Engineering, Construction & Maintenance
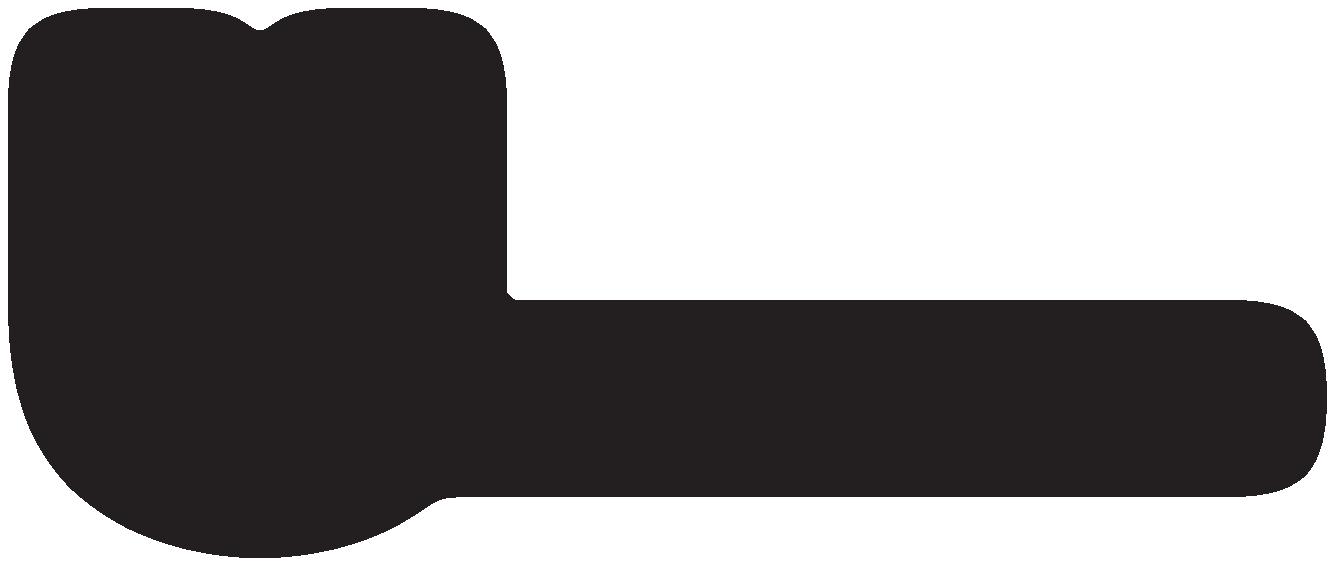
In full
Fitzroy to Gladstone Pipeline another step closer

Power across borders
What’s in store for Project EnergyConnect?
Engineering, Construction & Maintenance
In full
Fitzroy to Gladstone Pipeline another step closer
Power across borders
What’s in store for Project EnergyConnect?
Sydney Water’s long-term infrastructure roadmap
Smart welders create environment-based, fully-documented welds.
Plus, longer coupling lengths create more secure fusion zones and exposed wire fittings create stronger, faster welds. Speak to your local Reece Branch to find out more.
Scan to subscribe to Utility’s weekly newsletter – delivered to your inbox every Thursday morning.
Published by
Prime Creative Media
ABN: 51 127 239 212
379 Docklands Drive
Melbourne VIC 3008 Australia 03 9690 8766
www.primecreativemedia.com.au enquiries@primecreative.com.au
ISSN: 2203-2797
Editor
Katie Livingston
Journalist
Kody Cook
Art Director
Alejandro Molano
National Media Executive
Rima Munafo
Marketing Manager
Radhika Sud
Marketing Associate
Bella Predika
Digital Marketing Assistant
Emily Gray
Publisher
Sarah Baker
Managing Editor
Laura Pearsall
Cover
Sydney Water operational staff at the St Marys Water Recycling Plant.
Image: Tim Jones; Chee Productions, courtesy of Sydney Water
This document has been produced to international environmental management standard ISO14001 by a certified green printing company.
Welcome to the first issue of Utility for 2025. As we settle into the new year, we’re celebrating the turn of the quartercentury with one of our biggest editions yet, jam-packed with insights from some of the sector’s best and brightest.
The last three months have been a shining example of the industry’s dedication to not just safeguarding, but improving the services that communities depend on. As climate change and extreme weather usher in new challenges, utilities from all sectors are coming together to find new solutions.
Essential service providers from all over Australia and embracing innovation to keep customers connected. In this edition, Western Power took us through its resilience program and shared some of the technology it uses to keep its electricity network safe.
We also put a spotlight on more of the fantastic innovations that are uplifting the industry, including South East Water’s award-winning HydroTrak geofencing solution.
In Queensland, the Fitzroy to Gladstone Pipeline is yet another step closer to safeguarding Gladstone’s water supply, and in this issue, that GAWB took us through the project’s latest milestones and what it has in store for 2025.
In this era of unprecedented growth, increasing populations require even more essential infrastructure, and big things are happening at Sydney Water. We spoke with the utility about its new Long Term Capital and Operational Plan, which provides a clear roadmap to deliver the infrastructure that will keep Sydney’s water services sustainable and resilient all the way through to 2050.
Over in the energy sector, Australia’s largest transmission project is powering ahead, and Transgrid gave us the full tour of EnergyConnect’s achievements and offered a glimpse into what’s still to come.
While these major projects are the key to building Australia’s future, none of this would be possible without brilliant people on the ground, and in this edition, we took a deep dive into how the industry as a whole can address the skills shortage. The Institute for Sustainable Futures and RACE for 2030 shared their projections for the workforce numbers required to deliver AEMO’s ISP, while UnityWater and Stanwell Corporation led by example and took us through the work they’re already doing to nurture tomorrow’s workforce.
As we step into the new year, it’s fantastic to see the incredible work that utilities from all sectors are doing to build a secure and sustainable future, and I can’t wait to see what unfolds in 2025.
Katie Livingston Editor
Drop Katie a line at katherine.livingston@primecreative.com.au or feel free to call us on 03 9690 8766 to let us know what you think. Don't forget to follow Utility on social media – find us on LinkedIn, X and YouTube.
For critical power systems, trust Century Yuasa to deliver:
Life Cycle Replacement: Prevent unexpected failures with planned battery replacements tailored to your operational needs.
Supported by decades of expertise and a nationwide service team, we help you:
Extend the lifespan of your assets
Asset Management Program : Ensure system reliability with comprehensive testing, reporting, and maintenance. Protect your investment with Intelepower Power Systems by Century Yuasa.
Reduce downtime and operational risks
Achieve compliance with Australian Standards
Energy Networks Australia (ENA) has welcomed SA Power Networks CEO, Andrew Bills, and AusNet CEO, David Smales, to its Board of Directors.
Both Mr Bills and Mr Smales were appointed as directors for a three-year term, which commenced in November 2024. The ENA Board for 2025 is:
• Essential Energy CEO, John Cleland (Chair)
Horizon Power CEO, Stephanie Unwin (Director)
• CitiPower and Powercor CEO, Tim Rourke (Director)
Endeavour Energy CEO, Guy Chalkley (Director)
• Powerlink CEO, Paul Simshauser (Director)
TasNetworks CEO, Seán Mc Goldrick (Director)
• ElectraNet Chief Executive, Simmon Emms (Director)
Western Power CEO, Sam Barbaro (Director)
• Energy Queensland CEO, Peter Scott (Director)
• APA Group CEO, Adam Watson (Director)
AusNet CEO, David Smales (Director) SA Power Networks CEO, Andrew Bills (Director)
ENA Board Chair, John Cleland, said the new appointments would complement existing board expertise.
“Both Andrew and David bring a deep understanding of the sector and a commitment to delivering safe, reliable and affordable energy networks, which will be invaluable as we navigate the challenges and opportunities ahead,” Mr Cleland said.
ENA CEO, Dom van den Berg, said the team looks forward to working with Mr Bills and Mr Smales, who have already made a significant contribution to the energy industry in their respective CEO roles.
Image: earth phakphum/shutterstock.com
“Our new directors bring a large amount of experience from within the sector and I look forward to working with them as we ENA continues to drive tangible and innovative outcomes for electricity and gas networks to enable the energy transition,” Ms van den Berg said.
“It is an exciting, yet challenging time for the sector and we are committed to continuing to enable the rapid growth of renewables and support customers through the energy transition in an affordable and sustainable way.”
Mr Cleland and Ms van den Berg also thanked outgoing directors, Power and Water CEO, Djuna Pollard, and AGIG CEO, Craig de Laine, for their leadership and contributions over the duration of their appointment and their ongoing commitment to delivering real outcomes for customers and the energy sector.
WSAA has put together a comprehensive framework to achieve a nature positive future.
In August 2024, WSAA released Nature Positive Water, a paper showcasing nature positive opportunities for water utilities, which provides guidance on reporting and measuring nature positive initiatives. With nature loss impacting our economy and society, understanding these risks and opportunities is essential for ensuring resilient infrastructure and services for our communities and future generations.
To achieve a nature positive future, it is essential to recognise the interconnectedness of climate, nature and the circular economy. Addressing the complex challenges of our future requires a systematic and balanced approach across these three areas. Water, as a critical element linking all three, must play a significant role in implementing and leading nature positive actions.
The following five focus were used in the case studies and the paper to frame the key enablers and drivers that supported the implementation of nature positive water:
• Resilient water supplies and water conservation
Efficient and effective treatment reducing water pollution
• Achieving net zero greenhouse gas emissions
Regeneration to restore balance with nature
• Systems transition and partnerships. The 24 case studies cover locations from Australia and Aotearoa New Zealand, and across the water sector (e.g. companies, utilities and government) and include:
Impacts and dependencies on nature
• Understanding nature’s impacts and dependencies – Yarra Valley Water
Resilient water supplies
• Purified Recycled Water Discovery Centre – Sydney Water
• Removal of disused water infrastructure and reconnecting headwaters of Yarram Creek – Barwon Water Healing County with Water Returns to Traditional Owners –Victorian Government
• That’s My Water! Bush Schools – Power and Water
Efficient and effective treatment
• Achieving net zero nutrients –Unitywater
• Enhancing drainage systems and mitigating pollution- drainage freshwater mussel research and demonstration – Water Corporation
• Floating wetland pilot project –Westernport Water
• Floating wetland trial to extend the life of built wastewater assets – TasWater
Achieving net zero
Nitrous oxide trials and scenario testing – Watercare
• Global collaboration towards net zero emissions – Melbourne water collab Demands for carbon offsets with benefits for biodiversity – Victorian water corporations
Regeneration to restore balance
Regenerating waterways and reconnecting local water cycles – WaterNSW Protecting catchment health and restoring threatened habitat – SA Water
• Bush Regeneration at Fosters Spur –Rous County Council
• Restoring land and enhancing biodiversity – Icon Water
• Restoring flows for the platypus in Monbulk Creek – Melbourne Water and South East Water
Drought-proof koala habitat –Urban Utilities
• Restoring habitat for critically endangered species and cultural values – Yarra Valley Water
• Reef guardian councils – Cairns
Regional Council
• Thrive 2035 net clearing objective –Water Corporation
Systems transition
• Circular economy roadmap and toolkit –Wannon Water
• Greening using sustainability bonds –New South Wales Government Establishing Water Funds as a collective action structures to investment for impact – The Nature Conservancy The paper also includes the development of recommended actions for the water sector and governments that aim to support water utilities in better achieving nature positive water.
WSAA expects that the water sector will use the lessons and key recommendations from the case studies to refine their nature positive approaches.
The report and case studies are available on wsaa.asn.au
When relying on a manual system to bill water carters for hydrant use was causing water loss and quality issues, South East Water brought its expert teams together to develop a new solution.
Emergency services depend on water hydrants to keep communities safe, but while firefighting is their primary function, these hydrants also enable water to be transported to areas outside the limitations of the network.
Private water carters in South East Water’s service area are required to report whenever they draw water from these hydrants for billing purposes. However, with more than 60,000 hydrants in its network, keeping track of this usage is a mammoth undertaking.
South East Water Product Development Manager, Ninad Dharmadhikari, explained that prior to 2012, water carters kept track of their fill via a paper-based log.
“We soon realised that’s not the most efficient way to go about it. Processing these logs required a lot of manual effort and it was prone to errors – it wasn’t sustainable in the long term,” Mr Dharmadhikari said.
“So, in 2012, we started the journey to develop a system called HydroTrak®. Initially a very basic system, now
in 2024 it is much more complex, featuring real-time GPS reporting and complex geofencing algorithms. As part of the permit process, we install a little device on the dashboard of a water carter’s vehicle. Every time they fill from a hydrant, they simply press the button on the device and it sends a digital transaction message to our system, so we can ensure their bill is fair and accurate.”
HydroTrak is an IoT device that continuously logs and reports GPS coordinates via the cellular network to a
designated online database server and was designed to be as minimally intrusive and as maintenance free as possible.
South East Water also developed an online portal that allowed water carters to track water usage across their fleet and automated the workflow of permit applications and HydroTrak installations.
As part of the test and trial process, South East Water applied a robust, stage-gate research and development process, involving various prototypes and checkpoints at each stage to justify further business investment in developing the system.
During the process, the utility found that while the prototype units were a step up from the paper-based system, Mr Dharmadhikari said the organisation recognised there was still room for improvement.
South East Water found that a number of fills made by water carters were still going unreported, so the organisation continued to develop the HydroTrak device. After speaking with the drivers, Mr Dharmadhikari said that in most cases this lack of reporting wasn’t intentional, but rather the result of drivers forgetting to press the button on the HydroTrak device.
“What surprised us was the number of times this had happened, and that insight was enough to make the decision to develop a solution,” he said.
Another issue was that drivers had very little means of identifying which hydrants were suitable for their vehicle.
“If the pipe network underneath
the hydrant is not the right size, then filling from that hydrant can unsettle sediment that might have accumulated in the pipe over time, leading to turbidity and potential water quality issues and complaints,” Mr Dharmadhikari said.
Without the means to easily identify these hydrants, there was an increased likelihood of drivers filling from unsuitable hydrants and no easy way for South East Water to trace these fills back to the vehicle.
A collaborative effort
To overcome the limitations of the early iterations of HydroTrak, South East Water devised a geofencing algorithm that could detect fills in real-time.
Mr Dharmadhikari said that developing a complex geofencing solution required a collective and coordinated effort from several areas of the business.
“We did our stakeholder engagement with various teams at South East Water – that’s when we pulled in our operational technology team as well, who are the owners of the HydroTrak technology, and their support was key to our success.
“Together, we envisaged an update to the system that would help solve the problem, and that update was the HydroTrak Geofencing system.”
This new generation of the technology leverages GPS data from the existing HydroTrak devices already installed in the carter’s vehicles, which is then fed into a sophisticated geofencing algorithm installed on a secure South East Water server.
This software is also connected
to the GIS system via an application programming interface (API), which provides it with up-to-date location information for all the hydrants in South East Water’s network. The algorithm then uses these two data sets to detect fills in real-time and pinpoint the hydrant being used.
“The algorithm can identify stoppages that the vehicle makes in close to realtime. Of all those stoppages, it can then detect the ones that are likely to be fills – because not all of them are fills, some could just be a driver parked next to a hydrant, but in reality they’ve gone to a cafe nearby; or it could be that the driver is stuck in traffic or has stopped at traffic lights and there happens to be a hydrant nearby,” Mr Dharmadhikari said.
“The algorithm then considers all of these different scenarios to identify those stoppages that are highly likely to be fills, and when that happens, the server sends a message to the device installed in the vehicles, and that causes the device to issue an audible alert.”
Upon receiving the message from the system, the LED light on the HydroTrak device activates, indicating green for a suitable fill hydrant or red for an unsuitable one.
After two minutes, the device then makes a continuous beeping sound and drivers can either press the ‘fill’ button, which acknowledges that they are filling their tanker and generates billing data, or the reject button to acknowledge that they engaged in an activity near a hydrant but were not filling, which suppresses the sound and doesn’t charge the driver.
The system also actively tracks the number of times a vehicle rejects the detected fills or uses unsuitable hydrants, which then enables South East Water to carry out further investigations and to engage and learn with the water carters about their water usage practices and behaviours.
Mr Dharmadhikari said that prior to launching the updated software in 2022, the algorithm was developed over a series of prototype iterations.
“We quickly realised when we started looking into geofencing, that while the technology itself is not new, it hasn’t been applied in this context to solve this specific problem, so we had to do a lot of trials.”
The first stage was to develop a minimal investment proof-of-concept geofencing algorithm, which was implemented using Python programming language and executed on a computer.
This early development iteration took GPS data and combined it with the GIS data to detect fills. South East Water then visually monitored a small group of water carters and compared the time of their fills with the results detected by the proof-of-concept algorithm.
“We had to do robust and exhaustive testing before we could even connect a single customer to this system,” Mr Dharmadhikari said.
“So, we first plugged these devices into our own vehicles and tested within our service region, parking next to hydrants to see if the system response is appropriate or not.”
The results from these trials not only demonstrated that the Geofencing system could successfully detect fills in real-time and send alerts to drivers, but also that the optimised algorithm could do so with greater accuracy.
“We also issued a user experience survey to these drivers to see what the experience is like, and almost all of them said they appreciated that it was reminding them to push the button.”
With positive results from the trial and support from water carters, South East Water made the decision to commence a fleet-wide rollout in December 2022. In addition to saving an estimated 65ML of non-revenue water across its network, the latest generation of HydroTrak allowed most of the workflows relating to hydrant billing to be automated, reducing both manual input and errors.
Despite these strong results, Mr Dharmadhikari said that there is still scope for further innovation and an opportunity to harness the power of machine learning and AI.
“Machine learning models could further improve the accuracy of these detections to a point where we may not even need the driver to push the button,” he said.
While the results showed promise and proved the feasibility of the system, it was not yet able to detect fills in real time, nor send alerts to drivers.
“Off the back off that, we then developed a more mature system, which we called the Alpha prototype,”
Mr Dharmadhikari said.
During this next stage, the algorithm was converted into a software service and hosted on a secure server.
This enabled the system to now detect fills in real time, distinguish between suitable and unsuitable hydrants and generate audible alerts.
Mr Dharmadhikari explained that throughout the innovation process, each iteration of the system was optimised based on feedback from internal stakeholders and users.
“As we were developing this system, one of the requirements that emerged was from our water quality protection teams was they wanted a way to assess if a turbidity issue was likely to be linked to use of an unsuitable hydrant,” he said.
“In partnership with our operational technology team, we upgraded our existing business portal. It has a map view, where you can see any customer complaints within each region, the metadata associated with those complaints and then any water carter activity in the area.”
In the final stages of development, South East Water recruited a small group of carter vehicles for a three-month trial.
“In 2022, we connected 100 vehicles to the new system prior to launch to see if it was going to succeed. And through that trial group, we quickly saw a revenue improvement of around 36 per cent,” Mr Dharmadhikari said.
According to Mr Dharmadhikari, the data collected from the HydroTrak Geofencing system could be used to train a machine learning algorithm, with South East Water planning to investigate the viability of this solution once the fleet-wide rollout is complete.
The current iteration of HydroTrak Geofencing is also only able to detect usage from permitted water carters, however, South East Water hopes to leverage its growing digital meter network to change this.
As the utility continues to digitise its network, the data provided by digital meters and leak detection sensors can be used in conjunction with the geofencing system to track and identify unexplained water usage and streamline audits.
While there is a bright future ahead for the further generations of HydroTrak, the technology is already enjoying international fame. HydroTrak claimed two titles in the Water Technology Excellence category at the 2024 Asian Water awards (Research and Development – Australia; and Water Resource Management – Australia) and was also Highly Commended for Research and Development Excellence at the 2024 AWA Victorian Water Awards.
For Mr Dharmadhikari, HydroTrak has been a journey of continuous improvement, and one that he hopes the water industry as a whole will be able to benefit from.
“Moving from one generation to another didn’t happen overnight –it took as a long time,” he said.
“As far as the technology is concerned, I’m just keen to see the water industry as a whole benefit from something that South East Water has invested in, because it’s provided us with some real benefits.”
An accurate condition assessment of a pipeline empowers utilities to make the best use of their resources, but it’s important to use the right technology for your asset type.
Information is the key to success in asset management. With finite resources at their disposal, utilities need to ensure that they can allocate their time and budgets where it’s needed the most, especially when it comes to critical pipeline infrastructure.
Condition assessment technology can create a clear overall picture of a pipeline and identify the precise locations of leaks and structural weaknesses, measure corrosion levels and provide data-driven insights into performance and potential remaining life – however it’s important to choose a solution that aligns with the characteristics of your asset.
According to Detection Services Chief Operations Officer, Chris Evans, there is a huge range of technologies available to
utilities across Australasia, but not all of them have been validated and some are used incorrectly.
“For example, at Detection Services we offer a number of validated noninvasive technologies for pressurised assets – ranging from air/gas/blockage detection, illegal offtake assessments, wall lining loss and remaining life analysis to autonomous free-floating multi parameter sensors, magnetic flux leakage (MFL) assessments, and laser and Sonar equipment with LIDAR,” he said.
But Mr Evans said that the efficacy of these technologies varies greatly depending on your objectives and the nature of the pipeline. And to choose the right condition
The efficacy of condition assessment technologies varies greatly depending on the nature of a pipeline.
assessment solution, utilities need to understand how different variables interact with these technologies.
Material thinking
To get the right outcome and make an informed decision about condition assessment technology, Mr Evans said that utilities need to consider the material, diameter, length and location of the pipeline, as well as its function.
“The material type will begin to dictate the selection criteria, often pipelines are a mix of materials and if this should be the case then it helps define the right technology that will provide the outcome you seek,” he said.
“For example, depending on the outcomes required, Detection Services would suggest that a long-range screening tool like p-CAT would be the most appropriate for mild stell cementlined, asbestos cement, ductile iron, cast iron and pre-stressed concrete pipe.
“However, for GRP and plastic – we have some interesting new technology from the p-CAT suite of technologies. We now offer p-CAT Spectrum for assessing the condition of such pipelines to a very high degree of accuracy and outcomes. For long-range leak detection in such pipelines, we would suggest the use of a free-floating sensor, which provides a cost-effective assessment.”
The length and diameter of the asset are also key factors to consider, and Mr Evans said that it’s often more efficient and cost-effective to choose one technology that can accurately cover many different scenarios.
“For longer lengths, the selection criteria can be somewhat limited, however, p-CAT has completed surveys of 180km on a large diameter pipeline.
“Traditional, and some emerging solutions, are limited in larger diameter assessments due to the density or lack of available fittings. Ensuring a technology that can scale from 100mm to more than 2m in diameter covers many of the current roadblocks when performing a condition assessment,” Mr Evans said.
It’s important not to overlook the environment surrounding the pipeline too, and Mr Evans said that having access to GIS data or plans can help service providers understand the location, alignment and types of fittings, which in turn refines the technology selection process.
“Providing information on defect locations is highly desirable for asset owners who cannot take the asset out of service, but in some instances the pipeline is under canals, rivers or rail lines and is not accessible.
“In those cases, we’d suggest a longrange screening tool with sub-sectional defect analysis, such as p-CAT,” he said.
Mr Evans said that understanding other characteristics, such as the hydraulic profile and function of a pipeline, is also immensely helpful in refining the technology and test durations.
“Depending on the situation, gas pipelines could either require an
intrusive or non-intrusive solution, so Detection Services offers several innovative technologies to support the gas industry, such as free-floating sensors, or external analysis by MFL or SCT. Detection Services has also worked with a leading industry partner to develop a high-definition camera for live environments,” he said.
While in general many assessment technologies can be used for both gas and water pipelines, the different substances carry different risks.
“For example, in a wastewater pipeline a gas pocket can be highly corrosive,” Mr Evans said.
“If the pipeline is metallic, we can use our magnetic flux leakage (MFL) tool, smart-CAT, to give the pipeline an MRI so we can see the very highest levels of corrosion inside and outside the pipe.”
“We can also use p-CAT for pipelines that carry water and for pipelines that carry gas, but they need to be the right pressure. For assets that can’t meet the requirements of p-CAT, we use a free-floating multi-sensor system.”
We’re in this together
According to Mr Evans, a well-thought-out, well-informed condition assessment program can help utilities be more surgical about their refurbishment strategy, reduce failure risks, enhance safety, extend asset life and lower long-term costs.
“Utilities can identify performance issues, prepare emergency response plans and update risk registers to ensure the right actions are taken to prevent failures and to respond effectively.
“Knowing the most fragile elements of the pipeline allows utilities to prepare an intervention response, by way of the failure consequence and type, and prepare intervention strategies on the sections identified that carry the most risk, saving time and money," he said.
“By understanding issues such as air pockets, blockages and wall lining loss, utilities can also surgically provide interventions to deal with the locations identified, as opposed to a broadbrush capital replacement approach.”
As pipelines are often expensive assets to replace, Mr Evans said that it’s important that utilities can be confident in the outcomes of their condition assessments.
“This really means you have to partner with a technology provider who has significant experience in all environments and has technologies that can meet every situation. At Detection Services our pipeline tests are completed by experienced staff who have worked in some of the most challenging of environments using the very latest of our portfolio.
“Asset owners need full confidence that the technology is appropriate, has a long portfolio of verification assessments and is operated by experienced teams.”
The Streets Opening Coordination Council is working to build a culture of collaboration between utilities, traffic authorities and councils across Australia.
Uncoordinated street works present several critical challenges, including financial waste, public inconvenience and reduced asset integrity due to repeated excavation and repairs.
By working together, councils, road authorities and water, energy and telecommunications asset owners can coordinate their capital works programs with each other to minimise community disruptions, reduce costs and deliver better outcomes for customers.
This is the mission that underpins the ethos of the Streets Opening Coordination Council (SOCC), but the association’s goals don’t stop there.
Sydney Water Maintenance Programs Planning and Monitoring Manager and SOCC Chair, Stuart McDonald, explained that these industries have so much they could learn from each other.
“Whether you’re a utility asset owner, a council asset owner, a service provider or a designer, we want to upskill and inform for the betterment of the entire industry.
“By working together, we can look at solutions together,” he said.
Down memory lane
Mr McDonald explained that SOCC was initiated in 1909 to address challenges surrounding Sydney’s street works.
“Prior to 1909, there were a lot of issues with the Postmaster General and councils, particularly regarding where their assets have been constructed,” he said.
“Then, as the city developed further with trams and other utility services, the roads were being dug up time and time again. And the community was getting really frustrated.”
It was clear that the city needed a centralised organisation to bring these parties together and coordinate future capital works, so the Lord Mayor of Sydney convened the first Streets Opening Conference on 10 March 1909.
“It was originally hosted by the City of Sydney, it was well attended by all the utilities and Sydney Water was one of the foundation members within that forum,”
Mr McDonald said.
“Then around the 1940s or 1950s, SOCC endorsed a proposal from the City of Sydney for an agreed allocation of utilities within the street space, which gave each organisation dedicated space to lay their services to ensure that there was a consistent approach for where assets were being constructed.”
Mr McDonald said that SOCC also initiated Dial Before You Dig in New South Wales.
“In the late 1980s, the Sydney One Call was first floated in SOCC, and it was
kicked off in the early 1990s. This was later known as Dial Before You Dig New South Wales and ACT. Each state’s Dial Before You Dig service was combined into a nationally operated service about two years ago,” he said.
While previously only covering the Sydney Metropolitan area, SOCC was reconstituted in 1995 to encompass the whole of New South Wales and the ACT.
During this time, the collaboration process was still a manual task, and Mr McDonald said that he would have to scour excel spreadsheets for more than 40 councils to find potential overlap with Sydney Water projects.
“So, in the late 2000s, SOCC saw an opportunity to make everyone’s capital works programs easily available on a common digital platform,” he said.
Over several years, the specifications were finalised and then the infrastructure WORks Coordination System (iWORCS) was trialled in a proof of concept.
Mr McDonald said that SOCC went out to tender with iWORCS in 2016, and the first generation of the software was launched.
“We’ve now gone on to iWORCS II, with a new provider and partner and we’re able to promote iWORCS nationally,” he said.
By working together, councils, road authorities and utilities can coordinate their capital works programs and deliver better outcomes for customers.
With the national expansion of iWORCS, SOCC saw a need to share its knowledge and collaborative culture with the rest of Australia.
“The issues that our members have day to day are the same issues that will be happening in every other state in Australia,” Mr McDonald said.
“We saw a great opportunity to open chapters in other states so they can share the same level of collaboration that we enjoy in New South Wales.
“I know that I can ring up Jemena, Ausgrid or Telstra and have a chat about how that organisation might deal with certain scenarios, and I can then inform my organisation about how we need to work with another party.
“It’s really beneficial to be able to have those conversations. Many of the members have been on the Board for a while, and over time you get to build trusting connections between organisations.”
Fostering collaboration
In his role at Sydney Water, Mr McDonald said there’s been several instances where SOCC members have helped him solve a complex problem.
“I’ve worked closely with Jemena. When one of their assets was too close to our water main, we were able to be respectful of each other’s assets and ensure that assets are constructed as per the technical guidelines that have been endorsed by all of our members,” he said.
“Another example was a traffic kiosk that was immediately adjacent to an operational water valve, which took away some of the space required to operate that valve. Through collaboration with the road authority we achieved a positive outcome for both parties. In that instance, working together informed a change within the best practice guidelines to consider not just the underground space, but also ensure that the operational space above ground that is not impeded by other surface related infrastructure.”
Transport for NSW Senior Manager, Utilities Services, Thanh Ha, said that he joined SOCC ten years ago, and having a network of people to connect him to other organisations has been hugely beneficial.
“At intersections, we have traffic signal facilties, and Sydney Water’s got water mains that are generally allocated to a section near the kerb,” Mr Ha said.
“We have to place our traffic signal facilities in the footway as well, and it may clash with other utilities. So SOCC is very important to mediate that and help all the other service providers to collaborate, and there is now an allocated space for transports traffic signal facility in the footway.”
Mr Ha said that SOCC has helped Transport for NSW work together with utilities to reach a positive outcome for both parties.
“For example, we needed to upgrade our stormwater in Newcastle, but Jemena had an old gas pipeline in the way that was redundant but was kept or reserved to accommodate possible future use.
“Through SOCC, they gave us approval to do it, on the condition that we just cut out a section to get our pipe through.”
Mr McDonald said that in October 2022, SOCC saw a need to add further value to its members.
“Part of that is running community practice sessions to share innovation and share success stories about how we’re doing something different and how other organisations can utilise that.
“Within the community practice events, we’ve also showcased a number of safety innovations that have then been shared across all industry service providers.”
Through these events and its board meetings, SOCC shares safety alerts and lessons.
“While we may not share the exact particulars, we can still share the lesson that has been learned without naming names,” Mr McDonald said.
“This is not necessarily just when someone is injured, but it could also be a potential incident that can be shared before it occurs across all industry, not just within one organisation.
“What we’re also looking to do is highlight these safety lessons on our web page – that’s coming in 2025.”
United across sectors
SOCC is supported by several other organisations that work in the same space but have different objectives.
“By working together, we can cover a much wider group of interested parties to share common messages. And we’re really proud that we have an MoU with IPWEA New South Wales and ACT,” Mr McDonald said.
SOCC’s focus for 2025 is to continue its engagement across all sectors, and open chapters in each state where local utilities, councils and stakeholders can come together.
“There’s great value in learning from someone else that’s done it all before. SOCC is not for profit, we’re here to help everyone create a positive change in their state,” Mr McDonald said.
“Wouldn’t that be great if everyone had a story to share that helps to prevent damage and safety issues, and provide cost savings right across the industry.
“We’ve embedded a collaborative culture within SOCC where we can grow together across all industries. It’s important to protect your organisation, but we can be better together.”
For more information, contact SOCC CEO, Nabil Issa, at ceo@streetsopening.com.au or visit streetsopening.com.au
To support a booming population, meet net zero targets and safeguard its ageing assets, Sydney Water has unveiled a long-term capital delivery plan with customers at its heart.
By decentralising its network Sydney Water aims to avoid expensive upgrades and strengthen. Images: Sydney Water
As Australia’s largest water utility, Sydney Water provides vital services to more than five million people across Sydney, the Illawarra and the Blue Mountains. For 136 years, the utility has evolved alongside the needs of its customers, maintaining and improving its ageing infrastructure and optimising its network to balance efficiency with affordability.
But as the city enters an era of unprecedented change, Sydney Water is facing new challenges that have tested the limits of its network.
Sydney Water Executive General Manager of Infrastructure Delivery, Nicholle Sparkes, explained that Greater Sydney’s population is forecast to increase from five million to eight million by 2056.
“It’s really once in a generation. We need to expand the capacity of our water and wastewater services to meet the demands of that population growth, but we’re also dealing with ageing infrastructure and many of our assets are reaching the end of their operational life,” she said
“Thankfully, they were built to last, and some of our assets have an extraordinary history so a lot of the work we’re doing is to keep them going for as long as we can, as well as supporting our communities and customers with new infrastructure.
“We’re also dealing with climate change like we haven’t previously. The severe weather, prolonged drought and flooding are quite a strain on our existing systems.
“And on top of managing all that, we also have to meet the needs of our customers and their expectations for more reliable, environmentally conscious services – that’s just basic human needs.”
To navigate these complex challenges, Sydney Water developed a new Long Term Capital and Operational Plan (LTCOP), which gives the utility a clear roadmap to deliver the vital infrastructure that will keep its network sustainable and resilient for the next three decades.
“It's quite an adaptive framework, and it looks to balance cost, risk and service level,” Ms Sparkes said.
“The framework guides $83 billion of investment up to 2050, and $32 billion of that is earmarked for the next decade. It really focuses on decentralising systems so that we’re improving resilience, and then we’re leveraging off innovative technologies to meet the demands of our customers.
“It also really ensures that those investments are aligned with our customer priorities and long-term sustainability goals.”
When developing the LTCOP, Sydney Water carefully evaluated several investment options to ensure that it was able to deliver the best possible outcomes for its customers.
Ms Sparkes explained that Sydney Water undertook extensive studies to inform the LTCOP.
“We’ve engaged with more than 13,000 customers through a program
called Our Water, Our Voice, which really helped to align our investment with our customer priorities,” she said.
“Along with the customer engagement, there was a lot of collaboration with government agencies like WaterNSW, NSW Health and NSW Department of Planning & Environment.
Ms Sparkes said that Sydney Water undertook a lot of scenario modelling to assess risks, and stress tested its infrastructure against climate and population forecasts. It also looked at the services levels it provides and how all this would impact cost outcomes.
“It was really well informed, but at the forefront of all this was the cost to our customers, and so that we can make sure that we’re delivering the best outcomes in an economical way.”
Ms Sparkes explained that Western Sydney in particular has experienced the highest growth due to major housing developments and the new Western Sydney Aerotropolis. And when the utility factored in the region’s current and projected population increases, the subsequent economic expansion and ongoing greenfield developments, it identified this area as a priority.
“Sydney Water focused on addressing that growth by expanding wastewater treatment capacity and developing decentralised systems and stormwater management solutions. Then on top of that, we’ve got our advanced recycled water scheme to meet environmental and customer needs.” Ms Sparkes said.
Over the next ten years, Sydney Water will invest about $34 billion in its network.
By decentralising its water and wastewater systems and disrupting the west-to-east flow, Sydney Water aims to reduce its reliance on some key assets, and therefore avoiding expensive upgrades, strengthening its resilience and lowering long-term costs.
Over the course of 2025, Sydney Water aims to advance the first four key infrastructure projects in under LTCOP:
• The $1.5 billion North West Treatment Hub
The $1 billion Upper South Creek Networks Program
• The $838 million upgrade and augmentation of the Prospect PreTreatment Plant
A $1.2 billion Advanced Wastewater Recycling Centre to service the new Aerotropolis
Ms Sparkes said that the ongoing design and construction efforts for the North West Treatment Hub was at the top of that list.
“It really supports that rapid population growth and ensures the wastewater management for that booming north-west region,” she said.
“Then, the Upper South Creek Networks Program is really critical for the Aerotropolis and enabling sustainable urban growth within
that area. Next, we move out to the Prospect Pre-Treatment Plant, and the upgrade there will improve water quality and reliability for 80 per cent of Sydney’s population.”
The Advanced Wastewater Recycling Centre for the Western Sydney Aerotropolis is also set to reach the completion and commissioning phase in mid-2025.
“That [facility will] enhance water reuse, reduce reliance on rainfall and help to protect our natural resources,”
Ms Sparkes said.
Looking ahead to 2033, Ms Sparkes said that Sydney Water has another four projects in the pipeline.
“There’s the Upper Nepean Advanced Water Resource Recovery Facility, which will build resilience in water supply through an innovative treatment program. Then we’ve got the Purified Recycled Water Schemes at Liverpool, Glenfield and Quakers Hill, which will provide drought-proof water supplies and reduce our environmental impacts,” she said.
“[We’ve also got plans for] a water resource recovery facility in Camelia to enhance the treatment capacity in central Sydney, and then the Upper South Creek Water Resource Recovery
Facility, which is going to support the greenfield developments and integrate circular economy principles in that Western Sydney area.”
We’re all in this together
With a groundbreaking program of works ahead, the framework provided by the LTCOP is essential for Sydney Water to ensure a smooth and timely delivery of this new infrastructure.
“The initial challenge is securing the funding, we’ve got to navigate current regulatory emerging frameworks and any changes that are happening, and the LTCOP serves as a comprehensive guide to ensure alignment with our stakeholder and customer expectations, and then we use proactive risk management and resource allocation to deliver on that.
“It gives us really clear parameters and guidelines of what we need to do and how we can best deliver to Greater Sydney.
As Sydney Water is implementing innovative new technologies in these projects, the LTCOP also helps the utility to encourage community acceptance with the community and provide customers with a clear picture of the work it’s doing.
“The advanced treatment process for recycled water, I think, is going to be a great piece of innovation that will be important for our customers. On top of that we’re using smart water monitoring to enhance reliability and customer service and digital twins to help optimise our infrastructure performance, [and the LTCOP helps with] community acceptance of these new technologies,” Ms Sparkes said.
According to Ms Sparkes, collaboration is a key value that underpins everything Sydney Water does.
“Through programs like Our Water, Our Voice we ensure that our customers are really shaping the decision making, and we’re leveraging off the expertise of our industry partners to deliver projects efficiently, and then really fostering innovation through that process,” she said.
“Collaboration isn’t just a word that we stick on the wall. When we set up a new project, we work to deliver it together.”
Going with the flow
As priorities, challenges and future trends change over time, the LTCOP will adapt and grow to incorporate emerging technologies and ensure that it meets evolving expectations.
While the LTCOP will undergo a review every 12 months, as well as a major review every five years, Ms Sparkes said that this adaptivity is embedded in Sydney Water’s day-to-day activities.
“We’re constantly updating our climate data and evolving our customer needs – it’s something that goes right across the corporation to ensure that the investment remains responsive to the long-term challenges.
“We’re really thinking ahead, but the crux of all that is to make sure that we are managing to meet our customer’s needs and deliver that economically and affordably.
“Because some of these costs are passed on to our customers, we’ve got to be pragmatic about this approach. I’d say it’s a Sydney Water value that customers are at the heart of everything we do, but really it’s the
first and the last question that we ask ourselves – are we sure that this is the right thing for our customers?”
At the end of the day, Ms Sparkes said that the goal of LTCOP was to deliver safe, reliable and affordable water services to its customers.
“By enhancing the water recycling and stormwater management, we’re also reducing emissions and meeting our net zero targets.
“And on top of that we’re creating infrastructure to enable economic growth, and it’s supporting 510,000 jobs,” Ms Sparkes said.
For Ms Sparkes, the LTCOP is about forward thinking, and addressing both today’s and tomorrow’s challenges.
“I think we’ve got a responsibility to do this in a way that lays the foundation for a resilient network. We’re trying to reduce the reliance on rainfall and make sure that the infrastructure that we’re building then adapts to those changing demands.
“It’s about ensuring that Sydney Water remains prepared for the future generations and shaping a sustainable future.”
An innovative approach to sealing and monitoring could set a new standard for water management and pave the way to a more sustainable utility sector.
Water authorities work around the clock to maintain ageing infrastructure while making the most of limited budgets and adhering to rising environmental standards. Outdated or generic equipment can often drive higher maintenance costs and cause unexpected breakdowns, which disrupt operations and add even more expenses.
Innovative sealing and condition monitoring technology can help mitigate these challenges, and help the sector move towards a more resilient and sustainable future.
Advanced seals can enhance equipment performance and longevity, reducing the need for frequent repairs. Condition monitoring systems provide real-time data on equipment health, enabling proactive maintenance and preventing unexpected failures.
These advancements offer the sector an opportunity to optimise their operations, extend the lifespan of critical assets and meet the growing demands for sustainable water.
Split seal technology enables maintenance without the timeconsuming disassembly traditionally required for pump and mixer repairs.
In many facilities, disassembling equipment can mean hours of labour
and significant downtime, both of which come at a premium. Split seals, however, can be installed directly onto equipment, eliminating the need to dismantle motors, couplings or shafts. This saves time, reduces maintenance costs and enhances safety by limiting the need for heavy lifting and complex reassembly.
Another critical advancement is active throat bushing technology, which optimises the environment around seals and minimises the need for flush water, a resource that is both expensive and increasingly precious.
Traditional seals often require a continuous water flush to keep the seal faces cool and prevent contaminants from entering the stuffing box, consuming substantial water resources.
Active throat bushings use innovative design features to reduce or even eliminate this requirement, helping minimise water consumption while maintaining an ideal sealing environment.
Possibly the most revolutionary shift, however, is integrating smart condition monitoring technology for pumps and seals.
By equipping systems with remote sensors that monitor critical parameters – such as temperature, pressure and vibration – facilities can
Adopting advanced sealing and monitoring technologies can help utilities contribute to a more sustainable future.
track real-time data on equipment health and respond to potential issues before they become costly problems.
Bluetooth-enabled and cloud-connected, these sensors allow operators to monitor equipment performance remotely, transforming maintenance from a reactive to a predictive approach.
This transition to predictive maintenance means fewer unexpected breakdowns, reduced downtime and extended equipment life – a considerable benefit for any facility managing critical infrastructure.
As water and wastewater management challenges grow, adopting advanced sealing technologies and condition monitoring can help position facilities for long-term success.
Not only do these solutions help reduce immediate operational costs, but they also contribute to a more sustainable water management strategy by reducing water and energy consumption.
As facilities implement these state-ofthe-art solutions, they are safeguarding their operations and investing in a future with efficiency, resilience and sustainability at its
For more information, visit chesterton.com or chestertoncustomseal.com.au
It’s the Chesterton® standard.
The Chesterton 1510 represents over 40 years of engineering excellence in our most streamlined mechanical seal yet.
Maximize maintenance efficiency and increase plant productivity with the 1510 Single Cartridge Seal.
Designed to fit process equipment plant-wide by incorporating Chesterton T.A.B.S. (Tapered Adjustable Bolting System), the compact profile makes seal installation easy.
Advantages
n Reliable through temperature cycling and intermittent process with monolithic seal faces
n In service impeller adjustment is possible with the unique centering strap
n Prevents damage to your equipment and internal components via true non-fretting design
Download Our FREE E-Book: “Taking the Mystery Out of Mechanical Seals”
Safety on the worksite is a must, but this can prove challenging on major pipelaying projects as traditional methods often involve workers being near moving machinery.
To minimise risks, water organisations are looking to new methods of pipelaying that increase safety without sacrificing efficiency.
Melbourne Water teamed up with Delcon Group and Global Pipeline Equipment to deliver a critical pipeline that would meet the growing demand for water in the northern and western suburbs of Greater Melbourne.
The new pipeline connects the Yan Yean Water Treatment Plant with the Bald Hill, Kalkallo tank site, and improves the reliability of the water supply in the northern suburbs and frees up capacity to transfer more water to the western suburbs.
Delcon Project Director – Water Services, Tom Mulhall, said that the project took eight months to complete and stretched over 10km.
“Every project has challenges, and one of the main ones we faced was being able to load and unload pipe safely,” Mr Mulhall said.
“That’s why we utilised the vac-lift system from Global Pipeline, so that we could improve that safety aspect. We didn’t have to have people on the back of trucks or trying to sling pipes. We were able to do it all from the ground, create greater exclusion zones and lay pipes much more safely.”
Melbourne Water Health and Safety Manager, Peter Cations, said that the lifting, shifting and placement of various pipes – often in lengths of up to 13m and up to 2m in diameter – was one of the most dangerous parts of pipelaying.
“Typically, you would have a dogman rigger who would have a tagline on the load to control it. So, you’ve got one
Vacuum lift technology eliminates the need to personnel to be in close proximity to pipes while they’re in the air.
or more persons in proximity to that load while it’s being lifted and shifted,” Mr Cations said.
“But now with the vacuum lifter, once the tension is taken off the strapping on the loads, there’s no need for any personnel to be within proximity of those pipes while they’re being unloaded.
“The excavator will move and position the vacuum lifter onto the relevant pipe, pick that pipe up, position it into the necessary area and then release the vacuum.
“The beauty of the vac-lifter is you can rotate the pipe 360 degrees horizontally, you can tilt it up and down, left and right, so it can be placed into a trench without any need for other personnel to be in the trench at that time.
“The direct interaction between people and pipes is reduced back to almost zero, which is a huge reduction of risk.”
Mr Mulhall said that working with Global Pipeline was easy. The supplier provided reliable, comprehensive support for crews using the machine.
“In Victoria, there’s not too many people who have experience with this technology. But Global was able to explain to the crew how to use the machine, how to maintain the machine and how make sure that it is operating in a safe manner.
“We were also able to bring them in with our safety team and help create our own checks and balances and create the documentation that was needed to make sure that people were safe, and that's the reason we’re using this at the end of the day; to make worksites safer.”
For more information, visit pipelineplanthire.com.au
The PL1500 is a gamechanger for pipeline construction. The unique, quick-hitch, vacuum lifter attaches to your existing excavator, reducing your machine hire cost and getting things moving fast. Capable of safely lifting 15,000kg, the heavy-duty, self-contained unit can handle all types and lengths of pipe. It integrates seamlessly with the host excavator, using the main controls and hydraulics to operate the vacuum lifter. Plus, built-in smart tech ensures it’ll only pick up or put down a pipe on a solid surface. That’s safer than many other vacuum lifters on the market. To find out more, speak to the Pipeline Plant Hire team today.
Burkert’s servo-assisted diaphragm valves meet the new WaterMark requirements. Image: son Photo/shutterstock.com
The requirements for the WaterMark certification are changing – here’s what you need to know.
The World Health Organisation has recognised that lead is a chemical of major public health concern and that the primary source of lead in drinking water is leaching from lead-containing materials in water systems, including plumbing and valves1
As a result, the Australian Building Codes Board (ABCB) released amendments to the National Construction Code (NCC) designed to limit exposure to lead that may leach into drinking water.
Australia's WaterMark certification for lead-free plumbing products now specifies that products intended for use with drinking water must contain no more than 0.25 per cent lead by weight. This applies to copper alloy products and all similar materials that come into direct contact with drinking water.
After 1 May 2026, products that do not meet the lead-free criteria will no longer be authorised for use in drinking water applications, even if they have current WaterMark certification.
The regulation will not affect existing installations, but only new installations or replacement parts from May 2026.
The transition period for Australia’s lead-free plumbing requirements, which runs from May 2023 to May 2026, allows industry stakeholders to adapt to the new regulations 2
During this period, products that are not yet lead-free but have current WaterMark certification can still be used in installations involving drinking water. Stakeholders are urged to manage their stock of products that contain lead, to ensure a smooth transition by minimising leftover stock of non-compliant products.
After the transition period, unsold or unused non-lead-free products cannot be installed or sold for use with drinking water.
If spare parts are required, they also need to comply with lead-free standards by the end of the transition period.
Certifications from other jurisdictions, such as the NSF/ANSI/ CAN 372 lead-free standard, may be accepted during the assessment process, but in Australia the final decision rests with the WaterMark Conformity Assessment Bodies.
For water utilities and other industries that use drinking water in their processes, all valves that come into contact with potable water will also need to meet the new standards from May 2026 – and spare parts inventories will also need to be adjusted accordingly. Luckily, two of Bürkert’s servo-assisted diaphragm valves – the Type 6213 and the Type 6281 with stainless steel bodies – have already achieved the new WaterMark certification. Verified against Australian standards, the valves are compliant with the Plumbing Code of Australia, ensuring reliability and safety for water applications. Featuring a flat-sealing external thread (0.25” to 1.5”), the valves’ designs allow for simple installation and quick replacement, streamlining service work. The design of the valve body also reduces water hammer and noise while optimising flow. Combining innovative design, high-quality materials, Bürkert’s WaterMark-certified valves provide superior performance and reliability.
For more information, visit burkert.com.au
1. World Health Organization 2022, Lead in drinking-water: health risks, monitoring and corrective actions, https://iris.who.int/bitstream/hand le/10665/361821/9789240020863-eng.pdf
2. Australian Building Codes Board 2021, Notice of Direction 2021/4.0 - Certification transition arrangements for lead free plumbing products, https:// ncc.abcb.gov.au/sites/default/files/resources/2022/2021-4-0-NoD-Lead-free-certification-transition-arrangements.pdf
The Fitzroy to Gladstone Pipeline has made a milestone connection, bringing the region another step closer to a secure water future.
The Fitzroy to Gladstone Pipeline (FGP), an almost $1 billion project that will deliver water security and up to 30GL of water a year to Gladstone, has made significant progress since the project was announced in February 2023.
In late November 2024, the FGP team connected the pipeline to the Gladstone Area Water Board (GAWB) network at Mount Miller – a huge achievement that brings GAWB one step closer to securing long-term water reliability for the Gladstone community. Since construction commenced, more than 110km of the 117km pipeline has been installed with GAWB expecting the remaining pipe to be installed by mid2025 and it is anticipated that the FGP
will be operational by 2026, weather and site conditions permitting.
While GAWB is still some time away from reaping the benefits of water flowing from the Fitzroy River to its customers, this connection will enable the integrity of the new pipeline infrastructure to be tested using water from Awoonga Dam before full system integration is completed – which means issues can be identified and rectified prior to the facilities going live.
As with any infrastructure project of this size, months of planning were undertaken to ensure potential impacts to existing GAWB customers were minimised. Around 80 per cent of water supplied to Gladstone is for industrial use. Without this planning,
three major industrial water users with 24/7 operations and significant water demands would have potentially been impacted by the FGP connection. Any disruptions to their supply could have substantial economic and operational consequences.
To address this risk, the GAWB network team and the FGP team engaged extensively with stakeholders to understand their operational needs and implement a solution that maintained uninterrupted water supply during the connection works. This collaboration led to the construction of a temporary bypass system, which allowed for continued water delivery while the permanent connection was constructed.
Following successful connection and testing, the bypass system facilitated seamless water supply to industrial customers for more than two weeks. Once the permanent connection was established, the temporary infrastructure was decommissioned and removed with supply being reinstated from the now modified main line.
Upon completion, the 117km pipeline will run from the Lower Fitzroy River in Rockhampton and connect to GAWB’s existing water network at Yarwun. The pipeline comprises:
• An intake structure at Laurel Bank to collect water from the Fitzroy River
A water treatment plant, pump station and reservoir at Alton Downs
• Two 50ML reservoirs at Aldoga to store water before it connects to GAWB’s existing network at Yarwun
Once water begins to flow, the pipeline will have the capacity to transport 30GL per annum from the Fitzroy River to Gladstone. The pipeline’s design enables it to be retrofitted with additional infrastructure if bi-directional flow is need in the future.
The FGP is not just about water security – it also has substantial economic and social benefits.
Delivered by the McConnell Dowell BMD Group Joint Venture (MBJV), the project has prioritised local engagement and investment, resulting in significant contributions to central Queensland’s economy.
The project set a local spend target of $90 million within the Gladstone and Rockhampton regions. As of the end of October 2024, this target was exceeded, with $123 million spent locally and an additional $167 million invested across Queensland.
Job creation
At the peak of construction, the project created more than 400 jobs, including apprenticeships and traineeships. This investment in workforce development enhances the region’s skill base and supports long-term employment opportunities.
The project set a First Nations Australians workforce target of 10,000 hours. As of the end of October 2024, this target was exceeded, with more than 44,000 hours worked by First Nations Australians.
Queensland Minister for Local Government and Water and Minister for Fire, Disaster Recovery and Volunteers, Ann Leahy, said industry in Gladstone generates $6 billion in gross regional product every year and these activities depend on significant quantities of water now and into the future.
“Our regions are the economic powerhouses of Queensland’s economy. We know that this project and the many economic benefits it creates are important to the people and businesses that call the Gladstone region home. The State Government is committed to valuing and acknowledging the vital role regional Queensland plays in shaping our state and ensuring it remains integral to Queensland’s future,” Ms Leahy said.
“The FGP will enable Gladstone to tap into its water allocation from the Fitzroy River, ensuring the provision of safe, reliable water services and job security, that will improve the liveability of the region.”
Gladstone Area Water Board CEO, Darren Barlow, stated how the investment in the project highlights the region’s significance to the state's economy.
“The FGP is crucial for securing water for Gladstone’s industries, supporting the Queensland economy, and creating jobs,” Mr Barlow said.
“Water security has long been a critical issue for Gladstone, given its reliance on the single-source supply from Awoonga Dam.”
“MBJV has worked hard to engage with and employ local suppliers. Their commitment to supporting local businesses has, and continues to, deliver real benefits to the Central Queensland region, including job opportunities, supply contracts, and the growth of local capabilities.”
Kicking concrete goals
Alongside the connecting of the pipeline to the GAWB network, the FGP team have achieved several other significant milestones.
A total of 580m3 of concrete has been poured at the Alton Downs Water Treatment Plant on Ridgelands Road.
This milestone involved: 14 truckloads of concrete 110 local workers
• 14 hours of pouring throughout the cooler night hours to ensure the concrete didn’t set too quickly Once complete, the water treatment plant will play a critical role in ensuring the supply of safe, high-quality water for both residential and industrial use.
The FGP team has also commenced the construction of two water storage reservoirs at Aldoga.
MBJV coordinated the pouring of a whopping 3000m3 of concrete to form these bases, which involved:
More than 200 truckloads of concrete
• 20 local workers
• Two batching plants located in Gladstone and Calliope
Four 12-hour pours throughout the cooler night hours to ensure the concrete didn’t set too quickly
The FGP team are now focusing on constructing and placing concrete panels to form the walls for these reservoirs, which are being fabricated on-site.
Once constructed, each reservoir will be 76m in diameter (wider than the wingspan of a Boeing 737), 12m high (equal to the height of a three-story building) and will have the capacity to store 50ML of water. Combined, the reservoirs will hold a maximum of 100ML (equal to 20 Olympic sized swimming pools).
“Successfully completing the pouring of the two bases for these enormous water storage reservoirs was a mammoth task. Being able to mobilise local batching plants and workers is something we pride ourselves on,” Mr Barlow said.
“I am delighted the FGP has exceeded its local spend target. GAWB and MBJV have spent considerable time and effort engaging with businesses, suppliers and sub-contractors in the Gladstone region to achieve this success.
“In mid-September 2024, our Chief Operating Officer – FGP, Hugh Barbour, presented at the Capricorn Enterprise Major Projects Forum in Rockhampton.
“In October, he presented at the Gladstone Engineering Alliance Major Industry, Energy and Manufacturing Conference in Gladstone to provide an update on the FGP and to outline future opportunities to work with GAWB. And in 2025, we will continue this advocacy.
“But we are not resting on our laurels and will continue to engage with the communities in which we operate as we progress the project.
Mr Barlow said that 2024 has been an incredibly busy yet rewarding year for both GAWB and the MBJV.
“We’ve made solid progress and I’m really proud of the team,” he said.
The FGP is expected to be operational in 2026, weather and site conditions permitting. Once constructed, the FGP and associated infrastructure will be owned and managed by GAWB.
Link-Seals offer hundreds of solutions to seal pipe penetrations ranging in size from 10mm to 3.6 metres diameter.
Link-Seals are suitable for most types of pipes including PVC, HDPE, Copper and Steel
Resistant to water, oil, gas, aggressive chemicals and fire
Projex Group helps calculate the right Link-Seal size and model for your application
As electrofusion technology advances, innovative industry training can help utilities set the standard for safe, effective and consistent welds.
Communities depend on utility infrastructure to deliver vital services, so it is critical that these projects are completed on time and to the highest safety standard.
But when you’re dealing with tight deadlines, it can be a challenge to ensure your contractors are taking all the right steps for a successful and safe electrofusion installation.
Done right, electrofusion is an effective method for joining polyethylene pipe systems to supply liquids and gases. Done incorrectly, the process can pose problems for organisations, with poor installation practices often leading to expensive mistakes.
For those working on the frontline of piping, there are two ways to tackle this. The first is to use the very best in electrofusion products. The second is to upskill your team with training.
Australian piping manufacturer Vinidex teamed up with German electrofusion powerhouse FRIATEC to change the game for polyethylene pipeline installations in Australia. With a new nationally accredited poly welding course (PMBWELD302E) and strict adherence to the POP001 Guidelines, installers can get hands-on with electrofusion and pick up best-practice techniques that make a real difference on the job.
FRIATEC’s innovative electrofusion fittings system is engineered in Germany with cutting-edge technology and is available exclusively through Reece.
Unlike many standard electrofusion systems, FRIATEC’s solution offers both the pipe and the electrofusion fittings, making it idea for a diverse range of projects, including water pipelines,
The Poly Welding Accredited Course gives installers hands-on training that can make a real difference on the job.
plumbing and building, mining and gas. FRIATEC fittings also include a patented exposed wire design, allowing for faster and more efficient fusion for each and every joint. This, paired with longer coupling lengths and smart welder technology, provides piece of mind to installers when completing electrofusion connections.
But even with the best products at hand, there’s still a growing need across the industry to ensure installers’ skills are keeping pace with the technology. Lack of adequate electrofusion training poses a major problem for Australian organisations, but often training is seen as either too expensive, too timeconsuming or just too hard to pull staff off the job.
A one-day course was the answer for Sam McGarvie, Director of Sam’s Plumbing and Gas, and he signed his
Comprehensive training can help utilities ensure that all welds are completed to a safe, effective and consistent standard.
Images: Reece
team up for the Vinidex Poly Welding National Accreditation training course in March 2024.
“I decided to put our company through the training to educate the employees on the right and wrong ways to do electrofusion,” Mr McGarvie said.
“This included understanding the correct techniques, safety measures, quality standards, and identifying and avoiding common mistakes.”
Steering a course for installers Working in partnership with the Rogue Institute, the Vinidex Poly Welding Accredited electrofusion course is designed to educate installers on how to install Electrofusion systems to the correct standards, plus best-practice tips on how to use tooling and fittings.
The course is self-paced and includes a minimum of three welds of varying sizes and types of electrofusion fittings. There is also a demonstration on how to install large bore fittings, exploring root failure causes, and the correct use of tooling in line with current Plastics Industry Piping Associations (PIPA) guidelines. No other manufacturer in Australia currently offers this level of accreditation directly into the marketplace.
Rogue Institute Course Trainer Luke Cummins said the course is high impact, hands-on and focused on the practical
application of skillsets that can be used same day.
Alongside Vinidex, Mr Cummins conducts the course face-to-face – either in-house or at a convenient location for the students – and includes theory training that enables each student to perform electrofusion to a high standard.
Through theoretical and practical assessments, the course aims to empower trainees to be able to identify compatibility of various commercially available control systems; assess the quality of completed joints; maintain equipment for optimal performance; and to complete safe work method statements (SWMS) on site.
Mr McGarvie said he found that the insights into current industry downfalls were particularly enlightening.
“It really highlighted the need for proper training and adherence to standards in electrofusion,” he said.
“The course has given my employees the confidence to carry out welds, knowing that they will not have any failures. It has also given the builders and engineers confidence that we will consistently deliver a fault-free system by holding a certificate in electrofusion.”
Some of the key tips for a safe and sturdy installation outlined in the Poly Welding Accredited course are:
• Use only reputable brands from companies you trust. Reece is the national distributor of the FRIATEC electrofusion fittings system, available from all Reece Civil branches along with all the associated welders and tools required to install the system.
• Always follow the procedures provided by the suppliers, and make sure systems are fitted to correct manufacturer's standards to ensure a safe and sound connection.
• Get yourself and your team trained in electrofusion via an accredited training course.
• Avoid taking any shortcuts with products and installation. Missing vital steps in the electrofusion process can lead to costly mistakes. Invest in your team and your tools to ensure a successful installation.
While it’s hard taking time away from jobs, the Vinidex Poly Welding Accredited electrofusion course offers employers peace of mind that their employees will walk away from the training with industryacknowledged accreditation compliant with PMBWELD302E and a toolkit of skills that can be applied on site, straight away. Students who complete the course also get the real-world benefits of a nationally recognised Statement of Attainment; a Poly Weld Ticket that’s valid for two years; a Workflow Digital QA Subscription Trial Package; and direct access to the specialised Vinidex technical team. The course is suited to anyone in the civil, plumbing or irrigation industry looking to meet ISO standards in electrofusion and butt welding, and is a great option for businesses wanting to up-skill employees in the space of day. Ultimately, training installers on electrofusion welding is one of the best ways to protect against expensive mistakes, while also giving businesses the edge to successfully complete jobs and maintain their reputation.
To find out more about the course scan the QR code to register your interest, or find out more about the FRIATEC electrofusion fittings system at reece.com.au/civil/brands/friatec
Australia’s climate presents unique challenges for sewer and stormwater asset maintenance, so it’s important to work with a supplier that can give the right advice.
Modern sewer and drainage systems are challenging operational environments at the best of times, but with frequent floods, prolonged droughts and extreme storms, Australian asset owners have a lot to contend with.
Communities depend on utilities to keep these assets in good working order, so it’s important that they are working with the most effective maintenance equipment that can meet their specific needs.
For more than 25 years, DCS Manufacturing has been crafting specialised, customer-tailored cleaning solutions from its Melbourne-based facility. With a passion for research and development, this family-owned business is a leader in product innovation and the company’s focus is to build long-term relationships with customers by delivering quality products, the right advice and the best outcomes.
This specialist manufacturer has a proven track record in designing, developing and producing highperformance sewer cleaning vehicles, which are built to meet the specific demands of a wide range of industries, including modern sewer and drainage systems, and non destructive digging.
Nothing short of perfection
DCS follows a rigorous and structured design and engineering process to ensure that each sewer cleaning vehicle is tailored to the specific needs and requirements of its clients.
During the manufacturing stage, DCS incorporates state-of-the-art technology and skilled craftsmanship to produce each sewer cleaning vehicle to the highest standards. Quality control is a key priority for the team at DCS, and each vehicle undergoes an extensive testing and quality assurance process to ensure that it meets the highest standards of performance, safety and reliability.
Functional and operational testing
Each vehicle is tested in real-world conditions to verify the performance of its systems, including the highpressure water jetting system, vacuum functionality, and wastewater disposal mechanisms. DCS conducts detailed trials to assess the cleaning efficiency, waste recovery capacity, and ease of operation. This testing ensures that the vehicle performs effectively across a range of sewer cleaning tasks, from routine maintenance to challenging blockages.
Meeting safety and environmental standards
DCS ensures that each vehicle complies with relevant industry safety standards, including vehicle stability, emissions control and operator safety. The team ensures that all vehicles meet environmental regulations related to wastewater disposal and air quality. Safety features such as ergonomic controls, spill prevention mechanisms, and reliable fail-safes are rigorously tested to ensure the vehicle’s safety during operation.
Durability and endurance testing
Each vehicle is subjected to endurance testing to simulate extended periods of use. This includes repeated cycles of high-pressure jetting and vacuuming operations, as well as driving over rough terrain. DCS tests the vehicle’s
durability to ensure it can withstand long-term wear and tear while maintaining peak performance.
Final inspection and quality control
Before delivery, each vehicle undergoes a final inspection where the quality control team ensures that all systems are functioning correctly, and that the vehicle meets the design specifications. DCS also checks for visual quality, and ensure that all components are properly installed and secured. Only vehicles that pass this rigorous inspection are cleared for delivery. The in-house service department is now also equipped with a set of truck lifting hoists to ensure your asset is back in operation as soon as possible.
With a customer-centred approach, advanced technology and a dedicated team, DCS is committed to delivering vehicles that are engineered to meet the most challenging operational environments. From concept through to final delivery and after-sales support, DCS ensures that every project is executed with precision, quality and customer satisfaction in mind.
For more information, visit dcsmanufacturing.com.au
Next generation satellite communications.
With Vocus Satellite – Starlink, it’s never been easier for your workers to have effective field communication that supports worker safety during emergency responses in remote areas. It’s the secure, high-performance and reliable connectivity that’s enabling brilliant possibilities for industry and communities.
Construction of Australia’s largest transmission project is powering ahead, with hundreds of workers building the EnergyConnect interconnector.
Transgrid and its construction partner Elecnor Australia are delivering the 700km New South Wales segment of EnergyConnect, which extends from Wagga Wagga to the South Australian border, with a link to Red Cliffs in Victoria. In November 2024, New South Wales, Victoria and South Australia were successfully connected when the two lines on EnergyConnect’s western alignment were energised for internetwork testing. The completion of the 135km 330kV transmission line from Buronga, New South Wales to the South Australian border and the
24km 220kV line from Buronga to Red Cliffs in Victoria allows the transfer of renewable energy directly between the three states for the first time.
Internetwork testing by the Australian Energy Market Operator ensures that EnergyConnect can operate as required to deliver 150MW of power between New South Wales, South Australia and Victoria.
EnergyConnect also reached another significant milestone in 2024, with the integration of the initial section of the new Buronga substation.
of the most advanced in the Southern Hemisphere.
Works are well underway to construct the 330kV Dinawan substation.
Image: Transgrid
The 16ha substation is set to become one of the largest and most advanced in the Southern Hemisphere, equipped with five phase-shifting transformers, two synchronous condensers and four shunt reactors.
Transgrid CEO, Brett Redman, said that the utility is expanding interstate connections to increase security and reliability of supply across the National Electricity Market and provide consumers with access to the lowest-cost generation available.
“The energisation of these new lines has taken millions of hours, and I’d like to thank everyone who has played a role in delivering Australia’s largest transmission project,” Mr Redman said.
“I would also like to specially recognise the landowners and local communities along the western alignment who have worked closely with us to deliver this nation-critical project. We are pleased to have delivered social and economic benefits to them – including jobs, support for local businesses, education and training opportunities and community grants.”
Meanwhile, construction efforts are intensifying on the project’s 540km eastern alignment, with hundreds of workers delivering two transmission lines between Buronga and Wagga Wagga and a world-class substation at Dinawan, near Coleambally.
Hundreds of workers are being accommodated at camps at Lockhart, Dinawan and the Cobb Highway, near Hay, as tower foundation, assembly and erection works move into overdrive. The camps relieve pressure on limited housing in local communities, reduce travel to construction sites and ensure the health and wellbeing of workers with quality living amenities.
Additionally, work is progressing on the 330kV Dinawan substation with foundation works being completed before sophisticated electrical equipment is delivered and installed on-site. Once completed, the substation will enhance power flows between New South Wales, Victoria, and South Australia to support new electricity generation in renewable energy zones.
EnergyConnect is also providing an economic boost to local communities along the project alignment, with more than $200 million invested with 230 local and First Nations businesses to date.
Transgrid Executive General Manager of Stakeholder, Regulatory and Corporate Affairs, Maryanne Graham, said that regional communities are at the forefront of the clean energy transition, benefiting from local investment and job opportunities as this critical project progresses.
“EnergyConnect is delivering substantial social and economic benefits, including employment, skills development, education, and support for local businesses,” she said.
“Our commitment to local procurement fosters business growth and creates lasting job pathways, contributing to a meaningful social legacy for regional Australia. We are proud to collaborate with regional communities and businesses to deliver this essential interconnector, which will provide access to cleaner, more affordable renewable energy and help Australia achieve its emissions reduction targets.”
Regional New South Wales businesses supplying the project have included Kurrajong Timber (Wagga Wagga), Absolute Mesh and Steel (Wagga Wagga), Kennards Hire (Wagga Wagga), Sturt Motel (Balranald), BDS Automotive (Balranald), BIG4 Holiday Park (Deniliquin), and Caruso Bros. Transport (Deniliquin).
Absolute Mesh and Steel Director, Wayne Green, said EnergyConnect has provided a big boost to the Wagga-based business that he established in 2016.
Mr Green said his business is supplying hundreds of tonnes of reinforcing bar for concrete foundations.
“The project has had a very positive impact, helping us to break into the larger commercial area whereas previously we focused only on residential and mediumsized commercial development,” he said.
“EnergyConnect has allowed us to employ additional people and reinvest in the business by installing automated machinery and putting another vehicle on the road.”
In 2024, EnergyConnect became the first electricity transmission project in Australia to receive an official sustainability rating, which recognised a series of industry-leading sustainability initiatives in the design and delivery of the critical interconnector.
The Infrastructure Sustainability Council awarded EnergyConnect the highest design rating of ‘Leading’.
“We are going above and beyond to set the benchmark in sustainability best practice for the future pipeline of energy transmission projects across the country,” Mr Redman said.
Absolute Mesh & Steel Director Wayne Green. Image: Justine Brentnall Studio
“We are delivering real sustainable outcomes with innovative solutions to reducing our carbon footprint, minimising the use of energy and water, protecting valuable biodiversity, decreasing waste, and building in resilience against forecast climate impacts.
“Transgrid is delivering the nation’s critical transition to a clean energy future in a sustainable way by designing and constructing our critical transmission infrastructure to optimise environmental, social and economic outcomes.”
Transgrid and Elecnor Australia have also successfully rolled out the nationleading Legacy 100 program to boost skills in the power transmission sector across regional New South Wales.
Participants complete formal and practical training on EnergyConnect,
gaining valuable qualifications, knowledge and experience in building high-voltage electricity towers and lines.
Executive General Manager of Major Projects, Gordon Taylor, said Transgrid is committed to investing in the nation’s energy workforce to address skills and jobs shortages and support Australia’s great transition to clean energy.
“Legacy 100 has helped to grow Australia’s own riggers and doggers and reduce reliance on overseas trained workers. Program participants will form the backbone of the future workforce in the transmission tower construction industry as thousands of kilometres of new lines are built to support our renewable energy future,” Mr Taylor said.
Graduate Ally Tahau, from Adelaide, left sheep shearing to join Legacy 100.
“We have learnt so much with this program. It’s been absolutely fantastic. We’ve got four tickets, we’ve had heaps of on-site experience,” she said.
“This has been probably one of the best opportunities I’ve had in my life. I think it’s great for females to be getting out on the job and doing such high-risk work.”
Mr Redman said EnergyConnect, along with Transgrid’s HumeLink and VNI West, will revolutionise the NEM.
“EnergyConnect is our first big transmission project in 30 years and it's the absolute bow wave for Australia's energy transition. It will provide system security and access to cleaner and cheaper electricity for consumers well into the future.”
Innovative satellite technology is helping SA Power Networks set a new standard in emergency response. Images: Vocus
When disaster strikes, real-time communication with field crews is critical. To safeguard locals and workers, SA Power Networks is revolutionising its emergency response.
SA Power Networks delivers a vital service to more than 1.7 million South Australians and manages a network of essential assets across the state, including several remote locations.
An unplanned outage can be devastating for these isolated communities, so it’s critical that power is restored as soon as possible – and effective field communication is the key to a swift emergency response.
With its end-of-life satellite system only capable of reaching a maximum speed of 0.5Mbps, SA Power Networks determined that it was hindering timely data uploads and delaying responses during power outages.
Additionally, with the shutdown of the 3G network looming, SA Power Networks’ regional vehicle coverage was under threat. Ensuring worker safety during emergency responses in remote areas was also crucial, meaning that whatever solution the company came to would need to be designed to keep teams connected in isolated environments.
Recognising the need to upgrade its field communication capabilities, SA Power Networks partnered with Vocus and Advanced Mobile IT to develop a modern solution for emergency response.
Developing the right solution
SA Power Networks Project Manager, Mir Asim, said the organisation was intent on finding a solution for enhanced communications.
“Our existing satellite communication technology needed to keep pace with a changing environment and our customer and crews’ high-performance expectations,” Mr Asim said.
Vocus worked closely with SA Power Networks to address its unique requirements and develop a tailored solution.
Ultimately the partnership led to the deployment of Vocus – Starlink satellite technology across SA Power Networks’ field services, emergency response vehicle fleet and remote sites.
“We were looking for what’s next in the field of satellite communications. We did
an analysis, and Starlink was identified as the best option. We procured some units, did some testing, then we looked at deploying it.”
Advanced Mobile IT, with its strong track record in maintaining the IT requirements of SA Power Networks’ vehicle fleet, was tasked with the design and install of custom mounting, power and routing solutions for the Vocus –Starlink satellite equipment.
Mr Asim said developing a telecommunication unit suitable for mounting on fleet vehicles was challenging.
“We had to try a lot of different configurations across our variety of fleet vehicles and the different operating conditions and terrain that these vehicles operate in.
“We came up with about eleven different use cases and implemented them, testing them in a pilot. Now, we are very excited to be rolling it out at an enterprise scale.”
The deployment of 179 Starlink units on emergency vehicles and 21 in fixed locations, along with Advanced Mobile
IT’s custom mounting solutions, has revolutionised SA Power Networks’ response capabilities.
Mr Asim explained that fast and consistent communications with field teams is vital for their work, especially during emergency outage responses.
“A lot of information flows into our outage management systems from the crews that are in the field. Their asset assessments and photos go back to their supervisors, at the depot, and ultimately our network operation centre, to get authorised. Only then can crews receive confirmation to switch power or perform some other maintenance action. It is a significant channel of information, and it needs to happen quickly.”
Mr Asim said that SA Power Networks has seen significant improvements in efficiency after the implementation of the Starlink systems.
“Safety is a key area which is being improved through this initiative, along with timely access to information about our assets, notifications to customers, and the ability to restore power outages faster.”
“The Vocus and Advanced Mobile IT teams have helped realise our goal – it’s been a tremendously productive partnership.”
Mr Asim said Vocus has been a long-term partner with SA Power Networks.
“We’ve got lots of services with Vocus and when it was time for Starlink, we were aware that Vocus had been working with SpaceX on this technology,” Mr Asim said.
“We went through a thorough procurement process and arrived at Vocus as the best choice.”
“As of now, we’re rolling it out for our powerline and electrical services teams, and we have a lot of demand coming in from various other areas of the business.”
Mr Asim said Advanced Mobile IT has also been a partner of SA Power Networks for many years.
“They manage our annual maintenance fleet for the vehicles, so they are quite well versed in the variety of our fleet, as well as contacts at depots,” Mr Asim said.
Mr Asim said that the feedback from field crews has been very positive.
“The only thing we hear at the end of every conversation is ‘when can we have more?’ They are thrilled with the uplifted capability and efficiency which comes with strong connectivity.”
With more demand from different areas of the business, Mr Asim said the utility is analysing its requirements and looking at deploying more of this technology in the future.
“We’ve seen good connectivity when it comes to metropolitan and major regional centres, but just outside that – and especially with the 3G network decommissioning – the need for satellite communication is still being felt”.
“We are setting a new standard in emergency response and community resilience, and it has been made possible by the seamless connectivity that low-earth orbit satellites can provide.”
For more information, visit vocus.com.au/satellite
Effective field communication is the key to the quick resolution of unplanned outages.
Without effective demand management strategies, a rapid influx of new electric vehicles could threaten the stability of Australia’s electricity grid.
As the energy sector powers towards a renewable future, consumers are eager to play their part in the transition, and the adoption of electric vehicles (EVs) is accelerating at an incredible pace.
To facilitate this rapid uptake in EVs the National Construction Code (NCC) 2022 requires a dedicated electric vehicle distribution board (EV DB) to be incorporated into new buildings, and a certain percentage of parking spaces in new developments and in significant renovations must be equipped with EV charging points.
A dedicated EV distribution board is designed to handle the unique electrical demands of multiple EV chargers simultaneously. It ensures a seamless charging experience for EV users while preventing overloads and electrical hazards.
Stress-free charging
Strategic control of electricity demand to prevent grid overloads and supply issues is paramount. Load management ensures that EVs can be charged efficiently without putting undue stress on the grid. New buildings and renovations should employ these strategies such as smart charging and demand response technologies to stagger the charging times of multiple EVs. Doing so avoids demand spikes, maximises the utilisation of renewable energy and minimises the cost of charging.
NHP has developed EnergySync, a cutting-edge load management system that can be easily fitted to an EV DB. There are three modes of EV charging:
1. The EV is directly connected to a standard household socket. This is the simplest charging method, often referred to as 'trickle charging'. It has a maximum current of 10–16A and voltage up to 240V and provides about 8km of range per hour of charging.
2. This method addresses safety concerns related to using standard household sockets. It uses a dedicated charging unit, typically installed at home or in public locations, with a maximum current of 32A and voltage up to 240V (singlephase) or 415V (three-phase). These chargers can provide 19 to 129km of range per hour of charging.
3. DC Fast Charging, employs several control and protection functions for public safety. It delivers DC current directly to the EV battery, bypassing the on-board charger. These chargers can provide a rapid charge, typically reaching up to 80 per cent in just 20–30 minutes, with power levels ranging from 25kW to 350kW.
The best choice of charger depends on factors like convenience, safety and speed, so understanding these modes helps optimise the EV charging experience.
As the demand for EV infrastructure soars in Australia, the utility sector is in a pivotal position to drive change. To help utilities take advantage of this opportunity, NHP has partnered with Delta – one of the world’s largest EV charger manufacturers –to bring a range of high-quality products to the local market that are suitable for most applications in most industries.
NHP offers a range of Delta EV chargers from the basic 7kW AC to the 350kW ultra-fast charging option. The company’s team of dedicated engineers have also developed in-house solutions to meet local changing EV infrastructure needs, including EV readiness site assessment services and NCC compliant EV DBs, which can incorporate NHP’s new cutting-edge load management system, EnergySync.
For more information, visit nhp.com.au/EV
The NHP Services and Solutions team of highly skilled and qualified service technicians across Australia and New Zealand can help your organisation with:
Preventative maintenance
Commissioning and start-up
Modernisation: retrofits and upgrades
Site assessments and reliability evaluations
A host of training options
Repairs in accordance with the manufacturers’ recommendations
For more information, please go to nhp.com.au/services
Australia nhp.com.au
1300 647 647 nhpservice@nhp.com.au
By Beth Griggs, Group Executive Strategy and Corporate Development
Including gas powered generation in a capacity investment scheme could help support an orderly energy transition.
If Australia is to meet its emissions reduction targets, the retirement of coal power stations is one of the biggest steps we can undertake.
However, unless we have reliable, long duration sources of energy to replace coal generation, governments will keep coal open for longer than necessary, which will also delay the further deployment of renewables.
In an energy system that will be increasingly dominated by renewables, giving state governments the peace of mind to allow the closure of ageing coal power stations is going to be easier said than done.
We have already seen this in Victoria, and in May 2024 the New South Wales Government secured a two-year extension to Eraring Power Station, the biggest coal power station in the National Energy Market (NEM).1
This is why we think the Federal Opposition’s proposal on to include gas in the Capacity Investment Scheme (CIS) is a sensible one. The Energy Users Association of Australia also supports this idea, recognising that gas is a critical enabler of a least cost transition to net zero.
As APA has previously highlighted, including gas in a capacity scheme would fill an existing policy gap in our energy framework.
While a great deal of work has been done on the important job of building electricity transmission and connecting renewables, an important piece of the net zero puzzle continues to be overlooked – the alternative source of reliable, dispatchable power when the wind isn’t blowing and the sun isn’t shining.
Until storage solutions like batteries, pumped hydro or compressed air storage can provide the long-term, deep storage we need, we must look elsewhere to ensure that power is available 24/7.
That gap could be filled by gas powered generation (GPG), which would run infrequently but will be essential for backing up renewables during renewable ‘droughts’.
The Federal Government’s May 2024 Future Gas Strategy and the Australian Energy Market Operator’s (AEMO) June 2024 Integrated System Plan (ISP) both recognise the very important role that flexible GPG will play in backing up renewables and storage on the pathway to net zero.
In fact, the ISP clearly stipulates that “Renewable energy connected by transmission and distribution, firmed with storage and backed up by gas-fired generation is the lowest cost way to supply electricity to homes and businesses as Australia transitions to a net zero economy.”
And we can already see this playing out in South Australia. This state is a world leader in renewable energy, but the low wind generation in April 2024 offers a clear example of how important GPG will be as coal power stations are retired across the country.
For three consecutive days in the middle of April 2024, there was little wind across South Australia. GPG stepped up to fill the gap, providing more than 60 per cent of the state’s power needs at peak times when the sun went down, and solar generation went to zero.
Gas stepping in to fill the gaps is not an uncommon occurrence. South Australia closed its last coal power station in 2016, and since then there have been many occasions where periods of low wind and solar required GPG to provide long duration dispatchable generation.
This is why including gas in a capacity scheme would fill an obvious gap in the policy framework.
Throughout 2023–24, Australia’s energy ministers have commenced policy development processes to support various generation projects across the NEM.
In November 2023, the Federal Government announced an expansion of the CIS to a total of 32GW of capacity. The Federal and state governments are now in the process of rolling out the CIS framework across jurisdictions.
In December 2023, energy ministers announced the development of an Orderly Exit Management (OEM) Framework to support the exit and compensation of coal generation across Australia. Draft legislation was published in June 2024.2
The CIS and OEM frameworks are expected to provide financial support to renewables and coal through the energy transition.
However, despite the need for at least 12GW of new GPG to support the increase in renewables and provide security to the NEM, there has been no policy development to support investment in GPG.
In 2022 the Energy Security Board (ESB) recognised that the NEM’s in-built investment signals may not be sufficient to encourage investment in enough generation to maintain a reliable system.
Given its increasingly important role as coal retires from the NEM, government policy must support long term investment in new GPG.
APA Group Executive, Strategy & Corporate Development, Beth Griggs. Image: Daniel Sommer Photography, courtesy of APA Group.
Consistent with the ESB’s findings, the Federal and state governments need to consider whether alternative policy arrangements, such as long-term availability or capacity payments, are needed to support this.
Again, South Australia is leading the way.
AEMO’s 2024 Electricity Statement of Opportunities reports that six of South Australia’s gas power stations are expected to close in or before 2034.3 Faced with these closures, South Australia has introduced legislation that would help establish a capacity scheme that will ensure secure, reliable and affordable electricity supply for the state
Including GPG in the CIS or a similar capacity scheme could help extract other jurisdictions from having to keep coal power stations open for longer than necessary. In March 2024, energy ministers announced a review of the NEM, which could provide another avenue for a capacity scheme to be established. Keeping coal power stations open for longer than necessary will increase the risk of jurisdictions missing their interim emissions targets.
The right policy settings for GPG, and the bringing online of critical new gas reserves, will go a long way in helping reduce the risk of this happening and will help accelerate the roll out of renewable energy, not delay it.
Beth Griggs joined APA Group in 2023 and was appointed Group Executive, Strategy & Corporate Development in October 2024.
Ms Griggs is a highly skilled energy executive with more 20 years’ experience across gas and electricity infrastructure, wholesale and retail markets, and is responsible for APA Group’s strategy, market analytics, corporate development and regulation and policy functions.
1. https://www.nsw.gov.au/media-releases/nsw-government-secures-two-year-extension-to-eraring-power-station
2. https://www.energy.gov.au/energy-and-climate-change-ministerial-council/working-groups/system-planning-working-group/ orderly-exit-management-framework-draft-exposure-bill-and-rule-june-2024
3. AEMO, Electricity Statement of Opportunities, August 2024, p48
As energy demand grows across Australia, utility providers face increasing pressure to ensure the reliability and safety of critical assets.
Battery chargers and stationary
VRLA batteries are essential for maintaining operations during power outages. The new Australian Standard AS4044:2024, effective from 15 November 2024, provides asset owners a clear framework for ensuring compliance and protecting these investments.
What you need to know
The updated standard introduces guidelines tailored for Australian environmental conditions, ensuring equipment longevity and reducing operational risks. Key features include:
• Compatibility with modern switch mode rectifiers and phase-controlled chargers
Limitations on neutral current to match or remain below phase active current
• Built-in battery charge current control
• Updated cable colour standards (black or blue for negative, red for positive)
Allowance for modern digital instrumentation
• Compliance with EMC standards
For asset owners using Intelepower Systems, Century Yuasa proudly confirms compliance with AS4044:2024, ensuring optimal performance, safety and reliability for your critical systems.
Why compliance matters
Battery ventilation is critical for maintaining DC Power Systems safely. Australian Standards such as AS3011.2 and AS2676.2 require that hydrogen (H₂) concentration in battery rooms or enclosures must remain below two per cent, well under the explosive threshold of four per cent.
A growing trend is to fit small plastic ventilation tubes into the valve covers of VRLA batteries to avoid the challenge of properly ventilating the battery cabinet or room.
Battery
Century Yuasa
However, this approach does not comply with the requirements of the standard.
Key non-compliance risks
Insufficient ventilation
Tubes often lack the required cross-sectional area to vent hydrogen effectively, especially when linked in series.
Formation of gas pockets
Downhill bends and condensation blockages in tubes create explosive hydrogen pockets.
Maintenance hazards
Tubes require meticulous upkeep to avoid blockages, increasing safety risks for maintenance personnel and operations.
Hydrogen release under fault conditions
Tubes are usually attached to the valve cover of the battery. Aged or stressed batteries may release hydrogen from other
parts of the casing, such as around post seals or via cracks in the lid seal. This gas bypasses the tubes and vents directly into the enclosure, increasing explosion risk without proper cabinet or room ventilation.
By adhering to the natural ventilation principles outlined in AS2676.2, Century Yuasa ensures that its Intelepower Systems and battery banks meet all safety requirements, eliminating risks associated with substandard practices.
For more than 30 years, Century Yuasa has delivered future-proof energy solutions across Australia and New Zealand. The team’s expertise in industrial power systems ensures utilities benefit from safe, reliable and compliant solutions. With nationwide service and a commitment to innovation, Century Yuasa is ready to help you meet AS4044:2024 and ventilation standards.
For more information, visit intelepower.com.au
Our team of Network Infrastructure specialists deliver innovative solutions for major telecommunications projects across our nation – helping to futureproof Australia’s fibre network so we all stay connected.
Western Power invests around $1B each year to safeguard its network against disaster. Images: Western Power
In the face of extreme heat, increased bushfire risk and severe storms, Western Power is fortifying its network for summer and into the future.
With a warming climate and increasing instances of extreme weather, often alternating in quick succession between severe storms, heatwaves and bushfires, the pressures on Western Power’s electricity network have never been greater.
Coupled with changing energy-use patterns, greater draw from residences due to a push towards electrification of appliances at a household level, and an overall growing peak electricity demand during hot weather, networks throughout the world are reaching a perfect storm of conditions that are driving a need for innovation.
Western Power has an important role to play when it comes to managing the network it has now, as well as planning the energy grid of the future.
For several years, the utility has invested about $1 billion annually in key maintenance activities and network upgrades to address safety, reliability and environmental risks – and these summer preparedness works have an emphasis on increasingly extreme weather conditions.
Western Power Executive Manager Asset Operations, Zane Christmas, said that as the risk of heatwaves and bushfires increases, the organisation has taken steps to ensure the network is as prepared as possible for severe weather.
“This includes finalising current bushfire mitigation work, ongoing maintenance programs and investing in network infrastructure upgrades such as insulator replacements, distribution transformer upgrades, managing trees and vegetation and washing and applying silicone to insulators via helicopter,” he said.
“We also work closely with the Department of Fire and Emergency Services and local governments to ensure we can access outage locations easily – particularly during high fire weather conditions – and restore power quickly, provided it is safe to do so.
“This is increasingly important in the metropolitan area in particular, as while this is predominantly an issue for the hills and the regions, many metropolitan residential areas have infrastructure which traverses areas of fire-prone bush and parkland, and we take our responsibility to minimise the chances of our machinery or infrastructure causing a bushfire extremely seriously.”
This targeted resilience work is paying off. In January and February 2024, the network recorded six of its ten highest demand days in history,
with multiple heatwaves and temperatures above 40 degrees putting massive pressure on the network.
Despite the huge growth in power demand, a comparison between two of the highest demand days – 26 December 2021 and 18 February 2024 – showed that in 2024 the utility experienced significantly fewer fuse overloads and no feeder trips, and therefore a greatly reduced number of outages.
But with an energy network that was built for one-way, generator-to-household supply and more predictable weather conditions, the race is now on to understand how Western Power can continue to facilitate the transition to renewable generation, while managing an ageing network.
Western Power Executive Manager Energy Transition & Sustainability, Matt Cheney, said that while the changing climate and increasingly extreme weather conditions pose challenges for the current network, Western Australia’s sun and wind resources will continue to be a key element of Western Power’s strategy as it moves towards net zero.
Washing and siliconing of power lines is a proven method of mitigating power reliability issues.
“In the South West Interconnected System (SWIS), 40 per cent of households now have rooftop solar, contributing more than 2GW to a system with a peak demand of 4.3GW – five times the capacity of the largest coalfired power station,” he said.
“Each month, about 3000 new rooftop solar systems and 500 batteries are added, with these systems supplying three-quarters of the state’s energy demand in September 2024 – setting a new record.”
Western Power’s distribution network is the platform for unlocking greater potential from customer distributed energy resources (DER), and it’s helping to address some of the big challenges of the energy transition.
As part of the State Government’s DER Roadmap, several actions are underway to refine policy, regulation, market mechanisms, technology, and organisational functionality – aimed at connecting and activating more customer-owned DER, such as solar panels, batteries, smart home appliances and electric vehicles (EVs), into the future.
The award-winning Project Symphony–a collaboration between Western Power, Synergy, AEMO, and Energy Policy WA – showed that engaging customers in a new energy market and aggregating
passive DER into a virtual power plant can help manage network peaks and troughs, reduce outage risks, and create additional value for customers.
Larger-scale community assets can also play a role. As part of Project Symphony a community battery was installed at Harrisdale, which was able to prove that storage systems could help smooth fluctuations that can lead to system instability, and thereby avoid customer outages. Battery storage and EVs are another key piece of the longterm puzzle, providing the ability to store and release energy at the right time, rather than having to prevent assets from feeding into the grid and essentially ‘losing’ the energy that was captured.
Western Power said that it knows energy storage is essential to getting the most from its generation capacity, which is why it’s working to install more community batteries.
According to Mr Christmas, another measure that will enable greater uptake of renewables while also building resilience on the network is undergrounding.
“Undergrounding enables us to get more network capacity than traditional poles and wires, which means more solar and EVs can be connected in residential communities while also keeping assets cooler in extreme temperatures and giving them greater protection in severe weather like high winds and thunderstorms,” he said.
“For rural and regional customers, greater adoption of stand-alone power systems is another way we’re embracing renewables and reducing the resilience challenges for customers currently serviced by long, remote feeder lines which are exposed to the elements, difficult to access and thus vulnerable to extended outages.
“There is no single way to manage the challenges faced by rapidly changing climate. Increasing the resilience of the existing Western Power network, enabling greater connection of residential, community, and large-scale renewable generation, and innovating our operations to become more future-focused all must work in cohesion for us to get the balance right for the community.”
Corrosion is a major threat to pipeline infrastructure, but a proactive approach can help extend asset life and reduce long-term costs.
As Australia’s pipeline networks age and extreme weather events become more frequent due to climate change, taking a proactive approach to corrosion management is more crucial than ever.
Corrosion accelerates the deterioration of pipeline systems, shortening their lifespan and necessitating expensive repairs. Several factors make pipelines more susceptible to corrosion including weather, temperature, soil type and water. Extreme weather events can increase the risk of asset failure in already corroded pipelines, leading to service disruptions, flooding, road closures and significant costs. By incorporating corrosion resilience into both new pipelines and rehabilitation projects, asset owners can better manage pipeline corrosion and extend the lifespan of infrastructure.
One beneficial tool for mitigating pipeline corrosion is the installation of an appropriate spacer system.
Spacers ensure proper pipe alignment and provide a physical barrier between the pipe and external surfaces, reducing contact with moisture, debris and corrosive elements. Spacers also promote airflow and drainage, reducing the likelihood of corrosion-inducing conditions like trapped water or stagnant moisture.
When selecting a spacer system, it’s important to consider potential materials and their properties. Spacers made from metals, such as steel, are more vulnerable to deterioration, especially in harsh environments.
Kwik-ZIP General Manager, Paul Jefferys, said, “In regions with high salt levels, tropical conditions, or acid sulphate soils, pipelines are particularly susceptible to rapid corrosion.
“For example, in areas with acid sulphate soils, metallic spacers can suffer significant corrosion upon contact with these soils.”
Mr Jefferys said that in these conditions the corrosion can be transferred to via metallic spacer to the steel pipeline itself.
Non-metallic spacers, made from high-grade, inert materials, are ideal for preventing the transfer of corrosion.
Kwik-ZIP’s range of spacers are specifically designed to meet the challenges posed by the Australia’s unique climate and environmental conditions.
Engineered in Australia, Kwik-ZIP spacers are manufactured from an engineered thermoplastic blend –a high-grade thermoplastic that is flexible, extremely tough and has a low coefficient of friction.
“Kwik-ZIP’s highly resistant spacers are particularly suited to harsh environments where spacers made from other materials such as metal do not hold up as well,” Mr Jefferys said.
Even when in contact with harsh environments for long periods of time, Kwik-ZIP spacers remain highly resistant to corrosion, offering the ideal solution for asset owners seeking to improve the resilience of their networks.
Kwik-ZIP spacers are suitable for use in both pressure and non-pressure pipelines, and can be used for a wide range of pipe materials, including steel, ductile iron, PVC and PE. The HDXT Series, for example, is designed for medium- to heavy-weight pipes and is suitable for both grouted and un-grouted installations.
Kwik-ZIP’s HD, HDX and HDXT series spacers have been successfully appraised by the Water Services Association of Australia (WSAA) against the WSA PS-324 Product Specification, which prescribes casings spacer requirements for correct protection of carrier pipes when installed inside casings.
Kwik-ZIP Products are also approved for use within many utilities’ infrastructure, including Melbourne Retail Water Association, South-East Queensland’s Infrastructure and Materials (IPAM) list, Sydney Water and the Water Corporation. All products are certified by the Australian Water Quality Centre (AWQC) for use in contact with drinking water.
Kwik-ZIP maintains a focus on price effectiveness, simplicity and rapid on-site assembly to ensure that its systems deliver significant cost, time and operational advantages to all customers.
For more information, visit kwikzip.com
When asset failure can have serious impacts on operations, the local environment and public health, it is vital to increase asset protection and reduce risk wherever possible.
With extreme weather events increasing in frequency in many regions of Australia, utilities need to ensure that their assets are well protected, or risk facing costly repairs and severe impacts to local communities and environments.
According to Enviroline Managing Director, Brent Wiggins, one of the biggest impacts that extreme weather events have on utility assets is the movement of the ground, which can disturb underground networks.
“When the wet weather comes, we can have a lot of water infiltration into our sewer systems, which overloads the treatment plants and can lead to overflows,” he said.
Mr Wiggins said that the age of the infrastructure can greatly impact the risks associated with extreme weather.
“A lot of our infrastructure is getting older now. There was a lot of earthenware and clay in the early days and as the ground dries out and then becomes wet again, this can cause a lot of strain and movement.”
When utility assets fail, one of the biggest threats posed to the environment is when large spills or overflows occur in the sewer network.
“This generally happens because of heavy rain events or in extreme weather conditions where there’s a lot of water infiltration. That’s when fresh water enters the sewer system, eventually overloading and resulting in an overflow event.”
Keeping assets safe Utilities are increasingly relying on preventative maintenance to ensure that assets are always in the best possible condition, reducing the likelihood of failures occurring and catching failures before they become serious issues.
Mr Wiggins said that these kinds of programs generally include regular cleaning and inspection of underground assets.
“It’s very critical to partner up with a supplier that can provide the right equipment and advice for the network that you’re dealing with.
“You need to have a supplier that can maintain and back up that equipment and keep it in good working order so the maintenance program can be ran successfully.”
Mr Wiggins said that it’s important to work with an Australian supplier that can provide high-quality products specifically designed for Australian conditions.
Aussie-made Enviroline has been a local supplier of a wide range of water jetters, inspection cameras, flow plug tools and accessories to plumbers, councils, water authorities and civil contractors across Australia for more than five decades.
“I don’t think there’s anyone in this space that spends quite as much on research and development as we do. We have an engineering team that consists of four full-time engineers, and we’re always working to develop new products to keep at the cutting edge of the industry and improve our existing offerings,” Mr Wiggins said.
“Our products are all Australian-made to a high standard of quality control, so you know that if you’re buying equipment from Enviroline, it’s going to be a high-quality product that's going to work for years.
“We’ve got a plan for massive growth over the next few years, which will involve multiple locations. Moving forward, we’re going to be in an even better position to provide and support our equipment Australia-wide.”
For more information, visit enviroline.com.au Sewer
Fleet Solutions: Jetting Trucks, Vans, Trailers.
Whether you need a trailer fitted out for serious stormwater work, or a whole fleet of customised trucks for a state-wide Water Authority, Enviroline Group has the range, knowledge and services to deliver a solution tailored just for you.
From SA Water to Singleton Council to the Shire of Kojonup, we work with local, state and federal government authorities, water authorities and major civil contractors across Australia to provide expert advice, tailored commercial equipment, servicing, repairs, parts and accessories.
Regular inspections are vital for water infrastructure assets – but standard testing techniques often require this essential infrastructure to be taken offline.
Across Australia, water and wastewater assets are often decades old. Many are nearing the end of their service life and owners and operators are seeking ways to ascertain their structural integrity and remaining service life (RSL). The need to pay close attention to inspection, ongoing maintenance and replacement planning is pivotal to ensuring the continued safety of an asset for both staff and the community, and the return on investment (ROI) of the asset to the owner.
External forces such as growing populations and extreme weather events are adding further strain on essential water and wastewater infrastructure.
Asset owners, managers and engineers must balance planning for future growth with the need to keep infrastructure functioning and maximise its lifespan. They must also plan for minimal service interruptions due to inspections, maintenance, or equipment replacement.
Providing superior corrosion resistance at lower cost than stainless steel, glassreinforced plastic (GRP) composites are already widely used in potable water and wastewater systems for pipes, storage tanks, scrubbers, ducting, covers and other equipment.
RPC Technologies is one of the most experienced manufacturers of GRP assets in Australia and Southeast Asia, and it also has the exclusive licence to a worldleading condition assessment technology, UltraAnalytix®.
Most asset management programs require periodic inspection and evaluation of the equipment’s RSL. However, while there are established objective methods for determining RSL of equipment made from steel, there are no consensus standards that apply to inspecting GRP.
With ducting and piping, traditional techniques that rely on visual inspection – often requiring the asset to taken offline – are impractical, expensive, time-consuming and often provide limited insight. As a result, inspection delays occur and subsequently a failure may happen without warning. RPC’s condition assessment using the UltraAnalytix® NDT system is a proven, non-intrusive and non-destructive evaluation method that provides objective data to evaluate the current condition and RSL of GRP equipment – without taking the asset offline. As well as pipes and tanks, composites are used in reverse osmosis (RO) pressure vessels for desalination facilities that supply potable water.
The technology is still used today meaning there are potentially tens of thousands of RO units worldwide that may be nearing the end of their service life. However, while design and construction codes cover how RO vessels must be manufactured, they provide no guidance for determining ongoing fitness-for-service.
Collaborative research between RPC and UTComp has demonstrated that UltraAnalytix® technology can provide a fast, reliable and cost-effective method for determining the fitness-for-service of RO vessels.
Regular condition assessment and inspection using the UltraAnalytix® system can save the water sector significant costs by reducing losses of valuable assets through leaks and other failures, improving safety and reliability, and increasing operational uptime and lowering capital replacement costs.
UltraAnalytix® non-destructive testing is a fast, accurate, safe and cost-effective way for asset owners to assess the RSL of their GRP assets while avoiding unnecessary downtime and replacement costs.
For more information, visit rpctechnologies.com
Hydrogen sulphide wreaks havoc in sewer assets, leading to widespread disruptions and costly corrosion damage, but a team of Queensland researchers may have a new solution.
In Australia, sewer systems have an estimated asset value of $100 billion, representing 70 per cent of the total wastewater services infrastructure.
Hydrogen sulphide-induced corrosion can reduce the service life of sewerage infrastructure assets to just 20 per cent of their designed lifespan. Meanwhile, sewer odour nuisance accounts for over 90 per cent of community complaints.
Dr Jiuling Li, research fellow at The University of Queensland’s (UQ) Australian Centre for Water and Environmental Biotechnology (ACWEB), set out with his team to devise a system capable of better maintaining sulphide levels, thereby reducing odour complaints and costly corrosion issues.
This led to the development of a new real-time control and chemical dosing technology, which has now been recognised worldwide and was awarded a Silver Project Innovation Award from the International Water Association (IWA), for successfully and innovatively tackling odour and corrosion in sewers.
Where it all began
Equipped with a bachelor’s degree in Automation from China’s Harbin Institute of Technology, Dr Li first dipped his toes into the world of water monitoring when he completed a PhD at UQ in 2021.
“My research mainly centres around digital water systems,” Dr Li said.
“More specifically, it includes developing tools like model predictive control, real-time control systems, IoT sensor networks and high-performance computing. These innovations help optimise the operational maintenance of sewer systems and wastewater treatment plants, as well as promoting more sustainable water management practices.”
Dr Li explained that hydrogen sulphide is produced by the sulphate reducing bacteria found in sewers.
“This gas is volatile and can escape from the wastewater network into the sewer air, creating unpleasant odours. Additionally, when the sulphide in the sewer air interacts with the sewer waters, it can convert to sulphuric acid, leading to the corrosion of the sewer infrastructure,” he said.
“Sulphide is a major cause of sewer corrosion, resulting in the premature degradation of sewer assets. Replacing or repairing damage to sewers costs billions of dollars per year.
“Moreover, the frequent inspections and maintenance that is required regularly exposes workers to hazardous environments and increases the water bills of residents.”
According to Dr Li, the odour of sulphide gas can also cause significant disruption to people living and working in the area and can even result in health risks due to its toxicity.
To mitigate these challenges, water utilities often use methods like constant, flow-paced and profile dosing for controlling hydrogen sulphide levels.
“But these approaches rely on fixed guidelines and they don't account for fluctuations in the sewer systems, leading to ineffective control and resulting large amounts of chemicals wasted,” Dr Li said.
According to Dr Li, with the predictive modelling sulphate control technology, network managers can use historical data from their sewer operations to predict the changes in sewerage flow and sulphide levels across the entire sewer network ahead of time.
“The technology employs an efficient optimisation algorithm to determine the ideal amount of chemicals to dose in real time. This ensures that the right amount of chemicals can be delivered to the sulphide hotspots whenever the pump runs, providing continuous control with minimum chemical costs.
“The technology is a result of a long-standing partnership between UQ and our industry partners, supported by more than 20 years of collaboration with more than 25 projects funded by the Australian Research Council and the government.
“In 2013 our team developed the first generation of this control methodology for chemicals, which was limited. With advances in digital technology, we developed the second-generation system which digitalised the whole chemical dosing control process.
“This work was supported by the Australian Research Council and our industry partners, including Urban Utilities Brisbane, Gold Coast City Council and SA Water.”
The IWA holds the Project Innovation Awards biennially at its World Water Congress & Exhibition, to recognise and promote excellence and innovation in water management, research and technology.
At the 2024 congress, Dr Li and his team were celebrated for their efforts and awarded silver in the ‘Smart Systems and the Digital Water Economy’ category.
“What sets us apart is our commitment to knowledge transfer. Every aspect of our work is designed with the ultimate goal of real-world application, all held to a high scientific standard.
“Our multidisciplinary approach has brought together academic researchers and sewer operators to develop an innovative digital solution for sewer maintenance,” Dr Li said.
“The term ‘digital water’ is an emerging concept, and most efforts remain at the research or lab stage. We are the first team globally to have successful implemented an advanced control theory in a real, large-scale sewer network for chemical dosing.
“By focusing on practicality and user needs from the start, we have been able to transform innovative ideas into effective and real-world applications.”
The control system is currently being tested in two sewer networks in Queensland – one on the Gold Coast and one in Brisbane’s western suburbs.
“By improving dosing effectiveness and efficiency, we estimate the technology can reduce chemical use by around 40 per cent in most dry weather scenarios,” Dr Li said.
Dr Li said that the technology presented significant challenges due to its multidisciplinary nature.
“Unlike most control projects that focus solely on sewerage flow, we have to account for the complex chemical and biological processes occurring within the whole sewer catchment.
“The real-time evaluation requires high-resolution predictions of dynamic changes across a large-scale network at the millisecond level. This results in not only a demanding task in water engineering, but also a complex problem in mathematics and automation.
“With the support from our partners, we overcame these challenges by assembling a diverse team of engineers, microbiologists, mathematical modelers, computer scientists and sewer operators and I think our team’s perseverance has been key to our success.”
Dr Li said that this technology will greatly reduce odour complaints in residential areas and provide effective tools for ongoing sewer maintenance.
“It helps ensure the integrity of the sewer system, preventing overflows and even flooding, which reduces the risk of
pollution and the spread of pestilence.
“Ultimately it creates a safer and more pleasant environment for residents.”
Dr Li said that the technology is expected to extend the service life of sewer infrastructure and reduce chemical consumption.
“It will also decrease the need for new construction, and the less sewer infrastructure being replaced means less solid waste production. It also lowers the energy cost associated with the pump and reduces the carbon footprint of maintenance activities. All of this contributes to net zero goals.
“Although the hydrogen sulphide itself is not greenhouse gas, the sewer system generates significant amounts of methane, a potent contributor to global warming. Chemical dosing is also the key approach for methane mitigation, which is another major focus of our ongoing research.”
Dr Li said that it’s important for utility managers to recognise that the hydraulic retention time and the sulphide levels across the sewer network can vary significantly from hour to hour, and day to day.
“Additionally, the optimal amount of chemical dosing can be quite different between pump cycles,” he said.
According to Dr Li, current sensor technology is still susceptible to issues like humidity and sulphide exposure, so implementing a smart monitoring system and backup plans for anomalies or sensor failures is crucial for optimal sewer operation and maintenance.
The next phase
While the technology has already shown great results, Dr Li said that this is just the beginning.
“We still have some theoretical designs that haven’t yet been implemented in practice, and we believe this could further enhance the control performance, so we are actively seeking opportunities to test them,” he said.
“Meanwhile, we plan to automate technologies designed to ensure that operators and engineers without specific expertise can easily use them. Our goal is to commercialise the technology, making it accessible to a broad range of users.”
Hydrogen
Image: DimaBerlin/shutterstock.com
Dr Li said that the technology also holds great potential for broader applications across not only the sewer system, but across the water supply and wastewater sectors, supporting a more integrated approach to water management.
“This will be essential for developing sustainable cities and ensuring the longterm effectiveness of water services,” he said.
“Digital management of sewer networks offers benefits far beyond the sewer system itself. It can improve the operation of clean water systems and
wastewater treatment plants as well.
“All of these systems are managed independently. The future of digital management should focus on creating integrated solutions that consider broader, collaborative management.
“My hope is that digital water technologies, whether lead by the industry or a research institution, will result in practical, wide-ranging and long-lasting technologies rather than individual solutions, so that these technologies can contribute to environmental protection and public health across the water industry.”
> Still the market leaders in laser guided microtunnelling
> Bore diameters from 325mm up to 2800mm
> Specialists in ‘free bore’, sleeve boring and pipe jacking in all sizes
> Used for gravity sewers, water mains, storm water, gas and electrical conduits.
As extreme weather continues to threaten many parts of Australia, utilities are seeking to improve the lifespan of their assets to keep customers connected to vital services.
The efficiency and durability of pipe joining methods are crucial for the long-term success of any project, and utilities are looking to new technologies to improve the longevity of their assets.
Electrofusion is a welding method typically used to join high and mediumdensity polyethylene piping. It uses prefabricated fittings incorporating an electrical heating coil that melts the polyethylene of both the fitting and the pipe, causing them to fuse together when the material cools.
One of the most significant advantages of fusion welding is its ability to create reliable, leak-free joints. But ProPipe Managing Director, Andrew Day, said that achieving this requires more than just the fusion process itself – it depends on proper tooling, adequate training and high-quality HDPE fittings.
“Electrofusion produces highly durable, corrosion-immune joints, extending the lifespan of pipelines,” Mr Day said.
The fusion process creates a seamless connection, eliminating weak points where leaks could develop. When performed using the correct tools, trained personnel and certified HDPE fittings, the process achieves the highest standard of reliability.
“Electrofusion minimises maintenance needs by creating leakproof connections, even in challenging environments, but only when all components – tools, training and fittings –work together,” Mr Day said. Fusion welds are as strong as the
Electrofusion creates leak-proof connections, but only when all components work together. Image: rdonar/shutterstock.com
pipe material itself, offering exceptional resistance to environmental stress, pressure fluctuations and mechanical impacts. This strength, combined with accurate tooling, skilled operators and high-quality fittings, ensures the longevity of the pipe system and reduces the need for costly repairs.
“This method enhances pipeline resilience against extreme weather and operational stresses, provided the process is carried out correctly and with quality materials,” Mr Day said.
Unlike metal pipes, thermoplastic pipes joined by fusion welding are immune to corrosion, making them ideal for harsh environments such as water treatment facilities and underground installations.
Additionally, fusion welding requires minimal use of hazardous chemicals, solvents or adhesives, which contributes to a safer job site.
Mr Day said that investing in the right tooling, comprehensive training, and high-quality HDPE fittings is essential to harness the full benefits of fusion welding.
“When all these elements are aligned, the result is a pipeline system with dependable, leak-free joints that stand the test of time,” he said.
As with all procurement, it’s important to find a trusted provider that can deliver high-quality products that are designed with excellence and innovation in mind.
Since 2013, the team at ProPipe Dynamics has been committed to not only meeting, but exceed industry standards, ensuring optimal performance, reliability and efficiency.
Mr Day explained that because its products are manufactured in Australia, ProPipe offers ongoing support and faster turnarounds for custom orders.
“With knowledge of Australian conditions, ProPipe can design and manufacture bespoke tools to meet unique project requirements or customer preferences.”
Recently rebranded from Caldertech Australia, ProPipe Dynamics now includes Plastitalia products alongside its own offerings, improving the breadth and versatility of its product range.
“The rebranding reflects a renewed focus on serving Australian customers with localised manufacturing and comprehensive support.
“ProPipe aims to better support HDPE projects with a seamless supply of pipe, fittings and tooling, while also addressing the common issue of delayed orders.”
Mr Day said that Plastitalia’s highquality electrofusion fittings enhance pipeline integrity by creating strong, leak-resistant joints.
“Combined with ProPipe’s tooling, they offer a reliable, end-to-end solution for utility projects, perfect for harsh environments and critical infrastructure.”
For more information, visit propipe.com.au
When five council water authorities merged to form Urban Utilities, they brought with them varying legacy security systems. To move forward, it needed a unified, digital solution.
When organisations are merged or acquired there are typically legacy systems that must be carried over during the transition period to ensure that the merger continues smoothly. These include IT systems, assets, processes and in many cases both electronic and physical security.
When the water services of Brisbane, Ipswich, Lockyer Valley, Scenic Rim and Somerset councils were merged to form Urban Utilities, each of the five water authorities had varying legacy mechanical key systems that were used across their networks.
Urban Utilities Security Operations Coordinator, David Badke, said, “After the merger, these systems continued to be utilised for a period of time to allow a solution to be identified that met the technology requirements, reliability standards and unique access profile hierarchies, and could cater for a moving work force spread over 14,300km².”
With mechanical key systems, it is extremely difficult to keep track of
where keys are or maintain an audit trail of who has used what key and when. These issues mean making securitybased decisions are an educated guess at best. The critical nature of any utility company means locks and padlocks are required to secure assets with varying security levels which are often spread out across vast distances and sometimes even in different states.
Urban Utilities recognised that the solution would have to come in the form of an electro-mechanical key system, capable of overcoming a number of risks and costs, including:
The unfeasible cost of hard-wired access control across each site
• The inherent limitations of a mechanical master key system from an audit trail perspective
• The limitations of a mechanical master key system from a key management point of view (contractors or staff picking up and dropping off keys, key registrations, offline database management, etc.)
Urban Utilities needed to overcome these challenges by designing and implementing an enterprise security keying solution.
The company undertook a diligent assessment of the market, including trialling several electro-mechanical master key systems. Ultimately, Urban Utilities decided that the EKA Cyberlock was the right master key system for its assets.
EKA CyberLock was chosen because of its ability to reprogram keys on demand with customised individual user access profiles, which allows a single key to be shared between multiple users.
The CyberLock system is also capable of recording secure audit trail data to inform security management.
“Key sharing is simple because CyberKeys can be updated by any user using the CyberLink mobile app and the CyberKey’s Bluetooth capabilities to communicate to the database,”
Mr Badke said.
“The update process is quick and simple, and as it is portable to the user’s location, it has increased staff productivity.”
Urban Utilities was introduced the technology when its partner, John Barnes & Co, was conducting product training on a new product suite by EKA CyberLock.
Retired Locksmith Manager at John Barnes & Co, John Neroni, recalled this training session by the EKA team.
“One particular solution that stood out to us was the CyberKey Blue2 with the newly developed CyberAudit Link mobile app,” Mr Neroni said.
“This development was a game changer. Keys could now be updated anywhere via the app without the key holder visiting a set location which offered potential clients massive productivity savings. Needless to say, we were blown away by it. The next day, I contacted David at Urban Utilities and requested a meeting to explain the CyberKey solution.”
After becoming interested in the system, Urban Utilities decided to trial EKA CyberLock in a real-world scenario by installing several Carbine C45Marine grade padlocks fitted with IP68 rated electronic CyberLock cylinders.
The system was to be administered in the cloud on a demonstration CyberAudit Web server, which, if later adopted, could be simply migrated to a production server.
Part of the trial involved using the CyberKeys how a typical user would, by:
1. Recharging the CyberKeys in their cars
2. Leaving CyberKeys on the dashboard in the heat
3. Activating a Bluetooth CyberKey with the CyberAudit Link mobile app when in mobile reception and visit multiple sites where there is minimal or no mobile reception and see if the CyberKey would open the Carbine padlocks
4. Unlocking access points, leaving them open, and verifying from the CyberAudit Web management software what detailed audit trail and reporting would be available to address these types of safety risks
During the trial the company also made use of over the phone trouble shooting with EKA CyberLock support staff, which resolved more than 95 per cent of all issues in the field.
“The trial was a success,” Mr Badke said.
“The next steps were determining the number of locks, CyberKeys and other CyberLock hardware or communicators we required to make our staff and contractors’ access as seamless as possible."
Satisfied with its choice, Urban Utilities proceeded to roll out more than 500 locks fitted with EKA CyberLock IP68 electronic cylinders and issued over 300 CyberKeys across its water networks.
“As part of our rollout plan, EKA CyberLock delivered a comprehensive training package to my team,” Mr Badke said.
“This included detailed ‘how to’ videos and documentation that catered for all types of users, from office staff to technicians and contractors.”
Now, Urban Utilities’ CyberLocks average 2,300 recorded opens per month, or 75 opens a day.
Since the installation, there have been zero CyberLock cylinders failed in the field, with only between five and ten locks found to have function issues which were detected before deployment.
“With any IT or physical system that is implemented, you do expect a very small number of hiccups or failures. We are quite pleased that EKA CyberLock has stood up well to these challenging environments the locks are installed in,” Mr Badke said.
The installation of EKA CyberLock has aided Urban Utilities in modernising its security and provided the ability to secure water assets in an efficient way.
As the water industry digitises, utilities must be aware that the advantages of these technologies are accompanied by new vulnerabilities.
The increased connectivity of critical operations presents a significant security risk, as any unauthorised access could result in potentially disastrous disruptions to services.
Utilities that seek to gain the full benefits of emerging digital technologies will need to invest in cybersecurity devices and services to minimise the associated risks, keeping operations and customers safe.
Digital vulnerabilities
Improper maintenance of components, such as failing to update systems with the latest security patches or allowing devices to operate beyond their expected service life, can leave an operational system highly vulnerable to attack.
If these devices are compromised, they could provide adversaries with remote access to operational systems or IT network.
Malicious attackers may then attempt to steal sensitive data, either to sell, ransom or be used to move laterally within a network to access other, more sensitive systems.
Cyber-attackers can also directly ransom a facility’s operations, by preventing access and disrupting key systems until their demands are met.
Built-in security
VEGA, a global manufacturer of sensors for measuring level, point level and pressure as well as devices to support software for integration, has delivered what it believes to be the world’s first level sensor with built-in cybersecurity features.
This development comes as VEGA recognises the increasing threat of cybercrime in the water industry and is taking action to ensure that utilities can better protect their vital services.
The VEGAPULS 6X radar sensor has been developed with cyber protection as an integral component. Developed in compliance with Industrial Cyber Security Standard IEC 62443-4-2, the VEGAPULS meets the highest standards implemented in the sector.
VEGA Grieshaber KG Team Lead of Project Management, Florian Burgert, was involved in the conception of the universal level sensor from the very beginning.
“Being able to use secure measurement data at all times is now one of the most important requirements of our customers,” Mr Burgert said.“We hear this from customers in almost every industrial sector.”
To achieve the best possible security, not only does the production system as a whole have to be secure, but all the individual components as well. Everything must comply with the standards. Especially when it comes to cyber security, plant operators want equipment they can depend on in order to stay one step ahead of the latest threats.
VEGA said that it doesn’t want to rest on its laurels. Having delivered a groundbreaking tool with the VEGAPULS, the company now intends to develop future products with cybersecurity front of mind. Protective measures will be consistently expanded to create a reliable basis for secure plant operation going forward.
For more information, visit vega.com
Touch down with VEGA’s comprehensive range of accurate and reliable pressure measurement sensors for all applications.
PROCESS, HYDROSTATIC AND DIFFERENTIAL PRESSURE.
When Central Highlands Regional Council set out on a digital metering journey to tackle water waste, careful planning was needed to get 100 per cent coverage from every meter.
In early 2024, Central Highlands Regional Council (CHRC) partnered with Taggle to pilot digital water meters. This Stage 1 trial was designed to evaluate the technology, demonstrate its benefits, build a solid business case, integrate the data into Council’s workflow and resolve potential challenges before scaling up.
Ensuring complete data collection from every property is crucial for effective demand management and accurately quantifying non-revenue water. However, reaching 100 per cent connectivity can be a challenge due meters being in tough radio environments and the diversity of types and sizes, so CHRC needed to assess Taggle’s technology and ensure that every meter can be reliably connected.
Queensland’s Central Highlands region is home to approximately 30,000 residents spread across 13 communities. Capella was selected as the site for this pilot program, which includes 514 meters.
Taggle Network Operations Manager, George Zisis, said that meticulous planning was the key to achieving 100 per cent connectivity.
“For every meter rollout we take the time up front to get the network right. This ensures a smooth process with minimal surprises or challenges during installation,” he said.
The team used CloudRF, an advanced radio frequency modelling tool, to identify optimal locations for network receivers. Out of six potential sites, two were chosen to provide the best coverage. By overlaying tag locations and simulating signal strength, the team
confirmed that 100 per cent coverage was achievable.
However, theoretical models can only go so far. Field tests were conducted to validate the plan and ensure the receivers could be installed without unexpected issues.
After installing the receivers, another round of on-the-ground testing was conducted prior to the meter installation. Taggle performed connectivity checks with survey tags and specialised equipment. While the overall results were promising, the field tests revealed common but manageable challenges.
Several of the water meters were located under dense foliage, which means that when it rains the wet foliage can block the signal from getting out – particularly for those on the fringe of coverage areas.
“To address this, we can install an add on tag that we elevate above the foliage or a high-power tag, which will improve the connectivity,” Mr Zisis said.
Taggle also found one meter beneath a steel drum surrounded by an electric fence, while this is sometimes done to protect the plumbing from cattle is also posed a safety risk for installation teams. Another meter was buried in a deep concrete pit, and one was covered in dirt. Identifying these issues ahead of time allowed the Council to notify residents and prepare contractors, avoiding delays.
Despite these obstacles, the Capella pilot achieved 100 per cent network coverage, with all 514 meters transmitting hourly data reliably.
Taggle’s rigorous planning and pre-installation testing were pivotal to the project’s success.
This enabled CHRC to accurately calculate the town’s water usage and detect leaks rapidly.
Since the installation in May 2024, a number of properties have been identified as having potential internal leaks and approximately 50 residents have signed up to the customer portal. Council is contacting residents with the largest leaks first.
This real-time data improves water management and enhances customer service by enabling quick resolution of issues.
Taggle’s rigorous planning and pre-installation testing were pivotal to the project’s success. By addressing connectivity challenges early and accommodating unique site conditions, CHRC transitioned to digital water metering with minimal disruption, unlocking significant operational, financial and water security benefits.
Meters are the backbone for many utility operations, which is why it’s critical that these assets are properly secured.
The Exact & Track system is designed to give utility providers unmatched serial number management.
Image: Harcor
When compliance issues arise, being able to verify that a seal number is unique to your company can make all the difference. For utility companies managing sensitive infrastructure, this traceability deters unauthorised access and offers reliable documentation that the security seal applied to a meter is one-of-a-kind and specific to your organisation.
Harcor said that it is Australia’s first dedicated security seal supplier, so it understands the vital role of traceable meter security seals for exposing tampering and ensuring regulatory compliance in metering systems. To tackle this challenge, Harcor
designed its exclusive Exact & Track system to give utility providers peace of mind with unmatched serial number management.
This custom serial management solution was developed in conjunction with Exact Software. The Exact Software management system conforms to NEN-EN-ISO 9001:2015. The NEN-EN-ISO 9001:2015 certificate specifically includes custom solutions in the scope.
When you purchase meter security seals from Harcor, you’re gaining more than just a tamper-evident seal – you’re securing a traceable system that aligns with industry best practices.
With more than 54 years in the business, Harcor is one of Australia’s most established security seal suppliers. The team’s expertise, combined with the Exact & Track system, confirms that each seal number is both unique and traceable.
When choosing a security seal provider for your utility meters, consider not just the seal, but the quality and reliability of its serial numbering system. For utility organisations looking to secure their metering systems, Harcor offers a comprehensive solution that combines robust security seals with advanced tracking for unparalleled accountability and peace of mind.
By leveraging AI, utilities can enhance efficiency, optimise resource allocation and adopt proactive maintenance strategies. Image: metamorworks/shutterstock.com
Faced with increased flooding and droughts, population growth and ageing infrastructure, the water sector needs a smart solution to help tackle these challenges.
Climate change and rapid urbanisation are placing more demand on Australia’s water network than ever before – and on top of this growing demand, utilities are also racing against time to repair and maintain existing assets.
To meet these challenges, it’s critical that water authorities can allocate their resources efficiently, but this requires highly accurate data and forecasting.
Artificial intelligence (AI) and machine learning (ML) can draw from historical data, weather conditions, population growth and other relevant factors to accurately predict operational needs and help utilities to adopt proactive maintenance strategies.
This information is also invaluable in demand forecasting and can help the sector ensure that ample water is available at the right time and place.
Highly accurate hyperlocal weather forecasts are changing how councils can control localised flooding, how utilities manage remote raw water sources and how pollution events are reduced – and for years Metasphere has been tailoring smart network management solutions to the unique needs of the water sector.
Metasphere’s mantra is “no spills” and the company believes shifting from a reactive “monitor and alarm” approach to proactive “predict and prevent” operational mentality, is the key to eliminating spills altogether.
AI and ML technology has already proven its worth in energy optimisation for water utilities. By analysing energy consumption and system performance data, utilities can identify opportunities for improvement. ML algorithms can optimise pumping schedules, adjust treatment processes based on real-time conditions and predict energy demand. This allows utilities to operate at optimal efficiency, reducing costs and minimising environmental impact.
A significant challenge for utilities is transitioning from the management of isolated assets to automated and integrated networks. Taking a holistic approach by considering catchment areas, weather data and utility network information allows for better prediction of impacts on natural watercourses and coastlines. In addition, predicting water quality, including soil moisture data and information on agricultural use – such as fertiliser by crop type and proximity to watercourses – is a valuable addition to catchment-based management.
Leveraging the full potential Integrating data from various sources, such as traditional, IoT and citizen science data, is essential but presents challenges.
To overcome these challenges and fully leverage the potential of AI and ML, it’s critical that utilities can tap into the knowledge of subject matter experts who can offer the right advice.
Specialising in wastewater management, Metasphere provides smart network management solutions to the global utility industry.
The company’s intelligent solutions offer full visibility and forecasting for remote assets and systems, reducing telemetry ownership costs.
In 2023, Metasphere was acquired by Grundfos, a global leader in advanced pump solutions and water technologies, and together the two companies are committed to helping utilities enhance efficiency, reduce costs, optimise networks and protect the environment while delivering sustainable water services to the communities they serve.
For more information, visit metasphere.co.uk
Metasphere helps customers prevent leaks and spills for a cleaner, greener world
Our intelligent, innovative all-in-one telemetry solutions provide full network visibility, performance and forecasting.
Reducing telemetry ownership cost for customers to manage time-critical remote assets and systems.
Digital IDs can help utilities improve security measures and set new standards for operational efficiency. Image: Tint Media/shutterstock.com
When workforces are spread across vast distances, onboarding new personnel poses a risk to security and operational efficiency – so utilities are turning to digital solutions.
Adispersed workforce makes onboarding new team members particularly cumbersome, as it frequently requires field workers to be taken off-site, resulting in wasted time and resources. To tackle these challenges, one of Australia’s largest energy providers has embraced the digital transformation.
Power partners
Digital ID systems can ensure that all employees have an ID readily available, regardless of their location. Even in remote areas without internet access, employees can access their secure identification, ensuring they are always equipped with the necessary access and credentials.
Unicard and HID have worked hand in hand for many years to deliver advanced digital ID solutions, and this partnership drives them to improve both innovation and security, providing reliable technology for their clients.
Recently, the dynamic duo successfully deployed more than 10,000 digital IDs for a major energy utility, a remarkable achievement that showcases the power of Unicard’s cutting-edge solutions in transforming identity management.
This essential service provider powers 95 per cent of New South Wales and parts of southern Queensland, and with so many Australians relying on the utility there was no room for error when it came to security.
Dynamic digital identity technology offered a promising answer to these challenges, so the utility sought assistance from Unicard’s IdentityONE, CaptureME, and IDmobile solutions. identityONE streamlines the creation, management, and issuance of IDs. This tool ensures security and durability while significantly reducing production time and errors. As a cloud-based solution, identityONE allows office workers to access necessary data whether they are in the office, at home, or on-site.
CaptureME makes the onboarding and verification process straightforward for both new and existing employees. It enables employees to submit their details, capture and upload ID images, and provide verification documents remotely from any device. This eliminates the need for trips to designated administration stations, saving valuable time and effort. IDmobile ensures that all employees have a digital ID readily available, regardless of their location. Even in remote areas without internet, employees always have access to their secure IDs.
Secure, sustainable, efficient
In an industry where security is paramount, Unicards’ client faced the challenge of enhancing personnel, cyber, and physical security while ensuring efficient operations.
By transitioning to digital IDs, the company was able to significantly improved security measures, streamline processes and set new standards for operational efficiency.
Deploying digital IDs with integrated HID mobile credentials has simplified the issuance of ‘Authorised Service Providers’ cards.
Users can easily download these secure digital credentials to mobile devices, enhancing security, offering instant updates, eliminating the wait for physical cards, and ensuring continuous preparedness with or without phone data coverage.
The adoption of digital IDs has also contributed to sustainability by reducing plastic waste. Digital IDs can be created, reused, replaces or cancelled without needing new plastic cards, allowing organisations to better align with their environmental goals.
By using Unicard’s digital ID solutions, utilities not only boost their security and efficiency but also contribute to sustainability. The adoption of Unicard's security solutions marks a significant move in the sector’s digital transformation, setting an example for others to follow.
For more information, visit identityone.com/utilities-energy
Hey team, I hope you’re all doing well! I wanted to share some exciting news about our onboarding process. We can now send digital IDs to new staff instantly, even when they can’t make it to the office. This means we can onboard new remote workers in real time, providing them with their digital IDs before their first day. It’s a great way to enhance both efficiency and security with our streamlined process.
Intellihub General Manager of Smart Water, Inge Diamond. Image: Intellihub
As capital programs accelerate across the water sector, utilities are being reminded about the value of data-driven insights to help manage costs.
In 2025–26 its estimated that annual capital expenditure across Australia’s largest water utilities will hit more than $12 billion a year – double what it was in 2022.
According to the Water Services Association of Australia (WSAA), this is a trend that is only expected to continue over the coming decade as property developments in growth areas come online and old assets are replaced.
While the water sector has known that this uplift in expenditure was coming, the homes and businesses that will fund it through water charges may not be as prepared.
Data is key
According to Intellihub General Manager of Smart Water, Inge Diamond, data driven insights on both sides of the meter are the key to helping water utilities and their customers manage the impacts of this once in a generation investment cycle.
“We’ve been working with Hunter Water in New South Wales on digital metering solutions to help both business and residential customers better understand their water usage and costs,” Ms Diamond said.
“We can help save millions of litres of water across a customer base by detecting leaks, but the real opportunity is in the insights gained by water providers through data.
“Those insight can help direct investment where it’s most needed.”
Ms Diamond is a water engineer who made the move into the data driven side of water management with Intellihub after realising the benefits of being able to deploy at scale.
She said that better leveraging data from a digital network can reduce capital expenditure for new water infrastructure by as much as 20 per cent.
“Knowing how to use the data in complex systems is the key. I’ve helped
hundreds of large commercial and industrial customers access and understand their data to drive efficiency.
“Now I have the opportunity to work with Intellihub to implement solutions over much larger networks.”
Intellihub is a new player in smart water, but it has deep roots in the energy sector where it plays a leading role in leveraging smart technology.
Smart meter controls and data insights are driving the uptake of consumer devices and virtual power plants that allow renewable energy to be injected into the grid with lightning speed to address frequency and voltage imbalances.
The distribution providers can therefore drive better network management, reduce network congestion and improve outage management for customers.
“We’re now bringing parallel solutions and insights to the water sector,” Ms Diamond said.
“We take care of the difficult part, which is building and deploying the solution, so that water utilities can move more quickly to the stage where they are leveraging data from their smart network.
“The ongoing benefit is that demand is reduced, and infrastructure can be more accurately sized.
Ms Diamond said the sheer scale of investment needed across the water networks provides an opportunity for alternate funding models.
“Our metering-as a-service model helps utilities free up capital for the major infrastructure projects. It offers the flexibility to align the digital delivery model with a water provider’s strategic aims. That could be the management of customer demand or reduction of bursts through pressure management.
“This supports everyone’s overall goal of leaving more water in nature.” For
Service Stream has created a specialised team to take on major telecommunications projects. Image: Service Stream
Digital solutions like smart meters, AI and IoT are becoming integral to the utility sector, so it’s critical that telecommunications infrastructure can keep up with demand.
Digital connectivity underpins every facet of the industry.
Not only is it a key enabler in the transition to renewable energy, but utilities from all sectors are leaning on emerging technologies to streamline their operations and maintenance, improve their disaster resilience and meet changing customer needs.
It’s a race against time to keep up with demand, and Australia needs fibre networks that are future-proof and capable of cost-effective evolution as innovation, technology and bandwidth requirements grow.
But Australia is also one of the most sparsely populated countries in the world, and this network needs to cover vast distances, reach both urban and extremely remote locations, and tackle harsh climatic conditions.
To meet these challenges, Service Stream created a specialised Network Infrastructure team to take on major telecommunications projects across the nation.
From strength to strength
Service Stream has installed more than 1.5 million meters of cable conduit in 2024 alone – a feat that was made possible by its specialised approach.
Charged with delivering industry-leading design and construction for large-scale, complex projects of national significance, the Network Infrastructure business unit brings together more than 2230
contractors and direct staff from various areas of expertise and tailors their skillsets to the industry’s unique needs.
Excellence in delivery starts with accurate, complete and detailed designs, and this approach laid the foundations for the business unit’s wider success.
Network Infrastructure has an integrated design team that works closely with construction leads and land access professionals to consider constructability, cost optimisation and local, cultural, environmental and state heritage right from inception.
Safety is also a key consideration for the design team, and their goal is to produce a telecommunications network that is both technically fit-for-purpose and safe to construct and maintain.
A focus on data-driven analytics allows Service Stream to provide industry-leading design generation that can be tailored to suit any system or format – with a commitment to safety and payload accuracy.
This is supported by a dedicated team of system and automation professionals, who are tasked with developing and implementing advanced data checking and design tools to guarantee quality and automate the transformation of data between software platforms, removing limitations and allowing for seamless integration into native systems.
Service Stream General Manager Network Infrastructure, Sean Bryan, said the company is proud to have built a team
that has the experience and knowledge to take on the biggest and most complex connectivity projects.
“Our innovative approach has allowed us to provide state-of-the-art solutions, which incorporate the latest technology and methodologies to transform how these connectivity projects are delivered,” he said.
To track, manage and protect its people out in the field, the team also developed a series of smart solutions.
“When dealing with the astronomical number of underground services we cross each day, reliance on paper alone is not compatible with a mindset focused on safety,” Mr Bryan said.
“Our civil operators and their support workers are also required to undergo targeted training on the identification and protection of underground assets.
“In collaboration with our field supervisors and authorised personal they utilise a two-stage approach, which requires a second person removed from the on-site team to review the controls in place and confirm that the planned works can proceed in a safe, controlled manner.”
“With a national footprint and a focus on constant improvement, the Network Infrastructure team delivers turnkey solutions to meet today’s needs while delivering for tomorrow’s growth.”
For more information, visit servicestream.com.au
With every Australian depending on utilities to keep things running, field technicians need to be able to respond quickly – but increasing productivity in the face of a labour shortage is no easy task.
As populations grow and the industry strides towards a digital future, there’s greater expectation placed on essential service providers to deliver real-time information and solve issues as soon as possible.
To do this, many utilities are rolling out digital meter programs, which require many hours of work from field crews and add to the demand placed on an already expanding sector.
Utilities’ resources are already stretched thin thanks to supply chain and skills shortages, and the recent increase in extreme weather adds yet another challenge to the mix by chewing up technicians’ time as they restore unplanned outages. Australian field services logistics partner, Droppoint, saw a real need to help the sector tackle these challenges and ease the burden on field crews – but first the team wanted to gain a deeper understanding of the barriers that utility technicians face.
Let’s get technical Droppoint asked a range of industries that operate in the field services space about key logistics challenges in 2024, and out of all these sectors surveyed utilities and telecommunications companies felt the least equipped to navigate supply chain challenges and labour shortages.
Respondents in this sector also reported that response time was the most critical metric in their service level agreements (SLAs) with customers, however inventory challenges make it harder for field technicians to meet these targets.
Almost half of respondents in this area experience long waits for parts, and those in these industries reported this to be a top challenge for them more so than other industries.
Other key barriers included limited real-time visibility of inventory levels and a lack of accurate inventory demand prediction.
Intellihub Head of Supply Chain, Stuart Sproull, said, “Inventory visibility is key because Intellihub keeps the asset for its lifetime, and most smart electrical meters last between 15 and 20 years.
“Humans don’t always do the right thing at the right time. Sometimes they could be in a rush and forget to scan.
“Droppoint allows us to step into that scanning compliance; they know they’ve delivered a product and if it hasn’t been scanned within 48 hours, they can ring that technician and ask [if they’ve picked it up yet],” he said.
As expectations increase and Australians become more dependent on utilities than ever before, field services and inventory management software offers a solution to these challenges – but utilities need a provider that they can trust to truly understand their needs.
Always on
Droppoint’s Materials Orchestration System (MOS) is built exclusively for field service organistions by Australian field service professionals.
This unique logistics solution combines transport, inventory and
location management and leverages AI and machine learning to act as a single source of truth, improving field technician productivity and inventory management.
MOS can easily integrate with existing systems, and it allows Droppoint to craft a bespoke solution that meets your unique requirements.
Droppoint offers in-night delivery and has a pickup-drop off network with more than 500 locations across Australia and New Zealand, so technicians can receive parts either on-site or close to home before they start their working day.
Mr Sproull said that Droppoint allows Intellihub to make better use of technicians’ time.
“The less travel that a technician has to do to get the product that they need, the more jobs per day that they can actually do,” he said.
MOS then allows all users to manage workflows at every stage of the part lifecycle, and provides end-to-end inventory visibility, right down to the serial number.
As every sector and region have their own unique challenges, Droppoint needed to take a local approach. Its state-based teams offer regional expertise, ensuring clear communication, rapid responses times and proactive problem solving. It also has a national customer service team that are always on – ensuring you get the right part, to the right place at the right time.
For more information, visit www.droppoint.com.au
As Unitywater enters an era unprecedented growth, the utility needs a talented workforce in order to tackle these challenges head-on.
Unitywater currently provides water and wastewater services to more than 800,000 people across Queensland’s south-east and over the next 20 years this figure is forecast to increase by an extraordinary 65 per cent, to more than 1.3 million residents.
The backdrop to this significant growth trajectory is an exceptional natural environment and lifestyle, with coastal and hinterland communities that also welcome more than eleven million tourists annually.
The organisations new southern base at Mango Hill sits between Brisbane city and the stunning Glasshouse Mountains, and for Unitywater CEO, Anna Jackson, it’s a privilege to live and work in this beautiful part of the world
“With many others now wanting their holiday destination of choice to become their day-to-day lifestyle setting, it’s one of Australia’s fastest growing regions,” Ms Jackson said.
“At Unitywater, our purpose is to be here for healthy and thriving communities.”
“We need to serve our customers of today, protect the beautiful landscapes and lifestyle we all enjoy, and plan sustainably and responsibly for what we hand over to our customers of tomorrow – from the health of our environment to the reliability of our essential services and their affordability.
“Joining Unitywater, I found a business that was ready to leverage its strong operational base and committed team through a growth phase, while having positive impact within our operating environment and its communities.”
Last year, after consulting customers, team members and stakeholders, Unitywater outlined its 2030 Strategic Ambition.
Aligned around four strategic themes – value every drop, customer of the future, keep it simple, and one Unitywater – the 2030 Strategic Ambition guides the team to shape healthy and thriving communities.
“The strategy is an ambition for our organisation, to become a mature, transformed business with a leadership role in the communities we serve.
“Our goal is to meet growth challenges head on, while working towards net zero targets and meeting the community’s expectations, now and into the future,” Ms Jackson said.
“Realising this shift, while meeting the needs of a growing region, means we need additional talented and motivated working people working within and alongside our business.”
Competing for this talent against large multinational corporations based in the nearby capital city and navigating the changed workplace flexibility expectations of a post-pandemic employment market, Unitywater needed to better meet the market.
“Millennials are the largest cohort in the working population – including the water sector – and are less likely to stay in one role, with more emphasis on development and work-life balance over financial reward,” Ms Jackson said.
“Around this time, news reports and conversations with other organisations were confirming that mandated office attendance ratios were impacting culture and talent attraction.”
Towards the end of 2023, 87 per cent of Australian businesses were reported to have introduced mandates – with four days a week being the most common – and 31 per cent having lost employees because of it.
“In this context we developed our Working Better Together principles, to give our teams a framework to locally design and manage their normal work patterns, to balance our specific operational requirements, with their internal and external customer needs and personal preferences.
“To start, we acknowledged that as a 24/7 essential service there are some roles that can’t be performed flexibly, and we were also clear that no one works from home all the time because we consider face to face contact integral to our strong organisational culture,” Ms Jackson said.
“We then gave guidance on the moments and activities that can work remotely, those that are better in-person and those that are expected in-person.
“Each team built a charter that defines how this works for them and their expectations of each other –from valuing time spent together, to which of our work locations they attend – and provides a mechanism for leaders to ensure their people are working safely.”
Balancing traditional business thinking and contemporary employee expectations has been important to recruitment and retention, with Unitywater reporting that 100 per cent of candidates ask about flexible arrangements and around 40 per cent say they would decline a role if mandated significant office attendance.
The utility’s turnover is down to 12 per cent, compared to the national average of 15 per cent. Cultural outcomes look positive too, with team involvement measures lifting 7.6 per cent halfway through the implementation process.
Recognition for employment practices also recently came from Work180 ranking Unitywater its number one employer for gender pay equity, and BenchmarCX certifying it as a Triple R employer implementing responsive and respectful recruitment.
“We believe that we are better together, and that when we share space, we increase creativity and collaboration,” Ms Jackson said.
“Physical workspaces must support this way of working, so in May 2024 we moved our Southern Corporate Centre from Caboolture to Mango Hill, a location central to transport and closer to home for more of our future team and customers.
“We reconsidered our traditional ways of working and aligned ourselves with an activity-based, technology-supported hybrid model that maximises the geography of our service area.
“It complements our Northern Corporate Centre in Maroochydore, with the two office locations now better catering to people travelling to work from either Brisbane and Moreton Bay, or the Sunshine Coast and Noosa, contributing to our employee value proposition and attracting a stronger depth of skills and experience.”
The location and modern fit out at the new Mango Hill office have seen daily occupancy levels regularly exceed 80 per cent, while the team-defined working patterns have lifted total real estate utilisation across all Unitywater sites by 21 per cent per square meter.
These numbers will increase further, as Unitywater’s new longterm capital delivery partners start working alongside their team to Build Better Together.
Earlier in 2024, the business signed initial five-year framework agreements with Downer, Dormway and Elevate (a joint venture of Aurecon and AECOM) to streamline the capital delivery process to support an era of significant growth.
“We can see the influence population growth is having on our capital program, with 70 per cent of projects this year being growth-related, up from an average of 30 per cent over the past three years.
“Our partners will support us to deliver our $1.8 billion capital investment program over the next five years, to secure reliable water services for our growing customer base,” Ms Jackson said.
“We’re mitigating the impact of external factors like tight labour markets and booming infrastructure programs, by making sure our partners will be ready to work on our projects, meaning certainty and reliability for program delivery.”
With 88 per cent of Unitywater’s team members living within the region they serve, their sense of working together also extends to the community they are part of.
“Whether it’s the way we work as a core team, the way we partner to extend our team, or the way we share common experiences with our customers and communities, it’s always going to be better when we do it together.”
Quinlan Cranes is training the next generation of certified professionals who are trained to work around live assets.
Image: Quinlan Cranes
A trailblazing apprenticeship program is tackling the sector’s skilled labour shortage by empowering the next generation of professionals.
Utility construction sites are high-risk environments, and personnel working with live high-voltage assets or active water infrastructure need to be highly experienced to tackle these complex projects.
But many of the seasoned professionals the sector relies on are now approaching retirement age, and there’s not enough skilled workers to take their place.
It was clear that the sector urgently needed a new generation of industryready professionals, especially ones who are certified to work around live assets, and in 2019 a group of crane companies banded together to find a solution.
Quinlan Cranes Founder and Director, Tom Quinlan, recognised that the right education was the foundation of expertise, so – in partnership with P&D Rigging and Crane Hire Managing Director, Barry Stockdale, and Mobile Cranes CEO, Peter Booth – he launched the Victorian Mobile Crane Training Apprenticeship (VMCTA).
Setting up success
According to VMCTA Training Coordinator, Kylie Owen, a prospective crane operator is technically qualified to get out on the field after just five days of training.
“It’s a very high-risk industry, but you and I could go to a registered training organisation over the next five days and get what we call a ‘dogman’s ticket’ and could go out in the field,” Ms Owen said.
“A good operator is someone that’s done their time on the ground in a dogman’s role. They’re basically the eyes and ears of the crane operator, and to be successful as an operator, you should know what’s happening on the ground.
“So, Tom, Barry and Peter said, ‘why don’t we bring them in very green, but we train them in a controlled environment over a two-year period’?”
Ms Owen explained that they also saw this as an opportunity for the older workforce to pass down their skills and mentor the next generation.
“If you’re going to implement something innovative, involve
the older generation in the concept and make it a communal, collaborative effort.
“The old culture was to keep your craft to yourself, but the younger generation can’t learn what we know from a book or from a telephone.
“If you involve them in the conversation at the very early days, you'll find that the older generation will feel empowered because their voice has been heard. They then get to share their wisdom and you get a very united team.”
Now on its tenth group, Ms Owen said that the program has seen a 97 per cent retention rate post-graduation – but the aim of the VMCTA program isn’t just to hand out a qualification, it’s to set the younger generation up with a job for life.
“After two years they will graduate with what’s called a C6 ticket, but generally around three years post-graduation is when they actually start to get a bit of crane time.”
“It doesn’t just end there. We’ve now got a supervisor’s course that can run 12 months after they’ve graduated, and we want to really bridge the gap between the ageing workforce and today’s youth and set them up with actual careers.”
Ms Owen said that she wants the VMCTA graduates to be able stand tall and be proud to have a career in construction.
“Everyone, as a collective, acknowledges this job is gruesome. We say pack your breakfast, lunch and tea, because we don’t know what time you’re going to come home. We’ve all learned the hard way. So, we’re trying to share our wisdom about wellness as well.
“What we’re trying to do is not only teach them the tricks of the trade, but all the other life skills that they need to be successful at this job. It’s not just ‘get a ticket, get on the ground’. It’s a well-rounded human that comes out at the end.”
While the program’s trainees are an incredibly diverse group, the one thing that they all share is a real and genuine love of the industry.
For Ashleigh Bond, it was working a traffic management job alongside Quinlan Cranes that inspired her to take up a career in the industry.
“I always enjoyed being outdoors and working with my hands. When I was working in traffic management I just enjoyed working with cranes – that’s what got me into going and getting my dogman’s ticket,” she said.
Ms Bond is now set to complete the program in March 2025, and has nothing but praise for the VMCTA.
“They’re alongside you the whole way. All the staff there have been amazing and if you’ve got any questions, they’re just there to support you – Kylie’s like your little cheerleader in the background.
“The knowledge that they pass on is second to none, and I’m glad I’m doing it through the traineeship, and I didn’t just get my ticket on my own,” she said.
Ms Bond said one of the highlights of the apprenticeship was her peers.
“I get along really well with them, and because we all started at the same time, it’s nice to be on the same level when we talk about work and bounce off one another,” she said.
First year trainee, Vaughn Adams, said that the program gives everyone an equal opportunity to get their foot in the door.
“The trainers are very knowledgeable, and I find you could relate to them regardless of where you come from –they cater to pretty much everyone and anything,” he said.
“I came into the traineeship just to try and make it easier on my body. But it’s instilled a want to stay within this industry for the long run.
“I’ve known many other crane operators, and they wish they had something like this around their time. Back then, you had to have a relationship with a someone within the industry, not just to be able to get in the industry, but also to gain the knowledge and experience.
“But with this traineeship, you can come in knowing nothing and coming out knowing a lot.”
Ms Owen said she can’t stress enough that the key to a successful career is the ability to be your authentic self.
“What you want to be known for is your great work ethic, your integrity – and it doesn't matter what your gender identity or your ethnicity is, we’re here for everybody,” she said.
“I think the younger generation are better at doing this. Our intakes are groups of all varied ages, different backgrounds, men and women, but they just seem to bond like a family.”
According to Ms Owen, one of the key drivers of the program’s success was that the employer is the one choosing the trainee.
She said that despite the business’ success, both Mr Quinlan, and Quinlan Cranes second Director, Sacha Sikka, still take a very hands-on approach.
“They just get on the ground, get dirty and get to know their workers – and they really listen to them,” Ms Owen said.
Quinlan Cranes apprenticed the program’s youngest ever trainee, Sam Fonesca.
“Tom has an eye for someone who’s got a natural gift with operating equipment. Sam was 18 or 19 when he came in; he was sassy and had a little bit of an attitude – but Tom saw something in him,” Ms Owen said.
“Sam graduated a couple of years ago, and already he’s operating one of their 250 cranes.”
Ms Owen said that the team at Quinlan Cranes are very passionate about their involvement in the program, and they don’t choose their apprentices lightly.
“They really get to know their people, and they choose appropriate mentors that can bring out the best in them,” she said.
Ms Bond had a similar story to tell.
“Quinlan has been great. They’ve all been very helpful, and they push me to my limits in a good way,” she said.
“They get me outside my comfort zone and helped me prove to myself that I can do things that was doubting myself on.”
For Ms Owen, the right person for job is someone who truly loves what they do.
“If you’re passionate about what you do, it won’t seem like work,” she said.
“We had an amazing young woman who started off her career as a hairdresser, and then when COVID hit she took a career change to advanced cranes. She finished her traineeship at 33 weeks pregnant and did an extraordinary job – she didn’t miss a beat.
“We had to modify a few things, but she just got on with the job and she truly loves it.”
Following the success of the VMCTA, three other traineeships have been formed: the Victorian Scaffolding Traineeship Association (VSTA), the Victorian Demolition Traineeship Association (VDTA) and the Victorian Civil Traineeship Association (VCTA).
“We have a large Indigenous cohort in the civil traineeship, and that has been the most rewarding part of my year,” Ms Owen said.
“For some of these young individuals it would be highly unusual that they have the opportunity to hold a full-time job, let alone get a Certificate III, and it’s truly rewarding to see someone putting belief into them, giving them the time and listening to what they want to do.”
Ms Owen encourages the next generation not to give up on a career they’re truly passionate about.
“Every door that gets closed and every knockback you get – make that the motivation to stand tall and say, ‘you think I can’t do it? You watch. I can’.”
For more information, visit quinlancranes.com.au
Increasing workforce participation from underrepresented groups is critical to increasing skilled labour. Image: ultramansk/shutterstock.com
By Elianor Gerrard, Chris Briggs and Jay Rutovitz, Institute for Sustainable Futures, University of Technology
Sydney
Powering towards net zero means doubling the electricity sector workforce – but addressing the skills shortage has its challenges.
Australia is racing towards decarbonisation of the electricity system, but a recent report from the Institute for Sustainable Futures (ISF), University of Technology Sydney found that delivering on the Federal Government’s renewable energy targets across the National Electricity Market (NEM) will require a doubling of the electricity sector workforce by 2029.
Most growth in the workforce will happen in wind, rooftop solar and distributed batteries, accounting for 80 per cent of the workforce. In a sign of the transition occurring to our energy system, there will be more jobs in electricity storage than domestic coal and gas generation by 2027.
The ISF was commissioned by The RACE for 2030 Co-operative Research Centre and the Australian Energy Market Operator (AEMO) to model workforce numbers required to deliver the Integrated System Plan (ISP).
The ISP uses three different energy scenarios or ‘development pathways’ for the NEM to transition away from coal power generation to renewable energy: Progressive Change – a slower rate of change due to a constrained economy and supply chains
Step Change – broadly aligned with current government policy towards 2030 targets and net zero by 2050 • Green Energy Exports – a scenario that would see Australia become a ‘renewable energy superpower’, exporting green energy globally
Using a ‘Delphi Panel’ method, AEMO assigned likelihoods to each scenario, with 43 per cent for Step Change, 42 per cent for Progressive Change and 15 per cent for Green Energy Exports.
Our modelling approach
We modelled the projected workforce using an employment factor methodology, applying labour intensity factors (FTE/MW) for the construction, operation and maintenance and manufacturing of renewable energy technologies to projected installed capacity in the ISP scenarios. When we talk about jobs, we are referring to the total full-time equivalent (FTE) roles in a year.
An FTE could mean two people working on six-month contracts each across construction for renewable projects,
or one person working full-time in operations and maintenance. We model jobs associated with construction, operations and maintenance, manufacturing and in coal and gas for domestic energy production (not export).
What is needed for the most likely scenario?
Under the Step Change scenario, we will need to grow the electricity sector workforce from 33,000 to a peak of 66,000 by 2029. More than 40 per cent of these jobs will be in rooftop solar and batteries, a sector that is projected to experience steady growth in coming years. Wind and solar farms represent a third and ten per cent of total jobs respectively. The workforce for transmission construction is smaller but the significant investment in transmission
line infrastructure in regional areas sees jobs in transmission line construction increase three-fold.
Importantly, these projections do not capture all the workers. What isn’t included in these projections is the workforce upstream in the supply-chain (e.g. critical minerals mining) or associated with home electrification, energy efficiency and demand and energy management, meaning the workforce needed to deliver the energy transformation is much larger than presented here. To date there is limited understanding of this diverse and evolving workforce; data and information is urgently needed to support effective workforce planning.
The ISP only covers the states in the NEM, so Western Australia and the Northern Territory’s workforce requirements are also not captured here.
Jobs in operations and maintenance will become larger than construction in the 2030s
While there is a significant boom in construction jobs as renewable energy projects ramp up, by 2032 more than 50 per cent of the electricity sector workforce is in operations and maintenance.
By 2050, this number reaches 76 per cent, with the steady growth in consumer energy resources (CER), like rooftop solar and batteries contributing the demand for ongoing operations and maintenance roles.
Becoming a renewable superpower would require prodigious employment growth, especially in Queensland
Under the Green Energy Exports scenario, where Australia uses renewables to scale-up heavy industry and export green hydrogen to international markets, the electricity sector workforce would need to increase threefold by 2029. There would be an annual average of 82,100 jobs from now until 2050, if Australia pursues a green energy exports pathway.
In 2033, after construction to build infrastructure for the domestic energy transition peaks, a sharp drop in workforce numbers is projected, triggering an employment downturn during the 2030s. By 2039, however, things would pick up pace again as states invest in infrastructure for energy exports. By 2050, jobs would peak again at 120,000.
Under the Green Energy Exports scenario, Queensland is set to become the state with the most electricity sector
employment, most of which will be driven by demand from wind farms. The modelling also doesn’t include the very large projects proposed in off-grid areas such as the Pilbara.
Significant employment growth is required even under ‘Progressive Change’ Scenario Progressive Change (which was voted only one per cent behind Step Change in likelihood) assumes a significantly constrained economy and challenges with supply chains, including minerals, products and labour. Despite these constraints, the workforce would still need to grow by 19,000 to meet the peaks in construction by 2029.
How many jobs could be created by developing local manufacturing? We also modelled an ‘enhanced manufacturing’ sensitivity, which assumes around 30 per cent of most renewable energy inputs are manufactured in Australia (wind, batteries, pumped hydro) or ten per cent in the case of utility and rooftop solar. At its peak, this scenario would add an additional 5000 jobs.
The local share of manufacturing is uncertain and will be shaped by a range of factors including funding from the Future Made in Australia package just passed by the Australian Parliament.
Building out the renewable energy projects required to support an orderly and timely closure of coal power stations has its challenges. As our modelling demonstrates, the workforce needs to grow significantly under each scenario. And this growth is occurring at a time when the electricity sector is experiencing a skills shortage.
As Australia’s Skills Priority List shows, there is a shortage of many of the essential occupations in the sector, with some in persistent shortage.
The skill and worker shortages in the electricity sector are further compounded by the ongoing growth of the major infrastructure project pipeline in Australia. Infrastructure Australia’s 2023 market capacity report highlights that labour shortages continue to constrain projects, and it is many of these same workers that the electricity sector is competing for against major infrastructure projects.
Historically, Australia has been dependent on skilled migrants to fill labour and skills shortages and gaps. While Australia intends to do the same again, this is happening in the context of a global renewables boom, with policies such the US’s Inflation Reduction Act driving unprecedented investment.
The training system is strained, and this shortage impacts on our ability to rapidly skill up potential workers. Similarly, the renewable energy sector is generally not well-connected with the vocational education and training sector – and it needs to increase investment in training.
In each of the modelled scenarios, there are huge employment peaks, driven by construction booms largely in the lead up to state targets. This will lead to boom-and-bust cycles, increasing skills shortages and negatively impacting regional host communities.
How can we build up the electricity sector workforce and deliver on our net zero targets?
Addressing the skills shortage is a vital step to growing our electricity sector workforce; to do this, we need to increase apprentices and build the training system’s capacity to be able to deliver more training.
Supporting young people and school students living in regional areas that are renewable energy zones into renewable energy training, could not only benefit them by providing career and employment opportunities close to home, but it could also ease labour supply issues and reduce the need for external workers in REZs.
The Federal Government has taken some steps to boosting uptake through its New Energy Apprenticeships Program.
But making sure that renewable energy projects take on learning workers is also key.
Jobs and Skills Australia has recommended that the Australian Skills Guarantee – which sets mandatory requirements for ten per cent of labour hours on major Commonwealth funded constructions and ICT projects be completed by apprentices or trainees – be applied to renewable energy generation and transmission projects.
Government-funded initiatives, such as the Capacity Investment Scheme, Rewiring the Nation and grants from the Clean Energy Finance Corporation and the Australian Renewable Energy Agency, should have similar targets for trainees and apprentices. Government support is required to assist renewable energy companies meet targets as they themselves are experiencing shortages and constraints.
Increasing workforce participation from underrepresented groups is also a critical part of increasing our supply of skilled labour. It also makes for greater equity and diversity in a sector that lags well behind most Australian industries.
As Jobs and Skills Australia points out, we can’t grow the workforce at the pace and scale required if large groups of the population are excluded, including women, First Nations people, people with disability and recent migrants whose skills’ potential are underutilised.1
Pre-employment programs and specialised programs such as gender and First Nations targets, mentorship and employment-support initiatives, can play an essential role in creating a more diverse and inclusive workforce.
Lastly, smoothing the project pipeline could have a powerful effect in reducing skills and labour shortages associated with construction booms.
While there are challenges ahead as we transform our energy system and mitigate against climate change’s most negative impacts, there are also opportunities to reinvigorate our training system, direct government funds to on-the-job learning, and to create more equity and diversity in our sector.
1 Jobs Skills Australia, p17.
Automated Inspections: Perform rapid, accurate access hole inspections with high-definition 360-degree video (scan QR code below).
Cloud Connectivity: Seamlessly transfer inspection data to the cloud via the WinCan WebFlex app.
Actionable Data in Minutes: Generate reports quickly with features like AI-driven defect identification, 3D modelling, and laser range finding.
Efficiency Boost: Inspect more access holes in a single day, transforming hours of manual work into minutes.
Portable and Wireless: Operates without cables, increasing operator mobility and ease of use.
Contact SECA today to discover how pairing the Quickview 360 and WinCan can save you time and enhance the accuracy of your access hole inspections.
Everyone deserves an injury-free workplace, and SA Water found that sometimes the little things can make a big difference to on-site safety.
As sewer networks age, the maintenance holes and chambers that provide access to these assets can become damaged or buried and need to be raised before works can begin.
SA Water Operations Water Network Interface Specialist, Mark Evans, explained that this traditionally involved a heavy concrete ring.
“The really small rings are around about 10–20kg. For the thicker ones, you’re looking at between 250–300kg,” Mr Evans said.
“We used to have to find a way down to the manhole with a concrete ring and then lift that concrete ring into place.”
With a maximum weight less than 7kg, even the heaviest Pro-Ring can be held in one hand. Image: ISC Services
Working with these heavy rings caused years of manual handling issues for the team, and SA Water knew it needed to find a safer way to work.
“Safety is at the heart of everything we do, it’s one of our core pillars, and the business is very open to looking at innovative ways to be able to make things safer for our teams,” Mr Evans said.
While at a conference, Mr Evans met ISC Services Owner, Dennis Bentink, who introduced him to the Pro-Ring™.
Going pro
The Cretex Pro-Ring is an expanded polypropylene (EPP) make-up ring designed for sewerage maintenance holes and access chambers.
These rings weigh approximately onetwentieth of the mass of concrete and even the largest rings don’t exceed 7kg.
“I walked into a district leaders forum a few years ago holding the largest Pro-Ring with one finger,” Mr Evans said
This lightweight alternative can easily be installed by a single worker and can significantly reduce the risk of injury –including sudden sprains and impacts, as well as accumulative strains and musculoskeletal disorders.
Mr Evans said that the Pro-Ring also makes installation faster and makes for more efficient use of resources.
“You don’t need machines to lift these things in and out. It’s easy to transport because it's lighter, and it’s easy to install because it’s lighter – the job just becomes simpler,” he said.
Traditional concrete make-up rings are also porous, which makes them vulnerable to corrosion. EPP, on the other hand, is not affected by hydrogen sulphide and is resistant to corrosion without the need for any coatings.
Multiple Pro-Rings can easily be joined via an upper and lower keyway and offers a water and gas-tight seal that safeguards assets against infiltration.
“My whole team have just embraced it, and Dennis has been nothing but supportive,” Mr Evans said.
“I’ve been working with Dennis on a smaller version that we could potentially use for valve and fire plug chambers.
“If we could remove the concrete rings underneath cast-iron chambers and use the smaller version of the Pro-Ring, even for new construction, I think that would be a huge benefit to the water industry as a whole.”
For more information, visit iscservices.com.au
• Lighter and Safer
•
• Better value for money
• Half the CO2 emissions of concrete to manufacture
• Leak tight
• Trafficable Class - D
• Proven solution
• Recyclable
Innovative products to improve the return on your valuable sewer, stormwater and potable assets
• Raise MHs to surface safely, quickly and cost-effectively
• Permanently seal leaking pipes and MH joints
• Prevent leaks forming
To address the urgent need for qualified energy workers, Stanwell is creating pathways to equip the next generation with the skills that will be in demand for years to come.
The Electricity Sector Workforce Projections for the 2024 Integrated System Plan report has raised concerns about the looming shortage of skilled workers needed to drive the clean energy transformation.
Created in collaboration between the Institute for Sustainable Futures (ISF) at the University of Technology Sydney (UTS) and the Australian Energy Market Operator (AEMO), the report highlights the urgent need for more skilled workers in the electricity sector.
Jobs in the sector are expected to double by 2029 with renewable energy, particularly wind, solar, and battery storage, leading the charge. According to the report, operations and maintenance roles are expected to make up 65 per cent of the sector’s workforce by 2033.
However, the report also found that the renewables industry invests very little in skills development and training. This lack of investment is further complicated by the regional nature of many renewable energy projects, which will compete with major infrastructure projects in urban areas for labour.
In the face of these challenges, Queensland power generator, Stanwell Corporation, is playing a proactive role in preparing the state’s workforce for the energy transition.
Stanwell has a specialist team dedicated to developing future pathways for its people to ensure they realise opportunities from the energy transformation. It is also establishing a Future Energy Training and Innovation Hub that will specialise in delivering a real-world training environment in renewables for Queensland energy workers.
Empowering the future workforce Through its recently established subsidiary, Stanwell Asset Maintenance Company (SAMCo), Stanwell is creating future pathways for technically skilled energy workers in Queensland’s regions, equipping them with the skills needed to thrive in the clean energy sector.
Launched in 2023, SAMCo builds on Stanwell’s decades of experience as a reliable and efficient operator in the National Electricity Market (NEM). With a strong track record in maintaining complex energy assets, Stanwell’s expertise in safety, reliability, and performance is now being applied to asset maintenance within the renewable energy sector through SAMCo.
SAMCo is partnering with asset owners, original equipment manufacturers and engineering procurement construction companies across Australia to provide operations and maintenance services and asset management for all forms of renewable energy assets.
Stanwell General Manager Renewable Maintenance Services, Steve Clark, said that the utility understands what asset owners need because it has been in their shoes.
“We act like an owner, representing our clients’ interests to ensure their investment delivers expected returns,” Mr Clark said.
With established systems, skilled personnel, and deep expertise in renewable energy technologies, SAMCo is quickly becoming Queensland’s go-to partner for renewable energy maintenance.
A key initiative driving SAMCo is the Development Pathways Program, which is providing Queensland’s energy workers with hands-on experience operating and maintaining renewable assets owned by host companies on the eastern seaboard of Australia.
Participants in the Development Pathways Program either come from Stanwell’s thermal power stations – the Stanwell Power Station near Rockhampton in central Queensland, and Tarong power stations near Nanango in the South Burnett region – or from local private industry and have either mechanical or electrical trade skills.
Participants are scheduled onto rosters and have the opportunity to work on a variety of renewable energy sites while receiving competitive salaries and travel allowances.
Stanwell provides participants with training in areas such as large-scale solar operations and maintenance, wind safety and rescue, thermography, and more.
For workers like Ivor Ralph, the Development Pathways Program has been a gateway to the clean energy industry.
Mr Ralph is a mechanical fitter and machinist who began his career with Stanwell in 2019. He said that he joined the program to broaden his skills and gain experience with renewable technologies.
“I saw it as a way to get a taste of the renewable energy industry,” Mr Ralph said.
“After all, most of Queensland’s energy will come from renewables by 2035. It won’t be long until renewable energy is just...energy.”
Throughout the program, Mr Ralph has worked on wind and solar projects across Australia, gaining valuable experience in inspecting, troubleshooting, and repairing renewable energy assets. After 18 months, he transitioned to a permanent role as a Travelling Service Technician
with SAMCo, a position that now takes him to a variety of wind, solar, and battery sites around the state.
For Mr Clark, the program is about providing future pathways and opportunities for those who want to start building their capabilities now.
“The Development Pathways Program aligns with the Queensland Energy Workers’ Charter and the Job Security Guarantee, ensuring a secure future for our energy workforce,” Mr Clark said.
For host companies, the Development Pathways Program offers the benefit of experienced labour at a fraction of the cost of subcontractors, while supporting the development of a skilled workforce crucial to Australia’s energy transition.
Stanwell’s commitment to workforce development doesn’t stop with SAMCo. The company is also building the Future Energy Innovation and Training Hub (FEITH), a state-of-the-art facility at the Stanwell Power Station in Central Queensland.
Once complete, the hub will provide hands-on training with emerging clean energy technologies, including wind, solar, hydrogen, and battery storage.
FEITH will serve as a pilot and testing facility for new energy technologies, while also offering a real-world training environment for Queensland energy workers. Stanwell has also partnered with CQUniversity to collaborate on skills, training and technology initiatives.
Stanwell is working closely with its people, delivering on its commitments under the Queensland Energy Workers’ Charter.
To create careers and opportunities for its people, the Future Pathways team is identifying the talent Stanwell already has in its workforce and the skills that will be required to build Queensland’s renewable energy future.
As the energy transition accelerates, the need for skilled workers has never been more pressing. Through initiatives like its Future Pathways, SAMCo and FEITH, Stanwell aims to ensuring that its workforce is equipped to seize the opportunities presented by the clean energy transformation, and to provide the spark for a bright future.
By David Brown, Associate Vice President, APAC, Geotab
Vehicles are major producers of carbon emissions, but they’re also vital to field services and emergency responses – so how can utilities make their fleets more sustainable?
In Australia, the transport sector is the third largest source of the country’s greenhouse gas emissions, contributing to 21 per cent of national emissions in 2023. Since 2005, these emissions have risen by 19 per cent and are projected to become the largest by 2030.
The Federal Government aims to reduce greenhouse gas emissions to 43 per cent below 2005 levels by 2030 and achieve net zero emissions by 2050. Innovation and sustainability are crucial to improving operations and reducing emissions in the utlity sector.
A successful sustainability initiative incorporates these three key elements: technology and innovation; laws, public policy, and governance; and economic and financial incentives. Companies want to become more sustainable, but how and where do you start? The answer is telematics.
Leveraging connected vehicle technology not only supports new road safety and sustainability legislation but also reduces emissions with data-driven insights. Data insights from telematics solutions can help with the fleet
sustainability strategy and mitigate costs while increasing efficiency.
Utilities can use data insights to optimise routing for a wide variety of delivery and service vehicles, prepare fuel management reporting to reduce idling and improve fuel efficiency for all vehicle types, and efficiently use and determine the right-size vehicles, ensuring the right vehicle for the job.
The fuel economy of a vehicle plays a significant role in the overall operating costs of a fleet, accounting for approximately 60 per cent of the total. Key effective strategies to control fuel consumption and emissions are to reduce unnecessary idling, control driver behaviour, set speed restrictions, optimise routes, practise preventative maintenance, right-size vehicles to their tasks, lighten the load, use fuel cards, and adopt electric vehicles (EVs).
While it is important to revisit and consider the sustainable fleet strategy, reducing vehicle emissions is equally crucial. The urgent need for climate action has put the onus on governments globally to integrate policies and regulations to enable a market shift to zero-emission transportation. Electrification is on the rise.
Recently, there has been a large push to transition fleets to EVs. With the growing number of EVs in the market, there has never been a better time to begin the process of fleet electrification to improve the bottom line.
Before you can start adding EVs, it is important to understand the vehicle’s daily route, operating cost and vehicle dwell time. Using telematics will provide access to the fleet’s driving data points and help determine where it makes sense to electrify. It provides vehicle recommendations based on the models available in your region, as well as the projected cost savings and avoided CO 2 emissions.
The time to act is now, as sustainability becomes a significant concern for both governments and corporations. By integrating advanced analytics with telematics expertise, companies can develop sustainable transportation solutions and enhance fleet management. Collectively, this will help the industry demonstrate the profound impact that innovative technology can have on the transportation system today and create safer systems worldwide. For more information, visit geotab.com/au
2 & 3 April 2025 | Bendigo Showgrounds, VIC
Get ready for our largest and most prestigious gathering of water industry operations professionals in Bendigo! Join us for a day filled with insightful discussions, networking opportunities, and exciting exhibitions. Whether you're a seasoned pro or starting your journey in the Water industry, this event is perfect for expanding your knowledge and connecting with like-minded individuals to drive the industry forward.
Interflow has pushed past the boundaries of common pipe renewal solutions. Image: Interflow
To address a growing need for a renewal technology that is specifically optimised for pressure pipelines, Interflow has developed a suite of sustainable solutions.
When it comes to ageing water infrastructure, pressure pipes have traditionally been excavated for repair or replacement. This has disrupted communities and increased costs and time scales.
As corrosion from aggressive soils attacks underground pipes, a trenchless renewal option becomes increasingly attractive.
Interflow National Product Manager, Will Zillmann, said that proactive trenchless renewals are one of the keys to defending critical water and wastewater services in a sustainable and cost-effective way.
“Comprehensive renewal solutions should not just fix a specific problem but should reset the lifespan of the pipeline. They should essentially perform as a new product,” Mr Zillmann said.
“Our objective was to build a suitable suite of proven solutions that enable us to match the right product or approach to the pressure pipeline’s condition, material, size and location.”
At the core of Interflow’s suite of solutions is a polyethylene liner technology known as Titeflow. It’s a structural liner that has its diameter
reduced with a die during installation, so it can be drawn into the host pipe. Once inside, it expands again to press against the host walls, creating a new pipe within the existing pipeline.
As a lining technology, it fits within the ISO classifications for trenchless solutions, primarily at Class A (can survive failure of host pipe and is a fully structural solution).
According to Mr Zillmann, it’s a solution that balances performance, safety and environmental impact.
“As the triple bottom line of environmental, social and economic impacts becomes increasingly important to water authorities and government, sustainable pipeline renewal methods will become the norm,” he said.
Interflow’s purpose is to improve lives, which extends to the communities and environments they operate within. This has led the company on a journey to find, assess and develop renewal solutions that are sustainable and support the needs of the industry, customers and their communities.
As part of this journey, Interflow is running an exhaustive and ongoing research project.
Through such research projects, and by working closely with customers, Interflow has been able to push the boundaries of common approaches like slip lining and large diameter die-reduction lining.
“For example, we’ve had success renewing longer lengths of water main using both of these technologies by thinking differently about how we store, string out and weld pipe sections, and how we facilitate insertion,”
Mr Zillmann said.
“We can now offer renewal options for pressure pipes in varying condition states and covering a large range of sizes and materials.”
“Our approach to renewal opportunities is to be solution-agnostic and develop an optimal methodology based on project-specific network capacity needs, pipe condition and material, internal diameter, access constraints, budget and community needs.”
For more information, visit interflow.com.au
By Hannah
EnergyCo has committed to collaborative change in partnership with the Energy Charter.
Energy powers every aspect of modern life. At EnergyCo, we aim to drive an affordable, reliable, sustainable energy future through innovative projects, trusted partnerships, and dedicated people. We enable NSW’s energy transition by delivering renewable energy zones (REZs) and priority network projects.
As CEO, I am deeply committed to ensuring this transition benefits consumers and the communities that host this critical infrastructure. With a career spanning energy, utilities, and carbon reduction in the UK and Australia, I am passionate about fostering collaboration and driving meaningful outcomes that leave a lasting legacy.
The Central-West Orana REZ is a prime example of the transformative potential of this work. This REZ is
expected to deliver $3 billion in net benefits for energy consumers, while more than $20 billion in private investment will support the development of networks, generation and storage.
These projects will create 5,000 jobs during peak construction and reduce consumer bill impacts by more than $200 million, supported by $490 million in Clean Energy Finance Corporation investment. We aim to ensure these benefits extend to the local communities, creating a positive and enduring legacy.
EnergyCo has developed a Community and Employment Benefit Program for the Central-West Orana REZ to achieve this. Community groups, councils and First Nations organisations within the Central-West Orana region will be able to apply for $70 million
in grants before construction starts and $128 million in the first four years. EnergyCo worked with regional communities to ensure the program reflects local priorities.
New South Wales has also introduced a Strategic Benefit Payments Scheme to directly support landowners hosting high-voltage infrastructure. Under this scheme, landowners will receive annual payments, reinforcing our commitment to sharing the benefits of the energy transition.
EnergyCo is proud to have joined the Energy Charter, which unites organisations across the energy sector under a shared vision: to create an energy system that works for everyone.
The Energy Charter’s principles guide our work, fostering transparency, accountability, and a relentless focus on community outcomes.
Collaborating for a shared vision Collaboration has been a cornerstone of these successes; for example, EnergyCo’s Waratah Super Battery exemplifies how government, private investors and network operators can come together to enhance grid reliability in innovative ways, enabled by advancements in battery technology and regulatory frameworks. Equally vital has been the engagement with local communities to ensure this project delivers value for consumers and the people in the region.
The Energy Charter’s members collaborate through groups like a CEO Council to drive measurable outcomes that benefit communities. This cooperation highlights the community's recognition of the REZ’s importance for regional and environmental benefits.
EnergyCo has engaged with individual landholders more than 3600 times
through face-to-face meetings, community information sessions and regular updates. In Central-West Orana, EnergyCo has reached an agreement with more than 97 per cent of private landowners to host critical transmission infrastructure for the REZ. We are committed to a thorough, respectful, and transparent process that ensures landholders feel heard, informed and supported.
This collaborative approach will also ensure we can more effectively respond to our communities’ evolving needs as the transition unfolds.
Fostering transparency and accountability are high priorities for EnergyCo. The Energy Charter’s Maturity Model provides strong principles to enhance our approach. It reinforces our commitment to high community engagement and environmental stewardship standards, ensuring we remain responsive to our communities.
The #BetterTogether program is also a cornerstone of the Energy Charter.
It enables organisations across the sector to work on shared challenges. We leverage #BetterTogether to address our state's unique challenges. From delivering new energy supplies to creating pathways for community involvement, this program facilitates partnerships that help shape an energy transition for all.
Part of EnergyCo’s mandate is to foster support for the energy transition. We do this by ensuring benefits are not just secured but shared. Our Community and Employment Benefit Programs empower Aboriginal organisations, create local job opportunities, and enhance community infrastructure, ensuring the benefits of renewable energy development are shared equitably.
Joining the Energy Charter is a key milestone for EnergyCo. By delivering projects that benefit consumers, partnering with communities, government and industry, and putting people at the heart of the transition, we can help create an affordable, reliable, sustainable energy future for everyone in New South Wales.
An innovative approach to construction could be the key to building a more sustainable future for the utility sector.
Agroundbreaking partnership, known as QuadraSola, has been formed between Decon Corporation, Solagenica, Deloitte Emissions Solutions, and GreenRen Power to introduce innovative solar structural insulated panels (SSIPs) to the Australian market. This collaboration marks a significant milestone in the nation’s journey towards a sustainable and energy-independent future.
Decon Corporation, a leader in manufacturing switchboards, electrical components, and clean energy solutions, will spearhead the production of these revolutionary SSIPs at its expansive facility in Scoresby, Victoria. Featuring a proprietary fiberglass skin and EPS core, these SSIPs surpass traditional wood or steel structures in both strength and energy efficiency.
QuadraSola will utilise advanced no-glass, no-soldering interdigitated back contact (IBC) solar cell technology in the SSIPs, which maximises solar cell efficiency and ensures optimal power output.
This partnership harnesses the collective expertise of all parties in advanced solar technology, paired with Decon's extensive manufacturing capabilities and deep understanding of Australia’s electrical and telecommunications infrastructure. The synergy promises to drive widespread adoption of sustainable building practices across the country.
SSIP technology offers a powerful solution to Australia's energy challenges:
• Decentralised energy generation: by integrating solar power into building structures, SSIPs can reduce reliance
on the traditional grid, improving energy security and resilience.
• Enhanced energy efficiency: SSIPs provide superior insulation, reducing energy consumption for heating and cooling, leading to significant cost savings.
• Reduced carbon footprint: SSIPs contribute to a cleaner environment by generating clean, renewable energy and reducing greenhouse gas emissions.
• Increased grid stability: SSIPs can help stabilise the grid by providing distributed energy resources and reducing peak demand.
• New economic opportunities: the production, installation, and maintenance of SSIPs can create jobs and stimulate economic growth in the renewable energy sector.
The versatility of SSIP technology makes it suitable for a wide range of applications within the utility sector:
• Utility buildings and substations: SSIPs can be used to construct energy-efficient and sustainable infrastructure.
• Remote and off-grid installations: SSIPs provide a reliable and costeffective solution for powering remote and off-grid installations, such as telecommunications towers and remote monitoring stations.
• Community energy projects: SSIPs can empower communities to generate their own clean energy.
• Grid-connected solar farms: SSIPs can be used to build large-scale solar farms, contributing to the nation’s renewable energy targets.
By embracing innovative technologies like SSIPs, Australian utilities can play a pivotal role in driving the transition to a sustainable and lowcarbon future.
As the demand for renewable energy grows, SSIP technology offers a promising solution to meet the energy needs of Australia’s growing population and economy. By working together, utilities, government and
industry can accelerate the adoption of SSIPs and create a more sustainable and resilient energy future.
For more information, visit deconcorp.com.au
Converge is the only Australian-owned event bringing together decision makers from the municipal works, civil and commercial construction and utilities industries to share knowledge and explore the future of the industry.
On 17-18 September 2025, Converge is set to host contractors, project engineers, council fleet managers and large-scale construction contractors working across the municipal works, civil construction and infrastructure sectors.
Being held at the Melbourne Convention and Exhibition Centre, the event will serve as a one-stop-shop for utility managers and subcontractors, with a focus on sustainable technology.
Converge sponsor, OPT HIRE, said that it is proud to support this inaugural event.
As a leading supplier of quality equipment for construction and traffic management, OPT HIRE is dedicated to leveraging its industry expertise and skills to provide innovative, sustainable solutions to the industry. These values align perfectly with Converge, which is why it has chosen to back the event.
OPT HIRE Business Manager, David Ewan, said that Converge promises to be a fantastic opportunity to connect with industry leaders and explore the future of the civil, construction and utility sectors.
“I am proud to lead a company that is committed to driving positive change in the civil, construction and utility sectors,” Mr Ewan said.
“At OPT HIRE, we strive to reduce carbon emissions and minimise our environmental impact for our clients.
“We are driven by three core principles: support, sustainability and innovation. By focusing on these areas, we aim to provide exceptional service, promote eco-friendly practices and continually explore new solutions to meet the evolving needs of our industry.”
OPT HIRE is a leading provider of construction equipment and services and has been at the forefront of the industry for more than 30 years.
“We’re driven by a commitment to sustainability and innovation, aiming to reduce carbon emissions and minimise environmental impact for our clients.
“We offer comprehensive support services, including equipment rental, maintenance and logistics to ensure seamless operations for our clients. By prioritising sustainability, we invest in eco-friendly equipment and practices to reduce our carbon footprint.
“Our commitment to innovation drives us to explore new technologies and solutions that enhance efficiency and reduce environmental impact.”
More than just an exhibition, the event promises an immersive experience that takes utility operators on a journey from the small scale to the large. Attendees can expect equipment showcases, live demonstrations and thought-provoking conference spaces offering invaluable insight to drive future development and maintenance across Australia’s utility networks.
Mr Ewan said that OPT HIRE hopes to leverage Converge to elevate brand awareness and showcase its commitment to sustainable construction practices.
“By sharing our expertise in powering construction sites with hybrid power solutions, we aim to foster knowledge exchange and collaboration with industry peers. Ultimately, we aspire to inspire positive environmental change by demonstrating the tangible benefits of reducing carbon emissions and minimising our ecological footprint.
“We believe that by working together with like-minded companies, suppliers, and stakeholders, we can identify new opportunities to innovate and drive sustainable solutions across the construction and utility industries.”
Mr Ewan said that Converge will positively impact all attendees, enabling companies like OPT HIRE to highlight significant technological advancements.
“We're particularly excited about the prospect of collaborating with other industry players to identify innovative solutions and drive sustainable practices. The event provides a platform to discuss emerging trends, share insights, and forge new partnerships.”
For more information, visit convergeexpo.com.au
Converge is Australia’s premier event for Sub-Contractors, Project Engineers, Council Fleet Managers, and Large-Scale Construction Contractors across the municipal works, civil construction and infrastructure space.
Through a mixture of live demonstrations, equipment showcases, and conference spaces, Converge will bring industry experts together to share knowledge and deliver solutions for building and maintaining Australia’s future. convergeexpo.com.au A new event for the municipal works, commercial and civil construction industries.
An update to the formal definition of microtunnelling means utilities can now adopt innovative, cost-effective solutions without compromising on quality.
Vacuum technology has been used successfully in microtunnelling projects in Australia for many years but has not previously been recognised in official definitions.
In September 2024, the International Society for Trenchless Technology (ISTT) formally included vacuum technology in its definition of microtunnelling – a change that follows efforts by Edge Underground Founder and CEO of OptionX Group, Stuart Harrison, in collaboration with the ISTT and the
Japanese Society for Trenchless Technology (JSTT), to bring clarity to this issue.
“I was approached by a member of the ISTT to look at the merits of a change of definition in microtunnelling to include vacuum technology, which to me, was a huge compliment to be given that opportunity,” Mr Harrison said.
“For years, companies using vacuum microtunnelling technology have faced challenges during project tenders, having to submit non-conforming bids just to use this method, despite hundreds
of kilometres of successful vacuum microtunnelling completed in Australia.
“To be given the opportunity to rewrite that definition and to put vacuum officially in as a microtunnelling method was an honour.”
Mr Harrison said that he was very excited to see vacuum technology be accepted worldwide.
“With the ISTT’s formal recognition, this technology can now be positioned on an equal footing, helping to streamline bid processes and allowing for greater competition in project tenders.
“This change represents a major development in the industry and could have wide-reaching implications, particularly as local Australian bodies and agencies begin to adopt these new standards. It also opens the world to the possibility of vacuum technologies and all their benefits.”
Vacuum microtunnelling offers significant advantages, particularly in consolidated ground or rock. It immediately removes broken material from the bore, leaving a dry, stable tunnel and reducing the forces required to advance the pipe.
“The beauty of vacuum extraction is that it clears the path for the pipe, so you’re only dealing with skin friction,” Mr Harrison explained.
“In rock, it’s even better – you eliminate regrind and reduce wear, saving time and money. Vacuum's ability to cut straight from the face gives you the minimum amount of pressure to be able to get a line from A to B.”
Although vacuum technology has been widely used in Australia, its global adoption has been slower. But with the ISTT now recognising vacuum extraction as a key method, the global industry is catching up to what Australian contractors have known for years.
Mr Harrison said that he recalled a project that he was a part of in the US in 2009 for BRH Garver Constructions, that exemplified the advantages of vacuum microtunnelling.
“They were doing a 450mm installation in a highly reactive clay and they had a 300t slurry microtunnelling machine. They started off on a 180m line, and halfway into that line they were stuck in the ground. 300t, nothing’s moving.
“They dug a shaft down at that point, and they created an interim shaft where they removed the tunnel head, and we went in there with an AXIS machine – a vacuum microtunnelling machine – and we set it up.
“The AXIS machine, much like the new AdaptX machine, sets out by putting a 350mm pilot line vacuum extracted through the ground. We pilot the next 90m of a 350 through the ground, and at no point do we come anywhere near our max thrust loads.”
Mr Harrison said that once this line was completed, Garver’s staff were concerned that the machine would struggle under the additional tonnage required for the next phase.
“We went about the upsizing process where we took it from 350mm to around about a 500mm bore to install the 450mm pipe. We did that the next day and at no point did we use more than five tonnes of jacking force.
“Now, when you compare 300t and you’re stuck in the ground to 5t and you’re moving freely, I think that says a lot about the benefits of a vacuum system. That is something that the world will continue to embrace and understand as we see more and more of this new wave technology hit the world market.”
Improvise, adapt, overcome OptionX Group’s new AdaptX is uniquely positioned to take full advantage of the ISTT’s new definition.
Unlike other drilling machines on the market, its modular design means it can be adapted for a range of drilling methods to best suit the conditions at the site and client specifications.
It can switch between various methods – vacuum, slurry, auger boring, pipe jacking and more – depending on the ground conditions, making it the perfect choice for contractors.
“AdaptX isn’t just about vacuum extraction," Mr Harrison said.
“It’s about giving contractors the flexibility to choose the best method. But when it comes to vacuum, AdaptX really shines.”
The AdaptX Mini features a torque range of 10,000 to 60,000 with a max thrust of 40t. The AdaptX Maxi has a max thrust of 125t and a torque range of 17,500 to 180,000. Other capabilities of the AdaptX include pressure air vacuum, HDD, displacement pilot, canopy tunnel drilling, pipe assist and pipe bursting. Torque and speed can also be adjusted to suit the job.
“With the updated definition of microtunnelling, utilities now have a clear path to awarding contracts that meet international standards and offer cost-effective solutions. This change enables utilities to consider bids that were previously non-conforming, reducing costs without compromising on quality.
“For end users, it means greater access to proven, effective methods that have long been used in Australia, now recognised as fully conforming.
“While the AdaptX machine offers multiple methods of operation, I firmly believe vacuum technology will prove to be the most effective. In fact, I’m confident we’re on the brink of a vacuum microtunnelling revolution! Nothing can compete with this technology, from consolidated ground to very hard rock.”
For more information, visit optionxgroup.com.au
Important developments in the utility industry – we round up the key appointments, resignations and other staff changes within the sector.
AEMO Executive General Manager, Western Australia & Strategy, Kate Ryan, stepped down from the role on 20 September 2024. On an interim basis, Group Manager Victorian Planning and Connections, Nicola Falcon, will lead AEMO’s Western Australian Division, while recruitment takes place.
Australian Energy Regulator (AER) Deputy Chair, Justin Oliver, has been reappointed to the board for a five-year term. Mr Oliver has been a Board member since 2020, and was first appointed as Deputy Chair in June 2024.
Aurora Energy has welcomed Trevor Danos as the new Chair of its Board of Directors, taking over from Acting Chair, Keryn Nylander.
Mr Danos also Chairs the Northern Sydney Local Health District, the NSW Treasury Social Investment Expert Advisory Group, the New South Wales Government Community Housing Industry Council, and sits on the boards of Endeavour Energy, the privatised New South Wales Land Registry Office and Viral Vector Manufacturing Facility.
Elly Patira has joined the Essential Services Commission (ESC), commencing her new role as a commissioner on 4 November 2024.
Prior to joining the ESC, Ms Patira was CEO of Aboriginal Investment NT, a corporate Commonwealth entity responsible for deploying $680 million in capital for the benefit of First Nations communities.
Rachel Watson has been appointed as Hydro Tasmania’s next CEO, following the retirement outgoing CEO, Ian Brooksbank. Hydro Tasmania Executive General Manager, Strategy, Erin van Maanen will continue as Acting CEO until Ms Watson officially starts on 14 April 2025.
In 2024, three new appointments were made to the NBN Co Board:
NBN Co CEO, Ellie Sweeney, has been appointed Executive Director for a threeyear term from 3 December 2024.
Kevin Russell has been reappointed as Chair on an interim basis for up to six months from 1 January 2025.
Nerida Caesar has also been reappointed as Non-Executive Director for a further two years from 1 January 2025.
Sydney Water’s Board has appointed Niall Blair as its new Chair, replacing outgoing Chair Grant King, who held the role for three years.
The appointment follows Mr Blair’s recent position as Director on the board of Sydney Water, with previous posts as New South Wales Minister for Water (2015–17) and involvement with Charles Sturt University.
South East Water has welcomed its firstever First Nations Delegate, Eveanne Liddle, a proud Arrernte/Luritja woman.
The utility has also made a new addition to its executive leadership team, with the appointment of Tim Lloyd as General Manager Service Delivery. Mr Lloyd commenced the role from 11 November 2024.
TasWater has appointed current Board Director, Kevin Young, as its next Chair, replacing outgoing Chair Dr Stephen Gumley AO who retired in November 2024 after 18 years in the role.
The Water Services Association of Australia (WSAA) formally elected four new Board Members at its AGM in early December 2024.
The new members, Melbourne Water Managing Director, Dr Nerina Di Lorenzo; Southern Rural Water Managing Director, Cameron Fitzgerald; Unitywater CEO, Anna Jackson; and Greater Western Water Managing Director, Maree Lang, will join re-elected Directors, Sydney Water Managing Director, Roch Cheroux, and Power and Water Corporation CEO, Djuna Pollard.
Water Corporation CEO, Pat Donovan, and SA Water Chief Executive, David Ryan, will remain on the Board.
Yarra Valley Water has appointed Yorta Yorta and Boonwurrung man Jamil Tye as its first-ever Independent Aboriginal Delegate to its Board of Directors.
Zinfra General Manager of Power Services North, Kevin Moloney, has retired after four years in the role. After a career in energy that spans more than 49 years, Mr Moloney stepped down at the end of December 2024 to spend more time with his family.
Zinfra Operations Manager, Chris Kelly, has been appointed as the new General Manager of Power Services North effective from 6 January 2025.
Australia is lagging overseas markets. Currently, new cars in Australia use 40% more fuel than the EU, 20% more than the US, and 15% more than New Zealand. Transportation accounts for approximately 19% of Australia’s total greenhouse gas emissions, and it’s on track to be the largest source of emissions by 2030.
However, the government is introducing fuel efficiency standards and a plan to accelerate the rollout of EVs nationally. State and federal governments are working to reduce emissions across their own fleets, and many businesses are too. Sustainability is good news for fleet managers. An efficient fleet isn’t just good for the environment, it’s good for business too. And telematics makes the change easier than ever.
By providing visibility over a fleet, managers can find ways to reduce costs and mitigate environmental impacts. Real-time analytics allow for immediate adjustments, leading to reduced carbon footprint and a move towards achieving environmental targets. Detailed data on maintenance, fuel consumption and driver behaviours can help businesses unlock more efficiencies. And by reducing unnecessary idling and optimising routes, telematics can help reduce emissions and operational costs.
Geotab’s Green Fleet Dashboard helps fleet managers monitor indicators ranging from fuel usage to emissions, and compares fleet fuel economy with a benchmark of similar fleets in the Geotab ecosystem. It provides the hard data needed to validate green initiatives to stakeholders and regulatory bodies.
As governments worldwide push for lower emissions, the transition to EVs is accelerating. In practice, EVs are more likely to be integrated into a fleet slowly, with managers transitioning when they retire their oldest and least efficient vehicles. Telematics makes it simple for managers to figure out which vehicles to replace, providing guidance on which EVs provide the greatest long-term financial benefits and environmental impact.
Geotab’s Electric Vehicle Suitability Assessment report offers fleet managers transparency by gathering data about a fleet and comparing it with the manufacturers data for EVs in each market. After making the switch, telematics can optimise range management, while remote monitoring and diagnostics capabilities allow access to real-time data, enabling prompt and effective vehicle maintenance.
Telematics stands at the centre of modern fleet operations and Geotab is committed to enabling real and measurable progress towards sustainability, while helping businesses manage their costs.
For more information, visit geotab.com/au/