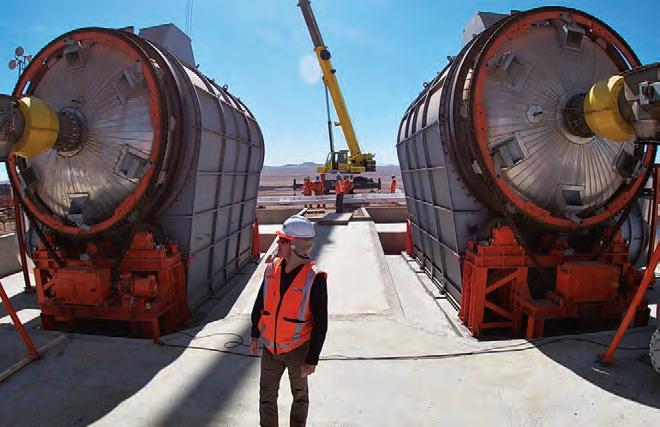
5 minute read
OFF-THE-ROAD TYRE TRACTION
A CRITICAL FIRST STEP TO ACCELERATING OFF-THE-ROAD TYRE RESOURCE RECOVERY HAS BEEN COMPLETED, WITH THE RELEASE OF A NEW REPORT COMMISSIONED BY TYRE STEWARDSHIP AUSTRALIA.
While the Australian tyre recycling conversation has traditionally focused on passenger and truck tyres, the disposal and recycling of off-the-road (OTR) tyres is largely uncharted territory.
OTR disposal and recycling is particularly challenging in the mining sector, where their size, construction and remote location makes material processing onerous.
To get an accurate picture of OTR, Tyre Stewardship Australia (TSA) engaged Randell Environmental Consulting for a research projec t. Working with Brock Baker Environmental consulting, the firms completed an analysis of the consumption and fate of OTR tyres.
The analysis was borne from the recommendations of a previous report that same year which identified the need to better understand OTR tyre consumption and fate. This was given the estimated recovery rate in 2018-19 was a mere 11 per cent, compared to 89 per cent recovery within the passenger and truck sector. The remaining 89 per cent of OTR tyres were not recovered, with an assumed 81 per cent disposed onsite at mining, farming or similar sites.
The report covers the agriculture, aviation, construction, manufacturing and trade and mining sectors. In breaking down the findings, the mining sector had the highest OTR generation in 2018-19 at 68,000 (58 per cent), followed by agriculture at 31,400 (27 per cent) and the other sectors. Combining all the sectors collectively, the five-year average for OTR generation is around 119,000.
Importantly, the report is an entry point to facilitate more informed discussions and does not look to provide the answers to improved used mining tyre recovery.
Lina Goodman, TSA CEO, says stakeholder interviews and visits will inform further information-gathering.
“OTR tyres have been left off the discourse for a while. This is largely because the opportunites to manage them from a resource recovery
KALTIRE is building a plant at Le Negra, Chile, which will be capable of processing 7500 tonnes per year of large mining tyres.
perspective haven’t been there, or were limited. We’re now starting to see that change,” Lina says.
“While OTR research has traditionally focused on the mining sector, this report tells us there are other parts of OTR that are just as important like agriculture and construction.
“What’s significant is they may be a little bit simpler to manage than the large earthmoving tyres on mining sites.”
WHAT HAPPENED TO THE TYRES? Australia’s used OTR tyres are subject to a range of different fates possible, including retreading for reuse, civil engineering, turned into processed
rubber products, pyrolysis, stockpiles, landfill and exported overseas. The report’s authors consulted with state and territory regulators and the used tyre recycling industry to understand the fate of these tyres.
Around 93 per cent of used OTR tyres within the mining sector, or 63,300 tonnes, went to onsite disposal.
Industry consultation finds that while repair of large mining tyres is a well-established practice, retreading of OTRs is not practised in Australia except in aviation, where retreading is a normal practice.
Civil engineering is not a significant fate either, with an uptake of around 1200 tonnes of used OTR tyres used in the construction of retaining walls or similar.
Notably, illegal stockpiling, excluding onsite disposal of OTRs was not common in 2018-19, with only 2300 tonnes. Likewise landfilling is unlikely (at 4000 tonnes) and pyrolysis and crumb, granules and buffing is rare.
An estimated 14,400 tonnes of used OTR tyres were exported overseas for processing in 2018-19, with 2500 tonnes of this from the aviation sector. The remaining 12,000 tonnes is believed to be from the construction and manufacturing sectors and sectioned into manageable sized pieces for export.
FUTURE AND EXISTING PRACTICES After consultation with key mining jurisdictions (WA, QLD, NSW and NT), environment protection agencies and the waste industry, the report highlighted the various storage practices which differ from state to state.
Onsite disposal has been the historical practice as there hasn’t been alternatives. The report points out that mining companies should expect the current practice to cease.
A key point is that only a few of Australia’s used tyre processors
Lina Goodman, TSA CEO
are currently able to receive large mining OTR tyres.
Moreover, the report estimates the collection cost of large mining tyres can fall anywhere between $300 to $770 per tonne, with indicative processing per tonne a further $300 to $800 per tonne depending on the recovery outcomes.
All jurisdictions consulted allowed onsite tyre disposal but the requirements were nuanced.
For example, WA permits used mining tyres to be disposed onsite in designated areas defined in the mining site environmental licence. Conversely, Queensland had no limits on quantities or location for onsite storage and disposal, but specific projects had their own requirements. Consultation with EPA NSW staff found that mining tyres were allowed by EPA to be stored and disposed onsite with no limits on quantities or location.
QLD, NSW and WA are all reviewing the current practise of allowing onsite disposal and the QLD Government has raised the issue with the Minerals Council of Australia.
Other areas such as converting mining OTRs into crumbed rubber and steel or tyre-derived fuel are technically feasible, but energy intensive.
Recovery by pyrolysis remains an emerging option, with several sites in Australia targeting used mining tyres as a primary feedstock. This includes the Pearl Global facility and Tytec Recycling as examples which are all based in Queensland.
“The good news is there is a lot of interest from organisations to invest in providing solutions for the sector,” Lina says.
As for the critical next steps? An OTR working group is already underway comprising the earthmoving sector, tyre companies and government.
To improve Australian OTR recovery, the report proposes a range of options to consider. This covers continued collaborative discussions via the working group and OTR manufacturers contributing to the scheme with an aim of expediting the solutions.
Additionally, State and Federal Government intervention is also proposed with a regulatory framework to support these activities.
The framework should work in tandem with OTR sector moving towards the cessation of onsite disposal in all jurisdictions. Recyclers could then support that by developing onshore energy markets for tyre-derived fuel recovery.
Lina says all of these factors, in addition to a roadmap coming in 2020 from the working group, will be critical to achieving change.