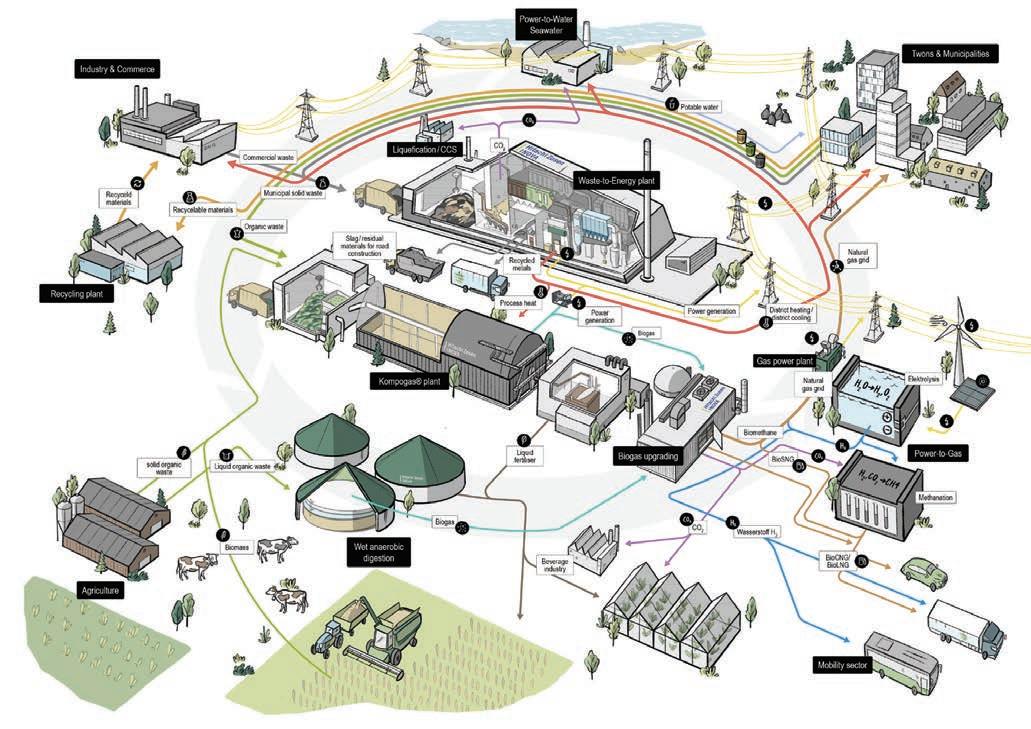
4 minute read
LEADING THE CHALLENGE
GLOBAL CLEANTECH COMPANY HITACHI ZOSEN INOVA IS SETTING THE STANDARD IN DEVELOPING WASTE PLANTS AND SUSTAINABLE ENERGY FOR THE FUTURE.
A graphic of HZI’s vision of the circular economy – the plant of the future.
Waste prevention, reuse and recycling are key priorities as countries strive to tackle what has been described as the “biggest challenge of our age” – managing waste resources more sustainably, reducing carbon footprints and progressing toward a circular economy.
Hitachi Zosen Inova (HZI) has been building and maintaining waste management plants for almost 90 years and is constantly evolving to develop new technologies that provide long-term, proven solutions to world problems in sustainable waste management.
The company develops projects alongside clients and then draws on its experience as an engineering, procurement and construction contractor to deliver turnkey plants and systems solutions for thermal and biological Energy from Waste (EfW) recovery, gas upgrading and Power to Gas.
Dr Marc Stammbach, HZI’s Managing Director for Australia, says the company’s technologies focus on the efficient recovery of energy from solid and organic waste, reducing the need for landfill, which produces climate-degrading methane gas.
“Our long experience, comprehensive engineering and project management skills allow us to implement forwardlooking projects in our core areas: EfW, fl ue gas treatment and residue handling, as well as anaerobic digestion and biogas upgrading,” he says.
“HZI always looks at what technical solutions it can offer the market and developing more technologies to build up solutions to support circular economies. The treatment of residues from EfW, for example, is now an urban mining concept – HZI recovers metals and other raw materials with effi cient combinations of dry and wet deslagging.”
Marc says one of HZI’s most iconic EfW facilities is under construction for the city of Dubai. The joint venture between HZI and BESIX (Belgium) will realise one of the world’s biggest EfW plants and be a key component in Dubai’s sustainability strategy.
The two companies will not only build the turnkey facility, from 2024 they will operate the plant for 35 years.
It’s not just the size of the plant that’s impressive, net energy effi ciency of more than 31 per cent puts it at the very top of the international rankings.
PLANTS FOR THE FUTURE
Through new technology and innovation, HZI has developed equipment that can even recover salts from fl ue gas treatment residues. It has also signed a Memorandum of Understanding with leading suppliers of carbon capture use and storage technologies, enabling HZI to offer its customers solutions that are tailored to their specifi c needs.
“We look at each of our technologies to see if we can improve them for our customers and the environment,” Marc says. “For example, we now have hydrogen production technologies in our portfolio, as well as hydrogen liquefaction, biological/catalytic methanisation, and further Power to Gas concepts.
“Ultimately, all of HZI’s technologies for waste stream management view the building of circular economies as an opportunity.”
HZI has also made a name for itself in the renewable gas sector. This is partly because solutions are offered for both wet and dry digestion, but also because HZI owns two of its own plants, one in California and one in Sweden.
At the San Luis Obispo plant in California, about 33,000 tonnes of source-separated organic waste are processed into biogas annually using HZI’s Kompogas dry anaerobic digestion process. This produces more than six million kilowatt-hour per annum of electricity and about 1500 tonnes of liquid fertiliser.
In addition, 16,000 tonnes of solid digestion residue are produced annually, which will be processed into 1200 tonnes of green hydrogen and 2500 tonnes of biochar in the future through a pilot project with the Canadian specialist CHAR Technologies. The hydrogen is expected to be fed into the grid, while the biochar can be used for the upgrading of agricultural land.
Marc says this will completely close the material cycle of the plant.
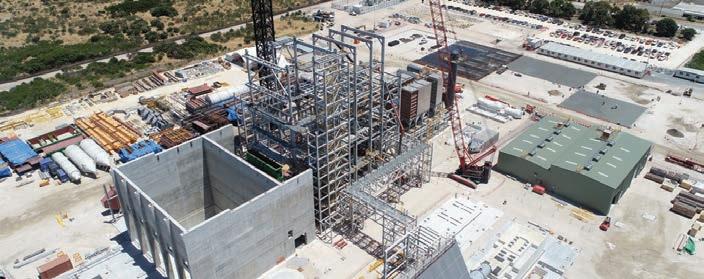
CLOSING THE CYCLE
He says the challenges of the circular economy are enabling ever better processes. The most recent example is in EfW decarbonisation. HZI has reached an agreement with suppliers to develop joint concepts for several processes. The captured CO2 can not only be separated from the fl ue gas but can be converted into a valuable product by means of mineralisation.
In this case, the CO2 is converted with calcium into mineral calcium carbonate, a stable, non-hazardous/nontoxic and valuable component, which is used, among other things, as a raw material in construction, as a fertiliser and as a mineral fi ller in the paper, paint and plastics industries. Due to the high capture rates, EfW plants can become carbon sinks through these processes.
HZI’s East Rockingham 300,000 tpa project in Perth is under construction. It will be operated jointly by HZI and SUEZ and will recycle aggregate and metals. Once the plant enters full operation in 2023, the owners will also evaluate value-add options such as Power to Gas, salt mining, and carbon capture.
The path that HZI is taking is not an easy one, because it is always entering unknown territory, but Marc says the development has shown it is the right way to master the challenges of the circular economy. “The most important prerequisite for such an approach is to work with very agile and fl exible teams in all corners of the world,” he says.
www.erwte.com.au Image supplied:
The Rockingham Waste-to-Energy plant under construction. For more information, visit: www.hz-inova.com
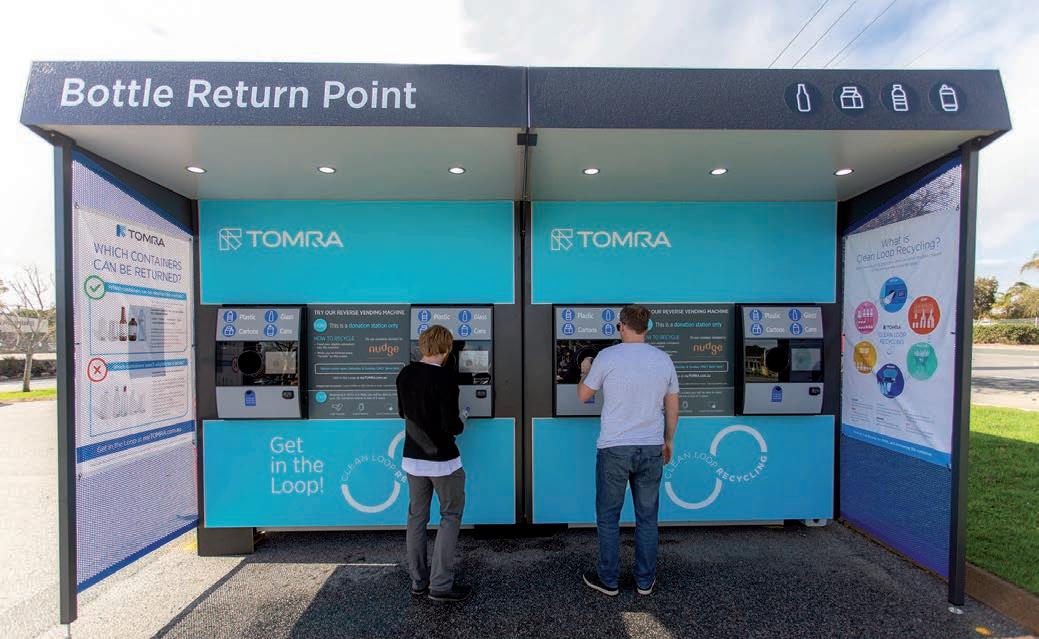

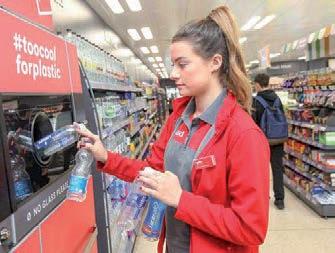
