
FEATURES
Changing of the guard
Upwardly mobile
Family ties
Electrifying waste management

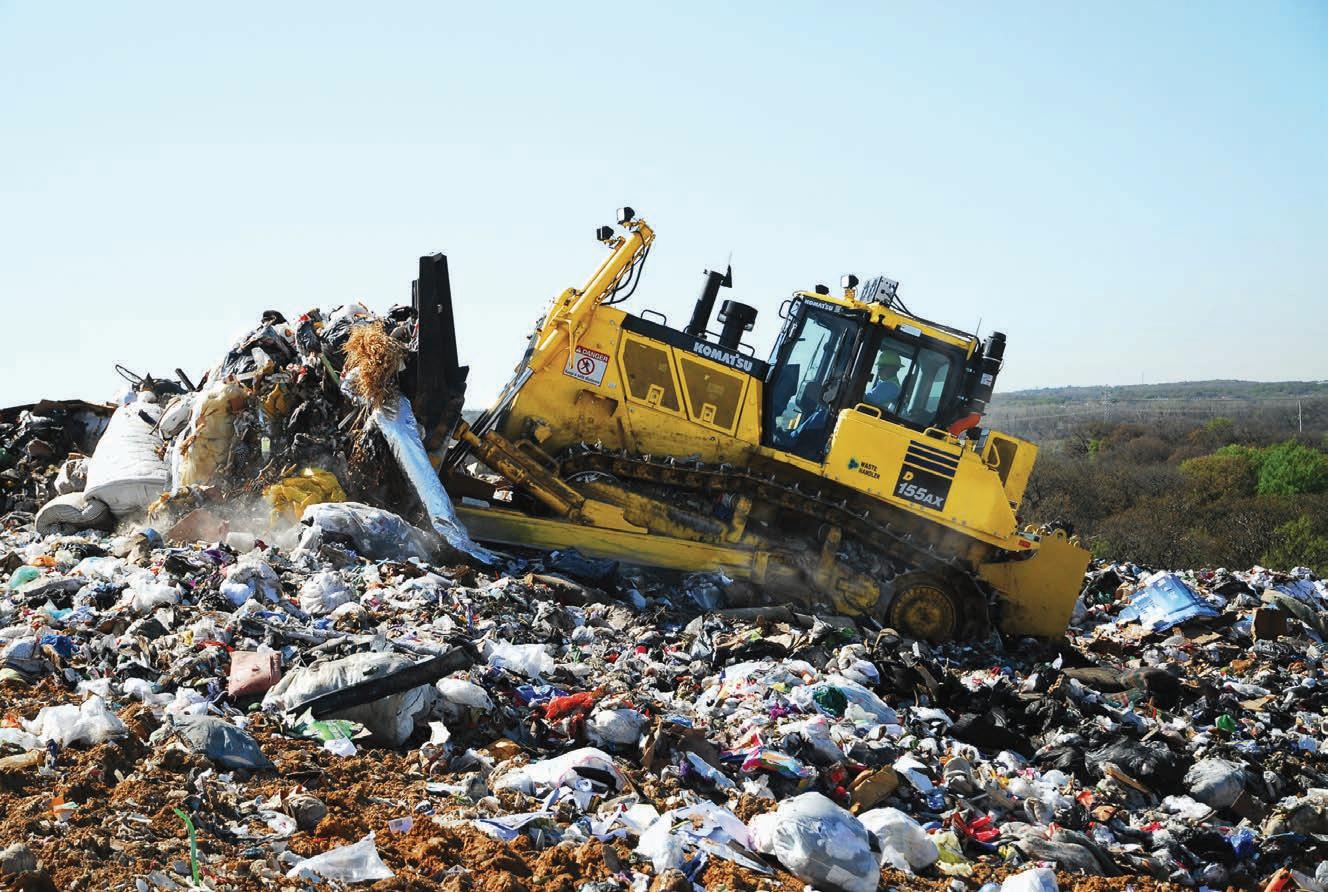

FEATURES
Changing of the guard
Upwardly mobile
Family ties
Electrifying waste management
The waste processing industry requires purpose-built equipment for moving highly variable materials. Komatsu creates machines and solutions designed specifically for the difficult terrain and materials involved with handling waste. Our advanced Dozers equipped with smart technology, are engineered for productivity to support your goals of a zero-harm environment.
How Komatsu is helping to overcome the challenges of waste management operations.
Lacey Webb’s journey from opera singer to becoming a voice for the
and resource recovery industry.
What
Deep
Lacey
An
One area of business sets
Using
Speedie
New
Examining the concerns, risks and management of forever chemicals.
New patented particle size reduction technology transforming waste into value.
“I
- Lacey Webb, Resource Hub Founder and Chief Executive Officer.
It’s a wrap at the Australian Organics Recycling Association 2024 Annual Conference.
How Volvo’s electric wheel loader is revolutionising the industry.
Who will lead Australia’s entry into
Next generation of machinery for
How Komatsu is helping to
Minimising environmental impact through innovative technologies and sustainable practices.
Who won the Women in Industry Awards?
A global audience and breakthrough products – what’s in store at Waste Expo Australia 2024.
Get ready for this year’s Waste Innovation and Recycling Awards.
“[We need to be] Intentionally not ‘gender badging’ roles, careers, or industries in our stories, because there really aren’t any ‘girls’ jobs’ or ‘boys’ jobs’ – there are just jobs.”
ey are powerful words from Anne Modderno, after being recognised for her excellence in transport at this year’s Women in Industry Awards.
Representing Swietelsky Rail Australia, Anne is the rst female Managing Director of any Swieteslky International subsidiaries. It’s a huge step toward empowering women in previously male dominated industries.
And she’s not alone. As more industries aim to inspire gender inclusion and expression, women are stepping out of the shadows and into top jobs.
In this month’s edition of Waste Management Review, we talk with some inspiring women who have purpose, believe in what they’re doing, encourage others and think big.
And no one thinks bigger than the focus of our cover story. Lacey Webb shares her journey from being “the person behind the person”, to leading a successful waste management consultancy rm.
We also speak with Nikita Sharma and Victoria McKay who are at the coalface of an innovative solution for leachate for environmental solutions provider BeneTerra, and Jessica Barilla, who is steering a statewide waste and recycling business into a new era.
en there’s Tiana Nairn, who was at the forefront of signi cant waste policy and law reforms for the South Australian Environment Protection Authority, who is now leading the LMS Energy policy team considering waste, circular economy and carbon-related laws across Australia and New Zealand.
And of course, there’s a full wrap of all the winners from this year’s Women in Industry Awards. We hope that by shining a light on women in waste, it will give others the con dence to achieve anything.
“ e earlier our daughters, nieces and granddaughters hear about what types of jobs and careers are out there for them, the less likely they are to be intimidated by an industry or doubt themselves in any way,” Anne says ….
“Future generations will know no limit.”
Happy reading.
CHIEF OPERATING OFFICER
Christine Clancy christine.clancy@primecreative.com.au
PUBLISHER
Sarah Baker sarah.baker@primecreative.com.au
MANAGING EDITOR
Lisa Korycki lisa.korycki@primecreative.com.au
JOURNALIST
Chris Edwards chris.edwards@primecreative.com.au
DESIGN PRODUCTION MANAGER
Michelle Weston michelle.weston@primecreative.com.au
ART DIRECTOR
Blake Storey blake.storey@primecreative.com.au
DESIGN
Laura Drinkwater
BRAND MANAGER
Chelsea Daniel chelsea.daniel@primecreative.com.au p: +61 425 699 878
CLIENT SUCCESS MANAGER
Justine Nardone justine.nardone@primecreative.com.au
HEAD OFFICE
Prime Creative Pty Ltd
379 Docklands Drive Docklands VIC 3008 Australia P: +61 3 9690 8766 enquiries@primecreative.com.au www.wastemanagementreview.com.au
SUBSCRIPTIONS
+61 3 9690 8766 subscriptions@primecreative.com.au
Waste Management Review is available by subscription from the publisher. e rights of refusal are reserved by the publisher
ARTICLES
All articles submitted for publication become the property of the publisher. e Editor reserves the right to adjust any article to conform with the magazine format.
COVER
Cover image: Wild Rhubarb Photography
COPYRIGHT
Waste Management Review is owned by Prime Creative Media and published by John Murphy. All material in Waste Management Review is copyright and no part may be reproduced or copied in any form or by any means (graphic, electronic or mechanical including information and retrieval systems) without written permission of the publisher. e Editor welcomes contributions but reserves the right to accept or reject any material. While every e ort has been made to ensure the accuracy of information, Prime Creative Media will not accept responsibility for errors or omissions or for any consequences arising from reliance on information published. e opinions expressed in Waste Management Review are not necessarily the opinions of, or endorsed by the publisher unless otherwise stated.
With its multi-rotor design the Genox J-series pipe shredder easily shreds HDPE pipes of all sizes.
When combined with a Genox washing plant and Genox pelletising system, you can truly close the loop on HDPE pipes. Pipe to pellets. Pellets to pipe. This is the circular economy in action.
Genox make world-class recycling solutions, for real-world recycling applications.
The Breakdown is a monthly column giving industry leaders and decision makers a chance to share their views on topics central to the sector.
This month we asked: “How is your organisation contributing to zero emissions targets?”
Tara Osborne
General Manager – Strategy and Innovation
Bingo Industries
Our pathway to decarbonisation is underpinned by partnerships and collaboration across industries to achieve a common goal.
At BINGO, we’re passionate about working with our suppliers, customers, and stakeholders in pioneering innovative solutions to optimise recycling and reuse of waste by producing new products, or finding alternative use for materials to reduce the reliance on virgin materials.
We continue to invest in recycling infrastructure to build further capability to achieve more sustainable outcomes and our vision of a waste free Australia. Collaboration is essential as we push to accelerate the transition to a circular economy.
John McKew
National Executive Officer, Australian Organics Recycling Association (AORA)
Organic recycling plays a crucial role in mitigating greenhouse gas (GHG) emissions.
The total estimated GHG savings from organics recycling of materials received in Australia in 2021-22 was about 3.9 million tonnes of carbon dioxide equivalent (CO2-e) – about 5.8 million trees that would have to be planted to absorb the same amount of CO2 or the GHG emissions that 902,311 cars would produce in a year.
By diverting organic material from landfill and promoting practices such as composting, we can achieve significant environmental benefits.
Composting transforms organic matter into valuable resources. By diverting from landfill, this results in reduced methane emissions, a potent GHG produced during organic decomposition.
Organic recycling isn’t just about waste management; it’s a powerful tool for emission reduction, fostering a more sustainable and resilient future.
Dr Johann Glueck
National Sustainability Manager
Hanson and Alex Fraser
We are committed to working with the Australian construction industry towards achieving carbon-zero.
Our work is guided by our national Sustainability Charter; underpinned by Heidelberg Materials’ Sustainability Commitments 2030.
The practical application of our Sustainability Charter is demonstrated through our resource recovery and recycling of materials into reusable resources.
We remain firmly focused on reducing our carbon footprint and improving customer outcomes.
If you or someone at your organisation is an industry leader and would like to be a part of this monthly column in 2024, please get in touch with Editor, Lisa Korycki lisa.korycki@primecreative.com.au
Pure Environmental is a wholly Australian-owned company founded with the mission to transform the circular economy through advanced resource recovery. We believe in pushing boundaries and challenging norms in waste management, providing exceptional, innovative, and sustainable solutions. Scan Code
Rural and regional Australia have their own challenges in managing waste streams. Waste 2024 Conference looked at some of the struggles and how they are being tackled.
With 537 local councils across Australia, more than half are regional, rural, or remote. In New South Wales, that gure is 72 per cent (93 of 128 local councils), managing about 98 per cent of the state’s land area and 38 per cent of the population. at creates unique challenges for regional councils despite their geographic in uence.
Guada Lado is the Manager of Regional Waste at Armidale Regional Council. Having spent much of her waste career in the Sydney metropolitan
context, she believes in implementing multidisciplinary thinking and solutions to solve the challenges of the future.
“Armidale Regional Council has many challenges regarding waste management,” Guada says. “Waste was not the most important thing for the council when I arrived. ey provide water, sewage, and a range of other services. It runs an airport, childcare centres, aged care centres, and its own agricultural service.”
With those competing priorities, everything appears important, and very little is pro table. Community expectations are signi cant in a regional
council, and being isolated makes things a challenge. However, councils work hard to achieve positive outcomes for their residents.
“Armidale Regional Council has the newest land ll in Australia, 12 kilometres outside the city centre,” says Guada.
“Council operates in-house land ll management, implementing high-tech lids to maximise space at the land ll. Procurement has also been a focus, with new contracts for recycling collection, with garbage and food organics, garden organics (FOGO) under a di erent contract. at improved
our technology across the system to streamline service collections.”
Route optimisation software is one area where the council is improving its e ciency and introducing community recycling centres. e sale of compost from resource recovery, along with crushed concrete, can generate funds for the council. e introduction of crate recycling has meant more than 3000 tons are processed each year, with less than 80 tonnes redirected to land lls due to contamination.
Giles Perryman is the Director of ASK, which provides consultancy services for regional and rural customers. Most recently, ASK developed Cooee, a gatehouse data solution for small to medium-sized facilities.
“We pride ourselves on providing solutions to rural customers,” Giles says. “It’s why we developed Cooee, to provide better data for those councils.”
A rural transfer station must consider a range of factors, including access and control, sta ng, safety, maximising recovery, and e cient operations.
It needs to be a resilient system that can handle anything. If an old land ll is being replaced with a modern transfer station, does it have power, water, and mobile signals? How close is it to the main population centre? Is it close to the point of waste disposal?
“Access, oversight and control are determined, in part, by the size of the transfer station,” Giles says. “Sta ng a transfer station with limited opening hours is probably better. Introducing automated remote entry systems can also help. It’s critical to design a controlled entry and exit system while minimising contamination for residents.”
Maximising resource recovery comes mainly from the initial layout of the facility. Having the correct pricing and signage are both crucial aspects to
consider. Sta guidance and oversight can explain and educate the community. It’s also critical to consider how sta can do a second sort of the materials to reduce contamination.
“We have aggregated data for hook lift bins,” Giles says. “On average, a hook lift bin has between 1.7 to 3.75 tonnes, making them fairly ine cient. If you have the option to introduce technology to improve the economics, how do we go about doing it?”
Giles says that Cooee is built for rural facilities to provide the information needed for managers to monitor facilities, report data, and make data-based decisions. at data can include usage times, volume of material, voucher use, gate fee take, and operational checklists.
Kylie Jacky is a Nyangbal Bundjalung woman and the Lead for Aboriginal Initiatives at the New South Wales Environment Protection Authority (NSW EPA).
For more than 20 years, she has led many government strategies and initiatives across a range of sectors to improve outcomes for Aboriginal people and communities. She is also invested in her local community of Ballina and Cabbage Tree Island, volunteering and supporting land rights, protecting culture and heritage, and promoting the health and education aspirations of the local community.
Embedding First Nations knowledge and culture into an organisation can be exciting and dynamic work. Kylie says building relationships with Aboriginal people has helped maintain relationships across Country. at’s why having an Aboriginal Initiatives Team at the NSW EPA is so important.
“One of the rst things we wanted to do was to make it visible and clear that the team exists,” Kylie says. “We were gifted some beautiful art for our visual
identity, that also provides a language and cultural interpretation of what the team does. We held 18 Yarning sessions with the EPA during NAIDOC Week 2021 while still in lockdown.”
Healing and caring for Country were considered essential parts of the NSW EPA’s work, even if the authority was unaware of it. Having that connection to the Country started with listening through these Yarning sessions.
is led to the foundational blocks of a dynamic journey for bringing Aboriginal knowledge and culture into the organisation.
“We are still doing a lot of foundational knowledge,” says Kylie. “However, it’s about embedding that knowledge and ensuring the surety of Aboriginal culture into the organisation. One of these is our Statement of Commitment to Aboriginal Peoples.”
While this statement was a good start, it required the NSW EPA to continue communicating with Aboriginal peoples across the state. Its symbolic nature has 12 concrete principles that can be easily actioned. It is a connection between Western and Aboriginal thinking – they can work together, and it has been a game changer for NSW EPA.
e creation of an Aboriginal Peoples Working Group has provided an opportunity for the NSW EPA to give Aboriginal peoples a voice while also listening to them with every bre of their being, Kyle says.
Jonathan Beckett has almost 30 years of operational, managerial, business development, and consulting experience within the waste industry. He understands waste management strategy, legislation, policies, principles, and practices across Australia and is the Waste Team Lead (New South Wales) for Talis Consultants.
He looked at the feasibility of a regional circular economy centre of
How does a classically trained opera singer wind up as a waste levy expert and a voice for waste and resource recovery operators?
Lacey Webb didn’t wake up one morning wanting to own a waste management consultancy. Like many in the industry, she fell into it.
And she fell into it in a big way. e girl from Ipswich, who loves maths and data, has taken “all the boring stu that saves money” and grown a waste management consultancy with a focus on waste levies and a reach across Australia.
Four years since its inception, Resource Hub boasts an impressive resume, working with 90 per cent of waste levy zone facilities in Queensland alone, plus more facilities each week
across New South Wales, Victoria, and Tasmania, as well as South Australia and Western Australia. Resource Hub helps them become more nancially and operationally e ective and comply with waste levy and auditing regulations.
at’s more than 300 waste sites visited, and more than 10 million weighbridge transactions audited.
But Lacey is most proud of how quickly Resource Hub has embedded itself in the market – and that it’s not just “the Lacey show” any more.
“One of the measures of success when I started was how quickly the brand
would just be known as Resource Hub,” she says.
“For so long people would say, just call Lacey but within three years, I’d gone from being Lacey at Mandalay Tech to Lacey at Resource Hub, to someone asking, ‘so who owns Resource Hub?’
“I liked that, because it meant we’d grown the right way. It shouldn’t be the Lacey show. We’re more than that. We’re working hard to service the industry. We are not the big four. We are 13 people working across Australia, with one of us even working out of a caravan.”
Ipswich, in southeast Queensland, is a coal mining Labor heartland with an active art and cultural scene. Lacey’s family goes back six generations – they were the rst publicans and owned the largest dance studio in town for many years.
Having trained in dance and as a classical opera singer, she admits to being a little di erent from her family because she was a natural at maths and science as well as music and humanities. But, it wasn’t until she was at university that she decided there was no money to be made as an opera singer in Australia, and instead became a Certi ed Practising Accountant (CPA).
It was with this focus on her nance career that Lacey took what she thought was a job in property development at BMI Group in Brisbane.
“Four weeks in, I realised property was a tiny piece of what BMI did and I very quickly fell in love with the waste industry and the people,” she says.
Over two decades, Lacey held roles as Financial Controller, Chief Financial O cer (CFO) and later as a Consulting Lead within the waste and resource recovery sector. She says those roles gave her a keen insight into the industry and helped her identify a gap in the market.
While she helped people re ne their data and process in her role with software leader, Mandalay, she often spent more time discussing levies, operational e ciency and how to make facilities work.
“ ere aren’t a lot of organisations that focus on how to make their processes work so they’re being as e cient and pro table as possible while still meeting big strategy commitment,” Lacey says. “All the boring stu that makes you money.”
Enter Resource Hub. Resource Hub exists to work with local and state governments, and commercial waste organisations, to improve their business processes and their levy management.
e team o ers project-based consultancy work and ongoing remote support within regulation and waste levy, data administration, and operations.
Lacey describes it as an extra set of hands to help a business work more e ectively, whether that’s doing the job for them or upskilling sta to help them perform the task.
“We don’t have a business to deliver work that someone can do on their own; Resource Hub wants to ll a gap to make someone’s life easier,” she says.
While she has set out to make things easier for others, building a successful waste consultancy has its challenges. Surprisingly, one of the biggest was talking to people.
Despite decades of industry experience, Lacey was often the person behind the person and, as such, was relatively out of the spotlight. Since starting Resource Hub, she’s worked hard to build a pro le by attending conferences, visiting sites and building networks. e shift in dynamic is not one that she’s always been comfortable with though.
“Everyone who knows me knows I can talk,” she says. “But I struggled to talk to people about our brand and services. I’ve
learned to focus on other people’s challenges though, and have a chat instead.”
e other challenge was getting the company structure right. Resource Hub works on subscription based, repeatable services and as-needed projects that tend to be smaller than traditional waste consultancies. While that’s been deliberate so the service o ering is highly targeted and the team stays within its wheelhouse, it has been di cult to make it clear to the market what they do, and what they actively chose not to deliver.
But they’ve struck the right balance, and Resource Hub has embedded itself in the market. Most of the work is supporting regional facilities, and the team gets a lot of joy from knowing that it can add a little bit of help or extra time to get some big outcomes, especially for quite rural councils.
“I don’t think there’s anyone in Queensland who doesn’t know who to ring about a waste levy,” Lacey says. “More importantly, it’s not ‘ring Lacey’, it’s ring Resource Hub. I like that. It speaks to the breadth of knowledge that our team has. I like the trust the industry has, and that this is now expanding to the service o ering and team.”
And team is clearly a priority as, Resource Hub is all about the people. While the team has broad industry experience, personality and the right t are foremost. at doesn’t mean being another Lacey, or being super outgoing. It does mean actively wanting to help someone make their day a little easier and take the pressure o . Team members have come from local government areas, industry and even from the regulatory authorities.
As Resource Hub continues to grow, Lacey seeks out people from within the industry who want to make someone’s day job easier.
Case in point: In 2023 Resource Hub delivered waste levy and gatehouse best practice training to more than 60 local government teams in addition to commercial operators, and it prepared waste levy returns every month for more than 100 facilities.
It also worked closely with a client for 18 months to de ne a new data approach for their region.
“It’s taken a lot of time, e ort and money, but now, nearly two years on, that customer has more than three million dollars in funding coming back
from the state because we’ve been able to x the data, build a story around why an issue happened and support why the funds should come back,” Lacey says. “We’ve done that 15 times over with our client base.
“Last year, we managed $9 million of local government adjustments relating to the waste levy or contractual or nancial risk – that’s only local governments. We’ve also had some big wins for commercial operators because we take the time to look at the boring data. It’s the boring stu . But it’s critical.
“We undertake operational e ciency audits, take what facilities do well and set that as a benchmark.”
Lacey says there’s meaning in seeing the value you can have in changing a process. at resonates within the company through a people- rst approach. e aim is to make work as suitable as possible for whatever life an employee needs, including exible hours or a change of role. Lacey’s seen the challenge parents, particularly women, struggle with when they aren’t a orded the exibility they need in a job.
“There’s great talent out there that can’t work full-time hours, and I’ll be exible to get that,” Lacey says. “ ose people are my people.”
When it comes to talent, the waste and resource recovery sector is in good hands.
ere’s always been a depth of female talent within the industry, and those women are now breaking through the glass ceiling and taking on more leadership and chief executive roles. at is inspiring the next generation of women to view the industry as a growth sector with many opportunities.
Lacey describes her own journey as a baptism of re. ere were some tough conversations and plenty of times when she was the only woman at the table and undervalued herself.
But she says she’s also had people who pointed out her value.
“ ere is a piece that exists being a woman in this industry; you can’t escape it,” she says.
“But regardless of who you are, our industry is hugely accepting.”
Resource Hub has grown quickly, and the team has worked hard to ensure that any growth doesn’t a ect the clients who have been with them from the start.
But that growth has also a orded new opportunities. At the 2024 Waste Conference in Co s Harbour, Lacey and Resource Hub unveiled AUDRRI, a new software program that analyses a facility’s processes and benchmarks them against best practice standards of operational and regulatory e ciency and e ectiveness.
While AUDRRI is still only for internal use, a new service o ering, AUDRRI
Onsite, is in development to allow facilities to self serve, and improve their own outcomes.
Lacey says Resource Hub will always be there as a helping hand. But she may not.
“One of the reasons I’ve been successful is I that I like to have a plan,” she says.
“As Resource Hub continues to grow and provide services, there will come a point where I want a new challenge, and there are team members here who want the opportunity to lead.
“I want someone else to have the opportunity to be the face for a while and maybe I will go and solve something else.”
And does that something else involve singing?
Until this year, Lacey’s father was the president of his RSL chapter, so she performed at the occasional Anzac Day dawn service in Brunswick Heads, but there’s no time for rehearsals anymore. Resource Hub instead sponsors several dance and music events.
“Despite leaving Ipswich – the home of Queensland’s largest waste volumes – I now own a company servicing those major land lls, and I sponsor the Ipswich dancing Eisteddfod,” she says. “You can take the girl out of Ipswich, but you sure can’t take Ipswich out of the girl.”
For more information, visit: www.resourcehub.com.au
At STG, our primary goal is to provide innovative and dependable products, and our waste truck fleet is no exception. Our state-of-the-art waste trucks feature a patent-pending modular design that excels in efficiency without compromising load capacity.
Advanced technology that enhances performance and efficiency, with a single-screen interface and in-cab controls for easy operation.
Designed for minimal downtime, with accessible components and expert support from STG.
Carry more waste with fewer trips, enhancing your operational efficiency.
Tailor your waste truck with our versatile modules to meet specific requirements.
Reliable and comprehensive support to keep your trucks running smoothly, with dedicated service teams and readily available spare parts. Our remote dial-in feature allows STG engineers to diagnose and resolve issues remotely, minimizing downtime.
An innovative solution for leachate is now accessible in even the remotest landfills in New South Wales.
Environmental solutions provider BeneTerra is mobilising its waste management team.
e New South Wales Environment Protection Authority (NSW EPA) recently granted the Queensland-based company a mobile treatment licence to deploy its BeneVap technology to manage leachate at land lls across the state.
Victoria McKay is the Project Manager for BeneTerra’s waste management sector. She says it’s a win for land ll operators seeking an environmentally and economically sound solution to leachate management.
By actively reducing the total leachate volume that a site needs to manage, BeneTerra’s BeneVap technology reduces the cost and risk associated with onsite passive evaporation ponds or sending leachate, either by trucking or direct connection, through a sewer system.
“ is style of licensing means these types of advanced management techniques are no longer only feasible for the big players with the time and budget to put into lengthy licence amendments and capex projects. It’s a win for the small-to-medium land ll operators who are nding it harder to access even the more common leachate management options and technologies as disposal costs rise and emerging contaminants become problematic for sewer operators,” Victoria says.
Leachate is formed when rain lters through the waste placed in a land ll. If it’s not adequately managed, it can leak pollutants, including heavy metals
and per- and poly uoroalkyl substances (PFAS) into groundwater or stormwater systems, damaging the environment directly or leading to bioaccumulation in the food chain.
Additionally, common characteristic of leachate, including high nitrogen or suspended solids, can upset the biological processes of the sewerage treatment plants that often don’t have capacity to accept the volume of leachate being managed by land lls daily as a result of legacy leachate issues.
Victoria says the adoption of better land ll design, retro tting capture systems into legacy wastes, and improvements in land ll operations practices has triggered a greater awareness of contaminant management in land lls. However, as land ll operators get better at capture and containment of leachate, the cost and environmental impacts of managing these higher volumes using traditional methods needs to be acknowledged.
e push to obtain a mobile licence for BeneTerra was based around councils
serving small-to medium populations and those in regional settings, allowing them use of the technology without the need to approve the signi cant capital investment of a connection to sewer or pond, or solely relying on a trade waste agreement as the regulatory space evolves.
It’s been a four-year process, but BeneTerra is now believed to be the only company with a mobile treatment licence for leachate in New South Wales. is means clients can use the BeneVap technology in their land ll for up to six months every calendar year without requiring direct amendments to their site environmental licence.
e BeneVap was an adaptation of a submerged combustion technology initially invented as management technique for piles of cleared salted snow in the United States. With BeneTerra’s version of the technology, the process can be used to reduce the volume of leachate handled on-site by between 90 and 95 per cent.
e system evaporates the water component of the leachate, leaving behind a more benign form of the original contaminants which can then be safely returned to the land ll containment cell. Unlike a kettle evaporating water, BeneTerra’s technology doesn’t bulk boil the leachate to drive
o the water vapour and it also isn’t a pressure vessel, making it safe to operate physically and environmentally.
BeneTerra Chemical Engineer Nikita Sharma worked closely with NSW EPA throughout the licence application, answering technical questions about the environmental impacts and how the BeneVap process works. is ensured that the NSW EPA was satis ed the technology was safe to use across the range of land ll types.
Nikita, who also has a Masters degree in Environmental Engineering, devised a site-speci c risk assessment framework to guide the mobile licence’s process and monitoring practices. is framework will ensure environmental protection for every land ll site using the technology.
“ e waste characteristics in land ll will determine the leachate chemistry, its contaminant levels and volumes,” Nikita says. “We match our operations to the speci c leachate and site characteristics and model our emissions pro le to give each site and the regulator con dence in the unit’s capability.”
e BeneVap system was rst used in Australian land lls to remove leachate after extreme rain events in southeast Queensland in 2017. e success of that project has led to its deployment across more than 12 land lls across the east
coast of Australia, Northern Territory, Tasmania, New Zealand, and the USA to ensure contaminants don’t enter the environment.
BeneTerra’s in-house engineering team continues to improve the technology as market pressures evolve. One improvement was developing the machines to run on a variety of fuels including land ll gas. is means land ll operators who participate in an Emissions Reduction Fund project, capturing and combusting their land ll gas, can claim carbon credits while managing their leachate using a BeneVap.
Victoria, who will lead the mobile operations, has a perfect alignment of passions and experience – she has a PhD in organic chemistry and worked for several years in Bundaberg Regional Council’s waste operations team, following this up with a stint in the land ll gas industry.
“Having worked for a regional land ll operations and compliance team, I have experienced what it’s like to try and nd leachate solutions that meet compliance requirements, are practical, and don’t add budget pressure on a community,” Victoria says.
“Understanding that land ll gas is a resource and being aware of the practical and nancial value of it, the BeneVap is a nice combination of those two concepts.”
BeneTerra has been solving di cult wastewater challenges in Australia since 2010, drawing on the experience of a team of scientists, engineers, regulatory experts and contractors.
Tony Stapleton, Chief Executive O cer, says the team understands the complexities of environmental sustainability and tailors solutions to meet the unique needs of clients across the di erent industries the business supports.
is involves rst looking at the chemistry then a detailed understanding of the environmental impacts and conditions of the local site.
He’s con dent the mobile treatment licence for leachate will have wideranging bene ts, given the increasing focus on environmental outcomes and regulatory restrictions.
“We’re always looking for technological or engineering solutions to the problems the industry faces every day,” Tony says.
“With BeneTerra’s team today and the technology, we’ve got enough runs on the board in land ll management in Australia and New Zealand to know that this treatment has applicability across the entire industry.
“It’s our mission to ensure that contaminants in wastewater do not negatively impact the surrounding environment whether that be air, local water/groundwater or soils.”
For more information, visit:
LMS Energy is at the forefront of methane abatement and renewable energy solutions.
One of Australia’s largest emissions reducers
100% Australian owned and operated
Partners with over 40 local government organisations at landfills
Full in-house business model (incl. local manufacturing)
40 years industry experience
Impeccable safety and environmental compliance record
Circular economy solutions
Anaerobic digestion technology for organic waste
Renewable gas and electricity
Leachate services
Wastech is a well-established player in the waste management and resource recovery sectors, known for its design, engineering, and manufacturing services. However, one area of the business sets it apart from the rest.
With an extensive product range and an end-to-end service o ering, Wastech supports a diverse range of businesses and governments that want technologyenabled solutions to manage waste and resources e ectively and e ciently. It is committed to sustainability and innovation across multiple business areas.
Wastech’s consulting arm focuses on aligning its clients’ development goals with best practice design to achieve sustainable outcomes. is includes supporting operational waste and resource management plans, construction and demolition resource management plans, green star reporting, early engineering design,
educational programs, and operational e ciency audits.
Djanisa Trinder is Wastech’s National Consultancy Manager. While she didn’t plan on entering the waste management industry, she has developed a fond appreciation for it.
“It has tied in beautifully with my love of the environment and all things sustainability,” says Djanisa. “I’ve been working in the sector for 11 years and cannot imagine being elsewhere now.”
Wastech has only recently re-started its consulting arm. Djanisa advises that the consulting business enables Wastech to reach clients earlier in the project life cycle ensuring a better nal product and outcome.
“ at starts at the concept and planning phase,” she says. “We work on all types of developments, whether residential, retail, utilities or other key pieces of infrastructure. We like to get involved nice and early and work closely with many di erent modalities to meet the project’s scope.
“By drilling down on di erent aspects of the project and collaborating with other experts, we can develop bespoke solutions for each client on a project-by-project basis.
“When I started 11 years ago, it was common to receive a phone call from a developer who wanted a one-page waste management plan, following
“I see us pushing the boundaries of the industry, challenging the status quo and providing solutions for things that the industry has been seeking for quite some time.”
Djanisa Trinder, Wastech National Consultancy Manager
the approval for their development application from the council,” says Djanisa.
“We have developed a long way since then because we are working with clients and they understand that in order to get a good outcome Wastech needs to be involved early. I think the industry is also beginning to appreciate the crucial role we play in determining the future success of waste and resource management infrastructure.”
Another challenge is con icting priorities with regards to developers’ nancial yield expectations. From a developer’s perspective, waste management infrastructure does not generate a return, hence they want the smallest physical footprint possible. is can lead to compromised operational and nancial life cycle outcomes.
Djanisa encourages them to give her the minimum space she needs to achieve the goal.
“My nearly daily challenge is talking about this with developers,” she says. “I usually present them with three options. e rst option is to give me the space I am requesting. e second option is for me to acquiesce to their land o ering. e impact of this is that the development can incur signi cant additional operational expenditures per year. at’s because they rely on
more frequent collections and have more operating personnel. e third option is to wait for a few years, realise your solution is not working, and spend, signi cant expenses on a retro t solution.
“It’s all about talking to them in terms and a language they understand to help connect with them at their level. at applies to a developer, an architect or even the local council.”
In developing bespoke solutions for its clients, Wastech has considered sustainability and the United Nations Sustainable Development Goals (SDGs) for 2030.
“Some SDGs extend into 2050, such as the Sustainable Development Solutions Network, e World in 2050 (TWI2050). We need to keep an eye on industry best practices, the guidelines around them, and how to apply them to our client’s projects,” Djanisa says.
“It’s not just looking domestically. We need to see what is happening overseas and determine whether it could apply here. Some of our clients have asked about technologies that have worked overseas, which means we need to study them. Can they work in this application, or will they fail? Applying the same technology
here won’t necessarily work because of economic, infrastructure and geographical di erences.”
Sustainability extends to reduced need for maintenance, and this saves time and money.
“One thing I have noticed is that our clients praise us for the quality of our products,” she says. “Our clients keep coming back to us time and time again. Some of them have had waste compactors for 15 years or more. Even if they haven’t maintained the device as well as they probably should have, it’s still working extremely well. e upfront cost saves them signi cantly in the long run, as they are not replacing the product after ve years.”
e Boots theory of economics, made famous by Sir Terry Pratchett, does apply in this situation, as Wastech’s customers can be con dent that they have high-quality machines and a responsive customer service team.
“Being responsive to customers is something that I and our entire service team pride ourselves on,” Djanisa says. “It’s another reason why people choose Wastech. If they tell us about a problem, we are out there as soon as possible to x or troubleshoot it.”
As an industry expert, Djanisa sees Wastech continuing to expand and push boundaries, providing solutions the industry has long demanded.
“If I don’t know the answer to your question, I’ll nd out, and then we’ll both be in the know,” she says.
“I do see the consulting business growing and being its own beast as such, humming away. I see us pushing the boundaries of the industry, challenging the status quo and providing solutions for things that the industry has been seeking for quite some time.”
For more information, visit www.wastech.com.au
The Phoenix is an extraordinary mythical creature. At the end of its life when just ashes remain, something magical happens. New life merges out of something that seems lifeless. What we consider to be the end, suddenly transforms into a new beginning. We give ash a new life in the real world.
The ash in our line of business comes from the new Energy-from-Waste facility Avertas Energy. Incineration of municipal solid waste (MSW) is an effective way to reduce waste volume and reduce our reliance on fossil fuels for energy.
We process the remaining ash and extract valuable resources. With our state-of-the-art technology we recover metals to produce a secondary aggregate used for civil construction work. Environmental protection is at the forefront of our day-to-day operations. We assure the proper use of aggregates, limiting the impact on the environment.
We believe our work is only valuable if it contributes to a better future. We prevent landfilling and the negative impacts associated with the extraction of virgin raw materials by producing a secondary aggregate that contributes to the circular economy.
Having the right systems in place is vital to driving waste avoidance and higher-order outcomes. Tiana Nairn is using her strategic and policy experience to examine where we are today, where we want to be, and how we get there.
People rarely end up doing the exact kind of job they imagined for themselves when they were 15 years old.
Tiana Nairn grew up enamoured by British biologist and natural historian Sir David Attenborough’s work. She was exposed at a young age to environmental activist David Suzuki and his research into environmental conservation. So, it was no surprise when Tiana opted to study science and environmental law at university.
A strong belief that good policy matters has since seen Tiana at the forefront of signi cant strategic waste policy and law reforms for the South Australian Environment Protection Authority (EPA). She’s now leading the LMS Energy policy team, considering waste, circular economy, and carbonrelated laws across Australia and New Zealand.
“I studied under an eminent professor who did some groundbreaking investigations into South Australia’s arid lands,” Tiana said. “I thought I could trust people like him to do the investigation, but wondered how identi ed needs were then pursued?
“Applied policy goes into the details. It examines the options, opportunities, and barriers from A to B. It works to achieve goals on a uni ed level.
“Within the waste and recycling industry, we have a lot of good opportunities to help create practical policy that protects our environment.”
Tiana’s work with the South Australian EPA has led the way for improvements to waste laws in Australia. e state-mandated resource recovery of most waste and selected land ll bans were well ahead of national e orts. e laws introduced important o ence provisions that made tackling illegal dumping a simpler task than it had been previously. ey later extended powers and opportunities in that space.
“ e South Australian Government has been progressive in stepping forward and empowering regulation to act directly on waste versus some of the more general pollution laws,” Tiana says. “It was exciting to be part of that.”
After 21 years in government, Tiana moved to LMS Energy, seeing the opportunity to help more directly reduce carbon emissions to the atmosphere. LMS Energy exists to
protect the environment from the impact of waste and is Australia’s leading methane abatement and bioenergy company.
Recognised as an innovator, the company’s ‘ rsts’ include purifying biogas for injection into gas networks in 1988, generating electricity from biogas in 1990, generating carbon credits from biogas in 2000, and installing Australia’s rst solar project built on a land ll site in 2017. e recovery of land ll biogas reduces methane emissions and provides a reliable renewable energy source. Across 67 sites in Australia, New Zealand and the United States, LMS Energy captures harmful methane and converts it into clean, reliable, renewable energy or destroys it using ares.
Each year, LMS Energy abates greenhouse gases equivalent to nearly ve million tonnes of carbon, making it the largest carbon abatement company under Australia’s Emissions Reduction Fund. Its sites collectively generate more than 600,000 megawatt hours of baseload renewable energy–enough to power 115,000 homes daily.
e company’s methane abatement is equivalent to planting 68 million trees over 10 years, or removing 1.6 million cars from the road every year.
LMS is also innovating in the recovery of organic waste, to enable the capture of biogas, heat and nutrients from suitable organic matter. It has commenced operating its own anaerobic digestion (AD) pilot facility
in South Australia, an Australian rst, and is pursuing several other large AD projects across Australia, including agricultural projects.
“Here is a company passionate about the circular economy and achieving massive carbon reductions,” Tiana says. “LMS is experienced in taking an initial idea through to commercialisation, and now I get to have a closer connection to actions driving positive change at ground level.”
Tiana considers policy directions within di erent jurisdictions and how LMS Energy can work within that space. She considers laws in detail, emerging concepts, and available opportunities.
She says that while she always believed in the importance of policy, her role now more than ever highlights the need for clear, certain, and balanced policy.
“When you are a company looking to invest in signi cant assets with multi-decade lives, having that clear policy direction and intent is really
signi cant,” she says. “I’m able to help make sure we do the right thing by our environment and are supporting businesses with a level playing eld and policy certainty.”
e South Australian Branch President of the Waste Management and Resource Recovery Association of Australia and an active member of Bioenergy Australia’s Renewable Gas Alliance, Tiana has also lectured at UniSA on environmental policy and regulation.
She sees the need for more integrated policy often, with a crossover between waste, energy, and planning policies needed to help deliver the big picture –having the right systems to drive waste avoidance and higher-order outcomes.
A culture of innovation to achieve those higher-order outcomes motivated Tiana to join LMS Energy. e company is committed to doing things right and protecting the environment. at commitment extends to policies and initiatives to attract and retain a diverse workforce. All jobs at LMS Energy are o ered as part-time roles,
including operational jobs that have been redesigned to be part-time or exible. A dedicated ‘wellbeing hour’ of an employee’s choice is o ered weekly, and there’s the option to ‘work from anywhere’ for short periods, including overseas.
Sta have access to leadership courses and mentoring opportunities, including the company’s “Women Leaders: Own Your Success” training through the Australian Institute of Management, 10-weeks employer-paid parental leave and return to work support payments, and wellbeing rooms with childrens play areas and breastfeeding facilities.
“A culture of ‘keeping on stepping forward’, implementing progressive policies aimed at improving diversity, employee wellbeing and job satisfaction, is evident all the time at LMS Energy,” Tiana says.
“As leaders in the sector, we have the responsibility to make interesting jobs accessible to all.”
For more information, visit: www.lms.com.au
Melbourne-based Speedie Waste & Recycle has spent the past 70 years building a community.
An ex-army pick-up truck and a vision to start a business and support his family were Francesco Barilla’s introduction to the waste industry.
Servicing Melbourne’s greengrocer and fresh produce markets, Francesco earned a reputation for exceptional service.
Seventy years and three generations later, customer service remains the cornerstone of his legacy ¬ Speedie Waste & Recycle.
e company has grown to cater to the wider business sector, o ering waste management solutions for commercial, industrial, and domestic customers throughout Victoria and interstate. It employs 103 people and has a eet
of trucks. Francesco’s granddaughter, Jessica Barilla, is at the helm.
For the past 11 years, Jessica has worked alongside her father, uncles, and cousins to build a company that is driven by sustainable practices to ensure tomorrow.
“We’ve got something to be proud of and to extend the legacy of my late grandfather,” Jessica says. “I’m here every day because of my family. It’s not just a job for me; it’s our company, and it supports my family. But more than that, it supports our sta and their families.”
Jessica cut her teeth in the business watching her father, Vince, and his
brothers mould the company as waste streams and community expectations changed over the years.
Still, she admits it was a learning curve when asked to take the reins.
She leaned into her family background and knowledge while gaining an understanding of the industry’s intricacies. She also drew on 11 years of management experience in the medical industry.
“When I rst walked in, some people were a bit sceptical,” Jessica says. “But I got in and learnt everything my team did. I drove them up the wall at rst because I sat with a notepad, watched everything, and asked lots of questions.
“Management skills are management skills; you can apply them anywhere, but a good leader should understand what their team does.”
ere’s also an art to balancing a business and family. One Jessica manages with the support of her father and uncles. Being a woman in a male-dominated workplace has also made a di erence.
“Women have a di erent type of strength, and we can balance things di erently,” she says.
e waste industry has changed over the past decade, with a focus on environmental, social, and governance outcomes.
Jessica says sustainability is a core value at Speedie Waste & Recycle.
e company takes pride in providing exceptional service and maintaining customer relationships while helping them meet their goals.
“We’re working towards a circular economy and trying to close the loop with recycling and reducing what goes to land ll,” Jessica says.
“Our business is all about o ering our customers sustainable waste and recycling options.”
at requires Speedie Waste & Recycle to innovate and adapt, including its eet of trucks.
e company recently took delivery of two UD Quon heavy duty trucks tted with STG Global’s Tusks front loader. e latest Volvo FM11-410 is on its way.
Australian manufacturer STG Global has built a reputation for building trucks that can navigate Australia’s versatile and sometimes tough conditions.
e company’s very rst truck, a water tanker, was a combination of ingenuity and grit. e latest iterations have been described as ‘smart trucks’ with advanced functionality, including a single digital screen and selfdiagnostic capabilities.
e single screen, an iPad Pro that connects with the STG Global app, has everything a truck operator would need at the tip of their nger. If there’s a fault, the truck’s self-diagnostic system will alert STG Global technicians, who can dial in and x it remotely.
A mix of strength, long-lasting materials and intelligent automation have made the Tusks a rm favourite in the waste sector.
Shane Sinclair, STG Global National Fleet Manager, says the Tusks are a good t for the diverse customer base of Speedie Waste & Recycle.
“STG understands the challenges of the waste and recycling industry,” he says. “We manufacture truck bodies that optimise payload capabilities, streamline operations, and boost on-site e ciency.
“As a family-owned Australian business, we know the importance of
values and maintaining customer trust. We’re excited to be part of Speedie Waste & Recycle’s growth.”
Jessica says Speedie Waste & Recycle is on a growth trajectory, but it’s not about to forget its roots. It will continue to value its customers – large or small.
“It’s not about the size,” Jessica says. “We have big customers; we also service those smaller family-run businesses.
“We’re di erent from large companies because we have hands-on management and experience.
“We have long-term customers who have been with us 40 to 50 years, and on any given day, we’ll still have one of the uncles in the yard happy to have a chat with them.”
For more information, visit: www.stgglobal.net
Pure Environmental’s new professional graduate program will introduce young scientists and engineers to opportunities within the waste industry.
The waste and resource recovery industry has an opportunity to impact emissions reductions and waste diversion, but reaching national and state targets is not going to happen by default.
Dr Karlis Baltpurvins, Chief Executive O cer for Pure Environmental, says the industry has an opportunity to achieve great things. However, if the same people keep doing the same thing, it will deliver the same result.
at is why Pure Environmental has launched a professional graduate program to induct young scientists and engineers into the waste industry. e 12-month program focuses
on the circular economy and will include ve placements at various Pure Environmental operations facilities.
“If we truly want to innovate and do things di erently and nd circular economy outcomes, we need to continually build a pipeline for new talent and develop those people,” Karlis says. “It’s vital for our industry to attract the next generation.”
e program aims to give graduates a holistic understanding of how di erent facets of the business work together.
At the end of 12 months, the graduates will be o ered a role in the business in a area that is matched to their skills and interests. ey will also present a project incorporating learnings from their placements to Pure Environmental’s national team.
Two graduates began the program in April and have entrenched themselves in the industry, attending seminars and conferences. Karlis says they are encouraged to help Pure Environmental innovate and think outside the box.
“We often look at things the same way because we’ve been exposed to them longer. By bringing in someone fresh and giving them a broader understanding of how the company ts together, we’re hoping they will see things through a di erent lens,” Karlis says.
Karlis has a PhD in chemistry and is regarded as a leading expert in the industry. He’s invested in nurturing and developing talent. Otherwise, the industry remains stagnant.
“It is essential that all industry participants put aside valuable time to mentor our junior sta to develop the leaders of the future,” he says. “We know diversity and recognising new ideas makes us stronger. e graduates will learn the technical aspects of our business and be supported to innovate.” e graduate program attracted more than 100 quality applications. A pleasant surprise for Karlis, who admits
waste is not typically high on the radar of top performing graduates.
He believes the high level of interest in the program is because of the company’s focus on circular and sustainable outcomes and the increasing awareness of both in the broader community.
ere is a focus on encouraging the graduates and Pure Environmental’s team to take a broader look at circularity, not just within the con nes of the business.
Brisbane. e facility is licensed to receive a range of hazardous liquid, solid and packaged chemical wastes.
As an environmentally conscious scientist, Mehelet says the promise of sustainable resource use, innovative technology and the opportunity to reshape material consumption patterns is appealing.
For Richard Pope, the opportunity to investigate important projects so early in the program was unexpected, but it was one he relishes. He’s been working
“If we truly want to innovate and do things differently . . . we need to continually build a pipeline for new talent,”
Karlis Baltpurvins, Chief Executive Officer, Pure Environmental
“We don’t have to o er the full circle ourselves,” Karlis says. “We have a talented technical team who can look at every waste stream we bring in, break down the physical and chemical components and determine what we can separate or purify to be a valuable feedstock for another process.
“By understanding the concept of a circular economy and gaining insight into di erent feedstocks used by di erent manufacturers, I’m hoping our developing graduates can nd more opportunities.”
Program applicants’ academic achievements were not the only factors considered. Real-world and work experience also played a role.
Mehelet Abraha, one of the two graduates in the rst intake, was attracted to the program because of its diversity of rotations and insight into the business. Her rst rotation was at Wacol, a waste processing treatment and resource recovery facility in greater
at the Jackson facility, which services various waste streams originating predominantly from coal seam gas production and related industries.
“ e potential to explore a new industry and develop my abilities as a scientist was a primary factor that drove me to the Pure Environmental graduate program,” he says.
“Not only am I able to expand my abilities, but I have the chance to do so with an established and recognised company that cares about its impact on the environment and its people.” e graduate program has been so well received it will continue into 2025.
“From a business perspective, we are receiving excellent feedback,” Karlis says. “ e graduates are very clever but are also very capable of using their chemistry and technical background to apply what they’re learning.”
For more information, visit: www.purenv.com.au
With per- and polyfluoroalkyl substances (PFAS) continuing to be a big issue for the waste management industry, the Waste 2024 Conference hosted a workshop to examine the concerns, risks and management of these ‘forever chemicals’.
Key thought leaders across the waste and resource recovery industry shared how their organisations are dealing with per- and poly uoroalkyl substances (PFAS), their anticipated priorities, and their impact of PFAS on realworld projects.
e workshop, facilitated by Gayle Sloan, Chief Executive O cer of the Waste Management and Resource Recovery (WMRR) Association Australia, was made up of David Springer, Commercial Manager at Envirolab, David Burns, Senior Scientist at EPOC Enviro, and Charmaine Cheah, Senior Engineer at HUESKER Australia.
Together, they looked at aspects such as characterisation, assessment, remediation, and management of PFAS in the community. e panel sought to recognise how much has been learned
and understood through investigating and managing PFAS contamination over the past decade. It also focused on where the industry needs to be in Australia and how to get there.
“Australia could become a dumping ground for PFAS-laden products in the future if we do not do something about it,” Gayle said.
David Springer discussed the contents of PFAS, which encompasses anywhere from 5000 to 15,000 chemicals. However, laboratories mainly test for just 28 of these chemicals known for their extreme persistence and longrange dispersion.
ese chemicals are still manufactured overseas, imported into everyday consumer goods, and are now in our blood.
“In the past, we would see PFAS in re ghting foam,” David said. “Fire ghters weren’t allowed to buy dishwashing liquid during a period of budget cuts in the 1990s. As a result, they would use that foam to wash the dishes. It was also used for the slip-andslide around Christmas.”
David said people do not realise that innocuous things contain these forever chemicals. He spoke of nding 400 parts per billion (ppb) of PFAS in plumbers’ tape that had been soaking in water for three days. is was before he pointed to eye pencils and makeup containing PFAS as ingredients.
David Burns highlighted that Australia is not a PFAS manufacturer but a passive receiver of these chemicals. He said it’s also important to remember that when a product is PFAS-free, there are less than 100 parts per million of PFAS chemicals, or 100 million nanograms per litre.
“When we go into a shop where the packaging claims that a product is PFAS-free or Per uorooctanoic acid (PFOA) free, it’s important to understand what that means,” he said.
“Does it mean that there is no PFAS in there and there is no risk?
“It means the company has signed up for a voluntary code of conduct that says there are fewer than 100 parts per million. at is 100 million nanograms
per litre, or 100,000 parts per billion. It only has to be less than that number to be considered PFAS or PFOA-free.”
David sought to connect sewage treatment plants to the broader waste networks, including land ll operations and composting.
He aimed to show how the waste network is being unwittingly used to disperse PFAS from highly concentrated levels down to much lower levels that are too expensive and dispersed to do anything about. At the same time, those levels are much higher than what the United States and European Union say is unsafe.
“Even with governments wanting to divert 80 per cent of waste from land ll, how can we do that if there’s a festering contamination problem?” he asked. “ e reality is that land lls in Australia are already a dumping ground for PFAS.
“Land lls will become permanent dumps for PFAS, which then leaches into the groundwater or into a sewer connection. at’s unfair for us in the waste management industry, particularly when the chemicals being leached into the groundwater could be millions of times more potent than the PFAS-free products.”
Charmaine Cheah discussed some of the technologies available for dealing with PFAS and highlighted the di erence between destruction technologies and remediation techniques.
“Destruction technology is almost exclusively in the form of incineration equipment,” she said. “However, there are two practices that we can use to improve land lls across Australia. ey are land ll disposal and remediation.”
Charmaine spoke about how land lls are made up of layers, and installing a mineral liner can help manage PFAS leaching into the ground. ese liners consist of nanowaves and a geomembrane, along with drainage and mineral layers.
“However, this technique does allow for some di usion through the geomembrane and leakage through traditional composite liners,” she said.
“Di erent jurisdictions have di erent rules as to the permitted level of leakage. Even the scienti c literature indicates that these layers can be manufactured imperfectly.”
She also pointed out that granulated activated carbon (or GAC) could be an e ective method for removing PFAS from water, in a technique called desorption. is is the release of an adsorbed substance from a surface.
“We found that activated carbon is a very popular practice, but it is only really good at dealing with long-chain PFAS,” Charmaine said. “It is not very good at ultra-short-chain PFAS. is is why we nd that liners need to incorporate granulated active carbon.”
Such liners would capture more of the PFAS chemicals, with the groundwater ltering through to be clean. Even under heavy rain, these liners become e ective lters, as proved through tests in Germany and Australia. e number of questions asked throughout the workshop was an indication of the level of uncertainty around PFAS.
Gayle said the workshop was designed to alert, not alarm, but it was clear one of the di culties facing the waste sector was the con icting approaches to PFAS and its impacts. She said recycled
products were subjected to standards, regulations, and enforcements not imposed on virgin and other products, sti ing a transition to a circular economy. At the same time, hazardous materials are readily available in everyday products.
“As a sector, we’re continually told you can’t make products with that,” she said. “Yet you can buy as much PFAS as
you like at a pharmacy. Is it dangerous, or isn’t it? You cannot keep putting a product on the market showing PFAS levels way beyond what we do.”
Gayle reiterated a common thread from the conference – moving the conversation from waste disposal to product design. “We’ve got to stop solving everyone else’s poor design issues and stop making it in the rst place.”
Komptech CEA is a leading supplier of machinery and systems for the treatment of solid waste through mechanical and mechanical biological treatments, as well as the treatment of biomass as a renewable energy source. Komptech CEA is proud to provide innovative solutions for handling waste and biomass.
Komptech CEA’s extensive range of products cover all key processing steps in modern waste handling. At Komptech CEA the focus is always on innovative technology and solutions ensuring maximum benefit to the customer. Like to know more? why not speak to one of our team today?
Where Function Meets Technology
A slow-running, single-shaft shredder suited to all types of waste.
Less Fuel, More Power
Ideal for shredding all types of wood and green cuttings.
Screening with a Star Makes waste wood and biomass processing highly efficient
The Ideal Combination of Performance and Design
With a sturdy frame, powerful hydraulics and large drum, the Topturn X is ready to handle any work situation.
Robust and Reliable
Combining the practice-proven virtues of its predecessors with new solutions for even greater performance
Enhancing the quality of the recyclable output.
Providing effective removal of plastic film from screen overflow.
New patented particle size reduction technology is transforming waste into value.
It sounds like something straight from the pages of a science- ction novel – a machine that turns household waste into powder.
But the unimaginable is now imaginable, according to Vortair Chief Executive O cer Je Lang.
Vortair Pty Ltd is an Australian company that o ers autogenous grinding systems to process waste materials with unmatched e ciency. It’s developed the Vortair system to mill waste materials into a ne powder. e technology is applicable across multiple industries, milling materials such as plastic, glass and cardboard, thus reducing the volume of waste, minimising disposal costs and in many cases turning the waste into a saleable commodity.
It’s also showing promise converting farm waste, including plant biomass and damaged fruit, vegetables and produce, into a viable commercial commodity in the form of powders, pastes and purees.
“We’re looking at how we can rede ne waste reduction protocols,” Je says. “Australia is running out of land lls; we have to think forward, and we have to minimise waste. We’ve got an answer.
“By turning waste into a powder form the Vortair system can reduce the volume of material going to land ll by up to 90 per cent, with the added bene ts of minimising carbon footprint and waste reduction resources.
“We envisage this technology in every household in the future where all waste will be reduced to a powder and picked up by a waste contractor.”
e inventor of the Vortair technology, Axel Andre, has partnered with Je and Tom Debney, Business Development Manager, to commercialise the patented technology at a global scale.
e Vortair system combines several pulverising principles that release stored kinetic energy in the material being milled to reduce particle size without crushing or mechanically shearing the product. us, it needs no regular blade replacement or sharpening.
It can replace ball mills, pin mills, jet mills, hammer mills, rotating disc mills, and others, signi cantly reducing industrial grinding costs.
Je is an experienced CEO and board director with more than 35 years
of industrial commercialisation of new research, patent intellectual property (IP), advanced materials, digital systems, and advanced manufacturing technologies across multiple industry sectors.
He has received international awards, raised more than $200 million in capital for various companies and has led multiple e orts in the development of future advanced technologies, by driving a culture of “outside the box” strategic thinking.
He describes the Vortair technology as the “next level approach” to waste.
One of the key elements in the use of high-density polyethylene (HDPE) or low-density polyethylene (LDPE) plastics is the ability to recycle it into new product.
Je says the Vortair system can mill plastic wrap or bag waste from farms back to a ake or ner powder that has potential to be reused in the manufacture of LDPE and HDPE products, such as wraps, or used in blow moulded product.
e machine is capable of milling poly lined paper bags to separate
the poly liner and paper. e paper can be separated and used in cardboard manufacture and the poly, which is mainly LDPE, can be used in new extrusions for timber wrap or consumer fertiliser bags, mulch bags etc.
e Vortair machine uses a HumanMachine Interface (HMI) display control system to change the milling speeds for di erent applications, depending on the desired particle size required for the nished product.
e food grade Vortair 500 uses food grade stainless-steel 316 with a single piece titanium rotor for milling food grade materials, while the standard Vortair 500 is made from high tensile steel with tungsten carbide blades for increased wear resistance for milling hard and tough materials. e Vortair 500 has successfully milled polyethylene plastic waste to a 100 micron powder.
e Vortair has shown its best results come from introducing materials that are 60 per cent moisture or lower as these will mill e ciently to a powder at under two per cent nal moisture and a controlled micron size.
Je says it’s important that the size of material introduced to the machine can t in the chamber. If some size reduction is needed at infeed, this is readily available o the shelf.
One of the limiting factors of the process is the moisture content of the materials as powder is not produced in a single pass until the moisture content is below 55 per cent. is can be reached by reducing the input size and using a heat pump and desiccation technology to gain initial drying at a low cost.
Milling material that is frozen is not economical as the energy used to get back above zero is higher compared to other methods.
e machines are proudly manufactured in Australia and are assembled in Bayswater with fabrication taking place in Shepparton, Melbourne, and Dandenong.
Titanium rotors are used in the food grade machines and are balanced to be able to spin safely at 9000 rpm. Rotor drive balancing is done in Melbourne and the control systems designed and installed in Bayswater with interfaces to most manufacturing systems as needed.
“We’re looking at some phenomenal technology that will take us into the future,” Je says. “ is is not only going to help waste reduction volumes, but is profound separation technology for across industries.”
For more information, email: je @agentel.com.au
Strong foundations for collaboration were secured at the Australian Organics Recycling Association 2024 Annual Conference.
Themed ‘Collaboration for Success
– Securing our industry’s future,’ the three-day Australian Organics Recycling Association (AORA) 2024 Annual Conference on the Gold Coast, brought together key stakeholders from Australia’s organics recycling industry.
Business, government, and academia discussed the importance of working together to secure the industry’s future, with a focus on navigating regulatory landscapes, identifying priority issues, and exploring investment avenues for sustainable growth.
John McKew, AORA National Executive O cer, says several key themes emerged from this year’s conference. Several of them are worthy of consideration and further deliberation.
AORA believes organics recycling will be at the forefront of Australia’s circular economy transition. With almost half of Australia’s waste streams constituting organic material, an e ective circular economy will be elusive without a sustainable and e ective Australian organics recycling industry.
Lisa McLean, Chief Executive O cer and Managing Director for Circular Australia, provided further insights into the circular economy transition, why it is essential, and what needs to happen for it to succeed.
e circular economy is a systems transition – not one person, business, industry, or government can do it alone. Collaboration is essential across business, government and agencies.
Driving circular solutions will require prioritising sustainable products and services that will help drive demand for new circular technologies, materials and processes; cut waste to land ll; help boost recycling; reduce emissions; support local jobs; and deliver a future re-made in Australia, enabling goods to be recycled and remanufactured onshore.
John says that while the Australian organic recycling industry ticks all six boxes and is already a clear contributor to the circular economy, its future growth is not assured. A lack of harmonisation of regulations across the Australian states and territories is of concern in securing the much-needed future investment and con dence in the industry.
e current review of the AS4454 standards (Composts, Soil Conditioners, and Mulches) is well supported by the industry through
the consultation phase of the review, but concerns exist that the revised standard will not be accepted and adopted by state and territory regulators, potentially resulting in an impotent outcome.
“Collaboration, clarity, and certainty will be essential for the future of the Australian organics recycling industry and the circular economy generally,” John says.
e critical importance of soil and soil health continues to emerge, and organics have a role to play in achieving this.
Aside from the importance of diversion from land lls and the bene ts of this to help mitigate the impacts of climate change, organics will increasingly become vital to improving soils through
better carbon storage, improving water retention capacity, increasing organic matter and, consequently, increasing soil microbial activity.
Professor Sally Brown from the University of Washington knows this better than most and noted in her conference presentation that soil is ‘the living skin of the earth’.
She says the evidence of the bene cial role of organics via compost to soil health is compelling.
John says building on this knowledge through further research and developing the organic/ soil health story will become increasingly important, but it will not happen without commitment and collaboration.
For more information, visit: www.aora.org.au
How Volvo’s L25 Electric Wheel Loader is revolutionising the industry.
As the waste management sector prioritises sustainability and operational e ciency, introducing electric compact wheel loaders, such as the Volvo L25 Electric Wheel Loader, presents a transformative opportunity. is innovative machine aligns with environmental goals and o ers practical advantages that make it suitable for waste management operations.
e Volvo L25 Electric Wheel Loader marks an advancement in construction and waste management machinery. e ve-tonne loader is powered by a 48V
Lithium-ion battery with a 40kWh capacity and is engineered to provide high performance while reducing its environmental impact.
e loader is equipped with a dual electric motor system, with one motor dedicated to working hydraulics and steering and another for the driveline, ensuring optimal energy e ciency and peak performance.
e L25 Electric is equipped with a 1.2 cubic-metre standard bucket and supports various attachments such as forklifts, grapples, and material handling arms, making it versatile for di erent waste management tasks.
Its zero exhaust emissions and reduced noise levels are bene cial for operations near residential areas or within indoor facilities, where traditional diesel engines might pose challenges.
One of the standout features of the L25 Electric is its powertrain design, which o ers instantaneous torque control and eliminates the delay associated with diesel engines. is results in enhanced responsiveness and controllability, which is crucial for the dynamic demands of waste management.
e electric powertrain’s simplicity, characterised by fewer moving parts, also translates to lower maintenance requirements and costs. e machine’s electrical components, batteries, and motors are inherently maintenance free, reducing downtime and operational expenses.
e L25 Electric’s 40kWh battery can be fully charged in under six hours using an onboard charger with a Type 2 automotive standard inlet. is ensures the loader is always ready for use, enhancing productivity.
Moreover, the electric motors reduce noise levels and vibrations, creating a more comfortable and safer work environment for operators. Features such as the electric park brake with hill-hold functionality and the Electric Machine Management App, which provide
real-time insights into charging status and machine location, further enhance operational e ciency and safety.
e L25 Electric can be quickly recharged in as little as two hours with its e cient charging capabilities and the option for fast o -board chargers, making it suitable for facilities that require near-continuous operation.
In an era when reducing carbon footprints is critical, the Volvo L25 Electric Wheel Loader sets new standards for sustainability in the waste management sector. Its zero tailpipe emissions and reduced noise pollution make it a responsible choice for environmentally conscious operations.
e collaboration between CJD Equipment and Volvo CE ensures that this innovative machine is backed by a robust support network, guaranteeing high productivity and e ciency.
e Volvo L25 Electric Wheel Loader is well-suited for various tasks in waste management, particularly in environments where low emissions and reduced noise are crucial. Speci c tasks the wheel loaders are suitable for include
moving and transporting waste materials within recycling centres or waste management facilities. With zero exhaust emissions, the L25 Electric can operate seamlessly in indoor environments and emission-restricted zones, making it ideal for enclosed waste sorting facilities or transfer stations.
e loader’s high lifting and breakout forces and roll-back and dump angles make it suitable for loading waste materials onto trucks or into processing equipment, while the machine’s weight and power can be used for light compacting tasks in waste management sites.
e L25 Electric supports various attachments such as forklifts, grapples, and material handling arms, allowing it to perform diverse tasks such as sorting recyclables or handling bulky waste items.
e Volvo L25 Electric Wheel Loader’s combination of zero tailpipe emissions, reduced noise, versatility, and e cient performance makes it an excellent choice for waste management operations looking to improve their environmental footprint while maintaining high productivity. It o ers signi cant advantages over traditional diesel models with up to
35 per cent lower maintenance costs compared to equivalent diesel models.
e electric powertrain has fewer moving parts, eliminating the need for engine maintenance and associated products such as engine oil, oil lters, diesel particulate lters, and diesel exhaust uid.
e fully electric driveline cuts hydraulic oil use by up to 50 per cent, reducing maintenance requirements and new wet-disc brakes require less maintenance than traditional brake systems. When maintenance is required, lubrication and maintenance points are easily accessible at ground level.
A new Human-Machine Interface (HMI) allows operators to navigate machine information and settings easily, potentially preventing issues before they require costly repairs.
ese factors collectively contribute to lower long-term operational costs and reduced downtime for the Volvo L25 Electric Wheel Loader compared to traditional diesel models, making it an economically attractive option for waste management operations seeking to reduce maintenance expenses.
For more information, visit: www.cjd.com.au
As Australia prepares to enter a new era in waste management, Blue Phoenix Australia has assembled a team of experts to lead the way. We meet Paul Visser, the new Commercial Development Manager, Australia.
Blue Phoenix welcomed Paul Visser to the Australian team in November 2023.
In his more than 30-year career, Paul has worked with some innovative, resourceful, and sustainabilityfocused organisations.
But he says joining Blue Phoenix Australia as its Commercial Development Manager has heightened his awareness of the need to protect the environment through reducing a reliance on natural resources and burying waste.
“Resource recovery and sustainability are my focus with Blue Phoenix,” Paul says.
He’s been inspired by the passionate and dedicated people within the Blue Phoenix Group and those in the Australian waste recovery industry.
“ ere is a commitment to reduce waste from the original source, recycling and recovery and now the diversion from land ll through alternate disposal via waste-to-energy (WtE),” he says.
During a recent trip to the United Kingdom and European Blue Phoenix operations, Paul saw rst-hand the bene ts of incorporating WtE into local areas, returning electricity and heat to the community, and recovering precious metals and aggregate materials from the residual incinerated bottom ash (IBA) for reuse.
As Australia proceeds down the path of WtE, with the commissioning of two plants in Western Australia, Paul says he’s proud to be part of Blue Phoenix Australia and Australia’s rst IBA processing facility. e rst of its type in the Southern Hemisphere, the plant will recover the metals and aggregate for reuse within Western Australia, with plans to expand interstate.
It will bring together decades of experience in IBA processing and knowledge of the metals and aggregates industry, with innovative technology and sustainable best practice to produce reliable, low-
carbon alternatives to primary mined minerals and metals.
“On receipt of IBA from the WtE plant, our Blue Phoenix Australia team takes responsibility of the handling, storage, processing, extraction, and recovery of reusable material which has not reached end-of-life but rather ‘re-life’,” Paul says.
“Sourcing this re-life material reduces the impact of extracting natural resources and the environment.”
In his role as Commercial Development Manager, Paul aims to assist Blue Phoenix and the waste industry to grow the IBA market.
His background in nance and contract management, and exposure to operational management and safety, will help create a circular outcome.
“I don’t want to see more land lls,” Paul says. “We should be protecting the environment in which we live, the underground aquifers that provide our water and look to alternative ways to create electricity, heat, and reusable materials. As one of the world’s largest ash processors, Blue Phoenix prides itself on operational excellence with proven processes, professional teams, and the highest commitment to health, safety, and sustainable performance. is is why I joined Blue Phoenix.”
Subscriptions
•
•
•
•
Introducing the next generation of machinery for post-industrial and post-consumer plastics processing.
Next Generation
Recyclingmaschinen GmbH (NGR), is an innovator in machinery for plastic recycling. e launch of its updated C:GRAN series at National Plastics Exposition (NPE 2024) in Orlando, is being hailed as a breakthrough in the industry due to its performance, e ciency, and sustainability.
Robert Cobban, Managing Director of BK Sales Australia, a distributor of NGR, says the technology is a game changer for plastic recyclers.
“ e updated NGR C:GRAN series spearheads a shift in the standards of plastic recycling, transcending traditional norms to deliver unparalleled performance and quality,” Robert says.
“ e NGR advanced technology ensures the transformation of various waste materials into high-quality granulate that can then be used as a
valuable resource in the production of new products, reducing the need for virgin materials and promoting a circular economy.”
e C:GRAN can process everything from biaxially-oriented polypropylene (BOPP) and polyethylene terephthalate (BOPET) lms generated as production scrap, to materials from washing plants and heavily printed lms that have rigorous degassing requirements. is capability ensures the e ective reintegration of diverse end-of-life plastic streams back into the production cycle as quality granulate.
e C:GRAN series features two independent extruder drives, allowing optimal speed settings for both the melting and degassing extruders. is con guration optimises degassing and melting performance while maintaining lower melt temperatures due to the short process unit.
“Moreover, a clean separation between the extruder and cascade, with melt ltration in between, ensures that no contamination bypasses the melt lter, leading to a very stable process and preventing the production of o -spec granulate,” says Raimon Wong, of NGR.
e C:GRAN series features a modular design that o ers exibility for custom recycling needs. It includes options such as retro tting additional degassing zones or integrating a cascade with a second ltration stage – adjustments that can be made quickly to optimise e ciency.
e enlarged cutter-compactor section of the C:GRAN series is designed to ensure high throughputs and high process stability despite varying input qualities. For high input moisture levels, the cuttercompactor can also be equipped with a special DRY-Boost to enhance material drying performance. Raimon says a notable feature of the C:GRAN series is
the cascade con guration equipped with Power Venting Section. is setup is crucial for processing materials with high contamination and moisture.
“ e cascade’s Power Venting Section, with three degassing openings and an innovative material ow path, provides the ability to remove even the most challenging volatile contaminants, thus ensuring exceptional pellet quality,” Raimon says. “ e location of the vent, after ltration, ensures optimised throughput and energy e ciency.”
e new Auto-Pilot control system for the C:GRAN series automates the entire recycling process, adapting to changes in material characteristics, such as density and moisture.
is system adjusts the intake slider, cutter-compactor, extruder, and pelletising speeds automatically to maintain optimal processing conditions
and consistent pellet quality without operator intervention.
“ e Auto-Pilot feature virtually eliminates operator error, reduces the likelihood of unscheduled downtime and especially prevents meltdowns,” Raimon
says. “It ensures that our machines operate at peak e ciency, with minimised energy use and enhanced safety.”
For more information, visit: www.bksalesaustralia.com
The waste management space poses numerous challenges for keeping dozers operational, and Komatsu’s leadership in this area is critical.
Waste management is a harsh application for dozers, says Pat Munro, National Business Manager – Construction at Komatsu Australia.
“It’s not just about the volume of waste, but about all the debris, oc and oating material that gets into places it’s not welcome.”
Pat grew up in the Darling Downs, west of the Great Dividing Range in southern Queensland. e region is noted for its strong and diverse agricultural industry, partly due to the soils with moderate to high fertility and available water capacity.
“I started with Komatsu as a territory sales account manager in
southwest Queensland for 11 years, working some of the territory where my parents and grandparents grew up,” Pat says.
“At the time, I was doing a lot of work with tree and scrub clearing. I also spent a fair chunk of time in the desert, focusing on seismic work. ere are quite a few Komatsu dozers that have applications in that space.”
It’s broadly accepted that waste management is one of the toughest environments for heavy machinery. Many types of waste could impact the operation of dozers, while the facility’s layout can create new ways
to damage a machine. However, it’s the smallest things that can create the most problems.
“Rubbish always gets in the cooling packs and air-conditioning systems,” Pat says. “It doesn’t matter what you do to the machines – including the type or brand of machine – it’s ultimately about how you manage and maintain those spaces.”
“In northern Australia, the temperature is not so much the problem we worry about. It’s the higher humidity levels that cause most problems. Everything feels wet, and once you add dust to a wet surface, that turns into mud. at creates a whole new set of problems.”
“iMC machines allow accurate and automatic cutting and stripping .”
Pat
Munro National Business Manager,
e introduction of smart technology is enhancing the productivity and e ciency of dozers. For Komatsu, this is called Intelligent Machine Control (iMC), and the latest version of this is iMC 2.0. e “intelligent” iMC Dozers are fully integrated with the machine, meaning there are no masts on blades or exposed sensors and cables to catch on rubbish in a waste management application.
“One of the big challenges with dozers is having the proper control of the work being done,” Pat says. “iMC machines allow accurate and automatic cutting and stripping from existing terrain with minimal input from operators. is provides a bene t to end-users and allows accurate capping to be completed with signi cant productivity gains.
“We had a situation with a client in southern Sydney where they thought they had a slanted capping. I had to get out there and look, and discovered that the survey pegs had slipped down the slope with the soil.
“ e iMC dozer was capping to an accurate at surface and this led to the confusion for the operator. e dozer was correct, and the site now puts much more reliance on the technology in the dozer than it does on survey pegs.”
Technology is taking the lead in helping clients across the country. Lift Layer Control in iMC Dozers allows operators to automatically cap at a
de ned height, per layer, above the existing terrain. No complex models are required, the operator just goes to work.
Similarly, Proactive Dozing Control allows an operator to cut at de ned depths below the existing terrain, again without models. e machine guides itself to the correct height.
When using this and other technology functions in the iMC machines, operators report a doubling in productivity. is ows through to lower maintenance costs etc per tonne of material moved as well as better fuel e ciency and therefore emissions per tonne moved.
Standardised models do not always suit the needs of local conditions.
at’s not the case with Komatsu, as the Australian supplier has developed modi cations designed for Australian conditions.
“In the waste industry, we put considerable focus on cooling packs, focusing on their maintenance and cleaning,” Pat says.
“We also try to put a range of systems outside the cabins and engine bay to reduce the impact of debris. It will always get in, but these design changes allow us to reduce it where possible.
“My colleagues and I work closely with our clients to make even the
slightest changes to reduce the impact of debris on the cooling packs.”
Servicing and cleaning Komatsu or any machines correctly in this application is essential. Komatsu provides service manuals so that the end-users can conduct all cleaning and maintenance schedules without issue. Maintenance schedules vary depending on the site and its variables.
Komatsu has a range of dozers that are perfect for the waste management industry.
“We have smaller HST dozers, which o er more visibility to the blade and rippers through their short sloping bonnet design, rear-mounted radiators and large glass areas,” says Pat.
“Another machine is the 5-series of dozers, which are far more suitable for the waste industry. ey have external push arms, which protect the hydraulic pipe work. ere is also more space to install appropriate cooling packs for waste application.”
Looking into the future, Pat believes the continued integration of smart technology into high-end dozers will allow Komatsu to improve productivity and safety in any application.
For more information, visit: www.komatsu.com.au
The Environmental Group aims to minimise environmental impact through innovative technologies and sustainable practices.
Environmental sustainability is at the core of e Environmental Group whether that’s reducing waste, conserving natural resources, or preventing pollution.
e environmental engineering company provides products and engineering services to various industries to improve environmental outcomes.
Jason Dixon, Chief Executive O cer of e Environmental Group Ltd says the company has worked hard over the past three years to consolidate the business under the singular vision of working towards a sustainable future.
“We believe we can achieve this by reducing all types of waste through our integrated business model,” Jason says.
“We bring leading global technologies to our customers and markets to ensure a sustainable and better future for all.”
e group operates across several specialised divisions, focusing on a diverse range of technologies and environmental management solutions. ese divisions include recycling and sorting technologies designed for e cient material processing, and comprehensive air pollution control systems addressing gas emissions, particle removal, and odour control.
Its energy solutions encompass combustion-e cient boilers, heat exchangers, biomass boilers, and autoclaves, all aimed at enhancing energy e ciency and sustainability. Additionally, the group o ers gas turbine
inlet ltration systems ( lter houses), inlet cooling/fogging systems, acoustical components, expansion joints and complete exhaust systems with guillotine and diverter dampers.
e group’s newest development is its PFAS separation technology to remove per- and poly uoroalkyl substances from various waste streams e ectively.
“All divisions play a role in providing a one-stop-shop solution for waste treatment across the circular economy,” Jason says.
e Environmental Group collaborates closely with local and international corporations. Jason says the company’s commitment to protecting the environment is re ected in the innovative technologies it has developed or brought to Australia under license.
e Environmental Group combines worldwide knowledge and expertise to provide the best outcomes for customers.
From idea, to design, conceptualisation, implementation, build, maintenance, and service delivery, the dedicated project management team ensures that projects are on time, within budget and exceed expectations.
“We are committed to delivering solutions that make a tangible di erence,” Jason says.
e Waste Services division provides engineering services to create world-
leading exchange facilities with plants capable of handling all types of waste, including PFAS.
e group’s Australian-patented PFAS Separation technology plays a crucial role in safeguarding the environment, allowing waste and water management facilities to remove 99 per cent of PFAS from water, soil and biosolids while adhering to stringent quality and safety standards.
e easy-to-install technology allows waste and water treatment sites to reduce PFAS storage facilities, eliminate human interaction with contaminated materials and stay operational when treating contaminated waste or water.
Dust and fumes are common pollutants that can impact the atmosphere, air quality, and health. Hydrogen sulphide and odour emissions are often generated when processing Food Organics and Garden Organics (FOGO) or by wastewater treatment plants. e Environmental Group has a longstanding commitment to combating these harmful pollutants.
By implementing advanced technologies such as wet and dry scrubbers, odorous emissions can be controlled, and their adverse e ects on human health and the environment mitigated.
Air and dust pollution control solutions are speci cally designed to support global and local industries and
businesses. e Environmental Group’s experts work to eliminate fumes and dust particles from emissions, tailoring their approach to meet customer needs and legislative requirements. is proactive strategy ensures that toxins are not released into the atmosphere, safeguarding the wellbeing of employees, communities, and the natural environment.
e Environmental Group’s energy services enable various sectors to access heat and steam while minimising energy consumption.
rough a recent agreement with Fulton Boilers, it is now o ering a complete range of high-quality heat transfer products.
“In Australia, our dedicated team o ers expert guidance and cutting-edge products to promote the use of the latest technology for a sustainable future,” Jason says.
“Moreover, we are actively involved in biomass and waste-to-energy plants
which convert waste materials into valuable energy resources.
ese initiatives not only reduce reliance on fossil fuels but also contribute to sustainable waste management practices, further supporting our mission to create a healthier environment and a sustainable future.”
e engineering team specialises in providing services for the gas turbine and solar industries, adapting to evolving consumption patterns and addressing current challenges.
“By providing damper and silencer solutions to reduce noise pollution from gas turbines, our team has quickly evolved and is now providing stateof-the-art gas turbine enhancements suitable for peaking load turbines, ensuring e ciency and continuous energy production, when required,” Jason says.
Aligned with the company’s mission, e Environmental Group is committed to transitioning the
energy market towards sustainable methods of generating energy and reducing the reliance on fossil fuels and gases.
Using solar and wind power o ers one of the most sustainable approaches to energy generation, although it poses challenges such as overheating problems with energy inverters.
e engineering team has devised a solution to prevent particle intake, causing overheating and explosions in inverters.
“ e Environmental Group Limited, in collaboration with our partners, clients, and sta , consistently showcases its expertise in engineering a sustainable future for both emerging and established industries and government sectors,” Jason says.
“We are committed to creating a cleaner, healthier world, one innovation at a time.”
For more information, visit: www.environmental.com.au
The Women in Industry Awards filled the Doltone House Hyde Park Ballroom. Do you know who won?
Derelle Mitchell’s drive to rekindle her career after raising her children led her to seize an opportunity to acquire the assets of a cosmetic manufacturing company in 2011, marking the humble beginning of Health Focus Manufacturing (HFM).
Starting with a small team in a “big green shed”, Derelle has grown HFM over the past decade to accommodate more than 40 sta members with more than 200 years of combined experience.
As the Managing Director of HFM, she has built a world-class manufacturing facility, ensuring a hands-on approach with a focus on e cient processes and quality products
while nurturing its partners. In June, Derelle was rewarded with the Woman of the Year award (sponsored by Fulton Hogan) and the Excellence in Manufacturing Award (sponsored by PACCAR Australia), at the 2024 Women in Industry Awards.
“I started this business from very humble beginnings,” she told a sold-out audience at Doltone House during the awards ceremony.
“ e most enjoyable thing I get from my job is getting people jobs, and I love what I do. My husband sees what I’m putting into the business. It takes a lot of blood, sweat, tears, and sacri ces for work every day.
“I wake up every day at 4 o’clock in the morning, and I love it, especially the people I work with. I wouldn’t be sitting here right now if it wasn’t for them.”
e Women in Industry Awards continue to celebrate the achievements of women in traditionally maledominated sectors such as mining, manufacturing, engineering and transport and logistics and hope to highlight these industries as great career choices for other women by acknowledging the success stories.
In 2024, the 11th annual awards showcased exceptional examples of industry advocacy, mentorship and sector excellence with a record 164 nominations received across 12 categories.
e judging panel faced a di cult task deciding the winners but in front of their peers across the country, 11 category winners and the Woman of the Year were announced.
Having the right mentor or mentors when entering a male-dominated industry is vital for ongoing success.
Kirstin Reblin, the winner of this year’s Mentor of the Year award, embodies the essence of the award through self-driven initiatives and unwavering advocacy for women as the General Manager of Transformation at Opal Packaging.
Kirstin has tirelessly fostered female talent at Opal across all functional areas, hierarchy levels, and sites, ensuring inclusivity and empowerment at every turn.
As a National Association of Women in Operations (NAWO) mentor since 2020, Kirstin has spearheaded expanding mentoring programs, including driving Opal’s NAWO Mentoring initiative and engaging senior leaders to participate as mentors.
Her dedication to fostering diversity is evident in creating “ inking Diversity: Women at Opal” in September 2022, a network boasting more than 450 members in March 2024.
She has championed women’s development through structured catchups and individual mentoring, as evidenced by heartfelt testimonials from several mentees and senior leaders.
“I’m so grateful to the Women in Industry Awards,” Kirstin said. “I want to thank everybody who is here and nominated for this award because we are putting ourselves out there to be courageous and go above and beyond.”
She said she continues to mentor others because she’s energised by seeing women grow in maledominated industries.
Acknowledging the Safety Advocacy Award winner recognises the best work in ensuring people’s safety.
e winner in 2024 is Kathleen Kelly, a Health and Safety Advisor at McConnell Dowell. With a management background spanning construction, operations, human resources, occupational health and
safety, training, WorkCover claims, and injury management, Kathleen is passionate about crafting and implementing health, safety, and wellbeing programs.
“I’ve been in the industry for a long time,” Kathleen said. “I love my job. I’ve been blessed with the industries and companies I’ve worked for. I work at McConnell Dowell, and I am proud to work with this company and its fantastic values.”
e Excellence in Transport Award (sponsored by Kenter Logistics) recognises an individual who has gone above and beyond to improve and positively impact the Australian transport industry.
Representing Swietelsky Rail Australia (SRA) is Anne Modderno, the rst female Managing Director of any Swietelsky international subsidiaries. She spearheaded the development of the company’s Sustainability Strategy, re ecting her dedication to driving positive social and environmental impact.
Beyond her professional achievements, Anne advocates for inclusivity and diversity within the sector, promoting initiatives to increase female participation and close the gender pay gap.
“If you ask any of my sta , family or colleagues here tonight, they will tell you that I have no trouble speaking at all,” said a shaken Anne. “But when I thought about coming up here and taking credit and being grateful for something I’ve done as an individual, I found it really uncomfortable and nerve-wracking. en I realised that this is why we need awards like this.
“We need to get uncomfortable to talk about what we have achieved. We need to get comfortable about being uncomfortable because if we can’t project that, no one else will see it.”
• Allyson Woodford (APA Group) –Excellence in Engineering (proudly sponsored by SEW-Eurodrive)
• Anne Modderno (Swietelsky) –Excellence in Transport (proudly sponsored by Kenter)
• Kate Leone (UGL – M6 Stage 1 Project) – Rising Star of the Year (proudly sponsored by Atlas Copco)
• Kathleen Kelly (McConnell Dowell)
– Safety Advocacy Award
• Kirstin Reblin (Opal Packaging) –Mentor of the Year
• Sandra Robinson (United Rentals)
– Business Development Success of the Year
• Sinead Booth (Fortescue) –Excellence in Mining
• Sinead Redmond (GeelongPort) –Excellence in Construction
• Steph Gee (CM & SM Gee Electrical) – Industry Advocacy Award (proudly sponsored by Komatsu)
• Vesna Olles (BOC Limited) –Excellence in Energy
• Derelle Mitchell (Health Focus Manufacturing) – Excellence in Manufacturing (proudly sponsored by PACCAR Australia) and Women of the Year (proudly sponsored by Fulton Hogan)
For more information, visit: www.womeninindustry.com.au
Waste Expo Australia attracts a global audience with breakthrough products, leading voices in the sector and networking opportunities. Will you be there?
Waste Expo Australia didn’t become the largest gathering of waste management and resource recovery professionals in the country by chance.
Behind the scenes, an advisory board brings together stakeholders from across the resource recovery, recycling, and waste industries. Together, they bring experience in a diverse range of sectors to the table, ensuring the expo
remains at the forefront of challenges and opportunities.
Michelle Mandl, General Manager of Communications, Customer, and Engagement with TOMRA Cleanaway, says evolving in response to industry and participant feedback is one factor behind Waste Expo Australia’s longevity and success.
On the advisory board for the past three years, Michelle says the expo has
a strong national presence because of its carefully curated conference program, plus an expo oor with more than 120 leading industry suppliers.
“Waste Expo Australia draws diversity from across Australia, and it a ords fantastic learning and development opportunities,” Michelle says.
“Being co-located with All Energy Australia gives it another dimension for
delegates to engage. at’s becoming more relevant as the renewable energy and waste sectors integrate.”
Staying relevant is vital, says Erin Ford, Senior Brand and Marketing Manager for Repurpose It. She says board members continue to question industry trends, areas of concern, innovations, or gaps.
Case studies also play a central role in showing attendees what is, and can be, achieved within the industry.
“ e expo is an area to learn and share knowledge,” Erin says. “Case studies can really step it up. ey can show people the impact a company or technology is having.”
So, what does the 2024 event have in store?
Plastics, batteries and the circular economy continue to be important.
“ e number of abstracts that focused on plastics highlights that they are a huge area of concern,” Erin says.
“With single-use plastics we are trying to change embedded behaviours. We’re improving, but it’s still a big issue.
“And we have massive issues with batteries across all waste streams.
“ e conference program will provide some insight into the challenges and what the industry is doing to address them.”
e expo has achieved 27 per cent visitor growth since the 2022 event. In 2023, more than 3500 professionals attended across the two days, putting exhibitors face-to-face with potential customers from Australia and overseas.
Attendees include local, state, and federal government, waste service providers, consultants, engineers, technology and equipment suppliers, project developers, facility managers and land ll owners/operators.
Erin says the cross-section of attendees is a big drawcard, providing exhibitors with the chance to engage with people they would normally not be exposed to. She believes crowd numbers are bolstered because the expo is free to attend.
“It removes the nancial barriers that could stop some people from
attending,” she says. “As exhibitors, Repurpose It makes a lot of connections through the expo.
“Education is a big part of Repurpose It, and the expo gives us a chance to highlight what we do while listening to the consumer market.
“Nothing beats face-to-face business. Whether you are already in the industry, new to the market or expanding in it, Waste Expo Australia provides access to key decision-makers.”
e 2024 Waste Expo Australia, to be held at the Melbourne Convention and Exhibition Centre (MCEC) from 23-24 October, will focus on advancing toward sustainable resource recovery.
Local and international suppliers, including representatives from Ireland, Germany, France, and Japan, have con rmed their attendance.
Exhibitor and sponsorship opportunities are still available.
For more information, visit: www.wasteexpoaustralia.com.au
The Waste Innovation and Recycling Awards help raise awareness, inspire change, and drive progress within the industry. Don’t miss your chance to be involved.
The Waste Innovation and Recycling Awards (WIRA) are not just acknowledgments of past achievements but also catalysts for future growth and innovation.
After a successful 2023 event, the 2024 awards are expected to garner even more interest. ey salute the companies and people who deliver value to the recycling and resource recovery industry daily.
e awards, held in conjunction with Waste Australia Expo, will take place in Melbourne on October 23, 2024, with a venue yet to be nalised. Industry heavyweights Veolia, REMONDIS, Visy, and ReGroup have signed on as sponsors, and more opportunities are still available. Organisers are agging record-breaking nominations across 10 award categories.
Resource recovery specialist Repurpose It has featured prominently at past awards. e operations team earned the Operational Excellence award in 2022, the year Founder and Chief Executive O cer George Hatzimanolis won Leader of the Year. In 2023, Jelena Hercegovac was awarded the Women in Waste.
George says the awards process is more than just a ceremony; it’s an
opportunity to re ect on how the company conducts its business, evaluate successes, and identify areas for growth. Re ection is invaluable in driving the company to continually improve and innovate.
He says while the awards shine a spotlight on the business and raise awareness of the important work being done within the industry, the visibility that comes with such accolades is crucial in educating industry stakeholders about the principles and bene ts of the circular economy.
“ e need for greater awareness and education in this area cannot be overstated. Awards are one vehicle for promoting this knowledge,” George says.
“Our commitment to sustainability and operational excellence is at the core of everything we do at Repurpose It. e recognition from WIRA validates our e orts and motivates us to push further. It highlights the dedication of our entire team and underscores the impact of our collective e orts on the environment and the industry.”
For Jelena, mentoring young professionals in the industry and encouraging and empowering more women to join the STEMM (Science, Technology, Engineering, Math, and Medicine) sector is a career legacy to aspire to.
“ at is what makes this award meaningful and special to me,” she says.
Nominations for the 2024 awards are now open and will close at 11.59 pm, Friday 30 August 2024.
Awards will be presented for Outstanding WARR Project (Metro); Outstanding WARR Project (Regional/ Rural); Operational Excellence; Innovation (proudly sponsored by Veolia); Outstanding Facility; Young Professional (proudly sponsored by REMONDIS Australia); Woman of Waste (proudly sponsored by Re.Group); Community Engagement Success of the Year (proudly sponsored by Visy); WIAR Workplace of the Year, and Leader of the Year.
“ e 2023 awards night was a highlight of our events calendar,” says the General Manager of Events for Prime Creative Media, Siobhan Rocks. “It is a very competitive industry, evidenced by the quality and number of nominations received.
“ e awards night is an ideal opportunity to network with peers and friends. But more than that, it’s an opportunity to highlight the inspiring
ideas and help grow individuals, organisations and the industry.”
Sponsorship opportunities are still available.
For more information, visit: www.wasteawards.com.au
Recognising excellence across the waste and resource recovery sector. Sponsorship opportunities are now available for 2024.
www.wasteawards.com.au
The Cutmetall group is a leading manufacturer and distributor of industrial knives, screens, spare and wear parts, as well as complete machine assemblies for the recycling and shredding industry.
Since 1996, the group has created solutions for customers in the size reduction industry to shred the respective input material, optimising their process and efficiency through quality products, customer-oriented services, and expert consulting.
As a full-range supplier with high market coverage, Cutmetall provides engineered spare parts and systems for more than 50 shredder and granulator brands including Eldan, Lindner, Vecoplan, Herbold, Previero and more.
The products are durable, economical, and precision-designed for individual machines and specific applications such as solid recovered fuel/refuse-derived fuel (SRF/RDF), tyre recycling, waste electrical and electronic equipment (WEEE), plastics,
Western Australia’s waste and recycling industry is pulling its weight to reach national targets, but the state needs a customised recycling model tailored to its unique geography, says Michael Bobrowicz, Executive Officer of Waste and Recycling Industry Association of Western Australia.
Watching the Senate Environment Committee hearing held in Sydney in May 2024: Inquiry into waste reduction and recycling policies, it probably escaped most people’s attention that what they were hearing and seeing was almost entirely an east coast view. Not to imply that there are no common issues between eastern
and western sides, because there are, but there are also many signi cant di erences that simply didn’t get an airing.
e East Rockingham and Kwinana waste-to-energy (WtE) power plants in outer Perth are about to come online, with a combined capacity of 700,000 tonnes.
No fuss, no bother with both plants; they are appropriately sited and will operate under State Governmentmandated emissions standards.
e Acciona plant at Kwinana was to start taking in feedstock in late June. Together, the two plants will play an important role in achieving the state’s waste strategy.
It was timely that in late May, the Western Australian Waste Authority issued its Waste Avoidance and Resource Recovery Strategy 2030 Consultation Draft. is draft document contains the clearest statement industry has yet seen on WtE, including the headline: Recover energy only from residual waste designed to ensure WtE feedstock is not recyclable material that should be recovered from higher in the value chain.
Jim Fairweather, Chief Executive O cer of Tyrecycle, was in Perth in May to o cially open the company’s tyre recycling plant in East Rockingham. With a capacity of 40,000 tonnes, including 7000 tonnes of crumbed rubber, and with a further feeder plant targeting the mining industry planned for Port Hedland.
Joint federal and state funding of $5.2 million supported the building of this plant and is widely regarded in Western Australia as one of the best applications of the Recycling Modernisation Fund to date.
Go Organics is mid-way through increasing the capacity of its Food Organics Garden Organics (FOGO) processing facility at Gingin, assisted by a $3.5 million grant from the federal Food Waste for Healthy Soils fund, allowing the processing of an additional 75,000 tonnes of organic waste each year.
Mastec is rolling out 80,000 new lime-topped mobile garbage bins (MGB’s) to Perth local government areas to keep up with the FOGO expansion.
Cleanaway has built Australia’s rst “post China National Sword” materials recovery facility (MRF) at Guildford. e MRF can process up to 200,000 tonnes of recyclables per year and recover up to 90 per cent of reusable product while delivering up to 99.5 per cent purity across bre and plastic outputs.
Containers for Change, already approaching 64 per cent container recovery, is now extending its focus to mine site operations where tens of millions of eligible containers are consumed. Trial container recovery projects at two large mine sites in the Pilbara are underway to capture those containers and avoid sending them to land ll.
REMONDIS Australia is installing a soft plastics pelletising unit that converts old plastics to top-quality pellets with a capacity of 5000 tonnes per annum.
Meanwhile, on the government side, since Main Roads WA (MRWA) put in place the Roads to Reuse (RTR) program four companies in Western Australia have completed the required quality assurance (QA) certi cation. Together, they have capacity to recover 400,000 tonnes per annum of QAcerti ed crushed recycled concrete (CRC) and one million tonnes of recovered sand. MRWA has mandated the use of 500,000 tonnes of RTR product in 2023-24.
Western Australia is currently the only state in Australia with uni ed statewide guidelines for what can and can’t go in both a FOGO and a yellow-topped recycling bin, removing the massive confusion that results when each local government area has its own speci cation.
It’s clear Western Australia still has a long way to go, but it’s also clear that the state’s waste and recycling industry is more than pulling its weight, as measured against any objective standard.
It doesn’t help, however, when policy makers at a federal level are focused on a model that simply is not viable in the west.
Western Australia is the largest state by area, and the logistics of collecting recyclables are formidable but never considered by national
policy. e state is geographically isolated from recycling hubs located in eastern Australia, transport distances are too large, and recyclers are unable to access synergies to support secondary recycling.
It is questionable if Western Australia has su cient tonnages of some product to support an economically viable stand-alone secondary recycling industry. e value of recyclables has declined in the state since the inception of export bans, and recyclers are transporting material to New South Wales and South Australia to secondary processing facilities to gain export licences. At which point, the carbon footprint of moving those recyclables has negated any recovery bene t.
Australia is a federation of states, with each state uniquely delivering solutions that t local conditions.
e Federal Government has responsibility for the country, including Australia’s relationship with the rest of the world. Mostly this works out, or at least it’s a constant interplay and negotiation.
Western Australia has a unique commercial advantage, and that is its proximity to Asia, one of the largest markets in the world. Unfortunately, the Recycling and Waste Reduction Act and export bans have negated that advantage.
One size doesn’t t all, and progressive Australian governments need to understand that ‘same’ is not necessarily equal. Western Australia needs a customised recycling model that focuses on its unique geography, and above all it needs a model that is exible and responsive to di ering market conditions.
ere is no one single perfect answer to how Australia achieves an 80 per cent recycling target, but sti ing innovation across Western Australia won’t help.