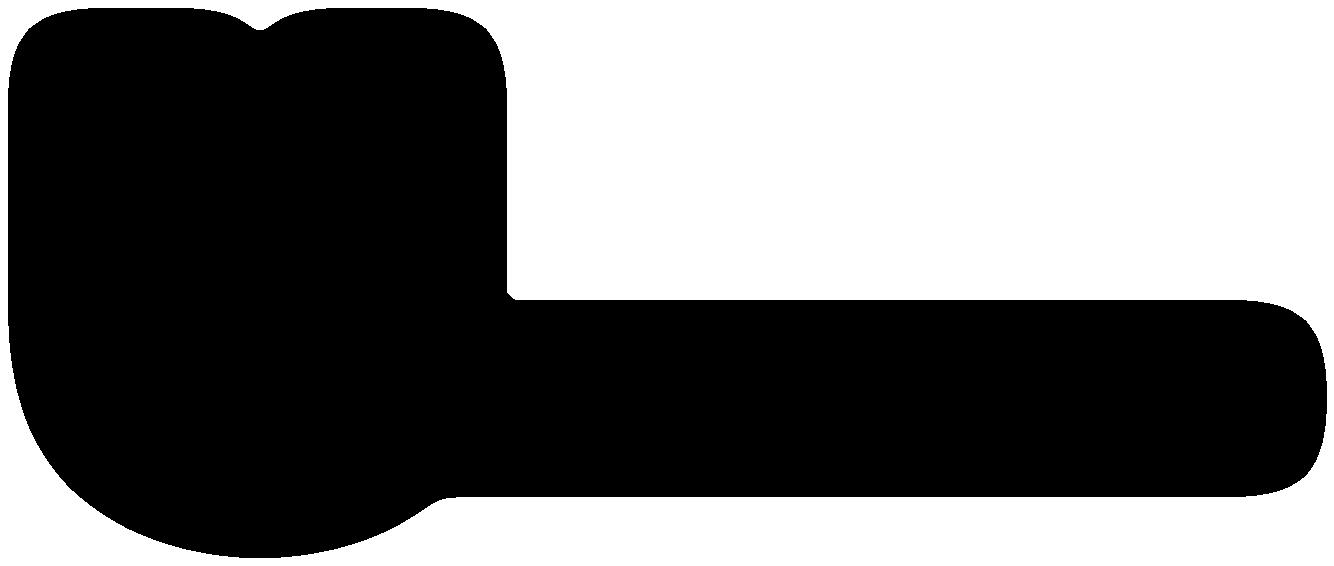
the gas UNPACKING THE FUTURE GAS STRATEGY

the gas UNPACKING THE FUTURE GAS STRATEGY
Australia is lagging overseas markets. Currently, new cars in Australia use 40% more fuel than the EU, 20% more than the US, and 15% more than New Zealand. Transportation accounts for approximately 19% of Australia’s total greenhouse gas emissions, and it’s on track to be the largest source of emissions by 2030.
However, the government is introducing fuel efficiency standards and a plan to accelerate the rollout of EVs nationally. State and federal governments are working to reduce emissions across their own fleets, and many businesses are too. Sustainability is good news for fleet managers. An efficient fleet isn’t just good for the environment, it’s good for business too. And telematics makes the change easier than ever.
By providing visibility over a fleet, managers can find ways to reduce costs and mitigate environmental impacts. Real-time analytics allow for immediate adjustments, leading to reduced carbon footprint and a move towards achieving environmental targets. Detailed data on maintenance, fuel consumption and driver behaviours can help businesses unlock more efficiencies. And by reducing unnecessary idling and optimising routes, telematics can help reduce emissions and operational costs.
Geotab’s Green Fleet Dashboard helps fleet managers monitor indicators ranging from fuel usage to emissions, and compares fleet fuel economy with a benchmark of similar fleets in the Geotab ecosystem. It provides the hard data needed to validate green initiatives to stakeholders and regulatory bodies.
As governments worldwide push for lower emissions, the transition to EVs is accelerating. In practice, EVs are more likely to be integrated into a fleet slowly, with managers transitioning when they retire their oldest and least efficient vehicles. Telematics makes it simple for managers to figure out which vehicles to replace, providing guidance on which EVs provide the greatest long-term financial benefits and environmental impact.
Geotab’s Electric Vehicle Suitability Assessment report offers fleet managers transparency by gathering data about a fleet and comparing it with the manufacturers data for EVs in each market. After making the switch, telematics can optimise range management, while remote monitoring and diagnostics capabilities allow access to real-time data, enabling prompt and effective vehicle maintenance.
Telematics stands at the centre of modern fleet operations and Geotab is committed to enabling real and measurable progress towards sustainability, while helping businesses manage their costs.
For more information, visit geotab.com/au/
Scan to subscribe to Utility magazine’s weekly newsletter – delivered to your inbox every Thursday
Published by
ABN: 51 127 239
379 Docklands Drive
Melbourne VIC 3008 Australia
P: (03) 9690 8766
www.primecreativemedia.com.au enquiries@primecreative.com.au
ISSN: 2203-2797
Editor Katie Livingston
Assistant Editor
Steph Barker
Journalists
Tess Macallan, Kody Cook, Sarah MacNamara
Art Director
Alejandro Molano
Designers
Danielle Harris, Jacqueline Buckmaster
National Media Executives
Rima Munafo
Marketing Manager
Radhika Sud
Marketing Associates
Bella Predika
Digital Marketing Assistant
Emily Gray
Publisher
Sarah Baker
Managing Editor
Laura Harvey
As we wrap up the first month of the new financial year, it’s hard to believe that we’re already halfway through 2024.
The recent allocations in the Federal Budget further demonstrate that 2030 is just around the corner and the race to net zero is front of mind for utilities in every sector.
In this August 2024 issue of Utility, we take a look at some of the astounding work that these utilities are undertaking to reduce their carbon emissions, build a circular economy and drive the transition to renewable energy – as well as to support the people who both depend on their essential services and help deliver them.
To kick things off, we travel up to the sunshine state, where the several major water infrastructure projects are underway. The Gladstone Area Water Board shared the latest updates on the Fitzroy to Gladstone Pipeline – which is now more than 50 per cent complete –and we also look at the new partnerships that are helping Sunwater to deliver essential infrastructure projects on time and in budget.
Over in Western Australia, both Synergy and Horizon Power are undertaking some exceptional work in energy storage, and we take a deep dive into the state’s isolated electricity system and the unique challenges that this presents for the transition to renewable energy in Western Australia.
Reaching net zero isn’t just a hurdle for the energy sector, and many water utilities are already working hard to play their part. In this issue, we cover two brilliant projects that Yarra Valley Water and the University of Technology Sydney are undertaking to turn food waste into a source of energy.
While innovative technology and groundbreaking projects are needed to
drive Australia towards net zero, what’s just as important are the people driving that innovation. We spoke with South East Water about the utility’s recent pilot enterprise process, which focuses on human centred design and puts it’s people at the heart of innovation. We also cover the recently announced Safety by Design partnership that seeks to aid utilities in protecting vulnerable customers experiencing domestic violence.
It’s inspiring to see the fantastic drive and innovation that is continuously pushing the industry forward, and it’s an incredible privilege to be able to share the fantastic achievements of utilities across the country.
Katie Livingston Editor
Advancing customer outcomes by quantifying customer values 20
Technical to flexible: how values-led hiring is opening the door for women in water
From then to now: a trenchless transformation
Safety by Design: how utilities can lead the charge against domestic violence
Transforming fleet management with
Shaping the future of
Driving
Securing Central Queensland’s water future 40
Central Queensland has endured some of the most severe dry conditions the state has ever seen over the past decade.
FMT named as Australian distributor for SFE Group 44
Innovating the future: setting new standards in HDD accuracy 46
Spoilt for choice: AVK unveils new high-quality valve solutions �����������48
Sunwater takes an integrated approach to deliver critical water infrastructure 50
With the growing focus on improving long-term water security and availability across Queensland, the delivery of quality infrastructure projects has never been more important.
Urban organics are an important resource in Australia’s biogas production
The energy, water and waste sectors are all striving to achieve net zero emissions by 2050. A recent study from researchers at the University of Technology Sydney (UTS) found that urban organic waste has a significant role to play in meeting this goal.
Gippsland Water has renewed its Climate Change Strategy, building on the knowledge it has gained since the strategy was originally launched in 2017. This renewal sets ambitious new targets to achieve net zero emissions by 2030 – two decades earlier than first planned.. The right tool for the job: how effective maintenance can
Innovating for a sustainable future: Yarra Valley Water’s Lilydale Food Waste to Energy Facility 86
As the demand for sustainable waste management solutions grows, Yarra Valley Water is at the forefront, developing food waste to energy facilities that convert commercial food waste into clean, renewable energy. These initiatives make recycling food waste easier and more affordable for local businesses in the area.
Net zero on the Horizon: piloting innovative LDES solutions 74
Changing the game: tacking network constraints with third-party innovation 60
As populations grow and consumers become more reliant on electricity, it’s essential than energy networks are upgraded to ensure that they have the capacity to meet demand. To assist with delivering these essential upgrades, CitiPower and Powercor have launched an online platform for third party solutions to network constraints.
Harnessing Australia’s solar power: Avonlie Solar Farm driving sustainable electrification 62
Leading the charge: large-scale BESS supporting renewables in WA 64
Filling in the gas with the Future Gas Strategy 68
In May 2024, the Federal Government released its Future Gas Strategy, providing the gas industry and utilities with greater clarity on how the government is approaching the unfolding energy transition.
Empowering remote communities with revolutionary generation technology 72
Long-duration energy storage (LDES) will play a critical role in supporting Western Australia's journey to net zero carbon emissions by 2050. The state’s regional energy provider, Horizon Power, is embracing the latest technology, with innovative LDES trials to support the state's acceleration to a cleaner, greener future.
Improving the energy resilience of municipal pumping stations 78
The increase in extreme weather, flooding and bushfire events underscores the importance of resilient utility infrastructure, as failure of these assets can have devastating consequences. In a unique pilot project, Shoalhaven Water and the University of Wollongong are collaborating to improve the energy resilience of sewage pumping stations with innovative battery energy storage systems.
Batteries hosted on the grid side of the meter can be used for the benefit of all customers, not just those who can afford to buy them.
The Australian Energy Market Operator’s (AEMO) Integrated System Plan (ISP), highlights the enormous role that energy storage will play in the future grid. This includes customer energy resource (CER) batteries installed behind customer meters, as well as grid-scale storage and deeper energy storage systems, such as pumped hydro.
RACKING AND STACKING THE VALUE OF BATTERIES
Batteries can play versatile roles as veritable ‘swiss army knives’ of the grid. The balance between power capacity (in MW) and energy capacity (in MWh) varies across a broad spectrum and determines the role a storage system is best suited to playing, such as:
• Shorter duration resources – CER batteries or ‘two-hour’ grid-scale batteries – are suited to moving smaller volumes of energy around during the day to fill small gaps.
• Longer duration resources – pumped hydro or other long duration technologies – are suited to moving much larger volumes of energy across weeks or months.
These roles for storage create real value for customers. However, the focus is on ensuring that the supply is there to balance with demand in real time in a system that is increasingly dominated by renewable sources of generation.
These vast changes in the patterns of supply and demand system place new stresses and operating conditions on the energy system, impacting reliability.
However, many of the challenges faced by the physical electricity system in the future grid can be alleviated by moving energy across time. Batteries can provide network service value to the users of the shared electricity grid by: Reducing peak electricity load – this can avoid the need to invest in firming the physical grid assets to withstand higher electricity flows
• Allowing more hosting capacity for residential solar PV – for example, by safely allowing more homes to export excess solar into the grid
• Reducing minimum net system load – excess solar during the day reduces system load and, if left unmanaged, will drive higher network costs in the future grid. Batteries that soak up this excess solar can help avoid these costs.
• Helping control voltage – this allows networks to keep the system within the technical limits at lowest cost to customers
• Providing backup power – this can reduce the impact of a network constraint or outage, which is particularly useful for remote areas
• Providing a more resilient grid – in the face of natural disasters or other emergencies, battery storage can provide backup power to critical infrastructure, reducing outages and improving grid and community resilience beyond simple measures of electricity system reliability.
Batteries can also help control frequency on the power system by interacting with frequency control markets, and provide system security services, such as inertia and system strength.
Batteries in the future grid will likely be at all scales and locations. The tricky question for policy makers will be in how to incentivise the right mix and balance of resources to ensure efficient energy costs for customers over the long-term. This will require a good measure of system planning and clear policy direction.
The most important objective, as we move from around 5GW of storage today to more than 50GW in 2050, is to get the most out of these resources for customers.
There is a strong case for batteries to be hosted on the shared distribution networks as the most efficient and equitable approach to delivering battery storage at scale. This approach:
• Is lower cost to deliver – a program of larger batteries (around 5MW in capacity) can be rolled out at a lower capital cost per unit of installed capacity
• Leverages the most network value – batteries embedded in the right locations in the distribution grid allow the best network value to be captured
Delivers certainty in operation – a smaller number of larger batteries on the distribution grid that have clear contractual arrangements helps keep the grid within its limits, and provides greater certainty of compliance and delivery of services to the network and market operator
This approach is also more equitable, CER batteries currently require government incentives to support uptake, which in itself is a significant transfer of wealth to those who are able to afford the rest of the up-front cost of a battery. Battery owners
will also be able to offset a larger proportion of their network and energy costs behind their meter, and, if orchestrated into a virtual power plant, will also be compensated for the value their asset provides to the broader energy system.
DNSP-owned, retailer-operated, medium-scale battery storage connected to the distribution grid could maintain the balance between a competitive market, thereby ensuring system security and reliability, maximising the overlooked potential of the poles and wires in the street and helping to close the growing energy equity gap.
As batteries can provide both network and market services, both networks and other parties can lead the roll-out of infrastructure. There are, however, several natural advantages for distribution network business in rolling out batteries at scale, allowing them to pass on a greater share of value to customers, including the ability to:
Move at speed and scale, fully leveraging scale efficiencies and delivering policy objectives on time
• Use existing land assets to host batteries, lowering the cost of delivery. This also avoids the social license cost of procuring new land within communities and navigating its change of use
• Fully embed battery storage into the planning and design of networks
Leverage existing processes and workforce for the operation and maintenance of assets
• Partner with market facing third parties at scale, which can reduce the barriers for those parties to manage wholesale energy market risks through physical hedging. This would also improve retail competition
This does not all mean that distribution connected batteries should only be built by distribution networks. All network connected batteries will have value, and networks will need to do more to provide transparent and up to date information on evolving network needs, and also to provide efficient avenues for battery proponents to provide non-network services and to connect to the power system.
It is critical that a distribution network battery roll-out transparently and effectively addresses the ‘who pays for what’ question. While customers ultimately pay, it is important that networks only recover the costs of batteries to the extent that they provide valuable services to customers.
There are existing regulatory tools to manage this, such as the cost allocation methodologies that each network business has approved by the Australian Energy Regulator (AER). These methodologies define the network’s approach to allocating costs between the different categories of services that it provides.
While networks can own batteries, they are restricted from using them for non-network services unless they obtain a waiver. This gives the AER comfort that the arrangements in place for each network-owned battery are appropriate. As all parties become comfortable with these bespoke arrangements, it is likely that in time they will prove unnecessary and can fall away in favour of more enabling and enduring arrangements for the transition.
Given the broad range of network services that batteries provide, it is likely that they will soon be seen as being as integral to the provision of network services as transformers or poles and wires. A direct analogy can be found in our gas transmission networks, which provide an inherent storage value that is valued by customers in their reliable gas supply.
It would be unusual if our battery ‘best and fairest’ award winner were to face pervasive or unnecessary regulatory hurdles to delivering core network services to customers as batteries shift from ‘innovative’ to ‘ordinary’. On the flip side, regulators will need to see real value for customers if they are to evolve their approach.
To help with this, ENA has partnered with L.E.K. Consulting and other modelling experts in a wide-ranging scenario exercise that draws out the value of different actions that could be taken on the distribution grid to drive the greatest value for customers while helping deliver the transition. This work explores the value of distribution connected batteries in more detail.
WSAA’s new guide seeks to initiate the process of fostering a comprehensive understanding and recognition of the significance of Scope 3 emissions. It aims to facilitate increased consistency and credibility in managing these emissions across the water sector.
For the majority of Australian enterprises, the costs associated with greenhouse gas (GHG) emissions and the opportunities for their reduction largely lie beyond their organisational boundaries.
However, this paradigm does not necessarily apply to water utilities, which are at the forefront of achieving net zero (Scope 1 and 2) emissions.
Through pioneering investments in renewable energy technologies – such as pumped hydro, enhancements in efficiency measures, the conversion of waste to energy, and the development of resource production products like biochar – water utilities are adopting circular, innovative approaches to mitigate direct emissions while bolstering the resilience of water and wastewater systems.
Nevertheless, the measurement and management of Scope 3 emissions – indirect value chain emissions stemming from a water utility’s operations but not under its direct ownership or control – present substantial opportunities to holistically reduce cross-sector emissions in the delivery of water services.
The water sector is poised to continue its leadership role in societal stewardship through effective cross-sector partnerships, which is pivotal as we transition to a low-carbon economy. This transition aims to lower community costs, enhance the liveability of urban and rural areas, and foster public health and economic prosperity.
Addressing Scope 3 emissions in the water sector is an emerging challenge with only a few utilities publicly reporting.
The sector faces hurdles such as the multitude of available frameworks and standards, establishing measurement boundaries, achieving methodological consistency, and new climate-related financial disclosure requirements. One example is the anticipated release of the Australian Sustainability Reporting Standards – Disclosure of Climaterelated Financial Information by the Australian Accounting Standards Board which will further underscore the need for robust Scope 3 emissions reporting.
The Guide to Scope 3 Emissions Management for the Water Sector supports utilities in evaluating their Scope 3 emissions profiles, provides agreed principles for defining Scope 3 emission boundaries, and explains the complexities and assumptions in various reporting methods and tools. The ultimate objective is to reduce material emission sources from value chains.
Designed in an accessible, step-by-step format, the Guide supports water utilities at varying stages of Scope 3 emissions management, from initial investigations to setting targets and actively reporting on these emissions.
WSAA remains committed to continuous improvement and updating the Guide to reflect member feedback or regulatory changes, including any new climate-related financial disclosure requirements. By embracing this Guide, water utilities can better navigate the complexities of Scope 3 emissions management, moving forward to reduce emissions.
To
In the utility industry, ensuring the integrity of security seals is paramount, and when a legal issue arises, proving that a seal’s number is unique and exclusively issued to your company is crucial. But how do you ensure your supplier can provide the necessary documentation?
A TOOLLESS METER SEAL WITH WIRE.
IMAGE: HARCOR
As Australia’s first dedicated security seal supplier, Harcor understands just how important a well-managed and precise seal numbering system is for utilities.
Building on its local seal printing capabilities and extensive experience, Harcor’s leadership in this area stems from its Exact and Track system, which is specifically designed to manage seal numbers with precision and accountability.
Harcor’s Exact system exemplifies how serial number duplication is prevented, offering not just a seal but the assurance of seal number management.
Establishing a robust seal numbering system that meets conformity and regulatory requirements is vital. For Harcor, partnering with Exact Software was essential. The system complies with NEN-EN-ISO 9001:2015 standards, including custom solutions within its certification scope.
This allows Harcor to verify the uniqueness of each security seal number provided to customers, supported by the current NEN-EN-ISO 9001:2015 certificate.
For those in the utility sector, the uniqueness of security seal numbers should never be overlooked. Professionally managed numbering systems are why Harcor remains a highly trusted security seal supplier in Australia. Choose Harcor for peace of mind and unmatched reliability in security seal management.
HARCOR’S EXACT AND TRACK SYSTEM ALLOWS IT TO VERIFY THE UNIQUENESS OF EACH SECURITY SEAL NUMBER.
THE CLIMATE SMART ENGINEERING CONFERENCE IS AN EVENT DEDICATED TO ADDRESSING CLIMATE CHANGE FROM AN ENGINEERING PERSPECTIVE.
The shift to renewable and clean energy sources requires innovative engineering solutions that ensure reliability, cost-effectiveness and sustainability.
Climate Smart Engineering Conference Thursday 22 August | Brisbane
To view the program and register, visit engineersaustralia.org.au/cse
On 22 August 2024, Engineers Australia will deliver the Climate Smart Engineering Conference (CSE24), an engaging, one-day program focused on a significant climate challenge – the clean energy transition. Engineers Australia CEO, Romilly Madew AO, said this conference is an opportunity to hear from a wide range of experts in climate smart engineering, learn from successful technical solutions and strategies, and connect with peers.
“CSE24 brings you the latest insights and engineering innovations – examining everything from the role of digital technology and AI to the challenges of decarbonising transport and upskilling in renewable energy,” Ms Madew said.
Navigating regulatory and policy frameworks, and taking a system-of-systems approach to planning future energy systems will also be key themes at the event.
Now in its fourth year, CSE24 is dedicated to addressing climate change from the engineering perspective.
With engineers and industry poised to play a major role in Australia’s clean energy transition, this is an opportunity to network, connect and collaborate to build a better and more sustainable world.
Trackable Serial Numbering
Expose Unauthorised Access
EJ’s innovative composite access covers are engineered and tested to Australian Standards, for harsh, challenging conditions. High-quality composite access covers are lightweight and anti-corrosive, which provides new advantages and a fresh level of choice for project managers of utilities and municipalities, engineers and designers.
WHY USE COMPOSITE ACCESS COVERS?
High-performance composite access covers are a relatively new arrival in the Australian market and come with many key benefits that make them a valuable solution across the board, and allows them to meet the specific needs of certain industry sectors, including:
• Ergonomic design – resulting in lower product weight
Corrosion resistance – material resistance to corrosion for H2S or other chemicals
No signal interference – radio frequency (RF) friendly for transfer of signals
• Environmentally friendly – low energy consumption in manufacturing
• Minimal risk of theft – due to no scrap value
Variety of colour options – colours are permanent and UV resistant
The Australian Standard AS3996:2019 sets the industry benchmark for access covers, grates and frames for the Asia Pacific region.
Composite products must meet a number of specified design features and a comprehensive series of tests that must be passed to fully comply with the Standard.
As an industry leader, EJ has commissioned its own research and testing to demonstrate its commitment to the Standard, ensuring that all requirements are met.
The company maintains its own NATA Accredited testing facility in Brendale, Queensland and also utilises independent third party NATA test resources.
For more information, visit ejco.com/global or email au.info@ejco.com
The Victorian Government has released a prospectus outlining its future intentions under the Murray Darling Basin Plan, aimed at minimising the impacts of recent changes to the plan from the Federal Government.
Victorian Minister for Water, Harriet Shing, recently published Planning Our Basin Future Together: A prospectus to safeguard Victoria’s environments and communities across the Murray-Darling Basin.
The prospectus was developed following extensive and meaningful engagement by, with, and for Victoria’s Basin communities. It details the next steps Victoria will take following the Federal Government’s decision to buy back up to 450GL of additional water.
Following the release of the prospectus, community engagement will continue across Victorian Basin towns, with industries and stakeholders to identify innovative new alternatives to open tender water purchases – projects and outcomes that deliver healthy waterways and resilient environments –without causing harm to communities.
The community-driven options will then form the basis of negotiations with the Federal Government on delivery, to ensure Victorian Basin communities’ priorities are front and centre in the Federal Government’s delivery of the Basin Plan.
The prospectus follows the Federal Government’s agreement that funding for Victorian environmental projects is essential to the delivery of the Basin Plan.
The Victorian Government said it remains opposed to buybacks and has not signed any agreement with the Federal Government in exchange for this funding.
Victorian Minister for Water, Harriet Shing, said, “Our communities know better than anyone that healthy waterways mean healthy communities and productive crops –and we will continue to work with the Commonwealth and all Basin states to innovate, collaborate, and deliver better outcomes for the entire Basin.
“We will continue our advocacy with and for Victorian communities and the environments they depend upon, while protecting households from avoidable increases to the cost of living,” Ms Shing said.
• NEW BLUETOOTH CAPABILITY FOR MAPPING
• COMPATIBLE WITH TRIMBLE DA2 GPS ANTENNA
• IMPROVED PERFORMANCE ON WEAKER SIGNALS
• STANDARD LITHIUM BATTERIES FOR RX & TX
• TRANSMITTER TO RECEIVER COMS
• PASSIVE POWER HARMONICS MODES
• BEST VALUE PROFESSIONAL LOCATOR
• NEXT GENERATION DUAL FREQUENCY
• COMPACT, LIGHTWEIGHT DURABLE DESIGN
• ROUGH TERRAIN ABILITIES WITH LARGER WHEELS
• VIEWPOINT AND EXTERNAL GNNS/GPS FOR ACCURATE MAPPING ABILITIES
• SEE WHY SO MANY PROFESSIONAL LOCATORS USE THE PINPOINTR
• INNOVATIVE PRODUCT FOR LOCATING CABLES.
• POWERFUL INBUILT TRANSMITTER
• 33, 65 & 131 KHZ STANDARD FREQUENCIES
• PHONE APP CAPABLE ALLOWS YOU TO CHANGE POWER AND FREQUENCY FROM YOUR PHONE.
• AVAILABLE IN 150MM 100MM AND SOON 50MM SIZE
The funding includes a $324 million investment that will allow Western Power to continue assessing and developing potential Clean Energy Link transmission projects, including the procurement of long-lead items.
Funded in the 2024–25 State Budget, the $500 million Strategic Industries Fund is expected to deliver commonuser and other enabling infrastructure at SIAs across regional and metropolitan Western Australia.
The fund will also enable Western Power to continue to assess and develop potential Clean Energy Link transmission projects, including the procurement of long-lead items, as well as expanding the South West Interconnected System in the central, southern, and northern sections.
The $500 million funding is designed to unlock Western Australia’s strategic industrial areas (SIAs) and to pave the way for the state to become a global clean energy powerhouse.
Western Australia is home to 13 SIAs spanning the entire state, including Browse, Boodarie, Burrup, Maitland, Anketell, Ashburton North, Oakajee, Kwinana, Rockingham, Kemerton, Shotts, Mungari and Mirambeena.
There has been significant interest in access to industrial land across Western Australia for renewable hydrogen, critical minerals processing and other job-creating industries.
The Strategic Industries Fund will be used to prepare land for future industrial projects, ensuring that the state is primed for sustainable growth and development.
An initial $125 million will be invested to open up new industrial land at Latitude 32 in Kwinana, given the strong demand for land in Perth’s industrial heartland – with recent allocations in the Kwinana and Rockingham SIAs towards a range of job-creating projects.
A further $20 million will be allocated to develop general industrial land in Karratha and in the Peel region, while $20
million has been set aside to unlock land in the Goldfields and South West.
Those investments build on the $35 million investment into the Industrial Land Development Fund included in 2023’s Budget, which has progressed planning works on priority SIAs at the Pilbara.
The Strategic Industries Fund is on top of the $160 million industrial lease incentive scheme announced late last year, designed to attract clean energy projects to SIAs.
Western Australia Premier, Roger Cook, said, “Western Australia is the engine room of the nation’s economy, and I want to make sure our state becomes a global clean energy powerhouse.
“We have the renewable resources, skills and trading partnerships to become home to job-creating clean energy mega-projects, and our Strategic Industries Fund will help to unlock the industrial land we need to get these projects off the ground.
“This $500 million fund will open up industrial land right across our regions and in Perth, helping us to attract the major clean energy industries of the future to Western Australia.
“My government will always do what’s right for Western Australia, and that means setting up our state’s economy for the long term.”
Western Australia Lands Minister, John Carey, said, “Through the 2024–25 State Budget and a major $500 million investment, the Western Australia Government continues to facilitate and support more clean energy production across metropolitan and regional Western Australia.
“Our 13 strategic industrial areas each attract important investment into the state to grow emerging industries and support local jobs.
“Our government remains focused on supporting renewable energy industries that will help transform and
future-proof our economy, while creating skilled local jobs for the future.”
Western Power welcomed the funding, which includes a $324 million investment into the state’s main electricity network to enable industry to expand and unlock job-creating renewable energy projects.
The investment will fund Western Power to continue assessing and developing potential Clean Energy Link transmission projects, including the procurement of long-lead items.
Clean Energy Link transmission projects have been identified to meet renewable generation demand for Western Australia’s future, expanding the South West Interconnected System in the central, south and northern sections.
This investment builds on the more than $4 billion committed to unlocking Western Australia’s cleaner, affordable and reliable energy future through investment in wind generation, battery systems and the electricity grid over the past 12 months.
The Western Australia Government has also allocated $147.6 million to support the development of common user network infrastructure in the North West Interconnected System, designed to open up new opportunities for clean energy, subject to Traditional Owner negotiations.
Other new investments include:
$18.4 million for the deployment of 50 standalone power systems in Esperance and the Mid West
$7.5 million to fund rebuilding the Blackstone remote community’s power station
• $ 4.5 million to buy existing power station assets in Ardyaloon, Bidyadanga, Beagle Bay, Djarindjin Lombadina and Warmun
The additional investments in the 2024–25 Budget bring the total investment by the Western Australia Government into the energy transition to more than $5.4 billion since 2017, including new generation, transmission and storage.
CitiPower crews have begun works on one of Melbourne’s largest underground tunnels, which carries high voltage cables powering large parts of the CBD.
The tunnel, first built in the 1930s and stretching 80m beneath Little Queen Street, is receiving an upgrade to secure the structure for another century while also allowing room for greater power flows as the city grows.
The tunnel upgrade is a precursor to a larger three-year revamp of the nearby zone substation that will provide greater capacity and flexibility to support both planned new developments in the city
and greater electrification of existing customers across the CBD.
CitiPower Head of Network Planning, Andrew Dinning, said demand across Melbourne CBD is expected to increase by at least 60 per cent over the coming decade, with demand set to grow from its current peak of 470MW from recent years to more than 700MW.
“Melbourne is growing and we are continuing to develop the infrastructure that is essential for powering our city into the future,” Mr Dinning said.
“This major upgrade will allow us to maintain the reliable, flexible and secure power supply that is critical to our
city’s economy, future growth and clean energy transition.”
CitiPower Major Projects Project Manager, Mal Harrison, said the utility has dozens of specialist underground crews who are specially trained to work at high voltages beneath street level, which also gives them a rare view of Melbourne’s CBD.
“We’ve found some amazing things on the job, from old tram pulleys, to forgotten railways, old horseshoes – it’s incredible,” Mr Harrison said.
“There are parts of Melbourne’s underground that nobody knows exist, and we get to work in them every day, so it’s not a bad office.”
> Still the market leaders in laser guided microtunnelling > Bore diameters from 325mm up to 2800mm
> Specialists in ‘free bore’, sleeve boring and pipe jacking in all sizes
> Used for gravity sewers, water mains, storm water, gas and electrical conduits.
Urban Utilities has undertaken a $400,000 project in partnership with industry to develop a valve locking device designed to improve safety and water network security.
The project involved designing a fit-for-purpose lock-out device which allows valves in the water network to be securely
Urban Utilities spokesperson, Michelle Cull, said that the innovation would help protect workers and members of the public during network maintenance activities.
“The water network is pressurised to ensure a safe and reliable service for customers, but this means there can be hazards if water is released when or where it shouldn’t be,” Ms Cull said.
“This device means operators can’t inadvertently open or close a valve, improving safety for our workers and the wider community.
“It also prevents the potential tampering of valves which could lead to unnecessary water supply interruptions.”
While there are similar devices already on the market, Urban Utilities identified a gap, working with Mass Products to custom design a lock specifically for round valve boxes.
These types of valves are commonly found throughout the water network in the Brisbane CBD. They will be used on all compatible valves during network isolations, and a mandatory condition of network access permits issued to delivery partners.
The partnership will see AGL roll out Kaluza’s digital technology platform over the next three years, designed to provide a flexible technology solution that digitises and simplifies energy billing.
The platform is designed to transform its customer operations as part of its Retail Transformation Program.
The program is expected to focus on enhancing the customer and agent experience by significantly reducing operating costs and improving speed to market, and is a key step to accelerating AGL’s ambition to connect customers to a sustainable future through electrification.
The Kaluza software platform is a scalable solution designed to reduce cost to serve and enable faster product innovation.
The Kaluza platform is used by OVO Energy in the UK to service more than six million customers.
AGL said it will deploy the software into its customer base over the next three years, transferring 4 million consumer electricity and gas customer services onto the platform.
The Retail Transformation Program aims to deliver a reduction in operating costs and capital expenditure, with net benefits expected to commence in FY28 and expected pre-tax cash savings of
approximately $70–90 million annually from FY29.
The estimated implementation costs for the residential and small business customer solution component of the Retail Transformation Program will be approximately $300 million over four financial years, beginning in FY24. This includes costs associated with the program and change management, customer migration, systems integration and change within supporting platforms.
In addition, AGL will transform its operating model to deliver effortless experiences for customers, supported by nimble, flexible and empowered teams underpinned by the platform.
The Public Transport Authority WA is calling for tenders for an experienced gas infrastructure expert with a relevant technical tertiary qualification. The Consultant must possess significant understanding of the Western Australian and Australian gas regulatory regimes, business models, commercial drivers and risks associated with operating gas utility companies along with audit and assurance capabilities relating to gas infrastructure designs.
The Consultant will also serve as a subject matter expert, offering technical guidance to various project delivery teams which includes analysing technical designs of pipeline and gas infrastructure, addressing engineering requirement and managing stakeholder engagements.
This is an exciting opportunity to contribute to the future of transport in Western Australia with the potential to extension.
For further information, log into www.tenders.wa.gov.au | Ref PTA240067 - Provision of Expert Technical Advice for Gas Pipeline Specifications.
Unitywater has announced that it has signed contracts for the delivery of $1.8 billion of capital investment over the next five years to provide reliable water services to one of the fastest growing regions in South East Queensland.
Contracts were signed with Downer for programs of work across Unitywater’s portfolio of wastewater treatment plants and its southern distribution networks, along with Dormway for work on the northern distribution networks. Elevate – a joint venture of Aurecon and AECOM – was appointed as professional services partner to provide front end engineering and design services.
if performance standards are met and maintained.
Unitywater CEO, Anna Jackson, said that the collaborative partnerships will streamline the capital delivery process to deliver better cost, time and quality outcomes.
“Our delivery partners are being integrated with our own teams through a trusted partnership model, where we more openly exchange knowledge and move projects through into delivery faster,” Ms Jackson said.
“Each of our new partners was chosen for their expertise and experience and collectively bring time spent working locally on Unitywater’s assets as well as some of the biggest and most challenging water infrastructure projects both onshore and internationally.”
Among the first programs of work to be delivered by Unitywater’s new partners are upgrades at Coolum and Noosa wastewater treatment plants, new wastewater pipe networks around Narangba, upgrades to a series of wastewater pump stations in the northern catchment, and construction of a new water storage reservoir in Pine Valley.
The new capital delivery partnerships were selected through a multistage procurement process that began in December 2022 with organisations assessed against cultural alignment, their ability to deliver the works safely, efficiently and cost-effectively and make a positive contribution to Unitywater’s environmental and community engagement goals.
Link-Seals offer hundreds of solutions to seal pipe penetrations ranging in size from 10mm to 3.6 metres diameter.
Link-Seals are suitable for most types of pipes including PVC, HDPE, Copper and Steel.
Resistant to water, oil, gas, aggressive chemicals and fire.
Projex Group helps calculate the right Link-Seal size and model for your application.
Link-Seal
As the NEM undergoes the biggest transition in history, electricity distribution networks need to ensure that plans for their networks align with the longterm needs of consumers. To achieve this, AusNet undertook a groundbreaking study to quantify value customers place on a range of benefits.
Twenty years ago, it may have been hard to believe that we could power our cars using a standard power-point in our home garage, or use smart technology to automatically warm our homes before we arrive home on a cold winter evening.
People are engaging with the energy system in new ways, such as electric vehicles, solar and smart technologies. The journey toward net-zero emissions and electrification also means many in our community are facing a greater reliance on electricity, while at the same time we are experiencing the impact of climate change through severe weather events and cost-of-living challenges.
PLANNING A NETWORK THAT MEETS FUTURE CUSTOMER NEEDS, IN A TIME OF TRANSITION
Amid these and other challenges, electricity distribution networks need to ensure that plans for their networks align to customers’ preferences, needs and long-term interests.
Every five years, distribution networks in the National Energy Market (NEM) engage extensively with their customers to formulate plans that determine the service levels customers will receive and the prices they will be charged.
In addition, network investments across the NEM are subject to rigorous economic tests, to numerically check that the customer benefits of the investments are higher than their costs. The customer benefits have traditionally focused on reducing short outages. This worked well in a stable operating environment, where the focus is on maintaining the status quo. In these circumstances, traditional economic tests are very useful for keeping costs
However, we are in the midst of a once-in-a-generation energy transition and customers are interacting with the network in new ways. The benefits delivered by network investment are much broader than in the past and can be qualitative, intangible and hard to quantify.
To bridge this gap, AusNet saw an opportunity to extend existing research about what electricity distribution customers value – to help better connect network investment plans with customers’ needs and preferences amid a key time in the energy transition.
CUSTOMERS PLACED A HIGHER VALUE ON RESILIENCE TO LONG OUTAGES THAN ANY OTHER BENEFIT.
“People power is at the heart of the transformation of our energy system that is underway, from one that is carbon-based to one that is net zero by 2050, based on renewables and storage. Yet it is the area that is the least researched – the area where we have the least knowledge.”
Excerpt from keynote presentation at Energy Research Conference by Lynne Gallagher, former CEO of Energy Consumers Australia.
AusNet undertook a study to quantify the value customers place on a range of benefits. These benefits include how much value customers place on reliability, enabling electric vehicle charging, ensuring rooftop solar is not ‘wasted’ and for the electricity distribution network to better cope with increasingly frequent extreme weather events.
Importantly, AusNet considered not only how much customers value certain benefits, but what service changes they’d also be willing to accept. For example, whether customers would accept a lower level of service for cost savings and adjustments for overall affordability.
This enabled AusNet to consider the value customers place on individual benefits, and their overall willingness to accept changes to their electricity bills. In turn, these insights help AusNet better understand which investments in services customers find most valuable.
This groundbreaking study is believed to be the largest of its type in the NEM and is the first time AusNet customers’ values have been quantified at scale. The study included more than 3,500 residential and small business customers on AusNet’s distribution network in the north and east of Victoria.
The study was initiated in early 2023 and began with extensive engagement with customer advocates on the design, and a program of qualitative research before collecting quantitative data between November 2023 and January 2024.
The participation of customer advocates in the study’s design was a major part of the process. A sub-set of AusNet’s Electricity Distribution Price Review (EDPR) 2026–31 customer panel members formed a working group and together collaborated on all key aspects of the study, including the scope, selection of research partners, values to be quantified (e.g. reliability, resilience, exporting solar and EV charging flexibility), wording, and recruitment strategies.
The work was scrutinised by an independent reviewer.
Striking agreement on the design was not straightforward and passionate customer advocates on the working group brought different perspectives to this debate. Given the importance of this study to customer outcomes, it needed to be robust and subject to appropriate scrutiny. This process helped ensure customers, government, regulators and AusNet could trust the study and its insights.
“The process wasn’t always straightforward, but we all understood that the insights from this study could have considerable implications in terms of ensuring our plans aligned to customers preferences. We knew we had to spend time ensuring everyone was comfortable with the design.”
Lucy Holder, Customer Engagement Manager, AusNet
The design that was ultimately adopted comprised of:
• A qualitative phase involving 12 in-depth interviews
A total of five customer workshops with approximately 120 customers
• A quantitative phase that involved an online survey of 3,178 residential and 349 business customers. Cognitive interviews were also used to pre-test the questionnaire to ensure that customers understood the questions.
The study also combined the research data with actual network data on customer usage and outage probabilities to calculate an overall network value of customer reliability, suitable for use in network planning decisions.
The results validated findings from other sources of research and customer engagement: that customers are concerned about cost-of-living pressures or place the highest value on resilience are two examples of this.
However, beyond the validation of existing themes lie rich, quantified, and at times surprising insights into what customers value and would be prepared to pay for, or forgo. Among these, the study verified that:
Resilience is valued above all
• Both households and small businesses placed a higher value on resilience to long outages than any other tested benefit.
Electricity needs to be affordable, but customers want value
• Customers are concerned about affordability but still see the value of investment in the network.
R esidential customers were about half as willing to pay for a total bundle of values (e.g. flexibility in EV charging, plus enabling more solar exports and improving reliability for those with poorest supply) than paying for each value individually. This suggests that while customers are concerned about overall affordability, they still see value in investment.
Customers are thinking of others (as well as themselves)
C ustomer segments are willing to fund investments that benefit others even if they themselves will not directly benefit. Qualitative research suggests that this is coming from a strong desire for equity (supply improvements for customers with the poorest reliability) and an aversion to waste (solar), and the “beneficiary” not always being clear (in the case of solar exports, a household sharing their excess and a household receiving cleaner electricity may both be beneficiaries of an investment).
THE STUDY REVEALED THAT BOTH HOUSEHOLD AND BUSINESS CUSTOMERS ATTACH A POSITIVE VALUE TO HAVING FLEXIBILITY IN THEIR EV CHARGING.
Households and businesses customers would pay more to improve reliability for those with poorest supply.
Customers want to minimise solar wastage
Customers place a high value on ensuring that both their own and others’ solar exports are not “wasted”.
Household and businesses customers also both attach a positive value to investing to enable more solar exports – they would pay more to enable the more solar to be exported.
An expectation that EV charging is flexible and convenient Convenience is highly valued, including flexibility around when they choose to charge EVs.
• Both household and business customers attach a positive value to having flexibility in their EV charging. In other words, they indicated they would pay more to have more flexibility in when they can charge their EV.
Insights such as these will play a key role in AusNet’s decision-making about future investments in its electricity distribution network. These planned investments will be outlined in the EDPR 2026–31 proposal it submits to the AER for assessment, the draft of which will be published in late September. Research outputs will inform decisions on topics such as network resilience and reliability, improving reliability for those with poorest service, EV charging, and solar exports.
As collaboration was key to the study’s development, so too will it inform the application of the study’s findings. AusNet’s Coordination Group is now discussing how best to apply the insights to AusNet’s EDPR 2026–31 proposal. Others in the industry are also looking closely at this study and its insights – more than 100 industry stakeholders attended a recent webinar on the study as part of a research seminar series.
BEYOND NUMBERS: INNOVATION AND ENGAGEMENT KEY TO MEASURING WHAT CUSTOMERS VALUE
A study of the scale and complexity of Quantifying Customer Vaues is not a small or straightforward undertaking. Utility businesses that do so, however will be rewarded with richer insights into their customers, and plans that can be more closely aligned with customer needs and preferences.
CUSTOMER ADVOCATES DISCUSS THE RESULTS AND THEIR APPLICATION TO AUSNET’S ELECTRICITY DISTRIBUTION PRICE REVIEW 2026–31 PROPOSAL. IMAGE: AUSNET
“Networks have an opportunity to investigate and apply new approaches to ensure rigorous, up-to-date customer insights inform planning, decisions and, ultimately, the services customers receive.”
Among the many learnings, there are four that AusNet call out:
1. Allow plenty of time to engage on research design. Investing in this earlier stage of the process will build confidence and trust in the results.
2. Electrification is highlighting equity issues between customers who have very reliable electricity, and those who don’t. Customers with a reliable service are aware of this.
3. Customers do have affordability concerns – however given their evolving needs and expectations of the network, they see investing in the network as value-for-money.
4. Both qualitative and quantitative research have valuable roles to play. In this case quantitative research results closely match with findings from the earlier qualitative stage and AusNet’s other customer engagement, building an understanding of customers’ thinking that sits behind the numbers revealed in the QCV study. Customers are changing their interactions with energy – be it plugging in their EVs to charge from the comfort of their (remotely-heated) home or setting smart appliances to make the most of solar energy. Networks have an opportunity to investigate and apply new approaches to ensure rigorous, up-todate customer insights inform planning, decisions and, ultimately, the services customers receive.
AusNet Tomorrow Customer Insights series
AT A GLANCE: SHIFTING
THE DIAL TO ENSURE OUR PROPOSAL BETTER MEETS CUSTOMER NEEDS AND PREFERENCES
The QCV study: attaches hard numbers to things customers value that otherwise would be hard to quantify, building more holistic, customercentric business plans;
• provides robust customer data stakeholders can trust; shows customers’ priorities across investment drivers;
• captures value-of-service improvements and degradations to support cost-benefit assessments and trade-off discussions;
• complements qualitative engagement.
The results:
• apply to residential and small business customers on AusNet’s electricity distribution network;
• connect to and validate relevant insights from other customer research, for example know that customers hate it when solar energy is ‘wasted’;
• offer relevant insights to stakeholders who are involved in the price reset process e.g. regulators, customer advocates, industry groups, government agencies and other distribution businesses.
Over the coming months, AusNet will share more insights from its industry-leading customer research and engagement initiatives through the AusNet Tomorrow Customer Insights Series. Those interested can register to receive updates about future events via the QR code below. Recordings of past webinars and copies of the slides are also available. Scan the QR code for more information about AusNet’s broader program of customer research and engagement, available via Community Hub, AusNet’s online engagement platform.
Gender equity is widely recognised as a meaningful way to foster better outcomes for workers, customers, and the community. While targets and quotas play an important role in keeping diversity on the agenda, many organisations are left wondering what they can do to attract and retain more women.
Leading pipeline infrastructure company, Interflow, may have a solution. By shifting the conversation from “who is most qualified for the job?” to “who is best for the team, and who will add to the culture and bring new ideas?” Interflow has been able to welcome a diversity of perspectives into the business.
Chris Godsil, Operations Manager at Interflow, said that the company previously had success bringing people from the field into traditional engineering and project management roles.
“We took that idea and cast the net wider, outside of the engineering industry,” Mr Godsil said.
“We were looking for people from any industry with strong value and behaviour alignment with Interflow, people who could communicate and build trust.
“Technical skills can be developed through training and on-the-job experience. What’s really important to us is that behaviour alignment and transferable skills.”
These skills and behaviours were evident in Sam Woods, who made the
move from retail to become a project coordinator at Interflow.
“I have key skills like communication, stakeholder engagement and managing timelines and budgets,” Ms Woods said.
“These have really helped me in my new role.”
Interflow’s shift in focus from technical to transferable skills has been proven to encourage more women through the door. Just as important is providing clear career pathways that enable women to stay and thrive once they get there.
“One of the factors that made me interested in the role was that I could see the progression here,” Ms Woods explained.
“That came from conversations I’d had and from looking at who was already at Interflow and where they had come from.
“It made the risk of changing industries so much easier, knowing there was so much room to grow.”
Interflow’s simple change of approach has solved two problems; it has opened
the talent pool in a competitive market, and it created a pathway for women to enter the water industry.
Mr Godsil explained that the benefits extend even further in practice.
“Exposure to different leadership styles gained from other industries will unlock potential in our teams and enable them to be their best,” Mr Godsil said.
“At a time when our industry faces complex issues like water affordability, water security, climate change, the more diverse our thinking, the better position we’re in to tackle them.”
Also apparent is the impact that value and behaviour-led recruiting has had on the culture at Interflow.
“We have seen a real uplift in culture and retention,” Mr Godsil said.
“You walk around the office and there’s this really nice buzz because people feel they are working towards something they truly believe in. That’s pretty special.”
We’re Creating the Future of Water for people and communities, for generations to come
VERMEER IS CONSTANTLY EVOLVING AND UPDATING ITS RANGE TO ENSURE THAT IT ALWAYS MEETS CHANGING HDD REQUIREMENTS.
In addition to reliability and experience, adaptability is a key characteristic that can help companies stand out from the crowd. Companies that embrace innovation not only prove that they can keep up with the times but can also ensure they don’t get left in the
Technological innovations have seen the construction industry in particular progress in leaps and bounds. A significant breakthrough in the construction industry was the introduction of trenchless technology – a game changer in major pipeline and underground utility installation.
Having always prided itself on being ahead of the game, Vermeer saw the potential of game changing trenchless technology and rose to the occasion.
In the 1970s, Gary Vermeer had a vision: if Vermeer could develop a machine that could dig in a similar manner to a mole tunnelling underneath the surface – without opening a trench – it would blow open the market and make Vermeer an industry pioneer.
Over the following decades this vision became a reality, and the industry realised the impact this would have in underground construction.
Trenchless machines started appearing on the Australian market in the 1990s, with demand for this technology swiftly rising. From Vermeer’s perspective, it was the perfect time to start designing its own trenchless machinery, putting its own unique spin on the cutting edge technology.
The first horizontal directional drilling (HDD) machine that Vermeer brought to the market was the Navigator® 9 (later known as the D7 model) in 1991. The Navigator® was a more basic model than the HDD machinery on offer today and required a large amount of labour to set up and commence drilling. Also, at this point in time, everything on the machines involved a manual process.
A characteristic of Vermeer that sets it apart from its competitors is its commitment to listening to and working with its customers. The team spent a lot of time staging demonstrations of its HDD machinery for customers, gathering their feedback and introducing them to the technology.
In 1995 the second generation of self-contained HDD drills were introduced to the Australian market – a defining moment for Vermeer, which allowed it to put its mark on this up-and-coming industry. Additionally, the rollout of Foxtel and cable television meant an uptick in trenchless technology and Vermeer’s HDDs were often the machine of choice.
THE FIRST HDD MACHINE THAT VERMEER BROUGHT TO THE MARKET WAS THE NAVIGATOR® 9.
The late 1990s and early 2000s saw the introduction of Vermeer’s more compact HDDs, like the D7x11 and D16x20, which offered more variety and versatility for those working with a fleet of HDDs, particularly on larger projects.
As HDD needs have shifted, Vermeer has evolved and updated its range to ensure that it always offers the best technology to customers.
Vermeer’s S3 range was introduced in 2015 and made rock drilling a lot simpler for operators, from the smaller D10x15 S3 HDD, weighing just over 3,000kg, to the 17,000kg D60x90 S3 HDD, and more recently, the new D100x140 S3 weighing in at more than 22,000kg.
As HDD requirements change, Vermeer is there every step of the way, constantly updating its range and continuing to prove itself as a high-quality solution for trenchless needs – from telecommunications and electricity to gas, water and energy pipelines.
The Essential Services Commission has formed a partnership with key experts to develop better practice guides for energy and water utilities to support consumers who are experiencing family violence. Utility spoke with social entrepreneur and Adjunct Associate Professor, University of New South Wales School of Social Sciences, Catherine Fitzpatrick, about her role in this partnership and how utilities can help put a stop to domestic violence.
The Essential Services Commission’s (ESC) Safety by Design partnership brings together a team of independent experts in family violence and economic abuse – Thriving Communities Partnership, Flequity Ventures (Catherine Fitzpatrick), Safe and Equal, and the Centre for Women’s Economic Safety – to investigate potential risks in the systems of energy and water businesses and prevent these products and services from being weaponised against consumers experiencing family violence.
Ms Fitzpatrick has already authored two ‘Designed to Disrupt’ reports for the Centre for Women’s Economic Safety that identified key risks for product misuse in the banking and general insurance sectors. As part of this partnership, she will be creating two new reports for the energy and water sectors.
Family violence and economic abuse often go hand in hand, with one in four Australian women impacted by domestic abuse, and one in six suffering from economic abuse.
Financial abuse is a subset of economic abuse where the perpetrator controls the victim by denying or restricting their access to money. This kind of abuse can have devastating effects on the victim, ultimately making it more difficult for them to escape an abusive situation.
Ms Fitzpatrick explained that financial abuse is often a hidden problem, and many victims/survivors don’t even realise that they are experiencing it.
“Financial abuse is a form of control, exploitation or sabotage that means that the victim survivor has no financial security, which limits their potential for any self-sufficiency.
“What that could look like is racking up of debts in somebody else's name.
In water or energy, if there's an ability to open an account online and not necessarily check that the person who's paying that bill is the person who's actually incurring the cost, then that could be weaponised in the context of domestic and family violence.
“Financial abuse is not just a form of coercive control; it also is one reason why women might need to choose between violence or poverty,” Ms Fitzpatrick said
Financial abuse can also start or worsen with separation and the effects are long lasting for the victims, including:
• Making it harder for victims to leave or seek help
Victims can be left with long-term debt
• Victims’ ability to gain employment can be restricted, as they are unable to access a vehicle or other essentials
• Victims’ credit scores can be impacted
It affects physical and mental wellbeing, housing security, access to insurance and access to utilities and other essential needs
Perpetrators of financial abuse often restrict or weaponise these essential needs and services against victims, and the Safety by Design partnership is striving to put a stop to this misuse.
Ms Fitzpatrick said that the partnership is looking to uncover these tactics and investigate the ways in which perpetrators are weaponising water and energy services.
“What we do know, from what victims/survivors and people who work in financial counselling and the women's safety sector tell us, is that any services that have a joint account or can be accessed online, are ripe for financial abuse.
“What I might imagine that we would uncover is – similar to banking and insurance – a perpetrator might refuse to pay the bill and then leave that for the
victim/survivor to try to pay on their own. So, they are incurring a debt that they can't really afford, and [perpetrators would] do that constantly as a form of coercive control.
“There has also been research that shows that 60 per cent of women who fled abuse reported one or more of the following: they couldn't pay electricity, gas or telephone bills on time; they couldn't heat or cool their home; they couldn't pay their mortgage on time; and they have pawned something to get cash or gone without meals. That's a huge proportion of women who experienced domestic and family violence who can't pay their bills,” Ms Fitzpatrick said.
The partnership will also investigate some of the key signs that a customer is experiencing this type of abuse and how processes can be improved to better identify and support these women.
Ms Fitzpatrick’s first piece of advice is to believe someone if they tell you they're experiencing domestic violence.
“You need to understand that they're only going to tell you about this because they want you to factor in their need for flexibility and safety, as they are seeking help.
“Someone also might not say the words ‘domestic and family violence’, but they may talk about having trouble paying their bills. They may say, ‘I didn't know that there was that account in my name’ or ‘can you give me details of my account?’ Because all of those things might be being withheld.
“If you think about the courage it takes to disclose something that’s making them extremely unsafe and that is deeply personal, then that's why it's really important that organisations believe them and put into place appropriate responses,” Ms Fitzpatrick said.
To tackle this issue, the Safety by Design partnership will conduct research with victims/survivors and support workers in the women's safety sector to gain an in-depth understanding of victims’ experience with energy and water utilities and uncover any loopholes in their services that can be weaponised. It will then look at how these products can be updated to disrupt that abuse.
“I just think it's a great partnership because it brings together the regulator, the community sector and my experiences in business,” Ms Fitzpatrick said.
“What will come out of the partnership is that I will be writing two more Designed to Disrupt papers. I've written two of these industry blueprints so far: one is for banking, and one is for insurance. The next two will be on water and one on energy.
“These papers will make a series of observations about the ways that products and services are being weaponised and also make recommendations – based on that lived experience and based on consultations with the industry regulators and ombudsman – on how energy and water companies can address them, and how the industry might respond collectively. It will also potentially include recommendations for how regulators could think about things differently.
“The blueprint of Designed to Disrupt is aiming to give a really practical guide to business on what they can do in response. Some of it will be complex, but some of it will be easy.
“The aim of my paper is to provide that blueprint and then the rest of the project, beyond the papers, will then help to develop toolkits and resources that should make it easier for businesses to prevent the weaponisation of their products and services and to provide greater protection to victims survivors.”
Ms Fitzpatrick said that the results from her previous work in the banking and insurance sectors could potentially inform not just the steps that utilities can take, but how Australia’s essential services as a whole could better support survivors and victims of domestic abuse.
“I think there's a real opportunity to look across sectors and say, ‘what are the common issues?’ Our systems and processes and products and services can be enabling abuse, because they don't necessarily have a design that protects against abuse.
“When people start thinking about how they can support customers, they obviously start with, how do they better support victims/survivors. What my papers aim to do is say, ‘well, while you're doing that, can you also take a look at if you are inadvertently enabling abuse and close some of those loopholes’,”
“What we've seen in banking is that people were sending one cent payments to others with threats and abuse and intimidation in the payment description. After speaking to the eSafety Commissioner, banks have now put blocks in to stop bad or inappropriate language in real time.”
Ms Fitzpatrick said that artificial intelligence is also used to run over the
transactions and detect patterns. From there, several banks will write to people who send the inappropriate messages to inform them that the messages have been seen and that there could be repercussions, including account closures or suspension.
“What we found is that 90 per cent of customers who receive those letters, stop sending abuse through bank accounts.”
Ms Fitzpatrick says that she hopes her paper will help energy and water utilities gain a better understanding of the ways in which their products and services are being misused and weaponised in the context of domestic and family violence.
“I'd like the project to be able to shine a light on where the opportunities are for businesses, for the industry more broadly and for regulators to take further steps to both provide greater protection for victims/survivors.
Ms Fitzpatrick said she also hopes her papers send a strong signal that everyone has a role to play in preventing domestic and financial abuse, and that everyone should take it seriously.
“We want to change this terrible crisis in Australia and make it safer for women. It's quite extraordinary when a business takes action to say, this is what acceptable customer behaviour is and this is what is not tolerated. It can change human behaviour. I believe that putting financial abuse in the spotlight, talking about the weaponisation of products and sending that very strong signal from business, is likely to drive a cultural change.”
By David Brown, Associate Vice President, APAC, Geotab
Fleet sustainability is one of the most impactful ways for companies to reduce their carbon emissions, and accurate data insights are key to supporting this transition, increasing fleet efficiency and reducing costs.
DAVID BROWN, ASSOCIATE VICE PRESIDENT, APAC, GEOTAB. IMAGE: GEOTAB
The automotive sector is a major contributor to global greenhouse gas emissions. In Australia, the transport sector is the third largest source of the country’s greenhouse gas emissions, contributing to 21 per cent of national emissions in 2023. Since 2005, these emissions have risen by 19 per cent and are projected to become the largest by 2030.
The Federal Government aims to reduce greenhouse gas emissions to 43 per cent below 2005 levels by 2030 and achieve net zero emissions by 2050. Companies have
a unique opportunity to measure their impact and take responsibility. Innovation and sustainability are crucial to improving operations and reducing emissions in the transport industry.
A successful sustainability initiative incorporates three elements: technology and innovation; laws, public policy, and governance; and economic and financial incentives. Companies want to become more sustainable, but how do you start?
Leveraging connected vehicle technology not only supports new road safety and sustainability legislation, but also reduces emissions with data-driven insights. Data insights from telematics solutions can help with the fleet sustainability strategy and mitigate costs while increasing efficiency.
Companies can use data insights to optimise routing for a wide variety of delivery and service vehicles, prepare fuel management reporting to reduce idling and improve fuel efficiency for all vehicle types, and efficiently use and determine the right size vehicles, ensuring the right vehicle for the job.
While it is important to consider the sustainable fleet strategy, reducing vehicle emissions is equally crucial. The urgent need for climate action has
put the onus on governments globally to integrate policies and regulations to enable a market shift to zero-emission transportation.
Recently, there has been a large push to transition fleets to electric vehicles (EV). With the growing number of EVs in the market, there has never been a better time to begin the fleet electrification process.
Before you can start adding EVs, it is important to understand the vehicle's daily route, operating cost, and vehicle dwell time.
Using telematics will provide access to the fleet's driving data points and help determine where it makes sense to electrify. It provides vehicle recommendations based on available models in your region, as well as projected cost savings and avoided CO2 emissions.
The time to act is now. By integrating advanced analytics with telematics, companies can develop sustainable transportation solutions and enhance fleet management.
Collectively, this will help the industry demonstrate the profound impact that innovative technology can have on the transportation system today and create safer systems worldwide.
For more information, visit www.geotab.com/au
From humble beginnings in Germany, VEGA is now a world-leading innovator in pressure sensor technology. John Leadbetter, Managing Director at VEGA Australia, shares how the company has served diverse industries across the globe with its reliable solutions and commitment to customer service.
VEGA, a family-owned company, was established in 1959 in Germany’s Black Forest, with an initial focus on the development and production of electrical switches for level control in industrial applications.
Primarily servicing the German market, VEGA spent its first decade consolidating its position as a reliable supplier of level measurement instruments.
In the 1980s, VEGA established subsidiaries and sales offices in various countries across Europe, Asia, and the Americas.
The company eventually expanded to Australia in 1987, initially based in Brook Vale, then relocating to Kirrawee in 2000, and finally to Caringbah in 2019.
VEGA offers a comprehensive range of pressure instrumentation including gauge pressure transmitters, differential pressure sensors (both conventional and electronic), and hydrostatic pressure sensors.
“We also offer factory automation pressure or what they call a simplistic pressure, and that will be tied in with other communication devices within the units themselves used a lot in the factory automation,” John Leadbetter, Managing Director at VEGA Australia, said.
“Whether it’s measuring the pressure of a pipe, or the level of a slurry in the hopper, or the depth of a ball with the ball fields, we have a device that would suit pretty much all types of applications.”
VEGA provides fittings and approvals for industries like water, food, pharmaceuticals, offshore, and chemical, ensuring compliance and suitability for diverse monitoring systems across 14 main industries.
“Our pressure instrumentation comes equipped with the necessary certifications and approvals for use in Australia, including food-grade and ship approvals,” Mr Leadbetter said.
Mr Leadbetter explained that VEGA is committed to improving and innovating its offerings.
“Seven years ago, we introduced Bluetooth communication across our range, and now we’re focusing on IoT integration,” he said.
“We’re constantly developing our instrumentation, incorporating new features, and staying abreast of industry trends. Whether it’s wireless communication, Ethernet, or other protocols, we’re committed to keeping pace with market demands.”
One of its latest products, the VEGAPULS 42, offers precise non-contact level measurement for simple to moderate applications.
It’s an optimal sensor for non-contact level measurement in straightforward to moderate scenarios, accurately gauging liquids, and bulk solids.
Its optional universal connection for hygienic adapters minimises installation complexity and inventory management, meeting the stringent standards of hygienic processes.
Simultaneously, the VEGAPULS 42’s IO-Link capability ensures seamless, uninterrupted digital data transmission.
VEGA differentiates itself in the market by prioritising reliability, customer service, and adaptability to individual client needs.
“When you’re talking about competition, it’s not just the price of the instrument, there’s also the availability, compatibility with it with the requirement of approvals, there’s a support and service, there’s training,” Mr Leadbetter said.
With 38 years of presence in Australia, VEGA offers repair facilities, local stock, and knowledgeable technicians to support customers effectively.
The team at VEGA Australia prides themselves on two key pillars: being German-made, synonymous with high quality, and prioritising exceptional customer service.
Mr Leadbetter explained that VEGA operates with honesty as its guiding principle, ensuring transparent communication with clients.
“We prioritise honesty above all else in how we operate,” he said.
“If we can’t deliver on something, we’re upfront about it. If an order will take eight weeks, that’s what we communicate; we don’t promise miracles.
“It’s essential to be completely transparent with clients, even if it means potentially losing an order due to delivery issues. In the end, our clients appreciate dealing with an honest company.”
VEGA’s success stems from understanding and meeting the unique needs of various industries, such as water, oil, gas, mining, food, and chemical.
“Ensuring a long-term relationship with clients comes down to understanding what they’re looking for providing a good service, a good product,” Mr Leadbetter said.
“We believe in selling solutions, not just instruments, by actively engaging with customers to understand their needs and provide the best options available,” Mr Leadbetter said.
“Our commitment to personalised service is reflected in our willingness to travel extensive distances to meet with clients face-to-face, demonstrating our dedication to reliability and support.”
Innovation extends far beyond the realm of new technology; people, cultures, processes, strategies – and even the way in which we drive innovation itself –are all areas that can benefit from new ideas. To foster continuous improvement, South East Water has adopted a human-centred design approach to innovation.
South East Water’s Corporate Strategy 2028 outlines a clear vision for the utility: to innovate with purpose, and act with care.
The deployment of its groundbreaking digital metering program, adoption of circular economy principals and the development of its Environmental Sensitivity Map initiative are already placing South East Water at the forefront of innovation; with the utility ranking sixth on the Australian Financial Review’s (AFR) Most Innovative Companies list in 2023.
However, there’s more to innovation than technology and products; it starts by empowering people to be creative and fostering a culture of collaboration and curiosity.
To encourage this mindset, South East Water is piloting a new enterprise process that takes a collaborative approach to innovation with human-centred design (HCD) principles.
In 2024, utilities are exploring the potential of rapid advancements in AI, IoT enabled devices, and network automation. Reaching the full potential of this digital transformation starts with building a culture of innovation that encourages experimentation, embraces change and drives business-wide collaboration and communication.
As workplace flexibility becomes more and more important to employees, office spaces are becoming spaces for purposeful and deliberate collaboration. For South East Water, WatersEdge HQ is transitioning into a co-working space where employees can connect and share ideas.
By nurturing an environment of creativity, South East Water strives to not only tap in to the valuable knowledge and diverse experiences of its employees, but empower collaboration between different areas of the business.
“In order to innovate, you really have to be in the right environment. That includes both your mindset, and your physical environment, and we tried to drive that [with this process],” Ms Vincent said.
In the lead up to South East Water’s inclusion in the AFR Most Innovative Companies list 2023, the utility undertook an external assessment, which identified enterprise process as a key area for improvement.
The utility then looked at how it could create an enterprise process that drives innovation.
South East Water Innovation Manager, Olivia Vincent, explained that the utility chose to leverage HCD methodology as a starting point for this process.
“We built out this enterprise process called the Innovation Pathway, which has a number of key milestone moments that match to how you take innovation from an idea through to market, and embed it in the business,” Ms Vincent said.
HCD methodology is informed by the ‘Double Diamond framework’, which centres around divergent (where multiple options are suggested) and convergent (where decisions are made) thinking. The Innovation Pathway encompasses the five key stages of this framework: align, discover, define, develop and deliver.
Collaboration was key to actioning this pathway, and the utility sought to facilitate this approach by hosting an Innovation Summit, which brought people from all aspects of the organisation together to define key challenges and brainstorm solutions.
Before the summit could take place, the first milestone in the pathway was to create alignment at an executive level.
“Driving deliberate alignment, both at the executive level and then the next level down, the senior leadership level, before we started to innovate or come up with the ideas was really important,” Ms Vincent said.
“So, [the next step was figuring out] how do we actually align around an innovation challenge?”
To achieve this, the Executive Team was tasked with deciding on a theme for the inaugural Innovation Summit.
THE NEXT STEP FOR SOUTH EAST WATER IS TO TAKE EVERYTHING THAT IT HAD LEARNED FROM THE INNOVATION SUMMIT AND DEVELOP IT FURTHER INTO POSSIBLE APPLICATIONS.
“There can be a tendency, particularly when you're dealing with ambiguity and the unknown, to either divest responsibility somewhere or to finger point [and fall into] an ‘us and them’ mentality. So, [the next question was] what's that together piece and how do we drive that?”
The cross-business Innovation Summit held on 5–6 June 2024 made up the next two steps in the pathway.
The two-day event comprised of two milestone activities: a Senior Leadership Team (SLT) Alignment Session, and the Hackathon.
Ms Vincent explained that on the first day, the SLT received the theme from the executives and they got to work on identifying innovation opportunities and translating them into ‘how might we’ statements to define the challenge.
“We started with a half-day futures and foresight capability uplift, which we worked on with Reanna Brown [founder of Work Futures], who's really terrific in this space. What she does is take a futures perspective, but translates it into the practical,” Ms Vincent said.
“That masterclass gave people a different way of looking at our external landscape collectively to identify some of the things from a water industry perspective that might be declining or changing.
“Then, in the second half of the day they broke up into eight tables to condense that external landscape view and then distill it into a ‘how might we’ statement.”
These statements then paved the way for the Cross-business Hackathon on day two, where 60 subject matter experts (SME) collaborated to develop solutions to those challenges.
A winning idea was chosen for two categories:
1. Ready to launch: an idea that could reasonably be piloted within 12 to 18 months; is as applicable for frontline workers as it is for office-based workers; and has identifiable benefits to customers. This idea would be expanded upon and tested later in the year
2. Most disruptive: casting aside all constraints, this idea has the most potential to positively disrupt South East Water for the benefit of itself, its customers community and the environment. This idea would be unpacked into smaller components that can be piloted in the future
This structured innovation process provides South East Water with a clear pathway for identifying problems and
brainstorming solutions and then transforming these ideas into tangible outcomes and actions.
Prior to launching the Innovation Pathway, South East Water established its Wellbeing Framework, which outlines the utility’s commitment to becoming a psychologically safe organisation and Ms Vincent explained that their goal was to see innovation as an expression of that.
“I think, at scale, we can do a lot more around psychological safety, and feeling safe to fail,” Ms Vincent said.
“You've got this natural tension between engineers and scientists and people whose very jobs ride on the fact that they get it right, with very significant implications if they get it wrong. But acknowledging all of that, there are still windows where you can delineate that this is the space where it's safe to fail.
“If we have a psychologically safe environment, and we have empowered people, and we can provide these ring-fenced areas for experimentation where people feel safe to fail, learn and try again, then the outcome of all of that should be that we're an organisation that generates high innovation.”
The next step in the process was to take everything that the utility had learned from the innovation summit and develop it further into possible applications.
“One part of that is that we need to look at the ready to launch idea and activate that into pilot within the business. Similarly, with disruptive idea, there's less of a hard commitment around how this gets taken forward. But we want to explore and unpack that further to see what ideas might be applicable for us in the future,” Ms Vincent said.
The second part is to look at the summit itself and identify the aspects that were a success and how the pilot event could be built upon and improved in 2025.
One aspect the utility is contemplating is how it can get great involvement from frontline employees and how it can get the right evidence – both from customers and employees – to inform the conversation that executives are having.
The utility also looked at feedback from attendees about how they could improve the experience next year.
“Failure is essential to innovation. We need to get better at not just saying, ‘look at what we did well’, but saying, ‘yeah, [that particular element was a miss’,” Ms Vincent said.
“One of the misses was that we didn't get the executives to explain why they chose a theme in their own words. They had a very high level bit of context around the theme, but some more nuance around this theme right now would have been very helpful for that senior leadership team.
“On a personal level as well as an enterprise level, if we're going to say to people that it’s safe to fail, then we need to be leading from the front with that with this programme. So, things like saying ‘we don't quite know yet’ or ‘there are certain things we could have done better’ are important.
“People are the greatest enabler of innovation. While we have a tendency to associate innovation and technology, galvanising the diversity of people's opinions, their perspectives, their smarts, their quirks, and bundling them together in service of your organisation’s vision and strategy, and then saying, ‘how do we innovate?’ – that's the magic.”
DISCREPANCIES BETWEEN HISTORICAL UTILITY PLANS AND INVESTIGATIONS EVIDENCE, VISUALISED IN 3D THROUGH THE POWER OF THE UNIFIED UTILITY MODEL.
A streamlined construction process begins with access to accurate underground data at the design phase of a project, but how can engineers ensure that they are working with precise and up-to-date information? Utility explores how new utility modelling technology is helping engineers navigate the murky world of underground utilities.
Most infrastructure construction projects begin with an engineer or CAD designer compiling maps from asset owners of all the existing utilities in a project scope area. It’s a painstaking and time-consuming exercise and, as many project managers will know, it can also be fruitless; existing utility plans are often incomplete and inaccurate, leading to inevitable design rework and delays on the ground as contractors uncover unknown utilities.
Slot trenches and trial holes can be dug to verify existing plans, but these low-coverage necessary investigations often impact larger areas and cost more than required; causing major disruption to the public and the community through traffic closures, noise, pollution, and carbon emission.
The field of utility locating has emerged over the past few decades to fill the gap in providing accurate data on the location of underground utilities. However, typically this information is
only gathered by contractors prior to starting construction. Vital information about anomalies or undocumented utilities that could help inform design decisions goes unrecorded or remains as paint marks on the ground to be washed away over time.
To improve project outcomes and drive safer, more efficient infrastructure construction, Reveal has developed the concept of a Unified Utility Model – a 3D utility map that combines all sources of data on the underground in a framework that can be accessed and understood by engineers at the concept and design phases of a project.
The Unified Utility Model takes existing utility plans and informs them with the results of geophysical investigations and visual verifications to produce accurate, comprehensive models of the underground that
are compatible with BIM and CAD design environments.
The Unified Utility Model applies internationally supported utility detection and mapping standards such as PAS-128 and AS-5488. Engineers can easily interpret and rely on the intuitive visualisations that accurately describe both the underground detections and the risks associated with them.
The Unified Utility Model depicts the existing utility record, the results of the utility investigation and the updated 3D visualisation of the asset, with a chain of evidence showing how the model has been derived.
Armed with the Unified Utility Model findings, engineers can design with confidence, knowing they are minimising the risks of project delay and cost overrun that affect most infrastructure construction in Australia.
Contact Reveal today to learn more about how your engineering consultancy can deploy Unified Utility Models on your next project.
Sign your site up to Undermaps for threeyears and Reveal will process all your existing utility records and information into Undermaps for free.
An easy-to-understand pricing structure, based on data coverage. No per-user license fees.
Hosting, maintenance, and software support included. Start now at www.reveal.nz/buryyourpdfs a utilities data management platform where users can create a single source of truth to be accessed over the lifetime of a site by all necessary stakeholders.
ONCE COMPLETE, THE FITZROY TO GLADSTONE PIPELINE WILL HAVE CAPACITY TO TRANSPORT 30GL OF WATER PER ANNUM TO GLADSTONE.
Central Queensland has endured some of the most severe dry conditions the state has ever seen over the past decade.
Climate change is delivering extreme and increasingly frequent weather events, from flooding rains to prolonged droughts. The Queensland Government’s 2020 State of the Environment report revealed that 67 per cent of Queensland was drought declared from 2013 to 2020.
Queenslanders are always mindful that no matter how things are right now, they can change quickly, which drove the Queensland Government’s focus on resilient infrastructure that improves both drought and flood resilience.
Water has always been extremely critical for Central Queensland – a region home to some of the nation’s
biggest cattle producers, heavy industry as well emerging renewables industries – all of which rely on a steady, reliable stream of water.
Gladstone is the major regional centre in the Boyne River Basin and is an area of economic significance at both a state and a national level due to its metals processing industries, power generation and port facilities, which all utilise water sourced from the Boyne River, more specifically Awoonga Dam.
For the past 15 years, the Gladstone Area Water Board (GAWB), and the Department of Water Manufacturing and Regional Development has undertaken multiple studies to evaluate options to mitigate the single-source water supply risk.
GAWB’s Strategic Water Plan 2004 (updated in 2013), identified several options to improve water security for Gladstone to meet increased demand, identifying the
Fitzroy to Gladstone Pipeline as the preferred water source augmentation option.
Fast-forward to 2024, the $983 million Fitzroy to Gladstone Pipeline is already halfway to Gladstone, with 50 per cent of the pipeline installed – a major milestone in the construction progress.
The pipeline connecting the Lower Fitzroy River near Rockhampton to Yarwun near Gladstone is expected to drive fresh economic prosperity for future generations to not only live – but thrive.
The Fitzroy to Gladstone Pipeline is an assurance for long-term water security and economic development for the region. The pipeline is owned by GAWB with Principal Contractors, McConnell Dowell BMD Joint Venture (MBJV) driving the construction.
Minister for Water and Member for Gladstone, Glenn Butcher said, once completed, the Fitzroy to Gladstone Pipeline will leave a remarkable legacy for the region.
“There has been meticulous planning and preparation to get to this point in the project and it is thanks to the GAWB and MBJV teams for their commitment to safety and quality that we have now arrived smoothly and on time at the halfway mark,” Mr Butcher said.
“A total of 21 trainees have worked on the project, as part of GAWB’s dedication to upskilling the next generation. That’s more than 23,000 hours spent learning and upskilling locals,” he said.
GAWB is also delivering on its commitment to diversity and inclusion, with more than 86,000 hours worked by 90 women on the project, and more than 25,000 hours worked by First Nations Australians.
GAWB CEO, Daren Barlow said, it is fantastic that 50 per cent of the pipeline is now in the ground.
“In less than a year from the first pipes arriving in Gracemere we have laid more than 63km of pipeline.
“Once complete, the pipeline will have capacity to transport 30GL of water per annum to Gladstone, equivalent to 12,000 Olympic-sized pools,” Mr Barlow said.
“This is an important milestone for GAWB and I look forward to celebrating the completion of the pipeline installation later this year, weather and construction conditions permitting.
The $983 million project includes a 117km pipeline, an intake facility at Laurel Bank on the Fitzroy River, a water treatment plant and pumping station at Alton Downs and Reservoirs at Aldoga.
“Construction work at the Laurel Bank intake, Alton Downs water treatment plant and Aldoga Reservoirs are all progressing well, and we are on track for commissioning and operation of the pipeline in 2026,” Mr Barlow said.
“We are committed to keeping local communities informed about ongoing works and have recently hosted a series of community information sessions in Gracemere, Alton Downs and Yarwun.”
On the Fitzroy River approximately 16km upstream of the Fitzroy Barrage in Rockhampton is the Laurel Bank intake structure.
Once completed, the project will consist of two main structures: a combined single concrete structure on the riverbank to house the intake facility and pump station and a separate control building.
The pump station and combined river intake will be a rectangular reinforced concrete structure, approximately 11m wide by 9.5m high and built into the riverbank (approximately 5m visible above the river level).
The structure will collect up to 100ML of water per day from the Fitzroy River and has been designed to avoid drawing fish and other marine animals into the structure. Particles more than 2mm in size are separated out before the water passes through a finer filter to remove smaller particles. Once filtered, the water will be pumped approximately 3km via the Fitzroy to Gladstone Pipeline to the Alton Downs Water Treatment Plant (WTP).
Processing up to 100ML of water a day, the Alton Downs WTP is a critical component of the Fitzroy to Gladstone Pipeline as it will treat, store and pump water from the Fitzroy River along the pipeline to two new 50ML reservoirs being constructed in Aldoga – approximately 20km from Gladstone. The WTP site is approximately 3km from the Laurel Bank intake structure and will comprise of several buildings and structures including an office, control building, clarifier, dewatering building, chemical dosing area, reservoirs and pump stations.
The pipeline is connected to the Aldoga Reservoirs, which will hold up to 100ML of water.
Located at the southern end of the pipeline corridor, water from the reservoirs will be gravity fed to GAWB’s existing water network – serving as a vital piece of infrastructure for the project. The design of the reservoirs consists of two similar 50ML concrete tanks, each 76m in diameter and 12m high.
The concrete structures will be cast in-situ with posttensioned walls and floor. The reservoirs will have roofs that will be constructed with galvanised steel rafters supporting profiled steel sheeting.
Mr Barlow said the Fitzroy to Gladstone Pipeline will have lasting benefits in the Gladstone and Rockhampton regions not only for the future of water but also through the employment of a diverse local workforce.
“We are proud to be making significant progress in terms of diversity and inclusion, and trainees working on the project. In total there will be 10,000 hours of First Nations People’s workforce participation, creating 25 traineeships with more than 10,000 hours of training and upskilling to the delivery team,” Mr Barlow said.
“Furthermore, we are currently on track to meet our target of 40 per cent of construction costs to be spent locally and more than 400 workers have been engaged so far – that really is an enormously positive impact on our region.”
FMT Group - providers of one of the most complete product lines available to OEM equipment manufacturers, maintenance providers, field service companies, power stations, petrochemical plants and related industries - has been announced as the representative Australian distributor for Specialised Fabrication Equipment (SFE) Group. The partnership is set to drastically increase FMT’s product range with specialised tools and equipment.
SFE Group was founded in 2019 after the merger of three world leading original equipment manufacturers in the field of pipe fabrication equipment, tooling and machinery: B&B Pipe and Industrial Tools LLC, Mathey Dearman Inc and TAG Pipe Equipment Specialists. SFE Group has also acquired the AXXAIR Group, Magnatech LLC and, most recently, Climax Portable Machining & Welding Systems LLC. SFE Group was formed with the vision of merging various fabrication tool businesses and brands together to offer the world’s most comprehensive range of orbital welding, pipe fabrication, precision engineered applications and cutting solutions for a wide variety of industries.
By combining forces with Climax, SFE Group now offers the world’s most
extensive range of highly engineered industrial tools for portable machining, cutting, orbital welding and specialized fabrication. Climax offers one of the most comprehensive product ranges on the market with over 53 years’ experience in the industry. Climax is a global company that delivers a wide variety of portable machining, welding and valve testing and repair tools that are sold and used all over the world.
The new partnership will see a significant increase to FMT Group’s product lines, offering a wide range of new equipment. New products and tools include pipe flaming, pipe jacks, pipe cold cutting machines, orbital cutting, pipe purging, alignment and layout tools, and tube welding machines. As the Australian distributor for SFE Group and an existing supplier of Climax tools and
products, FMT has cemented itself as Australia’s leading supplier for specialist on-site machining equipment and portable maintenance machines.
FMT Group provides a very broad range of products and accessories for the industry it serves. The company has achieved this through unconventional means. FMT has developed relationships with job shops and manufacturers in the US, Europe and other overseas sources to deliver quality products in Australia. This strategy enables FMT to furnish customers with the best products available and the most affordable pricing in the industry. FMT stocks a comprehensive range of pipe cutting and bevelling machines, portable lathes, portable milling machines, flange facers, bore welding machines and line boring machines.
Precision and flexibility are key to a successful trenchless installation; however, meeting these unique demands presents an ongoing challenge. Sensing a need for improvement, OptionX Group developed a groundbreaking centraliser solution that is purpose-built for the industry. Here, OptionX Group CEO, Stuart Harrison, shares the ten-year journey that led to the creation of Riteline centralisers.
guided boring system and AdaptX – and, most recently, Riteline. What inspired you to develop Riteline?
SH: Working with Edge Underground, I saw a need for improved accuracy and efficiency in trenchless projects. Traditional casing spacer and centraliser systems often fell short in these areas, prompting me to create a solution that would set new standards in the industry. How did AXIS and AdaptX influence the creation of Riteline?
SH: The AXIS system addressed significant shortfalls in accuracy and general microtunnelling capabilities. Seeing its positive reception and the impact it had for Edge Underground inspired me to continue innovating. Riteline has been almost ten years in the making, developed alongside AdaptX. While AdaptX is the next evolution of the AXIS, Riteline is a centraliser system that ensures precise pipe alignment and support under various conditions, providing unique benefits to the industry. Taking Riteline to market
the key issues in current installations. We then designed, tested, and refined Riteline at Edge Underground, ensuring it met the highest standards of performance and reliability. This involved extensive field tests and feedback from industry professionals to perfect the design. The product has undergone many iterations to reach its current form, which we believe outperforms anything else on the market.
What makes Riteline stand out in the market?
SH: Riteline centralisers offer several unique benefits. They are designed to be incrementally adjusted, allowing on-site height modifications as needed. We offer a Flex and Rigid Series, with the Flex Series having the unique ability to flex around deformities in the bore, keeping the pipe centred. Additionally, Riteline centralisers are easy to install, saving time and labour costs. Their robust construction ensures durability and reliability, even in challenging
conditions. They are also applied individually to the pipe based on load requirements, ensuring optimal performance for each project and reducing wastage and costs.
How was Riteline received by the industry?
SH: Riteline has been received exceptionally well. It was a finalist in the ASTT New Technology Award for 2023, where AdaptX won the category. We've showcased Riteline at several expos, including in the USA at IFCEE this year, and at No-Dig Down Under in Brisbane, where it garnered significant interest and orders. It was a surprise hit at Drillfest, which primarily focusses on the vertical drilling industry. While Riteline was developed for the horizontal drilling industry, with input from our microtunnelling teams at Edge Underground, its precise adjustability and ease of application have proven valuable in both horizontal and vertical drilling sectors.
How has the WSAA appraisal helped with the launch of Riteline?
SH: WSAA’s rigorous appraisal process was an essential step in finding our place in the market. Riteline underwent extensive testing, confirming its reliability and effectiveness. This endorsement has been vital in gaining traction across Australia and has bolstered our credibility for launching in both the US and UK markets, where we now have distributors.
What’s next for Riteline and other innovations?
SH: The entire OptionX Group aims to continue pushing the boundaries of technology and capabilities across the drilling, tunnelling and boring industry. Expanding Riteline’s reach globally and continuously improving our products are our top priorities.
The PL1500 is a gamechanger for pipeline construction. The unique, quick-hitch, vacuum lifter attaches to your existing excavator, reducing your machine hire cost and getting things moving fast. Capable of safely lifting 15,000kg, the heavy-duty, self-contained unit can handle all types and lengths of pipe. It integrates seamlessly
with the host excavator, using the main controls and hydraulics to operate the vacuum lifter. Plus, built-in smart tech ensures it’ll only pick up or put down a pipe on a solid surface. That’s safer than many other vacuum lifters on the market. To find out more, speak to the Pipeline Plant Hire team today.
Communities all over Australia depend on water utilities to provide an essential service, so it’s critical that their assets are up to scratch and built for the task. In an effort to offer the sector both greater choice and exceptional quality solutions, AVK has expanded its range of resilient seated gate valves.
AVK is excited to introduce the new 91 and 51 models to its 570 series of resilient seated gate valves; high-quality flanged and socket valves, complete with all the essential features and benefits you would expect from AVK.
These new solutions offer:
• Low lead copper alloy wedge nut and thrust collar, which are designed to comply with the low lead requirements of the Australian Building Codes Board (ABCB) and New Zealand Building codes that will be mandatory in 2026 Reduced weight design that incorporates a slim line bonnet and gland flange improving general handling
• High AVK quality with local manufacturing, coating and individual pressure testing at the AVK Wingfield, South Australian facility.
AVK has introduced these new valves into its Performance range, providing installers with a cost-effective, high-quality option.
These new valves are available in both flanged and socket versions, ranging from DN80 to DN300 with a PN16 pressure rating. They are accompanied by the circle of confidence of StandardsMark and WaterMark and are WSAA appraised to AS/NZS 2638.2. Installers can also choose to stay with or upgrade to the Premium 90 or 92 Series 570 models that they are accustomed to, which feature the traditional stainless steel gland flange.
AVK HAS INTRODUCED TWO NEW VALVES INTO ITS PERFORMANCE RANGE, PROVIDING INSTALLERS WITH A COST-EFFECTIVE, HIGH-QUALITY OPTION.
For more information, visit www.avkcivil.com.au THE NEW MODELS ARE COMPLETE WITH ALL THE BENEFITS YOU WOULD EXPECT FROM AVK.
This Premium range is the gateway to the Premium Plus range, which offers 16 value-add options for customisation. AVK provides a variety of gate/seat types, actuation options, gearboxes, extension spindles, materials, coatings and extended warranties to suit demanding water supply applications. All AVK branded products come with a five-year quality assurance guarantee covering both material and workmanship.
Installers are now spoilt for choice as AVK maintains its renowned quality, so make the right choice.
Check out our new high-quality flanged and socket valves, complete with all the essential features and benefits you would Expect from AVK.
DN80 - 300
PN 16 pressure rating
Flange and socket connections
Manufactured in Australia
Low lead copper alloy wedge nut and thrust collar
#ASKAVK
AS PART OF THE THE MAREEBA-DIMBULAH WATER SUPPLY SCHEME EFFICIENCY PROJECT, SUNWATER REPLACED 14KM OF PIPELINE.
With the growing focus on improving long-term water security and availability across Queensland, the delivery of quality infrastructure projects has never been more important.
Ensuring that these projects are implemented to the highest standard requires a coordinated approach, with technical specialists and mature industry experience essential to achieve desired outcomes.
Regional Queensland’s biggest bulk water supplier, Sunwater, is actively expanding its capability to deliver a significant program of critical water infrastructure projects.
In meeting its purpose of delivering water for prosperity, Sunwater has broadened its remit from an operate and maintain business to being an infrastructure business that delivers water.
By its very nature as an owner operator of large dams, industrial water pipelines and irrigation schemes, Sunwater requires the capacity to develop, plan, design and deliver significant, complex bulk water infrastructure projects.
By increasing business capability and capacity to successfully plan, design, construct and commission quality bulk water infrastructure, creating regional jobs and helping drive economic growth, Sunwater is focused on its role as a water industry leader.
Responsible for providing around 40 per cent of all water used commercially in
Queensland, Sunwater has expanded in-house skill across operations, engineering and water resources and infrastructure development, to meet growing needs in water infrastructure.
But, with a predicted increase in demand for engineering and professional services across Queensland and Australia, Sunwater is now taking a long-term approach to building its internal capacity.
Sunwater Chief Executive Officer, Glenn Stockton, said that for Sunwater to deliver its significant program of work, an integrated approach with top-tier industry expertise is required.
“Sunwater has a strong pipeline of work in the years ahead,” he said, “We recently completed construction of Rookwood Weir near Rockhampton, and are now focused on other forecast improvement works across our dam portfolio,” Mr Stockton said.
“We are delivering the Paradise Dam Improvement Project, for which we have appointed alliance partners – a consortium between CPB Contractors and Georgiou, and design firm GHD. We will also soon tender for detailed design of the Burdekin Falls Dam Raising and Improvement Project.
“All this work requires an additional depth of expertise and experience to complement our existing capacity.
“Planning for and delivering these projects to ensure the right asset is built means looking to the broader industry for support in the Queensland market, engaging leaders in the field of dam engineering and engaging with overseas firms who can bring proven contemporary global experience to the Australian market.”
As part of this new approach, Sunwater has entered two arrangements that strengthens its position as an experienced and reliable water infrastructure business.
Firstly, Sunwater has partnered with a joint venture between AECOM and Jacobs to provide access to a broad range of engineering capability to support its work and build internal proficiency.
Through the collaboration, Sunwater and its customers will benefit from increased efficiencies, improved engineering outcomes and knowledge sharing, economies of scale and new career path opportunities.
“Historically, we have procured engineering and professional services on an as-needs basis through panel arrangements,” Mr Stockton said.
“With the significant increase in major infrastructure investment over the
coming years, an alternate approach that builds both Sunwater’s and our partners capability and capacity over time was required.
“The long-term partnership with the JV, enables Sunwater to access a broad range of engineering capability and will include a core team co-located in our offices.”
Sunwater has also contracted international engineering, geoscience, and environmental consulting firm, Klohn Crippen Berger (KCB Australia Pty Ltd) for project engineering support services.
KCB Australia, which has a presence in Canada, the United States, United Kingdom, Peru, and Brazil, will provide specialist technical dam engineering expertise, working with Sunwater’s hydrological, geotechnical, civil, dam safety, instrumentation, and operations teams.
Sunwater’s Chief Development Officer, Mal Shepherd, said that KCB Australia will bolster the business’s capacity at key project stages.
“The addition of KCB engineering personnel to Sunwater’s Infrastructure Development and Delivery function, will allow us to flex to meet the needs of different project stages whilst developing and delivering these major projects,” Mr Shepherd said.
“Queensland has an emergent dam design and construction industry which creates a platform to grow the dam industry and provide career opportunities for people.
“As an extension to Sunwater’s owner role across its major projects, this project engineering support service will assist with the development of
construction methodologies, support the technical review of third-party designs and the resolution of technical queries, provide advice on dam safety construction impacts, and perform on-site construction surveillance.
“Excitingly, this seven-to-eightyear partnership is the first time Sunwater has awarded such a support service contract.”
KCB Australia will undertake independent technical reviews, predominantly for the Paradise Dam Improvement Project detailed design and the Burdekin Falls Dam Raising and Improvement Project preliminary planning. This will help ensure that Sunwater is taking a best practice approach to work packages.
Contributing to these projects will be one of the largest packages of work for KCB since entering the Australian market in 1993.
WORKERS AT THE ROOKWOOD WEIR
CONSTRUCTION SITE IN JUNE 2023.
Where previously external engineering support was procured on a short-term basis as required, these arrangements will provide opportunity for Sunwater to improve long-term, integrated technical planning capabilities.
It will also allow for a degree of flexibility that would be otherwise difficult to achieve in the current employment market.
The partnerships will strengthen Sunwater’s capacity to deliver highquality water infrastructure improvements, which will enhance water availability for urban, industrial and irrigation customers across regional Queensland.
Water is our most precious resource, and utilities can’t take chances when it comes to the supply of water to our communities. Understanding the condition of water pipelines is integral to supplying safe drinking water for communities, and here, we look at technology that allows for thorough condition assessment without supply interruption.
To optimise infrastructure management and ensure the reliability of its water supply network, a leading water utility in Australia initiated a comprehensive pipeline rehabilitation and replacement project on what it described as one of the most critical assets in the entire water network. This approach, while straightforward, often leads to unnecessary expenditures and disruptions, as entire pipeline segments are replaced regardless of their actual condition. To address these inefficiencies, the utility decided to adopt an innovative condition assessment program that allowed for a much more targeted and strategic approach to pipeline replacement and rehabilitation, potentially saving tens of millions of dollars annually.
As part of the targeted condition assessment of this section of water pipeline, Detection Services was commissioned to conduct p-CAT™ testing and provide detailed findings regarding the pipeline’s condition. The primary objectives of the assessment were to evaluate the pipeline’s condition and identify features and anomalies such as blockages, air pockets, and wall thickness deterioration.
The pipeline in question, constructed in two stages in 1982 and 1983, spans approximately 6.5km. Stage one was completed in 1982 while stage two was completed in 1983.
The pipeline is predominantly composed of OD965 mild steel cement lined (MSCL) pipes, with several short sections of DN960 MSCL replacements.
“It is one of the most critical assets in the water network,” said a Project Engineer from the utility.
“There were question marks over the condition of this pipeline based on its history, as well as another pipe close by.”
Given its critical role in the water network, there were significant concerns regarding the pipeline’s construction and materials. Notably, the pipeline had been stored dockside for an extended period before installation, raising questions about its integrity. Furthermore, there was minimal failure history, primarily relating to fittings and rubber ring joints, which compounded the concerns about the pipeline’s overall condition.
Based on historical information and the potential risks associated with the pipeline, the initial plan was to replace the entire section, with an
estimated cost of between $30 and $40 million. This plan was included in the capital forecast, reflecting the utility’s commitment to ensuring the reliability of its infrastructure.
However, the utility recognised there was a need for a better understanding of the business risks associated with potential pipeline failures, which prompted the utility to seek alternative solutions through Detection Services.
Detection Services undertook p-CAT™ testing on the pipeline, which uses two main techniques for interpreting the transient pressure wave tests results:
• Sub-section partitioned wave speed analysis for assessment of the level of deterioration of the pipe wall in a sub-section
• Signal analysis for detection of known features and significant anomalies such as air pockets and blockages
The following condition was identified during the p-CAT™ analysis:
• 12.5 per cent of the total pipeline length has a remaining wall thickness of 74 to 76 per cent
• 23.4 per cent of the total pipeline length has a remaining wall thickness of between 77 to 79 per cent
• The rest of the pipeline (59.9 per cent of the total length) has a remaining wall thickness of 80 to 89 per cent
The following known features and anomalies, and their resulting recommended actions were also identified during the signal analysis:
• Two high priority anomalies representing the presence of large pockets of permanently entrained air
• Three medium priority anomalies:
» An open off-take (OT4) which was presumed closed
» And a pocket of permanently entrained air at an air valve (AV5.1)
THE CONDITION ASSESSMENT CONDUCTED BY DETECTION SERVICES PROVIDED DETAILED INFORMATION WITHOUT TAKING THE ASSET OUT OF SERVICE.
• Seven low priority anomalies representing the following known features:
» A large open off-take
» Four replacement sections of pipe
» The branches on two sealed off-takes
The condition assessment conducted by Detection Services provided invaluable
insights, ultimately deferring the planned capital project.
This proactive approach allowed the utility to implement a more strategic condition assessment program, leveraging innovative technologies and methodologies to maintain and enhance their water network more efficiently.
“The cost replacing the pipeline was estimated at 30 to 40 million dollars and it was in the capital program,” said the
utility Project Engineer. “We had every intention to go ahead with that.”
This highlights the level of detail p-CAT™ testing can provide on critical infrastructure; and underscores the importance of targeted infrastructure management in modern utility operations. Importantly, the detailed information was acquired without taking the asset out of service and without carrying out any invasive techniques.
As energy costs continue to increase globally, industry strives to achieve energy efficiency and to reduce overheads to minimise the total cost of operations.
Improved awareness of energy usage is the foundation for any strategic energy management program, but the implementation is complex and it can be difficult to know where to start. This is why NHP is excited to introduce FactoryTalk® Energy Manager™ from Rockwell Automation, an industrial energy management and optimisation solution that helps to improve energy awareness, reduce energy costs and achieve sustainability goals.
FactoryTalk Energy Manager is an IT/OT convergence platform-based energy monitoring application that provides WAGES (water, air, gas, electricity and steam) and production information based on an energy plant model of the underlying process at a plant, process area, line and machine level.
The platform allows organisations to understand where, when and how their facilities use energy to establish the necessary scope of their energy savings efforts and define key metrics. The system will help to compare assets, gain insights on savings and baseload as well as provide a forecast on important
KPIs against greenhouse gas protocol scopes and emissions.
Furthermore, the platform allows operators to contextualise energy data with production data, execute intelligent energy assessments and run data or asset correlations to identify inefficiencies or anomalies. This offering leverages FactoryTalk®DataMosaix™ to enable contextualised analytics to monitor, analyse and optimise energy performance across the enterprise.
Rockwell Automation’s strategy is based on environmental, social and corporate governance (ESG) standards and remains focused on driving three outcomes for organisations: sustainable customers, sustainable companies and sustainable communities.
Energy management systems are integral to Australia’s transition to widespread electrification and decarbonisation. The FactoryTalk Energy Manager industry solution will help organisations connect energy, water and production data from different data sources and provide them the
appropriate functionalities to monitor and analyse consumption, demand, intensity, costs and emissions.
The system helps compare assets, gain insights on savings and baseload, and provides a forecast on important KPIs. Furthermore, it allows organisations to contextualise energy data with production data, execute intelligent energy assessments and run data or asset correlations to identify inefficiencies or anomalies.
The FactoryTalk DataMosaix solution allows businesses to make informed decisions based on their energy consumption and transform their energy management capabilities.
CAPABILITIES
• Aggregate and contextualise energy data from disparate sources Monitor, analyse and compare energy performance in real-time across the enterprise
• Prebuilt real-time energy performance dashboards Energy consumption, demand and energy intensity
• Energy cost allocation Emissions tracking
• Reporting
• Notification management
EXAMPLE APPLICATIONS
Energy monitoring and reporting to improve energy awareness
• Energy emissions tracking and reporting to achieve sustainability goals
• Energy data contextualisation to analyse and optimise energy performance.
Aim for net zero. NHP can help you get there.
Gippsland Water has renewed its Climate Change Strategy, building on the knowledge it has gained since the strategy was originally launched in 2017. This renewal sets ambitious new targets to achieve net zero emissions by 2030 – two decades earlier than first planned.
is critical, which is where this plan comes into play.”
Gippsland Water has said that when shaping this strategy update it has called on the in-depth knowledge and understanding of its region and operations it has gained over many years of service, as well as the latest climate research.
From consultation with internal and external stakeholders, Gippsland Water said that it has expanded its knowledge base and identified the
designed to align with Gippsland Water’s vision to provide a healthy and sustainable Gippsland for generations to come.
“Climate change planning isn’t new to us,” Ms Cumming said.
“For many years, we’ve been undertaking comprehensive modelling to understand what’s happening and where we need to adjust. We’ve also spoken with our customers to find out what they think and expect of us.
“In short, they want us to plan for the future, invest in climate resilience,
Since the release of its strategy Gippsland Water has already taken significant action towards achieving its targets.
Progress so far includes:
Almost doubling its renewable energy generation from 2,806MWh per year in 2017 to 5,451MW per year in 2022
Upgrading its Gippsland Water Factory with two 330kW biogas generators, a 385kW hydroelectric generator and a 1.3MW solar installation
operating costs which ultimately allows us to put downward pressure on customer bills.
“Tackling climate change will involve a combination of engineering solutions, strategic thinking, technological improvements and behavioural changes.
“Innovation in the way we think, plan and engineer is essential. That includes exploring and developing ways to potentially capture and use energy within our systems.”
renewable energy target of 100 per cent by 2025 and contribute to achieving our target of net-zero greenhouse emissions by 2030. They also positively impact the wastewater treatment process by reducing evaporation,” Mr Aquilina said.
“At peak capacity, the solar array can fully power the treatment plant, producing enough kilowatts to power nearly 90 homes per day.”
Drouin was the eighth Gippsland Water facility to be partially powered by solar energy.
“We’ll measure and track our performance and report back to customers with how we’re doing and to also seek their feedback,” Ms Cumming said.
“While no single policy or plan will solve the challenges climate change poses on its own, this strategy brings together the various things we’ll be doing to prepare, respond and adapt so that our customers can continue to rely on us to provide safe and reliable services for decades to come.”
The growing frequency and intensity of extreme rainfall events is putting increasing pressure on Australia’s stormwater assets, which play a critical role in mitigating flood risk.
During floods or heavy rainfall events, stormwater and sewer asset failure has severe consequences including loss of life, public health hazards, environmental degradation and the destruction of homes and critical infrastructure.
Therefore, for Australia’s water utilities, implementing a preventative maintenance program that utilises the right equipment is essential.
REDUCING RISK OF FAILURE
Sewer asset failure can occur when floodwaters or heavy rainfall infiltrates sewage systems and overwhelms the capacity of the system to handle excess water, leading to backups and overflows.
Likewise, stormwater systems play an essential role in mitigating flood risk, however, heavy rainfall and floods can still overwhelm these drainage networks, which results in flooding, erosion, property damage and endangers people’s lives.
There are several factors that can increase the risk of stormwater and sewer asset failure during floods
or heavy rainfall events, including, insufficient maintenance, damaged infrastructure, corrosion and blockages.
Without proactive planning and regular upkeep, these minor issues can escalate into major problems. A well‑thought out preventative maintenance program can empower utilities to stay ahead of potential problems, ultimately enhancing the resilience and reliability of systems.
Integral to effective maintenance programs is the selection of equipment designed to withstand the demanding conditions of utility works, while ensuring efficient and reliable operation.
Beyond functionality, utilities need to ensure they have ongoing support with access to responsive technical assistance and knowledgeable experts. By partnering with a reputable Australian provider, utilities can navigate maintenance challenges with confidence.
Enviroline is one of Australia’s leading specialists in water jetting and pipe maintenance equipment, with more than 50 years of experience helping maintain water infrastructure across the country.
When it comes to preventative maintenance programs, the Enviroline team understands the importance of being able to accurately assess the condition of assets before any
major work is undertaken. Enviroline’s CCTV pipe inspection cameras are an indispensable tool for utilities, enabling a thorough inspection of pipelines to identify potential issues early on before they escalate into major failures. This proactive approach helps avoid costly repairs, environmental cleanup efforts and minimises disruption to communities.
In the event of blockages, utilities can then harness the power of Enviroline’s water jetting trucks, which provide high pressure cleaning capabilities, allowing for thorough removal of debris and blockages from sewer and stormwater systems.
By efficiently clearing blockages, in a way that is targeted, water jetting systems support utilities to limit waste generation and eliminate the need for disruptive excavation and dredging.
Enviroline’s water jetting systems are locally manufactured in the company’s Sydney facility, tailored to meet the specific needs of Australian businesses and incorporating the latest industry advancements.
Utilities can work with Enviroline to customise their fit out to meet their unique requirements, whether its additional storage, specialised equipment mounts or enhanced safety features.
Enviroline customers also gain access to the company’s knowledgeable team and industry expertise, so utilities get the advice they need to get the job done.
Fleet Solutions: Jetting Trucks, Vans, Trailers.
Whether you need a trailer fitted out for serious stormwater work, or a whole fleet of customised trucks for a state-wide Water Authority, Enviroline Group has the range, knowledge and services to deliver a solution tailored just for you.
From SA Water to Singleton Council to the Shire of Kojonup, we work with local, state and federal government authorities, water authorities and major civil contractors across Australia to provide expert advice, tailored commercial equipment, servicing, repairs, parts and accessories.
CITIPOWER & POWERCOR SENIOR ENGINEER, PIENG TRUONG (LEFT) AND CITIPOWER & POWERCOR HEAD OF NETWORK PLANNING, ANDREW DINNING (RIGHT).
As populations grow and consumers become more reliant on electricity, it’s essential that energy networks are upgraded to ensure that they have the capacity to meet demand. To assist with delivering these essential upgrades, CitiPower and Powercor have launched an online platform for third party solutions to network constraints.
When power networks reach their capacity, they usually get a ‘traditional’ network upgrade to supply the extra power that customers need. These works might be a transformer upgrade or an uprated powerline, and these typical ‘poles and wires’ works help utilities to deliver reliable supply to customers.
However, as technologies advance there is potential for new and innovative solutions to be able to deliver similar results using different technology at a lower cost – which in turn could potentially create value or reduce costs for electricity customers.
To explore these options, Victorian networks CitiPower and Powercor have opened up network constraints in a new platform that creates a marketplace for alternatives to traditional poles and wires work.
While the networks have been running tenders for nonnetwork solutions for several years now, over and above the regulated requirements, this is the first using a map-based marketplace solution to make the process easier and more intuitive for bidders.
The online flexibility marketplace was created with global technology provider, Piclo, and offers an interactive map of local network constraints, and more intuitive information about the network needs in a particular area. This allows providers to more easily match their solutions to network opportunities close to them that existing assets or new systems could support.
CitiPower and Powercor are using the flexibility marketplace to offer funding for non network solution providers network-wide, with several tenders and expressions of interest
CITIPOWER & POWERCOR PRODUCT MANAGER, ABBY PERONCHIK, (LEFT) AND CITIPOWER & POWERCOR SENIOR ENGINEER, PIENG TRUONG (RIGHT).
constraints at a range of levels and capacities; from as low as a few dozen kilowatts, to tens of megawatts.
The first flexibility tender in the Piclo platform offers hundreds of opportunities for providers across our networks to defer the need for upgrades, and expressions of interest are also encouraged for millions of dollars of opportunities into the future.
Powercor’s Head of Network Planning, Andrew Dinning, said he hoped providers would bid into the tenders to deliver competitive options and keep costs low for customers.
“We’re really keen to see how much the market has matured to help us deliver for our customers at a lower cost than our traditional ‘poles and wires’ alternative,” Mr Dinning said.
“This might include batteries, virtual power plants or demand management programs, we’d love to hear what’s out there today.”
Mr Dinning said Powercor’s constraint data was already open and transparent and now is easier to access than ever through the marketplace.
“Our new platform further enhances our transparency with network upgrades,” Mr Dinning said.
“Anyone can use the marketplace, look at sites we plan to upgrade, and see if they can compete with traditional network solutions to solve network constraints.”
Mr Dinning said Piclo’s Flex product provided an engaging way for networks to interact with third party suppliers on non-network solutions.
“Having seen Piclo’s work with other networks internationally, we’re excited to partner with them in 2024.”
as a Distribution System Operator and open more of our network constraints to build the market for flex in Australia.”
Piclo CEO and co-founder, James Johnston, said the need for grid flexibility has never been more important for networks, with a rapid energy transition, population growth, home electrification, and rise of EVs making flexibility critical.
“We’re thrilled to announce our partnership with CitiPower and Powercor, which signals our launch into Australia, as the country continues to embrace a rapid energy transition and the potential of distributed energy resources,” Mr Johnston said.
“This represents a significant milestone for Australia as it embarks on its flexibility journey.”
Mr Johnston said the flexibility marketplace enables network service providers such as Powercor to source flexible electricity from sellers during times of high demand or low supply.
This not only helps to remove constraints and reduce the costs for networks to serve customers, but also supports in the decarbonisation of grids, providing flexible electricity over expensive bulk power from traditional coal or gas powered sources.
This platform allows Victorian networks to explore third party options to solve network constraints, seeking flex capacity across their networks.
Solutions successful in Powercor’s current tender may be rewarded with multi-year contracts to provide network support that helps to meet the challenges of increasing maximum demand.
Australia possesses abundant solar resources due to its geographic location and climatic conditions. However, in order to harness theses resources, generation technology needs to be able to withstand the unique environmental challenges our climate presents. Here, we look at how innovate cable solutions tackled termite damage and ensured longevity at the 245MW Avonlie Solar Farm.
Situated close to the equator, the Australia receives intense sunlight throughout the year. The country’s vast landmass and predominantly arid terrain ensure minimal cloud cover, maximizing sunlight exposure; and, furthermore, Australia's clear skies and low atmospheric pollution enhance solar irradiance levels. These factors combine to create optimal conditions for solar energy generation.
Establishing solar farms in Australia yields significant environmental benefits. By harnessing abundant sunlight, these farms generate clean, renewable energy, reducing reliance on fossil fuels and cutting greenhouse gas emissions. This transition to solar power helps combat climate change, mitigating environmental degradation and preserving ecosystems.
The Avonlie Solar Farm is a large solar generation facility located in Narrandera, New South Wales. The project comprises of more than 450,000 solar panels, with a total energy output capacity of approximately 245MW(DC).
The project received development approval from the Department of Planning & Environment in August 2019, siteworks commenced early December 2021 and the project began commercial operation in 2023.
Avonlie Solar Farm is directly connected to a dual 132kV grid connection, which passes through the project site about 20 kilometres south of Narrandera.
The Avonlie Solar Farm is expected to generate approximately 500GW/h of renewable energy per year, providing a diversified supply of low-cost clean energy to approximately 100,000 homes.
In alignment with Nexans’ vision to electrify the future and work towards the new world of sustainable electrification – decarbonised, renewable, and accessible to everyone – Nexans supplied the Avonlie Solar Farm project with 162km of 33kV medium voltage (MV) cables and 613km of 1,500/1,800V DC cables all manufactured at the Nexans’ Shandong China factory.
Termites have a major impact on the longevity of cables throughout many parts of Australia, particularly in the warmer climate areas.
All termites eat plant fibre – typically wood – to derive the cellulose and nutrients they need to live. Obstacles to those food sources, including cable, are therefore eaten and destroyed as a result.
To address these unique challenges, Nexans utilised its more than 50 years of experience with termite resistant cables to develop a new generation of termite barrier, ECOTERM™.
For this project, all underground cables were supplied with the Nexans ECOTERM™ termite barrier solution. ECOTERM™ satisfied a unique environmental, OH&S and chemically free termite protection solution for the project, while aiding installation with reduced bend radii.
As a pivotal player and strategic partner in solar energy, Nexans is renowned for its cable reliability and technical expertise, backed by substantial production capacity. This dedication ensures that Nexans continues to lead in powering Australia’s energy transition towards a more connected and sustainable future.
With an unwavering commitment to empowering Australia's journey towards a more sustainable future, your local manufacturer, Nexans Australia, delivers comprehensive and sustainable electrification solutions to meet the country's network requirements and the growing energy demands of the modern world.
Our dedicated efforts drive us forward, fostering a more sustainable future for all.
As the one of the largest isolated power systems in the world, Western Australia’s energy grid has to tackle some unique challenges in order to successfully manage the transition to renewable energy. Synergy Executive General Manager, Future Energy, Kurt Baker, shares how battery energy storage systems (BESS) are helping the state navigate this transition.
Western Australia is home to world-class solar and wind resources, abundant gas supply and a wealth of battery metals. However, as its grids are isolated from the rest of the country this presents both challenges and new opportunities for the state.
Large-scale battery storage offers an opportunity to provide long-term system stability and support additional renewable generation. To achieve this, Synergy has three major BESS projects in the pipeline, with one already operational and two under construction.
In June 2022, the Western Australian Government announced that the Collie Power Station is set to be retired in late 2027, followed by the Muja D power station in late 2029, which would remove
a combined 1,127MW of electricity generation from the South West Interconnected System (SWIS).
To help replace this capacity, Synergy is delivering an additional 410MW of renewable generation, backed by 1,100MW of energy storage infrastructure.
Synergy Executive General Manager, Future Energy, Kurt Baker, explained that in order to deliver on these projects, Synergy established a new business unit in 2022 called Future Energy, to lead the development of this renewable generation and storage infrastructure, from concept, pre-feasibility and feasibility, through to execution and operation.
“The challenge we have on our hands, or the opportunity, is to deliver those programmes of investments,” Mr Baker said.
“We're putting in 1,100MW of additional storage to assist with the retirement of our coal plants. This storage will both help to soak up the rooftop solar generated during the day and timeshift that into the evening peaks. And to help contribute to keeping the system reliable and stable.”
Mr Baker said that as Western Australia’s grid operates differently from the way in which the National Electricity Market (NEM) operates in the rest of the country, this means that the state has to take a unique approach to its energy transition.
“The way we're set up over here in Western Australia is that while we have some similarities to the NEM – for example in that we have the AEMO as our market operator – the Wholesale Electricity Market (WEM) operates a little differently.
“In the NEM you have many different transmission systems, which are owned by different parties. Here, we only have one party, which is Western Power who are also owned by the State Government.
“In terms of Synergy itself, we do everything generation and retail. We are a government trading enterprise, but we are also one of many market participants in the generation and storage side of the market. One of the unique characteristics of Synergy is that we're the only entity that can actually sell to the residential customers here in Western Australia,” Mr Baker said.
There are two separate electricity grids in Western Australia, the NorthWest Interconnected System (NWIS), which covers the north-western part of the state and the South-West Interconnected System (SWIS), which is the main grid and covers the southwestern part of Western Australia. Western Power owns and operates the transmission and distribution infrastructure within the SWIS. Synergy is the generator and retailer of electricity in the SWIS.
Mr Baker explained that the SWIS is a fraction of the size of the NEM, and completely isolated from the rest of Australia.
“Unlike the NEM, where you've got transmission networks that connect each state together, we're all on our own here in Western Australia.
“We've got abundance of wind and solar resources, which is a great opportunity for us. But, that also brings about challenges in managing the overall system.
“There is lots of sun during the day, but once that sun goes down, that generation associated with that sun disappears. This means we've got a big differential between demand on the system during the middle of the day, when the sun is shining, versus the peak periods.
“We also don’t have geographical diversity. In the NEM, if the sun stops shining because the clouds come over in Queensland, then there might be sun down in New South Wales and because the transmission lines are interconnected you can move electricity from state to state. We don't have that luxury with the system here. So generally, if it's not windy, it's not windy everywhere on our system.
“Rooftop PV is also being installed at a great rate, which is excellent for the decarbonisation of the system.
“However, all that electricity that gets generated during the day needs to be soaked up, and then we need to replace it when the sun goes down at night.
“We want to support customers to continue to put solar on their roofs. It's generating the renewable electricity, which is great for the energy transition and decarbonising the energy system.
“By installing the battery energy systems, they soak up the rooftop solar produced on people's homes and can then time shift energy to the peak period, so that we can then withdraw that energy from the batteries to support the peak load on the system.
“Battery energy storage systems also help contribute to the Essential System Services, which help keep the electricity grid in a safe, stable, and secure operating state.”
To date, Synergy has completed one major BESS project – Kwinana Stage 1 (KBESS1) – and has two more in the pipeline; Kwinana Stage 2 (KBESS2) and the Collie Battery Energy Storage System (CBESS).
“Our first one was what we now call KBESS1, which is 100MW/200MW/h or, in other words, two-hour storage. We completed that in September 2023, but we were about halfway through the construction of that particular system when the State Government made its announcements in 2022, which lead us to launch into KBESS2,” Mr Baker said.
“As the name suggests, KBESS2 is pretty much next door to that existing facility, but it's a 200MW/800MW/h, so it's a four-hour battery. This one will be complete in October this year.
“The next one underway is CBESS, which is 500MW/2,000MW/h. So that project, like KBESS 2 is on track, on schedule and budget.”
Mr Baker explained that both KBESS2 and CBESS are schedule-driven, as the overall system in the state has a need for these projects as soon as they can be completed.
“Demand for electricity is growing at even greater rates than initially thought, which results in these projects having pressure to deliver on time,” Mr Baker said.
In May 2024 Synergy awarded a $160 million contract to SCEE Electrical to undertake civil, electrical and major equipment installation works for CBESS.
“We've completed all the all the early stage earth works for that particular project, so we’re pleased to say we’re off and running,” Mr Baker said.
Synergy also announced in January 2024 that it had reached another milestone in the delivery of KBESS2, having completed the installation of containerised battery systems.
Mr Baker said, however, that with the three batteries combined, Synergy was still 400MW shy of it’s 1100MW target.
“Now we're investigating what our next project will be. We've got quite a good pipeline of storage projects, and like all infrastructure projects, they've got challenges. But we're pleased to say we've been able to navigate our way around those various challenges
successfully so far to get these things delivered on time,” Mr Baker said.
Mr Baker also said that another focus area for Synergy is to support the transition with distributed energy resources (DER).
“We're doing the work to grow our capabilities, so that we can orchestrate those assets in customers’ homes and help customers contribute to keeping the system stable, and help them get better value out of systems they've got installed in their homes. So, it's complementary to the large scale storage as well.”
Despite the positive outcomes for the BESS projects, delivering these works was not without its challenges, which required exceptional problem solving from Synergy.
“For storage projects, when you're trying to deliver those as quickly as you can, one of the challenges is securing long lead items, which is the batteries themselves, the battery modules, and the inverters,” Mr Baker said.
“One of the initiatives that we took is we engaged with the battery inverter market early and then put our supply arrangements in place so that we could essentially forward book production slots for batteries and inverters before we finished fully designing out the remainder of the projects.
“This also helped us build the relationships with the suppliers early in these projects, which allowed us to work more closely together with them.”
Mr Baker explained that another challenge for Synergy was securing the
resources and capability needed to deliver the projects.
“The initiative that we took there was to approach these projects with an integrated project management team, which really means we've got a combination of Synergy people and engineering partners, and put together a project team to do both engineering and project management.
“In the interest of making sure that we deliver these projects as quickly as we can, we've been trying to engage organisations, partners and people who are aligned to our objectives, with our plan as much as possible. If you can get the right motivated people who are all aligned with a common purpose and objectives, then you can just about overcome anything,” Mr Baker said.
Mr Baker notes that this approach helped Synergy to tackle some major obstacles with KBESS2.
“We were due to ship our inverters out of Spain, but not too long after a lot of geopolitical tension was created across the Suez Canal and we couldn't get our inverters to come through the standard shipping routes.
“That was going to set our delivery right back. So, what we did was we worked with shipping agents, we worked with the inverter suppliers themselves, and we ended up chartering vessels to come the long way around. And we actually managed to do it in a way that those inverters landed In Fremantle Port slightly ahead of the original schedule. Which is just an example of how having the right people, the right partners, all with the same common purpose working together helps to overcome these challenges.”
As part of delivering it’s BESS projects, Synergy is committed to making a positive impact on the communities that it serves, and the utility ensures that it works with local Western Australian suppliers whenever possible.
Synergy also supports community organisations, charities and not-for profits driving positive, sustainable outcomes for people and the environment across the SWIS through its Community Investment programs.
Synergy’s Collie Small Grants Program provides one-off grants of up to $5,000 to local not-for-profit organisations that demonstrate their ability to deliver social, economic or environmental benefits to the Collie community.
As of 2024, this is the sixth year Synergy’s Collie Small Grants Program has been making a positive impact in the region. During that time about $170,000 has been distributed to the community.
“We try and get the local community involved as much as we possibly can,” Mr Baker said.
Synergy regularly hosts face-to-face engagement and information sessions with Collie community members, supports local community initiatives and events and recently arranged a local jobs fair to aid in the appointment of local people in the project.
200+ successful hydrogen projects to date
// See why green energy prefer to partner with us >
In May 2024, the Federal Government released its Future Gas Strategy, providing utilities with greater clarity on how it will approach the unfolding energy transition.
BY PROVIDING MORE CLARITY AROUND THE ROLE OF GAS IN AUSTRALIA’S FUTURE, THE FUTURE GAS STRATEGY HELPS ADDRESS SOME OF THE CHALLENGES AND UNCERTAINTIES OF THE ENERGY TRANSITION FACING UTILITIES.
Australia’s renewable transition is well underway, with solar, wind and hydro accounting for an increasing share of the nation’s energy grid. Coal-fired power stations are retiring faster than expected. Since Munmorah ceased operations in 2012, ten major coal-fired generators have closed and retirements have been announced for all but one of the remaining fleet – with about half shutting down by 2035 and the rest by 2051.
However, when it comes to decarbonisation there’s no quick fix. Fossil fuels continue to play a role in powering homes and industries, and under the Federal Government’s Future Gas Strategy, gas will remain an important source of energy in Australia’s medium and long-term future, through to 2050 and beyond.
The Future Gas Strategy provides a framework for gas production and consumption moving forward, which revolves around six principles that will form the foundation of government policy on gas. These are:
• Australia is committed to supporting global emissions reductions to reduce the impacts of climate change and will reach net zero emissions by 2050
• Gas must remain affordable for Australian users throughout the transition to net zero New sources of gas supply are needed to meet demand during the economy-wide transition
• Reliable gas supply will gradually and inevitably support a shift towards higher-value and non-substitutable gas uses, households will continue to have a choice over how their energy needs are met
• Gas and electricity markets must adapt to remain fit for purpose throughout the energy transformation Australia is, and will remain, a reliable trading partner for energy, including LNG and low emission gases In addition to the principles, the strategy also identifies actions to guide Australia forward. These include: Prevent gas shortfalls by working with industry and state and territory governments to encourage more timely development of existing gas discoveries in gas-producing regions
Reduce gas related emissions by working with industry and regulators to minimise venting and flaring of methane from operations and consider further emissions reductions measures through the government’s six decarbonisation plans. The government will also adopt a technology-neutral approach to exploration data acquisition to minimise seismic surveying where possible
• Support households and businesses through the transition to net zero by working closely with the states and territories to manage pricing impacts and the Gas Market Code
According to the Federal Government’s analytic report, which serves to support the strategy, gas consumption is forecast to continue beyond 2050. This is due to its role as back up for peak loads and as firming in power generation. Looking past 2050, the government forecasts that gas will also be used where electrification, other renewable technologies and low emissions gases unavailable or too expensive.
As stated in the Future Gas Strategy, “Gas-powered generation GPG will underpin Australia’s electricity supply in the transition to a net zero economy. It is likely that gas will still play a role in electricity generation up to and beyond 2050.”
By providing more clarity around the role of gas in Australia’s future, the Future Gas Strategy helps address some of the challenges and uncertainties of the energy transition facing utilities.
The variability and unpredictability of renewable generation is one of the main challenges facing utilities during the energy transition. As more and more coal-fired power plants reach retirement, there are increasing concerns around maintaining grid security and stability. The Australian Energy Market Operator’s (AEMO) 2024 Integrated System Plan (ISP) noted that gas-powered generation is required during the energy transition. It posits that gas-powered generation will provide necessary back up with critical power supply when it is needed, both for ‘renewable droughts’ of ‘dark and still’ conditions, or to meet peaks in consumer demand.
According to the ISP, investment in gas, alongside batteries and other network investments, will also deliver essential power system services to maintain grid security and stability.
The latest instalment of the 2024 AEMO Gas Statement of Opportunities report (GSOO) found that gas consumption is expected to decline over the outlook period to 2043, however, gas production in southern Australia is expected to decline at a much faster rate, due to rapidly depleting gas fields in Victoria’s Gippsland region. According to the GSOO, new investment in gas is required to meet demand and mitigate the risk of shortfalls and supply gaps.
The Future Gas Strategy offers industry more certainty that the Federal Government will continue to support the use of gas to meet energy needs. It means utilities can continue to rely on gas-fired power plants as a bridge technology while renewable energy sources are integrated into the grid.
There are several other challenges facing utilities during the energy transition, including:
The need for investment in new infrastructure and technologies to accommodate renewables
• Uncertainties around future regulatory and policy changes that can affect the long-term planning and strategies of utilities and the gas industry
• Promote geological storage of CO₂ and support the region’s transition to net zero by releasing acreage for offshore carbon capture and storage (CCS) and establish a new initiative on regional cooperation on transboundary CCS, which will provide options for energy security and carbon management solutions for regional partners
• The management of future energy costs while ensuring affordability for consumers
With the Federal Government expecting gas to remain in use beyond 2050, the industry has a pathway for planning and investment in infrastructure. This also means there will continue to be policy and regulatory frameworks in place to support the continued use of gas in power generation, offering utilities a more predictable environment to operate in.
COAL-FIRED POWER STATIONS ARE RETIRING FASTER THAN EXPECTED. GAS CAN SERVE AS A BACK UP FOR PEAK LOADS AND AS FIRMING IN POWER GENERATION AS AUSTRALIA TRANSITIONS TO NET ZERO.
With gas set to play a crucial role in balancing supply and demand, adequate storage near high demand areas will be necessary to ensure timely delivery during peak times, which means current gas infrastructure will need to be upgraded.
The strategy also notes that biomethane can be used in existing natural gas infrastructure. Infrastructure used to move gas across big distances to alleviate gas shortfalls may also be adaptable for low emissions gases in the future.
The Future Gas Strategy says that geological storage of CO2 has an important role in supporting the transition to net zero, with the government to continue to release offshore acreage for greenhouse gas storage as well as supporting carbon capture and storage.
Alongside the announcement of the strategy, Federal Minister for Resources and Northern Australia, Madeleine King, said, “Ensuring Australia continues to have adequate access to reasonably priced gas will be key to delivering an 82 per cent renewable energy grid by 2030, and to achieve our commitment to net zero emissions by 2050.”
“The strategy makes it clear that gas will remain an important source of energy through to 2050 and beyond, and its uses will change as we improve industrial energy efficiency, firm renewables, and reduce emissions.
“But it is clear we will need continued exploration, investment and development in the sector to support the path to net zero for Australia and for our export partners, and to avoid a shortfall in gas supplies.”
Ms King said that gas is crucial for Australia as it supports manufacturing, food processing and refining of critical minerals which will help Australia and the world to lower emissions. Gas supplies 27 per cent of Australia’s energy needs and represents 14 per cent of Australia’s export income.
“Gas will play an important role in firming renewable power generation and is needed in hard-to-abate sectors like manufacturing and minerals processing until such time as alternatives are viable and can be deployed.”
When it comes to planning the future energy mix, the Future Gas Strategy makes clear the Federal Government is taking an integrated approach to ensuring energy security and affordability throughout the energy transition.
Protect your critical assets with the most reliable systems made in Australia.
Century Yuasa has been protecting critical power assets for 30 years with our local design, construct and onsite teams. Our DC systems are built with the best of global technologies and supported with the globally recognised Yuasa VRLA batteries which are the only batteries you can genuinely rely on to protect your critical assets and business services year after year.
To learn more about Australia’s own DC power systems, maintenance services, and the Yuasa range of VRLA batteries, visit our website.
For enquiries call 1300 364 877 https://cyb.com.au/industries-markets/industrial
DThe Victorian State Government recently backed the launch of a groundbreaking new standalone power solution – the H2PowerBox – which combines solar and renewable hydrogen to provide a reliable zero-emissions alternative to mobile diesel generators.
econ Corporation is proud to share its significant contribution to the launch of the revolutionary H2PowerBox, a pioneering solution for the Australian utilities sector.
This innovative project is a collaborative effort between industry leaders: Clayton Hydrogen Technology Cluster, GreenRen Power, Deloitte Emissions Solutions, and Decon Corporation. More than two years of intensive research and development have culminated in this state-of-the-art system, positioning Australia as a global leader in hydrogen power technology.
Unveiled on 6 May 2024, at Decon’s Scoresby facility, the H2PowerBox represents a critical leap forward in the transition towards clean and sustainable energy sources.
The momentous occasion was marked by a visit from the Honourable Lily D'Ambrosio MP, Minister for Energy and Resources, who commended the project's contribution.
“This is a shining example of innovative Victorian design that is being championed by our leadership in developing and manufacturing cutting-edge technologies that drive the renewable energy transition,” Ms D'Ambrosio said.
BOOSTING RELIABILITY AND RESILIENCE
Decon's expertise in manufacturing played a pivotal role in the H2PowerBox project. The company’s brand-new Scoresby facility manufactured the customised trailer that houses the system's core technology.
This technology integrates solar energy capture with a revolutionary hydrogen production and storage system. The captured solar energy is converted directly into hydrogen, which can then be used to generate clean, reliable, and 100 per cent renewable energy – even during periods without sunlight.
The H2PowerBox holds immense potential for the utility sector, particularly in empowering remote communities and enhancing disaster relief capabilities.
This technology also eliminates dependence on traditional water sources and significantly reduces reliance on fossil fuels – delivering energy infrastructure that is more resilience and environmentally friendly. This aligns perfectly with Decon's commitment to developing sustainable solutions for the utility industry.
John Iacovangelo, Managing Director of GreenRen Power said, “The H2PowerBox is more than an alternative to diesel; it is a forward leap towards sustainable, self-sufficient power generation.”
Elaborating on the broader implications of the technology, Suren Thurairajah, Partner at Deloitte Emissions Solutions, said, “Designed for scalability and sustainability, the H2PowerBox offers a viable and eco-friendly power solution for remote areas traditionally dependent on diesel generators.”
Throughout 2024, the H2PowerBox will undergo trials at various client locations. This data collection phase will pave the way for full-scale commercial production in 2025, marking a significant milestone for the renewable energy industry.
The H2PowerBox is a testament to the power of collaboration with industry leaders. By combining expertise across research, manufacturing, and energy production, this solution has the potential to transform the way we deliver power. Decon Corporation is proud to be a part of this collective effort, and it looks forward to collaborating further to bring the H2PowerBox to utilities nationwide.
Long-duration energy storage (LDES) will play a critical role in supporting Western Australia’s journey to net zero carbon emissions by 2050. The state’s regional energy provider, Horizon Power, is embracing the latest technology, with innovative LDES trials to support the state's acceleration to a cleaner, greener future.
THE 78KW/220KWH VANADIUM REDOX FLOW BATTERY REPRESENTS A MILESTONE IN HORIZON POWER’S QUEST TO TEST AND HARNESS THE CAPABILITIES OF PROVIDING LONG PERIODS OF 100 PER CENT RENEWABLE ENERGY IN WESTERN AUSTRALIA.
In March 2024, the Albanese and Cook Governments announced a partnership to fund trials of long-duration batteries to help Australians living in off-grid communities access the benefits of cheaper, cleaner solar energy.
With $2.85 million each from the Western Australian Government and the Australian Renewable Energy Agency (ARENA), regional energy provider Horizon Power is responsible for piloting two new battery technologies in remote communities that are powered by regional microgrids.
The trials will test alternative battery chemistries that provide LDES to help Horizon Power understand their suitability for extreme climates.
In Carnarvon, located in the Gascoyne region of Western Australia, BASF's 250kW/1.45MWh sodium-sulphur battery will be the first of its kind in Australia to connect to a regulated network and a distributed energy resource management systems (DERMS) platform. Meanwhile, Redflow's 100kW/400kWh zinc-bromine flow battery will be put to the test in temperatures well over 40oC, further north in the Pilbara community of Nullagine. Both batteries are expected to be deployed in early 2025.
These groundbreaking trials support both the Federal and Western Australian governments’ carbon emissions reduction targets, while making renewables more accessible for regional and remote customers. They will also provide the Horizon Power’s project team with key learnings around how the technologies can be effectively integrated into its network and test their temperature resilience in regions with extreme environmental conditions.
As Western Australia’s only vertically integrated electricity utility, Horizon Power operates across the full energy supply chain: generation, transmission, distribution, and retail services.
Its service area covers about a third of the country, making it the largest geographical catchment of any Australian energy provider, managing the North West Interconnected System (NWIS) in the Pilbara; the connected network that covers three interconnected systems in Kununurra, Wyndham and Lake Argyle; and 34 microgrids tailored to meet the unique needs of some of the most isolated and remote communities in the world.
In July 2023, Horizon Power also assumed responsibility for the delivery of power to 117 remote Aboriginal communities, formerly under the responsibility of the Department of Communities. The Remote Communities program aims to standardise power services for these communities, enabling all Horizon Power customers to have access to the same standard of power as others living in similar sized communities.
Horizon Power Chief Executive Officer, Stephanie Unwin, said the energy provider had been an early adopter of advanced energy storage, and over the past 15 years has been exploring how energy storage can best be used to promote increased uptake of renewable energy across regional Western Australia.
“Our latest trials will continue our exploration of LDES technologies that are suitable for withstanding the extreme temperatures in our regions, providing valuable insights for our team, which will support future battery deployment in our regions,” Ms Unwin said.
“These trials demonstrate our commitment and significant investment toward a cleaner and more sustainable energy future.”
The latest announcement follows Horizon Power's purchase in August 2023 of a Vanadium Redox Flow Battery for a long-duration energy storage pilot in Kununurra, in Western Australia’s Kimberley region.
The 78kW/220kWh battery, from Invinity, represents a milestone in Horizon Power’s quest to test, understand and
VANADIUM BATTERIES BOAST EXCEPTIONAL CHARACTERISTICS, INCLUDING TEMPERATURE RESILIENCE IN HARSH ENVIRONMENTS, LONGDURATION CAPACITY AND STABLE ENERGY STORAGE.
harness the capabilities of providing long periods of 100 per cent renewable energy in Western Australia.
Vanadium batteries boast exceptional characteristics, including temperature resilience in harsh environments, longduration capacity and stable energy storage.
The vanadium battery is undergoing factory acceptance testing in Perth, before it will be transported to Kununurra later this year, for the start of the pilot program.
Horizon Power is eager to demonstrate the potential of long-duration, 100 per cent renewable energy and envisions a future where such solutions power its portfolio of microgrids across its vast service area.
Horizon Power Future Technology & Innovation Manager, David Edwards, said that through decarbonisation planning and extensive modelling it became evident that the regional energy provider would need batteries larger than anything they had previously installed.
“It also became clear, through our work with the regional deployment of lithium-ion batteries across our service area, that lithium technology will only get us part of the way in decarbonising microgrids, particularly due to the amount of energy that's required to keep the batteries cool, which can be challenging in very small systems,” Mr Edwards said.
What followed was a deep dive and techno-economic assessment of the battery technologies available, using 28 dimensions of assessment – to assess their suitability for regional microgrids and small indigenous communities.
“There are a lot of companies out there offering LDES solutions with differing technology and commercial readiness levels,” Mr Edwards said.
"When we were assessing different battery types it was essential for us to partner with battery manufacturers with a local team.
“They had to have someone in Western Australia who could support the battery and experience connecting devices to a regulated network in Australia and working in regional areas.”
“We put different technologies through our assessment criteria – looking at everything from whether it was modular to how much had been installed overseas and if it was weather or cyclone rated. We also needed the product to display a reliable level of technological and commercial readiness.”
As a result, Horizon Power’s focus turned to flow batteries and sodium-sulphur batteries.
“We understood that the sodium-sulphur batteries could scale up cost effectively to large storage systems suited to our decarbonisation aspirations in our seven gas-fired towns,” Mr Edwards said.
“Meanwhile, flow batteries look like a good fit for most of our mid-sized towns, so we’re testing the Redflow (Australian invention) bromine flow battery, and also the vanadium redox flow battery from VSUN Energy.
“Through all these LDES trials we want to demonstrate our commitment and play a part in lifting the energy storage capability ecosystem here in Australia,” Mr Edwards said.
“The batteries have been chosen because they display resilience at high temperatures, improved depth of discharge, modular scalability and most importantly, (minimal) risk of thermal runaway.
“We're integrating the Redflow battery with a new control system and will be testing it for its ability to run the town in ‘hydrocarbons-off’ mode. Time will tell whether it's possible or not. We've done this with lithium-ion but not with a flow battery."
The vanadium battery will be tested in Kununurra, and the sodium-sulphur battery is being deployed to Carnarvon, with room for expansion.
“It made sense to test this one in a gas-fired town because that’s where we see it bringing the most value in the future,” Mr Edwards said.
Mr Edwards said that Horizon Power is proud to be playing a role in the market validation of new and innovative ways to store renewable energy and the network orchestration of energy storage assets via DERMS.
“As Horizon Power is running small, geographically isolated and non-interconnected networks, the utility has to be careful with energy management,” Mr Edwards said.
"The last thing we want to do is unnecessarily curb renewable energy, so it’s incumbent on us to find a solution to cost-effectively store that otherwise curtailed renewable energy. That's where long duration energy storage comes in. The hope is that we will progress to a point where we deploy this technology across our regions to save precious renewable energy for use at another time of the day.
“As we have more storage at our disposal, we can start to develop additional customer-facing products to help them not only more effectively manage their own energy generation, but
REDFLOW'S ZINC-BROMINE FLOW BATTERY, WHICH WILL BE TESTED IN TEMPERATURES ABOVE 40o C IN THE PILBARA COMMUNITY OF NULLAGINE.
The increase in extreme weather, flooding and bushfire events underscores the importance of resilient utility infrastructure, as failure of these assets can have devastating consequences. In a unique pilot project, Shoalhaven Water and the University of Wollongong are collaborating to improve the energy resilience of sewage pumping stations with innovative battery energy storage systems.
Municipal water authorities in regional Australia are responsible for the drinking water supply and sewage treatment processing for towns and communities across a wide range of geographic regions and natural environments.
The flooding and bushfire emergencies in New South Wales during recent years have highlighted the importance of resilient infrastructure, as the frequency of natural disasters increases with climate change. Failure of sewage pumping stations can lead to discharge of untreated sewage to the environment, with serious impacts for local communities.
In the utilities sector there is an increasing appreciation of the complex interdependency between water and energy critical infrastructure, which is sometimes referred to as the water-energy nexus. At the same time, the electricity grid is undergoing a rapid decarbonisation of energy generation, and an evolution of the electricity grid towards a distributed architecture.
Electricity costs are a significant percentage of the operating costs for water utilities, which is driving an increasing investment in on-site renewable electricity generation, which combined with the use of energy storage technology allows for increased flexibility in the operation and scheduling of pumps, and enhanced resilience during grid failures. This is being enabled by technical advances in electrochemical energy storage, particularly for stationary applications such as critical infrastructure, with higher energy capacity and improved safety and reliability, along with the emergence of next generation digital technology for monitoring, control, and optimisation.
In a reticulated sewage system that is not pressurised the wastewater is transported to treatment plants through a combination of gravity fed lines and intermediate pumping stations, or sewage pumping stations (SPS), which pump wastewater from low-lying areas to wastewater treatment plants.
The SPS or lift station consist of a wet well or reservoir, and two or more submersible pumps that are controlled to regulate the level of wastewater in the well, as it fills from nearby premises.
A large municipality can manage several hundred SPS of different sizes across its network, which is a significant operation and maintenance cost for the utility. Power outages or mechanical failures can lead to discharge of untreated sewage to the environment. As such, an emergency back-up system is required. This often involves dispatching service technicians or repair teams with mobile diesel generators, which are expensive to deploy and might not be readily available in an emergency.
Shoalhaven Water is responsible for operating and maintaining the water distribution network (WDN), including water treatment and sewage infrastructure within the Shoalhaven City Local Government Area, on the South Coast of New South Wales.
In a unique pilot project, the Australian Power Quality Research Centre (APQRC) at the University of Wollongong are collaborating with the utility in the design and trial of innovative battery energy storage systems (BESS), aimed at improving the energy resilience of sewage pumping stations.
The pilot project has received funding from the Australian Research Council (ARC), Research Hub for Safe and Reliable Energy, which is promoting research into battery technologies that are focussed on enhanced safety and reliability. The pilot project is located at Shoalhaven Heads, which is a coastal community on the Shoalhaven River north of Nowra.
The project involves a three-year field trial of battery energy systems at ten pumping stations to evaluate the performance and resilience of various existing and emerging technologies, with active involvement of students and graduates across several research disciplines. The research objectives are:
• To develop an understanding of the long-term performance, safety and reliability requirements for a sewage pumping station or distributed infrastructure deployment. This involves long-term data gathering to monitor performance, such as energy throughput, capacity degradation rates, cell imbalance, alarms, and faults
To develop advanced operation and control strategies for distributed pumping stations using energy storage and variable speed drives. This addresses the problem of optimal operational management of distributed municipal pumping stations and aims to operate the system at the
point of maximum efficiency and minimal O&M cost to the utility. One solution is predictive control, which uses system data inputs such as flows, levels, weather data, battery state of charge and energy flows to schedule optimal pump operating profiles. This is a common application for machine learning tools
• To investigate grid-interactive modes of operation such as demand response, market participation, and other grid services, including the aggregated utilisation of distributed battery assets
• To extend conventional reliability-based planning and design methodologies based on probabilistic analysis by utilising resilience-based frameworks for assessment of distributed infrastructure. Resilience includes notions of resourcefulness and adaptability, which are important when considering high impact low probability (HILP) events, like natural hazards
As part of its modernisation program, Shoalhaven Water plans to deploy a new control panel design in parallel with the battery energy storage trial. The field deployment methodology was to select SPS sites where a planned replacement of the legacy pump control panel was already scheduled.
The new control panels require a new concrete plinth, and the legacy control panels are normally stripped of parts and stored at the depot. It was therefore decided to assemble the battery energy system components inside the legacy control panels, which are then installed onto the spare plinth on site. This can be seen in Figure 1, which shows the new control panel in the photo on the top, and the BESS installed onto the existing plinth in the photo on the bottom.
Re-purposing the existing control panels for the BESS was a cost-effective and more environmentally sustainable approach.
The battery system has a maintenance bypass switch which enables faulty components to be replaced or repaired online without losing power to the pump. The stored energy capacity is either 6kWh, 9kWh, or 12kWh depending on the pumping power, which is intended to provide several hours of emergency back-up in the event of a power outage.
The site power usage is dependent on the service duty cycle of the pump, which follows a diurnal usage pattern that is unique for each site. The battery capacity dimensioning procedure utilised a probabilistic approach based on a statistical analysis of telemetry power failure data over several years.
Additionally, conventional Direct Online (DOL) motor starters were changed to the more modern Variable Speed Drives (VSDs) to eliminate very high discharge currents during pump starting, which is in line with other energy saving initiatives.
The field performance of first site was successfully demonstrated during a planned outage of an electricity feeder by Endeavour Energy, which lasted for eight hours before power was restored.
The BESS panels were pre-assembled at the University of Wollongong’s Sustainable Buildings Research Centre then shipped to Shoalhaven Water’s depot in South Nowra, and internally wired by Shoalhaven Water electrical apprentices before final checks and being deployed to site.
The installation and commissioning procedure can be completed in a few hours including electrical testing and programming before the systems are put into service.
All the pilot sites are remotely monitored using system control and data acquisition (SCADA) radio, which sends telemetry data back to the control room.
Battery system data is being analysed by research students as an important part of the trial. The equipment panels experience a wide range of climatic conditions such as temperature cycling that affects the rate of capacity degradation, which are also being investigated.
ENERGY EFFICIENT GRID-INTERACTIVE PUMPING SYSTEMS
Energy is a significant cost for water utilities, with around 80 per cent of the electricity in the wastewater treatment process used by pumps 1
Just as residential electricity usage can be seen to follow a characteristic daily usage profile, similarly the wastewater inflow to the SPS from surrounding premises has a diurnal profile that is reflected in the pump run times and grid power usage.
THE AVERAGE INFLOW TO AN SPS HAS A DIURNAL PROFILE.
The BESS enables a level of flexibility in grid power usage. For example, the BESS can be programmed to supply the pump from the batteries during periods of high grid demand then switch over to grid supply during low demand periods.
In this way, the flow of power from the grid can be optimized to find the least-cost operating strategy for the SPS.
The control objective is to operate the system along the maximum efficiency curve and to minimise the energy consumption, and therefore operating cost, of the pumping station.
Another important feature for future grid applications involves utilising the grid-interactive ability of the BESS to both import and export power to the grid.
This enables the SPS to sell power back to the grid during idle periods. Extending this capability to a large group of SPS sites can facilitate creation of what is known as a virtual power plant (VPP), where the control of a group of batteries is orchestrated to trade energy or provide different grid services.
Rather than use the battery system for a single application, slots of battery capacity can be allocated to different applications. The idea of value-stacking according to the application is not new for grid-scale batteries, where the different applications are known as ancillary services that are bid into the electricity market.
Lithium-ion batteries (LIB) are now a ubiquitous energy storage solution for stationary applications, this technology has been commercially available for several decades and is field proven with advantages that include a high energy density and roundtrip efficiency.
The first phase of the SPS pilot project is utilising lithium-iron phosphate (LFP) technology, which is a robust and safe battery chemistry well suited to this application.
Due to concerns over the long-term cost and environmental impact of lithium extraction for battery manufacturing, research and commercialisation efforts are focussed on sodium ion batteries as an alternative.
Sodium has similar chemical properties to lithium, and the working principle of sodium-ion batteries (SIB) is similar to LIB, though a significant advantage is the natural abundance of sodium compared to lithium.
Due to these similarities, the manufacturing knowledge that was developed over many years for LIB can be applied to SIB.
In the long term, it is expected that SIB can replace LIB for a wide range of applications. The University of Wollongong, Institute for Superconducting & Electronic Materials (ISEM) is actively involved in SIB research and development, and the next phase of the SPS pilot project aims to trial the use of these new batteries at selected SPS sites.
The Shoalhaven Heads Pilot Project is currently in the field deployment phase, with two sites commissioned and another two sites under construction. When completed in 2025, the project will be a showcase for how the innovative use of battery technology can improve the resilience of critical distributed infrastructure.
CONCEPT OF VALUE STACKING IN BESS CAPACITY ALLOCATION.
By Dr. Melita Jazbec, Research Principal, Institute for Sustainable Futures, UTS
The energy, water and waste sectors are all striving to achieve net zero emissions by 2050. A recent study from researchers at the University of Technology Sydney (UTS) found that urban organic waste has a significant role to play in meeting this goal.
Recent Intergovernmental Panel on Climate Change (IPPC) assessment reports2 have stated that the transition to renewable energy from fossil fuels would only address 54 per cent of greenhouse gas (GHG) global emissions. The remaining 46 per cent of the anthropogenic GHG are the result of the production of goods and the management of land – this includes the food system and organic waste generated along its value chain.
Around three-quarters of GHG emissions for the waste sector are produced by organic waste disposed of in landfills, where it decomposes to generate methane. However, only a small amount (eight per cent) of this landfill gas is captured to generate energy 3. To tackle organic waste in landfills, the waste sector has set targets to firstly, half the generation of food waste, and secondly, divert the organic wastes going to landfill via separate organic waste collection and processing.
At the same time, the water sector is aiming to become energy self-sufficient. This could be achieved by utilising anaerobic digestion to process sludge at wastewater treatment plants (WWTP). Anaerobic digestion is a biological process that generates biogas (a mix of methane and carbon dioxide) and digestate. This biogas can then be utilised for energy generation or as a replacement for natural gas. Digestate, which contains nutrients (nitrogen, phosphorous and potassium), is normally used as soil conditioner.
Energy self-sufficiency has been successfully achieved at WWTPs internationally. For example, Ejby Mølle WWTP in Denmark4 has optimised operating conditions to enhance nutrient release and subsequently
increase biogas and energy generation. Other WWTPs have effectively increased generation of biogas through co-digestion of wastewater sludge with other external organic waste feedstocks. Combining wastewater sludge with organic and green household wastes; organic waste from hospitality (e.g. restaurants and catering); from food manufacturing (e.g. dairies, slaughterhouses); and manure from farms, transforms WWTPs into circular economy hubs or biorefineries. A great example is Billund BioRefinery in Denmark5, which processes food waste collected from households and farms, and in return provides energy to households and fertiliser to farms. Co-digestion of multiple feedstocks often results in generation of excess energy (more than the WWTP needs) enabling WWTPs to become energy self-sufficient and export any excess energy.
Billund BioRefinery also explored other circular economy solutions that add value to the business. These include capturing carbon dioxide through algae production and subsequently harvesting and utilising the algae. The company also explored production of bioplastics and proteins from biogas, and use digestate as a soil conditioner, which replaces the need for synthetic and non-renewable fertilisers. Furthermore, Billund is generating additional income by sharing this knowledge and assisting other businesses to implement similar technologies.
In our recent study1, we identified the energy potential of the urban organic wastes that could be co-digested at three selected Sydney WWTP’s. We developed a methodology to quantify urban organic wastes by sector type, including
commercial and industrial waste, for which there is no publicly available data. We also identified energy potential hot spots in the areas surrounding WWTPs, which could assist planners in the development of organic waste collection and processing infrastructure.
In this research, we estimated that urban organic waste from the study area could generate 37.8 billion litres of biogas per year, equivalent to the natural gas used by 30,000 households in a year 1
The generated bioenergy would be 4.5 times higher than the energy currently generated by solar panels in this area. Almost half of all food waste from the study area could be processed at the three Sydney WWTPs.
Utilising the existing anaerobic digestors at the WWTPs would mitigate the need to build new infrastructure to process food waste and divert it from landfills. These three WWTPs alone could fill as much as 20 per cent of the planned anaerobic
digestion infrastructure that needs to be built by 2030 to process Sydney’s projected food waste.
Australia generates 7.7Mt of food waste along the value chain, of which only 40kt are processed through anaerobic digestion and just 736kt of food waste (mainly industrial and commercial) are processed at the wastewater treatment plants. While the main method of processing food waste is composting (2.2Mt including home composting), almost half of food waste still ends in landfills (3.3Mt) 6 . Most of the food waste in landfills are from households and hospitality.
As anerobic digestion processing of urban organic waste not only generates energy but also captures valuable nutrients, why are we not utilising this opportunity more?
In our study1, consultation with stakeholders identified several barriers.
These include operational challenges, such as dealing with inconsistency of feedstock, feedstock contamination (e.g. PFAS, microplastics), and necessary additional pre-processing.
Respondents also described regulatory hurdles (especially in relation to application of digestate to land), issues with zoning, and complex and lengthy contractual agreements in the waste sector.
Many stakeholders were also concerned about the lack of incentives to make this business case viable. There are no subsidies in place for generation of biomethane, despite it being a renewable resource. To be financially viable, there is a need for scaling up, and establishing the new logistics presents additional costs.
Stakeholders also reported that there is already a competition for the organic wastes and there is a challenge in establishing a sustainable gate fee that can compete with the current relatively low landfill disposal fee.
However, stakeholders also saw a lot of opportunities in processing urban organic waste at WWTPs. A main benefit is that WWTPs are located close to sources of the organic waste, which omits the need for it be transported to composting facilities that are generally located on the city’s outskirts.
With the emerging technologies promising a better separation of organic wastes and decontamination
of the digestate, anaerobic digestion would provide similar benefits as composting (producing soil nutrients and fertilisers)and more, as it also generates biogas, an important component in the renewable energy mix.
Stakeholders stated that there is need to conduct further feasibility studies to understand costs, gate fees, the economy of scale, and the economics of capturing carbon. They
also expressed the urgency to gather more up-to-date and high-quality data on the available feedstocks that could be used for generation of biogas.
In addition, solving barriers to utilise digestate as a fertiliser would bring additional revenue for the WWTPs. Currently, WWTPs are disposing of biosolids at cost.
An additional challenge has been presented due to the current strategic direction, and requirement, for the collection of food waste with garden organics (FOGO) from the households.
As FOGO cannot be fed directly into anaerobic digestor, it requires costly additional pre-processing. This makes anerobic digestion more expensive, due to capital and operational costs.
Finally, there is also a need to better understand international benchmarks of best practice, how Australia compares with these, and what are the pathways for Australia to reach the world scale standards. These could include favourable feed-in tariffs, capital grants, guaranteed access to the gas pipeline network at a reasonable fixed cost. Setting renewable gas targets with support will create demand.
Urban organics present an attractive opportunity as a source of biogas, especially if processed in the existing infrastructure at the WWTPs. This pathway will not only solve problems that waste sector faces, but will also assist the water sector in becoming energy self-sufficient and contribute to the transition to renewable energy, with the possibility to generate energy behind the meter or feed into the existing gas networks.
Acknowledgement: Co-authors of the study Dr Andrea Turner and Dr Ben Madden, Funding: RACE for 2030 CRC and it's partners: Sydney Water, NSW EPA, NSW DPIE
1 Jazbec, M., Turner, A., Madden, B., and Nghiem, D.L. (2023). Mapping Organic Waste in Sydney: Advancing Anerobic Co-Digestion for Energy Generation and GHG Reduction. Fast track Project for Research Theme B5 Anaerobic digestion for electricity, transport and gas. RACE for 2030 CRC
2 Pathak, M., et al., Technical Summary, in Climate Change 2022: Mitigation of Climate Change. Contribution of Working Group III to the Sixth Assessment Report of the Intergovernmental Panel on Climate Change. 2022, Cambridge University Press.
3 Pickin, J., Wardle, C., O'Farrell, K., Nyunt, P., and Donovan, S. (2020) National Waste Report 2020. Department of Agriculture, Water and the Environment.
4 Jazbec, M., and Turner, A., 2020 Wastewater gas recovery opportunities in a circulareconomy, report prepared by the Institute for Sustainable Futures, University of Technology Sydney, for Sydney Water
5 Jazbec, M., and Turner, A., 2018, Creating a circular economy precinct, report prepared by the Institute for Sustainable Futures, University of Technology Sydney, for Sydney Water.
6 https://www.fial.com.au/sharing-knowledge/food-waste
As the demand for sustainable waste management solutions grows, Yarra Valley Water is at the forefront, developing food waste to energy facilities that convert commercial food waste into clean, renewable energy. These initiatives make recycling food waste easier and more affordable for local businesses in the area.
Yarra Valley Water is now constructing a second food waste to energy facility in Lilydale, in Melbourne’s east. The cutting-edge facility will cut greenhouse emissions and produce green energy, helping Yarra Valley Water achieve its targets to become net zero and use 100 per cent renewable electricity in 2025.
Valley Water Managing Director, Pat
that the utility is committed to reducing greenhouse gas emissions to help address the effects of climate change.
“The new Lilydale facility has the potential to reduce greenhouse gas emissions by 24,700 CO2 equivalent tonnes every year – that’s similar
to taking 23,000 cars off the road,” Mr McCafferty said.
PIONEERING THE PATH: WOLLERT FOOD WASTE TO ENERGY FACILITY
In 2017, Yarra Valley Water launched Victoria’s first commercial-scale food waste to energy facility at Wollert,
located approximately 26km north of Melbourne's CBD.
The facility processes 33,000t of food waste annually from commercial producers such as markets and food manufacturers, generating approximately 22,000kWh of electricity per day – enough to meet the power demands of about 1,300 homes.
“When we built Victoria’s first commercial scale food waste to energy facility, it was one of the first of its kind in Australia.”
“We’ve been successfully operating one of Australia’s largest food waste to energy facilities in Wollert since May 2017. Our Wollert facility has converted more than 175,000t of food waste to clean renewable energy so far,” Mr McCafferty said.
The electricity generated not only powers the facility and the sewage treatment plant but also supplies a significant surplus to the electricity grid.
Following the success of Wollert, Yarra Valley Water is building a second, even bigger, food waste to energy facility in Lilydale. The new facility will accept 55,000t of food waste annually.
Manager Waste to Energy Services, Stephanie Salinas, said that the organic waste can be anything from fruit and
vegetables from markets, to fats and grease from a fast-food restaurant.
“It is exciting that the Lilydale plant will also be equipped to de-package food from places such as supermarkets.”
“The waste is fed into digestors that work pretty much like a human stomach,” Ms Salinas said.
“We’re converting food waste to renewable energy using the gas that's produced by the anaerobic bacteria inside the digestors,” she said.
This will produce more than enough renewable energy to power itself and the adjacent sewage treatment plant, with roughly 70 per cent of the energy used on site and 30 per cent exported to the grid – making the facility not just environmentally sustainable but also commercially viable.
“The new facility will generate 39,000kWh of electricity per day – which is enough to power the equivalent of more than 2,200 Victorian households,” Ms Salinas said.
Yarra Valley Water says it is on track to meet its goal of generating 100 per cent of its energy needs through renewable sources and achieving net zero emissions in 2025.
This supports the Victorian water sector’s world-leading targets to cut
emissions, as outlined in the Statement of Obligations (Zero Emissions) launched by the Minister for Water, Harriet Shing.
Victoria’s water sector is the first in Australia to commit to being net zero no later than 2035.
“The Victorian Government is playing a lead role in reaching net zero emissions," Mr McCafferty said.
COUNCIL
COUNCIL,
“We’re at the forefront of slashing greenhouse gas emissions, not just locally, but globally. Thanks to projects like our food waste to energy facilities, Yarra Valley Water is set to reach these targets a decade earlier."
“This new facility demonstrates how the water industry can innovate to change operations in order to hit these targets and make a real difference for our environment,” Mr McCafferty said.
Yarra Valley Water's food waste to energy initiatives at Wollert and Lilydale represent significant strides towards a sustainable, circular economy. These facilities highlight the potential for innovative projects to transform waste management, reduce environmental impact, and contribute to renewable
As Yarra Valley Water continues to lead by example, it demonstrates how the water sector can adapt and thrive by implementing innovative waste
We round up the key appointments, resignations and other staff changes within the sector.
Transgrid has appointed Grant King as a Non-Executive Director and Chair to its Board, following the impending retirement of current Chair, Jerry Maycock. Mr King will join the Board from 5 August 2024 and is expected to be appointed to the role of Chair after a short transition period. Mr King has previously worked at Origin Energy and brings more than 30 years’ experience in utilities, engineering, public policy, finance and business.
CSIRO has announced the appointment of Kirsten Rose to the newly-created role of Deputy Chief Executive. Ms Rose has been CSIRO’s Executive Director Future Industries since 2020, leading a diverse portfolio that includes research in agriculture and food, human and animal health, biosecurity and manufacturing. Ms Rose will help lead CSIRO’s strategic direction, focusing on how CSIRO engages and collaborates with the innovation ecosystem while driving simplification and sustainability to increase the impact of science.
Jemena has appointed David Gillespie to the position of Managing Director. Mr Gillespie has been with the business for 17 years, having started in finance and working his way up to the position of Chief Financial Officer (CFO). Prior to joining the team at Jemena, Mr Gillespie worked for Alinta Energy. Mr Gillespie said that the introduction of electric vehicles would be a major focus for Jemena in the near future.
CQUniversity has appointed Paul Hodgson as its new Director of Centre for Hydrogen and Renewable Energies and Executive Director Regional Futures – Energy Transitions.
Prior to commencing at CQUniversity, Mr Hodgson was the interim Chief Executive Officer (CEO) of a bid for a Scaling Green Hydrogen Cooperative Research Centre, where he secured $163 million in cash and in-kind support from 97 partners, including CQUniversity.
Hydro Tasmania’s CEO, Ian Brooksbank, has announced that he will step down on 3 October 2024, moving into semiretirement to spend more time with family. Mr Brooksbank started at Hydro Tasmania as CFO in 2019 and acted in the CEO role from August 2021. He was officially appointed CEO in July 2022. His successor has not yet been announced.
Squadron Energy has announced changes to its leadership team with the appointment of a new CEO and Chairman. Former APA Group CEO and Managing Director, Rob Wheals, has been appointed CEO. Mr Wheals has more than 25 years’ experience as a key executive within the energy infrastructure and telecommunications sectors in Australia and internationally.
Squadron’s current CEO, Jason Willoughby, is set to become Chairman. Mr Willoughby, who was previously CEO of CWP Renewables, said that as Chairman he would take an active role working with regional communities where Squadron’s projects are located. The move comes as Squadron, which is owned by Tattarang group, announced its plans to grow its focus on collaborating with regional communities to ensure they share in the benefits of renewable energy projects.
Sunshine Coast, Queensland
24 & 25th July, 2024
Join your peers at our QLD Water Industry event fostering information exchange among operational roles in water, wastewater, and recycled water sectors. Our Conference and Exhibition offers a platform for water professionals to update skills, network with peers, and explore cutting-edge technical advancements.
An Operationally focused event program spanning two days which includes 15+ Paper Presentations, Poster Presentations, a Keynote speaker and WIOA Members forum
UniSC Water Battery and Lake Tour
QLD Women of Water Breakfast
IXOM Water of Origin Competition
2024 QLD Gala Awards Dinner
QLD Main Tapping Competition
Free Visitor Admission to the Expo Hall with over 110 exhibitors showcasing their latest innovations, services and products
Competitions, entertainment, freebies and charity raffle
PROUDLY SPONSORED BY