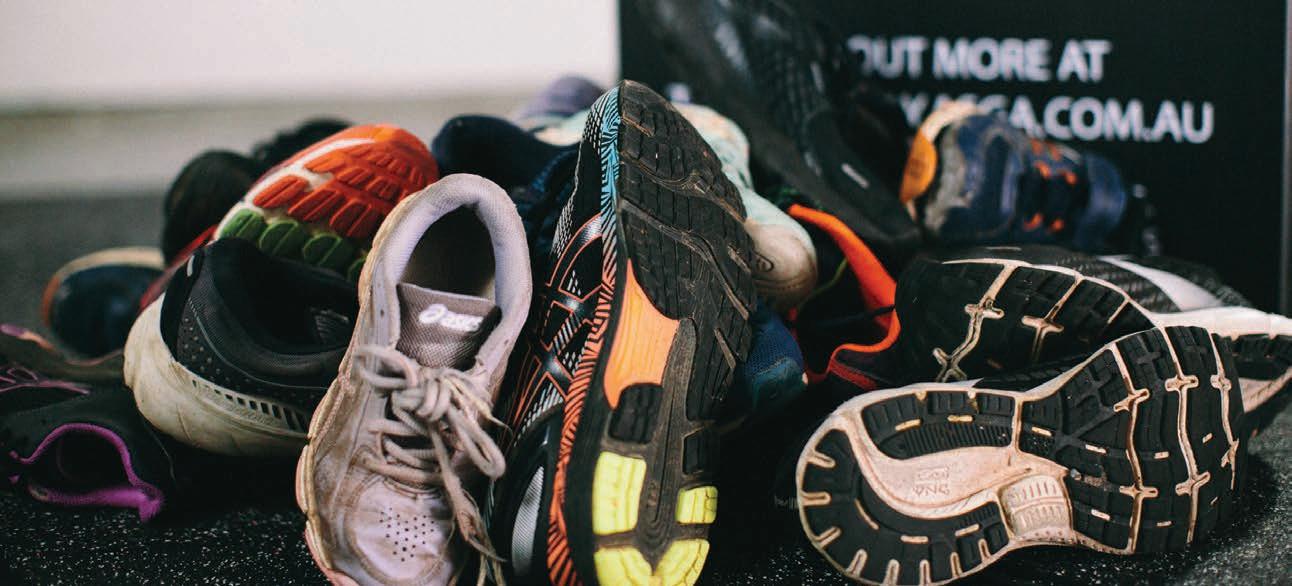
16 minute read
FEATURE NEWS
Sole traders
TreadLightly aims to recycle more than one million pairs of sporting and athletic shoes by June 2023.
AUSTRALIAN SPORTING GOODS ASSOCIATION IS WALKING THE WALK WHEN IT COMES TO RECYCLING AND SUSTAINABILITY. SHAUN BAJADA, ASSOCIATION EXECUTIVE DIRECTOR, EXPLAINS.
New research shows Australians are stockpiling more than 100 million unused shoes – posing major landfi ll and environmental concerns.
TreadLightly, a new industry-led national recycling initiative powered by the Australian Sporting Goods Association (ASGA) and recycler Save Our Soles (SOS), is giving unwanted sports and active lifestyle shoes a new lease on life as mats and fl ooring for retail stores, gyms and playgrounds.
“TreadLightly exists to solve a very real industry issue,” says Shaun Bajada, ASGA Executive Director. “We’re committed to working closely with retailers, manufacturers and consumers to reduce the industry’s environmental footprint and to stop millions of shoes ending up as landfi ll every year.
“Over 110 million shoes make their way to Australian shores each year, of which 25 million are sporting and athletic lifestyle footwear. The wider industry, as well as consumers, want to do more to reduce their environmental impact and TreadLightly makes it easy for everyone to do their bit for the planet.”
TreadLightly involves pre-loved sports shoes being dropped off at a designated collection unit at participating retailers. Footwear is collected and sent to a recycling plant in Australia for sorting, break-down and processing. Reusable components are extracted, including rubber, leather and fi bres, and reclaimed materials are used to manufacture new products.
The program, backed by Federal Government, aims to recycle more than one million pairs of sporting and athletic shoes by June 2023 to save more than 400 tonnes of footwear going to landfi ll.
It might sound ambitious, but Shaun says the program is already walking tall – just three months in – and 40 tonnes of pre-loved shoes were collected nationally.
Shaun says 100,000 pairs of shoes were recycled through a pilot program during the COVID-19 pandemic
Unwanted sports and active lifestyle shoes are being given a new lease on life as fl ooring for retail stores, gyms and playgrounds.
and the fi rst of many lockdowns in Victoria in 2020.
“It showed there was an appetite still to recycle shoes,” he says. “This is the start of a program that’s going to make a difference and only get bigger. This is really what an industry association is all about, bringing in multiple brands and competitors for a common good.”
Shoe components can take more than 1000 years to break down. In September 2021, research by market research agency 10 THOUSAND FEET, commissioned by TreadLightly, found that the average Australian admits to owning about fi ve pairs of shoes they don’t wear – the equivalent of 100 million shoes that could go to landfi ll.
Nearly a quarter of respondents (24 per cent) keep their old shoes, with many people admitting it’s for a rainy day or for sentimental reasons, while half of respondents (51 per cent) confess to simply throwing their unwanted shoes in the rubbish.
“This research highlights just how many shoes are collecting dust at home, and how many shoes end up in the rubbish because we don’t know what else to do with them,” says Shaun.
He is encouraging everyone to “look around your home for any unwanted sports of active lifestyle shoes, from sneakers and trainers to golf shoes”, and take them into participating TreadLightly retailers.
So far more than 400 locations across Australia are involved in the program. Collection partners include adidas, Asics, Converse, Globe, Rebel, SportsPower and The Athlete’s Foot.
“At the heart of the program, we want to make it easy for collection sites to manage and be a part of,” Shaun says. “We also want to make this truly circular in nature and highlight how easy it is.
“We’ve been able to achieve this through collaboration. It’s great for partners because they can tell their own story about sustainability, but they’re also part of a bigger story.
“The end goal is to create a program that’s self-sustaining by the brands, that is free and easy for consumers and it becomes as easy as recycling paper and glass and plastic. We want this to be around forever.”
Rita Kimmerle, Group Sustainability Manager for Accent Group says TreadLightly aligns with the company’s own objectives for sustainability and recycling.
She advocated for a group-wide commitment to TreadLightly when she joined the company last year.
“We conducted a team engagement survey in June (2021) which provided the opportunity for team members to give feedback across a range of areas, including sustainability,” Rita says.
“It’s very clear our team members are very much supportive and engaged in sustainability initiatives.
“Our association with TreadLightly has really put a ‘fi re in the belly’ to move forward with our sustainability initiatives.”
Rita says while collection points for recycled goods are not new for customers – think soft plastics recycling at Coles or Woolworths and the opportunity to recycle sheets and towels at Sheridan – she expected a “slower burn” for the collection point program. However, this was not the case. The program has been successful.
Accent Group has now extended the program beyond retail stores and into its warehouses.
Faulty shoes, or shoes not able to be sold, are donated to charity organisations for distribution. However, any shoes not fi t to be donated are sent to TreadLightly for recycling.
A new initiative, being trialled in The Athlete’s Foot outlet stores, also offers some “less than perfect” shoes at a discount price.
“We’re trialling a number of initiatives,” Rita says. “Repurposing is also a key for us.
“Our sustainability program has made a signifi cant impact on our team and customers and shows that, for us, recycling and repurposing is more than just putting a few recycling bins outside. It’s something we can really foster in the community.”
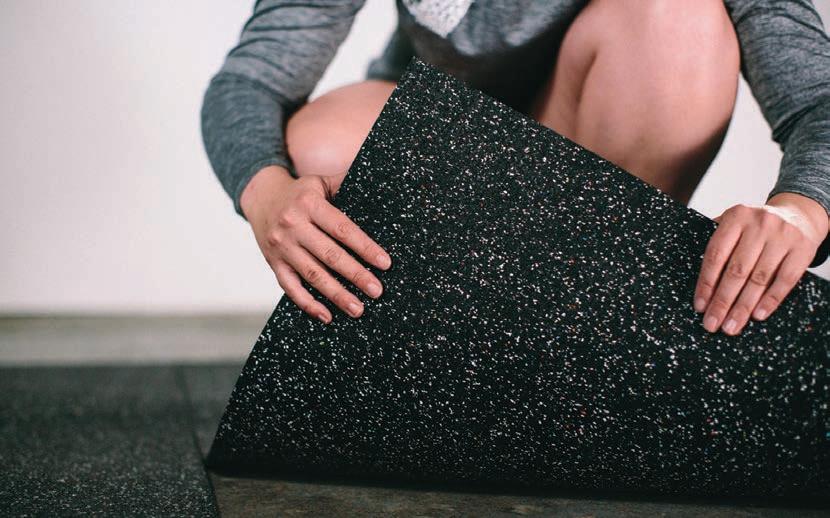
Springing to action to make a change
A NEW PARTNERSHIP IS HELPING PUT AN AGE-OLD WASTE MANAGEMENT ISSUE TO BED.
Douglas Shire Council is teaming up with disability service provider Endeavour Foundation to reduce the number of mattresses going to landfi ll, while creating jobs for people with disability.
More than 1040 mattresses were sent to landfi ll in the region last year. The joint initiative aims to recycle about 70 per cent of those, and in the process save more than 693 cubic metres of waste from going to landfi ll annually.
Michael Kerr, Douglas Shire Mayor, says anyone who has ever moved house or replaced their mattress knows they are bulky items, but once dismantled, they are easily recyclable and lead to a signifi cant reduction in waste.
“Once the springs, wood and other recyclable parts are pulled out, 100 mattresses can be reduced from 130 cubed metres of waste to just one cubed metre in waste,” he says. “Council is proud to join Endeavour Foundation and contribute to a really fantastic social outcome that also benefi ts our local environment.”
Providing work opportunities is one of three key platforms that Endeavour Foundation aims to fulfi l in supporting people with disability.
The foundation has up to 2000 people employed in “business solutions” – anything from assembling wheelbarrows, to making beef jerky and waste minimisation projects.
Paul Gunn, Endeavour Foundation National B2B Account Manager, says the mattress recycling initiative is a win for the environment and for employees with disability.
“Everybody now is more aware of minimising what goes into landfi ll both from a council point of view and the public questioning what their footprint is,” he says.
“For us, there’s the environmental impact but more importantly, its meaningful employment impact. We’re actively chasing these opportunities because it’s the right thing to do environmentally, and it provides another level of opportunity for people with disability to live their best lives.”
Paul Lydiard, a supported employee at Endeavour Foundation’s Mareeba Disability Enterprise says he enjoys dismantling mattresses, knowing it helps reduce landfi ll.
“It is fun and good to do the mattress recycling. It’s a different job to do,” Paul says. “I feel happy that I am helping the council to make space at the dump – it’s important.”
John Galligan dismantles and sorts e-waste in Townsville. He says that after working for 30 years he’s “getting [to be] an old boy now”.
“You take the screws out fi rst and put them in the bucket. Cut the wires and take out the circuit boards. A magnet tells you if it is metal or not.”
John says the best part of the job is going to work.
In the 2020-21 fi nancial year the Endeavour Foundation processed more than 13,000 tonnes of waste including 2688 tonnes of cardboard, 1464 tonnes of paper, 900 tonnes of e-Waste, 395 tonnes of plastics, 1715 tonnes of glass and 1400 tonnes of household goods.
Through partnerships it has successfully established e-waste processing sites at Townsville, Redcliffe and Southport, providing employment to more than 80 locals with disability. It is also one of the largest document destruction services in Queensland.
Paul Gunn says Endeavour Foundation employees work directly with councils across 27 waste transfer stations, managing about a dozen tip shops. The foundation is in discussions to extend its mattress dismantling program and other opportunities.
The foundation is being approached for customer-specifi c waste solutions, including recycling oil testing kits for a heavy machinery manufacturer.
“The long-term goal is to continue to expand our waste minimisation strategy and explore any avenue,” he says. “We like to think we can fi nd a solution to any commercial customer’s need.”
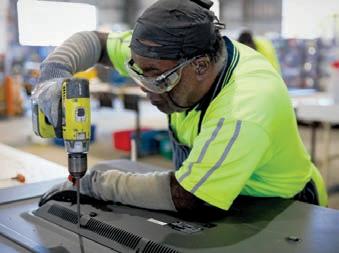
John Galligan has been dismantling e-waste for 30 years.
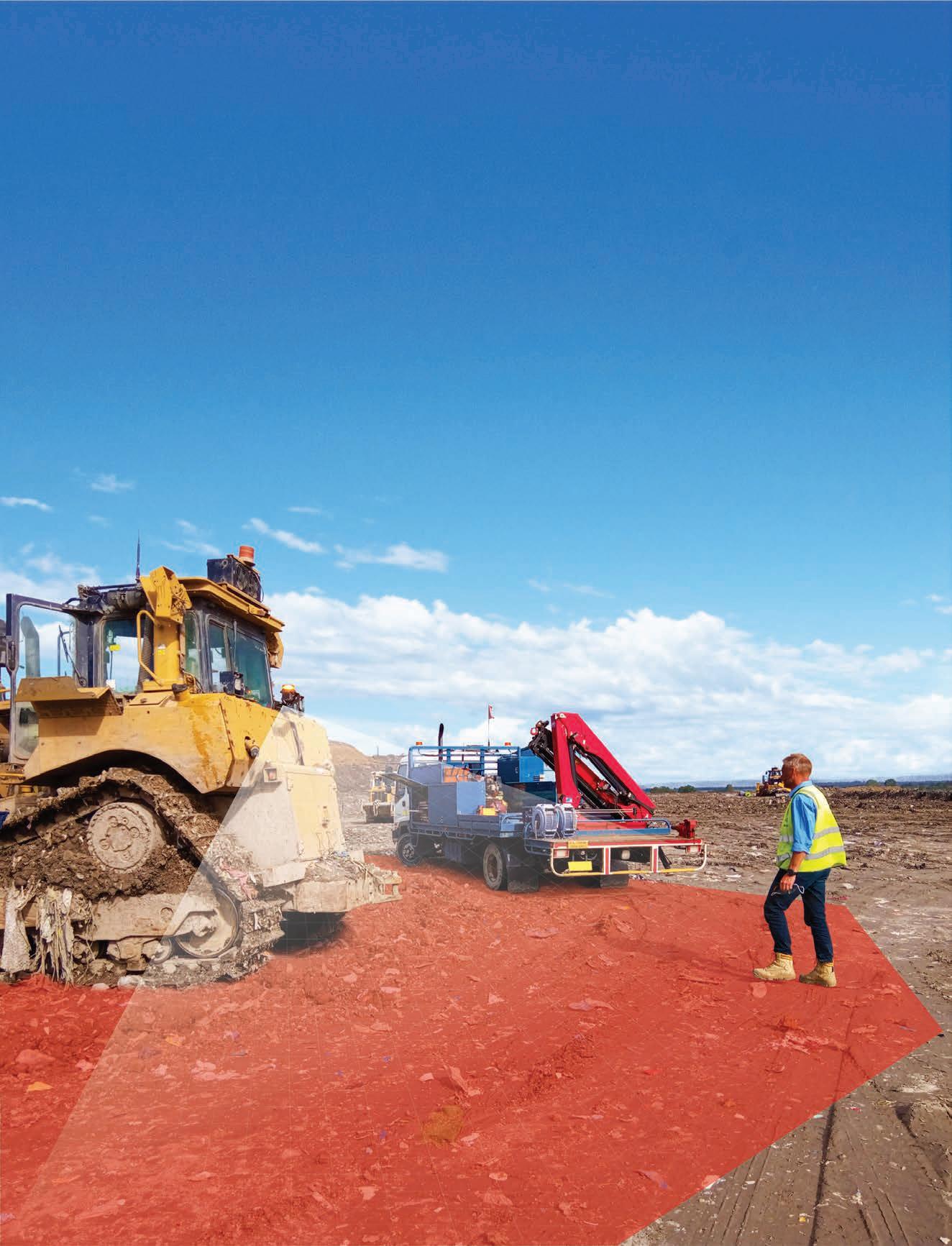
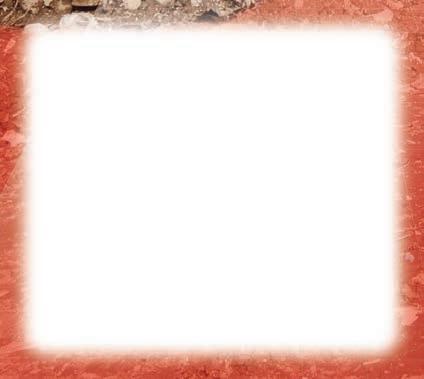
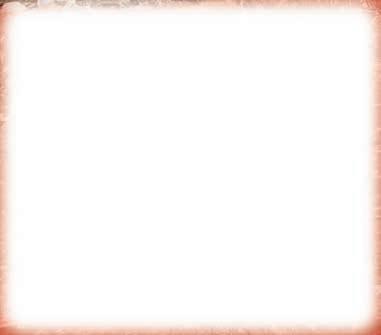
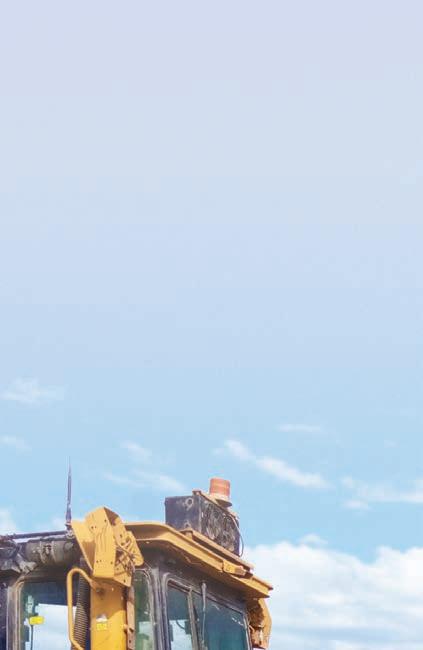
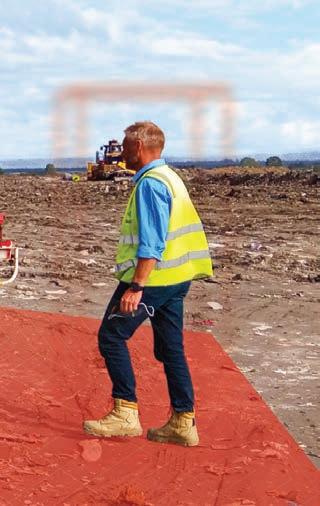
Supporting a FOGO focus
FOCUS ENVIRO IS SUPPORTING THE MACHINERY REQUIREMENTS OF SUEZ’S GREEN WASTE PROCESSING SITE AT EASTERN CREEK, IN NEW SOUTH WALES. SITE SUPERVISOR TERI TE WHIU EXPLAINS THE IMMEDIATE IMPACT THE MACHINES HAVE HAD.
The incorrect disposal and storage of green waste is a widespread issue in the waste sector, requiring alternative forms of processing and treatment.
SUEZ’s Eastern Creek site, in New South Wales, uses modern technology, machinery and skilled operators to provide sustainable outcomes for the local supply of green waste.
Teri Te Whiu, Site Supervisor, says the operation is helping to establish a circular economy, a market that is still in its infancy but is a priority area for SUEZ.
“We receive green waste material, which we then recycle into top dresses and garden mixes and then distribute back to the community,” she says. “These products are mainly coming from community parks, councils and transfer stations, as well as landscapers.”
Eastern Creek green waste service not only diverts materials away from landfill but also reduces the volume of methane gas released into the atmosphere – a double win for the environment.
Once received, green waste is sorted on site at the site’s picking station. It is here that contaminants such as paper and plastic are removed, to enable efficient processing. Kerbside collections are also received at the site.
Teri explains it is at local council kerbside collections that green waste can become contaminated. She says this contamination, in many cases, can be attributed to a lack of knowledge surrounding the correct disposal of green waste.
“I think currently there isn’t enough education out there in the community regarding green waste. This is an aspect which has heavily contributed to green waste still ending up in landfill,” Teri says. “Education is proving to be effective for streams
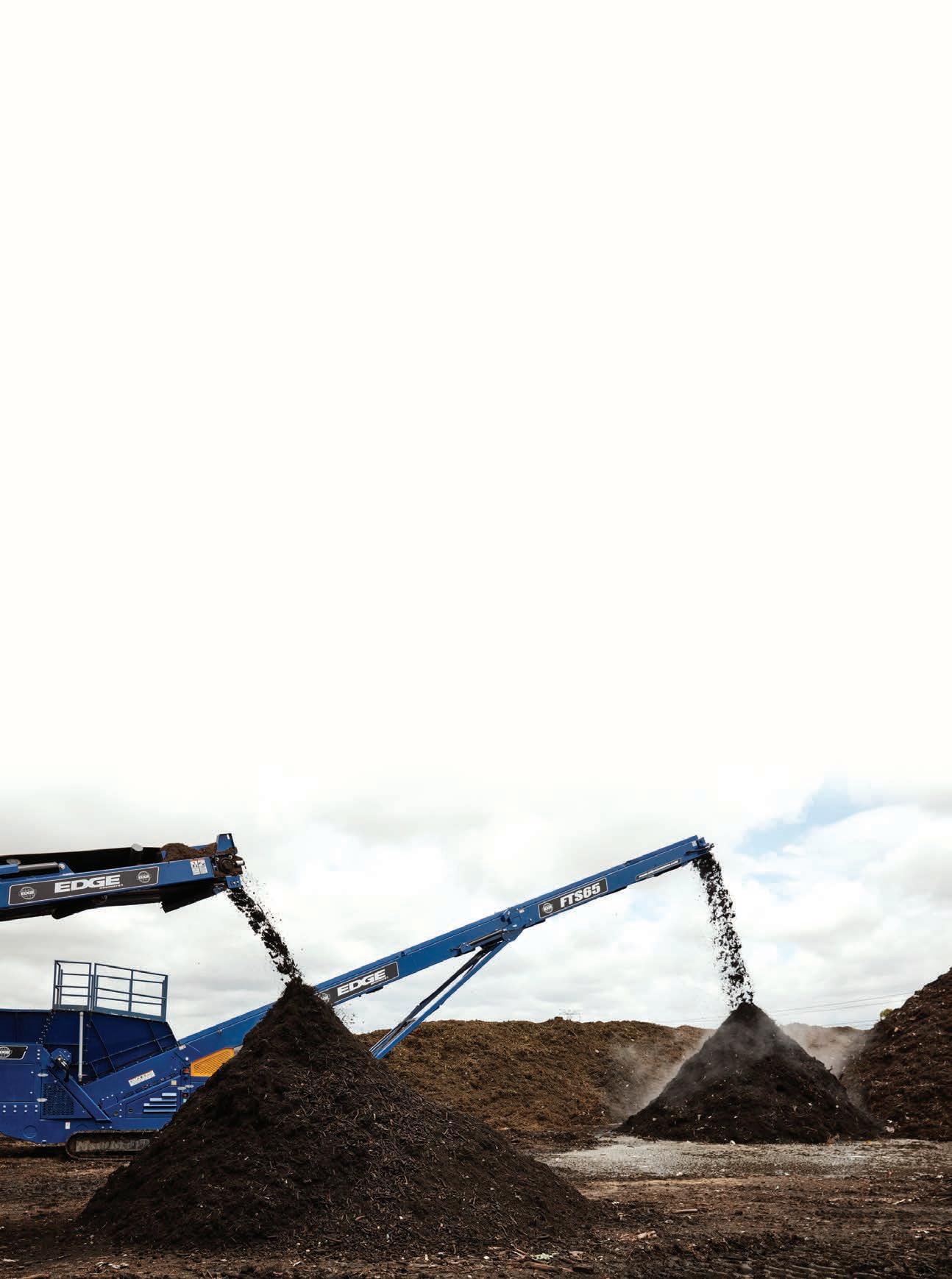
The Eastern Creek site looked to Focus Enviro when selecting new machinery.
The Eastern Creek site has added the FTS65 Mulch Master and the TRT622 Tracked Trommel to its existing machinery.
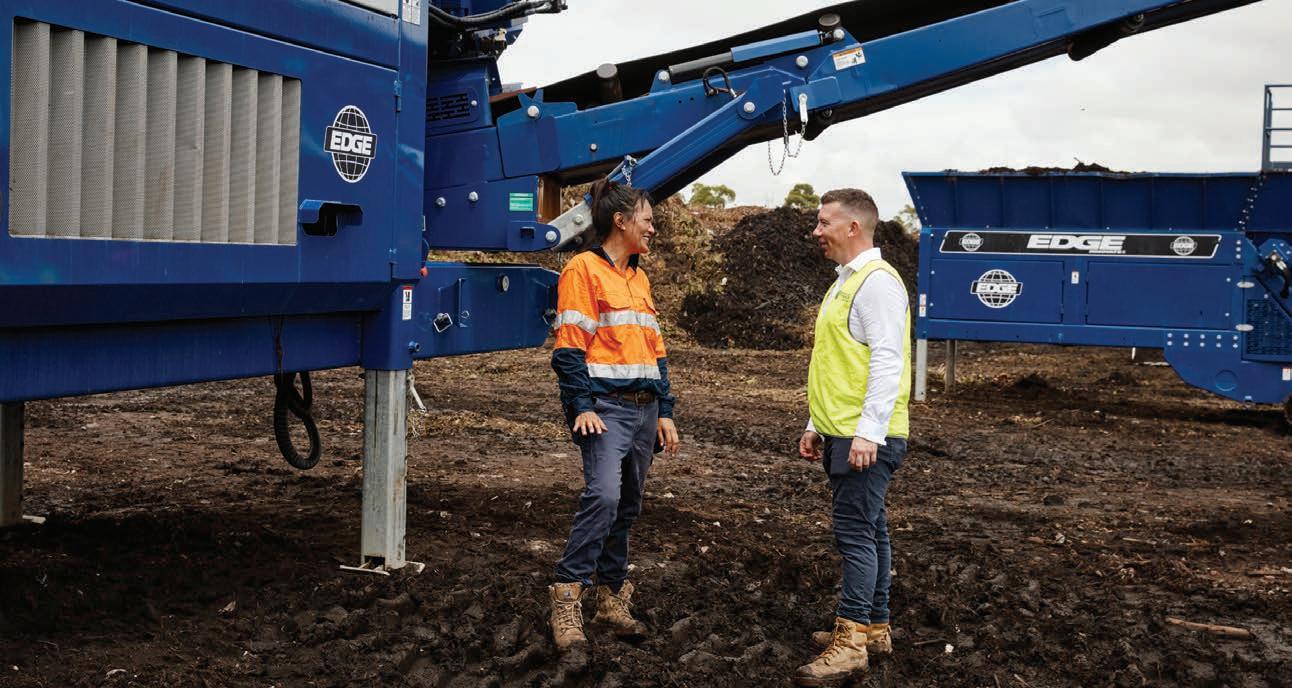
such as cardboard, plastic and FOGO, but there is still more that I believe can be done to educate the community on the importance of responsibly processing green waste.
“If there was a greater understanding it would change the whole process. We spend a huge amount of time sorting through rubbish at our picking station.”
THE COVID-19 IMPACT
Teri says that facilities such as the picking station were placed under greater pressure in 2020 during the COVID-19 pandemic.
She believes that increased participation in mowing lawns, gardening and tree maintenance during COVID-19 lockdowns led to a significant rise in green waste volumes received at the facility.
“The demand placed on our facility hit us hard and fast,” she says. “The tonnage of material which was coming in increased substantially. We also had to take in products from nearby transfer stations so they could sustain their operation.”
The influx of green waste materials also placed greater pressure on the storage capacity of the Eastern Creek site. New South Wales Environment Protection Authority regulations meant that stockpiling was limited at the site.
Teri says the culmination of these factors meant efficiency was paramount.
“One of the biggest challenges for our operation is limitations on stockpile heights. Currently we are only able to stack materials up to four metres,” Teri says. “Once we did start receiving larger amounts, the four-metre restriction put pressure on the facility.
“With this large amount coming in there was also the risk of fires due to stockpiling. Processing efficiency was definitely an important aspect.”
NECESSARY UPGRADES
Teri says it was the culmination of these factors that led management to look at acquiring new machinery.
An infrastructure update was also required to support the skilled workforce needed to process material quicker, reducing downtime at the site.
“Mid 2020 was when we first started looking for machines,” Teri says. “We had just completed a round of organics processing, which allowed us to have more room on site to begin processing larger sales and composting orders.
“After the first surge of COVID-19 we realised that it would be better to have a proactive approach. So, I was looking for a machine which would alter our actual footprint on site, to satisfy our needs,” she says.
It was during this period that Teri came across Focus Enviro’s FTS65 Mulch Master. The FTS65 Mulch Master has a bespoke hopper, complete
The FTS65 Mulch Master’s mobility has provided greater flexibility at the Eastern Creek site. with a forward and reverse auger, which it combines with a high-speed discharge conveyor thus ensuring an even spread of material. It also removes the need for separate feeders and stockpile units.
Teri says the introduction of an FTS65 Mulch Master at Eastern Creek has added greater flexibility to the site’s operation.
“The FTS65 Mulch Master is the new machine in our organic operation,” she says. “With an average throughput of 500m³/hr the FTS65 Mulch Master has allowed us to increase our ability to turn material, in comparison to what was achievable with the plant we previously operated. Its design provides optimum aeration of feed stock resulting in a dryer final product.”
“For me, it gives me the ability to manage run-off and leachate better. It really contributed to our ability to adhere to EPA regulations on site,” Teri says. “The throughput on the machine is also very fast.”
Teri says a windrow turner machine, which was elevated and on tracks, was previously used at the site. The windrow turner required a concrete hardstand and windrows needed to be a certain width, height, and size.
In contrast, the FTS65 Mulch Master is designed for quick and easy transportation, while its unique hopper design ensures all feed stock passes through the turner – a process not possible with traditional windrow turners.
“The Mulch Master enables us to have greater mobility in our operation, so we are able to drive that machine into the windrow, rather than taking time to displace the machine,” Teri says. “It greatly reduces downtime”.
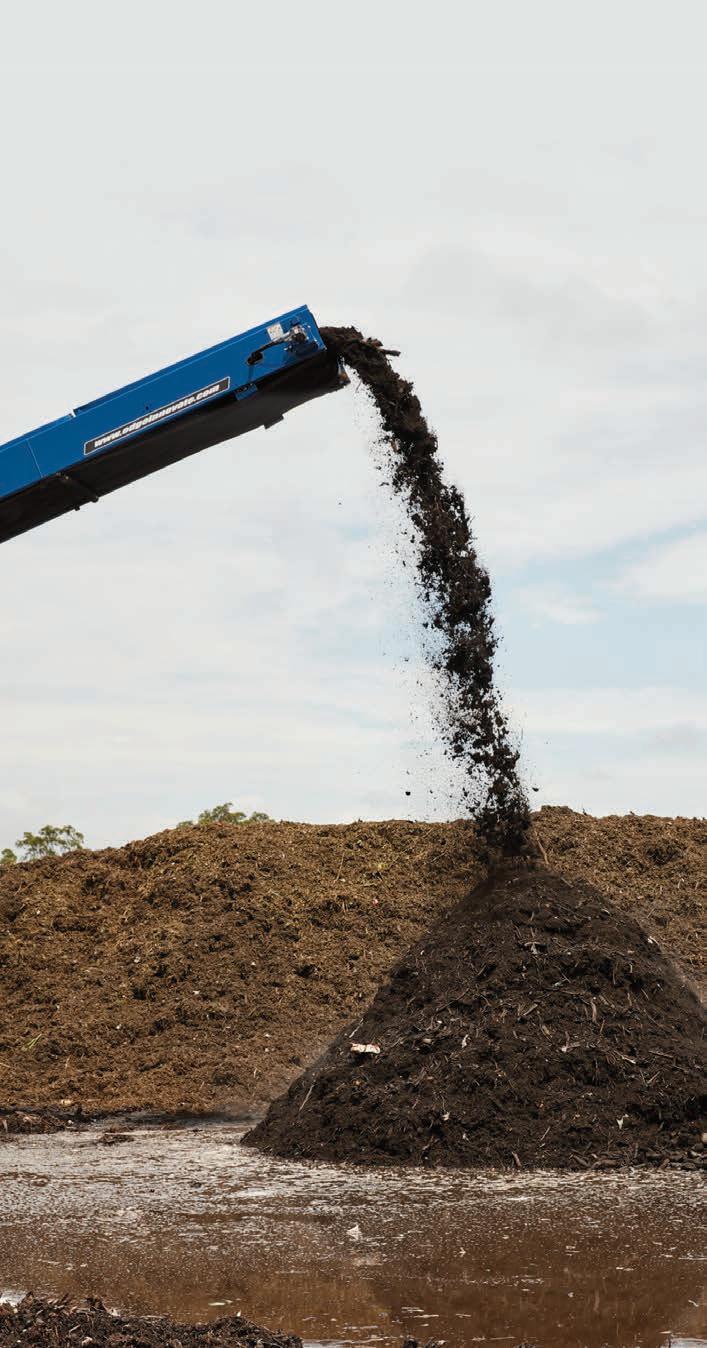
AN EYE-CATCHING FEATURE Teri says that purchasing a second machine from Focus Enviro was not planned. But when she and her team
went to learn more about the FTS65 Mulch Master, another product caught her eye.
“Initially when I went to Focus Enviro, I was going to have a look at the FTS65 Mulch Master, but we also came home with a TRT622 Tracked Trommel,” she says.
“When we got there, we were shown the 180 degree radial stacker on the TRT622 Tracked Trommel. At that point we decided to go with that product as well. I was immediately sold on that feature alone.”
The TRT622 offers a number of features including a unique load-sensing hydraulic-drive system, eco-power saving functionality that automatically reduces engine speed when material is not detected, and a user-friendly control panel to suit varying applications.
The TRT622 Tracked Trommel can process a wide range of waste streams, including C&D, industrial and skip management.
Its seven metre-long drum allows operators to use higher capacity when compared to general trommels.
The longer trommel barrel also allows material to spend more time screening, resulting in less oversize material being mixed with fine material. In turn, this means less material is required to be reprocessed, removing the need for double handling.
The screening angle of the TRT622 Tracked Trommel is adjustable, again providing added flexibility for operators.
Teri says the size and remote capability of the machine have also been standout features.
“The Tracked Trommel itself is actually larger than the other trommels we have on site,” she says.
“The remote stacker was another selling point for me. We have stackers on wheels at the site, which we move with loaders. Once I saw that this product can be accessed remotely, while our workers are inside their loaders filling the screen itself, for me that was a game changer.”
Teri adds that ease of operation is an essential pre-requisite, which both machines comfortably satisfy.
“The machines on our site need to be user friendly. Our operators need to be able to look at a machine and understand its basic functions. These machines are very straight forward,” she says.
“We have a large number of machines at this site, and the EDGE products supplied by Focus Enviro have performed as good, if not better, than anything else we have in use out there.”
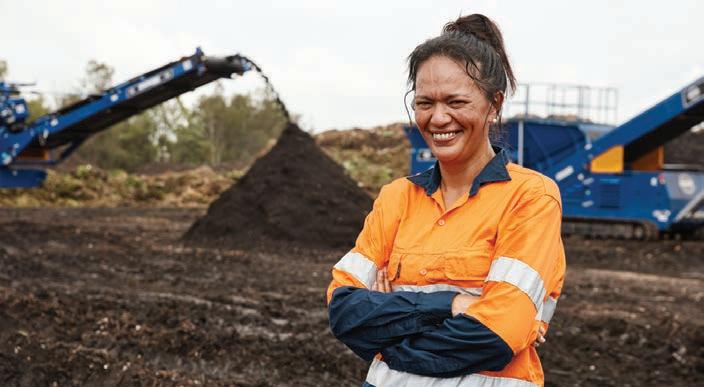
Teri Te Whiu, Site Supervisor at Eastern Creek.
FULL-FOCUSED SUPPORT
Teri says that Focus Enviro “is never too busy to help” when it comes to modification and maintenance requirements of the machines, although she says both machines have required minimal servicing.
“The machines do come from overseas and the Australian standards are slightly different so we have had to make safety modifications, such as hand railing at the top of the FTS65 Mulch Master,” she says.
“We purchased the Trommel in May last year and the machine has already accumulated 1300 hours of use. The Mulch Master has been in operation for approximately 700 hours. There has been very minimal downtime during this period.
“For any required upgrades we have requested, Focus Enviro has supplied the parts and supported us.
“My site now considers Focus Enviro a part of our team. They have come out and created great relationships with our operators, as well as myself.”
John McGuinness, State Manager for Focus Enviro, says it is an honour to be able to work with Teri in developing new strategies and processes to increase production and profitability at their facility.
“We were invited to demonstrate the merits of our equipment and impart the experience we have gained both in Australia and Europe in the processing of organics for recycling.
“The results ultimately ensured a fresh approach to machinery selection and the start of a great working relationship,” he says.
For more information, visit: www.focusenviro.com.au