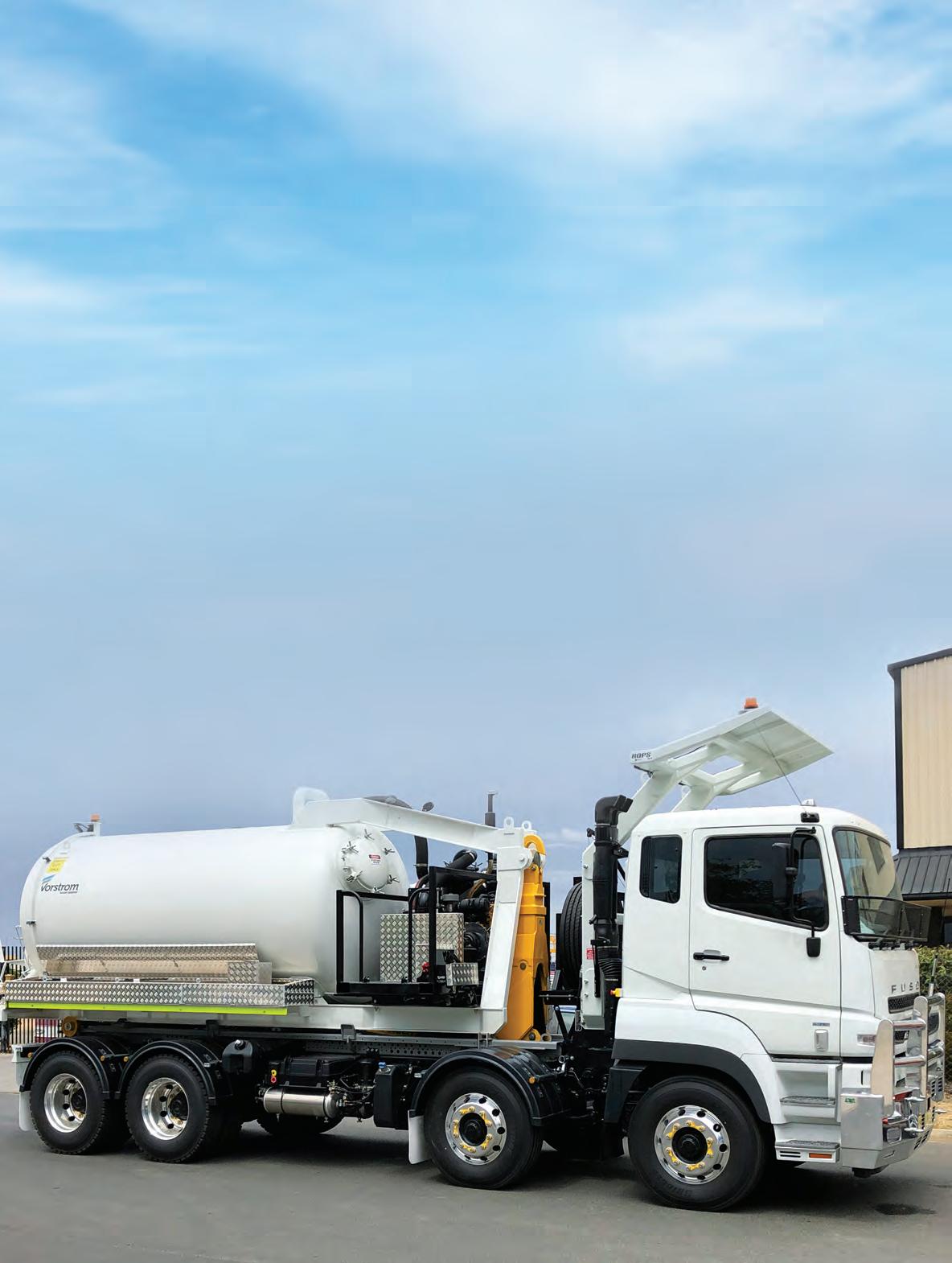
4 minute read
LIFTING SUCKER TRUCKS
WITH FLEXIBILITY AND SECURE CONTAINMENT CRITICAL TO LIQUID WASTE MOVEMENT, DARRYL WIGGINS OF VORSTROM DETAILS A SOLUTIONSBASED COLLABORATION WITH PALFINGER. D esigned to suck often contaminated liquids, sludges and slurries from their point of origin to a tank for disposal, vacuum trucks, also known as sucker trucks, require precise componentry. This is a reality known all too well by Darryl Wiggins, Vorstrom National Sales Manager, who has been working with liquid waste for over 30 years.
Vorstrom specialises in the manufacturing and sales of a wide range of liquid vacuum trucks, with clients ranging from the mining sector to essential services. According to Darryl, his truck models are well suited to any type of liquid including grease trap waste, septic and sewer waste and oily water.
Darryl says the variability of his client base highlights the evergreen nature of waste and disposal. He adds that no matter the scope or sustainability initiatives of a client’s operations, there’s always material that requires carting away.
“When transferring sludge, slurry or other liquid waste, it’s incredibly important that the equipment is sturdy and reliable. Constant operator feedback guides our product development to ensure our units are easy to use, adaptable to different conditions and fully functional,” Darryl says. In late 2019, Darryl engaged Palfinger, through QLD/ NT Hook and Skip Loader Account Manager Glen Woodrow, to design and install a T22A hookloader on a Vorstrom vacuum truck.
“One of our clients needed a solution for a very remote site in Western Australia. They required a truck capable of transporting a range of waste products and performing multiple tasks,” Darryl says.
“To address the customer’s requirements, we collaborated with Glen to manufacture a stand-alone hookloader vacuum unit that can operate on and off the truck.”
Vorstrom’s aim, Darryl says, is to
ensure that regardless of the material in use, Vorstrom vacuum trucks work to reduce total cost of ownership. He adds that this is a value shared by Glen and the entire Palfinger network.
“We aim to provide our clients with trucks they can count on, so it’s important we ensure all the componentry is top quality, which is why we rely on Palfinger for our hookloaders,” he says.
“We have known Palfinger’s sales representatives for many years and often discus upcoming projects and hookloader concepts with them. We can rely on Palfinger’s knowledge base and ability to incorporate the appropriate technology into our Vorstrom vacuum units.”
Palfinger has acted as Vorstrom’s preferred supplier for hookloader trucks for some time, Darryl says, highlighting the quality and flexibility of their units, and their team’s willingness to attack challenges head on.
“Palfinger has always stood out as a provider of quality hookloaders. Their products are consistently a good match for the units we supply to customers, so working with them on this project was an obvious choice,” he says.
The telescopic T22A hookloader facilitates the use of tanks and containers with different lengths. The telescopic function makes it easy to operate, Darryl says, with universal application and increased tipping force due to a bi-point design.
“The hookloader’s bi-point design means horizontal forces are reduced and tipping capacity is increased, resulting in maximum uptime and efficiency for our client,” Darryl adds.
The units come standard with an articulated arm, allowing the transport of shorter tanks, and flexibility in loading and unloading. Palfinger supplies mounting kits specifically designed to fit, Darryl says, with a fast
The T22A’s design reduces cargo movement to facilitate liquid waste transport.
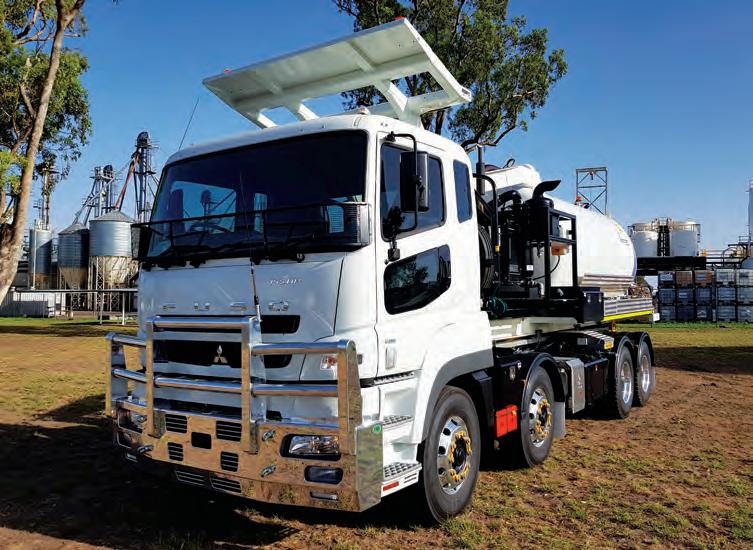
and easy fitting process, ensuring a durable and reliable unit.
The unit also comes with an automatic mechanical safety latch that secures tanks from falling during loading and unloading. Darryl says this means drivers c an open the latch on demand, providing additional safety value for his clients.
“In addition to the hook and standard rear locking mechanisms, Palfinger offers an additional front external locking system, which significantly reduces cargo movement by increasing container handling from three to five points of contact. This makes it safer to carry loads of sludges and liquids, as less force is required to secure the container while the vehicle is in motion,” Darryl says.
The T22A also features integrated in-cab controls, Darryl says, which position the articulated arm during low loading situations, creating a maximum tipping angle of 48 degrees.
Before assembly, the unit’s main components are sandblasted, degreased, primer painted and electrostatically coated according to customer specifications. All additional parts are treated for anti-corrosion, maximising the life of the unit and providing greater resale value.
“The hookloader vacuum unit is designed to support the liquid waste requirements of our client’s site, as well as the movement of dry waste hooklift bins – one truck, multiple uses,” Darryl says.
“The customer also has a tray for the unit, which enables the transportation of bulky materials and products to their site. This flexibility is highly valued, by both Vorstrom and our client.”
Darryl notes Palfinger’s attention to after-sales support, highlighting Vorstrom’s relationship with Glen as a key driver for their continued collaboration.
“Glen has also been very helpful with pre-and after-sales support at Vorstrom’s manufacturing facility. He’s always available in person to ensure our hookloaders are commissioned and working to Palfinger’s specification,” Darryl says.