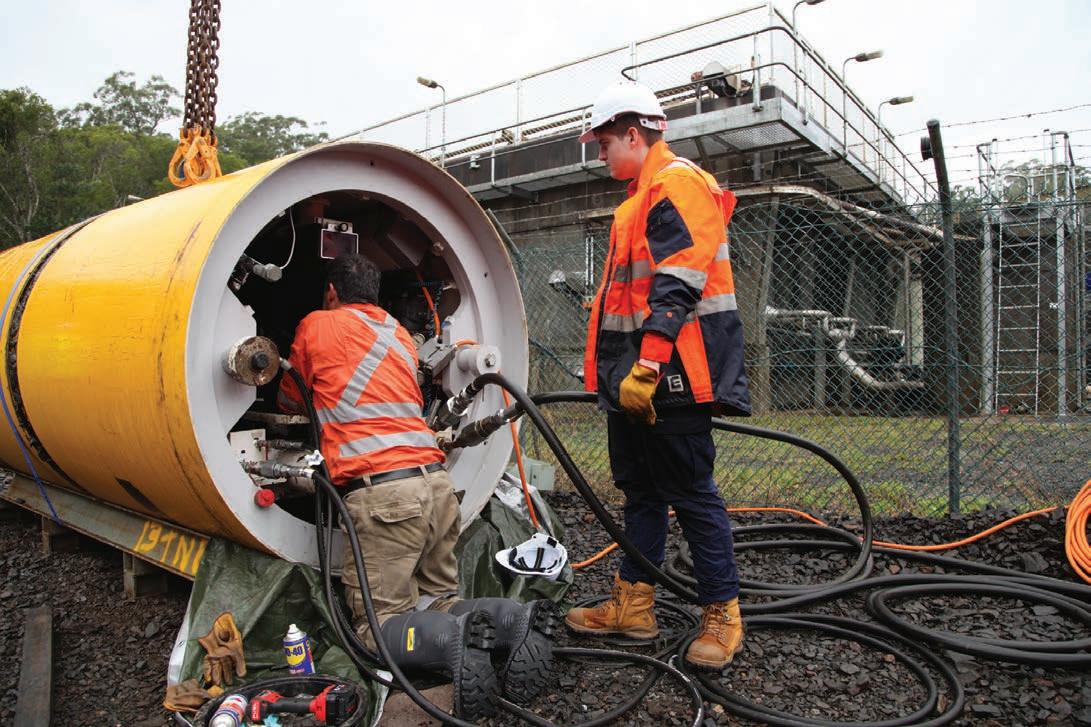
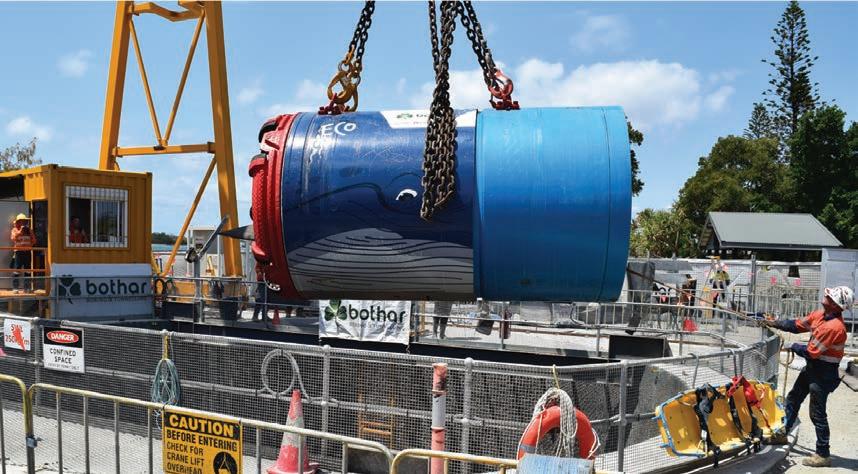
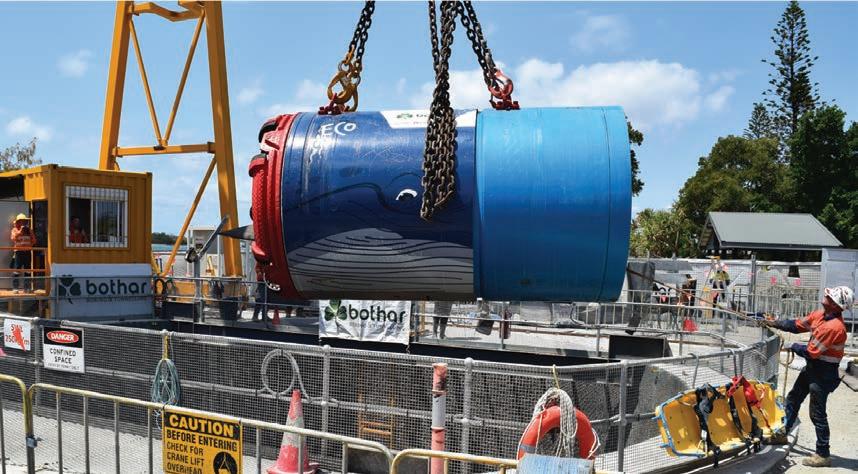
DISCOVER THE FUTURE WITH BOTHAR, A GLOBAL TRENCHLESS CONSTRUCTION EXPERT.
Ensure your project is delivered safely, sustainably, and successfully.
Bothar possesses comprehensive trenchless solutions alongside expertise in shaft construction and civil capabilities.
With over 30 years’ experience, Bothar is your partner for the delivery of complex infrastructure solutions.
Our Services
•Vermeer Axis Laser Guided Systems
•Auger Boring
•Direct Pipe Installations
•Shaft Construction
•Herrenknecht AVN MTBMs
•Bothar Built EPB - TBMs
•Open Face TBMs
•Tunnel Boring & Pipe Jacking
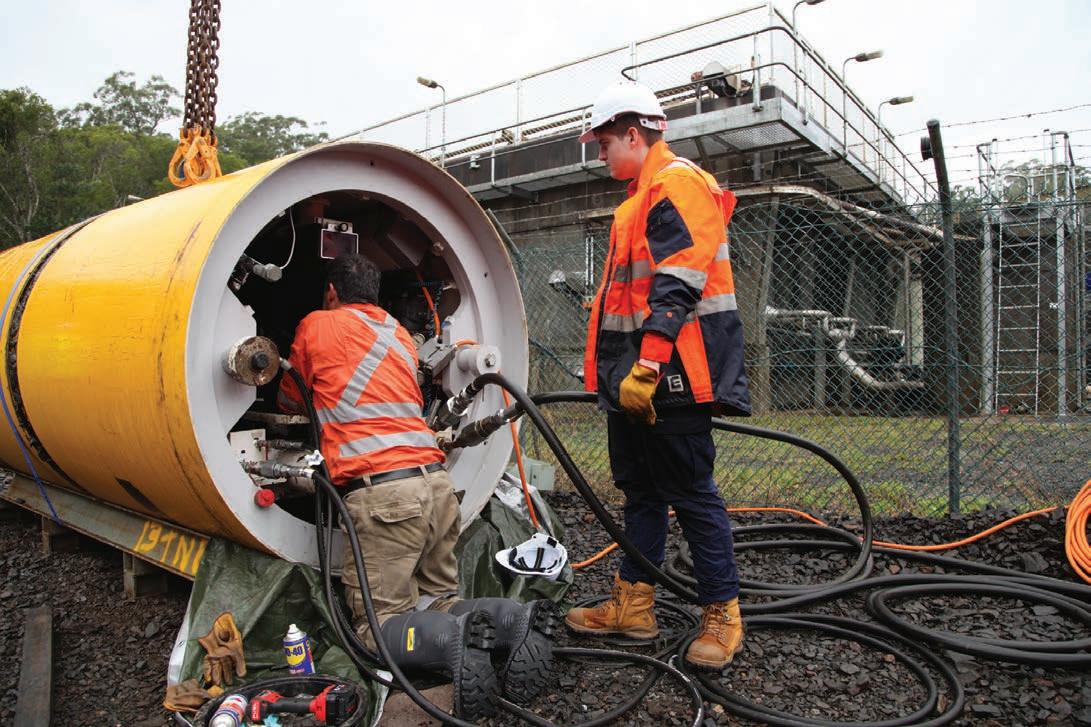
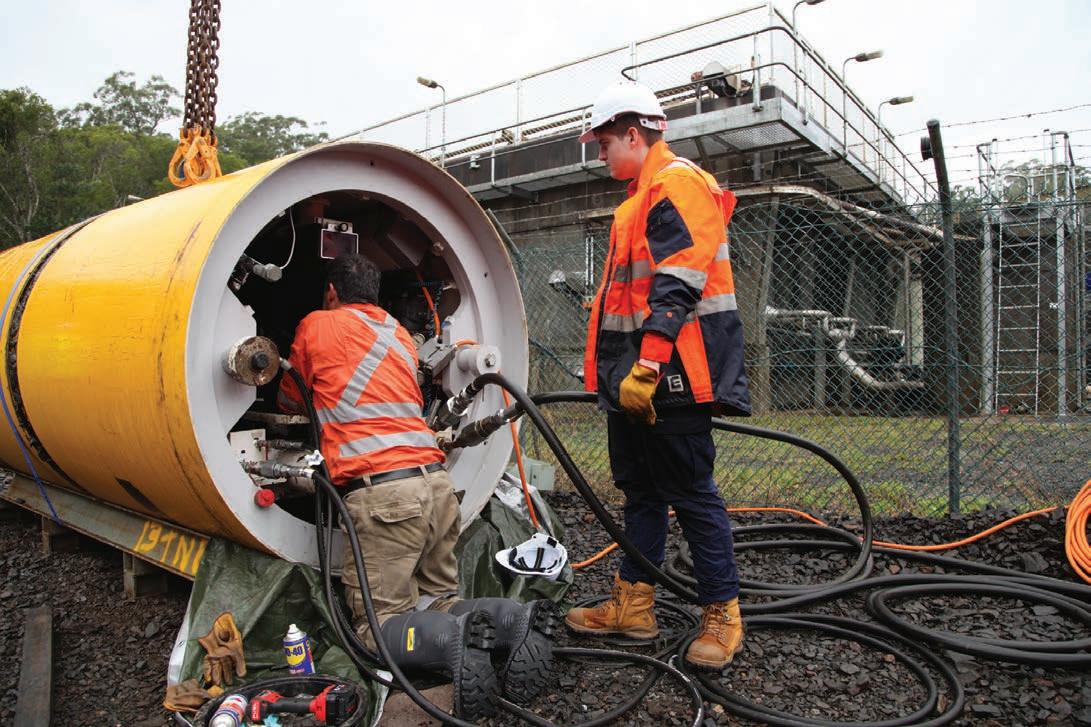
Rob Carr awarded contract for major WA sewer project
Utilities infrastructure expert Rob Carr has been awarded the contract for the construction of the Eleventh Road Collection Sewer, a major capital works project for Parcel Property in WA.
Rob Carr will self-perform the construction of 356m of DN600 sewer, 517m of DN450 sewer, 277m of DN375 sewer and 12 access chambers.
The sewer will be predominantly constructed via microtunnelling, with the longest drive being 186m. There is also a small amount of open trench excavation works.
The work will commence in January 2025 with completion scheduled for September 2025.
Sydney Metro project a ‘feat of tunnelling’

Trenchless project in NSW receives international recognition
More than 23,000 workers, 11 tunnel boring machines (TBMs) and an army of roadheaders and excavators were required by CPB Contractors to construct more than 80 kilometres of tunnels and caverns as part of the Sydney Metro project.
The transformational project celebrated its official opening of the Chatswood to Sydenham stretch recently.
With over 100 kilometres of rail track laid, CPB Contractors, a member of the CIMIC Group, has been part of the Sydney Metro journey since the very beginning.
Its teams delivered 100 per cent of the tunnelling works for the Sydney Metro line running from Tallawong in Sydney’s Northwest through to the heart of Sydney’s CBD.
An engineering and tunnelling feat, the construction of Sydney Metro included tunnelling, track-laying and fit-out works under Sydney Harbour and through the CBD with these twin tunnels and tracks now able to move more people across the harbour during peak-hour than the Sydney Harbour Bridge and Sydney Harbour Tunnel combined.
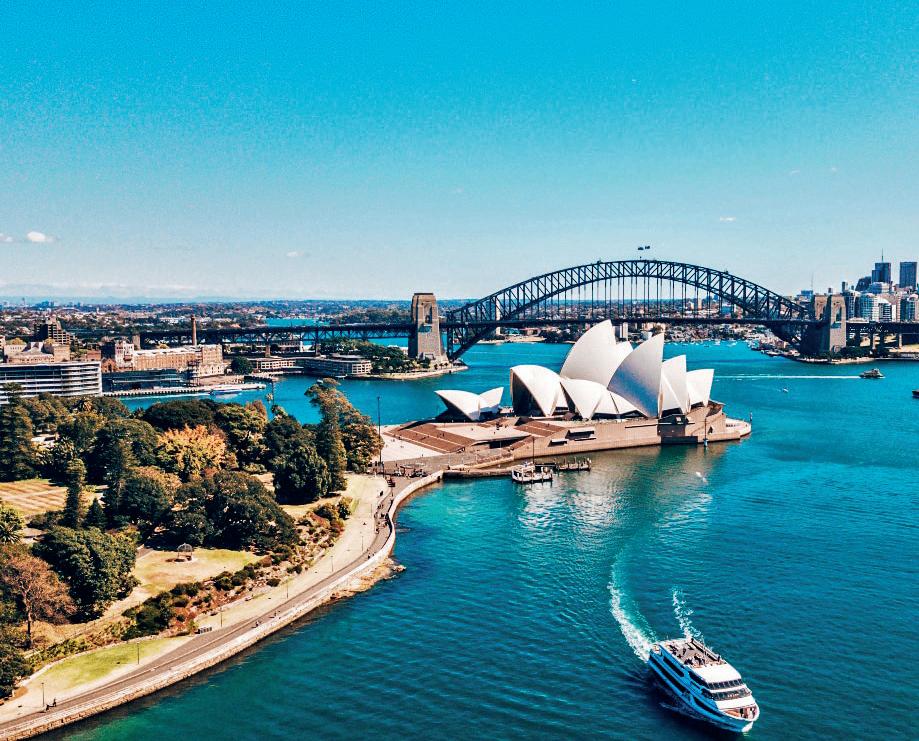

Michels Corporation has been recognised as the runner-up in the IPLOCA Excellence in Project Execution Awards for the company’s work on the Snowy 2.0 horizontal directional drill (HDD) in New South Wales. The project included a 2248m drill with a 563m vertical elevation change, and saw the drill and pipe installation completed by Michels Trenchless Pty Ltd, a branch of Michels Corporation.
Completing the project safely while maintaining strict environmental standards required Michels to innovate all phases of planning and construction.
Rather than perform a conventional one-rig pilot hole, Michels determined the pilot hole intersect method would be a better way to achieve the customer’s project goals.
The pilot hole intersect method deploys two drill rigs, one drilling from the entry side and one from the exit side, to meet at a predetermined location along the alignment.
The team used two Michels-designed and fabricated rigs, each with 880,000 pounds of push/pull force.
The pilot hole intersect method allowed the team to manage fluid pressure in the drilling column and from returns; contend with a high water table, minimise push forces; and facilitate steerability through hard and fractured rock.
The HDD project supports Snowy 2.0, the largest renewable energy project under construction in Australia.
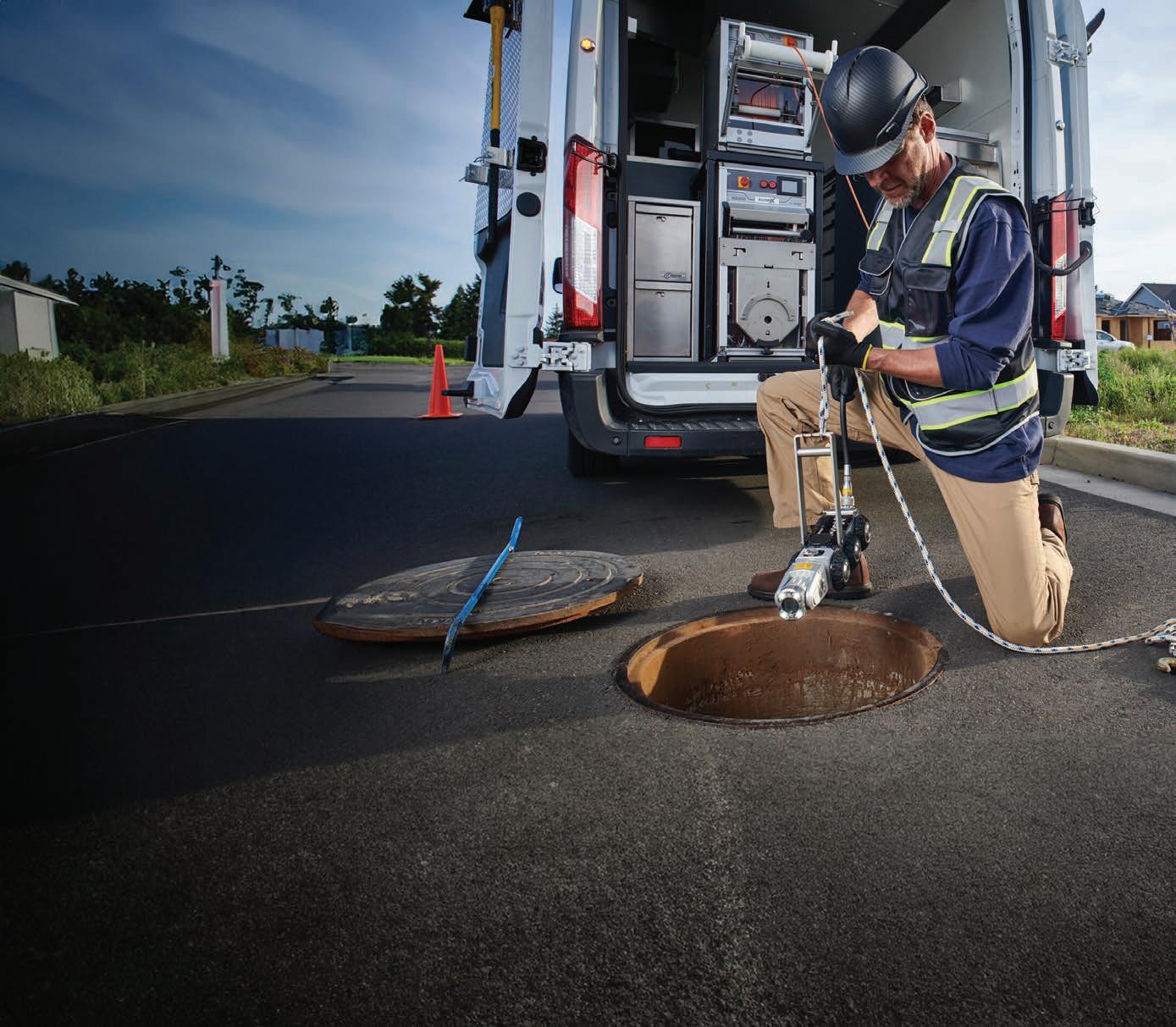
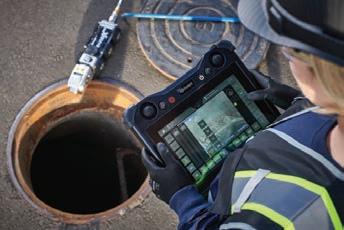
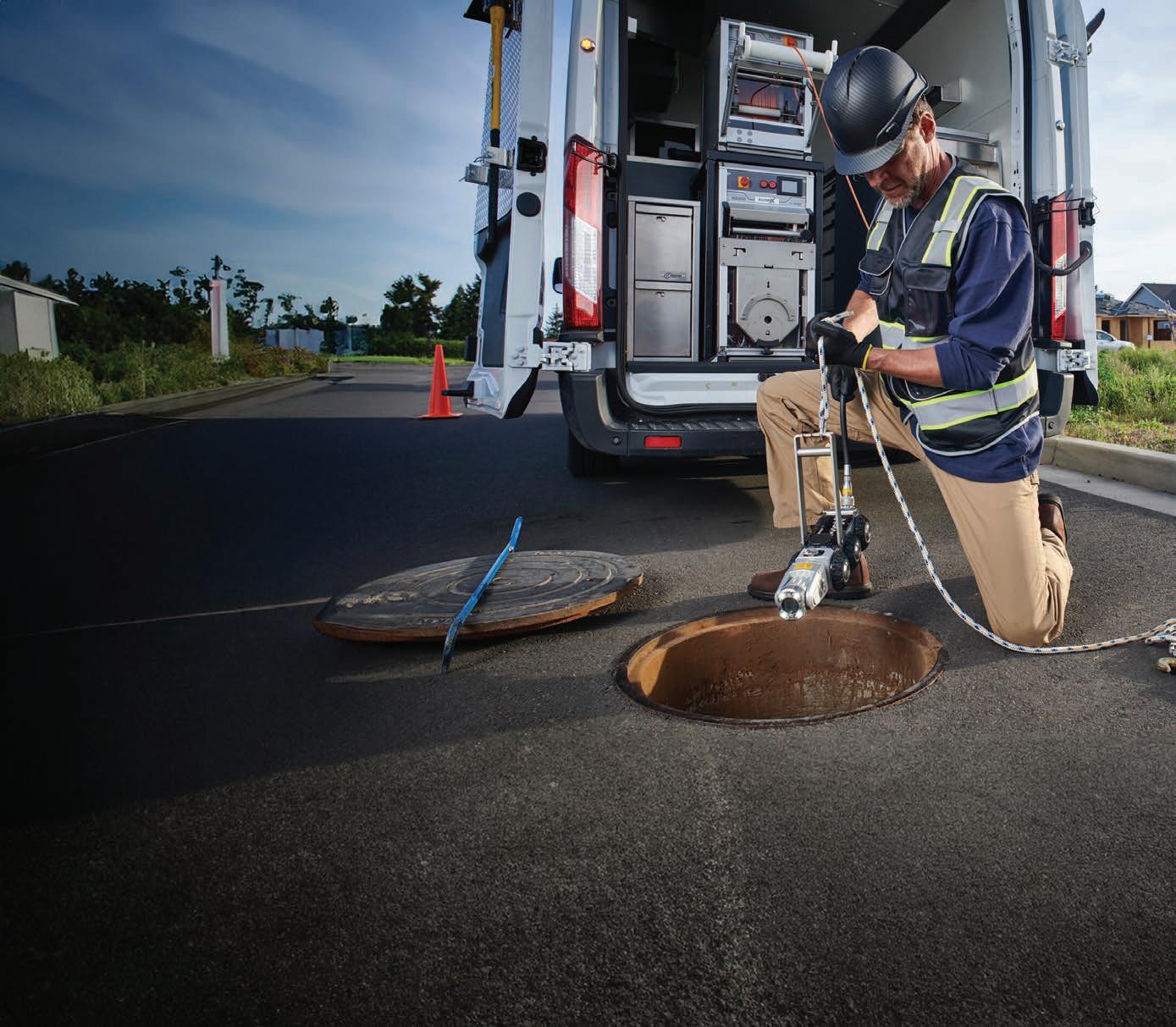
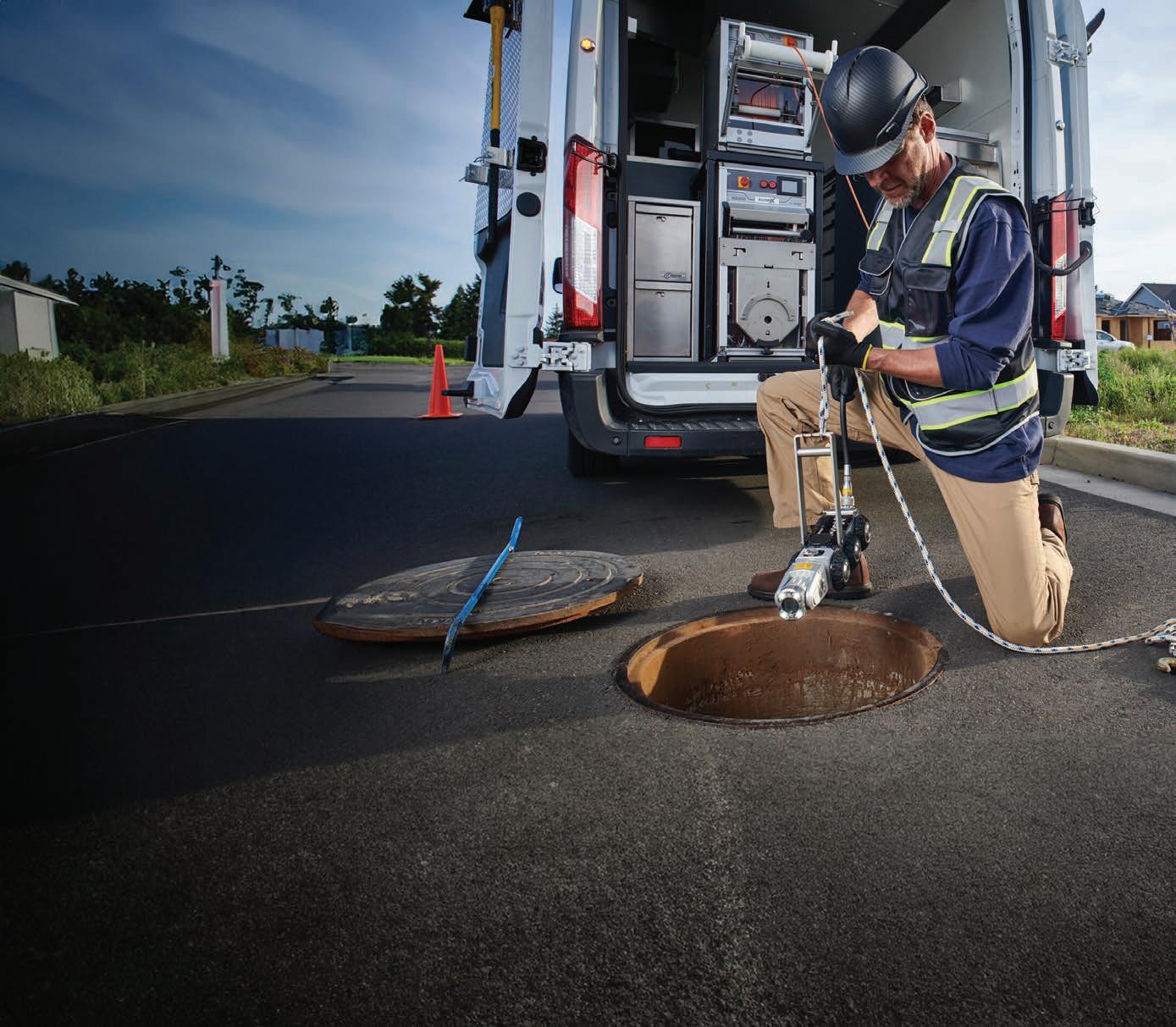
Modular System: Easily configurable for various pipe sizes and inspection challenges.
Reliable Design: Built to endure harsh conditions and reduce downtime.
Contact SECA today to learn how the ROVION HD can revolutionise your sewer inspections.
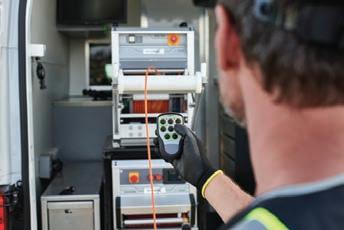
Auckland program saves seven million litres of water a day
A targeted water network improvement program – which hones in on leaks and water pressure at a neighbourhood level –has prevented an estimated seven million litres a day of water loss in Auckland in the past year.
Smart systems manager Dave Moore explained the program focuses on the areas in Auckland with the higher numbers of reported leaks.
“There will always be leaks in any water network – this is about prioritising our efforts so that we’re making the best use of our resources to prevent as much water loss as possible,” he said.
A recent focus on the western parts of Māngere, which had experienced one of the highest numbers of reported leaks in the network, yielded great results, preventing an estimated half a million litres of water loss per day.
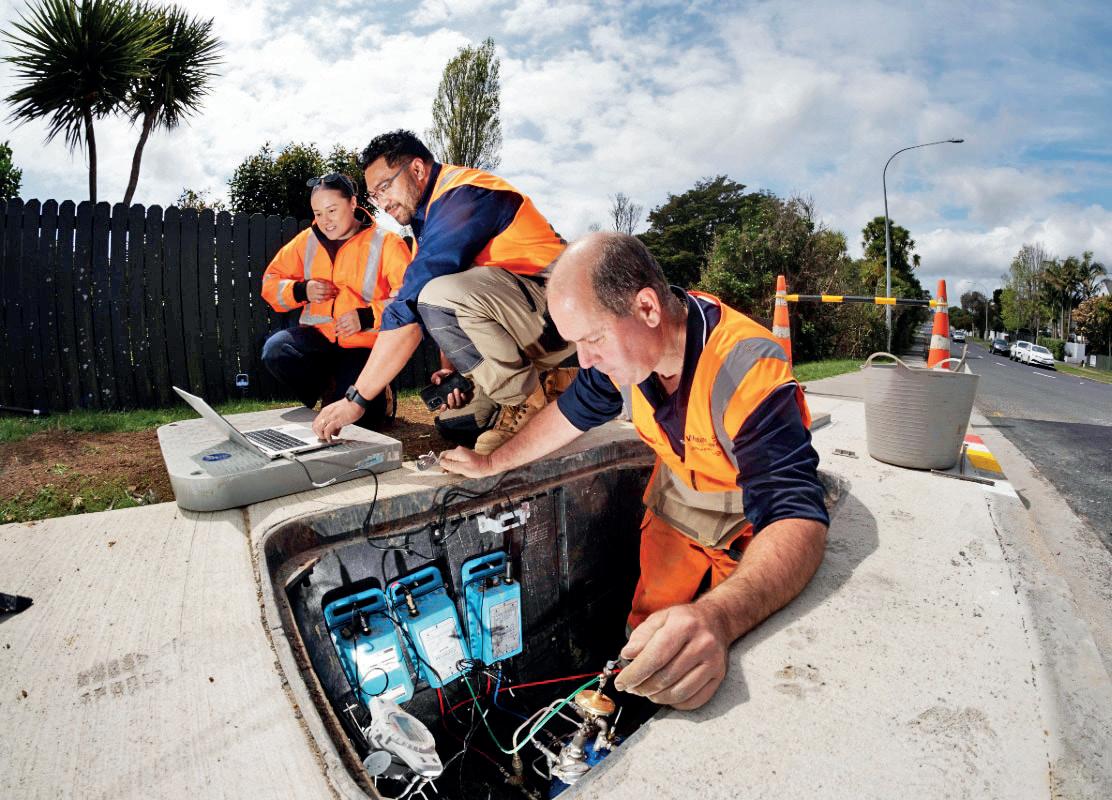
Groundbreaking purchase made for major SA project
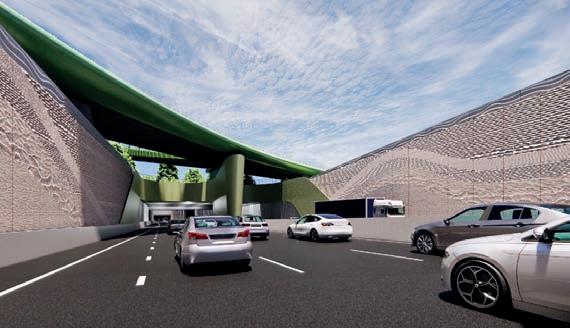
The South Australian Government and the T2D Alliance have signed the contract to purchase three tunnel boring machines (TBMs) from world-leading manufacturer Herrenknecht.
The purchase of the three TBMs comes just weeks after the main construction contract was officially signed by the consortium of John Holland, Bouygues Construction, Arcadis Australia, Jacobs and Ventia. The historic purchase of the TBMs was confirmed at the Herrenknecht Headquarters in Schwanau, Germany, with plans revealed for two smaller TBMs to also come to excavate between the main tunnels. Herrenknecht has delivered TBMs to countries around the world, including the United States, England, China, Singapore, Italy and Qatar, as well as Australia for projects such as the Sydney Metro and the North East Link and West Gate Tunnel Projects in Melbourne. The TBM components will be manufactured in Germany and China, before being assembled and factory assurance tested in China and then delivered to Adelaide. The first of three TBMs is expected to arrive in late 2025.
Contract awarded for $170m wastewater infrastructure project
Sydney Water has secured a delivery partner to manage the first stage of a multi-billion-dollar program of work, which will enable the construction of 90,000 new homes in Western Sydney.
Jacobs and Seymour Whyte (JSW), a joint venture, has been awarded a management contract for stage 1 of the multi-stage Upper South Creek Networks Program.
In this first stage, they will oversee the design, procurement, and construction of up to $170 million in critical wastewater infrastructure.
Over the next 12 years, the entire work program will deliver over 96 kilometres of wastewater pipelines and nine pumping stations within the Upper South Creek precinct.
By 2056, it is estimated 90,000 new dwellings and 200,000 jobs will be in the Upper South Creek Catchment region.
The Upper South Creek Catchment will also include innovative precincts focused on advanced manufacturing, technology, research, training and education, freight and logistics, agribusiness and mixed-use development. The Upper South Creek Networks Program will include five projects
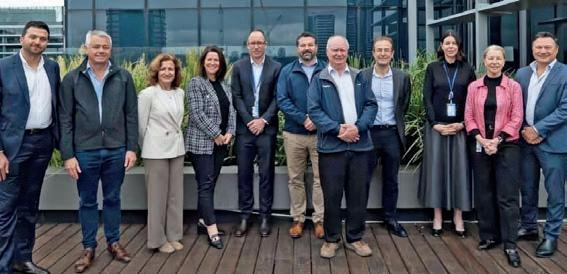
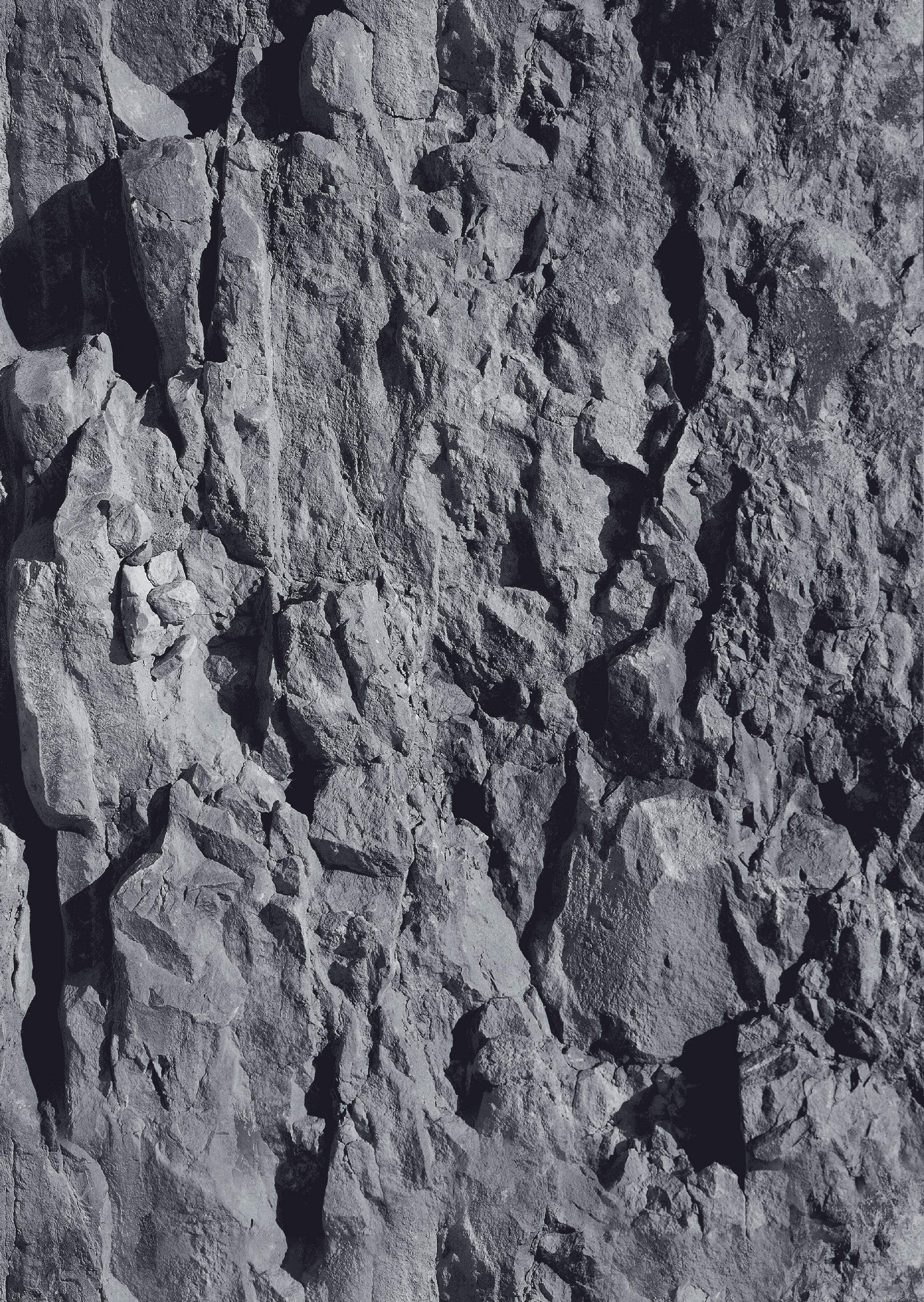
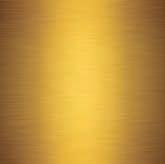


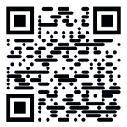
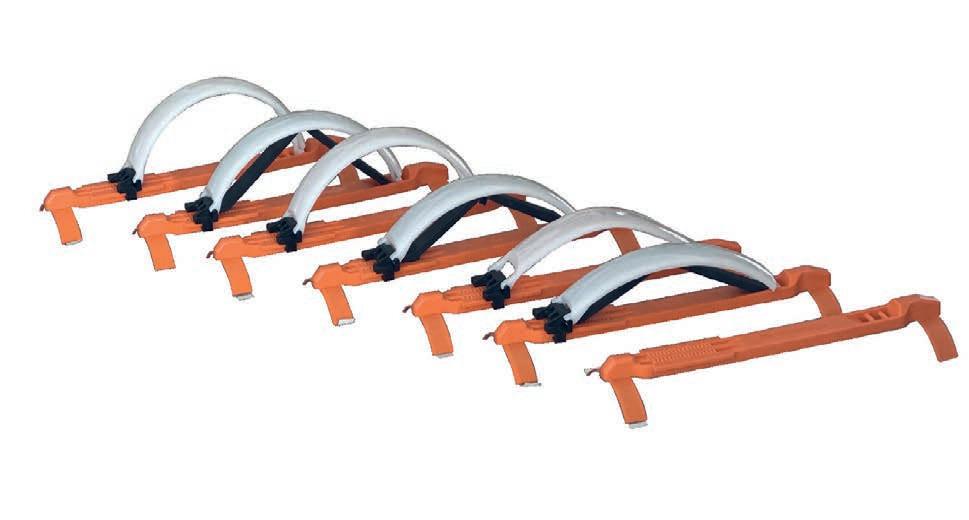


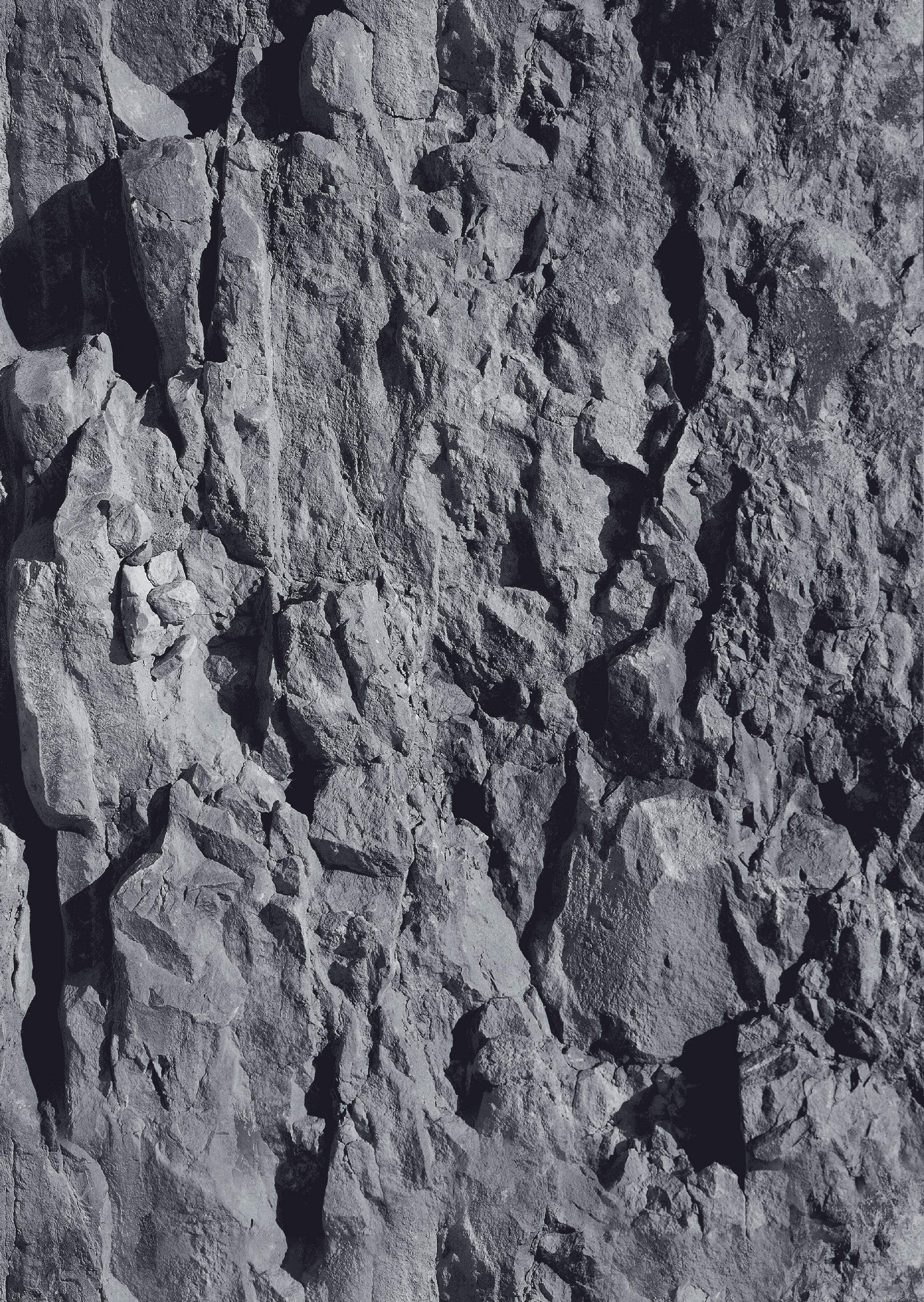
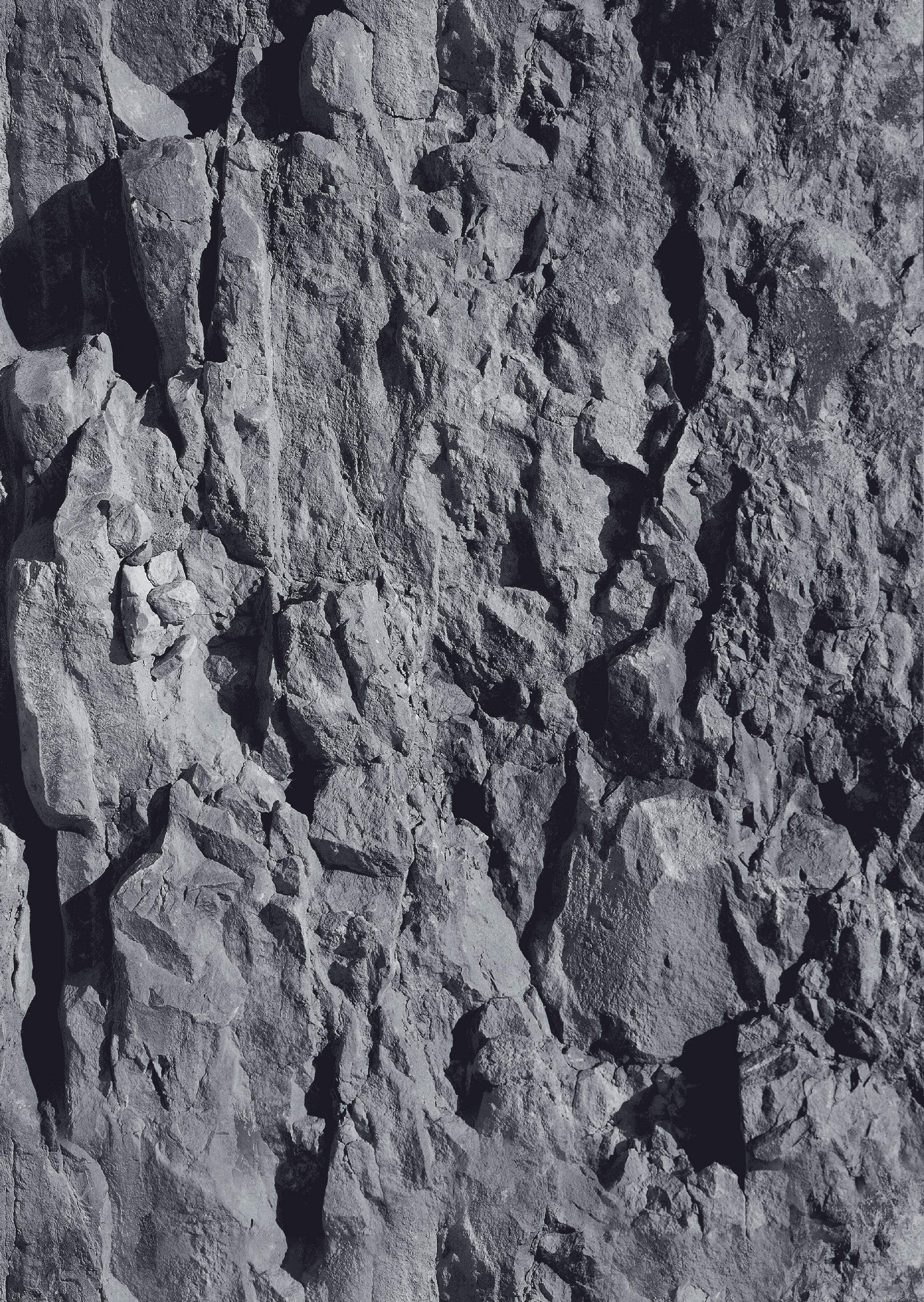
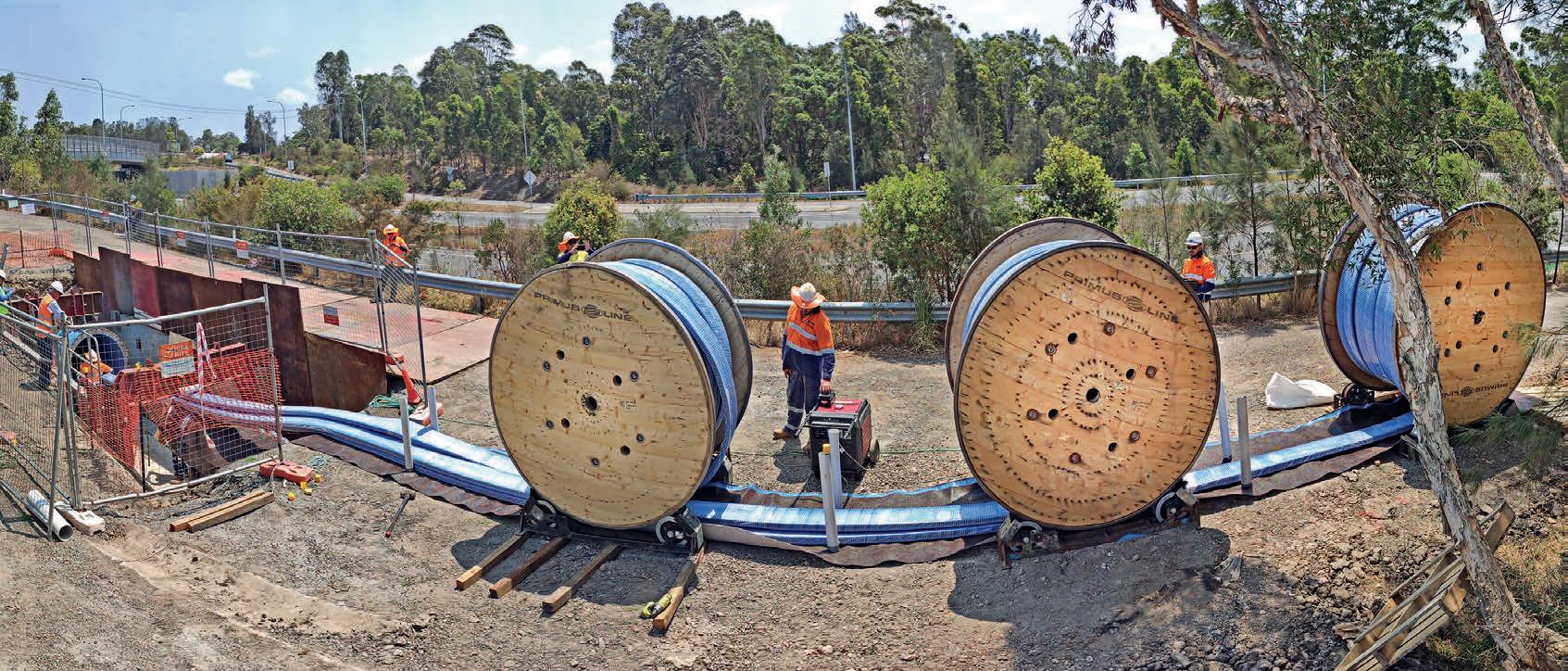
Ten years of Primus Line Down Under
With water an increasingly valuable commodity in Australia, the importance of innovative environmental approaches to pipeline rehabilitation cannot be overstated, and Primus Line has established its product as part of the solution.
Establishing a branch in Australia at a time when few pressure pipe rehabilitations were being carried out using trenchless technologies may seem like a bold move.
But German company Rädlinger Primus Line GmbH took precisely this step in 2016. is was preceded by more than two years of intensive preparation, persuasive work with network operators and the rst commissioned rehabilitation projects.
Laying the groundwork
In September 2013, Andreas Gross, now Head of Primus Line’s Business Unit for International Water Projects, visited International No-Dig in Sydney.
He collected information about the Australian market, especially about construction companies and network operators.
Rädlinger Primus Line was already aware that water is a precious commodity and valuable resource in Australia with its many arid regions, deserts and semi-deserts.
e standards for the construction of pipelines are correspondingly high. e pressure ratings for water pipes are between PN12/1,200 kpa and PN16/1,600 kpa, which suits the Primus Line® technology product portfolio.
Trenchless technologies for the rehabilitation of gravity pipelines and lining with continuous HDPE pipes were already known and in use in Australia at the time, and the technology for cleaning and camera inspection prior to rehabilitation was also available.
ese were the best prerequisites for establishing Primus Line Rehab as a trenchless system for the rehabilitation of pressure pipelines in Australia.
e visit to the trade fair brought immediate success – the rst rehabilitation project was initiated there, although it was realised in New Zealand rather than Australia at the end of 2013.
e approval process for the drinking water hygiene certi cate in accordance with AS/NZS
4020 for the Primus Line system was initiated and completed successfully at the end of 2014.
A year of firsts
e year 2014 was the year of rsts for Primus Line in Australia – the rst appearance at the OzWater trade show with an Australian partner; the certi cation of the rst local installation companies; and the discussion of the rst project Down Under, which was put to tender in 2015 and realised in 2016.
For this project, Primus Line secured the rehabilitation of a 460m-long leaking uPVC drinking water pipe in Lismore, New South Wales.
At the time, Primus Line’s Australian operation was managed from the German headquarters.
Gross toured Perth, Darwin, Adelaide, Melbourne, Sydney and Brisbane several times a year for three weeks at a time to raise awareness of Primus Line Rehab among network operators.
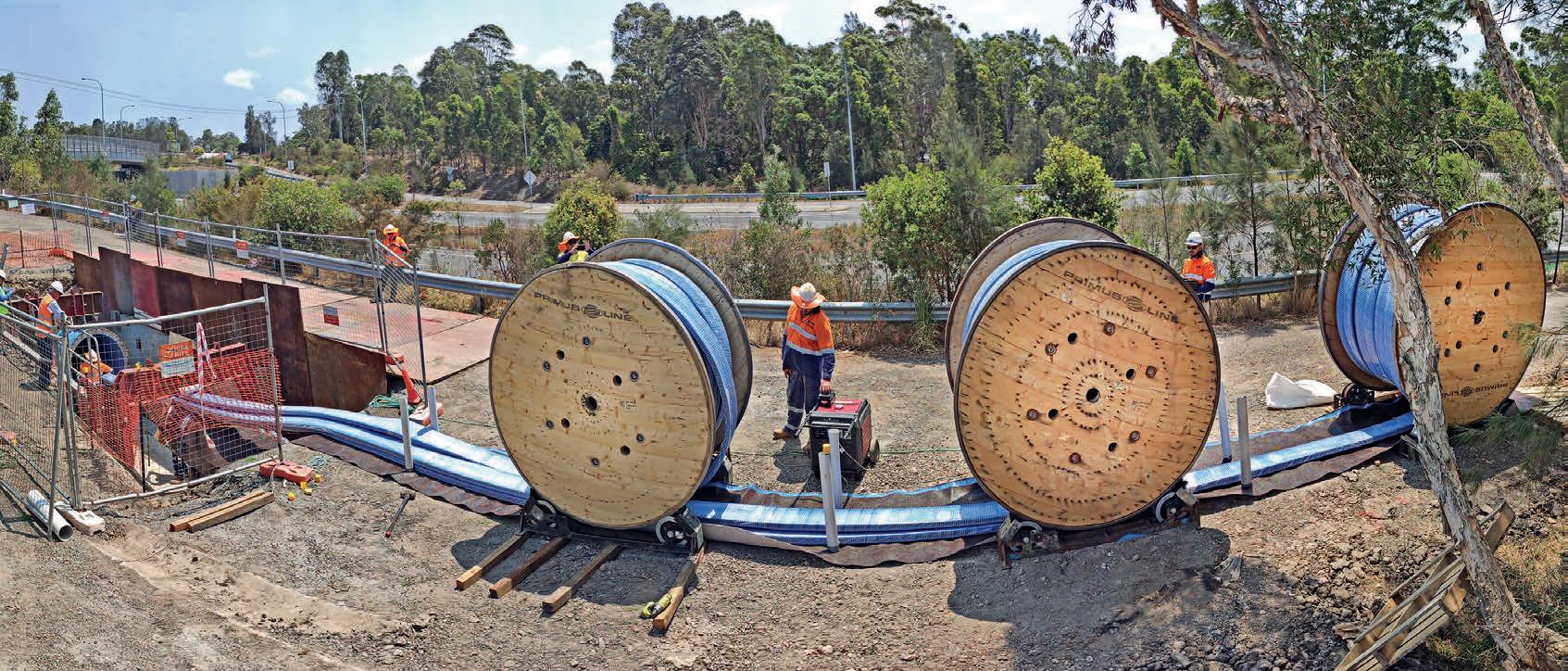
is led him to Urban Utilities, one of Australia’s largest water suppliers, in 2014.
Its interest in the innovative product was so great that in the same year, a delegation visited IFAT – the world’s leading trade fair for water, sewage, waste and raw materials management – in Munich.
e delegation also visited a nearby construction site to evaluate Primus Line as a solution.
It turned out that the anges of the connectors had to be customised speci cally for the Australian AS4087 standard, which the Primus Line engineers implemented accordingly.
During these initial visits and return visits, a rehabilitation project on Ann Street in Brisbane was discussed, which was nally realised in 2020 following a trial project in 2018.
e installation work took place exclusively at night to minimise the impact on residents and tra c.
Urban Utilities carried out the installation itself after thorough training, with a Primus Line supervisor on site to provide support.
Branching out
Convinced by the successful market development, the promising discussions, and the rst certi ed installation partners and installations, the Primus Line management team decided in 2016 to establish a branch in Australia. It also had the goal to be permanently on site with a local employee by the end of the same year.
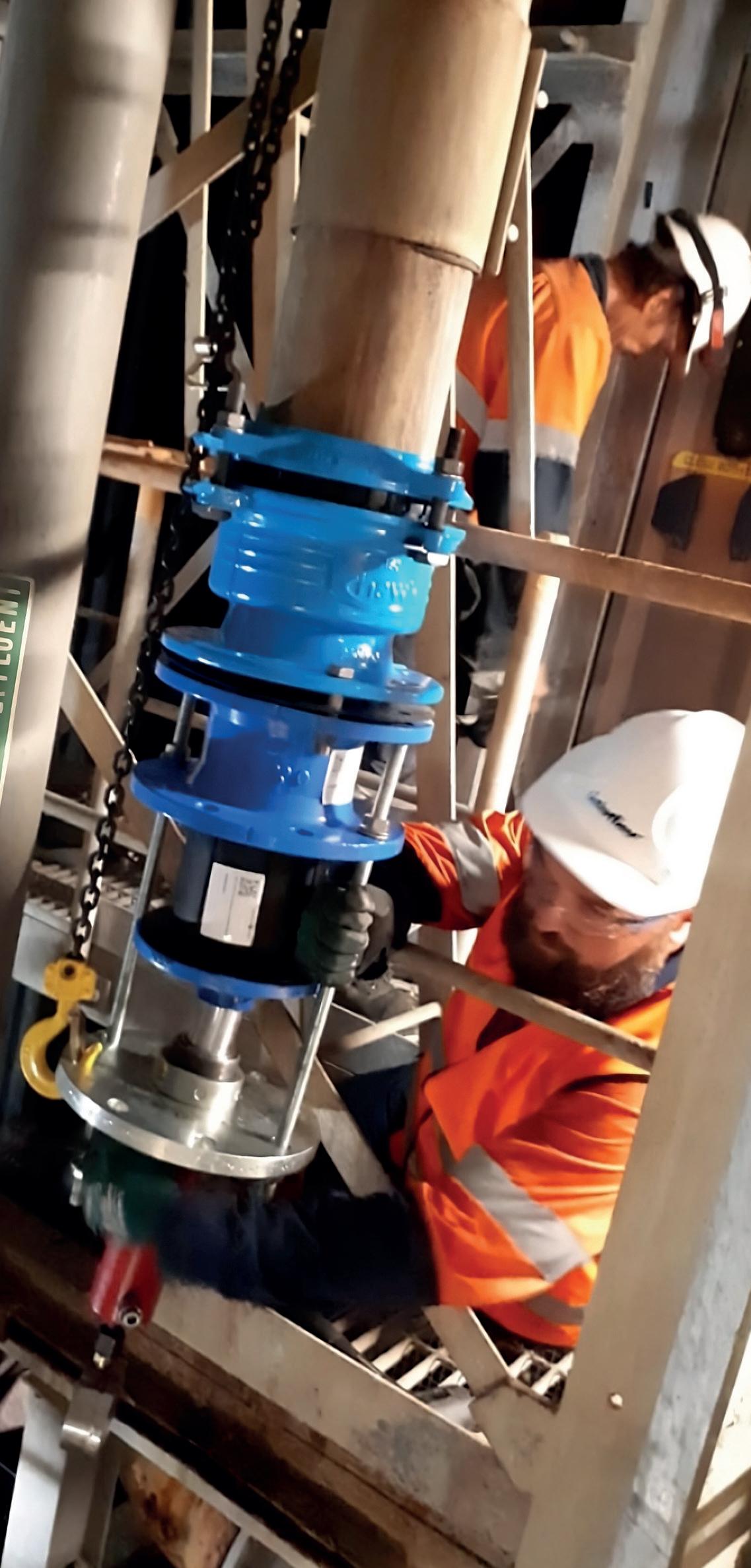
anks to the support provided by the German Australian Chamber of Foreign Trade in initiating business and the employee’s broad network of operators, engineering rms and construction companies, the number of projects and operators with Primus Line Rehab quali cations increased.
After successfully completing the tests and two trial projects involving the rehabilitation of short pipe sections, Primus Line Rehab was added to Sydney Water’s list of approved pipeline rehabilitation products.
Operators from Sydney Water have been installing Primus Line solutions since 2017 following extensive training.
Partnerships and plans
German engineer Heiko Manzke has been responsible for Primus Line’s Australian and New Zealand operations since 2019.
After many years at Primus Line’s headquarters in Germany, he relocated to the east coast of Australia and is contributing his technical expertise to the network built up by his predecessor, expanding it further and acting in an advisory capacity.
In addition to many rehabilitated wastewater pressure pipes, Manzke has been to the forefront of a number of unusual projects – such as the rehabilitation of a vertical pipe and the rst three-in-one project implemented in Australia with Hunter Water.
Projects were also realised in New Zealand and with mine operator Rio Tinto.
Primus Line celebrated a signi cant milestone during the Covid-19 pandemic, securing a partnership with Inter ow, one of Australia’s

market leaders for water and pipework infrastructure. Inter ow took Primus Line products into stock to reduce delivery times for emergency projects. e exclusive contract ended in mid-2024.
In future, Primus Line will work with regional specialists in the water sector alongside their existing installation partners, which will continue to include Inter ow.
Meanwhile, e orts to expand the use of Primus Line® Overland Piping as a temporary, above-ground pipeline in mining are showing initial success.
Pioneering product
Manzke said Australia and New Zealand are extremely interesting markets for a Primus Line’s products.
“ e local network operators and engineering rms are highly quali ed and therefore greatly
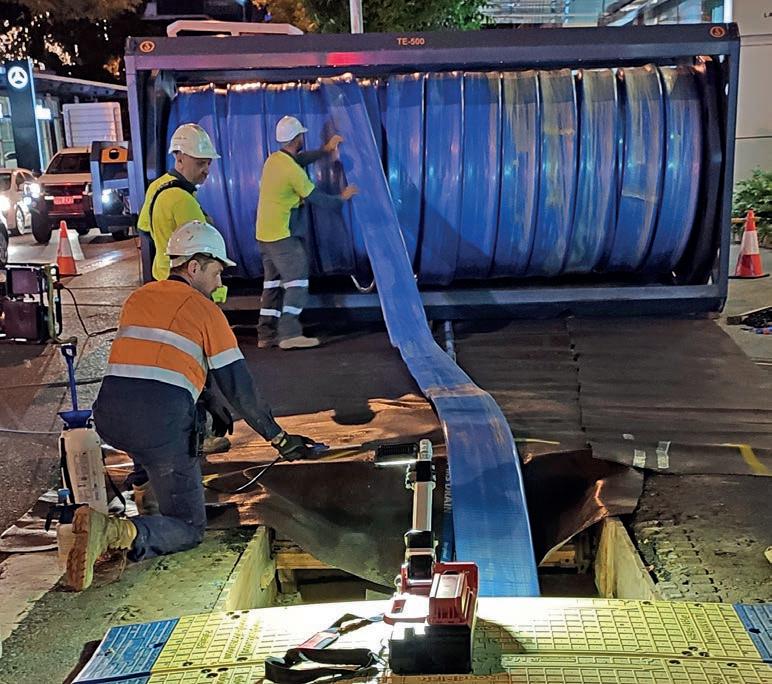
appreciate a high-quality product made in Germany,” he said.
“At Primus Line, we o er a carefree all-in-one package – a rst-class product with excellent customer support, combined with unrivalled expertise in the eld of exible piping.
“Nobody in the world can hold a candle to us in this area, and our customers in Australia and New Zealand recognise and appreciate that.”
Gross, who pioneered the work for Primus Line in Australia, said “as water is an increasingly scarce resource in Australia, awareness of e cient and resource-saving solutions is high”.
“ ere is a strong openness to innovative and trenchless technologies. is opens up excellent opportunities on the Australian market for companies that o er technological and environmentally friendly approaches,” he said.
Primus Line projects in Australia and New Zealand:
• More than 70 projects realised in total
• Longest rehabilitated stretch: around 3000m on Ann Street in Brisbane with Urban Utilities
• Longest single-shot installation: 1400m in one pull at Mt. Cole, Vic, for GWM Water
• Preferred applications: Rehabilitation of pipes in sensitive environments such as cultural heritage sites, city centres, under railway tracks, roads or rivers
Awards:
• ASTT Trenchless Rehabilitation Project of the Year 2019 for an emergency rehabilitation under Biggera Creek on the Gold Coast. Thanks to the combined material and human resources of various Primus Line installation partners, the rehabilitation was completed in just one working day.
• Infrastructure Project Innovation at the AWA VIC Water Awards for the Mount Cole 2022 project in Victoria. This involved the rehabilitation of almost 1400m of raw water pipeline in a sensitive area that is difficult to access.
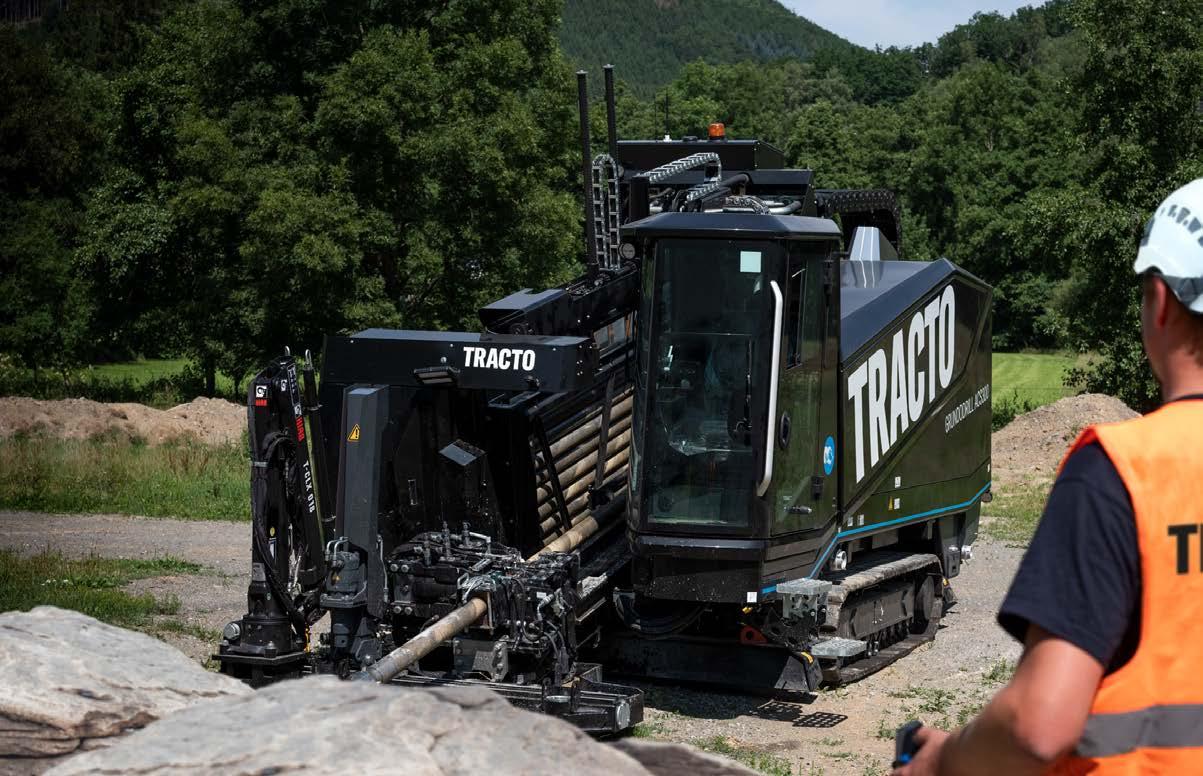
Trenchless project successes in Victoria
Trenchless Australasia takes a look at some innovative and award-winning projects in the region.
Trenchless methods were used across a range of projects in Victoria in recent months, with plans for more in the pipeline.
New 4.5km water main will last 100 years
Melbourne Water has completed a new 4.5km water main for Olinda and Mitcham reservoirs, a project that will endure for a century, ensuring a safe, reliable water supply for 365,000 customers.
To mark the completion of the Kilsyth to Croydon Water Main Renewal project, Member for the North-Eastern Metropolitan Region Sonja Terpstra MP joined Melbourne Water Head of Service Enablement One Water, Sean Hanrahan, and 20 toddlers at a local early learning centre to celebrate laying the nal pipe by turning on the taps.
e toddlers present will reach 100 years of age before a further replacement of the mains will be needed.
“Updating our infrastructure is critical for maintaining the reliable service Melbournians have had for generations. ank you to the community and our industry partners for their invaluable support as we completed this important project,” Hanrahan said.
e original water mains were built in 1936 with pipes of mild steel and lead joints and lined with concrete in the 1970s to guard against internal corrosion.
e new pipes are protected with a negative electrical charge to guard against stray electrical currents from trains and trams and prevent external damage.
Hobsons Bay sewer project claims Victorian Water Award
he Hobsons Bay Main Sewer Duplication Project was recently announced as the winner of the Victorian Water Award for infrastructure project innovation.
e Hobsons Bay Main Sewer is a critical part of Melbourne’s sewer network, transferring around 30 percent of Melbourne’s wastewater to the Western Treatment Plant.
e existing sewer was rst constructed in the 1960s, located under the Yarra River between Westgate Park in Port Melbourne and Scienceworks in Spotswood.
To rehabilitate the existing sewer, Melbourne Water and John Holland built a duplicate sewer which will allow sewage ows to be diverted during rehabilitation works.
ese critical works form part of a broader Melbourne Water sewer program on a number of ageing sewers around the city.
Since February 2022, the project team has established two construction sites at Scienceworks and Westgate Park.
Tunnelling works were completed when tunnel boring machine ‘Lucey’ completed her 670m journey under the Yarra River in November 2023.
e project, which is expected to conclude towards the end of this year, was named winner of the Infrastructure Project Innovation Award (METRO) at the recent Victorian Water Awards gala dinner.
Organisers said innovation and creativity are at the heart of the Hobsons Bay Main Sewer Project delivering outstanding results in the areas of sustainability, social value and community.
Setting new benchmarks for best practice in the water industry, the project will be the rst independently veri ed net-zero carbon infrastructure project in Australia.
Suburban Rail Loop tunnelling on track for 2026 start
Tunnelling works on the Suburban Rail Loop (SRL) in Victoria are on track to begin in 2026, with trains expected to take passengers in 2035.
Clayton Road recently reopened one week ahead of schedule after a blitz of works on the SRL, which has paved the way for major construction to start over the coming weeks.
Crews have moved underground services, completed building demolition and started constructing two new open community spaces – allowing for the start of works to begin on the southern section of the SRL twin tunnels.
Closing Clayton Road ensured critical work was completed in the shortest time possible – reducing overall impacts to the community, while emergency access to the hospital was maintained.
Works in the area will continue with some lane and speed restrictions on Clayton Road in the weeks ahead.
Works have been completed in time for a community event marking Diwali on ursday 31 October and a family fun day on Saturday 9 November.
Construction of SRL is forging ahead across all six station sites from Cheltenham to Box Hill, creating up to 8000 direct jobs, with more than 1500 people already working on the project.

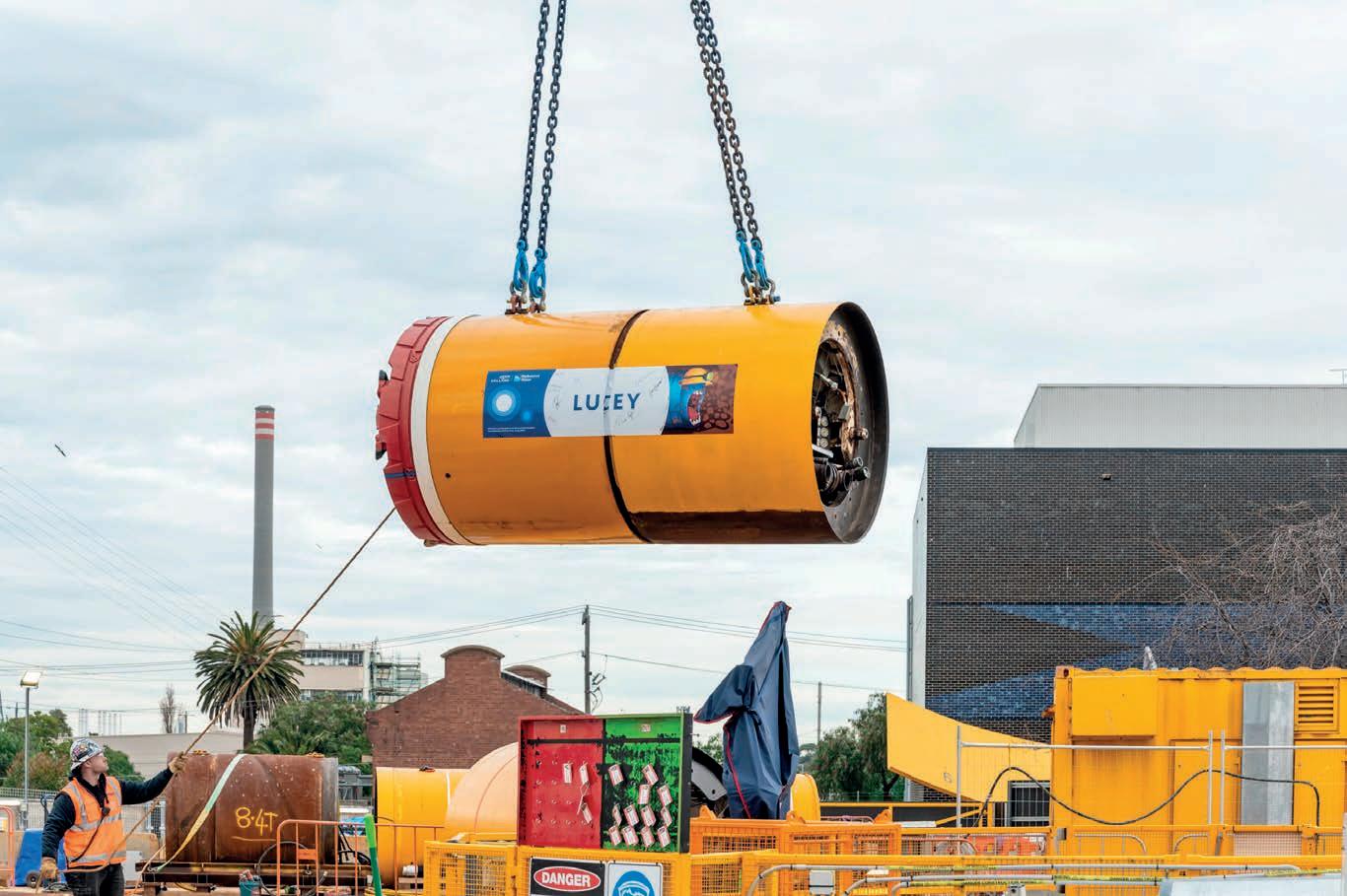
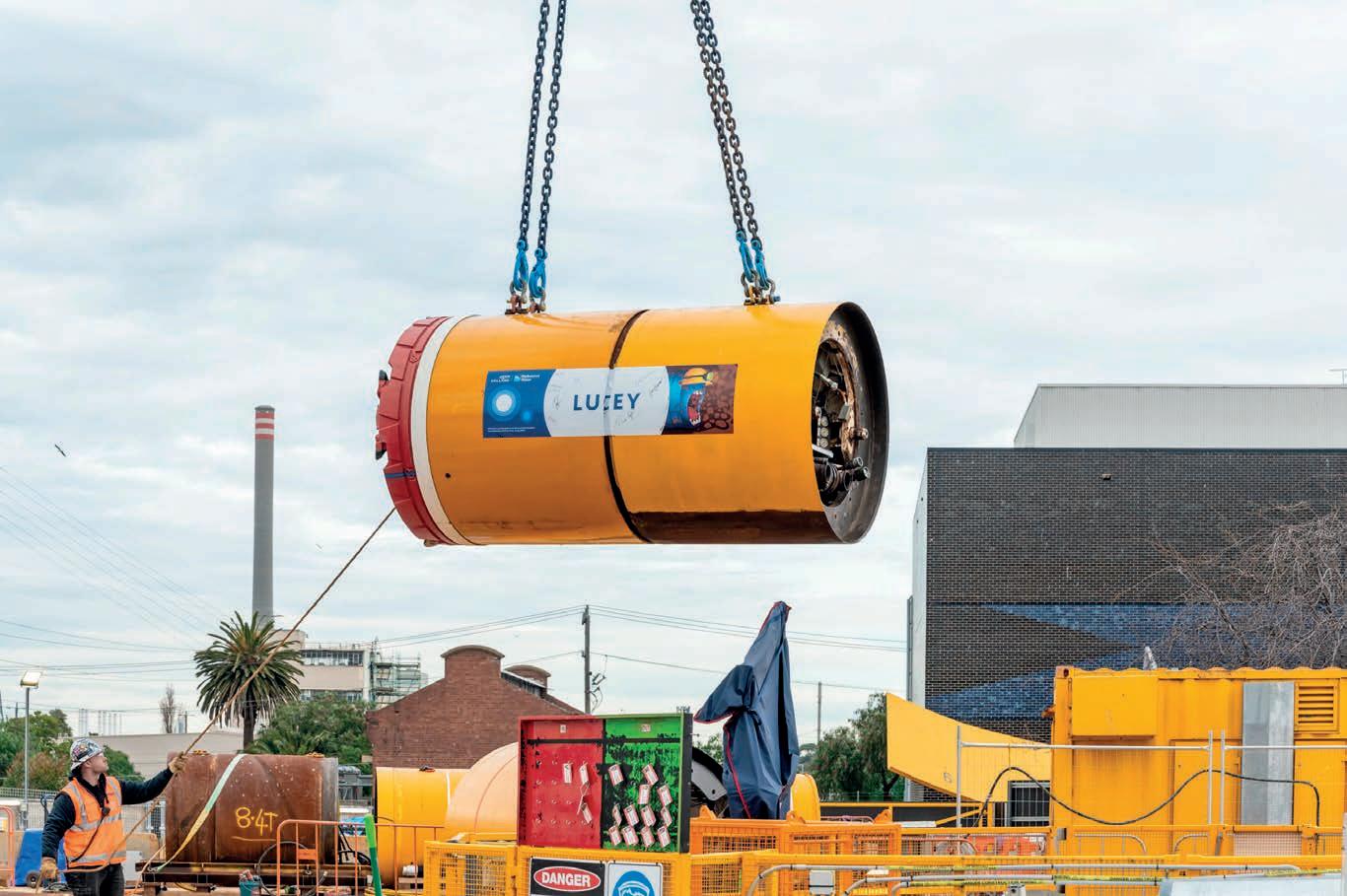

Backed by experience
Australian Custom Pipes maintains a highly trained team of experts due to its expertise and well-known status in the trenchless industry.
As a leading provider of high-quality polyethylene PE100 plastic pipes to a range of industrial sectors, Australian Custom Pipes (ACP) understands the importance of educating and training its sta .
“As a majority of our pipes are manufactured to the AS/NZS4130 standard, it is imperative that we have control of our processes and manufacturing equipment,”
ACP Managing Director Dennis Jones told Trenchless Australasia.
“ is allows us to reliably deliver high-quality products and services to our customers.”
e independent, Australian-owned pipe manufacturer has supported countless projects around the country and has continually proven to be compatible with trenchless methods of construction.
As part of ACP’s commitment to quality and its ISO9001 certi cation, the company has a full training matrix for all employees, which concentrates on key elements in the manufacturing and supply of plastic pipes.
As an example of this commitment, new pipe extruder technicians and sales team members go through a week of intense, on-the-job training and assessment to ensure they are competent for their role at ACP.
e company’s training plan also has a high commitment to safety promoted through its inhouse safety app, heads-up and toolbox talks, and face-to-face training on safety procedures and policies, which are conducted by committee members and department leaders.
Along with external training of buttwelding technicians, forklift operators, rst aiders and safety committee members, ACP strives to follow best practice in the industry to ensure only quality pipes, ttings and fabrications are manufactured.
“At ACP, training is the cornerstone of our commitment to supply only quality products to our customers,” ACP Warehouse Manager Mitchell Pitman said.
is dedication to its people has directly translated to commercial success for ACP.
Earlier this year, the company expanded its capabilities to manufacture a range of custom coils up to 500m in length.
ACP is able to provide custom coils for a range of applications, including polyethylene (PE) yellow stripes for gas pipes, PE blue stripes water pipes, PE red stripes for re hydrant pipes, PE orange electrical conduits, PE communication conduits, and compressed air piping systems.
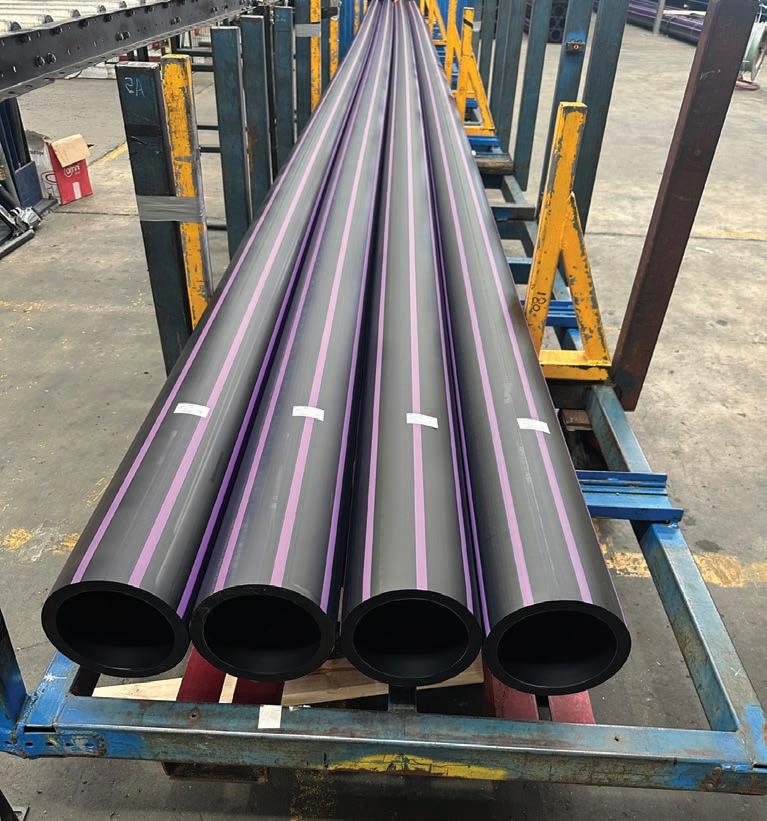
ACP prides itself on its quick turnaround times, both in customer service and manufacturing, and its products are approved to supply water authorities from Adelaide to south-east Queensland.
“As directional drilling projects get larger and longer, ACP has upgraded its pipe extrusion equipment, allowing us to deliver longer coils for our customer’s projects,” Jones said.
“We have had several customers requiring longer coils for underground river crossings, with thicker walls to suit their application.”
But even as the company grows in technical capability and reach, Jones has kept maintaining the quality of his team front of mind.
“Without ongoing training and awareness for all our sta , we could not be in such a great position as a company as we are in today,” Jones said.

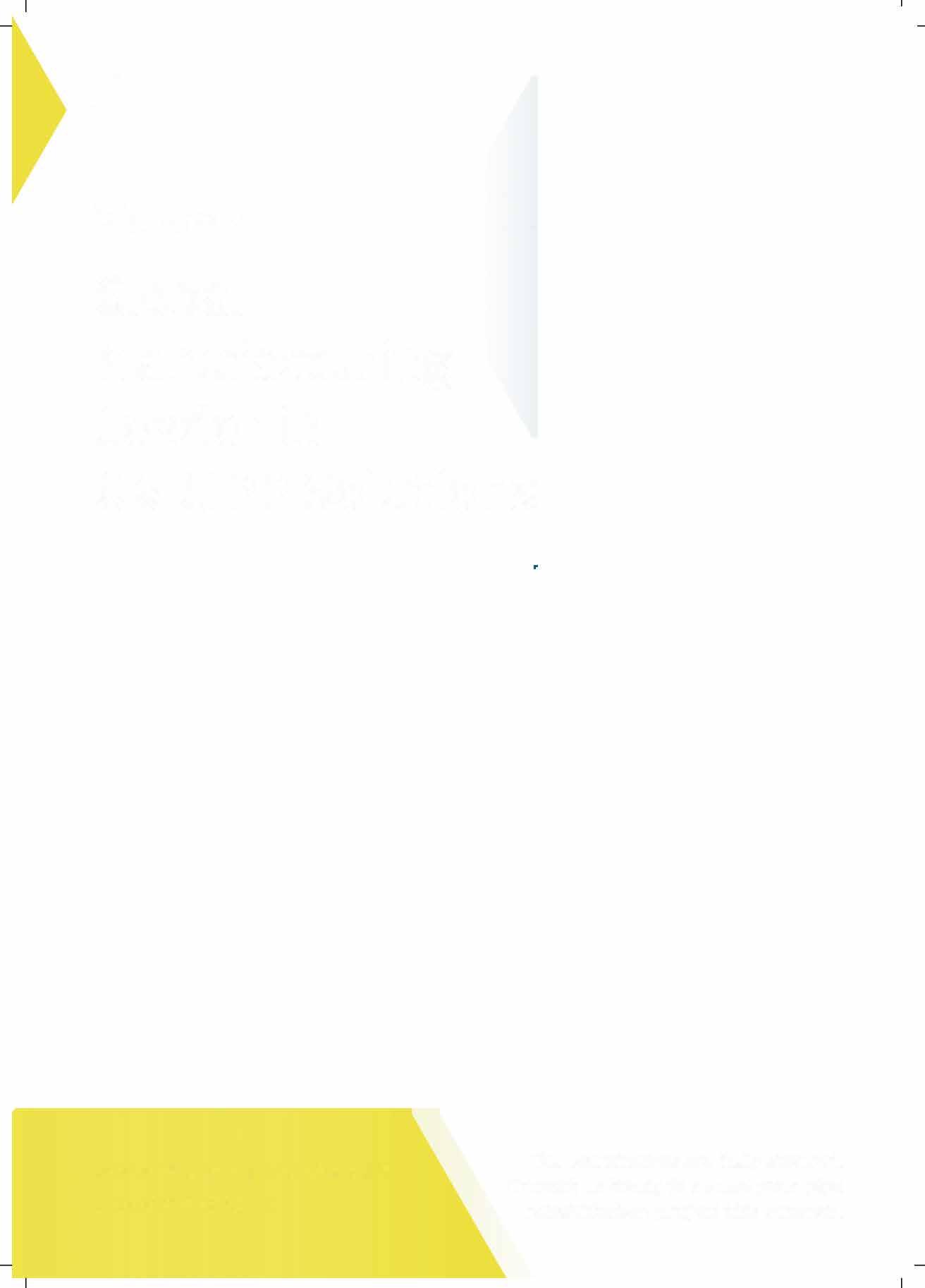

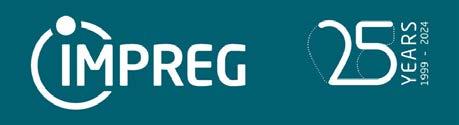
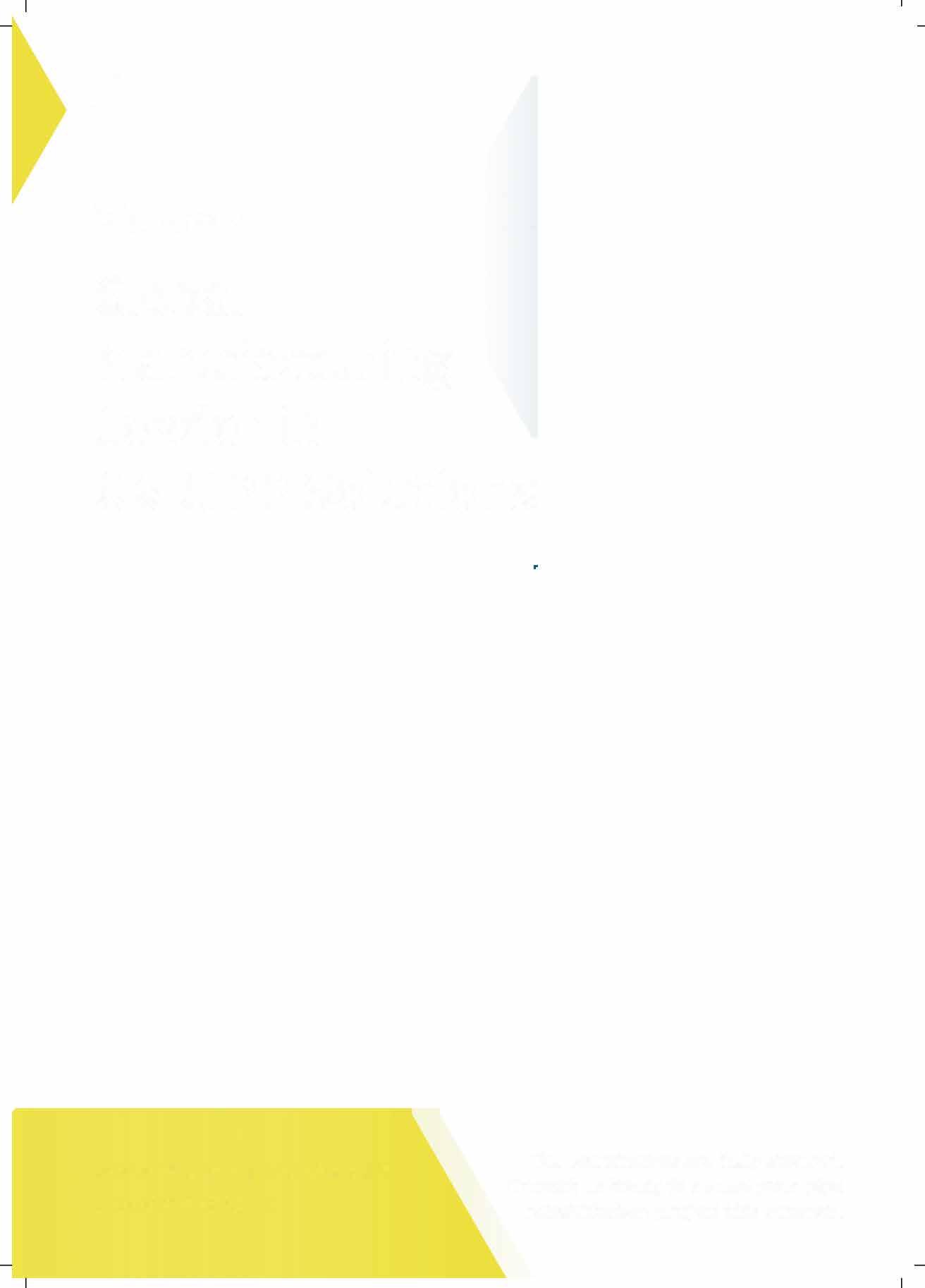

IBAK user meetings – more than just technical training
The annual user meetings IBAK organises for customers of its sewer cutting robot systems have become an essential component for training and experience exchange.
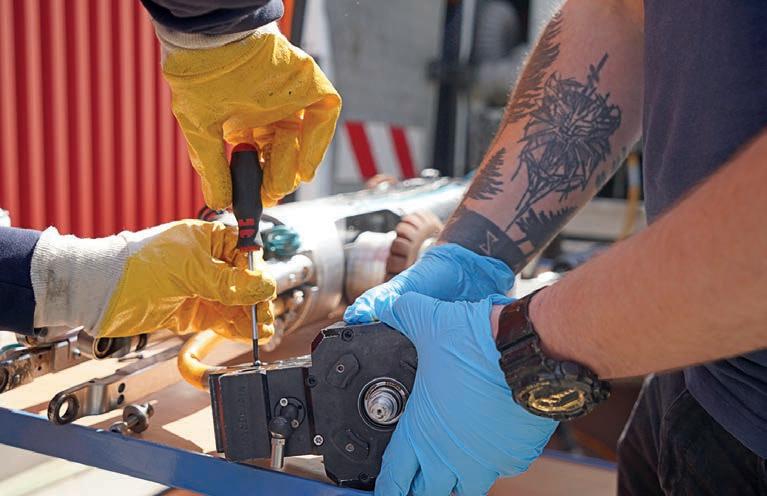
These events o er a unique opportunity to not only get to know the equipment thoroughly, but also to perform handson service tasks under expert supervision. With a well-balanced mix of theoretical and practical sessions, these meetings are not only informative but also engaging, ensuring a lasting learning experience.
Hands-on training
IBAK customers bene t from these meetings by exchanging practical experiences related to various sewer cutting tasks while learning from one another. IBAK service technicians guide the workshops, ensuring that every participant gains the necessary knowledge and skills for the e ective operation and maintenance of the systems. Live demonstrations, which are part of each event, make complex processes more tangible, enhancing participants’ understanding of the technology.
Particularly valuable are the hands-on sessions, where participants practice changing milling shaft seals and replacing hoses, nozzles, and wipers on observation cameras. Service work on the trolley is also covered in detail, enabling customers to maintain their vehicle systems independently and handle minor repairs on their own.
Comprehensive training
In addition to the technical aspects of the cutting robots, the operation of both the
electric and pneumatic cutting systems is thoroughly explained. From correct air pressure management to battery maintenance, no detail is overlooked. is training not only helps participants understand the technology but also teaches them how to use it e ciently.
Software is another crucial element of the training. IBAK demonstrates how participants can streamline their daily work by using modern digital tools to reduce paperwork. e training focuses on essential steps for digitising and optimising work processes, enhancing not only technical skills but also operational e ciency.
Building customer relationships
IBAK places great importance on customer relationships, which is re ected in the personalised support sessions o ered at these meetings. Each event provides a platform for direct interaction with technicians, allowing customers to address speci c questions and challenges. is personal dialogue helps resolve technical issues and strengthens long-term collaboration between IBAK and its customers, fostering a partnership that extends far beyond the use of the equipment.
Looking ahead
A special highlight is scheduled for the rst quarter 2025 when IBAK will host an open house at its Australian branch. Here, the successful format of the user meetings will
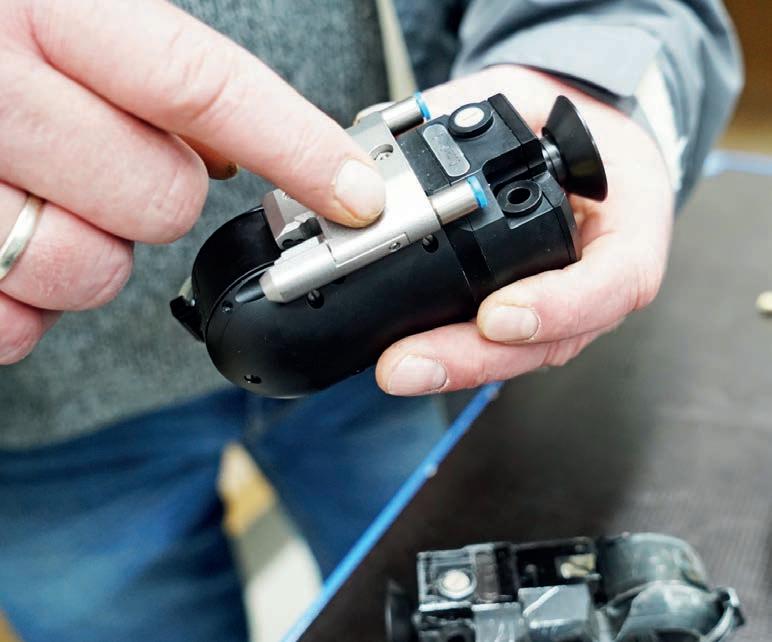
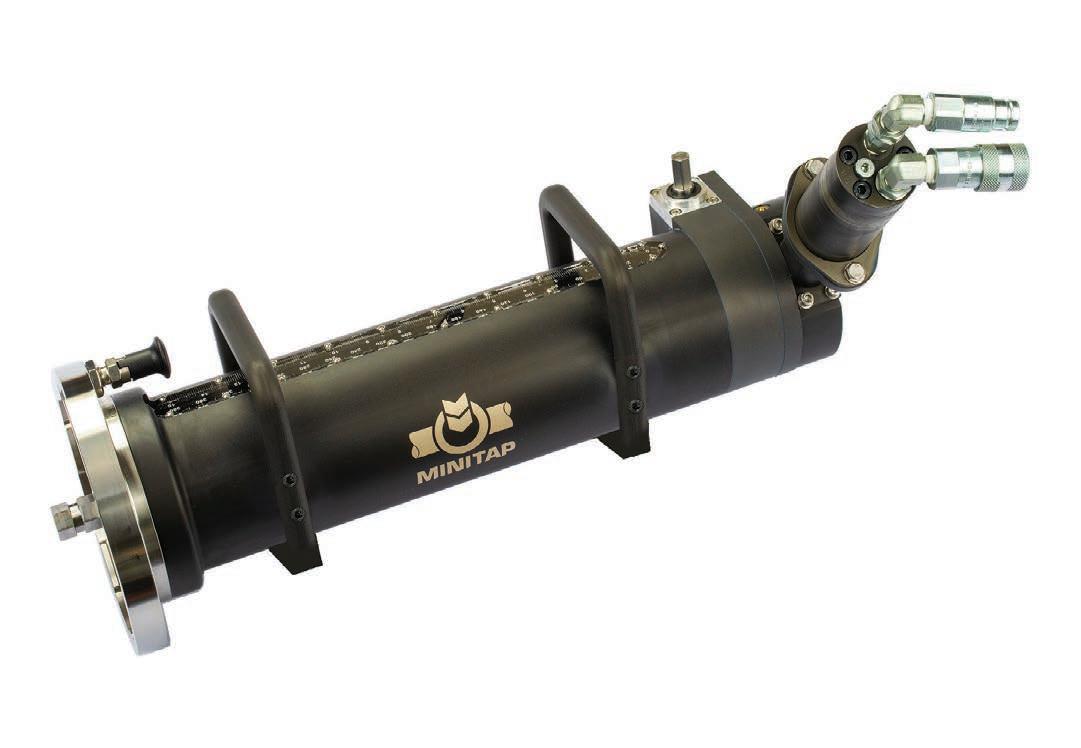
be continued, providing customers with a valuable opportunity to gain direct insights and bene ts. e event will feature the introduction of the new MicroGator 150 Air – an innovative cutting robot that sets new standards with its advanced pneumatic system. Participants will have the chance to see the MicroGator 150 Air in action and receive detailed training on its operation and maintenance from IBAK technicians.
Registration for this event is already open. Interested customers are encouraged to secure their spot early to take advantage of the latest advancements in milling technology and connect with other users and IBAK experts.
IBAK’s user meetings are much more than technical training sessions – they are an essential part of customer support and provide an ideal platform for knowledge exchange. By working closely with IBAK’s technicians, participants learn how to operate their milling robots e ciently and maintain them independently. e practical sessions and focus on individual questions make these meetings a valuable experience for any user. With the upcoming open house in Australia, IBAK demonstrates its commitment to customer service on a global scale, reinforcing its dedication to staying close to its clients.
Sign up now and secure a spot at the event.
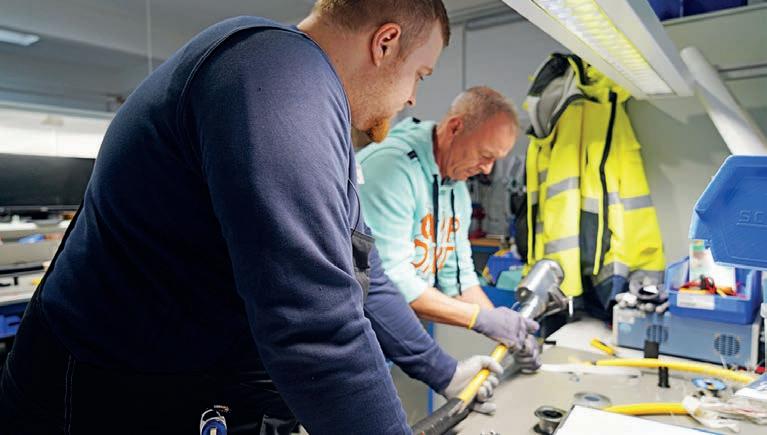
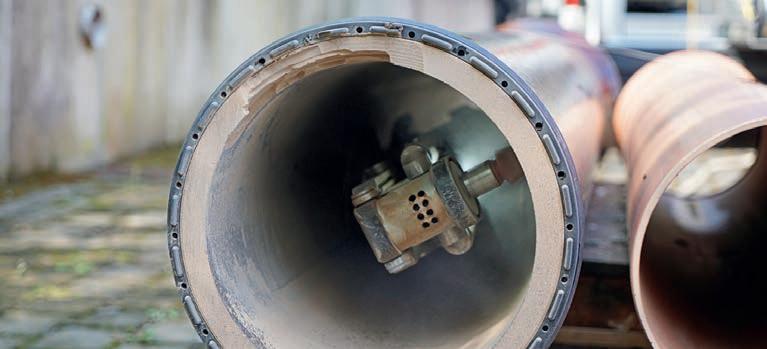
The world’s most compact hot
tapping machine
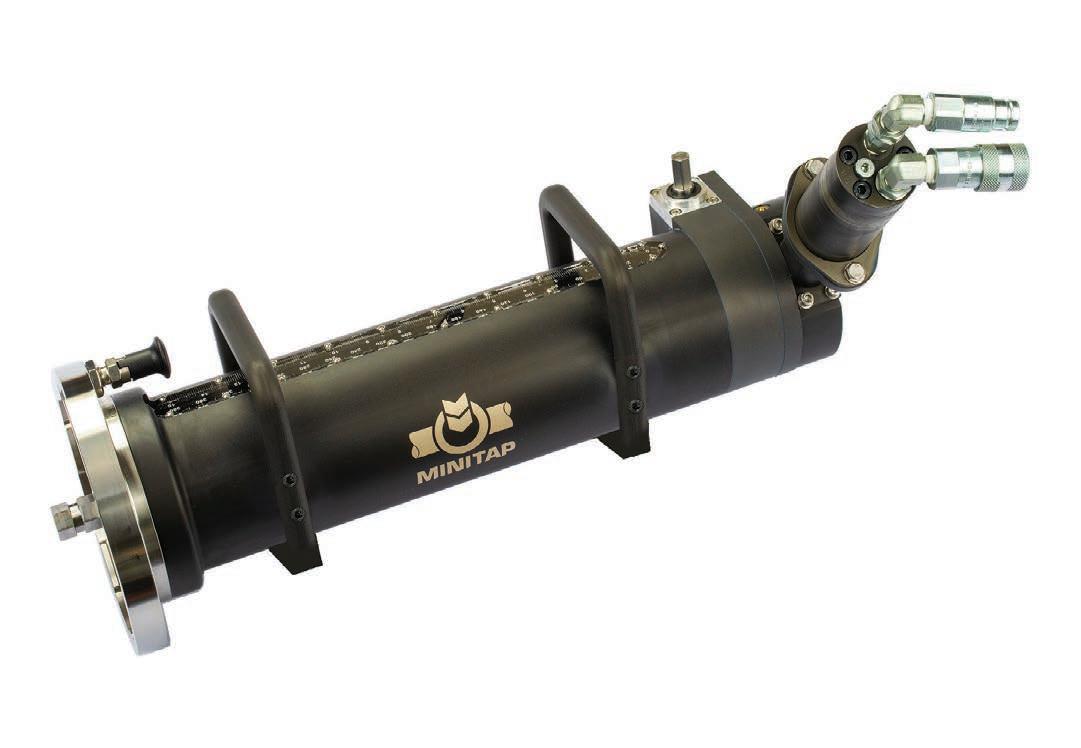
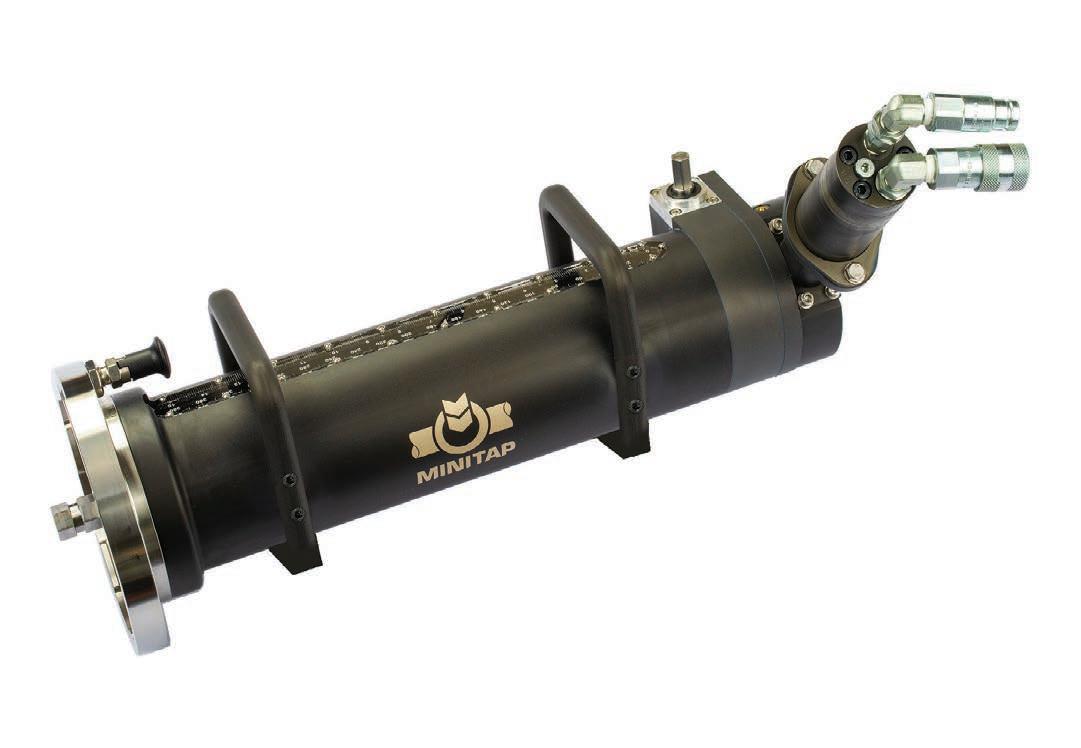
Minitap’s patented technology provides a portable, robust and safe hot tapping solution for large offtake hot tapping in confined space environments
• Advanced cutter designs
• Comprehensive training program
• Local service & support
• Designed and manufactured in Australia
Built on trust
Channeline is supporting customers with on-site training and supervision to ensure the perfect installation of its lining systems.
In a saturated global market, standing out can be a challenge. But since the 1980s,
Channeline has distinguished itself in the pipeline sector for its bespoke structural glass reinforced plastic (GRP) lining systems.
anks to the high quality and versatility of this technology, Channeline has a lining solution for almost any pipeline problem.
is has seen the company’s unique multisegmental GRP liners nd their way into major infrastructure projects all over the world.
But quality isn’t the company’s only de ning feature. Education and training to ensure the seamless integration of its products is a philosophy baked into the business model.
To learn more about this unique approach, Trenchless Australasia sat down with Channeline Quality Assurance and Quality Control Manager Dev Chelot.
“ e entire team shares the same vision: the end goal is to make sure that our liners meet and exceed the requirements of the contractor market,” he said.
To achieve this end, Channeline employs a variety of in-house and on-site training and
supervision for all of its sta and customers.
“Our own technical sta require proper training on how assembly needs to be done. is covers everything from assembly, inspection, quality assurance and quality control methods, as well as repair and maintenance procedures,” Chelot said.
“We also replicate this training on-site for our customers, helping their installation team customise the product to the site requirements, and teaching them the dos and don’ts to make sure that everything is perfect.”
Chelot, who is also Head of Research and Development at the company, recently travelled to Los Angeles for a mock installation of Channeline’s multi-segmental GRP lining system for a customer.
“I went to help train and supervise the contractors on how the assembly needs to be done,” he said.
“ e training covered many things, such as how the structural adhesive needs to be applied, what kind of resources are required, ensuring that the assembly is taking place smoothly, and identifying any issues during
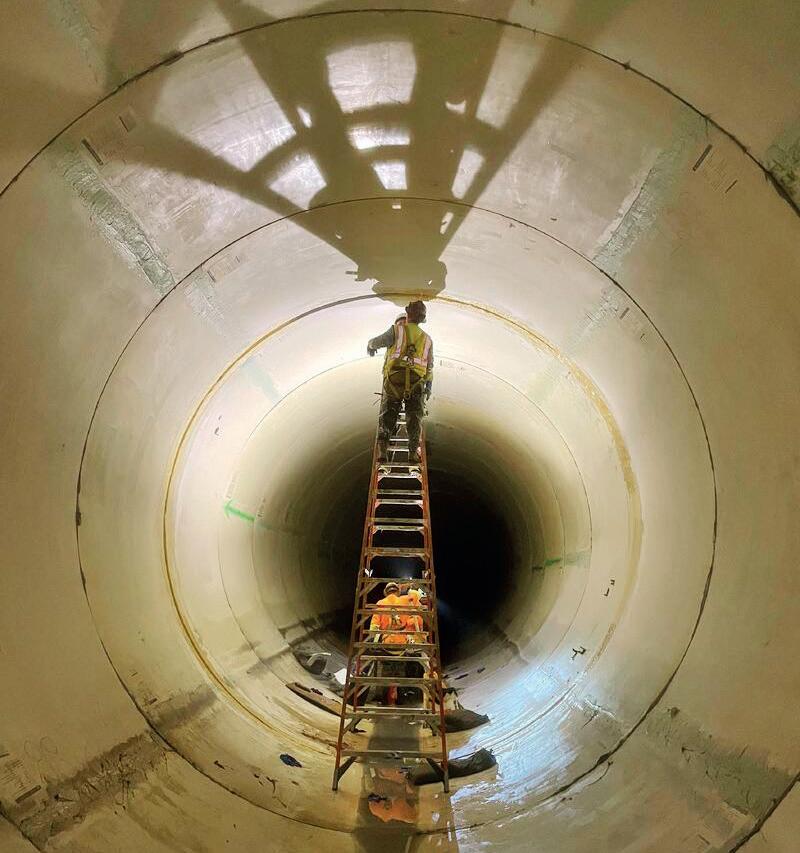

the process,” Chelot told Trenchless Australasia “After the mock test was done, the end client cut samples from the pipe for testing, and everything went well. at same contractor crew will also be the one to deliver the nal project.”
Chelot said that this on-site support isn’t a selling point of the Channeline product, but rather a part of the company’s responsibility.
“I think it’s very important to understand that there’s a relationship between the contractor and us as a manufacturer,” he said.
“Channeline develops all di erent kinds of solutions for pipeline rehabilitation, but there would be no purpose to that if we weren’t able to ensure our solutions were being delivered e ectively.
“It’s all built on trust, and we want to continue to build on that relationship.”
For more information, visit channeline.com
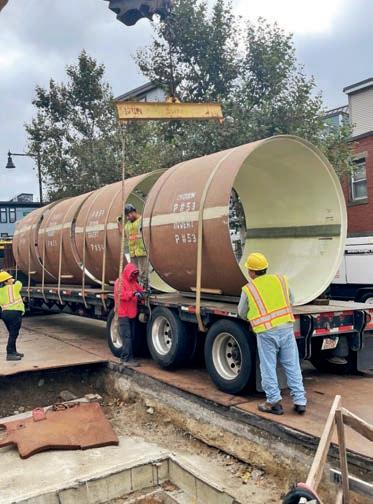
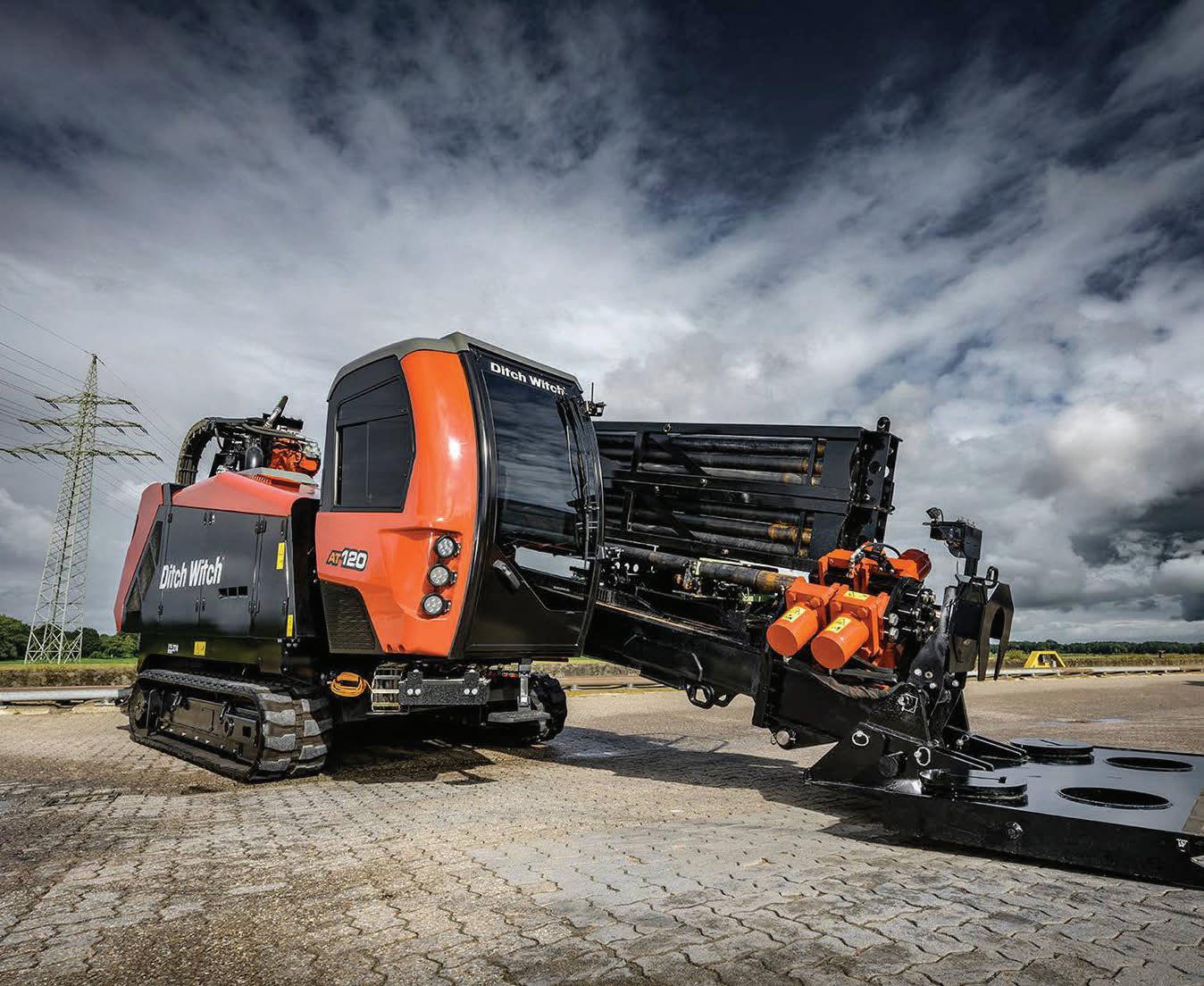

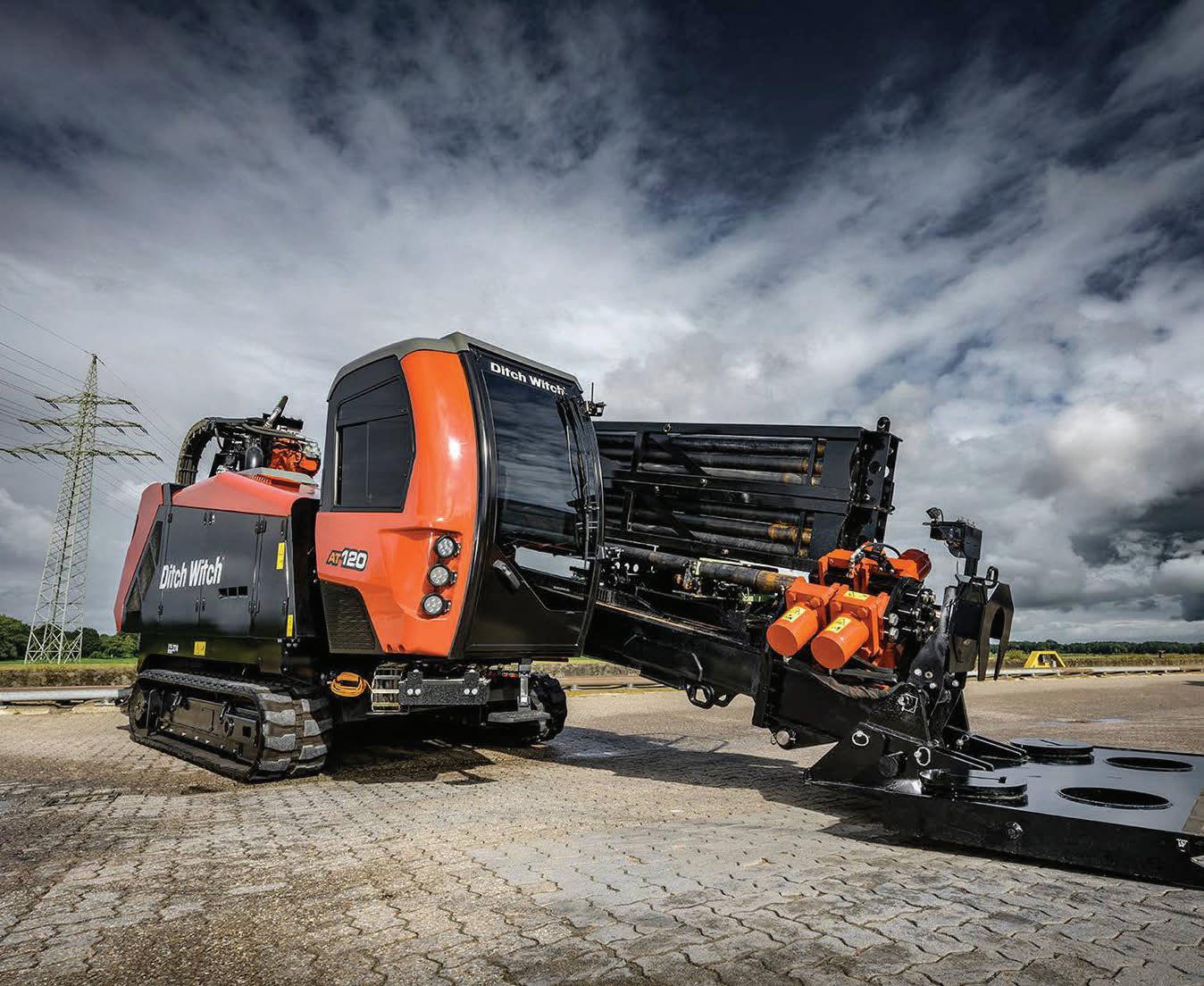
TERRAIN DRILL.


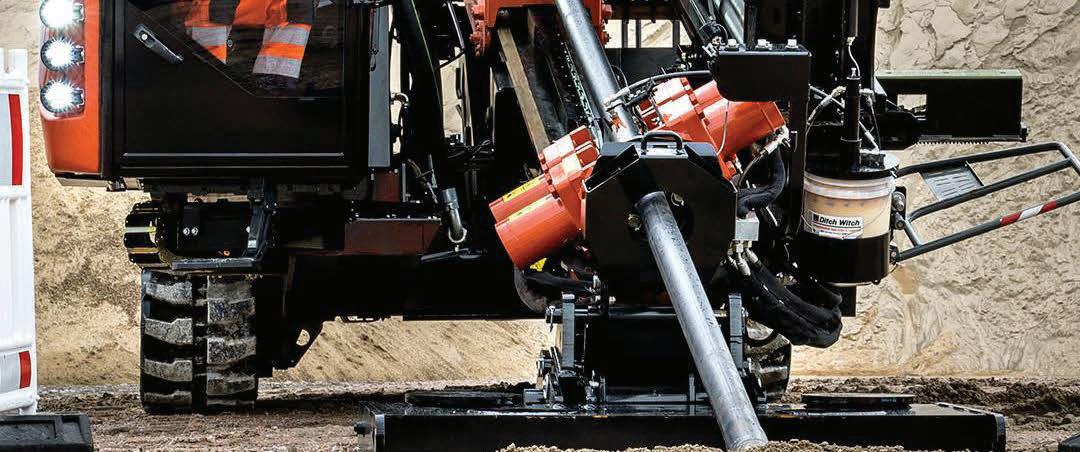
Loaded with 120,000 lbs (533.8 kN) of pullback/thrust and 15,500 ft-lbs (21015 N·m) of rotational torque, the AT120 not only opens you up to new types of jobs but moves through long bores and large diameter installs with eye-popping power.
Featuring All Terrain technology, a 280-hp (209 kW) Cummins® engine that reduces environmental impact without losing any power, and 3,000 ft·lbs (4067 N·m) of inner rotational torque providing a 50% increase over its predecessor the AT120 provides additional power to drill through the toughest terrain around.

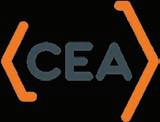

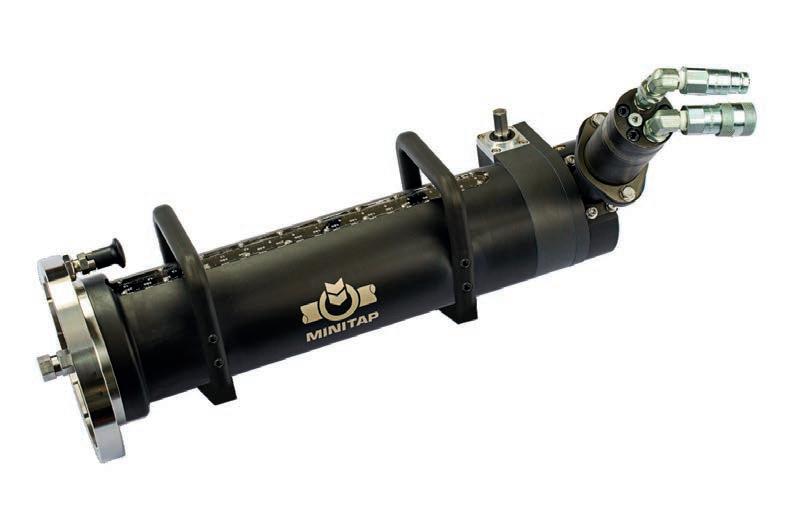
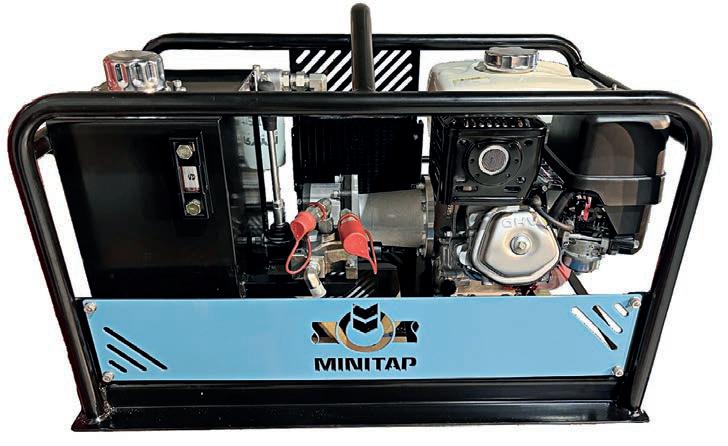
A mini solution for a big challenge
Minitap is shaking up the hot tapping sector with its compact and cost-effective solution.
As civil infrastructure develops, pipeline projects have become increasingly complex. Often, due to high-density residential areas and features such as highways, working space above the ground is limited. But the story below ground is no less convoluted.
e modern urban environment features an entire spider’s web of utility lines beneath the ground, which in many cases run parallel to one another. ese cramped conditions make it di cult to conduct construction and maintenance work such as live tapping on pipelines, which typically requires large machinery.
e only real solution to this problem is to excavate a larger working area or re-route pipework, which signi cantly adds to the time and cost involved for these projects. at was, until Minitap came around.
While conventional hot tapping machines are equipped with an elongated drive shaft that makes it di cult to t these machines into con ned spaces, Minitap is designed to t and operate in just a 1m¬2 area.
Minitap allows for large o take hot tapping (up to 200mm) in standard low pressure (up to 1000 kilopascals) pipes. It was designed speci cally for the water utility industry but can also handle other utility service pipes such as gas and chemicals.
Minitap o ers over 400mm of cutter travel from a 600mm machine length, making live
tapping work more compact and e cient than ever.
As Minitap Managing Director Ben Worst puts it, Minitap is ideal for service contractors delivering a high frequency of large o take tappings.
“ e crux of it is that Minitap is a tool designed by contractors for the contractor market,” he said.
“E ciency is one major aspect of the product. It’s highly mobile, requires smaller excavations, makes for a quicker job, and delivers a consistent result every time.
“Cost of ownership is another key area. Minitap is low maintenance, robust, and can handle all sorts of outdoor conditions – it can take a beating.”
Minitap is hydraulically driven, removing the risk of electricity from often waterlogged excavations. is both supports the compact design and further enhances user safety.
Minitap, and all of its individual components, were developed as a complete solution.
e entire suite of components, support and various training options are o ered in a singlesource support model.
While its primary function is making new connections, Minitap can also be used to support several ancillary services such as CCTV inspection, leak detection, and the installation of new valves and hydrants.
To compliment the super compact design of the machine, Minitap utilises custom-designed cutters, which it uses to handle a range of piping material including cast iron, ductile iron, steel, reinforced concrete, asbestos, PVC, and MDPE.
“Most cutters on the market are developed for concrete cutting in more of a construction environment,” Worst said.
“But in the world of service contracting, you’re dealing with di ering pipe surfaces and pressures, which requires a more tailored approach for optimal results.
“From the feedback we’re getting, our cutters are doing a better and faster job than other alternatives on the market. One of our customers even managed to achieve a tapping in just three minutes.”
Minitap was rst designed in 2016, with an early prototype tested and approved under the supervision of Water Corporation. Since then, Minitap has delivered thousands of hot tappings across Australia.
“ e size and mobility of Minitap has been a hit with contractors,” Worst said. “It’s allowing workers to get into spaces that are a lot smaller than what they used to be, which makes live tapping highly e cient. “One of our customers called Minitap impeccable in every aspect, from appearance to performance.”
For more information, visit minitap.net
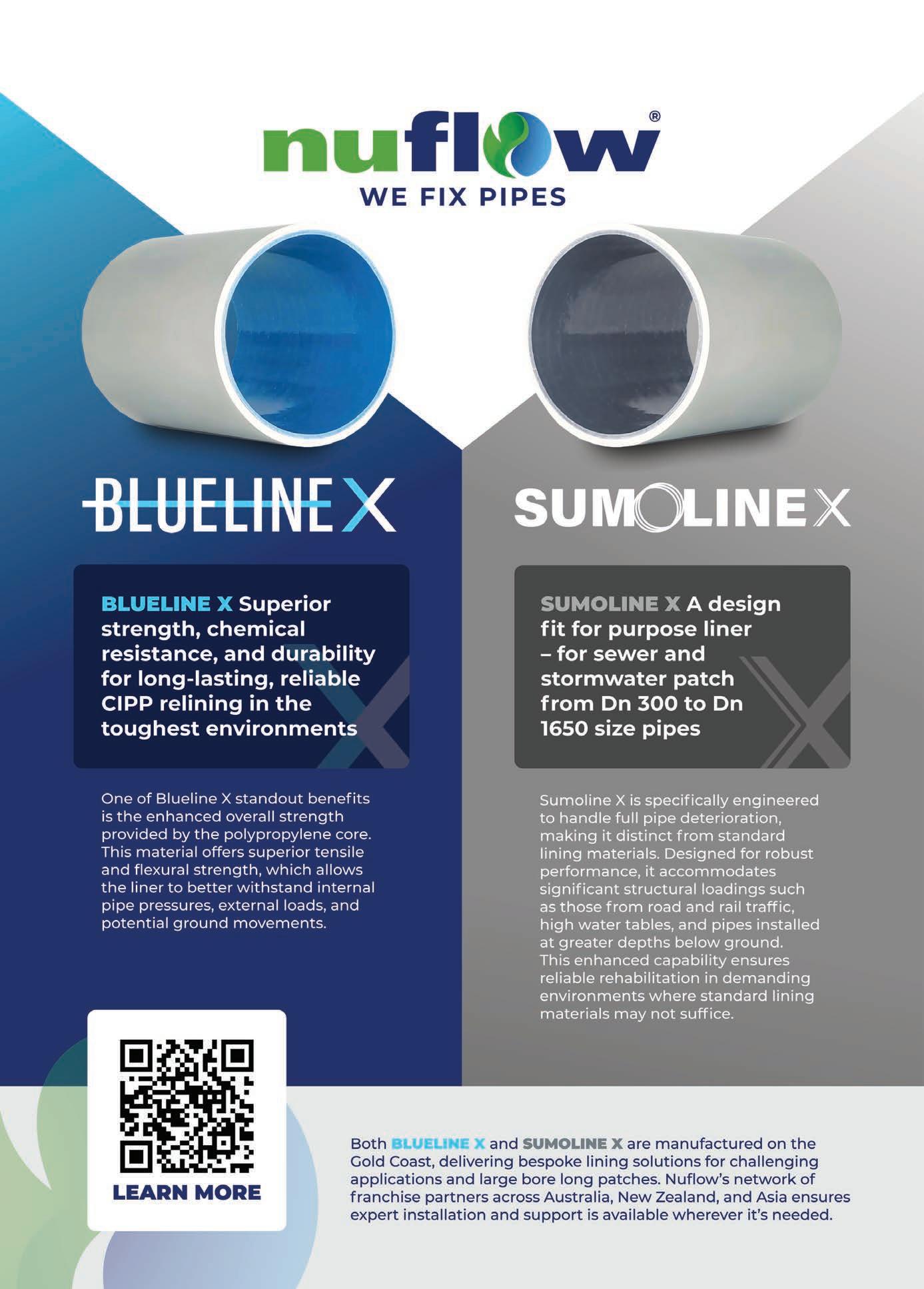
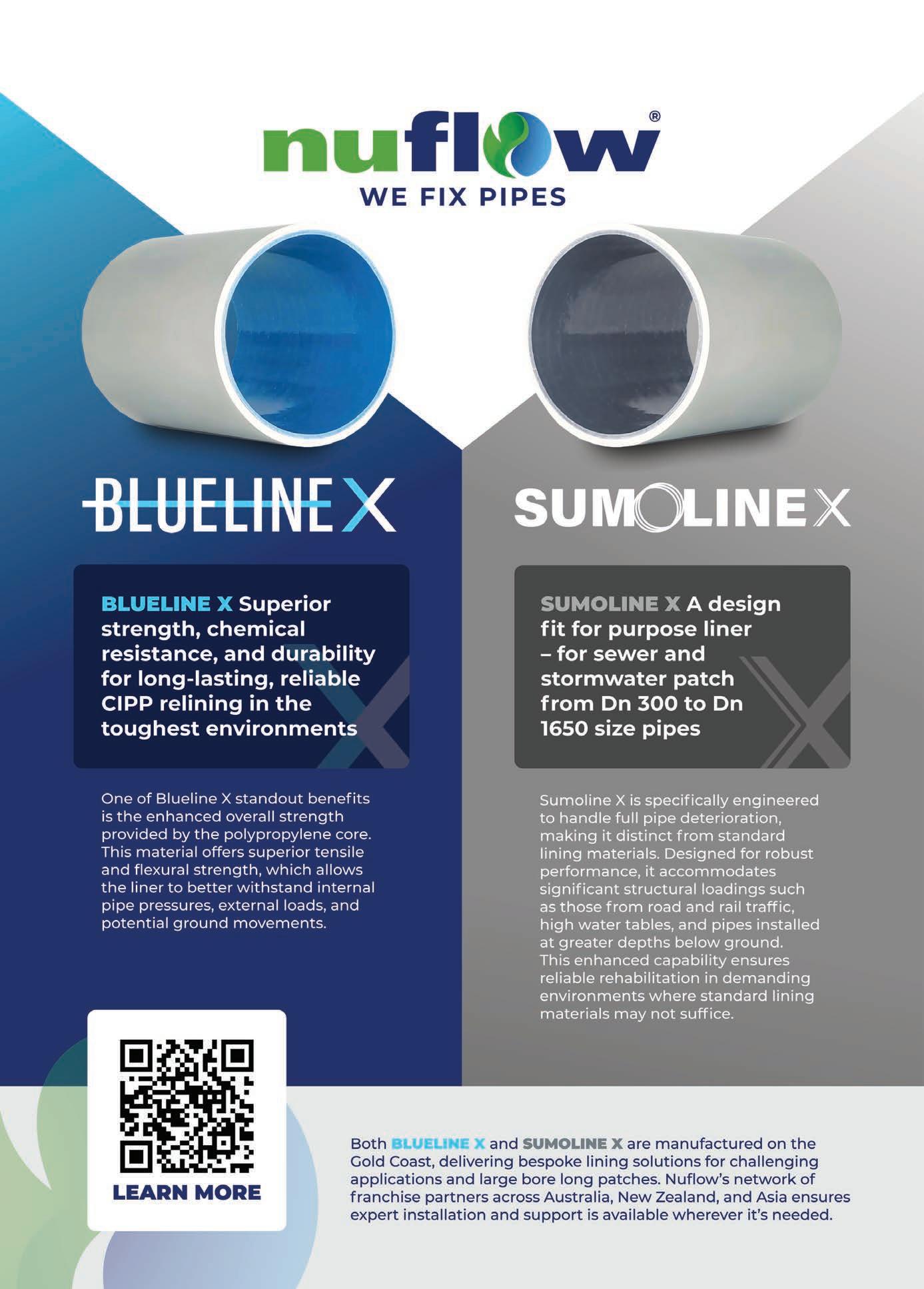
A cutting-edge revolution
Speed and accuracy are key aspects when it comes to urban infrastructure maintenance and inspection – and cutting-edge tools are providing just that.
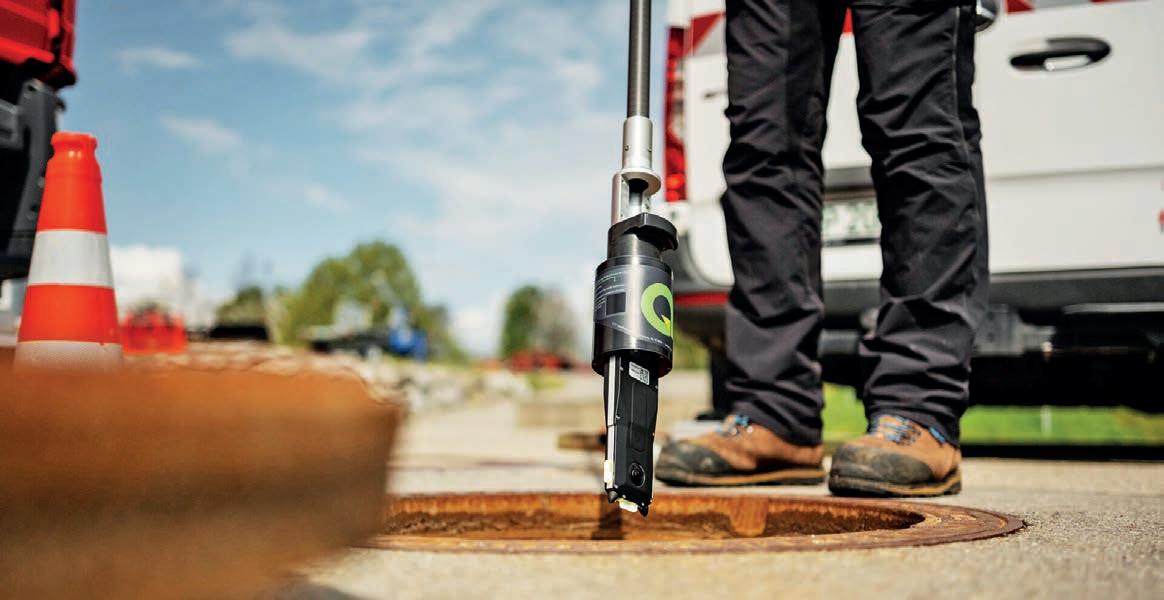
Together, two tools are revolutionising maintenance hole inspections by providing rapid, precise, and actionable data in a fraction of the time compared to traditional methods.
is is important when it comes to urban infrastructure maintenance and inspection, where time e ciency and accuracy are critical.
Cutting-edge technology from Sewer Equipment Company Australia, better known as SECA, o ers rapid and e cient maintenance hole inspections, and integration with WinCan enables seamless data management and reporting. e camera seamlessly integrates with the WinCan suite, allowing image-based inspections to be instantly transmitted to the cloud via the WinCan mobile app.
Data can be uploaded to WinCan Web, providing instant, actionable insights and enabling teams to analyse and share reports before even reaching the next inspection site. is integration enhances data analysis and reporting, with features like free movement within the virtual 360° video, ensuring a comprehensive review of maintenance hole conditions.
Features
e Quickview 360 is an automated maintenance hole inspection camera that allows operators to inspect more maintenance holes, drastically improving inspection times.
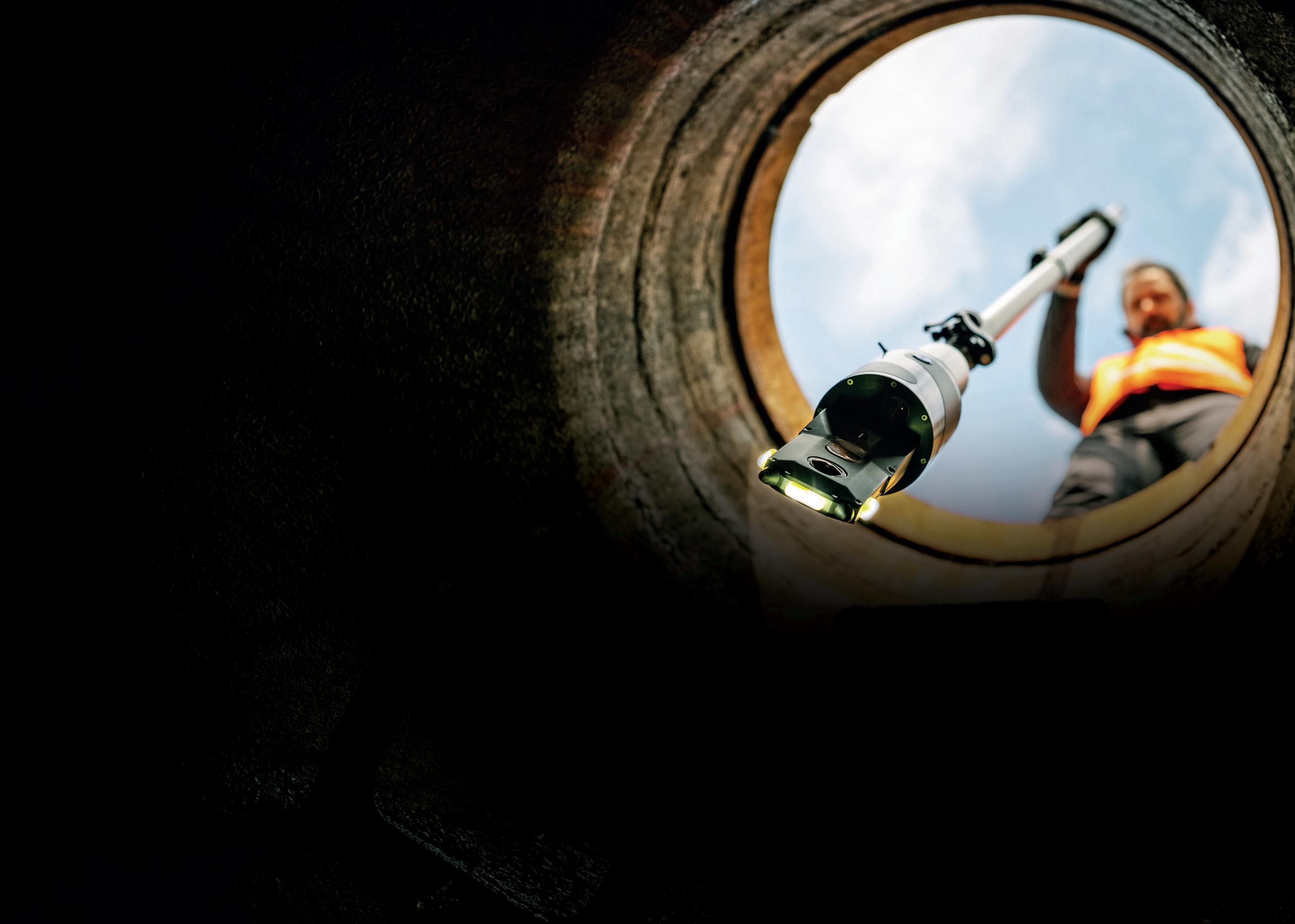
Key features include 4K panoramic video and 3D modelling capabilities, making it a powerful tool for maintenance hole condition assessment.
e system is equipped with a rechargeable battery, 360° LED lighting, and a laser range nder for enhanced precision.
e camera seamlessly integrates with the WinCan suite, allowing image-based inspections to be instantly transmitted to the cloud via the WinCan mobile app.
Data can be uploaded to WinCan Web, providing instant, actionable insights, an important feature that enables teams to analyse and share reports before even reaching the next inspection site.
is integration enhances data analysis and reporting, with features like free movement within the virtual 360° video, ensuring a comprehensive review of maintenance hole conditions.
e Quickview 360, combined with the WinCan suite, is transforming urban maintenance by providing municipalities and contractors with an e cient and highly accurate tool for maintaining the integrity of their maintenance hole and sewer infrastructure.
It enables teams to prioritise maintenance, reduce downtime, and ultimately ensure the safety and functionality of critical urban infrastructure.
In focus
Australia played host to an international event last month focused on shaping the future of infrastructure asset management, where tools that are revolutionising maintenance hole inspections took centre stage.
e Institute of Public Works Engineering Australia (IPWEA)’s annual International Asset Management Congress took place in Canberra on 28-29 November.
e event brought together international thought leaders and practitioners to engage attendees in the advancement of asset management practice locally and globally.
WinCan Managing Director Martin Hein was among the speakers at the recent IPWEA Congress.
ere he spoke about optimising the wastewater data cycle and strategies for e cient management and analysis.
is involved highlighting the Quickview 360 camera and its seamless integration with the WinCan suite of asset management software.
Speaking to Trenchless Australasia, Hein highlighted the bene ts of WinCan Enterprise Cloud.
“In today’s fast-paced wastewater industry, e cient and reliable asset management is crucial,” he said.
“WinCan Enterprise Cloud, an advanced asset management cloud portal, rede nes how municipalities and service
providers oversee their infrastructure overall.
“With a focus on work order management, WinCan Enterprise Cloud enables users to create, assign, and monitor work orders seamlessly through a GIS-based map interface.
“ e platform empowers teams to generate work orders directly from an interactive map,
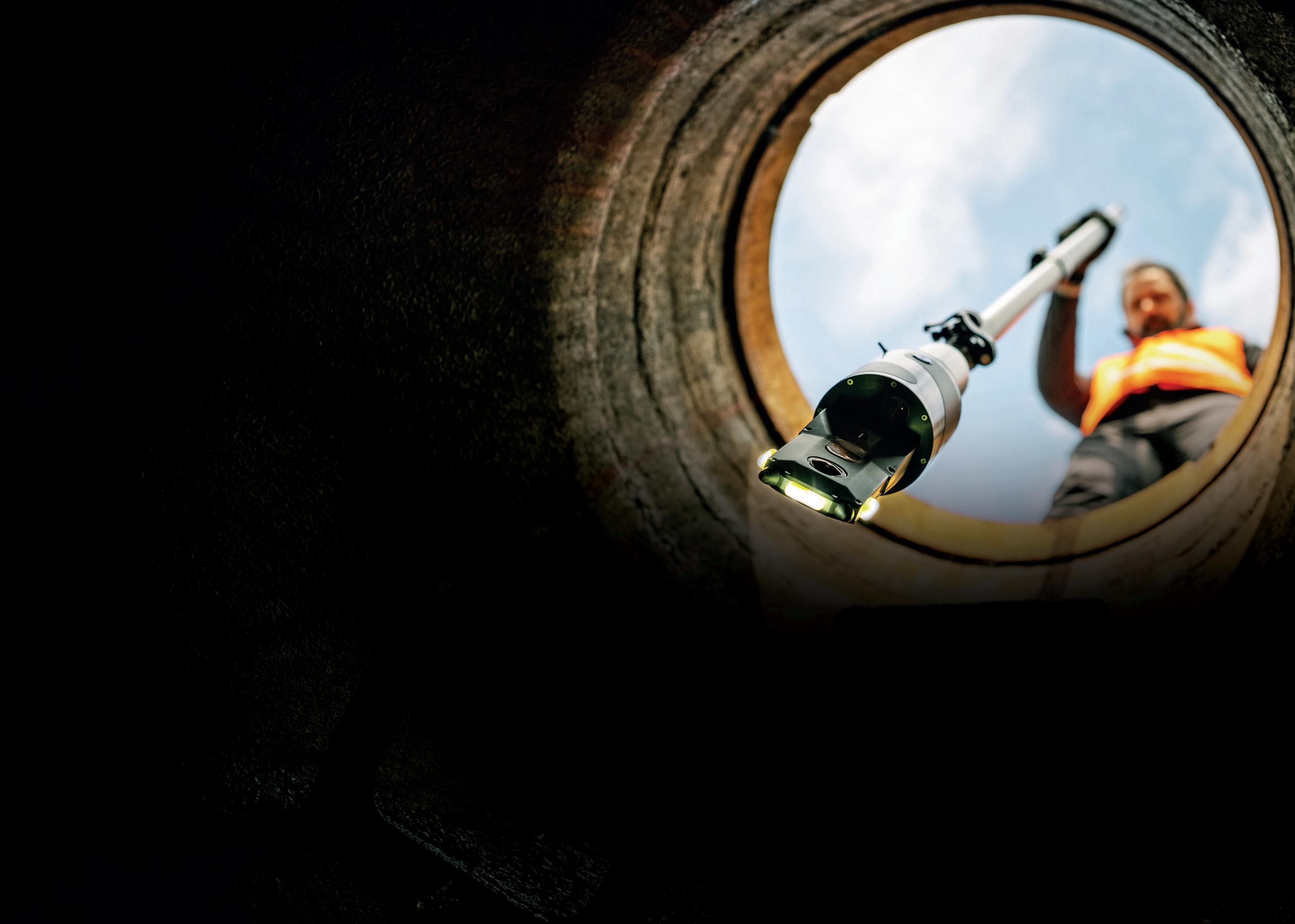
allowing asset inspections to be assigned and sent in real time to WinCan’s eld inspection software.
“ is integration allows for comprehensive condition data collection on assets, facilitating faster, more accurate reporting and follow-up.
“ e fully electronic data management
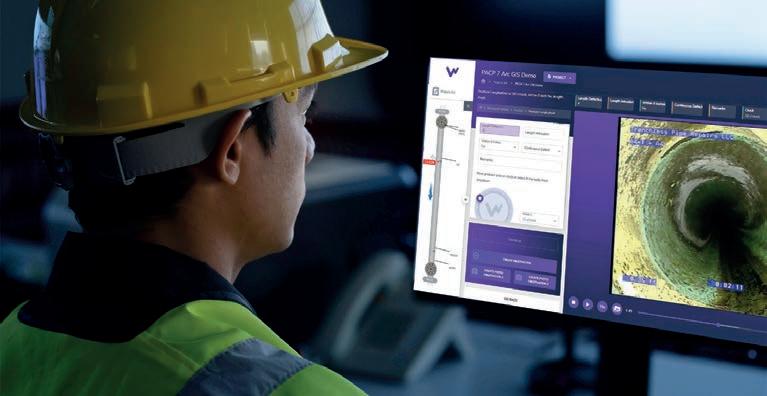
system ensures all data exchanges between WinCan Enterprise Cloud and eld solutions are streamlined through internet connectivity, signi cantly accelerating work ows while maintaining robust data security.”
Hein also highlighted key bene ts of WinCan Enterprise Cloud, including the automation of traditionally manual processes, a faster data exchange that reduces costs, and a minimised risk of data loss.
“By streamlining data collection and management, WinCan Enterprise Cloud not only enhances productivity but also o ers municipalities a cost-e ective solution that simpli es regulatory compliance and supports more informed decision-making,” he said.
“For the wastewater industry, WinCan Enterprise Cloud marks a pivotal advancement, enabling teams to focus more on strategic asset management and less on administrative tasks, ultimately driving improved service delivery and infrastructure sustainability.”
Championing the Michels values Down Under
Rowena Stockton’s expertise in health, safety, environment and quality reinforces the values of Michels Trenchless in Australia.
Michels Trenchless has been an established name in trenchless construction in North America since 1959.
Now a global leader, the company launched its Australian operations in 2021 and immediately sought people who would champion the Michels Trenchless values.
Rowena Stockton is one such professional, leveraging her expertise in health, safety, environment and quality (HSEQ) to ensure the organisation’s core values – including safety, the cornerstone of Michels Trenchless’ culture – are not lost in translation.
As the HSEQ Manager at Michels Trenchless, Stockton plays a vital role in the company, both as a member of the Australian leadership team and as an advocate in the eld.
Joining Michels Trenchless during its early days in Australia, she has been instrumental in establishing and delivering trenchless construction projects across Australia and the Asia Paci c region.
Renowned for completing some of the world’s most challenging trenchless projects, Michels Trenchless is poised to enhance the region’s trenchless construction capabilities, including Direct Pipe and horizontal directional drilling (HDD) approaches.
Michels Trenchless brings this expertise to Australia, focusing on the most technically demanding trenchless installations. e
Australian team bene ts from a substantial local eet of specialised equipment, seamlessly integrated with Michels’ globally experienced technical experts.
“ e depth of experience, global support, and the fact that Michels Trenchless is a family-owned and operated business with strong core values make it a great company to work for,” Stockton said.
Originally from Western Australia, Stockton began her career in the resources industry.
“My rst job out of university was at a gold mine, which set the path for the rest of my career,” she said.
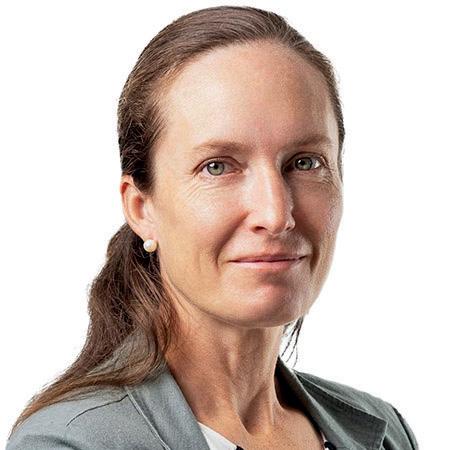
“I worked across a broad range of sectors, including consulting, mining, chemical processing, oil and gas, and agriculture, gaining wide and varied experience. I then found myself in the trenchless industry, which is where I have been for the past 15 years.
“My work has provided me with valuable experiences, opportunities to travel across Australia and work with great people.
“A good team can make all the di erence, and at Michels in Australia, we have a fantastic team that I am fortunate to be a part of.
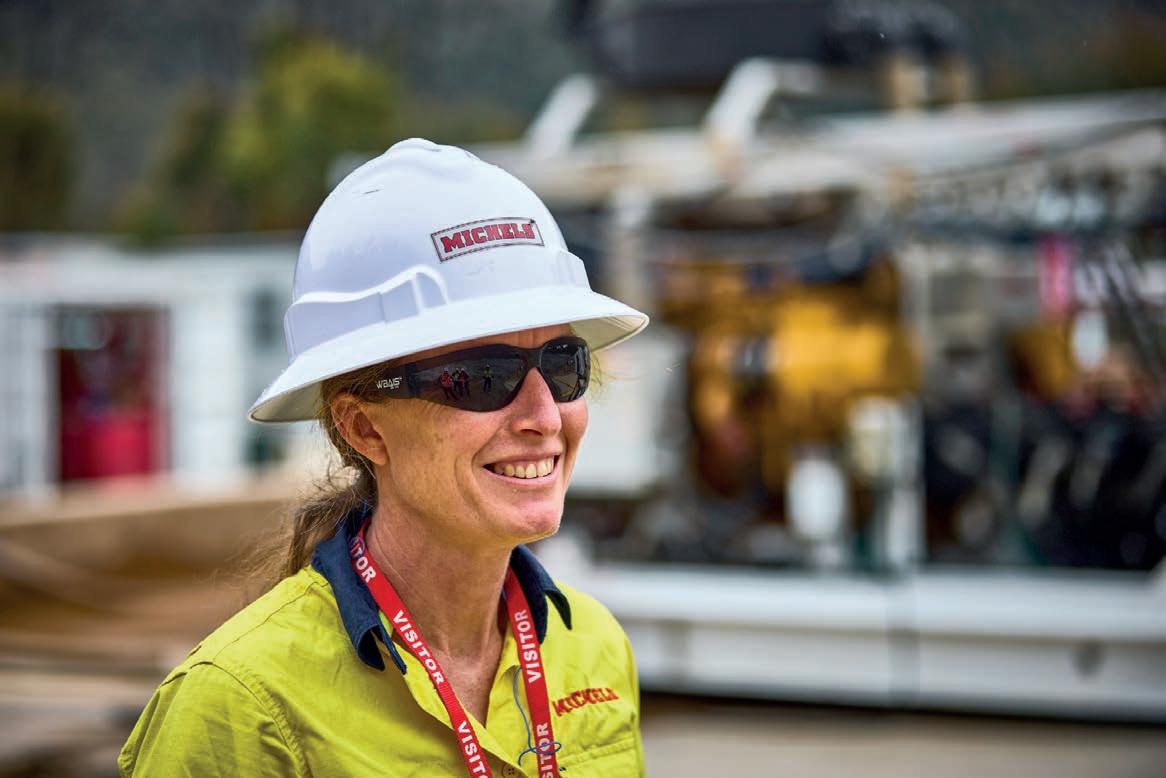

Ensuring that we have a strong HSEQ culture and that our core values are incorporated into everything we do is one of my key goals.
“I am also passionate about implementing best practices and ensuring that we protect our other most valuable asset, the environment.”
In her time at Michels Trenchless, Stockton has also played a key role in shaping the company’s strategic direction and managing operations in Australia.
She reports to and advises the General Manager, particularly on HSEQ matters, which have made great strides under her guidance.
Michels Trenchless recently completed two 2243m-long boreholes with elevation changes of a staggering 600m.
Additionally, the HSEQ management system at Michels Trenchless was recently certi ed to ISO 9001, 14001 and 45001 standards, marking another signi cant achievement for the company.
In line with Michels Trenchless’ spirit of innovation, Stockton drives forward-thinking HSEQ processes within the company.
Her leadership also extends beyond HSEQ, fostering a culture of continuous improvement and innovation at Michels Trenchless.
Her strategic insights help the company navigate complex projects while maintaining the highest standards of safety and quality.
Stockton and the rest of the Michels Trenchless team is already looking ahead
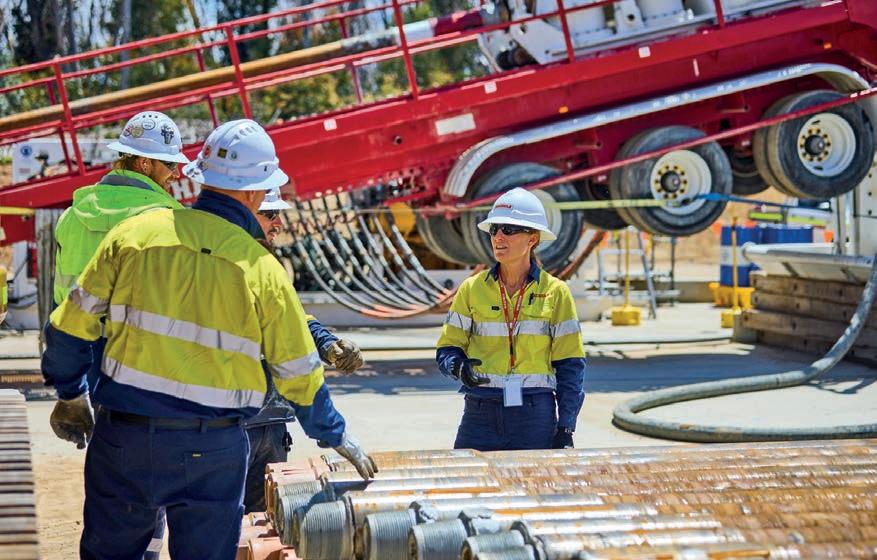
at new opportunities in HSEQ, such as the expansion of their sustainability focus, including implementing initiatives aimed at reducing environmental impact and transitioning towards net zero. Stockton looks forward to lending her expertise and passion to future Michels Trenchless’ projects as well.
“ ere is a high demand for safe, unobtrusive underground construction for
renewable and traditional energy projects throughout Australia and the Asia Paci c region,” she said. “No matter the complexity of the project, Michels Trenchless is positioned to deliver high-quality solutions, reliably and safely.”
For more information, visit michelstrenchless.com.au


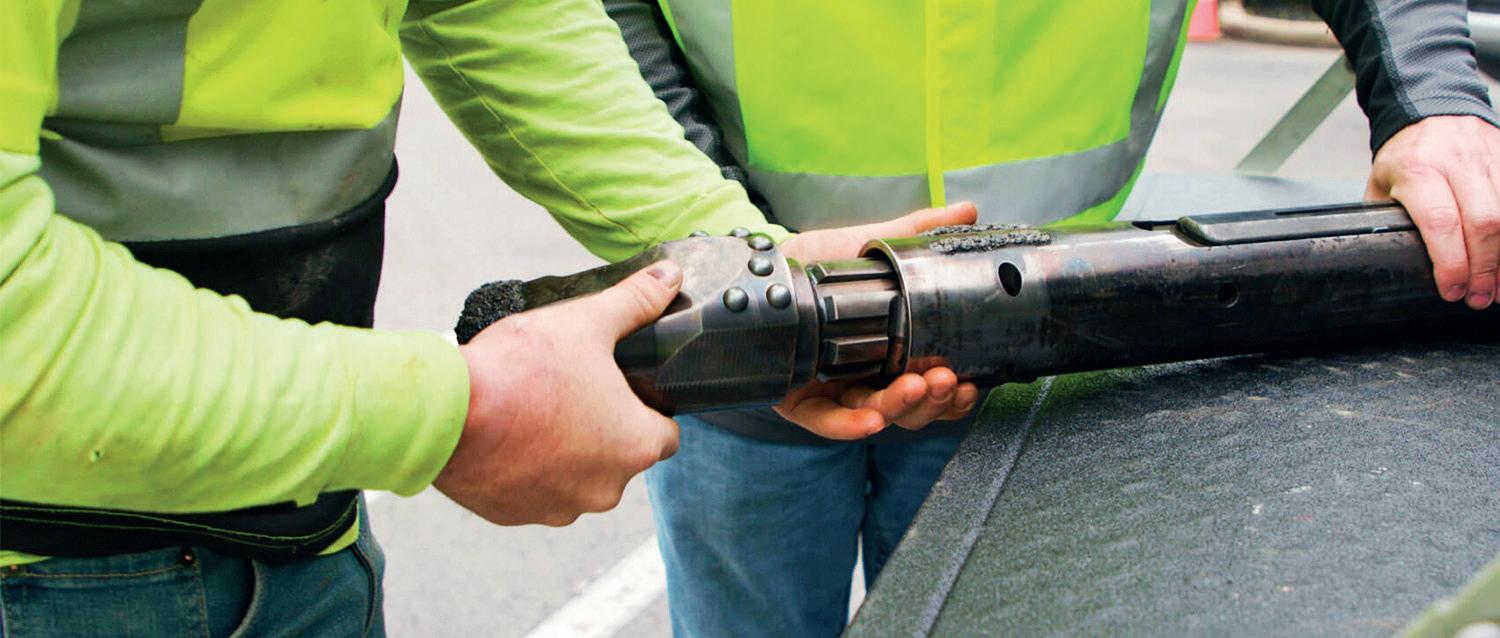
Correct HDD tooling can mean more fibre installed per day
Vermeer Cutting Edge Product Manager Cody Mecham and Product Sales Manager Chris Fontana discuss why the right horizontal directional drilling tools are needed to handle the unique conditions of a project.
With bre installation jobs, success is often measured in metres (or feet, depending on where you are).
“In many cases, if you’re not getting 305m (1000ft) per day out of a particular horizontal directional drill (HDD) crew, you’re not maximising your productivity,” Vermeer Cutting Edge Product Manager Cody Mecham said.
Time on an HDD bre installation crew can be measured in minutes per rod. Getting the most product installed during a shift starts with choosing the correct HDD tooling. ankfully, Vermeer o ers the proper tooling to handle the unique conditions you work in.
Select drill bits to match ground conditions
ere can be a tendency to use the HDD tooling you were trained on. However, using the same tooling for every job isn’t always the best choice.
ere may be opportunities to decrease the minutes per rod and wear on the drill bit with other tooling options. However, the metrics that drive the drill bit selection process can be subjective.
“Good starting points are the ground conditions and what other HDD contractors in the area are using,” noted Mecham.
You should also watch for obvious signs that the wrong drill bit is being used.
“If you’re burning a plate bit up in a couple of weeks to a month, it’s probably not the right choice for your ground conditions,” Mecham said. “You need something more durable.”
Tooling with increased durability often has a higher purchase price. ese factors need to be weighed against each other. According to Mecham, it may be more economical to purchase the right platform up front — rather than going through a higher quantity of less durable tooling.
Time not spent in the hole represents lost opportunity
“It’s not necessarily the productivity in the hole that creates the issue. It’s the time lost if you have to trip out prematurely for a worn-out bit or you’re taking the time to swap bits out between shots,” Vermeer Cutting Edge Product Sales Manager Chris Fontana said.
Vermeer helps address this issue with a complete line of Ace™ steep taper drill bits available in Standard, Pro, Pro Extreme and Premium o erings that t the unique needs of various ground conditions. e plug-style tooth design of the Ace bit allows teeth to be positioned closer to each other to help maximise carbide coverage for extended wear life.
e Standard Ace™ bit features a rounded bit face to assist steering performance. is HDD tooling is designed for softer ground conditions that are more abrasive, medium-packed soils and light gravel.
e Pro Ace™ steep taper bits are a step up from the Standard Ace bits. ey feature a semiaggressive tapered front design for penetration in harder ground conditions — from loam to
moderately aggressive cobble, sand and hardpan.
e Pro Ace Extreme bits share the same pro le of the Pro Ace bits, but they balance steerability and penetration. ey feature carbide teeth along the full edge of the bit to extend wear life in cobble, hard pan and light rock.
e Premium Ace™ steep taper bit features an aggressive tapered bit front to help penetration rates in aggressive ground conditions such as heavy cemented cobble, hard-packed soils and softer shale.
“ e decision ultimately comes down to what you can achieve,” Mecham said. “If you are not getting the life or the productivity out of the drill bits, then you creep up that food chain to get to a more premium product, such as the Pro Ace or Premium Ace bits.”
Premium offerings boost digging performance
Key design features help to di erentiate the premium products within the Vermeer HDD tooling line.
“ e Vermeer Premium housing has dual angled water ports which allow drilling uid to get toward the front of the bit,” Mecham said. “ is cleans the teeth. If you are drilling for volume, keeping the teeth cleaner is going to maximise performance. Traditional-style dirt housings feature jets that hit the back side of the plate instead of cleaning the teeth.”
In addition to the Vermeer Premium housing line, Vermeer also o ers the Armor and Ultra X3
drilling systems to target the most demanding applications. e Ultra X3 is set up to use a full o ering of plate bits and rock tooling like the Vermeer Gauntlet, Lance, Trident and roller cone bits.
“ e Ultra X3 is a premium product and can help increase your operation’s productivity,” Fontana said.
Since the Vermeer Ultra X3 uses a robust spline connection system, the HDD tooling doesn’t have to be threaded on, eliminating the need for breakout tongs to make and break torqued tooling connections. Operators just need to align the spline on the tooling with the spline on the housing, then secure by tapping in dowel pins.
e system can handle the torque of reaming directly from the transmitter housing at diameters up to 25cm (10-inches) in most ground conditions.
Pullback considerations
Pullback is one of the most important considerations when planning a bre optic cable installation.
“Many HDD crews installing bre are pulling directly by adding a puller to their plate bit,” Mecham said. “Some of them are having to slightly open the hole too. It depends on what that job looks like, whether it is bre to the home, which is really small in diameter, or whether you are pulling a couple of conduits back.”
Often the pulling eye is fastened to the bit along with a swivel that enables rotation.
“ e bene t of rotating is that you clean the hole up. You can compress the hole out to a bigger diameter or clean up what cutting might have been left in the hole,” Mecham explained. e decision on whether to pull back with the

bit or remove the bit is based on the diameter and how much annular space is in the hole.
“Our new pull back tab allows us to pull right o your bit versus removing that bit,” Mecham said.
In applications where there is cobble or sand, it is advised to use a reamer for hole integrity.
“Even if the hole is there and there is one cobble down in the hole, that can be problematic,” Mecham said. “It can potentially damage the product. One that is less of an absolute in my mind is sand. It is good insurance to pull back a reamer and make sure you can pull that product. In case that hole is lost somewhere along that patch, that reamer is going to open it up, hopefully enough that you can sneak that product past it.”
e Ultra X3 system simpli es the reaming process. e reamer can be directly attached to the housing, saving time and reducing the required space for setup. Similar to bits, Vermeer o ers a complete line of reamers, including uted reamers for ground conditions ranging
from hard pan to soft rock; the T-REX reamer for cobble, chunk rock and soft rock; Mix Master™ reamers for reactive ground conditions; and the Supreamer for aggressive cutting action and ease of pushback. All the available options for bits, housings and reamers make it possible to optimise your HDD operations for bre optic cable installation.
Vermeer even provides a tool that helps simplify the process of selecting HDD tooling with the Vermeer RigFitter HDD tooling con gurator. Simply indicate which Vermeer HDD model you are using, and the digital tool will then provide step-by-step recommendations for compatible tooling, including adapters, transmitter housings and bits or reamers, depending on whether you select pilot or pullback con guration. To help identify the best tooling for bre optic installations, work with the HDD specialist at your local Vermeer Australia.
For more information, call 1300 VERMEER or visit vermeeraustralia.com.au
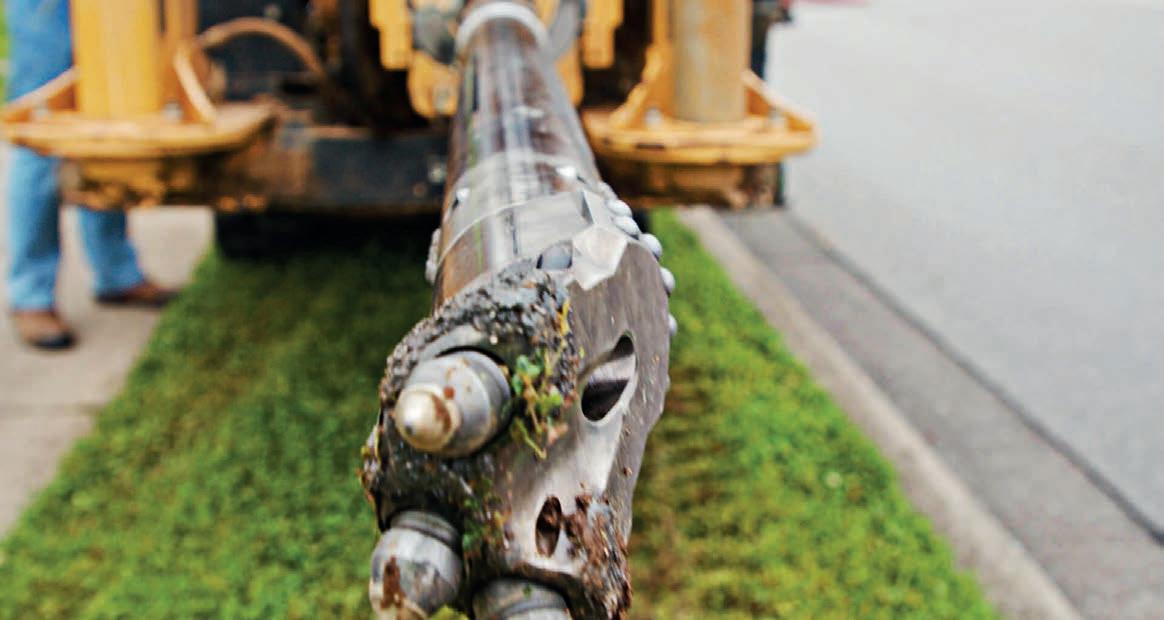
ParaTrack guides the way
The ParaTrack HDD Guidance System has been making waves in the Australian trenchless industry.
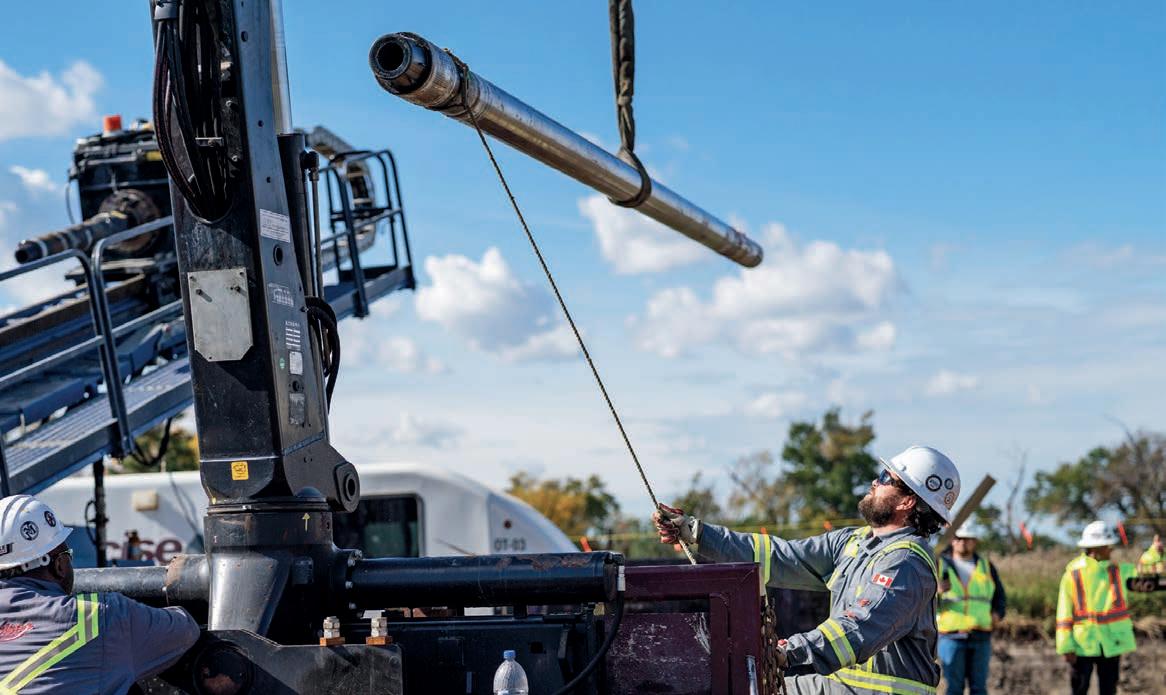
The ParaTrack HDD Guidance System is designed to navigate the toughest conditions and deliver results – and that’s exactly what it’s been doing in Australia and across the globe.
ParaTrack is a complete horizontal directional drilling (HDD) guidance system for steering, surveying, tracking and logging pilot bores, rapidly scaling up or down in capabilities according to the needs of each project.
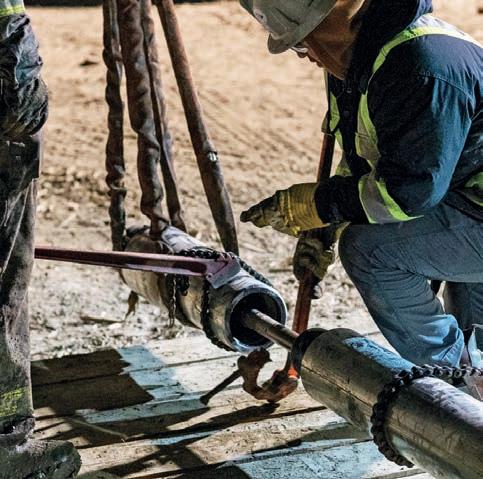
For nearly 25 years ParaTrack has been the guidance system of choice for owners of midito-maxi sized drill rigs looking to maximise the capabilities of their eet. No other largescale horizontal drilling guidance system o ers more exibility or drills more meterage than ParaTrack.
Technological advancements
ere has been an explosion of technological advancements in HDD guidance technology in recent years. However, ParaTrack stands out among the crowd with a unique selection of technologies allowing engineers exibility in their bore designs, and contractors the con dence to execute them.
ParaTrack Guidance performs four crucial roles in the drilling of a pilot bore:
• Steering – e Steering Tool provides real-time toolface to the driller, allowing the pilot to be drilled directionally.
• Surveying – e progress of the pilot is surveyed magnetically with the Steering Tool, or with the optional Gyro Module.
• Tracking – e surveyed position of the pilot can be veri ed with a P2 AC Magnetic guide wire or a portable Beacon Tracker, ensuring the calculated survey location is accurate.
• Logging – e Pressure Module is an optional accessory for monitoring annular and pipe pressure. Pressure data is transmitted in real
time and stored as a continuous log. As with all ParaTrack guidance data, pressure data may be exported for further analysis and record keeping.
At just 1.3m long and 4.45cm in diameter, the Steering Tool is compatible with a wide range of drill collar diameters, making it a suitable choice for rigs from compact models to one-million-pound maxis, and every size in-between.
e Steering Tool provides real-time information for steering the pilot bore and is an a ordable entry point to the wider ParaTrack family.
Meanwhile, the ParaTrack Gyro allows contractors to extend the interval that can be comfortably drilled without the use of secondary tracking.
e Gyro is suitable for drilling on job sites where surface access is impractical or not allowed, or in locations where surrounding infrastructure interferes with the Steering Tool’s magnetic azimuth measurement.
e ParaTrack Gyro is accurate to +/- 0.04°in azimuth and +/- 0.02° inclination, and not a ected by magnetic interference – this allows many pilot bores to be drilled with limited or no surface tracking. If surface access isn’t a problem, and especially if project tolerances are tight, P2 AC Guidance should be considered an essential part of your pilot bore plan.
e P2 AC Guide Wire is an economical guidance method that is fast, reliable, and designed to work in conjunction with a Steering Tool and/or Gyro to provide the most accurate pilot bore placement possible.
By generating a powerful, low-frequency magnetic eld from a known location, the calculated surveyed location of the pilot bore can be veri ed, maximising the accuracy of the installation.
e At-Bit Inclination Assembly (ABIA) is the industry’s only solution for monitoring inclination at the bit.
By providing inclination in near real-time measured at the bit, rather than 10m or more behind, the pilot bore’s elevation and radius can be precisely controlled.
Every ParaTrack Guidance System is fully compatible with the Pressure Module, which provides continuous recording of pipe and annular pressures.
Pressure records are stored permanently and easily exported in standard formats.
e Pressure Module is a ordable and designed to be completely rebuildable for a long service life.
In Australia, the ParaTrack Guidance system has been used on some major projects, including the Snowy 2.0 project, currently being undertaken by Michels Trenchless, a branch of Michels Corporation.
e project included a 2248m drill with a 563m vertical elevation change.
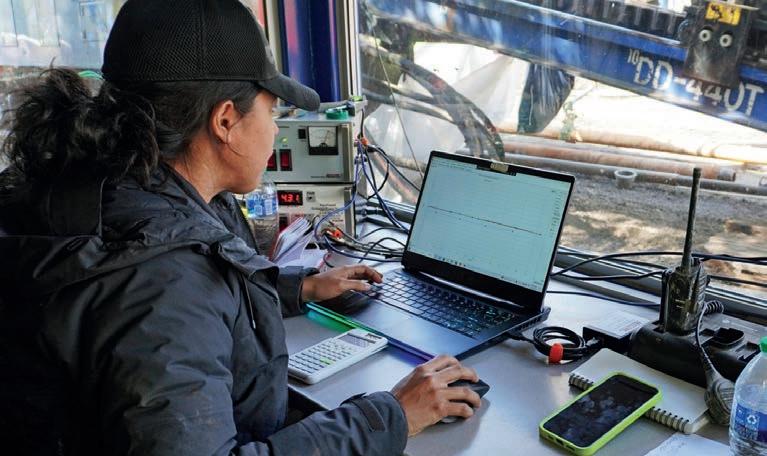
Rather than perform a conventional one-rig pilot hole, Michels Trenchless determined the pilot hole intersect method would be a better way to achieve the customer’s project goals.
e pilot hole intersect method deploys two drill rigs, one drilling from the entry side and one from the exit side, to meet at a predetermined location along the alignment.
e team used two Michels Trenchlessdesigned and fabricated rigs, each with 880,000 pounds of push/pull force. Guidance was provided by ParaTrack using a combination of the Steering Tool, Gyro Module, At-
The whole world of HDD Technology
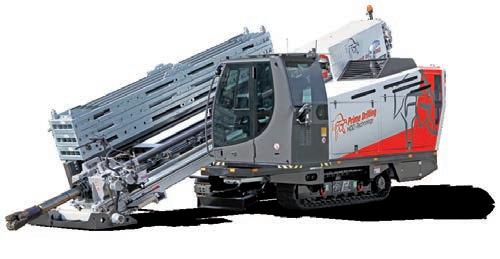

Bit Inclination Assembly, and Magnetic Intersect technologies.
e pilot hole intersect method allowed the team to manage uid pressure in the drilling column and from returns; contend with a highwater table, minimise push forces; and facilitate steerability through hard and fractured rock.
e HDD project supports Snowy 2.0, one of the largest renewable energy projects under construction in Australia.
For more information, visit vectormagnetics.com
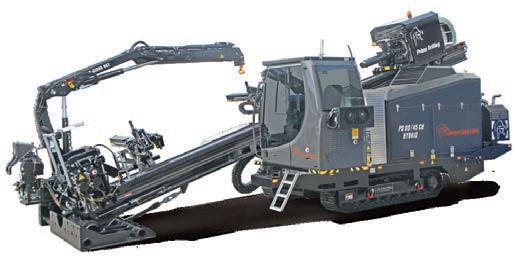
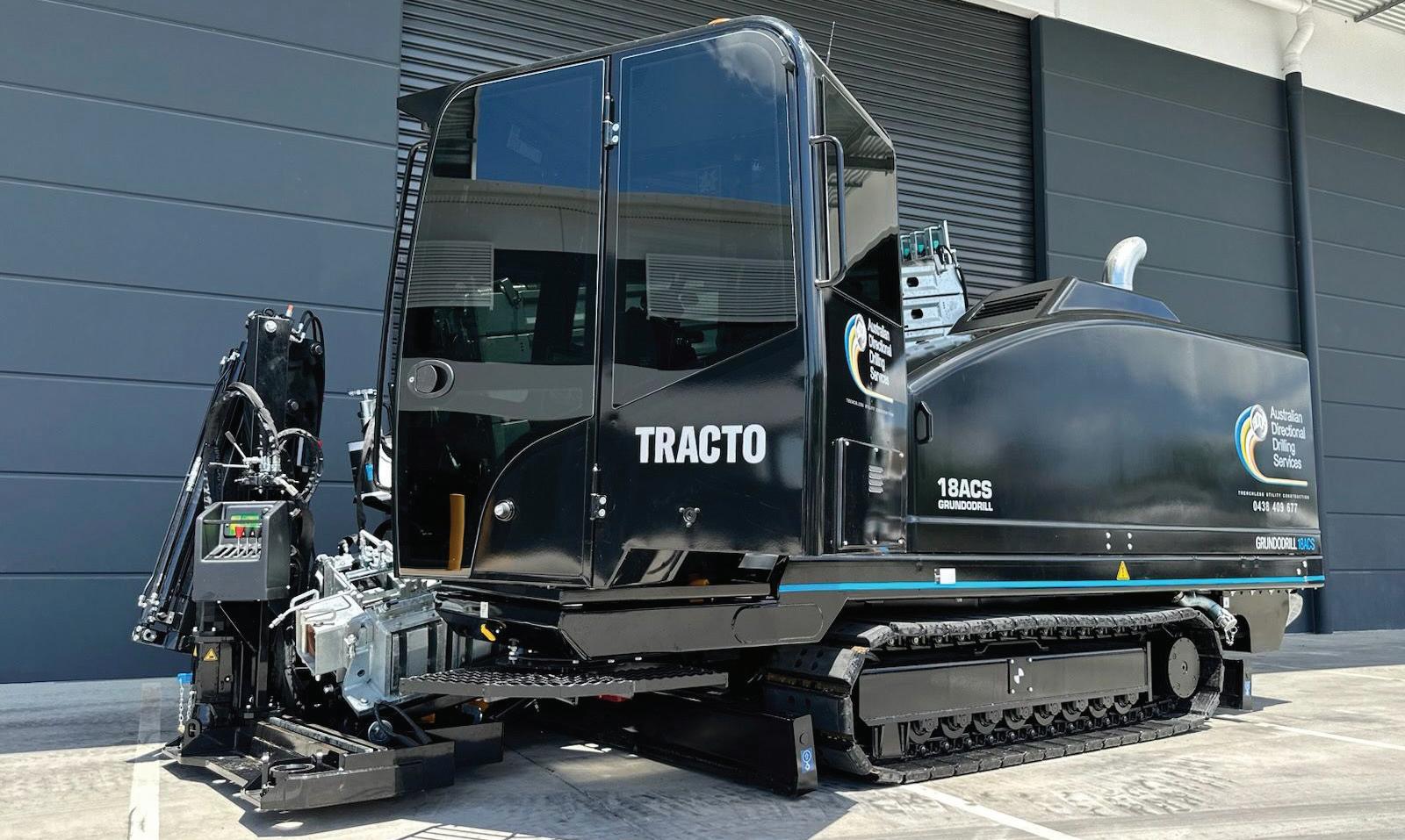
King of Rock ready to roll in WA
TRACTO Australia has shipped one of its 18ACS HDD rigs to a contractor in Western Australia. Dubbed the ‘king of rock’ for its ability to cut through the most challenging geologies, the machine is perfectly suited to navigate the unique and tough conditions under Perth.
Established in 2000 by Darren Smith, Australian Directional Drilling Services (ADDS) is one of WA’s leading horizontal directional drilling (HDD) contractors. Over the past 24 years, ADDS has remained a tight-knit, family business with Smith o ering his own personal services on-site as owner operator.
e company engages in all types of HDD projects, including conduit bores, river crossings, under-freeway bores, as well as excavating through granite, shale and rock over extensive distances.
Challenging geology
ADDS is often contracted to work in con ned spaces in the inner city and in the most remote locations where no services are available. When the company secured a number of contracts for projects along Perth’s coastline, Smith knew they would encounter the challenging geologies of limestone and capstone.
To deal with tough rock conditions in the region, the company engaged with TRACTO Australia, which is renowned for specialising in machines which are engineered to excel in the toughest ground conditions.
ADDS eventually invested in the company’s GRUNDODRILL 18ACS machine, which has since been shipped from TRACTO’s headquarters in Queensland and delivered to the contractor in Perth.
Rock ‘n’ roll
Known as the ‘King of Rock’, the GRUNDODRILL 18ACS has a stepless adjustment of torque and speed for maximum rotational power and maximum productivity and any speed.
e machine’s fully automatic operation ensures minimal downtime, maximum productivity and relief for the machine operator.
Elsewhere, the rotation of drill rods within the rod box is possible during normal operation, resulting in consistent use and consistent wear of the rods. e 18ACS can also optionally be converted for cable-guided bores when drilling in challenging terrain and at great depths.
With machines like the GRUNDODRILL 18ACS, TRACTO has earned a global reputation as a provider of innovative and advanced solutions for complicated trenchless and HDD projects.
In addition to supplying industry-leading trenchless solutions, all TRACTO machines are backed-up by in best-in-class training, service and spare parts – something the supplier has focused on in recent years. is has included securing a partnership with a WA-based company to support TRACTO’s partners in the region with servicing capabilities, as well as an extensive range of spare parts. e partnership is an important logistical step in supporting the company, and companies like ADDS, as TRACTO continues to grow it’s footprint in the state.
“We’re really excited to have this new service partnership in place, because it gives us and our end users access to industry-leading support right across the country,” TRACTO Australia Sales Manager Dan Toms said.
“We have seen the WA’s HDD and trenchless construction segment continue to grow over the past few years. ere’s also a growing demand for no-dig methods within the mining and resources sector, which contributes almost $100 billion to the state’s economy.”
For more information, visit tracto.com/au
NO-DIG DOWN UNDER

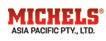

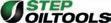
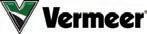
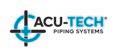



Ditch Witch is the ideal solution
Vacuum excavation is providing faster and more environmental digging methods, and the Ditch Witch AX30-300 is delivering the power to get the job done.
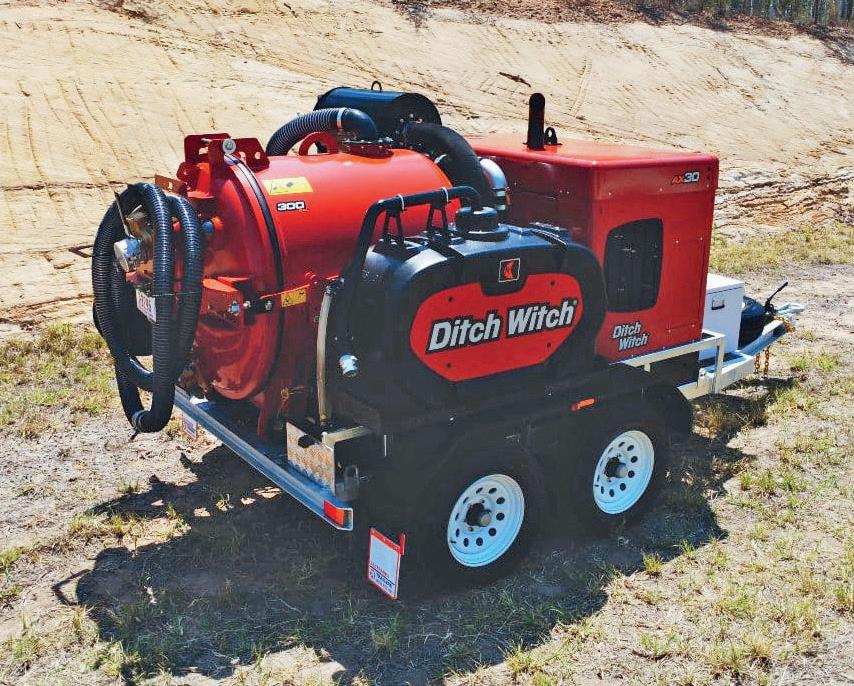
For many infrastructure projects, vacuum excavation is proving to be an ideal solution over traditional excavation methods.
e method is regarded as safer and more environmentally sound as allows for less disruption.
It is also considered quicker and cheaper than traditional methods.
When it comes to the right equipment for vacuum excavation, Ditch Witch CEA is a powerhouse with its AX30-300, developed exclusively for the Australian market by the team at Ditch Witch.
Providing new e ciencies for the trailer vac market to make operators more productive and pro table than ever before.
e Ditch Witch AX30-300 is equipped with a 32.5 horsepower Kubota diesel engine, delivering maximum power and performance.
With a vacuum tank capacity of 1135 litres (or 300 gallons), the Ditch Witch AX30-300 is crafted to meet the needs of vacuum excavation, with one of the largest spoils tanks available on a 4.49T GVM trailer in the Australian market.
Adding to the numerous bene ts above, some other ones include the AX30-300 o ering, a

cam-over auto locking hydraulic rear door, a hydraulic motor system for tank lift and tilt functions, kerb side controls, hose reel and tooling that can always be left connected and reverse ow control.
When it comes to maintenance, the Ditch Witch AX30-300 exceeds standards for contractors. All maintenance points are accessible with a lift-o power pack door design, making it very easy to perform routine maintenance.
e machine also has a high-capacity cyclonic ltration system, minimising lter cleaning frequency and increase productivity.
rough saving time, labour and costs for contractors, as well as reducing surface disruption and reducing the risk of damaging utilities, vacuum excavation is a growing method for excavation jobs.
e Ditch Witch AX30-300 is a testament to innovation and reliability with its highperformance engine and advanced vacuum excavation technology.
Paired with its operator-friendly design, the machine proves itself as a true partner for the construction industry.
As the use of vacuum excavation continues to rise across infrastructure projects, the Ditch Witch AX30-300 remains a top choice for contractors.
For more information, visit ditchwitchcea.com.au
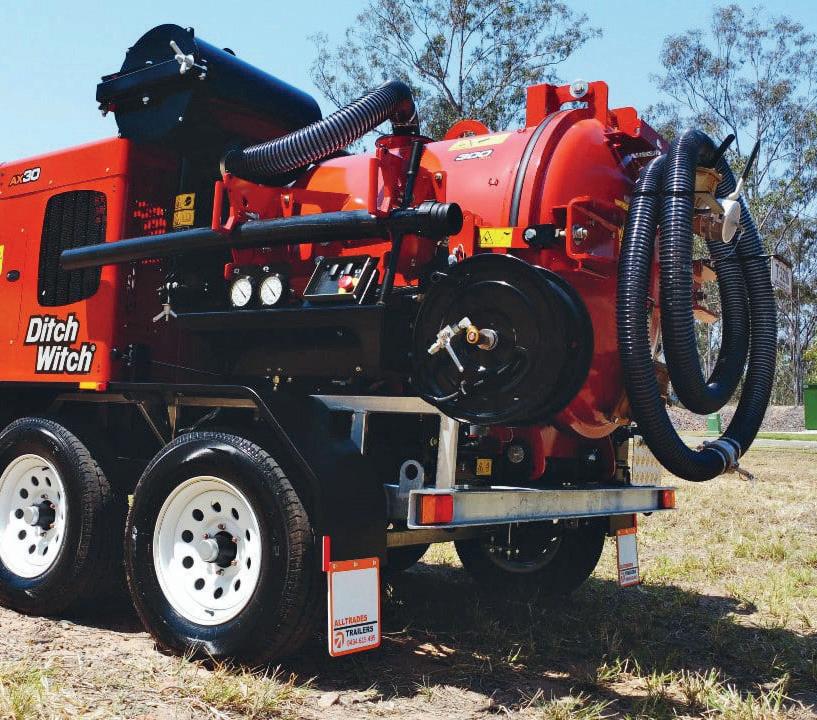
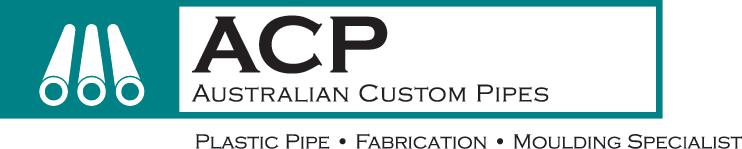
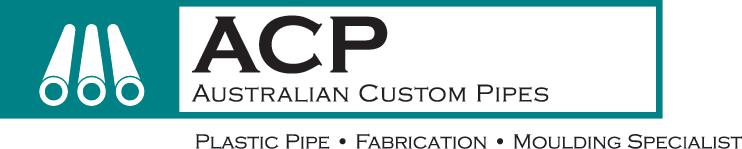
Manufacturing Quality PE100 Pipes
Delivering Customer Satisfaction with Quality Products and Service
Since 2004, Australian Custom Pipes (ACP) has been providing conventional piping systems, custom pipes, injection moulding and fabrication to the Gas, Water, Fire, Electrical and Communications pipeline construction industries
If it’s quality products and service you’re after give ACP the opportunity to impress.
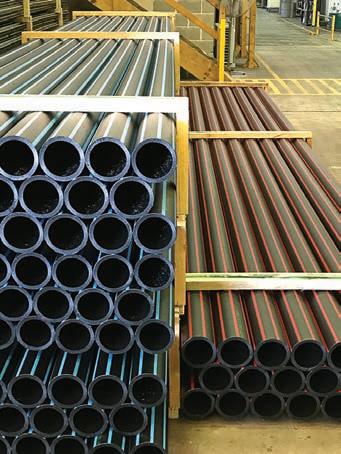
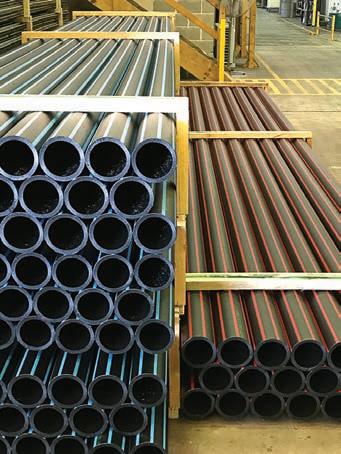
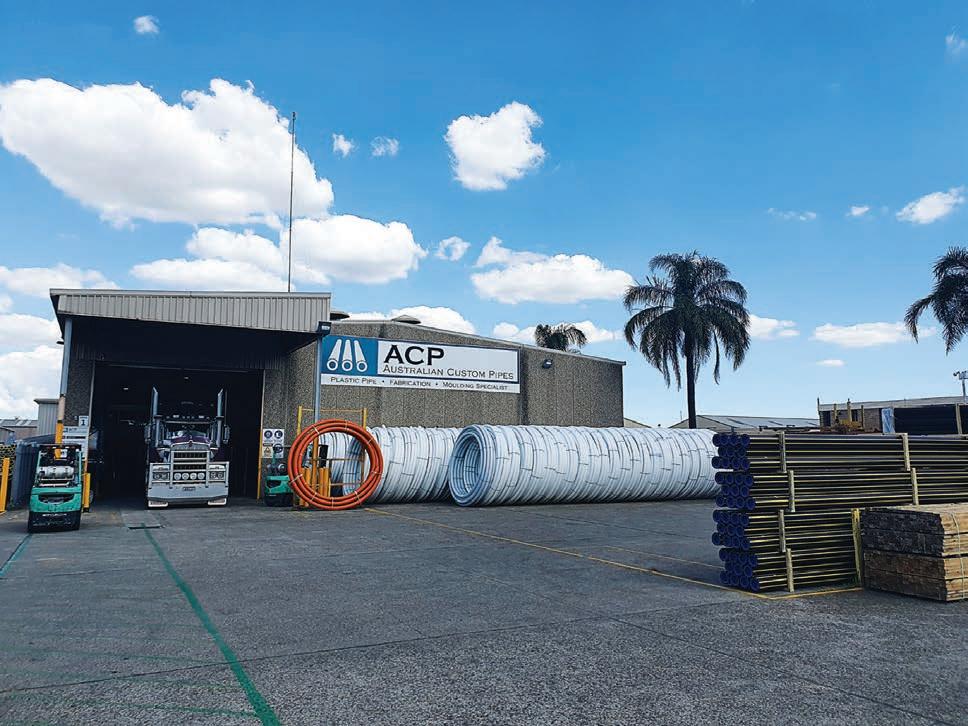
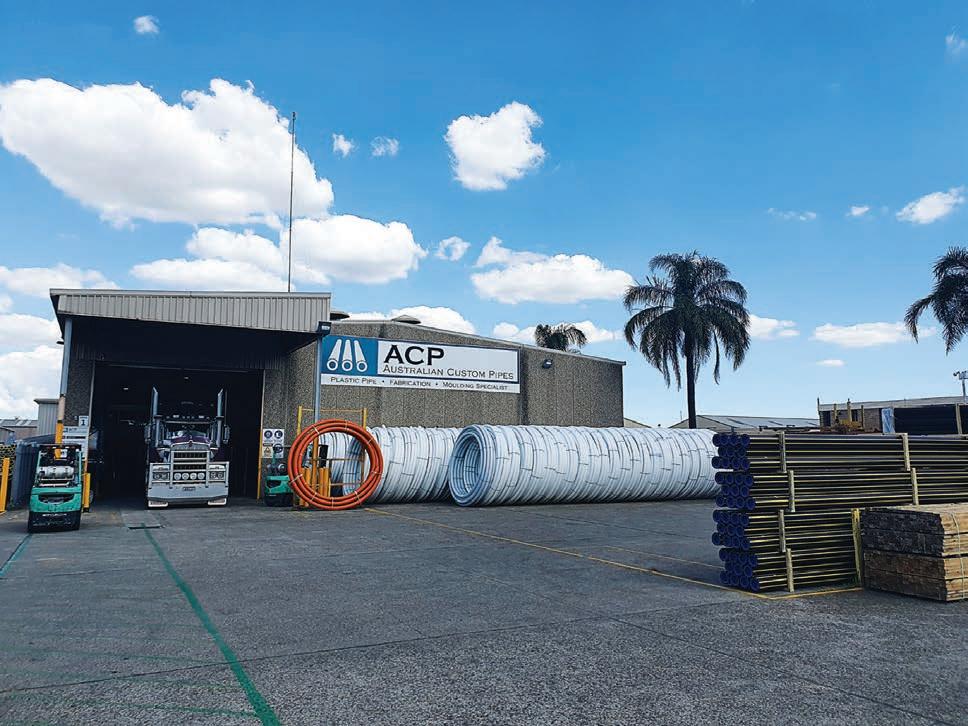
Making global strides in trenchless technology
Since its formation just two and a half years ago, OptionX Group has quickly emerged as a powerhouse in the trenchless technology industry.
Under the leadership of CEO Stuart Harrison, OptionX Group has focused on leveraging Australian innovation and strategic global partnerships to compete with some of the biggest names in the industry.
e past year has seen remarkable growth and key achievements, solidifying OptionX Group’s position on the world stage.
Global expansion and new partnerships
A pivotal moment in OptionX Group’s expansion strategy has been its growing international presence.
Harrison’s recent world tour included stops in the UK, Saudi Arabia, Dubai, and Switzerland, where he educated the market about the group’s agship products, AdaptX and Riteline.
His mission was twofold: to showcase Australian-made innovations and to forge new partnerships that would extend the group’s reach even further. Following the success of Trenchless Middle East, Harrison
travelled to Switzerland, where he nalised a key partnership agreement with TERRA, a leading manufacturer of trenchless technology equipment.
is new alliance marks a signi cant step forward for OptionX Group, as the company becomes TERRA’s o cial dealer and support partner in Australia.
By collaborating with TERRA, OptionX Group is now positioned to bring TERRA’s advanced products to the Australian market, providing on-the-ground support and enhancing the service o ering for local contractors.
“We’re thrilled to partner with TERRA,” Harrison said. “ eir reputation for quality and innovation aligns perfectly with our values at OptionX Group.
is partnership will not only expand our product range but also provide Australian contractors with access to some of the best trenchless equipment in the world, backed by local expertise.”
Leading the way with AdaptX and Riteline
At the core of OptionX Group’s success are two agship innovations: AdaptX and Riteline. AdaptX, the latest evolution of the Vermeer AXIS microtunnelling system, has quickly become a game-changer and is used exclusively by Edge Underground in Australia. Its versatility allows contractors to seamlessly switch between vacuum extraction, slurry, auger boring, and more, making it the preferred choice for a wide range of challenging ground conditions. While these options o er exible solutions, it is the vacuum microtunnelling revolution that is truly making waves globally, as the advantages of vacuum technology are just beginning to gain widespread recognition. e International Society for Trenchless Technology’s recent update to include vacuum extraction in the de nition of microtunnelling highlights the cutting-edge capabilities of AdaptX, solidifying its role as a leader in trenchless technology, and
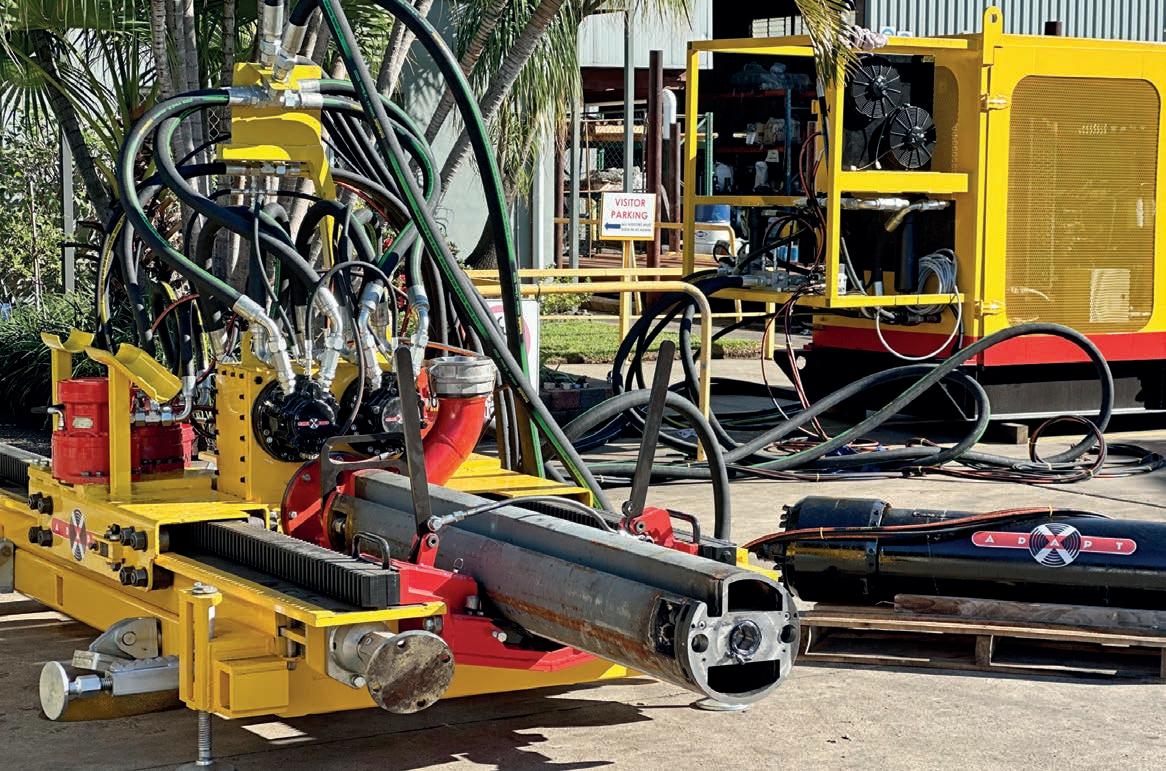

bringing it international attention. Riteline, an adaptable casing spacer system, has also made waves in the industry. Designed for both horizontal and vertical applications, Riteline simpli es pipe installation by allowing for incremental adjustments, reducing stock, and minimising material waste. It’s a product born from Australian ingenuity, already proving its value in projects across the globe.
“Australia has always been at the forefront of trenchless innovation,” Harrison said. “With AdaptX and Riteline, we’re continuing that legacy and providing contractors with solutions that address real-world challenges.”
A growing presence
Edge Underground, a key member of the OptionX Group, has seen multiple consecutive record-breaking months, driven by the increasing demand for microtunnelling and trenchless solutions. e synergy between sister companies Edge Underground and OptionX Bournedrill has allowed the group to o er tailored engineering solutions, leveraging in-house manufacturing capabilities to meet unique project requirements. Edge Underground has systematically upgraded its AXIS machines to align with the new AdaptX speci cations, signi cantly boosting reliability, e ciency, and capability. ese enhancements now enable the drilling of larger diameters than ever before. e acquisition of OptionX Bournedrill has been instrumental in
overcoming supply chain issues and enhancing Edge Underground’s ability to adapt to working conditions and deliver results. With a focus on continuous improvement, the group has invested heavily in research and development, with 11 active research and development projects underway.
Looking ahead, OptionX Group is poised for even greater growth. e partnership with TERRA AG and the global expansion e orts demonstrates a clear commitment to bringing the best trenchless technology solutions to the market. As the company continues to innovate and expand its product o erings, it remains
dedicated to solving the toughest challenges faced by contractors today.
“Our goal is simple,” Harrison said. “We want to provide the most e ective, e cient, and sustainable solutions in the industry. By partnering with leading companies like TERRA and continuously pushing the boundaries of what’s possible, we’re doing just that.”
OptionX Group has a strong track record, a growing list of international partnerships, and a commitment to innovation.
For more information, visit optionxgroup.com.au
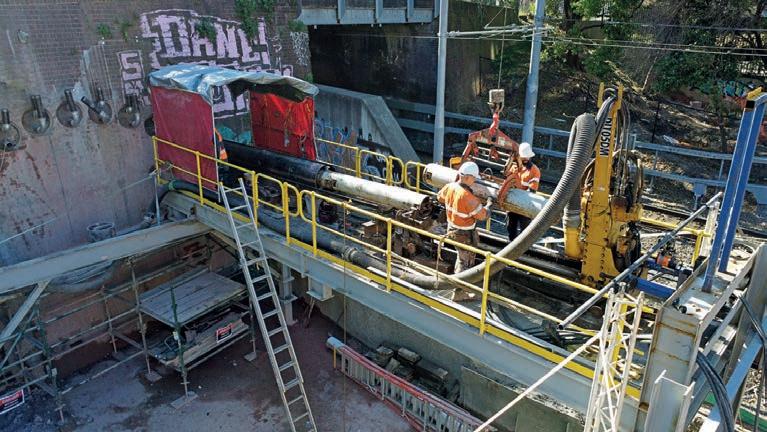
MicroGator 150 Air
• Fully compatible to every ManiLite inspection system
• One tractor for two applications: Cutting and CCTV
• Easy to integrate into existing systems


Celebrating 35 years of excellence
An action-packed 2024 has seen Rob Carr help deliver major trenchless projects across Australia.
When it comes to delivering complex utilities infrastructure projects, Rob Carr is a trusted name among major utilities, councils, and Tier 1 contractors alike.
Combining its highly skilled team with the best in civil and trenchless plant and equipment, Rob Carr boasts a wide range of capabilities from early concept and design phases, right through to delivery and commissioning.
When it comes to tunnelling, the company utilises two speci c techniques to undertake trenchless construction: slurry pressure balanced microtunnelling and pilot auger soil displacement tunnelling.
is is backed by Rob Carr’s eet of over 30 microtunnelling machines, with the largest machine diameter being 2180mm covering all ground conditions.
e machines are supported with a wide ranging ancillary equipment eet in the form of control cabins, jacking frames, slurry separation tanks and systems, gantry cranes, power generation and guidance equipment.
e company has also invested in German Herrenknecht AVN technology to facilitate larger scale tunnelling projects. Additional design and delivery capabilities include
deep access shafts, pump stations, and live service connections.
To round things out, Rob Carr engages in sound project management practices to ensure projects are appropriately planned and staged, and risks are considered, managed and mitigated accordingly.
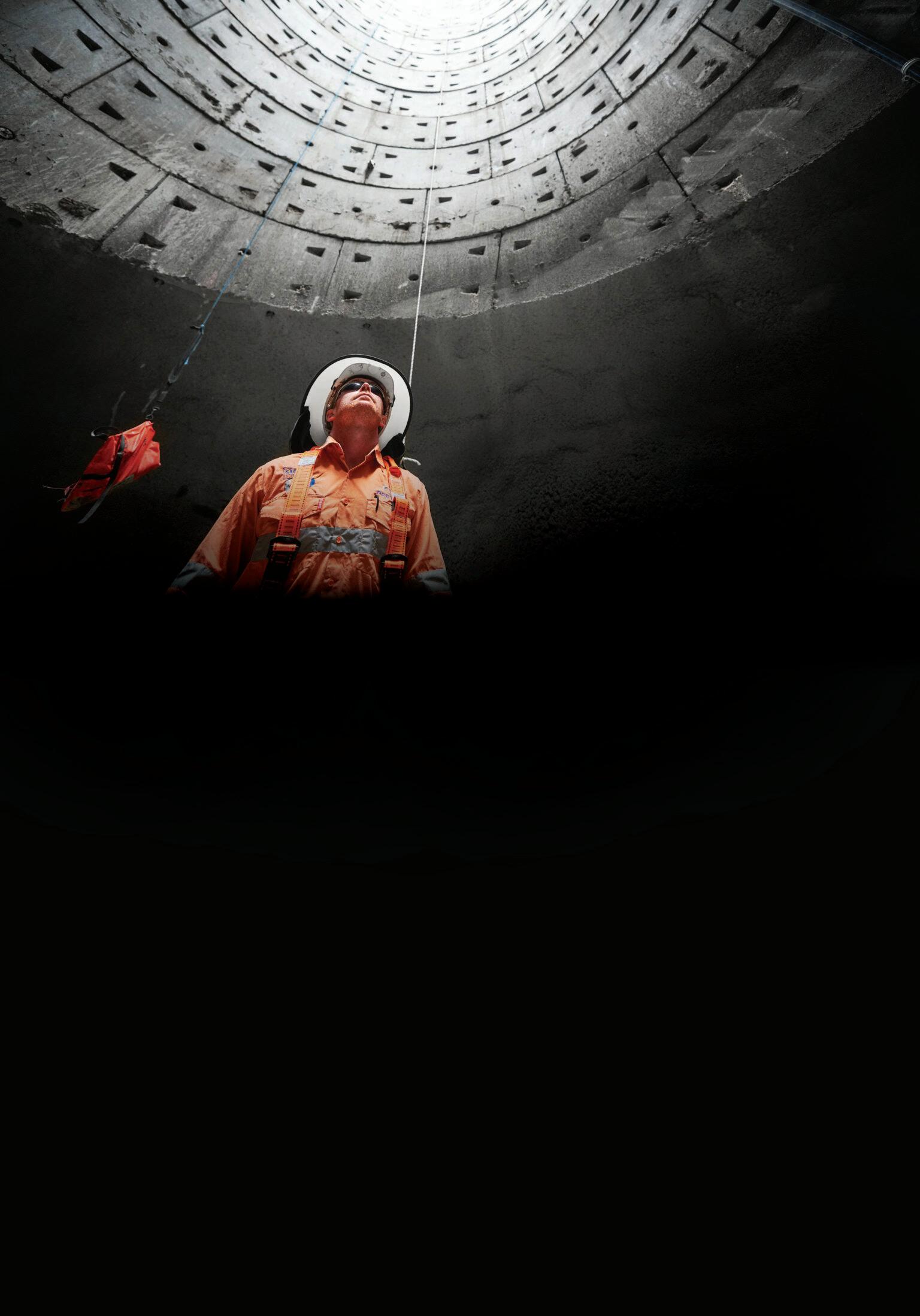
An exciting year is year marks the company’s 35th anniversary, and business is booming.
“Rob Carr has been in the business for thirty- ve years, and there’s a lot of technical knowledge within the company,” Rob Carr Project Manager ierry Candito said.
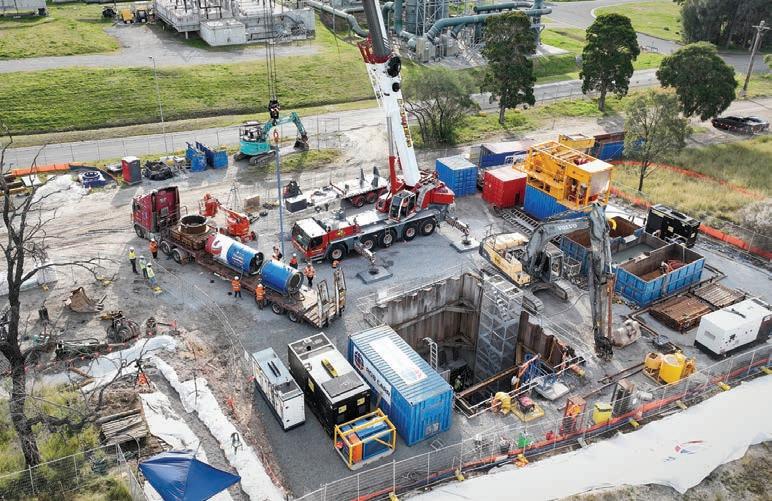
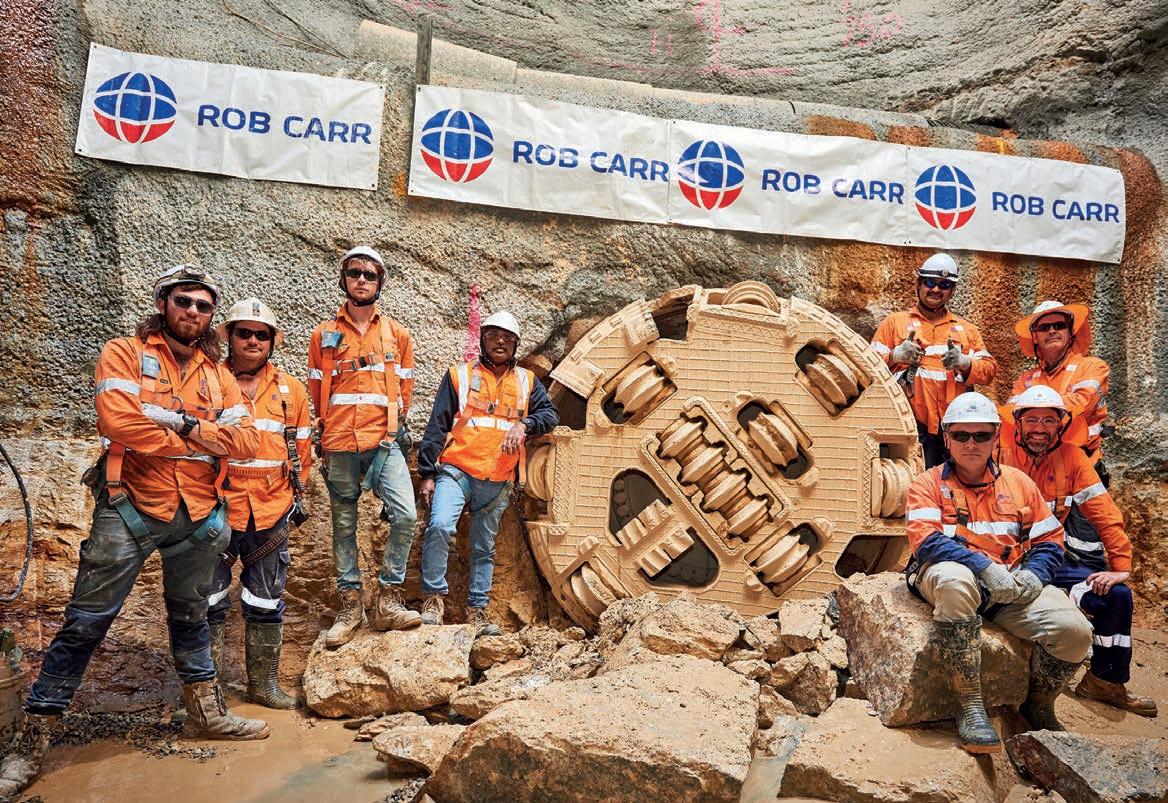
“We thrive o challenges, which makes Rob Carr the ideal partner for largerscale projects where you know there will be di culties.”
In Sydney, the company secured a contract to deliver part of a $90 million upgrade to the city’s North West Growth Area. e project will provide drinking water and wastewater services to roughly 17,000 homes by mid 2025.
Rob Carr’s scope of work entails signi cant early works investigation, complex temporary works design, construction of major bespoke access shafts, construction of two 270m long tunnels (DN1200) in parallel formation, construction of two 45m long tunnels (DN1200 and DN500) in parallel beneath rail infrastructure, and installation of multiple HDPE pressure mains.
ese works are well-advanced, with the company completing the rst 270m drive in September and the second in November.
Rob Carr also secured another Sydney contract to help deliver water and wastewater upgrades in the Cleveland development area. As part of the project, the company is presently constructing 1.45km of pipeline using slurry pressure balanced microtunnelling, along with associated civil works to aid the tunnelling operation.
In Brisbane, the company completed a highly technical sewer upgrade, which incorporated single 1002m drive by
microtunnelling with an internal diameter of 1.8m. is alignment travelled beneath arterial roads, railways, and waterways, presenting various technical challenges which the Rob Carr team were able to manage with expertise.
e company demonstrated its speed and e ciency on the time-sensitive Dudley Street project in the Gold Coast. Here, Rob Carr was contracted to deliver a time critical DN1800 stormwater pipe underneath the Gold Coast Highway, tunnelling through sand.
Impending light rail works in the area also posed a challenge to the project, but the Rob Carr team delivered the project e ectively and were o the scene well before the allocated timeframe.
In Melbourne, Rob Carr is helping to deliver an $80 million four-stage CBD sewer augmentation project. e company completed the third stage 700m Elizabeth Street sewer this year. e work was undertaken in a highly constrained site in amongst the CBD, with Rob Carr also constructing a series or access shafts, structures and service connections immediately adjacent to live rail.
In Western Australia, Rob Carr delivered the Mullewa water main project, which incorporated 7.2km of DN300 PVC pipe via open cut, and a DN700 reinforced concrete rail crossing; and the Benara water main project, which consisted of a DN1100
glass reinforced pipe road crossing. ese projects only reinforce Rob Carr’s one stop shop o ering.
Rob Carr’s order book is already starting to ll up for 2025, with the company securing a contract for a major capital works project in WA. Many more are currently in negotiation throughout NSW, Vic, SA, and Tas.
e project will see Rob Carr self-perform the construction of 356m of DN600 sewer, 517m of DN450 sewer, 277m of DN375 sewer and 12 access chambers in Armadale, Perth.
e sewer will be predominantly constructed via microtunnelling, with the longest drive being 186m. e work will commence in January 2025 with completion scheduled for September 2025.
Rob Carr General Manager Angelo Soumboulidis said that complex projects are where the company truly excels.
“Navigating tough geological conditions, rail and road crossings, and critical infrastructure connections requires not only technical precision, but also resilience and adaptability,” he said.
“Our team’s expertise and dedication ensures that whatever project we take on will be executed with the highest of standards, delivering a seamless outcome for our clients.”
Busy year for kwik-ZIP
With its products regularly utilised in projects in Australia and around the globe, and a new head office and warehouse in Perth, kwik-ZIP has had a big year.
This year has proved to be a busy year for kwik-ZIP with the global manufacturer opening a new head o ce in Australia and getting involved in projects Down Under and internationally.
Manufactured from high grade thermoplastic, kwik-ZIP products are used and recommended by pipeline contractors, water and gas utilities, drilling companies and international engineering rms.
e use of kwik-ZIP products helps contractors to comply with the numerous regulations that require casing centralisers or pipe spacers (slippers or spiders), including wastewater and sewerage codes and well construction standards.
Since its inception in 2000, the company has been designing centralisers and spacers systems for a wide range of applications across many di erent industry sectors.
With warehouse facilities in Perth, Sydney, the UK and Texas, the company has also established stockists in Australia, the US, the UK and New Zealand markets. kwik-ZIP products are recommended, speci ed and used by pipeline and civil contractors, water and gas utilities, drilling companies and international engineering rms across the world.
kwik-ZIP’s HD and HDX/HDXT spacer system series are providing the pipeline

sector with simple, cost-e ective, and highquality solutions.
e HD and HDX/HDXT spacer system series are lead and metal-free, non-corrosive, chemical and oil resistant, and suitable for use on all pipe materials, including steel, ductile

iron (DICL), high-density polyethylene (HDPE), concrete and mild steel cement lined (MSCL).
ey also have a quick and easy installation process, reduce point loading via a unique load sharing runner system, and minimise damaging vibration and movement transfer from outer casing to carrier pipe via suspension and dampening e ect. All kwik-ZIP spacers are designed to meet the requirements of Water Services Association of Australia (WSAA) product speci cation 324 (casing spacers).
kwik-ZIP products are also approved for use within many utilities’ infrastructure, including Melbourne Retail Water Association, South-East Queensland’s Infrastructure and Materials (IPAM) list, Sydney Water and the WA Water Corporation. All products are certi ed by the Australian Water Quality Centre (AWQC) for use in contact with drinking water. As a member of the Australian Water Association, kwik-ZIP is a liated with Water Industries Operators of Australia (WIOA), American Water Works Association, US National Ground Water Association, the ASTT and the Australasian Corrosion Association.
On the move
In early 2024, kwik-ZIP relocated its WA head o ce to new premises in Bayswater.
e company said the move ensures it is strategically positioned to service its customers.
e move has enabled kwik-ZIP to service WA clients more e ciently, while also allowing for increased inventory to be held on the west coast of Australia.
Existing or prospective customers are always welcome to drop in and say hello at kwik-ZIP’s new facility, General Manager Paul Je reys said.
On the ground
is year again saw kwik-ZIP products used on a range of projects across Australia and around the globe. Utilities infrastructure experts Rob Carr turned to kwik-ZIP for its project in Gosnells, Western Australia.
kwik-ZIP HDXT-103 spacers were installed to facilitate the slip-lining of a mild steel cement mortar lined (MSCL) wastewater pressure main into a RC Jacking pipe, running under a rail line for the Gosnells Main Pumping Station Wastewater Pressure Main Realignment project.
Rob Carr Project Manager Marie Piette saluted kwik-ZIP’s and its innovative spacers.
“ e MSCL pipes insertion is making good progress despite a challenging environment, with production e ciency notably enhanced by the simplicity of installation of the KwikZip spacers,” she said.
e simple and e cient installation process did not require any special tools or any requirement to pre-wrap the pipe.
Pezzimenti Trenchless were also among those praising kwik-ZIP’s products.
“Pezzimenti Trenchless has been using kwik-ZIP spacers for slip lining installations for many years,” Managing Director Joe Pezzimenti said.
In one project instance, kwik-ZIP HDX90 spacers were installed to facilitate the slip-lining of an 813mm cement lined steel water main into a steel encasing pipe by Pezzimenti Trenchless.
“Whether the carrier pipe is plastic, GRP or heavy weight steel, kwik-ZIP has a spacer to do the job,” Pezzimenti said.
“ eir technical support and excellent customer service make using kwik-ZIP spacers an easy decision.”
In August, it was announced that kwik-ZIP’s HD series has been successfully appraised against the Water Services Association of Australia’s (WSAA) product speci cation for casing spacers (WSA PS-324).
kwik-ZIP also made an impact on the global stage this year.
e company’s spacers were recently utilised on a speci c section of the Trans Mountain Pipeline Expansion Project in Canada to assist one of the contractors working on the project.
e contractor needed to complete an HDD component where two HDD pull-back casing sections needed to be protected at the entry and exit points of the run.
e Trans Mountain Pipeline System (TMPL) is a multiple product pipeline system that carries both crude and re ned products from Edmonton in Alberta Canada across to the Coast of British Columbia.
e initial pipeline system was completed in 1953, and then in 2013 a project commenced to build a second duplicate pipeline system, running parallel to the existing pipeline.
On show
As well as seeing its products involved on projects in Australia and around the globe, kwik-ZIP also showcased its range at a number of events in 2024. In Australia, the company exhibited its products at OzWater24 in Melbourne, and followed that up with a booth
at the Australian Drilling Industry Association showcase in Perth.
As a WIOA member kwik-ZIP also exhibited at the 2024 Water Industry Operations Association (WIOA) of Australia conference in both Bendigo and Tamworth.
kwik-ZIP also exhibited at the 2024 NoDig Live, which took place in Kenilworth, Warwickshire, UK from 1–3 October.
e company was on the ground at the the three-day event, showcasing its range of innovative and patented spacer and centraliser systems.
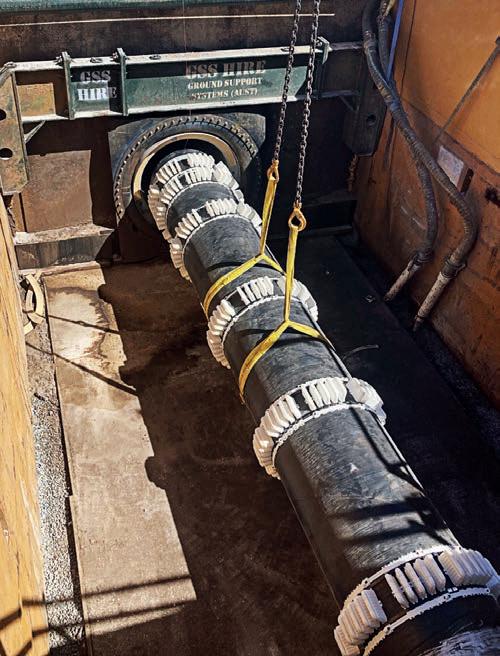
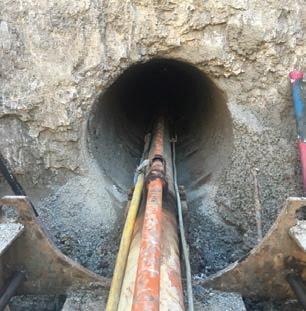
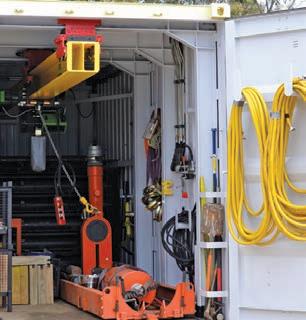
Total Plumbing Solutions delivers Australia’s first installation of SAERTEX-LINER H20
Setting a new standard in trenchless technology for potable water infrastructure.
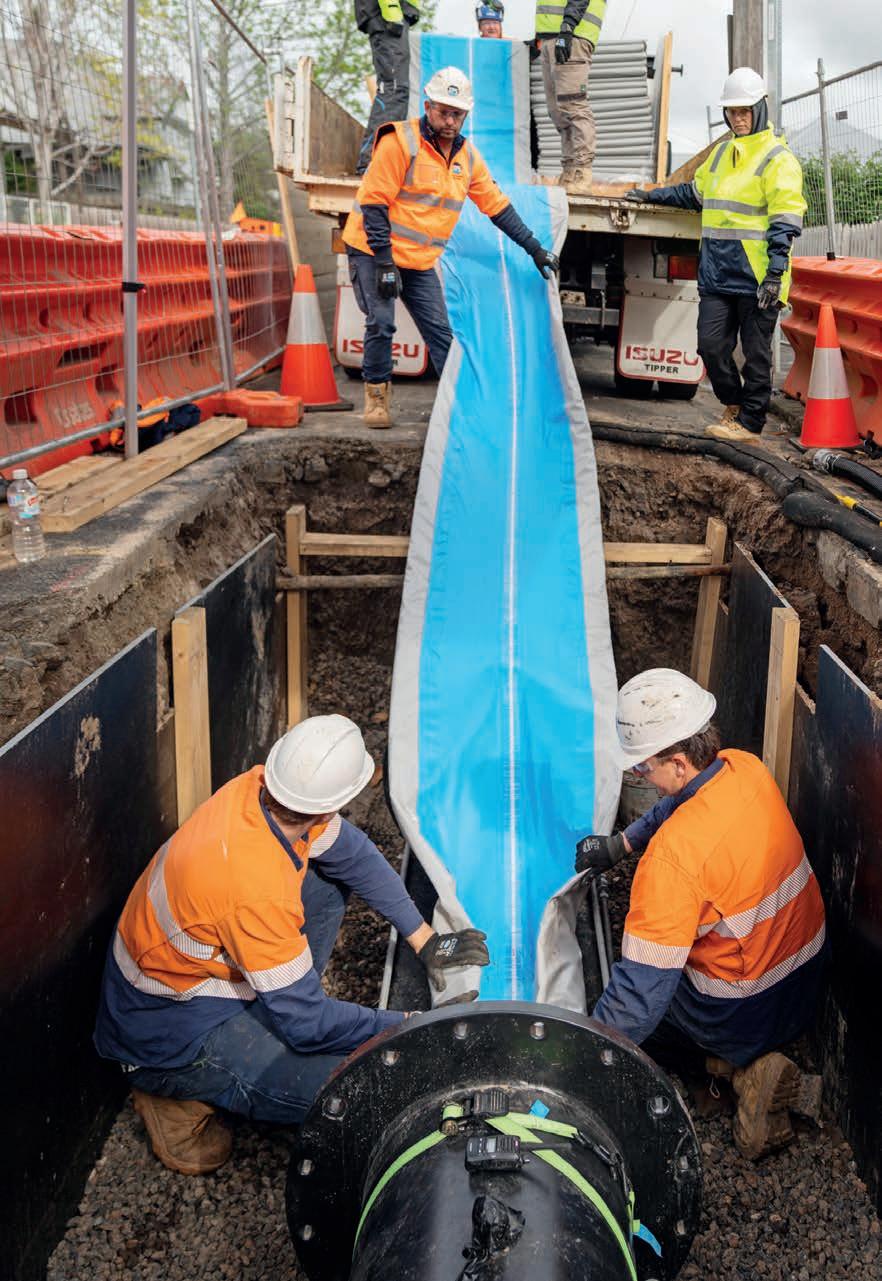
Total Plumbing Solutions (TPS) has set a new benchmark in potable water pipeline renewal in Australia with the rst-ever installation of the award-winning SAERTEXLINER® H2O for asset owner Barwon Water. is innovative liner represents a breakthrough in trenchless pipeline rehabilitation, o ering safe, clean and coste ective solutions for renewing drinking water pipelines.
Unique solution
SAERTEX multiCom® has developed a unique rehabilitation solution that enables the construction of a new, independent, fully structural pipe within the existing host pipe. is watertight GRP liner not only restores functionality and adheres to the highest of hygienic standards for potable water but also extends the pipeline’s lifespan by an impressive 50 years.
TPS, with its experience in relining, quickly recognised the bene ts of SAERTEX-LINER and the approvals that SAERTEX-LINER H2O Type S+XR had achieved for installation in Australia and New Zealand. ese approvals included an appraisal by the WSAA for renovating drinking water pipes and a certi cation to AS/NZS 4020 standards by the Australian Water Quality Centre (AWQC).
In November 2023, TPS completed SAERTEX multiCom’s certi ed installer training for pressure and gravity systems through local distributor Pipe Core. is training provided both theoretical and practical knowledge of SAERTEX multiCom’s versatile and structural UV-CIPP solutions.
“ is certi cation, combined with our crew’s experience, gave us con dence in presenting trenchless renewal to our client, over traditional methods like boring and dig-and-replace,” owner of TPS Steve Nolan said.
Trenchless rehabilitation
Selecting the right rehabilitation solution was critical for the trenchless rehabilitation of the DN463 feeder water main running through a busy street in the centre of Geelong, Victoria. e project for the asset owner Barwon Water covered 388m and had to meet strict hygienic standards, minimise costs and time, and reduce disruption to the local community while extending the life of the asset.
“ e main was deteriorating rapidly, and spot repairs were no longer feasible. We had to avoid emergency work and road closures that could disrupt the local community,” Nolan said.
As the principal contractor, TPS engaged in months of meticulous planning with SAERTEX multiCom, Rausch Rehab, and Pipe Core to ensure the project’s success.
“Despite the comprehensive planning, the relining process itself was considerably quicker compared to traditional dig-and-replace methods,” Nolan added.
In early 2024, TPS acquired the Rausch Rehab RRcure 1500 Compact through Pipe Core, a powerful UV curing system designed for e ciency in a wide range of projects.
“We were excited to enhance our operational capacity with the acquisition of the RRcure 1500 Compact, allowing us to undertake more complex projects more e ciently and e ectively,” Nolan said.
On the rst day of the installation in early October 2024, the site was a sea of high-vis uniforms and hard hats, showcasing TPS’s commitment to health and safety.
e crew had excavated three access pits, cleaned and inspected the pipe via CCTV in the weeks prior, and installed safety barricades.
With everything ready, the crew began pulling the gliding foil through the host pipe, preparing to insert the liner.
Due to the length of the host pipe and curing time required, Nolan said the reline was completed over two days, with each section covering 194m.
“We anticipated long days, so we scheduled two days of relining to ensure we managed the health and safety of our crew,” he said.
“We didn’t leave anything to chance and engineered success by meticulous planning to mitigate any risks.”
Seamless installation
TPS’s crew of six was supported by two SAERTEX multiCom application engineers, a representative from Rausch Rehab, and tra c management personnel.
“Everything was planned before starting onsite, including having the right representatives from our suppliers onsite to ensure a seamless installation,” Pipe Core CEO Jason Marshall said.
“Our team of application engineers and project managers provide technical support to installers, including feasibility analysis, static designs, project planning and on-site support to project’s success,” SAERTEX multiCom Business Development Manager Katharina Helming added.
Once the gliding foil was installed, the liner was pulled in using a winch directly from one of TPS’s trucks.
Despite facing uctuating weather conditions, including wind, rain, and even periods of hot sun, the installation progressed without delay.
“Having the right technology and equipment made all the di erence in the success of
the install,” TPS Senior Technician Ben Hochuli said.
Following the liner installation, the crew secured the SAERTEX-PACKERs with quickrelease fasteners and then pulled in the Rausch Rehab light source.
ey then began calibrating the liner, monitoring the process from a custom van equipped with the RRcure 1500 Compact curing unit.
Once everything was in place, the curing process began and was continuously monitored by a crew member for the entire vehours duration.
“It is great that curing doesn’t commence until we’re ready, giving us full control of the process,” Nolan said.
After curing and cooling, the crew cut back the liner to install the end seals. In the following days, they conducted CCTV inspection, pressure testing and recommissioned the pipe.
“All pressure tests went well, and we were
extremely pleased with the results. is was a signi cant milestone for our company and crew,” Nolan said.
“We’re proud to see TPS achieve such success with this project,” Marshall added.
“ e result of this reline opens exciting opportunities for TPS and our broader customer base, giving them con dence to take on more high-risk, high-value projects in the future.”
is installation demonstrates the capabilities of SAERTEX-LINER H2O and UV curing technology, setting a new standard in the industry and paving the way for future projects in potable water pipeline renewal.
e SAERTEX-LINER H2O has been approved in over 14 countries, including Australia, New Zealand, Germany, the USA, Brazil, and China, and has been used in more than 400 installations.
For more information, visit pipecore.com.au
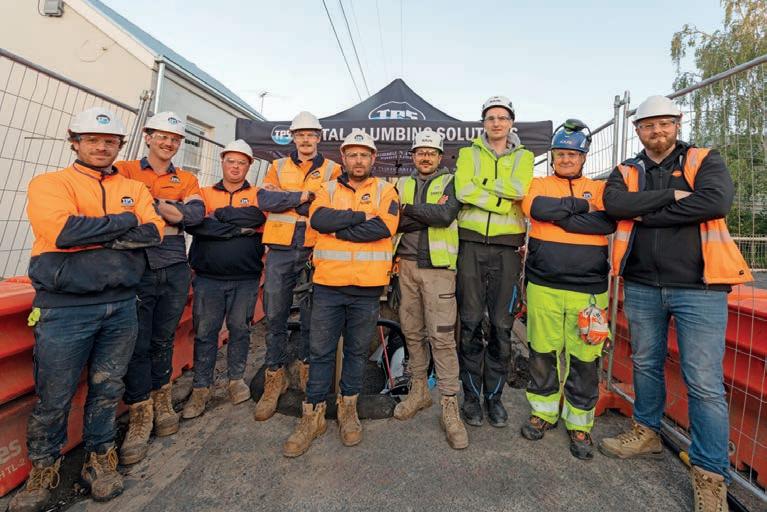
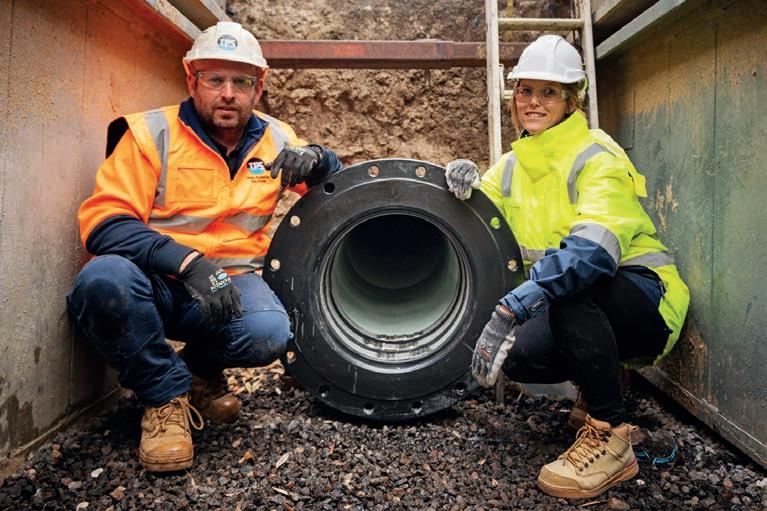
Infrastructure innovation: A better approach to pressure pipe renewal
With the water industry searching for renewal solutions, pipeline infrastructure specialist Interflow shares how it developed a suite of sustainable solutions.
As water infrastructure ages, pressure pipes have traditionally been excavated for repair or replacement. is has disrupted communities and increased costs and time scales.
“ e Water Services Association of Australia (WSAA) found that in Australia, there is around 40,000km of asbestos cement pipe,” Will Zillmann, Inter ow’s National Product Manager said.
“When you dig it up, a lot of precautions have to be taken, so the expense is signi cant. If you leave it in the ground and lay new pipe alongside it, you have to make sure nobody ever digs it up, which adds more administration expense. ere are a lot of issues.”
As corrosion from aggressive soils attacks underground pipes, including those made from cast iron, a trenchless renewal option for such pipelines becomes increasingly attractive.
What the pressure-pipe solutions looks like Comprehensive renewal solutions should not just x a speci c problem, Zillmann said, but should reset the lifespan of the pipeline. ey should essentially perform as a new product.
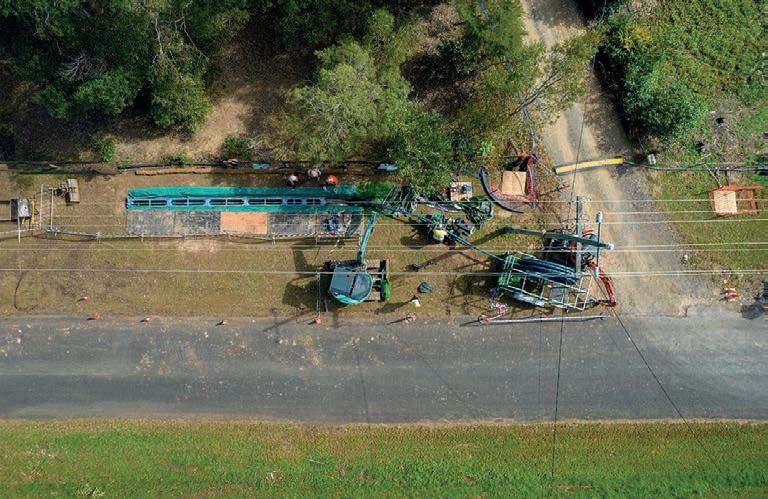
“Proactive trenchless renewals are one of the keys to defending our critical water and wastewater services in a sustainable and coste ective way,” he said.
“New or rehabilitated pipes can last decades, reducing the need for frequent interventions.
“Our objective was to build a suitable suite of proven solutions that enable us to match the right product or approach to the pressure pipeline’s condition, material, size and location.”
In response to the threats raised by the much-discussed infrastructure cli , and by the fact that a signi cant percentage of Australia’s water reticulation networks are made from asbestos cement, Inter ow developed the
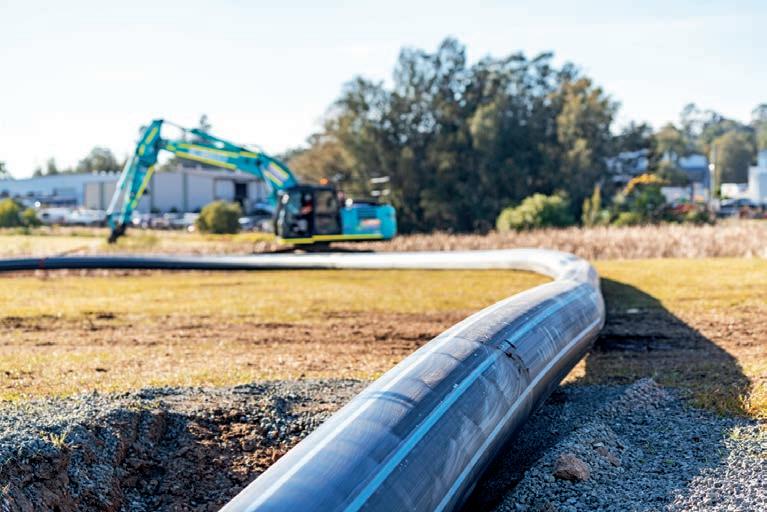
Redi ow bundle as a solution.
Redi ow includes its Tite ow diereduction lining as well as Infrastop linestopping technology.
Together, the innovations provide a complete reticulation renewal system that empower asset owners to conduct proactive renewal projects, dramatically reducing unexpected network shutdowns.
Trenchless – the most practical solution for ageing pressure pipelines
e Redi ow bundle is at the core of Inter ow’s suite of solutions and includes a polyethylene liner technology known as Tite ow.
It’s a structural liner that has its diameter reduced with a die during installation, so it can be drawn into the host pipe.
Once inside, it expands again to press against the host walls, creating a new pipe within the existing pipeline.
As a lining technology, it ts within the ISO classi cations for trenchless solutions, primarily at Class A (can survive failure of the host pipe and is a fully structural solution).
It’s a solution that balances performance, safety and environmental impact, with the many bene ts including:
• Reduced environmental impact: When it is compared to traditional methods that involve excavation along the line, trenchless technology minimises environmental impact by reducing emissions, creating dramatically less land disturbance and reducing waste management concerns.
• Lower community impact: As it requires only limited excavation for access points,
the Tite ow method drastically reduces the need for road closures and their resulting disruption to local communities, as well as unsightly trenches across the landscape.
• Long-term cost e ciency: While the up-front costs of trenchless methods may sometimes be comparable to traditional dig-and-replace methods, trenchless o ers long-term nancial bene ts as a result of its durability, reduced maintenance needs and shorter project timelines.
As the triple bottom line of environmental, social and economic impacts becomes increasingly important to water authorities and government, sustainable pipeline renewal methods will become the norm, Zillmann said.
How Interflow proved its suite of solutions
Inter ow’s purpose is to improve lives, which extends to the communities and environments they operate within.
is has led them on a journey to nd, assess and develop renewal solutions that are sustainable and support the needs of the industry, customers and their communities.
On this journey, and to ensure the trenchless solutions do what they promise, Inter ow ran an exhaustive and ongoing research project.
“To enable renewal programs and decrease the reliance on excavating and replacing ageing pipes, the water industry has been searching for renewal solutions speci cally optimised for pressure pipelines that meet the needs of asset owners and their communities,” Zillman said.
“We were active participants in WSAA’s Cooperative Research Centre for Smart Linings for Pipe and Infrastructure Project.” is involved water authorities, suppliers and delivery partners collaborating over several years to research and trial the e ectiveness of emerging lining technologies for water and wastewater assets.
“ is type of industry-led research is critical for objectively assessing technologies that are entering the Australian market for e ectiveness and suitability, and for creating product documentation and decision tools,” he said.
From idea to reality
rough such research projects, and by working closely with customers, Inter ow has been able to push the boundaries of common approaches like slip lining and large diameter die-reduction lining.
“For example, we’ve had success renewing longer lengths of water main using both of these technologies by thinking di erently about how we store, string out and weld pipe sections, and how we facilitate insertion,” Zillmann said.
“As a result of these approaches, we can now o er renewal options for pressure pipes in
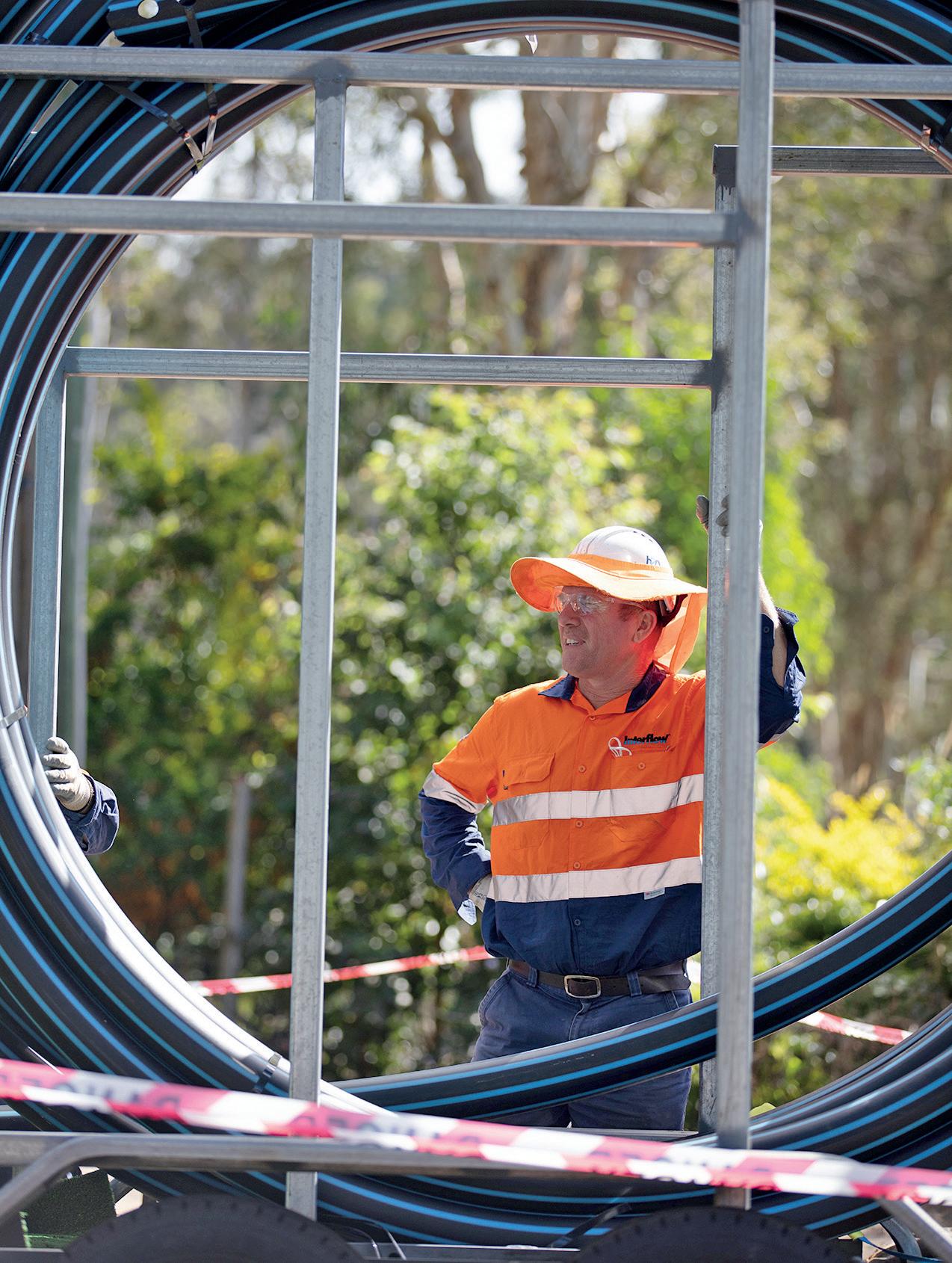
varying condition states and covering a large range of sizes and materials.
“Our approach to renewal opportunities is to be solution-agnostic and develop an optimal methodology based on project-speci c network capacity needs, pipe condition and material, internal diameter, access constraints, budget and community needs.”
It’s being used right now
Inter ow’s research led to the use of the trenchless pressure pipe solution in real projects.
is further added to the dataset utilised to inform the algorithm that predicts such information as pulling load, die size, insertion diameter, and more.
“ e algorithm is where the real magic is,” Zillmann said. “If you get it right, by the time you get to the site everything is relatively easy.”
Of course, there is always room for greater performance and more innovation, which is why the project is ongoing.
“We’re always working on optimising the performance of the solution, because its main drawback is that it naturally reduces the diameter of the pipe,” he said.
“ at can have an impact on ow capacity.
“But as long as we keep working on the materials and the algorithm, we can reduce that e ect as much as possible.”
For more information, visit interflow.com.au
Nuflow keeps Sydney Metro on track
When the Sydney Metro project encountered a major issue with pipelines, engineers needed a quick, effective solution that wouldn’t impact the project’s timeline. Nuflow stepped up.
The Sydney Metro project is one of Australia’s biggest public transport projects. By 2032, the New South Wales capital will have a network of four metro lines, along with 46 stations and 113km of metro rail. is is expected to move 40,000 people per hour instead of the current 24,000, and completely transform the regions along the rail. is means that a number of projects, upgrades and refurbishments are currently taking place, all on a careful schedule to ensure everything is ready on time.
So, when engineers working on Barangaroo Station as part of the Sydney Metro City and Southwest project encountered a major issue with some of the pipelines, they needed to get a guaranteed x that wouldn’t impact their timeline. Nu ow was more than up to the task.
New lease on life
Barangaroo Station is designed to provide access to a new business hub and will expect high levels of activity throughout the day.
Commuter comfort is a major consideration for projects of this scale, so the engineers have ensured there will be adequate air conditioning to keep everyone cool.
To facilitate this, the plan is to turn an existing space that currently contains four separate pipes leading to the Barangaroo foreshore into a pump room.
Seawater will be transported from the pump room via the pit and implemented into their station cooling loop.
e engineering team inspected the existing pipes to ensure they were able to handle their new role. Each pipe was 60m long and was made of GRP, lined with breglass.
e inspection revealed delamination of the pipe’s internal breglass lining, risking further deterioration that would make the pipes unsuitable for their new role. If left unaddressed, this could snowball into a much more costly and invasive issue. Not wanting to set up the whole pump room only for issues to start occurring down the track, the engineers decided a preventative measure was necessary.
Tailored solution
e Sydney Metro team wanted a suitable and trustworthy company that delivered peace of mind knowing they had an e ective solution that would keep things running smoothly.
After doing some research, they encountered Nu ow’s pipe relining solutions, commitment to quality assurance and the associated warranty on our products.
is gave Sydney Metro con dence that Nu ow’s solutions could go the distance.
During initial conversations, Nu ow’s head o ce team and the project engineers discussed the potential solutions for the project and infrastructure.
Because the pipes were bringing water from the harbour, the right solution needed speci c traits and speci cations that accounted for:
• Internal pressure and ow
• Pipe depth
• External loadings
• In ltration
Sydney Metro also needed the solution to deliver a completely relined system, from end-to-
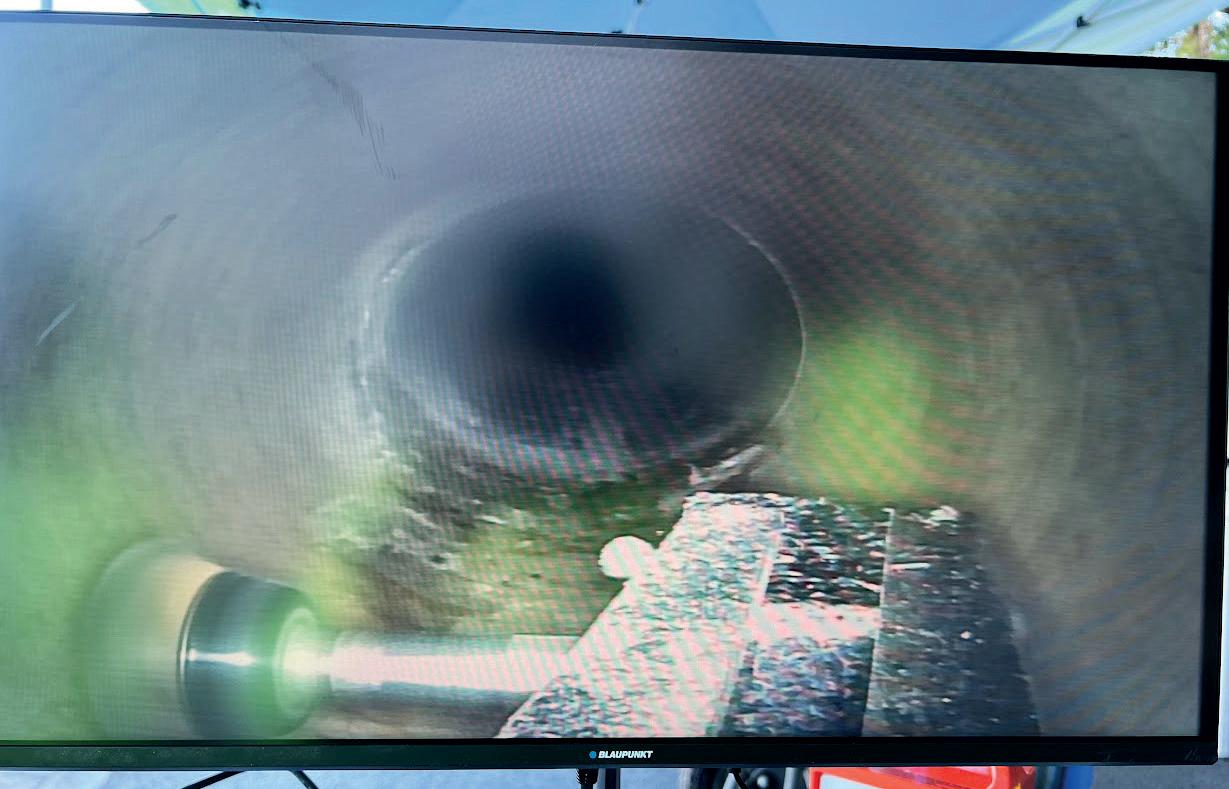
end, including the ange connections. is led them to identify Nu ow’s Hybrid Lining system as the best option. Once this was approved, the head o ce team got in touch with Nu ow Sydney City to put the plan into action.
Despite the scale and complexity of this project, Nu ow Sydney City is accustomed to challenges – such as the time they refurbished a seal enclosure at Taronga Zoo – so were ready to tackle things head on.
Nu ow Sydney City Director Michael Brock, and the rest of the team, assessed the situation and determined a plan of attack.
e site was busy with work being done by other utility professionals as part of the Sydney Metro City and Southwest project, so the team knew they had to act quickly and methodically so as to avoid impacting the larger project timeline. With this in mind, they got to work.
Quality and efficiency
Before Nu ow could begin the reline, Brock and the team needed to remove the delaminating breglass internal lining.
To do this, the company used a robotic cutter to cut away and sand back the loose sheets of breglass.
Once this was complete, the Nu ow team sent down a CCTV pipe inspection camera to con rm everything was in good condition and ready for the reline.
From ange to ange, the team began its restoration of the entire system.
Because the pipe reaches a maximum of 350Kpa for pressure testing, they needed a hybrid line to withstand the force. ey also needed a combination of rubber and vinyl bladders to account for the bends and straight sections of the pipeline.
ere were two access points for the reline, one was in the pump room and the other was in a 2.5m deep pit on the foreshore.
Because the pump room access point was on top of a mezzanine, the Sydney Metro engineers installed sca olding that granted Nu ow more direct admittance.
e pit on the other hand was close to a popular pedestrian walkway.
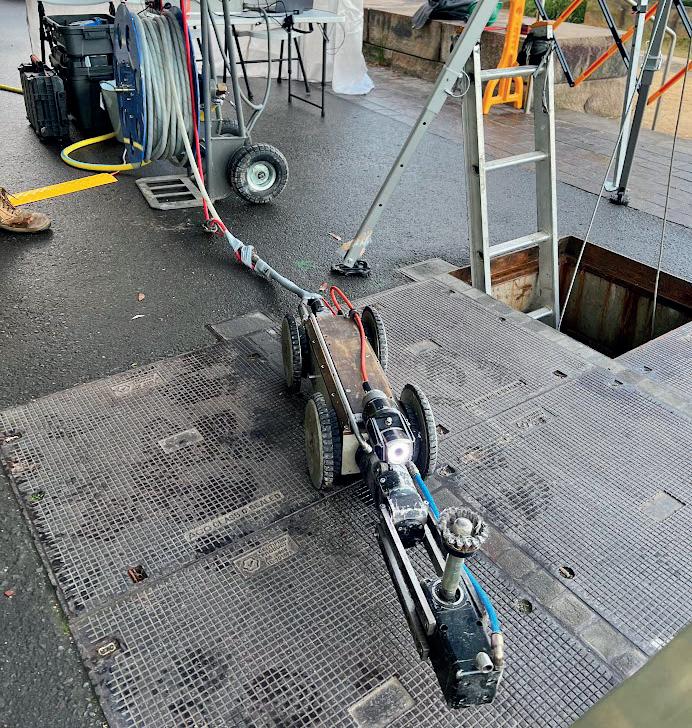
at meant that Nu ow needed to set up the site and block o the work area so the company could keep everyone safe.
Brock made sure to put out correct signage while encouraging the team to remain vigilant, putting in extra considerations to ensure the safety of all.
Beginning its work at the pit, Nu ow Sydney City completed the four 60m relines in two weeks, working for 10-12 hours a day to ensure the job could be done on time.
To complete the work e ectively, they needed to divide the reline into four sections,

with the pipe bends and the ange ends done separately.
is was mapped out carefully to guarantee e ciency, with two to three relines completed per day.
ey would install one liner, allow it to cure, and then move on to the next pipe, adjusting the liners as needed.
At the end of the day, Nu ow would leave someone on site to supervise the curing overnight to ensure quality and grant the best chance for success.
At the end of the two weeks, a complete system was in place on time, with no gaps to cause future issues, allowing metro engineers to maintain their schedule.
Quality was at the forefront at every stage of this reline, and the team did not disappoint.
On schedule
Not only did the work of Nu ow Sydney City grant the project quality assets for years to come, but the Sydney Metro engineers were also able to maintain their schedule for their part in a major infrastructure project.
e newly relined system will be in use for years to come, and its Nu ow warranty means Sydney Metro can trust in the quality of its solutions.

International No-Dig heads to New Zealand
Auckland will host the acclaimed global trenchless technology event for the first time.
International No-Dig, the International Society for Trenchless Technology’s (ISTT) annual event, will be held in New Zealand in 2026 following a successful bid by the Australasian Society for Trenchless Technology (ASTT).
e event will be held at the newly built New Zealand International Convention Centre in Auckland from September 28-30, 2026.
“We’re thrilled to have won the bid to host the 2026 ISTT International No-Dig Conference and Exhibition in Auckland,” ASTT President Ben Crosby said.
“It will be a fantastic opportunity to promote and showcase the vibrant trenchless technology community in the Australasian region, particularly in New Zealand, to the rest of the world.”
International No-Dig New Zealand will feature a diverse range of equipment showcases, demonstrations, and conference sessions,
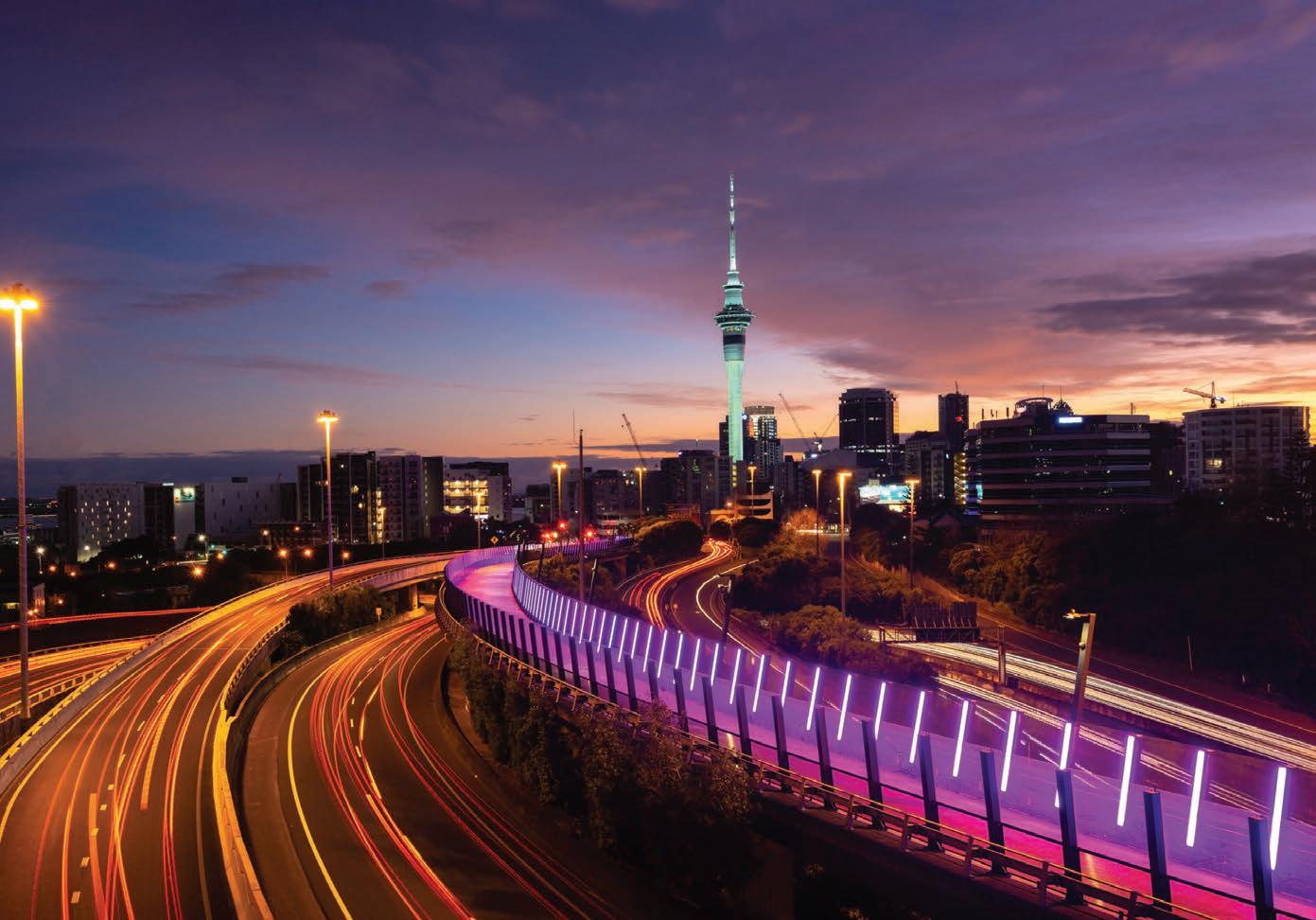
and highlighting the latest innovations in trenchless technology.
Delegates will gain valuable insights and solutions for critical infrastructure maintenance, projects, and upgrades.
is is the rst time that the prominent global industry event has been held in New Zealand. International No-Dig was last hosted in the Australasian region in Sydney in 2013.
New Zealand’s unique terrain presents challenges for traditional excavation methods, making trenchless solutions popular for infrastructure projects.
Signi cant projects have been completed, or are currently under construction, using trenchless technology including the 15km Central Interceptor wastewater storage tunnel, Project Hobson, and the Tauranga Southern Pipeline Harbour HDD crossing.
International No-Dig 2026 is organised in partnership with the ISTT by Prime Creative
Media, Australasia’s largest B2B publishing and events company.
“We’re excited to work closely with the ISTT to bring International No-Dig to New Zealand,” Show Director Lauren Chartres said.
In addition to publishing more than 50 plus leading industry publications across the resources, infrastructure and industrial sectors, including Trenchless Australasia, Prime Creative Media also runs No-Dig Down Under in partnership with the ASTT, the largest event for trenchless technology in the Southern Hemisphere.
“After the success of No-Dig Down Under over the last several years, we look forward to being able to bring this event to the global stage,” Chartres added.
International No-Dig 2026 is on sale with sponsorship and exhibition opportunities available now.
For more information, visit no-dignz.com

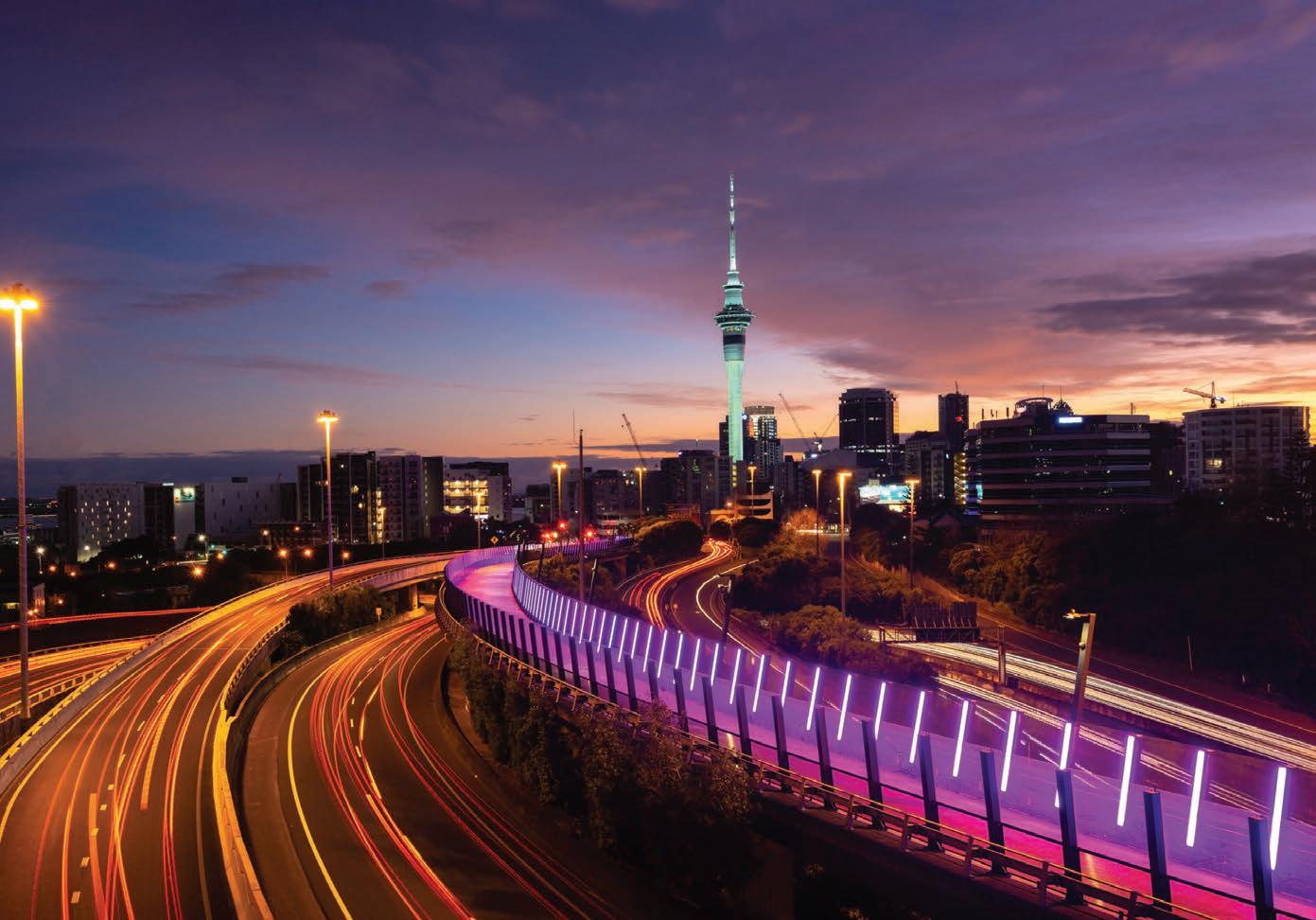
The ISTT’s International No-Dig is Landing in Auckland in 2026
New Zealand International Convention Centre, Auckland 28-30 September 2026
International No-Dig provides an unparalleled opportunity to connect with the global trenchless technology industry. Hosted each year in a different country to showcase the global industry, International No-Dig will bring together the best of the innovations and advancements in trenchless technology.
Corporate Members
Gold Corporate Members
DirectBor Australia
Herrenknecht AG
J&R Contracting Limited
Kellogg Brown & Root
Silver Corporate Members
Aaro Group
Abergeldie Rehabilitation Pty Ltd
ACP Australian Custom Pipes
Adept Drainage Pty Ltd
AECOM New Zealand Limited
AHD Trenchless
Applied Felts
Aqua Assets
AQUATEK Fluid Systems
Atteris Pty Ltd
Aurecon
Ausinland Pty Ltd
Aussie Trenchless Supplies Pty Ltd
Australian Pipeline Management Pty Ltd
Austunnel Pty Ltd
Ballarat Underroad Boring and Excavations Pty Ltd
BG Risk Solutions
Blick Group
Bortec Laser Bore Pty Ltd
BRP Corporation Pty Ltd
Bullseye Boring
CEA
CC Group
CDS New Zealand Ltd
Channeline International
D.J. Mac Cormick Contractors
DCS Manufacturing Pty Ltd
Derby Rubber Products
Digital Control - Australia
Directhitt Trenchless Pty Ltd
Diversified Services Australia
DM Civil
Dormway Pty Ltd
Draintech Solutions
Drillers World Australia
Dunstans
E&CC
Edge Underground
ELB Equipment Pty Ltd
Empire Infrastructure
FJA Consulting Engineers
Fulton Hogan
Asset Owners
Auckland Council
Barwon Water
Watercare Services Ltd
Michels Trenchless Pty. Ltd.
OptionX Group
Orion Consulting
Rangedale Rehabilitation and Renewals Pty Ltd
Systra Bamser
Fulton Hogan Construction Pty Ltd
Future-Proof Solutions
GCE Contractors Pty Ltd
GN Solids Control
Golder
Hard Metals Australia Pty Limited
HDI Lucas
Holcim (Australia) Pty Ltd
Hynds Pipe Systems Ltd
IMPREG (AUSTRALIA) PTY LTD
Independent Sewer Consulting Services
Pty Ltd
Insituform
Insituform Pacific Pty Ltd
Interflow Pty Ltd
Iplex Pipelines Australia
JB Trenchless Pty Ltd
kwik-ZIP Spacers
Kynection
L P Pipe Civil
LKL International Pty Ltd
M. Tucker & Sons Pty Ltd
March Cato Ltd
Matamata Directional Drilling
Maxibor Australia Pty Limited
McBerns Innovative Solutions
McConnell Dowell Constructors (Aust)
Pty Ltd
McElroy Manufacturing Inc.
McMillen Jacobs Associates (NZ)
Melbourne Water
Metrocorp Technologies
Mudex
Mullane Trenchless Pipeline Solutions Pty
Ltd
NEWest Alliance
NordiTube AUS Pty Ltd
Nu Flow Technologies 2000 Pty Ltd
Pezzimenti Laserbore Pty Ltd
Pezzimenti Trenchless Pty Ltd
Pezzimenti Tunnelbore Pty Ltd.
Pipe Core Pty Ltd
Pipe Doctor Australia Pty Ltd
Greater Western Water
Knox City Council
Bowley Plumbing Services
EnviroPacific- SOLVE
Tunnelling Solutions
Veolia
WSP New Zealand Ltd
Water Corporation
Pipe Technologies Ltd
Pipe Tek
Pipeline Drillers Group
Pipe Pro Drilling
PipeWorks
PLUMBLOGIC
Prime Creative Media
Prime Horizontal Pty Ltd
Qalchek Pty Ltd
Qenos Pty Ltd
R & R McClure Excavations
Raedlinger Primus Line Pty Ltd
Ravago NZ Ltd
RBM Plumbing and Drainage Pty Ltd
Ready Group Pty Ltd
Rob Carr Pty Ltd
Rose Atkins Rimmer (Infrastructure) Pty Ltd
RPC Pipe Systems
SA Water
SASTTI Joint Venture
Schauenburg MAB
SEKISUI Rib Loc Australia Pty Ltd
SEQ Trenchless
Sewer Equipment Company (Aust)
SLB-M-I SWACO
Smythe Contractors Limited
STRABAG
Sydney Water
TDG Environmental (NZ)
TDM Pipeline Solutions
TRACTO-TECHNIK Australia Pty Ltd
Trenchless Advisor Pty Ltd
UEA Pty Ltd
Vacvator
Vector Magnetics
Vermeer Australia
Vertical Horizonz Australia
Veolia (NZ)
Vinidex Pty Limited
Warren Smith & Partners
Yarra Valley Water
Zhangzhou Anyue Advanced Materials
Technology Co. Ltd
About the ASTT
The Australasian Society of Trenchless Technology (ASTT) is a non-pro t organisation comprising of members throughout Australia and New Zealand.
e successful establishment of the trenchless industry in Australasia has been supported and promoted by the peak industry organisation, the ASTT, since it was established in 1991.
e society works tirelessly to promote the use of trenchless technology in Australasia, lobbying government and client organisations to highlight the advantages of using trenchless technology and the bene ts of training for industry.
Membership is open to all who are concerned with the provision of gas, water, sewerage, drainage, roads, telecommunications and electrical services.
ASTT membership provides trenchless professionals the tools and services they need to be better informed and better connected in this industry.
e ASTT is part of the International Society for Trenchless Technology (ISTT), an a liation of societies in more than 30 countries worldwide.
Membership applications
e ASTT currently o ers seven levels of membership available to all residents of
Australia and New Zealand or anyone who is also a nancial member of an existing ISTT a liated society.
The benefits of Membership depending upon category can include:
Up to 10 people from your organisation may be included in your membership and are entitled to receive the below bene ts:
• Acknowledgment of your company in every edition of the Trenchless Australasia magazine.
• An annual subscription to Trenchless Australasia magazine (six issues per year).
• An annual subscription to ISTT’s Trenchless Works
• A company listing in the Australasian Trenchless Directory (print and digital).
• Opportunity to promote your membership of the association by including the ASTT logo on your business communications and website.
• Access to guidelines and standards.
• Discount rates (normally 10 per cent) at national conferences and exhibitions.
• Discount rates (normally 10 per cent) at international conferences and exhibitions.
• Discount rates (normally 10 per cent) at trenchless forums.
• Opportunity to become involved in our Special Interest Groups which
are technical divisions of the ASTT representing speci c trenchless sectors.
• Special o ers and links with international organisations including the ISTT.
• Opportunity to nominate for ASTT and ISTT awards.
• Free access to ISTT past conference proceedings.
• A communication network to keep abreast of the advancement of the science and practices of trenchless technology throughout the world.
• Discounted rates at international No-Digs and national events including No-Dig Down Under.
How to apply
Visit the ASTT website on www.astt.com.au and check out the membership bene ts that apply for each category.
Your membership request will be emailed directly to the ASTT for processing. You will receive an invoice based on the information you supply. Acceptance does not take e ect until payment is received in full.
For more information, visit astt.com.au or email secretary@astt.com.au
People on the move
Trenchless Australasia is tracking new appointments in Australia and New Zealand’s trenchless industries. Read all about the latest people moves.
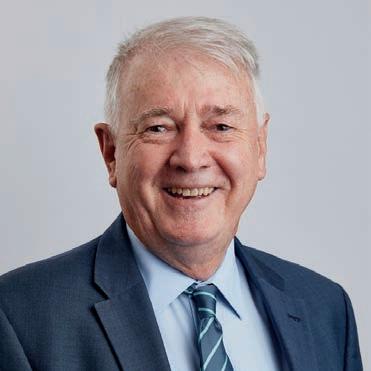
Kevin Young – Chairperson –TasWater
Current board director Kevin Young has been appointed as TasWater’s next chair, replacing outgoing Dr Stephen Gumley AO who has served in the role since 2018.
Young brings a wealth of experience to the role, with more than 40 years in the water and sewerage industry in Australia.
“It’s an exciting time to be taking on the role of chair at TasWater as we have recently endorsed a bold and ambitious strategy for the next phase of the organisation’s growth,” he said.
“I’m passionate about the future of the state and the role our organisation can have in delivering great community, environmental and economic outcomes for Tasmania.
“We are well underway in developing our next Price and Service Plan for submission in June 2025.
“Our plan is to deliver a $1.9 billion capital program over the next five years that will bring real benefits to the community and environment, responding to climate change to secure water resources.”

Rob Corrigan – General Manager –OptionX Bournedrill
Rob Corrigan has made the move to OptionX Bournedrill, where he has taken up the role of General Manager.
Corrigan brings a wealth of experience to the role as an experienced Manufacturing Manager with a demonstrated history of working in the automotive industry.
Corrigan’s previous experience includes stints at Apollo Manufacturing, Apollo Motorhome Holidays, Bruder Expedition and TJM 4x4.
He will be supported in his new role by another new hire with Craig Hills recently appointed as the OptionX Bournedrill’s Operations Manager.
Enrico Da Costa has also joined as Internal Sales and Purchasing Officer, adding renewed energy and a strong focus on customer service.
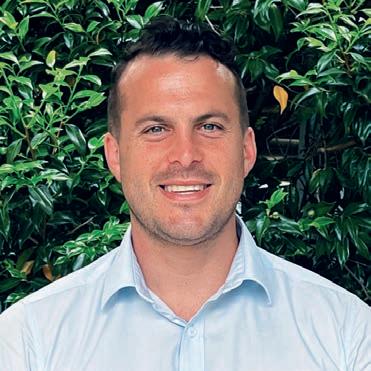
Jamil Tye – Independent Aboriginal Delegate – Yarra Valley Water
Yarra Valley Water has announced the appointment of Yorta Yorta and Boonwurrung man Jamil Tye, as an Independent Aboriginal Delegate to its board of directors.
Tye is the organisation’s first Independent Aboriginal Delegate to be engaged in the role, effective September 2024.
Before joining Yarra Valley Water, Tye was the Director of the William Cooper Institute, named a er the revered Yorta Yorta Aboriginal activist, and who is family to Jamil through his sister Ada.
He currently serves as the Executive Director of External Community Engagement and Impact at Monash University and has extensive experience across the education, government and mining sectors.
“This is an incredibly exciting opportunity for me,” Tye said.
“It aligns with my values, as well as my commitment to advocate for the education, health, and wellbeing of Aboriginal and Torres Strait Islander Peoples.”
If your company has recently employed a new person within your business you would like profiled in ‘People on the move’, send details of the career news alongside a high-res photo to Darragh Bermingham at darragh.bermingham@primecreative.com.au
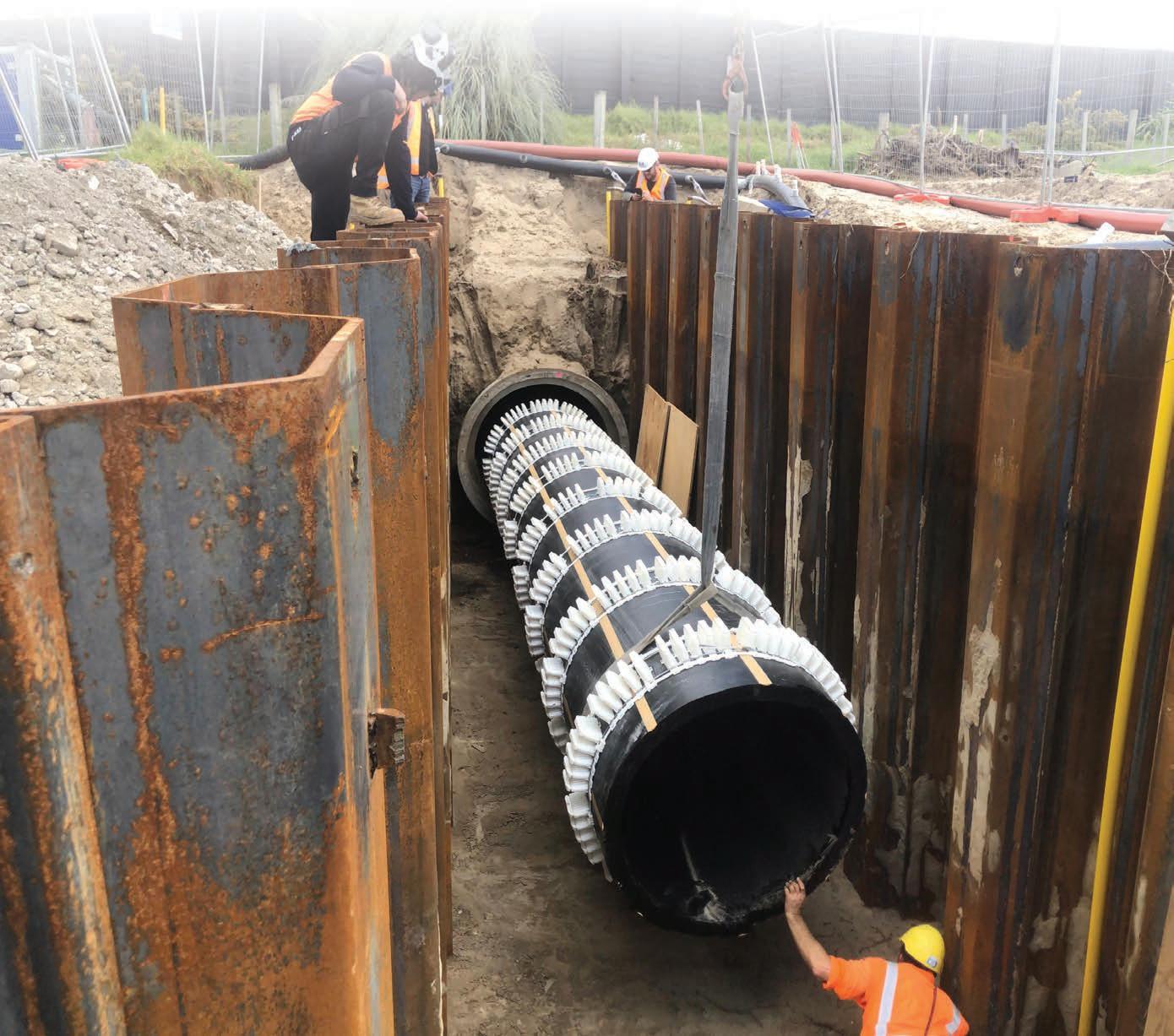
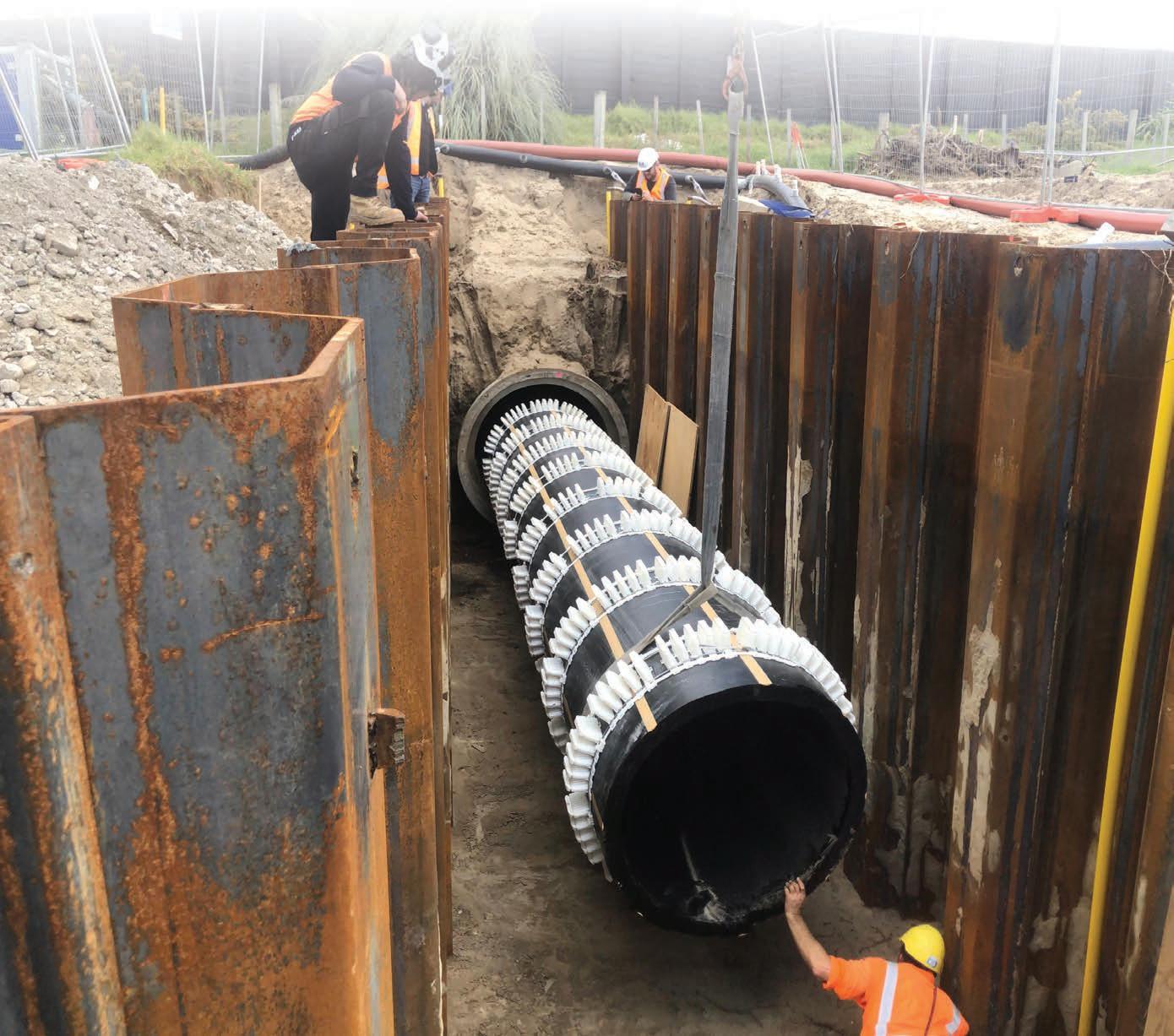
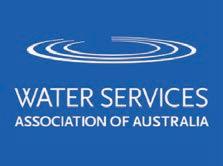
CONSTRUCTION SPECIALISTS YOUR UNDERGROUND
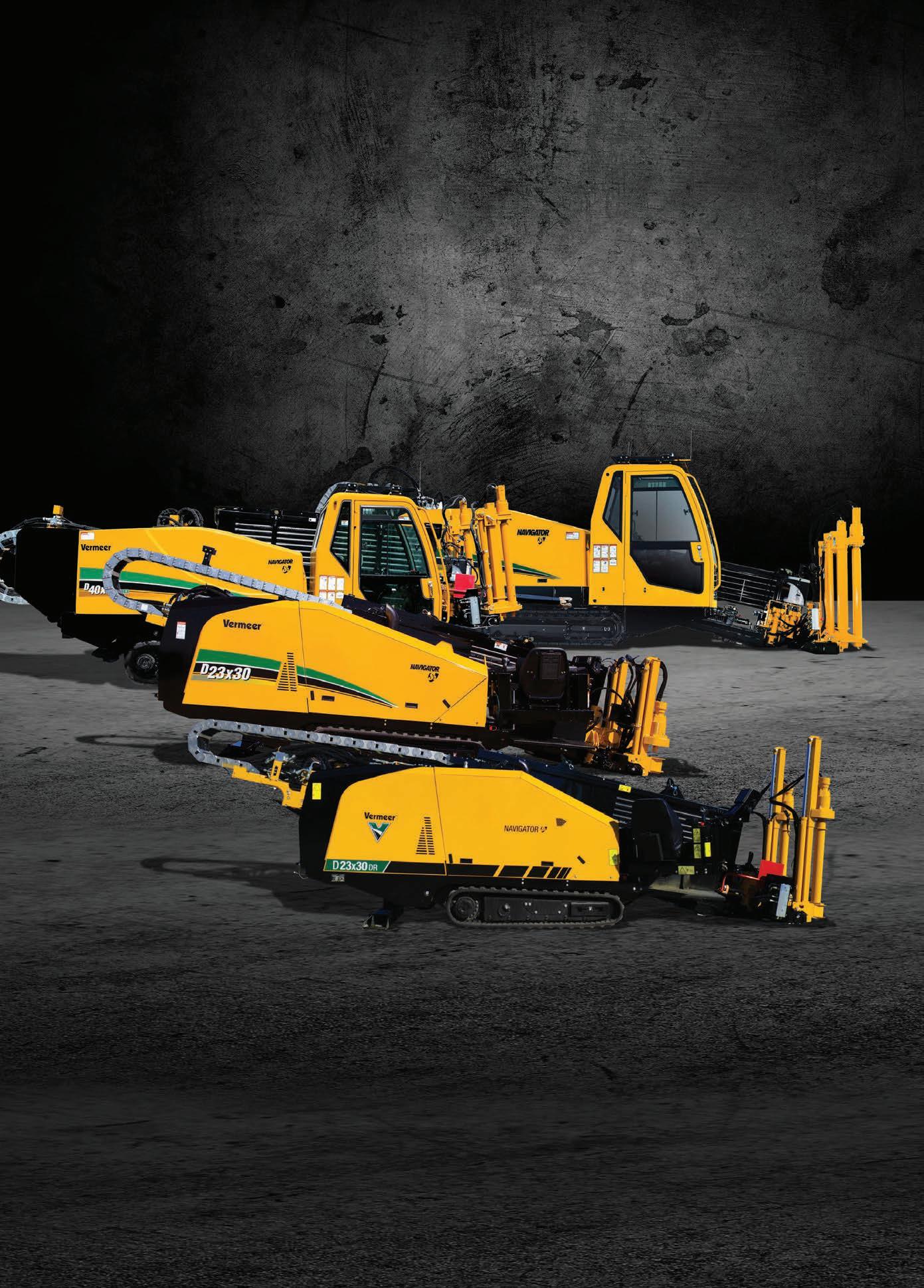
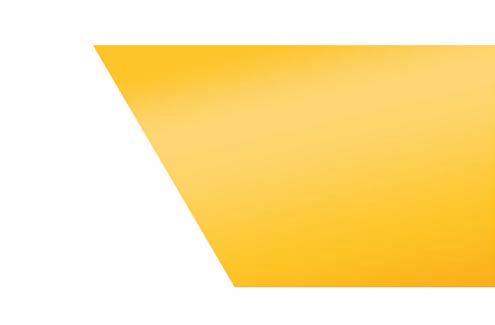